Как сделать осциллятор для плазмореза своими руками. Схема плазменный резак
схема, видео, самодельный для плазмы
Главная страница » Своими руками » Плазморез » Осциллятор
Осциллятор для плазмореза — это устройство для бесконтактного возбуждения дуги и стабилизации её горения. Эти опции он получает благодаря преобразованию параметров электроэнергии.
Самодельный осциллятор для плазмореза: немного теории
Внешний вид электронного блока осциллятора заводского изготовления представлен на рисунке.
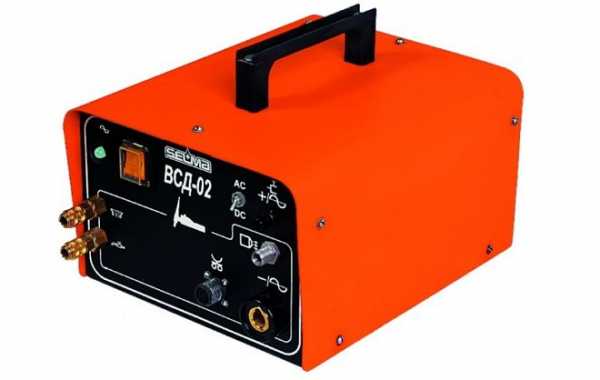
Сварочный осциллятор марки ВСД-02, используемый для стабилизации горения дуги. Ист. http://met-all.org/oborudovanie/svarochnye/svarochnyj-oscillyator-svoimi-rukami.html.
Современные осцилляторы делятся на два класса действия:
- непрерывного действия. Этот класс к сварочному току добавляется ток высокой частоты (150…250 КГц) и с большим значением напряжения (3000…6000 В). В таких условиях дуга будет зажигаться даже без прикосновения электрода к поверхности соединяемых заготовок. Более того, она будет гореть очень устойчиво даже при небольших значениях сварочного тока (благодаря высокой частоте тока, вырабатываемого осциллятором). И, что тоже не маловажно, электроэнергия с такими характеристиками не опасна для здоровья рабочего, работающего на этом устройстве;
- импульсные. Электрическая схема этого класса может предусматривать его параллельное или последовательное подключение.
Примеры электрических схем указаны на рисунке.

Параллельное и последовательное подключение осциллятора. Ист. http://met-all.org/oborudovanie/svarochnye/svarochnyj-oscillyator-svoimi-rukami.html.
Большую эффективность имеет устройства, которые подключены к электрической цепи плазмореза последовательно. Объясняется это тем, что в их схеме не применяется, за ненадобностью, защита от высокого напряжения. Применение осциллятора, кроме того, позволяет расширить опции плазмореза и обрабатывать «проблемные» металлы или сплавы:
- алюминий;
- «нержавейка» и т. п.
Осциллятор для плазмореза своими руками
Осциллятор, который при желании нетрудно изготовить своими руками, чаще всего, относится к устройствам непрерывного действия. Рассмотрим конструкцию гаджета.
В общем случае осциллятор состоит из следующих основных узлов:
- колебательный контур. Он играет роль искрового генератора затухающих колебаний. Колебательный контур состоит из следующих компонентов:
- накопительный конденсатор;
- катушка индуктивности. Её роль выполняет, как правило, обмотка высокочастотного трансформатора;
- разрядник;
- дроссельные катушки;
- трансформатор высокой частоты.
Если у вас есть необходимый инструмент, навыки работы с электронной техникой и желание собрать осциллятор для плазмореза своими руками, то вам предстоит собрать и настроить указанные выше узлы.
Схема
Чтобы было понятно, что вы будете создавать, расскажем, в общих чертах, о принципе действия осциллятора. Сетевое напряжение после повышающего трансформатора поступает на конденсатор колебательного контура и заряжает его. Когда конденсатор зарядился до оптимального значения, предусмотренного параметрами электросхемы, происходит его разряд через разрядник (пробой воздушного зазора).
Внешний вид самодельного разрядника приведён на рисунке.
