Быстрорежущая сталь. Ее свойства и классификация. Рапидная сталь
ГОСТ, состав, твердость, термическая обработка :: SYL.ru
Для того чтобы рабочая поверхность инструмента сохраняла заданные свойства длительное время, необходимо использование специальных сплавов и сталей для изготовления таких элементов. На сегодняшний день детали режущего инструмента производятся из твердых сплавов, инструментальных марок стали. Для фрез, резцов, зубил используется в основном быстрорежущая сталь.
Основные требования к сплавам для режущего инструмента
Детали такого типа длительное время работают в условиях трения и повышенных температур. Однако рабочая поверхность должна сохранять свои свойства, обладать высокой износостойкостью и твердостью. При больших скоростях, которые набирает инструмент в процессе резанья, нагревается и его кромка, и сама деталь, и стружка. Поэтому основная характеристика, которой должна обладать быстрорежущая сталь – теплостойкость. Для труднообрабатываемых материалов используют порошковые быстрорежущие стали. Они имеют более высокие режущие свойства. Недостатком таких сплавов является затруднительная обработка заготовок. Все необходимые характеристики достигаются путем введения определенных легирующих элементов и специальной термической обработкой.
Маркировка стали
Быстрорежущая сталь маркируется буквой Р, которая ставится впереди. Основными легирующими элементами являются вольфрам, хром. Также дополнительно вводят такие элементы, как ванадий, молибден. Цифра после буквы Р указывает процентное содержание вольфрама в стали. Как правило, в состав быстрорежущей стали входит около 4% хрома. Данный элемент в маркировке не указывается. Если цифры стоят перед буквой Р, то они указывают на процентное содержание углерода (например, сталь 11Р3АМ3Ф2 содержит 1,1% углерода). В основном стали данной группы являются высоколегированными.
Влияние легированных элементов на свойства стали
Высокую теплостойкость быстрорежущих марок стали обеспечивают вольфрам, молибден. На их основе образовываются карбиды, которые частично переходят в твердый раствор. После термообработки обеспечивается структура мартенсита. Вольфрам, молибден, а также ванадий замедляют его распад. Именно это обеспечивает необходимую красностойкость. Продолжительное время использовалась быстрорежущая сталь, легированная только вольфрамом. Однако из-за дефицитности данного металла его начали частично заменять молибденом. Этот элемент также положительно влияет на склонность вольфрамовых марок стали к карбидной неоднородности. Наиболее твердый карбид образовывает ванадий. Однако при этом содержание углерода должно быть достаточным для большего насыщения твердого раствора. Чем больше вводится ванадия, тем больше должно быть углерода в составе сплава. Основная задача хрома – придание стали высокой прокаливаемости. Красностойкость также повышает и кобальт.
Быстрорежущая сталь (твердость при легировании данным элементом повышается до 70 HRC) в данном случае будет иметь пониженную прочность. Стоит отметить, что введение хрома широко не применяется из-за большой стоимости элемента.
Термообработка быстрорежущей стали
Данные марки стали поступают в состоянии ковки (температура около 1200 °С). Производится нагрев до 860 °С, затем металл выдерживается при температуре около 760 °C. Термическая обработка инструмента включает закалку и отпуск. Стоит отметить, что такая обработка имеет свои особенности. Во-первых, необходим медленный, постепенный нагрев. Так как сталь высоколегированная, ее теплопроводность довольно низкая, стремительное нагревание может привести к образованию трещин. При этом очень важно нагревать заготовку равномерно. Используются электрические печи, соляные ванны. Процесс обработки быстрорежущей стали довольно трудоемкий, он требует четкого соблюдения всех этапов технологического процесса.
Главная задача закалки – растворение карбидов в аустените. Как правило, карбиды на основе вольфрама и хрома растворяются при 1200 °С, ванадий требует более высоких температур. После данного этапа структура имеет избыточные (те, что не растворились) карбиды. Они сдерживают рост зерна. Высокие температуры обеспечивают мелкозернистый аустенит. Охлаждение происходит в масле или расплаве солей. Температура по сечению детали выравнивается. Такая обработка быстрорежущей стали позволяет избежать появления трещин. После закалки сталь имеет следующую структуру: мартенсит, остаточный аустенит, карбиды.
Отпуск быстрорежущей стали
Отпуск стали способствует превращению мартенсита закалки в мартенсит отпуска, аустенита в мартенсит (так как первый не обладает достаточной твердостью), снятию остаточных напряжений. Как правило, термическая обработка быстрорежущей стали включает многократный отпуск. Начинается данный процесс при температуре 150 °С. Далее при 550 °С происходит дисперсионное твердение (выделяются карбиды из твердого раствора). В результате возрастает твердость сплава. Более высокие температуры отпуска нежелательны, так как будет происходить процесс распада мартенсита, и, соответственно, снижение твердости. Вольфрамовые стали после единичного отпуска имеют в составе остаточный аустенит. Полностью он превращается в мартенсит при втором отпуске. Остаточные напряжения снимаются в процессе третьего отпуска. Стали с содержанием кобальта могут подвергаться отпуску и в четвертый раз.
Нарушение технологии термообработки
Снижение количества углерода на поверхности заготовки может быть следствием плохой расскисленности соляной ванны, а также перегрева при аустенизации. Превышение температуры ведет к оплавлению границ зерна. Также обработанная деталь может иметь трещины. Такое явление возникает из-за быстрого нагрева металла. Еще одна причина – ускоренное охлаждение. Низкое значение твердости может быть следствием недостаточного легирования структуры мартенсита, нарушением температурного режима при отпуске, при котором остается остаточный аустенит. Еще один возможный дефект заготовки – нафталинистый излом.
