Большая Энциклопедия Нефти и Газа. Шлифование валов
техника выполнения, необходимые материалы и инструменты, пошаговая инструкция работы и советы специалистов
Шлифовка валов или, в принципе, операция шлифования - это процедура обработки заготовки, которая заключается в применении режущего инструмента из абразивного материала. Поверхность после такой обработки представляет собой совокупность микроследов. Их оставляют абразивные зерна, имеющиеся на инструменте. Поверхность же готового изделия отличается минимальной шероховатостью.
Описание шлифовального приспособления
Шлифовка валов проводится с применением шлифовального круга. Данный круг представляет собой тело пористого типа, состоящее из большого количества абразивных зерен. Эти зерна скрепляются между собой связкой. Кроме того, между данными зернами и связками располагаются поры. Сами по себе зерна изготовлены из очень прочного материала, а их количество достигает десятков или даже сотен тысяч.
Что касается рабочего профиля круга для шлифовки валов, то он состоит из режущих кромок зерен абразивного типа. Они располагаются на разном удалении от поверхности. Кроме того, процесс шлифовки - это процедура, во время которой снимается стружка. Из-за того что происходит снятие стружки в большом количестве, это приводит не только к измельчению материала, но и к значительному выделению тепла в зоне контакта. Именно по этой причине данная операция осуществляется лишь при наличии постоянного поступления большого количество смазочно-охлаждающих веществ.

Общие виды шлифовки
На сегодняшний день выделяется три основных вида шлифования валов - это тонкое, предварительное, чистовое. При применении предварительного типа шлифовки удается достичь точности 8-9 по квалитету. Что касается второго важного фактора - шероховатости, то она составляет от 0,4 до 6,3 мкм. Проводить шлифовку валов чистового типа можно только после того, как заготовка пройдет термическую обработку. Такая процедура позволяет увеличить точность до 6-7 по квалитету и уменьшить шероховатость до 0,2-3,2 мкм. Наиболее точный метод - это тонкое шлифование, которое позволяет достичь шероховатости в 0,025-0,1 мкм. Процесс также делится на два вида - это круглое и бесцентровое.
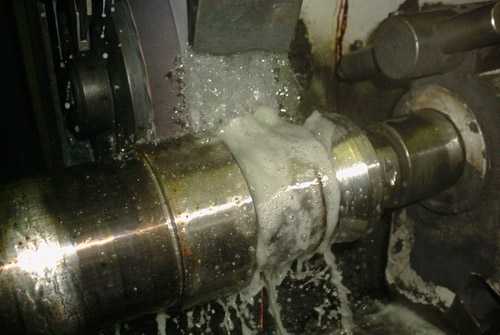
Шлифовка круглого типа
Станок для шлифовки шеек коленчатого вала или для любых других изделий круглого и цилиндрического типа выполняется на круглошлифовальных станках. При этом заготовка будет монтироваться в центре, в патроне или цанге устройства. На сегодняшний день различают два основных вида выполнения круглого шлифования - это продольная подача и метод врезания.
Что касается первого типа, то это процедура, которая проходит при помощи возвратно-поступательных перемещений. В данном случае перемещается деталь относительно шлифовального круга.
Шлифовка методом врезания осуществляется кругом, ширина которого должна быть больше, чем длина участка, который необходимо обработать. В таком случае круг будет иметь подачу лишь поперечного типа. Если использовать фасонный круг, то можно обрабатывать несколько деталей одновременно. Так как данный метод является более производительным, чем с продольной подачей, то его применяют гораздо чаще на крупносерийных и массовых производствах.
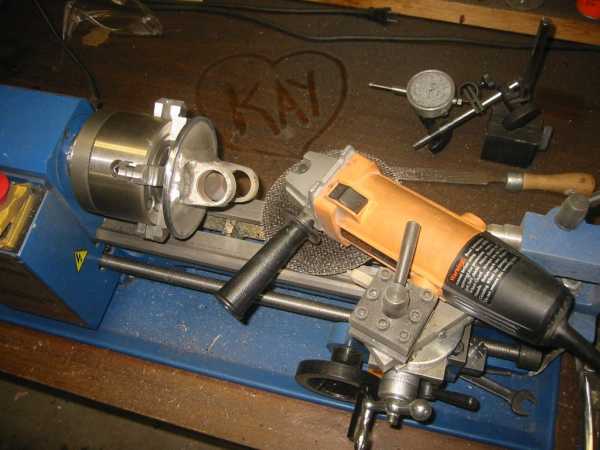
Бесцентровое шлифование
Что касается операции с продольной подачей, то она используется для обработки гладких валов. Процедура врезания применяется для обработки валов, имеющих буртик. Данным способом можно обрабатывать детали, которые характеризуются конической поверхностью. Для этого обычно применяется ведущий круг, заправленный на конус.
Стоит добавить, что при использовании метода резания круг постепенно теряет форму и режущую способность. Довольно часто это называют засаливанием круга. Для того чтобы вернуть круг в первоначальное состояние и тем самым вернуть его эксплуатационные характеристики на прежний уровень, используется процедура правки. Данная процедура осуществляется алмазами в оправах, алмазными карандашами и т.д. Сам по себе процесс правки не влияет на шлифовку, но если провести его некачественно, то характеристики круга ухудшатся, а значит, он будет хуже проводить операцию.
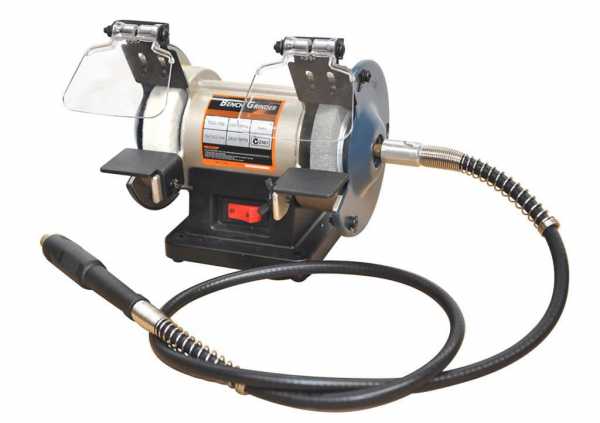
Станки для коленчатого вала
На сегодняшний день хорошим решением будет использовать станок для шлифовки коленчатых валов AMC-SCHOU.
