Большая Энциклопедия Нефти и Газа. Котельные марки стали. Котельные марки стали
Ꙭ Металлы котельных агрегатов — сталь и чугун — ikotel.info
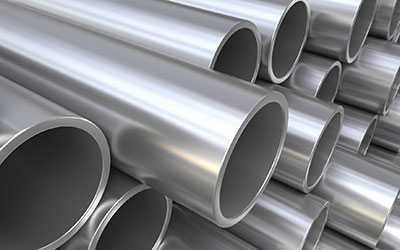
Основными металлами, применяемыми для изготовления котельных агрегатов, являются сталь и чугун.
Сталь применяют как относительно дешевую — углеродистую, так и более дорогую — легированную, т. е. такую, в которую для улучшения механических и физико-химических свойств добавлены в некотором количестве другие металлы. Различают низколегированную сталь, в которой присадки содержатся в незначительном количестве, не превышающем 0,5-1,0 %, и высоколегированную, в которую добавляется значительно большее количество присадок. Низколегированная котельная сталь принадлежит к классу перлитной, а высоколегированная - к классу аустенитной стали.
Углеродистая сталь широко применяется в котлостроении. Содержание углерода в этой стали не должно превышать 0,3 % во избежание ухудшения качества сварных соединений из-за воздушной закалки при сварке. Содержание серы и фосфора не должно превышать 0,045 % для каждого из этих элементов. Предельная температура, при которой углеродистая сталь может длительно и надежно работать, составляет 500 °С; превышение ее приводит к резкой интенсификации окалинообразования на металле.
Легирование котельной стали имеет назначение повысить ее прочность и окалиностойкость при высокой температуре. В качестве легирующих присадок применяют хром, молибден, никель, ванадий, титан, вольфрам, ниобий, марганец и бор, которые вводятся в различных комбинациях. Хром вводят в сталь для повышения ее жаростойкости, т. е. способности противостоять коррозии (образованию окалины) при высокой температуре; наличие в стали 12—14 % хрома делает ее нержавеющей. Молибден добавляют для повышения жаропрочности, т. е. для повышения предела прочности и предела текучести стали при высокой температуре, а также для улучшения ее технологических свойств (свариваемости) и упрощения термической обработки. Никель повышает вязкость стали, ее жаропрочность и сопротивляемость старению. Для повышения сопротивляемости ползучести, т. е. снижения предела текучести стали в результате длительной работы ее при высокой температуре, к низколегированной хромомолибденовой стали добавляют ванадий и ниобий, а к высоколегированной стали — титан и вольфрам. Наличие марганца в стали в пределах 0,3-0,8 % определяется технологическими требованиями процесса выплавки, а повышение содержания марганца в стали до 0,9-1,5 % преследует цель повысить ее прочность. Легирующие элементы в марках стали обозначают буквами русского алфавита: Б — ниобий; В — вольфрам; Г — марганец М — молибден; Н — никель; Р — бор; С — кремний; Т — титан; Ф — ванадий; X — хром.
В обозначении марок высоколегированной стали за буквами ставят цифры, которые означают содержание этих элементов в стали в процентах. Цифры перед буквенным обозначением указывают содержание углерода в стали в сотых долях процента для низколегированной стали и десятых долях процента для высоколегированной стали. Если при этом в высоколегированной стали количество углерода не ограничено нижним пределом при верхнем пределе 0,09 % и выше, цифры перед буквенным обозначением не ставят.
Среди большого числа различных марок высоколегированной стали в котлостроении применяют только сталь жаропрочную, т. е. предназначенную для работы в нагруженном состоянии при высокой температуре в течение длительного времени и обладающую достаточной окалиностойкостью.
Для изготовления котлов применяют сталь в виде листов, труб, поковок, литья, крепежных материалов (для фланцевых соединений), электродов и сварочной проволоки. Качество стали, употребляемой для этих целей, точно регламентировано «Правилами устройства и безопасной эксплуатации паровых и водогрейных котлов» Госгортехнадзора.
Характеристики марок стали, применяемых для изготовления барабанов и поковок для котлов, приведены в табл. 1, а для изготовления трубных систем и соединительных трубопроводов — в табл. 2.
Следует различать требования, предъявляемые к стали, применяемой для изготовления барабанов, и к стали для изготовления трубных систем поверхностей нагрева, коллекторов и соединительных трубопроводов. Выбор марки стали для изготовления барабанов котлов определяется стремлением получить барабан с возможно более тонкими стенками, т. е. более легкий, путем применения более прочной стали. Для трубных систем поверхностей нагрева, коллекторов и трубопроводов выбор марки стали определяется в первую очередь температурой, которую будет иметь стенка трубы во время работы котельного агрегата.
Для изготовления барабанов котлов по требованию «Правил» Госгортехнадзора применяют листовую сталь и поковки, полученные мартеновским способом или в электрических печах. Корпуса цилиндрических котлов, работающих при давлении до 9 aт, изготовляют из углеродистой стали марки Ст. 3 сп. Барабаны котлов с толщиной стенки до 60 мм изготовляют из углеродистой стали марок 15К и 20К. Для изготовления барабанов на давление 40—100 ат применяют сталь марки 22К с несколько повышенным содержанием марганца. Барабаны на давление от 100 ат и выше изготовляют из низколегированной стали марки 16ГНМ. Стали марок 16ГС, 09Г2С и 10Г2С1 являются относительно новыми сталями котлостроения.
