Конструкция станов горячей прокатки. Проектирование прокатных станов
Конструкция станов горячей прокатки
Агрегаты обжимных станов
В обжимных станах слитки нагревают в специальных колодцевых печах и затем клещевыми кранами подают на кольцевую слиткоподачу. Далее слитки попадают на приемный рольганг, оборудованный весовым устройством, и задаются в универсальную рабочую клеть слябинга 1250.
При необходимости получения слябов правильной прямоугольной формы в универсальной клети слябинга установлены вертикальные валки. У блюмингов, как правило, вертикальные валки отсутствуют. Для управления положением слитка при прокатке используют манипулятор и кантователь. После прокатки поверхность сляба зачищают машиной огневой зачистки и режут его на мерные длины на ножницах горячей резки с усилием 28 МН. Для уборки отходов имеется конвейер обрези. Там же установлены контрольные весы, клеймитель и устройство для транспортировки слябов на склад или для передачи их к непрерывному широкополосному стану 2000 горячей прокатки.
Агрегаты заготовочных станов
Заготовочные станы поставляют заготовки на сортовые, проволочные и трубопрокатные станы.
Непрерывные заготовочные станы с одной группой клетей (например, стан 700) катают блюмы сечением от 140 х 140 до 200 х 200 мм или крупные заготовки размером от 125 х 125 до 140 х 140 мм. Непрерывные заготовочные станы с двумя группами клетей (например, стан 700/500) выдают из первой группы блюмы сечением от 140 х 140 до 200 х 200 мм и заготовки размером от 120 х 120 до 140 х 140 мм. Из второй группы клетей получают готовую заготовку размером от 60 х 60 до 100 х 100 мм. На трубозаготовочных последовательных станах получают круглую заготовку диаметром 75-300 мм для прошивных станов.
Рассмотрим компановку агрегатов непрерывного заготовочного стана 900/700/500, состоящего из 14 двухвалковых клетей, установленных в трех группах. Первая группа состоит из двух клетей с диаметром валков 900 мм, вторая черновая группа включает шесть клетей — 900/1300 в первой и второй клетях и 730/1300 в остальных. Чистовая третья непрерывная группа состоит из шести клетей с диаметром валков 530/900 мм. Предусмотрено чередование горизонтальных и вертикальных валков, начиная с 5-ой клети.
После резки на мерные длины горячие блюмы по рольгангу поступают в первую группу, установленную отдельно от второй группы. Расстояние между первой и второй группами позволяет установить кантователь на рольганге для свободной кантовки блюмов.
Вторая группа позволяет получать из 4-ой, 6-ой и 8-ой клетей заготовки с соответствующими размерами 200 х 200, 170 х 170 и 150 х 150 мм.
Готовые заготовки отводятся поперечными транспортерами на боковой рольганг, где они ножницами с усилием 10 МН режутся на мерные длины и отправляются на холодильник. Заготовки 150 х 150 мм по рольгангу перемещаются к чистовой группе.
Здесь также можно на выходе из 10-ой, 12-ой и 14-ой клетей получать заготовки сечением соответственно 120 х 120, 100 х 100 и 80 х 80 мм. Для установления постоянной температуры у раската перед девятой клетью заготовки с помощью упоров некоторое время выдерживаются. В системе подачи установлены кантователи. Для обрезки неровных концов используют ножницы, после чего заготовки направляют на холодильник.
Агрегаты листовых станов
Основным параметром листового или полосового стана является длина бочки валков последней клети.
Находят применение станы:
- Широкополосные с длиной бочки валков от 1400 до 2500мм с двумя группами клетей — с последовательной черновой и непрерывной чистовой.
- Одно-двухклетевые реверсивные толстолистовые станы с длиной бочки от 2000 до 5000 мм и более, иногда с установкой вертикальных валков перед горизонтальными. Кроме листов на этих станах можно выкатывать слябы.
- Полунепрерывные широкополосные станы с длиной бочки в чистовой группе от 1200 до 3000 мм. Для горячей прокатки электротехнической стали применяют реверсивные четырехвалковые станы.
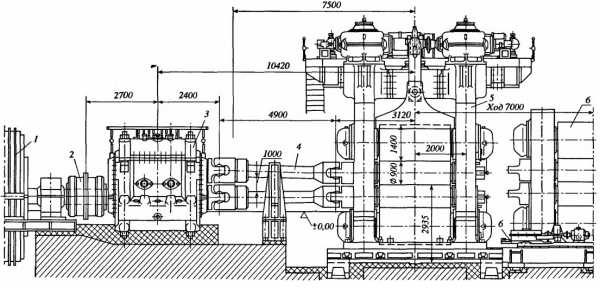
Оборудование непрерывного четырехвалкового стана 2800 включают нагрев литых слябов в нагревательных печах с предварительной зачисткой поверхности на фрезерных станках и последующей мойкой. Поступающая по рольгангу заготовка задается в стан 2800, состоящий из двух черновых клетей — первая четырехвалковая клеть 900/1400 х 2800 (рисунок 1), вторая — 750/1400 х 2800 и пяти чистовых клетей 650/1500 х 2800мм (рисунок 2).
Черновая клеть (рисунок 1) состоит из главного двигателя 1, зубчатой муфты 2, шестеренной клети 3, универсального шпинделя 4 и клети 5 с рабочими валками диаметром 900 мм, опорными 1400 мм и длиной бочки 2800 мм. Кроме того, клеть снабжена механизмом смены валков 6.
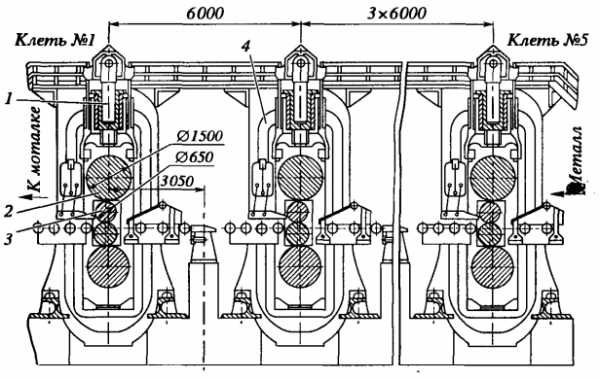
На рисунке 2 показана чистовая группа клетей 4 с рабочими 3 валками 650 мм, опорными 2 — 1500 мм и длиной бочки 2800 мм; расстояния между осями клетей 6000 мм. Для уменьшения разнотолщинности все чистовые клети снабжены гидромеханическими устройствами протовоизгиба. Рабочие валки установлены на подшипниках качения, опорные — в подшипниках жидкостного трения. Применяется гидравлическое уравновешивание валков и шпинделей 1.
За последней чистовой клетью расположены дисковые ножницы с кромкокрушителем для обрезки боковых кромок и две барабанные моталки с натяжением до 6 кН для смотки ленты в рулоны. Далее рулоны специальной тележкой кантуются, взвешиваются и после обвязки передаются на конвейер к термическим печам.
