Подготовка фундамента для токарных станков. Установка токарного станка
Фундамент для токарного станка
Токарный станок – оборудование требовательное к установке на фундамент. Для безопасности его использования для рабочего и минимизации поломок самого оборудования, особое внимание необходимо уделить подготовке фундамента.
Необычность фундамента под токарное оборудование заключается в том, что при его проектировании необходимо учесть подвод сжатого и подводку электропитания. Обязательны в системе болты заземления. Кроме самого станка на эту бетонную площадку, в зависимости модели, могут быть установлены:
- транспортёр, отводящий стружку от рабочего места;
- гидростанция с жёлобом подачи и отведения воды;
- электрошкаф.
Фундамент должен отвечать требованиям к установке станка, обозначенным в паспорте изделия. Существует несколько различных токарных установок, для каждой из них проект заливки разрабатывается индивидуально.
Необходимость крепления оборудования
Одним из основополагающих факторов для производства фундамента под станок является его назначение. Крепление станка к полу производится преимущественно в том случае, если предназначается он для изготовления деталей с точностью до микрон.
При условии, что оборудование мобильное и периодически перемещается, отдельный фундамент для него не требуется, для его установки необходим идеально ровный бетонный пол или подкладка из бетонной панели, толщиной около 15 см. Учитывая вес оборудования, вплоть до 30 тонн, о его устойчивости можно не беспокоиться.
Во избежание возникновения аварийных ситуаций в цеху, для токарного оборудования всё же необходим собственный фундамент с прокладкой трасс под коммуникационные составляющие, обеспечивающие его работоспособность. Металлические трубы под шланги для подачи воздуха, воды, и электричества с напряжением в 380 В, надёжно сохранят от деформации изолирующий слой и сами провода и шланги.
Высота площадки будет зависеть от диаметра труб и веса оборудования. Площадь фундамента рассчитывается под каждый элемент оборудования отдельно, отчего он может не иметь строгой четырёхугольной формы. Он может выглядеть созданным из отдельных элементов, составленных в единое целое. Несмотря на такую конструкцию, заливается он единой плитой, а не для каждого агрегата в отдельности.
Одним из требований к фундаменту для токарного станка или целого комплекса является выступ площадки из-под каждого узла со всех сторон одинаковой ширины.
Особенности заливки фундамента под токарный станок
На точность обработки на токарном станке оказывает вибрация. При малейшей погрешности в закладке фундамента токарного оборудования, вибрация рабочих частей может усиливаться, что приведёт к поломке сложного механизма.
Избежать подобного нежелательного эффекта поможет правильная проектирование и заливка фундамента. Начало работ должно начаться в конструкторском бюро, где будет составлен проект с указанием высоты, ширины, длины каждого элемента. Так же для большей прочности постамента необходимо равномерное распределение нагрузки, которое создаётся на 3 точки опор. Это отражается в проектно-строительной документации.
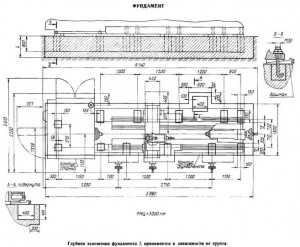
Чертеж фундамента
За пределы общей площади фундамента выносятся заглубляемые столбы, имеющие квадратное сечение, длина их сторон 50 см. Такие отметки осей применяются для создания платформ объёмом в 150 кубометров и больше.
Учитывая то, что устанавливается станок в цеху, где грунтовые воды, резкие перепады температур и вода не будут взаимодействовать с его фундаментом, достаточно использовать для заливки последнего марки цемента 110 — 140. Наполнителями для бетонов являются гравий, щебень и песок в определённой для каждой марки цемента пропорции.
Если вы нашли ошибку, пожалуйста, выделите фрагмент текста и нажмите Ctrl+Enter.
stankiexpert.ru
Монтаж токарного станка | Lathe.by
Подготовительные работы перед монтажом токарного станка
Токарный станок, как правило, поставляется в единой целостной упаковке или коробке. В зависимости от вида станка, его назначения, а, следовательно, веса и размера работы по монтажу также могут быть различными. После получения станка в производственный цех следует:
- произвести расчеты по величине и плотности опоры для станка;
- подготовить место для установки станка;
- правильно распаковать станок, используя чалки или другой гидравлический инструмент.