Таблица 1
Углеродистая(перлитная) Легированная (перлитная) | В.Ст.3сп. 15К20К22К22К16ГС 09Г2С10Г2С116ГНМ | 0,12-0,200,16-0,240,19-0,260,18-0,260,12-0,18 0,120,120,12-0,18 | 0,12-0,30 0,15-0,300,15-0,300,20-0,400,17-0,370,40-0,70 0,50-0,800,90-0,200,17-0,37 | 0,40-0,65 0,35-0,650,35-0,650,75-1,000,70-0,900,90-1,20 1,30-1,701,30-1,650,80-1,10 | — <0,30<0,30<0,4<0,30<0,30 <0,30<0,30<0,3 | — <0,30<0,30<0,30<0,25<0,30 <0,30<0,301,0-1,3 | — ————— ——0,40 0,55 | 38 38414444 46444651 | 27 27261820 22222216 | 23 2322—— 181818— | Барабаны, обечайки днища, затворы вертикально - цилиндрических котлов То же для котлов среднего давления Барабаны, обечайки днища затворы котлов давления до 100 ат Барабаны, обечайки, днища, затворыкотлов высокого давления | 200 450 450450 450 | 8 Не ограничено Не ограничено Не ограничено | 12 60 90160 160 | 380 - 60, группа В 5520 - 62 ТУГКТП1 - 55Технические условия 5520 - 62Технические условия |
Трубы для поверхностей нагрева, коллекторов и соединительных трубопроводов изготовляют из стали, выплавленной мартеновским способом или в электропечах. Трубные системы, в которых температура стенки не будет превышать 500 °С, изготовляют из углеродистой трубной стали марок 10 и 20. Трубные же системы, в которых температура стенки будет превышать 500 °С, изготовляют из легированной стали для предотвращения окалинообразования.
Следовательно, из сталей марок 10 и 20 можно изготовлять все поверхности нагрева как паровых, так и водогрейных котельных агрегатов на давление до 24 ат. При этом применение стали марки 10 нежелательно, так как она имеет значительно большую склонность к старению, чем сталь марки 20. Из стали марки 20 можно изготовлять также трубные системы экранов и водяных экономайзеров котельных агрегатов более высокого давления, так как температура стенок этих поверхностей нагрева в нормальной эксплуатации никогда не достигает 500 °С. Из легированной стали изготовляют трубные системы пароперегревателей, предназначенных для получения пара с температурой 440-450 °С и выше. В случаях, когда пароперегреватель выполняют двухступенчатым, из легированной стали изготовляют только змеевики второй ступени и выходной коллектор, так как через змеевики первой ступени проходит пар с более низкой температурой и омываются они дымовыми газами с менее высокой температурой. Даже при очень высокой конечной температуре пара температура стенок труб первой ступени пароперегревателя не превышает 500 °С. Для второй ступени пароперегревателей котлов с давлением 40 ат, предназначенных для перегрева пара до 440 °С, температура стенок которых может превышать 500 °С, применяют низколегированную хромомолибденовую сталь марки 12МХ.
Трубные системы топочных экранов и водяных экономайзеров, а также тех частей пароперегревателей, температура стенок которых не превышает 500 °С, у котельных агрегатов с давлением 100 ат и выше выполняют из стали марки 20, которую изготовляют по особым техническим условиям, предусматривающим более высокие требования. Части трубных систем пароперегревателей этих котлов с температурой стенок выше 500 °С выполняют из легированной стали. При этом для пароперегревателей, предназначенных для перегрева пара до 540 °С, когда температура стенок может доходить до 570-580 °С, рекомендуется сталь марки 12Х1МФ.
Пароперегреватели котельных агрегатов на давление 140 ат с перегревом пара до 570 °С изготовляют из стали марки 12Х2МФСР с несколько большим содержанием хрома, а также наличием бора. Кроме того, для таких пароперегревателей, а также для пароперегревателей на давление 255 ат, предназначенных для перегрева пара до 585 °С, у которых температура стенок труб превышает 600 °С, рекомендуется высоколегированная аустенитная сталь (см. табл. 2). Обычно выбирают сталь марки Х18Н12Т (1Х18Н12Т). Применяют также сталь марки 1Х1УН14В2М. Эта сталь, однако, имеет тот недостаток, что она склонна к межкристаллитной коррозии.
Воздухоподогреватели изготовляют из стали марки Ст. 3.
Литые детали, работающие под давлением, изготовляют из стали, выплавленной в мартеновских или электрических печах; при этом содержание серы и фосфора в углеродистой стали не должно превышать 0,05 % для каждого из этих элементов. В зависимости от температуры и давления применяют углеродистую сталь марок от 15Л до 35Л и легированную сталь марки 18МХ-Л. Соответствующие требования предъявляются также к металлу крепежных материалов (болты, шпильки, гайки), электродам и сварной проволоке.
Чугун для изготовления чугунных котлов для нагрева воды до 115 °С, согласно требованиям Госгортехнадзора по качеству должен быть не ниже марки СЧ 12-28 (ГОСТ 1412-54). Для поверхностей нагрева, коллекторов и камер чугунных ребристых водяных экономайзеров, устанавливаемых к котлам давлением до 24 ат, применяют чугун по качеству не ниже чугуна марки СЧ 12-28.
