Технология выпуска и производства бумажных денег. Для получения бумаги высокого качества раздробленные пропитанные особенным
Способ получения волокнистого полуфабриката высокого выхода для производства бумаги
Сущность изобретения: измельченное древесное сырье пропитывают щелочным раствором, предпочтительно сульфитом натрия или смесью его с гидроксидом натрия в присутствии насыщенного пара, либо при атмосферном давлении и температуре 30- 60° С в течение 12-24 ч, либо при повышенном давлении и температуре 100-110° С. Затем проводят варку пропитанного сырья с использованием насыщенного водяного пара при 180-210° С и давлении 9,3-18,9 атм. в течение 30-360 с мгновенно сбрасывают давление до атмосферного, полученную массу промывают и сразу же размалывают; 2 з.п. ф-лы, 1 табл.
СОЮЗ СОВЕТСКИХ
СОЦИАЛИСТИЧЕСКИХ
РЕСПУБЛИК (51)5 0 21 С 3/00
ГОСУДАРСТВЕННОЕ ПАТЕНТНОЕ
ВЕДОМСТВО СССР (I OCflATEHT CCCP) ОПИСАНИЕ ИЗОБРЕТЕНИЯ
К ПАТЕНТУ
С.1 (21) 4355464/12 (22) 23.03.88 (46) 15;08.93. Бюл. М 30 (31) 532871 (32) 24.03.87 (33) СА (71) Стейк Текнолоджи ЛТД (СА) (72) Богуслав В,Кокта (CA) (56) Журнал "Аппита", 32(3), 187-200, 1978. (54) СПОСОБ ПОЛУЧЕНИЯ ВОЛОКНИСТОГО ПОЛУФАБРИКАТА ВЫСОКОГО ВЫХОДА ДЛЯ ПРОИЗВОДСТВА БУМАГИ (57) Сущность изобретения: измельченное древесное сырье пропитывают щелочным Изобретение относится к технологии изготовления волокнистых полуфабрикатов с использованием взрывного (декомпрессионного) разделения целлюлозосодержащего сырья на волокна и может быть использовано в производстве целлюлозы для бумаги.
Целью изобретения является повышение эффективности процесса.
Поставленная цель достигается тем, что в способе получения волокнистого полуфабриката высокого выхода для производства бумаги, включающем пропитку измельченного древесного сырья щелочным водным раствором, предпочтительно сульфитом натрия или его смесью с гидроксидом натрия, варку пропитанного сырья с исполь- зованием насыщенного водяного пара при повышенной температуре и избыточном давлении, мгновенный сброс давления до атмосферного и последующий размол, со„„5U„„ 1834938 АЗ раствором, предпочтительно сульфитом натрия или смесью его с гидроксидом натрия в присутствии насыщенного пара, либо при атмосферном давлении и температуре 3060 С в течение 12-24 ч, либо при повышенном давлении и температуре 100-110 С.
Затем проводят варку пропитанного сырья с использованием насыщенного водяного пара при 180-210 С и давлении 9,3-18,9 атм. в течение 30-360 с мгновенно сбрасывают давление до атмосферного, полученную массу промывают и сразу же размалывают; 2 з.п. ф-лы, 1 табл. гласно изобретению, варку. пропитанного сырья проводят при 180 — 210 С и давлении
9,8-18,9 атм. . Пропитку могут осуществлять в присутствии насыщенного водяного пара, а варку проводят в течение 30-360 с.
В качестве исходного древесного сырья С используют древесную стружку или щепу, С
Пропитку могут осуществлять либо при атмосферном давлении и температуре 30-60
С в течение 12-24 ч, либо при повышенном . ( давлении и температуре 100-110 G, В качестве лролиточного щелочного раствора могут использоваться NazSOg или его смесь с NaOH. С
После сброса давления массу промывают и затем сразу же размалывают, что способствует избежанию потерь белизны, Изобретение иллюстрируется следующим примером его осуществления.
1834938
iI р и м е р. Измельченную осиновую щепу в количестве 150 г при ее сухости 50 смешивают с 375 г 8 -ного раствора сульфита натрия (NazSOz). Пропитку осуществляют в течение 24 ч при 60О С и жидкостном модуле, равном 6. Пропитанную массу продувают паром при атмосферном давлении в течение 60 с. Варку проводят в реакторе периодического действия с использованием насыщенного пара при 180 С и давлении
9,8 атм. в течение 300 с. После варки давление мгновенно сбрасывают (декомпрессионная обработка), и полученную волокнистую массу промывают, после чего сразу же раэмалывают в рафинере(смесителе типа острерайэер В-8614 при концентра ции массы 2о ).
Иэ массы готовят бумажные отливки и подвергают испытаниям.
Параллельно повторяют опыты при иных значениях параметров варки; приведенных в таблице. Здесь же приведены свойства полученных полуфабрикатов.
Из таблицы видно, что предлагаемый способ обеспечивает повышение эффективности процесса, так как приводит к снижению энергетических затрат при размоле и повышению механической прочности полуфабриката при сохранении его белизны.
При пропитке сырья смесью НарЯОз и NaOH имеет место дальнейшее повышение показателей разрывной длины волокнистого полуфабриката.
5 Выход волокнистого полуфабриката во всех опытах составляет 90+0,1 при степени помола 100 мл, определенной по Канадскому стандарту.
Формула изобретения
"0 1. Способ получения волокнистого полуфабриката высокого выхода для производства. бумаги, включающий пропитку измельченного древесного сырья щелочным водным раствором, предпочтительно суль15 фитом натрия или его смесью с гидроксидом натрия, варку пропитанного сырья с использованием насыщенного водяного пара при повышенной температуре и избыточном давлении, мгновенный сброс давления до
20 атмосферного и последующий размол полученной массы, о т л и ч а ю щ и.й с я тем, что, с целью повышения эффективности процесса, варку пропитанного сырья проводят при 180-210 С и 9,8 — 18,9 атм, 2. Способ по п.1, о тл и ч а ю щи и с я тем, что пропитку осуществляют в присутствии насыщенного водяного пара, 3. Способ по и 1, отличающийся тем, что варку проводят в течение 30-360 с.