Наиболее распространенные марки быстрорежущей стали
Быстрорежущая сталь (ГОСТ 19265-73) делится на сплавы нормальной и повышенной теплостойкости. Первая группа включает такие марки, как Р18, Р6М5. Твердость их достигает 63 HRC. Основное их предназначение – обработка чугунов, медных, алюминиевых сплавов. Более высокой теплостойкостью обладают вольфрамовые стали. Их применяют для изготовления сверл, фрез, резцов. Сталь Р6М5, которая содержит молибден, немного уступает в режущих свойствах, однако она существенно дешевле. К тому же пластичность ее несколько выше, а склонность к образованию трещин не столь высока. Более теплостойкие стали имеют в составе ванадий и кобальт (10Р6М5, Р9Ф5). Их твердость досягает 66 HRC. Используются они для обработки более прочных конструкционных сталей, жаропрочных сплавов, при изготовлении чистового инструмента. Характерно, что данные марки имеют более высокую износостойкость (благодаря наличию в составе ванадия). В последнее время все чаще применяется метод порошковой металлургии. Такие инструменты имеют более высокие режущие свойства.
www.syl.ru
Рапидная сталь. Термическая обработка быстрорежущей стали
Быстрорежущая сталь - Википедия
Быстроре́жущие ста́ли — легированные стали, предназначенные, главным образом, для изготовления металлорежущего инструмента, работающего при высоких скоростях резания.
Быстрорежущая сталь должна обладать высоким сопротивлением разрушению, твёрдостью (в холодном и горячем состояниях) и красностойкостью.
Высоким сопротивлением разрушению и твердостью в холодном состоянии обладают и углеродистые инструментальные стали. Однако инструмент из них не в состоянии обеспечить высокоскоростные режимы резания. Легирование быстрорежущих сталей вольфрамом, молибденом, ванадием и кобальтом обеспечивает горячую твердость и красностойкость стали.
Истории создания[ | ]
Сверло с покрытием из нитрида титанаДля обточки деталей из дерева, цветных металлов, мягкой стали резцы из обычной твердой стали были вполне пригодны, но при обработке стальных деталей резец быстро разогревался, скоро изнашивался и деталь нельзя было обтачивать со скоростью больше 5 м/мин[1].
Барьер этот удалось преодолеть после того, как в 1858 году Р. Мюшетт получил сталь, содержащую 1,85 % углерода, 9 % вольфрама и 2,5 % марганца. Спустя десять лет Мюшетт изготовил новую сталь, получившую название самокалки. Она содержала 2,15 % углерода, 0,38 % марганца, 5,44 % вольфрама и 0,4 % хрома. Через три года на заводе Самуэля Осберна в Шеффилде началось производство мюшеттовой стали. Она не теряла режущей способности при нагревании до 300 °C и позволяла в полтора раза увеличить скорость резания металла — 7,5 м/мин.
Спустя сорок лет на рынке появилась быстрорежущая сталь американских инженеров Тэйлора и Уатта. Резцы из этой стали допускали скорость резания до 18 м/мин. Эта сталь стала прообразом современной быстрорежущей стали Р18.
Ещё через 5—6 лет появилась сверхбыстрорежущая сталь, допускающая скорость резания до 35 м/мин. Так, благодаря вольфраму было достигнуто повышение скорости резания за 50 лет в семь раз и, следовательно, во столько же раз повысилась производительность металлорежущих станков.
Дальнейшее успешное использование вольфрама нашло себе применение в создании твердых сплавов, которые состоят из вольфрама, хрома, кобальта. Были созданы такие сплавы для резцов, как стеллит. Первый стеллит позволял повысить скорость резания до 45 м/мин при температуре 700—750 °C. Сплав вида, выпущенный Круппом в 1927 году, имел твердость по шкале Мооса 9,7—9,9 (твердость алмаза равна 10).
В 1970-х годах в связи с дефицитом вольфрама быстрорежущая сталь марки Р18 была почти повсеместно заменена на сталь марки Р6М5 (так называемый «самокал», самозакаливающаяся сталь), которая, в свою очередь, вытесняется безвольфрамовыми Р0М5Ф1 и Р0М2Ф3.
Характеристики быстрорежущих сталей[ | ]
Горячая твердость[ | ]
При нормальной температуре твердость углеродистой стали даже несколько выше твердости быстрорежущей стали. Однако в процессе работы режущего инструмента происходит интенсивное выделение тепла. При этом до 80 % выделившегося тепла уходит на разогрев инструмента. Вследствие повышения температуры ре
pellete.ru
Сталь рапидная. Большая Энциклопедия Нефти и Газа
Купим быстрорез Р6М5, Р9, Р12, Р18
На выгодных условиях компания ООО "ВеКо" купит лом быстрореза (Р6М6, Р18, Р9Р12). Быстрорез покупаем без остатка, с возможностью вывезти самостоятельно с вашего склада или территории
Быстрорежущие стали(быстрорезы) относят к так называемой группе инструментальных сталей. Быстрорезы предназначены для изготовления режущего инструмента, работающего при высоких скоростях резания. Быстрорежущая сталь должна обладать высоким сопротивлением разрушению, твердостью (в холодном состоянии и горячей) и красностойкостью.
ООО "ВеКо" принимает лом сверел, лом фрез!
Быстрорез купить готов любой пункт приема лома цветных металлов. Это и понятно, ведь в этих сталях содержатся такие элементы как молибден, ванадий, вольфрам и кобальт. Это объясняет и высокую цену стали быстрореза.
Условно марки быстрореза разделяют на две группы - нормальной и повышенной производительности. К первой группе относятся вольфрамовые и вольфрамомолибденовые стали, такие как Р6М5, Р9, Р12, Р18. К стали быстрорезу повышенной производительности относятся марки Р9К5, Р9К10, Р14Ф4, Р10К5Ф5 и др легированные кобальтом или ванадием
Сфера вторичной переработки металлов сейчас активно развивается, играя положительную роль в пополнении сырьевой базы промышленных предприятий, восполняя потребность в металлах и сплавах, в том числе, весьма редких. Часто в интернете можно встретить следующие запросы: "продам быстрорез, сдать быстрорез". Обратившись к нам, вы можете расчитывать начестный прием и высокую цену лома.
Мы принимаем лом Р6М5, Р9, Р12, Р18!
Высоким сопротивлением разрушению и твердостью в холодном состоянии обладают и углеродистые инструментальные стали. Однако инструмент из них не в состоянии обеспечить высокоскоростные режимы резания. Легирование быстрорежущих сталей вольфрамом, молибденом, ванадием и кобальтом обеспечивает горячую твердость и красностойкость стали.Инструмент из быстрорежущей сталей обладает высокой стабильностью свойств.
СМОТРЕТЬ ПРАЙС-ЛИСТ!
