Изготовление матриц для передних крыльев. Изготовление кузовных деталей из металла своими руками
Способ изготовления деталей кузова автомобиля
Использование: в способах изготовления деталей автомобиля, а конкретнее - в способах изготовления деталей кузова автомобиля, и может найти применение в автомобильной промышленности. Сущность изобретения: способ включает вырезку заготовки из металлического листа, последующую ее обработку на матрице. Согласно изобретению при вырезке заготовки в планируемых местах сопряжения трех поверхностей вырезают сегменты, вершины которых располагают в планируемых точках сопряжения указанных поверхностей, а ограничивающие сегменты края выполняют таким образом, что они совпадают при последующей обработке заготовки. Затем закрепляют заготовку на матрице, обжимают планируемые места сопряжения трех поверхностей. После этого сваривают ограничивающие сегменты края и обжимают остальные части поверхностей заготовки. 1 з. п. ф-лы, 6 ил.
Изобретение относится к способам изготовления деталей автомобиля, конкретно к способам изготовления деталей кузова автомобиля, и может быть использовано в автомобильной промышленности.
www.findpatent.ru
Изготовление матриц для передних крыльев
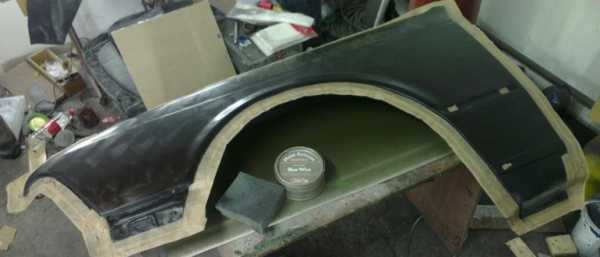
На данный момент все популярнее становится тюнинг и облегчение кузова автомобиля. Так же если вы обладаете достаточно старым автомобилем, то некоторые фрагменты кузова очень сложно достать, или же они будут стоить просто баснословные суммы денег. На первый взгляд, это является очень затратной частью, но ничего страшного в этом нет, ведь вы всегда можете сделать не большой custom своими руками.
Мы расскажем с помощью чего, можно сделать при минимальных затратах новые передние крылья не уступающие по прочности заводским аналогам.
С чего же начать?
- Первым этапом в постройке матрицы передних крыльев является выведение первоначальной формы крыла. Если есть неровности, вмятины, проржавевшие места, все это необходимо выровнять, за шпаклевать, и вышкурить, добиться максимального эффекта к заводским параметрам.
- Обклеиваем окантовку металлическим скотчем или плотным картоном
- Наносим втирая на нашу поверхность воск с помощью губки (данный этап проводится в 3-4 слоя с промежутком высыхания 1 час)
- После высыхания последнего слоя накладываем матричный гелькоут(наносится в 2 слоя с промежутком 20-25 минут. После чего необходимо отстоятся 4 часа для полного высыхания)
- Наносим слой стекловуали(тщательно укладываем и промазываем все неровности,впадины и изгибы что бы не образовалось пористого места)
- Наносим 2 слоя стекломата 300 с промежутком слоя 1 час и затем 600 с промежутком слоя 1 час. Даем высохнуть 5-6 часов.
- Что бы предать матрице более плотную форму и избежать деформации или поломки самой матрицы, необходимо сделать каркас жесткости. Для использования каркаса можно использовать деревянные доски
- Подгоняем доски под наше крыло,скручиваем саморезами для прочности и заливаем несколькими слоями с промежутком 1 час стекломат 600
После чего даем пару дней полностью высохнуть изделию.
- После высыхания, обрезаем лишние края и аккуратно извлекаем деталь из матрицы.
Матрица передних крыльев готова
Источник: DRIVE2
Понравилась статья? Поделить с друзьями:
avtosovet.info
Изготовление кузовных деталей | Изготовление деталей по чертежам от 1 детали до серий
Обращаясь в компанию Zavod-Detalej.ru вы обращаетесь к опытным специалистам занимающиеся изготовлением кузовных деталей. Мы в кротчайшие сроки произведем любые запчасти для кузовных автомобилей с учетом индивидуальных предпочтений.
Элементы деталей кузовов
Самым большим элементом каждого автомобиля считается его кузовная часть, она в большей степени устанавливает ключевые потребительские качества транспортных средств. Кузовная часть не является основным элементом конструкции, тем не менее, к его технологическим параметрам предъявляют довольно высокие требования, потому что, от качества изготовления кузова зависит несколько факторов:
- скорость машины;
- безопасность водителей и пассажиров;
- удобство;
- эстетические качества автомобиля.
Многие водители иногда сталкиваются с такого рода неприятностью, как повреждение кузовной части машины. Кроме деталей кузовов, мы предлагаем и изготовление деталей по образцу. Порча кузова полностью либо его единичных элементов, в основном наступает вследствие ДТП, некорректного использования автомобиля, хулиганских действий и других причин.
В отдельных случаях ремонт уже может не быть выходом из ситуации (возобновление геометрии кузовной части технически невозможен или экономически невыгоден) и необходима целостная замена элементов кузова.
Пришлите ваши чертежи или эскизы на [email protected]
Либо звоните 8-800-250-88-72. Доставка по России и СНГ!!!
Профессиональные сотрудники нашей компании помогут вам в подборе идеального варианта применения тех или иных элементов кузова вашего авто. Во многом благодаря современному техническому оборудованию, мы можем производить кузовные запчасти практически для всех автомобильных марок. Наши специалисты в короткие сроки и качественно произведут любые детали кузовной части из полимерного или металлического сырья:
- крыло,
- капот,
- крыша,
- двери,
- порог,
- обвес,
- бампер,
- радиаторные решетки,
- спойлеры и т.д.
Если вы желаете, то возможно изготовление кузовных деталей с измененными размерами и формой, а также создание обновленного кузовного дизайна.
Кузовные части автомобиля
Кузовная часть автомобиля – это один из основных составных. Обычно детали кузова производятся из высококачественной стали углеродистой. Даже имея незначительную толщину листа, они отличаются высокой прочностью, но повышенная влажность и дефекты могут приводить к образованию коррозии. Дорожно-транспортные происшествия также могут грозить куда более серьёзными проблемами.
Пришлите ваши чертежи или эскизы на [email protected]
Либо звоните 8-800-250-88-72. Доставка по России и СНГ!!!
В таких случаях необходима замена элементов, геометрическую форму которых восстановить не удается. В этом случае применяют специализированное оснащение, которое и помогает при изготовлении деталей трубопроводов и других изделий из металла. Нельзя обойтись и без фрезировальных, сверлильных, лентопилочных, шлифовальных установок. В период их подбора необходимо сосредоточить внимание на их качестве и кто производитель. Компания Zavod-Detalej.ru предлагает наилучшую технику, германские токарные станки обработки металла, которые обеспечивают выполнение множества технических процессов. За это время достигается необходимая степень безопасности, разгон скорости, первоначальная внешняя привлекательность облика запчастей, уют.
Кузовные элементы обязаны быть очень прочными. Важно также учитывать их лёгкость в производстве. В связи с этим применяют лиственную легированную. Недочетом этого материала считается высокая подверженность коррозии. Поэтому, после их штамповки и всех необходимых процедур проводят оцинковку. Чаще применяют специальный грунт. Перед его нанесением поверхность обрабатывают антижировым щелочным раствором. Затем наносят грунтовку, и деталь отправляют на сушку.
Алюминий же не имеет таких недостатков, именно поэтому потихоньку выталкивает сталь. Нельзя не сказать о лёгкости этого материала. Кузовная часть, изготовленная из алюминия, будет весить много меньше. Но также есть и другие особенности:
- низкая шумоизоляция,
- стоимость.
Для того чтобы избавиться от сторонних звуков и вибрации во время передвижения, необходима дополнительная шумоизоляция и качественное изготовление кузовных деталей. Ремонт таких элементов, производится с применением специализированного оборудования.
zavod-detalej.ru
Как сделать автомобиль своими руками
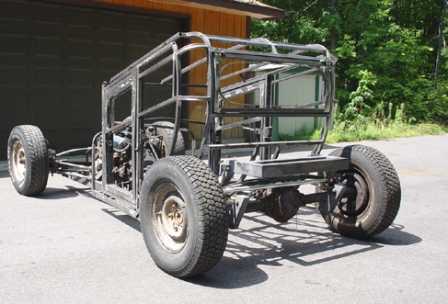
Содержание:
Желание сделать автомобиль своими руками возникает от вдохновения и мотивации. Это может быть дорогой спортивный автомобиль, который Вы не можете себе позволить купить, либо желание создать автомобиль с собственным дизайном. Есть несколько способов реализовать свою мечту. В этой статье я расскажу о том, как сделать автомобиль своими руками. Рассмотрим как создаётся макет-основа для формовки кузова, способы изготовления кузова автомобиля, а также как можно собрать автомобиль своими руками из готового набора (kit-car).