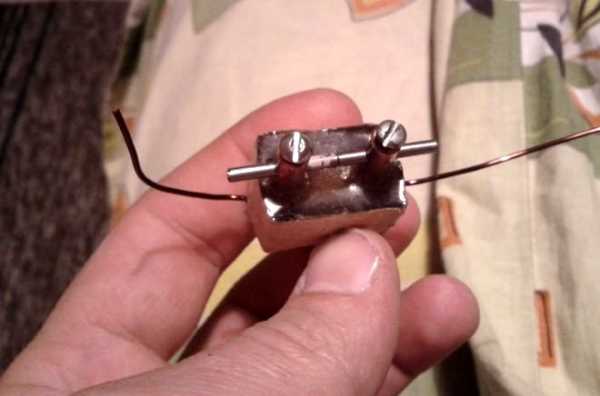
Самодельный одноискровый разрядник. Ист. http://met-all.org/oborudovanie/svarochnye/svarochnyj-oscillyator-svoimi-rukami.html.
Импульс, возникший в этот момент на разряднике, возбуждает колебания в колебательном контуре (колебания представляют собой обмен энергией между ёмкостью конденсатора и индуктивностью обмотки высокочастотного трансформатора). В колебательном контуре возникают затухающие высокочастотные электрические колебания, соответствующие его резонансной частоте.
В момент резонанса на обкладках конденсатора колебательного контура образуется высокое напряжение (величина зависит от добротности «Q» колебательного контура), которое через разделительный конденсатор и обмотку катушки поступает на резак и производит поджиг. Параметры разделительного конденсатора подбираются таким образом, чтобы его реактивное сопротивление препятствовало прохождению тока низкой (сетевой) частоты и не препятствовало высокой частоте.
Вот один из вариантов принципиальной электрической схемы самодельного осциллятора.
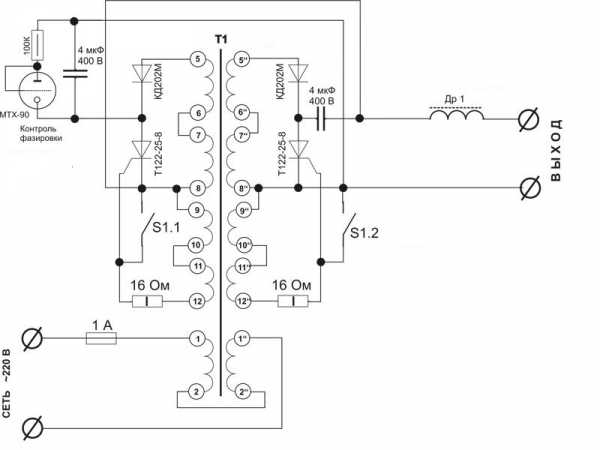
Принципиальная электрическая схема осциллятора, который можно собрать своими руками. Ист. http://ismith.ru/welding-equip/svarochnyj-oscillyator-svoimi-rukami/.
Пояснения к схеме:
1. Назначение индикатора «МТХ-90». В момент разряда накопительного конденсатора (при условии правильного подключения всего устройства) светится табло «Контроль фазировки».
2. S1- выключатель дугообразователя;
3. Дроссель Др1 представляет собой катушку из 15 витков провода сечением 2,5 кв. мм, намотанную на кольце R40 х 25 х 80 из феррита с магнитной проницаемостью M2000HM.
4. Т1 – импульсный трансформатор генератора строчной развёртки (на сленге — «строчник») типа «ТС180-2».
Большим «плюсом» этой электрической схемы служит тот факт, что для её реализации не требуются какие-либо дефицитные или дорогостоящие детали (материалы).
Следует учесть, что осциллятор в процессе работы, благодаря разряднику, создаёт большие электропомехи. Для их нейтрализации, необходимо осуществлять монтаж всех компонентов в «глухом» металлическом корпусе.
Пример конструкции приведён на рисунке.
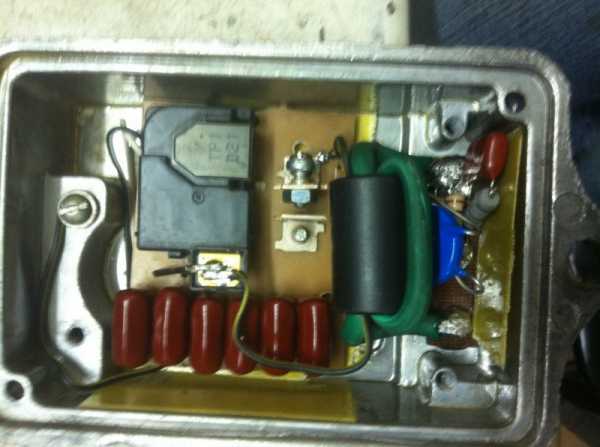
Пример монтажа осциллятора в «глухом» корпусе. Ист. http://m.radiokot.ru/forum/viewtopic.php?f=11&t=115840.