Таблица 2
Углеродистая(перлитная) | 102020 | 0,07-0,140,17-0,240,17-0,25 | 0,17-0,370,17-0,370,17-0,37 | 0,35-0,650,35-0,650,35-0,65 | ≤0,15≤0,25≤0,3 | ≤0,25≤0,25≤0,3 | ——— | ——— | ——— | ——— | ——— | ——— | 344141 | 242224 | ——— | ——— | Поверхности нагреваКоллекторы и соединительные трубопроводыПоверхности нагреваКоллекторы и соединительные трубопроводы | 6060Не ограниченоТо же | 500400500450 | 1050-601050-60Техническиеусловия |
Легированная(перлитная) | 15ГС12МХ15ХМ12Х1МФ12Х2МФСР15Х1М1Ф | 0,12-0,180,09-0,160,11-0,160,08-0,150,08-0,150,10-0,16 | 0,70-1,000,15-0,300,17-0,370,17-0,370,4-0,70,4-0,7 | 0,90-1,300,4-0,70,4-0,70,4-0,70,4-0,70,4-0,7 | <0,30,4-0,60,8-1,10,9-1,21,6-1,91,1-1,4 | <0,3—<0,25<0,25<0,25<0,25 | —————— | —————— | —0,4-0,60,4-0,550,25-0,350,5-0,70,90-1,10 | —————— | ———0,18-0,300,20-0,350,20-0,35 | ————0,002 - 0,005— | 50—45454850 | 28—21212118 | —————— | —————— | Поверхности нагреваКоллекторы и соединительные трубопроводыПоверхности нагреваКоллекторы и соединительные трубопроводыПоверхности нагреваКоллекторы и соединительные трубопроводыПоверхности нагреваКоллекторы и соединительные трубопроводы | »»» » »» | 500450550550585570585575 | То же»»»»»»» |
Высоколегированная(аустенитная) | 1Х11В2МФХ18Н12Т1Х14Н14В2М (ЭИ - 257)1Х14Н14Б (ЭИ - 694)1Х14Н16БВ (ЭИ - 694Р)1Х16Н15М3Б (ЭИ - 847)1Х14Н18В2Б (ЭИ - 695)1Х14Н18В2БР (ЭИ - 695Р) | 0,10-0,15≤0,120,4-0,50,07-0,120,07-0,12≤0,90,08-0,120,07-0,12 | ≤0,5≤0,8≤0,8≤0,6≤0,6≤0,8≤0,6≤0,6 | 0,50-0,801,0-2,0≤0,71,0-2,01,0-2,0≤0,61,0-2,01,0-2,0 | 10-1217-1913-1513-1513-1515-1713-1513-15 | <0,611-1313-1514-1714-1714-1618-2018-20 | —≤ (С - 0,02) × 5 - 0,7—————— | 1,7-2,2—2,0-2,75———2,0-2,752,0-2,75 | 0,6-0,9—0,25-0,40——2,5-3,0—— | ———0,9-1,30,9-1,30,9-1,30,9-1,30,9-1,3 | 0,15-0,30——————— | ————0,005——0,005 | 605450————— | 183016————— | —600600-650650650650700700 | —800850850850850850850 | Поверхности нагреваПоверхности нагрева; Коллекторы и соединительные трубопроводыПоверхности нагреваГОСТ 5632 - 61 рекомендуютсядля изготовления пароперегревательных труб и соединительных трубопроводов котлов высокого и закритического давления | »»» | 630640; 610650 | »»» |
ikotel.info
kaiser смесители
МЕТАЛЛ ЭЛЕМЕНТОВ КОТЛА В соответствии с указанными условиями работы металла элементов котла к металлу предъявляются следующие основные требования: высокие механические характеристики — прочность, пластичность, вязкость, твердость; стабильность структуры и механических характеристик при работе с высокими нагрузками и высокой температурой в течение длительного времени; высокая сопротивляемость воздействию агрессивных сред; возможность выполнения без особого усложнения технологических операций, необходимых при изготовлении и ремонте элементов котла. Этим требованиям удовлетворяют углеродистые и легированные стали. Для изготовления котлов широко применяют углеродистую сталь. Содержание углерода в этой стали допускается не более 0,3 % в целях обеспечения достаточной пластичности и вязкости, а также во избежание ухудшения качества сварных соединений. Содержание серы и фосфора должно быть не более 0,045 % в целях предотвращения хрупкости стали и ухудшения ее технологических качеств. Углеродистая сталь может длительно и надежно работать при температурах до 500 °С. При большей температуре в условиях газовой среды происходит резкая интенсификация окалинообразования поверхности металла. Легирование стали имеет назначение повысить ее прочность и сопротивляемость окалинообразованию при высокой температуре. В качестве легирующих присадок применяют хром, молибден, никель, ванадий, титан, вольфрам, ниобий, марганец и бор, которые добавляются в сталь в различных комбинациях. Хром вводят в сталь для повышения ее жаростойкости, т. е. способности противостоять кислородной коррозии при высокой температуре; наличие в стали 12— 14 % хрома делает ее нержавеющей. Молибден добавляют для повышения жаропрочности — повышения предела прочности и текучести стали при высоких температурах, а также для улучшения других ее свойств. Никель повышает вязкость стали, ее жаропрочность и сопротивляемость старению. Для повышения сопротивляемости ползучести к низколегированной хромомолибденовой стали добавляют ванадий и ниобий. Содержание марганца в стали в пределах 0,3—0,8 % определяется технологическими требованиями процесса ее выплавки, а содержание марганца в стали в количестве 0,9—1,5 % повышает ее прочность. Легирующие элементы в марках стали обозначают следующими буквами: Б — ниобий, В — вольфрам, Г — марганец, М — молибден, Н — никель, Р — бор, С — кремний, Т — титан, Ф — ванадий, X — хром. В обозначении марок легированной стали за буквами ставят цифры — содержание этих элементов в стали в процентах. Цифры перед буквенным обозначением указывают содержание углерода в стали в сотых долях процента для низколегированных сталей и в десятых долях процента для высоколегированной стали. Если в высоколегированной стали количество углерода не ограничено нижним пределом при верхнем пределе 0,09 % и выше, цифры перед буквенным обозначением не ставят. Барабаны котлов с толщиной до 60 мм изготовляют из углеродистой стали марок 15К и 20К. Для барабанов, работающих под давлением 4—10 МПа, применяют сталь 22К с повышенным содержанием марганца. Барабаны при давлении больше 10 МПа изготовляют из низколегированной стали марок 16ГНМ, 16ГС, 09Г2С и 10Г2С1. Трубы для поверхностей нагрева, коллекторов и соединительных