ОБОРУДОВАНИЕ ДЛЯ ТЕРМИЧЕСКОЙ ОБРАБОТКИ КРЕПЕЖА, МЕТИЗОВ И ДЕТАЛЕЙ. Чем закалка стали отличается от отпуска
Термообработка закалкой и отпуском стали: важность, отличия, этапы термической обработки
Металлы и сплавы обладают характерными показателями твердости и прочности. Эти характеристики можно найти в специальных таблицах. Современные технологии позволяют изменить базовые параметры, применяя технологию термообработки. Сам процесс термической обработки достаточно прост: металл доводят до необходимой температуры и затем охлаждают. В этом процессе важны два показателя:
-
Температура, до которой нагревается металл;
-
Время нагрева и последующего охлаждения.
Эти два показателя формируют режим термообработки, который состоит из нескольких этапов.
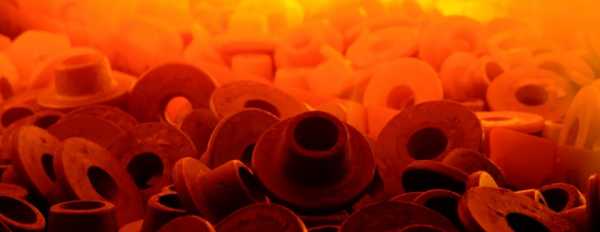
Этапы термообработки: отжиг и нормализация
В процессе термической обработки металлы проходят четыре основных этапа: отжиг, нормализацию, закалку, отпуск.
-
Отжиг. Этот процесс происходит при температуре 750 градусов Цельсия и выше. Широко применяется при термообработке стали. В результате отжига увеличивается вязкость стали, стабилизируются ее основные свойства. Охлаждается сталь вместе с печью не более чем на 60 градусов Цельсия в час. Главным показателем скорости охлаждения является легированность, чем она выше, тем скорость ниже.
-
Нормализация. Для этого процесса подъем температуры для обработки сталь идентичен предыдущему процессу, но вот процесс охлаждения резко отличается. В данном процессе охлаждения производится не в печи, а вне ее. При этом существуют два варианта с обдувом и без него. Процесс нормализации используется для низкоуглеродистых сталей, при этом их структура уплотняется за счет уменьшения диаметра зерен. Такую сталь легче обрабатывать и подвергать последующей шлифовке.
Закалка и отпуск
Эти два процесса наиболее важны, так как металлы, прошедшие закалку и отпуск, обладают особой прочностью и износоустойчивостью.
-
Закалка осуществляется в печах при температурах 770 или 960 градусов Цельсия в зависимости от вида металла. Охлаждение осуществляют в воде для углеродистых сталей, и в маслах для легированной. Подъем температуры и резкое охлаждение стали изменяет ее физическое состояние, сталь становится хрупкой. Для удаления этого эффекта, а также для снятия внутреннего структурного напряжения применяют следующий процесс.
-
Отпуск. Этот процесс заключается в повторном нагревании уже закаленной стали до температур 600 градусов Цельсия с последующим медленным охлаждением. При этом чем ниже скорость охлаждения, тем лучше снимается внутреннее напряжение металла.
Важность термообработки
Термообработку сложно переоценить. Только два показателя температура и время могут изменить физико-химические характеристики стали.
barion-ua.com
Закалка и отпуск стали.
Целью закалки и отпуска стали является повышение твердости и прочности. Закалка и отпуск стали необходимы для очень многих деталей и изделий. Закалка основана на перекристаллизации при нагреве и предотвращении перехода аустенита в перлит путем быстрого охлаждения. Закаленная сталь имеет неравновесную структуру мартенсита, троостита или сорбита.
Чаще всего сталь резко охлаждают на мартенсит. Для смягчения действия закалки сталь отпускают, нагревая до температуры ниже точки А1. При отпуске структура стали из мартенсита закалки переходит мартенсит отпуска, троостит отпуска, сорбит отпуска.
Закалка стали. Температура нагрева стали при закалке та же, что и при полном отжиге: для доэвтектоидной стали на 30—50 °С выше точки Ас3, для заэвтектоидной — на 30—50° выше точки Aс1. При нагреве доэвтектоидной стали до температуры между точками Ас1 и Ac3 (неполная закалка) в структуре быстро охлажденной стали наряду с закаленными участками будет присутствовать нерастворенный при нагреве (в аустените) феррит, резко снижающий твердость и прочность. Поэтому для доэвтектоидной стали обязательна полная закалка с нагревом выше точки Ас3.
В заэвтектоидной стали избыточной фазой является цементит, который по твердости не уступает мартенситу и даже превосходит его, поэтому сталь достаточно нагреть на 30—50 °С выше точки Ас1.
Нагревать заготовки, особенно крупные, нужно постепенно во избежание местных напряжений и трещин, а время выдержки нагретых заготовок должно быть достаточным, чтобы переход в структуру аустенита полностью завершился.
Скорость охлаждения заготовок при закалке должна быть такой, чтобы получить заданную структуру. Критическая скорость закалки изменяется в широких пределах в зависимости от наличия легирующих компонентов в стали. Для простых сплавов железо—углерод эта скорость очень высока. Присутствие в стали кремния и марганца облегчает закалку на мартенсит, так как для такой стали С-образные кривые на диаграмме изотермического превращения аустенита будут сдвинуты вправо и критическая скорость закалки понижается.
Наиболее распространено охлаждение заготовок погружением их в воду, в щелочные растворы воды, в масло, расплавленные соли и т. д. При этом сталь закаливается на мартенсит или на бейнит.
При закалке применяют различные способы охлаждения в зависимости от марки стали, формы и размеров заготовки.
Простую закалку в одном охладителе (чаще всего в воде или водных растворах) выполняют, погружая в него заготовки до полного охлаждения. На рис. 2 режим охлаждения при такой закалке характеризует кривая 1.
Для получения наибольшей глубины закаленного слоя применяют охлаждение при интенсивном обрызгивании.
Прерывистой закалкой называют такую, при которой заготовку охлаждают последовательно в двух средах: первая среда — охлаждающая жидкость (обычно вода), вторая — воздух или масло (см. кривую 2 на рис. 2). Резкость такой закалки меньше, чем предыдущей. Рис. 2.
При ступенчатой закалке заготовку быстро погружают в соляной расплав и охлаждают до температуры несколько выше Мн. Выдержка обеспечивает выравнивание температуры от поверхности к сердцевине заготовки, что уменьшает напряжения, возникающие при мартенситном превращении; затем заготовку охлаждают на воздухе (кривая 3 на рис. 2).
Изотермическая закалка (закалка в горячих средах) основана на изотермическом распадении аустенита. Охлаждение ведется до температуры несколько выше начала мартенситного превращения (200—300 °С) в зависимости от марки стали. В качестве охладителя используют соленые расплавы или масло, нагретое до 200—250 °С. При температуре горячей ванны заготовка выдерживается продолжительное время, пока пройдет инкубационный период и период превращения аустенита (кривая 4 на рис. 2). В результате получается структура бейнита, по твердости близкая к мартенситу, но более вязкая и пластичная. Последующее охлаждение производится на воздухе.
