Карманный справочник технолога-инструментальщика. Марки инструментальных сталей
Инструментальные стали
Стали для режущего инструмента
Инструментальная сталь должна обладать высокой твердостью, износостойкостью, достаточной прочностью и вязкостью (для инструментов ударного действия).
Режущие кромки могут нагреваться до температуры 500…900oС, поэтому важным свойством является теплостойкость, т. е., cпособность сохранять высокую твердость и режущую способность при продолжительном нагреве (красностойкость).
Углеродистые инструментальные стали (ГОСТ 1435).
Содержат 0,65…1,35% углерода.
Стали У7…У13А – обладают высокой твердостью, хорошо шлифуются, дешевы и недефицитны.
Из сталей марок У7, У8А изготавливают инструмент для работы по дереву и инструмент ударного действия, когда требуется повышенная вязкость – пуансоны, зубила, штампы, молотки.
Стали марок У9…У12 обладают более высокой твердостью и износостойкостью – используются для изготовления сверл, метчиков, фрез.
Сталь У13 обладает максимальной твердостью, используется для изготовления напильников, граверного инструмента.
Для снижения твердости и создания благоприятной структуры, все инструментальные стали до изготовления инструмента подвергают отжигу.
Для заэвтектоидных сталей проводят сфероидизирующий отжиг, в результате которого цементит вторичный приобретает зернистую форму. Регулируя скорость охлаждения можно получить любой размер зерен.
Окончательная термическая обработка – закалка с последующим отпуском.
Закалку для доэвтектоидных сталей проводят полную, а для заэвтектоидных – неполную. Структура закаленных сталей или мартенсит, или мартенсит и карбиды.
Температура отпуска выбирается в зависимости от твердости, необходимой для инструмента.
Для инструментов ударного действия, требующих повышенной вязкости, из сталей У7, У8 отпуск проводят при температуре 280…300oС, что обеспечивает твердость HRC 56…58.
Для напильников, метчиков, плашек отпуск проводят при температуре 150…200oС, при этом обеспечивается получение максимальной твердости — НRC 62…64.
Основными недостатками углеродистых инструментальных сталей является их невысокая прокаливаемость (5…10 мм), низкая теплостойкость (до 200oС), то есть инструменты могут работать только при невысоких скоростях резания.
Легированные инструментальные стали
Содержат 0,9…1,4 % углерода. В качестве легирующих элементов содержат хром, вольфрам, ванадий, марганец, кремний и другие. Общее содержание легирующих элементов до 5%.
Высокая твердость и износостойкость в основном определяются высоким содержанием углерода. Легирование используется для повышения закаливаемости и прокаливаемости, сохранения мелкого зерна, повыщения прочности и вязкости.
Термическая обработка включает закалку и отпуск.
Проводят закалку с температуры 800…850oС в масло или ступенчатую закалку, что уменьшает возможность коробления и образования закалочных трещин.
Отпуск проводят низкотемпературный, при температуре 150…200oС, что обеспечивает твердость HRC 61…66. Иногда, для увеличения вязкости, температуру отпуска увеличивают до 300oС, но при этом наблюдается снижение твердости HRC 55…60.
Для деревообрабатывающего инструмента из сталей 6ХС и 9ХФ рекомендуется изотермическая закалка, значительно улучшающая вязкость.
Повышенное содержание кремния (сталь 9ХС) способствует увеличению прокаливаемости до 40 мм и повышению устойчивости мартенсита при отпуске. Недостатками сталей, содержащих кремний, являются чувствительность их к обезуглероживанию при термообработке, плохая обрабатываемость резанием и деформированием из-за упрочнения феррита кремнием.
Повышенное содержание марганца (стали ХВГ, 9ХВСГ) способствует увеличению количества остаточного аустенита, что уменьшает деформацию инструмента при закалке. Это особенно важно для инструмента, имеющего большую длину при малом диаметре, например, протяжек.
Хром увеличивает прокаливаемость и твердость после закалки.
Стали используются для изготовления инструмента и ударного, и режущего.
Быстрорежущие стали
Стали получили свое название за свойства. В следствии высокой теплостойкости (550…650oС), изготовленные из них инструменты могут работать с достаточно высокими скоростями резания.
Стали содержат 0,7…1,5 % углерода, до 18 % основного легирующего элемента – вольфрама, до 5 % хрома и молибдена, до 10 % кобальта
Добавление ванадия повышает износостойкость инструмента, но ухудшает щлифуемость. Кобальт повышает теплостойкость до 650oС и вторичную твердость HRC 67…70.
Микроструктура быстрорежущей стали в литом состоянии имеет эвтектическую структурную составляющую. Для получения оптимальных свойств инструментов из быстрорежущей стали необходимо по возможности устранить структурную неоднородность стали – карбидную ликвацию. Для этого слитки из быстрорежущей стали подвергаются интенсивной пластической деформации (ковке). При этом происходит дробление карбидов эвтектики и достигается более однородное распределение карбидов по сечению заготовки.
Затем проводят отхиг стали при температуре 860…900oС. Структура отожженной быстрорежущей стали – мелкозернистый (сорбитообразный) перлит и карбиды, мелкие эвтектоидные и более крупные первичные. Количество карбидов около 25 %. Сталь с такой структурой хорошо обрабатывается резанием. Подавляющее количество легирующих элементов находятся в карбидной фазе. Для получения оптимальных свойств стали в готовом инструменте необходимо при термической обработке обеспечить максимальное насыщение мартенсита легирующими элементами. При закалке быстрорежущие стали требуют нагрева до очень высоких температур, около 1280oС. Нагрев осуществляют в хорошо раскисленных соляных ваннахBaCl2/, что улучшает равномерность прогрева и снижает возможность обезуглероживания поверхности. Для снижения термических фазовых напряжений нагрев осуществляют ступенчато: замедляют нагрев при температурах 600…650oС и при 850…900oС. График режима термической обработки быстрорежущей стали представлен на рис. 19.1.
Рис.19.1. График режима термической обработки быстрорежущей стали
Охлаждение от закалочной температуры производится в масле. Структура стали после закалки состоит из легированного, очень тонкодисперсного мартенсита, значительного количества (30…40 %) остаточного аустенита и карбидов вольфрама. Твердость составляет 60…62 HRC. Наличие аустенита остаточного в структуре закаленной стали ухудшает режущие свойства.
Для максимального удаления аустенита остаточного проводят трехкратный отпуск при температуре 560oС. При нагреве под отпуск выше 400oС наблюдается увеличение твердости. Это объясняется тем, что из легированного остаточного аустенита выделяются легированные карбиды. Аустенит при охлаждении от температуры отпуска превращается в мартенсит отпуска, что вызывает прирост твердости. Увеличению твердости содействуют и выделившиеся при температуре отпуска мелкодисперсные карбиды легирующих элементов. Максимальная твердость достигается при температуре отпуска 560oС.
После однократного отпуска количество аустенита остаточного снижается до 10%. Чтобы уменьшить его количество до минимума, необходим трехкратный отпуск.
Твердость стали после отпуска составляет 64…65 HRC. Структура стали после термообработки состоит из мартенсита отпуска и карбидов.
При термической обработке быстрорежущих сталей применяют обработку холодом. После закалки сталь охлаждают до температуры — 80 … — 100oС, после этого проводят однократный отпуск при температуре 560oС для снятия напряжений.
Иногда для повышения износостойкости быстрорежущих сталей применяют низкотемпературное цианирование.
Основными видами рехущих инструментов из быстрорежущей стали являются резцы, сверла, долбяки, протяжки, метчики машинные, ножи для резки бумаги. Часто из быстрорежущей стали изготавливают только рабочую часть инструмента.
Стали для измерительных инструментов
Основными требованиями, предъявляемыми к сталям, из которых изготавливаются измерительные инструменты, являются высокая твердость и износоустойчивость, стабильность в размерах в течение длительного времени. Последнее требование обеспечивается минимальным температурным коэффициентом линейного расширения и сведением к минимуму структурных превращений во времени.
Для изготовления измерительных инструментов применяются:
высокоуглеродистые инструментальные стали, легированные и углеродистые (стали У12, Х, Х9, ХГ), после закалки и стабилизирующего низкотемпературного (120…170 oС ) отпуска в течение 10…30 ч. До отпуска желательно провести обработку холодом. Получают твердость 62…67 HRC;
малоуглеродистые стали (сталь 15, 20) после цементации изакалки с низким отпуском;
нитралои (сталь 38ХМЮА) после азотирования на высокую твердость
Штамповые стали
Инструмент, применяемый для обработки металлов давлением (штампы, пуансоны, матрицы) изготавливают из штамповых сталей.
Различают стали для штампов холодного и горячего деформирования.
Стали для штампов холодного деформирования.
Стали должны обладать высокой твердостью, износостойкостью, прочностью, вязкостью (чтобы воспринимать ударные нагрузки), сопротивлением пластическим деформациям.
Для штампов небольших размеров (до 25 мм) используют углеродистые инструментальные стали У10, У11, У12 после закалки и низкого отпуска на твердость 57…59 HRC. Это позволяет получить хорошую износостойкость и ударную вязкость.
Для более крупных изделий применяют легированные стали Х, Х9, Х6ВФ. Для повышения износостойкости инструмента после термической обработки проводят цианирование или хромирование рабочих поверхностей.
Для уменьшения брака при закалке необходимо медленное охлаждение в области температур мартенситного превращения (например, закалка из воды в масло для углеродистых сталей, ступенчатая закалка для легированных сталей).
Если штамповый инструмент испытывает ударные нагрузки, то используют стали, обладающие большей вязкостью (стали 4ХС4, 5ХНМ). Это достигается снижением содержания углерода, введением легирующих элементов и соответствующей термической обработкой. После закалки проводят высокий отпуск при температуре 480…580oС, что обеспечивает твердость 38…45 HRC.
Стали для штампов горячего деформирования
Дополнительно к общим требованиям, от сталей этой группы требуется устойчивость против образования трещин при многократном нагреве и охлаждении, окалиностойкость, высокая теплопроводность для отвода теплоты от рабочих поверхностей штампа, высокая прокаливаемость для обеспечения высокой прочности по всему сечению инструмента.
Для изготовления молотовых штампов применяют хромоникелевые среднеуглеродистые стали 5ХНМ, 5ХНВ, 4ХСМФ. Вольфрам и молибден добавляют для снижения склонности к отпускной хрупкости. После термической обработки, включающей закалку с температуры 760…820oС и отпуск при 460…540oС, сталь имеет структуру – сорбит или троостит и сорбит отпуска. Твердость 40…45 HRC.
Штампы горячего прессования работают в более тяжелых условиях. Для их изготовления применяются стали повышенной теплостойкости. Сталь 3Х2В8Ф сохраняет теплостойкость до 650oС, но наличие карбидов вольфрама снижает вязкость. Сталь 4Х5В2ФС имеет высокую вязкость. Повышенное содержание хрома и кремния значительно увеличивает окалиностойкость стали.
В качестве материалов для инструментов используются твердые сплавы, которые состоят из твердых карбидов и связующей фазы. Они изготавливаются методами порошковой металлургии.