трубопроводов, в которых температура стенки будет не выше 500 °G, изготовляют из углеродистой стали марок 10 и 20. Трубы с температурой стенки выше 500°С изготовляют из легированной стали. Практически из углеродистой стали марок 10 и 20 изготовляют все поверхности нагрева котлов и водогрейных агрегатов на давление до 2,4 МПа. Из легированной стали изготовляют системы пароперегревателей при температуре перегрева пара более 450°С. Для первой ступени пароперегревателя может использоваться сталь 20. В котлах с давлением 10—14 МПа трубные системы топочных экранов и экономайзеров, а также частей пароперегревателя, у которых температура стенки не превышает 500 °С, выполняют из стали 20 повышенного качества. Для пароперегревателей, предназначенных для перегрева пара до 540°С, с температурой стенки труб 570— 580 °С рекомендуется применение легированной стали 12Х1МФ. Пароперегреватели котлов на давление 14 МПа с температурой перегрева пара 565°С изготовляют из стали с несколько повышенным содержанием хрома и наличием бора. Для пароперегревателей, у которых температура стенки труб превышает 600 °С, рекомендуется применение аустенитных сталей. Воздухоподогреватели и каркасы котла изготовляют из углеродистой стали 3. Стальные литые детали, работающие под давлением и при повышенной температуре, а также крепежные изделия изготовляют из стали марок 15Л—35Л. При этом содержание серы и фосфора в металле не должно превышать 0,05%. |
geyz.ru
Котельная сталь - Большая Энциклопедия Нефти и Газа, статья, страница 1
Котельная сталь
Cтраница 1
Котельные стали должны обладать высокой сопротивляемостью старению. [1]
Котельные стали для изготовления барабанов должны хорошо свариваться и допускать пластическое деформирование в процессе штамповки п вальцовки. [2]
Котельные стали должны обладать достаточно высоким комплексом механических свойств при комнатной и рабочей температурах. Как отмечалось, важными характеристиками механических свойств котельной стали при комнатной температуре являются временное сопротивление, предел - текучести, относительное удлинение, относительное сужение и ударная вязкость. [3]
Котельные стали должны обладать высокой сопротивляемостью старению. [4]
Котельные стали применяются для изготовления котлов, которые должны удовлетворять условиям работы при температуре до 650 С и при воздействии переменных динамических нагрузок. Эти стали пригодны для сварки деталей паровых котлов и сосудов, работающих под давлением при нормальной, повышенной и минусовой температурах. Характеризуются повышенными требованиями к пределу текучести при повышенных температурах. [5]
Котельные стали с содержанием углерода не выше 0 3 % не закаливаются; они применяются в отожженном или чаще в нормализованном состоянии. Структура таких сталей - феррит и перлит. При температурах, вызывающих развитие процесса ползучести, предпочтительны стали с крупным действительным зерном; они имеют более высокий предел ползучести, чем стали с мелким действительным зерном. При повышенных температурах, недостаточных для развития процесса ползучести, так же как и при нормальной температуре, лучшими прочностными свойствами обладают мелкозернистые стали. В технических условиях на трубные стали с молибденом оговаривается размер зерна: размер действительного зерна феррита должен лежать в пределах № 3 - 6 стандартной шкалы зернистости. [6]
Котельная сталь для изготовления паровозных и судовых котлов поставляется в виде листов. Сталь должна хорошо-свариваться, принимать деформацию в холодном состоянии ( загиб и отбортовку) и обладать пониженной склонностью к старению. [7]
Котельные стали ( 16ГНМ, 22К и др.) чувствительны к коррозионному растрескиванию под действием коррозионной среды и механических напряжений. Начальная стадия такого разрушения связана с электрохимическим воздействием на металл воды, которая с ним контактирует. При дальнейшем развитии коррозии процесс дополняется активным воздействием на металл концентраторов напряжений, появляющихся вблизи очагов коррозии и зародышей трещин. Вероятно, существует предельное напряжение, ниже которого коррозионное растрескивание этих сталей не наблюдается. Его величина зависит от состава стали. Для марок стали 16ГНМ и 22К он пока не определен. Однако эти стали могут подвергаться коррозионному разрушению и при более низком уровне средних растягивающих напряжений. Такое поведение сталей связано со склонностью их к водородной хрупкости и к так называемой щелевой коррозии. [8]
Испытанные котельные стали в продуктах сгорания березовского угля имеют высокую коррозионную стойкость из-за отсутствия в золе компонентов, ускоряющих процесс коррозии. [9]
Обычные малоуглеродистые котельные стали удовлетворительно сопротивляются газовой коррозии ( окислению) в условиях паровых котельных при температурах стенки не выше 450 - 500 С. [10]
Теплоустойчивые котельные стали перлитного класса чувствительны к воздушной закалке при различных технологических операциях, связанных с нагревом, склонны к хрупкому разрушению при остром надрезе и к нестабильности свойств при эксплуатации энергоустановок. [11]
Ряд котельных сталей подвержен отпускной хрупкости. Она наблюдается после отпуска при температурах 550 - 650 С и заключается в снижении в результате указанного процесса ударной вязкости при комнатной температуре. [12]
