Как сделать пескоструйный аппарат своими руками. Чертеж пескоструйного аппарата
Как самому сделать пескоструйный аппарат: чертежи и советы
Ассортимент магазинов изобилует различными установками для очистки материала. Самый эффективный инструмент – пескоструй. Качественная пескоструйная установка будет стоить довольно дорого, даже дешёвые установки от $180, которые быстро изнашиваются и постоянно забиваются. Альтернативный вариант – аппарат пескоструйный самодельный. При обретении небольших навыков можно вручную создать установку, она будет значительно дешевле готового варианта.
Принцип работы пескоструйного аппарата
Пескоструй работает по элементарной системе. Если сравнить чертёж простого аппарата для пескоструйки и базовых моделей краскопульта, наблюдается сходность конструкции. Нагнетённый воздух проходит по воздухопроводам и увлекает материал для абразивной обработки. Небольшие крупинки с большой скоростью направляются на поверхность, выбивая из неё частички.
Пескоструй самодельный разработать можно, а вот создать компрессор будет весьма сложно. Чтобы создать установку достаточного качества, рекомендуется покупать заводской компрессор, у которого будет производительность от 500 л/мин. Для избегания разрушения от перегрева, в нём должна быть устроена система охлаждения. Мощность установки от 3 кВт.
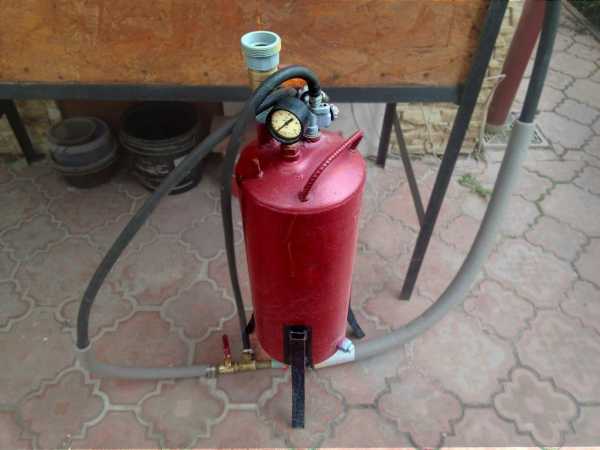
Самый простой аппарат – пескоструйный пистолет
Самодельная пескоструйка включает 2 основных элемента: рукоятку со специальным наконечником и 2 штуцера. Перед тем как сделать пескоструйный аппарат своими руками, рекомендуется купить сопло заводского производства. Через него выходит струя воздуха и абразивный материал. Вручную создать сопло приемлемого качества крайне сложно.
С учётом типа сопла изготавливают корпус, в дальнейшем с ним будет соединяться рукоятка и штуцеры. Простейший пескоструй своими руками изготавливают из фитингов водопроводного типа, пластиковой бутылки и тройника. Обязательно устраивается место для крепления шланга от компрессора со сжатым потоком воздуха.
Комплектующие для самодельной пескоструйной установки
Начинать создание пескоструйной установки следует с установки ёмкости, в ней будет находиться абразивное вещество. Удобно использовать в качестве резервуара отработанный баллон для хранения газа. Он изготавливается из прочного, высококачественного металла, рассчитанного на большие нагрузки. Баллон герметичный, соответственно, в него сложно вносить абразивное вещество. Для облегчения процесса сверху вваривается небольшой кусок трубы. В неё засыпают материал, через горловину он попадает внутрь.
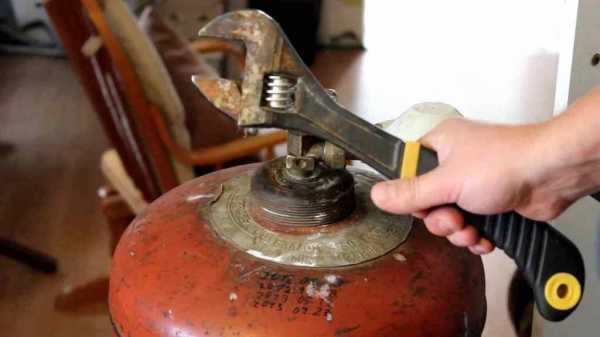
Важно с осторожностью разбирать ёмкость, так как в старых газовых баллонах чаще всего есть остаток газа.
Наибольшее влияние на качество пескоструя оказывает правильный выбор компрессора. Основная проблема – дороговизна такой установки. Заводские варианты с достаточной мощностью обойдутся дорого, снижая эффект экономии. Альтернативный вариант – сделать своими руками из недорогих комплектующих.
Собрать устройство в домашних условиях можно с помощью компрессорных головок, устанавливаемых на пневмопривод ЗИЛа или МАЗа. Мощности установки с указанными комплектующими будет достаточно для обработки любых автомобильных запчастей. Головки обязательно комплектуются ресивером. Для сокращения расходов его изготавливают из баллона для хранения сжиженного газа. Дополнительно потребуется электрический мотор с приводом и рама для крепления всех элементов.
Перед тем как самому сделать пескоструйный аппарат, следует подготовить:
- краны шарового типа. Они надёжны и долговечны, для уверенности в качестве рекомендуется покупать изделия известных производителей;
- шланг из резины с армированной вставкой от Ø14 мм. Важно покупать прочный вариант, который способен выдержать повышенное давление и влияние абразива;
- шланг для подачи газа. По нему будет поступать воздух в сжатом состоянии. В месте его установки мелкие крупицы отсутствуют, следовательно, диаметр меньше – от 10 мм;
- штуцеры для фиксации шлангов с другими компонентами системы. Пригодятся и цанговые зажимы;
- ФУМ-лента – она будет использована для создания целостного соединения всей конструкции установки, особенно участков, работающих под давлением.
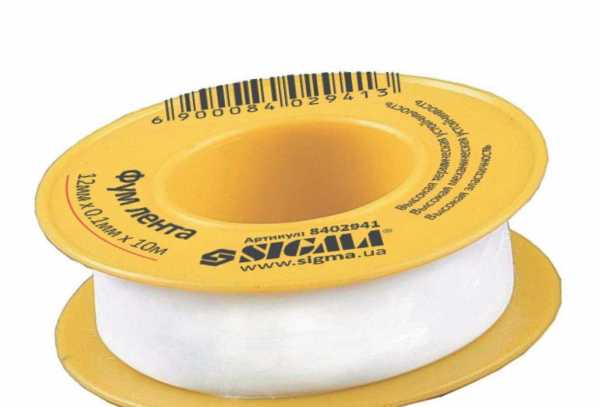
Подобная пескоструйка своими руками без компрессора обойдётся около $35. Экономия существенная, позволяет сохранить большую часть стоимости нового аппарата. Теперь следует переходить к созданию самодельной пескоструйки.