Основная задача токарного станка – это ровная, прочная устойчивая опора, необходимая для обработки металлов. Поэтому все работы по установке сводятся к обеспечению максимальной степени устойчивости, прочности и надежности. Очень важно погасить все возможные вибрационные эффекты, возможные в ходе выполнения работ.
Процедура правильной установки токарного станка
В зависимости от размера станка – небольшого, бытового, средней мощности или массивного промышленного, установку можно производить как на столе в первом случае, так и на заранее созданном бетонном фундаменте во втором случае. В каждом из вариантов главное вымерять уровнем все возможные отклонения от плоскости и максимально устранить их. При установке станка на пол, на бетонный фундамент, он крепится дополнительным слоем раствора в местах ножек и башмаков.
Кроме того, необходимо заранее побеспокоится о наличии специальных прорезиненных прокладок, дополнительно амортизирующих станок. Как правило, в большинстве комплектаций, они идут от производителя в упаковке, но по опыту отмечено, что наличие дополнительных никогда не помешает.
Финальные моменты монтажа токарного станка
После осуществления сборки станка (при необходимости) и установке станка на фундамент либо стол, затягивать анкерные болты. Важно также оценить паспортные характеристики, заданные на вырывание анкерных болтов из фундамента. Как правило, из этого значения нужно отбросить около 25% для максимально гарантированной прочности установки. Современные производители станков изготавливают крепежные болты из нержавеющих металлов, либо используя специальные оцинкованные покрытия. Не помешает также дополнительно обработать анкеры антикоррозийным материалом, особенно в местах возможного появления влаги.
После установки, последовательного затягивания анкеров следует ещё раз дополнительно вымерять все поверхности станка уровнем на момент отсутствия неровностей и перекосов. Если у Вас возникли вопросы по монтажу и требуются дополнительные пояснения на месте работ, то мы всегда рады предоставить услугу шефмонтажа. Наши специалисты выедут к Вам и дадут подробные консультации по вопросу правильной установки станка на каждом этапе работ.
Установка "нолей" токарного станка - Fanuc
By ETK_Delem · Posted 53 minutes ago
Я не могу понять логики гиб-разгиб, чтобы нарисовать хоть как-то углы мне нужные и расстояния, ибо там гиб без перекрытия невозможен. У него, в Делема невозможен, а у меня возможен. Дабы не быть голословным, предлагаю Вам, Господа, головоломку. xrest.dwg Кому удобней - может в Автокаде посмотреть, по ссылке выше перейдя. Вот так выглядит пуансон (покопался в сохраненном на компе бекапе), нашел похожий, поправил, чтобы выглядел как мой. Ибо маркировка на нем давным давно стерлась. Валяются и другие пуансоны и матрицы - 60 градусов, вроде, и на 30 но ими только фольгу загибать, ни разу не ставили даже еще. Зря валяются, думаю начальство с радостью бы поменяло оные железяки дорогие, на что-то более полезное, наверное, как-то позже их опишу, сфоткаю, может кому позарез нужны, оффтоплю... Матрица спаренная V8 - V12 Так у нас она прописана, если надо полное имя - найду. Как правило, - работаем с -2, но иногда приходится переставлять адаптеры и матрицы, ибо без +2 никак (жесть, какая опасная, упоры врезались, да, было дело. Не обессудьте, сам рисовал и правил рисунки. И да, теперь я знаю, что есть соединение, можно два (и больше) чертежей соединить, чтобы они загружались один за другим. Возможно я не знаю всех премудростей работы с данным пунктом меню, но, гиб без перекрытия невозможен по данному чертежу с данным инструментом. Если кто читал мой вчерашний опус, то понял - какой-то гиб нужно загнуть на 135 градусов, а в конце догнуть до 90. Честно, не помню, какой там гиб, могу программу, наверное даже сюда залить, но не хочу напрягаться. Лучше завтра напарник сфоткает и даже видео снимет, как раз одна заготовка имеется для загибания. Сам не могу, нечем, так как являюсь ярым противником хрустальных андроидов смартфоновых и прочих, не для работы с металлом они... Раньше мучились с такими моментами (перекрытиями), и такую хрень чертили, лишь бы нужные полки нарисовать... Но, потом приходилось править в "Правке данных" - до того дошло, что вводили меньшую толщину и увеличивали силу - в основном, для того, чтобы от коррекций избавиться, но также и для того, чтобы в гибах с отводом брака не наделать - пуансон не прижимал деталь перед отводом, и мы, слишком усердные, проталкивали заготовку вслед за упорами. После коррекций опорных точек данными извращениями заниматься перестали, так как и гнуть стал