Хрупкость котельной стали, вызываемая щелочностью питательной воды, носит название межкристаллигной коррозии или щелочной хрупкости, называемой еще каустической хрупкостью. Такая высокая концентрация, во много раз превышающая допустимую для котловой воды, может создаваться лишь в отдельных местах котла при пропариваяии котловой воды, например в соединениях элементов котла при наличии в них неплотностей - в пазухах заклепочных швов, вальцовочных соединениях. Отмечается, что агрессивность котловой воды возрастает, если в ней имеется кремниевая кислота. [13]
Свариваемость котельных сталей является сложной технологической характеристикой, охватывающей ( вопросы металлургии сварочной ванны и процессы теплового воздействия электрической дуги ( или другого источника тепла) на металл околошовной зоны. [14]
Коррозия котельной стали в большинстве случаев протекает с учетом растворенного в воде кислорода, и целесообразно выяснить термодинамическую вероятность процесса коррозии в присутствии кислорода. [15]
Страницы: 1 2 3 4
www.ngpedia.ru
Материалы и способы изготовления котлов
Строительные машины и оборудование, справочник
Категория:
Общие сведения о кранах и котлах
Материалы и способы изготовления котловПаровой котел работает под значительным давлением, поэтому является весьма ответственным агрегатом и должен обеспечивать надежность в работе.
Чем выше рабочее давление и температура, при которой работает котел, тем в более тяжелых условиях находится металл, из которого изготовлен котел.
Основные требования к металлу котлов:1) высокая теплоустойчивость — способность металла сохранять прочность в условиях высокой температуры и больших напряжений;2) высокая вязкость — способность металла сохранять свои механические свойства при меняющихся или повторных нагрузках;3) пониженная склонность к старению — способность металла сохранять свои механические свойства в течение длительного времени;4) устойчивость металла против коррозии — под воздействием воды и пара;5) стабильность структуры — устойчивость металла против структурных изменений, снижающих его механические свойства;6) плотность, однородность строения металла, отсутствие в нем внутренних дефектов: плен, трещин и посторонних включений.
Поэтому элементы котла, находящиеся под давлением, изготовляются исключительно из стали (ГОСТ 5520—62). Эта сталь, кроме высоких требований относительно ее химического состава, подвергается более тщательному контролю и дополнительным испытаниям на ударную вязкость и чувствительность к старению.
Листовая сталь марок Ст. 2 и Ст. 3 предназначена для котлов и сосудов, работающих при температуре не выше 120°С. Для котлов, работающих при более высоких температурах, применяется сталь марок 15К и 20К.
Детали котла, не находящиеся непосредственно под давлением, могут изготовляться из углеродистых сталей обыкновенного качества (ГОСТ 380—60) или качественной конструкционной углеродистой стали (ГОСТ В 1050-60).
Котельные трубы — пароперегревательные, кипятильные, дымогарные и жаровые — изготовляются из стали марки 10 (ГОСТ 8733—58-и 8731—58). Все трубы подвергаются гидравлическим испытаниям, а также технологическим пробам на сплющивание и раздачу. Для дымогарных труб испытание на раздачу может быть заменено на бортование.
Электросварные трубы, изготовляемые в соответствии с ГОСТ 1753—53 и дополнительными к нему техническими условиями № 14—32,. находят все более широкое применение в котлостроении. Раньше части котла соединялись исключительно посредством заклепок. Клепка являлась основной и весьма ответственной операцией в котельных работах. В настоящее время трудоемкие клепальные работы сохранились лишь при ремонте старых котлов клепаной конструкции. Вновь строящиеся котлы изготовляются сварной конструкции, в которых все элементы соединяются электросваркой.
Электродуговая сварка элементов металлическим электродом (метод Славянова) представляет собой процесс последовательного местного расплавления кромок основного металла электрической дугой, возникающей между электродом и основным металлом. Температура, возникающая в результате образования электрической дуги, достигает 5500 °С.
Электродуговая сварка может производиться электродами трех видов: – простыми электродами — стальная проволока; – тонкообмазанными — электроды, покрытые тонким слоем мела, чем достигается устойчивость дуги; – электродами с толстой обмазкой — обмазкой сложного состава, содержащей шлакообразующие, раскисляющие, легирующие и другие компоненты, повышающие механические свойства наплавленного металла и качество сварного соединения в целом.
За последнее десятилетие широкое распространение получила автоматическая сварка под слоем флюса по методу акад. Патона, обеспечивающая высокое качество сварного шва и наибольшую производительность при выполнении сварочных работ. Сущность процессов сварки под слоем флюса заключается в том, что электрическая дуга непрерывно горит под толстым слоем порошкообразного флюса. Благодаря этому свариваемый металл защищен от окисления кислородом окружающего воздуха, процесс расплавления электрода и основного металла происходит равномернее, сварной шов получается ровным, плотным и однородным с хорошим проваром по всей глубине шва. Непрерывность ведения сварки под слоем флюса осуществляется при помощи специального приспособления, в котором изделия и электроды автоматически непрерывно перемещаются относительно друг друга, при этом происходит непрерывная подача электрода по мере его расплавления и слой флюса автоматически создается впереди движущегося электрода.
