Рентгенографический контроль сварных соединений. Рентгеновский контроль качества
Рентгенографический РГК контроль качества
РГК контроль
ГОСТ_7512-82
Радиографический контроль применяют для выявления в сварных соединениях трещин, непроваров, пор, шлаковых, вольфромовых, окисных и других включений. Радиографический контроль применяют также для выявления прожогов, подрезов, оценки величины выпуклости и вогнутости корня шва, недоступных для внешнего осмотра.
Проведение дефектоскопии с применением рентгеновского просвечивания металла наиболее достоверный способ контроля сварных соединений и основного металла Данный вид контроля широко используется для проверки качества технологических трубопроводов, металлоконструкций, технологического оборудования, композитных материалов в различных отраслях промышленности и строительного комплекса. Рентген контроль сегодня активно используется для выявления различных дефектов в сварных швах и соединениях. Радиографический метод контроля сварных соединений (или рентгеновская дефектоскопия) осуществляется в соответствии с требованиями ГОСТ 7512-86.
Рентгеновский контроль основан на поглощении рентгеновских лучей, которое зависит от плотности среды и атомного номера элементов, образующих материал среды. Наличие таких дефектов, как трещины, раковины или включения инородного материала, приводит к тому, что проходящие через материал лучи ослабляются в различной степени. Регистрируя распределение интенсивности проходящих лучей, можно определить наличие и расположение различных неоднородностей материала. Рентгеновский контроль применяют для определения раковин, грубых трещин, ликвационных включений в литых и сварных стальных изделиях толщиной свыше 90 мм и в изделиях из лёгких сплавов толщиной до 250 мм. Для этого используют промышленные рентгеновские установки с энергией излучения от 5-10 до 200-400 кэв (1 эв = 1,60210 Ї 10-19 дж). Изделия большой толщины (до 500 мм) просвечивают сверх жёстким электромагнитным излучением с энергией в десятки Мэв, получаемым в бетатроне.
Основные возможности рентгеновского контроля:- Возможность обнаружить такие дефекты, которые невозможно выявить любым другим методом - например, непропаев, раковин и других;- Возможность точной локализации обнаруженных дефектов, что дает возможность быстрого ремонта;- Возможность оценки величины выпуклости и вогнутости валиков усиления сварного шва.
Данный метод позволяет контролировать металлы, сплавы, минералы, неорганические и органические соединения, полимеры, аморфные вещества.
Максимально полное покрытие всевозможных технологических дефектов.
отсутствие контактного приспособления
Ренгенографический метод контроля эффективен только в том случае, если выбраны оптимальные режимы контроля: определены геометрические параметры контроля, размер фокусного пятна трубки, фокусное расстояние, расстояние от контролируемого объекта до преобразователя излучения, напряжение и ток рентгеновской трубкиГрамотно выполненный РК контроль – чрезвычайно эффективный метод выявления дефектов!
Наша лаборатория качественно выполнит радиографическую дефектоскопию, а именно рентгенографический контроль сварных швов и основного металла, трубопроводов, емкостей, сосудов и металлоконструкций различного назначения. Наши специалисты правильно подберут устройства преобразования и усиления рентгеновского изображения, а также источник излучения, разработают схему просвечивания объекта.
Рентгенографический контроль (или РГК контроль) представляет собой один из наиболее часто использующихся в настоящее время способов контроля качества. А все потому, что РГК максимально надежен, эффективее и точен. Сфера, в которой рентгенографический контроль качества находит применения, достаточно широка. Но чаще всего данная методика используется для проверки разного рода металлоконструкций, технологических трубопроводов и т.д. Используется РГК контроль и для определения непроварок, подрезов, прожогов, выявления незаметных человеческому глазу трещин в сварных соединениях и т.д.
Основным преимуществом данного метода контроля качества является в достаточной степени невысокая стоимость, оперативность, а так же, что немаловажно, высокая степень простоты проводимого исследования.Персонал, который принимает участие в проведении такого исследования, как рентгенографический контроль качества, в обязательном порядке должны быть специально обучены и аттестованы в соответствии с действующими требованиями. Сотрудники, не прошедшие аттестацию и обучение к выполнению данных работ не допускаются, поскольку РГК контроль предполагает наличие высокого уровня профессионализма.
Как правило, рентгенографический контроль качества изделий осуществляется непосредственно на производстве. Но если речь идет не о крупном предприятии, то услуги проведения рентгенографического контроля могут быть заказаны и в сторонней организации, которая обладает соответствующей лицензией. Поскольку данная услуга в настоящее время востребована достаточно высоко, нет совершенно ничего удивительного в том,что ее предлагает достаточно большое количество различных компаний. Но несмотря на то, что на первый взгляд может показаться, что выбор специалистов для поведения РГК контроля очень велик, обращаться лучше к проверенным специалистам, которые работают в соответствующем секторе рынка достаточно длительный период времени и способный выявить любой, даже самый мелкий дефект.
Рентгеновский контроль (рентгенографический контроль) осуществляется в соответствии со следующими нормативными документами:
ГОСТ 25113-86. Контроль неразрушающий. Аппараты рентгеновские для промышленной дефектоскопии. Общиетехническиеусловия. (Non-destructive testing x-ray apparatus for industrial flaw detection. General specifications)
ГОСТ 20426-82. Контроль неразрушающий. Методы дефектоскопии радиационные. Область применения.
ГОСТ 23055-78. Контроль неразрушающий. Сварка металлов плавлением. Классификация сварных соединений по результатам радиографического контроля.
ГОСТ 24034-80. Контроль неразрушающий радиационный. Термины и определения.
ГОСТ 7512-82. Контроль неразрушающий. Соединения сварные. Радиографический метод.
ГОСТ 15843-79 (1980). Принадлежности для промышленной радиографии. Основные размеры.
ГОСТ 17489-72 (1999). Видиконы рентгеновские. Основные параметры и размеры.
ГОСТ 18061-90. Толщиномеры радиоизотопные. Общие технические условия (взамен ГОСТ 18061-80; ГОСТ 18701-83; ГОСТ 22555-77; ГОСТ 22556-77; ГОСТ 22987-78).
ГОСТ 20426-82. Контроль неразрушающий. Методы дефектоскопии радиационные. Область применения.
ГОСТ 21497-90. Уровнемеры радиоизотопные. Общие технические условия.
ГОСТ 22091.0-84. Приборы рентгеновские. Общие требования к измерению параметров.
ГОСТ 22091.10-84. Приборы рентгеновские. Метод измерения алюминиевого или медного эквивалента баллона рентгеновского прибора.
ГОСТ 22091.11-80 (1999). Приборы рентгеновские. Метод измерения времени готовности.
ГОСТ 22091.12-84. Приборы рентгеновские. Методы измерения токов и напряжений электродов в импульсе.
ГОСТ 22091.13-84. Приборы рентгеновские. Метод измерения междуэлектродной емкости сетка-катод.
ГОСТ 22091.14-86. Приборы рентгеновские. Метод измерения плотности потока энергии (плотности потока фотонов) рентгеновского излучения.
ГОСТ 22091.15-86. Приборы рентгеновские. Метод испытания на электрическую прочность.
ГОСТ 22091.1-84. Приборы рентгеновские. Методы измерения тока и напряжения накала.
ГОСТ 22091.2-84. Приборы рентгеновские. Методы измерения тока и напряжения инжекции рентгеновских бетатронных камер.
