Инверторные плазменные сварочные аппараты: что это, плюсы и минусы, какие бывают. Плазменный инверторный резак
Инверторный плазменный сварочный аппарат: резак, плазморез, какой лучше
Главная страница » Плазменная сварка » Оборудование » Аппараты плазменной сварки » Инверторные плазменные сварочные аппараты: что это, плюсы и минусы, какие бывают
В настоящее время альтернативой обычному электросварочному аппарату стал инвертор плазменной сварки и резки.
Ранее это устройство активно использовалось только в промышленности, однако с каждым днем оно все более часто находит свое применение и в бытовой сфере.
Этот факт и обусловил актуальность данной статьи, в которой будут рассмотрены инверторные сварочные аппараты как тип, охарактеризованы их основные виды, а также проанализированы преимущества и недостатки этого многофункционального устройства.
Инверторный плазменный сварочный аппарат – что это такое
Сварочный аппарат плазменного типа – устройство, имеющее сравнительно небольшой размер и потребляющее минимальное количество электроэнергии. При помощи плазменного инвертора осуществляется соединение и резка черных и цветных металлов.
Принцип его работы заключается в том, что при помощи электрических разрядов специальная смесь (аргон, азот, воздух или водород) превращается в плазму, максимальная температура которой колеблется в промежутке от 6 до 7 тысяч градусов (оценки температуры у разных производителей расходятся, да и не особо это важно для конечного потребителя в большинстве случаев).
Это приспособление состоит из плазмотрона (резака) и источника питания (в данном контексте, мы говорим об инверторе). Плазмотрон инвертора, в зависимости от функционального назначения установки, может быть прямого и косвенного действия. Сварочный аппарат с плазмотроном прямого действия используется при необходимости генерации дуги, а механизм косвенного действия активно применяют в случаях, когда требуется генерация струи плазмы.
После окончания работы плазмотрон нуждается в охлаждении, поскольку образуемая им плазма достигает очень высоких температур. В зависимости от способа охлаждения плазмотрона сварочные аппараты подразделяются на охлаждаемые при помощи воздуха и воды. Первый вид наиболее выгоден с финансовой точки зрения, а второй – максимально эффективен, но сложен в использовании.
- Аппарат для сварки превращает переменный электрический ток в постоянный, а затем снова возвращает его в прежнее состояние, в то время как выпрямитель работает лишь с переменным током.
- Инвертор потребляет в два раза меньше электроэнергии.
- Выпрямитель имеет силовой трансформатор, которого в сварочном аппарате нет.
- Размер и вес инвертора гораздо ниже.
Инвертор плазменной резки: плюсы и минусы
Как и любой другой сварочный аппарат, плазменный инвертор имеет свои достоинства и недостатки, в сравнении с устройствами для газовой, электродуговой, электрошлаковой, лазерной и другими видами сварки.
Достоинства инвертора плазменной резки
1. Имеет высокую эффективность нагрева металла, в отличие от газовой сварки, в процессе которой этого добиться практически невозможно.2. Может сваривать максимально толстые детали (это свойство, кроме плазменного, обеспечивает только аппарат для электрошлаковой сварки, в то время как все остальные устройства имеют ограничения в объеме деталей, с которыми работают).3. Способен работать со всеми видами металлов и даже с неметаллическими веществами, чего не может гарантировать больше ни один сварочный аппарат.4. Обладает небольшим размером, надежен и максимально прост в использовании.
Недостатки плазменного сварочного аппарата
1. Отличается высокой стоимостью, в отличие от устройства для газовой сварки, приобретение которого не ударит по кошельку среднестатистическому пользователю.2. Характеризуется инфракрасным и ультрафиолетовым излучением, а также насыщением воздуха вредными ионами, в противовес абсолютно безопасной лазерной сварке.3. В процессе работы выделяет вредные пары металлов, в противоположность агрегату для холодной сварки.
Где применяются
Плазменный сварочный аппарат многофункционален, в силу чего нашел свое применение во многих сферах деятельности. Его используют:
- В процессе термической обработки стали и других металлов.
- При соединении (сварке и пайке) или резке черных и цветных металлов.
- В процедуре воронения стали.
- Для резки плитки, стекла, бетона и прочих материалов.
Видео
Вот, к примеру резка керамической плитки Мультиплазом 3500:
К сожалению, из-за высокой стоимости этого устройства, его приобретение может себе позволить далеко не каждое предприятие.
Популярные производители и модели
Наиболее популярными производителями инверторных сварочных механизмов плазменного типа являются компании Горыныч, Плазариум и Мультиплаз. Какой лучше, судить конечным пользователям, вы можете перейти по ссылкам в тексте ниже, чтобы ознакомиться с отзывами по конкретным моделям.
Основной особенностью модели компании-производителя Горыныч является тот факт, что в качестве смеси, используемой для образования плазмы, в ней применяется вода в чистом виде или в смешении со спиртом.
Это свойство становится препятствием для образования коррозии. Работать такой аппарат может как от сети, так и от генератора.
Принцип работы устройства фирмы Мультиплаз схож с предыдущим. Еще одним достоинством этого инвертора является компактный размер, ведь вес его «младших моделей» (подробности см. по ссылке) не превышает шести килограмм. Кроме того, такой сварочный аппарат, в отличие от своих аналогов, в процессе работы практически не выделяет вредных веществ.
Компания Плазариум не разрабатывает таких мощных устройств, как ее конкуренты. Соответственно, цены на ее продукцию гораздо ниже. Однако характерным нововведением моделей этой фирмы является наличие на аппаратах специальных датчиков, помогающих регулировать температуру сварки, чтобы избежать поломки вследствие перегрева.
plazmen.ru
Плазморез своими руками из инвертора, подробности изготовления, видео
Домашние мастера, занимающиеся обработкой металла, сталкиваются с необходимостью раскраивать металлические заготовки. Это можно сделать при помощи угловой шлифовальной машины (болгарки), кислородного резака или плазмореза.