При изотермической закалке вначале требуется быстрое охлаждение со скоростью не менее критической, чтобы избежать распадения аустенита. Следовательно, по этому методу можно закаливать лишь небольшие (диаметром примерно до 8 мм) заготовки из углеродистой стали, так как массивные заготовки не удается быстро охладить. Это не относится однако к легированным сталям, большинство марок которых имеют значительно меньшие критические скорости закалки. Большим преимуществом изотермической закалки является возможность рихтовки (выправления искривлений) заготовок во время инкубационного периода превращения аустенита (который длится несколько минут), когда сталь еще пластична.
Закалка при помощи газовой горелки. Кислородно-ацетиленовое пламя газовой горелки с температурой около 3200 °С направляется на поверхность закаливаемой заготовки и быстро нагревает ее поверхностный слой до температуры выше критической. Вслед за горелкой перемещается трубка, из которой на поверхность заготовки направляется струя воды, закаливая нагретый слой. Этот способ применяется для изделий с большой поверхностью (например, для прокатных валков, зубьев больших шестерен и т. д.).
Закалка токами высокой частоты по методу В. П. Вологдина нашла очень широкое применение в промышленности, так как отличается высокой производительностью, легко поддается автоматизации.
Обработка холодом. Этот метод применяется для повышения твердости стали путем перевода остаточного аустенита закаленной стали в мартенсит. Холодом обрабатывают углеродистую сталь, содержащую больше 0,5 % С, у которой температура конца мартен-ситного превращения находится ниже 00 С, а также легированную сталь (например, быстрорежущую).
При низком отпуске (нагрев до температуры 150—200 °С) в структуре стали в основном остается мартенсит, который однако имеет другую решетку, как сказано выше. Кроме того, начинается выделение карбидов железа из пересыщенного твердого раствора углерода в -железе и начальное скопление их небольшими группами. Это влечет за собой некоторое уменьшение твердости и увеличение вязкости стали, а также уменьшение внутренних напряжений в заготовках. Для низкого отпуска, заготовки выдерживают в течение определенного времени обычно в масляных или солевых ваннах. Если для низкого отпуска заготовки нагревают в атмосфере воздуха, то для контроля температуры часто пользуются цветами побежалости, появляющимися на зачищенной поверхности заготовки. Появление этих цветов связано с интерференцией белого цвета в пленках оксида железа, возникающих на поверхности заготовки при ее нагреве. Для углеродистой стали в интервале температур от 220 до 330 °С в зависимости от толщины пленки цвет изменяется от светло-желтого до серого. Для легированной стали соответствующие температуры выше. Низкий отпуск применяют для режущего инструмента из углеродистых и легированных сталей, измерительного инструмента, цементированных заготовок, а также других изделий, работающих в условиях трения на износ.
При среднем (нагрев в пределах 300—500 °С) и высоком (500—700 °С) отпуске структура мартенсита переходит соответственно в структуру троостита или сорбита. Чем выше температура отпуска, тем меньше твердость отпущенной стали и тем больше ее вязкость. При высоком отпуске сталь получает наилучшее сочетание механических свойств: повышенные прочность, вязкость и пластичность; поэтому закалку на мартенсит с последующим высоким отпуском называют улучшением стали. Средний отпуск применяют при производстве кузнечных штампов, пружин, рессор, а высокий—для многих деталей, подверженных действию высоких напряжений (например, осей автомобилей, шатунов двигателей).
Закалка и отпуск стали - Сплавы
Закалка и отпуск сталиКатегория:
Сплавы
Закалка и отпуск сталиЦель закалки и отпуска стали — улучшение ее свойств. Операциям закалки и отпуска подвергается значительное количество стальных деталей, а в инструментальном производстве — все детали.
Операция закалки основана на явлении перекристаллизации и состоит в нагреве стали до температуры выше критической, выдержке при этой температуре и последующем быстром охлаждении. Закалкой предотвращают превращение аустенита в перлит, и при нормальной температуре получают состояния мартенсита, троостита или сорбита; эти состояния являются неравновесными. Крайним неравновесным состоянием в стали является переохлажденный аустенит, который в углеродистой стали неустойчив и в зависимости от степени переохлаждения переходит в одно из промежуточных состояний: мартенсит, троостит и сорбит.
Чаще всего закалка осуществляется путем резкого охлаждения стали, в результате чего в ней преобладает мартенсит. Для смягчения действия закалки производится отпуск, состоящий в нагреве стали до температуры ниже точки Av При отпуске сталь из состояния мартенсита переходит в состояние троостита или сорбита.
Рис. 1. Микроструктура зернистого перлита (Х500)
Температурный режим закалки. Температура нагрева стали при закалке та же, что и при полном отжиге: для доэвтектоидной стали на 30—50° выше точки Лс3, для заэвтектоидной — на 30—50° выше точки Асх.
В случае нагрева доэвтектоидной стали до температуры между точками Act и Ас3 (неполная закалка) в структуре быстро охлажденной стали, наряду с закаленными участками, будет присутствовать нерастворенный феррит, резко снижающий твердость и прочность. Поэтому для доэвтектоидной стали обязательна полная закалка (нагрев выше точки Ас3).
В заэвтектоидной стали избыточной фазой является цементит, который по твердости не уступает мартенситу и даже превосходит его; поэтому сталь достаточно нагреть на 30—50° вьЛце точки Acv
Нагрев изделий (особенно крупных) должен производиться постепенно, чтобы избежать напряжений и трещин, а время выдержки нагретого изделия должно быть достаточным, чтобы весь процесс перехода перлита в аустенит полностью завершился. Продолжительность выдержки обычно устанавливается равной 25% общей продолжительности нагрева.
Охлаждение при закалке. Охлаждение деталей при закалке — самый ответственный элемент этой операции. Скорость охлаждения должна обеспечивать получение нужного для данной детали состояния: мартенсита, троостита или сорбита. Нам известно, при какой скорости охлаждения аустенита получаются эти состояния. Скорость, обеспечивающая получение структуры мартенсита (с остаточным аустенитом, но Лез троостита), называется критической скоростью закалки.
Так как С-образные кривые доэвтектоидной и заэвтектоидной сталей смещены влево по сравнению с кривыми эвтектоидной стали, критическая скорость закалки их выше, и получение структуры мартенсита более затруднительно, а для некоторых марок стали невозможно.
При скорости охлаждения меньше критической в структуре закаленной стали, наряду с мартенситом, будет находиться троостит, а при дальнейшем уменьшении»с^йрости получаются структуры троостита или сорбита без мартенсита.
Степень резкости закалки (получение структуры мартенсита без троостита) зависит от природы и температуры охлаждающей среды. Охлаждение струей воздуха или- холодными металлическими плитами дает слабую закалку на сорбит. Наиболее распространенным является охлаждение деталей путем погружения их в жидкую среду: воду, растворы щелочей или кислот, масло, расплавленный свинец и др. При этом получается резкая или умеренная закалка (на мартенсит или троостит).
Охлаждающая способность воды резко изменяется в зависимости от ее температуры; если эту способность при 18° принять за единицу, то при 74° она будет иметь коэффициент 0,05.
К наиболее резким охладителям относится 10-процентный раствор NaOH в воде, имеющий при 18° коэффициент 2,0, к умеренным — минеральные масла с коэффициентом 0,2—0,25.
При закалке применяются различные приемы охлаждения в зависимости от марки стали, формы и размеров детали и технических требований к готовой детали.