ГОСТ 22091.3-84. Приборы рентгеновские. Методы измерения размера поля облучения и угла раствора рабочего пучка рентгеновского излучения.
ГОСТ 22091.4-86. Приборы рентгеновские. Методы измерения напряжения рентгеновской трубки.
ГОСТ 22091.5-86. Приборы рентгеновские. Методы измерения тока рентгеновской трубки.
ГОСТ 22091.6-84. Приборы рентгеновские. Методы измерения мощности экспозиционной дозы рентгеновского излучения и экспозиционной дозы рентгеновского излучения за импульс.
ГОСТ 22091.7-84. Приборы рентгеновские. Методы измерения равномерности распределения плотности потока энергии рентгеновского излучения по полю облучения.
ГОСТ 22091.8-84. Приборы рентгеновские. Метод измерения спектрального состава и относительной загрязненности спектра.
ГОСТ 22091.9-86. Приборы рентгеновские. Методы измерения размеров эффективного фокусного пятна.
ГОСТ 23055-78 (1992). Контроль неразрушающий. Сварка металлов плавлением. Классификация сварных соединений по результатам радиографического контроля
ГОСТ 23480-79. Контроль неразрушающий. Методы радиоволнового вида. Общие требования.
ГОСТ 23764-79. Гамма-дефектоскопы. Общие технические условия.
ГОСТ 25113-86. Контроль неразрушающий. Аппараты рентгеновские для промышленной дефектоскопии. Общие технические условия.
ГОСТ 25932-83. Влагомеры-плотномеры радиоизотопные переносные для бетонов и грунтов. Общие технические условия.
ГОСТ 27947-88. Контроль неразрушающий. Рентгенотелевизионный метод. Общие требования.
ГОСТ 28277-89. Контроль неразрушающий. Соединения сварные. Электрорадиографический метод. Общие требования.
ГОСТ 29025-91. Контроль неразрушающий. Дефектоскопы рентгенотелевизионные с рентгеновскими электронно-оптическими преобразователями и электрорентгенографические. Общие технические требования.
ГОСТ 4.198-85. Система показателей качества продукции. Аппараты рентгеновские аналитические. Номенклатура показателей.
ГОСТ 8.452-82. Государственная система обеспечения единства измерений. Приборы рентгенорадиометрические. Методы и средства поверки.
МИ 2453-2000. ГСИ. Методики радиационного контроля. Общие требования.
МУК 2.6.1.1087-02. Радиационный контроль металлолома.
МУК 2.6.1.2152-06. Радиационный контроль металлолома. Дополнение № 1 к МУК 2.6.1.1087-02.
ОСТ 36-59-81. Контроль неразрушающий. Сварные соединения трубопроводов и конструкций. Радиографический метод.
РД 07-10-2001. Методические указания по осуществлению надзора за обеспечением радиационной безопасности при эксплуатации приборов неразрушающего контроля, содержащих радиоактивные вещества (гамма-дефектоскопов).
РД 34.17.301. Ведомственная инструкция по радиографическому контролю сварных соединений металлоконструкций, трубных систем котлов и трубопроводов при изготовлении, монтаже и ремонте оборудования тепловых электростанций. 1980.
РД РОСЭК-01-002-96. Машины грузоподъемные. Конструкции металлические. Контроль радиационный. Основные положения.
СП 2.6.1.1283-03. Обеспечение радиационной безопасности при рентгеновской дефектоскопии (взамен СП 2191-80).
СП 2.6.1.1284-03. Обеспечение радиационной безопасности при радионуклидной дефектоскопии (взамен СП 1171-74).
izmerenie.pro
Рентгенографический контроль сварных соединений трубопроводов
Во время соединения металлических деталей с помощью сварки может возникнуть ситуация, которая затруднит образование нормального однородного шва. Когда в сварочную ванну попадают посторонние предметы или элементы, а также выбран неправильный режим сваривания, то вполне возможно образование брака. Это приводит к тому, что шов будет иметь более низкое качество и сможет выдержать меньшее количество нагрузок, чем предполагалось. Далеко не все виды дефектов можно увидеть сразу, так как зачастую они имеют скрытый характер. В особенности это относится к мелким трещинам и порам. Требования к сварным соединениям здесь могут быть очень высокими, так что любой недочет может привести к серьезным последствиям.
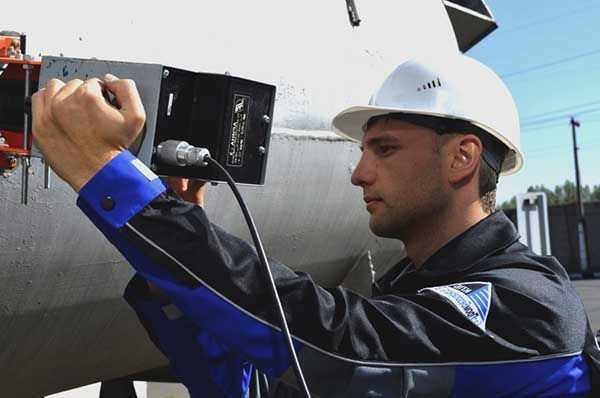
Рентгенографический контроль сварных соединений
Рентгенографический метод контроля сварных соединений это один из самых достоверных способов. Данный метод особенно популярен при проверке соединений технологических трубопроводов, различного ответственного оборудования, металлических конструкций и прочих материалов, применяющихся в самых разнообразных отраслях. Чаще всего высокие нагрузки встречаются в строительстве. Рентген контроль сварных соединений проводится по ГОСТ 7512-86.
Данный принцип основан на поглощении лучей плотными средами. Чем более плотная структура, тем меньше лучей пройдет наружу. Если внутри шва есть трещины, раковины, поры и прочие полые дефекты, то количество прохождения лучей здесь будет значительно большим. Регистрирующее устройство сможет выявить наличие дефекта, его размер, место расположения и другие особенности. Такими качествами не обладает ни один другой метод. Рентгеновский контроль сварных соединений является детальным показателем состояния локальных участков металлоконструкций
Свойства рентгеновских лучей
Лучи могут проходить через плотные непрозрачные тела, но чем выше плотность этих тел, тем ниже пропускание лучей. Проходимость зависит и от длины лучей. При большой длине им сложнее пройти сквозь плотные поверхности. Во время прохождения лучи поглощаются той поверхностью, с которой соприкасаются. Чем выше плотность, тем больше поглощение.
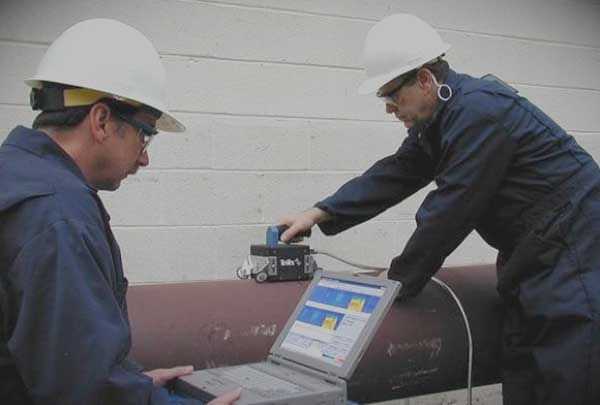
Принцип рентгенографическогой контроля сварных швов
Некоторые химические вещества при контакте с излучением получают видимое свечение. После окончания воздействия свечение прекращается, но некоторые вещества сохраняют заряд свечения еще на некоторое время. Это свойство является основой для создания рентгеновских снимков в данном методе. Воздействие лучей на светочувствительную часть фотопластинок создает изображение внутреннего состояния шва.