Пескоструйная камера
Если пескоструить большие детали, появляется проблема – быстрый расход абразива, большая его часть используется неэффективно, так как разлетается в стороны. Увеличить эффективность прибора позволит особая камера, которая имеет вид ящика, сваренного из металлических листов. Конструкция удобна для обработки небольших деталей автомобиля.
Изготовление камеры является затратной процедурой с точки зрения времени и сил, но оборудование реально сделать даже без особых навыков. Помимо простой конструкции сварного блока, в корпусе устанавливается стекло для контроля над процессом. Спереди просверливается 2 отверстия, к ним фиксируются перчатки несъёмного и грубого типа. Дно изготавливают из решётчатого металла или проволоки. Под дном размещают желоб для отвода использованного материала. Пистолет находится внутри. Для облегчения работ с камерой в неё устанавливают освещение и вентиляцию.
Готовое изделие устанавливают на стол. Инструкция по проведению работ раскрыта в видеороликах в сети.
Пескоструйные аппараты напорного типа
Специалистами разработана схема самодельной напорной установки. Для выполнения работ пригодится бочка из металла, с которой срезается днище. Внутрь устанавливают конус, а снизу крепят затвор и тройник для подключения компрессорного шланга и рукава с соплом.
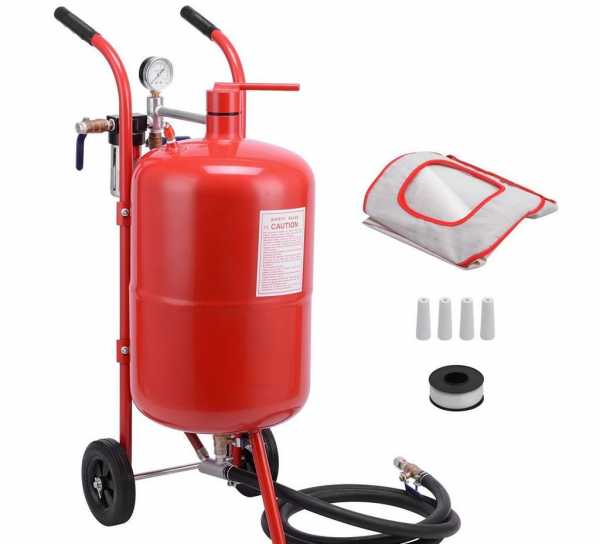
Гравирование стекла с помощью пескоструйного аппарата
Самый простой способ – использовать обдувочный аппарат с абразивом. Процесс выполняется пошагово:
- Изначально на стеклянную поверхность наносят самоклейку.
- На плёнке рисуют желаемое очертание или рисунок и с помощью строительного ножа вырезают его.
- Незащищённую поверхность обрабатывают пескоструем.
- Плёнка демонтируется, оставляя только выделенное изображение. Оно должно получиться ярким и чётко различимым.
Мастер вручную регулирует желаемую глубину рисунка, по необходимости обрабатывает поверхность 2-3 раза. Даже в подобном виде гравировка придаёт интересный и оригинальный вид, но по желанию к ней добавляют светодиодную ленту. Если сравнивать обычную пескоструйку и профессиональное оборудование, принципиальной разницы видно не будет.
Самый простой аппарат в силах вырезать отверстия в стекле, но для чёткой формы прорези потребуется оградить участок с помощью металла. В листе прорезают отверстие и накладывают на обрабатываемую поверхность. Прорезь внутри является формой для нужного отверстия в стекле. Процедура потребует некоторой выдержки, для создания 1 отверстия уходит около 5 минут и 1 л песка. В результате получают качественную, дешёвую и гладкую прорезь в стекле.
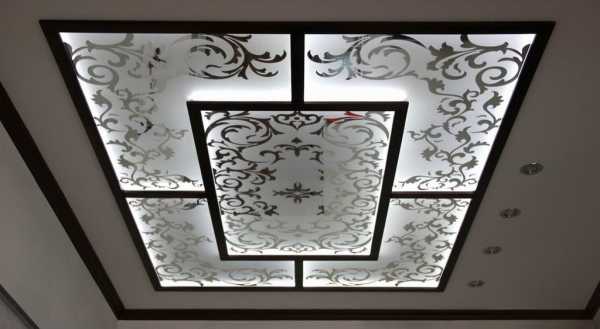
Сборка пескоструйного аппарата
Пескоструйный аппарат своими руками требует чертежей, наличия электроинструмента и подготовки материала.
Самый первый этап – это работы с баллоном, из которого поступает абразив. Идеально подойдёт резервуар, который содержал фреон, но другие типы тоже сгодятся. Работы с баллоном:
- С помощью ручной ножовки постепенно и аккуратно срезают латунную насадку.
- Для создания безопасных условий в работе со сварочной установкой потребуется удалить остатки газа из ёмкости. Компрессор без труда выдует его.
- После окончательной очистки просверливают 2 отверстия: снизу для удаления остатка материала и сбоку для поступления абразива к установке.
- В отверстия вводят и приваривают патрубки, они пригодятся для соединения с другими компонентами системы. Предпочтительно использовать патрубки с наконечниками для резьбы. От мастера требуется создание герметичного контура.
- Для создания мобильности установки и удобства транспортировки к низу привариваются маленькие колёса. Если не планируется перевозить конструкцию, рекомендуется устанавливать треногу.
- По желанию баллон оснащается вибратором, который будет воздействовать на ёмкость и разбивать комки материала. Использование станет более эффективным, и снизится частота забивания патрубков.
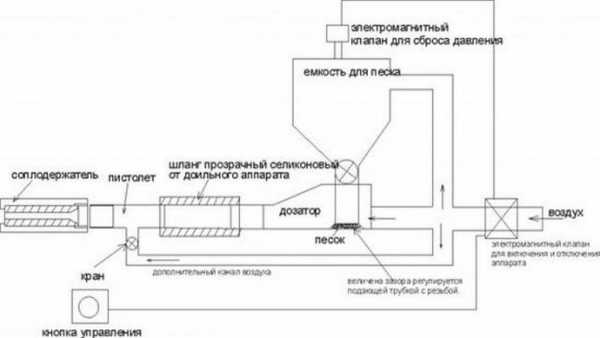
После изготовления резервуара, согласно чертежу, соединяют все элементы:
- На окончания труб фиксируются краны. Соединения осуществляются с помощью резьбы, а герметичность достигается ФУМ-лентой.