нормально, и пуансон надежно зажимает заготовку перед отводом упоров. То есть, по сути, загибая сложные детали использовали создать чертеж для затравки, а основная работа происходила в правке данных. Приходилось оперировать неудобными числами, например - для листа двойки положение упора 8,22 - это 10 мм полка. Но потом нашему инженеру приснилось, что пацаны с пробивного станка (криворежчики) будут складывать заготовки в установленном порядке (ага, а как же иначе, счас, прямо, разбежались они - если в кучу не свалили, то уже большое благо), а мы, кривогибщики, будем одну за одной заготовку брать, и на всЁ изделие будет одна программа, включающая все детали, одна за одной. Еще была задумка в зазорах между пуансонами, чтобы их каждый раз не переставлять. Правда как организовать цикл для повторяющейся детали (а бывает и по восемь деталей одинаковых) мы не знали, изделие то одно, а металл приходит разный, и не только по толщине - иногда пластилин приходит, иногда наоборот - как рессора, проще коррекции ввести, там три гиба для детали, но не для восьми деталей для каждой по отдельности по три гиба - 24 коррекции вместо 3, бред. Убедил отказаться от единой программы. О соединении мы тогда не знали, но оно бы сильно и не помогло, так как, если некоих ячеек нужно, скажем, 10 комплектов, то выбивка происходит по листах, скомпонованных для достижения максимальной экономии. Ну типа... То есть - выбивка началась и уже сейчас можно загнуть какие-то детали для десяти комплектов, а некоторые только завтра. Договорились для каждой детали отдельную программу делать, времени много и не занимает, чтобы ее найти, да и написание быстрее происходит, чем черчение. А детали в папках с понятным названием. А сами файлы называем в номере продукта по наибольшей длине развертки, и коментируем в пункте ниже, в номере чертежа. Это одна из самых бредовых вещей в делеме, может кто переубедит, объяснит? Номер продукта можно создать только один такой и только цыфрами, зачем тогда номер чертежа, который да - может для всех продуктов быть единым, вроде как по логике должно было бы наоборот быть. Но, чтобы хоть какую=то пользу извлечь - комментируем деталь по ключевых размерах, чтобы сразу видеть что это такое... Благо, можно посмотреть в выборе продукта вид развертки, и там коменты (номер чертежа) видны. А еще потом начали по толщинах разбрасывать, папки 1, 15, 2. Понравилось, поднаторели, теперь только в подготовке и правке данных работаем, очень изредка лишь, например, когда есть подозрение на вопиющее несоответствие раскройки. Очень бесило раскрытие 10 мм от чертежа. Поставил по умолчанию 50 - комфортно нам так, а после чертежа - все равно десять. И в подготовке данных вводим явные числа, соответствующие длинам требуемых полок, а коррекция Х автоматическая - и одинаково упор встает для десяти мм полки - 8,22 - что после чертежа, что после подготовки данных. Так выглядит после чертежа (рисунок правил, у меня на русском меню) А так после подготовки данных: То есть, после чертежа выходит положение упора с той же коррекцией СХ, уже прописанной в положении оси, а после правки видим полку, которая получится, и видим СХ, которое отнимается, чтобы упор встал на те же 8,22. Что в лоб, что полбу, но с целыми числами работать приятнее... И да, я пробовал вбивать данные средних линий из рассчитанных проектировщиками чертежей, убирая СХ в ноль - не сходится. Надеюсь, объяснил, почему слабоумный "создать чертеж" с его ограничениями не подходит. Да - если есть сомнения - что новую деталь сомнет при перекрытии - то делается пробничек - полоска из отходов - гнем и смотрим - упирается ли, или нет. Так и искали решения для сложных деталей, в том числе для того креста, приведенного выше. Да, после подготовки-правки данных нельзя посмотреть в правке чертежа, что это такое там... Но для множества деталей уже не удосуживаемся даже бумажный чертеж примагничивать, и заготовки не меряем даже, ибо видим, знаем помним. И так будет, пока не случится повальная модернизация всех изделий и принципа соединения деталей (шипами), а это случится буквально на днях, ну, спустя пару недель может быть, или там месяцев, может через год... А пока что - есть с десяток изделий, и для них уже давным давно программы написаны через подготовку-правку данных. И задам глупый вопрос - а можно копировать детали из одной папки в другую? Ибо есть детали, подходящие ко многим изделиям. Блин, интересно стало, побежал проверять. Потом постараюсь ответить всем на все остальные вопросы. Сожалею, что когда я сегодня открыл форум меня отвлекли, и я только что (недавно) смог начать отвечать.