Простая закалка в одном охладителе выполняется путем погружения детали в охладитель (чаще всего в воду или водные растворы), где она остается до полного охлаждения. При охлаждении необходимо освобождаться от слоя пара (паровой рубашки), производя энергичные движения детали в ванне, так как этот слой уменьшает скорость ее охлаждения. Такой способ закалки наиболее распространен.
Для получения высокой твердости и наибольшей глубины закалки углеродистой стали применяют душевое охлаждение, которое заключается в интенсивном обрызгивании.
Прерывистая закалка — это такая закалка, при которой охлаждение производится в двух средах: первой средой является охлаждающая жидкость (обычно вода), второй — воздух или масло. Резкость такой закалки меньше, чем предыдущей.
При ступенчатой закалке деталь быстро охлаждают в расплавленной соли до температуры несколько выше Мн, делают короткую выдержку и далее охлаждают на воздухе. Выдержка обеспечивает выравнивание температуры поверхности и сердцевины детали, что уменьшает величину напряжений при мартенситном превращении.
Способ погружения деталей в закалочную ванну должен быть таким, чтобы при закалке детали как можно меньше деформировались (коробились). Детали с большим отношением длины к диаметру или ширине (напильники, сверла и др.) следует погружать в охладитель вертикально.
Изотермическая закалка. Изотермическая закалка (закалка в горячих средах) основана на изотермическом распадении аустенит; она отличается тем, что охлаждение ведется не до комнатной температуры, а до температуры несколько выше начала мартенситного превращения (200—300°, в зависимости от марки стали). В качестве охладителя берутся расплавленные соли или нагретое до 200—250° масло. При температуре горячей ванны деталь выдерживается продолжительное время, пока пройдут инкубационный период и распадение аустенита; в результате получается структура игольчатого троостита, по твердости близкого к мартенситу, но более вязкого и прочного.
Последующее охлаждение до комнатной температуры производится на воздухе.
При изотермическои закалке вначале требуется быстрое охлаждение со скоростью не меньше критической, чтобы избежать распадения аустенита в месте перегиба С-образной кривой.
Следовательно, по этому методу можно закаливать только небольшие (в среднем, диаметром до 8 мм) детали из углеродистой стали, так как запас теплоты в более массивных деталях не позволит получить необходимой скорости охлаждения. Это не относится, однако, к большинству марок легированной стали, которая имеет значительно меньшую критическую скорость закалки. Большим преимуществом изотермической закалки является возможность рихтовки (исправление искривлений) изделий во время инкубационного периода распадения аустенита (который длится несколько минут), когда сталь еще мягка и пластична. После изотермической закалки детали свободны от внутренних напряжений и не имеют трещин.
Виды поверхностной закалки. При поверхностной закалке выше критической температуры нагревается только тонкий поверхностный слой детали, а внутренняя масса металла не нагревается и не закаливается. Поэтому получаются детали с твердым поверхностным слоем и вязкой сердцевиной.
Кислородно-ацетиленовое пламя газовой горелки, имеющее температуру около 3200°, направляется на поверхность закаливаемой детали и быстро нагревает ее до температуры выше критической. Вслед за горелкой из трубки на поверхность детали направляется струя воды, в результате чего нагретый слой стали закаливается. Этим способом достигается большая поверхностная твердость при вязкой сердцевине; он с успехом применяется, например, для закалки рабочих поверхностей зубьев больших шестерен, подверженных сильному износу.
Закалка токами высокой частоты по методу В. П. Вологдина нашла очень широкое применение в промышленности, так как отличается высокой производительностью, легко поддается регулированию и обеспечивает хорошее качество.
Закаливаемая деталь помещается в специальный индуктор (катушку), по которому пропускается ток высокой частоты. Ток поступает через трансформатор от машинного генератора, приводимого во вращение электродвигателем. Индуктирующийся (возбуждаемый) при этом в детали ток имеет наибольшую плотность у поверхности и производит сильный и быстрый нагрев поверхности детали. Когда нагрев закончен, на поверхность детали подается вода из индуктора, коюрый для этого делается полым и имеет отверстия, направленные к детали. Для улучшения коэффициента мощности установки включены конденсаторы.
Регулируя мощность тока и время выдержки, можно получить нагрев на толщину от долей миллиметра до десятков миллиметров.
Машинные генераторы обычно применяются для закалки на глубину свыше 2 мм они генерируют ток частотой до 10 000 гц . При закалке на глубину меньше 2 мм применяются высокочастотные ламповые генераторы, создающие ток весьма высокой частоты, которая может регулироваться в зависимости от особенностей закаливаемых деталей.
Обработка холодом. Обработка холодом — новый вид термической обработки. Этот метод разработан в Советском Союзе (работы С. С. Штейнберга, А. П. Гуляева и Н. А. Минкевича).
Рис. 2. Схема заАлки с помощью газовой горелки
Обработка холодом применяется для углеродистой стали, содержащей более 0,5% С, у которой точка Мк находится ниже 0°, а также для легированной стали, например, быстрорежущей.
Отпуск стали. Целью .операции отпуска является смягчение действия закалки — уменьшение или снятие остаточных напряжений, повышение вязкости, уменьшение твердости и хрупкости стали. Отпуск производится путем нагрева деталей, закаленных на мартенсит, до температуры ниже критической. При этом в зависимости от температуры нагрева могут быть получены состояния мартенсита, троостита или сорбита отпуска. Эти состояния несколько отличаются от соответственных состояний закалки по структуре и свойствам: при закалке цементит (в троостите и сорбите) получается в форме удлиненных пластинок, как в пластинчатом перлите, а при отпуске он получается в форме зернышек, или точек, как в зернистом перлите. Преимущества точечной структуры заключаются в более благоприятном сочетании прочностных и пластических свойств. При одинаковом химическом составе и одинаковой твердости точечная структура имеет значительно более высокое относительное сужение (4>) и ударную вязкость (ан), повышенное удлинение (6) и предел текучести (стг) по сравнению с пластинчатой структурой.
Рис. 3. Схема индукционной закалки
Мартенсит закалки имеет неустойчивую тетрагональную решетку, а мартенсит отпуска — устойчивую центрированную кубическую решетку а-железа.
Отпуск разделяют на низкий, средний и высокий в зависимости от температуры нагрева.
При низком отпуске (нагрев до температуры 200—300°) в структуре стали в основном остается мартенсит, который, однако, изменяет решетку. Кроме того, начинается выделение карбидов железа из твердого раствора углерода в а-железе и начальное скопление их в небольшие группы, что влечет за собой некоторое уменьшение твердости и увеличение пластических и вязких свойств стали, а также уменьшение внутренних напряжений в деталях.
Низкий отпуск обычно производят в масляных или соляных ваннах, где детали выдерживаются в течение определенного времени. Если низкий отпуск производится в атмосфера воздуха, то для контроля температуры нагрева часто пользуются цветами, появляющимися на поверхности детали. Появление этих цветов связано с интерференцией белого света в пленках окислов железа, возникающих на поверхности детали при ее нагреве. В интервале температур от 220 до 330° в зависимости от толщины пленки цвет изменяется от светло-желтого до серого.
Низкий отпуск применяется для режущего, измерительного инструмента, зубчатых колес.