Наибольшее распространение получили быстрорежущие стали марок Р6М5, Р9, Р12, Р18
ООО "ВеКо" принимает лом быстрорежущей стали по выгодной цене!
Быстрорезы маркируются в соответствии с ГОСТ 19265. Р в названии марки – быстрорежущая (от англ. слова “Rapid” – быстрый, скорый), цифра, следующая за буквой указывает на среднюю массовую долю вольфрама, М – молибден, Ф – ванадий, К – кобальт, А – азот; цифры, следующие за буквами, означают соответственно массовую долю молибдена, ванадия, кобальта; Ш – электрошлаковый переплав.В обозначении марок стали не указывают массовую долю: хрома – при любой массовой доле, молибдена – до 1 % включительно, ванадия – в стали марок Р18, Р6М5, Р9К5, Р6М5К5, Р9М4К8 и Р2АМ9К5.
Сталь Р6М5
За поледнее время в промышленности быстрорежущая сталь Р6М5 понемногу отодвинула на задний план марки марки стали Р9, Р12 и Р18 в виду своей высокой прочности, ударной вязкости и т
pellete.ru
Быстрорежущая сталь. Ее свойства и классификация
В наше время быстрорежущая сталь продолжает оставаться ведущим материалом для производства разнообразных металлообрабатывающих насадок и режущего инструмента. Такие сплавы часто используются при изготовлении станочных пил, сверл и рабочих головок буров. Несмотря на появившееся сейчас большое разнообразие всевозможных твердосплавных композитных и керамических материалов, обеспечивающих даже большую производительность обработки, быстрорежущие инструментальные стали прочно удерживают свои позиции.
Широкое применение таких сплавов для производства сложнопрофильных режущих инструментов обусловлено сочетанием в них высокого показателя прочности (до 68 HRC) и теплостойкости (они не теряют своих рабочих свойств даже при температуре 650°С) с высоким значением вязкости, значительно превышающим аналогичный показатель для твердосплавных композитных материалов. К тому же быстрорежущая сталь обладает чрезвычайно высокой технологичностью, что подразумевает хорошую обрабатываемость способом давления и резания.
Какие свойства будет иметь такой сплав, зависит от легирующих добавок. Обычно быстрорежущая сталь представляет собой многокомпонентную систему с содержанием хрома, молибдена, вольфрама, кобальта и ванадия. Наличие различных составляющих, а также их содержание в процентном отношении указывается при маркировке. Литера Р здесь означает, что сталь является быстрорежущей, последующая цифра указывает содержание вольфрама в процентах. Дальнейшие буквы обозначают наличие других легирующих элементов, а цифры, идущие вслед за литерами, – их процентную массовую долю в сплаве. Так, буква М означает наличие в системе молибдена, Ф – ванадия, К – кобальта, А – азота.
По содержанию легирующих добавок быстрорежущая сталь может классифицироваться на вольфрамовую, молибденовую, вольфрамо-молибденовую. В особую группу выделяются металлы, легированные кобальтом. Такие сплавы, как правило, применяются при изготовлении инструментов для обработки труднообрабатываемых деталей из жаропрочных сплавов. Быстрорежущая сталь, легированная ванадием главным образом предназначена для производства инструментов так называемой "чистовой" отделки – протяжек, разверток и прочих.
Самая распространенная и, пожалуй, старейшая марка быстрорежущей стали Р18 служит для изготовления сложных и фасонных резьбонарезных инструментов. Средства же стандартной формы для высококачественной обработки металла изготавливаются преимущественно из сплава марки Р9. Из нее делают фрезы, резцы и тому подобное.
По рабочему температурному режиму быстрорежущие стали делятся на три категории: сплавы с нормальной, повышенной и высокой теплостойкостью. К первой группе принадлежат вольфрамовые (Р18, Р9) и вольфрамо-молибденовые (Р6М5). Такие марки применяются при обработке цветных металлов, конструкционных сталей и чугуна.
Для материалов второй категории характерным является чрезвычайно высокое содержание кобальта, углерода и ванадия. Наиболее популярная марка в данной группе - Р6М5Ф3. Ванадиевым сталям свойственна повышенная износостойкость. Единственный их серьезный недостаток – плохая шлифуемость, так как твердость карбидов ванадия не уступает аналогичному показателю электрокорундового шлифовального диска.
И, наконец, стали третьей категории характеризуются невысоким процентом содержания углерода, что делает их пригодными для обработки жаропрочных, нержавеющих и титановых сплавов. Еще одна их характерная отличительная черта – большого число легирующих элементов. К этой группе относятся такие марки, как 3В20К20Х4Ф, В11М7К23 и др.
fb.ru
обработка, марки, изготовление сверл и резцов
Существует огромное количество различных металлов, которые обладают своими определенными достоинствами и недостатками. Быстрорежущие стали зачастую применяются для изготовления инструментов, которые должны обладать повышенной прочностью, некоторых ответственных деталей. Рассмотрим особенности этого сплава подробнее.

Быстрорежущие стали
Характеристики быстрорежущих сталей
Быстрорежущие стали – сплавы, которые имеют достаточно большое количество легированных добавок. За счет добавления различных химических веществ свойства металла серьезно меняются. Рассматривая характеристики следует отметить, что материал подобного типа специально создается для эксплуатации при высоком показателе трения, который возникает на момент резания. Состав быстрорежущей инструментальной стали существенно повышает твердость металла, за счет чего он может работать на повышенной скорости.
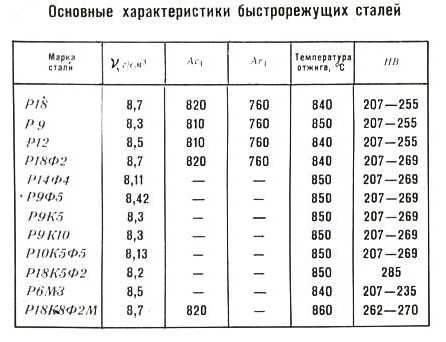
Основные характеристики быстрорежущих сталей
Характеристики быстрорежущей стали следующие:
- Высокая твердость. Рассматривая основное назначение подобного металла следует учитывать, что он может использоваться для обработки деталей или заготовок путем резания. Как показывают проведенные тесты, качественная быстрорежущая сталь сохраняет свои основные эксплуатационные качества при нагреве инструмента даже до температуры 6000 градусов Цельсия. Кроме этого быстрорежущая сталь обычного качества может иметь даже меньшую твердость в сравнении с обычным углеродистым металлом.