Что нужно уметь, чтобы сделать автомобиль своими руками?
Процесс создания автомобиля своими руками нельзя назвать простым. Даже известные автопроизводители иногда допускают ошибки в расчётах и сборке автомобилей. Тем не менее, если есть большое желание и умение работать руками, то, используя доступные материалы и инструменты, можно сделать автомобиль самостоятельно. Кроме всего прочего, для этого требуется сильная воля и упорство, тогда можно получить впечатляющие результаты.
Базовые знания и навыки, которые необходимы это: понимание устройства автомобиля, умение работать с металлом, стекловолокном и шпаклёвкой, умение пользоваться сварочным аппаратом, базовые знания электрики автомобиля.
Некоторым вещам, которые Вы не умеете делать, придётся научиться в процессе создания автомобиля. Многое можно изучить из руководств и информации из Интернета. На этом сайте есть статьи об автомобилях, созданных любителями, не обладающих большим опытом и обучавшихся всему в процессе постройки самодельной машины. Вот два примера: статья “о создании драгстера, стилизованного под Ferrari Enzo” и вторая статья “о создании автомобиля Scorpione”. Иногда будет разумно прибегнуть к помощи специалистов. Подумайте, что Вы сможете сделать сами, а для какого этапа лучше привлечь другого мастера. Многим хочется думать, что они первоклассные мастера на все руки и всё смогут сделать самостоятельно, без привлечения помощи. Это, порой, является причиной, почему проект затягивается на слишком долгое время. Ведь то, что может сделать опытный профессионал за день, любитель может провозиться неделю, а то и дольше. К примеру, если Вы не умеете красить, то можно самому подготовить кузов к покраске, а на саму покраску отвезти машину к маляру. Либо обтягивание салона обивочным материалом можно доверить специалистам в этом деле. Таким образом, общий процесс создания автомобиля не будет казаться нереальным.
Мастерская и инструменты
Нужно располагать тёплой мастерской с достаточным свободным пространством.
Изготовление автомобиля своими руками требует наличия необходимых инструментов. Специальные инструменты и станки позволяют сделать работу быстрее и проще, но без них можно обойтись.
Вот основные необходимые инструменты, которые нужны при создании автомобиля своими руками:
- Необходимо иметь хороший верстак с большими тисками.
- Полный набор ручных инструментов
- Дрель, а лучше установку для вертикального сверления
- Болгарка
- Сварочный аппарат (лучше полуавтомат)
- Компрессор. Для покраски и для функционирования пневмоинструментов.
- Краскопульт
- Зажимы разных размеров (для крепления деталей перед сваркой)
- Киянки разных размеров и форм, молотки и поддержки для формовки металла (в случае создания кузова из листового металла).
- Станок «английское колесо» и листогибочный станок (для более лёгкой формовки листового металла). Как уже упоминалось ранее, без этих станков, молотков и киянок можно обойтись, даже если делать кузов из листового металла. Разные методики создания кузова мы рассмотрим в этой статье ниже.
Как самому сделать автомобиль с нуля?
Изготовление автомобиля с нуля предполагает создание всех его компонентов и правильная их компоновка. Это очень непростой процесс и может затянуться на неопределённо долгое время. К примеру, американец Кен Имхофф делая копию автомобиля Lamborghini Countach, максимально приближенную к оригиналу, изготавливал практически всё с нуля, даже колёсные диски. Будучи профессиональным формовщиком металла, он потратил 17 лет, чтобы полностью завершить проект. В интервью он признался, что это было не выгодное занятие и было для него как интересная игра. Чаще всего, при создании автомобиля своими руками, в качестве основы берётся существующий серийный автомобиль и переделывается. Это самый реальный путь сделать автомобиль своими руками – сделать самостоятельно каркас, кузов и интерьер, а все остальные компоненты взять готовыми, у другого автомобиля или нескольких автомобилей. Точно также делают небольшие производители автомобилей по всему миру в последние 50 лет или больше.
Нужно обзавестись необходимыми руководствами по автомобилю, который будет использоваться в качестве донора, чтобы понимать устройство всех его узлов (двигателя, рулевого управления, подвески, тормозной системы, электрики).
Создание собственного дизайна кузова
Многие автолюбители мечтают об обладании одного единственного автомобиля с необычным дизайном, автомобилем своей мечты. Можно спроектировать и сделать такой автомобиль самостоятельно. Начало планирования дизайна и строительства автомобиля начинается с идеи. Дизайн может быть индивидуальным, либо комбинировать в себе существующие формы, взятые с других автомобилей. К примеру, это может быть передняя часть, похожая на одну машину, а задняя — на другую. Когда образ вашего автомобиля будет придуман, то его нужно нарисовать. Существует множество графических компьютерных программ, которые помогут спланировать и спроектировать автомобиль. Решив, как будет выглядеть ваш автомобиль, нужно понять, какая колёсная база под него подойдёт. Нужно выбрать донора, похожего по параметрам, чтобы колёсная база соответствовала, или же её нужно будет изменить.
Изготовление полномасштабного макета-основы для создания кузова
Для создания кузова нужно сделать макет-основу. По этой основе можно будет подгонять листовой металл (формуется станком “английское колесо” или молотками и киянками и на каждом этапе прикладывается к макету), либо сформовать стекловолокно, пропитанное полиэфирной смолой. После формовки кузова, макет-основа никак не участвует в конструкции автомобиля, а готовые панели крепятся к структурным элементам конструкции автомобиля.
Для проектирования может использоваться компьютер (программа CAD или Alias) с дальнейшей распечаткой полномасштабных чертежей на плоттере. Существуют и уже готовые шаблоны популярных автомобилей в электронном виде, которые можно купить или найти в свободном доступе в интернете. Также есть американские компании, которые могут изготовить шаблоны для макета-основы любого автомобиля на заказ.
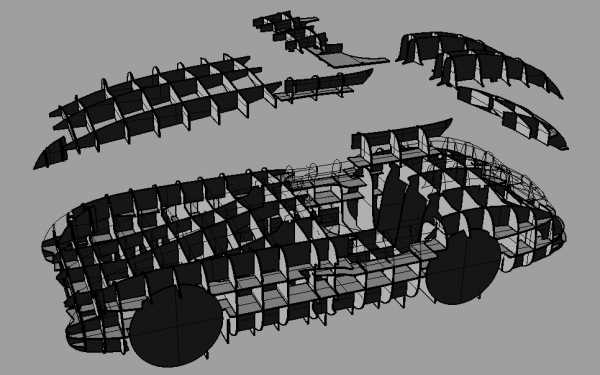
Можно использовать и старый метод создания макета-основы, без применения компьютера. В нём есть свои преимущества. Старый метод создания макета-основы применялся кузовостроителями много лет. Для этого должен быть нарисован рисунок всех сторон автомобиля (см. иллюстрацию) со шкалой, которая расчерчена на квадраты.
В переводе на реальный размер, расстояние между линиями составляет 10 дюймов (25 см). По квадратам будет проще контролировать размер и форму при изготовлении макета. Далее, чтобы получить трёхмерную модель рисунков, нужно сделать маленький макет автомобиля. Макет можно сделать из глины для лепки или пластилина. Во время работы с глиной, Вы, приближаясь к финальной форме, скорее всего, многое измените в дизайне. Так происходит, потому что модель предстаёт перед Вами в другой перспективе. После изменений в дизайне, нужно внести изменения в чертёж.
Далее слепленная модель разрезается на поперечные сегменты, которые очерчиваются по контуру (см. фото), и по ним изготавливаются шаблоны из картона. Так как обе стороны автомобиля симметричные, то шаблоны на вторую сторону можно делать только по одной стороне. Каждый шаблон должен быть пронумерован в соответствии с его расположением.
Следующим шагом нужно увеличить эти шаблоны до полного размера. Для увеличения и переноса на бумагу используется проектор. Если нет проектора, то можно увеличить шаблоны, копируя их на большую бумагу, соблюдая пропорции (по квадратам). Потом нужно сделать полноразмерные шаблоны. Для создания окончательных полномасштабных шаблонов лучше всего подходит берёзовая фанера 12 мм, но можно использовать и другой материал (рассмотрим ниже). Теперь нужно собрать все шаблоны воедино, чтобы получить макет-основу для формовки кузова.