cccp3d.ru
Установка токарных станков
Токарные станки представляют собой оборудование, предназначенное для обработки металла. Поэтому во время работы такой станок подвергается значительным нагрузкам, которые могут быть не только статическими, но и динамическими. Логическим выводом из этого есть необходимость серьезного подхода к его монтажу, ведь от этого зависит устойчивость станка, отсутствие вибрации и биений и, как следствие, снижение риска аварии и производственного травматизма. Следует понимать, что установка токарных станков целиком и полностью зависит от типа данного оборудования. К примеру, небольшие станки, так называемые мини, домашние и часовые токарные станки по причине небольшого веса, не превышающего сотню килограмм и отсутствия тумб, принято устанавливать на верстак или стол. Легкие станки, оснащенные тумбами, можно поставить на твердый пол, подложив под основание тумб виброизолирующие опоры или коврики. А вот средние полупрофессиональные станки, мощностью до 1000 Вт, а тем более тяжелые и точные станки требуют монтажа на основательный фундамент. Для того, что бы избежать неправильной установки, нужно точно следовать инструкции по эксплуатации станка. В случае с тяжелыми станками и станками с ЧПУ в инструкции очень подробно освещается данный вопрос, вплоть до наличия чертежа фундамента с указанием его размерных значений.
Правильная установка токарных станков гарантирует создание необходимых условий для безопасной и комфортной работы токаря. Поэтому при монтаже легкого станка на стол или верстак, нужно правильно рассчитать высоту. Станок должен располагаться так, что заготовка будет занимать положение в районе локтя стоящего возле станка токаря. Фундамент под тяжелые станки следует сделать до начала монтажа, затем внимательно проверить его на горизонтальность и отсутствие дефектов, влияющих на устойчивость монтируемого оборудования.
При монтаже токарного станка на фундамент используются башмаки, клинья и другие элементы, способствующие его правильной установке. Когда удалось добиться полной устойчивости и соответствия расположения по горизонтальной и вертикальной оси, нужно произвести окончательную доливку раствора на фундамент. Это служит дополнительным способом обеспечения неподвижности станка, наряду с затяжкой гаек фундаментных болтов.
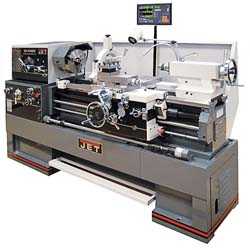
Токарный станок является одним из самых древних изобретений в области обработки материалов. Первые свидетельства (упоминания) о токарных станках относятся к 650 году до нашей эры. С тех пор принцип...
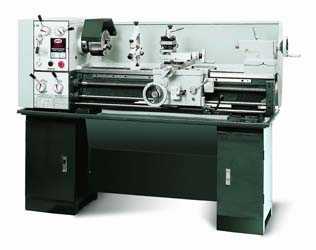
По-прежнему в промышленности, особенно в отечественной металлообработке распространены советские токарные станки, которые, несмотря на определенную степень устаревания и повышенный расход электроэнергии...