- Повышенная стойкость к высокой температуре. Устойчивость к воздействию повышенной температуры определяет то, как долго инструмент сможет работать без изменения своих эксплуатационных качеств. Из-за слишком высокого показателя трения металл может нагреваться, что становится причиной изменения кристаллической решетки. В результате основные свойства быстрорежущей стали могут существенно измениться. Как правило, нагрев становится причиной повышения пластичности и снижения твердости, за счет чего износ поверхности проходит намного быстрее.
- Устойчивость к разрушению. Режущий инструмент, который может работать на высокой скорости, должен обладать повышенной механической устойчивостью. Кроме этого инструмент может работать при высоком показателе подачи, что позволяет работать на большой глубине резания.
Именно химический состав быстрорежущей стали определяет ее основные эксплуатационные качества.
Классификация и маркировка быстрорежущих сталей
Все быстрорежущие стали классифицируются непосредственно по химическому составу, для чего проводится расшифровка маркировки. Инструментальные стали быстрорежущие делятся на следующие три группы:
- Сплавы с полезными примесями, в которых процентное содержание кобальта не более 10%, а вольфрама 22%. Маркировка металла этой группы следующая: P10M4Ф3К10 и Р6М5Ф2К8 и другие.
- Сплавы, в составе которых не более 5% кобальта и до 18% вольфрама. Виды быстрорежущей стали этой группы следующие: Р9К5, Р10Ф5К5 и другие.
- Варианты исполнения металла, расшифровка которых определяет процентное содержание кобальта и вольфрама более 16%. Представителями этой группы можно назвать марки Р9 и Р18, Р12 и Р6М5.
При применении подобного металла получающаяся кромка не реагирует на механическое воздействие, по всей длине показатель твердости остается неизменным и металл не выкрашивается. Вышеприведенная классификация быстрорежущей стали определяет то, при какой скорости резания и подаче может использоваться сплав.
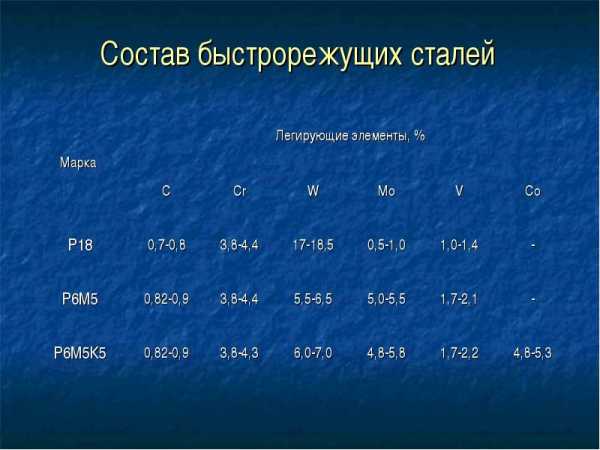
Состав быстрорежущих сталей различных марок
Рассматривая обозначение быстрорежущей стали следует уделить внимание тому, что первая буква для обозначения этой группы «Р». Цифра, которая идет первой в обозначении указывает процесс вольфрама в составе. Далее могут идти буквы, обозначающие легирующие элементы. Стоит учитывать, что расшифровка металла указывает на точное содержание определенных легирующих элементов, которые изменяют эксплуатационные качества материала.
Область применения различных марок быстрорежущих сталей
Рассматривая применение износостойкого металла следует уделить внимание тому, что конкретный состав металла определяет его эксплуатационные качества. Инструмент изготовленный из подобного металла может выдерживать длительную эксплуатацию.
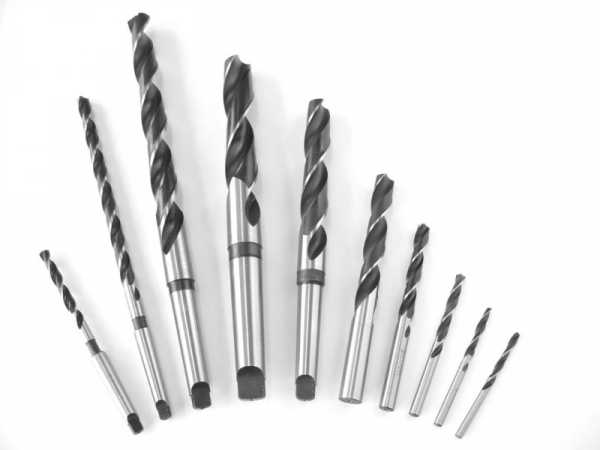
Режущий инструмент из быстрорежущей стали
Область применения достаточно обширна:
- Изготовление сверл. Сверла имеют достаточно сложную форму и конструкцию, которая получается путем литья.
- Изготовление резцов. Сегодня для удешевления резцов их основная часть изготавливается из недорого металла, и только режущая кромка из износостойкого материала.
- Изготовление напаек для режущего инструмента. В некоторые случаях режущая кромка сменная.
- Изготовление фрез. Фрезы также получаются методом литья расплавленного металла.
Материал может использоваться для получения инструмента, который будет выдерживать высокую нагрузку.
Сегодня, при повсеместной установке станков с ЧПУ, режущий инструмент повышенной устойчивости является единственным выходом из сложившейся ситуации, когда высокие скорости обработки создают проблемы.
Особенности термической обработки быстрорежущих сталей
Для увеличения эксплуатационных качеств быстрорежущей стали могут применяться стандартные методы обработки. Однако при этом учитывается состав металла. Примером назовем то, что процесс закалки предусматривает нагрев среды до температуры, которая позволяет обеспечить условия для растворения различных примесей и добавок.
После того, как обработка быстрорежущей стали была завершена, в сплаве остается до 30% аустенита, что существенно повышает теплопроводность и твердость.
Для уменьшения показателя аустенита в структуре могут применяться две технологии:
- Для повышения качества термической обработки нагрев проводится в несколько этапов. При этом выдержка проводится при определенной температуре, а также проводится многократный отпуск.
- Отпуск подразумевает охлаждение заготовки до низкой температуры, которая часто составляет — 800 градусов Цельсия.