- Штуцеры монтируются на выходы тройника: на один шланг 14 мм, второй – 10 мм, но перед его фиксацией вставляется трубка из меди.
- На штуцер 14 мм надевают шланг (закрепляется хомутом), а с другой стороны устанавливают ёмкость для абразива. В конце устанавливается зажим цангового типа для фиксации сопла.
- В отверстие для воздуха монтируется тройник, затем кран для загрузки песка.
- На первый выход монтируют шланг от компрессора, а во второй – рукав от ёмкости.
- Для управления силой потока в систему вводят специальные дозаторы и краны.
Рекомендации специалистов
Все вероятные проблемы с аппаратом сводятся к неграмотному изготовлению установки. При правильном подборе элементов и аккуратной сборке качество устройства будет несущественно уступать серийным моделям.
Несколько дополнительных советов:
- можно включить систему рециркуляции потока воздуха. Она значительно повысит эффективность работ с аппаратом;
- наибольшее внимание следует уделять выбору сопла и компрессора. Обычное сопло не подходит для пескоструйной установки, рекомендуются вольфрамовые варианты. В зависимости от типа сопла, абразива и обрабатываемой поверхности отличается вид компрессора;
- до окончательной сборки важно проверить герметичность соединений. При малейшем отверстии в баллоне существенно сократится мощность установки.
Самостоятельное изготовление конструкции позволяет сократить расходы в 3–5 раз. Максимальная экономия наступит при использовании самодельного компрессора, но в нём сложно добиться достаточной мощности. Оптимальный вариант – заводской компрессор и самодельный пескоструйный аппарат с баллоном.
mensdrive.ru
Как сделать пескоструй своими руками? +видео уроки
Пескоструй не зря давно завоевал популярность многих людей по всему миру. Используя его, можно очистить и обезжирить любые детали из металла. Ним можно также матировать стеклянные поверхности.
Содержание:
- Принципе работы этого прибора
- Как сделать пистолет своими руками
- Универсальный пескоструй закрытого типа своими руками
- Пескоструй своими руками – еще один вариант
- Как на стекле делать гравировку?
- Малогабаритный пескоструйный пистолет
- Видео уроки
Такой аппарат легко можно купить в любом строительном супермаркете, однако не каждый может себе это позволить.
Поэтому сегодня мы расскажем вам, как сделать пескоструй своими руками.
Принципе работы этого прибора
Аппарат выпускает абразивную струю под большим давлением, которая выпускается из пистолета. При этом, смотря какие вы выбрали материалы для обработки, таким и будет конечный результат.
Для того чтобы сделать пескоструй своими руками, вам понадобится наличие небольшого компрессора и строительного песка. При этом такой песок можно запросто сделать, просеяв обычный при помощи мелкого сита.
Не забывайте о том, что при обработке поверхностей песчинки вылетают под очень большим давлением и они могут рикошетить от обрабатываемой поверхности даже в вашу сторону. Поэтому перед началом работ защитите глаза и открытую кожу.
В зависимости от того, какой цели вы хотите достичь, такой вид аппарата и делайте. Например, если будете обрабатывать стекло, то делайте прибор в виде камеры, а если будете очищать детали из металла, то планируйте собирать пескоструй открытого типа.
Ни один аппарат не обойдется без пистолета. Начнем с него.
Как сделать пистолет своими руками?
Самый простой пистолет состоит из рукоятки, наконечника и двух штуцеров.
Один штуцер служит для поступания воздуха под давлением, другой предназначен для всасывания песка.
Начать изготовление нужно с приобретения насадки или сопла. Через сопло будет выбрасываться воздух с песком под давлением. Вытачивать самостоятельно или делать на заказ не рекомендуется, так как вряд ли вы получите в результате хорошее качество.
Десять привычек, которые делают людей хронически несчастливыми
Чего не следует делать в социальных сетях
Преимущества употребления кофе
Самый лучший вариант — это приобрести уже готовое карбидное, вольфрамовое или борное сопло. Поверьте, оно будет служить вам очень долгое время.
Исходя из размеров насадки, вытачиваете корпус к пистолету. К корпусу крепите рукоятку и оба штуцера. Самый простой способ — это собрать, используя водопроводные фитинги, тройник и пластиковую емкость, в которую будет засыпаться песок (для нее можно использовать пластиковую бутылку, которую нужно обрезать).Такой пескоструй можно собрать своими руками за короткий срок времени.
В емкость бутылки насыпаете песок и подсоединяете ко второму концу штуцера шланг со сжатым воздухом, который вырабатывается компрессором.
Универсальный пескоструй закрытого типа своими руками
Его используют, если вам нужно обработать детали небольшого размера. По сути это ящик из металла прямоугольной формы.
Берете металлические уголки и свариваете из них остов ящика. Этот каркас обшиваете, используя стальные листы (их толщина должна быть один миллиметр).На одной из длинных стенок камеры предусмотрите монтаж стеклянного смотрового окна.
Вырезаете две дырки сто миллиметров в диаметре под стеклянным окном. Они нужны для того, чтобы вы могли руками манипулировать предметами, которые находятся внутри. На них крепите перчатки. Подумайте, как их легко можно было бы заменить после износа.
Берете проволочную решетку и делаете из нее дно. Под этим дном располагаете желоб, который выходит в емкость для собирания ненужного песка. Внутри помещаете пистолет, а также подводите к нему трубку для подачи воздуха, используя разъем в стене.
Песочный шланг опускаете в коробку с песком. Теперь получается, когда конструкция работает, песок насыпается назад, не покидая рабочую зону.
Чтобы в подробностях наблюдать процесс шлифовки, установите внутри две лампочки, которые подойдут по размеру. Можно также смонтировать в изделие вентиляцию.
В боковой стенке делаете отверстие, которое можно закрыть (например, в виде лючка). Через него вы будете помещать детали, которые нужно обработать.