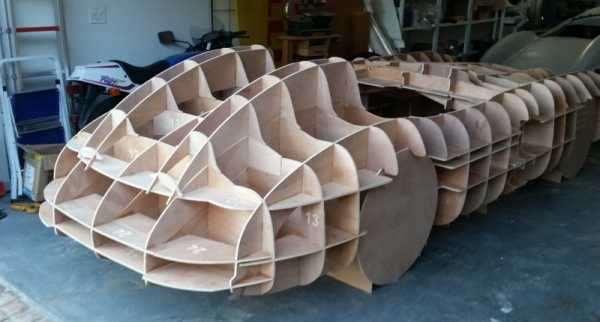
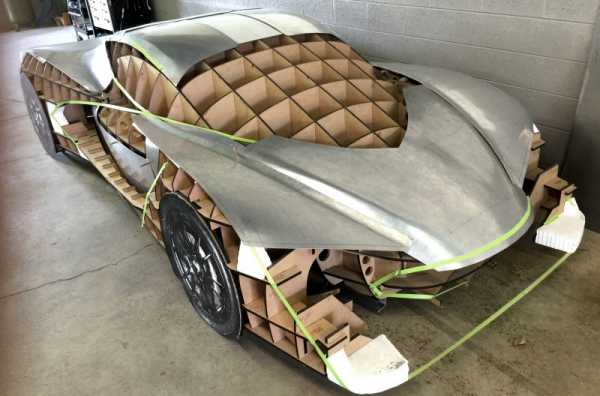
Для изготовления макета-основы могут использоваться разные материалы:
- Фанера
- МДФ (более дешёвый вариант фанеры)
- Проволока или арматура
- Монтажная пена+ картон (подходит для создания кузова из стекловолокна)
- Пластилин или глина для лепки
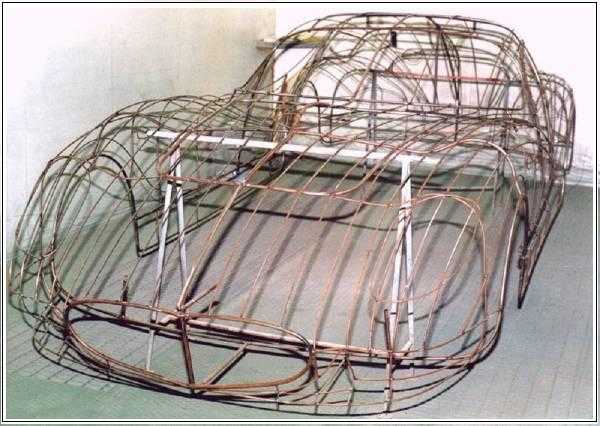
Разные материалы для создания макета-основы имеют разные особенности. Дерево даёт хорошую визуализацию во время процесса изготовления конструкции, но горит, когда на нём варятся панели кузова. Открытая конструкция (каркас из проволоки) хорошо гнётся в разные изгибы кузова, и дают лёгкий доступ с обратной стороны, для воздействия молотком и поддержкой на листовой металл. Картон и монтажная пена, создающая основной объём, хорошо подходят для создания кузова из стекловолокна (этот процесс мы рассмотрим ниже). Глина для лепки в этом процессе удобна, но самая дорогая вещь. Для создания полномасштабного макета потребуется более 200 кг глины. Стоимость пластилина или глины окупится, если её использовать повторно.
После того, как конструкция 3D-модели автомобиля готова, она будет служить формой для формовки листового металла для кузова автомобиля, либо кузова из стекловолокна.
Способы создания кузова автомобиля своими руками
Вот базовые способы, при помощи которых в наши дни можно сделать автомобильный кузов:
- Каркас + облицовка из формованного листового металла.
- Создание кузова без силового каркаса, с использованием более толстого металла для панелей.
- Создание панелей из отдельных сегментов, свариваемых вместе.
- Формовка из стекловолокна.
- Комбинация способов
Каркас и облицовка (панели из листового металла)
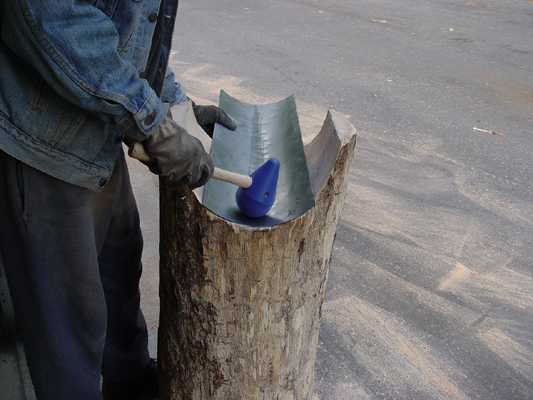
Это традиционный метод изготовления кузова, использовавшийся ещё при постройке карет. Базовый каркас кузова делается из дерева или металла. Далее листы облицовки крепятся на этот каркас. Кузов такой конструкции чаще всего применяют частные автомобилестроители, так как его легко спроектировать, построить и ремонтировать при повреждении (в отличие от кузова “монокок”, который считается более продвинутым, но применяется реже). Каркасом является так называемая пространственная рама (space frame). Кузов с такой рамой использует множество сегментов профильного металла (обычно стальных), соединённых вместе, чтобы сформировать прочную конструкцию. Прочность достигается за счёт поперечин. Нужно определить нагрузки, которые будут воздействовать на кузов и, в соответствии с этими нагрузками, нужно создать необходимые усиления профильными трубами. С трубами, имеющими квадратное сечение проще работать, чем с круглыми. Их проще стыковать друг с другом. Круглые трубы сложнее соединять, но они более прочные. При формовке листового металла используются киянки, молотки, поддержки, деревянные штампы, станок “английское колесо”.
Панели из толстого металла без пространственной рамы
При этом методе не используется силовой каркас (пространственная рама), на которую навариваются листы. Вместо этого применяются листы большей толщины, которые прочнее обычного листового металла. Жёсткость конструкции придаёт взаимное крепление панелей между собой. Такие кузова крепятся на шасси и должны иметь отдельные структурные элементы (не несущие большой нагрузки), на которые крепятся листы. Таким способом часто делают кузов для хот-рода. Недостатком такого способа является сложность формовки панелей из толстого металла и большой вес автомобиля.
Создание панелей из отдельных сегментов, свариваемых вместе
Панели для создания кузова могут создаваться из нескольких сегментов, сваренных вместе. Для этого, в качестве основы, используется проволочный каркас (для контроля и удержания формы), на который и приваривают все части панели. В зависимости от размера и формы, к обратной стороне панели могут быть добавлены усилители. Такой способ позволяет обойтись без формовки сложных панелей при помощи специальных формовочных станков.
Формовка кузова из стекловолокна
Спортивные автомобили с кузовом из стеклопластика появились ещё в конце 1951 года.
Chevrolet Corvette 1953 года выпуска был первым серийным автомобилем с кузовом из стекловолокна.
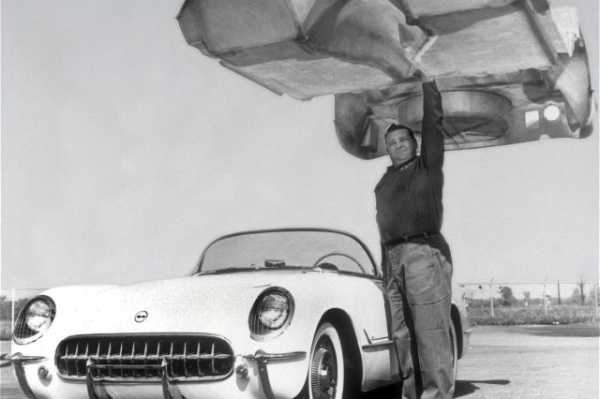
Стеклопластиковый кузов может быть сформован целиком, одной цельной частью.
Преимуществами кузова из стекловолокна являются лёгкий вес, дешевизна при производстве в небольших количествах, не подверженность коррозии. Недостатками являются низкое визуальное качество получаемой поверхности, требующей дальнейшего выравнивания, стекловолокно не может играть роль силовой конструкции, способной выдержать значительные нагрузки, поэтому должно устанавливаться на каркас.
Для создания макета в сегодняшние дни популярно применение картона (в качестве основного макета-основы, создание которого описано выше) со строительной пеной (для заполнения промежутков между картонными шаблонами) и дальнейшая доводка неровностей шпаклёвкой.

