Лекция №8 Приспособления для токарных и круглошлифовальных станков. Приспособления для круглошлифовальных станков
Приспособления к круглошлифовальным станкам модели ЛЗ-269Ф10
Съемник ЛЗ-269Ф1. 57.461Предназначен для демонтажа фланцев с шлифовальным кругом с конусного конца шлифовального шпинделя.
Втулка ЛЗ-269Ф10. 610.901Наружный диаметр втулки 100 мм, внутренний – 80 мм. Электрошпиндель ШФ36-48 устанавливается в приспособление для внутреннего шлифования без промежуточной втулки, т.к. отверстие в приспособлении и посадочная шейка электрошпинделя ШФ36-48 – Ø100 мм.При смене электрошпинделя ШФ36-48 на электрошпиндели ШФ60-90, ШФ90-120, ШФ120-150 в отверстие приспособления устанавливается втулка, т.к. посадочная шейка этих электрошпинделей – Ø80 мм.
Оправка ЛЗ-269Ф1.34.435 и съёмник ЛЗ-269Ф1.34.416Оправка является основной деталью цангового зажима поворотной бабки изделия ЛЗ-269.340.000. Устанавливается в шпиндель. Хвостовик оправки по наружному диаметру выполнен в виде конуса Морзе 2. Цанга вставляется в переднюю часть оправки. Зажимается с помощью штанги, ввёрнутой в резьбовое отверстие хвостовика.Съёмник служит для демонтажа оправки из шпинделя. При повороте он, упираясь торцем в шпиндель, вытягивает оправку из конусного гнезда шпинделя. Оправка и съемник входят в комплект обязательной поставки станка.Цанги поставляются по требованию заказчика за отдельную плату. Поставляются цанги с отверстием для крепления заготовки Ø1, 2, 3, 4, 5, 6, 7, 8 мм.
Центра укороченные ЛЗ-269Ф10.900.401Отличаются от покупных центров и оригинальных центров, применяемых в этом станке, общей длиной. Хвостовик имеет конус Морзе 2. Даёт возможность устанавливать в центра станка детали длиной до 250 мм, или приблизить зону шлифования к передней и задней бабкам для улучшения качества обработки.
Комплект хомутиковКомплект оригинальных малогабаритных хомутиков для деталей от 0,5 до 15 мм позволяет улучшить качество обработки, особенно при шлифовании миниатюрных деталей и деталей малого размера.
Втулка ЛЗ-269Ф1.34.445Представляет собой втулку с наружным конусом Морзе 2 и внутренним конусом Морзе 1.Предназначена для работ с поворотной бабкой изделия ЛЗ-269.340.000, шпиндель которой вращается. В отверстие шпинделя с конусом Морзе 2 поочерёдно устанавливаются патрон, цанговый зажим или втулка.
Патрон в сбореПредставляет собой сборку, состоящую из стандартного патрона 7100-001В ГОСТ 2675-80, или аналогичного импортного, и фланца. Хвостовик фланца выполнен в виде конуса Морзе 2.С помощью доработки кулачков стандартного патрона можно расширить диапазон изделий, устанавливаемых в патрон по наружному диаметру. Доработка чаще всего используется при внутреннем шлифовании.
Люнет двухопорный ЛЗ-269Ф1.21.000Используется при наружном шлифовании длинных валов и деталей с большим отношением длины к диаметру для компенсации прогиба, возникающего под воздействием сил резания.Двухопорный люнет позволяет вести процесс шлифования с осциллированием детали относительно шлифовального круга. Осциллирование производится ходом стола станка.Люнет съёмный. Устанавливается на стол станка и закрепляется с помощью зажимного устройства поворотом винта. Опоры люнета регулируемые. После установки люнета на стол каждая из них подводится к поверхности детали до соприкосновения. Опоры выполнены из антифрикционного материала.
Люнет трёхопорный ЛЗ-269Ф1. 22.000Используется при наружном шлифовании коротких шеек на длинных валах и деталях с большим отношением длины к диаметру для компенсации прогиба, возникающего под воздействием сил резания, а также при внутреннем шлифовании длинных деталей, закреплённых в патроне.При шлифовании коротких шеек опоры люнета устанавливаются на необрабатываемую поверхность вала вблизи обрабатываемой. При внутреннем шлифовании люнет, по возможности, устанавливается у правого торца детали.Для обеспечения возможности установки детали в люнет верхняя опора сделана откидной.Люнет съёмный. Устанавливается на стол станка и закрепляется с помощью зажимного устройства поворотом винта. Опоры люнета регулируемые. После установки люнета на стол каждая из них подводится к поверхности детали до соприкосновения.
Приспособление для правки шлифовального круга по радиусу ЛЗ-269Ф1.23.000Приспособление используется на всех исполнениях станка ЛЗ-269Ф10. С его помощью переферии круга придаётся торондальная форма. Это позволяет шлифовать на валах и в отверстиях радиусные канавки, галтели и другие поверхности.Приспособление съёмное. Устанавливается на стол станка на время правки. Закрепляется на столе с помощью зажимного устройства поворотом винта.Державка с алмазом находится в корпусе, поворачивающемся вокруг вертикальной оси от упора до упора. Величина радиуса правки настраивается заранее.В державку приспособления устанавливаются алмазные карандаши или алмазы в оправе.
Приспособление для правки шлифовального круга при внутреннем шлифования ЛЗ-269Ф1.24.000Используются на станках ЛЗ-269Ф10-01 и ЛЗ-269Ф10-02, на которых имеется устройство для внутреннего шлифования.Приспособление съёмное. Устанавливается на стол станка для правки. Закрепляется на столе с помощью зажимного устройства поворотом винта.Державка с алмазом находится в откидном корпусе. Это позволяет в ряде случаев не снимать приспособление при шлифовании детали.В державку приспособления устанавливаются алмазные карандаши или алмазы в оправе. Правильно проведённая правка круга при шлифовании деталей из конструкционных сталей обеспечивает шероховатость поверхности отверстия до Ra 0,08.
Приспособление для правки шлифовального круга под углом ЛЗ-269Ф1. 25.000Используется на станках ЛЗ-269Ф10-00, ЛЗ-269Ф10-01 и ЛЗ-269Ф10-02.Предназначено для правки периферии и торца круга для наружного шлифования. Его можно использовать для правки круга при внутреннем шлифовании.Приспособление съёмное. Устанавливается на стол станка на время правки. Закрепляется на столе с помощью зажимного устройства поворотом винта.Державка с алмазом смонтирована в корпус, который поворачивается вокруг вертикальной оси и может быть установлен под углом к оси шлифовального круга.В державку приспособления устанавливаются алмазные карандаши или алмазы в оправе.
Фланцы для шлифовального круга Ф150ммКруг с наружным диаметром 150мм устанавливается на правую конусную шейку шлифовального шпинделя.Используется при лобовом шлифовании – шлифовании торца детали периферией круга, при шлифовании конических поверхностей с большим углом конуса. При этих работах используется поворот шлифовальной бабки.На фланцы устанавливаются круги с наружным диаметром 150 мм, внутренним - 51 мм, шириной 10-20 мм.
Фланцы для шлифовального круга Ф200ммКруг с наружным диаметром 200 мм устанавливается на левую конусную шейку шлифовального шпинделя. Он используется при всех видах наружного шлифования и торцевом шлифовании.В связи с этим целесообразно иметь набор из нескольких комплектов фланцев в сборе кругами. Позволяется возможность заранее отбалансировать и профилировать круги для конкретных деталей и производить быструю переналадку при смене обрабатываемых деталей.На фланцы устанавливаются круги с наружным диаметром 200 мм, внутренним - 76 мм, шириной от 10 до 20 мм. При использовании алмазных или абразивных кругов с другим внутренним диаметром по спец. Заказу могут быть изготовлены необходимые фланцы.
Приспособление для балансировки шлифовальных кругов ЛЗ-269Ф1.54.000 и оправка для балансировки шлифовального круга ЛЗ-269Ф1.53.000После установки нового круга на фланцы необходимо произвести статическую балансировку.Для этого круг вместе с фланцами монтируется на оправку для балансировки. Оправка устанавливается на опоры приспособления. Поворотом ручки крана на приспособлении обеспечивают доступ воздуха, находящегося под давлением, из сети цеха или от блока подготовки воздуха, имеющегося на станке, в аэростатические опоры приспособления.Оправка с фланцами и кругом «всплывает» и начинает колебаться. Балансировка производится с помощью сухариков, находящихся на фланце круга.На приспособлении также производится балансировка круга после первой правки и при необходимости, в процессе эксплуатации станка. Приспособление обеспечивает сверхточную статическую балансировку шлифовального круга из-за отсутствия трения в аэростатических опорах.