- Болгарка. Качество среза очень высокого уровня. Однако выполнить фигурный раскрой невозможно, особенно если это касается внутренних отверстий с изогнутыми краями. К тому же есть ограничения по толщине металла. Тонкие листы резать болгаркой невозможно. Главное преимущество – ценовая доступность;
- Кислородный резак. Может вырезать отверстие любой конфигурации. Но добиться ровного среза невозможно в принципе. Края получаются рваными, с каплями оплавленного металла. Тяжело режется толщина более 5 мм. Приспособление не слишком дорогое, но требуется иметь большой запас кислорода для работы;
- Плазморез. Доступным этот прибор не зазовешь, но высокая стоимость оправдана качеством среза. После раскроя, заготовка практически не нуждается в дополнительной обработке.
Учитывая неподъемную для большинства домашних мастеров цену – многие умельцы «кулибины» изготавливают плазменный резак своими руками.
Способов несколько – можно создать конструкцию полностью «с нуля», или использовать готовые приспособления. Например – из сварочного аппарата, несколько модернизированного под новые задачи.
Изготовить плазморез своими руками реальная задача, но сначала необходимо понять, как он работает.
Общая схема изображена на иллюстрации:
Устройство плазмореза
Блок питания.
Он может быть сконструирован по-разному. Трансформатор имеет большие габариты и массу, но позволяет резать более толстые заготовки.
Потребление электроэнергии выше, это необходимо учитывать при выборе точки подключения. Такие блоки питания мало чувствительны к перепадам входного напряжения.
Инверторы экономичны, у них выше КПД. Дуга, полученная с помощью такого источника питания, горит стабильнее, что положительно влияет на качество реза.
Инвертор легче, и занимает меньше места в сравнение с трансформатором. Это делает прибор мобильным, что позволяет работать в труднодоступных местах.
Однако есть и недостатки. Толщина разрезаемой заготовки ограничена.
Плазмотрон.
Рабочая головка, с помощью которой производится резка.
Схема плазменного резака:
На электрод подается напряжение от инвертора для возбуждения плазменной дуги. Выбирается тугоплавкий металл, с образованием прочного окисла.
Например, цирконий, гафний или бериллий. Сопло служит для формирования плазменной струи. В зону образования плазмы подается сжатый воздух, который одновременно придает форму плазменной струе и охлаждает электрод.
Параметры сопла определяют характеристики реза. От диаметра зависит скорость разреза заготовки и размер прожигаемой щели. Величина отверстия на типовом резаке обычно равняется 3 мм. От длины напрямую зависит качество обработки. Однако слишком длинное сопло сильно нагревается и быстро изнашивается.
Охладитель (он же изолятор) частично отводит тепло от сопла, продлевая его ресурс. В рабочем режиме плазма достигает температуры более 25000°.
Поскольку плазма состоит не только из потока заряженных частиц, а еще и из воздуха – он должен подаваться в больших количествах. Этим вопросом заведует компрессор. Если рабочий ток не превышает пары сотен ампер, используется обычный воздух из атмосферы. Толщина разрезаемого металла менее 5 см.
В промышленных резаках выше сила тока и применяются различные газы: аргон, гелий, азот и даже кислород с водородом.
По управляющему комплекту шланг-кабель поступает как электрический ток, так и сжатый воздух (газ).
Подробное описание как сделать плазмотрон для плазмореза в этом видео.
Как работает плазморез
После нажатия управляющей клавиши, ток большой величины и частоты зажигает (в буквальном смысле) электрическую дугу между соплом и электродом. Температура в наконечнике поднимается до 7000° С.
Когда дежурная дуга заполняет все сопло, подается сжатый воздух (газ). От воздействия высокой температуры газ ионизируется, и становится проводником. Фактически возникает короткое замыкание через воздух, который превращается в газообразный электрод.
В этот момент из сопла вырывается сформированная конусом плазма с температурой более 20000° С. При таких условиях электропроводность раскаленного воздуха внутри плазменного потока, равна проводимости металла.
При соприкосновении плазмы с металлом заготовки, возникает классическая дуга, как при электродной сварке. В роли электрода выступает плазма. Дуга моментально нагревает металл в точке соприкосновения. Размер пятна равен диаметру сопла. Превратившийся в жидкость металл, моментально выдувается под напором сжатого воздуха. Происходит резка заготовки.
Важно! При работе с плазморезом требуется определенная сноровка. Двигаться необходимо равномерно, с правильно заданной скоростью.
Если головку вести слишком медленно – рез получится не таким ровным, и будет слишком широким. Нагревшиеся края металла станут корявыми. Быстрое перемещение не позволит качественно выдувать расплавленный металл, и рез потеряет непрерывность.
Этого недостатка лишены станки плазморезы, в которых сопло управляется механически.
Однако стоимость таких устройств слишком высока. Самостоятельное изготовление затруднено, по причине дороговизны комплектующих. Мы рассмотрим возможность изготовления ручного плазменного резака со средними параметрами.
Плазморез своими руками из инвертора
Основная сложность – изготовление собственно плазмотрона. Точнее – режущего сопла.
Металлы, из которых вытачиваются наконечники, к доступным не относятся. Поэтому есть смысл приобрести готовое сопло. Патрубок для подключения шланга, работающего под давлением – должен быть установлен промышленным путем.
Рабочая область имеет температуру в несколько тысяч градусов, поэтому любой доступный в домашних условиях способ сварки, не подойдет. Трубка просто отвалится. А вот готовую режущую готовку не составит труда разместить в рукоятке, которая рассчитана на высокие температуры. Если вы делаете плазморез из инвертора – такая рукоять входит в комплект.
Также необходимо всегда иметь запас расходных материалов. Сопло, из какого бы прочного металла оно не было сделано, изнашивается довольно быстро. Поэтому комплект из 5-10 насадок и катодов не помешает. К тому же лучше иметь несколько различных диаметров сопла, для работы с разными металлами.
Токопроводящий кабель от инвертора объединяют со шлангом для подачи сжатого воздуха. Вся конструкция должна составлять единое целое, иначе можно просто запутаться в шлангах во время работы.