Агрегаты широкополосных станов
Широкополосный стан 2000 предназначен для прокатки полос толщиной до 16 мм и шириной що 1850 мм в рулонах с массой 36 т из слябов толщиной от 150 мм.
В состав стана входят нагревательные печи, черновая группа клетей, промежуточный рольганг, чистовая группа клетей, отводящий рольганг, моталки и вспомогательное оборудование. Нагретые слябы после осмотра и зачистки поступают на приемный рольганг черновой группы стана. Черновая группа представляет двухвалковые вертикальные клети с диаметром валков 1200 мм и длиной бочки 650 мм и предназначена для обжатия боковых граней слябов с разрушением окалины. За ней следует двухвалковая горизонтальная клеть с валками 1400 х 2000 мм и затем четыре универсальные четырехвалковые клети с горизонтальными валками 1180/1600 х 2000 мм. За каждый проход обжатие составляет до 60 мм. В черновую группу входят также агрегаты для гидравлического сбива окалины, рольганги, линейки, сбрасыватели раскатов в случае понижения их температуры.
Перед чистовой группой клетей расположены летучие ножницы для обрезки концов подката и двухвалковый окалиноломатель. Между чистовыми клетьми располагаются петледержатели, гидросбивы окалины, линейки, проводки, моталки. После прокатки полоса поступает на рольганг, где ее снизу и сверху специальными душирующими установками охлаждают, после чего сматывают в рулоны для передачи в цех холодной прокатки или в отделение горячекатаных рулонов.
Агрегаты толстолистовых станов
Стан 3600 предназначен для горячей прокатки листов толщиной до 50 мм, шириной до 3200 мм и длиной от 6 до 28 м из слябов и плит толщиной до 200 мм, шириной до 3200 мм и длиной до 12 м.
После нагрева слябов в методических печах или слитков в колодцах заготовки по рольгангу подаются к стану.
Стан состоит из вертикальной двухвалковой клети 900 х 1400 и двух реверсивных четырехвалковых клетей: черновой 1130/1800 х 3600-3400 и чистовой 1030/1800 х 3600-3400.
В вертикальной клети сляб калибруют по ширине и сбивают окалину. После чего подкат кантуют на 90° и направляют в черновую клеть. При реверсивной прокатке в черновой четырехвалковой клети получают раскат ( при этом используют вертикальные клети) толщиной от 20 до 75 мм, который по рольгангам подается к чистовой четырехвалковой клети. Здесь полоса раскатывается до толщины 5-50 мм за несколько реверсивных проходов. Особенностью клетей является индивидуальный электродвигатель для каждого валка.
В черновой и чистовой группах стана усилие прокатки составляет 46 МН. Для обрезки переднего и заднего концов готового проката на отходящем рольганге установлены ножницы усилием 19 МН. Эти же ножницы используют для порезки проката на мерные длины. После ножниц прокат направляют по одному из следующих маршрутов:
- листы с большой коробоватостью подвергают горячей правке на роликовой машине и затем направляют на отделку;
- листы толщиной до 50 мм охлаждают и правят в полугорячем режиме на правильной машине и затем окончательно охлаждают;
- листы толщиной до 20 мм по шлепперу подают в печи для нормализации, затем их правят, охлаждают и передают на окончательную отделку;
- листы поступают на роликовую закалочную машину и далее идут на отделку.
После обработки листы подлежат дефектоскопии, зачистке и термообработке. Затем идет тщательный контроль и клеймение, укладка листов в пакеты на столе штабелирующего устройства и передача пакетов на участок резки и охлаждения.
Агрегаты сортовых станов горячей прокатки
Сортамент сортовых станов горячей прокатки включает профили:
- круг до 350 мм, угловую сталь с шириной полки до 250 мм, швеллеры высотой до 450 мм, широкополосные балки высотой до 1100 мм, рельсы;
- проволока;
- лист, полоса.
Основным параметром сортового стана является диаметр бочки валков рабочей клети (для многоклетевых станов у последней клети)
Агрегаты рельсобалочных станов
На рельсобалочном стане 950/800 линейного типа производят железнодорожные рельсы массой до 75 кг/м, двутавровые балки крупного сечения высотой до 600 мм, швеллеры высотой до 400мм, уголковую сталь с шириной полки до 250 мм и круглую заготовку диаметром до 350 мм и длиной до 8м. В качестве исходной заготовки применяют блюмы сечением до 350 х 350мм и длиной до 6 м.
От блюминга 1150 блюмы шлеппером подаются к нагревательным печам и после контроля и зачистки поступают на первую линию стана, которая состоит из реверсивной двухвалковой клети 950 х 2350. Здесь, как правило, за пять пропусков получают грубо профилированную полосу длиной до 12м. Затем рольгангами полосу передают к первой рабочей трехвалковой клети 800 х 1900 черновой линии. На этой линии полосе придается более точный профиль и она за четыре пропуска раскатывается на длину до 30 м. Во вторую трехвалковую клеть этой же линии полосу задают с помощью рольгангов и цепного шлеппера. Здесь полосе с помощью калибровок придается за 3-4 пропуска надлежащий профиль и она раскатывается до 100м.
Полуфабрикат передается в чистовую двухвалковую клеть 850 х 1200 рольгангами и цепными шлепперами, где за один пропуск полуфабрикату придается окончательный профиль.
Далее в зависимости от назначения проводится доработка полосы на следующих агрегатах.
При прокатке рельсов полосу из чистовой клети 850 х 1200 рольгангами передают к пилам горячей резки для разрезки на мерные заготовки длиной 25 м. Затем полуфабрикат проходит контроль, маркируется и направляется для правки в правильную машину. После правки рельсы рольгангами и шлепперами перемещают на холодильник для охлаждения.
Охлажденные рельсы направляют в печи изотермической выдержки и нормализации.
Затем их правят в роликоправильных машинах по нижнему основанию; окончательная правка в другой плоскости осуществляется на вертикальных правильных прессах. После этого рельсы попадают на автоматические линии, где фрезеруют их торцы, сверлят монтажные отверстия и проводят закалку поверхности головок. После автоматических линий рельсы поступают на контрольный стол, где проводится всесторонняя проверка их качества и исправление дефектов. Готовая продукция поступает на склад.
При прокатке двухтавровых и тавровых балок, швеллеров и угловой стали прокатанный полуфабрикат из чистовой клети 850 х 1300 рольгангом задают на участок резки, где его режут на мерные длины по 25 м. Затем полуфабрикат маркируют и направляют на холодильник, который имеет кантователь для поворота полуфабриката с тем, чтобы охлаждение проводилось более равномерно. Охлажденный полуфабрикат рольгангами передается на правильный участок, где его правят в однойплоскости роликоправильными машинами и после кантования в другой плоскости — правильным прессом. Выправленный прокат направляется на участок разбраковки с последующей передачей на склад готовой продукции.
Бракованные участки подлежат обрезке с помощью пилы холодной резки. Для повышения точности проката вместо чистовой клети используют универсальную клеть с вертикальными и горизонтальными валками.