Оправки для внутреннего шлифованияПри шлифовании отверстий в деталях, целесообразно для каждого конкретного случая разрабатывать оправку шлифовального круга. Правильно спроектированная оправка обеспечивает получение заданной геометрической точности и шероховатости обработанной поверхности, производительности и, что чрезвычайно важно, безопасность работы при шлифовании высокоскоростными электрошпинделями.По требованию заказчика за отдельную плату поставляются оправки, обладающие некоторой универсальностью. При заказе этих оправок необходимо обращать внимание на размеры шлифовального круга, если оправка поставляется с наклеенным кругом.Следует учитывать, что диаметр неизношенного, предварительно правленого круга, должен быть равен 0,6 (0,5) – 0,8 (0,9) от диаметра обрабатываемого отверстия.Поставляемые оправки делятся на следующие группы:1.Оправки для электрошпинделя ШФ 36-48 с креплением круга гайкой.1.1. Оправка ЛЗ-269Ф10.940.401, гайка ЛЗ-239В.94.462.Размеры устанавливаемого круга: - внутренний диаметр 6мм, - высота круга 20мм, - наружный диаметр в пределах 13-20мм выбирается по ГОСТ2424-83, исходя из соотношения 0,6 (0,5) – 0,8 от диаметра обрабатываемого отверстия.Наибольшая окружная скорость круга не должна превышать 35- 50м/с.1.2. Оправка ЛЗ-269Ф10.940.402, гайка ЛЗ-239В.94.462-03.Размеры устанавливаемого круга: - внутренний диаметр 4мм, - высота круга 13мм, - наружный диаметр в пределах 8-13мм выбирается так же, как в п.1.1.2. Оправки для электрошпинделя ШФ60-90. 2.1 Крепление круга гайкой.Оправка ЛЗ-269Ф10.940.403, гайка ЛЗ-239В.94.462-03Размеры устанавливаемого круга: - внутренний диаметр 4мм, - высота круга 13мм, - наружный диаметр в пределах 10-13мм выбирается по ГОСТ24242-83, исходя из соотношения 0,6(0,5) – 0,8 от диаметра обрабатываемого отверстия. Наибольшая окружная скорость круга не должна превышать 35-50м/с.2.2. Крепление круга клейкой.Оправки с кругами:ЛЗ-269Ф1.61.020 (4х6х1,8мм),ЛЗ-269Ф1.61.020-01 (5х6х2мм),ЛЗ-269Ф1.61.020-02 (6х5х3мм),ЛЗ-269Ф1.61.020-03 (8х7х3мм).При выборе оправки исходить из соотношения: диаметр круга 0,8(0,9) диаметра обрабатываемой детали.Оправки устанавливаются в электрошпиндель. Гнездо последнего имеет центрирующее и резьбовое отверстия под оправку.3. Оправки для электрошпинделей ШФ90-120 и ШФ120-150.3.1. Оправка ЛЗ-269Ф10.940.020.Крепление круга клейкой. Оправка устанавливается непосредственно в гнездо элекрошпинделя. Предназначена для ШФ90-120.Размеры шлифовального круга:* внутренний диаметр 3мм,* высота круга 5мм,* наружный диаметр круга 6-8мм.3.2. Оправки с кругами, крепление круга клейкой:* ЛЗ-242.94.090 (1х1,6х0,5мм),* ЛЗ-242.94.090-01 (1,5х1,7х0,8мм),* ЛЗ-242.94.090-02 (3х2,5х1,5мм),* ЛЗ-242.94.090-06 (4х3х2мм).При выборе оправки исходить из соотношения: диаметр круга 0,8 (0,9) диаметра обрабатываемой детали.Оправки устанавливаются в электрошпиндель с помощью цангового патрона, состоящего из цанги ЛЗ-242.94.412 и гайки ЛЗ-242.94.411.
zps.ru
Приспособления для шлифования | Приспособления для станков
Приспособление, изображенное на рис. 105, применяют для шлифования конуса центров, втулок и т. п. на круглошлифовальном станке. Приспособление устанавливают на стол станка и закрепляют винтами 1, а шлифуемую деталь - в сменную втулку 4. Верхнюю часть приспособления 3 поворачивают по лимбу на угол конуса детали и закрепляют гайками 2.
При малых углах конуса деталь вращается от передней бабки; при больших углах конуса деталь вращают вручную рукояткой 5.
Рис. 105. Приспособление для шлифования конусных деталей на круглошлифовальном станке
Приспособление для шлифования скосов фиксаторов. Скосы деталей типа фиксаторов шлифуют в приспособлении (рис. 106), состоящем из корпуса 1, втулки 2 и винта 3. Скосы корпуса 1 соответствуют углам скоса фиксатора. Отверстия под сменную втулку 2 и под резьбу винта 3 растачивают на координатно-расточном станке по центру скосов корпуса. Винт 3 фиксирует обрабатываемую деталь по шпоночному пазу.
Рис 106 - Приспособление для шлифования скосов фиксаторов
Внутреннее отверстие втулки 2 обеспечивает скользящую посадку фиксатора. При шлифовании скосов приспособление устанавливают на магнитную плиту станка поочередно на два скоса корпуса 1 и по нониусу выдерживают высоту Н шлифовального круга. Приспособление обеспечивает быструю и точную обработку симметричных скосов у деталей типа фиксаторов.
Приспособления для шлифования тонкостенных втулок. При шлифовании отверстий тонкостенных втулок с креплением в кулачковом патроне за наружную поверхность искажается геометрическая форма втулки. Слабое зажатие втулки опасно, так как возможен вырыв ее из патрона. Закрепление в разжимной втулке уменьшает деформацию, но не устраняет ее полностью.
Рис. 107 Приспособление для шлифования тонкостенных втулок: а - диаметром отверстия 50-200 мм; б - с толщиной стенки 2,5 мм и меньше
Приспособление, изображенное на рис. 107, а, устраняет деформацию втулок, так как втулку зажимают за торец и радиальные силы отсутствуют. Фиксирующие и зажимные сухари 2 и 3 перемещают в пазах планшайбы 7, они могут быть установлены для любого диаметра втулки в пределах 50-200 мм. Опорные поверхности сухарей 2 шлифуют после установки приспособления на станке. Опорные шпильки 4 регулируют по высоте в зависимости от высоты втулок. Приспособление с незначительной переналадкой используют для шлифования втулок различного диаметра и высоты.
Для шлифования втулок, толщина стенок которых равна 2,5 мм и меньше, применяют приспособление, показанное на рис. 107, б. Тонкостенные втулки шлифуют предварительно по наружной поверхности и торцам с посадкой Х3 и припуском под окончательное шлифование. Корпус 1 приспособления зажимают в кулачках патрона и шлифуют по внутренней поверхности, диаметр которой соответствует наружному диаметру втулки и торцу А с проверкой по индикатору. Шлифуемую втулку вставляют в отверстие корпуса 1 и зажимают гайкой 2 за торец Б.
Похожие материалы
www.metalcutting.ru
Приспособление для обработки на круглошлифовальных станках
Приспособление для обработки на круглошлифовальных станкахКатегория:
Шлифовальные станки
Приспособление для обработки на круглошлифовальных станкахНа круглошлифовальных станках в большинстве случаев деталь устанавливается на неподвижных центрах. На рис. 1, а приведена форма центрового отверстия с прямолинейной образующей несущего конуса. Точность установки детали при обработке зависит от точности формы и положения упорных центров станка и несущих поверхностей центровых отверстий детали (или оправки). При несовмещении осей конусов и погрешностей их формы неизбежно возникает неполное прилегание несущих поверхностей отверстий детали к упорным центрам станка, что вызывает неравномерный их износ и неплавное вращение из-за скачкообразного характера пространственного перемещения детали что приводит к погрешностям формы обрабатываемых поверхностей. Лучшие результаты достигаются при центровых отверстиях; с выпуклой образующей. Достоинства центровых отверстий такой формы — нечувствительность к угловым погрешностям, лучшее удержание смазки, снижение погрешности установки и повышение точности обработки. Однако и при них не устраняются погрешности, возникающие при несовмещении осей центровых отверстий детали и центров станка. Эти погрешности устраняются при сферической форме упорных центров станка, так как два сферических центра всегда соосны, зона контакта центров станка и центровых отверстий детали в процессе обработки сохраняется постоянной, а ее форма и размеры остаются неизменными.
Рис. 1. Формы центровых отверстий
Характерная особенность установки детали на сферические упорные центры станка заключается в том, что деталь совершает в пространстве простое вращательное движение вместо сложного скачкообразного движения при установке на конические упорные центры. Такие центры исключают возможность точечного контакта. Сферические центры обладают повышенной стойкостью и хорошей смазываемо-стью — капиллярный эффект способствует удержанию смазки у площадки сферической поверхности.
Для передачи вращательного движения шпинделя станка к детали, установленной в центрах, применяется поводковый хомутик. Одним из источников возникновения погрешностей формы в поперечном сечении детали является широко применяемый одноплечевой поводок, передающий крутящий момент от станка к детали» Снижение некруглости детали можно достичь применением торцовых поводковых устройств. На рис. 2 изображена поводковая планшайба, установленная на круглошлифовальном станке. Устройство имеет не менее двух ведущих кулачков. На одном из торцов детали выполняют несколько поводковых углублений в виде клиновых канавок или конусных углублений. Ведущие кулачки, рабочая часть которых соответствует форме поводковых углублений, входят в поводковые углубления детали и через их поверхность передают крутящий момент от станка. Точность расположения поводковых углублений друг относительно друга и относительно центрового отверстия достигается выдавливанием последнего одновременно с поводковыми углублениями одним инструментом.
Рис. 2. Торцовое поводковое устройство
Применение торцовых поводковых устройств одновременно обеспечивает снижение затрат вспомогательного времени, создает возможность обработки детали по всей длине без перезакрепления. Обработка деталей с установкой на сферических упорных центрах станка обеспечивает повышение точности формы деталей по сравнению с обработкой на конических упорных центрах станка. Повышение точности формы деталей достигается за счет исключения влияния неточностей взаимного положения центровых отверстий детали и взаимного положения центров станка. При передаче крутящего момента от станка детали посредством торцовых поводков также способствует повышению точности формы детали благодаря симметричному приложению окружного усилия.