В качестве корпуса для сопла хорошо использовать керамические втулки. Это и диэлектрик, и охладитель, неплохо рассеивающий лишнее тепло.
Самодельный плазморез, в отличие от обычного сварочника нуждается в управлении поджигом дежурной плазмы. Для этого в конструкцию готового инвертора встраивается осциллятор, который дает первичную искру для запала.
После появления рабочей плазмы его необходимо отключать. Для этого используется схема, работающая при помощи реле. Как только ток достигает рабочей величины – осциллятор выключается и дуга работает от основного (нагрузочного) выхода инвертора.
В остальном инвертор остается без изменений. Мощности хватает для обеспечения горелки при толщине металла до 20 мм. Обычно большую толщину в домашних условиях не обрабатывают.
Самодельный плазморез не может обойтись без компрессора. Для образования стабильной рабочей плазмы достаточно давления 2-2,5 атмосферы. Такую величину обеспечит даже обычный автомобильный компрессор.
Вся проблема в том, что во время работы расходуется огромное количество воздуха, и компрессор не может восполнить его с нужной скоростью. Если давление упадет – рабочая плазменная дуга разрушится, и резать металл будет невозможно.
Вопрос решается установкой воздушного ресивера. Он служит аккумулятором для накопления давления. Кратковременные интервалы работы резака не успевают снизить давление, а во время перерывов компрессор пополняет запас сжатого воздуха.
Можно использовать баллоны тормозной системы от грузовиков. Например – от «Камаза». Однако более практичным будет приобретение стандартного комплекта компрессора с ресивером.
Только обязательно оснастите комплект редуктором. Необходимо иметь возможность выставлять и поддерживать постоянное давление. Покупка компрессора не будет обременительной для бюджета, если использовать его для других целей. Например, для покраски с помощью краскопульта.
С помощью подобной самоделки можно резать как тонкую жесть толщиной 1 мм, так и толстые стальные пластины. Если работать по шаблону – можно вырезать качественные заготовки не хуже станка с ЧПУ.
В этом видео подробности сборки самодельного плазмореза.
obinstrumente.ru
Плазморез Ресанта ИПР-40К - цена и отзывы сварщиков
Прошли те времена, когда лидерство принадлежало исключительно газовым резакам. Технологии не стоят на месте и вслед за инверторными сварочными аппаратами начали появляться аппараты плазменной резки. Для получения плазмы этим устройствам достаточно электричества и подачи сжатого воздуха. Высокотемпературная плазма образуется в плазмотроне при прохождении воздуха через электрический разряд. Воздух ионизируется и переходит в необычное состояние. Истечение плазмы из сопла плазмотрона (или плазменной горелки) происходит благодаря приданию разрезаемому металлу положительного заряда. Отсюда следует, что масса подключается всегда к плюсовому полюсу.
Высокоточные резы на сталях толщиной до 12 мм теперь выполняют исключительно плазморезами, толстый металл (лом) по прежнему «рубят» газовым резаком.
Итак, очень хочется стать обладателем плазмореза, но трудно выбрать из имеющегося ассортимента. Что делать?
Отвечая на этот вопрос, нужно отметить, что на рынке сегодня прочно закрепился плазморез под названием CUT 40. Идет он под разными торговыми марками. Наиболее известная из них – это AuroraPRO AIRHOLD 40, вы наверное, слышали о ней. Она реализуется и под другим названием — Кедр CUT 40. И то, и другое – это одно и то же.
Так вот, этим зарекомендовавшим продуктам уже ни один год успешно противостоит Ресанта ИПР-40К, которая, кстати, зарекомендовала себя, как более стабильно работающий аппарат, чем CUT 40. Часто плазморез Ресанта выбирают обладатели успешно работающих (у кого они действительно успешно работают) многие годы сварочных инверторов Ресанта. И не жалеют о потраченных деньгах.
Характеристики резака Ресанта:
Питание:220В, 50Гц
Ток на выходе: 15-40А
Рабочий цикл: 40 А- 35% ;
30 А– 60% ;
20А-100%
Максимальные толщины в зависимости от металла:
углеродистые и конструкционные стали до 12 мм
коррозионностойкие стали – до 7 мм
алюминий и его сплавы – до 6мм.
Как видим, чем выше электропроводность металла – тем ниже толщина реза.
svarka-master.ru
Инверторный плазменный резак ИПР-40
Описание
Особенности и преимущества
- Инверторный плазменный резак ИПР 40 Ресанта изготовлен на основе прогрессивных инверторных технологий с применением в схемах IGBT транзисторов, что позволило сделать аппарат не только легким и компактным, но и сократить потребление электроэнергии, существенно повысившее его КПД.
- Агрегат можно использовать для резки черных, цветных металлов, а так же нержавеющей стали.
- Устройство оснащено удобной рукояткой и прочным наплечным ремнем для возможности ручной транспортировки.
- Панель управления резака содержит включатель сети, настройку рабочего тока, контрольный манометр и световые индикаторы – все, что необходимо для настройки полезного процесса.
- Основная часть аппарата оснащена эффективной системой принудительного охлаждения воздухом, что необходимо для обеспечения качественной работы оборудования.
- Автоматическая защита от перегрева не допустит работу элементов агрегата в аварийных условиях при опасных температурах.
- Корпус основной части резака имеет достаточный запас прочности и надежно защищает содержимое.
- Система позволяет производить быструю и точную резку без излишнего перегрева разделенных кромок.
Общее описание
Инверторный плазменный резак Ресанта ИПР 40 используется для ручной резки металлов любого типа и является детищем современных технологий, позволивших приспособить для этого процесса управляемую плазму, которая образуется при сильном нагреве струи воздуха, играющего роль плазменного газа, продуваемого через горящую электрическую дугу. Необходимое давление струи воздуха создается внешним компрессором. В результате этого получился легкий аппарат небольшого размера, выполняющий качественный, точный и быстрый разрез металла без особых усилий со стороны оператора. Питание агрегата происходит от бытовой электросети на 220 В (на передней панели загорается зеленый индикатор).