- Закалка должна проводится при достаточно высокой температуре, так как только в этом случае происходит полное перестроение кристаллической решетки.
- Для охлаждения используется самая различная среда. Примером назовем применение масла иди соляных ванн. Обычная вода становится причиной появления самых различных дефектов, к примеру, трещин или окалин. После этого приходится выполнять дополнительную обработку для удаления дефектов.
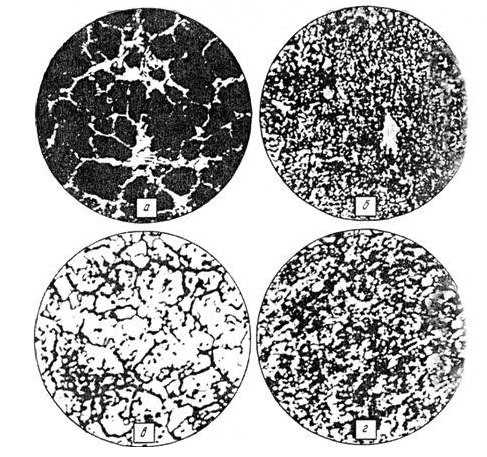
Микроструктура быстрорежущей стали Р6М5: а) литое состояние; б) после ковки и отжига; в) после закалки; г) после отпуска
Кроме этого улучшение характеристик проводится следующим образом:
- Проводится насыщение поверхностного слоя цинком. Для того чтобы оказать требуемое воздействие на поверхность подобная операция предусматривает нагрев поверхности до 5600 градусов Цельсия. Выдержка может проходить в течение от 5 до 30 минут.
- Также может происходить насыщение поверхности азотом. Чаще всего подобная процедура проводится в газовой среде. Выдерживается заготовка или деталь в течении 10-40 минут, температура нагрева варьирует в пределе 550-6600 градусов Цельсия.
- В некоторых случаях химический состав металла изменяется путем сульфидирования поверхности. Подобным образом можно повысить твердость и прочность поверхности.
- В качестве дополнительной обработки на поверхность напыляется различный материал. За счет этого существенно изменяются эксплуатационные качества инструмента или детали.
Сегодня часто встречается ситуация, когда поверхность обрабатывается паром, что позволяет существенно повысить характеристики поверхностного слоя. Зачастую дополнительная обработка проводится в случае, когда режущая кромка была полностью подготовлена.
Если вы нашли ошибку, пожалуйста, выделите фрагмент текста и нажмите Ctrl+Enter.
stankiexpert.ru
Высоколегированная быстрорежущая сталь | Сталь и всё о стали
. Быстрорежущая сталь получила свое название потому, что изготовленный из нее инструмент может применяться для работы с более-высокой скоростью резания, чем инструмент из простой углеродистой стали.
Существует значительное количество марок быстрорежущей стали; в их состав, кроме С и Fe, входят W, Сг, V, иногда Мо, Со и др. Основными легирующими элементами быстрорежущей стали являются Сг и W. Другие присутствующие элементы играют роль добавок, улучшающих свойства стали.
Широко применяемая в практике высококачественная быстрорежущая сталь, марки Р18, имеет следующий основной химический состав: 0,7-¦ 0,8% С; 3,8-4,6% Сг; 17,0-19,0% W; 1,0-1,4% V.
По структуре в , равновесном состоянии эта сталь относится к ледебуритному классу. Подобно белому доэвтектическому чугуну,, структура которого представляет аустенит (распавшийся) и ледебурит, литая быстрорежущая сталь также имеет ледебуритную эвтектику в сочетании с аустенитом или продуктами его распада.
Понятно, однако, что в состав ледебурита быстрорежущей сталш входит не простой цементит, а легированные карбиды; также и аустенит является легированным.
Отлитая в слитки быстрорежущая сталь подвергается обычно ковке на заготовки.
При этом ставится задача нё только придать стали форму в виде заготовок, но также преследуется цель раздробления ледебуритной эвтектики и более равномерного распределения карбидной составляющей в массе металла.
После обработки давлением быстрорежущая сталь с целью снижения твердости обычно подвергается отжигу. Чаще для этой цели применяется изотермический отжиг, состоящий в нагреве стали до 870-880°, последующем медленном охлаждении до 760° и выдержке при этой температуре до полного распада аустенита.
Отожженная быстрорежущая сталь имеет структуру из сорбитной основы в массе которой равномерно расположены мелкие округленные вторичные и несколько более крупные, входившие ранее в состав ледебурита, первичные карбиды
Содержащиеся в стали легирующие элементы распределяют между отдельными фазами примерно следующим образом; около половины хрома растворяется в о-железе (феррите), образующем с эвтектоидными карбидами сорбитную основу. Остальное количество Сг и другие карбидообразующие элементы W и V присутствуют в стали в виде разных карбидов, суммарное количество которых достигает 30-35% веса всего сплава.
Из отожженной быстрорежущей стали изготовляется инструмент, который затем поступает на термическую обработку. Термическая обработка инструмента состоит из закалки с температурой нагрева порядка 1260-1300° и последующего отпуска при 550-600°. Очень высокая температура нагрева при закалке быстрорежущей стали нужна для того, чтобы перевести в твердый раствор (легированный аустенит) возможно большее количество труднорастворимых при нагревании легированных карбидов.
Если закалка быстрорежущей стали будет производиться от более низких температур и, следовательно, карбиды не будут в значительной мере переведены в твердый раствор, то полученный после закалки мартенсит будет иметь недостаточную насыщенность легирующими элементами. По своим свойствам этот мартенсит не будет существенно отличаться от мартенсита низколегированной стали, который, как известно, не обладает достаточной красностойкостью.
С первого взгляда можно предположить, что применение столь высоких температур — нагрева, при закалке быстрорежущей стали должно было бы вызвать значительный перегрев стали и привести ее в совершенно хрупкое состояние. Однако в действительности этого не наблюдается ввиду того, что присутствующие в большом количестве в аустените труднорастворимые карбиды препятствуют росту аустенитного зерна.