Рис. 3. Жесткие оправки:а — установка по конусу, б — с закреплением по торцу, в — с подкладной шайбой
На шлифовальных станках детали часто устанавливаются на оправке —центровой и консольной. Оправки подразделяются на жесткие, разжимные, с раздвижными элементами, с гидравлическим или гидропластовым разжимом. Жесткие оправки показаны ка рис. 65. Деталь надевают на оправку со стороны приемного конуса, продвигают ее по цилиндрической части и заклинивают на конусе, для чего ударяют левым торцом оправки о деревянную подкладку. Если отверстие детали неточно, то ее закрепляют по торцу. При обработке коротких деталей на одну оправку можно насадить несколько деталей, закрепив их гайкой. Если диаметр гайки меньше диаметра отверстия обрабатываемых деталей, под гайку подкладывают разрезную шайбу. Для освобождения детали гайку слегка ослабляют, шайбу удаляют, а деталь снимают с оправки через гайку. У таких оправок резьба выполняется с крупным шагом. Конусность оправки зависит от длины детали. Чем длиннее отверстие, тем меньше должна быть конусность оправки, и наоборот. Это облегчает закрепление и снятие детали. В целях сокращения вспомогательного времени при работе используют две оправки. В то время как на одной ведется обработка, на другой закрепляют детали.
Разжимные оправки. При обработке тонкостенных деталей применение жестких оправок может вызвать искажение формы деталей, в этих случаях применяют разжимные оправки. У цанговых оправок цанга с продольными прорезями, перемещаясь с помощью гайки по конусу, упруго разжимается и закрепляет деталь. Штифт удерживает ее от поворота, а гайка служит для отжа-тия при снятии детали.
Раздвижные оправки. На рис. 67 показана консольная шариковая оправка для коротких деталей. В сепараторе имеется шесть отверстий с шариками диаметром 6— 10 мм, находящимися в контакте с конусом корпуса оправки. Осевое перемещение сепаратора в оправке производится винтом через скользящую втулку, к которой прикреплен сепаратор. При перемещении и раз-движении шариков деталь центрируется и одновременно поджимается к осевому упору. Для точного центрирований необходимо, чтобы шарики не отличались по диаметру больше, чем на 2 мкм, а установочный и центрирующий конусы были соосны. На шариковых оправках можно зажимать детали с разницей в диаметре до 5 мкм.
Оправки с гидравлическим или гидрапластовым зажимом. Оправки легче приспособить к неточностям формы отверстия, в результате чего точнее центрируется деталь. В такие оправки зажимают деталь вследствие деформирования тонкостенного цилиндра, находящегося под равномерным давлением изнутри. Для создания давления используется жидкость или пластмасса. Оправки подразделяются на два типа: А и Б. Тип А для диаметров 20— 40 мм, тип Б—свыше 40 мм. На корпус напрессована втулка центрирующая втулка, которая стопорится винтом. Пространство между корпусом и втулкой заливается гидропластом. Усилие зажима передается плунжером через винт. В оправках типа А есть отверстие для выхода воздуха, которое перекрывается прокладкой и винтом. Точность центрирования оправки с гидропластом зависит от точности изготовления корпуса и втулки.
Рис. 4. Разжимная оправка
Рис. 5. Раздвижная оправка
Рис. 6. Оправки с гидропластом
Рис. 7. Самозажимный плавающий патрон
Патрон с роликовым зажимом. Патрон служит для зажима цилиндрических деталей по наружной поверхности. Корпус патрона имеет фланец с центрирующим пояском и отверстиями для крепления станка к планшайбе. Рабочая часть патрона имеет наружную конусную поверхность и строго концентричное с пояском отверстие, в которое вставляется обрабатываемая деталь. Зажимное кольцо расточено на конус в соответствии с конусностью корпуса. Между корпусом и зажимным кольцом находится сепаратор с роликами, расположенными под небольшим углом к оси патрона. Для предохранения роликов от грязи и жидкости с обеих сторон сепаратора предусмотрены фетровые кольца, удерживаемые металлическими разрезными кольцами. Эти же кольца, между которыми заключен (с некоторым зазором) сепаратор, препятствуют самопроизвольному снятию зажимного кольца.
Читать далее:
Способы и особенности бесцентрового шлифования
Статьи по теме:
pereosnastka.ru
Лекция №8 Приспособления для токарных и круглошлифовальных станков
ЛЕКЦИЯ № 8Приспособления для токарных и круглошлифовальных станков
На токарных и круглошлифовальных станках обрабатываемые детали в зависимости от формы и размеров, устанавливают в центрах или в патроне. Один центр расположен в шпинделе передней бабки, а второй в шпинделе задней бабки токарного или шлифовального станка. Патрон устанавливают и закрепляют на конце шпинделя передней бабки станка.
Центры подразделяют на следующие типы:
1. Неподвижные нормальные и специальные;
2. Вращающиеся нормальные и специальные;
3. Плавающие специальные;
4. Рифленые специальные;
5. Срезанные.
Конусная поверхность центра предназначена для установки детали и имеет угол при вершине 60°, 90°, 120°; хвостовик центра изготовляют с конусом Морзе определенного номера (№ 2, 3, 4, 5, 6).
Не вращающиеся центры станков от трения сильно нагреваются и изнашиваются. Для уменьшения износа и увеличения срока их службы применяют вращающиеся задние центры, менее точные, чем не вращающиеся. Задний центр (рис. 1) применяют для
установки заготовок с центровыми отверстиями, а задний центр, показанный на рис. 2 для обработки заготовок полых деталей.
Основные размеры вращающихся центров нормализованы.
При обработке ступенчатых валов на многорезцовых станках для получения заданных линейных размеров заготовку вала устанавливают на плавающий (подпружиненный) передний центр.
На рис.3 показана конструкция такого подпружиненного центра. Такие центры применяют также при обработке на станках с ЧПУ.
Обработка валика в центрах токарного станка с поводковым устройством для вращения заготовки представлена на рис. 4.
Сила для вдавливания поводков в торец обрабатываемой заготовки:
При обработке заготовки в центрах с рифленым центром (рис. 5), представляющим собой поводок, вращающий деталь при обработке, сила, требуемая для вдавливания рифленого поводкового центра в заготовку:
Срезанные центры (рис. 6) позволяют обрабатывать торец заготовки, закрепленной в центрах.
^ применяют для передачи вращательного движения (крутящего момента) от шпинделя станка к обрабатываемой заготовке 2, установленной в центрах, на оправке или в патроне. К поводковым приспособлениям относятся хомутики 1, поводковые планшайбы 3. Схема поводкового патрона представлена на рис. 7.
Хомутик 1 с ручным зажимом надевают на заготовку 2, крепят винтом и затем заготовку с хомутиком устанавливают в центрах станка. При включении станка обрабатываемая заготовка через поводковую планшайбу и хомутик вращается от шпинделя станка.
Самозажимные поводковые патроны изготовляют с двумя или тремя эксцентриковыми кулачками с насечкой, которые в начале обработки под действием сил резания зажимают заготовку, установленную в центрах станка и передают ей крутящий момент от шпинделя станка.
При увеличении крутящего момента резания автоматически увеличивается и крутящий момент от шпинделя, передаваемый кулачками патрона на заготовку.
Для удобной установки заготовки в центры применяют поводковые патроны с автоматическими раскрывающимися кулачками. Равномерный зажим заготовки всеми кулачками обеспечивается тем, что применяют плавающие кулачки или кулачки с независимым перемещением. Самозажимные поводковые патроны позволяют устанавливать кулачки на различный диаметр обрабатываемых заготовок в определенном диапазоне. Эти патроны применяют при центровой обработке на многорезцовых станках или станках с ЧПУ для передачи заготовке от шпинделя станка больших крутящих моментов.
На рис. 11 показан поводковый патрон с двумя эксцентриковыми сменными кулачками. Фланец 8 патрона устанавливают коническим отверстием на шпиндель и крепят винтами к его фланцу. Корпус 10 патрона соединяется с фланцем 8 винтами 7, проходящими через распорные втулки 6, он имеет ведущие пальцы 9, на которых установлены кулачки 2. Для одновременного зажима заготовки двумя кулачками корпус 10 может перемещаться относительно фланца в направлении его пазов и пружиной 3 поворачиваться в начальное положение.
В момент включения станка шпиндель с патроном начинает вращаться и кулачки 2 под действием центробежных сил от грузов 1, мгновенно поворачиваясь на пальцах, предварительно зажимают заготовку, предупреждая ее провертывание в начале резания, окончательный зажим заготовки производится в начальный момент резания от составляющей силы резания Р. После обработки станок выключается, шпиндель не вращается, кулачки 2 толкателями 5 под действием пружин 4 поворачиваются на пальцах 9 в исходное положение и деталь разжимается.
Меняя кулачки патрона, обеспечивают изготовление деталей диаметром 30-150 мм.
Центробежную силу определяют через массу груза и угловую скорость вращения его центра тяжести:
Рц = mω2R,
Суммарная сила зажима кулачками патрона:
^
где Z — число кулачков патрона.
Двухкулачковые поводковые патроны нормализованы, они могут иметь плавающий (подпружиненный) центр.
^
применяют для установки и зажима заготовок различных деталей, обрабатываемых на токарных и шлифовальных станках. В зависимости от количества кулачков патроны разделяются на двух-, трех- и четырехкулачковые. Патроны двух- и трех- кулачковые являются самоцентрирующими; четырехкулачковые патроны изготовляют в основном с независимым перемещением кулачков, но бывают и самоцентрирующие.