При среднем (нагрев в пределах 300—500°) и высоком (500—700°) отпуске сталь из состояния мартенсита переходит соответственно в состояние троостита или сорбита. Чем выше отпуск, тем меньше твердость отпущенной стали и тем больше ее пластичность и вязкость. Происходящее при этом изменение свойств стали можно проследить по кривым диаграммы, приведенной на рис. 83. При высоком отпуске сталь получает наилучшее сочетание механических свойств — повышенные прочность, пластичность и вязкость, поэтому высокий отпуск стали после закалки ее на мартенсит называют улучшением стали.
Средний отпуск применяется при производстве кузнечных штампов, пружин, рессор; высокий — для многих деталей, подверженных действию высоких напряжений (например, осей автомобилей, шатунов двигателей).
Для некоторых марок стали отпуск производят после нормализации. Это относится к мелкозернистой легированной доэвтектоидной стали (особенно никелевой), имеющей высокую вязкость и поэтому плохую обрабатываемость режущим инструментом. Для улучшения обрабатываемости производят нормализацию стали при повышенной температуре (до 950—970°), в результате чего она приобретает крупную структуру (определяющую лучшую обрабатываемость) и одновременно повышенную твердость (ввиду малой критической скорости закалки никелевой стали). С целью уменьшения твердости производят высокий отпуск этой стали.
Дефекты закалки. Дефектами закалки являются трещины, поводка или коробление и обезуглероживание.
Главная причина трещин и поводки — неравномерное изменение объема детали при нагреве и особенно при резком охлаждении; другая причина — увеличение объема при закалке на мартенсит.
Трещины являются результатом того, что напряжения, возникающие при неравномерном изменении объема в отдельных местах детали, превышают прочность металла в этих местах.
Наиболее эффективным способом уменьшения напряжений является медленное охлаждение у точки мартенситного превращения (точка Мн). При конструировании деталей необходимо учитывать, что наличие острых углов и резких изменений сечения увеличивает внутренние напряжения* вызываемые закалкой.
Коробление (или поводка) возникает также от напряжений в результате неравномерного охлаждения и Проявляется в искривлениях деталей. Если эти искривления невелики, они могут быть исправлены дальнейшей обработкой (шлифованием). Трещины и коробление могут быть предотвращены предварительным отжигом деталей, равномерным и постепенным нагревом их, а также применением ступенчатой и изотермической закалки.
Обезуглероживание стали с поверхности — результат выгорания углерода при высоком и продолжительном нагреве детали в окислительной среде. Для предотвращения обезуглероживания нагрев деталей нужно производить в восстановительной или нейтральной среде (восстановительное пламя, муфельные печи, нагрев в жидких средах).
Читать далее:
Печи для термической обработки
Статьи по теме:
pereosnastka.ru
отжиг, закалка, отпуск и нормализация
Для придания стальным заготовкам особых свойств выполняют термическую обработку. Технология зависит от конечных параметров и свойств металла, его качества. На выбор вида термической обработки влияет марка стали, требуемые эксплуатационные характеристики конечного изделия.
Виды отжигов
Суть процесса заключается в нагреве металлического изделия и последующего медленного охлаждения. В результате этого улучшается показатель вязкости, достигается химическая и структурная однородность. Термическая обработка методом отжига негативно влияет на жесткость стали.
В зависимости от требуемых качеств изделия выполняют такие виды отжига:
- Диффузионный. Цель обработки – уменьшение химической неоднородности состава. Сначала сталь нагревают до температуры +1150°С и в таком состоянии заготовка остается 10-15 часов. Затем выполняют медленное (естественное) охлаждение.
- Полный. Она выполняется для штамповочных изделий или заготовок, сделанных методом литья или ковки. Цель – формирование мелкозернистой структуры. Сталь нагревается до температуры, превышающей значение критической верхней точки на +50°С. Затем происходит медленное охлаждение со скоростью не более 75°С (для легированных сортов) или +200°С (для углеродистых марок) в час.
- Неполный отжиг. Термическая обработка применяется для уменьшения показателя жесткости и снятия напряжения структуры. Технология аналогична вышеописанной, за исключением значения максимальной температуры. Она не должна превышать +750°С.
- Изотермический. Он актуален только для легированных сортов стали. Температура воздействия выше критической точки на 20-30%. Отличия от полного отжига – быстрое охлаждение до +600°С. Методика применяется для оперативной обработки стальных заготовок.
Для выполнения этих процедур необходимо специальное оборудование. Качество обработки зависит от выполняемых требований. В случае несоблюдения технологии велика вероятность появления дефектов – пережог.
Закалка
Методика актуальна для создания неравномерной структуры стали заготовки. Это увеличивает твердость, но также повышает хрупкость конструкции. Выбор температуры воздействия зависит от химического состава. Также важными являются скорость охлаждения и периодичность повторения процедуры.
При выборе технологии закаливания учитывают следующие факторы:
- Температура обработки. Если она не превышает критическое значение – закалка относится к категории неполной. Для обработки всей структуры заготовки термическое воздействие должно быть выше точки Асз на 30-40°.
- Охлаждение. Оно может выполняться быстро или медленно. В первом случае твердость неравномерная, ближе к поверхности. При медленном охлаждении напряжение структуры выравнивается.
- Выбор среды для закалки. Чаще всего используют соляную ванную или масло с добавлением специальных веществ.
- Периодичность. Она влияет на распределение жесткости в структуре стали.
Способы закалки рассчитываются индивидуально для каждого типа изделия. О том, как закаливать и делать отпуск металла в домашних условиях, читайте здесь.
Отпуск
Для нормализации характеристик стальных заготовок после закалки рекомендуется делать ее отпуск. Его суть заключается в термическом воздействии температурами, при которых не происходит фазового превращения. Итогом этой операции будет однородность структуры стали.
Виды отпуска для металлических заготовок:
- Низкий. Применяется для углеродистых сортов стали. Максимальная температура воздействия — +200°С. В результате уменьшается показатель хрупкости и снижается натяжение в структуре.
- Средний. Термическая обработка происходит при +400°С. Технология необходима для удаления избыточного углерода. При этом кристаллическая решетка становится кубической.
- Высокий. Температура обработки – до +650°С. Применяется для появления оптимальных характеристик прочности, вязкости и пластичности.
Определяющим показателем для этого процесса является отпускная хрупкость. Она указывает на степень падения ударной вязкости при резких перепадах температур.
Нормализация металлических заготовок
Технология схожа с отжигом стали. Разница заключается в способе охлаждения заготовки. Это происходит не в печи, как в первом случае, а на воздухе. В результате происходит нормализация структуры кристаллической решетки, повышаются показатели прочности и вязкости.
При выполнении этого процесса учитывают такие показатели:
- Выдержка. Она характеризует степень равномерного термического воздействия на все слои стальной заготовки.
- Скорость охлаждения. Влияет на толщины перлитных пластин.
- Поэтапное охлаждение. В некоторых случаях после достижения определенного уровня снижения температуры деталь помещают в масло для оперативного охлаждения.