Пескоструй своими руками – еще один вариант
О чем больше всего сожалеют люди в конце жизни
Чего не следует делать в социальных сетях
9 самых жутких пыток древнего мира
Пистолет делаете, используя пластиковую бутылку емкостью полтора литра. Также нужно запастись водопроводным шаровым краном, тройником и клапаном от краскопульта.
Учтите, что несколько частей вам будет нужно вытачивать при помощи станка (если вы в этом не специалист, лучше доверьте эту работу токарю).
В качестве инжектора вы будете использовать вкладыш. В той точке, где сходятся конические отверстия, будет образовываться низкое давление. При этом воздух, который попадет в емкость, дальше будет выходить через шланг, засасывая при этом песочные крупинки.
Используя кран, можно с легкостью регулировать количество расходуемого песка.
Используя резьбовую шайбу, прикручиваете пробку от бутылки к смесителю. Такая пробка служит не очень долго, поэтому приготовьтесь к тому, что ее время от времени нужно будет менять.
Что еще нужно купить, так это сопло из керамики, которое присутствует в зуботехническом пескоструйном аппарате. Такую деталь можно легко найти в медицинских магазинах.
Схема пескоструйного устройства.
Как мы уже отмечали выше, этим инструментом можно также обрабатывать стекло.
Как на стекле делать гравировку?
Отрезок стекла необходимого вам размера заклеиваете, используя самоклеящуюся пленку. Потом рисуете любой рисунок и вырезаете его по контурам, используя офисный нож.
Далее обрабатываете стекло, направив на него струю. Теперь снимаете пленку.
Получившуюся поделку можно осветить, используя светодиоды. Будет смотреться очень красиво.
Малогабаритный пескоструйный пистолет
Единственный его недостаток в том, что исходя из габаритов, в емкость придется часто насыпать песок. Но я думаю, с этим можно смириться.
Для изготовления вам понадобится сварка и паяльник, потому что придется к одним деталям применить сварку, а к другим пайку. Пистолет такого вида легко выдерживает восемь атмосфер внутреннего давления.
Трубы из латуни прикрепляете к банке, используя эпоксидный пластилин.
Для продолжения работы вам нужно будет купить в автомобильном магазине пистолет для обдува. Его приклеиваете при помощи эпоксидной смолы к изделию.
Как видите, такой инструмент можно сделать в домашних условиях. А рассмотрев его достоинства и простоту в использовании, думаю каждый захочет иметь у себя в наличии пескоструйку.
Видео уроки
uchieto.ru
Пескоструй своими руками из баллона: подробное описание с фото
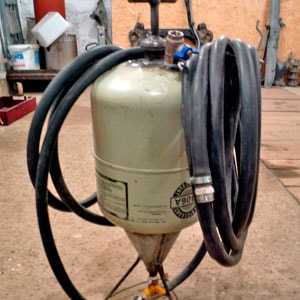
Изготовление пескоструйного аппарата своими руками от автора самоделки: фото изготовления с подробным описанием.
Для начала хочу показать схему моего самодельного пескоструя.
Итак, был куплен компрессор (в гараже штука нужная, но такой мощный брался для пескоструя) 2-х поршневой, с ресивером на 100 литров, ременной передачей, принудительным охлаждением поршней и двигателя мощностью 3кВт и производительностью 500л\мин — самый мощный однофазный компрессор из представленных у нас на рынке.
Хочу уточнить. Для нормальной производительной пескоструйки этот компрессор слабоват, и по этому если кто надумает делать пескоструй мощнее того, которым песочат свечи, минимальная производительность компрессора должна быть от 500 л/мин и выше!
Ещё один важный момент — диаметр шланга должен быль в 3-4 раза больше диаметра сопла, шланг должен иметь как можно меньше соединений и изгибов, все сгоны не должны понижать внутреннее проходное сечение, длина шланга не должна превышать требуемую.
Если нужен длинный шланг, то нужно отыграться на удлинении воздушной части, а не той в которой будет транспортироваться песок, её я сделал всего 3 м, а воздушную часть — около 8-ми метров, что позволяет компрессору находится подальше от пескоструйки, и втягивать меньше пыли.Шланг был взят с внутренним сечением 18 мм. При этом сгоны подошли на ½ (16мм) и ¾ дюйма (20 мм).
Большое сечение должно сохраняться на всем трубопроводе, начиная от компрессора, и заканчивая соплом. По этому, быстросъемные соединения применяемые для краскопульта и пр. неприменимы для пескоструя в виду того, что на быстросъемных соединениях диаметр внутреннего сечения всего 5 мм.
По этому пришлось выкрутить заглушку на ресивере, и ввернуть на ее место шаровой кран, так как сечение заглушки 16 мм. На кран устанавливается накидная гайка, именуемая у сантехников «американкой», чтобы можно было легко отсоединять пескоструй от компрессора. Опять же подбираем сгоны так, чтобы не уменьшать проходное сечение
Подачу воздуха организовал, но столкнулся с еще одной проблемой — когда в бачке заканчивается песок, то основная его масса остается на краях сосуда, а в центре — пустота.
Решение простое — нужно сделать дно конусным. Понеслась: срезаю старое дно, из бляхи 1 мм делаю конус и привариваю его к ёмкости, снизу ввариваю резьбу 16 мм, перевариваю ножки на конус.
Теперь нужно сделать крючки для шлангов, чтобы их можно было удобно сматывать. Кроме того хочу сказать, что подавать воздух в баллон сверху оказалось лишним, более того без него все работает даже лучше, поэтому оставил только кран, при помощи которого можно стравливать давление с баллона, в том случае если в конусе забивается песок.
А это общий вид пескоструя в собранном виде — получилось довольно компактно, не смотря на длинный и толстый шланг)
Теперь осталось самое главное — сопло. Во первых должен быть кран для удобной работы, во вторых быстросъемный (ну или хотя бы чтоб снимался без инструментов) держатель сопла, и собственно само сопло из износостойкого материала.Кран был взят на ¾ дюйма (20 мм), по тому как его внутреннее сечение всего 18 мм. Вся рукоятка в сборе вместе с соплом выглядит так:
Держатель сопла сделал из накидной гайки на ¾-ти и переходной муфты с 16 мм на 12 мм, которую накидной гайкой прикручиваем к крану.
В получившийся держатель вставляется керамическое сопло, а его несоответствие по диаметру устраняется подбором резинки нужного диаметра
Касательно сопла — его не трудно изготовить из свечи зажигания — была взята свечка от бензопилы, так как у нее электрод тоньше, и соответственно диаметр будущего сопла — 4 мм. Из свечи от классики получается сопло в 5 мм, что для моего компрессора очень много — слишком стремительно падает давление и компрессор не успевает его восполнять.