При воздействии лучей на клетки организма они производят определенные воздействия, которые зависят от типа ткани и интенсивности полученной дозы. Это может использоваться в медицине, но также имеет и обратный эффект, который проявляется в лучевой болезни.
Лучи могут ионизировать воздух, расщепляя составные части воздушной массы на отдельные частицы, имеющие электрический заряд. Из-за этого воздух может проводить электричество.
Преимущества
- Рентгенографический контроль сварных соединений трубопроводов является одним из самых точных и надежных методов дефектоскопии;
- Можно увидеть скрытые дефекты;
- Возможно определение абсолютных и относительных размеров бракованного места;
- Скорость проведения процедур достаточно высокая.
Недостатки
- Эффективность метода зависит от правильности установки параметров;
- Оборудование для его проведения имеет высокую стоимость;
- Здесь нужно использовать особую пленку для фиксации результата;
- Это опасный для здоровья метод дефектоскопии сварных швов.
Устройство и принцип работы оборудования
Излучающий элемент представлен в виде вакуумного сосуда, в котором находится три электрода: анод, накал катода и катод. Сами рентгеновские лучи возникают тога, когда заряженные частицы получают сильное ускорение. Это может случиться и при высокоэнергетическом переходе, что происходит в оболочке атомов. Рентгенографические трубки используют оба этих варианта. Основным конструктивным элементом устройства выступает анод и катод.
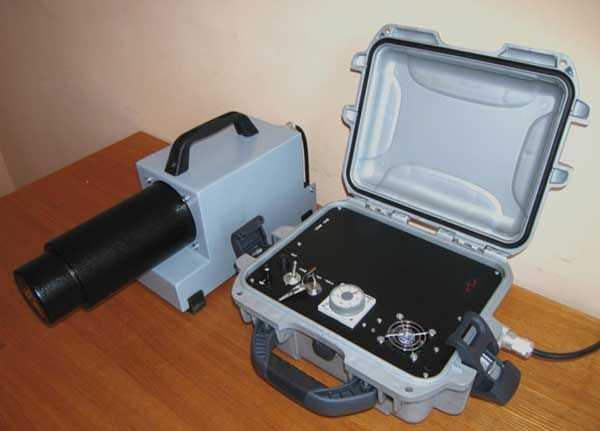
Устройство для рентгенографическогой контроля сварных соединений
Электроны, которые испускаются катодом получают ускорение от различных электрических потенциалов, находящихся в области между анодом и катодом. В это время рентгеновские лучи еще не испускаются, по причине малого своего количества. Они ударяются об анод, после чего происходит их резкое торможение. За счет этого происходит генерация лучей в рентгеновском диапазоне. В это же время из внутренних оболочек атомов анода выбиваются электроны. На места выбитых частиц становятся другие электроны. Выпускаемое излучение приобретает характерные черты, которыми обладает материал анода.
Когда лучи уже вышли, то они передвигаются в соответствии с заданным направлением сквозь выбранный участок шва. Затем они сталкиваются с плотной поверхностью и часть остается в металле. Остальные частицы, которым удалось прорваться, попадают на пленку. Там отображается интенсивность излучения в каждом отдельном месте. При наличии пустых мест в структуре наплавленного металла, количество лучей становится большим. Таким образом можно выявить где находится тот или иной дефект, а также какой он формы и размера.
Методика проведения контроля
Методика проведения рентгенографического контроля сварных соединений очень схожа с радиографическим контролем. Первым делом происходит настройка аппаратуры под определенную плотность металла, чтобы излучение смогло пройти сквозь его поверхность. Затем происходит подготовка сделанного шва к контролю. Для этого с него оббивают шлак, обрабатывают до требуемой высоты валика и зачищают саму поверхность.
После этого изделие перемещается в аппарат на то место, где будет происходить выпуск лучей. Оно должно находиться между излучателей и фотопленкой. Затем включается аппарат и лучи моментально проникают сквозь сварной шов, попадая в итоге на пленку. На ней отображаются все неровности интенсивности, которые показывают наличие дефектов.
«Важно!
Данный процесс может оказать вред здоровью, так что необходимо соблюдать все правила техники безопасности.»
Меры по технике безопасности
Чтобы сохранить свое здоровье при частом проведении подобных процедур, следует придерживаться ряда предписанных требований. В первую очередь, устройство должно быть экранировано, чтобы излучение не распространялось по всему помещению, а действовало только в строго направленное место. Для экранирования зачастую используют металлические пластины. Они же могут пригодиться для обустройства стен помещения, которые также должны быть ограждением для распространения излучения.
Во время работы следует держаться как можно дальше от излучателя, насколько это возможно. Также стоит уменьшить время пребывания в помещении во время работы техники. В данном месте не должно быть ни каких посторонних людей. Все работники должны иметь средства индивидуальной защиты.
Все работы должны проводиться только при условии, что техника исправна и правильно настроена. Стоит понимать, что минимальной дозы излучения сложно избежать, но она со временем накапливается, если процедуры проводятся часто и это может вызвать серьезные осложнения, перерастающие в хроническую профессиональную болезнь. Исходя из этого, необходимо следить за тем, какую дозу человек получает за один проход действия аппарата. Для этого используются специальные дозиметры. Также нужно обратить внимание на ионизацию воздуха в помещении, так как при сильно высоком ее уровне может случиться электрический разряд, потому что воздушная масса перестанет быть диэлектриком.
svarkaipayka.ru
Рентгенографический контроль сварных швов и соединений
Являясь фактически одной из разновидностей радиографического контроля, этот метод не требует применения используемых в гамма-дефектоскопах радиоактивных изотопов. Источником излучения в этом случае являются рентгеновские лампы. Генерируемые лампой лучи проходят через обследуемый участок детали. При этом они интенсивнее поглощаются однородным металлом, а при прохождении сквозь пустоты, трещины или просто рыхлый металл, интенсивность поглощения снижается. Основываясь на этом эффекте, на различных светочувствительных материалах – бумаге, плёнке, пластиковых или стеклянных пластинах, получают изображение, где места дефекта выглядят более светлыми. Это позволяет зафиксировать результаты обследования документально. Если же применить специальный преобразователь излучения, то результаты дефектоскопии можно вывести на экран и, по полученному изображению, исследовать в реальном времени.
Возможности технологии
Используя рентгеновский контроль, удаётся с высокой степенью точности выявить:
- Плохо проваренные места соединительных швов.
- Трещины и каверны, причём даже те, которые находятся под поверхностью детали и не обнаруживаются другими методами дефектоскопии.
- Включения инородных материалов – шлаков, окислов и т. п.
Также появляется возможность оценить вогнутость и выпуклость корня сварного шва.
Впрочем, с помощью прогрессивной технологии контроля удаётся обследовать не только детали, изготовленные из металла. Изменение интенсивности рентгеновского излучения регистрируется при его прохождении через минералы и полимеры, органические и неорганические вещества. Таким образом, значительно расширяется область применения рентгенографического контроля.
Достоинства и недостатки
Любым технологиям присущи как достоинства, так и недостатки. Именно они влияют на их развитие в первую очередь. Оценивая метод дефектоскопии, использующий рентгеновское излучение, к его достоинствам можно отнести:
- Высокую точность получаемых данных. По этому параметру соперничать с рентгенографией очень трудно. Ведь с её помощью удаётся обнаружить не только дефекты микроскопического размера, но также определить форму и характер повреждения.