Настройка осциллятора должна осуществляться с тем плазморезом, с которым он будет в дальнейшем работать. Заключается она в подборе опытным путём терристоров. Ориентироваться следует на устойчивость сварочной дуги.
Внимание! При настройке и последующей работе с осциллятором следует строго соблюдать правила техники безопасности при работе с электроприборами. Гаджет – устройство непрерывного действия с импульсным питанием, и на его выходных контактах остаётся напряжение после отключения питания от сети.
Видео
Посмотрите небольшой ролик с описанием одного из вариантов осциллятора своими руками:
Полезная информация по теме:
Теперь, когда вы знаете, как сделать осциллятор для плазмы, будет легче сделать плазморез своими руками.
Рекомендуем ознакомиться и с другими материалами раздела «Своими руками» на нашем сайте.
Также вам может понадобиться для приобретения деталей и расходников список адресов и телефонов в разных городах, где можно приобрести комплектующие для плазменной резки.
Может быть, вам будет полезен также раздел контактов сервисных центров по плазменному оборудованию в разных городах.
plazmen.ru
Самодельный плазморез из сварочного трансформатора
Главная страница » Своими руками » Плазморез » Из сварочного трансформатора
Как сказано в статье про изготовление плазмореза своими руками, источником питания может быть трансформатор. Наиболее подходящим является сварочный. Плазморез из сварочного трансформатора представляет собой устройство, в котором генератором тока сварочной дуги служит трансформатор. Внешний вид такого гаджета приведён на рисунке.
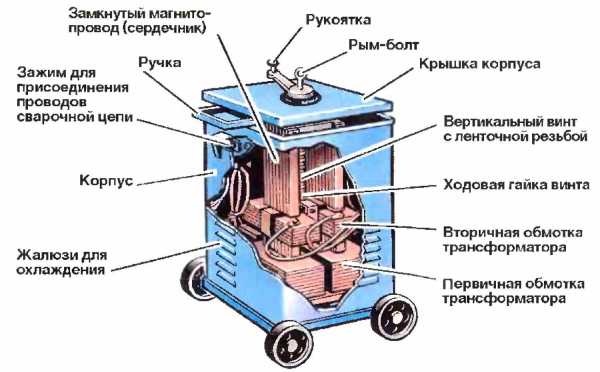
Внешний вид сварочного трансформатора. Ист. http://remoskop.ru/shema-ustrojstvo-remont-svarochnogo-transformatora.html.
Сварочный трансформатор применяется для преобразования высокого напряжения источника питания (220 или 380 В) в низкое. В нашем случае он будет служить генератором тока для плазмореза. На рисунке приведена схема подключения.
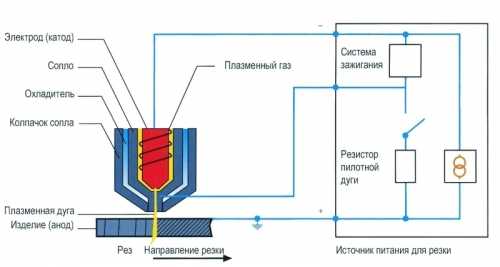
Схема подключения плазмотрона к трансформатору. Ист. http://strport.ru/instrumenty/printsip-raboty-plazmoreza.
Электрический ток от трансформатора на плазмотрон поступает через электрический проводник кабель-шлангового пакета. Посредством его он передаётся на находящийся внутри корпуса плазмотрона электрод, который используется для возбуждения электрической дуги.
Рекомендуем посмотреть: полезный видеоролик о самодельном кабель-шланговом пакете вы найдете в статье «Плазморез своими руками«.При нажатии кнопки «Розжиг», трансформатор начинает подавать на плазмотрон напряжение сварочной дуги (цепь не замкнута и сварочного тока ещё нет), а осциллятор — токи высокой частоты (далее – ТВЧ). Благодаря ТВЧ, внутри плазмотрона возникает дежурная электрическая дуга (образование рабочей дуги между электродом и обрабатываемой заготовкой сразу – затруднительно). В камеру начинает поступать сжатый воздух, он нагревается, увеличивается в объеме (до 100 раз) и ионизируется. Плазма вырывается из сопла, соприкасается с разрезаемым металлом: зажигается режущая дуга, а дежурная — гаснет. Трансформатор генерирует ток для сварочной дуги. Происходит раскрой металла.