100fondue.ru
Установка резца на токарном станке
Для чего нужна правильная установка резца на токарный станок и как правильно осуществить монтаж? Основные правила, а также некоторые тонкости.
Весь ход процесса точения на токарных станках от самого начала и вплоть до окончательного результата в основном определяется грамотной установкой резца в резцедержателе. В противном же случае при его неправильном положении станку грозит довольно быстрый износ режущей кромки.
Не редко также из-за этой неполадки возникают серьёзные поломки оборудования, которые часто влекут за собой следом ощутимые материальные убытки на производстве.
Перед началом необходимо сперва тщательно очистить опорные поверхности держателя. Главное правило установки резца на токарный станок по сути заключается в том, что его вершина обязательно должна находиться на уровни линии центров станка.
Помните, что установка ниже этой линии приведёт к выталкиванию детали из центров при набегании, а установка выше — к недопустимому нагреву и крайне быстрому износу.
Но в иных случаях для дополнительного улучшения работы резца допускаются незначительные отклонения. К примеру, в процессе черновой обработки деталь устанавливают с небольшим превышением над уровнем центров, составляющем от 0.3 до 1.2 мм (зависит исключительно от диаметра обрабатываемого изделия).
Совершенно другой случай — чистовое точение, при котором установка резца осуществляется со снижением на аналогичную величину.
Будучи закреплённым в резцедержателе не менее, чем двумя болтами, резец необходимо подвести строго к центру задней или же передней бабки и отрегулировать по высоте, подстилая при этом под него не более трёх подкладок. Это придаст максимальную точность при установке детали.
Отдельного упоминания также заслуживают сами подкладки: их следует подготавливать целым комплектом сразу же заблаговременно. Не стоить их заменять на куски металла или же другие иные материалы.
Подкладки нужно класть на опорную поверхность резцедержателя, при этом контролируйте вылет резца — он не должен превышать 1.5 высоты стержня, в противном случае вибрации детали при работе станка не избежать.
Дальнейшая регулировка резца на необходимую глубину может быть произведена двумя путями: методом пробных стружек или с лимбом поперечной подачи. Выбирая первую технологию, резец подводят вплотную до первого касания к поверхности вращающейся детали.
После чего он отводится вправо и далее глубина резания устанавливается уже глаз. Если диаметр проточки детали после этого вышел больше необходимого, всё повторяется с новой глубиной резания до получения требуемого результата.
Видео: подгонка (установка) резцов под токарный станок.
metmastanki.ru
Установка патрона на токарный станок своими руками
Установка патрона на токарный станок может осуществляться несколькими методами, все зависит от конкретной вида этого элемента, с которым вы будете иметь дело.
Существует два вида крепления патрона на шпинделе токарного станка:
- резьбовое;
- фланцевое.
Резьбовое крепление применяется на малых станках с легкими видами патронов, фланцевое на средних и тяжёлых станках.
Если он лёгкий, достаточно легко устанавливается на станке без посторонней помощи, то тяжёлые (более 20 кг) устанавливаются при помощи вспомогательных подъёмных механизмов, или в паре с напарником. Рассмотрим порядок установки на токарный станок именно тяжелого патрона с фланцевым креплением.
Для установки тяжелого патрона необходимо подготовить два приспособления для монтажа.
- монтажная подставка;
- направляющая.
Монтажная подставка изготавливается из доски толщиной приблизительно 50 мм. Ширина равная 1,5 ширины устанавливаемого патрона, длина подставки L- соответствует ширине станины- B и радиусу -D.
К низу подставки крепятся брусочки. Через вертикальные сквозные отверстия, подставка болтами крепится к подвижному люнету суппорта станка. Подгонка подставки по высоте осуществляется толщиной брусков.
Между подогнанной до упора люнеттой с прикрепленной к ней подставкой и ещё установленным на станке патроном, зазор должен составлять 1-3 мм.
Направляющая представляет из себя цилиндрический вал диаметром 25-40 мм., с хвостовиком в виде конуса морзе не менее третьего номера. Длина цилиндрической части направляющей, равная 1,5-2,0 ширины устанавливаемого патрона.
Порядок установки
Перед его установкой , следует тщательно проверить состояние поверхностей шпинделя и патрона. Поверхности не должны иметь забоин, царапин, заусениц и загрязненных мест.