www.findpatent.ru
Обратная связь ПОЗНАВАТЕЛЬНОЕ Сила воли ведет к действию, а позитивные действия формируют позитивное отношение Как определить диапазон голоса - ваш вокал Как цель узнает о ваших желаниях прежде, чем вы начнете действовать. Как компании прогнозируют привычки и манипулируют ими Целительная привычка Как самому избавиться от обидчивости Противоречивые взгляды на качества, присущие мужчинам Тренинг уверенности в себе Вкуснейший "Салат из свеклы с чесноком" Натюрморт и его изобразительные возможности Применение, как принимать мумие? Мумие для волос, лица, при переломах, при кровотечении и т.д. Как научиться брать на себя ответственность Зачем нужны границы в отношениях с детьми? Световозвращающие элементы на детской одежде Как победить свой возраст? Восемь уникальных способов, которые помогут достичь долголетия Как слышать голос Бога Классификация ожирения по ИМТ (ВОЗ) Глава 3. Завет мужчины с женщиной Оси и плоскости тела человека - Тело человека состоит из определенных топографических частей и участков, в которых расположены органы, мышцы, сосуды, нервы и т.д. Отёска стен и прирубка косяков - Когда на доме не достаёт окон и дверей, красивое высокое крыльцо ещё только в воображении, приходится подниматься с улицы в дом по трапу. Дифференциальные уравнения второго порядка (модель рынка с прогнозируемыми ценами) - В простых моделях рынка спрос и предложение обычно полагают зависящими только от текущей цены на товар. | Доклад ДИСЦИПЛИНА:Введение в профиль подготовки
ТЕМА: «Технология изготовления бумажных денег в современных условиях. Бумажные деньги современности, их особенности.»
Выполнила студентка №16-19411/1-1 группы Сивцова О.С. Проверил к.э.н.,доц. Туркович Л.И. Технология выпуска и производства бумажных денег Существует две разновидности денежного обращения: наличное и безналичное. Обращение наличных денег начинается с их эмиссии. В соответствии с Законом "О Центральном банке Российской Федерации" эмиссия наличных денег, организация их обращения и изъятия из обращения на территории Федерации осуществляются исключительно Банком России. Изготовление банкнот начинается с производства специальной бумаги. Способы изготовления защитных сортов бумаги хранятся производителями в строжайшем секрете. Технологии принципиально отличаются от производства обычной бумаги: используется хлопок и лен, а не дерево, специальное оборудование, особые способы обработки бумаги, а также эксклюзивные приемы внедрения в бумажную массу защитных элементов, которые недоступны обычным производителям. Бумага - это весьма необычное, специфическое изделие, сложное в изготовлении. Бумагоделательное производство основано на физико-химических процессах. Лист бумаги состоит из слоя специально обработанных мелких растительных волокон, в основном из целлюлозы, которые прочно соединены между собой за счет механического переплетения и химических связей. Бумага формируется (отливается) на сетке бумагоделательной машины из жидкой массы, состоящей из взвеси в воде волокнистых компонентов. В процессе отлива вода стекает (отсасывается), а на сетке образуется волокнистый слой, из которого после удаления избыточной воды сначала прессованием, а затем высушиванием получается бумага. В качестве волокнистых материалов применяются древесная целлюлоза и древесная масса, а для высокосортных и прочных бумаг, какими и являются денежные знаки, используется хлопковое и льняное волокно. В древесине содержится чистой целлюлозы в пределах 40-50 процентов, а хлопковое и льняное волокна на 90 процентов и более состоят из чистой целлюлозы. Этим определяются высокие механические качества и долговечность бумаги из хлопка и льна. Для придания большой прочности и других свойств бумага проклеивается в массе или с поверхности, в нее добавляются наполнители. Для проклейки применяется крахмал, меламиноформальдегидная смола и другие подобные материалы. Бумажное производство Гознака оснащено двумя видами бумагоделательных машин: плоскосеточными (столовыми) и круглосеточными (цилиндрическими) . Главное различие между ними состоит в том, что на плоскосеточных машинах формование бумаги осуществляется на длинной горизонтальной сетке, а на круглосеточных - на сеточном цилиндре. В бумажной промышленности наиболее распространены плоскосеточные машины, которые производят почти весь объем бумаги. Цилиндрические машины (с несколькими цилиндрами) применяются в основном для изготовления многослойной бумаги и картона. На бумажных фабриках Гознака денежные и ценные бумаги делаются как на столовых, так и на цилиндрических машинах. Однако бумаги с локальным водяным знаком изготовляются только на цилиндрических машинах. Скорость движения бумажной ленты в бумагоделательной машине составляет более 50 м в минуту. Производительность современных бумагоделательных машин достигает 250 - 500 т бумаги в сутки, масса машины - примерно 3500 т, длина - 115 м, ширина - 20 м и высота - до 15 м. Важнейшим требованием к денежной бумаге является - износоустойчивость. Принято считать основным показателем, характеризующим износоустойчивость, сопротивление излому и разрыву. Бумажные деньги в обращении многократно сгибаются и разгибаются. Поэтому при испытании на специальном приборе фальцере образцы бумаги должны выдерживать несколько тысяч двойных перегибов. Высокая прочность должна быть и на разрыв. Она определяется на динамометре и выражается расчетной длиной в метрах полосы бумаги, которая разрывается от собственного веса. Разрывная длина денежной бумаги исчисляется тысячами метров (значительно больше, чем у обычных бумаг). В процессе печатания типографским и орловским способами прочность бумаги частично снижается, особенно при плохо отрегулированном давлении. Для обеспечения высокого качества и прочности печатного рисунка денежная бумага обладает необходимой степенью белизны, непрозрачности, гладкости и светопрочности. Она не должна изменять своего цвета (белизны) и снижать механическую прочность под воздействием света, солнечных лучей. Красочный слой на бумаге должен хорошо закрепляться и быть достаточно прочным на истирание. Особое значение для денежной бумаги имеют водяные знаки, которые являются важной защитой от подделки. Кроме того, водяной знак, особенно локальный в виде портрета или другого рисунка, повышает художественный уровень денег. Водяной знак образуется при отливе бумаги за счет различной толщины слоя волокна. Создание отчетливых и красивых водяных знаков является сложной самостоятельной задачей в технологическом процессе изготовления бумаги. Знак может быть общим, то есть с непрерывно повторяющимся рисунком (узором), или локальным - рисунком, расположенным на листе бумаги в определенном месте. Он обычно размещается на купоне, а также на другом фиксированном месте денежной купюры. Зарождение рисунка знака происходит в мастерской водяных знаков, в которой готовятся штампы и дендироли. Здесь работают граверы и другие высококвалифицированные специалисты, которые