Данное оборудование изготавливается из сверхпрочных отливок. Устройство обладает гидравлическим подводом круга, а также фиксирующими штифтами. Отличительная особенность прибора заключается в достаточно быстром регулировании подачи круга, которое осуществляется без обратной реакции.
Основная процедура, которая требуется при ремонте коленвала - это шлифовка. Данная операция позволяет исправить геометрию устройства, исправить сколы, повысить ресурс двигателя, а также снизить риск появления новых проблем.
Шлифовка шеек коленчатого вала в настоящее время позволяет устранять задиры и износы. Сам по себе процесс шлифовки данного приспособления - это опция, которая требует наличия специального станочного оборудования, а также высоких навыков специалиста.
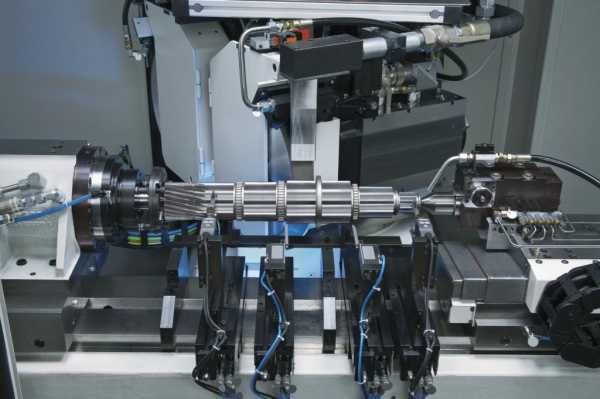
Шлифовка рулевой рейки
Шлифовка рулевого вала - это также достаточно распространенная операция. Специалисты рекомендуют применять ее лишь в том случае, если ржавчина на приспособлении поверхностного типа. Кроме того, максимальное уменьшение диаметра допускается не более 0,1 мм. В том случае, если коррозия считается глубокой, то допускается стачивание детали на 0,5 мм, не более. Если шлифовка происходит самостоятельно, то очень важно, чтобы рабочая зона вала была идеально отшлифована. Чаще всего при ручной обработке для этого используется наждачная бумага. Обычно обработка начинается при использовании очень грубой бумаги Р80. Далее зернистость уменьшается, а для финальной обработки вовсе используется наиболее мелкая наждачная бумага.
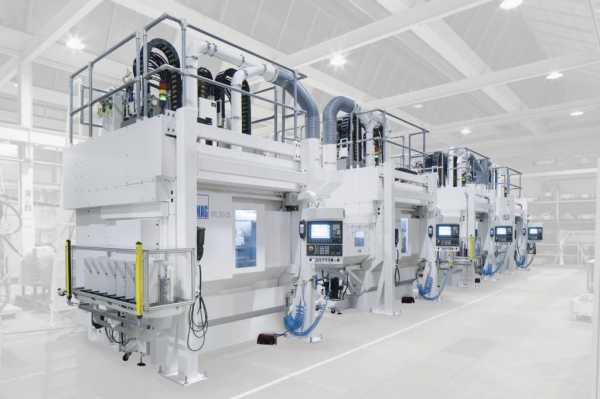
Заводские работы
Что касается шлифовки вала рулевой рейки в мастерской или на производстве, то для этого используется специальный станок, которым должен управлять опытный токарь. При этом важно знать, что во время работы необходимо постоянно контролировать отклонение формы. Оно должно идти в соответствии с нормативными документами. Прежде чем начать ремонт, необходимо провести визуальный осмотр детали, чтобы сделать вывод о целесообразности проведения шлифовки вала.
На сегодняшний день достаточно важным аспектом процедуры стала ее стоимость. Она зависит от таких факторов, как тип штока, объем работы и толщины корродированного слоя. Основным преимуществом шлифовки силовых валов реек в мастерских стало то, что у них имеются стенды для проверки работоспособности изделия. Если появляются какие-либо недочеты, то есть возможность их моментального устранения.
fb.ru
Шлифование - вал - Большая Энциклопедия Нефти и Газа, статья, страница 1
Шлифование - вал
Cтраница 1
Шлифование валов производится на центровых и бесцентровых шлифовальных станках. Центровое шлифование осуществляется на круглошлифовальных ставках моделей 3151, 316М, 3115 и др. Скорость вращения детали при обычном шлифовании находится в пределах 25 - 30 м / мин, а при скоростном в два раза больше. Большое значение для точности при центровом шлифовании имеет состояние опорных поверхностей центровых отверстий. Они долж-ны быть выполнены очень тщательно, так как погрешности центров сказываются на точности детали. [1]
Шлифование валов производят на круглошлифоваль-ных и бесцентрово-шлифовальных станках соответственно 6-му квалитету. При обработке валов на круглошлифовальных станках технологической базой являются центровые отверстия на торцах заготовки. [2]
Шлифование валов выполняют круглым или бесцентровым способами, причем подача может быть продольной или поперечной. Продольную подачу применяют для шлифования длинных валов, а поперечную ( врезание) - для коротких. [3]
Шлифование вала в соответствии с размером отверстия производится различными способами. [4]
Метод шлифования вала по сопрягаемой детали применяется в зарубежной машиностроительной промышленности. Он используется в сопряжениях деталей насосов и других гидромеханизмов, шарико - и роликоподшипников и пр. Он может частично заменить в серийном и мелкосерийном производстве применяемый в настоящее время метод селективной сборки. [5]
Для правильного шлифования вала необходима выверка опорных подшипников, чтобы исключить биение вала. Шлифовальный круг 3 устанавливают по верхней образующей шейки вала 2, а вал компрессора вращают вручную в сторону, противоположную вращению шлифовального круга. В ходе шлифования осуществляют контроль за центровкой вала по его обработанной нерабочей поверхности. Размер, до которого необходимо шлифовать шейки вала, определяется наименьшим диаметром шеек, причем допуск на отклонения диаметра шеек одного вала друг от друга не должен превышать 0 05 мм. Если ремонт шеек вала осуществлялся несколько раз, то перед последующим ремонтом необходимо производить проверочный расчет шеек на прочность. Приблизительно считают, что не следует уменьшать диаметр вала больше, чем на 3 % от его начального размера. [6]
Для правильного шлифования вала необходима выверка опорных подшипников, чтобы исключить биение вала. Шлифовальный круг 3 устанавливают по верхней образующей шейки вала 2, а вал компрессора вращают вручную в сторону, противоположную вращению шлифовального круга. В ходе шлифования осуществляют контроль за центровкой вала по его обработанной нерабочей поверхности. Размер, до которого необходимо шлифовать шейки вала, определяется наименьшим диаметром шеек, причем допуск на отклонения диаметра шеек одного вала друг от друга не должен превышать 0 05 мм. Если ремонт шеек вала осуществлялся несколько раз, то перед последующим ремонтом необходимо производить проверочный расчет шеек ка прочность. Приблизительно считают, что не следует уменьшать диаметр вала больше, чем на 3 % от его начального размера. [7]