Наибольшее применение имеют универсальные трехкулачковые спирально-реечные патроны. На рис. 12 показан трехкулачковый спирально-реечный самоцентрирующий патрон, устанавливаемый на резьбовом конце шпинделя токарного станка. В корпусе 1 патрона расположен диск 2, имеющий на одном торце коническое зубчатое колесо, а на другом — спиральные реечные пазы, находящиеся в зацеплении с рейками 3. В крестообразном пазу реек 3 устанавливают и закрепляют винтами 4 прямые или обратные накладные кулачки 5. При вращении торцовым ключом одного из трех конических колес 6, находящихся в зацеплении с коническим колесом диска 2, последний поворачивается и перемещает рейки 3 с кулачками 5 к оси патрона при зажиме заготовки и от оси — при разжиме.
Крышка 7 удерживает диск 2 в корпусе патрона от продольного смещения и препятствует попаданию в патрон стружки и грязи.
Некоторые патроны изготавливаются с цельными прямыми или обратными кулачками с нарезанными на их торцах рейками для непосредственного сопряжения со спиральными пазами диска 2. Недостаток этих патронов состоит в том, что радиусы кривизны на различных участках спирали диска 2 различны, а радиус реек 3 кулачков одинаков, поэтому соприкосновение реек 3 с витками спирали диска 2 происходит не по всей поверхности, а по небольшим узким участкам.
При неполном зацеплении витков спирали диска с рейками кулачков возникают высокие удельные давления в сопряжении и происходит значительный износ центрирующего механизма и потеря точности патрона. Для повышения износоустойчивости применяют закалку, и шлифование витков спирали диска и реек кулачков патрона.
Универсальные четырехкулачковые патроны применяют для установки и зажима заготовок некруглой формы, обрабатываемых на токарных, револьверных, сверлильных станках в единичном и серийном производствах. На рис. 13 показан универсальный четырехкулачковый патрон с механизированным приводом для перемещения кулачков к оси и от оси патрона.
Каждый кулачок независимо от других можно устанавливать на требуемое расстояние от оси патрона в соответствии с формой и размерами обрабатываемых заготовок. Предварительный зажим заготовки производится одной парой кулачков и затем - второй, окончательный, всеми четырьмя кулачками одновременно. При перемещении поршня со штоком в пневмоцилиндре влево шток через тягу и винт 1 передвигает втулки 2 и 7, последняя установлена на резьбе втулки 2. При перемещении влево втулка 7 через плавающие шарики 8 передвигает втулки 3 и 4. Эти втулки имеют по два диаметрально расположенных паза, в которых установлены попарно длинными плечами рычаги 6 и 10. Каждая втулка 3 и 4 поворачивает только одну пару рычагов 10 и 6. Втулки 3 и 4 под действием плавающих шариков 8, перемещаясь влево, поворачивают рычаги 10 на осях 11 и рычаги 6 на осях 5, а короткими плечами каждая пара рычагов 10 и 6 сдвигает кулачки 9 к центру патрона, и деталь зажимается.
При перемещении поршня со штоком в пневмоцилиндре вправо шток через тягу и винт 1 передвигает втулки 2 и 7 и втулка 2 через плавающие шарики 8 смещает втулки 3 и 4 вправо. Тогда и втулки поворачивают длинные плечи каждой пары рычагов 10 и 6 вправо, а короткие плечи рычагов разводят кулачки 9, деталь разжимается.
Зажим и разжим каждой парой кулачков производится последовательно с помощью плавающих секторов 8 и 12, перемещающихся перпендикулярно относительно оси патрона.
Сила зажима заготовки одним кулачком патрона:
К=1,3…1,6 – коэффициент
запаса;
R – радиус зажатой кулачками части заготовки;
Rо – радиус обрабатываемой части детали;
f – коэффициент трения между заготовкой и кулачками.
^
Патроны для закрепления цилиндрических и конических зубчатых колес при шлифовании отверстий используются после закалки профиля зубьев. Эта операция обычно является последней и обеспечивает концентричность оси начальной окружности колеса с осью центрального отверстия. Центрирование и закрепление зубчатого колеса в патронах при шлифовании центрального отверстия производится по боковым профилям зубьев. Для этого во впадины прямозубого цилиндрического колеса устанавливают ролики, во впадины косозубого цилиндрического колеса - шарики или витые упругие ролики, во впадины конического колеса — шарики.
Патроны для центрирования и закрепления зубчатых колес при шлифовании отверстия подразделяют на четыре группы:
1. Для одновенцовых цилиндрических колес;
2. Для двух- и многовенцовых цилиндрических колес;
3. Для цилиндрических колес с внутренним зацеплением;
4. Для конических зубчатых колес.
Патроны подразделяют на специальные и универсальные. Специальные патроны применяют для шлифования отверстия зубчатых колес одного типоразмера, универсальные - для нескольких типоразмеров. При проектировании таких патронов необходимо рассчитывать диаметр роликов (шариков), устанавливаемых во впадинах зубчатого колеса, и расстояние между осью роликов и осью патрона.
На рис. 15 показан мембранный патрон с пятью кулачками для шлифования отверстия в цилиндрических зубчатых колесах. Эти патроны обеспечивают высокую точность центрирования колес, надежны в эксплуатации и просты в изготовлении. В патроне можно закреплять цилиндрические колеса с прямыми зубьями с наибольшим наружным диаметром 175 мм и числом зубьев, кратным пяти.
Корпус патрона 1 крепится к планшайбе 9 винтами 8. Патрон с планшайбой устанавливают внутри шлифовального станка.
В патроне имеется мембрана (диск) 10, изготовленная заодно с пятью рожками (кулачками), равномерно расположенными по окружности мембраны. В отверстиях рожков мембраны закреплены сферические опоры 11. Мембрана 10 крепится к корпусу 1 десятью винтами. На передней части корпуса имеются пять радиальных прямоугольных пазов, в которых установлены направляющие колодки 18, закрываемые секторами 17, закрепленными на корпусе. Колодки 18 имеют на торце крестообразные пазы для установки сменных кулачков 13, закрепляемых на колодках винтами. В отверстие вставлены резиновые стержни 14, в которые ввинчены ролики 15.
Центрирование обрабатываемого зубчатого колеса производится роликами 15, которые свободно расположены во впадине между зубьями колеса. Торцом зубчатое колесо упирается в торцы сменных кулачков 13. При подаче сжатого воздуха в левую полость пневмоцилиндра поршень со штоком и тягой двигается вправо и шток через тягу и втулку 4 перемещает втулку 3, которая головкой нажимает на мембрану 10 и выгибает ее, а рожки с кулачками 13 разводятся и зубчатое колесо устанавливается в патрон.
Во время подачи сжатого воздуха в правую полость пневмоцилиндра поршень со штоком и тягой перемещается влево и шток через тягу и втулку 4 отводит втулку 3 от мембраны 10. Мембрана 10 за счет упругих сил выпрямляется, и рожки и опоры 11 через сферические шайбы 12 перемещают колодки 18 с кулачками 13 к центру. Кулачки 13, нажимая на ролики 15, центрируют и зажимают зубчатое колесо.
При смене кулачков 13 рабочая поверхность установочных кулачков и их опорные торцы шлифуются на станке. При шлифовании кулачки находятся в сведенном положении и между ними по поверхностям "А" закрепляется кольцо 16.
Втулка 7 предохраняет мембрану 10 от излишнего прогиба. Перемещение кулачков 13 регулируется продольным перемещением втулки 3, которая крепится шариком 6 и винтом 5.
^
различают двух видов: круглые патроны с постоянными магнитами и круглые электромагнитные патроны.
Круглые патроны с постоянными магнитами применяют для установки и закрепления заготовок на токарных и шлифовальных станках. Закрепление заготовок на таких патронах происходит быстро. Базовые поверхности заготовок — колец, дисков — должны представлять собой плоскость с шероховатостью Ra=2,5…l,25 мкм. С увеличением шероховатости на базовой поверхности заготовок сила ее крепления на патроне значительно снижается, так как увеличивается воздушный зазор, который создает большое сопротивление прохождению магнитного потока.
Сила закрепления при установке на патрон закаленных заготовок больше, чем при установке незакаленных деталей.
Магнитные патроны применяют при чистовом протачивании поверхностей небольших деталей на токарных станках и при шлифовании наружных и внутренних поверхностей на шлифовальных станках.
На рис.16 показан патрон с постоянным магнитом с наружным диаметром 265 мм. Патрон имеет корпус 8 из силумина, верхнюю 11 и нижнюю 14 плиты. В корпусе размещается магнитный блок, состоящий из цилиндрических постоянных магнитов 6 и пластин 7 из железа Армко, залитых эпоксидным клеем. Магнитный блок смонтирован на промежуточной плите 16, на которой закреплены крайние пластины 5 и 12 магнитного блока. В пластине 5 закреплена гайка 4 с внутренней трапецеидальной резьбой, а с гайкой связан винт 2, вращающийся в двух бронзовых втулках 3, установленных в корпусе патрона. Винт 2 имеет цилиндрический буртик, который не дает ему перемещаться в осевом направлении. При вращении торцовым ключом 1 гайка 4 с пластиной 5 и магнитным блоком перемещаются, а винт 2 не смещается в осевом направлении.