Для появления нужных свойств стальной заготовки могут выполняться несколько типов термической обработки.
ismith.ru
Закалка и отпуск стали — Мегаобучалка
Превращения в стали при охлаждении. При медленном охлаждении стали образуются структуры, соответствующие диаграмме Fе-Fе3C. Вначале происходит выделение феррита (в доэвтектоидных сталях) или вторичного цементита (в заэвтектоидных сталях), а затем происходит превращение аустенита в перлит. Это превращение заключается в распаде аустенита на феррит, почти не содержащий углерода и цементит, содержащий 6,67 % С. Поэтому превращение сопровождается диффузией, перераспределением углерода. Диффузионные процессы происходят в течение некоторого времени, причем скорость диффузии резко падает с понижением температуры. Обычно изучают изотермическое превращение аустенита (происходящее при выдержке при постоянной температуре) для эвтектоидной стали. Влияние температуры на скорость и характер превращения представляют в виде диаграммы изотермического превращения аустенита (рис. 16).
Диаграмма строится в координатах температура — логарифм времени. Выше температуры 72 °С на диаграмме находится область устойчивою аустенита. Ниже этой температуры аустенит является неустойчивым и превращается в другие структуры. Первая С - образная кривая на диаграмме соответствует началу превращения аустенита, а вторая — его завершению. При небольшом переохлаждении — приблизительно до 550 °С происходит упомянутое выше диффузионное перлитное превращение.
В зависимости от степени переохлаждения образуются структуры, называемые перлит, сорбит и тростит. Это структуры одного типа — механические смеси феррита и цементита, имеющие пластинчатое строение. Отличаются они лишь степенью дисперсности, т. е. толщиной пластинок феррита и цементита. Наиболее крупнодисперсная структура — перлит, наиболее мелкодисперсная — тростит. При переохлаждении аустенита приблизительно ниже 240 °С скорость диффузии падает почти до нуля и происходит бездиффузионное мартенситное превращение. Образуется мартенсит — пересыщенный твердый раствор углерода в α - железе. Мартенсит имеет ту же концентрацию углерода, что и исходный аустенит. Из-за высокой пересыщенности углеродом решетка мартенсита сильно искажается, благодаря чему мартенсит имеет высокую твердость (до НRС 65). Горизонтальная линия Мн диаграммы соответствует началу .превращения аустенита в мартенсит, а линия Мк — завершению этого процесса.
В диапазоне температур от мартенситного до перлитного превращения происходит промежуточное превращение и образуется структура, называемая бейнит.
Закалка — это вид термической обработки, состоящий в нагреве стали до определенной температуры, выдержке и последующем быстром охлаждении. В результате закалки повышается твердость и прочность, но снижается вязкость и пластичность. Нагрев стали производится на 30…50 °С выше линии GSK диаграммы Fе-Fе3С. В доэвтектоидных сталях нагрев выше линии GS необходим для того, чтобы после закалки в структуре не было мягких ферритных включений. Для заэвтектоидных сталей применяется нагрев выше линии SК, так как присутствие цементита не снижает твердость стали.
Обычно в результате закалки образуется мартенситная структура. Поэтому охлаждать сталь следует с такой скоростью, чтобы кривая охлаждения не пересекала С- образные кривые диаграммы изотермического превращения аустенита (рис. 16). Для достижения высокой скорости охлаждения закаливаемые детали погружают в воду (для углеродистых сталей) или минеральные масла (для легированных сталей).
Способность стали закаливаться на мартенсит называется закаливаемостью. Она характеризуется значением твердости, приобретаемой сталью после закалки и зависит от содержания углерода. Стали с низким содержанием углерода (до 0,3 %) практически не закаливаются и закалка для них не применяется.
Прокаливаемостью называется глубина проникновения закаленной зоны. Отсутствие сквозной прокаливаемости объясняется тем, что при охлаждении сердцевина остывает медленнее, чем поверхность. Прокаливаемость характеризует критический диаметр Dкр, т. е. максимальный диаметр детали цилиндрического сечения, которая прокаливается насквозь в данном охладителе.
Отпуск стали — это вид термической обработки, следующий за закалкой и заключающийся в нагреве стали до определенной температуры (ниже линии РSК), выдержке и охлаждении. Цель отпуска — получение более равновесной по сравнению с мартенситом структуры, снятие внутренних напряжений, повышение вязкости и пластичности. Различают низкий, средний и высокий отпуск.
Низкий отпуск проводится при температуре 150…200 °С. В результате снимаются внутренние напряжения, происходит некоторое увеличение пластичности и вязкости без заметного снижения твердости. Образуется структура мартенсит отпуска. Низкому отпуску подвергают режущий и мерительный инструмент, а также детали, которые должны обладать высокой твердостью и износостойкостью.
При среднем отпуске производится нагрев до 350…450 °С. При этом происходит некоторое снижение твердости при значительном увеличении предела упругости и улучшении сопротивляемости действию ударных нагрузок. Структура стали представляет собой тростит отпуска, который имеет зернистое, а не пластинчатое строение. Применяется для пружин, рессор, ударного инструмента.
Высокий отпуск проводится при 550…650 °С. В результате твердость и прочность снижаются значительно, но сильно возрастают вязкость и пластичность и получается оптимальное для конструкционных сталей сочетание механических свойств. Структура стали — сорбит отпуска с зернистым строением цементита. Применяется для деталей, подвергающихся действию высоких нагрузок. Термическая обработка, состоящая из закалки и высокого отпуска, называется улучшением. Она является основным видом обработки конструкционных сталей.
megaobuchalka.ru
Закалка и отпуск стали |
Целью закалки и отпуска стали является повышение твердости и прочности. Закалка и отпуск стали необходимы для очень многих деталей и изделий. Закалка основана на перекристаллизации при нагреве и предотвращении перехода аустенита в перлит путем быстрого охлаждения. Закаленная сталь имеет неравновесную структуру мартенсита, троостита или сорбита.
Чаще всего сталь резко охлаждают на мартенсит. Для смягчения действия закалки сталь отпускают, нагревая до температуры ниже точки А1. При отпуске структура стали из мартенсита закалки переходит мартенсит отпуска, троостит отпуска, сорбит отпуска.
Закалка стали. Температура нагрева стали при закалке та же, что и при полном отжиге: для доэвтектоидной стали на 30—50 °С выше точки Ас3, для заэвтектоидной — на 30—50° выше точки Aс1. При нагреве доэвтектоидной стали до температуры между точками Ас1и Ac3(неполная закалка) в структуре быстро охлажденной стали наряду с закаленными участками будет присутствовать нерастворенный при нагреве (в аустените) феррит, резко снижающий твердость и прочность. Поэтому для доэвтектоидной стали обязательна полная закалка с нагревом выше точки Ас3.
В заэвтектоидной стали избыточной фазой является цементит, который по твердости не уступает мартенситу и даже превосходит его, поэтому сталь достаточно нагреть на 30—50 °С выше точки Ас1.
Нагревать заготовки, особенно крупные, нужно постепенно во избежание местных напряжений и трещин, а время выдержки нагретых заготовок должно быть достаточным, чтобы переход в структуру аустенита полностью завершился.
Скорость охлаждения заготовок при закалке должна быть такой, чтобы получить заданную структуру. Критическая скорость закалки изменяется в широких пределах в зависимости от наличия легирующих компонентов в стали. Для простых сплавов железо—углерод эта скорость очень высока. Присутствие в стали кремния и марганца облегчает закалку на мартенсит, так как для такой стали С-образные кривые на диаграмме изотермического превращения аустенита будут сдвинуты вправо и критическая скорость закалки понижается.