Для правильного шлифования вала необходима выверка опорных подшипников, чтобы исключить биение вала. В ходе шлифования осуществляют контроль за центровкой вала по его обработанной нерабочей поверхности. Размер, до которого необходимо шлифовать шейки вала, определяется наименьшим диаметром шеек, причем допуск на отклонения диаметра шеек одного вала друг от друга не должен превышать 0 05 мм. Если ремонт шеек вала осуществлялся несколько раз, то перед последующим ремонтом необходимо производить проверочный расчет шеек на прочность. Приблизительно считают, что не следует уменьшать диаметр вала больше, чем на 3 % от его начального размера. [8]
При шлифований многоступенчатого вала ( 2 - 3 ступени) контроль осуществляется несколькими рычажными накидными скобами, каждая из которых настроена на определенный размер. Все скобы расположены на поворотной головке / / соответственно размерам ступеней вала. [9]
Перед шлифованием вала проверяют его центровку валовым индикатором, а горизонтальность положения - валовым уровнем. Если обнаружится биение вала в размере, превышающем допускаемые пределы ( 0 03 - 0 04 мм) или непараллельность оси вала свыше 0 02 мм на 100 мм длины шейки, шлифовать вал нельзя, так как нарушится соосность вала. Перед шлифованием вала, чтобы исключить его биение, необходимо выверить опорные подшипники. [10]
При шлифовании валов со шлицами или шпоночными канавками могут быть применены обычные трехконтактные индикаторные скобы, у которых рабочие поверхности опор имеют длину не менее двойного шага шлицев. [12]
При шлифовании валов по 4-му классу точности с посадками Х4, Л4, Ш4 допускается уменьшение припуска, а при шлифовании валов по прессовым посадкам 3 и 4-го классов точности - увеличение припуска на значение верхнего отклонения данной посадки, если эта величина составляет не менее 20 % припуска. [13]
При шлифовании валов следует отличать периферическую подачу. [14]
При шлифовании прямобочных шлнцевых валов иногда получается поднутрение их зубьев. [15]
Страницы: 1 2 3 4
www.ngpedia.ru
Способы обработки валов
За очень редкими исключениями обработка всех видов валов строится при применении центровых станков и в этом случае технология состоит из следующих операций: отрезание заготовок, подрезание торцов и центрирование, в дальнейшем производятся токарные операции на центровых токарных станках, чаще всего на многорезцовых станках стандартного типа, после вытачивания заготовки выполняется операция рифления, а затем все шлифовальные операции, фрезерование шпоночных канавок производится чаще всего перед операциями шлифования вала.
После окончания всей механической обработки валов приходится проводить слесарную зачистку шпоночных канавок, вследствие их искажения по ширине после шлифования из-за затягивания кромок. Поэтому некоторые заводы предпочитают производить фрезерование шпоночных канавок, в особенности если выполняются канавки для полукруглых шпонок после шлифования вала. В этом случае, вследствие некоторого поднятия кромок, также приходится выполнять операцию ручной зачистки, т. е. снятие фасок, однако эта операция менее трудоемка, чем в первом случае, кроме того, уменьшается опасность порчи вала при зачистке.
Вся токарная обработка вала производится, как правило, в две установки на многорезцовых токарных станках, обтачивая за каждую установку часть вала. Кроме того, в зависимости от конструкции вала и состояния оборудования, производят еще иногда чистовое протачивание вала и несколько коротких токарных операций, носящих характер доделки, в том числе подрезки торцов выточки галтелей, канавок ц т. д.
Операция накатывания рифления зачастую производится на обычном токарном станке, при помощи одного или двух накатных роликов, укрепленных в специальной державке. Ролики производят накатывание при продольной подаче будучи прижатыми к валу в такой степени, чтобы за один проход образовывалось рифление полного профиля.
Операции шлифования производятся на обычных центровых круглых шлифовальных станках. Большинство поверхностей шлифуются при продольном перемещении изделия по отношению к кругу и лишь в отдельных случаях применяется более производительный способ шлифования широкими кругами, в соответствии с шириной обрабатываемой поверхности, при поперечных подачах.
Фрезерование шпоночных канавок производится на простых горизонтальных фрезерных станках. При изготовлении канавок для шпонок с большим успехом применяются небольшие ручные фрезерные станки с рычажным управлением. Несмотря на свою простоту и примитивность, такие фрезерные станки оказываются очень удобными и высокопроизводительными при подобного рода кратковременных операциях.
При изготовлении длинных и тонких валов перед шлифованием вводится операция правки, производимая либо на прессах с ручным или механическим приводом, либо на малых гидравлических или пневматических прессах. Контроль всех размеров в процессе производства осуществляется при помощи жестких предельных калибров и шаблонов. За исключением проверок на биение и при операции правки индикаторные приспособления почти не применяются.
