Основные работы, выполняемые на токарном станке. Все о токарной обработке
Токарная обработка. Виды токарных работ :: SYL.ru
Токарная обработка – наиболее распространенный тип обработки изделий из металла. Детали, имеющие форму тел вращения, составляют значительную долю продукции машиностроительных производств и входят в состав большинства машин и механизмов.
Краткая характеристика
Современное машиностроение характеризуется широкой номенклатурой изделий, при этом нестабильностью величины производственной партии деталей, которая меняется от нескольких штук до нескольких тысяч или десятков тысяч. Технологический процесс (ТП) обработки тел вращения отличается разнообразием технологических операций, маршрутов обработки и металлорежущего оборудования, применяемого при их изготовлении.
Согласно типовым маршрутам обработки и в зависимости от конструктивно-технологических особенностей и величины производственной партии тела вращения могут обрабатываться на различных типах токарных станков с ручным управлением и с ЧПУ при использовании как в качестве стандартной, так и специальной технологической оснастки.
История
Токарная обработка деталей на специализированных станках известна с VII века до н. э. Первые механизмы были примитивными: между двумя центрами устанавливалась костяная либо деревянная заготовка. Один человек (как правило, раб) крутил изделие, а мастер, удерживая в руках резец, снимал слой стружки. Процедура была долгой и трудоемкой.
После эпохи упадка (раннее Средневековье), в XIV веке, токарные работы уже проводились на механизмах, где вращение заготовке придавали при помощи ножного привода. К XVI веку станки обзавелись центрами из металла и люнетом. Стало возможным придавать изделиям сложную форму – вплоть до шара, однако механический привод не обеспечивал должной мощности. В XVIII веке усилиями русского изобретателя Нартова была решена задача жесткого крепления резца, что позволило точно нарезать резьбы, сложные узоры и т. д.
К XIX столетию создали мощные станки, полностью выполненные из металла, которые стали основой набиравшего обороты машиностроения. Вслед за массовой электрофикацией станки обзавелись электродвигателями, фактически приняв современную форму. Следующий значимый эволюционный этап связан с внедрением автоматизации и компьютеризацией.
Виды токарных работ
Обработка тел вращения выполняется на станках:
- токарно-винторезных;
- токарно-револьверных;
- с ЧПУ;
- многоцелевых;
- многошпиндельных;
- многорезцовых полуавтоматах.
При этом в зависимости от концентрации технологических переходов (последовательная, параллельная и последовательно-параллельная) применяются одно- или многорезцовые наладки с использованием стандартных или специальных режущих и вспомогательных инструментов.
Обработка на токарных станках отверстий производится как путем одноинструментной последовательной обработки, так и с использованием многошпиндельных головок и комбинированных осевых инструментов.
Выбор техпроцесса
Определяющее влияние на выбор типа токарных станков имеет величина производственной партии деталей и ее конструктивно-технологические особенности:
- максимальный диаметр;
- длина;
- требуемая точность;
- шероховатость поверхности.
Многообразие токарных станков приводит к росту числа конкурирующих вариантов техпроцесса. Например, пользуясь схемой формирования конкурирующих вариантов обработки валов, можно сформировать 20-30 возможных вариантов обработки ступенчатого вала. Поэтому необходимо выбрать правильный (оптимальный) токарный станок, обеспечивающий минимальную трудоемкость при максимальной экономической эффективности. При выборе варианта ТП также учитываются объем выпуска продукции и другие производственные условия.
Технико-экономические показатели
Токарная обработка металла объединяет два определяющих фактора – техническую возможность и целесообразность. В условиях многономенклатурного производства, которое характеризуется нестабильностью объектов и величины производственных партий деталей, выбор выгодного варианта техпроцесса из числа конкурирующих является сложной и трудоемкой задачей, которая требует проведения большого количества расчетов, связанных с определением технико-экономических показателей.
Основными показателями деятельности машиностроительных предприятий являются:
- производительность труда;
- прибыль;
- себестоимость продукции;
- интенсивность и эффективность использования финансовых ресурсов;
- материало- и энергоемкость продукции;
- рентабельность;
- фондоемкость и фондоотдача;
- коэффициент использования оборудования и другие.
Важной задачей является обеспечение конкурентоспособности продукции с учетом постоянно растущих требований к качеству изделий и ограничения затрат трудовых, материальных, финансовых и энергетических ресурсов.
Типы обрабатываемых деталей
Токарный станок позволяет обрабатывать заготовки типа тел вращения:
Наименование заготовки | Классификация | Изделия |
Цилиндрические детали вращения | Втулки | Втулки, вкладыши, буксы, гильзы |
Валы | Валы, валики, оси, штоки, цапфы, пальцы, штифты | |
Плоские детали вращения | Диски | Диски, кольца, маховики, шкивы, фланцы |
Многоосные детали | Эксцентрические изделия | Коленчатые валы, эксцентрики |
Детали вращения с перекрещивающимися осями | Крестовины | Крестовины, арматура |
Прочие заготовки | Зубчатые колеса | Одно- и многовенцовые зубчатые колеса, венцы, зубчатые колеса-валы, колеса-диски |
Фасонные кулачки | ||
Ходовые винты и червячные изделия | ||
Крепеж | Болты, гайки, винты |
Обработка ступенчатых валов
Токарная обработка вала может проводиться при помощи токарного, токарно-копировального, горизонтального многорезцового станка, вертикального одношпиндельного и многошпиндельного автомата, станка с ЧПУ. Устанавливают вал в центрах станка или закрепляют в патроне (планшайбе). Короткие заготовки, отливки, поковки закрепляют в трехкулачковом и реже в четырехкулачковом патронах. Валы с отношением длины к диаметру более 12 обтачивают с использованием подвижных и неподвижных люнетов.
Обычно на многорезцовых станках предусмотрены два суппорта (задний, передний). Передний предназначен для продольной обточки заготовок. Задний суппорт – для подрезания торцов, прорезания канавок, фасонной обточки. Количество резцов на мульти-суппортах может достигать 20. Движения суппортов автоматизированы.
Нарезание резьбы
В конструкциях валов встречаются внешние и внутренние крепежные резьбы. Токарная обработка осуществляется специальными резьбовыми резцами. Станки должны иметь быстрый реверс шпинделя для быстрой смены направления рабочего вращения на обратное, когда резьба будет нарезана до нужной глубины. При нарезании глухих резьб используют самовыключающиеся патроны. Внешние резьбы нарезают резьбонарезными головками, гребешками, резьбовыми резцами и другими методами. Калибровки резьбы выполняют плашками с доводочными режущими кромками.
Нарезание червяков
Винтовая поверхность червяков в зависимости от серийности может быть нарезана с помощью токарного либо профильного токарно-винторезного станка. Резцы для токарного станка выбирают с прямолинейным профилем. Нужный профиль витка при этом обеспечивается соответствующей установкой резца. При крупносерийном производстве червяки нарезают кольцевой резцовой головкой.
При чистовом нарезании червяков с некрупным модулем используются специальные пружинящие резцы. Для однозаходных заготовок, имеющих малый угол (до 7 градусов) подъема винтовой линии резцу придают профиль, соответствующий профилю впадины червяка.
Обработка корпусов
С помощью карусельно-токарных станков осуществляют точение корпусных деталей паровых турбин, крупногабаритных вентилей, электродвигателей, компрессоров, планшайб станков, центробежных насосов, генераторов и т. д. Использование простого и дешевого инструмента – резцов – позволяет снимать за рабочий ход до 15 мм, устанавливать относительно высокие режимы резания, выполнять непрерывную обработку. В результате токарные работы становятся более производительными.
Обрабатываемые заготовки со сложной пространственной формой или формой тел вращения с внутренними либо внешними коническими, цилиндрическими поверхностями, перпендикулярными торцами сравнительно просто получать путем точения.
Токарная обработка ЧПУ
Станки токарные с числовым программным управлением являются одними из самых распространенных видов оборудования современного серийного машиностроительного производства. Существенным преимуществом станков с ЧПУ по сравнению с другими станками, работающими в автоматическом и полуавтоматическом режимах, являются малые затраты времени и материальные на переход от обрабатываемой партии деталей к следующей. В настоящее время в машиностроении распространилось использование станков с ОПК (оперативным программным управлением). В этих устройствах программа может вводиться непосредственно с клавиатуры пульта управления отладчиком-оператором.
Технологические возможности
Станки с ЧПУ классифицируются по расположению оси вращения шпинделя (горизонтальные, вертикальные), расположению направляющих (наклонные, горизонтальные, вертикальные), структуре инструментальной системы (с револьверной головкой или инструментальным магазином), виду работ:
- патронные;
- центровые;
- патронно-центровые;
- карусельные.
Центровые станки (составляют около 10 % от всех станков с ЧПУ) служат для наружной отделки валов, включая нарезания резьбы резцом (наибольший диаметр Dmax заготовки 250-380 мм).
Патронные станки (около 40 %) применяют для обработки (наружной и внутренней) втулок, фланцев и прочих. Кроме обточки, расточки и подрезки торцов токарная обработка может на этих станках дополняться сверлением, зенкерованием, развертыванием, нарезанием резьбы метчиками, плашками, а также нарезанием внешней и внутренней резьбы резцом (Dmax 160-1250 мм).
Патронно-центровые (около 35 % парка ЧПУ-станков) сочетают технологические возможности первых двух групп. Их используют для патронной и центровой обработки деталей Dmax 160-630 мм. Для обработки изделий типа фланцев, дисков и корпусов больших размеров применяют карусельные станки.