Существует два способа сформовать панели из стекловолокна. Оба способа требуют создания полномасштабного макета (как было описано выше).
- Кузов формуется напрямую, сверху макета. Такая формовка потребует дальнейшего выравнивания шпаклёвкой, так как поверхность получается грубой.
- Поверхность макета идеально выравнивается и даже окрашивается. С него делается форма из полиэфирной смолы и стекловолокна. Далее полученная форма усиливается. Её внутренняя часть получается очень гладкой и может использоваться для создания копий панелей из стеклопластика с гораздо более ровной поверхностью, чем при первом способе. Если требуется создавать несколько копий одинаковых деталей, то лучше создать такую форму. В остальных случаях, стекловолокно формуется поверх полноразмерного макета напрямую.
Выбор донора
Автомобиль-донор должен подходить по геометрическим параметрам к вашему проекту. Лучше в качестве донора выбрать надёжный и простой в обслуживании автомобиль, запчасти на который стоят не очень дорого. Чтобы сэкономить, можно, в качестве донора, купить машину с повреждённым кузовом.
Иногда, при создании автомобиля своими руками, используются двигатели от мощных мотоциклов. Они сочетают лёгкий вес и приличную мощность при маленьком объёме.
Кит-кар
Это ещё один способ сделать автомобиль своими руками. Кит-кар (от англ. kit-car) – это автомобильный набор, который продаётся производителем, как комплект запчастей и содержит подробную инструкцию по сборке, а покупатель потом его собирает самостоятельно. Обычно основные механические системы, такие как двигатель и трансмиссия берутся от автомобиля-донора или же покупаются новыми у отдельных производителей.
Кит-кары появились с ранних лет автомобилестроения. В 1896 году англичанин Томас Хилер-Вайт (Englishman Thomas Hyler-White) разработал дизайн для автомобиля, который можно было собирать дома.
В течение 1970-х годов кит-кары имели кузова, стилизованные под спортивные автомобили, которые были спроектированы, чтобы прикрепляться на раму VW Beetle. Это было популярно, так как кузов этого автомобиля мог легко отделяться от шасси, после чего оставались все механические компоненты, прикреплённые к раме. По этой причине, VW Жук стал одним из самых популярных доноров всех времён. Примеры такой переделки включают Bradley GT, Sterling и Sebring, которые изготавливались тысячами и многие по-прежнему сохранились.
Современные кит-кары представляют собой реплики известных и дорогих автомобилей. Реплики имеют внешний вид, идентичный оригиналу, но кузов сделан из стекловолокна и полиэфирной смолы, вместо листового металла, как оригинальный кузов. Места крепления капота, дверей и крышки багажника, усиливаются металлическими вставками, заламинированными в стекловолокно и смолу.
Infinity G35 coupe, подготовленный к установке нового кузова из стеклопластика. Часть кузова срезана, добавлен силовой каркас нужной формы.Кит-кары могут быть разной комплектации. Больше распространены кит-кары, которые предназначены только для замены кузова конкретного донора (Re-body Fiberglass Kit). К примеру, Vaydor Body Kit, производит кузова из стекловолокна для Infinity G35 coupe 2003–2007 года. Часть кузова срезается и устанавливается каркас, подходящий по форме к кузову из стекловолокна. Такая переделка требует меньше технических знаний, так как вся техническая часть остаётся от работающего серийного автомобиля.
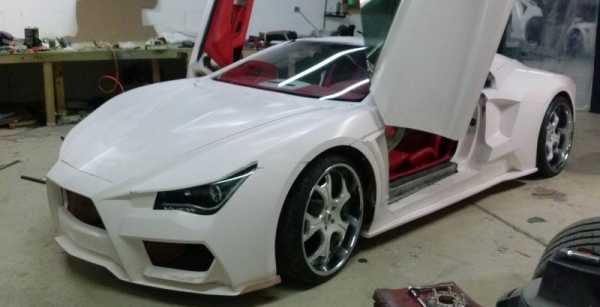
Преимущество изготовление автомобиля из набора kit-кара в том, что до вас это уже много раз делали и могут помочь советом. К тому же, сам производитель всегда может оказать поддержку в создании автомобиля. Если же изготавливаете эксклюзивный автомобиль с нуля самостоятельно, то вам остаётся надеяться только на себя.
Подготовка автомобиля к покраске и покраска
По подготовке к покраске есть множество видео и текстового материала. Покраску можно перепоручить другим мастерам, либо сделать самому. Качество покраски на 95% зависит от правильной, качественной подготовки. Краска не скроет неровности и несовершенства поверхности, а лишь подчеркнёт их.
Регистрация самодельного автомобиля
Многое зависит от страны, где вы живёте и требований к автомобилям при регистрации. Если же Вы не собираетесь ездить на автомобиле по дорогам общего пользования, то с этим проблем не возникнет.
В России регистрация самодельного автомобиля реальна. Для этого необходимо пройти целый ряд процедур. Машину нужно будет сертифицировать в лаборатории «Ростехрегулирования». Нужно будет предоставить техническую документацию и чертежи самодельного автомобиля. Конструкция машины должна соответствовать установленным техническим требованиям. Эксперты обратят внимание на габариты автомобиля, рулевое управление, эффективность тормозной системы, работу светотехники. Также будет проверено содержание вредных веществ в выхлопе. После прохождения всех процедур экспертизы владелец самодельной машины получит одобрение (документ). Это даёт возможность получения техпаспорта. Далее следует ещё ряд формальностей до окончательной регистрации автомобиля. При удачном завершении регистрации, владелец автомобиля получает свидетельство о регистрации транспортного средства, где в графе марка авто числится «Самодельный».
Ещё интересные статьи:
kuzov.info
Стеклопластиковый кузов автомобиля | Так делают
С помощью стеклоткани или стекломатов можно создать любую и даже очень сложную форму кузова автомобиля. Кузова из композитных материалов не ржавеют, легко обрабатываются и ремонтируются, обладают исключительной прочностью, способны гасить колебания и просты в изготовлении. Пропитывая стекломат или стеклоткань эпоксидной, полиэфирной или фенолформальдегидной смолой получают стеклопластик. При пропитке стекломатов или стеклоткани фенолформальдегидной смолой получается деталь с высокой температурной устойчивостью и механической прочностью. К тому же у стеклопластиков на этой основе самая низкая стоимость исходного материала. Большую прочность имеют стеклопластики на основе эпоксидных смол, но стоимость их выше.
Изготовление мастер модели.
Прежде чем начать создавать мастер модель, оцените имеющийся подручный материал: ДСП, пластилин, пенопласт, глину, алебастр, гипс. Если есть поблизости глина и песок, можно начинать с них, но наилучшим материалом является скульптурный пластилин. Любые твёрдые поверхности, как застывший гипс или алебастр Вы будете часами шлифовать и спиливать, а пластилин нужно всего лишь поскоблить шпателем или скребком.Перед началом работ необходимо выровнять площадку. Настил должен быть выровнен по уровню и чем точнее, тем вернее получится мастер модель. На настил устанавливают раму с колесами, а к ним крепится каркас будущего кузова. Каркас изготавливается из любых подручных материалов- фанера, ДСП, пенопласт, монтажная пена. Не забываем уменьшить размер каркаса и оставить место для нанесения пластилина.
Для того чтобы не перекосить кузов в двух взаимно перпендикулярных плоскостях, изготовьте два шаблона. Один с чертёжными размерами вида сверху, другой вида спереди (сзади). Для более точного выравнивания каркаса по высоте используйте гидроуровень.Далее обмазываем каркас пластилином и формируем будущий кузов автомобиля. Перед Вами широкое поле деятельности: пластилин позволяет срезать слои и образовывать любую поверхность. Заготовьте шаблоны на все криволинейные сечения поверхностей, капот, крыша, двери, облицовка радиатора и т. д. Кроме того, хорошо иметь ровную рейку длиной 3,5…4 м с сечением 20х30 мм. Эта рейка позволит проводить на поверхностях мастер модели лекальные кривые и проверить плавность построенных поверхностей.Если Вы используете стёкла от серийного автомобиля, а не делаете их на заказ, то установите стёкла на мастер модель. Стекло смачивают водой и устанавливают на мастер модели по предварительно сделанной разметке, которая переносится с чертежа будущего автомобиля на мастер модель.
Так же следует поступить и с серийными приборами освещения, ручками дверей и т.д. по списку, если Вы не собираетесь их изготавливать самостоятельно или делать на заказ. Это позволит избежать многих ошибок проектирования и убережет будущий кузов от многочасовых подгонок нестыкующихся деталей.