Недостатки описанной технологии сводятся в основном к следующему:
1) применяемое оборудование и способы изготовления обладают невысокой производительностью и отстали от современных способов массового производства;
2) в качестве исходного материала применяется в большинстве случаев сталь в виде черных некалиброванных прутков, что приводит к необходимости протачивать также и среднюю часть вала, имеющую наибольший диаметр. Одно это обстоятельство, увеличивая трудоемкость обработки приводит к потерям материала, минимум в 15—20%;
3) операции отрезки заготовки, протачивания торцов и засверливания центров производятся на обычном оборудовании, предназначенном для работы в серийном производстве и поэтому обладающем невысокой производительностью, при сравнительно большом удельном весе ручного вспомогательного времени. Так, например, засверливание центров чаще всего выполняют на вертикальных сверлильных станках в два перехода, т. е. каждую сторону вала самостоятельно, поворачивая вал;
4) токарные операции тоже производятся на недостаточно производительном оборудовании универсального назначения. Особым недостатком применяемых многорезцовых станков является их малая приспособленность к быстрой смене настройки с одного типоразмера вала на другой, что приводит к большим потерям времени при переналадках. Особо следует остановиться на применяемом способе производства рифления. При существующем способе накатывания на токарных станках предварительно проточенных валов невозможно выдержать достаточно точно размеры диаметров и избежать недопустимых колебаний в размерах и отступлений от необходимой прямолинейности рифления. Последнее требуется для правильной посадки сердечника ротора (якоря). Наконец, практикуемый способ шлифования узкими кругами при продольной подаче является малопроизводительным. Нужно отметить, что, как правило, даже там, где это вполне возможно и рационально, как, например, при шлифовании шеек, станки не снабжаются приспособлениями для измерения шлифуемых размеров в процессе работы, т. е. на ходу станка, а для проверки размеров станок останавливается.
Следует указать, что очистка и промывка вала в процессе обработки, в частности перед окончательной шлифовкой, и в готовом виде в действующей технологии не предусматривается. В таком виде выглядит самый распространенный процесс центровой обработки валов.
Существует, однако, и совершенно отличный процесс бесцентровой обработки валов, обладающий рядом преимуществ по сравнению с центровым способом и приводящий к значительному уменьшению трудоемкости обработки. Этот процесс с большим успехом применяется при изготовлении валов в производстве автотракторного электрооборудования.
При бесцентровом способе исходным материалом обязательно должен быть калиброванный и тщательно выправленный пруток. Первая операция — полное вытачивание вала производится на прутковом автомате. Для того чтобы при протачивании избежать искривления длинных валов, последние поддерживаются при помощи роликовых люнетов. В последующие операции обработки валов, производится предварительное шлифование на бесцентровых шлифовальных станках, причем первые операции выполняются при сквозной подаче изделий, на двух-трех последовательно стоящих станках.
В дальнейшем производится накатывание рифления. Эта операция в производстве автотракторного электрооборудования выполнялась отлично от того, как это делается на других электромашиностроительных заводах. Для обеспечения правильности размеров диаметров и соблюдения одинаковой прочности запрессовки различных валов последние перед накатыванием обязательно проходили шлифование по своему диаметру при этом размеры выдерживались по третьему классу точности. Операция накатывания выполняется на мощном резьбонакатном станке горизонтального типа. Наряду с очень высокой производительностью этого способа накатывания, обеспечивается также полная прямолинейность рифления, что в некоторых конструкциях машин является безусловно, необходимым.
Действительно, если на рифленый вал производится на прессовка сердечника ротора, то отдельные его листы в процессе прессования неизбежно стремятся следовать форме и направлению рифления. Поэтому, если рифления имеют хотя бы очень незначительные искривления и идут по крутой спирали, то все пазы сердечника должны повторить кривизну рифлений.
Известно, что искажения в форме пазов совершенно недопустимы, особенно при машинной обмотке якоря. Не следует думать, что если якорь электрической машины должен иметь косые пазы, то и рифление может иметь соответствующий наклон. В действительности у всех без исключений конструкций якорей и роторов рифление должно быть возможно более прямым, а необходимый скос пазов получается в процессе запрессовки применяя соответствующие наклонные направляющие ножи в приспособлении для прессования.
Часто отсутствие на заводе возможности изготовить валы с абсолютно прямым рифлением вынуждает пользоваться другими, значительно более дорогими способами крепления сердечника на валу и, в частности, применять для этой цели шпонки.
Для рифления валов необязательно применять станки с плоскими плашками и поступательным рабочим ходом, а можно с успехом пользоваться и другими типами резьбонакатного оборудования. После накатывания рифления валы проходят шлифовальные операции на бесцентровых шлифовальных станках, частично при продольной, но, главным образом, при поперечной подаче.
Одновременно обязательно шлифуется также и наружный диаметр рифленой поверхности с целью выдержать размер в пределах третьего класса точности и несколько притупить верхушки отдельных зубчиков, обеспечив тем самым одинаковую величину натяга и высокое качество прессового соединения.
Способ бесцентровой обработки требует меньшего числа операций чем центровой, и, в частности, отпадают все заготовительные операции — отрезание заготовки, протачивание ее торцов и центрирование. Применяемое в этом случае оборудование обладает также более высокой производительностью. Прутковый автомат для вытачивания вала требует меньшего обслуживания со стороны рабочего, чем многорезцовый токарный станок. Качество валов, полученных обоими способами, примерно одинаково. При бесцентровой обработке валов, имеющих несколько уступов по длине, величины их биений могут быть выдержаны в пределах требуемых допусков.