Плазменная резка стала широко распространенным способом ручной обработки металлов. Не требуется громоздкое и небезопасное оборудование на основе газового топлива и кислорода, система стала легкой, мобильной и компактной. Кроме этого, воздушно-плазменная резка не вызывает температурную деформацию разрезанных краев, не приводит к её отпуску или закалке. Обучение работе на таком оборудовании не требует длительного времени и может быть сведено к небольшому циклу практических занятий. Все эти качества позволили аппарату ручной плазменной резки выйти за рамки строго профессионального использования и значительно расширить область его применения, используя по назначению даже в обычных бытовых условиях.
Обладая возможностью создавать режущий ток силой до 40 А, плазменный резак Ресанта ИПР 40 способен производить резку стали толщиной 12 мм. При этом более вязкая нержавейка позволяет себя резать, только если она имеет толщину до 7-и мм, а алюминий – до 6-и мм. Если вдруг аппарат разогреется до температуры, близкой к опасной, автоматика отключит питание, сохранив работающий вентилятор для более быстрого остывания (на панели управления загорится красный индикатор). Как только температура нормализуется, система автоматически опять готова к эксплуатации (красный индикатор погаснет).
Аппарат оснащен устройством (плазмотроном), создающим непосредственно режущую плазму, которое соединено с корпусом шлангом-кабелем. Клавиша на плазмотроне позволяет зажечь электрическую дугу в ручном режиме, при контакте разрезаемой поверхности с горелкой (на панели управления загорается желтый индикатор). Довольно длинный шнур для электрического подключения делает достаточным радиус действия аппарата, а плавный ручной потенциометр позволяет точно выставлять требуемое значение силы тока.
Применение инверторного процесса преобразования тока в совокупности с IGBT технологиями позволили не только сократить размеры и вес оборудования, но и сделали возможной его работу при нестабильном напряжении питания. Кроме этого, аппарат сравнительно прост в обслуживании и не требует особого ухода.
Устройство и принцип действия
Инверторный плазменный резак Ресанта ИПР 40 выгодно отличается от своих более ранних собратьев сравнительной простотой и удобством. Система не имеет громоздких и опасных баллонов с горючим и окислителем, нет необходимости использовать длинные и тяжелые специальные шланги высокого давления. Все устройство – это небольшой и мало весящий инверторный преобразователь, легко переносимый вручную или при помощи наплечного ремня, а так же ручной плазмотрон в виде пистолета, соединенного с корпусом преобразователя специальным шлангом-кабелем. Корпус изготовлен из стального листа с прорезями для системы охлаждения. Прямоугольная, слегка вытянутая форма корпуса оптимальна в практике, так как позволяет установить устройство на поверхности, а так же делает его удобным при ручной переноске в место использования.
Передняя часть корпуса содержит панель управления, где конструкторы поместили контрольный манометр, клавишу сети, контрольные индикаторы, а так же ручной потенциометр, позволяющий плавно регулировать рабочий ток в диапазоне 15-40 А. Здесь же, на передней панели, расположен шланг-кабель с ручным плазмотроном, а так же клемма для подсоединения кабеля с зажимом, который должен обеспечивать замкнутость цепи.
На задней стенке корпуса находится питающий провод с вилкой для розетки, а так же специальное крепление для монтажа редуктора и подключения шланга от воздушного компрессора.
Основной элемент в корпусе прибора – это специальный трансформатор с инверторной системой преобразования тока до рабочих параметров. В процессе работы такого оборудования выделяется значительное количество теплоты, поэтому, чтобы обезопасить устройство от быстрого перегрева, здесь устроена система принудительного воздушного охлаждения. Электрический вентилятор обдувает нагреваемые поверхности, унося излишки тепла наружу. В случае возникновения нестандартной ситуации вентилятор может не справиться со своей задачей, поэтому автоматика отключит электропитание прибора. После остывания прибор сам восстановит свою работоспособность.
Главный рабочий инструмент плазменного резака – это плазмотрон, то есть устройство, где непосредственно формируется управляемая струя режущей плазмы. Плазма представляет собой ионизированный светящийся газ (в данном случае воздух), который образуется при сильном его нагреве, и способен проводить электрический ток. Изначально, в специальной камере сопла плазмотрона, образуется вспомогательная дежурная электрическая дуга с силой тока до 40 А, которая выдувается наружу струей воздуха. При касании металла эта вспомогательная дуга замыкает цепь, что вызывает розжиг основной режущей дуги. Подача воздуха резко усиливается, и он, от сильного нагрева, превращается в плазму. Объем этого воздуха увеличивается в десятки раз, что приводит к выходу струи из сопла плазмотрона с околозвуковой скоростью. Дежурная дуга при этом отключается. В результате происходит выдувание расплавленного в нужной точке металла и получается точный аккуратный разрез.
Подготовка к работе
Сам ручной плазменный резак Ресанта ИПР 40 является довольно простым устройством. Для непосредственной подготовки его к эксплуатации нет необходимости выполнять какие-либо сложные и трудоемкие операции. Аппарат соединяется шлангом с компрессором, питающий шнур включается в заземленную розетку, кабель массы крепится зажимом к разрезаемому элементу, и система готова к работе. Важно только выполнять все эти операции в полном соответствии с нормами технической инструкции по подготовке и эксплуатации, которая сопровождает комплект поставки.
Если подготовка устройства к работе не вызывает никаких сложностей, то сам процесс резки относится к работам тонким и ответственным. Чтобы получить качественный рез, оператору придется предварительно пройти некоторый курс практической подготовки, чтобы приобрести необходимые базовые навыки.
Учитывая процесс, сопровождающий работу плазменного резака, не лишним будет особо обратить внимание на соблюдение правил пожарной безопасности. Кроме этого, работать с устройством желательно только на открытом пространстве или там, где можно обеспечить достаточный воздухообмен. Оператору необходимо обязательно пользоваться защитной одеждой и обувью, перчатками, а так же средствами защиты органов дыхания и глаз.
resanta24.ru
Аппарат для плазменной резки и сварки: лучшие модели
Плазменные аппараты сварки, резки, пайки приобрели обширное распространение за счет обеспечения возможности выполнения задач с высокой эффективностью в короткие сроки. При помощи них можно работать практически с любым металлом и электропроводящими материалами.