На рис. 16 показано включенное положение магнитного патрона; при этом пластины 7 магнитного блока совпадают со вставками 9 из железа Армко верхней плиты 11. В этом положении патрона магнитный поток должен пройти через обрабатываемую заготовку. Магнитный блок во включенном положении патрона фиксируется упором 17, в который после перемещения магнитного блока упирается пластина 5.
Для выключения патрона ключом 1 вращают гайку 4 и перемещают магнитный блок на 4,25 мм, при этом крайняя пластина 12 блока прижимается к упору.
Внутрь патрона через резьбовое отверстие с пробкой 13 заливают минеральное масло.
Фактическая сила притяжения патрона зависит от многих причин: размеров детали, ее материала, состояния базовой поверхности и т.д. Например, стальная заготовка, закрепленная на поверхности магнитного патрона, требует силу 400 кгс для отрыва ее в направлении оси патрона, а для сдвига этой заготовки по плоскости патрона в направлении, перпендикулярном оси патрона, требуется сила 80 кгс, т.е. в пять раз меньше. Поэтому для предупреждения сдвига заготовки в радиальном направлении следует применять упоры.
Круглые электромагнитные патроны применяют для установки и закрепления заготовок тонких плоских деталей и деталей другой формы, обрабатываемых на токарных и шлифовальных станках.
На рис. 17 показана конструкция круглого электромагнитного патрона к токарному станку для закрепления заготовок тонких плоских деталей. Электромагнитный патрон состоит из корпуса 4, в выточке которого установлен каркас с намотанной на него катушкой 6. Концы катушки выведены через отверстие в корпусе 4 и соединены с двумя контактными кольцами 8 с помощью двух шпилек 11. Контактные кольца 8 электрически изолированы между собой и корпусом 4.
Каркас с катушкой 6 неподвижно установлен в корпусе 4 и предохраняется от попадания пыли и грязи гайкой 5. Контактное устройство электромагнитного патрона состоит из хомута 9 с текстолитовым щитом 2, щеткодержателями и щетками 12, скользящими по цилиндрической поверхности контактных колец 8. Щеткодержатели со щетками 12 закрыты металлическим кожухом 1.
Контактное устройство крепят на неподвижной гайке 7 передней бабки станка. Для предохранения от абразивной пыли контактного устройства на корпус патрона установлено лабиринтное кольцо 3.
При включении катушки 7 в цепь постоянного тока создается магнитное поле, которое притягивает обрабатываемую заготовку к катушке и она закрепляется в патроне.
Магнитные силовые линии пройдут через стальной корпус 4 через заготовку, затем вернутся в корпус и в нем завернутся. Электромагнитный патрон резьбовым отверстием 10 устанавливается на шпиндель станка.
Необходимо отметить, что магнитные и электромагнитные зажимные приспособления имеют недостаток, заключающийся в намагничивании обрабатываемых заготовок вследствие чего, после обработки требуется демагнитизация деталей, которая производится в специальных устройствах — демагнитизаторах.
Люнеты
применяют как дополнительные опоры для уменьшения прогиба заготовок длинных деталей при ^ > 12d, обрабатываемых и шлифовальных станках (1 — длина детали; d — наибольший диаметр детали).
По конструкции люнеты разделяются на универсальные и специальные, по способу установки на станке — на неподвижные и подвижные.
Универсальные люнеты с раздвижными кулачками применяются при изготовлении деталей с разными диаметрами. Специальные люнеты применяются для обработки партии деталей одного размера или для поддержания приспособления, установленного на шпинделе станка с большим вылетом.
Универсальные люнеты устанавливают на станке (неподвижные), или на каретке станка, с которой они перемещаются (подвижные). На рис. 18 показан неподвижный универсальный люнет. В корпус 4 люнета вместо кулачков установлены два шарикоподшипника 5. В отверстие крышки 6 вставлен валик 9 с пружиной, на конце которого подвижно закреплена серьга 11 с двумя шарикоподшипниками 5. При закреплении обрабатываемого вала 7 опускают крышку 6 люнета и верхней гайкой 8 регулируют положение валика 9. Затем рукояткой 1 поворачивают эксцентрик 2, в спиральный паз которого входит штифт 3, установленный в крышке 6, и крышка перемещается к центру люнета. При этом пружина 10 прижмет серьгу 11 с верхними подшипниками 5 к валу 7, и он зажимается между верхними и нижними подшипниками люнета.
rushkolnik.ru
Устройство круглошлифовального центрового станка
Рекомендуем приобрести:
Установки для автоматической сварки продольных швов обечаек - в наличии на складе! Высокая производительность, удобство, простота в управлении и надежность в эксплуатации.
Сварочные экраны и защитные шторки - в наличии на складе! Защита от излучения при сварке и резке. Большой выбор. Доставка по всей России!
Эти станки предназначены для продольного и врезного шлифования наружных цилиндрических, пологих конических и торцовых поверхностей заготовок с установкой заготовок в центрах или патроне.
Станок состоит из станины 18 с направляющими (см. рис. 7.1, б), на которых смонтирован нижний стол 20, несущий на себе поворотный верхний стол 19 с установленными на нем передней 2 и задней 12 бабками. В задней бабке предусмотрены рукоятки 11 для ручного зажима пиноли бабки. Верхний стол 19 при шлифовании конусов может поворачиваться вокруг оси 16, закрепленной на нижнем столе 20. Ручное перемещение нижнего стола по направляющим станины осуществляется от маховика 17 через специальный механизм, а механическое — от гидравлического цилиндра, находящегося в станине.
На задней стороне станины на поперечных направляющих смонтирована шлифовальная бабка 7 с механизмом быстрого подвода шлифовального круга к заготовке. На корпусе шлифовальной бабки закреплен механизм 8 поперечных подач с маховиком 6 для ручного поперечного движения подачи, рукоятками включения автоматических подач и дросселями регулирования скорости черновой и чистовой подач. Здесь же установлен механизм 5 автоматической правки круга.
На лицевой стороне станины расположена панель гидроуправления 14 с рукояткой 13 быстрого подвода-отвода шлифовальной бабки и дросселями регулирования реверса и скорости стола. Педалью 15 производится гидравлический отвод пиноли задней бабки 12.
На стойке смонтирован пульт управления 9 с пусковыми кнопками и переключателями. С левой стороны станка расположен электрошкаф 1, а с правой — гидростанция 10. Подача СОЖ осуществляется рукояткой 3. При необходимости на станке может быть установлен люнет 4.
Главное движение резания — вращение шлифовального круга, установленного на шлифовальной бабке Д (рис. 7.3), производится от электродвигателя М2 через клиноременную передачу ф112/ ф147. Уравнение кинематической цепи главного движения имеет следующий вид:
где nш.к — частота вращения шлифовального круга, мин-1; 0,985 — коэффициент скольжения ремня.
Круговое движение подачи — вращение шлифуемой заготовки на передней бабке А — производится от электродвигателя M1 постоянного тока с бесступенчатым регулированием частоты вращения посредством двух клиноременных передач: ф63/ф130 и ф63/ф168, обеспечивающих частоту вращения шпинделя 40...400 мин-1. В передней бабке шпиндель Шп с центром неподвижен и вращение заготовки осуществляется от поводка планшайбы.
Ручное перемещение стола происходит от механизма Е при вращении маховика Мх2, от которого движение передается нижнему столу Ст через зубчатые колеса z= 17/51/51, червячную передачу i = 1/31, муфту Мф, реечное колесо z = 20 и рейку, закрепленную на нижнем столе.
Продольное гидравлическое перемещение стола осуществляется от гидравлического цилиндра Ц4, установленного неподвижно на станине. Концы штоков поршня цилиндра прикреплены к нижнему столу Ст станка. Скорость перемещения стола составляет 0,5...5 м/мин.
Ручное поперечное движение подачи шлифовальной бабки производится механизмом подачи В с помощью маховика Мх1 при включенной электромагнитной муфте Мэ1, вращение которого через коническую z = 39/39 и червячную i = 2/40 передачи передается на шариковую гайку винта 10 x1 поперечного движения подачи.
Быстрое установочное перемещение шлифовальной бабки к заготовке выполняется от гидродвигателя М3 при выключенной электромагнитной муфте Мэ1. В этом случае движение от гидродвигателя через зубчатые колеса z = 35/35 и указанную кинематическую цепь передается винту 10 х 1 поперечного движения подачи.
Непрерывные автоматические подачи шлифовальной бабки производятся от гидродвигателя М4 при включенной электромагнитной муфте Мэ2 через червячную передачу i = 1/50, муфту Мэ1 и далее через указанную кинематическую цепь на винт 10 х 1 поперечного движения подачи. При этом движении происходит вращение маховика Мх1 с лимбом Л.
Электромагнитная муфта Мэ2 включает периодическое автоматическое движение подачи шлифовальной бабки.
Движение при правке шлифовального круга обеспечивает одно- или двухпроходную правку по гладкому или ступенчатому копиру. Продольное перемещение устройства правки Б вдоль образующей круга осуществляется от гидроцилиндра Ц2. Поперечное движение подачи пиноли П с алмазом на глубину правки производится: вручную — от рукоятки Рк через конические колеса z = 22/22 и цилиндрические z = 27/27 и далее передается на винт 2 х 1 пиноли; автоматически — от гидравлического цилиндра Ц1 (см. сеч. А—А) через плунжер с собачкой, находящейся в зацеплении с храповым колесом z = 200, и далее на винт 2х 1 пиноли.