Возможно, Вас так же заинтересует:mse-online.ru
Припуски на шлифование валов
Припуски на шлифование валов
Диаметр вала d в мм | Характер шлифования | Характер вала | Длина вала L в мм | ||||||||
до 100 | св, 100 до 250 | св, 250 до 500 | св, 500 до 800 | св, 800 до 1200 | св, 1200 до 2000 | ||||||
Припуск 2a на диаметр в мм | |||||||||||
До 10 | Центровое | Сырой | 0,2 | 0,2 | 0,3 | - | - | - | |||
Закаливаемый | 0,3 | 0,3 | 0,4 | - | - | - | |||||
Бесцентровое | Сырой | 0,2 | 0,2 | 0,2 | - | - | - | ||||
Закаливаемый | 0,3 | 0,3 | 0,4 | - | - | - | |||||
Св. 10 до 18 | Центровое | Сырой | 0,2 | 0,3 | 0,3 | 0,3 | - | - | |||
Закаливаемый | 0,3 | 0,3 | 0,4 | 0,5 | - | - | |||||
Бесцентровое | Сырой | 0,2 | 0,2 | 0,2 | 0,3 | - | - | ||||
Закаливаемый | 0,3 | 0,3 | 0,4 | 0,5 | - | - | |||||
Св. 18 до 30 | Центровое | Сырой | 0,3 | 0,3 | 0,3 | 0,4 | 0,4 | - | |||
Закаливаемый | 0,3 | 0,4 | 0,4 | 0,5 | 0,6 | - | |||||
Бесцентровое | Сырой | 0,3 | 0,3 | 0,3 | 0,3 | - | - | ||||
Закаливаемый | 0,3 | 0,4 | 0,4 | 0,5 | - | - | |||||
Св.30 до 50 | Центровое | Сырой | 0,3 | 0,3 | 0,4 | 0,5 | 0,6 | 0,6 | |||
Закаливаемый | 0,4 | 0,4 | 0,5 | 0,6 | 0,7 | 0,7 | |||||
Бесцентровое | Сырой | 0,3 | 0,3 | 0,3 | 0,4 | - | - | ||||
Закаливаемый | 0,4 | 0,4 | 0,5 | 0,5 | |||||||
Св. 50 до 80 | Центровое | Сырой | 0,3 | 0,4 | 0,4 | 0,5 | 0,6 | 0,7 | |||
Закаливаемый | 0,4 | 0,5 | 0,5 | 0,6 | 0,8 | 0,9 | |||||
Бесцентровое | Сырой | 0,3 | 0,3 | 0,3 | 0,4 | - | - | ||||
Закаливаемый | 0,4 | 0,5 | 0,5 | 0,6 | - | - | |||||
Св. 80 до 120 | Центровое | Сырой | 0,4 | 0,4 | 0,5 | 0,5 | 0,6 | 0,7 | |||
Закаливаемый | 0,5 | 0,5 | 0,6 | 0,6 | 0,8 | 0,9 | |||||
Бесцентровое | Сырой | 0,4 | 0,4 | 0,4 | 0,5 | - | - | ||||
Закаливаемый | 0,5 | 0,5 | 0,6 | 0,7 | - | - | |||||
Св.120 до 180 | Центровое | Сырой | 0,5 | 0,5 | 0,6 | 0,6 | 0,7 | 0,8 | |||
Закаливаемый | 0,5 | 0,6 | 0,7 | 0,8 | 0,9 | 1,0 | |||||
Бесцентровое | Сырой | 0,5 | 0,5 | 0,5 | 0,5 | - | - | ||||
Закаливаемый | 0,5 | 0,6 | 0,7 | 0,8 | - | - | |||||
Св.180 до 260 | Центровое | Сырой | 0,5 | 0,6 | 0,6 | 0,7 | 0,8 | 0,9 | |||
Закаливаемый | 0,6 | 0,7 | 0,7 | 0,8 | 0,9 | 1,1 | |||||
Св.260 до 360 | Центровое | Сырой | 0,6 | 0,6 | 0,7 | 0,7 | 0,8 | 0,9 | |||
Закаливаемый | 0,7 | 0,7 | 0,8 | 0,9 | 1,0 | 1,1 | |||||
Св.360 до 500 | Центровое | Сырой | 0,7 | 0,7 | 0,8 | 0,8 | 0,9 | 1,0 | |||
Закаливаемый | 0,8 | 0,8 | 0,9 | 0,9 | 1,0 | 1,2 |
Примечание:
Для условий мелкосерийного или индивидуального производства величина припуска определяется умножением табличной величины на коэффициент К=1,2 с округлением до десятых в сторону увеличения.
Например: 0,4 х 1,2 = 0,48 . Принимаем 0,5. При этом допуск на предварительную обработку устанавливается по 4-му классу точности С4.
osntm.ru
Шлифование шеек коленчатых валов - Шлифовальные станки
Шлифование шеек коленчатых валовКатегория:
Шлифовальные станки
Шлифование шеек коленчатых валовКоленчатый вал служит для восприятия усилий от шатунов, свя-пнных с поршнем двигателя, и передачи этих усилий на трансмиссию автомобиля или трактора. Таким образом, коленчатый вал преобразует переменное возвратно-поступательное движение поршней во вращательное. В коленчатом вале подвергаются шлифованию коренные и шатунные шейки, при этом должны быть выдержаны допуски на диаметр 6—10 мкм, некруглость и нецилиндричность 3 мкм, шероховатость Ra = 0,63 мкм, непараллельность осей коренных и шатунных шеек 6—8 мкм.
Шлифование шеек коленчатых валов представляет значительные трудности из-за его сложной конфигурации, неуравновешенности, ограниченности шейки двумя бортами, большего отношения длины вала к диаметру шеек и поэтому пониженной его жесткости. Коренные шейки шлифуют на круглошлифовальных станках большой мощности. Для предварительного шлифования коренных шеек применяют многокруговые шлифовальные полуавтоматы для одновременной обработки всех шеек. Шлифование на автоматизированных многокруговых станках в сравнении с однокруговыми имеет следующие преимущества: достигается соосность шлифуемых поверхностей, что особенно важно для обработки коленчатых и кулачковых валов, стабилизируется шероховатость обработанной поверхности, требуется меньше оборудования и производственных площадей.