Аппарат для плазменной резки и сварки: описание
Резка происходит путем плавления и смешения металла с высокотемпературной плазмой, которая создается электрической дугой из инертного вещества. Так, в устройстве атмосферный ионизированный воздух направляется через отверстие в горелке под давлением в необходимом количестве и переводится в состояние плазмы.
Итоговый результат и эффективность могут быть улучшены при использовании нескольких видов инертного газа, что особенно актуально для цветных металлов. Именно поэтому стоит проявить внимательность при подборе устройств и учесть все параметры.
Выбор
Аппарат для плазменной резки и сварки подходит для обработки тугоплавких, цветных металлов (алюминия, меди), черного метала (чугун, нержавеющая сталь и варианты с различным легированием), а также других типов материалов. Сегодня в магазинах представлен обширный ассортимент инструментов, для выбора оптимального варианта необходимо определиться с имеющимися задачами и условиями эксплуатации. После этого производится выбор из подходящих моделей.
Главным критерием являются материалы, с которыми может работать устройство. Рекомендуется выбирать агрегат с широким набором функций и возможностью резки различных металлов. При этом нужно отметить, что стоимость напрямую зависит от функционала и известности марки. Также нужно обратить внимание на размеры толщины резки. Чаще всего данный параметр указывается для листов из стали, реже всего можно встретить обозначение для нержавейки. По этой информации можно понять возможности резки различных вариантов.
Поджиг дуги
Все модели объединены идентичной схемой работы и общим конструктивным исполнением, при этом данные параметры одинаковы у любых изготовителей. Различие заключается в способе поджига дуги, здесь возможны следующие варианты:
- Включение пилотной дуги возбуждает плоскость основного элемента. То есть вначале приводится в действие пилотная дуга с низкой мощностью, которая находится на дополнительном контуре плазмотрона. При помощи сжатого воздуха образуется дуга, она замыкается на плоскости материала, тем самым формируя главную дугу. Аппарат для плазменной резки и сварки с подобным методом поджига является оптимальным вариантом для работ с металлической обрешеткой и сеткой.
- Возбуждение с высокой частотностью. В этом случае формирование дуги происходит только при условии электрического разряда между головкой плазмотрона и листом материала. Такая методика сегодня является наиболее распространенной.
- Контактный поджиг. Дуга возникает при соприкосновении с заготовкой. Чаще всего можно встретить на приспособлениях бюджетной категории, отличающихся небольшой силой тока. Они характеризуются быстрым износом сопла плазматрона и других его деталей. В настоящее время изготовители все чаще устанавливают другие варианты поджига.
Принимая в расчет информацию, указанную выше, будет проще определиться с желаемой моделью и не ошибиться с имеющимися свойствами.
Преимущества и недостатки
Аппарат для плазменной резки и сварки, фото которого представлено выше, обладает множеством положительных сторон, среди которых стоит отметить следующие:
- Качество резки характеризуется высокой точностью и аккуратностью. Даже при наличии небольшого опыта соответствующих работ легко предотвратить такие недочеты, как наплывы и грат на обрабатываемых поверхностях.
- Безопасность. Вероятность возгорания сводится к минимуму при отсутствии взрывоопасных и воспламеняемых газов. Аналогичные характеристики способен обеспечить лишь дуговой ручной метод.
- Отсутствие деформации листов, волн и трещин на металлических поверхностях.
Некоторые устройства отличаются достаточно высокой стоимостью, что является единственным недостатком. При этом всегда можно постараться подобрать вариант с подходящей ценой и необходимыми характеристиками. Для осуществления резки в домашних условиях будет вполне достаточно агрегата со средними мощностными характеристиками.
“Горынычъ”
Устройство “Горынычъ” - аппарат плазменной сварки и резки российского производства подходит для работ, связанных с высокотемпературным воздействием. Возможно использование как для металлов, так и для других категорий материалов, не подверженных горению. Он представляет собой электродуговой генератор плазмы, образуемой при нагреве электронной дуги. Испарения рабочего состава, доходя до температуры ионизации, выводятся плазменной струей под давлением. В качестве рабочей жидкости может выступать этиловый спирт или вода, выбор того или иного варианта осуществляется в соответствии с поставленными задачами. Струя при этом имеет температуру в пределах 6000 градусов. Главными элементами аппарата являются блок управления и плазменный генератор.
“Горынычъ”, аппарат плазменной сварки и резки, отзывы в основном получает положительные. Многие пользователи отмечают его высокую скорость работы и многофункциональность.
“Сварог CUT 40 B”
Устройство отличается небольшим весом и компактными габаритами, его главное предназначение заключается в обработке тонких материалов. Оно создано на основе инверторной схемы и специальных транзисторов. Агрегат оснащается евроразъемом для горелки и удобной панелью управления. В процессе работ не возникает деформация материала, при этом желательно резать листы с толщиной в пределах 0,12 см.
Он имеет следующий принцип работы: ток подходит к электроду плазмотрона, сам плазменный факел поджигается осциллятором с высокой частотностью после нажатия на кнопку.
Достоинства:
- отсутствие возможности опрокидывания благодаря достаточной устойчивости;
- экономичность;
- низкая стоимость;
- нет необходимости в создании определенных условий работ;
- интуитивно понятное управление;
- удобная перевозка за счет специальной рукояти и небольшой массы.
Среди недостатков стоит отметить невысокий ресурс плазматронного устройства.
Rilon CUT 40
Данный агрегат, так же, как и аппарат плазменной сварки, резки металла “Горынычъ”, позволяет работать с любыми типами токопроводящих основ: это различные сплавы, оцинкованная сталь, алюминий, медь. Бесконтактный поджиг работает на высокочастотном управлении. Возможно использование для материалов с толщиной около 20 мм, благодаря высокому уровню режущего тока. Степень воздействия зависит от толщины заготовки и характеристик металла. При помощи цифрового индикатора устанавливаются необходимые критерии.