Характерной особенностью твердых сплавов является очень высокая твердость 87…92 HRC при достаточно высокой прочности. Твердость и прочность зависят от количества связующей фазы (кобальта) и величины зерен карбидов. Чем крупнее зерна карбидов, тем выше прочность. Твердые сплавы отличаются большой износостойкостью и теплостойкостью. Основными твердыми сплавами являются группы ВК (WC + Co), TK (WC + TiC + Co), TTK (WC + TiC + TaC + Co). Наиболее распространенными сплавами группы ВК являются сплавы марок ВК3, ВК6, ВК8, ВК20, где число показывает содержание кобальта в процентах, остальное – карбиды вольфрама WC. Сплавы группы ТК марок Т30К6, Т14К8 – первое число показывает содержание карбидов титана в процентах, второе – содержание кобальта в процентах. Сплаы этой группы лучше противостоят изнашиванию, обладают большей твердостью, тепло- и жаростойкостью, стойкостью к коррозии, но меньшей теплопроводностью и большей хрупкостью. Используются на средних и высоких скоростях резания.
Сплавы с малым количеством кобальта обладают повышенной твердостью и износостойкостью, но минимальной прочностью, Поэтому их используют для чистового точения (ВК3, Т30К4).
Сплавы с повышенным содержанием кобальтаиспользуют для чернового точения (ВК8, Т14К8).
Сплав ВК20 начинают использовать для армирования штампов, что повышает их износостойкость.
Износостойкость инструментов из твердых сплавов превышает износостойкость инструментов из быстрорежущих стале в 10…20 раз и сохраняется до температур 800…1000oС.
Алмаз как материал для изготовления инструментов
80 % добываемых природных алмазов и все синтетические алмазы используются в качестве инструментальных материалов.
Основное количество алмазов используется в виде алмазного порошка для изготовления алмазно-абразивного инструмента – шлифовальных кругов, притиров, хонов, надфилей и др., для обработки особо твердых металлов и горных пород. Большое значение имеют заточные круги для твердосплавного инструмента, это увеличивает производительность труда и срок службы инструмента. Повышение стойкости твердосплавного инструмента обеспечивается высокой чистотой (отсутствие зазубрин, мелких трещин) лезвия инструмента.
Алмазный инструмент изготовляется в виде алмазосодержащих кругов с бакелитовой или металлической связкой.
Также изготавливают алмазные резцы (для обработки корпусов часов), фильеры (для волочения проволоки из высокотвердых и драгоценных металлов) и др.
Коррозия электрохимическая и химическая.
Разрушение металла под воздействием окружающей среды называют коррозией.
Коррозия помимо уничтожения металла отрицательно влияет на эксплуатационные характеристики деталей, содействуя всем видам разрушения.
Коррозия в зависимости от характера окружающей среды может быть химической и электрохимической.
Электрохимическаякоррозия имеет место в водных растворах, а так же в обыкновенной атмосфере, где имеется влага.
Сущность этой коррозии в том, что ионы металла на поверхности детали, имея малую связь с глубинными ионами, легко отрываются от металла молекулами воды.
Металл, потеряв часть положительно заряженных частиц, ионов, заряжается отрицательно за счет избыточного количества оставшихся электронов. Одновременно слой воды, прилегающий к металлу, за счет ионов металла приобретает положительный заряд. Разность зарядов на границе металл – вода обуславливает скачок потенциала, который в процессе коррозии изменяется, увеличиваясь от растворения металла, и уменьшаясь от осаждения ионов из раствора на металле.
Если количество ионов переходящих в раствор и осаждающихся на металле одинаково, то скорости растворения и осаждения металла равны и процесс коррозии (разрушения металла) не происходит. Этому соответствует равновесный потенциал .
За нулевой потенциал принимают равновесный потенциал водородного иона в водном растворе при концентрации положительных ионов водорода, равной 1 моль ионов +на 1 литр.
Стандартные потенциалы других элементов измерены по отношению к водородному потенциалу.
Металлы, стандартный потенциал которых отрицательный – корродируют в воде, в которой растворен кислород тем активнее, чем отрицательней значение электрохимического потенциала.
Уходящие ионы металла, взаимодействуя с ионами , образуют гидроксиды, нерастворимые в воде, которые называютржавчиной,а процесс их образования –ржавлением.
Схема ржавления железа:
;
Гидроксид железа в присутствии кислорода, растворенного в воде, превращается в. Так как это нерастворимое соединение, то равновесный потенциал не может быть достигнут и коррозия будет продолжаться до полного разрушения.
В зависимости от структуры коррозия имеет разное проявление: при однородном металле – коррозия происходит равномерно по всей поверхности. При неоднородном металле – коррозия избирательная и называется точечной. Это явление наиболее опасно, так как приводит к быстрой порче всего изделия. Избирательная коррозия создает очаги концентрации напряжений, что содействует разрушению.
Химическая коррозияможет происходить за счет взаимодействия металла с газовой средой при отсутствии влаги. Продуктом коррозии являются оксиды металла. Образуется пленка на поверхности металла толщиной в 1…2 периода кристаллической решетки. Этот слой изолирует металл от кислорода и препятствует дальнейшему окислению, защищает от электрохимической коррозии в воде. При создании коррозионно-стойких сплавов – сплав должен иметь повышенное значение электрохимического потенциала и быть по возможности однофазным.
Классификация коррозионно-стойких сталей и сплавов
Коррозионная стойкость может быть повышена, если содержание углерода свести до минимума, если ввести легирующий элемент, образующий с железом твердые растворы в таком количестве, при котором скачкообразно повысится электродный потенциал сплава.
Важнейшими коррозионно-стойкими техническими сплавами являются нержавеющие стали с повышенным содержанием хрома: хромистые и хромоникелевые. На рис. 20.1 показано влияние количества хрома в железохромистых сплавах на электрохимический потенциал сплава.
Рис 20.1. Влияние хрома на потенциал сплавов
Хромистые стали.
Содержание хрома должно быть не менее 13% (13…18%).
Коррозионная стойкость объясняется образованием на поверхности защитной пленки оксида .
Углерод в нержавеющих сталях является нежелательным, так как он обедняет раствор хромом, связывая его в карбиды, и способствует получению двухфазного состояния. Чем ниже содержание углерода, тем выше коррозионная стойкость нержавеющих сталей.
Различают стали ферритного класса08Х13, 12Х17, 08Х25Т, 15Х28. Стали с повышенным содержанием хрома не имеют фазовых превращений в твердом состоянии и поэтому не могут быть подвергнуты закалке. Значительным недостатком ферритных хромистых сталей является повышенная хрупкость из-за крупнокристаллической структуры. Эти стали склонны к межкристаллитной коррозии (по границам зерен) из-за обеднения хромом границ зерен. Для избежания этого вводят небольшое количество титана. Межкристаллитная коррозия обусловлена тем, что часть хрома около границ зерна взаимодействует с углеродом и образует карбиды. Концентрация хрома в твердом растворе у границ становится меньше 13% и сталь приобретает отрицательный потенциал.
Из-за склонности к росту зерна ферритные стали требуют строгих режимов сварки и интенсивного охлаждения зоны сварного шва. Недостатком является и склонность к охрупчиванию при нагреве в интервале температур 450…500oС
Из ферритных сталей изготавливают оборудование азотно-кислотных заводов (емкости, трубы).
Для повышения механических свойств ферритных хромистых сталей в них добавляют 2…3 % никеля. Стали 10Х13Н3, 12Х17Н2 используются для изготовления тяжелонагруженных деталей, работающих в агрессивных средах.
После закалки от температуры 1000oC и отпуска при 700…750oС предел текучести сталей составляет 1000 МПа.
Термическую обработку для ферритных сталей проводят для получения структуры более однородного твердого раствора, что увеличивает коррозионную стойкость.
Стали мартенситного класса20Х13, 30Х13, 40Х13. После закалки и отпуска при 180…250oС стали 30Х13, 40Х13 имеют твердость 50…60 HRC и используются для изготовления режущего инструмента (хирургического), пружин для работы при температуре 400…450o, предметов домашнего обихода.
Стали аустенитного класса– высоколегированные хромоникелевые стали.
Никель – аустенитообразующий элемент, сильно понижающий критические точки превращения. После охлаждения на воздухе до комнатной температуры имеет структуру аустенита.
Нержавеющие стали аустенитного класса 04Х18Н10, 12Х18Н9Т имеют более высокую коррозионную стойкость, лучшие технологические свойства по сравнению с хромистыми нержавеющими сталями, лучше свариваются. Они сохраняют прочность до более высоких температур, менее склонны к росту зерна при нагреве и не теряют пластичности при низких температурах.
Хромоникелевые стали коррозионностойки в окислительных средах. Основным элементом является хром, никель только повышает коррозионную стойкость.
Для большей гомогенности хромоникелевые стали подвергают закалке с температуры 1050…1100oCв воде. При нагреве происходит растворение карбидов хрома в аустените. Выделение их из аустенита при закалке исключено, так как скорость охлаждения велика. Получают предел прочности= 500…600 МПа, и высокие характеристики пластичности, относительное удлинение= 35…45%.
Упрочняют аустенитные стали холодной пластической деформацией, что вызывает эффект наклепа. Предел текучести при этом может достигнуть значений 1000…1200 МПа, а предел прочности – 1200…1400 МПа.
Для уменьшения дефицитного никеля часть его заменяют марганцем (сталь 40Х14Г14Н3Т) или азотом (сталь 10Х20Н4АГ11).
Аустенитно-ферритные стали12Х21Н5Т, 08Х22Н6Т являются заменителями хромоникелевых сталей с целью экономии никеля.
Свойства сталей зависят от соотношения ферритной и аустенитной фаз (оптимальные свойства получают при соотношении – Ф:А=1:1 ). Термическая обработка сталей включает закалку от температуры 1100…1150oC и отпуск-старение при температуре 500…750oC.
Аустенитно-ферритные стали не подвержены коррозионному растрескиванию под напряжением: трещины могут возникать только на аустенитных участках, но ферритные участки задерживают их развитие. При комнатных температурах аустенитно-ферритные стали имеют твердость и прочность выше, а пластичность и ударную вязкость ниже, чем стали аустенитного класса.
Кроме нержавеющих сталей в промышленности применяют коррозионно-стойкие сплавы – это сплавына никелевой основе.Сплавы типахастеллойсодержат до 80 % никеля, другим элементом является молибден в количестве до 15…30 %. Сплавы являются коррозионно-стойкими в особо агрессивных средах (кипящая фосфорная или соляная кислота), обладают высокими механическими свойствами. После термической обработки – закалки и старения при температуре 800oС – сплавы имеют предел прочностиМПа, и твердость. Недостатком является склонность к межкристаллической коррозии, поэтому содержание углерода в этих сплавах должно быть минимальным.
Жаростойкость, жаростойкие стали и сплавы.
Жаростойкость (окалиностойкость)– это способность металлов и сплавов сопротивляться газовой коррозии при высоких температурах в течение длительного времени.
Если изделие работает в окислительной газовой среде при температуре 500..550oC без больших нагрузок, то достаточно, чтобы они были только жаростойкими (например, детали нагревательных печей).