При обработке на многокруговом станке деталь устанавливается центровыми отверстиями в хвостовике и фланце. В осевом направлении деталь базируется по упорному торцу. Деталь приводится во вращение планшайбой со специальным поводковым пальцем, который заходит в отверстие на фланце коленчатого вала. Цикл обработки на многокруговых станках следующий. Деталь устанавливается в призмах, расположенных на столе станка, и нажатием кнопки «Пуск цикла» подается команда на подвод упора осевой ориентации детали. Механизм осевой ориентации детали установлен на столе станка и работает с помощью гидравлики. Для ориентации детали шток поршня выдвигается вперед, упирается в базовый торец коленчатого вала и перемещают его вперед. Затем центр передней бабки прижимает вал к торцу штока и вал устанавливается в осевом положении. От команды упора подводится Центр передней бабки, и деталь фиксируется между упором и подведенным центром. В конце хода пиноли передней бабки подается команда на подвод центра задней бабки. Пиноль задней бабки вместе- с центром подводится к детали с помощью пружины, тарированной на соответствующее усилие зажима. Деталь зажимается в центрах, а упор отодвигается в исходное положение. Одновременно с отводом упора подается команда на быстрый подвод шлифовальной бабки. В начале быстрого подвода с помощью конечного выключателя включается вращение детали. В конце быстрого подвода нажатием на конечный выключатель включается механизм вреза. ния и происходит черновая подача кругов, скорость которой регулируется дросселем чернового врезания. Нажатием на микропереключатель черновая подача отключается и после выхаживания включается чистовая подача, скорость которой регулируется дросселем. Одновременно с включением чистого врезания происходит подвод люнетов и скобы измерительно-управляющего устройства (ИУУ). По окончании чистовой подачи через реле времени включается микроподача, величина одного импульса (перемещения шлифовальной бабки) составляет 1 мкм. Импульсная подача происходит до тех пор, пока ИУУ не подаст команду на отвод шлифовальной бабки, после достижения заданного размера. При этом происходит отвод шлифовальной бабки, останов детали, отвод люнетов и ИУУ. По окончании отвода подается команда на отвод центров, деталь разжимается и ложится на установочные призмы. Правка кругов производится автоматически. Включение правйльного прибора производится от реле счета импульсов, настраиваемого на определенное число обработанных валов.
На многокруговых полуавтоматах для шлифования коренных шеек применяют круги диаметром 900 мм, частота вращения обрабатываемой детали 70, 100, 150 об/мин. Мощность электродвигателя шлифовальной бабки 30 кВт.
Для шлифования шатунных шеек коленчатых валов применяют полуавтоматы модели JIT2-12. При обработке шатунных шеек базой служат предварительно прошлифованные коренные шейки. Для углового базирования коленчатого вала предусматривается специальная площадка на противовесе. Шлифование производится методом врезания мерным по ширине кругом диаметром 1060 мм я высотой 40—90 мм. Скорость шлифовального круга 50 м/с. Мощность электродвигателя круга 22 кВт. Частота вращения детали 60 об/мин. Пределы регулирования поперечных подач шлифовальной бабки 0,05—30 мм/мии. Пределы скоростей перемещения стола от гидропривода 0,15—5,5 м/мин. Величина быстрого подвода шлифовальной бабки от гидропривода 125 мм.
Полуавтоматический цикл работы станка модели ЛТ2-12 с ИУУ осуществляется в такой последовательности: осевая ориентация, зажим изделия в патронах, быстрый подвод шлифовальной бабки, включая вращение изделия и насоса СОЖ, шлифование заплечиков шатунной шейки (плечевая подача), черновая подача, выдержка времени 2—3 с, ввод люнета и ИУУ, чистовая подача, выдержка времени 2—3 с, импульсная микроподача, окончание цикла шлифования шейки, отвод шлифовальной бабки, останов вращения детали, отвод люнета и ИУУ, перемещение стола в положение для шлифования очередной шатунной шейки, автоматический разворот изделия на требуемый угол.
Механизм поперечных подач смонтирован на корпусе шлифо-альной бабки и состоит из шагового двигателя с гидроусилителем, закрепленным на плите. Вал гидроусилителя соединяется с червяком механизма быстрого подвода через шлицевую муфту. Управление шаговым двигателем осуществляется через пульт программного управления станком. С помощью механизма поперечных подач осуществляются следующие движения шлифовальной бабки: автоматические врезные черновые, чистовые и доводочные подачи, перегон по винту в обе стороны, подналадка на размер (импульсная в 1 и 10 мкм от руки), компенсация износа круга при правке. Шаговый двигатель за один оборот делает 240 шагов. Величины подач и величины износа круга при правке набираются декадными переключателями на пульте программного управления шаговым двигателем.
Механизм автоматического разворота коленчатого вала смонтирован в правом зажимном патроне и приводится в действие от гидросистемы. Механизм осевой ориентации крепится на подвижной части люнета и предназначен для точной осевой установки шлифуемой шатунной шейки коленчатого вала относительно шлифовального круга.
Механизм регулирования постоянства скорости резания предназначен для поддержания постоянной скорости резания по мере износа шлифовального круга и установлен на правйльном приборе. Регулирование постоянства скорости резания происходит на всем диапазоне износа круга от 1060 до 750 мм. Ползунок переключателя перемещается по контактным пластинам и вводит то или иное сопротивление, необходимое для обеспечения поддержания постоянства скорости двигателя шлифовального круга.
Гидросистема станка выполняет следующие функции: перегон стола установочный при переходе с одной шлифуемой шейки на другую, и перемещение стола при предварительной правке периферии шлифовального круга; быстрый отвод и подвод шлифовальной бабки; подвод и отвод шлифовальной бабки с регулируемой скорости при предварительной правке торца шлифовального круга; блокировка механизма ручного перемещения стола при его перегоне; зажим детали; вывод стопора из делительной линейки; развод губок механизма осевой ориентации; разворот детали на 90°; вывод упора механизма точной угловой ориентации; вывод поводка; ввод и вывод рычага люнета; ввод и вывод скобы, ввод и вывод губок люнета; обеспечивает врезные подачи шлифовальной бабки гидроусилителя; подача алмазного ролика на шлифовальный круг; перемещение правйльного прибора; торможение вращения алмазного ролика; смазка подшипников шпинделя шлифовальной бабки; смазка опоры винта механизма быстрого подвода; смазка направляющих стола; откачка утечек из станины в гидроагрегат.