Вывод
Используя методы токарной обработки, можно вытачивать разнообразные изделия, имеющие форму вращения, с требуемыми характеристиками. Обширный парк токарных станков позволяет изготавливать как миниатюрные детали, так и огромные – для энергетики, тяжелого машиностроения, судостроения и других отраслей.
www.syl.ru
Особенности проведения сложных токарных работ по металлу
Металловрезание имеет несколько видов, одним из них является токарная обработка, в том числе сложные токарные работы по металлу. Она представляет собой работу с поверхностью детали либо обработка, металл или древесина, при которой верхний слой обрабатываются с помощью специальных резцов, сверл или режущих насадок ,которые образуют на заготовке своеобразные припуски и бороздки. Токарная обработка может проводиться с целью подгона деталей под необходимые габариты либо целью получения необычной заготовки с технической точки зрения или необычной поверхности заготовки, при этом заказ работы токарной нужно только у квалифицированных мастеров.
Главным процессом, без которого невозможно представить работу на токарной установке, - это главное движение, именно так именуется вращение вокруг своей оси детали, во время которого наносятся насечки либо прорезается верхний слой. Очень важным является движение подачи, которое представляет собой постоянное главное движение без остановок и замедления скорости. Комбинирование движения подачи и главного движения позволяет работать с деталями различных форм, с различной поверхностью и, таким образом, на одном станке можно обрабатывать заготовки конической формы, цилиндра, с насечками, нанесёнными специальной резьбой, или фасонными деталями, при необходимости выполню токарные работы по металлу любой сложности на своем оборудовании.
Для того, чтобы мастер выполняя токарные работы заказ спб мог работать с различными деталями, заготовками, при этом выполнять разнообразные виды работ, в комплекте к токарному станку прилагаются специальные инструменты, с помощью которых можно сделать замеры, определить форму и обозначить местонахождение поверхности, на которой необходимо будет проводить резьбу, а также сверить схему работы с окончательным результатом. В случае, если производство не имеет серийный характер, то, как правило, применяются инструменты для измерения универсального характера, к ним в частности относятся штангенциркули, нутромеры и другие инструменты, а в случае серийного производства используются предельные калибры.
В этой работе мы расскажем определение токарной работы, токарного станка, особенности её проведения и дадим основное описание типам токарных работ, а также определим основные правила, в соответствии с которыми необходимо использовать станки токарного типа, при этом выполним токарные работы по металлу в ракурсе теоретического изучения. Информация предоставляется на базе изучение Учебной литературы научно-практическая информация, а также социально-экономическое и справочной информация, которая прилагается к работе. Всё это определяет теоретическую и методологическую основу работы.
Понятие токарной обработки. Типы проводимых работ на токарном станке
С помощью оборудования такого типа можно произвести следующие виды работ:
-
Обточить и очистить поверхность деталей, которые имеют цилиндрическую форму;
-
Скорректировать торцы;
-
Выточить канавки наружного типа;
-
Осуществить резку металла;
-
Высверлить на различные отверстия;
-
Провести зенкерование детали;
-
Развернуть или расточить отверстие канала по внутреннему типу;
-
Осуществить шлифовку и заказ металлообработки поверхности детали с помощью фасонных резцов;
-
Обработать резьбу с помощью плашек, резцов, метчиков и головок резьбы накатного устройства;
-
Работать с коническими деталями.
Работа осуществляется посредством специальных резцов, которые подбираются в зависимости от типа токарной обработки металла и делятся на черновые и чистовые. С помощью токарного станка можно обработать обширные и небольшие площади, провести сложные токарные работы по металлу, при этом обеспечить сечение необходимой глубины и регулировать срезаемый слой. Такую функцию обеспечивают различные геометрические параметры резцов. Резцы делятся на несколько типов:
Особенностью оттянутых резцов является то, что их лезвия более узкие по отношению к крепежной части и могут закрепляться симметрично.
Если рассматривать направление движения резцов, то они могут производить обработку детали справа налево и слева направо. Если резец располагаются с правой стороны, эта работа будет проводиться со стороны правой руки, резец будет располагаться недалеко от большого пальца. Функциональная особенность резца такого типа заключается в том, что он движется от задней и передней бабке, непосредственно справа налево. Лезвия отогнутого типа располагаются аналогично, единственной особенностью является то, что движущей является левая рука и расположены они также под большим пальцем левой руки. Движение производится слева направо. В зависимости от вида работ, которые могут ли проводиться, резцы для токарного станка делятся на:
-
Резцы проходного типа;
-
Резцы расточного типа;
-
Резцы для подрезания и отрезания;
-
Образцы для фасонной обработки;
-
Для проведения резьбовых отделочных работ.
Выбор геометрии резца влияет не только на точность выполненных работ, но и подбирается в зависимости от качества детали и поверхности, на которой будут проводиться работы. Очень важно учесть имеет ли деталь углы. В данном случае учитываются углы, которые образуются по краю резца и определяют направление движения токарной установки.
Главная и вспомогательная установка подбирается в зависимости от способа её установки, угол на вершине регулируются заточкой деталей.Если вспомогательный угол небольшой, то задействуется режущая кромка, а также повышаются показатели отвода теплоты и меняется уровень стойкости резца. При увеличении главного угла отжим увеличивается, вспомогательная кромка задействуется в меньшей степени, следовательно, уровень стойкости резца уменьшается. Если токарная установка работает с заготовкой, которая имеет большую длину и при этом небольшой диаметр, нужно учитывать возможность ее прогиба. В таком случае рекомендуется выбрать резцы, которые обладают наибольшим на главным углом, при этом для обработки детали потребуется применение меньшей силы и опасность прогиба будет практически исключена. Если работы проводятся на детали достаточно большого диаметра, рекомендуется выбирать главный угол в радиусе от 30 до 45 градусов, а для тонких заготовках выбирается угол 60 до 90 градусов.
Вспомогательный угол определяет расстояние и соотношение кромки вспомогательного типа и установкой резца. Неправильно подобранный угол может привести к тому, что кромка резца будет портить деталь, врезаясь в неё.
Резцы делятся на несколько подвидов:
-
Проходные подразделятся на прямые и изогнутые;
-
Бывают упорными или подрезного типа;
-
Расточные подразделяются на проходные и упорного типа;
-
Отрезные могут быть выполнены по типу фасонных и резьбовых.
Прямые резцы проходного отогнутого типа используются для нанесения резьбы на поверхности наружного типа. Где они, как правило, устанавливают главный угол в радиусе 45-60 градусов, а вспомогательный варьируется от 10 до 15 градусов. Проходные отогнутые резцы используются при продольном сечении. При поперечном могут использоваться исключительно подрезные. В случае, если обрабатывается цилиндрическая поверхность, возникает необходимость работы с торцовой частью, рекомендуется установить проходные упорные резцы, которые будут функционировать по продольному направлению. Резцы подрезного типа используют для отрезания заготовок, они функционируют по поперечному движению и контактируют с центром детали. Резцы различного типа устанавливают в случае необходимости увеличения отверстий, которые были предусмотрены штамповкой или выливанием детали. Такие резцы подразделяются на те, которые образуют сквозные отверстия и упорные. Основной их особенностью является форма лезвия, которое эффективно работает на разных углах. Резцы отрезного типа устанавливаются в том случае, если необходимо отрезать деталь либо выточить глубокие канавки. Резцы фасонного типа используются в том случае, если необходимо работать с фасонными поверхностями небольшой длины и при этом линия не превышает 30-40 миллиметров. Подбираются такие резцы в зависимости от профиля заготовки и могут быть стержневыми, округлыми или призматическими. В зависимости от направления работы они подразделяются на резцы радиального типа и тангенциального типа.
Такие резцы устанавливаются на токарных станках для обработки фасонной поверхности ,для которой применяются резцы стержневого типа либо резцы резьбового типа, которые помогают отрегулировать внутреннюю резьбу независимо от ее формы. Их подбирают в зависимости от профиля и размера резьбы, которая предусматривалась заготовкой.
В зависимости от строения, резцы делится на цельные, составные, припаянные, а также с механическим креплением пластин.
Державки резцов могут изготавливаться индивидуальные или серийные, их форма зависит от сечения и стали, которая используется, основными видами стали являются 40, 45, 50 и 40Х. Большой популярностью пользуется державки, которые крепятся на механическом креплении и изготовлены из твердосплавных пластин, так как они обладают большим уровнем прочности и предотвращают трещины, а также значительно продлевают срок эксплуатации крепежей.
Режущие пластины многогранного типа могут иметь три ,четыре, пять или шесть граней. Их необходимо подбирать в зависимости от положительного угла и лунок, с которыми необходимо будет работать.
Металлорежущий станок является универсальным, на него могут устанавливаться различные детали и принадлежности для того, чтобы обеспечить максимальную функциональность. Основными деталями являются патроны, центры и люнеты. Также очень часто используются такие детали, как сверлильные патроны, втулки для перехода, а также хомуты различного типа.
Кулачковый патрон обладает конструкцией, которая позволяет одновременно регулировать все 3 кулачка, в зависимости от радиального направления, именно благодаря этой особенности деталь может закрепляться по оси шпинделя.
В случае, если деталь имеет несимметричное сечение, очень важно закрепить её четырехкулачковый патрон с обязательным использованием планшайбы. Для того, чтобы обработать центр детали и обеспечить обращение, необходимо установить патроны подводкового типа. Длинные детали, которые имеют малый диаметр, закрепляются с помощью неподвижного либо подвижного люнета для того, чтобы предотвратить их деформацию.