Перемещение пиноли с центром задней бабки Г осуществляется автоматически от поршня-рейки гидроцилиндра Ц3 через зубчатое колесо z = 23 или вручную при вращении винта 1,5 х 1.
Шлифовальная бабка (рис. 7.4). Вращение шпинделю 14 круга 13 сообщается от электродвигателя через клиноременную передачу 5 на шкив 4.
Шпиндель смонтирован в корпусе 1 на двух трехвкладышных гидродинамических подшипниках скольжения 2. В подшипники от насоса смазывания подается под давлением масло, образующее масляный клин между шейкой шпинделя 14 и вкладышами подшипника 2. В осевом направлении шпиндель устанавливается по бурту между сферическими кольцами 10 и 12, закрепленными в неподвижной обойме 11 с помощью гайки 9 и контргайки 8. Поперечное движение подачи шлифовальной бабки по направляющим качения 6 станины 7 осуществляется от механизма поперечных подач, установленного на станине.
Устройство автоматической правки круга устанавливается на шлифовальной бабке 1 (рис. 7.5). Копирная система обеспечивает правку наружной поверхности круга по заданному профилю. Включение устройства происходит или автоматически от срабатывания реле счета обработанных заготовок, или вручную — от кнопки. Устройство смонтировано на каретке 5, перемещаемой штоком 20 гидроцилиндра вдоль круга по роликовым направляющим 2 шлифовальной бабки 1. Скорость движения штока регулируется бесступенчато дросселем. К каретке 3 привинчены направляющие 8, несущие суппорт 13 с пинолью 18 и установленным на ней алмазодержателем 19 с алмазом. Каретка под действием пружин прижимается к копиру 15, неподвижно укрепленному на шлифовальной бабке 7. Копир может точно выставляться с помощью винтов 16 и 17. Перемещение пиноли 18 в суппорте 13 осуществляется от ходового винта 12, получающего вращение от маховика Мх через вал 14 и пару зубчатых колес 7 и 5 или от храпового колеса 6, периодически поворачиваемого собачкой гидравлического плунжера 4. Устранение зазора в резьбе между ходовым винтом 12 и полугайками 9 и 11 осуществляется пружиной 10.
www.autowelding.ru
Лекция №8 Приспособления для токарных и круглошлифовальных станков
ЛЕКЦИЯ № 8Приспособления для токарных и круглошлифовальных станков
На токарных и круглошлифовальных станках обрабатываемые детали в зависимости от формы и размеров, устанавливают в центрах или в патроне. Один центр расположен в шпинделе передней бабки, а второй в шпинделе задней бабки токарного или шлифовального станка. Патрон устанавливают и закрепляют на конце шпинделя передней бабки станка.
Центры подразделяют на следующие типы:
1. Неподвижные нормальные и специальные;
2. Вращающиеся нормальные и специальные;
3. Плавающие специальные;
4. Рифленые специальные;
5. Срезанные.
Конусная поверхность центра предназначена для установки детали и имеет угол при вершине 60°, 90°, 120°; хвостовик центра изготовляют с конусом Морзе определенного номера (№ 2, 3, 4, 5, 6).
Не вращающиеся центры станков от трения сильно нагреваются и изнашиваются. Для уменьшения износа и увеличения срока их службы применяют вращающиеся задние центры, менее точные, чем не вращающиеся. Задний центр (рис. 1) применяют для
установки заготовок с центровыми отверстиями, а задний центр, показанный на рис. 2 для обработки заготовок полых деталей.
Основные размеры вращающихся центров нормализованы.
При обработке ступенчатых валов на многорезцовых станках для получения заданных линейных размеров заготовку вала устанавливают на плавающий (подпружиненный) передний центр.
На рис.3 показана конструкция такого подпружиненного центра. Такие центры применяют также при обработке на станках с ЧПУ.
Обработка валика в центрах токарного станка с поводковым устройством для вращения заготовки представлена на рис. 4.
Сила для вдавливания поводков в торец обрабатываемой заготовки:
При обработке заготовки в центрах с рифленым центром (рис. 5), представляющим собой поводок, вращающий деталь при обработке, сила, требуемая для вдавливания рифленого поводкового центра в заготовку:
Срезанные центры (рис. 6) позволяют обрабатывать торец заготовки, закрепленной в центрах.
Поводковые приспособления применяют для передачи вращательного движения (крутящего момента) от шпинделя станка к обрабатываемой заготовке 2, установленной в центрах, на оправке или в патроне. К поводковым приспособлениям относятся хомутики 1, поводковые планшайбы 3. Схема поводкового патрона представлена на рис. 7.
Хомутик 1 с ручным зажимом надевают на заготовку 2, крепят винтом и затем заготовку с хомутиком устанавливают в центрах станка. При включении станка обрабатываемая заготовка через поводковую планшайбу и хомутик вращается от шпинделя станка.
Самозажимные поводковые патроны изготовляют с двумя или тремя эксцентриковыми кулачками с насечкой, которые в начале обработки под действием сил резания зажимают заготовку, установленную в центрах станка и передают ей крутящий момент от шпинделя станка.
При увеличении крутящего момента резания автоматически увеличивается и крутящий момент от шпинделя, передаваемый кулачками патрона на заготовку.
Для удобной установки заготовки в центры применяют поводковые патроны с автоматическими раскрывающимися кулачками. Равномерный зажим заготовки всеми кулачками обеспечивается тем, что применяют плавающие кулачки или кулачки с независимым перемещением. Самозажимные поводковые патроны позволяют устанавливать кулачки на различный диаметр обрабатываемых заготовок в определенном диапазоне. Эти патроны применяют при центровой обработке на многорезцовых станках или станках с ЧПУ для передачи заготовке от шпинделя станка больших крутящих моментов.
На рис. 11 показан поводковый патрон с двумя эксцентриковыми сменными кулачками. Фланец 8 патрона устанавливают коническим отверстием на шпиндель и крепят винтами к его фланцу. Корпус 10 патрона соединяется с фланцем 8 винтами 7, проходящими через распорные втулки 6, он имеет ведущие пальцы 9, на которых установлены кулачки 2. Для одновременного зажима заготовки двумя кулачками корпус 10 может перемещаться относительно фланца в направлении его пазов и пружиной 3 поворачиваться в начальное положение.
В момент включения станка шпиндель с патроном начинает вращаться и кулачки 2 под действием центробежных сил от грузов 1, мгновенно поворачиваясь на пальцах, предварительно зажимают заготовку, предупреждая ее провертывание в начале резания, окончательный зажим заготовки производится в начальный момент резания от составляющей силы резания Р. После обработки станок выключается, шпиндель не вращается, кулачки 2 толкателями 5 под действием пружин 4 поворачиваются на пальцах 9 в исходное положение и деталь разжимается.
Меняя кулачки патрона, обеспечивают изготовление деталей диаметром 30-150 мм.
Центробежную силу определяют через массу груза и угловую скорость вращения его центра тяжести:
Рц = mω2R,
Суммарная сила зажима кулачками патрона:
^
где Z — число кулачков патрона.
Двухкулачковые поводковые патроны нормализованы, они могут иметь плавающий (подпружиненный) центр.
^
применяют для установки и зажима заготовок различных деталей, обрабатываемых на токарных и шлифовальных станках. В зависимости от количества кулачков патроны разделяются на двух-, трех- и четырехкулачковые. Патроны двух- и трех- кулачковые являются самоцентрирующими; четырехкулачковые патроны изготовляют в основном с независимым перемещением кулачков, но бывают и самоцентрирующие.
Наибольшее применение имеют универсальные трехкулачковые спирально-реечные патроны. На рис. 12 показан трехкулачковый спирально-реечный самоцентрирующий патрон, устанавливаемый на резьбовом конце шпинделя токарного станка. В корпусе 1 патрона расположен диск 2, имеющий на одном торце коническое зубчатое колесо, а на другом — спиральные реечные пазы, находящиеся в зацеплении с рейками 3. В крестообразном пазу реек 3 устанавливают и закрепляют винтами 4 прямые или обратные накладные кулачки 5. При вращении торцовым ключом одного из трех конических колес 6, находящихся в зацеплении с коническим колесом диска 2, последний поворачивается и перемещает рейки 3 с кулачками 5 к оси патрона при зажиме заготовки и от оси — при разжиме.
Крышка 7 удерживает диск 2 в корпусе патрона от продольного смещения и препятствует попаданию в патрон стружки и грязи.
Некоторые патроны изготавливаются с цельными прямыми или обратными кулачками с нарезанными на их торцах рейками для непосредственного сопряжения со спиральными пазами диска 2. Недостаток этих патронов состоит в том, что радиусы кривизны на различных участках спирали диска 2 различны, а радиус реек 3 кулачков одинаков, поэтому соприкосновение реек 3 с витками спирали диска 2 происходит не по всей поверхности, а по небольшим узким участкам.
При неполном зацеплении витков спирали диска с рейками кулачков возникают высокие удельные давления в сопряжении и происходит значительный износ центрирующего механизма и потеря точности патрона. Для повышения износоустойчивости применяют закалку, и шлифование витков спирали диска и реек кулачков патрона.
Универсальные четырехкулачковые патроны применяют для установки и зажима заготовок некруглой формы, обрабатываемых на токарных, револьверных, сверлильных станках в единичном и серийном производствах. На рис. 13 показан универсальный четырехкулачковый патрон с механизированным приводом для перемещения кулачков к оси и от оси патрона.