Коленчатый вал устанавливается в призмы патрона станка, при этом поводок механизма автоматического разворота вала входит б отверстие, являющееся угловой базой для шатунных шеек на фланце коленвала. В зону шлифования шатунной шейки вводится рычаг люнета с механизмом осевой ориентации, который осуществляет точную установку шатунной шейки относительно круга. Как только осуществляется осевая ориентация, происходит зажим коленвала в призмах патрона.
При нажиме кнопки «Пуск цикла» начинается автоматический цикл, включается вращение детали и быстрый подвод шлифовальной бабки. В конце быстрого подвода скорость бабки замедляется дросселем и включается плечевая подача, при которой происходит шлифование буртиков шатунной шейки. По окончании шлифования буртиков скорость шлифовальной бабки еще больше снижается, начинается врезная подача — черновое шлифование шейки. По окончании черновой подачи осуществляется выхаживание (2—3 с). В этот момент обе губки люнета подводятся до контакта со шлифуемой шейкой, вводится измерительная скоба. После окончания выхаживания включается чистовая подача.
Гидравлический правйльный прибор предназначен для автоматической правки шлифовального круга по периферии и двум радиусам. Правка производится алмазным роликом, описывающим движение по периферии круга, аналогичное движению щупа по копиру. Шпиндель алмазного ролика приводится во вращение от отдельного электродвигателя. Скорость перемещения ролика может устанавливаться в диапазоне 50—800 мм/мин. Алмазный ролик имеет диаметр 70 мм. Частота вращения ролика 2840 об/мин. Профильный круг одновременно шлифует заплечики, галтели и цилиндрическую часть шейки. Цикл работы прибора для правки включен в автоматический цикл работы станка. Правка осуществляется; после шлифования каждой шейки. После достижения размера а обрабатываемой шейки прибор активного контроля подает команду на отвод шлифовальной бабки и одновременно подается команда на включение в работу прибора для правки.
Рис. 2. Шлифование шеек коленчатого вала профильным кругом
На рис. 2 показан специальный патрон с гидравлическим зажимом предназначенный для установки и закрепления коленвала на операции шлифования шатунных шеек. Базирование детали происходит по пятой коренной шейке во вкладыше. Угловое ориентирование вала происходит по вспомогательной базовой площадке, профрезерованной на противовесе восьмой щеки. Этой площадкой вал прижимается к упору. Этим же упором вал приводится во вращение. Зажим детали происходит сухарем, прикрепленным к рычагу. Этот рычаг может поворачиваться вокруг оси на определенный угол. Усилие зажима от поршня гидроцилиндра через тягу передается рычагу, который своим вторым плечом через сухарь прижимает деталь к вкладышу. Ось коренной шейки смещена относительно оси вращения патрона с таким расчетом, чтобы ось вращения шатунной шейки совпадала с осью вращения патрона, т. е. на величину радиуса кривошипа. Отжим детали происходит с помощью пружины. При выпуске масла из правой полости цилиндра пружина отводит поршень вправо и через тягу поворачивает рычаг в обратную сторону, освобождая деталь. После обработки двух соосных шатунных шеек вал необходимо повернуть вокруг оси коренных шеек на угол 90° для совмещения оси двух других шатунных шеек с осью патрона. Для этой цели служит делительный механизм, который укрепляется в самом патроне. После освобождения от сил зажима вал поворачивают на угол 90° вместе с делительным диском. Диск имеет угловые выступы, расположенные через 90°. При повороте скошенная сторона выемки нажимает на собачку, которая, поворачиваясь вокруг своей оси, выходит из выемки и своими скосами скользит по наружной поверхности делительного диска. При этом пружина сжимается плунжером. При повороте на 90° собачка оказывается против выемки в диске и под действием пружины входит в выемку диска и фиксирует положение вала. Регулирование углового положения производится винтом и упором. Ввиду смещения осей вала и патрона, последний балансируется в сборе с валом с помощью свинцовой заливки.
Рис. 2. Специальный патрон для закрепления коленчатых валов
Принцип действия люнета со слежением за изменением размера представлен на рис. 3. В люнете штоки с опорными колодками перемещаются при уменьшении диаметра обрабатываемой поверхности от клиньев, выжимаемых пружинами. После окончания шлифования клин возвращается в исходное положение, преодолевая сопротивление пружины под действием поршня гидроцилиндра. Возникающие при шлифовании детали деформации воспринимаются штоками с опорными колодками и клиньями, т. е. происходит жесткое силовое замыкание.
Рис. 3. Схема действия следящего люнета
Читать далее:
Шлифование распределительных (кулачковых) валов
Статьи по теме:
pereosnastka.ru
Шлифование - длинный вал - Большая Энциклопедия Нефти и Газа, статья, страница 1
Шлифование - длинный вал
Cтраница 1
Шлифование длинных валов требует применения люнетов. Кулачки люнета делаются либо из твердых пород дерева с упором по торцам волокон дерева, либо из текстолита. В качестве охлаждения применяется эмульсия. [1]
Для шлифования длинных валов бесцентрово-шлифовальные станки должны иметь поддерживающие устройства с загрузочной и разгрузочной стороны. [3]
При шлифовании длинных валов этот способ является наиболее распространенным. [5]
При шлифовании длинных валов эта схема обработки является наиболее распространенной. [7]
При шлифовании длинных валов применяют люнеты. Точность шлифования длинных валов в значительной степени зависит от правильной наладки люнетов. Чтобы прошлифовать гладкие втулки, цанги, диски и другие детали с отверстием, применяют цанговые, раздвижные и гидропластмассовые оправки. [9]
Схема наладки при шлифовании длинных валов: / - шлифовальный круг; 2 - ведущий круг; 3 - склиз призматической формы; 4 - стойка; 5 - деталь; 6 - опорный, нож. [10]
Съема, сокращает время настройки и позволяет автоматизировать процесс шлифования длинных валов. [12]