Агрегаты для прокатки круглых профилей включают нагревательное оборудование, рольганги, шлеппера и две группы клетей: черновую, состоящую из одной двухвалковой клети 950 х 2350 и двух трехвалковых клетей 800 х 1900, и чистовую — двухвалковая клеть 850 х 1200. После маркирования и контроля круглый прокат рольгангами подают к пилам для резки на мерные длины, затем на холодильник и на склад готовой продукции.
Агрегаты крупно-, средне- и мелкосортных станов
Крупносортный стан 600 предназначен для производства двухтавровых балок высотой до 200 мм, угловой стали с шириной полок до 160 мм, круглой стали диаметром до 120 мм, квадратного профиля сечением до 100 х 100 мм, полос шириной до 200 и высотой до 50 мм и рельс массой до 24 кг/м. Заготовкой служит блюм сечением 300 х 300 мм и длиной 6 м.
Стан состоит из 17 рабочих клетей, установленных по трем параллельным линиям. Линии связаны пятью шлепперами, что позволяет миновать некоторые клети. Для кантовок используют кантователи с углом поворота 45 и 90°. Последняя клеть может быть выполнена универсального исполнения. Из этих клетей пять (2—6) и три (8-10) объединены в две группы, остальные расположены последовательно и в шахматном порядке:
Заготовки из нагревательных печей согласно технологическому циклу после сбива окалины поступают в соответствующие клети стана. Как и для предыдущих агрегатов широко используются ножницы, пилы, толкатели, манипуляторы, правильные машины и правильные прессы. Для обработки концевых элементов профилей применяют механическое оборудование, клеймители и закалочные устройства.
Непрерывный среднесортный стан 450, состоящий из 16 клетей, предназначен для производства следующих профилей: круг диаметром до 60 мм, квадрат со стороной до 55 мм, полоса шириной до 200 мм и толщиной до 22 мм, а также уголок с шириной полок до 125 мм, двутавр и швеллер высотой до 300 мм. В качестве заготовки используют раскат сечением до 200 х 250 мм и длиной до 12 м. После заготовочного стана 850/700/500 заготовки поступают в две нагревательные печи с шагающими балками. После нагрева заготовки поступают по рольгангу к ножницам для обрезки переднего и заднего концов и к гидросбиву окалины. Далее металл передается к непрерывной черновой группе рабочих клетей стана, состоящей их девяти двухвалковых клетей 630 х 1300, из них №1, №3, №4, №6, №7 и №9 — горизонтального исполнения и №2, №5 и №8 — комбинированного исполнения могут иметь как вертикальные, так и горизонтальные валки. Клети разбиты на три группы по три клети в каждой с двумя горизонтальными и одной комбинированной клетью между ними. По промежуточному рольгангу раскат направляется в чистовую группу, содержащую семь клетей: три (№10, №13 и №15) — комбинированного типа 530 х х 630 и четыре (№11, №12, №14 и №16) — универсального типа с горизонтальными валками 530 х 630 и с вертикальными холостыми валками 900 х 600.
Практика показывает, что хороший вариант при прокатке балок, швеллеров и штрипсов создают применение комбинированных клетей с горизонтальными валками и окончанием прокатки в универсальной клети. Уголок прокатывают совместным воздействием на раскат комбинированных и универсальных клетей.
Перед чистовой группой устанавливают летучие ножницы для обрезки концов раската и гидравлические ножницы для его резки на мерные длины. После чистовой прокатки готовый профиль направляют на холодильник, клеймение, резку и склад готовой продукции.
Мелкосортный стан 250 предназначен для производства сортовых профилейв бунтах массой до 2,1т. Исходной заготовкой служит квадрат сечением 150 х 150мм и длиной до 12м. Выпускаемая продукция включает: круглую сталь диаметром до 42 мм, квадратную сечением до 36 х 36мм и шестигранную. В составе стана 20 клетей с чередующимися горизонтальными и вертикальными валками; клети объединены в три непрерывные группы. Нагрев заготовок осуществляется в печи с шагающим подом. Прокатанный и охлажденный металл сматывается на трех моталках. В отделении отделки установлены правильные машины, дефектоскопы и машины абразивной зачистки.
Агрегаты проволочных станов
Непрерывный стан 250 предназначен для горячей прокатки алюминиевой катанки диаметром 7—11 мм. Исходной заготовкой служит литая заготовка сечением 300 х 300 мм и длиной до 3 м. Стан состоит из 20 рабочих клетей, разбитых на три группы: черновая группа имеет шесть клетей 400 х 700 и две клети 350 х 700 (рисунок 3), две промежуточные группы — две рабочие клети 300 х 700 и две чистовые группы — четыре последовательно расположенные вертикальные клети 250 х 400 (рисунок 4).
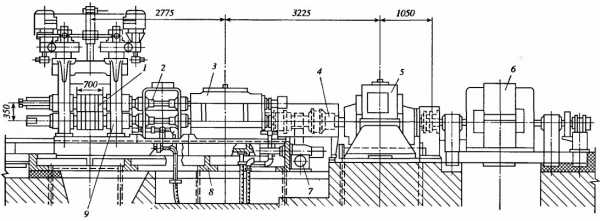
Прокатку в черновой и двух промежуточных группах осуществляют в две нитки, в чистовой — в одну нитку.
В трех проходных печах заготовки нагревают до заданной температуры и затем поочередно задают в правый и левый калибры черновой группы клетей, где их прокатывают до квадрата сечением 22 х 22 мм. Конструктивно черновые клети оформляются как все станы горячей прокатки. От электродвигателя 6 вращение передается через редуктор 5, зубчатую муфту 4, шестеренную клеть 3, универсальные шпиндели 2 на валки 1 клети 9. Для поддержания шпинделей установлены специальные поддерживающие устройства 7. Клеть, шпиндели и шестеренная клеть смонтированы на жесткой плитавине 8. Примерно такая конструкция у всех горизонтальных клетей черновой группы. За последней черновой группой установлены летучие ножницы для обрезки на ходу переднего конца проката перед задачей его в чистовые группы. Между промежуточными группами клетей и между последней промежуточной и чистовой группой предусмотрены специальные петлеобразователи, служащие для поддержания непрерывной работы агрегата при не согласовании скоростей соседних клетей.