Наиболее распространено охлаждение заготовок погружением их в воду, в щелочные растворы воды, в масло, расплавленные соли и т. д. При этом сталь закаливается на мартенсит или на бейнит.
При закалке применяют различные способы охлаждения в зависимости от марки стали, формы и размеров заготовки.
Простую закалку в одном охладителе (чаще всего в воде или водных растворах) выполняют, погружая в него заготовки до полного охлаждения. На рис. 1 режим охлаждения при такой закалке характеризует кривая 1. Для получения наибольшей глубины закаленного слоя применяют охлаждение при интенсивном обрызгивании. Прерывистой закалкой называют такую, при которой заготовку охлаждают последовательно в двух средах: первая среда — охлаждающая жидкость (обычно вода), вторая — воздух или масло (см. кривую 2 на рис. 1). Резкость такой закалки меньше, чем предыдущей.
При ступенчатой закалке заготовку быстро погружают в соляной расплав и охлаждают до температуры несколько выше Мн. Выдержка обеспечивает выравнивание температуры от поверхности к сердцевине заготовки, что уменьшает напряжения, возникающие при мартенситном превращении; затем заготовку охлаждают на воздухе (кривая 3 на рис. 1).
Изотермическая закалка (закалка в горячих средах) основана на изотермическом распаде аустенита. Охлаждение ведется до температуры несколько выше начала мартенситного превращения (200—300 °С) в зависимости от марки стали. В качестве охладителя используют соленые расплавы или масло, нагретое до 200—250 °С. При температуре горячей ванны заготовка выдерживается продолжительное время, пока пройдет инкубационный период и период превращения аустенита (кривая 4 на рис. 1). В результате получается структура бейнита, по твердости близкая к мартенситу, но более вязкая и пластичная. Последующее охлаждение производится на воздухе.
При изотермической закалке вначале требуется быстрое охлаждение со скоростью не менее критической, чтобы избежать распад аустенита. Следовательно, по этому методу можно закаливать лишь небольшие (диаметром примерно до 8 мм) заготовки из углеродистой стали, так как массивные заготовки не удается быстро охладить. Это не относится однако к легированным сталям, большинство марок которых имеют значительно меньшие критические скорости закалки. Большим преимуществом изотермической закалки является возможность рихтовки (выправления искривлений) заготовок во время инкубационного периода превращения аустенита (который длится несколько минут), когда сталь еще пластична.
Закалка при помощи газовой горелки. Кислородно-ацетиленовое пламя газовой горелки с температурой около 3200 °С направляется на поверхность закаливаемой заготовки и быстро нагревает ее поверхностный слой до температуры выше критической. Вслед за горелкой перемещается трубка, из которой на поверхность заготовки направляется струя воды, закаливая нагретый слой. Этот способ применяется для изделий с большой поверхностью (например, для прокатных валков, зубьев больших шестерен и т. д.).
Обработка холодом. Этот метод применяется для повышения твердости стали путем перевода остаточного аустенита закаленной стали в мартенсит. Холодом обрабатывают углеродистую сталь, содержащую больше 0,5 % С, у которой температура конца мартенситного превращения находится ниже 00 С, а также легированную сталь (например, быстрорежущую).
Отпуск стали. Отпуск смягчает действие закалки, снимает или уменьшает остаточные напряжения, повышает вязкость, уменьшает твердость и хрупкость стали. Отпуск производится путем нагрева заготовок до температуры ниже критической; при этом в зависимости от температуры могут быть получены структуры мартенсита, троостита или сорбита отпуска.
При низком отпуске (нагрев до температуры 150—200 °С) в структуре стали в основном остается мартенсит, который однако имеет другую решетку, как сказано выше. Кроме того, начинается выделение карбидов железа из пересыщенного твердого раствора углерода в a-железе и начальное скопление их небольшими группами. Это влечет за собой некоторое уменьшение твердости и увеличение вязкости стали, а также уменьшение внутренних напряжений в заготовках. Для низкого отпуска, заготовки выдерживают в течение определенного времени обычно в масляных или солевых ваннах. Если для низкого отпуска заготовки нагревают в атмосфере воздуха, то для контроля температуры часто пользуются цветами побежалости, появляющимися на зачищенной поверхности заготовки. Появление этих цветов связано с интерференцией белого цвета в пленках оксида железа, возникающих на поверхности заготовки при ее нагреве. Для углеродистой стали в интервале температур от 220 до 330 °С в зависимости от толщины пленки цвет изменяется от светло-желтого до серого. Для легированной стали соответствующие температуры выше. Низкий отпуск применяют для режущего инструмента из углеродистых и легированных сталей, измерительного инструмента, цементированных заготовок, а также других изделий, работающих в условиях трения на износ.
При среднем (нагрев в пределах 300—500 °С) и высоком (500—700 °С) отпуске структура мартенсита переходит соответственно в структуру троостита или сорбита. Чем выше температура отпуска, тем меньше твердость отпущенной стали и тем больше ее вязкость. При высоком отпуске сталь получает наилучшее сочетание механических свойств: повышенные прочность, вязкость и пластичность; поэтому закалку на мартенсит с последующим высоким отпуском называют улучшением стали. Средний отпуск применяют при производстве кузнечных штампов, пружин, рессор, а высокий—для многих деталей, подверженных действию высоких напряжений (например, осей автомобилей, шатунов двигателей).
ndt-welding.com
Термическая обработка металлов
вернуться на главную страницу оборудования для термической обработки металлов
Термическая обработка (термообработка) стали, сплавов бывает следующих видов: отжиг, нормализация, закалка, отпуск.
- Отжиг - термическая обработка (термообработка) металла, при которой производится нагревание металла, а затем медленное охлаждение. Эта термобработка (т.е. отжиг) бывает разных видов (вид отжига зависит от температуры нагрева, скорости охлаждения металла).
- Закалка - термическая обработка (термообработка) стали, сплавов, основанная на перекристаллизации стали (сплавов) при нагреве до температуры выше критической; после достаточной выдержки при критической температуре для завершения термической обработки следует быстрое охлаждение. Закаленная сталь (сплав) имеет неравновесную структуру, поэтому применим другой вид термообработки - отпуск.
- Отпуск - термическая обработка (термообработка) стали, сплавов, проводимая после закалки для уменьшения или снятия остаточных напряжений в стали и сплавах, повышающая вязкость, уменьшающая твердость и хрупкость металла.
- Нормализация - термическая обработка (термообработка), схожая с отжигом. Различия этих термобработок (нормализации и отжига) состоит в том, что при нормализации сталь охлаждается на воздухе (при отжиге - в печи).
ОТЖИГ СТАЛИ
Отжиг - процесс термообработки металла, при котором производится нагревание, затем медленное охлаждение металла. Переход структуры из неравновесного состояния до более равновесного. Отжиг первого рода, его виды: возврат (он же отдых металла), рекристаллизационный отжиг (он же называется рекристаллизация), отжиг для снятия внутренних напряжений, диффузионный отжиг (еще называется гомогенизация). Отжиг второго рода – изменение структуры сплава посредством перекристаллизации около критических точек с целью получения равновесных структур. Отжиг второго рода, его виды: полный, неполный, изотермический отжиги. Ниже рассмотрен отжиг, его виды, применительно к стали.