- Возможность выявления скрытых дефектов, вне зависимости от глубины их расположения. При использовании большинства других способов контроля такая задача невыполнима.
- Достаточно высокая скорость получения результатов, благодаря которой становится возможным использование технологии в массовом производстве и при изучении сварных швов большой суммарной протяжённости.
Что касается основных недостатков, то ими принято считать:
- Значительную стоимость оборудования и сложность его обслуживания.
- Опасность для здоровья, которую может представлять метод рентгеновского контроля при нарушении норм безопасности и неграмотном его использовании.
- Необходимость в специальных расходных материалах для фиксации результатов.
- Наличие способного работать на сложном оборудовании квалифицированного персонала, поскольку эффективность метода напрямую зависит от правильности его применения.
- Влияние заданных параметров регулировки измерительной аппаратуры на точность результатов.
Как можно понять, недостатки являются хотя и сложными, но преодолимыми, а значит, не мешают внедрению рентгеновской дефектоскопии там, где в ней существует необходимость.
Как это работает
Очевидно, что для оценки возможностей технологии и особенностей её применения, желательно знать её основные принципы. В основе процесса – рентгеновское излучение, открытое ещё в 1895 году Вильгельмом Конрадом Рентгеном. Мог ли знать проводивший эксперименты знаменитый учёный, во скольких областях человеческой деятельности благодаря его открытию произойдут изменения?!
Во всех аппаратах, использующих описываемый принцип дефектоскопии, источником регистрируемого излучения служат рентгеновские трубки. Характеристики этих трубок влияют на возможности аппаратуры и результаты замеров. Максимальная толщина металла, которую способен просветить рентгеновский аппарат, напрямую зависит от излучения, жёсткость которого, в свою очередь, связана с параметрами подаваемого на трубку тока. По используемому напряжению оборудование делят на три основные группы.
- Малого, в пределах от 60 до 120 кВ.
- Среднего, от 200 до 400 кВ.
- Высокого, от 1 до 2 МэВ, напряжения.
Если первые два типа удаётся сделать переносными, то последний может быть либо передвижным (установленным на самоходное или буксируемое шасси), либо стационарным.
Рентгеновские трубки высокого напряжения могут быть использованы для выявления дефектов в деталях, изготовленных из стали толщиной до 500 мм.
Благодаря особенностям конструкции рентгеновской трубки, предусмотрена возможность регулировки размеров фокусного пятна. Излучатель помещается внутрь специальной защитной капсулы, имеющей отверстие или прорезь, сквозь которые лучи направляют на исследуемый участок. В некоторых конструкциях аппаратов пятно фокусируется с помощью дополнительных линз.
Прошедшее сквозь материал излучение попадает на светочувствительный материал, оставляя на нём отпечаток, подобный тому, какие получаются при использовании технологии классической фотографии. В случаях, когда существует необходимость непрерывно получать данные в реальном времени, прибегают к использованию так называемых сцинтилляторов. Эти вещества обладают способностью преобразовывать невидимое жёсткое излучение в свет, видимый человеческому глазу, благодаря чему появляется возможность задействовать специальный преобразователь и вывести изображение на экран. Работающие по такому принципу установки иногда называют рентгенотелевизионными.
Некоторые особенности
В зависимости от устройства трубки аппараты делят на импульсные, в которых поток излучения выдаётся сжатыми порциями, и постоянного действия, где излучение идёт непрерывно. Ввиду того что при создании короткого импульса удаётся повысить пиковые значения излучателя без существенного увеличения его размеров и параметров напряжения, в последнее время именно таким аппаратам отдаётся предпочтение.
Важные моменты
В любом случае на конечные результаты проводимых замеров влияют несколько основных факторов.
- Стабильность характеристик подаваемого напряжения.
- Точные геометрические параметры контроля.
- Регулировка размеров фокусного пятна.
- Фокусное расстояние между дефектоскопируемым объектом и преобразователем излучения.
Согласно требованиям ГОСТ 7512-86, распространяющим своё действие на методы РК контроля, для каждого обследуемого изделия должна быть разработана технологическая карта. Это важно, поскольку свою эффективность рентгеновский контроль демонстрирует только при полном соблюдении всех нормативов.
Нужно обеспечить безопасность
На участке производства, где используется полезная, но всё же опасная технология, существует очевидная необходимость в строжайшем соблюдении норм техники безопасности. Ведь полученное даже в малых дозах, жёсткое излучение накапливается в организме и способно нанести непоправимый вред здоровью. Чтобы этого не случилось, следует выполнять следующие правила.
- При проведении замеров недопустимо присутствие на участке работ посторонних лиц. Даже допуск людей к прошедшим дефектоскопию деталям на какое-то время следует ограничить.
- Всё излучающее оборудование должно быть надёжно защищено специальными экранами. В качестве материала для таких экранов может быть использован свинец, или иные вещества, поглощающие жёсткое излучение.
- Управляющий процессом оператор должен быть максимально удалён от излучателя, а его рабочее место также защищено поглощающими экранами.
- При необходимости посещения зоны повышенной опасности сотрудники должны быть обеспечены надёжными средствами индивидуальной защиты. Время их пребывания рядом с излучателем следует свести к минимуму.
Недопустимо использование неисправных рентгенографических установок. Ремонт оборудования должен производиться только квалифицированными специалистами, имеющими соответствующий допуск. Совершенно очевидно, что применять технологию в домашних условиях не стоит.
Попытки изготовить оборудование самостоятельно, а тем более выполнить с его помощью необходимые замеры, почти наверняка приведут к тяжелейшим последствиям для здоровья оказавшихся рядом людей. К счастью, в этом нет необходимости. Промышленность выпускает в достаточном количестве эффективные и вполне надёжные приборы, способные обеспечить точный рентгенконтроль. Нужно лишь правильно выбрать устройство, возможности которого соответствуют намеченным задачам.
Где можно применить?
При правильном подходе и соблюдении всех требований, технология безопасна и весьма эффективна. Она постепенно вытесняет устаревшие методы и всё чаще рентгенографические установки можно встретить в самых разных местах.
- На строительстве новых или обслуживании уже находившихся в эксплуатации трубопроводов. Ведь это один из самых удобных способов проверки надёжности сварных соединений и герметичности трасс, по которым перекачиваются различные химические вещества.
- В местах возведения многоэтажных зданий, от прочности несущего каркаса которых будут зависеть жизни огромного количества людей. Чтобы исключить ненужные риски, стоит проверить качество сварных швов заблаговременно.
- На судостроительных верфях, де строятся огромные грузовые суда или фешенебельные пассажирские лайнеры. Лишь надёжным сварным соединениям не страшны шторма.
- В цехах, где собирают на стапелях самые современные самолёты, и даже ракеты. Подняться в небо или достигнуть звёзд они смогут лишь в том случае, если их сварные швы не имеют дефектов.
- У сборочных конвейеров, с которых сходят новейшие модели автомобилей. Количество звёзд, заработанных на краш-тестах, зависит от многих факторов. В том числе и от хорошо выполненной дефектоскопии.
Безусловно, это далеко не весь перечень возможностей рентгенографического контроля. Ведь подробное перечисление заняло бы не одну страницу. Вполне возможно, что именно сейчас кто-то придумал, как ещё можно использовать эту имеющую широкие возможности технологию.