Достоинства:
- используется в широком диапазоне температур;
- обеспечивает обработку любых сплавов и материалов;
- основан на современной технологии;
- отличается высокой скоростью резки и качественным формированием шва;
- не возникает деформация заготовки.
Стоит отметить, что устройство не подходит для промышленных условий и активного использования.
BRIMA CUT-120
Аппарат для плазменной резки и сварки отличается небольшой массой основного трансформатора и компактными размерами, при этом он оптимально подходит для использования при демонтаже металлических конструкций. Применяется для работ с медью, цветным металлом, углеродистой и нержавеющей сталью с толщиной не более 35 мм. Состоит из газового редуктора, обратного силового провода и воздушного рукава.
Достоинства:
- экономичность;
- постепенное изменение основных параметров процесса;
- качественное отведение тепла благодаря наличию множества отверстий в корпусе;
- возможность регулировки дуги;
- эффективная резка материала;
- легкая и чистая обработка металлических элементов с большой толщиной;
- высокая скорость проведения работ.
FUBAG PLASMA 40
Аппарат для плазменной резки и сварки подходит для любых токопроводящих материалов с толщиной не более 12 мм. Расходные элементы, такие как катод и сопло, отличаются длительным периодом использования. Поджиг дуги имеет высокочастотное управление.
Положительные стороны:
- обеспечивает быструю резку заготовок;
- возможно подключение к стандартной сети 220 В, благодаря чему расширяется область использования и упрощается эксплуатация;
- достаточно надежный резак;
- образуется качественный шов без наплывов.
fb.ru
Плазморез своими руками из инверторной сварки
Резка листового металла плазмой обычно применяется на крупных производствах для изготовления сложных по конфигурации деталей. Резать на промышленных станках можно любые металлы — сталь обычную и нержавеющую, алюминий, медь, латунь, сверхтвердые сплавы. Плазморез своими руками сделать тоже можно, причем вполне работоспособную конструкцию, правда с несколько ограниченными возможностями.
Для крупносерийного производства она будет непригодна, но вырезать несколько деталей в слесарной мастерской, металлообрабатывающем цехе или в домашних условиях, в гараже, например, всегда получится. При этом по сложности конфигурации и твердости обрабатываемого металла ограничений практически нет. Ограничения касаются толщины металла, размеров листа и скорости резания.
Что нужно для плазмореза
Проще всего построить плазменный аппарат для резки на базе инверторного сварочного аппарата. Плазморез своими руками из инвертора отличается относительно простой конструкцией, работоспособностью, доступностью основных узлов и деталей. Которые нет возможности купить, можно сделать самостоятельно в условиях мастерской средней оснащенности оборудованием.
Самодельный аппарат плазменной резки не оборудуется ЧПУ — в этом его недостаток и преимущество. Недостаток состоит в том, что сложно изготовить две абсолютно точные детали при управлении вручную. Даже мелкие серии заготовок будут в чем-то отличаться.
Преимущество же состоит в том, что один из самых дорогостоящих узлов не придется покупать. Сделать его под силу не каждому инженеру высшей квалификации, а собирать из готовых узлов — то же, что покупать новое устройство. Для мобильного резака ЧПУ не нужно, в силу других задач, которые он выполняет.
Главными составными частями самодельного плазмореза являются:
- источник постоянного тока;
- плазмотрон;
- осциллятор
- компрессор или баллон со сжатым газом;
- шланги подключения;
- кабеля питания.
Как видно, ничего особо сложного в состав аппарата не входит. Но сложности начинаются при ближайшем рассмотрении характеристик того или иного узла.
Источник тока
Особенности плазменной резки требуют, чтобы сила тока находилась по меньшей мере на уровне сварочного аппарата средней мощности. Такой ток вырабатывается обычным сварочным трансформатором и инверторным аппаратом. В первом случае установка получится условно мобильной — большой вес и габариты трансформатора затруднит ее перемещение. В сочетании с баллоном для сжатого газа или компрессором система получится довольно громоздкой.
Кроме того, трансформаторы отличаются невысоким КПД, что приведет к повышенному расходу электроэнергии при резке металла. Схема с использованием инвертора несколько проще и удобнее в эксплуатации, как и выгоднее по затратам энергии. Из сварочного инвертора получится довольно компактный плазморез, который без труда справиться с резкой металла толщиной до 25-30 мм. Именно для таких толщин применяются и промышленные установки. Плазменный резак на трансформаторе сможет обрабатывать более толстые заготовки, но это требуется реже. Все преимущества плазменной резки проявляются именно на тонких и сверхтонких листах. Это:
- точность линии;
- гладкость кромок;
- отсутствие брызг металла;
- нет перегретых зон вблизи места взаимодействия дуги и металла.
Самодельный плазморез собирается на базе любого инверторного аппарата для сварки. Количество режимов работы не имеет значения — нужен только постоянный ток силой более 30А.
Плазмотрон
Второй по важности элемент плазмореза. Рассмотрим коротко принцип его работы. Плазменный резак состоит из двух электродов, один из которых, основной, сделан из тугоплавкого металла, вторым является сопло. Обычно его делают из меди. Катодом служит основной электрод, анодом сопло, а при работе — обрабатываемая токопроводящая деталь.
В данном случае мы рассматриваем плазмотрон прямого действия для резки металлов. Дуга возникает между резаком и обрабатываемой деталью. Существуют еще плазмотроны косвенного действия, которые режут плазменной струей, но о них будет сказано ниже. Плазморез из инвертора рассчитан на прямое действие.
Кроме электрода и сопла, которые являются расходными материалами и могут заменяться по мере износа, в корпусе плазмотрона есть изолятор, разделяющий катодный и анодный узлы и небольшая камера, в которой подаваемый газ завихрятся. В сопле конической или полусферической сделано тонкое отверстие, сквозь которое вырывается раскаленный до температуры 5000-3000 0С газ.
Плазмотрон прямого действия
Подается в камеру газ из баллона или от компрессора по шлангу, совмещенному с кабелями питания, которые образуют шлангово-кабельный пакет. Они соединены в одном изоляционном рукаве, или соединены в виде жгута. Газ поступает в камеру через прямой патрубок, расположенный сверху или сбоку вихревой камеры, которая нужна, чтобы рабочая среда перемещалась только в одну сторону.