Бесцентрово-шлифовальные станки обладают рядом преимуществ по сравнению с круглошлифовальными: 1) более высокой производительностью, так как при сквозном шлифовании процесс идет непрерывно без затрат вспомогательного времени; 2) не требуется центрование заготовок; 3) нет необходимости применять люнеты при шлифовании длинных валов; 4) достигается высокая точность обработки без повышенных требований к квалификации шлифовщика. Но при бесцентровом шлифовании нельзя достичь точной концентричности наружной шлифуемой поверхности и внутренней, если последняя была получена на предшествующих операциях, у ступенчатых валов нельзя шлифовать каждую шейку отдельно, так как не будет достигнута соосность шеек; настройка бесцентрово-шлифовальных станков, особенно при одновременном шлифовании нескольких шеек ступенчатых валов, требует значительной затраты времени, что окупается только при больших партиях заготовок. [13]
Бесцентрово-шлифовальные станки обладают рядом преимуществ в сравнении с круглошлифовальными, а именно: 1) более высокой производительностью, так как при сквозном шлифовании процесс идет непрерывно без затрат вспомогательного времени; 2) не требуется центрования заготовок; 3) нет необходимости применять люнеты при шлифовании длинных валов; 4) достигается высокая точность обработки без повышенных требований к квалификации шлифовщика. [14]
Шлифование н доводка сложных ответственных детален н инструмента с большим числом переходов и установок по 6 м квалптет ( 1 - - 2 - м классам точности) п зуборезного инструмента по 6 - й степени точности, требующих комбинированного крепления и точной выверки в нескольких плоскостях на шлифовальных станках различных типов и конструкций Шлифование и доводка наружных и внутренних фасонных поверхностей и сопряженных с криволинейными цилиндрических поверхностен, с труднодоступными для обработки н измерения местами. Шлифование длинных валов и винтов с применением нескольких люнетов Шлифование сложных ответственных крупногабаритных деталей и узлов на уникальном оборудовании. [15]
Страницы: 1 2
www.ngpedia.ru
2.2.9. Шлифование валов
Шлифование производится абразивными кругами при обильной подаче в зону резания СОЖ и является основным методом чистовой обработки наружных поверхностей. Различают предварительное, чистовое и тонкое шлифование. Предварительным шлифованием обеспечивают точность по 8-9 квалитету. Шероховатость поверхности составляет 0,4 – 6,3 мкм. Чистовое шлифование осуществляют после термической обработки. Им обеспечивают точность по 6 – 7 квалитету с шероховатостью поверхности 0,2 – 3,2 мкм. Более высокая точность достигается тонким шлифованием с шероховатостью поверхности 0,025 – 0,1 мкм. Шлифование делится на вида: круглое и бесцентровое.
Круглое шлифованиенаружных цилиндрических и конических поверхностей выполняют, на круглошлифовальных станках. Деталь устанавливается в центрах, патроне или цанге. Существует два основных метода круглого шлифования: с продольной подачей и методом врезания.
Шлифование с продольной подачейосуществляется возвратно-поступательным перемещением детали относительно шлифовального круга. На каждый двойной ход стола круг перемещается к центру заготовки на 0,005 – 0,02 мм. Схема шлифования с продольной подачей представлена на рис 2.75, а.
Шлифование методом врезанияпроизводится кругом, ширина которого больше длины обрабатываемого участка (рис. 2.75, б). В данном случае круг имеет только поперечную подачу. Одновременное шлифование нескольких поверхностей методом врезания может быть осуществлено фасонным кругом (рис. 2.75, в; г). Данный метод более производителен чем шлифование с продольной подачей, поэтому его применяют в массовом и крупносерийном производстве.
Бесцентровое шлифованиеосуществляется на бесцентрово-шлифовальных станках. Здесь также применяются два метода шлифования: с продольной подачей и врезанием.
Бесцентровое шлифование с продольной подачейприменяют для обработки гладких валов. Схема шлифования представлена на рис. 2.76, а; б. Деталь 2 при шлифовании не закрепляется, а свободно перемещается между двумя шлифовальными кругами вдоль своей оси. Круг 1 большего диаметра является шлифовальным, а круг 3 меньшего диаметра является ведущим. Этот круг устанавливается под углом 1 – 5о к оси шлифовального круга и вращает деталь с подачей в осевом направлении. Деталь опирается на нож 4 со скосом, благодаря которому она прижимается к ведущему кругу. Детали при шлифовании одна за другой поступают в зону обработки с одной стороны, а выходят с другой.
Бесцентровое шлифование врезанием применяют для обработки валов с буртиком. Схема шлифования представлена на рис. 2.76, в. Перед обработкой ведущий круг отводят на некоторое расстояние от опоры и устанавливают деталь на опору сверху или сбоку. Затем круг подводят к детали для обработки. Шлифование осуществляется с подачей ведущего круга к шлифовальному кругу. Этим методом можно шлифовать детали с конической поверхностью, применяя ведущий круг, заправленный на конус.
В процессе резания шлифовальный круг теряет форму и режущую способность, т.е. круг засаливается. Для восстановления формы и режущей способности шлифовальных кругов их подвергают правке. Правку осуществляют алмазами в оправах, алмазными карандашами, роликами и пр. Алмазный карандаш представляет собой абразивный инструмент, в котором мелкие алмазы, синтетические или естественные, закреплены в связке. Связка представляет собой затвердевший полимерный материал. Масса отдельных алмазов в карандаше находится в пределах 0,03 – 0,5 карата (1 карат равен 0,2 грамма). Алмазы в оправах могут также иметь искусственное или естественное происхождение. Они, как правило, крупнее, чем алмазы в карандашах. Их масса достигает 2 карат. На рис. 2.77, а представлена схема правки круга алмазом в оправе при шлифовании поворотного кулака. Правка производится периодически перемещением алмаза по копиру. Недостатком правки широких кругов по копиру является необходимость перерывов в работе станка для правки. Это время может составлять 10 – 15% от основного.
Правка круга алмазными роликами осуществляется также периодически, но одновременно по всей его образующей, т.к. форма роликов соответствует профилю круга. Это сокращает время правки в 2 – 3 раза. На рис 2.77, б представлен совмещенный эскиз для трех операций шлифования вала. На первых двух операциях, отмеченных позициями А и Б шлифуются шейки и прилегающие к ним торцовые поверхности. На третьей операции в позиции В на закаленном валу твердостью HRC60 производится прорезка кругами двух кольцевых канавок, что исключает их предварительное точение.
studfiles.net