Чтобы получить из свечи сопло, нужно слезать с нее юбку и вообще весь металл. Затем алмазным диском (диск по камню, плитке керамической и т.п.) отпилить от керамического изолятора свечи нижнюю часть, ту которая находилась в юбке. Затем нужно выкрутить электрод из будущего сопла, а если не выкручивается, то необходимо высверлить его сверлом соотвественного диаметра. При наличии сверл с алмазным наконечником не плохо было бы сделать конус на сопле, со стороны крана, но в принципе и так все работает.
Самодельное сито тоже оказалось неудобным, да и камешки через него проскакивали, по этому было найдено металлическое сито для муки которое отлично себя зарекомендовало)
При пескоструйке пыль стоит непроглядная, по этом нужно использовать респиратор, желательно с «выхлопом» вниз.
Для защиты лица и глаз можно использовать маску из оргстекла, но она довольно быстро матуется — это уже вторая… Кстати, «выхлоп» вниз для того чтоб эта маска не потела.
Проверяем работу пескоструя на чашке задней пружины.
После обработки.
Ну и в заключение хочу сказать, что пескоструйный аппарат система комплексная, и при несоответствии хотя бы одной его части нормально работать не будет. Здесь можно провести аналогию — крепость цепи определяется крепостью ее самого слабого звена. По этому, для тех, кто решит делать пескоструй своими руками подведу итог, на что нужно обратить внимание чтобы создать рабочий аппарат:
1. Компрессор с производительностью от 500 л/мин и выше, с принудительным охлаждением, большим ресивером (50л минимум) и желательно с ременнойпередачей, так как они не так греются, а при пескоструйке компрессор не выключается.
2. Диаметр внутреннего сечения всех шлангов и сгонов, начиная от компрессора и до сопла не должен быть меньше 16 мм, или хотя бы быть в 4 раза больше диаметра сопла, но тут кашу маслом не испортишь) Так же по возможности (а это возможно) нужно избегать изгибов на сгонах и шлангах уже при работе.
3. Баллон должен иметь конусное дно, с как можно более острым углом.
4. Сопла должны быть как можно тверже, к примеру сопло из закаленной стали проживет около часу — двух. Из керамики — около 100. Из карбида вольфрама — около 900-та часов. Боковое сечение сопла может быть как обычное прямолинейное, так и конусное (сопла Вентури). Последние дают прибавку в производительности, так как разгоняют частицы на последок до около 700 км/час (в прямолинейных соплах скорость приблизительно 300 км/час), но сопла Вентури дома пожалуй не изготовить, так как керамику нечем обрабатывать…
5. Песок. Он должен быть сеяный, желательно дважды, или даже трижды ситом, в котором размер ячейки меньше чем диаметр сопла. Кроме того песок должен быть полностью сухим, таким, чтобы он высыпался из кулака. Песок может быть речной серый, или желтый, или кварцевый, или любой как я понял, главное чтоб пескоструйный аппарат был красный, и абразив сухой и просеянный) Так же используют электрокорунд, стружку чугуна и прочие абразивы, но я думаю в гараже можно обойтись и без них.
6. Приведу некоторые показатели уже рабочего аппарата, что думаю облегчит постройку нового. И так: производительность компрессора — 500 л/мин, ресивер — 100 л, диаметр сопла — 4 мм, диаметр шлангов — 18 мм, Давление при пескоструйке — стремительно падает с 8 атм. до 1,5 и держится в этом диапазоне +/-0,5 атм. в зависимости от того, сколько времени открыт кран у сопла. Даже при таких низких давлениях успешно песочится краска и неглубокая ржавчина. Для случаев потяжелее приходится закрывать кран и немного ждать, пока нагноится давление повыше, но в принципе работать можно.
7. Бюджет. Если учится на чужих ошибках, и не наступать на те же грабли, то можно смастерить аппарат за примерно 50 у.е., если делать самому и уже иметь в наличии баллон и сварку с компрессором. Если включать в цену компрессор, тогда конечно цена другая будет, но я его не включал, по тому как в любом случае бы покупал его в гараж, и помощнее, чтобы в будущем пользоваться пневмоинструментом.
Ну вот вроде и все, вывалил на изнанку все что знал, но за то теперь есть статься, где собрано все что нужно для того, чтобы собрать аппарат в гаражных условиях.
Автор самоделки: Евгений Иримия. источник
Популярные самоделки из этой рубрики
Самодельный сверлильный станок из дрели...
Самодельный держатель для дрели...
Гибочный станок своими руками...
Самодельная бетономешалка
Самодельная чудо лопата своими руками...
Электролобзик своими руками...
Труборез своими руками
Ручная пила из цепи от бензопилы...
Самодельный пресс из домкрата...
Самодельный универсальный ключ для болгарки и дрел...
Стенд для ремонта двигателя...
Станок для холодной ковки своими руками...
sam-stroitel.com
Как сделать пескоструйный аппарат своими руками: устройство, процесс сборки, комплектующие
Главный принцип работы пескоструйного аппарата – чем больше давление, тем выше производительность процесса абразивной обработки — не предполагает присутствие в конструкции подобных агрегатов сложных или дорогостоящих узлов.
Любой аппарат состоит из резервуара с песком, генератора (или баллона) сжатого воздуха и пистолета-распылителя. В итоге, самодельный пескоструйный аппарат может собрать любой начинающий слесарь, соединив с помощью специальных шлангов готовые или самодельные узлы и детали. И в данной статье мы познакомим наших читателей с технологией сборки самодельных пескоструек.
Разновидности конструкций пескоструйных аппаратов
Перед тем, как сделать пескоструйный аппарат, вам придется выбрать одну из схем компоновки пескоструйного аппарата. Конструкционные схемы заводские агрегатов предполагают следующие варианты компоновки основных узлов:
Всасывающий вариант, для которого характерно использование энергии сжатого воздуха не только в процессе распыление абразивного облака, но и в ходе забора (всасывания) песка из резервуара. Такие конструкции реализуются без особых затруднений. Однако всасывающие пескоструйные аппараты используются лишь для легкой очистки поверхностей. Шлифование и прочие энергоемкие операции всасывающим пескоструйкам противопоказаны.