Сплавы на основе железа при температурах выше 570oC интенсивно окисляются, так как образующаяся в этих условиях на поверхности металла оксид железа(вюстит) с простой решеткой, имеющей дефицит атомов кислорода (твердый раствор вычитания), не препятствует диффузии кислорода и металла. Происходит интенсивное образование хрупкой окалины.
Рис. 20.2. Влияние хрома на жаростойкость хромистой стали
Для повышения жаростойкости в состав стали вводят элементы, которые образуют с кислородом оксиды с плотным строением кристаллической решетки (хром, кремний, алюминий).
Степень легированости стали, для предотвращения окисления, зависит от температуры. Влияние хрома на жаростойкость хромистой стали показано на рис.20.2.
Чем выше содержание хрома, тем более окалиностойки стали (например, сталь 15Х25Т является окалиностойкой до температуры 1100…1150oC).
Высокой жаростойкостью обладают сильхромы, сплавы на основе никеля – нихромы, стали 08Х17Т, 36Х18Н25С2, 15Х6СЮ.
Жаропрочность, жаропрочные стали и сплавы
Жаропрочность– это способность металла сопротивляться пластической деформации и разрушению при высоких температурах.
Жаропрочные материалы используются для изготовления деталей, работающих при высоких температурах, когда имеет место явление ползучести.
Критериями оценки жаропрочности являются кратковременная и длительная прочности, ползучесть.
Кратковременная прочностьопределяется с помощью испытаний на растяжение разрывных образцов. Образцы помещают в печь и испытывают при заданной температуре. Обозначают кратковременную прочность=, например300oС= 300МПа.
Прочность зависит от продолжительности испытаний.
Пределом длительной прочностиназывается максимальное напряжение, которое вызывает разрушение образца при заданной температуре за определенное время.
Например = 200 МПа, верхний индекс означает температуру испытаний, а нижний – заданную продолжительность испытания в часах. Для котельных установок требуется невысокое значение прочности, но в течение нескольких лет.
Ползучесть – свойство металла медленно пластически деформироваться под действием постоянной нагрузки при постоянной температуре.
При испытаниях образцы помещают в печь с заданной температурой и прикладывают постоянную нагрузку. Измеряют деформацию индикаторами.
При обычной температуре и напряжениях выше предела упругости ползучесть не наблюдается, а при температуре выше 0,6Тпл, когда протекают процессы разупрочнения, и при напряжениях выше предела упругостинаблюдается ползучесть.
В зависимости от температуры скорость деформации при постоянной нагрузке выражается кривой состоящей из трех участков (рис. 20.3):
Рис. 20.3. Кривая ползучести
ОА – упругая деформация образца в момент приложения нагрузки;
АВ – участок, соответствующий начальной скорости ползучести;
ВС – участок установившейся скорости ползучести, когда удлинение имеет постоянную скорость.
Если напряжения достаточно велики, то протекает третья стадия (участок СД), связанная с началом разрушения образца (образование шейки).
Для углеродистых сталей ползучесть наблюдается при нагреве выше 400oС.
Предел ползучести– напряжение, которое за определенное время при заданной температуре вызывает заданное суммарное удлинение или заданную скорость деформации.
НапримерМПа, где верхний индекс – температура испытания вoС, первый нижний индекс – заданное суммарное удлинение в процентах, второй – заданная продолжительность испытания в часах.
Классификация жаропрочных сталей и сплавов
В качестве современных жаропрочных материалов можно отметить перлитные,мартенситные и аустенитныежаропрочные стали,никелевые и кобальтоавыежаропрочные сплавы,тугоплавкиеметаллы.
При температурах до 300oC обычные конструкционные стали имеют высокую прочность, нет необходимости использовать высоколегированные стали.
Для работы в интервале температур 350…500oC применяют легированные стали перлитного, ферритного и мартенситного классов.
Перлитные жаропрочные стали. К этой группе относятся котельные стали и сильхромы. Эти стали применяются для изготовления деталей котельных агрегатов, паровых турбин, двигателей внутреннего сгорания. Стали содержат относительно мало углерода. Легирование сталей хромом, молибденом и ванадием производится для повышения температуры рекристаллизации (марки 12Х1МФ, 20Х3МФ). Используются в закаленном и высокоотпущенном состоянии. Иногда закалку заменяют нормализацией. В результате этого образуются пластинчатые продукты превращения аустенита, которые обеспечивают более высокую жаропрочность. Предел ползучести этих сталей должен обеспечить остаточную деформацию в пределах 1 % за время 10000…100000 ч работы.
Перлитные стали обладают удовлетворительной свариваемостью, поэтому используются для сварных конструкций (например, трубы пароперегревателей).
Для деталей газовых турбин применяют сложнолегированные стали мартенситногокласса12Х2МФСР, 12Х2МФБ, 15Х12ВНМФ. Увеличение содержания хрома повышает жаростойкость сталей. Хром, вольфрам, молибден и ванадий повышают температуру рекристаллизации, образуются карбиды, повышающие прочность после термической обработки. Термическая обработка состоит из закалки от температур выше 1000oС в масле или на воздухе и высокого отпуска при температурах выше температуры эксплуатации.
Для изготовления жаропрочных деталей, не требующих сварки (клапаны двигателей внутреннего сгорания), применяются хромокремнистые стали – сильхромы:40Х10С2М, 40Х9С2, Х6С.
Жаролрочные свойства растут с увеличением степени легированности. Сильхромы подвергаются закалке от температуры около 1000oС и отпуску при температуре 720…780oС.
При рабочих температурах 500…700oC применяются сталиаустенитного класса. Из этих сталей изготавливают клапаны двигателей, лопатки газовых турбин,сопловые аппараты реактивных двигателей и т.д.
Основными жаропрочными аустенитными сталями являются хромоникелевые стали, дополнительно легированные вольфрамом, молибденом, ванадием и другими элементами. Стали содержат 15…20 % хрома и 10…20 % никеля. Обладают жаропрочностью и жаростойкостью, пластичны, хорошо свариваются, но затруднена обработка резанием и давлением, охрупчиваются в интервале температур около 600oС, из-за выделения по границам различных фаз.
По структуре стали подразделяются на две группы:
1. Аустенитные стали с гомогенной структурой17Х18Н9, 09Х14Н19В2БР1,12Х18Н12Т. Содержание углерода в этих сталях минимальное. Для создания большей однородности аустенита стали подвергаются закалке с 1050…1100oС в воде, затем для стабилизации структуры – отпуску при 750oС.
2. Аустенитные стали с гетерогенной структурой 37Х12Н8Г8МФБ, 10Х11Н20Т3Р.
Термическая обработка сталей включает закалку с 1050…1100oС. После закалки старение при температуре выше эксплуатационной (600…750oС). В процессе выдержки при этих температурах в дисперсном виде выделяются карбиды, карбонитриды, вследствие чего прочность стали повышается.
Детали, работающие при температурах 700…900oC, изготавливают из сплавов на основеникеля и кобальта(например, турбины реактивных двигателей).
Никелевые сплавы преимущественно применяют в деформированном виде. Они содержат более 55 % никеля и минимальное количество углерода (0,06…0,12 %). По жаропрочным свойствам превосходят лучшие жаропрочные стали.
По структуре никелевые сплавы разделяют на гомогенные (нихромы)игетерогенные(нимоники).
Нихромы.Основой этих сплавов является никель, а основным легирующим элементом – хром (ХН60Ю, ХН78Т).
Нихромы не обладают высокой жаропрочностью, но они очень жаростойки. Их применяют для малонагруженных деталей, работающих в окислительных средах, в том числе и для нагревательных элементов.
Нимоники являются четвертными сплавами никель – хром (около 20 %) – титан (около 2%) – алюминий (около 1 %) (ХН77ТЮ, ХН70МВТЮБ, ХН55ВМТФКЮ). Используются только в термически обработанном состоянии. Термическая обработка состоит из закалки с 1050…1150oС на воздухе и отпуска – старения при 600…800oС.
Увеличение жаропрочности сложнолегированных никелевых сплавов достигается упрочнением твердого раствора введением кобальта, молибдена, вольфрама.
Основными материалами, которые могут работать при температурах выше 900oC (до 2500oС), являютсясплавы на основе тугоплавких металлов– вольфрама, молибдена, ниобия и других.
Температуры плавления основных тугоплавких металлов: вольфрам – 3400oС, тантал – 3000oС, молибден – 2640oС, ниобий – 2415oС, хром – 1900oС.
Высокая жаропрочность таких металлов обусловлена большими силами межатомных связей в кристаллической решетке и высокими температурами рекристаллизации.
Наиболее часто применяют сплавы на основе молибдена. В качестве легирующих добавок в сплавы вводят титан, цирконий, ниобий. С целью защиты от окисления проводят силицирование, на поверхности сплавов образуется слой MoSi2толщиной 0,03…0,04 мм. При температуре 1700oС силицированные детали могут работать 30 часов.
Вольфрам – наиболее тугоплавкий металл. Его используют в качестве легирующего элемента в сталях и сплавах различного назначения, в электротехнике и электронике (нити накала, нагреватели в вакуумных приборах).
В качестве легирующих элементов к вольфраму добавляют молибден, рений, тантал. Сплавы вольфрама с рением сохраняют пластичность до –196oС и имеют предел прочности 150 МПа при температуре 1800oС.
Для сплавов на основе вольфрама характерна низкая жаростойкость, пленки образующихся оксидов превышают объем металла более, чем в три раза, поэтому они растрескиваются и отслаиваются Изготавливают изделия, работающие в вакууме).
studfiles.net
Инструментальные стали
Инструментальные стали
Основными материалами для режущих инструментов являются инструментальные стали. К ним относятся углеродистые, легированные и быстрорежущие стали.
Углеродистые стали. Эти стали обладают высокой твердостью после окончательной термической обработки (закалки) HRC 62—64 и имеют низкую твердость в отожженном состоянии (НВ 187—207), что обеспечивает хорошую обрабатываемость резанием и давлением. Недостаток углеродистых сталей — низкая теплостойкость (200—250° С).
Углеродистые инструментальные стали применяют для режущих инструментов, работающих при небольших скоростях резания (υ = 10÷12 м/мин).
В табл. 1 дано назначение некоторых марок инструментальной углеродистой стали (ГОСТ 1435—54) при изготовлении режущих инструментов.
Легированные стали. В зависимости от назначения и свойств инструментальные легированные стали (ГОСТ 5950—63) подразделяют на две группы: стали для режущего и измерительного инструмента и стали для штампового инструмента. Для режущего инструмента наибольшее применение нашли марки 7ХФ, ИХ, 13Х, ХВ5. В1, Ф, 9ХС, ХВГ, 9Х5ВФ, ХВСГ др.
В обозначениях марок сталей первые цифры указывают среднее содержание углерода в десятых долях процента. Они могут не указываться, если содержание углерода близко к единице или больше единицы. Буквы за цифрами обозначают: Г — марганец, С — кремний; X — хром, В — вольфрам, Ф •— ванадий, Н — никель, М — молибден. Цифры, стоящие после букв, указывают среднее содержание соответствующего элемента в целых единицах. Отсутствие цифры обозначает, что содержание этого легирующего элемента равно примерно 1%. В отдельных случаях содержание легирующих элементов не указывается, если оно не превышает 1,8%.