Как работает плазмотрон
Газ, поступая под давлением в пространство между соплом (анодом) и электродом (катодом) спокойно проходит в рабочее отверстие и уходит в атмосферу. При включении осциллятора, устройства вырабатывающего импульсный высокочастотный ток, между электродами возникает дуга, которая называется предварительной и нагревает газ, находящийся в ограниченном пространстве камеры сгорания. Температура нагрева столь высока, что он переходит в другой вид физического состояния — плазму.
Этот вид материального состояния отличается тем, что практически все атомы ионизированы, то есть электрически заряженные. Кроме того, давление в камере резко возрастает и газ вырывается наружу в виде раскаленной струи. При поднесении плазмотрона к детали, возникает вторая дуга, более мощная. Если сила тока от осциллятора равна 30-60 А, то рабочая дуга возникает при 180-200 А.
Эта дуга дополнительно разогревает газ, которые разгоняется под действием электрических сил до чрезвычайно высокой скорости — до 1500 м/с. Комбинированное действие высокой температуры плазмы и скорости движения разрезает металл по очень тонкой линии. Толщина разреза зависит от свойств сопла.
По-другому работает плазмотрон косвенного действия, в нем в качестве основного анода выступает сопло. Из резака вырывается не дуга, а поток плазмы — струя, которая и режет не токопроводящие вещества. Оборудование-самоделка с такими плазмотронами работает очень редко.
Из–за сложности устройства плазмотрона и тончайших настроек изготовить его практически невозможно самостоятельно, несмотря на простые чертежи, которые есть в интернете. Он работает под высокими давлениями и температурами и становится попросту опасным, если что-то сделать не так. Плазморез по чертежам своими руками можно собрать из готовых деталей, которые продаются в магазинах сварочного оборудования. Но, как и большинство машин и механизмов, сборка из комплектующих стоит дороже, чем готовый резак в сборе.
Осциллятор
Это своеобразный стартер, служащий для запуска предварительной дуги. Для разбирающихся в электронике схема его несложна. Функциональная схема выглядит так:
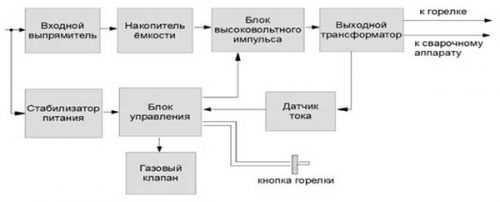
Функциональная схема осциллятора
А электрическая примерно так (один из вариантов):
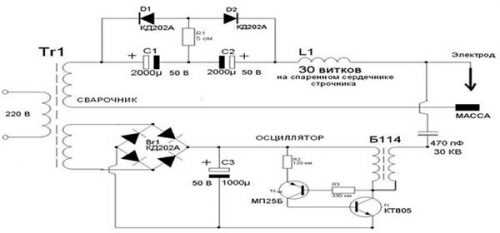
Электрическая схема осциллятора
Как выглядит и работает самодельный осциллятор видно на видео. Если сборкой электросхем и поиском деталей нет времени заниматься, воспользуйтесь осцилляторами заводского изготовления, например ВСД-02. Его характеристики лучше всего подходят для работы с инвертором. Подсоединяется осциллятор в схему питания плазмотрона параллельно или последовательно, в зависимости от требований инструкции конкретного прибора.
Рабочий газ
Перед тем, как сделать плазморез, следует очертить предварительную сферу его применения. Если вы собираетесь работать только с черными металлами, то обойтись можно только компрессором. Для меди, титана и латуни потребуется азот, а резка алюминия происходит в смеси азота с водородом. Высоколегированные стали режутся в аргоновой атмосфере. В этом случае аппарат рассчитывается еще и под сжатый газ.
Сборка устройства
Ввиду достаточной сложности и многочисленности компонентов аппарата плазменной резки, его трудно разместить в переносном корпусе или ящике. Лучше всего использовать складскую тележку для перевозки товаров. На ней можно компактно расположить инвертор, баллоны или компрессор, кабельно-шланговую группу. В пределах цеха или мастерской перемещать их очень легко. Если потребуется выезд на другой объект, то все можно загрузить в прицеп легкового автомобиля.
wikimetall.ru
Инверторный плазменный резак ИПР-40К
Описание
Особенности и преимущества
- Инверторный плазменный резак ИПР 40К Ресанта изготовлен на основе прогрессивных инверторных технологий с применением в схемах IGBT транзисторов, что позволило сделать аппарат не только легким и компактным, но и сократить потребление электроэнергии, существенно повысившее его КПД.
- Агрегат можно использовать для резки черных, цветных металлов, а так же нержавеющей стали.
- Устройство оснащено удобной рукояткой и прочным наплечным ремнем для возможности ручной транспортировки.
- Панель управления резака содержит включатель сети, настройку рабочего тока, контрольный манометр и световые индикаторы – все, что необходимо для настройки полезного процесса.
- Основная часть аппарата оснащена эффективной системой принудительного охлаждения воздухом, что необходимо для обеспечения качественной работы оборудования.
- Автоматическая защита от перегрева не допустит работу элементов агрегата в аварийных условиях при опасных температурах.
- Корпус основной части резака имеет достаточный запас прочности и надежно защищает содержимое.
- Система позволяет производить быструю и точную резку без излишнего перегрева разделенных кромок.
Общее описание
Инверторный плазменный резак Ресанта ИПР 40К используется для ручной резки металлов любого типа и является детищем современных технологий, позволивших приспособить для этого процесса управляемую плазму, которая образуется при сильном нагреве струи воздуха, играющего роль плазменного газа, продуваемого через горящую электрическую дугу. Необходимое давление струи воздуха создается внешним компрессором. В результате этого получился легкий аппарат небольшого размера, выполняющий качественный, точный и быстрый разрез металла без особых усилий со стороны оператора. Питание агрегата происходит от бытовой электросети на 220 В (на передней панели загорается зеленый индикатор).