Эта метод питания плазмотрона имеет несколько «плюсов»:
- сварочный трансформатор является самым простым источником сварочного тока (по сравнению со сварочными выпрямителем или инвертором), и, следовательно, самым надёжным;
- аппарат плазменной резки не чувствителен к перепадам напряжения;
- гаджет способен резать заготовки большой толщины.
Но, у самодельного плазмореза из сварочного трансформатора имеются и недостатки:
- большая масса. Он не удобен в эксплуатации;
- слишком высокое потребление электроэнергии (читай — низкий КПД).
plazmen.ru
выбор аппарата для воздушно плазменной резки, станки и портативное оборудование
Договоримся-ка сразу. Если вас интересуют вопросы, касающиеся сварки в бытовых или кустарных условиях, то вам эту статью можно не читать. Плазменный резак – не детский сад и никоим образом не домашний инструмент. Если работы простые и разовые, можно поработать болгаркой.
Но уж если технические задачи стоят серьезные, а объемы работ огромные, то без резака для плазменной резки будет сложно. Это любимый инструмент в машиностроении всех профилей и многих других серьезных отраслях, где нужны «кройка и шитье» из металла.
Виды плазменных резаков
Все зависит от того, какие у вам планы, и где вы собираетесь работать. Дело в том, что плазморезы отличаются высокой вариативностью моделей. Они отличаются друг от друга не только эстетически, но и конструктивно: у них, к примеру, разные виды поджига электрической дуги и разные системы охлаждения.
Плазморезы могут быть переносными, могут представлять из себя целые портальные установки. Есть модели шарнирно-консольного типа, встречаются установки с приводом координатного вида. Особое место занимают аппараты с программным управлением.
Все резаки можно разделить следующим образом:
- Аппараты для работы в среде инертных и защитных газов: водорода, гелия и, конечно же, аргона.
- Резаки, функционирующие в среде окислительных газов – газов, которые насыщены кислородом.
- Резаки для работы с различными смесями.
- Для использования в стабилизаторах.
- Резаки с магнитной стабилизацией.
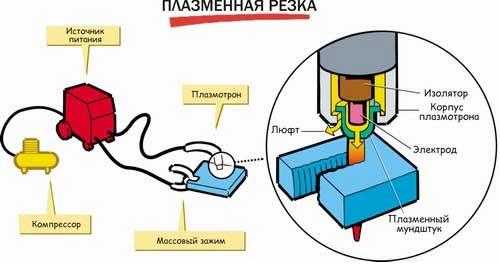
Принцип работы плазменной резки.
Классификация по виду потребляемой энергии:
- Бытовые резаки, которые подключаются к сети с напряжением 220 В.
- Профессиональные или промышленные, работающие только от сети с напряжением 380 В.
Следует учитывать, что даже бытовой плазменный резак с самыми скромными показателями мощности нужно проверить с подключением к общей сети: нагрузка сети будет очень серьезной. К тому же к резаку часто подключается компрессор для охлаждения. Его совсем немаленькую мощность также нужно учитывать при подключении.
Еще один критерий делит плазморезы ровно на две группы:
Резаки инверторного типа
отличный инструмент эконом-класса, который способен резать металл толщиной до 30-ти мм. Их используют чаще в быту и в малых мастерских. Энергопотребление у них весьма скоромное, они компактны: небольшого веса и изящных габаритов.
Большинство моделей являются переносными или ручными аппаратами. С их помощью можно работать в труднодоступных местах. Дополнительное преимущество – неплохой коэффициент полезного действия — выше на 30%.
Плазморезы трансформаторного типа
Они стоимостью подороже. Это больше походе на станок плазменной резки, как большой короб на колесиках. Режут металл с серьезной толщиной – вплоть до 80-ти мм. Они значительно тяжелее и больше по габаритам, чем инверторные.
Эти вес и размеры можно простить за большую надежность: обычно они не выходят из строя при скачках напряжения в сети, что чрезвычайно актуально для некоторых регионов. Продолжительность бесперебойного включения у этих аппаратов фантастическая – вплоть до 100%.