Кроме того, выдержка при температуре нагрева под закалку обычно бывает непродолжительной. В качестве охлаждающей среды при закалке быстрорежущей стали обычно применяется масло. Однако быстрорежущая сталь, обладая малой критической скоростью закалки, может закаливаться не только в масле,но даже и на воздухе. Впрочем, как показывает опыт, инструмент, закаленный в масле, имеет несколько лучшие показатели стойкости при работе, чем инструмент, закаленный на воздухе.
Микроструктура закаленной быстрорежущей стали состоит из основной массы мартенсита и остаточного аустенита (около 30%), с большим числом рассеянных в основной массе, первичных (ледебу-ритного происхождения) карбидных зернышек. Твердость закаленной быстрорежущей стали велика и достигает 60-62 Rc. Однако, несмотря на высокую твердость, инструмент из закаленной, но неотпущенной быстрорежущей стали, обладает сравнительно низкой красностойкостью и уже при разогреве до 300-400° быстро затупляется или, как говорят в практике, садится.
Полагают, что понижение твердости в этом интервале температур отпуска связано со снятием возникающих при закалке внутрикристаллических напряжений. Однако прямые доказательства этого отсутствуют, и вопрос о природе процесса остается открытым. Тем не менее, факт .понижения твердости при нагреве закаленной быстрорежущей стали до температур 300-400° легко объясняет причину быстрого затупления закаленного, но не-отпущенного инструмента из быстрорежущей стали при его работе в случае разогрева до 300-400°.
Вместе с тем видно, что быстрорежущая сталь после отпуска при 550° приобретает более высокую, так называемую вторичную, твердость. Ранее полагали, что вторичная твердость вызвана превращением остаточного аустенита в мартенсит в процессе выдержки при отпуске стали.
В настоящее время установлено,что при нагреве в процессе отпуска при 550-600° наблюдается лишь выделение из аустенита дисперсных легированных карбидов, в результате чего степень легирования аустенита понижается, он становится менее устойчивым и при охлаждении до температуры мартенситного превращения и ниже переходит в мартенсит. Выделение из аустенита дисперсных карбидов приводит к повышению температуры Мартенситной точки.
Следовательно, переход остаточного аустенита в мартенсит протекает не при отпуске, как ранее полагали, а при охлаждении после отпуска. Роль отпуска заключается лишь в предварительной подготовке аустенита к превращению за счет уменьшения степени легирования. Однако остаточный аустенит в быстрорежущей стали обладает большой устойчивое! и для его почти полного превращения требуется несколько циклов высокого отпуска при 550-600° с последующим охлаждением после каждого из них.
Этим объясняется, что в практике термической обработки быстрорежущей стали ее обычно подвергают после закалки двух- или трехкратному отпуску при 560-570°.
Таким образом, возникновение вторичной твердости после отпуска быстрорежущей стали при 560° является результатом двух факторов — выделения из остаточного аустенита дисперсных карбидов и последующего превращения обедненного легирующими элементами остаточного аустенита в мартенсит. Последнее и представляет вторичную закалку стали.
Советскими учеными (С. С. Штейнберг, Н. А. Минкевич, А. П. Гуляев) впервые была предложена обработка быстрорежущей стали холодом путем охлаждения закаленной стали до весьма низких температур (ниже мартенситной точки этой стали) порядка от -80 до -100° С (см. § 120). В результате этой обработки достигается более полное превращение остаточного аустенита, и твердость быстрорежущей стали соответственно несколько повышается.
После закалки и двух- или трехкратного отпуска при 560-570° быстрорежущая сталь приобретает высокую твердость 62-65 Rc> большую износоустойчивость, связанную со значительным содержанием в стали твердых легированных карбидов, и способность сохранять твердость при нагревании до температуры ее предшествующего отпуска, т. е. до 570° и даже более — до 600°.
Микроструктура термически обработанной стали (фиг. 200) представляет чрезвычайно мелкоигольчатый («бесструктурный») мартенсит, в массе которого расположено-значительное количество карбидов (в основном первичных) вольфрама и ванадия.
Комплекс свойств быстрорежущей стали — высокая красностойкость, твердость и сопротивление износу- создают ее высокие режущие свойства. Если принять при обработке стали допускаемую скорость резания инструмента из углеродистой стали за единицу, то допускаемая скорость резания инструмента из быстрорежущей стали будет в 3-4 раза выше.
Следует заметить, что термическая обработка быстрорежущей стали должна производиться со значительными предосторожностями. Быстрорежущая сталь весьма мало теплопроводна.
Поэтому, во избежание возникновения трещин, нагревание для закалки должно осуществляться (по крайней мере, до температур 750-850°) медленно. В практике термической обработки обычно производится ступенчатый нагрев быстрорежущей стали. Первоначально быстрорежущую сталь медленно подогревают до 750-850°, затем переносят в другую печь, где и осуществляется нагрев до закалочных температур.
Весьма часто второй нагрев ведется в соляных ваннах, применение которых позволяете большой точностью выдержать заданный температурный режим, а также избегать опасного для всех видов инструментальной стали обезуглероживания стали с поверхности.
Для повышения твердости режущей кромки инструмента и уничтожения обезуглероживания слоя иногда термически обработанный инструмент из быстрорежущей стали подвергают низкотемпературному цианированию.
Наряду с высоколегированной вольфрамом быстрорежущей сталью типа рассмотренной выше марки Р18, в практике широко используются марки быстрорежущей стали менее легированные вольфрамом.
В отечественной промышленности распространение получила предложенная М. В. Приданцевым малолегированная марка быстрорежущей стали Р9 состава: С = 0,85-0,95%; Сг = 3,8-4,4%; W= 8,5-10,0%; V= 2,0-2,6%. Эта сталь имеет почти одинаковые режущие свойства с нормальной быстрорежущей сталью Р18, если твердость обрабатываемого материала не превышает 250-280 единиц по Бринелю.
Однако в случае обработки более твердого металла сталь Р9 несколько уступает Р18.
www.inmetal.ru
Быстрорежущая сталь Википедия
Быстроре́жущие ста́ли — легированные стали, предназначенные, главным образом, для изготовления металлорежущего инструмента, работающего при высоких скоростях резания.
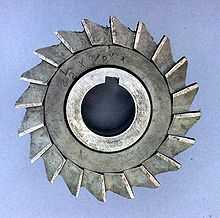
Быстрорежущая сталь должна обладать высокими сопротивлением разрушению, твёрдостью (в холодном и горячем состояниях) и красностойкостью.