переносят рисунки художников (или фотографии) на штампы и далее на металлическую сетку вала-дендироля или непосредственно на сетку цилиндра круглосеточной бумажной машины. Дендироль (ровнитель) устанавливается на сетку столовой бумагоделательной машины и при своем вращении образует на влажном бумажном полотне отпечаток своего рельефа (водяного знака). Как правило, таким способом получают бумагу с общим водяным знаком. Хороший и тем более художественный локальный знак, такой как портрет, можно получить при ручном отливе. В промышленном масштабе денежную бумагу с локальным знаком готовят на цилиндрической бумажной машине. Именно на сетке цилиндра, где отштампованы рисунки знака, при формировании бумажного полотна создаются необходимые условия для получения многотонового художественного знака, который строго фиксируется на площади будущих бумажных листов. Это позволяет в дальнейшем при печатании обеспечить точное совпадение локального знака с печатным рисунком. На сетке столовой бумагоделательной машины подобных условий для получения художественного и фиксированного знака нет. Знак должен хорошо просматриваться на просвет и быть идентичным на протяжении всего тиража. Наиболее ценными и трудными для подделки являются многотоновые водяные знаки и прежде всего портреты. Водяные знаки в ряде случаев являются настоящими произведениями изобразительного искусства. Примером таких художественных знаков являются портреты на денежных билетах Петра I, Екатерины II, Ленина. Способы печати · Высокая печать. Рельефные печатающие элементы расположены в одной плоскости и выше, чем пробельные элементы. При печати лист бумаги прижимают к печатающей форме и находящаяся на печатающих элементах краска выдавливается к краям элементов. При этом по краям получаемых изображений образуется характерный "бортик" из краски и создаётся небольшая деформация бумаги. Именно таким образом выполнены изображения серий и номеров купюр на большинстве валют мира, в том числе и на российских рублях. · Глубокая металлографская печать. Элементы изображений углублены в печатной форме. При печати краска из форм прилипает к бумаге и при высыхании образует выступающий над поверхностью бумаги красочный слой достаточно большой толщины, который легко почувствовать на ощупь. С помощью металлографской печати достигается высокая точность и четкость воспроизведения рисунка. Самые мельчайшие элементы изображений на купюрах выполнены именно данным способом. · Офсетная (плоская) печать. В формах офсетной печати, печатающие и пробельные элементы, расположены в одной плоскости. Процесс печати с таких форм основан на избирательном смачивании пробельных элементов водой, а печатающих - жирной краской. Для получения форм плоской печати необходимо создать на поверхности формной основы устойчивые печатающие и пробельные элементы. · Орловская печать. В элементах получаемых изображений присутствует переход одного цвета в другой. При этом граница перехода является четкой, отсутствуют перекосы и разрывы штрихов, наложение одного цвета на другой. Способ назван по фамилии техника экспедиции И.И. Орлова, который в конце XIX века изобрёл способ многоцветного печатания. Для орловской печати используется сложнейшее высокоточное оборудование. Воспроизвести эффект орловской печати обычными классическими способами печати невозможно. |
megapredmet.ru
Производство бумаги и картона из древесины - Технологии стоительства - Каталог статей
Производство бумаги
и картона из древесины
Чаще всего человек использует лес в качестве топлива. Однако ценность леса как природного богатства широко применяемого сырья определяется производством древесины и бумаги. Спрос на древесину всегда высок: она под рукой, при помощи резки ей легко придать нужную форму, детали дерева без труда присоединяются друг к другу, а изделия из него хорошо смотрятся. Древесина и бумага
(Лесоповал в американском штате Вашингтон. Каждое спиленное дерево очищается от веток и загружается на транспортер. Затем лес по железной дороге доставляется на деревообрабатывающие предприятия, где очищается от коры, перерабатывается в целлюлозу, а затем в бумагу.)
Твердая и мягкая древесина
Древесина бывает двух основных видов — твердая и мягкая. Мягкую древесину дают хвойные деревья: сосна, ель, пихта, тсуга, секвойя. На производство твердой древесины идут такие широколиственные древесные породы, как бук, береза, клен, дуб и тополь. В тропиках твердую древесину получают из черного эбенового дерева, видов красного дерева, тика и других ценных пород. Красиво выглядящая твердая древесина всегда была в большом почете у производителей и покупателей мебели. К сожалению, деревья твердых пород растут медленно, и в тропических лесах их становится все меньше и меньше.
(Сплав связанного в плоты леса по рекам, с участием плотогонов или же просто так, представляет собой дешевый способ его транспортировки.)
Заготовка леса
Обычно деревья валят при помощи мощных циркулярных пил; затем стволы освобождают от веток и свозят на места обработки для дальнейшей транспортировки. При этом задействуется самая разнообразная техника — краны, гусеничные тракторы, бульдозеры. Если лес подлежит перевозке по суше, его кранами загружают на колесный транспорт, хотя в Индии н Бирме для таски спиленных деревьев, совсем как в старые Времена, используют слонов. В некоторых регионах лес легче сплавлять по рекам: спиленные деревья укладывают в плоты и сталкивают на воду при помощи кранов. Затем сотни таких плотов связывают вместе и буксируют до пунктов сортировки и маркировки. В отдаленных районах, где на реках нет судоходства, бревна просто сплавляют вниз по течению — вплоть до пункта назначения. Во многих странах — и в особенности тех, где заготавливают твердые породы древесины, — нет собственных мощностей для распилки леса. Следовательно, большая часть заготовленного леса вывозится в промышленно развитые страны в виде бревен на деревообрабатывающие комбинаты.
(Каждая вязка лесоматериалов на этом складе весит 4 тысячи тонн. Вязки расположены так, чтобы воздух обдувал и высушивал свежеспиленные стволы.)
На лесозаводе бревно, прежде всего, очищается от коры, а затем механическими пилами разрезается на заготовки нужных размеров. На этом этапе переработки древесина все еще содержит живицу и требует предварительной сушки. Естественная сушка возможна, но отнимает до года времени, и поэтому древесина обычно поступает на быструю сушку в специальные лесосушилки. В результате такой искусственной сушки, или выдерживания, происходит усаживание и подчас даже коробление древесины; таким образом, древесина должна идти на переработку только после полной просушки, когда она, если только вновь не промокнет, приобретает относительную стойкость. Пиленые лесоматериалы без дальнейшей обработки подлежат использованию в строительстве, а деревянные поверхности, которые будут на виду, потребуют доводки. Нередко брусья пускают на продольную разрезку, с покраской или протравкой досок.