Поделись с друзьями
0
0
0
0
svarkalegko.com
Как проходит радиографический контроль сварных соединений
При соединении металлов с помощью сварки у неопытных мастеров могут возникнуть трудности. В частности, они могут просто не увидеть всех дефектов сварного шва, которые образовались из-за ошибок сварщика. Визуального контроля недостаточно, чтобы выявить скрытые недочеты. И если в условиях домашней сварки это не критично, то на крупном производстве бракованные изделия лишают прибыли.
Существует множество видов контроля сварных швов. От визуального, когда сварщик просто осматривает шов на предмет видимых дефектов, до передовых способов, для которых необходимо специальное оборудование. Об одном из таких способов мы и хотим вам рассказать. В этой статье вы узнаете, что такое радиографический контроль сварных соединений и какова его методика.
Содержание статьи
Общая информация
Радиографический метод контроля сварных соединений (также рентгенография, рентгеноскопия, рентгенографический контроль) — метод контроля качества с применением рентгеновских лучей. Специальный аппарат устанавливает на место сварного шва. Здесь все по аналогии с рентген аппаратом для снимков костей человека. Рентгеновские лучи пронизывают металл и в случае обнаружения внутренних дефектов легко выходят наружу. Ну а если структура шва плотная и не имеет дефектов, то луч просто не пройдет.
Специальное устройство регистрирует прохождение лучей и делает снимок. На снимке без проблем можно обнаружить наличие дефектов, их размеры и точное расположение. Рентгеновский контроль сварных соединений — это один из наиболее точных методов контроля качества швов. Его часто используют при проверке трубопровода, ответственных изделий, металлоконструкций, к которым предъявлены повышенные требования качества. Особенно заметна популярность радиографического контроля в строительной сфере.
Принцип работы
«Сердцем» рентгеновского аппарата является излучатель, который генерирует и выпускает лучи. Излучатель представляет собой вакуумный сосуд, который содержит анод, катод и его накал. Все эти частицы заряжены и являются электродами. Во время их сильного ускорения как раз и образуются рентгеновские лучи. Это простейшее объяснение.
Читайте также: СНИП и контроль качества
Для интересующихся объясним подробнее. Катод испускает электроны, которые ускоряются от электрического потенциала, образующегося между анодом и катодом. В этот момент рентгеновские лучи уже начинают образовываться, но их недостаточно. Однако, лучи все же сталкиваются с анодом и начинается их торможение. Из-за этого лучи начинают генерироваться сильнее. В тот же момент из-за столкновения начинают появляться электроны анода. Так образуются лучи, достаточные для формирования полноценного излучения.
Далее лучи выходят и пускаются в заданном направлении. Лучи сталкиваются с металлом и в случае наличия дефектов проходят сквозь него. Либо поглощаются металлом, если дефектов нет. Здесь нужно уточнить, что лучи поглощаются не полностью, некоторые частицы все же остаются. Именно они попадают на пленку и позволяют сделать снимок. На снимке фиксируется количество лучей, прошедших сквозь металл. Если дефектов много, то и лучей тоже будет много. За счет такой особенности и получается узнать размер дефекта и его расположение.
Особенности рентгеновских лучей
Чтобы лучше понять суть рентгенографии нужно разобраться с особенностями самих лучей, благодаря которым как раз и возможен контроль. Лучи обладают свойствами, которые позволяют им проходить сквозь материалы. В нашем случае металл. Чем выше плотность металла, тем хуже проходят лучи. И, соответственно, чем ниже плотность металла, тем лучше они проходят. Здесь все просто: наименьшая плотность присутствует как раз в местах с дефектами.
Поэтому лучи беспрепятственно проходят сквозь металл и это фиксируется на специальном устройстве. Ну а если у шва нет дефектов и структура плотная, то лучи не пройдут, а просто поглотятся металлом. И чем выше плотность, тем больше степень поглощения.
Что касается снимков, то здесь тоже все просто. Существуют химические вещества, которые при контакте с рентгеновским излучением начинают буквально «светиться». Такими веществами покрывается светочувствительная часть фотопластинки, на которой затем появится снимок. Этот принцип является основой для создания рентгеновских снимков сварных швов.
Теперь о некоторых других особенностях. Наверняка вы слышали, что рентгеновское излучение в большом количестве может пагубно влиять на здоровье человека. Это правда. Лучи легко воздействуют на ткани и клетки, облучая их за считанные минуты. В больших дозах это может привести к лучевой болезни. Так что нужно соблюдать осторожность, если вы используете радиографический метод контроля сварных соединений.
Еще один интересный факт: благодаря излучения привычный нам воздух способен проводить электрический ток. Это связано с тем, что рентгеновские лучи ионизируют воздух и расщепляют его частицы на небольшие составляющие, которые в свою очередь имеют электрический заряд.
Плюсы и минусы метода
Плюсы:
- Рентгенографический контроль сварных соединений — один из самых достоверных методов контроля качества швов.
- С помощью этого метода за считанные минуты выявляются дефекты любого уровня.
- Есть возможность определить точный размер и расположение дефекта.
- Контроль занимает мало времени и требует только рентген-аппарат.
- Возможен контроль сварных соединений трубопроводов и любых других сложных систем.
Минусы:
- Качество контроля напрямую зависит от настройки рентген-аппарата.
- Современные рентген-аппараты стоят дорого, особенно компактные модели, которые так популярны в строительной сфере.
- Для работы понадобится специальная светочувствительная пленка, которая также стоит недешево.
- Этот метод контроля сварных швов сопряжен с опасностью для здоровья.
Методика контроля
Методика радиографического контроля проста и во многом схожа с обычной рентгенографией, которую мы делаем в поликлинике. Сначала контролер или ответственное лицо устанавливает необходимые настройки аппарата, учитывая плотность металла. Помните, что именно плотность влияет на конечный результат.
Далее подготавливается сварное соединение. Нужно удалить шлак, обработать валик шва и зачистить металл. Затем либо деталь помещается в аппарат (если контроль стационарный в отдельной комнате), либо аппарат помещается на соединение (если контроль выездной и используются компактные модели). Шов должен находиться между излучателем и пленкой. Излучатель включается, лучи проходят сквозь металл и попадают на пленку. Мы получаем снимок, на котором видны все дефекты. Теперь можно выключить аппарат и подождать 10-20 секунд. Затем деталь извлекается из ренигенографа (или рентгенограф снимается с металла). Снимки отдаются специалисту для их изучения или остаются у контролера.
Техника безопасности
Как мы уже говорили, данный метод контроля сопряжен с некоторой опасностью для здоровья. Не нужно пренебрегать этим, думая, что небольшие дозы радиации не повлияют на вас. Если вы работаете контролером и постоянно имеете дело с рентгенографией, то соблюдайте следующие рекомендации.
Во-первых, самое главное правило при работе с рентгеном — нужно экранировать прибор. Это не даст лучам распространяться за пределы зоны контроля. Для этих целей можно использовать металлические листы. Если вы работаете в помещении, то его стены также должны быть оборудованы экранирующими пластинами. Так лучи не будут представлять опасности для других работников, находящихся на объекте или в цеху.
Во-вторых, постарайтесь как можно меньше времени проводить рядом с аппаратом. Если вы проводите радиографический метод контроля сварных соединений на улице, то лучше отойдите в сторону. Если вы работаете в помещении, то постарайтесь сократить время своего пребывания в нем. Также на вас должны быть средства индивидуальной защиты. В помещении и рядом с аппаратом на улице не должны проходить посторонние работники.