Высокими сопротивлением разрушению и твердостью в холодном состоянии обладают и углеродистые инструментальные стали. Однако инструмент из них не в состоянии обеспечить высокоскоростные режимы резания. Легирование быстрорежущих сталей вольфрамом, молибденом, ванадием и кобальтом обеспечивает горячую твердость и красностойкость стали.
Истории создания
Сверло с покрытием из нитрида титанаДля обточки деталей из дерева, цветных металлов, мягкой стали резцы из обычной твердой стали были вполне пригодны, но при обработке стальных деталей резец быстро разогревался, скоро изнашивался и деталь нельзя было обтачивать со скоростью больше 5 м/мин[1].
Барьер этот удалось преодолеть после того, как в 1858 году Р. Мюшетт получил сталь, содержащую 1,85 % углерода, 9 % вольфрама и 2,5 % марганца. Спустя десять лет Мюшетт изготовил новую сталь, получившую название самокалки. Она содержала 2,15 % углерода, 0,38 % марганца, 5,44 % вольфрама и 0,4 % хрома. Через три года на заводе Самуэля Осберна в Шеффилде началось производство мюшеттовой стали. Она не теряла режущей способности при нагревании до 300 °C и позволяла в полтора раза увеличить скорость резания металла — 7,5 м/мин.
Спустя сорок лет на рынке появилась быстрорежущая сталь американских инженеров Тэйлора и Уатта. Резцы из этой стали допускали скорость резания до 18 м/мин. Эта сталь стала прообразом современной быстрорежущей стали Р18.
Ещё через 5—6 лет появилась сверхбыстрорежущая сталь, допускающая скорость резания до 35 м/мин. Так, благодаря вольфраму было достигнуто повышение скорости резания за 50 лет в семь раз и, следовательно, во столько же раз повысилась производительность металлорежущих станков.
Дальнейшее успешное использование вольфрама нашло себе применение в создании твердых сплавов, которые состоят из вольфрама, хрома, кобальта. Были созданы такие сплавы для резцов, как стеллит. Первый стеллит позволял повысить скорость резания до 45 м/мин при температуре 700—750 °C. Сплав вида, выпущенный Круппом в 1927 году, имел твердость по шкале Мооса 9,7—9,9 (твердость алмаза равна 10).
В 1970-х годах в связи с дефицитом вольфрама быстрорежущая сталь марки Р18 была почти повсеместно заменена на сталь марки Р6М5 (так называемый «самокал», самозакаливающаяся сталь), которая, в свою очередь, вытесняется безвольфрамовыми Р0М5Ф1 и Р0М2Ф3.
Характеристики быстрорежущих сталей
Горячая твердость
При нормальной температуре твердость углеродистой стали даже несколько выше твердости быстрорежущей стали. Однако в процессе работы режущего инструмента происходит интенсивное выделение тепла. При этом до 80 % выделившегося тепла уходит на разогрев инструмента. Вследствие повышения температуры режущей кромки начинается отпуск материала инструмента и снижается его твердость.
После нагрева до 200 °C твердость углеродистой стали начинает быстро падать. Для этой стали недопустим режим резания, при котором инструмент нагревался бы выше 200 °C. У быстрорежущей стали высокая твердость сохраняется при нагреве до 500—600 °C. Инструмент из быстрорежущей стали более производителен, чем инструмент из углеродистой стали.
Красностойкость
Если горячая твердость характеризует то, какую температуру сталь может выдержать, то красностойкость характеризует, сколько времени сталь будет выдерживать такую температуру. То есть насколько длительное время закаленная и отпущенная сталь будет сопротивляться разупрочнению при разогреве.
Существует несколько характеристик красностойкости. Приведем две из них.
Первая характеристика показывает, какую твердость будет иметь сталь после отпуска при определенной температуре в течение заданного времени.
Второй способ охарактеризовать красностойкость основан на том, что интенсивность снижения горячей твердости можно измерить не только при высокой температуре, но и при комнатной, так как кривые снижения твердости при высокой температуре и комнатной идут эквидистантно, а измерить твердость при комнатной температуре, разумеется, гораздо проще, чем при высокой. Опытами установлено, что режущие свойства теряются при твердости 50 HRC при температуре резания, что соответствует примерно 58 HRC при комнатной. Отсюда красностойкость характеризуется температурой отпуска, при которой за 4 часа твердость снижается до 58 HRC (обозначение K4р58).
У7, У8, У10, У12 | 150—160 | 1 | 63 |
Р9 | 580 | 4 | |
У7, У8, У10, У12 | 200—220 | 1 | 59 |
Р6М5К5, Р9, Р9М4К8, Р18 | 620—630 | 4 |
Сопротивление разрушению
Кроме «горячих» свойств, от материала для режущего инструмента требуются и высокие механические свойства; под этим подразумевается сопротивление хрупкому разрушению, так как при высокой твердости (более 60 HRC) разрушение всегда происходит по хрупкому механизму. Прочность таких высокотвердых материалов обычно определяют как сопротивление разрушению при изгибе призматических, не надрезанных образцов, при статическом (медленном) и динамическом (быстром) нагружении. Чем выше прочность, тем большее усилие может выдержать рабочая часть инструмента, тем большую подачу и глубину резания можно применить, и это увеличивает производительность процесса резания.
Химический состав быстрорежущих сталей
Р0М2Ф3 | 1,10—1,25 | 3,8—4,6 | — | 2,3—2,9 | 2,6—3,3 | — |
Р6М5 | 0,82—0,90 | 3,8—4,4 | 5,5—6,5 | 4,8—5,3 | 1,7—2,1 | < 0,50 |
Р6М5Ф2К8 | 0,95—1,05 | 3,8—4,4 | 5,5—6,6 | 4,6—5,2 | 1,8—2,4 | 7,5—8,5 |
Р9 | 0,85—0,95 | 3,8—4,4 | 8,5—10,0 | < 1,0 | 2,0—2,6 | — |
Р18 | 0,73—0,83 | 3,8—4,4 | 17,0—18,5 | < 1,0 | 1,0—1,4 | < 0,50 |
Изготовление и обработка быстрорежущих сталей
Быстрорежущие стали изготавливают как классическим способом (разливка стали в слитки, прокатка и проковка), так и методами порошковой металлургии (распыление струи жидкой стали азотом)[3]. Качество быстрорежущей стали в значительной степени определяется степенью её прокованности. При недостаточной проковке изготовленной классическим способом стали наблюдается карбидная ликвация.