- Возврат (отдых) стали – нагрев до 200 – 400C°, отжиг для уменьшения или снятия наклепа. По результатам отжига наблюдается уменьшение искажений кристаллических решеток у кристаллитов и частичное восстановление физико-химических свойств стали.
- Рекристаллизационный отжиг стали (рекристаллизация) - нагрев до температур 500 – 550C°; отжиг для снятия внутренних напряжений – нагрев до температур 600 – 700C°. Эти виды отжига снимают внутренние напряжения металла отливок от неравномерного охлаждения их частей, также в заготовках, обработанных давлением (прокаткой, волочением, штамповкой) с использованием температур ниже критических. Вследствиии рекристаллизационного отжига из деформированных зерен вырастают новые кристаллы, ближе к равновесным, поэтому твердость стали снижается, а пластичность, ударная вязкость увеличиваются. Чтобы полностью снять внутренние напряжения стали нужна температура не менее 600C°. Охлаждение после выдержки при заданной температуре должно быть достаточно медленным: вследствии ускоренного охлаждения металла вновь возникают внутренние напряжения.
- Диффузионный отжиг стали (гомогенизация) применяется тогда, когда сталь имеет внутрикристаллическую ликвацию. Выравнивание состава в зернах аустенита достигается диффузией углерода и других примесей в твердом состоянии, наряду с самодиффузией железа. По результатам отжига, сталь становится однородной по составу (гомогенной), поэтому диффузионный отжиг называет также гомогенизацией. Температура гомогенизации должна быть достаточно высокой, однако нельзя допускать пережога, оплавления зерен. Если допустить пережог, то кислород воздуха окисляет железо, проникая в толщу его, образуются кристаллиты, разобщенные окисными оболочками. Пережог устранить нельзя, поэтому пережженные заготовки являются окончательным браком. Диффузионный отжиг стали обычно приводит к слишком сильному укрупнению зерна, что следует исправлять последующим полным отжигом (на мелкое зерно).
- Полный отжиг стали связан с фазовой перекристаллизацией, измельчением зерна при температурах точек АС1 и АС2. Назначение его – улучшение структуры стали для облегчения последующей обработки резанием, штамповкой или закалкой, а также получение мелкозернистой равновесной перлитной структуры готовой детали. Для полного отжига сталь нагревают на 30-50C°выше температуры линии GSK и медленно охлаждают. После отжига избыточный цементит (в заэвтектоидных сталях) и эвтектоидный цементит имеют форму пластинок, поэтому и перлит называют пластинчатым
- При отжиге стали на пластинчатый перлит заготовки оставляют в печи до охлаждения, чаще всего при частичном подогреве печи топливом, чтобы скорость охлаждения была не больше 10-20C° в час. Отжигом также достигается измельчение зерна. Крупнозернистая структура, например, доэвтектоидной стали, получается при затвердевании вследствие свободного роста зерен (если охлаждение отливок медленное), а также в результате перегрева стали. Эта структура называется видманштетовой (по имени австрийского астронома А. Видманштеттена, открывшего в 1808 г. такую структуру на метеорном железе). Такая структура придает низкую прочность заготовке. Структура характерна тем, что включения феррита (светлые участки) и перлита (темные участки) располагаются в виде вытянутых пластин под различными углами друг к другу. В заэвтектоидный сталях видманштетова структура характеризуется штрихообразным расположением избыточного цементита. Размельчение зерна связано с перекристаллизацией альфа-железа в гамма-железо; вследствии охлаждения и обратного переходе гамма-железа в aльфа-железо мелкозернистая структура сохраняется. Таким образом, одним из результатов отжига на пластинчатый перлит является мелкозернистая структура.
- Неполный отжиг стали связан с фазовой перекристаллизацией лишь при температуре точки А С1; неполный отжиг применяется после горячей обработки давлением, когда у заготовки мелкозернистая структура.
- Отжиг стали на зернистый перлит применяют обычно для эвтектоидных, заэвтектоидных сталей, для повышения пластичности, вязкости стали и уменьшения ее твердости. Для получения зернистого перлита сталь нагревают выше точки АС1, затем выдерживают недолго, чтобы цементит растворился в аустените не полностью. Затем сталь охлаждают до температуры несколько ниже Ar1, выдерживают при такой температуре несколько часов. При этом частицы оставшегося цементита служат зародышами кристаллизации для всего выделяющегося цементита, который нарастает округлыми (глобулярными) кристаллитами, рассеянными в феррите. Свойство зернистого перлита существенно отличаются от свойств пластинчатого в сторону меньшей твердости, но большей пластинчатости и вязкости. Особенно это относится к заэвтектоидной стали, где весь цементит (как эвтектоидный, так избыточный) получается в виде глобулей.
- Изотермический отжиг - после нагрева и выдержки сталь быстро охлаждают до температуры несколько ниже точки А 1, затем выдерживают при этой температуре до полного распадения аустенита на перлит, после чего охлаждают на воздухе. Применение изотермического отжига значительно сокращает время, а также повышает производительность. Например, обыкновенный отжиг легированной стали длится 13-15 ч, а изотермический – всего 4-7 ч.
ЗАКАЛКА СТАЛИ
Различают закалку с полиморфным превращением, для сталей, и закалку без полиморфного превращения, для большинства цветных металлов. Материал, подвергшийся закалке приобретает большую твердость, но становится хрупким, менее пластичным и вязким, если сделать большее количество повторов нагревание-охлаждение. Для снижения хрупкости и увеличения пластичности и вязкости, после закалки с полиморфным превращением применяют отпуск. После закалки без полиморфного превращения применяют старение. При отпуске имеет место некоторое снижение твердости и прочности материала.
В зависимости от температуры нагрева, закалку подразделяют на полную и неполную. В случае полной закалки материал нагревают на 30 - 50°С выше линии GS для доэвтектоидной стали и эвтектоидной, заэвтектоидная линия PSK, в этом случае сталь приобретает структуру аустенит и аустенит + цементит. При неполной закалке производят нагрев выше линии PSK диаграммы, что приводит к образованию избыточных фаз по окончании закалки. Неполная закалка, как правило, применяетсядля инструментальных сталей. Закалка снимается отпуском материала. В некоторых изделиях закалка выполняется частично, например при изготовлении японских катан, закалке подвергается только режущая кромка меча.
Закалочные среды
При закалке для переохлаждения аустенита до температуры мартенситного превращения требуется быстрое охлаждение, но не во всём интервале температур, а только в пределах 650-400 °C, то есть в том интервале температур в котором аустенит менее всего устойчив, быстрее всего превращается в феритно-цементитную смесь. Выше 650 °C скорость превращения аустенита мала, и поэтому смесь при закалке можно охлаждать в этом интервале температур медленно, но, конечно, не настолько, чтобы началось выпадение феррита или превращение аустенита в перлит.
Механизм действия закалочных сред (вода, масло, водополимерная закалочная среда (Термат), а также охлаждение деталей в растворах солей) следующий. В момент погружения изделия в закалочную среду вокруг него образуется плёнка перегретого пара, охлаждение происходит через слой этой паровой рубашки, то есть относительно медленно. Когда температура поверхности достигает некоторого значения (определяемого составом закаливающей жидкости), при котором паровая рубашка разрывается, то жидкость начинает кипеть на поверхности детали, и охлаждение происходит быстро.