Легированные стали обладают по сравнению с углеродистыми повышенной вязкостью в закаленном состоянии, более глубокой прокаливаемостью, меньшей склонностью к деформациям и трещинам при закалке. Режущие свойства легированных сталей примерно такие же, как у углеродистых инструментальных сталей, потому что они тоже имеют низкую теплостойкость (200—250° С).
Назначение легированных сталей, применяемых для изготовления режущих инструментов, дано в табл. 2.
Быстрорежущие стали. Инструментальные быстрорежущие стали (ГОСТ 9373—60) приобретают после термообработки высокую твердость, прочность и износостойкость, сохраняя режущие свойства при нагревании во время работы до 600—650° С. Это позволяет увеличить скорость резания инструментами из быстрорежущей стали в 2—4 раза и повышает их стойкость по сравнению с инструментами из углеродистой или легированной стали. Преимущества быстрорежущей стали проявляются главным образом при обработке прочных (σв = 100 кГ/мм2) и твердых сталей (НВ 200—250) и резании с повышенной скоростью.
Основные марки и химический состав быстрорежущих сталей приведены в табл. 3.
Таблица 1
Назначение углеродистых сталей при изготовлении режущих инструментов
Марки быстрорежущей стали обозначают буквами и цифрами: Р означает, что сталь относится к группе быстрорежущих, а цифра после буквы Р показывает среднее содержание вольфрама (в %) в стали. Среднее содержание ванадия (в %) отмечают цифрой, следующей за буквой Ф1 кобальта — цифрой после буквы К.
Таблица 2
Назначение легированных сталей, применяемых для режущих инструментов
Таблица 3
Марки и химический состав быстрорежущих сталей
Быстрорежущие стали делятся на стали нормальной теплостойкости (Р18, Р12, Р6МЗ) и стали повышенной теплостойкости (Р18Ф2, Р14Ф4, Р9Ф5 и др.). Для обработки конструкционных сталей с твердостью до НВ260—280 и чугунов используют стали нормальной теплостойкости. При обработке более прочных и улучшенных конструкционных сталей необходимы стали ванадиевые Р18Ф2 и для очень тяжелых режимов резания — кобальтовые Р18К5Ф2, Р9К5 и Р9К10.
В настоящее время металлургическая промышленность выпускает новую марку высоковольфрамовой кобальтованадиевой быстрорежущей стали ЭПЗ79 (Р18Ф2К8М). Эту сталь поставляет завод «Электросталь»
По сравнению со стандартными сталями повышенной теплостойкости сталь ЭП379 содержит больше углерода, кобальта и меньше молибдена. По сравнению со сталью Р18 сталь ЭП379 обладает повышенной горячей твердостью и теплостойкостью.
Сталь ЭП379 предназначена для инструментов любой формы при обработке титановых, жаропрочных и закаленных сталей с твердостью до HRC 52—55.
Свойства быстрорежущих сталей по сравнению со сталью Р18 приведены в табл. 4. Назначение быстрорежущих сталей для изготовления режущих инструментов дано в табл. 5.
Для оснащения инструментов пластинками из быстрорежущих сталей в зависимости от их назначения ГОСТ 2379—67 предусматривает несколько форм (табл. 6).
Таблица 4
Свойства быстрорежущих сталей
Таблица 5
Примерное назначение быстрорежущих сталей
Конструкционные стали. Для экономии быстрорежущих сталей и твердых сплавов многие режущие инструменты изготовляются составными; например, режущая часть — из стали марки Р18, а хвостовик или державка — из конструкционной стали.
Для державок, хвостовиков и корпусов применяются углеродистые инструментальные стали обыкновенного качества (ГОСТ 380—60), качественные (ГОСТ 1050—60) и конструкционные легированные (ГОСТ 4543—61).
Рекомендуемые марки сталей для составного режущего инструмента приведены в табл. 7.
Таблица 6
Форма, размеры и назначение пластинок из быстрорежущей стали
Продолжение табл. 6
Продолжение табл, б
Таблица 7
Рекомендуемые марки сталей для державок, корпусов и хвостовиков составного режущего инструмента
Смотрите также
spravochnik-tehnologa.ru
Углеродистые инструментальные стали: марки, свойства, обозначение, применение
В машиностроении и других областях промышленности производственная деятельность заключается в выпуске заготовок и деталей, которые получаются путем механической обработки. Современные материалы могут обладать весьма высокими показателями твердости и прочности, за счет чего усложняется их обработка. Для того чтобы обеспечить быструю и качественную механическую обработку при изготовлении режущего инструмента или их кромки используются углеродистые инструментальные стали. Их особенность заключается в высокой стойкости к механическому воздействию.
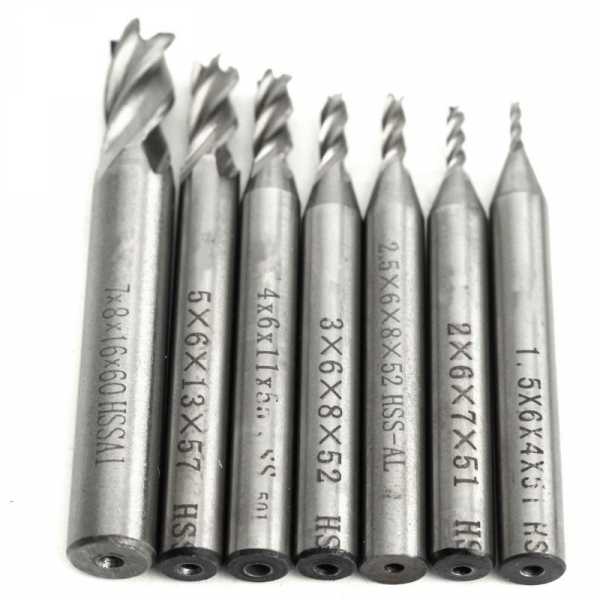
Углеродистые инструментальные стали
Подобные металлы также могут использоваться при выпуске ответственных деталей, к которым предъявляются высокие требования в плане прочности и твердости.
Основные характеристики
Рассматривая основные свойства инструментальной стали следует отметить нижеприведенные моменты:
- Низкая чувствительность к перегреву. При механической обработке снятие слоя материала с заготовки происходит за счет оказываемого требования. Нагрев металла приводит к изменению его основных качеств. Поэтому углеродистые инструментальные качественные стали не нагреваются даже при длительном трении с другими поверхностями.
- Низкая чувствительно к привариванию к обрабатываемым деталям. Из-за оказываемого давления при подаче инструмента на момент обработки заготовок зона трения может несущественно нагреваться, что становится причиной повышения пластичности некоторые материалов. Если инструментальная сталь будет привариваться при этом к поверхности возникнет дополнительное сопротивление и качество получаемой детали существенно снизиться.
- Для того чтобы упростить обработку металла его делают боле восприимчивой к обработке методом резки.
- Восприимчивость к прокаливанию также определяется особым химическим составом.
- Высокая пластичность в горячем состоянии позволяет получать заготовки метод плавления металла.
- Высокое сопротивление процессу обезуглероживания позволяет получить наилучший результат при проведении закалки или других процессом химико-термической обработки.
- Во время обработки может возникать ударная нагрузка, которая в большинстве случаев становится причиной образования трещин. Высококачественная углеродистая инструментальная сталь не имеет подобного недостатка.
- Износостойкость и высокая прочность, твердость поверхности.
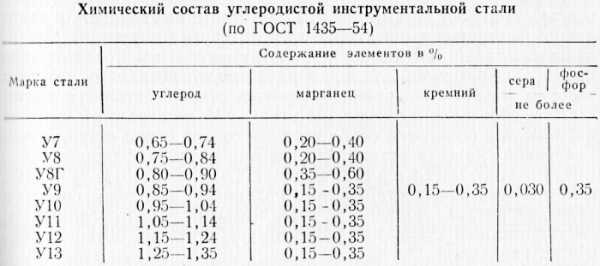
Химический состав углеродистых инструментальных сталей
Химический состав инструментальных углеродистых сталей во многом определяют основные эксплуатационные качества металла.
Применение
Применение инструментальных углеродистых сталей во многом зависит от химического состава. Чаще всего применяется для получения:
- Режущего инструмента. На протяжении многих лет для изготовления инструментов использовали обычную сталь, которая в процессе работы могла нагреваться и быстро изнашиваться. На тот момент устанавливались станки токарной и сверлильной группы, которые могли проводить обработку только при низкой скорости и невысокой подачи. Появление современного оборудования, в частности станков с ЧПУ, привело к повышению требований, предъявляемых к инструменту. Только появление инструментальной стали и твердых сплавов позволило полностью раскрыть потенциал современного оборудования. Также не стоит забывать, что для получения качественных поверхностей должна существенно увеличиваться скорость подачи, повысить производительность можно при увеличении подачи. Современные режущие инструменты могут выдерживать неоднократные циклы нагрева и охлаждения, срок эксплуатации при этом увеличивается в несколько десятков раз.
- Высококачественных деталей. Примером можно назвать конструкцию ДВС, которая имеет поверхности с точными размерами и шероховатостью. Для того чтобы при эксплуатации подвижные элементы не меняли свою форму по причине нагрева их изготавливают из инструментальной стали.
- Приборов, применяемых для проведения точных измерений. Для получения небольших деталей с точностью линейных размеров в несколько сотен миллиметров заготовка не должна нагреваться или деформироваться за счет оказываемого давления со стороны режущего инструмента.
- Литейной прессформы, которая должна выдерживать существенное давление.
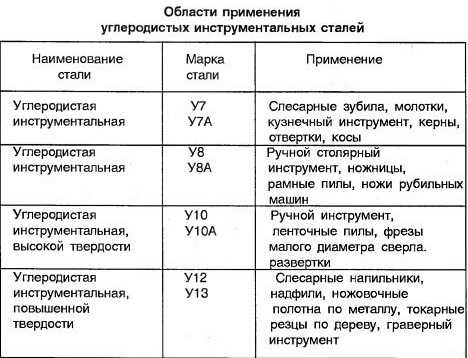
Применение углеродистых инструментальных сталей в зависимости от марки
Для изготовления деталей больше всего подходить марка У7 или У7А, для изготовления режущего и другого инструмента У10 или У12. Данная закономерность связана с тем, что для получения режущего инструмента должны использоваться более твердые металлы.
Маркировка углеродистых инструментальных сталей в данном случае указывает на процентное содержание углерода и наличие других примесей.
Свойства углеродистой инструментальной стали во многом определяются концентрацией углерода – чем больше, тем поверхность тверже, но повышается и хрупкость.
При холодном прессовании могут применяться марки У10 – У12. Проведенные тесты указывают на то, что их твердость составляет 57-59 HRC. Среди особенностей отметим:
- Достаточно высокую вязкость.
- Высокий уровень сопротивления деформациям пластического типа.
- Повышенная износостойкость.
Если габариты инструмента большие, то могут применяться сплавы, в состав которых включаются полезные примеси.
Классификация
Принято разделять инструментальные качественные стали на 5 основных групп:
- Износостойкие, теплостойкие и высокотвердые – группа, представленная быстрорежущей легированной сталью. Кроме этого в данную группу относят сплавы с ледебуритной структурой, которая характеризуется повышенной концентрацией углерода (более 3%). Применение инструментальных углеродистых сталей данной группы заключается в изготовлении инструментов, которые могут подвергаться воздействию высокой температуры из-за установки высоких скоростей резания.