Для конической обработки используют широкий токарный резец, регулируют верхние салазки, а также могут изменять расположение корпуса задней бабки. Это обеспечивается с помощью линейки копирной или конусной.
Широкий резец применяется для работы с короткими деталями конической формы, которые не превышают длину 25-30 мм.Коническая обработка предусматривает использование верхнего суппорта, а также регулирование угла его расположения, который должен быть равен 1/2 угла по вершине конуса детали, которая обрабатывается. В данном случае работа проводится исключительно при ручной подаче.
Если необходимо обточить заднюю бабку, то корпус смещается поперечно, если же необходимо провести обработку конической детали, то смещением детали производят под небольшим углом.
Если во время обработки использовать конусную линейку, можно изготовить поверхность конического типа, при этом угол на вершине будет достигать 40 градусов. В данном случае используется исключительно механическая подача.
Изучив форму и длину детали, можно определить какой способ крепления будет оптимальным:
-
Крепление в патроне;
-
Крепление в центре;
-
Крепление с помощью люнетов.
Работа с деталью, расположенной в центрах, позволяет устанавливать заготовку на несколько различных станках без проведения выверки. Обязательным условием такой обработки является предварительное засверливание отверстий центрового типа. Как правило, тип и размер таких отверстий стандартный. При креплении детали передняя и задняя бабка станка крепится именно в этих отверстиях и обеспечивает качественную фиксацию. Проводниковый патрон помогает вращать деталь от шпинделя по обрабатываемой поверхности.
Пиноли задней бабки и шпиндель используется для крепления центров. Такой центр обеспечивает вращение вместе с деталью, а в случае простоя и установки простого центра, который не вращается в ходе работы, наблюдается изнашивание центра и ухудшается состояние центрового отверстия детали. Для того, чтобы исключить эти негативные последствия, используют специальный центр срезанного типа, который применяется при подрезке торца, а также центр обратного типа, который может применяться в случае проведения токарных работ с деталью небольшого диаметра.
Обработка конструкционных материалов на малогабаритном широкоуниверсальном станке
Назначение и область применения станка
Малогабаритный станок мод. ЕРТ-03 относится к типу малогабаритных и позволяет проводить токарные работы с различными видами материалов, в том числе обрабатывать древесину и пластмассы. Характерной чертой данной модели является возможность настройки базового токарного варианта и изменения всех видов наладки, в том числе сверлильной и деревообрабатывающей. Такой станок многофункциональный и позволяет выполнять токарные работы по металлу, все виды сверлильных и расточных работ, а также фрезеровочные работы. А также с помощью него можно обрезать деталь, распиливать древесину, строгать, а также зачищать поверхность и полировать её.
Основные узлы и органы управления станком:
-
основа устройства;
-
рычаг для управления подачей механического запуска продольного типа;
-
покрытие гитары, под которой расположены зубчатые колеса сменного типа, они относятся к коробке подач;
-
рычаг управления диапазонами и скоростью движения шпинделя;
-
шпиндельная коробка;
-
сигнализатор работы электроустановки;
-
рычаг подключения движения шпинделя, как прямого, так и обратного;
-
кнопка «пуск» запуска блока электроустановки;
-
кнопка «стоп» для прекращения работы электроустановки;
-
крышка шпиндельной коробки;
-
стойка вертикального перемещения шпиндельной коробки с подвижной кареткой;
-
крышка блока электрооборудования станка;
-
маховик вертикального перемещения шпиндельной коробки;
-
винт вертикального перемещения стойки;
-
кожух ограждения электродвигателя и блока электрооборудования станка;
-
болт крепления каретки на стойке вертикального перемещения шпиндельной коробки;
-
трех кулачковый патрон;
-
резцедержка;
-
суппорт;
-
рукоятка зажима пиноли задней бабки;
-
задняя бабка;
-
маховик перемещения пиноли задней бабки;
-
маховик ручного продольного перемещения суппорта;
-
ходовой винт продольного перемещения суппорта;
-
маховик поперечного перемещения стола суппорта.
Основные технические характеристики станка
Диаметр детали, которая может устанавливаться на токарный станок:
-
в центральных частях - 105х440;
-
в патроне - 230 размер диаметра над суппортом;
-
на столе - 140 х 160 х 180.
Максимальные размеры детали, которая может устанавливаться:
-
на планшайбе или в патроне, 600 мм
-
Максимальный диаметр сверления, 10 мм
-
Диаметр отверстия в шпинделе, пинали задней Конус Морзе2 АТ6
-
бабки и вертикально-фрезерной головки (ГОСТ2848-75)
Максимальные перемещения рабочих органов, мм:
-
продольное суппорта при точении 440 (220)
-
продольное суппорта при фрезеровании 600 (480)
-
поперечное суппорта 100
-
вертикальное шпиндельной коробки 18
-
пиноли задней бабки 50
Максимальные наладочные перемещения стойки, мм:
-
Вертикальное 80
-
Горизонтальное 420
-
Максимальный ход зажимных губок тисок, 100 мм
-
Поворот резцедержки, град. 90х4
-
Максимальные размеры деревообработки,mmi
-
толщина распиловки (дисковой пилой) 35
-
ширина фугования 100
-
Максимальный ход вертикального стола, 100 мм
-
Максимальный ход подвижной резцедержки, 70 мм
-
Угол поворота подвижной резцедержки, 45 град
-
Максимальный угол поворота вертикально-фрезерной головки, 45 град
-
Количество ступеней частот вращения шпинделя 6
-
Диапазон частот вращения шпинделя, 1/мин. 160...2500
-
Продольная механическая подача, мм/об. 0,1…0,16
Шаг нарезаемых резьб:
-
метрических, 0,5...2,5 мм
-
дюймовых, п/1» (ниток на дюйм) 10...20
-
Цена деления лимба маховика, мм
-
суппорта, шпиндельной коробки и продольной подачи 0,02
-
пиноли задней бабки 0,04
-
Мощность электродвигателя, 0,37квт
-
Питание электрооборудования однофазное, 220B; 50 Гц
-
Габарит станка (длина х ширина х высота), 1120х680х640 мм
-
Масса (без оснастки и инструмента), 160 кг
Нормы работы с токарным оборудованием. Наиболее распространенные ошибки
Основными деталями и, на характеристики которых необходимо обращать внимание для длительной эксплуатации токарных устройств являются:
-
Вращающиеся детали и заготовки станочного типа;
-
Стружка, которая является результатом процесса резки.
Для того, чтобы обеспечить максимальный срок эксплуатации токарного устройства, необходимо хорошо закреплять детали перед началом проведения работ или регулировать скорость в зависимости от надежности крепления.
При проведении точения и чистовых видов работ точность сохраняется на уровне 7-8 квивалента, шероховатость сохраняется на уровне 1,6-3,2 мкм. Разрезка деталей осуществляется посредством специальных отрезных резцов, которые выбираются исходя из материала детали и диаметра. Могут использоваться прямые и обратные резцы такого типа. Особенностью прямых резцов является их длинная и неширокая головка, которая приспособлена для прорезывания детали и образования небольшого количества стружки. Их недостатком является невысокий уровень прочности и жесткости, эти факторы необходимо учитывать при выборе деталей, которые изготовлены из очень прочного материала. Если необходимо провести разрезание жестких заготовок, то место среза выбирается максимально близко к кулачкам патрона и не должно превышать 1 миллиметр от заготовки. Резец отрезного типа закрепляется рядом с линией центров станка, а по отношению к оси заготовки устанавливается перпендикулярно.
В случае, если возникает необходимость разреза детали большого диаметра, возможен такой вид поломки как обламывание резца. Такой эффект возникает в результате того, что перемычка прогибается и резец отрезного типа может быть защемлен в прорези. В таком случае рекомендуется не дорабатывать деталь до центра приблизительно 1,5-2,0 миллиметра, после чего прекратить работу с помощью резца и вручную далее осуществлять вращение шпинделя. Ни в коем случае нельзя поддерживать руками часть детали, которая отрезается. Также стоит учитывать, что если прорезь узкая и глубокая, то стружка может выходить достаточно медленно, поэтому режим работы станка необходимо отрегулировать, а диаметр прорези постепенно расширять.
Перед проведением сверления, зенкерование и развертывания, рекомендуется несколько раз проверить прибор для того, чтобы правильно соотнести центры.
Необходимыми условиями для правильного функционирования токарного станка являются:
-
правильная фиксация деталей;
-
правильное соотношение торца оси вращения и установка её строго перпендикулярно;
-
исключение выпуклостей на торце;
-
правильная установка сверла.
Для того, чтобы обеспечить все эти условия, необходимо подрезать торец перед началом проведения работ, а при установке детали обеспечить минимальный вылет. Для того, чтобы правильно установить направление движения сверла, рекомендуется сделать специальное углубление на детали с помощью центровочного сверла. Очень важно учесть, что глубина сверления должна соответствовать диаметру отверстия, которое должно получиться.
Очень редко сверление производится в ручном режиме, так как оно требует больших усилий и не всегда может быть проведено без нарушение центровки. В связи с этим рекомендуется обрабатывать детали диаметром более 20 мм двумя сверлами в автоматическом режиме. Первое сверло должно быть два раза тоньше предполагаемого отверстия, это обеспечивает равномерный выход стружки, постепенное врезание и значительно снизит усилие подачи.
Для того, чтобы зачистить поверхность и исключить образование заусенец, а также снять небольших фасок используют опиливание. Для его проведения выбирают напильники различной формы и с разными насечками. В зависимости от типа детали и предпочтения токаря, который проводит токарные работы по металлу в спб можно использовать насаженную или цельную ручку. Для того, чтобы избежать получения травм, рекомендуется выполнять опиливание примерно под углом 45 градусов с разворотом вправо. При этом ручка напильника должна находиться в левой руке, а его конец фиксируется правой.