Выявленные дефекты устраняются точечно надфилем, или шабером.Следует проверить биение торца и конуса посадочной базы шпинделя, которое не должно превышать трёх микронов.
Завести в него металлический прут или трубу диаметром около 20 мм. зажать её кулачками. С напарником взявшись с двух сторон за прут, или при помощи подъёмных механизмов, через монтажную петлю, переместить патрон на монтажную подставку закрепленную на суппорте станка.
Направляющую установить в задней бабке. Патрон следует сместить перекатыванием к оси шпинделя.
Продольной подачей переместить его к фланцу шпинделя так, что бы шпильки патрона не доходили до посадочных отверстий порядка 10 мм. В станке следует установить нейтральную скорость для свободного вращения шпинделя.
Заднюю бабку с полностью убранной пинолью подать вперед к патрону так, что бы направляющая зашла на всю ширину призм кулачков и зафиксировать заднюю бабку.
Зажать кулачки патрона для переноса тяжести на направляющую. Совместить шпонку на фланце шпинделя с посадочным отверстием. Поворотную шайбу выставить в положение открытых отверстий. Пинолью подать патрон вперед до упора.
Убедившись, что все гайки шпилек вышли с обратной стороны фланца шпинделя, повернуть поворотную шайбу в замкнутое положение. Зажать верхнюю гайку с усилием достаточным для переноса веса патрона на шпиндель. Распустить кулачки и отвести заднюю бабку назад. Обжать гайки по правилу крест на крест равномерно распределяя усилие между шпильками.
После завершения монтажа, патрон следует проверить на осевое и торцевое биение. В случае превышения норм, следует его снять и внимательно продефектовать все сопрягаемые части этого узла.
Видео: монтаж легкого патрона на резьбовом креплении.
metmastanki.ru
Работа на токарном станке или управление токарным станком
Эта статья посвящена правилам и технике управления токарным станком. От соблюдения правил работы на токарном станке зависит ваша безопасность. Уверенная техника управления токарным станком влияет на качество изделия и производительность управляемых работ.
1.Шаг 1. Проверка токарного станка перед пуском
Прежде, чем запустить токарный станок, должен быть произведен допусковой контроль, а именно:
- При сменной работе на производстве сменщик, передающий вам токарный станок, обязан доложить о замеченных в нем неполадках (устно, письменно, по телефону). Отсутствие замечаний подразумевает, что токарный станок находится в исправном состоянии.
На производстве устранением неисправностей токарного станка занимается ремонтная служба. Станочник должен только информировать их об возникновении неисправности.
Перед включением токарного станка в электропитание убедитесь:
- Что на станке нет какого-либо предупреждения, типа (токарный станок в ремонте не включать);
- Кожухи, дверки, люки, которые закрывают основные детали, и механизмы токарного станка должны быть закрыты.
- Рукоятки управления шпинделем, подачами, маточной гайкой должны находятся в нейтральном положении.
- Подача охлаждения выключена, сопла подачи жидкости направлены вниз.
- Частоты оборотов и шаги подач установлены такие, какими вы их хотите увидеть, после запуска шпинделя.
- Установленная вами деталь, которую следует обработать должна быть надежна закреплена.
- Пол возле токарного станка должен быть чистым, а под ногами не должно быть лишних предметов.
- Одежда токаря должна быть аккуратно (без свисающих лоскутов).
- Не забыть ключ в патроне (всегда следить за выемкой ключа из патрона).
Выполнив допусковой контроль: включаем главный рубильник токарного станка, дополнительные включатели, если такие имеются. Далее проводится смазка токарного станка.
2.Шаг 2. Управление шпинделем.
Перед запуском шпинделя или главного двигателя, обязательно убеждаемся, что у вращающихся элементов на нем, в частности патрона, не будет препятствий вращению со стороны неподвижных частей станка. Особую опасность при запуске шпинделя на высоких оборотах представляют собой выступающие за его пределы тонкие прутковые заготовки.
Также это касается деталей больших диаметров со значительным вылетом из патрона и не поджатым с другого конца центром задней бабки.