В-третьих, перед началом работ нужно убедиться, что аппарат работает исправно и все настройки выставлены правильно. Большинство несчастных случаев связаны именно с неправильной настройкой или неисправностью рентгена.
В-четвертых, следите за дозой лучей, которые вы получаете при каждом контроле. Да, небольшие дозы не вредны для здоровья, но они обладают свойством накапливания и в конечном итоге могут стать причиной серьезных заболеваний. Следите, чтобы полученная вами доза радиации успевала выводиться из организма до начала следующего контроля. Чтобы узнать дозу можно использовать дозиметр.
В-пятых, не забывайте, что из-за лучей воздух может сильно ионизироваться, что приведет к образованию электрического тока. Следите за допустимым значением ионизации воздуха, особенно, если работаете в закрытом помещении.
Вместо заключения
Вот и все, что мы хотели рассказать вам о рентгенографическом методе контроля. Это один из самых точных и достоверных способов выявить скрытые от глаз дефекты. С его помощью можно провести контроль как на производстве, так и на выезде, поскольку производители предлагают компактные модели. Их легко можно взять с собой и выполнять контроль даже под открытым небом.
Конечно, радиографический контроль сварных соединений требует определенных знаний и опыта, чтобы читать снимки. Но вместе с тем вы получаете навык, который поможет вам безошибочно выявлять дефекты даже в идеальных на вид швах. А вы использовали в работе рентгенограф? Поделитесь в комментариях своим опытом контроля качества швов с помощью данного прибора, это будет полезно для наших читателей. Желаем удачи в работе!
[Всего голосов: 0 Средний: 0/5]svarkaed.ru
Применение рентгеновского контроля в производстве электроники
Подробности Автор: EngineerDeveloper®
Преимущества
Преимущества использования рентгена очень широки, в силу его возможности «смотреть сквозь корпус», включая: корпуса полупроводниковых приборов, теплооотводы для ИС и металлические экраны, для выявления дефектов соединения, и позволяет распознавать потенциальные проблемы качества с помощью неразрушающего метода контроля. Особенно рентгеновский контроль выгоден при работе с такими типами корпусов как: BGA, CSP, FC, WLP, POP, SIP, QFN; ввиду недостаточного качества оценки таких компонентов другими методами инспекции (Автоматическая Оптическая Инспекция, 2D/3D контроль, электрический тест и т.д.).
Рентгеновский контроль стал незаменимым инструментом для оценки качества и контроля проведённых ремонтных работ. Используя возможности цифровой обработки изображения, инструменты обнаружения неисправностей и их анализа производство получает возможность точно отладить технологический процесс. Что в конечном итоге приводит к улучшению качества выпускаемых изделий, сокращается брак и уменьшается возврат готовых изделий по гарантии. Одним словом, наличие рентгена положительно воздействует на жизненный цикл конечного продукта. Исходя из этих причин, всё больше и больше производителей электроники, а также их заказчики, считают наличие рентгеновского контроля обязательным требованием к производственному процессу.
Дефекты, обнаруживаемые с помощью рентгеновского контроля
Дефекты паяного соединения возникают из-за множества различных температурных и механических условий, которые возникают во время производственных процессов. Ниже приведен список типичных производственных дефектов, с примерами изображений, оценкой неисправности и возможной причиной их возникновения.
Стратегия использования рентгеновского контроля
При использовании таких системы контроля (рентгеновский осмотр в реальном времени), быстрая и точная оценка может быть достигнута, используя следующие методы:
Соответствие техническим требованиям
Системы рентгеновского контроля отличаются друг от друга дизайном и возможностями, но все же, всех они имеют подобные фундаментальные основы, которые делают их системами рентгена. Поэтому, чтобы ответить на вопрос соответствия системы к техническим требованиям, предъявляемым к технологии рентгеноскопии, требуются пояснения, описанные ниже:
Размеры печатной платы
При выборе установки рентгеновского контроля необходимо обратить внимание на максимально возможные габаритные размеры печатной платы: поместится ли печатная плата в область загрузки установки?
ПРИМЕЧАНИЕ: Обычно, это первый вопрос, который задают, подбирая систему для инспекции необходимого спектра печатных плат.
Манипулирование образцом (инспекция образца под углом)
Эта способность вращать образец (печатную плату) при проведении рентгеноскопического исследования позволяет отображать форму, размер и размещение дефектов под различными углами обзора. Это особенно важно для плат с двусторонним монтажом, где верхние и нижние компоненты могут затенять интересующую область инспекции. Так же, данная функция делает возможным более точно определять дефекты электрических соединений для микросхем (BGA, QFP, QFN и т.д.).
ПРИМЕЧАНИЕ: Угол наклона от 0 до 40° идеален для такого применения. Ручное или механическое вращение будет влиять на стоимость оборудования и удобство оператора, и имеют небольшие отличия в эффективности.
Увеличение и поле обзора (FOV)
Увеличение и поле обзора (FOV) имеют прямо пропорциональную взаимосвязь. В конечном счете, цель должна состоять получении оптимального баланса между достаточным увеличением (детализация инспекции) и достаточным полем обзора (область инспекции), чтобы просматривать насколько возможно большую инспектируемую область и минимизировать время, требуемое для полного осмотра печатной платы.
ПРИМЕЧАНИЕ: Используя сильное увеличение, поле обзора становится меньшим, таким образом, скорость инспекции уменьшается. Поэтому, производительность и увеличение являются противостоящими целями, и наилучшее их соотношение зависит от применения и опыта оператора.
Рентгеновская трубка - Разрешение
Для всех систем рентгеновского контроля такие параметры как: размер фокусного пятна, форма фокусного пятна и мощность рентгеновской трубки являются характеризирующими факторами разрешения. Наиболее часто используемый параметр для системы рентгеновского контроля это размер фокусного пятна.
ПРИМЕЧАНИЕ: Поскольку размер фокусного пятна изменяется в соответствии с мощностью электронного пучка, то при увеличении напряжения на источнике рентгеновских лучей, размер пятна быстро меняется от нанофокусного до микрофокусного размера (при проникновении на большую глубину материала образца).
Рентгеновская трубка - Напряжение
Напряжение рентгеновской трубки измеряется в кВ (Киловольт). С помощью регулировки числа испускаемых фотонов рентгеном, можно обеспечить необходимую степень проникновения излучения в материал образца. При использовании низкого напряжения отображаются токопроводящие дорожки и форма паяного соединения, в то время как высокое напряжение используется для отображения скрытых внутренних характеристик компонента (например, пустот паяного соединения).
ПРИМЕЧАНИЕ: Обычно, в рентгеновских систем, работающих в реальном времени, напряжение на рентгеновских трубках может изменяется в переделах 50-130кВ. Выбор мощности рентгеновской трубки зависит от материала инспектируемых образцов. Большинству печатных плат и SMD компонентов требуется мощность в диапазоне от 50 до 90кВ. Тогда как, экранированным компонентам, литью и механосборочной продукции может понадобиться от 90 до 130кВ или более, в зависимости от материалов и плотности монтажа.