(При том, что почти все виды бумажной продукции легко поддаются переработке, лишь четверть всех бумажных отходов находит повторное применение.)
Самая привлекательная древесина режется на очень тонкие листы — облицовочный шпон, который затем наклеивается на основу из древесины попроще. Фанера состоит из нескольких листов древесины, склеенных так, чтобы волокна соседних листов образовывали прямой угол. Фанерный лист значительно прочнее листа таких же размеров, выделанного из обычной древесины. Фанеру намного труднее согнуть и расколоть; вероятность коробления невелика. В деревообрабатывающей промышленности мало отходов — человек нашел применение всему. Рейки из древесины низкого качества помещают между листами хорошей древесины и производят столярную плиту, а остающийся скрап превращается в опилки, обрабатывается клеем и прессуется в ДСП —древесностружчатую плиту.
(Специальное подъемное устройство собирает заготовленный лес в готовые к отгрузке связки.)
(Распил кругляка на доски происходит с каждой стороны поочередно. Когда доска спилена со всех четырех сторон, из центральной части бревна может быть вырезан прочный брус для несущих конструкций.)
Сырье для бумаги
Древесная целлюлоза является основным сырьем для производства бумаги, хотя вместо нее также могут быть использованы иные виды растительного волокна. Целлюлозу получают из самых разных твердых и мягких лесных пород: ели, сосны, эвкалипта, тополя, березы, каштана и других деревьев. Самый экономичный способ получения древесной целлюлозы — механический: на деревообрабатывающем предприятий лесоматериалы измельчаются до крошки, которая смешивается с водой. Бумага, изготовленная на основе такой целлюлозы, непрочна и чаще всего идет на производство, например, газет. Бумагу более высокого качества дела ют из целлюлозы, полученной химическим способом: деревянный брус режется на малые щепы, которые погружаются в химический раствор и нагреваются подавлением. Из такой древесной массы изготавливают бумагу для книг, брошюр модных журналов, а также прочные оберточные материалы.
(На современных деревообрабатывающих предприятиях технологические процессы полностью автоматизированы. Оператор наблюдает за различными этапами технологического процесса.)
Изготовление
На деревоперерабатывающем предприятии для удаления примесей целлюлоза промывается и фильтруется. Целлюлоза, предназначенная для изготовления белой бумаги, дополнительно подлежит выбелке. После этого она превращается в лист и сушится, что впоследствии облегчит процесс производства бумаги. Лист в кипах поступает на целлюлозно-бумажный комбинат, где специальная машина, называемая разрывателем целлюлозы, вспарывает листы и смешивает их с водой. Зачастую варка целлюлозы и производство из нее бумаги проходят в непрерывном режиме, без промежуточного сушения. К обрабатываемой бумажной массе может быть добавлена макулатура, но лишь после удаления чернил. На этом этапе производства обрабатываемая масса, состоящая из древесных волокон н воды, называется бумажным сырьем.
(Куча древесных щепок размерами 25х25х5 мм перед превращением их в целлюлозу для изготовления бумаги.)
Затем на специальной перерабатывающей машине меняются форма н структура бумажных волокон — в соответствии с требованиями, которым должна отвечать производимая бумага. На следующем этапе бумажная масса смешивается с другими веществами, задающими конечному продукту желаемые свойства. Клеи — это вещества, присутствие которых в писчей бумаге отталкивает влагу. Для проклеивания бумаги чаще всего используются смолы. Благодаря им написанное на бумаге приготовленными на водной основе чернилами не растекается и легко распознается человеческим глазом. Бумага, используемая для печатания, не требует такого проклеивания, как писчая, поскольку печатные краски готовятся не на водной основе и не растекаются. После этого бумагу окрашивают в смесителе, куда добавляют красители или компоненты, — например, мелко размельченные вещества для мелования. Так, добавки каолина делают бумагу белой и непрозрачной.Наиболее распространенным способом изготовления бумаги является метод Фурдринье. Из миксера бумажная масса через цилиндр подается на конвейер, лента которого представляет собой сетку с ячейками: ширина этой ленты может достигать 9 метров. Конвейер движется со скоростью до 1000 м в мини”. От скорости поступления сырья зависит толщина и вес сходящей с конвейера бумаги.
(Древесный ствол в разрезе: хорошо видно строение дерева. Рост камбиева слоя приводит к образованию луба внутри и коры снаружи.)
Водяные знаки
По мере продвижения бумажной массы по ленточному конвейеру часть содержащейся в ней воды вытекает через ячеистые отверстия, и бумажные волокна начинают сплетаться друг с другом, образуя так называемую рулонную ленту. Прежде чем она сойдет с конвейера, из волокон выйдет еще больше воды — за счет всасывания влаги снизу. Именно теперь на волокнах бумаги можно поставить водяной знак. Для этого понадобится специальный валик с наперед заданным рисунком. Далее лента поступит на движущийся ременной транспортер из натурального войлока и пройдет через несколько последовательно расположенных тяжелых валиков, которые выдавят из бумаги еще больше влаги и сильнее спрессуют ее волокна. Затем бумажная лента, достигшая достаточной прочности, чтобы перемещаться сама по себе, выпарят из ленты почти всю оставшуюся влагу. После сушки бумага через несколько расположенных в ряд безупречно отшлифованных железных цилиндров, называемых каландра каландрами, которые разгладят ее поверхность. После бумагу мотают на бобины, которые могут разрезаться на более мелкие катушки. Затем бумага режется на более мелкие листы.
(Эта машина для очистки леса от коры представляет собой огромный вращающийся барабан, сбивающий кору с подаваемых внутрь бревен.)
Отделка поверхности
Для придания бумаге или картону вида, необходимого для того или иного конкретного применения, существует множество методов отделки. Например, бумага покрывается тончайшим слоем измельченного белого красителя, которым могут быть или каолин, или «матовая белизна» — смесь окиси алюминия и сульфата кальция. Краситель держится на бумаге благодаря особому клеящему веществу — это или молочный белок казеин, или поливинилацетат, более известный как ПВА. Краситель заполняет мельчайшие поверхности бумаги и придает ей гладкость и характерный глянец. Иногда бумагу и картон обрабатывают парафином: вощеная бумага отталкивает воду. Один их технологических процессов подобного рода предусматривает прохождение бумаги через емкость с расплавленным воском.