- Теплостойкие и вязкие стали представлены сплавом, который имеет в своем составе молибден, хром и вольфрам. Химический состав инструментальной углеродистой стали данной группы характеризуется низким значением концентрации углерода.
- Нетеплостойкие, вязкие и высокотвердые стали имеют небольшое количество примесей и среднее значение углерода. Данной группе характерен невысокий показатель прокаливаемости.
- Средняя теплостойкость, высокая твердость, износостойкость – качества, свойственные металлам с 2-3% углерода и 5-12% хрома.
- Низкая устойчивость к теплу и высокая твердость характерны сталям с заэвтектоидной структурой. В большинстве случае они не имеют легирующих элементов или их концентрация очень мала. Высокий уровень твердости обеспечивается за счет высокой концентрации углерода.
Высококачественная инструментальная сталь может подвергаться дополнительной химико-термической обработке для изменения состава и перестроения кристаллической решетки, за счет чего и достигаются необычные эксплуатационные качества.
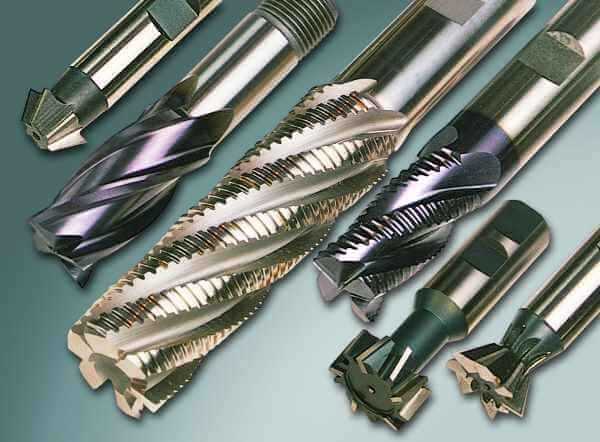
Изделия из углеродистой инструментальной стали
Твердость считается основным параметром, высокое значение которого не позволяет использовать сталь при изготовлении инструментов или деталей, подвергающихся во время эксплуатации ударам или вибрации. Эта рекомендация связана с тем, что при увеличении концентрации углерода повышается твердость, но вязкость уменьшается. Уменьшение вязкости становится причиной повышения хрупкости структуры, в результате воздействия ударной нагрузки могут появляться трещины и другие дефекты, поверхность откалываться.
Классификация по уровню твердости выглядит следующим образом:
- Высокий показатель вязкости и пониженная твердость характерны металлам, которые в составе имеют не более 0,4-0,7% углерода.
- Высокая износостойкость и твердость поверхностного слоя достигаются при насыщении структуры металла углеродом до 0,7-1,5%.
Больший показатель концентрации углерода делает металл очень хрупким, что не позволяет его использовать в качестве материала при изготовлении инструмента. Кроме этого легирующие элементы способны повысить вязкость и снизить хрупкость при условии большой концентрации углерода. В некоторых случаях проводится химическая обработка для обеспечения износостойкой поверхности и вязкого основания, за счет чего инструмент или деталь приобретает высокие эксплуатационные качества.
Маркировка
Углеродистая инструментальная сталь марки могут иметь как цифры, так и буквенные обозначения. В большинстве случаев маркировка инструментальных углеродистых сталей в самом начале имеет букву «У», которая и указывает на тип металла. Обозначение углеродистой инструментальной стали также имеет следующие особенности:
- Первое цифирное обозначение после буквы указывает в десятых долях количество углерода в отношении всего состава.
- Встречается и буква «А», идущая за цифрой, обозначающей концентрацию углерода в составе. Она указывает на то, что углеродистая инструментальная сталь марка имеет высокое качество.
- Для обозначения группы рассматриваемой стали может применяться буква «Р». В данном случае после этого обозначения идет буква, которая указывает на концентрацию вольфрама.
- Другие легирующие вещества также указываются соответствующей буквой, после которой идет цифра для обозначения концентрации.
- Принято считать, что у стали и рассматриваемой группы в обязательном порядке в составе есть хром, но его концентрация не более 4%. Если после соответствующего буквенного обозначения указывается цифра, то концентрация этого вещества уточняется.
Также можно встретить маркировку инструментальных углеродистых сталей начинающуюся с цифры. Примером приведем распространенные сплавы 9Х или 6ХГВ. Первая цифра также указывает на концентрацию в составе углерода, следующие буквы на легирующие элементы. Если после буквы легирующего элемента не указывается цифра, то принято считать, что их концентрация равна 1%. Кроме этого сама маркировка может начинаться с буквенных обозначений, свойственных легирующим элементам – это указывает на то, что концентрация.
Если вы нашли ошибку, пожалуйста, выделите фрагмент текста и нажмите Ctrl+Enter.
stankiexpert.ru
Инструментальные стали - Слесарно-инструментальные работы
Инструментальные сталиКатегория:
Слесарно-инструментальные работы
Инструментальные сталиИнструментальные стали характерны тем, что после соответствующей термической обработки они получают очень высокую-твердость. Такая твердость позволяет изготовленным из стали инструментом обрабатывать другие стали — конструкционные.
Инструментальные стали могут быть разделены на углеродистые, легированные и высоколегированные или быстрорежущие стали. Свойства углеродистых инструментальных сталей как качественных, так и высококачественных (с добавкой индекса А в обозначении марки) зависят также от процентного содержания углерода в их составе. О процентном содержании этого элемента в той или иной стали можно судить по цифрам, входящим в условное обозначение марки стали, соответственно содержанию углерода в десятых долях процента.
С ростом процентного содержания углерода увеличивается твердость стали, но одновременно растет и хрупкость. Поэтому для> ударных инструментов и вырубных штампов применяются только> стали У7 и У8, а для режущих и измерительных инструментов, от. которых требуется высокая твердость и износостойкость,—- стали У10—У12. Однако стали У10—У12’Пригодны для режущих инструментов, работающих только с небольшими скоростями резания и в спокойных условиях (развертки, метчики и т. п.). Точно также и детали приспособлений, подверженные ударам (упоры, установочные планки), изготовляются из сталей У7 — У8, а работающие на истирание,— из сталей У10 — У12.
Свойства, углеродистых сталей могут быть улучшены добавкой-марганца. Такие стали менее хрупки и более износостойки.
Несмотря на многие положительные качества, инструментальные углеродистые стали все же не лишены серьезных недостатков..
1. Они не обладают достаточной теплостойкостью, так как при нагреве приблизительно до 200° начинают терять высокую твердость, а, следовательно и режущие свойства. По этой причине их нельзя использовать для режущего инструмента, работающего в тяжелых условиях, т. е. в условиях сильного нагрева режущих кромок.
2. Их форма и размеры сильно изменяются при закалке, что не позволяет использовать такие стали для сложных по конструкции и точных по размерам инструментов и некоторых других деталей технологической оснастки.
Стремление повысить теплостойкость и износостойкость, а также прочность инструментальных материалов привело к созданию легированных сталей. Однако теплостойкость этих сталей лишь немного выше, чем ,у углеродистых, зато значительно выше их износостойкость и прокаливаемость и в то же время намного меньше изменяемость размеров при закалке.
Наиболее употребительны следующие марки инструментальных сталей: углеродистые качественные стали (по ГОСТ 1435—54) — У7, У8, У10, У12; углеродистые высококачественные — У7А, У8А, У10А, У12А, У8ГА, У10ГА; легированные (по ГОСТ 5951—51) —X, Х12, Х12Ф, 9ХС, ХГ, ХВГ, ХВ5, 5ХВС, 6ХВС, 5ХНТ, 5ХНВ; быстрорежущие (по ГОСТ 5952—51) — Р9 и Р18. Условные обозначения этих марок почти совпадают с обозначениями легированных конструкционных сталей, с той только разницей, что первое число означает не сотые доли процента, а десятые. В том случае, если процентное со- ! держание углерода в марке составляет 1 % и более, цифра в условном обозначении опускается.
Каковы же свойства и назначение марок легированных инструментальных сталей?
Хромистые инструментальные стали (X, Х12) отличаются большой износостойкостью и малой изменяемостью формы и размеров (деформацией) при закалке. Сталь марки X широко применяется для изготовления разверток, винторезных гребенок, небольших протяжек, калибров и кондукторных втулок, рабочие размеры которых нельзя подвергнуть шлифованию. Сталь марки XI2 и особенно хро—мованадиевая Х12Ф — идут на изготовление накатных плашек, волочильных инструментов, а также гибочных и холодновысадочных штампов.
Хромокремнистая сталь (9ХС) — более теплостойка по сравнению с углеродистой сталью и служит, главным образом, для изготовления режущего инструмента.
Хромомарганцевая сталь (ХГ) — дает наименьшие деформации при закалке и представляет поэтому наилучший материал для резьбовых и иных точных и сложных калибров, закаленных кондукторных планок и втулок малых диаметров, подвергаемых после закалки только доводке.
Хромовольфрамовые стали (ХВГ и ХВ5) также мало деформируются при закалке, обладают большей теплостойкостью, однако весьма склонны к появлению трещин и прижогов при шлифовании.
Хромовольфрамокремнистые (5ХВС и 6ХВС) обладают рядом ценных свойств, способствующих их применению для изготовления штампов холодной штамповки. Стали 5ХНТ и 5XITB служат для изготовления ковочных штампов.
Открытие высоколегированных быстрорежущих сталей, сохраняющих режущие свойства при температуре 550°, т. е. обладающих почти в 3 раза большей теплостойкостью, явилось крупным шагом вперед в получении совершенных материалов для изготовления режущего инструмента. Быстрорежущая сталь — очень дорогой материал. Ее стоимость в 10—15 раз выше углеродистой стали, а поэтому она используется только для изготовления режущего инструмента, работающего на повышенных режимах резания.
ГОСТ 5952—51 установлено две марки быстрорежущей стали: марка Р18, имеющая в своем составе около 18% вольфрама, и марка Р9 с 9% вольфрама. Быстрорежущая сталь Р18, как более дорогостоящая, применяется реже; во всех случаях, когда это возможно, применяют низколегированную сталь Р9. Применение стали Р18 допускается только для изготовления инструмента, работающего в особенно тяжелых условиях, т. е. при обработке материалов высокой прочности и при работе с большими сечениями стружки и скоростями резания. Эта сталь также применяется для сложного фасонного и зубообрабатывающего инструмента. Сталь Р9 при обработке материалов высокой прочности имеет несколько пониженную стойкость и кроме этого отличается худшей шлифуемостью, склонностью к прижогам при шлифовании, а также трудностью ее закалки, в связи с узким интервалом закалочных температур.
—
Требования к сталям. К инструментальным сталям предъявляются более высокие требования, чем к конструкционным. Это объясняется тем, что рабочие поверхности инструментов, изготовленных из инструментальных сталей, работают при высоких контактных напряжениях, больших удельных давлениях и подвергаются износу и нагреву. Инструментальные стали обладают высокой твердостью, прочностью, износостойкостью и рядом других свойств, необходимых для обработки материалов резанием и давлением.