Это означает, что трансформаторный резак может работать весь день без перерыва. Кроме большого веса и крупных габаритов у этого вида аппаратов есть еще один недостаток: высокое потребление энергии. Как говориться, большому кораблю большое плавание.
Плазменные резаки можно разделить по виду контакта:
- Контактные, которые имеют контакт с металлом. Режут детали с толщиной не больше 18-ти мм.
- Бесконтактные, которым под силу резка металлов практически любой толщины.
Контактная плазменная резка
Это выглядит следующим образом: электрическая дуга соединяет плазмотрон и поверхность разрезаемой металлической детали, иными словами – дуга прямого действия. Вектор этой дуги всегда совмещается с потоком плазмы, выходящим из сопла под большим давлением с высокой скоростью.
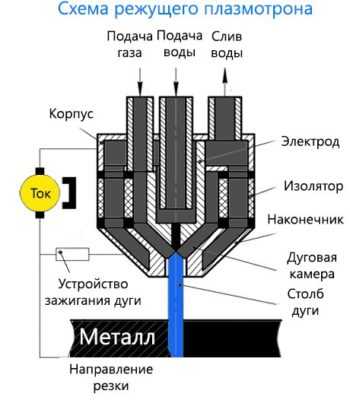
Схема режущего плазмотрона.
Раскаленный воздух представляет из себя плазму, он давит на дугу и сообщает ей режущие свойства. Если учесть высочайшую температуру на уровне 3000°С, происходит то самое механическое воздействие на металл, которое называется резкой.
Данный тип резки используется в работе с высокопроводными металлами. Преимущественно это детали с неправильными контурами, трубы, прутки, металлические полосы и уголки, различные отверстия в заготовках и т.д.
Бесконтактная плазменная резка
Здесь режущим инструментом является струя из плазмы, идущая из сопла с огромной скоростью. Что же касается дуги, то она формируется между наконечником плазмотрона и электродом.
Эта технология применяется в работе с материалами, которые плохо проводят ток. Это неметаллы, к примеру, камень.
Еще один принцип классификации резаков на аппараты ручной или машинной резки.
Ручные воздушно-плазменные резаки
Это самые демократичные модели и по цепне, и по сфере применения. Нельзя сказать, что они стали эдакими домашними котиками для резки новогодней фольги, но в автомастерских, к примеру, они стали широко использоваться для резки деталей самого разного калибра.
Производительность у них не бог весть какая прежде всего потому, что резак находится в руках у оператора, которому приходится держать его на весу и вести по линии разреза. Понятно, что об идеальной точности и ровности разреза говорить не приходится.
Чтобы исправить это, можно использовать специальный упор. Этот упор размещают на сопле, придавливают к поверхности заготовки и таким образом ведут резак по линии разреза.
Стоимость ручного плазменного резака зависит от их функциональных возможностей, включая применяемую силу тока и максимальную толщину металла, которую можно будет с их помощью разрезать.
На рынке появились чрезвычайно интересные универсальные модели, с помощью которых можно как резать, так и варить металлические детали. Стоят они недешево, но вполне приемлемо: около 500 USD. Заметить такие модели можно с помощью маркировки.
Аппараты плазменной резки машинного типа
Данные модели практически всегда снабжены программным обеспечением, благодаря которому участие оператора из процесса исключено. Понятно, что сразу же повышаются производительность и общая эффективность работы аппарата. Ну а главная фишка – идеальная точность резки.
Дополнительный бонус от машинного резака – отсутствие какой-либо необходимости обрабатывать края после резки, они и так идеальные.
Для начала работы вводится схема, по которой будет произведена любая форма или фигура резки.
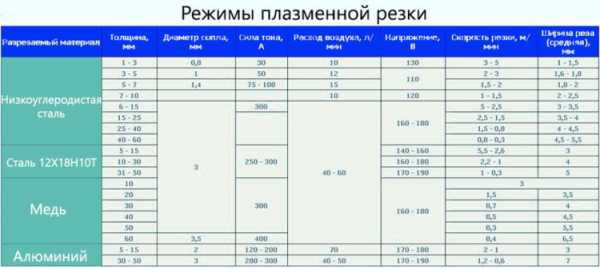
Режимы плазменной резки.
Стоимость машинных устройств на несколько порядков выше, чем у ручных аппаратов плазменной резки. Данные аппараты состоят из мощных трансформаторов и технического стола в виде ровной поверхности с направляющими.