Вакуумный вариант, предполагающий циклическую схему использования абразивного материала, который собирается из поддона и транспортируется в резервуар прямо в процессе пескоструйной обработки. Разумеется, такая схема усложняет конструкцию агрегата. Поэтому вакуумные пескоструйные аппараты в кустарных условиях практически не производятся. Да и практика повторного использования абразива интересна только в случае массового применения технологии пескоструйной обработки, что характерно только для крупносерийного производства.
Пневматический вариант, функционирующий в условиях максимально возможного давления и в системе забора и в пистолете-распылителе. Именно поэтому самодельные пневматические пескоструйки не имеют ни малейшего шанса на существование: построить такой аппарат без точных инженерных расчетов и чертежей практически невозможно. Но даже подробный чертеж пескоструйного аппарата высокого давления, дополненный схемой сборки, не приблизит вас к желаемому результату – в домашних условиях монтаж подобных конструкций попросту невозможен, из-за отсутствия технологий кустарной сборки систем, работающих под высоким давлением.
В итоге, своими руками вы сможете собрать только всасывающий аппарата с напорной или инжекторной схемой подачи абразивного материала в рабочую зону. Отличия в конструкциях заключаются в том, что при напорной схеме работы сжатым воздухом «питается» и пистолет и резервуар с песком, а в инжекторной схеме – воздух подается только в пистолет, а песок попадает в рабочую зону «самотеком».
В итоге, напорная схема пескоструйного аппарата обеспечивает лучшую производительность, но требует намного большего расхода сжатого воздуха, а инжекторный вариант, при меньшей производительности, расходует совсем незначительный объем воздуха и более подходит для бытового применения или мелкосерийного производства.
Исходя из вышесказанного, лучшей схемой компоновки пескоструйного аппарата, собираемого своими руками, является всасывающий вариант конструкции с инжекторной подачей абразива.
Комплектующие пескоструйных аппаратов
Устройство пескоструйного аппарата предполагает компоновку подобного агрегата из трех групп комплектующих, именно:
- Компрессионной группы, в которую входит генератор (или баллон) сжатого воздуха, редуктор и соединительные шланги.
- Узла хранения и транспортировки абразивного материала, который состоит из резервуара, шлангов подачи и регулятора объемов подачи (пропускной способности) абразива.
- Распыляющего узла (пистолета), который состоит из смесителя (где формируется абразивная взвесь), сопла, (распыляющей форсунки) и органов управления подачей песка и сжатого воздуха.
Соответственно, для сборки самодельной пескоструйки нам понадобится полный комплект деталей и узлов, относящихся и к первой, и ко второй, и к третьей группе.
Поэтому перед сборкой вы должны приобрести следующие детали:
- Компрессор мощностью не менее трех киловатт и производительностью не менее 500 литров/минуту.
- Стальная емкость для абразивного материала, в качестве которой можно использовать обычный баллон для портативных газовых плиток или емкость из-под старого огнетушителя.
- Регуляторы пропускной способности – шаровые краны.
- Два отрезка резинового шланга: первый – диаметром на 14 мм и длиной до 2 метров, второй – диаметром 10 миллиметров и длиной до пяти метров.
- Стальные штуцеры с двумя резьбовыми торцами, диаметром 15 миллиметров. Стальной штуцер резьбовым сгоном на два дюйма и заглушкой на втором торце.
- Сопло для пескоструйного аппарата – высокопрочная форсунка из вольфрама, приобретаемая только в «заводском» исполнении. Обычные форсунки забьются или поменяют диаметр пропускного отверстия за считанные минуты.
- Фум-лента, для изоляции резьбовых соединений, цанговые зажимы или винтовые хомуты – для монтажа шлангов.
Сборку аппарата рекомендуют начинать только после покупки всех составляющих из этого списка.
Пескоструйный аппарат своими руками: схема сборки
Сборка пескоструйки реализуется следующим образом:
- Вначале подготавливается бункер под абразивный материал. Для этого следует демонтировать с баллона газовый вентиль и заменить его штуцером с заглушкой, сквозь который будет засыпаться песок или многокомпонентная смесь абразивных материалов. После монтажа первого штуцера, на противоположной стороне баллона высверливается отверстие на 12 миллиметров, поверх которого приваривают 15-миллиметровый штуцер.
- Вокруг дна, из которого выходит второй штуцер, наваривают три-четыре опоры, на которых будет «стоять» баллон с песком. После чего на нижний штуцер емкости с абразивом накручивают кран, используя в качестве уплотнителя фум-ленту.
- Далее готовится самодельный пистолет-распылитель, который собирают из тройника, на торцы которого накручивают штуцеры для шлангов на 10 и 14 миллиметров.
- После сборки полуфабриката пистолета штуцер на 14 миллиметров соединяют с вентилем емкости с абразивом, фиксируя 14-миллиметровый резиновый шланг на цанговый зажим (у баллона) и на хомут (у тройника).
- На следующем этапе к свободному торцу тройника, который расположен на одной оси с торцом, «принявшим» 14-миллиметровый шланг, присоединяется шланг, связывающий тройник (смеситель) и форсунку (сопло) пескоструйного аппарата.
- Далее смеситель подсоединяют к компрессору с помощью 10-миллиметрового шланга.
После сборки и фиксации всех соединений можно включать компрессор и пользоваться самодельной пескоструйкой.
Причем для повышения эффективности работы аппарата в баллон с песком можно ввести еще один штуцер, соединенный с компрессором, реализовав нагнетательную схему подачи песка.
Упрощенный процесс сборки пескоструйного аппарата
Если вы не желаете возиться с газовыми баллонами, штуцерами и тройниками, а пескоструйка необходима вам лишь для разового или очень редкого применения, то вам, скорее всего, подойдет упрощенная конструкция аппарата.
В данном случае роль баллона с песком играет обычная пластиковая бутылка, которую вкручивают прямо в тройник-смеситель. То есть, к одному торцу тройника присоединяют шланг компрессора, на противоположный торец монтируют форсунку, а на ответвление сверху накручивают баллон с песком.
Причем шатровый кран располагается между бутылкой с песком и принимающим ответвлением тройника-смесителя, а подачу воздуха можно контролировать с помощью рукояти от краскопульта, выходное отверстие которой соединяют с тройником.