(Гофрокартон - упаковочный материал с несколькими рядами волокон. Эти рулоны сошли с прессовальных барабанов, на которых собиралась целлюлоза; именно так, в отличие от изготовления бумаги по методу Фурдринье, чаще всего производится картон.)
Специальные валки очищают избыточные восковые наслоения, а остающийся воск затвердевает под струей холодной воды. Если на такой бумаге нужно что-то напечатать, сделать это следует до вощения, так как пропарафиненная поверхность краску не впитает. Другая технология вощения бумаги предполагает первоначальное покрытие воском лишь одной стороны листа, после чего другая, еще не обработанная поверхность подается на разогретый барабан. Его жар плавит воск; расплавленный воск впитывается волокнами бумаги. На обработанной таким способом бумаге возможна последующая печать.
(В некоторых регионах бумажные и прочие отходы со свалок используются для производства газа. Отходы засыпаются землей и гниют, высвобождая метан, впоследствии используемый как топливо.)
Знаете ли вы?
- Первую бумагу сделали древние китайцы. Секрет изготовления бумаги им подсказали осы и шершни, которые разжевывают древесные крошки и строят из этой клейкой массы свои гнезда.
- В печатном деле бумага измеряется в граммах на кв.м.
- С экономической точки зрения производство бумаги из отходов дороже, чем изготовление ее из древесины.
(На этой схеме в упрощенном виде показаны механическая и химическая переработка древесины в целлюлозу. Процессы дефибрирования и выделывания бумаги происходят в разных местах, и поэтому целлюлоза формируется в лист для отгрузки на бумажный комбинат. Затем по методу Фурдринье из целлюлозы получают бумагу.)
(В процессе очищения бумаги от краски воздух и мыло добавляются в кашицу из бумажных отходов. краска сходит с бумаги и с мыльной пеной всплывает на поверхность для последующего удаления.)
См. также:
ingenious.ucoz.ru
Сырье для производства бумажной тары и картона
Основным сырьем является древесная целлюлоза. Ее получают химической переработкой древесины хвойных или лиственных пород деревьев. Существует 2 способа: сульфатный и сульфитный. В первом методе используют древесину любых пород. Измельченную в щепу древесину обрабатывают путем варки в сульфатном щелоке, содержащем 9-10% NaOH при температуре 165-170 °С и давлении 0,6-0,8 МПа. Это наиболее распространенный метод. Сульфитный применяют преимущественно для хвойных пород. Щепу обрабатывают сульфитным щелоком, в состав которого входят сернистая и серная кислоты в виде гидросульфитов натрия, магния, кальция и аммония, при 130-135 °С и давлении 0,5-0,8 МПа. В обоих случаях варка длится не менее 5-7 часов. После этого из целлюлозной массы удаляют механические примеси и, если необходимо, подвергают дополнительной химической обработке — отбеливанию. Отбеливание проводят хлорсодержащими окислителями (хлор или ангидриты его кислот) или соединениями, в состав которых входит активный кислород (пероксиды). Последний способ обработки более экологичен. Эта операция важна с точки зрения качества, т. к. отбеленная целлюлоза идет на производство высокачественных сортов бумаги и картона.
При выработке целлюлозы из древесины удаляется большая часть лигнина, который повышает жесткость бумаги, но снижает качество бумаги, и других веществ. Выход целлюлозы после обработки составляет 50-60%. Сульфатная целлюлоза служит полуфабрикатом в производстве упаковочных видов бумаги и картона, и ее содержание во многом определяет прочностные свойства тары. Она дороже сульфитной целлюлозы и темнее ее (небеленые виды). Сульфатная целлюлоза — основной
полуфабрикат для производства мешочной и оберточной бумаги марки А (обладает высокими прочностными свойствами).
Для удешевления в состав пульпы вводят древесную массу — продукт истирания древесины, и термомеханическую древесную массу, получаемую при размоле пропаренной древесной щепы. Ее добавление придает бумаге пухлость, жесткость, снижает прочностные свойства, долговечность, показатель излома. Древесную массу используют при изготовлении пачек и коробочного картона. Также используют в качестве добавок полуцеллюлозу (измельченный продукт неполной переработки древесины), натуральные хлопковые волокна — хлопок, лен, пеньку и джут.
В производстве используют для удешевления бумажную макулатуру. Различают ее по кратности использования волокон. Первичная или возвратная — это отходы бумагоделательного производства, самая чистая. Макулатура второго поколения, прошедшая полиграфическое оформление, является отходом полиграфии. Макулатура, извлеченная из твердых бытовых отходов или макулатура рециклинга — наименее чистая. Она требует специальной санитарной обработки. Слой бумаги или картона, контактирующий с пищевыми продуктами, не должен содержать макулатуру.
Сырьевые компоненты и полуфабрикаты для производства картона зависят от вида картона и его назначения. Для производства плоского картона используют первичное сырье — беленую или небеленую целлюлозу. Для удешевления картонов в состав компонентов вводят облагороженную бумажную макулатуру и древесную массу.
В производстве гофрированного картона используют сульфатную или сульфитную небеленую целлюлозу, древесную массу, отходы сортирования целлюлозы, бумажную массу из сортированной макулатуры, несортированную макулатуру.
Похожие статьи
znaytovar.ru
Из каких деревьев делают бумагу
Бумага – это давно используемый и очень известный материал. С бумагой в человеческой жизни связано очень многое: от косметики, оберток и упаковок. До книг и других предметов, используемых повседневно. И, как известно, бумагу производят из дерева.
Этот замечательный материал впервые появился в Китае, где и были разработаны первые методы бумажного производства, хотя в древность не существовало таких мощных технологических решений, как сейчас. В настоящее же время процесс может показаться очень интересным, поэтому стоит рассмотреть его подробнее.
Такой материал, как бумага, сейчас производится на специализированных бумажных фабриках, куда поставляют спиленные деревья для дальнейшей обработки. Основа бумаги - целлюлоза, которую получают из некоторых лесных пород. Таким образом, станки срывают с деревьев кору, и измельчают древесные волокна в мелкие щепки, или даже муку.
После измельчения муку смешивают с водой и подвергают термообработке, а затем прессуют и отглаживают, придавая фотку очень тонких листов. Так получается низкосортная, но более чистая, бумага. Этот способ хоть и экономичен, но позволяет производить бумагу низкого сорта, которая чаще всего называется газетной.