Закончив изготовление мастер модели, выверив все ее поверхности и линии, приступают к подготовке ее для изготовления кузова или матрицы. Сделав качественную мастер модель, лучше сделать матрицу, а по ней выклеивать кузов (один, два и более). Стеклопластик позволяет получить качественную поверхности кузова без последующего шлифования.
Прежде чем изготавливать матрицу, необходимо хорошо подготовить поверхность, так как любой выступ и любая впадина точно отобразятся на внутренней поверхности матрицы, а затем и на внешней поверхности кузова. Выровнять поверхности на мастер модели проще, чем на кузове автомобиля, да и лучше эту работу выполнить один раз, а не для каждого экземпляра кузова.
Если Вы изготовили мастер модель из пластилина, то нужно нанести разделительный слой и приступать к выклейке матрицы. Если же мастер модель изготовлена из глины, гипса или алебастра, то необходимо покрасить мастер модель, зачистить и отполировать. После этого необходимо нанести разделительный антиадгезионный слой, для облегчения снятия готовой матрицы. Для получения такого слоя применяют целлофановые, полиэтиленовые, полиамидные и другие полимерные пленки, а также пленкообразующие растворы или полировальные пасты и мастики, которые после высыхания образуют на поверхности тончайшую пленку антиадгезионного слоя.
Вот несколько рецептов самодельных составов для разделительного слоя:
- 2 части воска и 1 часть скипидара. Воск растапливают на водяной бане, затем снимают с огня и вливают скипидар. Проверьте качество состава, если высохший слой можно отполировать, то состав подходящий, в противном случае добавьте скипидар.
- 30% парафина, 30% бензина и 40% мыльной воды
Изготовление матрицы.
Мастер модель готова, приступаем к изготовлению матрицы.
Нам понадобится следующий инструмент:
- Ножницы для раскроя ткани или матов;
- Шпатели различной ширины;
- Кисти с жесткой щетиной;
- Резиновый ролик для прикатки;
- Банки и противни для смолы.
Смолу приготавливают небольшими порциями, так как время до начала отверждения и потери клеящих свойств 40-60 мин. Поэтому Обычно берут 1-2 кг смолы. Смолу готовят согласно инструкции, но предварительно нужно проверить состав на небольшом куске стекломата или стеклоткани, так как клеящие свойства зависят не только от состава и качества смолы, но и от способа соединения слоёв, перемешивания, температуры, влажности окружающей среды и других причин.
Сначала на готовую поверхность наносят, так называемый, декоративный слой (смолы 50% и алюминиевой пудры 50%) толщиной 1 мм и дают ему загустеть до такого состояния, чтобы следы смолы не оставались на пальце («до отлипа»). После этого наносят тонкий слой жидкой смолы и накладывают стеклоткань. Ее прокатывают роликом и обрабатывают жесткой кистью, следя за тем, чтобы не образовывались воздушные пузыри.
Если все же они возникают, то, прорезав пузырь ножницами, «прибивают» его кистью, смоченной смолой.
К первому слою сразу же прикладывают второй спой ткани и «прибивают» его, как и первый. Ни в коем случае нельзя проводить кистью по ткани, так как кисть может потащить за собой ткань и испортить работу.
Если матрица изготавливается из элементов: крылья, двери, капот, крыша, то матрицу нужно сделать разъёмной. Для начала размечаем линии разъёма матрицы, в дальнейшем они станут швами на кузове автомобиля, далее монтируем опалубку разъёма. Делается она из металла, картона или фанеры. В пластилиновую мастер модель опалубка просто втыкается по намеченным линиям, а с твёрдой мастер моделью из глины, гипса или алебастра поступают иначе.Наклеивают 2-3 слоя стеклоткани на всю мастер модель. Затем, как и на пластилиновой мастер модели, намечают линии разъема матрицы. Разметку следует проводить после полной полимеризации смолы. Затем подготавливают полосы, шириной 80- 100 мм. из металла, фанеры или картона. Один край будущей опалубки вырезают так, чтобы он повторял контуры плоскости, так как его нужно будет ввести в разрез, сделанный для разъема. На полосы наносится, упомянутый выше, разделительный слой. Ножовкой или «болгаркой» разрезают уложенные слои, вводят в зазоры полосы опалубки и дальше проводят выклейку по выше указанной технологии . При раскрое стеклоткани учитывается припуск на плоскости разъема.
Затем, уложив пять-шесть слоев на предыдущие, укрепляют плоскости разъема деревянными брусками. Для этого брусок и отбортованные плоскости стеклоткани попарно смазывают смолой и затем их скрепляют гвоздями, после полной полимеризации смолы борта сверлят и скрепляют болтами и гайками М6 или М8.Для предотвращения «игры» поверхностей, опалубку укрепляют брусками или накладывают ребра жесткости в виде жгутов стеклоткани, пропитанной смолой. После полимеризации смолы матрицу с мастер модели снимают.
Если разделительный слой был уложен равномерно и без пропусков, элементы матрицы будут сниматься без значительного усилия, нужно только ввести острый предмет в места разъема — отделить кромки стеклоткани от стальных полосок и руками потянуть на себя снимаемый элемент матрицы.
Оголив всю мастер модель проводят контрольную сборку матрицы, затем разбирают ее на элементы.
Выклейка кузова.
Элементы матрицы кузова очищают от разделительного слоя, оставшегося на внутренней поверхности. Затем внутреннюю поверхность шпатлюют и полируют.
Если на внутренней поверхности имеются большие раковины, то шпатлевку лучше производить эпоксидной смолой с наполнителем. Выступы снимают грубым напильником (стеклопластики хорошо обрабатываются), а затем поверхность шлифуют.
Внимательно осмотрев поверхность и убедившись, что на ней нет изъянов, наносят разделительный слой, при этом стараются сделать его как можно тоньше. Разделительный слой обязательно надо отполировать, так как какая поверхность получится на внутренней стороне матрицы, такой же будет и внешняя сторона готовой детали.
На разделительный слой наносят декоративный слой смолы, выдерживают его. Затем наносят жидкий слой, укладывают и прикатывают стекломат или стеклоткань так, чтобы не образовывалось пузырей; первый слой — лицевой слой. Обработав кистью со смолой первый слой, прикатывают второй, за ним — третий и т. д.
Рекомендовать количество слоев трудно, так как толщина композита зависит от толщины стеклоткани. Для того чтобы определить требуемую толщину, лучше всего провести эксперимент на небольших размеров образце. Однако менее 3 мм слой не делают! При использовании кевлара толщина слоя может быть 0,5…1,5 мм.
Уложив последний слой стеклоткани, тщательно прикатывают его резиновым валиком или пропитывают смолой с помощью кисти. После полной полимеризации смолы деталь вынимают из матрицы.
Следует учесть, что избыток смолы приведёт к деформации детали. Опытные мастера советуют наносить новый слой только после полимеризации предыдущего и его зачистки наждачной бумагой.
Если нет времени ждать полимеризации каждого слоя, попробуйте воспользоваться технологией, используемой на промышленном производстве. Деталь, вместе с матрицей помещают в мешок из тонкой мембраны и откачивают воздух. Мембрана плотно обжимает каждый изгиб детали и выдавливает излишки смолы. В таком виде деталь оставляют до полной полимеризации смолы.
Окраска.
Стеклопластик хорошо окрашивается как синтетической, масляной красками, так и нитрокраской. Для этого нужно только обезжирить наружную поверхность, зачистить ее наждачной бумагой, положить один слой грунта, а по нему производить окраску.
Можно предложить и другой метод. В эпоксидную смолу надо добавить 2-3% анилинового красителя. Прежде чем приступить к выклейке панелей с такой смолой, надо выполнить в порядке эксперимента операции окраски на отдельном куске стеклоткани и смолы, так как краска может изменить свой цвет при внесении ее в смолу.
Для первого декоративного слоя следует применять состав: 100 массовых частей смолы ПН-1, 6 частей инициатора и 8 частей ускорителя. Этот слой не только создает блестящую поверхность. но и защищает стекпонаполнитель от воздействия влаги и химикатов.
Окрашенный кузов шлифуют водостойкой мелкозернистой шлифовальной бумагой, полируют пастой или жидкостью для обработки кузова автомобилей.
Кузов из стеклопластика, изготовленный по каркасу автомобиля.
Некоторые конструкторы пришли к выводу, что для изготовления одного образца делать матрицу нецелесообразно.