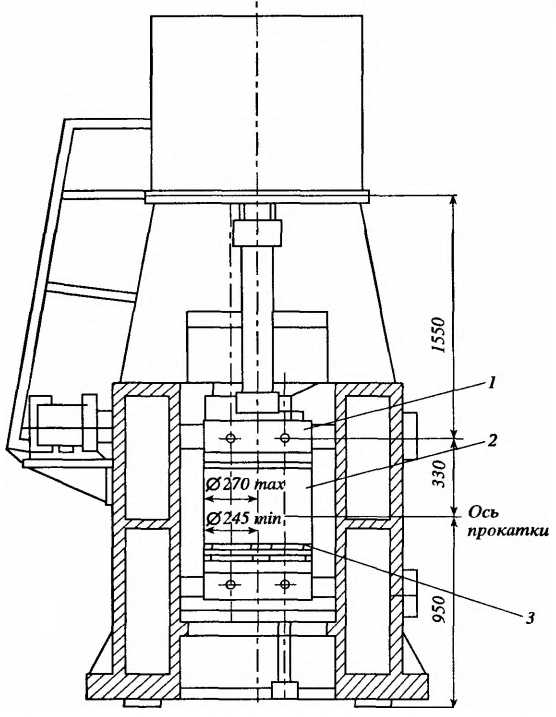
На рисунки 4 представлена чистовая клеть с вертикальными валками стана 250. Она состоит из вертикальных валков 2, установленных в подушках 1. В калибрах 3 валков формируется катанка. На выходе из последней чистовой клети катанка сматывается в бунты на одной из двух моталок. Затем сформированный бунт толкателем сталкивается на транспортер и перемещается для связки к пакетировщику, а затем на склад готовой продукции.
metallurgy.zp.ua
Сортамент прокатных станов
Под сортаментом прокатной продукции понимают изделия, получаемые в промышленности прокаткой. Под сортаментом стана понимают профили, прокатываемые на данном стане. Сортамент прокатываемых изделий весьма разнообразен. Его можно разделить на сортовые профили; простые, фасонные и специального назначения (рис. 45).
Наиболее экономичными считаются те профили, при использовании которых получаются наименьшие отходы. Таковыми в основном являются профили, конфигурация которых приближается к форме и размерам готовых изделий. Изделия, входящие в сортамент, в большинстве случаев содержатся в таблицах стандартов, помещаемых в специальных книгах, справочниках и каталогах.
В сортаменте в соответствии со специализацией прокатных станов имеется более 1500 типоразмеров простых и свыше 1000 типоразмеров фасонных профилей общего и специального назначений. Сортамент прокатных изделий, так же как и калибровка, тесно связан с общим развитием прокатного производства и вместе с ним непрерывно изменяется и дополняется. Профили облегченного п специального назначений приобретают в нем все большую долю.
Анализ производства сортовой прокатной продукции показывает, что основная доля приходится на трубную заготовку, катанку, крупносортный и мелкосортный металл. Значительно расширен сортамент экономичных профилей проката. Расширение сортамента обусловлено освоением новых экономичных профилей: широкополочных двутавровых балок, тонкостенных двутавровых балок, швеллеров и угловой стали с полкой переменной толщины.
За последние годы проведена большая работа по созданию новых станов для производства тонкостенных фасонных профилей общего назначения и специальных фасонных профилей. Ширина полок облегченных двутавровых балок и шнеллеров по новому стандарту увеличена на 20%, а толщина стенок уменьшена на 18—25%. Применение облегченных двутавровых балок швеллеров и уголков с переменной толщиной полок позволяет сэкономить от 10 до 20 % металла.
Стремление снизить массу конструкций привело также к прокатке профилей периодического сечения. Периодические профили служат заготовкой для изготовления деталей в машиностроении и, кроме экономии металла, дают резкое снижение трудоемкости изготовления машин. Улучшение сортамента не ограничивается только облегчением профилей и разработкой новых, более жестких профилей с высоким отношением момента сопротивления к единице сечения.
Важное значение имеет развитие производства термически упрочненного проката из низколегированных марок сталей, дающих возможность резко снизить (на 20—25%) массу машин. Металлургические заводы освоили прокат арматурной стали из низколегированных марок с временным сопротивлением σв≥550 МПа. Подбором химического состава металла добились еще более высоких показателей — σв арматурной стали достигло 900 МПа.
Применяя термомеханическую обработку сразу после прокатки, можно повысить σв арматуры еще в 2—3 раза. Поэтому перед научно-исследовательскими институтами и металлургическими заводами поставлена задача — разработать регламентированный режим прокатки и охлаждения профилей из низколегированной стали с σв=2500— 3000 МПа. Дальнейшее развитие прокатного производства позволит еще шире развернуть борьбу за улучшение качества проката и освоение производства новых профилей.
Сортовая сталь
Эту сталь разделяют на профили с простой геометрической формой (круглой, квадратной и полосовой) и фасонные профили.
Круглую сталь прокатывают на сортовых рельсобалочных станах диаметром от 5 до 250 мм. Круглую сталь диаметром до 9 мм (катанку) прокатывают на проволочных станах литейного типа и поставляют в бунтах массой 80— 100 кг и на проволочных непрерывных и полунепрерывных станах в бунтах массой 200—500 кг. Круглую сталь диаметром до 10 мм прокатывают на проволочных станах и поставляют в бунтах; круглую сталь диаметром до 30 мм прокатывают па мелкосортных станах, ее можно поставлять в бунтах.
Квадратную сталь прокатывают с размерами сторон от 5 до 250 мм. Квадратную сталь всех размеров прокатывают в прутках, а со стороной квадрата до 16 мм—в прутках и в бунтах. Квадратную сталь до 100 мм прокатывают с острыми углами, свыше 100 мм —с закругленными углами радиусом не более 0,15 стороны квадрата.
К полосовой стали относят ленту стальную горячекатаную (сталь обручную), прокатываемую на сортовых станах с катаной кромкой или из рулонной листовой стали, разрезаемой на дисковых ножницах на ленту определенной ширины, а также штрипсы сортовые, прокатываемые на сортовых и штрипсовых станах. Полосовую сталь прокатывают шириной от 12 до 200 мм и толщиной от 4 мм и более.
Фасонные профили
Фасонные профили проката подразделяют на профили общего назначения (угловую равнобокую и неравнобокую сталь) и специального (отраслевого) назначения, применяемые в различных отраслях народного хозяйства.
Угловые профили прокатывают на сортовых и рельсобалочных станах. В ГОСТах их обозначают номерами, которые соответствуют ширине полок. Угловые равнобокие профили прокатывают от № 2 до № 25, что соответствует ширине полок от 20 до 250 мм. Неравнобокис угловые профили (номер указывают дробью) прокатывают от № 2,5/1,6 до № 25/16. Толщина полок уголков составляет в зависимости от номера профиля от 3 до 30 мм, причем угловые профили одинакового номера прокатывают с различной толщиной полок (50×50×3÷4; 40×50×5; 75×75×5÷9 и др).
Двутавровые балки прокатывают на рельсобалочных станах (размером от 20 и выше) и сортовых станах (размером до № 20). Внутренние грани фланцев имеют уклон 1 : 10. Прочность балок характеризуется моментом сопротивления, который зависит от соотношения площади отдельных элементов сечения.
Для строительства применяют балки с тонкой стенкой и с возможно более широкими полками. Такие балки при меньшей массе обладают большей прочностью, чем соответствующие по номеру балки, но с более толстой стенкой и менее широкими полками.
На прокатных станах изготавливают также балки с параллельными полками, для получения которых станы оборудуют специальными универсальными клетями с горизонтальными и вертикальными валками.
Швеллеры прокатывают на рельсобалочных станах (крупные размеры от № 20 и выше) и сортовых станах (мелкие размеры до № 20 высотой от 50 до 400 мм). В некоторых отраслях народного хозяйства используют профили швеллеров № 14, 16, 18, 20, 30. Швеллеры стремятся получать с возможно более тонкими стенками и более широкими полками. При высокой прочности такие швеллеры имеют меньшую толщину стенки и меньшую массу, чем обычные швеллеры такого же номера.