Одним из заключительных этапов обработки детали является полирование, которое позволяет практически полностью исключить шероховатость и подготовить поверхность для дальнейшей обработки. Для полировки используют шлифовальные шкурки, которые подбираются в зависимости от поверхности и могут обладать разным уровнем в зернистости. Полировка проводится в ручную только правой рукой либо обеими руками, если поверхность достаточно обширна, при этом положение токаря, который проводит токарно фрезерные работы по металлу, должно быть аналогично положению при опиливании. Таким образом, шкурка удерживается левой рукой, а задний её конец придерживается правой. Меры предосторожности при ручном зашкуривании: одной из них является запрет охватывать рукой шкурку, так как существует риск наматывания на заготовку и защемления пальцев рук.
Учитывая то, что при опиливании, шлифовке с токарного станка не снимаются нерабочие резцы, необходимо проводить такой вид работы достаточно аккуратно для того, чтобы исключить порезы рук.
Заключение
При написании данной работы были выполнены все поставленные цели и задачи, а также проведён полный обзор работы на токарном станке, особенностей проведения определённых видов работы, мер предосторожности и устранения неисправностей.
На сегодняшний день обработка различных деталей на токарных станках пользуются большой популярностью, благодаря высокой точности замеров и обеспечению хорошего уровня полировки и шлифовки. Такие детали полностью готовы к дальнейшей обработке, при этом трудоемкость составляет от 20 до 35 процентов по отношению к трудоемкости обработки деталей, которые были обработаны на бортовом оборудовании. На сегодняшний день токарные станки модернизируют и основной задачей такого улучшения являются обеспечение высокой производительности и уменьшение времени на операции по подготовке перед проведением работ. Дальнейшая модернизация предусматривает полный отказ от ручного управления, которая чревато травмами и возможными неточностями при проведении работ. Основной целью модернизации токарного станка является включение ручного управления только на стадии заключительной обработки, а также изготовления деталей в единственном числе, максимальная автоматизация для того, чтобы оптимизировать оплату труда и уменьшить затраты на расходные материалы.
С помощью токарных станков можно:
-
производить различные детали цилиндрической и конической или фасонной формы, обрезать заготовки и осуществлять нарезку с помощью резцов метчиков и плашек.
-
очистить или обрабатывать резьбу различными сверлами с зенкером или развертками, которые позволяют подстроить деталь под необходимые параметры;
-
накатать рельеф или создать зубчатые колеса мелкомодульного типа.
Токарная установка пользуется большой популярностью благодаря своей функциональности и универсальности, так как на ней можно обрабатывать детали, изготовленные из различных материалов и подстраивать установку под практически любую форму и качество детали. Возможность проведения работ вручную позволяет обрабатывать даже самые хрупкие детали, при этом выполнять все требования по проведению работ. Как правило, последнее время токарная установка используется в качестве универсального оборудования с применением ручных настроек, это обусловливается большим количеством индивидуально изготовленных деталей, которые требуют индивидуального подхода, таким образом, стоимость проведения работ на токарной установке увеличивается, а квалификация токарей требует повышения.
karavangard.ru
Основные работы, выполняемые на токарном станке - Кустарь
Элементы и режимы резания
Прежде чем говорить о способах обработки, познакомимся вкратце с элементами и режимом резания.
Здесь нам встретятся новые понятия: глубина резания, подача, скорость резания.
Все они связаны между собой, и величина их зависит от различных причин.
Глубиной резания называется толщина слоя металла, снимаемого за один проход резца. Она обозначается буквой t и колеблется от 0,5 до 3 и больше миллиметров при черновой обработке до десятых долей миллиметра при чистовой обточке.
Подача —это движение резца вдоль обрабатываемой поверхности. Численно она выражается в миллиметрах, обозначается буквой S и указывает на величину смещения резца за один оборот детали. В зависимости от прочности обрабатываемого материала, жесткости узлов станка и резца, величина подачи может меняться от 0,1—0,15 мм/об до 2—3 мм/об при скоростных режимах резания. Чем тверже металл, тем меньше должна быть подача.
Скорость резания зависит от числа оборотов шпинделя и диаметра детали и подсчитывается по формуле.
Выбирая ту или иную скорость резания, нужно учитывать твердость обрабатываемого материала и стойкость резца, которая измеряется временем непрерывной работы его до затупления в минутах. Она зависит от формы резца, его размеров, материала, из которого изготовлен резец, от точения с охлаждающей эмульсией или без нее.
Наибольшую стойкость имеют резцы с пластинками из твердых сплавов, наименьшую — резцы из углеродистой стали.
Вот, например, какие скорости резания можно рекомендовать при точении различных материалов резцом из быстрорежущей стали. Стойкость его без охлаждения равна 60 минутам.
Примерные данные о скорости резания металлов:
Материал | Скорость резанияв м/мин. |
Серый чугун | 25 |
Твердая сталь | 25 |
Мягкая сталь | 50 |
Бронза | 75 |
Латунь | 100 |
Алюминий | 250 |
Обтачивание гладких цилиндрических поверхностей
Гладкие цилиндрические поверхности деталей обтачивают проходными резцами в два приема. Сначала черновым резцом производят обдирку — грубое обтачивание, — быстро снимая основную массу лишнего металла. На рисунке изображен прямой резец для черновой обработки:
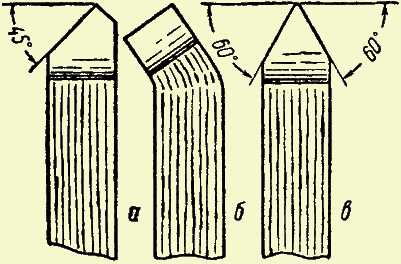
Черновые резцы: а — прямой; б — отогнутый; в — конструкции Чекалина.
Отогнутый резец удобен при протачивании поверхности детали около кулачков патрона и для подрезания торцов. Обычно резцы имеют рабочий ход только в одну сторону, чаще всего справа налево. Двухсторонний проходной резец конструкции токаря-новатора Н. Чекалина позволяет ликвидировать обратный холостой ход резца, сокращая время обработки.
После обточки черновым резцом на поверхности детали остаются крупные риски и качество обработанной поверхности поэтому невысоко. Для окончательной обработки служат чистовые резцы:
Чистовые резцы: а — нормальный; б — с широкой режущей кромкой; в — отогнутый, конструкции А. В. Колесова.
Нормальный тип чистового резца применяется при точении с небольшой глубиной резания и малой подачей. Чистовой резец с широкой режущей кромкой позволяет работать на больших подачах и дает чистую и гладкую поверхность.
Подрезание торцов и уступов
Для подрезания торцов и уступов на токарном станке пользуются обычно подрезными резцами. Такой резец изображен на следующем рисунке:
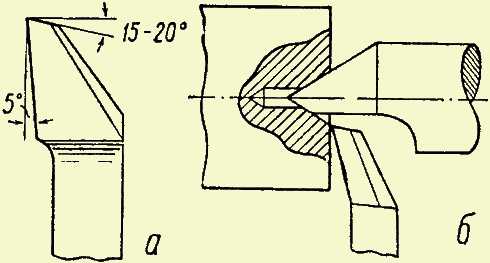
Подрезание в центрах: а — подрезной резец; б — подрезание торца с полуцентром.
Его лучше употреблять при точении детали в центрах. Для того, чтобы торец можно было обрабатывать целиком, в заднюю бабку вставляется так называемый полуцентр.
Если деталь закреплена только одним своим концом — при обработке в патроне, — то для проточки торца может быть использован и проходной отогнутый резец. Для этой же цели и для проточки уступов используются и специальные подрезные упорные резцы, которые работают с поперечной и с продольной подачей.
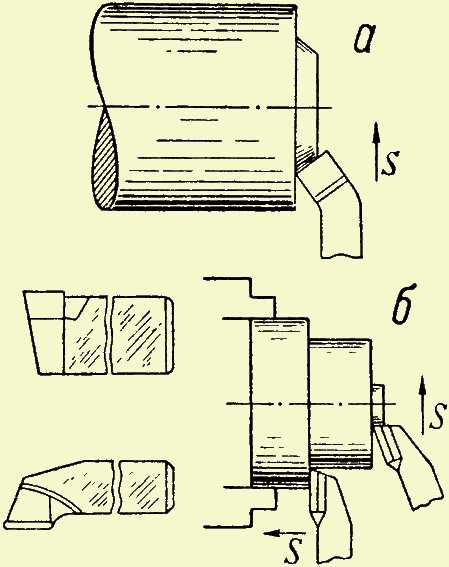
Подрезание торцов: а — подрезание проходным отогнутым резцом, б — подрезной упорный резец и его работа.
При подрезании торцов и уступов юный мастер должен следить за тем, чтобы вершина резца была всегда установлена строго на уровне центров. Резец, установленный выше или ниже уровня центров, оставит на середине сплошного торца неподрезанный выступ.
Вытачивание канавок
Для вытачивания канавок служат прорезные резцы. Их режущая кромка точно воспроизводит форму канавки. Так как ширина канавок обычно невелика, режущую кромку прорезного резца приходится делать узкой, поэтому она получается довольно ломкой. Для повышения прочности такого резца высоту его головки делают в несколько раз больше ширины.