Цена зависит от комплектующих, габаритов и функциональности программного обеспечения. Так или иначе стоимость любой машинной модели будет находиться в диапазоне 3000 – 20000 USD.
Водно-плазменные резаки
Помимо аппаратов воздушно-плазменной резки существуют и модели водно-плазменного типа. В этом случае вода играет роль охладителя, а плазму образует не воздух, а водяной пар.
Устройства воздушно-плазменной резки – отличная опция благодаря низкой цене и компактности, но у них есть существенный недостаток – ограничения в толщине разрезаемого металла, этот лимит составляет всего 80 мм.
А вот мощность водно-плазменных резаков намного выше, и поэтому позволяет работать с массивными деталями. Если говорить о пресловутой стоимости, то да, эти модели дороже.
Принцип работы у них совсем другой. Вместо воздуха под давлением используется водяной пар. При таком раскладе не нужен компрессор для воздуха, не нужны баллоны с газом – водяной пар отлично справляется со всеми задачами самостоятельно.
Дело в том, что по консистенции водяной пар значительно более вязкий, чем воздух. В результате этой «счастливой» вязкости водяного пара нужно намного меньше.
При прохождении через плазмотрон электрической дуги в него подается вода, которая мгновенно начинает испаряться. Пар ионизируется под действием загоревшейся электрической дуги и рабочей жидкости, которая поднимает катод полюса с минусом от катода полюса сопла с плюсом.
Одна из самых известных моделей водно-плазменного типа – аппарат «Горыныч» со стоимость примерно 800 USD.
Физика процесса плазменной резки
Чтобы аппарат плазменной резки работал, нужны всего лишь воздух и электрическая энергия. На режущую часть аппарата подается ток с высокой частотой. В результате в плазмотроне формируется дуга с очень высокой температурой: около 8000°С.
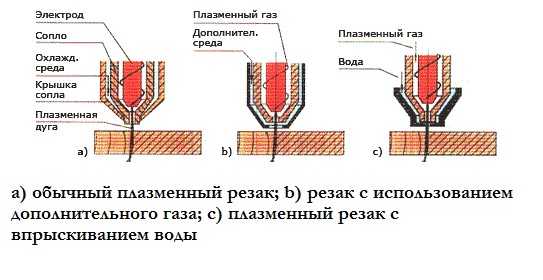
Разновидности плазменных резаков.
Туда же, в плазмотрон, поступает и проходит через раскаленную дугу воздух в сжатом состоянии, который впоследствии ионизируется. В результате этот воздух становится отличным проводником тока, он становится той самой плазмой.
Плазма под большим давлением выходит из сопла и разогревает металлическую деталь до начала плавления. Расплавленный металл частицами выдувается воздухом, выходящим из сопла под большим давлением. Это и есть та самая резка металла.
Скорость потока плазмы зависит от расхода воздуха: если его увеличить, скорость потока плазмы повысится. При силе переменного тока в 250 А скорость плазменного потока составляет примерно 800 м/сек.
Как устроен аппарат плазменной резки?
Главные элементы аппаратов плазменной резки металла – плазмотрон, источник электропитания и так называемый кабель-шланговый пакет для соединения с компрессором. В качестве источника питания могут быть использованы инвертор или трансформатор.
Плазмотрон
Это главная часть аппарата плазменной резки. В свою очередь, он состоит из сопла, электрода и изолятора. По своей форме это корпус с камерой цилиндрической формы и малым выходным каналом, в котором формируется дуга. Электрод находится с тыла камеры, его функция – возбуждение дуги.
Электроды
Это специальные расходники, сделанные именно для резки металла. Чаще их производят из циркония, тория или гафния. Самые распространенные – из гафния.
С бериллием и торием нужно быть поосторожнее – эти элементы обладают радиоактивным компонентом.
Все эти элементы отличаются тем, что на их поверхности формируются оксиды с тугоплавкими свойствами. Эти оксиды как раз и защищают электрод от разрушения.
Розжиг или возбуждение дуги напрямую между электродом и металлической заготовкой произвести сразу трудно. Поэтому первым делом разжигается промежуточная дуга между электродом и плазмотроном. Затем воздух под давлением проходит чрез дугу, ионизируясь и нагреваясь.