Шестигранную сталь (с диаметром вписанного круга от 8 до 100 мм) прокатывают на сортовых станах. Прокатывают также следующие размеры этой стали: 23, 27, 29, 41, 43, 44, 46, 53, 56, 57 и 67 мм.
К фасонным профилям специального (отраслевого) назначения можно отнести следующие.
По ГОСТ 5781—75 прокатывают круглую периодическую сталь 21 (арматурную) для армирования обычных и предварительно напряженных железобетонных конструкций на сортовых станах. Арматурная сталь периодического профиля представляет собой круглые стержни с двумя продольными ребрами (усами) в местах разъема валков и с поперечными выступами на верхнем и нижнем контурах профиля, идущими по трехзаходной или двухзаходной (для диаметров 6—8 мм) винтовой линии (рис. 46). Профили выпускают от № 6 до № 80, причем номер периодического профиля обозначает его номинальный диаметр, соответствующий номинальному диаметру равновеликой по площади поперечного сечения гладкой круглой стали. Выступы на профиле обеспечивают увеличение сцепления арматуры с бетоном (у периодической стали оно в 2—4 раза больше, чем у круглой гладкой).
В зависимости от механических свойств (табл. 4) арматурную сталь периодического профиля делят на четыре класса: А-II, А-III, А-IV, А-V. Профиль арматурной стали класса А-II приведен на рис. 46, а. Специальная арматурная сталь Ас-II имеет профиль, показанный на рис. 46, в. Арматурная сталь этого типа имеет поперечные выступы, идущие по винтовым линиям с одинаковым заходом на верхнем и нижнем контурах профиля. Профиль арматурной стали класса А-III показан на рис. 46,б, а классов А-IV и А-V — на рис. 46, г. Поперечные выступы арматурной стали этих классов идут по винтовым линиям, но имеют на одном контуре профиль правый, а на другом левый заходы «елочкой». Специальная арматурная сталь классов Ас-II, А-IV и А-V (рис. 46, в, г) предназначена для использования прн пониженных температурах. Особенность профиля этой арматурной стали — чередование на его верхнем и нижнем контурах пологих полукруглых углублений и выступов.
Потребителям арматурную сталь периодического профиля класса А-II диаметром до 12 мм и класса А-III диаметром до 10 мм поставляют в бунтах или прутках, а сталь больших диаметров — только в прутках. Арматурную сталь классов А-IV и А-V прокатывают в прутках, а диаметром до 8 мм — в прутках или бунтах по согласованию с потребителем. Длина прутков составляет от 6 до 12 м, допускается изготовление прутков длиной от 5 до 25 м.
Профили № 2, 3, 4, 6, 8 для оконных и фонарных переплетов в промышленных зданиях прокатывают на мелкосортных станах. Профили толщиной 3,3 мм используют взамен старых профилей такой же конфигурации толщиной 3,8 мм. Для переплетов попой конструкции это дает до 20 % экономии металла и значительную экономию топлива в результате уменьшения потерь тепла зданиями.
Полособульбовые несимметричные и симметричные профили прокатывают на сортопрокатных станах для судостроения. Полособульбовые симметричные профили предусмотрены высотой от 40 до 300 мм, шириной от 17—18 до 86—90 мм в зависимости от высоты. Масса 1 м профиля составляет от 1,75 до 47,8 кг. Усиленные профили предусмотрены высотой от 60 до 400 мм, шириной от 31—33,5 до 147—151 мм в зависимости от высоты и толщины от 5 до 15 мм. Масса 1 м усиленного профиля от 4,15 до 101,1 кг.
Применение полособульбовых симметричных профилей взамен профилей несимметричных дает значительную экономию металла и позволяет сократить трудоемкость работ при строительстве судов в связи с тем, что отпадает часть операций по гибке и правке профилей, а также уменьшается объем работ по сварке и резке.
Шпунтовые профили прокатывают на рельсобалочных станах и применяют в гидростроительстве. Для сооружения ячеистых конструкций используют шпунтовые плоские профили ШП-1 и ШП-2 для протинофильтрацнонных завес (шпунтовые корытные профили ШК-1, ШК-2) и для подпорных стенок и причальных сооружений (шпунтовые зетовые профили).
Различают рельсы железнодорожные для широкой и узкой колеи. Профиль рельса характеризуется массой 1 м длины. Рельсы шириной колен Р38, Р43, Р50, Р65, Р75 и узкой колеи Р8, P11, Р15, Р18, Р24 прокатывают на рельсобалочных станах по соответствующим стандартам, техническим условиям и согласованным с Министерством путей сообщения чертежам.
Листовую сталь подразделяют на тонколистовую (толщина листа менее 4 мм) и толстолистовую (толщина листа больше 4 мм). Различают листовой прокат: котельный, топочный, судостроительный, автотракторный, электротехнический, жаропрочный, жесть и др.
Трубы подразделяют на бесшовные и сварные. Сортамент труб весьма разнообразный. По поперечному сечению различают круглые, овальные, прямоугольные, ребристые и другие трубы; по назначению водогазопроводные, нефтепроводные, бурильные, обсадные, котельные, конструкционные, для магистральных трубопроводов и др.
metallurgy.zp.ua
Основные требовании при проектировании прокатных цехов
Проектирование прокатных цехов ведется в соответствии с Правилами безопасности в прокатном производстве, а также в соответствии с действующими санитарными нормами и правилами. Требования указанных Правил распространяются и на заводы-изготовители прокатного оборудования. При проектировании прокатные цехи располагают на территории предприятия таким образом, чтобы они составляли последовательное продолжение металлургического цикла. Ось прокатного цеха должна быть перпендикулярна направлению господствующих в данной местности ветров. Конструктивно здания прокатных цехов не отличаются от типовых. Стены выполняются из кирпичной кладки или сборного железобетона. Световые проемы по длине здания могут быть выполнены в 2—3 ряда. Окна и проемы в верхней части -здания располагают на высоте не менее 1,2 м от уровня подкрановых путей. Световые проемы в торцовой части здания не обязательны, если световые проемы вдоль здания и аэрационные фонари создают нормальную световую естественную освещенность на любом участке цеха. В связи с большими теплоизлучениями повышенные требования предъявляют к кровле здания, которая должна выполняться из прочных негорючих материалов. Применение конструкции кровли без аэрационных фонарей нежелательно. Полезная площадь производственных зданий прокатных цехов по своим размерам должна быть такой, чтобы обеспечить достаточное освещение дневным светом, хорошее естественное проветривание (аэрацию) и удовлетворять требованиям безопасного размещения оборудования с необходимыми проходами между ними. Она должна обеспечить также возможность свободной транспортировки прокатываемого металла и готовой продукции.