Существует метод выклейки панелей кузова непосредственно по мастер модели без изготовления матрицы. Было замечено, что стеклоткань, пропитанная смолой и хорошо прикатанная к поверхности мастер модели, повторяет ее рисунок с учетом всех линий кузова. Если при этом последний (наружный) слой сделать декоративным, то фактически готова форма кузова автомобиля, и при соответствующей шпатлевке имеется возможность из этой заготовки изготовить кузов автомобиля. Удалив из внутренней части скорлупы оставшиеся части мастер модели, можно разрезать получившийся кузов на элементы, подклеить к ним той же смолой внутренние декоративные и несущие элементы и установить все на раму автомобиля. При таком изготовлении кузова требуется тщательно наложить каждый слой ткани и проверить поверхности на блики. При неправильном выполнении этих операций неоправданно возрастает расход шпатлевки при доводке и подготовке к окраске.
Данная статья была подготовлена по материалам книги «Я строю автомобиль» В. Захарченко и И. Туревский изд. «Машиностроение» 1989 г.
takdelayut.ru
Самодельный автомобиль. Кузов из стеклопластика. / BOSSCAR.RU
Самодельные автомобили (то, что мы сегодня называем самоделками) начали строить еще с появлением первых заводских моделей. Использование отдельных серийных агрегатов, и целых кузовов без наружных панелей дает возможность строить автомобили с оригинальным дизайном и нестандартными потребительскими свойствами. Поменять серийный руль на руль с тюнингом (анатомия + кожа)
Причем, техническая начинка донора обеспечивает самодельному автомобилю современные характеристики передвижения и комфорта.
Автомобиль-реплика Morgan Aero-8 построен на шасси японского представительского седана Toyota Crown. Привлекательность этого донора в его конструкции. Кузов Крауна стоит на полноразмерном подрамнике (хотя и не жестком), к которому крепятся все элементы двигателя, трансмиссии, подвески и топливной системы. Для изготовления на его базе самодельного автомобиля можно полностью отказаться от использования родных кузовных элементов.
Компоновка ходовой части оставлена без изменений, двигатель не передвигался, но радиатор переставлен за двигатель.
Панели нового кузова сделаны из стеклопластика и смонтированы на пространственной трубчатой раме. В крыше врезан стеклянный люк. Сама крыша съемная и крепится к кузову и рамке ветрового стекла четырьмя болтами. Зеркала заднего вида от Crown закреплены на самодельных кронштейнах. Как и у прототипа, на реплике установлены фары от Volkswagen New Beetle. Решетка радиатора изготовлена из латуни и покрыта хромом. Дверные ручки от Alfa Romeo, приборы от Crown.
Детали интерьера изготовлены из стеклопластика и обтянуты кожей и алькантарой.
На выставке «Автоэкзотика» в Тушино в 1999 году, мы с моим товарищем- вдохновителем постройки эксклюзивных автомобилей выставляли свой первый самодельный автомобиль Агата. К нам подошел молодой парень и поинтересовался, сможем ли мы сделать автомобиль по его проекту. Мы согласились. Мой товарищ взялся руководить этой стройкой, а я обещал слепить, склеить и собрать кузовные детали на раме донора.
Сначала был найден донор: в приличном состоянии, сравнительно свежая Toyota Crown.
Макет прототипа взяли из магазина игрушек. Масштабная модель автомобиля Morgan Aero-8 прослужил нам ориентиром для построения пропорций и пластики кузова.
На подрамнике донора я свинтил каркас из ДСП, брусьев и натянул на него оргалит.
Каркас в местах, где форма кузова имела округлые поверхности, я завалил пластилином и придал форме пластику схожую с прототипом. В целом пропорции и размеры кузова отличаются от английского Моргана. Наша реплика шире, длиннее и выше оригинала.
По пластилину я наформовал стеклопластик и сделал матрицу. Это был мой рекорд, когда я в одиночку склеил матрицу кузова за одну неделю…
Снимали корки матрицы уже вдвоем. Очищать их от пластилина и шкурить было, наверное, самой тяжелой и грязной работой. Часть макета во время съема матрицы, естественно, разрушилась.
Зашкуренные фрагменты матрицы мы свинтили и установили собранную матрицу для формовки кузовных панелей. В этой чаше мне предстояло построить в негативе форму внутренних поверхностей деталей кузова.
Поэтапно, в порядке очередности расположения деталей в кузове, я простраивал и вылепливал из пластилина боковины дверей, дверные проемы, отвороты-водостоки проемов капота и багажника, фланцы съемной крыши, ниши номерного знака, фар, фонарей и крышки топливного бака. Так же, поэтапно мы заформовывали эти опалубки стеклопластиком.
Прямо в матрице мы сварили и собрали легкую трубчатую раму по контуру уже готовых стеклопластиковых деталей. По фланцам дверных проемов, водостоков и отворотам порогов мы приклеили эту раму к кузовным панелям.
В результате, после съема матрицы у нас получился жесткий кузовной верх, с дверями, съемной крышей, капотом и крышкой багажника.
Много времени ушло на установку верха кузова на раму донора и изготовление пола. Панели пола, моторный щит, дно багажника и арки колес мы выклеивали из стеклопластика. Стеклопластиком же склеили между собой верх кузова и полы. Получилась достаточно жесткая конструкция, тем более, что пол мы тоже укрепили металлическим каркасом. Раму пола закрепили на раме Крауна на родных подушках.
Под капотом сделали раму и закрепили на ней радиатор с вытяжными вентиляторами позади двигателя. В передней части кузова мы склеили моторный щит, на котором закрепили остальные детали. Поскольку Toyota Crown праворульный автомобиль, пришлось переносить рулевой механизм на левую сторону.
К сожалению, время изготовления кузова до покраски было ограничено шестью месяцами, а количество исполнителей — бюджетом, поэтому во многих случаях приходилось поддаваться на компромиссные решения. Уложиться в сроки, в частности, нам помогло упрощенное конструктивное и технологическое решение капота. Мы объединили капот с бампером и крыльями, хотя из-за этого он стал значительно тяжелее. Вся эта корка поднимается на двух трубчатых кронштейнах-петлях, закрепленных на раме кузова над приборным щитом. Стеклопластиковая панель капота сама имеет стальной подрамник и металлическую фальшпанель, которая расположена близко к двигателю. В опущенном положении вся конструкция крепится с боков и спереди к раме кузова. Крышка багажника тоже усилена рамкой из стального профиля и закреплена на кронштейнах – петлях к раме кузова. Для фар и фонарей в стеклопластике отформованы ниши, защищающие заднюю сторону светотехники.
В кузове реплики мы сразу заложили конструкцию съемной жесткой крыши. Снизу через фланцы она опирается на полку за задними сидениями и крепится к раме кузова, а спереди к раме рамки лобового стекла. Заднее стекло на съемной крыше, лобовое и боковые стекла плоские, изготовлены по индивидуальным размерам. Трудно было подобрать подходящие уплотнители для наших безрамочных дверных стекол. Так до конца эту проблему нам на этом кузове решить не удалось. Впредь решили, по возможности, использовать в комплекте стекло с уплотнителем от подходящего донора.
Внутри дверных коробов я собрал подрамники из металлического профиля для монтажа направляющих стекол, установки петель, замков и ручек. Двери повесил на петли в проемах и подогнал зазоры. После этого были изготовлены кронштейны из металлического профиля и стеклопластика для штатных зеркал и прикручены к дверям. Ручки от Alfa Romeo встали на свои места на дверях.
В салоне поставили кресла и прикрепили их через пол к раме кузова. Смонтировали консоль с рычагом ручного тормоза и ручкой переключения передач, педальный узел и рулевую колонку с рулем на удобном расстоянии от сидения. По сидениям же спроектировали и изготовили из стеклопластика подоконники, обшивки и ручки дверей, панели щитка приборов и корпуса консоли. После покраски кузова все детали интерьера обтянули кожей и алькантарой.
Автомобиль эксплуатируется уже несколько лет в сухую и теплую погоду.
Спасибо всем, кто принимал участие в изготовлении автомобиля.
Статьи о тюнинге своими руками.
Автор: Михаил РомановСайт: http://bosscar.ru
При копировании статьи поставьте, пожалуйста, ссылку на мой блог.
bosscar.ru
Тюнинг кузова
Тюнинг кузова своими руками. Серийные машины, особенно восьмидесятых и девяностых годов, обычно имеют одинаковый угловатый и не очень привлекательный дизайн, и освежить его или поменять, можно несколькими способами, которые будут описаны в этой статье.