Для получения бумаги более высокого качества, целлюлозу обрабатывают специальными химическими материалами. Такая бумага уже годится для использования в книгах, тетрадях и других печатных целях.
Для производства качественной бумаги, древесный материал сортируется по размерам, и в него добавляются различные химикаты, после чего варится, а затем промывается и фильтруется, чтобы в сырье не присутствовало примесей.
После варки, сырье прессуется, раскатывается и разглаживается, а потом сушится при большой температуре, чтобы волокна приняли нужную форму и застыли, образовав непосредственно бумагу. Таким образом, получается скорее рулонная лента, нежели листы. Но в дальнейшем, рулоны подлежат разрезке и дальнейшей подготовке. К дополнительной подготовке можно отнести дальнейшее глянцевание бумаги, окраска и другие процедуры.
Также, при производстве может использоваться краска, или специальные примеси. Это все и отличает бумагу по качеству, сорту и другим свойствам. Получаются такие типы бумаги, как книжная, газетная, офсетная, упаковочная, и так далее.
Как может показаться, производство бумаги является очень простым. Но на самом деле, это сложный технологический процесс, для которого требуются специальные станки и приспособления, а также наличие огромного количества людей, которые следят за производством и работой станков. В целом, производство бумаги очень даже интересный процесс.
wood-prom.ru
Состав для изготовления бумаги
Состав предназначен для изготовления бумаги и относится к области целлюлозно-бумажной промышленности. Состав содержит волокнистую составляющую, в качестве которой используют целлюлозу, древесную массу или макулатуру; проклеивающую составляющую, в качестве которой используют канифольный клей или алкилдимеркетен; наполнитель, в качестве которого используют каолин, двуокись титана или мел; крахмал, модифицированный биоцидной добавкой, в качестве которой используют синергетическую смесь полигексаметиленгуанидина с диметилбензилалкиламмонием при их соотношении (10-1):(1-10). Техническим результатом является улучшение показателей качества получаемой бумаги, в том числе антимикробной активности, а также упрощается и удешевляется процесс изготовления бумаги. 2 з.п. ф-лы, 4 табл.
Изобретение относится к области целлюлозно-бумажной промышленности и может быть использовано при производстве бумаги.
Известен состав для изготовления бактерицидной бумаги, содержащий воду, волокнистую суспензию и химическую добавку - блоксополимер полигексаметиленгуанидина (ПГМГ) и полиэтиленимина (ПЭИ), в качестве блок-сополимера используют блоксополимер с молекулярной массой от 5000-100000 при соотношении ПГМГ:ПЭИ (100-1):(1-100) в количестве 0,01-5,00% к массе абсолютно сухих волокон (пат. №2181808, кл. D 21 Н 27/00, 2001 г.).Недостатком этого состава для изготовления бумаги является недостаточно высокая бактерицидность, а также высокая жесткость и низкая впитывающая способность бумаги.Наиболее близким техническим решением к предлагаемому является состав для изготовления бумаги, содержащий воду, волокнистую суспензию, катионоактивный крахмал, полученный модификацией нативного картофельного крахмала, поли-N-2-гидроксипропил-гексаметиленгуанидином (а.с. №2083601, Д 21 Н 17/29, 1997).Недостатком известного способа является сложность осуществления процесса из-за использования легколетучих ацетона и спирта. Кроме того, достигаемые при этом показатели бумаги, в том числе физико-механические свойства и бактерицидность недостаточно высоки.Техническая задача, решаемая данным изобретением, состоит в улучшении показателей качества получаемой бумаги, в том числе антимикробной активности. Кроме того, упрощается и удешевляется процесс изготовления бумаги.Для решения технической задачи в составе для изготовления бумаги, включающем волокнистую составляющую, проклеивающую составляющую, наполнитель, крахмал, модифицированный биоцидной добавкой, и воду, в качестве волокнистой составляющей используют целлюлозу, или древесную массу, или макулатуру, в качестве проклеивающей составляющей используют канифольный клей или алкилдимеркетен, в качестве наполнителя используют каолин, или двуокись титана, или мел, в качестве биоцидной добавки используют синергетическую смесь полигексаметиленгуанидина с диметилбензилалкиламмонием при соотношении (10-1):(1-10) при следующем соотношении компонентов, маc.%:Волокнистая составляющая 65,0-75,0Проклеивающая составляющая 0,05-5,00Наполнитель 0,01-20,00Крахмал, модифицированныйсинергетической смесьюполигексаметиленгуанидина сдиметилбензилалкиламмонием 0,5-5,0Вода ОстальноеВ качестве полигексаметиленгуанидина используют хлорид полигексаметиленгуанидина или фосфат полигексаметиленгуанидина, или его соли с органическими физиологически активными кислотами.В качестве физиологически активных кислот используют борную или бензойную, или муравьиную, или дегидрацетовую, или сорбиновую.Присутствие диметилбензилалкиламмония (Катамина АБ) в составе смеси с ПГМГ приводит к явлению синергизма и способствует повышению антимикробных, биоцидных и фунгицидных свойств как самой смеси, так и конечного продукта, то есть бумаги.