Обработка изображений
Для всех систем рентгеновского контроля, обработка изображений и программное обеспечение имеют прямое воздействие на скорость, точность и повторяемость процесса инспекции. Типичный набор программного обеспечения включает в себя основные программные средства улучшения качества изображения как то: усреднение изображения (удаление шумов) и фильтры улучшения изображения. В результате такой совокупной обработки изображения, улучшается детализация рентгеновского изображения, таким образом, облегчая оператору возможность быстро оценить качество и обнаружить дефекты. Другие программные инструменты, как сбор данных, инструменты измерений и анализа используются для сбора информации, её структуризации и последующей обработки.
ПРИМЕЧАНИЕ: Следует отметить, что большинство операторов используют минимальный набор инструментов, необходимых для выполнения работы, а некоторые продвинутые особенности визуализации (3D рендеринг, например) являются трудоёмкими и не особенно полезными для оценки качества инспекции инструментами.
Заключение
Наилучшая стратегия использования рентгеновского контроля
Хорошая стратегия должна использовать баланс между работой в режиме слабого увеличения (чтобы одновременно просматривать насколько возможно большую инспектируемую область для быстрого выявления основных дефектов) и сильного увеличения (чтобы обеспечить соответствующую детализацию анализа неисправностей). Наилучший баланс зависит от предмета инспекции и опыта оператора.
Соответствие техническим требованиям
Первое: Удовлетворяет ли система Вашим запросам (возможность установки печатной платы необходимого размера, мощность рентгеновской трубки и т.д.)? По большей части, это вопрос специфики использования, с условием, что выбор системы должен соответствовать фактическим требованиям назначения системы. В большинстве случаев, задача звучит так: «Сделать необходимую работу быстро, просто и эффективно и использовать минимальный набор инструментов для выполнения этой задачи. Резюме: приобретайте то, что Вам нужно, и то, что Вы будете действительно использовать.
Второе: Соответствует ли система Вашему бюджету? Бюджет, кроме начальной стоимости всей системы, должен включать в себя долгосрочную стоимость владения: сервис, поддержку и гарантию, так же как и легкость дальнейшего обслуживания, простоту использования и минимальные требования к обучению персонала. Резюме: Цена (Возврат инвестиций) это зависимость полной себестоимости и эффективности работы в течении периода эксплуатации.
portal-ed.ru
Контроль сварных соединений рентгеновскими и гамма-лучами
Контроль сварных соединений рентгеновскими и гамма-лучамиКатегория:
Сварка металлов
Контроль сварных соединений рентгеновскими и гамма-лучамиМетод контроля сварных соединений рентгеновскими и гамма-лучами основан на различной проницаемости для коротковолновых электромагнитных колебаний сплошного металла и различных находящихся в нем неоднородностей, заполненных шлаками, окислами и газами. Поглощение коротковолновых лучей металлом значительно сильнее поглощения их неметаллическими включениями. При рентгеновском контроле применяются специальные мощные рентгеновские аппараты для просвечивания металлов: стационарные — для испытаний в лабораторных условиях и передвижные — для испытаний непосредственно в заводских условиях.
Передвижные рентгеновские аппараты для контроля качества сварки в заводских условиях изготовляются обычно на максимальное рабочее напряжение 150 — 350 кв. Существуют также специальные рентгеновские аппараты с рабочим напряжением 1000 кв и более.
В последнеее время началось успешное применение особых аппаратов — бетатронов, дающих особенно мощное жесткое рентгеновское излучение, используемое для просвечивания металлов. 13 бетатроне электроны ускоряются переменным магнитным полем.
Рис. 1. Передвижной рентгеновский аппарат РУП: 1 — рентгеновский аппарат; 2 — пульт управления; 3 — рентгеновская трубка; 4 — масляный насос
Для защиты обслуживающего персонала от высокого напряжения и вредного воздействия рентгеновских лучей передвижные аппараты снабжены специальными приспособлениями, уменьшающими опасность и вредность работы на них. Рентгеновская трубка заключена в толстостенный свинцовый футляр — бленду, охлаждаемую циркулирующим маслом. Для пропуска рентгеновских лучей бленда имеет боковое окошко, закрытое листовым алюминием.
Наиболее употребительный на наших заводах рентгеновский аппарат типа РУГ1 (рис. 1) может давать на трубку рабочее напряжение до 200 кв при максимальном токе 20 ма. Аппарат позволяет просвечивать сталь толщиной до 80 мм, алюминий до 300 мм. Аппарат питается от нормальной силовой сети переменного тока напряжением 220 в. Это напряжение повышается до необходимой величины трансформаторами и конденсаторами, встроенными в аппарат, выпрямляется кенотронами; выпрямленный ток подается на рентгеновскую трубку гибкими кабелями с особо прочной резиновой изоляцией, выдерживающей напряжение 200 кв.
При рентгеновском контроле можно наблюдать дефекты визуально на флюоресцирующем экране или фотографировать их, получая так называемую рентгенограмму. Визуальный метод обнаружения дефектов на экране для сварных швов не применяется, дефекты в большинстве настолько мелки, что на экране не выявляются.
Для получения рентгенограммы пучок рентгеновских лучей направляется на испытуемый сварной шов (рис. 2). С обратной стороны закладывают специальную рентгеновскую фотопленку с двусторонней чувствительной эмульсией. Пленку закладывают в светонепроницаемую кассету или пакет из плотной черной бумаги. Для сокращения экспозиции пленку закладывают между флуоресцирующими экранами и защищают снизу свинцовым экраном от вторичных излучений, снижающих четкость снимка. Время экспозиции зависит от толщины металла, сорта фотопленки и расстояния трубки от металла; оно определяется по таблицам или, что удобнее, по специальным диаграммам и колеблется обычно от нескольких минут до получаса. По окончании экспозиции фотопленку обрабатывают, проявляют и фиксируют обычными методами.
Рентгенограмма представляет собой негативное, теневое изображение сварного шва с прилегающим основным металлом. Всякого рода включения, меньше поглощающие рентгеновские лучи, дают на рентгенограмме местные более интенсивные почернения по сравнению с окружающим сплошным металлом. Хороший рентгеновский снимок выявляет дефекты величиной от нескольких десятых долей миллиметра, причем для выявления дефекта имеет значение главным образом размер его в направлении рентгеновского луча.
Непровары выявляются на снимке в виде довольно резкой прямой черной линии, трещина дает обычно извилистую линию; выявляются также поры и шлаковые включения. Рассматривать нужно всегда подлинную рентгенограмму или отпечаток с нее на фотопленке, так как отпечаток на бумаге не передает многих тонких подробностей рентгенограммы и не может служить для надежной оценки сварного шва (рис. 232). Полученную рентгенограмму сравнивают с типовыми рентгенограммами для данного изделия.
Рис. 3. Схема получения рентгеновского снимка: 1 — рентгеновская трубка; 2 — фотопленка; з — экран; 4 — кассета
По характеру рентгенограмм сварные швы обычно разделяют на три группы: плохие (бракуют), удовлетворительные (могут быть приняты) и хорошие (подлежат безусловной приемке). Совершенно не допускаются трещины, поэтому при наличии трещин, хотя бы мелких, шов относят к группе плохих. В минимальных размерах, определяемых условиями приемки, допускаются частичные непровары. Шлаковые включения и поры в ограниченных пределах, определяемых условиями приемки, считаются допустимыми.
Рис. 4. Рентгенограмма сварного шва
Рентгеновский контроль получил широкое применение на наших заводах и для ряда ответственных изделий, например подлежащих приемке инспекцией Госгортехнадзора, является обязательным.