Применение тех или иных материалов определяется требованиями, предъявляемыми к различным инструментам.
Материалы, из которых изготовляют режущие инструменты, должны обладать следующими свойствами: – высокой прочностью, так как в процессе резания инструменты испытывают большие усилия; – высокой твердостью, потому что процесс резания можно осуществить только в том случае, если твердость материала инструмента значительно больше твердости обрабатываемого материала; – высокой износостойкостью, потому что стойкость инструмента зависит от степени истирания режущих кромок; – высокой теплостойкостью, так как в процессе резания выделяется большое количество тепла, часть которого идет на нагрев режущих кромок инструмента, а последний, нагреваясь, теряет первоначальную твердость и быстро выходит из строя.
Стали для измерительных инструментов и деталей высокой точности должны обладать высокой износостойкостью, необходимой для сохранения инструментами размеров и формы в процессе эксплуатации, а также хорошей обрабатываемостью для получения высокого класса шероховатости поверхности измерительных инструментов.
Углеродистые стали. Эти стали обладают высокой твердостью после окончательной термической обработки (HRC 62…64) и низкой твердостью в отожженном состоянии (НВ 187…207), что обеспечивает хорошую обрабатываемость резанием и давлением. Недостаток углеродистых сталей — низкая теплостойкость (200…250°С).
По ГОСТу 1435—74 промышленность выпускает следующие инструментальные углеродистые стали: У7, У8, У8Г, У9, У10, У И, У12, У13, У7А, У8ГА, У9А, У10А, У11А, У12А и У13А.
К группе некачественных сталей относятся стали марок без буквы А, к группе высококачественных сталей, более чистых по содержанию серы и фосфора, а также примесей других элементов, — марки с буквой А.
Буквы и цифры в обозначении марок стали обозначают: У — углеродистая, следующие за ней цифры (цифра)—среднее содержание углерода в десятых долях процента, Г — повышенное содержание марганца.
Увеличение в стали содержания углерода повышает ее твердость, но одновременно увеличивает и хрупкость. Следовательно, для ударных инструментов надо применять стали с меньшим содержанием углерода (У7 и У8), а для режущих и измерительных инструментов, требующих высокой твердости и износоустойчивости,— с большим содержанием углерода (У 10 и У12).
Стали марок У7, У7А, У8, У8А, У8ГА, У9 и .У9А служат для изготовления зубил, ножниц для резки жести, пил по металлу и дереву, резцов по меди.
Из стали марок У10А, У11, У11А, У12 и У12А выполняют сверла малого диаметра, метчики, развертки, плашки, фрезы малого диаметра, пилы по металлу, ножовочные полотна, измерительные инструменты, зубила для насечки напильников.
Стали марок У13 и У13А служат для изготовления инструментов особо высокой точности: напильников, резцов, зубил для насечки напильников, шаберов и т. п. Из стали марок У8А и У10А выполняют пуансоны, матрицы, ножи и другие детали штампов.
Углеродистые стали поставляются в виде горячекатаных, кованых или калиброванных прутков различного сечения или в виде полос.
Легированные стали. В соответствии с ГОСТом 5950—73 инструментальные легированные стали по своему назначению подразделяются на две группы: для режущего и измерительного инструмента и для штам-пового инструмента.
Стали первой группы делятся на стали неглубокой прокаливаемое™ — 7ХФ, 8ХФ, 9ХФ, 11ХФ, 13Х, ХВ4 и В2Ф и стали глубокой нрокаливаемости — 9X1, X,. 12X1, 9ХС, ХГС, 9ХВГ, ХВГ, ХВСГ, 9Х5ВФ, 8Х6НФТ и 8Х4ВЗМЗФ2.
В обозначениях марок сталей первые цифры указывают среднее содержание углерода в десятых долях процента. Цифры могут и не указываться, если содержание углерода близко к единице или больше единицы. Буквы за цифрами обозначают: Г — марганец, С — кремний, X — хром, В — вольфрам, Ф — ванадий, Н — никель, М — молибден. Цифры, стоящие после букв, указывают среднее содержание соответствующего элемента в целых процентах. Отсутствие цифр означает, что содержание этого легирующего элемента составляет примерно 1%. В отдельных случаях содержание легирующих элементов не указывается, если оно не превышает 1,8%.
Легированные стали обладают по сравнению с углеродистыми повышенной вязкостью в закаленном состоянии, меньшей склонностью к деформациям и трещинам при закалке. Их режущие свойства примерно такие же, как и углеродистых инструментальных, потому что они имеют низкую теплостойкость (200…250 °С).
Легированные инструментальные стали применяются для изготовления инструментов и технологической оснастки. Из сталей марок 7ХФ, 8ХФ и 9ХФ выполняют круглые и ленточные пилы, ножи для холодной резки металлов, зубила, пуансоны, керны и другие инструменты, работающие с ударными нагрузками. Из сталей марок Д1ХФ, 13Х, ХВ4, В2Ф, 9X1 и X —зубила, пуансоны, ножи для холодной резки металла, кернеры, круглые и ленточные пилы, метчики и другие режущие инструменты диаметром до 30 мм, шаберы, резцы и фрезы для обработки с небольшой скоростью резания, ножовочные полотна и калибры.
Из сталей марок 12X1, ХВГ и 9ХВГ изготовляют измерительные инструменты — плитки, калибры и шаблоны, а также измерительные и режущие инструменты, для которых повышенное коробление при закалке недопустимо, — резьбовые калибры, протяжки, длинные метчики и развертки, плашки и лекала сложной формы. Для деревообрабатывающих инструментов служат стали марок 8Х6НФТ, 9X5ВФ и 8Х4ВЗМЗФ2. Резьбона-катный инструмент, ручные ножовочные полотна и инструменты, предназначенные для холодной пластической деформации, выполняют из стали марки Х6ВФ.
Легированные стали второй группы применяют для изготовления деталей штампов и пресс-форм. Они в настоящей книге не рассматриваются.
Быстрорежущие стали. Быстрорежущей называется сталь, в состав которой помимо углерода входят легирующие элементы — вольфрам, хром, ванадий и молибден, образующие после термической обработки устойчивые карбиды. Кроме карбидообразующих элементов в некоторые марки быстрорежущих сталей входит также кобальт.
Быстрорежущие стали (ГОСТ 19265—73) приобретают после закалки и отпуска высокую твердость, прочность, износостойкость, теплостойкость и сохраняют режущие свойства при нагревании до температуры 600…650° С. Скорости резания инструментами из быстрорежущей стали в 2…4 раза выше, чем инструментами из легированной стали, кроме того, они обладают повышенной стойкостью.
Преимущества быстрорежущей стали проявляются главным образом при обработке прочных (ств= = 100 кгс/мм2) и твердых сталей (НВ 200..250) и резании с повышенной скоростью. По ГОСТу 19265—73 промышленность выпускает следующие марки быстрорежущей стали: Р18, Р12, Р9, Р6М5, Р6М5ФЗ, Р12ФЗ, Р18К5Ф2, Р9К5, Р6М5К5, Р9КЮ, Р9М4К8 и
Р10К5Ф5. В обозначениях марок буквы и цифры указывают: Р — быстрорежущая сталь; цифра, стоящая за буквой, — среднее содержание вольфрама в процентах; М — молибден, Ф — ванадий, К — кобальт; цифры, следующие за этими буквами, — соответственно содержание молибдена, ванадия и кобальта.
Быстрорежущие стали делятся на стали нормальной (Р18, Р12, Р9 и Р6М5) и повышенной (Р18К5Ф2, Р9М4К8, Р6М5К5, Р9К5, Р9КЮ, Р12ФЗ и др.) производительности. Почти все виды режущих инструментов для обработки обычных конструкционных сталей изготовляют из стали марок Р18, Р12, Р9 и Р6М5. Из стали марки Р6М5 с пониженной шлифуемостью производят инструменты простой формы, не требующие большого объема шлифования.
Инструменты для обработки высокопрочных нержавеющих и жаропрочных сталей и сплавов в условиях повышенного разогрева режущей кромки изготовляют из сталей марок Р18К5Ф2, Р9М4К8, Р6М5К5 и Р10К5Ф5. Инструментами из стали последней марки можно также обрабатывать материалы, обладающие абразивными свойствами.
Для обработки сталей и сплавов повышенной твердости и вязкости и для работы с ударом применяют инструменты из стали марки Р9К5, а нержавеющих и жаропрочных сталей и сплавов и сталей повышенной твердости и вязкости — инструменты из стали марки Р9К10. Резцы, зенкеры, развертки и другие инструменты для чистовой обработки вязких аустенитных сталей, а также материалов с абразивными свойствами изготовляют из стали марки Р12ФЗ. Развертки, протяжки и фрезы из стали марки Р6М5ФЗ предназначены для чистовой и получистовой обработки углеродистых и легированных сталей на средних скоростях резания.
Вольфрамомолибденовая сталь Р6М5 не только дешевле стали марки Р18, но и отличается хорошей теплопроводностью, мало склонна к трещинообразованию в процессе шлифования. По режущим свойствам при чистовой обработке она несколько уступает сталям Р18 и Р12, однако при черновой обработке режущие свойства ее лучше, чем у стали Р18. Недостаток стали Р6М5 — чувствительность к перегреву.
Сталь Р6М5К5, обладающая более высокими значениями теплостойкости, прочности и вязкости, чем сталь Р6М5, рекомендуется для черновой обработки.
В последние годы наблюдается тенденция к повышению содержания углерода в быстрорежущих сталях в среднем на 0,25% (до 1,1%) при содержании ванадия не более 2,8%- Стали с повышенным содержанием углерода отличаются более высокой износостойкостью.
В настоящее время быстрорежущую сталь начинают получать методом порошковой металлургии (пульвер-сталь или металлокерамическая сталь), что позволяет резко сократить карбидную неоднородность и повысить режущие свойства инструмента, особенно крупногабаритного. Из металлокерамической стали марки 10Р6М5 (она не стандартизована) изготовляют зуборезные инструменты.
Конструкционные стали. В инструментальном производстве применяют углеродистые качественные конструкционные стали, регламентированные ГОСТом 1050—74. Настоящий стандарт распространяется на сортовую углеродистую качественную конструкционную сталь горячекатаную и кованую марок 08, 10, 15, 20, 25, 30, 35, 40, 45, 50, 55, 58 и 60 диаметром или толщиной до 250 мм, марок 65, 70, 75, 80, 85, 60Г, 65Г и 70Г диаметром или толщиной до 60 мм, а также сталь калиброванную и серебрянку всех марок.
В обозначениях марок стали цифры указывают среднее содержание углерода в сотых долях процента, буква Г — содержание марганца (около 1%).
Конструкционные углеродистые стали широко используются для производства составного режущего инструмента. Нерабочую часть инструмента — державки, корпуса, хвостовики и др. — изготовляют из этих сталей. Из низкоуглеродистых сталей 20 и 25 с последующей цементацией и закалкой и среднеуглеродистых марок 50 или 55 изготовляют измерительные инструменты— скобы, шаблоны, калибры и др. Из конструкционных сталей выполняют также различные детали приспособлений.