Для получения сварного соединения высокого качества свариваемые детали должны быть соответственно подготовлены: очищены от ржавчины и масла (до металлического блеска), кромки деталей соответствующим образом разделаны. Подготовка кромки под сварку производится согласно чертежам и зависит от характера соединения и толщины свариваемых элементов.
На рис. 24 и 25 представлены основные типы сварных соединений котла крана ПК-ЦУМЗ-15.
Одним из основных моментов, задержавших применение сварки в ответственных изделиях, какими являются паровые котлы, долгое время были затруднения в контроле качества сварного соединения.
Рис. 24. Примеры электросварных стыковых соединений: а —соединение огневой решетки с барабаном топки; б —соединение дымовой решетки с наружным барабаном котла; 1— огневая решетка; 2 — барабан топки; 3 —дымовая решетка; 4 — наружный барабан котла
Рис. 25. Соединение грязевого и шуровочного колец с барабаном топки и наружным барабаном котла:1—наружный барабан котла; 2 —барабан топки; 3—грязевое кольцо; 4 —-шуро-вочное кольцо; 5—предохранительный лист шуровочного кольца; 6 — лапа котла
В результате несовершенства способов контроля не было достаточной гарантии в том, что внутри сварного шва отсутствуют такие пороки, как пористость, газовые раковины, посторонние включения и малозаметные трещины, снижающие прочность соединения. По мере совершенствования технологии производства сварочных работ и методов контроля область применения сварки все более расширяется, в том числе и в котлостроении, но при этом следует иметь в виду, что ответственную сварку производят лишь сварщики, получившие на это разрешение после сдачи проб; пробы периодически повторяются.
Контроль сварного соединения заключается в следующем: – проверяют исходные материалы: исходный металл, подлежащий сварке, металл электрода, состав обмазки и флюса; – проводят испытания специальных контрольных образцов на растяжение и определение ударной вязкости; – анализируют химический состав наплавленного металла; – производят рентгеновские снимки, отражающие все внутренние пороки шва; – гидравлически испытывают сваренные изделия, работающие под давлением; – сварочный шов осматривают снаружи.
Читать далее: Характеристика топлива и процесс его сжигания в топке котла
Категория: - Общие сведения о кранах и котлах
Главная → Справочник → Статьи → Форум
stroy-technics.ru
Конструкционная углеродистая (котельная) сталь. Марки стали. Применение стали.
Справочная информация
Марки конструкционной углеродистой котельной стали ГОСТ 1050-88ст.12К, ст.15К, ст.16К, ст.18К, ст.20К
Применение конструкционной углеродистой котельной стали ГОСТ 1050-88Сталь 12К * Применяется для изготовления деталей, частей котлов и соссудов, работающих под давлением при комнатной, повышенной и пониженной температурах. Сталь 15К * Применяется для изготовления фланцев, днищ, цельнокованых и сварных барабанов паровых котлов, корпусов аппаратов и других деталей котлостроения и сосудов, работающих под давлением при температуре до +450 °С. Сталь 16К * Применяется для изготовления деталей и частей котлов, сосудов, работающих под давлением при комнатной, повышенной и пониженной температурах. Сталь 18К * Применяется для изготовления деталей и частей котлов, сосудов, работающих под давлением при комнатной, повышенной и пониженной температурах. Сталь 20К * Применяется для изготовления фланцев, днищ, цельнокованных и сварных барабанов паровых котлов; полумуфт, корпусов аппаратов и других деталей котлостроения и сосудов, работающих под давлением и при температуре до +450 °С; в качестве основного слоя при изготовлении горячекатаных двухслойных коррозионностойких листов.
ГП Стальмаш поставляет металлопрокат (более 2000 марко-профиле-размеров металлопродукции) в более чем 250 марках легированных сталей по следующей нормативно-технической документации (стандарты на сталь):
ГОСТ 4543-71, ГОСТ 19281-89, ГОСТ 1414-75, ГОСТ 1435-99,
ГОСТ 20072-74, ГОСТ 14959-79, ГОСТ 801-78, ГОСТ 5950-2000,
ГОСТ В 10230-75, ГОСТ 4728-99, ГОСТ 10884-94, ГОСТ 1050-88
и другие ГОСТ, ОСТ, ТУ, ТС.
Из наличия прокат стальной круглый отпускается от 100 - 500 килограмм, в зависимости от марко-профиле-размеров проката.
ГП Стальмаш производит отгрузку круглой металлопродукции со склада в г.Екатеринбург:
*на самовывоз,
*контейнерами (3-х, 5-ти, 20-ти тонные и 40-ка футовые),
*вагонами,
*отправка автотранспортными компаниями по всей территории России,
*отгрузка через желдорэкспедицию
Оперативная информация о ПОЛНОМ наличии на складе, ценах, условиях отгрузки по телефонам ГУП «Стальмаш»:
(343) 268-0789, (343) 269-2099,
(343) 268-6713, (343) 269-2102,
(343) 268-6735, (343) 269-3066,
(343) 268-7815, (343) 269-3106,
ГП Стальмаш поставляет металлопрокат (более 2000 марко-профиле-размеров металлопродукции) в более чем 250 марках легированных сталей по следующей нормативно-технической документации (стандарты на сталь):
ГОСТ 4543-71, ГОСТ 19281-89, ГОСТ 1414-75, ГОСТ 1435-99,
ГОСТ 20072-74, ГОСТ 14959-79, ГОСТ 801-78, ГОСТ 5950-2000,
ГОСТ В 10230-75, ГОСТ 4728-99, ГОСТ 10884-94, ГОСТ 1050-88
и другие ГОСТ, ОСТ, ТУ, ТС.