Модифицированный такой смесью крахмальный клейстер обладает значительно большей стабильностью к деструкции по сравнению с раствором немодифицированного крахмала, о чем можно судить из результатов измерения характеристической вязкости крахмальных растворов в процессе их хранения.В табл.1 представлены характеристики крахмального клейстера.При изготовлении бумаги с использованием добавки модифицированного крахмала в количестве 0,05-5,00% от массы абсолютно сухих волокон отмечено снижение степени помола и ускорение обезвоживания волокнистой суспензии на 20-30%. При этом, вследствие благоприятных условий формования бумаги и образования дополнительных связей в бумаге за счет модифицированного крахмала, показатели прочности бумаги возрастают на 10-30%. Кроме того, уменьшается жесткость и возрастает впитывающая способность бумаги.Предлагаемая добавка модифицированного крахмала обеспечивает высокую скорость обезвоживания волокнистой суспензии, что особенно важно при использовании волокнистых полуфабрикатов с высокой степенью помола. Применение модифицированного крахмала в указанных количествах приводит к снижению электрокинетического потенциала используемых для изготовления бумаги волокон, что вызывает их взаимное притяжение и микрофлокуляцию. Все это способствует более легкой водоотдаче и выражается снижением показателя степени помола и ускорением обезвоживания волокнистого полуфабриката. Одновременно отмечено повышение удержания в бумаге мелких волокон и частиц наполнителя.Достижение оптимальных технологических условий процесса изготовления бумаги на машине, а также появление дополнительных связей за счет модифицированного крахмала способствуют получению бумаги с более высокими физико-механическими показателями.Применение для модификации крахмала Катамина АБ в смеси с солями полигексаметиленгуанидина (ПГМГ) приводит к снижению жесткости бумаги и повышению ее впитывающей способности. Кроме того, наличие в модифицирующем составе двух бактерицидных добавок приводит к явлению синергизма, в результате чего антимикробная активность бумаги возрастает.Положительным моментом использования добавки является возможность изготовления бумаги в нейтральной среде, вследствие чего бумага в меньшей степени подвергается процессу старения, что важно для таких видов бумаги, как документная или банкнотная.Состав для изготовления бумаги готовят следующим образом: волокнистая составляющая (целлюлоза или древесная масса, или макулатура) размалывается в воде до определенной степени помола, затем в полученную волокнистую суспензию при перемешивании добавляют проклеивающую составляющую в виде канифольного или другого вида клея, наполнитель в виде суспензии, одновременно вводят крахмал, модифицированный синергетической смесью. Полученный состав подают на бумагоделательную машину.Для получения биоцидной добавки готовят 1-5%-ную смесь полигексаметиленгуанидина с деметилбензилалкиламмонием при соотношении (10-1):(1-10). Для приготовления смеси используют емкость с перемешивающим устройством. Проводят варку крахмала (нативного, окисленного или катионного) в другой емкости с перемешивающим устройством. Для этого емкость заполняют водой и при перемешивании и постепенном подъеме температуры до 90С загружают необходимую для приготовления клейстера порцию крахмала и синергетической смеси полигексаметиленгуанидина с ди-метилбензилалкиламмонием. Концентрация модифицированного крахмала - 1-20%. Количество модифицирующей смеси составляет 1-5% к абсолютно сухому веществу крахмала.Готовый раствор модифицированного крахмала, стабильность которого значительно повышена, вводят при перемешивании в суспензию для изготовления бумаги в технологически удобном месте, например в переливной бак на бумагоделательной машине или в оборотную воду.Кроме введения раствора модифицированного крахмала в волокнистую суспензию, возможно использование приготовленного раствора путем нанесения его на поверхность бумажного полотна методом распыления или пропитки в процессе получения бумаги на бумагоделательной машине или другом оборудовании, например, при изготовлении картонных коробок.Кроме того, возможно использование данного состава химикатов в качестве клея при склеивании отдельных слоев картона или бумаги.Примеры конкретного выполнения состава.Пример 1. Сульфатная беленая хвойная целлюлоза размалывается в воде до степени помола 50ШР. В полученную суспензию при перемешивании добавляют димер алкилкетена в количестве 2,5% к массе абсолютно сухих волокон, 20% двуокиси титана. Из полученной массы формуют бумажное полотно, которое обрабатывают с поверхности крахмалом, модифицированным синергетической смесью хлорида ПГМГ с диметилбензилалкиламмонием в соотношении 1:1, путем добавления в емкость при приготовлении крахмального клейстера 3% смеси к абсолютно сухому крахмалу.Содержание модифицированного крахмала составляет 3% от массы сухого вещества бумаги.Состав для изготовления бумаги имеет следующее соотношение компонентов, мас.