Такая пескоструйка собирается за 1-1,5 часа, но работает не больше 10-20 минут - расположенное в нескольких сантиметрах от емкости с песком сопло забивается очень быстро.
steelguide.ru
Пескоструйный аппарат своими руками — Поделки для авто
Предложенный вашему вниманию вариант пескоструйного аппарата практически полностью собран из подручных материалов. За затраченные на его сооружение деньги купить на рынке что-то стоящее практически невозможно.
Пескоструйный аппарат своими руками
В первую очередь был модернизирован китайский пистолет инжекторного типа безымянного производителя. В первоначальном исполнении толком поработать он так и не смог. Только сопла стирались.
Именно по этой причине было куплено абразивоструйное сопло Venturi 5,5 мм из карбид-вольфрама. Приблизительный срок службы такого сопла при использовании кварцевого песка составляет 300-400 часов. В дальнейшем пистолет был замене на обычный шаровый кран со встроенным соплом.
Самое главное при работе – это использовать сухой, чистый и просеянный песок. Он отлично сыпется и не забивает отверстия.
За основу для пескоструйного аппарата был взят пропановый баллон, внизу которого вмонтирован тройной шаровый кран-смеситель. Подача песка происходит сверху, подача воздуха от компрессора – снизу. Третий выход служит для подключения напорного шланга.
Удобство такого крана заключается в том, что отдельно можно открыть подачу воздуха, чтобы продуть шланг и детали после обработки. Также он позволяет ссыпать песок, если необходимо сменить его фракцию.
Воздушная разводка выполнена при помощи обычной полипропиленовой трубы и фитингов. Сжатый воздух поступает с компрессора вверх, для выравнивания давления в баллоне с песком, и вниз – на напорный шланг. Воздух на входе перекрывается с помощью шарового крана. Вверху баллона предусмотрен кран на ? дюйма для стравливания давления.
Засыпная горловина выполнена из срезанного баллона из-под фреона. К корпусу аппарата она крепится через засыпной кран на 2 дюйма.
Сам кран с соплом (или пистолет) подключен к баллону при помощи БМС шланга с внутренним диаметром 20 мм. Одного крана хватает на 2-3 дня работы. Главное правило – держать его или в полностью открытом, или в полностью закрытом положении. В противном случае, из-за полученного завихрения, струя песка проедает плешь в стенке крана буквально за 10-15 минут работы.
Теперь о компрессоре. Оптимальная работа пескоструйного аппарата осуществляется при давлении воздуха 8-10 БАР. При использовании самодельного компрессора производительностью 550 литров в минуту при давлении 6 БАР и ресивере на 150 литров, максимальное время работы составляло всего 30-40 секунд. За это время давление падало с 8 до 3,5 БАР. Затем перерыв около минуты, пока давление в ресивере снова не поднимется до 8 БАР.
Отсюда вывод. Чтобы иметь возможность качественно работать, нужен хороший и производительный компрессор. Тут одним энтузиазмом не обойтись. Компрессор, производительностью 1350 литров в минуту при давлении 10 БАР – самая дорогостоящая часть этого пескоструя.
Роль ресивера выполняют два тепловозных баллона, емкостью 222 литра каждый. Они нашлись в пункте приема металлолома. Также можно поспрашивать в железнодорожном депо.
Баллоны устанавливаются на металлическую подставку. В нижней части ресивера необходимо врезать краны для слива конденсата.
Далее, для предания внешнего вида, всю конструкцию необходимо почистить и покрасить. Последний штрих — механический манометр для дополнительного контроля давления в ресивере.
При постоянной работе этого компрессора было замечено, что давление в ресивере может падать до 7-7,5 БАР. Это вовсе не критично. Так что можно вести работу не останавливаясь.
Похожие статьи:
xn----7sbgjfsnhxbk7a.xn--p1ai
Пескоструйный аппарат своими руками — Поделки для авто
Всем привет! Давно хотел замутить себе пескоструйный аппарат своими руками… вот собственно и замутил 🙂За образец принял фотку из сети.
вот с чего все началось
Набросал принципиальную схему на листке бумаги, дабы не запутаться во всех этих краниках и переходниках, купил на приеме металла баллон за 15 грн. ( от куда баллон не знаю ), купил нужную фасонину и понеслось.
Только переделал баллон, еще не успев приварить ножки, принялся тут же к испытанию), хоть и дуло со всех щелей, но результат меня порадовал, идем дальше…
И вот он, через 2 часа манипуляций болгаркой и сварочником, получил вот такой вот «самогонный аппарат»)
Проверив на герметичность тут же покрасил.
Не могу даже вам передать как у меня чесались руки поскорее попробовать его в действии. Ну и протестировал обработку металла.
PS. Может что то забыл написать, спрашивайте — отвечу.
Общий вид
схема монтажная
принципиальная схема
как есть
Еще добавил фотки сопла, сделал его из свечи системы зажигания, вынув керамический изолятор
разобранный вид
собранный вид
По многочисленным просьбам сделал видео, которое демонстрирует работу аппарата, снимал на телефон да еще и один, а в конце батарея села(, так что не пинайте сильно.
Автор; Вадим Орехов г.Мелитополь, Украина
Похожие статьи:
xn----7sbgjfsnhxbk7a.xn--p1ai
Пескоструйный аппарат своими руками: сборка установки
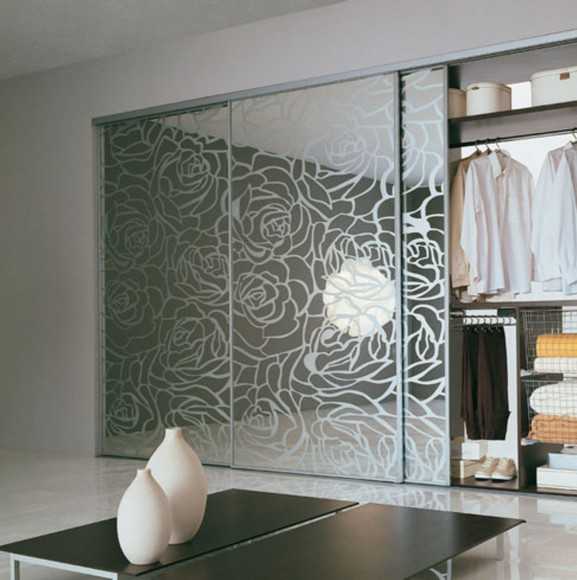
Пескоструйный аппарат предназначен для абразивной обработки поверхностей металлических, стеклянных, пластиковых и других изделий. Основными преимуществами, определяющими его востребованность, являются возможность обработки изделий сложной формы с криволинейными участками, а также равномерная матовая текстура поверхности с хорошими адгезивными свойствами и способностью рассеивать падающий на нее свет.