Плазменная резка стала широко распространенным способом ручной обработки металлов. Не требуется громоздкое и небезопасное оборудование на основе газового топлива и кислорода, система стала легкой, мобильной и компактной. Кроме этого, воздушно-плазменная резка не вызывает температурную деформацию разрезанных краев, не приводит к её отпуску или закалке. Обучение работе на таком оборудовании не требует длительного времени и может быть сведено к небольшому циклу практических занятий. Все эти качества позволили аппарату ручной плазменной резки выйти за рамки строго профессионального использования и значительно расширить область его применения, используя по назначению даже в обычных бытовых условиях.
Обладая возможностью создавать режущий ток силой до 40 А, плазменный резак Ресанта ИПР 40К способен производить резку стали толщиной 12 мм. При этом более вязкая нержавейка позволяет себя резать, только если она имеет толщину до 7-и мм, а алюминий – до 6-и мм. Если вдруг аппарат разогреется до температуры, близкой к опасной, автоматика отключит питание, сохранив работающий вентилятор для более быстрого остывания (на панели управления загорится красный индикатор). Как только температура нормализуется, система автоматически опять готова к эксплуатации (красный индикатор погаснет).
Аппарат оснащен устройством (плазмотроном), создающим непосредственно режущую плазму, которое соединено с корпусом шлангом-кабелем. Клавиша на плазмотроне позволяет зажечь электрическую дугу в ручном режиме, при контакте разрезаемой поверхности с горелкой (на панели управления загорается желтый индикатор). Довольно длинный шнур для электрического подключения делает достаточным радиус действия аппарата, а плавный ручной потенциометр позволяет точно выставлять требуемое значение силы тока.
Применение инверторного процесса преобразования тока в совокупности с IGBT технологиями позволили не только сократить размеры и вес оборудования, но и сделали возможной его работу при нестабильном напряжении питания. Кроме этого, аппарат сравнительно прост в обслуживании и не требует особого ухода.
Устройство и принцип действия
Инверторный плазменный резак Ресанта ИПР 40К выгодно отличается от своих более ранних собратьев сравнительной простотой и удобством. Система не имеет громоздких и опасных баллонов с горючим и окислителем, нет необходимости использовать длинные и тяжелые специальные шланги высокого давления. Все устройство – это небольшой и мало весящий инверторный преобразователь, легко переносимый вручную или при помощи наплечного ремня, а так же ручной плазмотрон в виде пистолета, соединенного с корпусом преобразователя специальным шлангом-кабелем. Корпус изготовлен из стального листа с прорезями для системы охлаждения. Прямоугольная, слегка вытянутая форма корпуса оптимальна в практике, так как позволяет установить устройство на поверхности, а так же делает его удобным при ручной переноске в место использования.
Передняя часть корпуса содержит панель управления, где конструкторы поместили контрольный манометр, клавишу сети, контрольные индикаторы, а так же ручной потенциометр, позволяющий плавно регулировать рабочий ток в диапазоне 15-40 А. Здесь же, на передней панели, расположен шланг-кабель с ручным плазмотроном, а так же клемма для подсоединения кабеля с зажимом, который должен обеспечивать замкнутость цепи.
На задней стенке корпуса находится питающий провод с вилкой для розетки, а так же специальное крепление для монтажа редуктора и подключения шланга от воздушного компрессора.
Основной элемент в корпусе прибора – это специальный трансформатор с инверторной системой преобразования тока до рабочих параметров. В процессе работы такого оборудования выделяется значительное количество теплоты, поэтому, чтобы обезопасить устройство от быстрого перегрева, здесь устроена система принудительного воздушного охлаждения. Электрический вентилятор обдувает нагреваемые поверхности, унося излишки тепла наружу. В случае возникновения нестандартной ситуации вентилятор может не справиться со своей задачей, поэтому автоматика отключит электропитание прибора. После остывания прибор сам восстановит свою работоспособность.
Главный рабочий инструмент плазменного резака – это плазмотрон, то есть устройство, где непосредственно формируется управляемая струя режущей плазмы. Плазма представляет собой ионизированный светящийся газ (в данном случае воздух), который образуется при сильном его нагреве, и способен проводить электрический ток. Изначально, в специальной камере сопла плазмотрона, образуется вспомогательная дежурная электрическая дуга с силой тока до 40 А, которая выдувается наружу струей воздуха. При касании металла эта вспомогательная дуга замыкает цепь, что вызывает розжиг основной режущей дуги. Подача воздуха резко усиливается, и он, от сильного нагрева, превращается в плазму. Объем этого воздуха увеличивается в десятки раз, что приводит к выходу струи из сопла плазмотрона с околозвуковой скоростью. Дежурная дуга при этом отключается. В результате происходит выдувание расплавленного в нужной точке металла и получается точный аккуратный разрез.
Подготовка к работе
Сам ручной плазменный резак Ресанта ИПР 40К является довольно простым устройством. Для непосредственной подготовки его к эксплуатации нет необходимости выполнять какие-либо сложные и трудоемкие операции. Аппарат соединяется шлангом с компрессором, питающий шнур включается в заземленную розетку, кабель массы крепится зажимом к разрезаемому элементу, и система готова к работе. Важно только выполнять все эти операции в полном соответствии с нормами технической инструкции по подготовке и эксплуатации, которая сопровождает комплект поставки.
Если подготовка устройства к работе не вызывает никаких сложностей, то сам процесс резки относится к работам тонким и ответственным. Чтобы получить качественный рез, оператору придется предварительно пройти некоторый курс практической подготовки, чтобы приобрести необходимые базовые навыки.
Учитывая процесс, сопровождающий работу плазменного резака, не лишним будет особо обратить внимание на соблюдение правил пожарной безопасности. Кроме этого, работать с устройством желательно только на открытом пространстве или там, где можно обеспечить достаточный воздухообмен. Оператору необходимо обязательно пользоваться защитной одеждой и обувью, перчатками, а так же средствами защиты органов дыхания и глаз.
resanta24.ru