Первый этап относительно медленного кипения называется стадией плёночного кипения, второй этап быстрого охлаждения - стадией пузырькового кипения. Когда температура поверхности металла ниже температуры кипения жидкости, жидкость кипеть уже не может, и охлаждение замедлится. Этот этап носит название конвективного теплообмена.
Способы закалки
- Закалка в одном охладителе — нагретую до определённых температур деталь погружают в закалочную жидкость, где она остаётся до полного охлаждения. Этот способ применяется при закалке несложных деталей из углеродистых и легированных сталей.
- Прерывистая закалка в двух средах — этот способ применяют при закалке высокоуглеродистых сталей. Деталь сначала быстро охлаждают в быстро охлаждающей среде (например воде), а затем в медленно охлаждающей (масло).
- Струйчатая закалка заключается в обрызгивании детали интенсивной струёй воды и обычно её применяют тогда, когда нужно закалить часть детали. При этом способе не образуется паровая рубашка, что обеспечивает более глубокую прокаливаемость, чем простая закалка в воде. Такая закалка обычно производится в индукторах на установках ТВЧ.
- Ступенчатая закалка — закалка, при которой деталь охлаждается в закалочной среде, имеющей температуру выше мартенситной точки для данной стали. При охлаждении и выдержке в этой среде закаливаемая деталь должна приобрести во всех точках сечения температуру закалочной ванны. Затем следует окончательное, обычно медленное, охлаждение, во время которого и происходит закалка, то есть превращение аустенита в мартенсит.
- Изотермическая закалка. В отличие от ступенчатой при изотермической закалке необходимо выдерживать сталь в закалочной среде столько времени, чтобы успело закончиться изотермическое превращение аустенита.
ОТПУСК СТАЛИ
Отпуск стали смягчает действие закалки, уменьшает или снимает остаточные напряжения, повышает вязкость, уменьшает твердость и хрупкость стали. Отпуск производится путем нагрева деталей, закаленных на мартенсит до температуры ниже критической. При этом в зависимости от температуры нагрева могут быть получены состояния мартенсита, троостита или сорбита отпуска. Эти состояния несколько отличаются от соответственных состояний закалки по структуре и свойствам: при закалке цементит (в троостите и сорбите) получается в форме удлиненных пластинок, как в пластинчатом перлите. А при отпуске он получается зернистым, или точечным, как в зернистом перлите.
Преимуществом точечной структуры является более благоприятное сочетание прочности и пластичности. При одинаковом химическом составе и одинаковой твердости сталь с точечной структурой имеет значительно более высокое относительное сужение y и ударную вязкость а н, повышенное удлинение d и предел текучести s т по сравнению со сталью с пластинчатой структурой.
Мартенсит закалки имеет неустойчивую тетрагональную решетку, а мартенсит отпуска – устойчивую центрированную кубическую решетку альфа-железа.
Отпуск разделяют на низкий, средний и высокий в зависимости от температуры нагрева.
Для определения температуры при отпуске изделия пользуются таблицей цветов побежалости. Тонкая пленка окисдов железа, придающая металлу различные быстро меняющиеся цвета - от светло-желтого до серого. Такая пленка появляется, если очищенное от окалины стальное изделие нагреть до 220C°; при увеличении времени нагрева или повышении температуры окисная пленка утолщается и цвет ее изменяется. Цвета побежалости одинаково проявляются как на сырой, так и на закаленной стали.
При низком отпуске (нагрев до температуры 200-300C°) в структуре стали в основном остается мартенсит, который, однако, изменяется решетку. Кроме того, начинается выделение карбидов железа из твердого раствора углерода в альфа-железе и начальное скопление их небольшими группами. Это влечет за собой некоторое уменьшение твердости и увеличение пластических и вязких свойств стали, а также уменьшение внутренних напряжений в деталях. Для низкого отпуска детали выдерживают в течение определенного времени обычно в масляных или соляных ваннах. Если для низкого отпуска детали нагревают на воздухе, то для контроля температуры часто пользуются цветами побежалости, появляющимися на поверхности детали. Появление этих цветов связано с интерференцией белого света в пленках окисла железа, возникающих на поверхности детали при ее нагреве. В интервале температур от 220 до 330C° в зависимости от толщины пленки цвет изменяется от светло-желтого до серого. Низкий отпуск применяется для режущего, измерительного инструмента и зубчатых колес.
При среднем (нагрев в пределах 300-500C°) и высоком (500-700C°) отпуске сталь из состояния мартенсита переходит соответственно в состояние троостита или сорбита. Чем выше отпуск, тем меньше твердость отпущенной стали и тем больше ее пластичность и вязкость. При высоком отпуске сталь получает наилучшее сочетание механических свойств, повышение таких показателей как прочность, пластичность и вязкость, поэтому высокий отпуск стали после закалки ее на мартенсит применяют для термической обработки кузнечным штампов, пружин, рессор, а высокий – для многих деталей, подверженных действию высоких напряжений (например, осей автомобилей, шатунов двигателей).
Для некоторых марок стали отпуск производят после нормализации. Этот относится к мелкозернистой легированной доэвтектоидной стали (особенно никелевой), имеющий высокую вязкость и поэтому плохую обрабатываемость режущим инструментом. Для улучшения обрабатываемости производят нормализацию стали при повышенной температуре (до 950-970C°), в результате чего она приобретает крупную структуру (определяющую лучшую обрабатываемость) и одновременно повышенную твердость (ввиду малой критической скорости закалки никелевой стали). С целью уменьшения твердости производят высокий отпуск этой стали.
НОРМАЛИЗАЦИЯ СТАЛИ
Нормализацией называют такой вид термической обработки, когда сталь нагревают на 30 - 50C° выше верхних критических температур Асз или Аст и после выдержки при этих температурах охлаждают на спокойном воздухе. Таким образом, от отжига нормализация отличается более быстрым охлаждением изделия (примерно в 2 раза).
Нормализация является более дешевой операцией, чем отжиг, так как печи используются только для нагрева и выдержки изделия при температуре нагрева, а охлаждение производится вне печи. Кроме того, нормализация ускоряет процесс термической обработки. Таким образом, отжиг выгодно заменять нормализацией. Однако это не всегда возможно, так как у некоторых сталей твердость после нормализации возрастает более значительно, чем при отжиге. Малоуглеродистые стали рекомендуется подвергать нормализации, так как у них практически отсутствует разница в свойствах после отжига и нормализации.
Стали, содержащие свыше 0,4% углерода, после нормализации получают повышенную твердость. Такие стали лучше отжигать. На практике и такие стали часто подвергают нормализации вместо отжига, а затем высокому отпуску при температурах 650 - 700C° для уменьшения твердости. Нормализацию применяют для получения мелкозернистой структуры в отливках и поковках, для устранения внутренних напряжений и наклепа, для подготовки структуры стали к закалке.
Для некоторых изделий нормализация является не предварительной, а окончательной операцией термической обработки. В этом случае после нормализации изделия подвергают высокому отпуску для снятия внутренних напряжений, образовавшихся при охлаждении изделия на воздухе.
www.metiz.com.tw