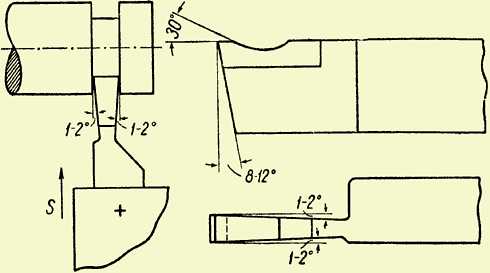
Прорезной и отрезной резцы
По этой же причине головка имеет небольшой передний угол.
Отрезные резцы очень похожи на прорезные, но имеют более длинную головку. Более узкая головка делается с целью сократить расход материала при отрезании.
Длина головки должна подбираться по размерам детали и быть несколько больше половины ее диаметра.
При установке прорезных и отрезных резцов нужно тоже быть очень внимательным и точным. Небрежная установка резца, например небольшой его перекос, вызовет трение резца о стенки канавки, брак в работе, поломку инструмента.
Вытачивание узких канавок производится за один проход резца, который подбирается по ширине будущей канавки. Широкие канавки вытачивают в несколько проходов.
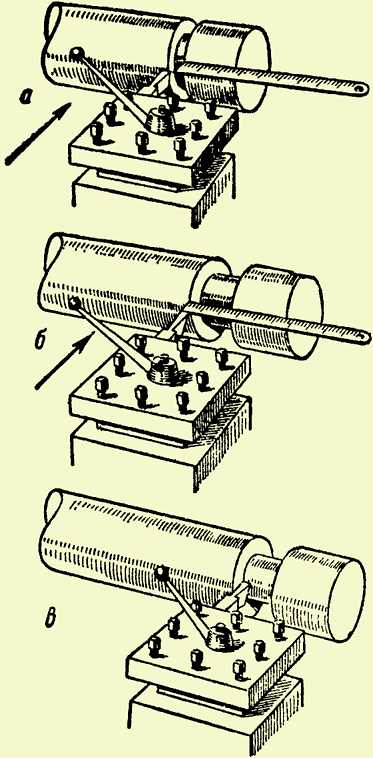
Последовательность операций при протачивании широкой канавки
Порядок работы таков: по линейке или другим мерительным инструментам намечают границу правой стенки канавки. Установив резец, протачивают узкую канавку, не доводя резец на 0,5 мм до нужной глубины — остаток для чистового прохода. Затем сдвигают резец вправо на ширину его режущей кромки и делают новую проточку. Выбрав таким образом канавку намеченной ширины, делают окончательный, чистовой проход резца, двигая его вдоль детали.
Установленную в центрах заготовку не следует разрезать до конца: обломившаяся часть может повредить инструмент. Короткую деталь, зажатую в патроне, можно отрезать начисто, пользуясь специальным отрезным резцом со скошенной кромкой.
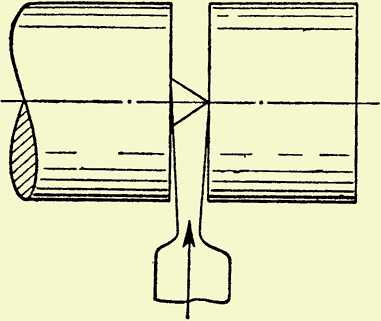
Прорезание детали до центра отрезным резцом со скошенной кромкой
Величина подачи и скорость резания при вытачивании канавок и отрезании должны быть меньше, чем при обработке цилиндров, потому что жесткость проходных и отрезных резцов не велика.
Вытачивание конусов
В практике юного токаря вытачивание конусов будет встречаться реже, чем другие работы. Наиболее простой способ— точение небольших конусов (не более 20 мм) специальным широким резцом.
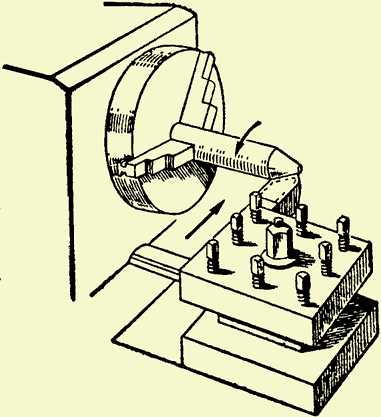
Вытачивание конуса широким резцом
При изготовлении наружного или внутреннего конуса на детали, закрепленной в патроне, пользуются другим приемом. Повернув верхнюю часть суппорта на угол, равный половине угла конуса при его вершине, протачивают деталь, двигая резец с помощью верхних салазок суппорта. Так точат относительно короткие конусы.
Для изготовления длинных и пологих конусов нужно сместить задний центр, передвинуть на определенное расстояние к себе или от себя заднюю бабку.
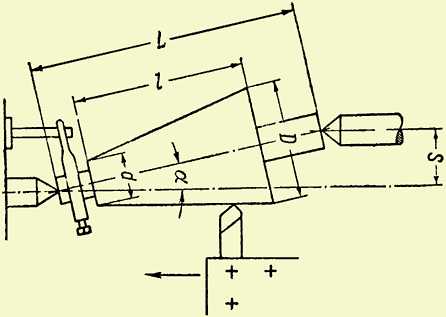
Обтачивание конической поверхности при поперечном смещении заднего центра
Если деталь закреплена в центрах таким образом, что широкая часть конуса будет у передней бабки, то заднюю бабку следует сместить к себе, и наоборот, при перемещении задней бабки от работающего широкая часть конуса будет находиться слева — у задней бабки.
Этот способ точения конусов имеет серьезный недостаток: вследствие смещения детали происходит быстрый и неравномерный износ центров и центровых отверстий.
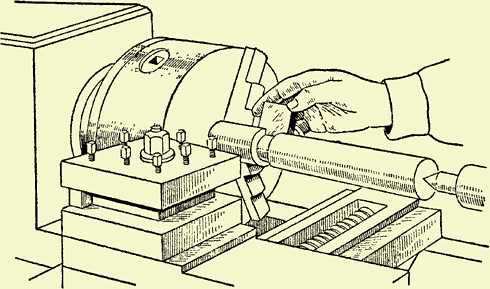
Проверка выточки шаблоном
Обработка внутренних поверхностей
Обработка отверстий может производиться различными инструментами, в зависимости от требуемой формы поверхности и точности обработки. На производстве встречаются заготовки с отверстиями, сделанными при отливке, ковке или штамповке. У юного металлиста готовые отверстия будут встречаться главным образом в отливках. Обработку отверстий в сплошных заготовках, не имеющих подготовленных отверстий, всегда придется начинать со сверления.
Сверление и рассверливание
Неглубокие отверстия на токарном станке сверлят перовыми и спиральными (цилиндрическими) сверлами.
Перовое сверло имеет плоскую лопатку с двумя режущими кромками, переходящую в стержень. Угол при вершине сверла обычно имеет 116—118°, однако он может быть, в зависимости от твердости материала, от 90 до 140°— чем тверже металл, тем больше угол. Точность отверстия при обработке перовым сверлом невелика, поэтому его употребляют тогда, когда большой точности не требуется.
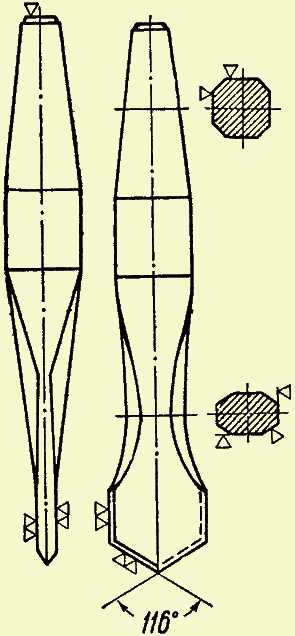
Перовое сверло
Спиральные сверла — основной инструмент для сверления. Точность обработки этими сверлами достаточно высока. Спиральное сверло состоит из рабочей и части конического или цилиндрического хвостовика, которым сверло крепится в пиноли задней бабки или в патроне.
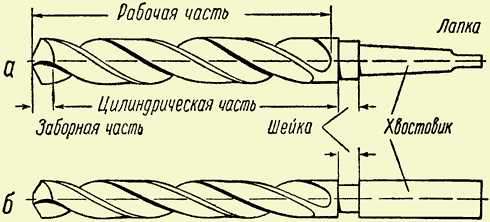
Спиральные сверла: а — с коническим хвостовиком; б — с цилиндрическим хвостовиком
Рабочая часть сверла — цилиндр с двумя винтовыми канавками, образующими режущие кромки сверла. По этим же канавкам выводится наружу стружка.
Головка сверла имеет переднюю и заднюю поверхности и две режущие кромки, соединенные перемычкой. Идущие вдоль винтовых канавок фаски направляют и центрируют сверло. Величина угла при вершине спирального сверла одинакова с перовым и может изменяться в тех же пределах. Изготовляются сверла из легированной или быстрорежущей стали. Иногда сверла из легированной стали оснащаются пластинками твердого сплава.
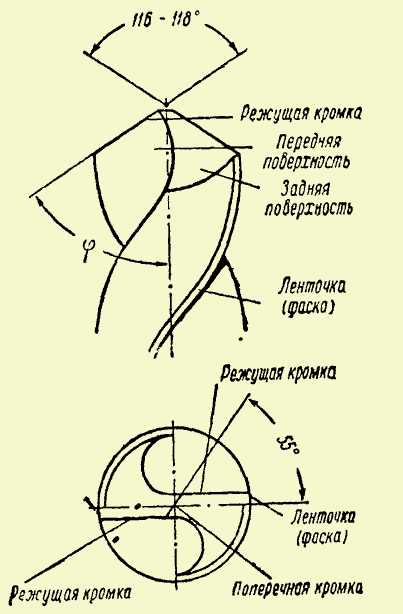
Передняя часть спирального сверла
Закрепление сверла производится двумя способами, в зависимости от формы хвостовика. Сверла с цилиндрическим хвостовиком закрепляются в пиноли задней бабки при помощи специального патрона, сверла с коническим хвостовиком вставляются прямо в отверстие пиноли.