Травильные, отделения, а также оцинковочные и лудильные должны быть расположены в изолированном помещении. Нагревательные устройства также в большинстве цехов изолируются от остальных производственных помещений, и сообщение между ними осуществляется лишь с помощью проемов в стенах. Размеры проемов не должны допускать попадания горячего воздуха из пролетов нагревательных устройств в другие производственные помещения. В местах транспортировки металла пол прокатных цехов настилают гладкими металлическими плитами, зазор между которыми должен отсутствовать. Для передвижения людей укладывают рифленые плиты, либо наносят на гладкие плиты точечную наварку. На складах слитков, заготовок и готового проката полы выполняют из каменной брусчатки, железобетона или металлических плит. Полы вспомогательных помещений прокатных цехов выполняют из асфальта, керамических плиток или деревянных торцовых шашек.Въездные и выездные ворота в торцах здания оборудуют воздушными или тепловыми завесами и механическим приводом для открывания и закрывания. При этом целесообразно сооружение блокирующего устройства, включающего вентилятор воздушной завесы при включении механизма открывания ворот. Для безопасного и удобного прохода людей к рабочим местам по периметру здания устраивают специальные двери. Современные многопролетные прокатные цехи оборудуют подземными пешеходными туннелями, имеющими выходы к основным производственным участкам и агрегатам. Вдоль всего цеха с обеих наружных сторон здания прокладывают пешеходные тротуары. Все свободные участки территории должны озеленяться.
Полезная информация:ohrana-bgd.narod.ru
СТАНИНА КЛЕТИ ПРОКАТНОГО СТАНА "НЛС-1700"
ЖЕЛЕЗОБЕТОННЫЕ ДЕТАЛИ МАШИН
Монолитное выполнение узла станин клети стана Кварто-200 в железобетоне является преимуществом для малых клетей и не может быть общим решением для тяжелых клетей станов, где габарит по высоте станин может превышать 10 лі, а вес узла станины 200 т. Значительная длина валков в листовых станах требует установки двух нажимных винтов, а следовательно, двух отверстий в поперечинах каждой станины. Это значительно усложняет конструктивное решение узла станин тяжелых прокатных клетей в железобетоне. Параллельно с НИИЖБом и ВНИИМЕТМАШем в г. Краматорске НИИПТМАШем создана конструкция узла станин клети непрерывно-листового стана НЛС-1700 в железобетонном исполнении [2]. Для выполнения этой задачи потребовались совершенно новые технические решения. Непрерывно-ли - стовой стан НЛС-1700 предназначен для горячей прокатки слябов весом до 15,5 /пи длиной от 2000 до 6300 мм в полосы толщиной 1,2—10 мм, свернутые в рулоны. Рабочие клети чистовой группы служат для непрерывной прокатки полосы, придания ей окончательных размеров и надлежащей чистоты поверхности. Диаметр рабочих валков 700 мм, опорных валков 1400 мм, длина бочки валка 1700 мм. Скорость прокатки 6—15 м/сек. На стане прокатывают углеродистые стали, а также возможен прокат полос из леги-
Н
Рованных сталей с пределом прочности до 98-106
На пониженных режимах.
При конструировании железобетонных станин клетей исходят из конкретных условий. Так, при разработке конструкции железобетонной станины стана НЛС-1700 для Карагандинского завода исходили h4jy^OBHH, что примыкающие к станинам узлы клети были уже изготовлены, то в основу проекта было положено требование максимально сохранить габарит станины. Жесткие требования сохранения в железобетонной станине формы и размеров повлекли за собой повышенный расход металла и большие трудности в обеспечении необходимой жесткости станины. При проектировании новых прокатных станов можно создать конструкции железобетонных станин любой нужной жесткости и прочности со значительно меньшим расходом металла.
Конструкция узла станины клетей стана HJ1C-1700 изображена на рис. 48 и представляет'собой две раздельные станины, жестко связанные между собой внизу двумя стальными поперечными траверсами 8, а вверху двумя боковыми и одной центральной траверсами. Стойки станин 2, верхняя 1 и нижняя 5 поперечины облицованы стальным листом. Планки 4 и 7 на нижней поперечине выполняют роль салазок, по которым выдвигают комплект валков при их смене. Внутри проем облицован листом толщиной 50 мм, к которому прикреплены сменные планки 3. Станины крепят к фундаменту анкерными болтами, пропуская их через отверстия в стальных полых литых плитах 6.
Все элементы станин, которые при действии усилий прокатки испытывают растягивающие напряжения, подвергаются предварительному напряжению за счет натяжения арматуры. В таких элементах бетон всегда будет работать на сжатие, а арматура — на растяжение. Рассмотрим конструирование отдельных узлов железобетонных станин клети прокатного стана HJ1C-1700 (рис. 49).
Узлы и элементы железобетонной станины клети, в которых по условиям работы возможны растягивающие напряжения, армируют напрягаемой стержневой арматурой диаметром 40 мм из стали 30ХГ2С. Чтобы не ослаблять сечение напрягаемых стержней нарезкой резьбы, с обеих концов их наваривают контактной стыковой электросваркой коротыши с резьбой М42.
При конструировании станин предусматривалось, что бетонировать их будут на месте монтажа. Металлический каркас станин проектировался таким, чтобы была обеспечена необходимая его жесткость при механической обработке и транспортировании. Разработанная конструкция технологична, изготовление отдельных элементов металлического каркаса несложно.
Металлический каркас станин запроектирован из полых стоек прямоугольного сечения и литых верхних и нижних балок. Стойки каркаса выполняют сварными из листовой стали толщиной 18 мм, а со стороны направляющих планок — окна станины из листа толщиной 50 мм для получения необходимой жесткости каркаса при механической обработке окна станины. Верхние и нижние балки сделаны из стального литья и в соединении со стойками образуют общую жесткую конструкцию каркаса. Такая конструкция каркаса станин позволяет производить: полную механическую обработку, контрольную сборку клети на заводе-изготовителе, транспортирование каркасов станин по железной дороге и бетонирование
Рис. 48. 'Узел станин прокатного стана НЛС-1700 с железобетонными отъемными станинами: |
/ — верхняя поперечина; 2 — стойки станин; 3 — сменные планкн; 4 и 7 — планки на нижней поперечине; 5 — нижняя поперечина; 6 — стальная литая полая плита; 8 — нижние траверсы |
|
Станин на месте монтажа, не нарушая классов точности посадочных мест. Поскольку напрягаемую арматуру натягивают после бетонирования, для размещения ее и предотвращения сцепления бетона с арматурой последняя размещается в трубах диаметром 62 мм. Стойки железобетонной станины клети, подвергающиеся растяжению, армируют продольной напрягаемой арматурой 7. Располагают ее в стойках так, чтобы центр тяжести сечения стойки совпадал с центром тяжести суммарной эпюры изгиба и растяжения и центром затяжки. В местах передачи усилий от затяжки арматуры 7 на верхнюю поперечину предусмотрены планки 6 и 13 из листа толщиной 100 мм для предотвращения местного смятия бетона и распределения давления по площади.