ВК4-В, В Кб, В Кб-А, ВК6-0М, ВК6-В, ВК8, ЁК8-ВК, ВК8-В, вкю, ВК10-М, ВКЮ-ОМ, ВК10-КС, вкп-в, BK11-BK, BK15, BIC20, ВК20-КС, BK20-K и ВК25.
Сплавы этой группы состоят из зерен карбидов вольфрама (WC), сцементированных кобальтом, и обозначаются буквами ВК и цифрой, показывающей процентное содержание кобальта. Буква М указывает на мелкозернистую структуру сплава в изделиях, буква В после цифры обозначает технологический признак и показывает, что изделие из этого сплава спекается в атмосфере водорода, буква К в конце марки указывает на крупнозернистую структуру сплава, получаемую по специальной технологии, а буквы ОМ — на особо мелкозернистую структуру сплава в изделиях. Твердость сплавов группы ВК HRA 83…91, предел прочности при изгибе (Ти— 110…240 кгс/мм1, плотность— 13… г/см3.
К титановольфрамовой группе относят твердые сплавы марок Т30К4, Т15К6, Т14К8, Т5КЮ и Т5К12. Структура сплавов этой группы состоит из зерен твердого раствора карбида и вольфрама в карбиде титана (TiC) и избыточных зерен карбида вольфрама, сцементированных кобальтом, или только из зерен твердого раствора карбида вольфрама в карбиде титана, сцементированных кобальтом. Сплавы этой группы обозначаются буквами ТК и цифрами. Так, марка Т30К4 обозначает: Т—титан, цифра 30 — 30% карбида титана, К —кобальт, цифра 4 — 4% кобальта. Карбид вольфрама определяют по разности 100—(30+4) =66%. Твердость сплавов группы ТК HRA 87…92, предел прочности при изгибе (Ги=-95…165 кгс/мм2, плотность—> 9,5… 13,5 г/см3.
В титанотанталовольфрамовую группу входят твердые сплавы марок ТТ7К12, ТТ8К6, ТТ10К8-Б иТТ20Щ Структура сплавов этой группы состоит из зерен твер^ дого раствора (Ti, Та, W)Co и избыточных зерен карбида вольфрама, сцементированного кобальтом. Обозначаются они буквами ТТК и цифрами: первая буква Т — титан, вторая — тантал, буква К — кобальт. Так, сплав марки ТТ7К12 содержит в среднем 7% карбидов титана и тантала (4+3), 12% кобальта и 81% карбида вольфрама. Твердость сплавов этой группы HRA 87…88, предел прочности при изгибе аи= 150… 165 кгс/мм2, плотность—12,8…13,3 г/см3.
Металлокерамические твердые сплавы обладают высокой красностойкостью и сохраняют режущие свойства при Hsrpese до температур #=900…1000° С; при этом сплавы группы ТК болеё Износоустойчивы и имеют лучшую красностойкость. С повышением содержания кобальта хрупкость сплавов уменьшается, однако одновременно понижается и их твердость. Сплавы группы ВК более вязки, чем сплавы группы ТК.
Твердые сплавы выпускают главным образом в виде стандартных пластинок разнообразной формы и различных размеров. Неперетачиваемые многогранные пластинки механически крепятся в дерновках режущего инструмента. Изготовляются также цельные твердосплавные инструменты — фрезы диаметром от 3 до 60 мм, машинные развертки диаметром от 6 до 12 мм, ручные метчики от М2 до М10 и спиральные сверла диаметром от 1,8 до 5,2 мм.
Для обработки резанием применяют сплавы различных марок. Сплавы ВКЗ, ВК4, ВК6 и ВК8 служат для обработки обычных чугунов на чистовых и получисто-вых операциях точения, растачивания, фрезерования, сверления, развертывания и нарезания резьб, а ВКЗ-М и ВК8 — для чистового и получистового точения и растачивания, нарезания резьбы на твердых чугунах. Сплавы В Кб, ВК8 и ВК6-М предназначены для строгания, чернового точения и растачивания, сверления и долбления, а ВК6-М пригоден для всех видов механической обработки чугунов.
Сплавы группы ТК используются главным образом для обработки сталей: Т30К4 — для чистовой и полу-чистовой обработки цементированных и закаленных углеродистых и легированных сталей, Т14К8 —для черновой, а Т15К6 — для любых видов обработки тех же сталей, Т5КЮ — для чернового точения при неравномерном сечении среза и прерывистом резании, фасонном точении, отрезке, строгании, черновом фрезеровании.
Сплавы группы ТТК марки ТТ7К12 применяют при тяжелом черновом точении при неравномерном сечении среза и наличии ударов, а также при работе на изношенном оборудовании, сплав ТТ10К8-Б — для черновой и получистовой обработки труднообрабатываемых материалов, включая жаропрочные стали и сплавы.
—
Швейцарская фирма Gebruder Sulzer применяет для машиностроительных деталей, подверженных истиранию, например для деталей швейных и текстильных машин, инструментальную сталь GS-85CrVW4, содержащую (%) 0,86 С, 0,45 Si, 0,55 Мп, 1,0 Сг, 0,14 W, 0,3 V.
В ГДР используют инструментальные стали по TGL 14415.
В ЧССР применяют инструментальную сталь для штампов по ON 422870 и быстрорежущую сталь для литого инструмента по CSN 423992.
Для точных отливок, эксплуатирующихся при высоких температурах, применяют специальные сплавы на базе никеля, легированные хромом и кобальтом и небольшим количеством других легирующих элементов (Ti, Al, В, Zr, Та, V).
Большинство специальных – сплавов, используемых в США, имеют фирменные названия. Так называемые сплавы Supper Alloys пригодны для литья в вакууме. Отливки из этих сталей используют под нагрузкой при высоких температурах (см. табл. 58). Для большинства специальных сплавов требуется особый режим термообработки, если необходимо получить оптимальные свойства. Режим термообработки зависит от толщины стенки отливок и обычно состоит из следующих операций: гомогенный отжиг (толщина стенки более 75 мм) при 1150 °С с выдержкой 4 ч; охлаждение на воздухе; отпуск в течение 1 ч при 595 °С; текучести 1600 Н/мм2 при относительном удлинении 8% и относительном сужении 20%. Эти величины прочности можно получить и при больших толщинах.
Отливки из сплава Maraging не имеют поверхностного обезуглероживания. В гомогенизированном состоянии их обрабатываемость приблизительно такая же, как коррозионно-стойких сталей. В отвержденном состоянии обрабатываемость приблизительно на 50% хуже. Свариваемость хорошая, если используются электроды из того же сплава, выплавленного в вакууме, но без бора, циркония и титана. Сварку проводят в атмосфере инертного газа.
Читать далее:
Прочность и твердость металла
Статьи по теме:
pereosnastka.ru
Маркировка инструментальных сталей
Маркировка инструментальных сталей зависит от их типа – углеродистые или легированные.
Если инструментальная сталь углеродистая, то ее обозначают буквой «У» и одной или двумя цифрами, показывающими среднее содержание углерода в десятых процента (ГОСТ 1435–99 «Прутки, полосы и мотки из инструментальной стали. Общие технические условия»). Буква «А» в конце маркировки показывает, что сталь является высококачественной. Например, У10А – углеродистая высококачественная сталь, содержащая в среднем 1,0 % С.
У легированных инструментальных сталей маркировка начинается с одной цифры, показывающей содержание углерода в десятых долях процента. Если сталь содержит около 1,0 % С и более, то цифру опускают. Буквы, указывающие на легирующие элементы, и цифры, показывающие их количественное содержание, соответствуют обозначениям для конструкционных легированных сталей. Например, сталь ХВГ – содержит 0,90 – 1,05 % С; 1,20 – 1,60 % W; 0,80 – 1,10 % Mn. Сталь 6ХВ2С – 0,55 – 0,65 % С; 1,0 – 1,3 % Cr; 2,2 – 2,7 % W; 0,5 – 0,8 % Si.
Между тем, существует ряд исключений из этих правил. Так, хромистые стали, которые идут на изготовление подшипников, маркируют буквами «ШХ» и цифрами, которые показывают содержание основного легирующего элемента (хрома) в десятых долях процента (ГОСТ 810–78). Например, сталь ШХ15 содержит около 1 % С и 1,5 % Cr.
Быстрорежущие стали обозначают буквами «Р» и цифрами, показывающими содержание основного легирующего элемента – вольфрама. Во всех быстрорежущих сталях содержится около 4 % Cr и его содержание в марке стали не указывают, так же не указывают содержание углерода. Например, сталь Р6М5К5 содержит около 1 % С; 6 %W; 5 % Mo; 5 % Co.
Некоторые высоколегированные стали с большим количеством легирующих элементов упрощенно обозначают по заводу–изготовителю и порядковому номеру разработки. Например, стали производства металлургического завода «Электросталь» (Россия) обозначают «ЭИ» (Электросталь исследовательская), «ЭП» (Электросталь пробная), производства завода «Днепроспецсталь» обозначают «ДИ».
По ГОСТ 5521–93 «Прокат стальной для судостроения» выпускают ряд сталей повышенной прочности. К этим сталям предъявляют повышенные требования к стабильности свойств и сохранению их при низкой температуре эксплуатации. В начале маркировки этих сталей стоит одна из букв «А», «В», «D», «Е», которая указывает на гарантированный уровень свойств и условия испытания данной стали. Химический состав самой стали определен в стандарте. Сталь обычной прочности обозначают одной буквой из указанных выше (например, B). Сталь повышенной прочности обозначается буквой (А, D или Е) и цифрами – А27S, D36, E40S. Например, широко распространенная сталь D32 входит в группу, которую испытывают на ударный изгиб при –20 oС, стали группы «Е» испытывают при –40 ОС. Индекс «РС» перед маркой стали указывает, что она изготовлена под надзором Регистра (инспектор Регистра оформляет сертификат) – РС А32.
uas.su
Инструментальные, углеродистые, качественные, высококачественные стали. применение, маркировка, расшифровка.
⇐ ПредыдущаяСтр 2 из 5Следующая ⇒Инструментальная сталь по сравнению с конструкционными углеродистыми сталями обладает значительно большей твердостью (особенно после закалки), но является более хрупкой. По химическому составу инструментальные стали подразделяются на инструментальные углеродистые (ГОСТ 1435- 54), легированные инструментальные (ГОСТ 5952-51) и быстрорежущие (ГОСТ 5952-51).
Инструментальные углеродистые стали по содержанию углерода и твердости подразделяются на низкоуглеродистые, содержащие углерод до 0,25%; среднеуглеродистые - от 0,25% до 0,6% и высокоуглеродистые - от 0,6 до 2%.
Углеродистые инструментальные стали в соответствии с ГОСТ 1435-54 обозначаются следующими марками: У7; У8; У8Г; У9; У10; У11; У12; У13. Буква У указывает, что сталь углеродистая, а следующая за ней цифра - среднее содержание углерода в десятых долях процента. Буква Г в марке показывает повышенное содержание марганца.
Углеродистые инструментальные стали бывают качественные и высококачественные.