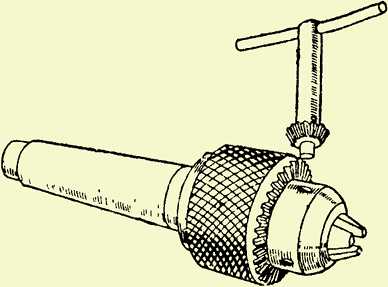
Патрон для закрепления сверл с цилиндрическим хвостовиком
Может случиться, что конический хвостовик мал по своим размерам, не подходит к отверстию. Тогда придется воспользоваться переходной втулкой, которая вместе со сверлом вставляется в пиноль.
Переходная втулка к сверлам с коническими хвостовиками: 1 — хвостовик сверла; 2 — втулка.
Чтобы вытолкнуть сверло из пиноли, нужно вращением маховичка затянуть ее в корпус задней бабки. Винт упрется в хвостовик сверла и вытолкнет его. С помощью специальной державки можно закрепить сверло и в резцодержателе.
При сверлении нужно внимательно следить за тем, чтобы сверло не уводило в сторону, иначе отверстие будет неправильным, а инструмент может сломаться. Подачу сверла производят медленным и равномерным вращением маховичка задней бабки или перемещением суппорта, если сверло с державкой закреплено в резцодержателе.
Высверливая глубокие отверстия, нужно время от времени выводить сверло из отверстия и убирать из канавки стружку.
Глубина отверстия не должна превышать длины рабочей части сверла, в противном случае стружка не будет выводиться из отверстия и сверло сломается. При сверлении глухих отверстий на заданную глубину можно проверять глубину сверления по делениям на пиноли. Если их нет, то отметку ставят мелом на самом сверле. Когда при сверлении слышится характерный визг, это значит, что либо сверло имеет перекос, либо оно затупилось. Сверление нужно немедленно прекратить, убрав сверло из отверстия. После этого можно остановить станок, выяснить и устранить причину визга.
Рассверливание — это то же сверление, но сверлом большего диаметра по уже имеющемуся отверстию. Поэтому все правила сверления относятся и к рассверливанию.
Другие методы обработки внутренних поверхностей
В практике юного токаря может встретиться и такой случай, когда диаметр нужного отверстия гораздо больше диаметра самого большого сверла в его наборе, когда в отверстии нужно выточить канавку или сделать его конусным. Для каждого из этих случаев существует свой метод обработки.
Растачивание отверстий ведется специальными расточными резцами — черновыми и чистовыми, в зависимости от нужной чистоты и точности обработки. Черновые резцы для проточки глухих отверстий отличаются от черновых резцов для точения сквозных отверстий. Чистовую обработку сквозных и глухих отверстий проводят одним и тем же чистовым резцом.
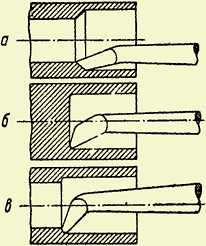
Расточные резцы: а — черновой для сквозных отверстий; б — черновой для глухих отверстий; в — чистовой
Растачивание имеет свои трудности по сравнению с наружным точением. Расточные резцы обладают малой жесткостью, их приходится значительно выдвигать из резцодержателя. Поэтому резец .может пружинить и гнуться, что, конечно, отрицательно влияет на качество обработки. Кроме того, затруднено наблюдение за работой резца. Скорость резания и величина подачи резца должны быть поэтому меньше, чем при наружной обработке, на 10—20%.
Особую трудность представляет обработка тонкостенных деталей. Зажимая такую деталь в патроне, ее легко деформировать, и резец выберет на вдавленных частях более толстую стружку. Отверстие не будет строго цилиндрическим.
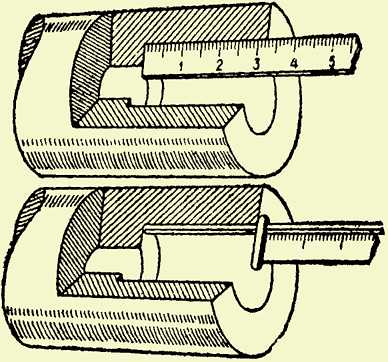
Измерение глубины расточенного отверстия
Для правильной обработки при растачивании резец устанавливается на уровне центров. Затем нужно расточить отверстие на 2—3 мм в длину и замерить диаметр.
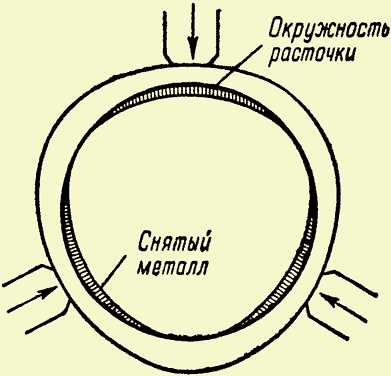
Неправильное растачивание детали, сильно зажатой в патроне
Если размер верен, можно растачивать отверстие на всю длину. При растачивании глухих отверстий или отверстий с уступами, так же как и при сверлении, на резце делают мелом отметку, указывающую глубину растачивания.
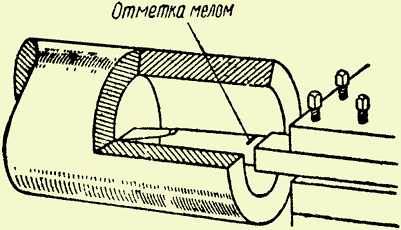
Подрезание внутреннего торца
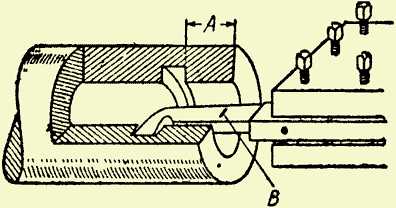
Вытачивание внутренней канавки
Подрезание внутренних торцов производится подрезными резцами, а вытачивание внутренних канавок — специальными прорезными канавочными резцами, у которых ширина режущей кромки в точности соответствует ширине канавки. Резец устанавливается на соответствующую глубину по меловой риске на теле резца.
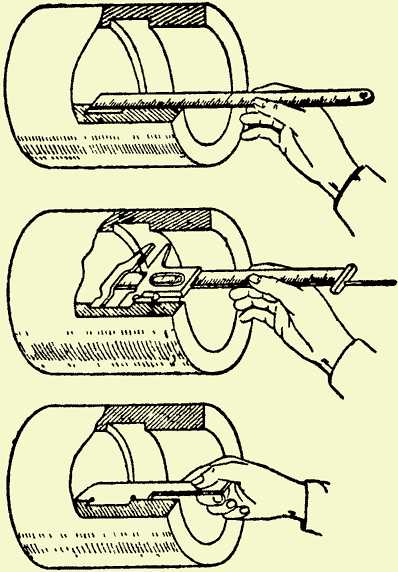
Измерение внутренней канавки: линейкой, штангенциркулем и шаблоном
Кроме расточных резцов, для растачивания цилиндрических отверстий употребляются зенкеры. Они похожи на спиральные сверла, но имеют три или четыре режущие кромки и не годятся для получения отверстий в сплошном материале.
Спиральные хвостовые зенкеры: а — из быстрорежущей стали; б — с пластинками из твердого сплава
Очень чистые и точные цилиндрические отверстия делают развертками. Оба эти инструмента применяют не для расширения отверстия, а для подгонки под точный размер и форму.
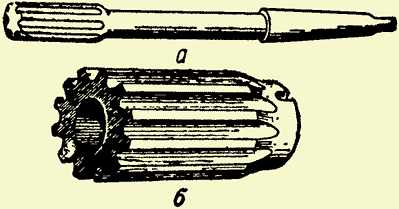
Развертки: а — хвостовая; б — назадная
Изготовление конических отверстий
Вытачивание внутренних конусов, пожалуй, наиболее трудное дело. Обработка ведется несколькими способами. Часто конические отверстия делают растачиванием резцом с поворотом верхней части суппорта.
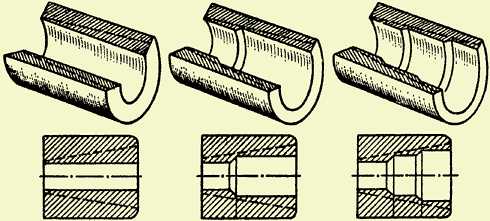
Высверливание ступенчатого отверстия под конус
В сплошном материале предварительно нужно высверлить отверстие. Для облегчения растачивания можно высверлить ступенчатое отверстие. Следует помнить, что диаметр сверла нужно подбирать с таким расчетом, чтобы оставался припуск в 1,5—2 мм на сторону, который затем снимается резцом. После точения можно воспользоваться коническим зенкером и разверткой. Если уклон конуса невелик, сразу же после сверления применяют набор конических разверток.
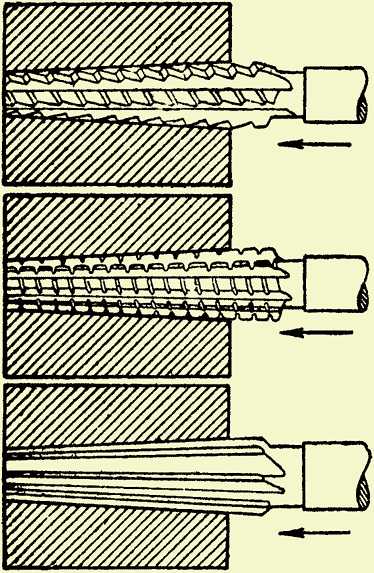
Изготовление конического отверстия набором разверток
Последняя из основных операций, производимых на токарном станке, — нарезание резьбы.