Чаще всего такие устройства используются для очистки металлических изделий от ржавчины, окалины, старого покрытия при подготовке к покрасочным работам или гальванической обработке. При обработке участков полированных поверхностей из металла или стекла (пескоструйной гравировке) получается четкий контрастный рисунок, благодаря чему аппарат можно применять в производстве декоративных изделий.
Типы пескоструйных аппаратов и принципы их работы
Высокая стоимость подобных устройств, встречающихся в продаже, и относительная простота их конструкции заставляют задуматься об изготовлении пескоструйного аппарата своими руками. Существует несколько видов пескоструйных аппаратов, отличающихся по принципу действия, но наибольший интерес представляют два из них:
Аппарат всасывающего действия. Конструкция такого пескоструя весьма проста: аппарат состоит из бункера с абразивом, шланга, один конец которого подсоединен к источнику сжатого воздуха, а второй заканчивается соплом. Шланг соединяется с бункером посредством тройника, через который производится подача абразивного материала. Всасывание песка в шланг происходит под действием газового потока. Смешивание воздуха с абразивом происходит на выходе, благодаря чему такая система обладает высокой надежностью и долговечностью. Единственным элементом, нуждающимся в периодической замене, является сопло. Основным недостатком такой конструкции считается ее низкий КПД.
Аппарат нагнетательного действия. Данный пескоструйный аппарат немного сложнее в изготовлении, имеет больше деталей, соответственно, точек отказа. Кроме этого, шланги и сопла нуждаются в более частой замене, чем на всасывающем аппарате. Основным его преимуществом считается высокая производительность. В сравнении с предыдущей схемой, здесь добавлен тройник для разделения потока воздуха, часть которого направляется в бункер для создания в нем положительного давления. Подача воздуха в бункер может осуществляться как через донную, так и через верхнюю часть. Первый вариант более эффективен, поскольку воздушно-песчаная смесь формируется уже в бункере. Одним из элементов, отвечающих за безотказность работы аппарата, является фильтрующий элемент, предназначенный для удаления влаги из сжатого воздуха.
Основные узлы пескоструйных аппаратов и особенности их конструкции
Источник сжатого воздуха. Чаще всего его функции выполняет компрессор. Для автомастерских, где используется ручной пневматический инструмент, проблема его выбора отпадает сама собой, поскольку такие устройства способны создавать достаточное для пескоструйки давление (от 2 до 6 атмосфер). В других случаях его придется купить или взять в аренду, если выполняемые работы имеют разовый или периодический характер.
Бункер. Основные требования к конструкции бункера – это герметичность, достаточный объём и способность выдерживать рабочее давление в системе. Для его изготовления можно использовать подручные материалы, которые можно найти в любом гараже: старая скороварка, отрезки канализационной трубы, корпус от огнетушителя или даже обычная пластиковая бутылка от газированных напитков. Герметизацию стыков и соединений можно выполнить при помощи любого двухкомпонентного состава на основе эпоксидной или полиэфирной смолы. Получаемые таким образом малогабаритные бункеры можно присоединять непосредственно к пескоструйному пистолету.
Стационарную конструкцию можно изготовить из обрезка трубы большого диаметра, старого газового баллона или листового металла при помощи дуговой сварки. Такая емкость подойдет для выполнения постоянных работ, поскольку может иметь большой объем и редко нуждается в перезарядке. Для обеспечения хорошей производительности длина соединительных шлангов от источника до бункера и от бункера до пистолета не должна превышать 10 и 3 метра соответственно.
Пистолет. Простой по конструкции и удобный в работе пистолет, показанный на рисунке выше, можно изготовить из сантехнических фитингов (тройника с накидными гайками и шарового вентиля) и рукоятки с клапаном от краскопульта. Единственный элемент пескоструйного аппарата, который нельзя сделать своими руками, за которым придется идти в магазин, остается износостойкое сопло. Однако, если аппарат будет использоваться редко, его можно выточить из стали или применить отрезок трубки, развальцованной с одного края для крепления накидной гайкой. Также придется выточить фланцевое крепление для присоединения бункера. Включение пистолета производится при помощи клапана, а подача песка регулируется вентилем.
При использовании стационарного бункера к месту крепления съёмного подключается второй шланг. Таким образом несколько снижается вес конструкции и повышается удобство работы.
Камера. Такой элемент вводится в конструкцию для обеспечения возможности работы в закрытых помещениях. Чаще всего он представляет собой цельносварной герметичный короб со стеклянным смотровым окном в верхней части для зрительного контроля и плотно закрывающимися дверями на левой боковине. Габариты камеры и дверей определяются размерами обрабатываемых деталей.
Трубопроводы для подачи песчано-воздушной смеси проходят через правую боковую стенку. На фронтальной стенке вырезаются круглые отверстия для рук, к которым через фланцы прижимаются длинные каучуковые перчатки. Вместо них можно также использовать текстильные рукава из плотной ткани с пришитыми к ним рукавицами.
Каркас камеры можно сварить из уголка (25×25 или 20×20) и обшить листом толщиной не менее 2 мм. В качестве днища камеры можно использовать перфорированный лист (4 – 5 мм) или решетку из прутка, чтобы отработанный песок мог свободно уходить в нижнюю часть камеры пирамидальной формы и через горловину высыпаться в ящик, который размещают на полу. После просеивания отработанный песок можно использовать повторно.
Дверь можно навесить на петли (наружные), а в качестве замков использовать винты с барашковыми гайками, расположенными по ее периметру. В качестве уплотнения подойдет резина от автомобильной камеры, которую можно нарезать полосами и приклеить по периметру проёма любым контактным клеем типа «Момент».
Камеры заводского производства чаще всего снабжены регенераторами и циклонами для очистки отработанного абразива от пыли и автоматической перезарядки бункера. Самостоятельное изготовление таких устройств представляет ряд сложностей. Обязательным элементом системы будет установка вытяжного вентилятора небольшой мощности, создающего разрежение в камере и предотвращающего попадание пыли в помещение.
Уважаемые читатели, если у вас остались вопросы, задавайте их, используя форму ниже. Мы будем рады общению с вами ;)
Рекомендуем другие статьи по теме
stroi-specialist.ru