Из наличия прокат стальной круглый отпускается от 100 - 500 килограмм, в зависимости от марко-профиле-размеров проката.
ГП Стальмаш производит отгрузку круглой металлопродукции со склада в г.Екатеринбург:
*на самовывоз,
*контейнерами (3-х, 5-ти, 20-ти тонные и 40-ка футовые),
*вагонами,
*отправка автотранспортными компаниями по всей территории России,
*отгрузка через желдорэкспедицию
Оперативная информация о ПОЛНОМ наличии на складе, ценах, условиях отгрузки по телефонам ГУП «Стальмаш»:
(343) 268-0789, (343) 269-2099,
(343) 268-6713, (343) 269-2102,
(343) 268-6735, (343) 269-3066,
(343) 268-7815, (343) 269-3106,
yaruse.ru
Углеродистая котельная сталь - Большая Энциклопедия Нефти и Газа, статья, страница 1
Углеродистая котельная сталь
Cтраница 1
Углеродистые котельные стали 15К и 20К содержат небольшие количества серы и фосфора, и к ним предъявляются более жесткие требования в отношении обеспечения соответствующих свойств. Эти стали применяют при максимальной температуре 475 С. Температурный предел эксплуатации для этой стали такой же, как и для углеродистых сталей 15К и 20К, но сталь 16ГС лучше сваривается и отличается повышенной прочностью и ударной вязкостью. В то же время в изделиях она более склонна к трещинообразованию. [1]
Барабаны изготовляют из углеродистой котельной стали специальных марок или легированной стали. [2]
Объяснить, чем отличается выбранная сталь от углеродистой котельной стали. [3]
Силикат натрия обеспечивает практически полную защиту от коррозии углеродистых котельных сталей, независимо от механического напряжения и состояния поверхности. В отличие от действия одного едкого натра, недостаточная концентрация силиката натрия для полной защиты практически не вызывает локальной коррозии. [4]
Внутри корпуса концентрически вставлены экран 11 и жаровая труба 8, предохраняющие корпус, изготовленный из углеродистой котельной стали, от воздействия высокой температуры факела. Между корпусом и экраном, а также между экраном и жаровой трубой циркулирует в небольшом количестве воздух, который выпускается в конце камеры через отверстия в центрирующем конусе. Экран и жаровая труба опираются друг на друга ребрами и фиксируются относительно корпуса путем двусторонней приварки передних ребер. Лопасти его для жесткости и предохранения от вибрации соединены между собой при помощи двух приваленных колец, а также связаны двумя рядами проволоки. В передней части камеры сгорания расположено фронтовое устройство 6 с центральным 5, средним 5 и наружным 7 завихрителями. Фронтовое устройство подвешивается в корпусе с помощью трех радиальных полых пальцев, распределенных равномерно по окружности. Один из пальцев, расположенных в верхней половине, используется для датчика фотореле, а другой - в качестве глазка для визуального наблюдения за работой. [5]
Внутри корпуса концентрически вставлены экран 11 и жаровая труба 8, предохраняющие корпус, изготовленный из углеродистой котельной стали, от воздействия высокой температуры факела. Между корпусом и экраном, а также между экраном и жаровой трубой циркулирует в небольшом количестве воздух, который выпускается в конце камеры через отверстия в центрирующем конусе. Экран и жаровая труба опираются друг на друга ребрами и фиксируются относительно корпуса путем двусторонней приварки передних ребер. Лопасти его для жесткости и предохранения от вибрации соединены между собой при помощи двух приваренных колец, а также связаны двумя рядами проволоки. В передней части камеры сгорания расположено фронтовое устройство 6 с центральным 3, средним 5 и наружным 7 завихрителями. Фронтовое устройство подвешивается в корпусе с помощью трех радиальных полых пальцев, распределенных равномерно по окружности. Один из пальцев, расположенных в верхней половине, используется для датчика фотореле, а другой - в качестве глазка для визуального наблюдения за работой. [6]
Трубки конденсатора, промывочные дырчатые листы и жалюзийный сепаратор изготовляются из легированных нержавеющих сталей, корпус испарителя и остальные элементы установки - из углеродистых котельных сталей. [7]
Кривые относятся к стали, содержащей 0 05 - 0 15 % С в нормализованном состоянии. Характерным является изменение крутизны кривых временного сопротивления од и предела текучести стт и сближение их значений при температуре около - 150 С. Очень наглядно это явление можно проследить на диаграммах разрыва образцов углеродистой котельной стали марки 15К, приведенных на фиг. Для углеродистой стали характерным является наличие порога хладноломкости на кривой зависимости ударной вязкости от температуры, положение которого, как было отмечено ранее, даже в пределах одной марки зависит от целого ряда факторов, связанных как с условиями испытания, так и с технологией изготовления стали. [8]