Как уже говорилось в первом уроке «Устройство токарного станка», настройки частот оборотов шпинделя производят установкой переключателей и рычагов на его узлах в определенное положение согласно таблице, расположенной на станке.
Правила переключение можно обобщить так – «Нельзя переключать или доводить до конца переключения, если таковые вызывают характерный звук не входящих в зацепление зубьев шестерен. В таком случае нужные переключения следует делать при полной остановке.
На всех токарных станках прямые обороты включаются подачей рукоятки включения на себя, а обратные от себя. У рукоятки с вертикальным ходом (на себя это вверх), а у рукоятки с горизонтальным перемещением (на себя это соответственно вправо).
Прямые обороты на всех токарных станках соответствуют вращению шпинделя по часовой стрелке, если смотреть с задней стороны шпинделя. Торможение шпинделя на высоких оборотахза счет реверсирования фрикционов или обратной тяги главного двигателяэто недопустимо, так как ведет к перегрузке и перегреву механизма. Торможение должно выполняться тормозом. А если эффективности тормоза недостаточно, то ее следует восстановить регулировкой или ремонтом.
Для крепления в трехкулачковом патроне деталей обычно используется одно гнездо «0» для введения в него ключа, что требует установки этого гнезда в верхнее положение зажима и отжима. В станках с механическим фрикционом это действие (при некоторых навыках) можно выполнять рукояткой управления фрикционов.
При обработке резцом нельзя останавливать шпиндель при включенной подаче и не отведенном от детали резце (это приводит к поломке резца).
3.Шаг 3. Управление подачей токарного станка
Ручное управление подачей станка подразумевает подачу инструмента на небольшие длины (при обработках, настройках, подводках).
Ручное управление подачей позволяет быстро вести, прерывать и возобновлять подачу, а также мгновенно изменять ее скорость (в зависимости от изменения условий и ситуаций обработки). Ручная подача в продольном направлении приводится маховиком с горизонтальной ручкой или без нее. Вращение маховика против часовой стрелки приводит движение суппорта влево, а по часовой стрелке вправо.
Продольное перемещение суппорта на токарном станке осуществляется за счет шестеренно реечной передачи. У таких передач есть люфты или зазоры в контактах деталей и ее механизмах.
Ручное управление поперечной подачей (выполняется Т-образной рукояткой с горизонтальной ручкой). Вращение рукоятки по часовой стрелке подает салазки инструмент вперед, то есть от себя, вращение рукоятки против часовой стрелки подает инструмент к себе. На нашем станке есть ускоренное включение перемещения салазок. Существуют разные техники вращения маховика одной и двумя руками, которые применяются в зависимости от выполняемой работы на токарном станке.
Подача верхними салазками
На верхних салазках вращение рукоятки по часовой стрелке двигает салазки вперед, а вращение против часовой стрелки назад. Быстрое холостое перемещение таких рукояток можно делать за одну из ручек. При этом салазки должны быть отрегулированы на легкое перемещение. Более подробно о регулировке механизмов, салазок, токарного станка мы рассмотрим в следующем уроке по токарному делу.
4.Шаг 4. Управление механическими подачами
Механические подачи работают от привода через ходовой вал, а управление ими делается ручкой 4-х позиционного переключателя. Направление перемещение рукоятки переключателя соответствует направлению движения инструмента на суппорте.
Перед включением механической подачи в любом направлении нужно визуально убедиться в отсутствии у всех точек суппорта препятствий со стороны других узлов станка особенно вращающихся. Частой оплошностью начинающих токарей является попытка приблизить суппорт к патрону при сдвинутых вправо салазок, что приводит к сталкиванию. Поэтому следует проверять беспрепятственное перемещение суппорта заранее.
Нужно отработать техники ручной подачи так, чтобы не происходила остановка резца или остановка была минимальной.
5.Шаг №5. Ускоренная подача токарного станка
На станках имеющих ускоренную подачу необходимо соблюдать такие требования:
- Для исключения случайного нажатия кнопки ускоренной подачи управление рычагом переключения подач необходимо производить приложением руки сбоку, но не сверху.