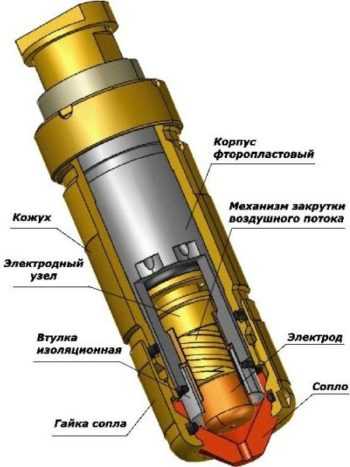
Схема устройства плазменного резака.
В итоге объем этого воздуха повышается в объеме во много раз, он превращается в поток плазмы. Плазма вырывается из суженого конца сопла с огромной скоростью и высочайшей температурой вплоть до 30000°С.
Такому потоку все по силам, в дополнение ко всему он обладает очень высокой теплопроводностью – практически такой же, как у металла заготовки, которую нужно резать.
Настоящая дуга – та самая, которая нужна, формируется при выходе плазмы из сопла плазмотрона. Теперь именно эта рабочая дуга является главным режущим фактором.
Сопло плазмотрона
Различается по диаметру, от которого будут зависеть функциональные возможности всего аппарата. Прежде всего эта зависимость касается объема ионизированного воздуха, выходящего из сопла: именно им обусловлены главные характеристики резака – скорости работы и охлаждения, ширина шага реза.
Чаще встречаются сопла с малым диаметром, не превышающим 3-х мм. Зато длина сопла больше – около 10-ти мм.
Защитные газы
Прежде всего эти газы образуют плазму, их даже называют плазмообразующими. Такие газы используются только в мощных промышленных аппаратах для резки толстых металлов. Чаще это гелий, аргон, азот и их различные смеси. Кстати, кислород сам по себе также является защитным и плазмообразующим газом. Он используется в резаках небольшой мощности для резки металлов не толще 50-ти мм.
В плазмотроне расходными материалами являются сопло и электроды. Их нужно менять в положенных сроки.
Преимущества метода плазменной резки
Плюсы этих устройств нужно хорошо знать, равно как и минусы, без которых не обходится ни одно техническое приспособление.
Прежде всего помним, что скромные бытовые задачи по резке металла вполне можно реализовать с помощью обычной болгарки и не заморачиваться с дорогим и непростым плазменным оборудованием.
Плазменный резак обладает следующими положительными свойствам:
- Высокая скорость рабочего процесса. Если сравнить ее с газовой горелкой, то скорость резки выше в шесть раз. Быстрее в природе только лазерная резка.
- Большая толщина металла, который он способен резать в отличие от болгарки.
- Плазменному резаку под силу любой тип металла. Для этого важно знать и верно выставлять необходимые режимы согласно спецификациям.
- Непродолжительные и несложные подготовительные работы. Не нужна зачистка поверхностей.
- Уникальная точность и ровность среза. Нет никаких наплывов, не нужны специальные упоры.
- Отсутствие каких-либо дефектов и деформаций металла благодаря невысокой температуре общего нагрева.
- Способность аппарата производить срезы любой формы, включая фигурные.
- Высокая безопасность процесса: нет баллонов с газом.
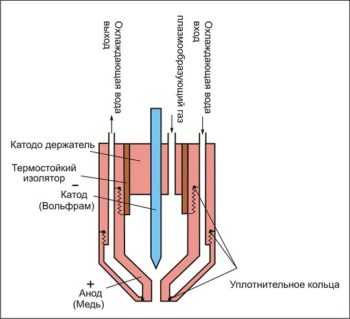
Чертеж устройства плазменного резака.
Недостатки плазменного резака:
- Высокая стоимость аппарата.
- Нет возможности резки одновременно несколькими резаками.
- Строгие требования к положению инструмента: плазма должна быть строго перпендикулярной поверхности заготовки. Сегодня выпускаются продвинутые аппараты, способные работать под углом от 20-ти до 50-ти градусов, но они еще дороже.
- Ограничение толщины разрезаемого металла – примерно до 10-ти с. В сравнении кислородная горелка режет металл толщиной в полметра.
При всех, казалось бы, значительных минусах плазморезы очень популярны. В небольших мастерских работают ручными моделями, которых предлагается на рынке огромное множество. Сегодня плазменная резка перестала быть недоступным элитарным методом работы.