Для восприятия растягивающих напряжений в верхней поперечине железобетонной станины от действия изгибающего момента и поперечной силы в поперечине располагают продольную напрягаемую арматуру 3 в виде сквозных шпилек длиной 4300 мм. Среднюю часть верхней поперечины в плоскости стоек армируют напрягаемой арматурой в виде коротких шпилек 12 длиной 1810 и 1410 мм. Один из концов шпилек в стальной отливке закрепляют на резьбе.
В местах передачи усилий от напряжения шпилек (арматуры) для равномерной передачи нагрузки на бетонные поверхности и защиты бетона от местного смятия на верхней поперечине предусмотрены планки 4 из листа толщиной 50 мм. Для связи поверху между обеими станинами клети предусмотрены стяжные шпильки 1 и 16 длиной соответственно 5000 и 6030 мм. Там, где они опираются на наружную поверхность бетона, ставят планки 2 и 15 из листа.
Верхняя траверса 8 соединена с верхней поперечиной станины болтами 9 (М64 X 280). В сжатой зоне верхней поперечины устанавливают ненапрягаемую арматуру 11 из стали класса А—I диаметром 24 мм, которая с помощью хомутов связана с напрягаемой араматурой в растянутой зоне поперечины. Для повышения жесткости станины, учитывая, что в стойках наблюдаются большие растягивающие усилия, верхняя и нижняя поперечины приняты несколько большей высоты.
За счет повышения жесткости поперечин удалось снизить величины напряжений от изгибающих моментов во внутренних входящих углах станины. В железобетонных рамах для смягчения перенапряжений входящие углы необходимо проектировать в виде закруглений или вутов. В станине НЛС-1700, конструктивно, по расположению узлов и механизмов, вуты выполнить нельзя, поэтому пришлось повысить жесткость поперечины. Верхние и нижние поперечины в железобетонных станинах можно выполнить в любых требуемых для железобетона сечениях.
Для повышения жесткости углов сопряжений поперечин со стойками устанавливают дополнительные наклонные стержни 10 82 диаметром 24 мм. Таким же образбм конструируй? НИЖНЮЮ поперечину станины. Напрягаемую арматуру (шпильки) располагают на таком расстоянии, чтобы обеспечить их нормальное натяжение с помощью гидравлических домкратов.
В станине НЛС-1700 расстояния между напрягаемой арматурой (шпильками) приняты от 160 до 200 мм. Арматуру верхних и нижних поперечин станин располагают таким образом, чтобы 'ее центры натяжения совпадали с центрами тяжести эпюр изгибающих моментов в зоне растягивающих напряжений. Наружный каркас станины, облицовка верхних и нижних поперечин листовой сталью запроектированы так, что они одновременно являются опалубкой при бетонировании.
При конструировании предусмотрена технологичность изготовления элементов и необходимая жесткость каркасов станин для транспортирования. Арматурные стержни в каркасе станины размещены так, что наконечники глубинных вибраторов могут свободно проходить между стержнями каркаса. В этом случае обеспечено качественное уплотнение бетона в конструкции. Для изготовления станин клетей следует предусматривать жесткие бетоны высоких марок (600 и более), так как в этом случае усадка бетона будет минимальной.
Для станины клети НЛС-1700 марка бетона принята 600. Чтобы предупредить возможность выпучивания боковых листов стоек при бетонировании, к листам приварены круглые стержни диаметром 10 мм в двух взаимно перпендикулярных направлениях. Для надежности анкеровки боковых листов стоек к ним приварены анкеры в виде отрезков стержней того же диаметра, длиной 200 мм с шагом 250 мм по вертикали.
В процессе эксплуатации стана необходимо периодически контролировать арматуру с помощью гидродомкратов с манометрами. При ослаблении затяжки натяжение доводят до требуемого.
Преимущества конструкции узла станин рабочих клетей стана НЛС-1700 заключаются в следующем: экономия металла на изготовление станин рабочих клетей составляет на одну клеть 130 т; значительно уменьшается цикл изготовления; снижения стоимости изготовления; на заводе изготовляется только металлический каркас станины, а бетонируют его на месте монтажа, что облегчает транспортирование станин и их монтаж; станина не уступает по прочности, жесткости и долговечности в работе станинам из стали. Для очень крупных станов и в тех случаях, когда по условиям' прокатки от станины не требуется большой жесткости, целесообразно применять составные станины. При этом облегчается изготовление, обработка и транспортирование.
В тонколистовых станах горячей и холодной прокатки имеет значение не только прочность станин (определяемая величиной возникающих в них напряжений), но и жесткость, т. е. величина их деформации при прокатке. Если деформация станин при 6* 83
Прокатке будет значительной, то это отразится На величине допусков по толщине прокатываемых листов.
Станины рассчитывают на максимальное усилие, действующее при прокатке на шейку валка и передающееся на нее через подушки, нажимной винт и нажимную гайку. Горизонтальными усилиями, действующими на валки и станину в момент захвата и при прокатке с натяжением, обычно пренебрегают, так как по сравнению с вертикальным усилием они незначительны.
В станине прокатного стана 1700 наибольшее давление прокатки Рпр = f800 т, а момент прокатки Мпр = 30 ООО кГм. Для расчета станины принимается, что давление металла на валок Р направлено вертикально.
Таким образом, на ригель каждой станины от шеек верхнего и нижнего опорных валков через подушки и нажимной винт
Р
Будут действовать силы, равные - у - = 900 т.
В конструктивно принятых параметрах железобетонной станины находят сечения и волокна, которые испытывают растягивающие напряжения.
В центре тяжести эпюры растяжения прикладывается результирующая усилий предварительного натяжения арматуры. Ее величину определяют с таким расчетом, чтобы в условиях эксплуатации бетон элементов станины работал на сжатие, а арматура на растяжение.
При определении напряжений в расчет вводят приведенную площадь, т. е. площадь арматуры и металла, входящего в расчетное сечение, приводят к площади бетона посредством расчетного числа п.
Кроме условий прочности, станина также должна удовлетворять условиям жесткости.
При расчете станины на жесткость определяют суммарную деформацию, слагающуюся из деформации стоек и ригелей. Полученную суммарную деформацию всей станины сравнивают с допустимой деформацией для станин.
Пример. Расчет предварительно напряженной железобетонной станины непрерывно-листового прокатного стана НЛС-1700.
Исходные данные для расчета: наибольший момент прокатки Мпр = = 30 000 кГм; наибольшее давление прокатки Рпр = 1800 т; расстояние между осями нажимных винтов 2800 мм; продолжительность цикла прокатки 40—120 сек; число пропусков за цикл — 1; максимальная деформация станины допускается равной 1,08 мм *. Бетон принят марки 600 с £б = 0,41-10в кГ/см2; напрягаемая арматура из стали Ст. 30ХГ2С со, = 9000 кГ/см2.
1. Проверка прочности станины.
Построение нейтральной линии станины и подсчет моментов инерции сечений. Схема станины изображена на рис. 50.
|
А. Сечение А—А. Координата нейтральной плоскости (рис. 51)
2 (ріУІ + nFWi)
У 2(^ + 0 '
Где F-t н F. — площади участков сечений бетона и металла; 2 Ы0в
П = q = ^>^25 — отношение модулей упругости металла и бе
Тона;
(/,• н уі — расстояние от центра тяжести участков сечений до нижней кромки сечения.