Механическое изготовление резьбы возможно только на специальных винторезных станках. На простых станках эта операция производится вручную. Приемы ручного изготовления наружной и внутренней резьбы изложены выше.
Измерительный инструмент
В токарных работах используется тот же инструмент, что и при слесарной обработке: стальная линейка, кронциркуль, штангенциркуль и другие. О них уже было сказано раньше. Новыми здесь могут быть различные шаблоны, которые юный мастер будет изготовлять сам. Они особенно удобны при изготовлении нескольких одинаковых деталей.
Помните, что все измерения можно производить только после полной остановки станка. Будьте осторожны! Не производите замеров вращающейся детали!
Меры предосторожности
При работе на токарном станке нужно руководствоваться следующими правилами:
1) начинать работать на станке можно только после детального ознакомления со станком и методами обработки;
2) не работать на неисправном станке или негодным (тупым) инструментом;
3) прочно закреплять деталь и следить за исправностью ограждающих устройств;
4) не работать в свободной одежде: рукава завязывать у кисти, длинные волосы прятать под головной убор;
5) своевременно убирать стружку и следить за порядком на рабочем месте;
6) не останавливать руками вращающийся патрон;
7) в случае неисправности немедленно выключить станок.
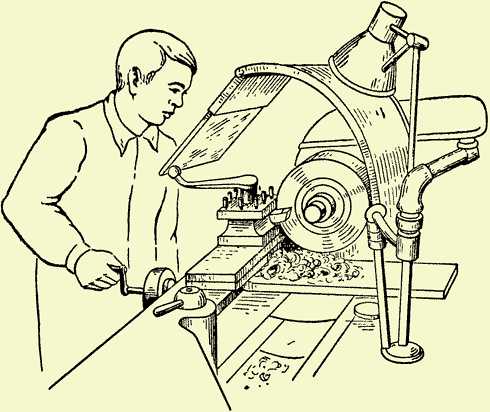
Применение защитного щитка при точении
Уход за станком
Чем тщательнее уход за станком, тем лучше и дольше он будет работать. Это простое правило следует твердо запомнить и аккуратно его выполнять. Уход за токарным станком сводится к следующему.
Основное — это смазка всех трущихся частей. Перед началом работы необходимо осмотреть станок и проверить, достаточно ли смазки. Наиболее внимательно нужно следить за смазкой подшипников, заполняя масленки и смазочные отверстия машинным маслом. Станок в это время, во избежание несчастного случая, должен быть остановлен.
После работы нужно вычистить станок, убрать стружку, протереть направляющие станины и суппорта, и смазать их тонким слоем масла.
Абсолютно чистыми должны быть и конические отверстия шпинделя и пиноли задней бабки. Точность работы станка будет зависеть от их хорошего состояния.
До начала работы нужно также проверить состояние приводного ремня. Его нужно оберегать от масляных брызг и капель, так как замасленный ремень проскальзывает и быстро срабатывается. Натяжение ремня должно быть не слишком сильным, но и не слишком слабым: слабо натянутый ремень проскальзывает, а при сильном его натяжении сильно греются и быстро изнашиваются подшипники. Ограждение приводного ремня тоже должно быть в порядке.
Автор: П.В. Леонтьев
Читайте еще:
www.sdelaysam.info
Все о токарной обработке - ВЕРЕС-С (Зеленоград)
Токарная обработка
Токарная обработка является одной из разновидностей обработки металлов резанием. Она осуществляется срезанием с поверхностей заготовки определенного слоя металла резцами, сверлами и другими режущими инструментами.
Вращение заготовки, посредством которого совершается процесс резания, называется главным движением, а поступательное перемещение инструмента, обеспечивающее непрерывность этого процесса,— движением подачи. Благодаря определенному сочетанию этих движений на токарных станках можно обрабатывать цилиндрические, конические, фасонные, резьбовые и другие поверхности.
При токарной обработке измерительные инструменты применяются для определения размеров, формы и взаимного расположения отдельных поверхностей деталей как в процессе их изготовления, так и после окончательной обработки. В единичном и мелкосерийном производстве используются универсальные измерительные инструменты — штангенциркули, микрометры, нутромеры и др., а в крупносерийном и массовом — предельные калибры.
Целью данной работы является определение сущности и особенностей организации токарной обработки, характеристика основных видов токарных работ, а также рассмотрение правил эксплуатации токарных станков.
Теоретической и методологической основой работы является анализ учебной, научно-практической, социально-экономической, а также справочной литературы, список которой прилагается.
Основные виды токарных работ
На токарных станках выполняют токарное обтачивание цилиндрических поверхностей, токарное подрезание торцов, токарное вытачивание наружных канавок, токарное отрезание металла, токарное сверление, токарное рассверливание, токарное зенкерование, токарное развертывание, токарное растачивание отверстий и внутренних канавок, токарное центрование, токарную обработку, токарную обработку поверхностей фасонными резцами, токарную нарезку резьбы плашками, метчиками, резцами, резьбонакатными головками, токарную обработку конических поверхностей.
Основными инструментами при токарной обработке являются резцы. В зависимости от характера обработки резцы бывают черновые и чистовые. Геометрические параметры режущей части этих резцов таковы, что они приспособлены к работе с большой и малой площадью сечения срезаемого слоя. По форме и расположению лезвия относительно стержня резцы подразделяют на прямые, отогнутые, и оттянутые. У оттянутых резцов ширина лезвия обычно меньше ширины крепежной части. Лезвие может располагаться симметрично.
Обработка на металлорежущих станках является наиболее распространенным методом формообразования поверхности твердых тел с высокой точностью размеров и низкой шероховатостью. Например, в общей трудоемкости радиотехнических изделий бортового оборудования 20 - 35 % составляет трудоемкость механической обработки. В настоящее время проводится политика замены предварительных операций обработки резанием на более высокопроизводительные методы (обработка давлением, точное литье и др.), чтобы на металлорежущих станках проводить только заключительные операции по изготовлению деталей РЭС с целью дальнейшего снижения затрат труда и материалов на производство РЭС.
На токарных станках производится обработка наружных и внутренних цилиндрических, конических, фасонных поверхностей, торцевых плоскостей; нарезка резьбы внутренней и наружной резцами, метчиками и плашками; обрабатываются отверстия сверлами, зенкерами, развертками; накатывается рельеф и мелкомодульные зубчатые колеса и другое.
Таким образом, токарная обработка является одним из самых универсальных видов обработки. Этим методом можно получать детали любой формы при любых требованиях к чистоте и точности обрабатываемых поверхностей. Однако универсальность токарной обработки (универсальные методы, универсальное оборудование) способствует увеличению стоимости изготовления, т.к. многие операции требуют ручного труда высокой квалификации.
zeltorg.com
Токарная обработка различных деталей
Токарная обработка кажется простым и понятным процессом. Это объясняется тем, что выбор нужной детали ограничен существующими телами вращения, а движение инструмента осуществляется только в одной плоскости. Однако в действительности это не так. В токарной обработке используются различные формы применяемого инструмента и широкий спектр разнообразных технологий.
Технические возможности
Токарная обработка с технической точки зрения позволяет выполнить следующие операции:
- обточку и расточку круга и поковок;
- торцевание и обработку плоскости;
- прорезку канавок разного профиля;
- нарезание резьбы.
Типы
Существует несколько типов токарной обработки, а именно:
- Токарная металлообработка. Этот метод позволяет получить цилиндрические детали за счет резания. Данный тип обработки считается наиболее востребованным. Для осуществления такой процедуры используется материал высокой степени твердости, прочности, тепло- и износостойкости. Зачастую на токарных станках обрабатывают инструментальные углеродные и легированные стали, включая металлокерамические сплавы.
- Сверление. Этот процесс позволяет сделать в металлических заготовках глухие и сквозные отверстия. Для этого используется спиральное сверло.
- Растачивание. Данная процедура применяется с целью увеличения диаметра отверстий в детали. Такая работа проводится на вертикальных либо горизонтальных расточных станках.
- Строгание. Данная процедура осуществляется при помощи возвратно-поступательной работы резцов. Различают для такой обработки продольно-строгальные и поперечно-строгальные станки.
- Протягивание. Эта процедура позволяет произвести механическую обработку изделия. В основе данной работы применяется инструмент с большим количеством лезвий.
- Фрезерование. Осуществляется такая процедура специальным эффективным инструментом с различными лезвиями либо фрезами разной формы.
- Шлифование. Токарная обработка на заключительном этапе представлена в виде данной процедуры, которая заключается в шлифовке поверхности изделия при помощи острых граней абразивных материалов, которые снимают тонкий слой металла.
Токарная обработка деталей
Чтобы получить цилиндрические детали, мастера применяют токарную обработку деталей. Эта процедура осуществляется в виде расточки и обточки цилиндрических, конических и фасонных поверхностей, а также подрезки и обработки торцов, сверления, нарезания резьбы. Токарная обработка деталей может осуществляться как на токарном станке по металлу, так и на токарном станке по дереву. Все зависит от имеющегося оборудования.