- До пуска ускоренной подачи нужно надежно убедиться в отсутствии препятствий для продвижения у любых точек на суппорте, в том числе и у инструмента, в направлении, куда вы хотите подать.
- Нельзя применять ускоренную подачу для коротких перемещений, особенно при подводам к вращающимся элементам.
- Тяжелые суппорты средних станков имеют инерцию, которую усиливается при ускоренной подаче механизмом его привода.
Бывают совмещенные подачи токарных станков (по виду привода, по направлениям). Такие токарные станки применяются для обработки неответственных конусов (неответственных фасок) и фасонных поверхностей.
5.1.Резьбовые подачи
Для нарезания резьб подача суппорта проводится за счетсмыкания маточной гайки с ходовым винтом. Включение и выключения маточной гайки делается отдельным рычагом. Шпиндель и ходовой винт вне зависимости от настроенного шага резьбы вращаются синхронно. Изменения направления вращения шпинделя приводит к изменению направления движения суппорта. Также изменение частоты вращения шпинделя приводит к изменению скорости перемещения суппорта. Попадание резца в ранее нарезанную канавку обеспечивается синхронизацией вращения шпинделя и ходового винта и соответственно хода суппорта.
Можно нарезать, как правую, так и левую резьбу с помощью переключателя на передней бабке, который изменяет направление движения винта относительно шпинделя. При нарезании резьб, не рекомендуется увлекаться высокими оборотами шпинделя, так как его вращение напрямую связано с перемещением суппорта.
6.Управление задней бабкой токарного станка
Фиксация задней бабкой токарного станка выполняется рычагом, по мере рабочего хода которого, нарастает усилие прижима. При обработках с большими нагрузками, требующей лучшей фиксации задней бабкой воздействие на рычаг должно быть энергичным. Важно не спутать сопротивление рычага при зажиме с его жестким упором в конце рабочего хода. Когда задняя бабка используется с минимальными нагрузками, ее максимальная фиксация со станиной не нужна. Зажим задней бабки рационально соизмерять с предстоящей нагрузкой.
Пиноль задней бабки приводится ручной подачей путем вращения маховика. Закрепление инструмента и приспособлений в конусе пиноли производится в следующем порядке:
- Проверка конусов пиноли и инструмента на отсутствие загрязнений;
- Введение наружного конуса в конус пиноли и нахождение положения совпадения разъема замка в пиноли с лапкой на конусе инструмента (для инструментов, не имеющих лапки, не требуется).
7.Управление резцедержателем
Резцедержатель представляет из себя, достаточно точный механизм, обеспечивающий жесткость крепления резца в заданных позициях. Правильное положение рукоятки резцедержателя в зажатом виде должно соответствовать положению часовой стрелки на 3-4 часа. Это положение обеспечивается положением проставной шайбы под гайкой рукоятки резцедержателя. Зажим рычага производится средним локтевым усилием. А отжис рукоятки нельзя делать давлением своего веса во избежание потери веса. Отжим рукоятки делается одним или несколькими короткими толчками основанием ладони в направлении против часовой стрелки. Перед поворотом резцедержателя убедитесь в отсутствии препятствий для него самого и закрепленного в нем инструмента. Большую опасность представляют препятствия со стороны вращающихся элементов станка.
8.Неисправности токарного станка
В процессе работы любому токарю рано или поздно придется столкнутся с непредвиденными ситуациями при работе на токарном станке.
Возможные ситуации при работе на токарном станке:
- Самопроизвольная остановка токарного станка во время работы, во время отключения электропитания или механической неисправности;
- Сталкивания вращающихся элементов с элементами суппорта;
- Проворот детали в патроне;
- Вырыв детали из зажимных приспособлений токарного станка;
Неисправности токарного станка могут быть выражены в посторонних шумах, запахом горящей электропроводки и т.д.
Отлучатся от токарного станка запрещено (нельзя оставлять токарный станок без внимания).
Для экстренной остановки обработки детали следует быстро отвести резец от детали, отключить подачу, остановить шпиндель и выключить главный двигатель. При остановке шпинделе главное не включить обратные обороты, а включить именно нейтральное положение. О неисправностях токарного станка следует сразу же доложить руководству.
www.autoezda.com