93,2.76,4-51,6— 28,3-2 (2-15 + 2,33 + 54 + 79 + 90) +
+ 5,125 [80.5.2,5 —80-1,8.99,1 +2.93,2-1,8.51,6 + 4.4,48.33 +
^______________ + 4-4,48-15 + 2-4,48 (54 + 79 + 90)]______________ =
Ja 93,2-76,4- 14-28,3 + 5,125.(80-5 + 80-1,8 + 2.93,2-1,8 +
+ 4.4,48+ 4.4,48 + 2.4,48 + 2.4,48 +2-4,48)
Приведенная площадь сечения F" = Fg + nFM. Площадь бетона Fq = 6724 см2. Площадь металла FM = 943 см2.
Fanp = 6724+ 5,125-943 = 11 561 см2. Приведенный момент инерции сечения А—А стоек станины
Janp = J6+
Где J б — момент ннерцни бетона; J іи — момент инерции металла.
7б = ^6^ + 76 4.93i2.5>62_ [ 14 ЗЛ^ + 4 304^ (312 + 132) +
2 3>1*'6 (82 + ЗЗ2 + 442)
^=^ + 80.5.43,52 + i^ + l,8-80.53,P + 2-W + + 2• 1,8• 93,2• 5,62 + 14 —(б4 — 5,554) + 4 (б2 — 5,552) (ЗІ2 + 132) +
+ 2 (б2 — 5,552) (82 + ЗЗ2 + 442) = 1 460 074 см*.
Janp = 5 047 681 + 5,125-1 460 074 = 12 523 000 см*.
Б. Сечение Д—Д Координата нейтральной плоскости (см. рис. 51) уа = 48,4 см.
JM = 7 590 966 см*. J6 = 34 070 997 см*. Приведенный момент инерции сечения Д—Д нижнего ригеля.
Jdnp = 34 070 997-f 5,125-7 590 966= 6,28-107 см4. Площадь бетона Fq = 16 862 см%. Площадь металла FM = 4260 см2. Приведенная площадь сечения
Fdnp = 16 862 + 5,125-4260 = 38 662 см2. В. Сечение В—В Координата нейтральной плоскости (см. рис. 51) ув = 71,5 см. J6 = 8 898 365 см*.
Jnp = 8 898 365 - г 5,125 13 895 729 = і
Площадь сечения бетона Fg = 9426 см2; площадь сечения металла FM = = 7680 еж2.
Приведенная площадь сечения
Fenp = 9426 + 5,125-7680 = 48776 см2. Определение деформаций в стаииие рабочей клети
Деформации (угловые и линейные) определяем исходя из упругой работы железобетонной рамы.
Г np Jnp
А)
Рис. 52. Расчетные характеристики станины:
А — расчетная схема железобетонной станины; б — момент в стойках; в — эпюра моментов
Исходные данные: Р = 900 000 кГ; 1= 251 см; Л = 709,9 см; J"np = : 80,1 • 10® см4; Jdnn = 62,8 • 10® см4; Janp = 12,523-106 см4; F°nn = 48 776 см2>
Пр
Кр 38 662 см2' Fnp = 11 561 см2> Еб = 0,41-10® кГ/см2; hx = 590 см. Расчетная схема станины дана на рис. 52, а. Моменты инерции и площади сечений приведены К бетону.
Удлинение стоек
0 = ГГ^ = о"ТГ. ГсТ - [3] кГ/см*.
0,0561 см.
И,-І І • і и"'
Прогиб верхнего ригеля
H /і + fi-fl Прогиб от изгибающего момента
F' РР 900 ООО • 2513 ПЛП0Л.
H = = 48-0,41.10«.80,1-Ю'" = °'°OSOb-
Прогиб от перерезывающей силы
Р1
Fi
2G6F°
- 1,2-— коэффициент формы прямоугольного сечения. Модуль упругости 2-го рода
^ Еб 1
°б= 2(1+]!)' при ^ = •
G6 = 0,42857£б = 0,42857-0,41.106 = 0,1755-106 кГ/см\
F,0 900 000-251 лП1СОс
= ^T^7^^T0®T48776 = 0,01585 см.
Выгиб
,„ ^ MtP. 1 8E6J°np ■
Момент в стойке (рис. 52, б)
I h, I
М _ Pl М _ pi Pl 4J"p ' J*P <Р
Р | 900 000 |
2Fa | 2-11561 |
Пр | |
Cf/Zx | 39.590 |
Еб | 0,41 • I06 |
М, _ _ _ М, _ _-------------- - ----- ---------- ---------------
9 Iа Iа 9 Iа " пр J пр " пр
РР Ji+Jz 9-105 - 2512
TOC \o "1-3" \h \z — X
16 , je Ja h 16
1 < Iе 4- Id \ 4- "Р "р
~2 V пР + Jnp) + ~~Та-------
Пр
(80,1 + 62,8) 106 , с, г
Эпюра моментов показана на рис. 52, в.
Г 1,67-106-2512 ПППЛ,
Fi = ОТГГО^™ = °'0004
Тогда
Fl = 0,00905 + 0,01585 — 0,0004 = 0,0245 см.
Прогиб нижнего ригеЛЯ
H = f2 + r3-n.
Прогиб от изгибающего момента
__ Р13 __ 900 ООО-2513 _ п п,, 2 ~ 48 E6Jdnp ~~ 48-0,41.106-62,8.106
Прогиб от перерезывающей силы
Г" и Pl 900 000-251
/2 = = ' 2-0,1755-106-38662 = °'01"
Выгиб
,» _ М, Р _ 1,67-106-2513 _ 2 ~ 8E6Jdn ~~ 8.0,41.10».62,8.10» ~ ,0° ' СМ'
Пр
/2 = 0,01155 + 0,0199 — 0,00051 = 0,03094 см. Общая деформация станины
/ = /і + /а + /з = 0,0245 + 0,03094 + 0,0561 = 0,11154 см.
Если вместо /з = 0,0561 см подставить величину Д2 = 0,0524 см (полученную из графика рис. 55), то получим
/ = /і + /а + д2 = 0,0245 + 0,03094 + 0,0524 = 0,10784 см <1,08,
Т. е. общая деформация станины находится в пределах допустимой величины. Построение нейтральной лииии станины и расчетной схемы нагружений.
I = 159 + 2 уа = 159 + 2-46 = 251 см.
H = 590 + ув + yd = 590 + 71,5 + 48,4 = 709,9 см.
Защемляющий момент в месте соединения поперечин со стойками.
Тогда
II. Определение напряжений в станине.
Напряжения в верхней поперечине (сеч. рис. 51) Растяжение в верхних волокнах бетона
(~-мЛ (135 — ув— 19)
АР = ---------------- L-------------------- =
Iе "Р
0 Q.10е.9S1 ' " - (1,6/. 10")
msd.com.ua