Токарная обработка дерева. Особенности и основные моменты
Еще одним немаловажным процессом в токарном деле является токарная обработка дерева. Для осуществления такой работы используются станки по дереву, предназначенные для вытачивания разных фигур из дерева цилиндрической формы. Неплохими инструментами принято считать те станки, рабочая поверхность которых изготовлена из стали высокого качества. Токарный станок позволяет изготовить самые разнообразные изделия: прялки, посуду, игрушки, прочие бытовые предметы.
fb.ru
1. Сущность токарной обработки. Основные виды токарных работ. Токарная обработка
Похожие главы из других работ:
Железоуглеродистые сплавы. Медь и ее сплавы
2.3 Основные виды термической обработки стали
...
Комплексное нормирование работ при изготовлении машины
5.1 Нормирование токарных работ
Определить штучно - калькуляционное время при обработке на токарно-винторезном станке (модель 1К62) детали с припуском под термообработку и шлифование. Шероховатость поверхности со всех сторон - Rа 25.Инструмент - резцы с пластинками Т15К6, Т5К10...
Обработка деталей на токарных станках
Основные понятия и определения токарной обработки
Токарная обработка (точение) - наиболее распространенный метод изготовления деталей типа тел вращения (валов, дисков, осей, пальцев, цапф, фланцев, колец, втулок, гаек, муфт и др.) на токарных станках...
Объемная штамповка и обработка металлов резанием
2.2 Основные типы токарных станков
Станки токарной группы наиболее распространены в машиностроении и металлообработке по сравнению с металлорежущими станками других групп. В состав этой группы входят токарно-винторезные, токарно-револьверные, токарно-карусельные...
Основные сведения о токарной обработке
1.1 Сущность токарной обработки
Токарная обработка является одной из разновидностей обработки металловрезанием. Она осуществляется срезанием с поверхностей заготовки определенного слоя металла (припуска) резцами, сверлами и другими режущими инструментами...
Повышение надежности технического обслуживания Перовской дистанции сигнализации и связи
2.1 Основные виды работ по техническому обслуживанию устройств СЦБ на Перовской дистанции
Основными видами работ по техническому обслуживанию устройств сигнализации...
Повышение надежности технического обслуживания Перовской дистанции сигнализации и связи
2.2 Основные виды работ по текущему ремонту устройств СЦБ
Основными видами работ по текущему ремонту устройств СЦБ являются: разборка, проверка, восстановление или замена износившихся деталей, сборка, измерение параметров и характеристик, регулировка и испытание аппаратуры и оборудования...
Разработка технологического процесса восстановления газораспределительного вала автомобиля ВАЗ-2109
2.5.3 Техническое нормирование токарных работ
Определить штучное время на обтачивание опорных шеек распредвала до наплавки. Припуск - 0,5 мм. Диаметр вала 45,02 мм, длина шейки - 26 мм. Оборудование - ТВС 1616. Дополнительные данные: - материал детали - сталь 20ХН3А или 25ХГН - резец - проходной...
Резцы, инструмент, режущий элемент, безопасность труда, токарный станок, резец, слесарное дело, токарное дело
2.1 Основные типы токарных станков
Станки токарной группы наиболее рас-пространены в машиностроении и металлообработке по сравнению с металлорежу-щими станками других групп. В состав этой группы входят токарно-винторезные, токарно-револьверные, токарно-карусельные...
Сооружение резервуара РВС 20000 м. куб. на ЛПДС "Торгили"
2.3 Основные виды производства работ
- подготовительные работы: намечают трассы временных подъездов и места отвалов растительного и подстилающего грунтов, после разметки срезают растительный грунт и делают остальные виды работ...
Сырье в промышленности. Металлорезание
2. Сущность, назначение и виды термической и химико-термической обработки
Термической обработкой стали называется совокупность технологических операций ее нагрева, выдержки и охлаждения в твердом состоянии с целью изменения ее структуры и создания у нее необходимых свойств: прочности, твердости, износостойкости...
Сырье в промышленности. Металлорезание
3.Современные способы обработки металлов резаньем. Сущность технологических процессов обработки на токарных станках. Элементы режимов резания при точении
Резанье металлов - это обработка путем снятия стружки. В процессе обработки рабочее движение сообщаемое заготовке и режущему инструменту обеспечивает снятие стружки нужных размеров...
Термическая и химико-термическая обработка сплавов
2.1. ОСНОВНЫЕ ВИДЫ ТЕРМИЧЕСКОЙ ОБРАБОТКИ
Собственно термическая обработка включает следующие виды: -отжиг 1-го рода, -отжиг 2-го рода, -закалку без полиморфного превращения и с полиморфным превращением - старение - отпуск...
Технология выполнения токарных работ
1. Виды и причины брака при изготовлении изделий на токарных станках
Брак при обтачивании цилиндрических поверхностей и меры его предупреждения...
Технология сварки металлов
1. Основные виды термической обработки стали
Термическая обработка стали - это совокупность операций нагрева, выдержки и охлаждения твёрдых металлических сплавов с целью придания им определённых свойств за счёт изменения внутреннего строения и структуры. После проката, литья, ковки...
prod.bobrodobro.ru
Технология и режимы работы токарной обработки
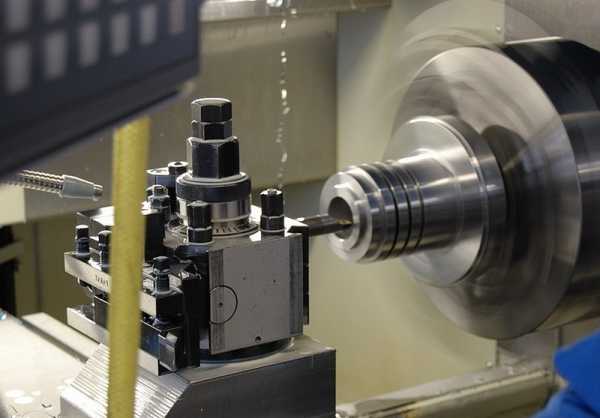
Токарная обработка
Токарные станки появились пару сотен лет назад. Они позволили добиться огромного прогресса в металлообработке. Технологии изменились, но назначение токарной обработки все то же. Суть процесса токарной обработки состоит в снятии лишних частей с поверхности металлической или деревянной заготовки и доведения ее до нужной шероховатости, размеров и формы.
Стандартной продукцией токарной обработки являются детали различных вращательных механизмов, например:
- Зубчатые колеса
- Болты
- Гайки
- Кольца
- Валы
- Муфты
- Шкивы и т.д.
Хотите уточнить Стоимость?
Виды токарных работ.
Новые технологии в токарном деле дают возможность вытачивать детали любой формы с помощью фрезы. Именно это современное оборудование оснащено программным обеспечением, которое автоматизирует весь процесс.
Такие токарные станки выполняют:
- Обработку цилиндрических и конических поверхностей заготовок как снаружи, так и внутри
- Вытачивание канавок
- Сверление, развертывание и зенкерование отверстий
- Отрезку заготовки
- Обработку фасонных поверхностей
- Обработку торцов и уступов
- Протачивание резьб: наружной и внутренней
- Накатывание рифлений.
Режимы токарной обработки
Выполняя токарные работы, необходимо выбрать режимы работы станка, а именно:
- Продольную подачу
- Глубину резки
- Скорости резки.
Эти три режима являются определяющими факторами в работе и помогают достичь:
- Высокой устойчивости режущего инструмента
- Сохранения поверхности в надлежащем состоянии для проведения работ
- Высокой скорости вращения шпинделя
- Допустимого количества металлической стружки
Скорость резания.
Скорость резки — величина, определяющая частоту вращения шпинделя. Прежде всего, скорость резания зависит от материала, помимо этого на нее влияет качество и прочность резцов, способ охлаждения, подача и глубина резки. Скорость резания является очень важным параметром: чем она выше, тем производительнее работа станка, а также качество и точность заготовок.
Глубина резания.
Глубина резки — определяется размером подачи резца. Поперечное резание зависит от ширины кромки применяемой резки. Как правило, припуск обработки снимается несколькими проходами, хотя стремиться нужно к минимальному значению количества проходов. В идеале, снятие припуска нужно выполнять в один проход, но только при высокой: жесткости детали, прочности резца и мощности токарного станка. Если имеется большой припуск и высокая чистота поверхности — припуск разделяется на 2 прохода.
Режим подачи.
Токарная обработка материала выполняется с большой подачей, это помогает добиться высокой производительности при работе с заготовкой. Для соблюдения нормальной подачи, нужно учитывать такие величины: жесткость детали, прочность механизма подачи и прочность резца. (для черновой обработки). Если же выполняется чистовая и получистовая токарная обработка — подача зависит от чистоты обрабатываемой поверхности и точности производства детали.
Технология токарной обработки
Технология токарной обработки.
Токарная обработка проходит по следующему сценарию: в заготовку врезается режущий инструмент, крайняя часть которого плотно прижимается к детали, борясь с силами сцепления внутри конструкции, снимает лишний слой металла на поверхности, превращая его в стружку.
Преимущества токарной обработки.
Токарная обработка является одним из главных способов изготовления различных металлических деталей. Без токарных станков не обходиться ни одно современное предприятие, все это благодаря неоспоримым преимуществам данных механизмов. Они позволяют производить изделия очень сложной геометрии и высокой точности. Процесс обработки заготовок оставляет мало отходов. К тому же, металлическая стружка может быть переплавлена повторно, что еще больше снижает процент отходов.
Мы принимаем заказы на изготовление, как единичных деталей, так и партий мелко и среднесерийного производства.
Узнать примерную стоимость токарных работ на заказ работ можно по:
Тел: +7 (495) 411-10-51
E-mail: [email protected]
kmkmsk.ru