К группе качественных сталей относятся марки стали без буквы А, к группе высококачественных сталей, более чистых по содержанию серы и фосфора, а также примесей других элементов - марки стали с буквой А. Буквы и цифры в обозначении этих марок стали означают: У - углеродистая, следующая за ней цифра - среднее содержание углерода в десятых долях процента, Г - повышенное содержание марганца.
Высококачественные углеродистые инструментальные стали, выплавляемые в электропечах, маркируются таким же образом, но с добавлением в конце буквы А, т. е. У7А, У8А и т. д. Буква А обозначает, что сталь является высококачественной (улучшенной), по составу более чистой, с пониженным содержанием серы (до 0,03%), фосфора (также до 0,03%), остаточных примесей и неметаллических включений. Содержание марганца в этих сталях колеблется в пределах от 0,15 до 0,40%; кремния от 0,15 до 0,35%.
Достоинством инструментальных углеродистых сталей является их хорошая обрабатываемость, невысокая твердость (160-180 НВ). Однако они имеют и крупные недостатки: небольшой интервал закалочных температур, необходимость быстрого охлаждения в воде при закалке, что приводит к короблению, деформации инструментов и даже образованию трещин.
Инструментальная углеродистая сталь применяется для изготовления различных инструментов (режущих, мерительных и др.), которые должны обладать высокой износоустойчивостью и красностойкостью.
Марки и области применения инструментальной стали приведены в табл.
Марка стали | Содержание углерода (%), ГОСТ 1435-54 | Твердость HB | Назначение (примерно) |
У7 | 0,65-0,74 | 156-187 | Зубила, гладильный кузнечный инструмент, штампы, клейма, кувалды, кузнечные и слесарные молотки, плотничный инструмент |
У8 У8Г | 0,75-0,84 0,80-0,90 | 156-187 187-190 | Ножи и вилы по металлу, пробойники, пуансоны, клейма, штампы, инструмент для обтески камня |
У9 | 0,85-0,94 | 159-192 | Дыропробойные штемпеля, кернеры, деревообрабатывающий инструмент |
У10 У11 | 0,95-1,04 1,05-1,14 | 163-197 170-207 | Резцы, сверла, метчики, развертки, плашки, ножовочные полотна, зубила для насечки напильников |
У12 | 1,15-1,24 | 170-207 | Резцы по металлу, фрезы, шаберы, развертки |
У13 | 1,25-1,35 | 170-217 | Резцы по твердому металлу, бритвы, шаберы, сверла |
Испытание на твердось по Бринеллю и Роквеллу.
Твердость по Бринеллю
Испытание на твердость по Бринелю проводится путем вдавливания стального закаленного шарика диаметром 10 мм, 5 мм или 2,5 мм под действием нагрузки, величина которой определяется толщиной образца и уровнем измеряемой твердость. После снятия нагрузки на поверхности остается отпечаток, который измеряют с использованием особой лупы с делениями. Твердость определяется по формуле:
,
где Р– усилие, действующее на шарик, кг;
S– площадь поверхности отпечатка, мм²;
D– диаметр шарика, мм;
d– диаметра отпечатка, мм;
НВ– твердость по Бринеллю.
Образец для испытания на твердость должен быть плоскопараллельным, очищенным от окалины и других загрязнений. С целью повышения точности измерений количество отпечатков должно быть не менее 2, каждый отпечаток промеряется в двух перпендикулярных направлениях, и результат определяется как среднеарифметический. При этом расстояние от края образца до центра отпечатка должно быть не менее 2,5d, а расстояние между отпечатками>4d. Диаметры отпечатков должны находиться в пределах 0,2D<d< 0,6D.
Число твердости при стандартных условиях (шарик 10 мм, нагрузка 3000 кг, выдержка под нагрузкой 10 с) пишут так: НВ400 (твердость 400 единиц по Бринеллю). Если условия испытания другие, то обозначение твердости дополняется этими условиями. Например, НВ5/250/30-200 означает: число твердости 200 при испытании шариком 5 мм под нагрузкой 250 кг в течение 30 с.
Твердость испытываемых методом Бринелля материалов не должна превышать НВ450 во избежание деформирования стального шарика и искажения результатов испытания. Такими материалами являются цветные металлы и сплавы, а также сырые незакаленные стали и чугуны.
Твердость по Роквеллу.
Если использование метода Бринелля ограничено средней твердостью (до 450 НВ), то метод Роквелла позволяет измерить твердость до 1000 НВ, что намного расширяет круг испытуемых материалов и делает этот метод более универсальным. Мягкие материалы испытываются стальным шариком D= 1,58 мм, твердые – алмазным конусом с углом 120°. Для этого предусмотрены разные нагрузки: шарик нагружается средней нагрузкой – 100 кг, а конус – двумя нагрузками 150 и 60 кг. Большая нагрузка предусмотрена для измерения твердых и относительно прочных материалов, таких как закаленные стали. Твердые и хрупкие материалы, например, твердые сплавы, испытываются при малой нагрузке. В соответствии с этими нагрузками прибор имеет три шкалы измерения: А,B,C. В отличие от метода Бринелля твердость по Роквеллу измеряется не в кг/мм2, а в условных единицах, соответствующих разности между глубиной отпечатка от предварительной нагрузки – 10 кг и окончательной нагрузки. За единицу измерения принята величина, отвечающая осевому перемещению шарика или конуса на глубину 0,002 мм.
Это перемещение измеряется автоматически на приборе, и стрелка индикатора сразу показывает отсчет твердости по соответствующей шкале. Запись чисел твердости производится с обозначением шкалы, например, НRС60, НRВ90, НRА70. Твердость по Роквеллу – безразмерная величина. При необходимости твердость по Роквеллу может быть переведена на твердость по Бринеллю с использованием соответствующих переводных таблиц.
Метод Роквелла вследствие относительной простоты и высокой скорости, широкого диапазона материалов по твердости, высокой точности и небольшого отпечатка на испытуемом материале получил широкое применение. Рекомендуемые условия испытания приведены в таблице 4.2. Расстояние между центрами отпечатков либо до края образца не должно быть меньше 3 мм.
Читайте также:
lektsia.com
Марки инструментальной стали в Ростове-на-Дону
Сталь инструментальная углеродистая | ||||
У10 | У10А | У11 | У11А | У12 |
У12А | У13 | У13А | У7 | У7А |
У8 | У8А | У8Г | У8ГА | У9 |
У9А |
Сталь инструментальная легированная | ||||
05Х12Н6Д2МФСГТ | 11Х4В2МФ3С2 | 11ХФ | 12Х1 | 13Х |
3Х2МНФ | 4ХМНФС | 4ХС | 5ХВ2СФ | 5ХНВ |
5ХНВС | 6Х3МФС | 6Х4М2ФС | 6Х6В3МФС | 7ХФ |
8Х4В2МФС2 | 8Х6НФТ | 8ХФ | 9Г2Ф | 9Х1 |
9Х5ВФ | 9ХВГ | 9ХС | 9ХФ | 9ХФМ |
В2Ф | Х | ХВ4 | ХВ4Ф | ХВГ |
ХВСГ | ХВСГФ | ХГС |
Сталь инструментальная штамповая | ||||
27Х2Н2М1Ф | 2Х6В8М2К8 | 3Х2В8Ф | 3Х2Н2МВФ | 3Х3М3Ф |
40Х5МФ | 4Х2В5МФ | 4Х2НМФ | 4Х3ВМФ | 4Х4ВМФС |
4Х5В2ФС | 4Х5МФ1С | 4Х5МФС | 4ХВ2С | 4ХМФС |
5Х2МНФ | 5Х3В3МФС | 5ХВ2С | 5ХГМ | 5ХНМ |
6ХВ2С | 6ХВГ | 6ХС | 7Х3 | 7ХГ2ВМ |
7ХГ2ВМФ | 8Х3 | 8Х4В3М3Ф2 | Х12 | Х12ВМ |
Х12ВМФ | Х12М | Х12МФ | Х12Ф1 | Х6ВФ |
Х6Ф4М |
Сталь инструментальная быстрорежущая | ||||
11М5Ф | 11Р3АМ3Ф2 | 9Х4М3Ф2АГСТ | Р10Ф5К5 | Р12 |
Р12Ф3 | Р14Ф4 | Р18 | Р18К5Ф2 | Р18Ф2 |
Р18Ф2К5 | Р2АМ9К5 | Р2М5 | Р6М3 | Р6М5 |
Р6М5К5 | Р6М5Ф3 | Р9 | Р9К10 | Р9К5 |
Р9М4К8 | Р9Ф5 |
Инструментальная углеродистая сталь — это сталь, содержащая от 0,7 % и более углерода. Инструментальная углеродистая сталь - тип, который характеризуют высокая твердостью и прочность, достигаемые после окончательной термообработки. Инструментальная углеродистая сталь используется для изготовления инструмента. Инструментальная сталь может быть двух видов: качественная и высококачественная. Отличаются стали процентом содержания серы и фосфора:
- Качественная сталь — 0,03 % серы и 0,035 % фосфора (К этой группе относят марки, не имеющие в конце маркировки букву «А»;
- Высококачественная сталь — 0,02 % и 0,03 % соответственно (продукция этой группы более чистая по содержанию серы и фосфора, а также примесей других элементов и имеет букву «А» в конце маркировки, например, марка у10а, у8а).
Буква «У» означает углеродистая сталь, последующая за ней цифра отражает среднее содержание углерода в стали в десятых долях процента. Инструментальная углеродистая сталь выпускается по ГОСТ 1435-99. Этот стандарт определяет параметры горячекатаной, кованой, калиброванной стали и серебрянки. Главное достоинство углеродистых сталей заключается в том, что стоимость их невысока, однако, эти стали достаточно тверды в сравнении с другими инструментальными материалами. Среди недостатков можно выделить довольно низкую изно- и теплостойкость. У8а применяют для производства инструментов, которые будут эксплуатироваться в не вызывающих разогрева режущей кромки условиях, например, для обработки дерева. Из стали марки У8а могут производить фрезы, зенковки, поковки, топоры, стамески, долото, пилы продольные и дисковые; накатные ролики, плиты и стержни для форм литья под давлением оловянно-свинцовистых сплавов.
Среди слесарно-монтажных инструментов сталь марки у8а также широко распространена: из этого сырья изготавливают обжимки для заклепок, кернеры, бородки, отвертки, комбинированные плоскогубцы, острогубцы, боковые кусачки. У10а часто становится сырьем для следующих предметов: сверла спиральные, пилы машинные столярные, а также ручные поперечные и столярные; вытяжные, высадочные, обрезные и вырубные штампы холодной штамповки небольших размеров, не имеющие резкие переходы по сечению; напильники, калибры простой формы и пониженных классов точности, шаберы слесарные, накатные ролики и т.д. Однако эти списком не исчерпывают возможности использования стали марки у10а, которая отличается сочетанием приемлемой цены и высокого качества. Компания «Углерод» функционирует на рынке металлопроката уже более 8 лет. Мы занимаемся не только реализацией металлопрокатной продукции, такой как лист и круг, но и осуществляем резку стали. Ознакомиться с нашим прайсом на сталь можно, связавшись с менеджерами компании. Для удобства наших клиентов сталь (круг, лист, квадрат, полоса и т.п.) поставляется в такие города юга России как:
karbin.ru