При изготовлении быстрорежущих сталей распространенной ошибкой является подход к ней как к «самозакаливающейся стали». То есть достаточно нагреть сталь и охладить на воздухе, и можно получить твердый износостойкий материал. Такой подход абсолютно не учитывает особенности высоколегированных инструментальных сталей.
Перед закалкой быстрорежущие стали необходимо подвергнуть отжигу. В плохо отожженных сталях наблюдается особый вид брака: нафталиновый излом, когда при нормальной твердости стали она обладает повышенной хрупкостью.
Грамотный выбор температуры закалки обеспечивает максимальную растворимость легирующих добавок в α-железе, но не приводит к росту зерна.
После закалки в стали остается 25—30 % остаточного аустенита. Помимо снижения твердости инструмента, остаточный аустенит приводит к снижению теплопроводности стали, что для условий работы с интенсивным нагревом режущей кромки является крайне нежелательным. Снижения количества остаточного аустенита добиваются двумя путями: обработкой стали холодом или многократным отпуском[3]. При обработке стали холодом её охлаждают до −80…−70 °C, затем проводят отпуск. При многократном отпуске цикл «нагрев — выдержка — охлаждение» проводят по 2—3 раза. В обоих случаях добиваются существенного снижения количества остаточного аустенита, однако полностью избавиться от него не получается.
Принципы легирования быстрорежущих сталей
Высокая твердость мартенсита объясняется растворением углерода в α-железе. Известно, что при отпуске из мартенсита в углеродистой стали выделяются мельчайшие частицы карбида. Пока выделившиеся карбиды ещё находятся в мельчайшем дисперсном рассеянии (то есть на первой стадии выделения при отпуске до 200 °C), твердость заметно не снижается. Но если температуру отпуска поднять выше 200 °C, происходит рост карбидных выделений, и твердость падает.
Чтобы сталь устойчиво сохраняла твердость при нагреве, нужно её легировать такими элементами, которые затрудняли бы процесс коагуляции карбидов. Если ввести в сталь какой-нибудь карбидообразующий элемент в таком количестве, что он образует специальный карбид, то красностойкость скачкообразно возрастает. Это обусловлено тем, что специальный карбид выделяется из мартенсита и коагулирует при более высоких температурах, чем карбид железа, так как для этого требуется не только диффузия углерода, но и диффузия легирующих элементов. Практически заметная коагуляция специальных карбидов хрома, вольфрама, молибдена, ванадия происходит при температурах выше 500 °C.
Красностойкость создается легированием стали карбидообразующими элементами (вольфрамом, молибденом, хромом, ванадием) в таком количестве, при котором они связывают почти весь углерод в специальные карбиды, и эти карбиды переходят в раствор при закалке. Несмотря на сильное различие в общем химическом составе, состав твердого раствора очень близок во всех сталях, атомная сумма W+Mo+V, определяющая красностойкость, равна примерно 4 % (атомн.), отсюда красностойкости и режущие свойства у разных марок быстрорежущих сталей близки. Быстрорежущая сталь, содержащая кобальт, превосходит по режущим свойствам остальные стали (он повышает красностойкость), но кобальт очень дорогой элемент.
Маркировка быстрорежущих сталей
В советских и российских марочниках сталей марки быстрорежущих сталей обычно имеют особую систему обозначений и начинаются с буквы «Р» (rapid — быстрый). Связано это с тем, что эти стали были изобретены в Англии, где такую сталь называли «rapid steel». Цифра после буквы «Р» обозначает среднее содержание в ней вольфрама (в процентах от общей массы, буква В пропускается). Затем указывается после букв М, Ф и К содержание молибдена, ванадия и кобальта. Инструменты из быстрорежущей стали иностранного производства обычно маркируются аббревиатурой HSS (High Speed Steel).
Применение
В последние десятилетия использование быстрорежущей стали сокращается в связи с широким распространением твёрдых сплавов. Из быстрорежущей стали изготавливают в основном концевой инструмент (метчики, свёрла, фрезы небольших диаметров) В токарной обработке резцы со сменными и напайными твердосплавными пластинами почти полностью вытеснили резцы из быстрорежущей стали.
По применению отечественных марок быстрорежущих сталей существуют следующие рекомендации.
- Сталь Р9 рекомендуют для изготовления инструментов простой формы, не требующих большого объёма шлифовки, для обработки обычных конструкционных материалов. (резцов, фрез, зенкеров).
- Для фасонных и сложных инструментов (для нарезания резьб и зубьев), для которых основным требованием является высокая износостойкость, рекомендуют использовать сталь Р18 (вольфрамовая).
- Кобальтовые быстрорежущие стали (Р9К5, Р9К10) применяют для обработки деталей из труднообрабатываемых коррозионно-стойких и жаропрочных сталей и сплавов, в условиях прерывистого резания, вибраций, недостаточного охлаждения.
- Ванадиевые быстрорежущие стали (Р9Ф5, Р14Ф4) рекомендуют для изготовления инструментов для чистовой обработки (протяжки, развёртки, шеверы). Их можно применять для обработки труднообрабатываемых материалов при срезании стружек небольшого поперечного сечения.
- Вольфрамомолибденовые стали (Р9М4, Р6М3) используют для инструментов, работающих в условиях черновой обработки, а также для изготовления протяжек, долбяков, шеверов, фрез.
Примечания
- ↑ Мезенин Н. А. Занимательно о железе. — М.: «Металлургия», 1972. — 200 с.
- ↑ Марочник сталей и сплавов / В. Г. Сорокин, А. В. Волосникова, С. А. Вяткин, и др. Под общ. ред. В. Г. Сорокина. — М.: Машиностроение, 1989. — 640 с.
- ↑ 1 2 Гуляев А. П. Металловедение. Учебник для втузов. 6-е изд., перераб. и доп. — М.: «Металлургия», 1986. — 544 с.
Литература
- Технология конструкционных материалов. Под ред. А. М. Дальского. — М.: «Машиностроение», 1958.
Ссылки
wikiredia.ru