Да и более современные машины, с более аэродинамически совершенными кузовами, всё же многие автовладельцы хотят выделить из толпы. Но серийные пластиковые обвесы, продающиеся в магазинах, довольно дороги, делаются только для определённых моделей, да и не добавляют машине самого главного — того, что обвес (а соответственно и дизайн машины) будет в единственном экземпляре.Конечно же описать в одной статье все нюансы и варианты существенного изменения кузова в лучшую сторону и все этапы работ с металлом и пластиком не так то просто, особенно для новичков. Но в этой статье будет всё описано по возможности понятно.
Сделать машину единственной и неповторимой по дизайну, можно только доработав (изменив) кузов своими руками. Самый быстрый и не требующий больших вмешательств в серийный кузов — это конечно же наружный пластиковый обвес.
Поменять серийный бампер, например, можно тоже по- разному. Например, купить готовый и выпускаемый какой- то фирмой под определённую модель, можно купить на авторазборке более дутый бампер, от более свежей и «зализаной «машины, и разрезав его посередине, подогнать под ширину своей машины, а так же переделав его крепления.
Можно изготовить с «нуля» из полиэфирной или эпоксидной смолы и стеклоткани. Этот способ наиболее трудоёмкий и дорогой, но только он позволит сделать эксклюзив в единственном экземпляре. Это так же относится и к всевозможным спойлерам, накладкам, воздухозаборникам, расширенным колёсным аркам.
И здесь следует определиться, из чего всё это будет сделано, из более лёгкого, но трудоёмкого стеклопластика или из более тяжёлого и ремонтнопригодного листового металла, из которого можно изготовить всё гораздо быстрее. Выбирать вам. Я считаю, что выбор нужно делать изходя из формы изделия. Если деталь имеет сложную форму со множеством мелких выпуклостей или выпуклых рисунков ( см. фото боковой крышки мотоцикла и кофра), то легче будет изготовить эту деталь из стеклопластика ( стеклоткань со смолой).
Если деталь более пологая и имеет ровную и однообразную выпуклость по всей длине, как например, имеет расширенная колёсная арка, то лучше её изготовить из стального листа, будет и легче, и быстрее, если иметь необходимый для этого инструмент. К тому же нет смысла думать как прикрепить пластиковую деталь к металическому кузову, намного проще сделать деталь из металла и просто приварить её к кузову.
Какой инструмент и приспособления нужны для работ с листовым металлом и какой для работ с стеклопластиком мы рассмотрим по оттдельности. Главным принципом всех этих работ- это такой же принцип, по которому пошли и производители современных автомобилей, имеющих привлекательный дизайн.
Это принцип» раздутия» современного кузова и придания ему более плавных форм и переходов, что позволяет добиться ещё и меньшего коэффициента сопротивления воздуха, обтекаемого машину, что в купе с современными двигателями позволяет сократить расход топлива почти вдвое. Но главным достоинством всех этих работ- это конечно же, более свежий, элегантный и привлекательный дизайн.
Практика. Постараюсь описать изготовление одной и той же детали, но из двух разных материалов — стеклопластика и листового металла. Изготовим, например, самое простое — передний воздухозаборник (на капоте). Для изготовления этой детали из стеклопластика понадобятся глина или пластилин, количество которых зависит от размера детали, эпоксидная или полиэфирная смола (грамм 250), стеклоткань, желательно разной толщины, стеклошпаклёвка и финишная шпаклёвка- их количество зависит от того как вы выравняете (зашлифуете) поверхность засохшей смолы, ну и наждачная бумага.
Про грунтовку и краску не пишу, так как о правильной подготовке и нанесению лакокрасочного покрытия мы поговорим в отдельной статье подробно (например вот тут и вот здесь). Самым первым и ответственным этапом будет определение формы и размеров детали, а как я уже говорил, понадобится глина или пластилин, придется на время вжиться в проффессию скульптора.
Кроме того, если форма детали не получится, то в любой момент можно всё поправить или добавить материал, если не хватило. Стелим клеёнку на капот и лепим прямо по месту, это позволит визуально наблюдать за размером, относительно капота ( отходим назад и осматриваем с разных сторон) ,и если нравится форма и размер, то заглаживаем и окончательно формируем форму макета.
К тому же лепка прямо на капоте (через полиэтиленовую плёнку или малярный скотч) позволит нижней части вашего воздухозаборника повторить плавный изгиб капота и это впоследствии позволит сделать красивую стыковку готовой детали и поверхности капота..
Кстати, при лепке не забывайте проверять линейкой или картонными шаблонами симметричность детали, то есть, постоянно сравнивайте высоту и ширину каждой половинки детали.
Вылепив форму детали не забудьте по периметру сделать четыре или шесть симметричных утолщений( бобышек) в нижней части детали, благодаря им вы сможете просверлить в конце работ в них отверстия для винтов крепления детали, а эти утолщения усилят и сделают прочными места креплений и вашей детали будет не страшна вибрация и порывы ветра.
Вылепив макет из пластилина или глины, и одобрив его внешний вид, можно начинать накладывать форму из стеклоткани, но перед этим нужно наложить на форму два — три слоя из кусочков обычной бумаги, а клей подойдёт обычный, селикатный или сваренный из крахмала. Отрываем от старых газет кусочки и предварительно смазав макет клейстером или клеем лепим эти кусочки на форму, и накладываем несколько слоёв.
Клей для бумаги сохнет очень быстро и только после этого начинаем накладывать кусочки стеклоткани на смазаные эпоксидным клеем слои бумаги. Если обойтись без бумажных слоёв, то потом после высыхания будет очень трудно отделить высохший пластиковый воздухозаборник от пластилинового (глиняного) макета. Вместо кусочков бумаги можно использовать и малярный скотч, если деталь не имеет слишком крутых и резких изгибов.
Там где поверхность довольно ровная накладываем более крупные и толстые куски нарезаной стеклоткани, а там где малые радиусы или закругления, ложим более мелкие и тонкие кусочки, и добиваемся чтобы все кусочки перекрывали друг друга примерно на треть, это добавит прочности, а так же добиваемся чтобы все кусочки стеклоткани хорошо пропитывались смолой. Накладываем всего три — четыре слоя, так как деталь не силовая ( не держит другую деталь) и между каждыми слоями хорошо промазываем эпоксидкой.
Можно использовать и полиэфирную смолу, если найдёте, она менее текуча, но зато имеет едкий запах, Работаем в резиновых перчатках, и сразу много эпоксидного клея не разводим (двухкомпонентный состав 1 к 10), клей начинает полимеризовываться (застывать) уже через час. Если смола начинает густеть и вы не успеваете её использовать, то смолу можно разбавить ацетоном (но не более 10 процентов ацетона).
Самый верхний слой, желательно, покрыть смолой, разведённой каким- нибудь наполнителем ( пластиковая стружка, алюминиевая пудра и др.) Это не даст верхнему слою потечь и с боков изделия не будет подтёков, и застывших капель, которые нужно потом будет удалять вышкуриванием.
При застывании эпоксидка имеет свойство, хотя бы чуть чуть, но застыть с мелкими неровностями, ямками. Наша задача создать в этих ямках (впадинах) риски и царапинки, можно это сделать наждачной бумагой ( 80 — 200 абразив) или железной кисточкой, сделанной из трубки и тросика. Покрыв всю поверхность (и ямки и выпуклости) сеткой мелких царапин мы добьёмся максимальной агдезии (сцепки) верхнего слоя и стеклошпаклёвки.
Работаем в перчатках и желательно, в респираторе, так как стеклоткань сделана из тончайших стеклянных частичек, которые попав даже на кожу (не дай бог в дыхательные пути) , если расчесать вызывают раздражение. Покрыв поверхность стеклошпаклёвкой, можно отделить почти готовый воздухозаборник от глиняного макета.
Кстати, глину можно сохранить и обжечь в печи, превратив в керамику, это позволит вам при желании организовать мелкосерийное производство детали воздухозаборника и не только его, в отличие от пенопластового макета, который многие потом просто вымывают из детали ацетоном. Отделив воздухозаборник от макета, остаётся его ещё раз зашкурить, подровнять и вывести финишной шпаклёвкой под последующую грунтовку и покраску.
О работе с стеклотканью и эпоксидной смолой, можно почитать так же в этой статье, где я описал изготовление подиумов для динамиков, устанавливаемых в дверях автомобиля. Ну или здесь — в статье про изготовление подиума для сабвуфера, усилителя и монитора.