Плазменный резак своими руками
Сразу заметим, что плазменной резки не обязательно быть профессиональным сварщиком, опыт в сварке здесь не нужен. Если вы задумали сделать такой аппарат своими руками, примите к сведению, что у вас появится возможность идеально резать кроме металла другие материалы: пластик, дерево, керамику и пр.
Плазменный резак – дорогое удовольствие даже в виде самых простых ручных моделей, поэтому сделать самодельный аппарат имеет смысл: овчинка выделки стоит.
Единственное, что нужно купить – это источник питания и сопло. Если вы все сделаете правильно, ваш аппарат не будет уступать заводским экземплярам по своим рабочим качествам.
Для образования плазмы нужен воздух, а для системы охлаждения нужна вода или тосол, которые заливаются в специальную емкость.
Стержень нужно брать вольфрамовый., с его помощью будет формироваться электрическая дуга. Все комплектующие всегда имеются в хозяйственных магазинах. Собрав все необходимое оборудование для плазменной резки металла, аппарат производится по схемам, которые представлены в сети в большом количестве.
Какой резак выбрать
Начнем с факта, известного любому сварщику, который распространяется и на плазменную резку: чем выше сила тока, тем выше скорость рабочего процесса. Есть и другие параметры, которые следует учитывать при выборе инструмента для своей работы.
Толщина и тип металла – один из главных критериев. В сети можно найти множество табличного материала с техническими характеристиками плазменных резаков в зависимости от них. К примеру, чтобы с успехом резать медный лист толщиной в 2 мм, вам понадобится устройство с допустимой силой тока в 12 А.
Важным правилом является обязательный «запас» силы тока: покупать резак помощнее, чем указывается в таблицах. Дело в том, что табличные параметры – это максимальные цифры, с этими значениями аппарат может работать лишь непродолжительное время.
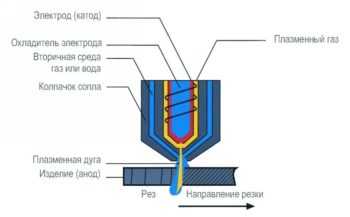
Схема работы плазменного резака.
Грамотнее всего выбор по трем критериям: скорости рабочего процесса, времени резки и мощности.
- Нужная рабочая мощность определяется с учетом толщины планируемого металла и его вида. К примеру, мощность в 90А позволит резать металл толщиной до 30-ти мм.
- Если металл толще, нужно выбирать резак с мощностью в диапазоне 80 – 180А.
- Диаметр сопла и выбор типа потока всегда зависит от типа разрезаемого металла.
- Важными параметрами выбора станка плазменного резака являются также номинальное первичное напряжение и сила тока.
- Нужно решить, какой тип аппарата вам нужен – универсальный или специального назначения.
- Проверка адекватности аппарата к электрической сети обязательна: можно ли его подключать к общей сети или нужна профессиональная с другим напряжением. Аппараты попроще работают только при 220 или 380В, фазы питания могут быть одно- и трехфазными.
- Скорость резки металла измеряется в см/мин.
- Еще один важный и показательный критерий – способность резака работать непрерывно в течение долгого времени, иными словами – продолжительность работы без перерыва. Если она указана как 50%, это значит, что аппарат после 5-ти минут непрерывной резки должен быть выключенным также 5 минут.
Полезные советы по покупке и уходу
Особенности выбора и ухода за резаком:
- Если есть выбор, всегда останавливайтесь на тех моделях, у которых есть евроразъем.В этих моделях не будет никаких проблем с подключением или удлинением кабель-шлангового пакета и других элементов между собой.
- На расходных материалах не экономим.Только качественные будут работать на идеальный рез и долговечность резака. Быстрее всего изнашиваются сопло и катод, следовательно, за стоянием этих элементов нужно следить с особой тщательностью.
- Резак – это резак, поэтому правила безопасности в данном случае имеют железобетонный характер.Нужно иметь защитный щиток, специальные очки. Имейте в виду, что плазменная резка – это брызги расплавленного металла. Поэтому вам не помешают и перчатки, и даже защитная обувь.
- Работа на максимальной мощности предопределяет последующую остановку в работе.Одна из важнейших технических характеристик станков плазменной резки металла – продолжительность их работы без перерыва.
- Если в вашем доме старая проводка, обязательно проверьте, как «подружится» ваш новый резак с вашей старой сетью.Скорее всего, дружбы не выйдет, это нужно принять во внимание.
tutsvarka.ru