Все разрывные машины должны подвергаться освидетельствованию и поверке не реже 1 раза в 2 года. Механические испытания на растяжение проводят при комнатной и при повышенной температурах. При повышении температуры характеристики механических свойств стали изменяются. Конфигурация кривых растяжения с ростом температуры также претерпевает изменения. На кривой полностью исчезает площадка текучести. В интервале температур от 200 до 300 С прочность углеродистых котельных сталей несколько повышается, а пластичность заметно снижается. Этот интервал температур назван интервалом синеломкости, так как окисная пленка, образующаяся на светлой механической обработанной поверхности металла, синего цвета. У легированных сталей температурный интервал понижения пластичности сдвинут в сторону более высоких температур и для стали 12Х1МФ составляет 500 - 510 С. [9]
При этом ударная вязкость снижается до 15 % по сравнению с исходным значением. Особенно резко при старении ухудшаются механические свойства, если степень пластической деформации составляет 3 - 10 %, что наблюдается при гнутье, вальцовке, клепке. Старение наклепанной стали происходит из-за ускоренного распада пересыщенных растворов углерода и азота в феррите с образованием мелкодисперсных карбидов и нитридов. Содержание углерода в стали в пределах 0 15 - 0 25 % существенно уменьшает склонность к старению. Существует еще один вид старения - механическое старение. При длительном нахождении на воздухе в условиях комнатной температуры или при кратковременном нагреве до температуры не менее 100 и не более ЗОО С ударная вязкость уменьшается, прочность увеличивается. При температуре более 400 С в углеродистых котельных сталях под действием давления рабочей среды и других нагрузок возникают и развиваются процессы ползучести. [11]
Страницы: 1
www.ngpedia.ru
Котельные марки стали. Kотельные трубы, классификация, особенности применения
Котельная сталь
Изобретение относится к металлургии, в частности к составу котельной стали, предназначенной для изготовления элементов энергетического оборудования (котлы, сосуды высокого давления), работающего в области температур до 500°С. Цель изобретения - повышение характеристик пластичности при 20, 500°С, ударной вязкости при комнатной температуре при сохранении уровня длительной прочности. Сталь содержит углерод, кремний, марганец, хром, ванадий, ниобий, железо при следующем соотношении компонентов, мас.%: углерод 0,17-0.20; кремний 0,17-0.37; марганец 0,65-1,00; хром 0,55-0,70; ванадий 0,05-0,08; ниобий 0,02-0,04; железо остальное , при выполнении соотношения хром ( ванадий 16.4-65.9. Применение углеродv ниобий г м стали позволяет повысить качество металлопродукции, сэкономить дефицитные легирующие элементы. 2 табл. Ј
СОн33 СОВЕТСКИХ
СОЦ1:",ЛЛИСТИЧГСК11Х
Р1 СПУГ,ЛИК
rsI>s С 22 С 38/26
ГОСУДЛРСТРГННЫй КОМИТЕТ
flO ИЗОГ>РГТРК НИЯМ И ОТКРЫТИЯМ
ПРИ ГКНТ СССР
ОПИСАНИЕ ИЗОБРЕТЕНИЯ
K АВТОРСКОМУ СВИДЕТЕЛЬСТВУ
° Ф 4
О
С)
О (21) 4829720/02 (22) 29.05.90 (46) 07,01.92. Бюл. ¹ 1 (71) Центральный научно-исследовательский институт черной металлургии им. И.П, Бардина (72) M.Â. Бобылев, Б.Ю. Зеличенок, В.Б. Киреев, А.М. Корешкова, В.В, Лебедев, О,В.
Носоченко, С.И. Ривкин. Ю.К. Петреня, В.И, Столяров, В.М. Хомяков и А.А, Чижик (53) 669. 14.018.4-194(088.8) (56) Авторское свидетельство СССР № 1420060, кл. С 22 С 38/26, 1988. (54) КОТЕЛЬНАЯ СТАЛЬ (57) Изобретение относится к металлургии, в частности к составу котельной стали, предназначенной для изготовления элементов энергетического оборудования (котлы, сосу%
Изобретение относится к металлургии, в частности к разработке котельной стали, предназначенной для изготовления элементов энергетического оборудования (котлы, сосуды высокого давления) работающего в области температур до 500 С.
Известна котельная сталь, содержащая, мас, 6: углерод 0,16-0,24; кремний 0,170,30; марганец 0,35-0,65; никель до 0,25; хром до 0,25; медь до 0,25; железо остальное, Недостатками данной стали являются низкие характеристики длительной прочности при температурах эксплуатации выше
400 С, низкая стабильность структуры при указанных температурах. Данная сталь применяется для изготовления элементов энергетического оборудования, работающего при температурах до 350- 400 С.
„„5U ÄÄ 1703709А1 ды высокого давления), работающего в области температур до 500 С, Цель изобретения — повышение характеристик пластичности при 20, 500 С, ударной вязкости при комнатной температуре при сохранении уровня длительной прочности. Сталь содержит углерод, кремний, марганец, хром, ванадий, ниобий, железо при следующем соотношении компонентов, мас. $: углерод 0,17-0,20; кремний 0,17-0,37; марганец 0,65 — 1,00; хром 0,55-0,70: ванадий 0,05 — 0,08; ниобий 0,02-0,04; железо остальное, при выполнении соотношения углерод ниобий (й )=16.4-65,9. Применение стали позволяет повысить качество металлопродукции, сэкономить дефицитные легирующие элементы. 2 табл.
Наиболее близкой по технической сущности и достигаемому эффекту к предлaraeмой является ст
pellete.ru