Последняя операция- это сверление крепёжных отверстий в бобышках изделия. Просверлив их, остаётся приложить воздухозаборник на заранее отмеренное посередине место на капоте и просверлить отверстия в металле капота, используя в начале сверления пластиковый воздухозаборник с отверстиями как кондуктор.
Так же нужно вырезать прямоугольные окна в капоте, соответственно форме воздухозаборника и подвести туда воздушный фильтр, это позволит создать инерционный надув и немного поднимет мощность.
Ещё советую на входных окнах капота закрепить металлическую сетку от всякого мусора и в местах отреза металла загрунтовать срезы и прокрасить. Остаётся покрасить готовое изделие и прикрепить к капоту с помощью винтов с красивыми хромированными головками, а можно сделать воздухозаборник (как на жёлтой машине), чтобы его крепления не были видны вообще. Для этого просто вклеиваются в воздухозаборник с обратной стороны гайки или бобышки с резьбой, а потом при закреплении воздухозаборника, болты или винты вворачиваются с обратной стороны капота.
Изготовление этого изделия из стального листа (0,8 — 1 мм) еще проще, так как потребуются кусок картона, скотч, ножницы по металлу и картону, кусочки листового металла, проволока диаметром 5 — 7 мм и сварочный полуавтомат.
Если вы захотите сделать верхнюю часть (потолок) воздухозаборника более выпуклую, тогда нужно будет повозиться подольше (используя английское колесо), однако, это не обязательно, так как эта деталь и с плоским верхом смотрится неплохо.
Для начала определяемся с размерами, только на этот раз работаем не с глиной, а с картоном. Вырезаем из картона верхнюю часть, боковинки , заднюю часть и склеив все эти детали скотчем, прикладываем к капоту машины. Не забываем проверять симметричность, верхнюю часть можно проверить сложив её пополам, а боковинки проверяем на одинаковость просто наложив одну на другую сверху. Если форма или размеры не устраивают, то вырезаем из картона побольше или поменьше и опять прикладываем, ведь картон это не металл и резать его очень легко.
Если приложенный на капот, пока картонный воздухозаборник устраивает по размерам и дизайну, то остаётся разобрать его, отклеив скотч, и приложив все картонки на листовой металл, просто обвести их чертилкой или маркером. Есть, правда, один нюанс, боковинки и верхнюю часть воздухозаборника можно слелать из цельного листа и потом только согнуть боковины на 90 или более градусов (зависит от выбранного дизайна) относительно верхней части, но для красивой и качественной гибки нужен листогиб — гибочный станок.
Если его нет, значит боковинки просто вырезаются отдельно и затем привариваются к верхней части, после шлифовки сварных швов деталь будет выглядеть как цельная. После переноски размеров на листовой металл вырезаем детали ножницами или болгаркой, затем прихватив боковинки к верхней части сваркой, проверяем требуемые углы, подгибаем, если нужно, а затем обвариваем.
изготовленные мной стеклопластиковые кофры для мотоцикла
самодельные бардачки из стеклоткани для мотоцикла
Далее, привариваем заднюю более низкую стенку, а затем к передним окнам, куда собственно, заходит воздух, нужно приварить выгнутые по форме окон из 5 — 7 мм проволоки кантики, которые придадут изделию законченный ( фирменый) вид и жёсткость, без этих кантиков создаётся впечатление незаконченного вида из за остроты кромки. Далее, остаётся приварить изнутри бобышки с резьбой или гайки для крепления воздухозаборника к капоту. Эти гайки приварите, приблизительно, на сантиметр выше кромки, так как нужно будет по кромке пустить резиновый уплотнитель.
После сварочных работ зашлифовываем все сварные швы снаружи, и если где- то неровности, кратеры и непровары, то просто перешпаклёвываем швы, ведь это же не швы бензобака. Остаётся всё отшлифовать брусочком с наждачкой, загрунтовать и покрасить изделие.
Расширение колёсных арок.
В изменении дизайна кузова автомобилей, наиболее частым и эффективным методом улучшения внешнего вида машины является расширение ступиц колёс, установка более широких колёс и соответственно расширение арок колёс. Колёса выдвигают в стороны с попощью ступичных переходников (в форме катушек) выточенных из качественных алюминиевых сплавов(например Д16) или титана (подробнее об этом в статье про широкие колёса — ссылка чуть выше).
После выдвижения колёс в стороны и замены их ширины на большую, машина приобретает вид мускулкара, а после замены пружин на более короткие ещё и приземестый спортивный вид с заниженным центром тяжести. Остаётся изменить только одно — расширить стандартные колёсные арки .
Работа начинается как всегда, с разметки и вырезания картонных шаблонов.Принцип один: вырезал примерил, не хватило ширины добавляем с помощью скотча полоску картона и опять примеряем, пока не добьёмся достаточной ширины прикрытия колеса и премлемого внешнего вида. Прикреплять картон к кузову для просмотра можно тем же скотчем.
Когда форма шаблона понравится, вырезаем из картона зеркальную копию. Один шаблон для правой арки, другой для левой в зеркальном отображении. То же самое проделываем и с задними арками, и после всего добавляем на каждой картонке по 2-3 сантиметра ширины (ну или запоминаем и потом добавляем эти 2-3 см на стальной детали) . Это нужно во первых для закатки наружных кромок арок на зиговочной машине, про которую читаем здесь.
Это придаст жёсткость и красивый вид («съест» примерно сантиметр — полтора ширины, может и больше, если арка большая и машина тоже), а во вторых ширина чуть уменьшится при придании выпуклости листовому металлу, ну а в третьих лишнее всегда легче отрезать чем добавить не достающий фрагмент.
Вырезав картонные шаблоны накладываем их на металический лист толщиной равной толщине кузова вашей машины(обычно от 0,7 у свежих до 1 мм у более древних моделей), обводим маркером и вырезаем сначала чуть с запасом болгаркой, а затем уже точно ножницами по металлу.
Далее для придания выпуклости понадобится кожаная подушка набитая дробью или песком, (пример кожаной подушки и молотков, можно посмотреть здесь) и молоток со сферическим и отполированным бойком. Определившись с какой стороны деталь будет выпуклой, этой стороной ложим на подушку и начинаем наносить частые удары, постепенно двигаясь по спирали от середины к краям.
Со временем деталь начинает приобретать выпуклый вид и одновременно приобретать жёсткость. Когда достигли необходимой глубины детали, ставим её уже не на подушку, а на плоскую и гладкую наковальню или плитку, и обязательно поверхность этой плитки должна быть если не полированной, то хотя бы шлифованной.
От этого зависит гладкость поверхности готовой детали. Уложив деталь на плитку, пластиковым молотком изнутри подравниваем неровности и шишки .Обстучав всю поверхность на плоской плите, вы естественно не выровняете деталь полностью .
Для окончательной отделки и придания гладкого и зеркального вида выпуклой детали её необходимо прокатать между роликами английского колеса (про английское колесо читаем вот тут). Начинаем прокатывать с небольшим прижимом и постепенно сжимаем штурвальчиком ролики скобы до максимального усилия. На выходе должна получиться идеально ровная делаль, которую выравнивать шпаклёвкой нет никакой необходимости.
Когда арка готова, пока не спешим её приваривать к кузову, так как нам необходимо сделать ещё одну( зеркальную копию) , которая пойдёт на другую сторону машины. А так как арка пока не приварена к кузову, то сверять с ней вторую арку при изготовлении будет намного легче.
И ещё, пока не приварили к кузову, нужно будет закатать кантик наружной кромки арки с помощью зигмашины (смотрите про зигмашинку кликнув по ссылке выше в тексте), это добавит жёсткости арке и придаст законченный фирменный вид.
И когда будете изготовлять вторую арку на другую сторону машины, то используйте картонный шаблон первой арки (только перевёрнутый), и при изготовлении второй арки, вы с помощью этого шаблона добьётесь одинаковой формы обоих арок.
Останется теперь приварить их точно к кузову, при необходимости обрезать часть родного крыла(с закатанной частью) и заполировать сварные швы. Задние арки делаем по такому же принципу, и когда будут приварены и задние арки, то желательно для полной гармонии и жёсткости соединить задние и передние арки расширенными порогами( см. фото на примере запорожца). Теперь нужно зашлифовать и перешпаклевать сварные швы, загрунтовать и покрасить.
Конечно же про тюнинг кузова дело интересное и необъятное и его невозможно описать в одной статье, но всё же надеюсь эта статья пригодится новичкам, творческих успехов всем!
suvorov-castom.ru