Каждый кулачок независимо от других можно устанавливать на требуемое расстояние от оси патрона в соответствии с формой и размерами обрабатываемых заготовок. Предварительный зажим заготовки производится одной парой кулачков и затем - второй, окончательный, всеми четырьмя кулачками одновременно. При перемещении поршня со штоком в пневмоцилиндре влево шток через тягу и винт 1 передвигает втулки 2 и 7, последняя установлена на резьбе втулки 2. При перемещении влево втулка 7 через плавающие шарики 8 передвигает втулки 3 и 4. Эти втулки имеют по два диаметрально расположенных паза, в которых установлены попарно длинными плечами рычаги 6 и 10. Каждая втулка 3 и 4 поворачивает только одну пару рычагов 10 и 6. Втулки 3 и 4 под действием плавающих шариков 8, перемещаясь влево, поворачивают рычаги 10 на осях 11 и рычаги 6 на осях 5, а короткими плечами каждая пара рычагов 10 и 6 сдвигает кулачки 9 к центру патрона, и деталь зажимается.
При перемещении поршня со штоком в пневмоцилиндре вправо шток через тягу и винт 1 передвигает втулки 2 и 7 и втулка 2 через плавающие шарики 8 смещает втулки 3 и 4 вправо. Тогда и втулки поворачивают длинные плечи каждой пары рычагов 10 и 6 вправо, а короткие плечи рычагов разводят кулачки 9, деталь разжимается.
Зажим и разжим каждой парой кулачков производится последовательно с помощью плавающих секторов 8 и 12, перемещающихся перпендикулярно относительно оси патрона.
Сила зажима заготовки одним кулачком патрона:
К=1,3…1,6 – коэффициент
запаса;
R – радиус зажатой кулачками части заготовки;
Rо – радиус обрабатываемой части детали;
f – коэффициент трения между заготовкой и кулачками.
^
Патроны для закрепления цилиндрических и конических зубчатых колес при шлифовании отверстий используются после закалки профиля зубьев. Эта операция обычно является последней и обеспечивает концентричность оси начальной окружности колеса с осью центрального отверстия. Центрирование и закрепление зубчатого колеса в патронах при шлифовании центрального отверстия производится по боковым профилям зубьев. Для этого во впадины прямозубого цилиндрического колеса устанавливают ролики, во впадины косозубого цилиндрического колеса - шарики или витые упругие ролики, во впадины конического колеса — шарики.
Патроны для центрирования и закрепления зубчатых колес при шлифовании отверстия подразделяют на четыре группы:
1. Для одновенцовых цилиндрических колес;
2. Для двух- и многовенцовых цилиндрических колес;
3. Для цилиндрических колес с внутренним зацеплением;
4. Для конических зубчатых колес.
Патроны подразделяют на специальные и универсальные. Специальные патроны применяют для шлифования отверстия зубчатых колес одного типоразмера, универсальные - для нескольких типоразмеров. При проектировании таких патронов необходимо рассчитывать диаметр роликов (шариков), устанавливаемых во впадинах зубчатого колеса, и расстояние между осью роликов и осью патрона.
На рис. 15 показан мембранный патрон с пятью кулачками для шлифования отверстия в цилиндрических зубчатых колесах. Эти патроны обеспечивают высокую точность центрирования колес, надежны в эксплуатации и просты в изготовлении. В патроне можно закреплять цилиндрические колеса с прямыми зубьями с наибольшим наружным диаметром 175 мм и числом зубьев, кратным пяти.
Корпус патрона 1 крепится к планшайбе 9 винтами 8. Патрон с планшайбой устанавливают внутри шлифовального станка.
В патроне имеется мембрана (диск) 10, изготовленная заодно с пятью рожками (кулачками), равномерно расположенными по окружности мембраны. В отверстиях рожков мембраны закреплены сферические опоры 11. Мембрана 10 крепится к корпусу 1 десятью винтами. На передней части корпуса имеются пять радиальных прямоугольных пазов, в которых установлены направляющие колодки 18, закрываемые секторами 17, закрепленными на корпусе. Колодки 18 имеют на торце крестообразные пазы для установки сменных кулачков 13, закрепляемых на колодках винтами. В отверстие вставлены резиновые стержни 14, в которые ввинчены ролики 15.
Центрирование обрабатываемого зубчатого колеса производится роликами 15, которые свободно расположены во впадине между зубьями колеса. Торцом зубчатое колесо упирается в торцы сменных кулачков 13. При подаче сжатого воздуха в левую полость пневмоцилиндра поршень со штоком и тягой двигается вправо и шток через тягу и втулку 4 перемещает втулку 3, которая головкой нажимает на мембрану 10 и выгибает ее, а рожки с кулачками 13 разводятся и зубчатое колесо устанавливается в патрон.
Во время подачи сжатого воздуха в правую полость пневмоцилиндра поршень со штоком и тягой перемещается влево и шток через тягу и втулку 4 отводит втулку 3 от мембраны 10. Мембрана 10 за счет упругих сил выпрямляется, и рожки и опоры 11 через сферические шайбы 12 перемещают колодки 18 с кулачками 13 к центру. Кулачки 13, нажимая на ролики 15, центрируют и зажимают зубчатое колесо.
При смене кулачков 13 рабочая поверхность установочных кулачков и их опорные торцы шлифуются на станке. При шлифовании кулачки находятся в сведенном положении и между ними по поверхностям "А" закрепляется кольцо 16.
Втулка 7 предохраняет мембрану 10 от излишнего прогиба. Перемещение кулачков 13 регулируется продольным перемещением втулки 3, которая крепится шариком 6 и винтом 5.
^
различают двух видов: круглые патроны с постоянными магнитами и круглые электромагнитные патроны.
Круглые патроны с постоянными магнитами применяют для установки и закрепления заготовок на токарных и шлифовальных станках. Закрепление заготовок на таких патронах происходит быстро. Базовые поверхности заготовок — колец, дисков — должны представлять собой плоскость с шероховатостью Ra=2,5…l,25 мкм. С увеличением шероховатости на базовой поверхности заготовок сила ее крепления на патроне значительно снижается, так как увеличивается воздушный зазор, который создает большое сопротивление прохождению магнитного потока.
Сила закрепления при установке на патрон закаленных заготовок больше, чем при установке незакаленных деталей.
Магнитные патроны применяют при чистовом протачивании поверхностей небольших деталей на токарных станках и при шлифовании наружных и внутренних поверхностей на шлифовальных станках.
На рис.16 показан патрон с постоянным магнитом с наружным диаметром 265 мм. Патрон имеет корпус 8 из силумина, верхнюю 11 и нижнюю 14 плиты. В корпусе размещается магнитный блок, состоящий из цилиндрических постоянных магнитов 6 и пластин 7 из железа Армко, залитых эпоксидным клеем. Магнитный блок смонтирован на промежуточной плите 16, на которой закреплены крайние пластины 5 и 12 магнитного блока. В пластине 5 закреплена гайка 4 с внутренней трапецеидальной резьбой, а с гайкой связан винт 2, вращающийся в двух бронзовых втулках 3, установленных в корпусе патрона. Винт 2 имеет цилиндрический буртик, который не дает ему перемещаться в осевом направлении. При вращении торцовым ключом 1 гайка 4 с пластиной 5 и магнитным блоком перемещаются, а винт 2 не смещается в осевом направлении.
На рис. 16 показано включенное положение магнитного патрона; при этом пластины 7 магнитного блока совпадают со вставками 9 из железа Армко верхней плиты 11. В этом положении патрона магнитный поток должен пройти через обрабатываемую заготовку. Магнитный блок во включенном положении патрона фиксируется упором 17, в который после перемещения магнитного блока упирается пластина 5.
Для выключения патрона ключом 1 вращают гайку 4 и перемещают магнитный блок на 4,25 мм, при этом крайняя пластина 12 блока прижимается к упору.
Внутрь патрона через резьбовое отверстие с пробкой 13 заливают минеральное масло.
Фактическая сила притяжения патрона зависит от многих причин: размеров детали, ее материала, состояния базовой поверхности и т.д. Например, стальная заготовка, закрепленная на поверхности магнитного патрона, требует силу 400 кгс для отрыва ее в направлении оси патрона, а для сдвига этой заготовки по плоскости патрона в направлении, перпендикулярном оси патрона, требуется сила 80 кгс, т.е. в пять раз меньше. Поэтому для предупреждения сдвига заготовки в радиальном направлении следует применять упоры.
Круглые электромагнитные патроны применяют для установки и закрепления заготовок тонких плоских деталей и деталей другой формы, обрабатываемых на токарных и шлифовальных станках.
На рис. 17 показана конструкция круглого электромагнитного патрона к токарному станку для закрепления заготовок тонких плоских деталей. Электромагнитный патрон состоит из корпуса 4, в выточке которого установлен каркас с намотанной на него катушкой 6. Концы катушки выведены через отверстие в корпусе 4 и соединены с двумя контактными кольцами 8 с помощью двух шпилек 11. Контактные кольца 8 электрически изолированы между собой и корпусом 4.
Каркас с катушкой 6 неподвижно установлен в корпусе 4 и предохраняется от попадания пыли и грязи гайкой 5. Контактное устройство электромагнитного патрона состоит из хомута 9 с текстолитовым щитом 2, щеткодержателями и щетками 12, скользящими по цилиндрической поверхности контактных колец 8. Щеткодержатели со щетками 12 закрыты металлическим кожухом 1.
Контактное устройство крепят на неподвижной гайке 7 передней бабки станка. Для предохранения от абразивной пыли контактного устройства на корпус патрона установлено лабиринтное кольцо 3.