Рентгеновский контроль ввиду расхода фотоматериалов и довольно значительного времени экспозиции снимка обходится сравнительно дорого, поэтому обычно просвечивают не все швы на всем протяжении, а лишь отдельные их участки. Выбор мест для съемки рентгенограмм и общая протяженность участков шва, подлежащих рентгенографированию, определяется условиями приемки. Обычно проверяют 10—15% общей длины швов. Минимальная величина дефекта в направлении рентгеновского луча, выявляемого рентгенограммой, составляет около 2% толщины просвечиваемого металла.
Рентгеновский аппарат требует наличия переменного тока и, кроме того, довольно громоздок; в ряде случаев, например в полевых условиях, применение рентгеновского контроля затруднительно. Поэтому представляет большой интерес контроль сварных швов гамма-лучами радиоактивных веществ. Гамма-лучи, испускаемые некоторыми радиоактивными веществами, являются электромагнитным излучением, по своей природе близким к рентгеновским лучам. Гамма-лучи имеют малую длину волны, обладают большой жесткостью и при просвечивании меньше поглощаются металлом, чем рентгеновские лучи от обычных аппаратов.
Средняя длина волны и жесткость рентгеновских лучей зависят от напряжения, подаваемого на рентгеновскую трубку; с увеличением напряжения длина волны уменьшается, а жесткость возрастает. При напряжении 150—200 кв средняя длина волны рентгеновских лучей равна ОДА, что достаточно для просвечивания стали толощиной до 50 мм. Средняя длина волны гамма-лучей равна 0,01 А, что достаточно для просвечивания стали толщиной до 300 мм и соответствует длине рентгеновских лучей при напряжении на трубке около 2000 кв. Принципиальная возможность применения гамма-лучей для просвечивания металлов с целью контроля качества и выявления всякого рода дефектов и включений известна давно. Но снимки, получаемые посредством гамма-лучей, так называемые радиограммы, получались столь низкого качества, что практически гамма-лучи были пригодны для выявления лишь очень крупных дефектов, например больших раковин, и непригодны для контроля сварных швов, дефекты которых отличаются малыми размерами.
Техника применения гамма-лучей для контроля сварных швов значительно усовершенствована,главным образом трудами С.Т.Назарова, и в настоящее время гамма-лучи представляют собой надежное средство контроля сварки и широко применяются в нашей промышленности. Источниками получения гамма-лучей служили препараты радия и различные радиоактивные вещества. Сейчас все это заменили дешевые искусственные радиоактивные изотопы.
Радиоактивный препарат помещают в ампулу — запаянную стеклянную трубочку диаметром около 3 мм. Препарат упаковывают в ампулу, по возможности плотно, а для получения более четкого фотоснимка источнику излучения придается точечный характер. Для защиты от повреждений стеклянную ампулу помещают в латунную гильзу. Латунная гильза хранится в толстостенном свинцовом контейнере весом около 20 кг, заключенном в металлический футляр с ручкой для переноски. При работе гильзу с ампулой вынимают из контейнера щипцами длиной не менее 1,5 м.
Наша промышленность дешево и в значительных количествах изготовляет искусственные радиоактивные препараты, пригодные для технического применения, в том числе для просвечивания металлов. Примером таких препаратов может служить радиоактивный изотоп кобальта СобО, имеющий атомный вес 60. Появление доступных, дешевых искусственных радиоактивных препаратов открывает широкие перспективы промышленного применения гамма-лучей для просвечивания металлов, в частности сварных соединений.
Следует помнить, что как рентгеновские, так и в особенности гамма-лучи чрезвычайно опасны для человеческого организма, поэтому при работе с ними нужно строго соблюдать установленные правила безопасности.
Для снятия радиограммы ампулу устанавливают на специальную подставку, а с противоположной стороны изделия, так же как и при рентгенографировании, закрепляют фотопленку с усиливающими и фильтрующими экранами. Полученный снимок — радиограмму — проявляют и фиксируют обычным порядком.
Современная техника радиографирования дает возможность выявлять примерно те же дефекты, которые выявляются рентгеновским исследованием, но полученная радиограмма отличается от хорошей рентгенограммы значительно меньшей четкостью и контрастностью, так что рассмотрение радиограмм и выявление дефектов по ним требует навыка.
Читать далее:
Магнитный, звуковой и другие способы контроля сварных соединений
Статьи по теме:
pereosnastka.ru
Рентгеновский контроль
Услуги рентгеновского контроля
Рентгеновский контроль печатных плат
Рентгеновский контроль изделий
Рентгеновский контроль сварных соединений
Рентгеновский контроль на территории нашего предприятия
Проведение рентгеновского контроля на территории предприятия Заказчика
Рентгеновский контроль в процессе монтажа
Гамма-контроль
Многие в жизни сталкивались с рентгендиагностикой. В медицине она позволяет увидеть то, что скрыто от глаз врача, оценить состояние пациента и назначить оптимальное лечение. Также и в промышленности этот метод дает возможность увидеть дефекты изделия и предотвратить его поломку.
Данный метод неразрушающего контроля основан на различной проникающей способности рентгеновских лучей через среды с отличающейся плотностью с последующей фиксацией полученного изображения на приборе. Широко используется в нефтегазовой промышленности, например, для контроля целостности труб и в электронной, электротехнической промышленности для контроля состояния печатных плат. Неразрушающему контролю необходимо подвергать изделия до ввода их в эксплуатацию, регулярно на протяжении всего периода эксплуатации и экстренно — в случае аварии либо при подозрении на возможность аварийного случая.
Какие дефекты поможет выявить система рентгеновского контроля:
- При рентгенографии сварных швов она позволит увидеть поры, скопления и цепочки пор, вогнутость корня шва, некоторые виды включений.
- При рентгенографии печатных плат — смещение слоев, нарушения в размерах переходных отверстий, нарушения качества металлизации переходных отверстий.
Плюсы рентгеновского неразрушающего контроля:
- Неразрушающий метод исследования позволяет определить дефекты, которые невозможно увидеть невооруженным глазом.
- Не требуется разрушение объекта исследования.
- Рентгенография позволяет определить локализацию дефекта относительно плоскости съемки.
- Для проведения исследования необходимо остановить рабочий процесс, однако, не требуется полный демонтаж объекта. По завершении дефектоскопии, если не было выявлено повреждений, объект может продолжать функционировать.
- Быстрый результат. Вы получите ответ сразу же по завершении исследования и обработки данных.
- Мы предоставляем также снимки, подтверждающие заключение нашего специалиста.
Это необходимо помнить:
Не существует идеального метода выявления дефектов. Важно знать также и про некоторые минусы технологии.
- Для проведения исследования необходима остановка рабочего процесса и обеспечение специалистам доступа к исследуемым областям объекта. При дефектоскопии печатных плат это не представляется проблемой. Однако, если проводится контроль качества сварных соединений труб, важно освободить их от содержимого на все время проведения исследования.
- Для проведения исследования должен быть обеспечен двухсторонний доступ к объекту.
- Рентгеновское излучение в высоких дозах способно вызывать лучевые ожоги, лучевую болезнь и онкологию. По этой причине для проведения исследования необходимо освободить помещение от персонала.
От качества изготовления изделий зависит не только ваша прибыль, но и зачастую жизни людей. В целях обеспечения безопасности эксплуатации объектов рекомендуется на регулярной основе проводить контроль их качества.
xn--d1acamja1abjrjv6m.xn--p1ai