При включении катушки 7 в цепь постоянного тока создается магнитное поле, которое притягивает обрабатываемую заготовку к катушке и она закрепляется в патроне.
Магнитные силовые линии пройдут через стальной корпус 4 через заготовку, затем вернутся в корпус и в нем завернутся. Электромагнитный патрон резьбовым отверстием 10 устанавливается на шпиндель станка.
Необходимо отметить, что магнитные и электромагнитные зажимные приспособления имеют недостаток, заключающийся в намагничивании обрабатываемых заготовок вследствие чего, после обработки требуется демагнитизация деталей, которая производится в специальных устройствах — демагнитизаторах.
Люнеты
применяют как дополнительные опоры для уменьшения прогиба заготовок длинных деталей при ^ > 12d, обрабатываемых и шлифовальных станках (1 — длина детали; d — наибольший диаметр детали).
По конструкции люнеты разделяются на универсальные и специальные, по способу установки на станке — на неподвижные и подвижные.
Универсальные люнеты с раздвижными кулачками применяются при изготовлении деталей с разными диаметрами. Специальные люнеты применяются для обработки партии деталей одного размера или для поддержания приспособления, установленного на шпинделе станка с большим вылетом.
Универсальные люнеты устанавливают на станке (неподвижные), или на каретке станка, с которой они перемещаются (подвижные). На рис. 18 показан неподвижный универсальный люнет. В корпус 4 люнета вместо кулачков установлены два шарикоподшипника 5. В отверстие крышки 6 вставлен валик 9 с пружиной, на конце которого подвижно закреплена серьга 11 с двумя шарикоподшипниками 5. При закреплении обрабатываемого вала 7 опускают крышку 6 люнета и верхней гайкой 8 регулируют положение валика 9. Затем рукояткой 1 поворачивают эксцентрик 2, в спиральный паз которого входит штифт 3, установленный в крышке 6, и крышка перемещается к центру люнета. При этом пружина 10 прижмет серьгу 11 с верхними подшипниками 5 к валу 7, и он зажимается между верхними и нижними подшипниками люнета.
fs.nashaucheba.ru
Круглошлифовальный станок: технические характеристики и схемы
Содержание статьи:
Круглошлифовальные станки относятся к классу металлообрабатывающего оборудования. С их помощью выполняют точное шлифование металлических заготовок по внешней поверхности. Конструктивно станки этого типа существенно отличаются от аналогичного оборудования.
Конструктивные особенности оборудования
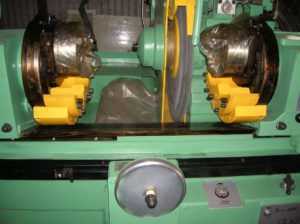
Рабочий блок станка
Принцип работы круглошлифовальных станков основан на прижиме заготовки с помощью направляющего круга либо монтажа в центах. Обработка при этом выполняется путем касания рабочего вращающего абразива с поверхностью детали. Таким образом выполняется равномерное удаление материала с формированием оптимального показателя шероховатости.
Классическая компоновка станка представляет собой сочетание токарного и шлифовального. Для фиксации заготовки в конструкции предусмотрен специальный блок. Это может быть система патронов, удерживающих деталь в горизонтальном положении. Альтернативным вариантом является применение дополнительного круга, который придавливает заготовку к абразиву.
Круглошлифовальный станок имеет следующие преимущества использования:
- возможность обрабатывать детали с различными габаритами. При этом важно учитывать их массу;
- точная настройка параметров. Для обеспечения высокого качества шлифовки рекомендуется приобретать модели с автоматической подачей;
- выбор модели станка под конкретные производственные задачи. Это обеспечит максимальную производительность и снизит себестоимость продукта.
Однако для выбора оптимальной модели станка необходимо детально ознакомиться с их разновидностями и эксплуатационными качествами. Все зависит от конфигурации обрабатываемых деталей, а также требований к качеству шлифования.
Немаловажным моментом является конфигурация абразивного диска – его зернистость, площадь рабочей поверхности. Эти характеристики напрямую влияют на качество шлифовки стальной заготовки.
Виды круглошлифовальных станков
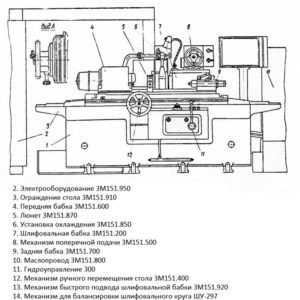
Пример компоновки станка ЗМ151
На практике на круглошлифовальных станках подвергаются обработке заготовки круглого или овального сечения. Шлифовка сложных деталей на этом оборудовании невозможна из-за специфики его конструкции. Это нужно учитывать при выборе модели станка.
Наиболее распространенными моделями круглошлифовальных станков является оборудование, в котором детали устанавливаются в центрах. Фиксация заготовки выполняется между передней и задней бабкой. Для повышения качества шлифования происходит вращение тела. При контакте его с абразивным диском происходит снятие излишка материала в виде металлической пыли стружки.
Кроме этой методики в последнее время набирают популярность так называемые бесцентровые круглошлифовальные станки. В них заготовка помещается на рабочий лафет и с одной стороны удерживается вспомогательным кругом, а другой подвергается шлифованию основным абразивом. Таким образом можно выполнить качественную тонкую обработку тонкостенных цилиндров или конусов. Степень прижатия регулируется с помощью системы автоматики.
Дополнительно необходимо учитывать такие особенности, которыми обладает круглошлифовальный станок:
- наличие поворотного стола. С его помощью можно осуществлять смещение заготовки относительно абразивного диска в горизонтальной и вертикальной плоскости;
- устройство механизма подач. Это может быть автоматизированный комплекс или его механический аналог. В последнем случае станки подобного типа применяют для чернового шлифования;
- возможность фиксации заготовки в центрах, патроне. Этот параметр относится только к оборудованию центрового типа.
В настоящее время выпускается большое количество моделей круглошлифовальных станков. Поэтому помимо выбора по конструктивным параметрам необходимо учитывать технические и эксплуатационные качества оборудования.
Для шлифовки по всей поверхности заготовки круглошлифовальный станок должен иметь механизм смещения абразивного круга. В таком случае учитываются продольные подачи абразива и поперечные детали.
Перечень основных технических характеристик
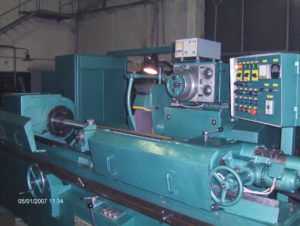
Круглошлифовальный станок 3М152
В качестве примера можно рассмотреть работу стандартной модели круглошлифовального станка 3М152. В нем обрабатываемая деталь устанавливается в центрах. Аналогичной конструкцией обладает большая часть такого оборудования.
Лучше всего технические характеристики станка условно разделить по его узлам. Конструктивно он состоит из блока фиксации заготовки, обрабатывающего центра (шлифовальная бабка) и системы управления. Средняя масса подобного станка составляет около 8 тонн. При этом он имеет большие габариты, что предъявляет особые условия к монтажу и эксплуатации.
Основные технические параметры:
- максимально допустимые габариты и масса обрабатываемой заготовки;
- диаметры шлифования – минимальный и максимальный;
- расстояние от оси шпинделя передней бабки до поверхности рабочего стола.
Характеристики рабочего стола:
- смещение рабочего стола – максимальная длина;
- параметры ручного ускорения и замедления движения;
- углы поворота по часовой и против часовой стрелки;
- характеристики смещения с помощью гидравлической системы. Это необходимо для обработки массивных деталей.
Фиксация детали происходит между передней и задней бабками. Они должны анализироваться по следующим параметрам:
- частота вращения;
- для задней бабки — величина смещения пиноли.
Кроме этого учитывается суммарная потребляемая мощность оборудования, возможность установки вспомогательных конструкций и параметры системы охлаждения. Наличие последней является обязательным требованием для промышленных моделей круглошлифовальных станков.
Для поддержания станка в рабочем состоянии необходимо периодически проводить профилактические и ремонтные работы. Особенно важно своевременно наносить смазку на движущиеся части оборудования.
Методы круглого шлифования
Способы наружного шлифования
Для выполнения наружного шлифования можно воспользоваться несколькими методиками. Выбор зависит от желаемого результата, а также фактических характеристик оборудования.
Наиболее распространенным является способ продольной обработки. Заготовка крепится в центрах. С помощью привода передней бабки ей придается вращение. Одновременно с этим механизм подачи обеспечивает продольное смещение детали относительно абразивного круга.
Кроме этого способа современные круглошлифовальные станки могут выполнять следующие типы обработки:
- глубинная. Применяется для шлифовки коротких деталей. За один проход может удаляться до 0,4 мм материала. Основной процесс обработки выполняется конической частью круга;
- врезная. С ее помощью можно эффективно делать обдирочное или чистовое шлифование. Для этого устанавливают широкие абразивные круги. В процессе обработки деталь не смещается относительно инструмента;
- уступами. Это комбинированный вид, сочетающий глубинное и врезное шлифование. Оптимальный вариант для снятия излишка материала с заготовок сложной формы.
Большинство моделей круглошлифовальных станков могут выполнять все вышеперечисленные типы обработки. Важно лишь правильно подобрать характеристики оборудования, чтобы добиться желаемой точности.
В качестве примера можно посмотреть видеоматериал, в котором показана работа круглошлифовального станка с ЧПУ:
stanokgid.ru