%:Волокнистая составляющая(сульфатная беленая хвойная целлюлоза) 70,0Проклеивающая составляющая (димералкилкетена) 2,5Наполнитель (двуокись титана) 20,0Крахмал, модифицированный синергетической смесью ПГМГ с диметилбензилалкиламмонием 3,0Вода ОстальноеПолученная бумага массой 70 г/м2 отличается высокими физико-механическими показателями и может быть использована для печати.Кроме высоких показателей прочности, бумага обладает антимикробными и фунгицидными свойствами.Пример 2. Волокнистый состав из древесной массы (50%) и макулатуры (50%) размалывается в воде до степени помола 80ШР. В полученную суспензию при перемешивании добавляют канифольный клей в количестве 3,5% от массы сухих волокон, 10% каолина, 0,5% крахмала, модифицированного синергетической смесью бензоата ПГМГ с диметилбензилалкиламмонием в соотношении 10:1, путем добавления в емкость при приготовлении крахмального клейстера 5% смеси к абсолютно сухому крахмалу.Содержание модифицированного крахмала составляет 3% от массы сухого вещества бумаги.Состав для изготовления бумаги имеет следующее соотношение компонентов, мас.%:Волокнистая составляющая(древесная масса и макулатура) 70,0Проклеивающая составляющая(канифольный клей) 3,5Наполнитель (каолин) 10,0Крахмал, модифицированныйсинергетической смесью ПГМГс диметилбензилалкиламмонием 0,5Вода ОстальноеПри введении модифицированного крахмала степень помола волокнистой суспензии уменьшается до с 80 до 50 ШР, что улучшает условия формования бумажного полотна. Полученная бумага массой 50 г/м2 отличается высокими физико-механическими показателями, антимикробными свойствами и может быть использована в качестве газетной бумаги.Пример 3. Состав для изготовления бумаги готовят по примеру 2 с использованием в качестве наполнителя мел в количестве 0,02%.Состав для изготовления бумаги имеет следующее соотношение компонентов, мас.%:Волокнистая составляющая(древесная масса и макулатура) 70,0Проклеивающая составляющая(канифольный клей) 1,5Наполнитель (мел) 0,02Крахмал, модифицированныйсинергетической смесью ПГМГс диметилбензилалкиламмонием 5,0Вода ОстальноеМодификацию крахмала (катионного) проводят синергетической смесью фосфата полигексаметиленгуанидина с диметилбензилалкиламмонием при соотношении 10:1 путем добавления в емкость при приготовлении крахмального клея 5% смеси к абсолютно сухому крахмалу.Полученная бумага массой 40 г/м2 может быть использована для изготовления изделий санитарно-бытового назначения: туалетной бумаги, полотенец, салфеток. Бумага отличается высокими антимикробными свойствами и впитывающей способностью.Пример 4. Состав для изготовления бумаги готовят по примеру 2 с использованием в качестве волокнистой составляющей макулатуры.Состав для изготовления бумаги имеет следующее соотношение компонентов, мас.%:Волокнистая составляющая(макулатура) 70,0Проклеивающая составляющая(канифольный клей) 3,5Наполнитель (каолин) 10,0Крахмал, модифицированныйсинергетической смесью ПГМГс диметилбензилалкиламмонием 5,0Вода ОстальноеМодификацию крахмала (катионного) проводят синергетической смесью дегидрацетовой соли полигексаметиленгуанидина с диметилбензилалкиламмонием при соотношении 1:1 путем добавления в емкость при приготовлении крахмального клейстера 4,5% смеси к абсолютно сухому крахмалу.Полученная двухслойная бумага массой 100 г/м2 может быть использована для изготовления изделий для упаковки продуктов. Бумага отличается высокими антимикробными и биоцидными свойствами.В табл.2 представлены данные, подтверждающие оптимальность заявленных пределов содержания компонентов состава для изготовления бумаги.В табл.3 представлены данные, подтверждающие оптимальное соотношение ПГМГ и Катамина АБ.В табл.4 представлены физико-механические показатели бумаги.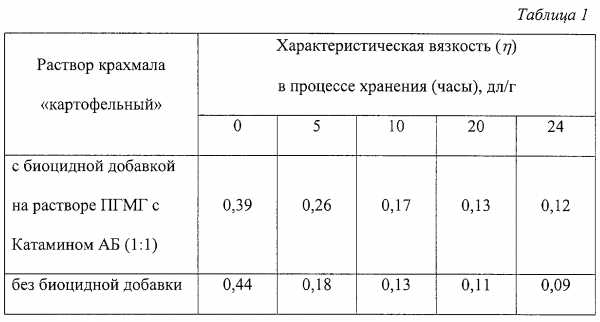
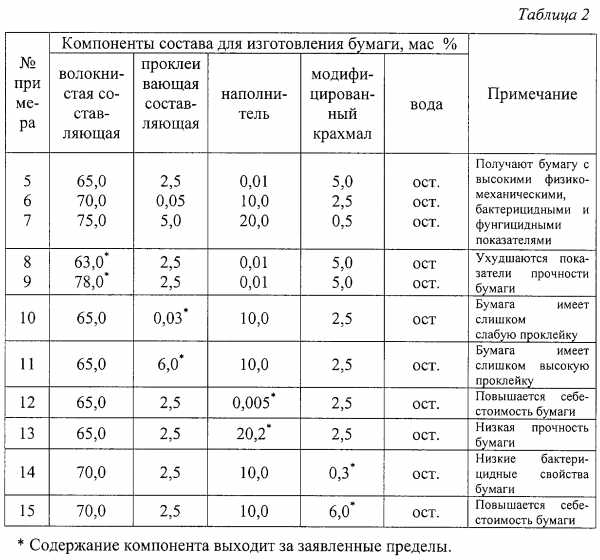
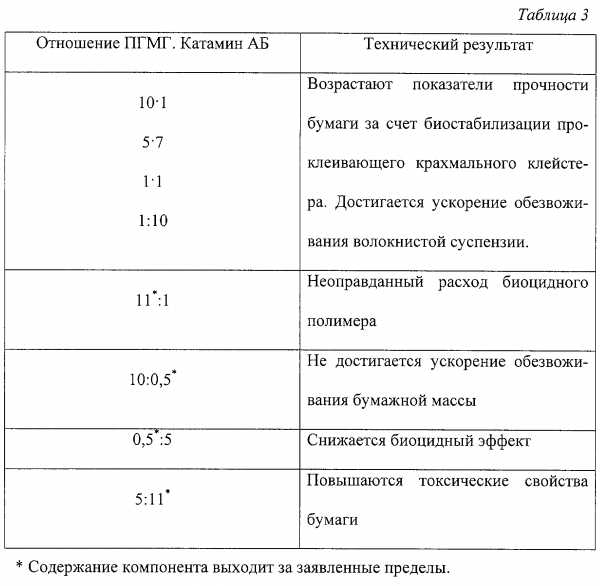
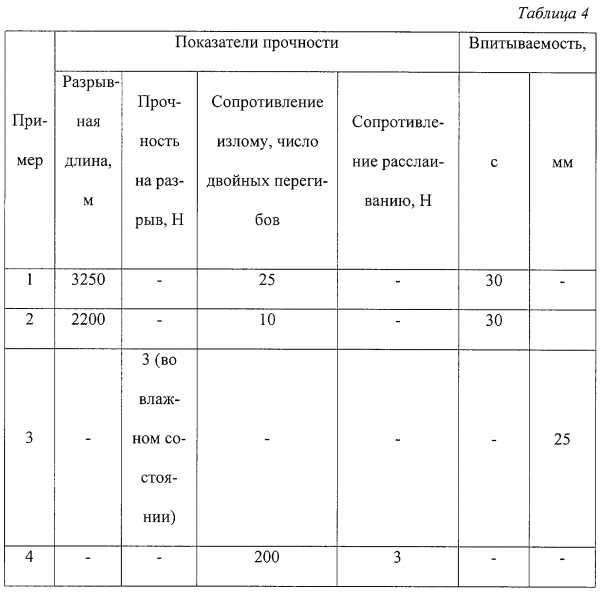
Формула изобретения
1. Состав для изготовления бумаги, включающий волокнистую составляющую, проклеивающую составляющую, наполнитель, крахмал, модифицированный биоцидной добавкой, и воду, отличающийся тем, что в качестве волокнистой составляющей используют целлюлозу, или древесную массу, или макулатуру, в качестве проклеивающей составляющей используют канифольный клей или алкилдимеркетен, в качестве наполнителя используют каолин, или двуокись титана, или мел, в качестве биоцидной добавки используют синергетическую смесь полигексаметиленгуанидина с диметилбензилалкиламмонием при соотношении (10-1):(1-10) при следующем соотношении компонентов, мас.%:Волокнистая составляющая 65,0-75,0Проклеивающая составляющая 0,05-5,00Наполнитель 0,01-20,00Крахмал, модифицированныйсинергетической смесьюполигексаметиленгуанидинас диметилбензилалкиламмонием 0,5-5,0Вода Остальное2. Состав для изготовления бумаги по п.1, отличающийся тем, что в качестве полигексаметиленгуанидина используют соли ПГМГ - хлоридполигексаметиленгуанидина или фосфат полигексаметиленгуанидина, или соли ПГМГ с органическими физиологически активными кислотами.3. Состав для изготовления бумаги по п.2, отличающийся тем, что в качестве физиологически активных кислот используют борную, или бензойную, или муравьиную, или дегидрацетовую, или сорбиновую.www.findpatent.ru
Бумага: состав, производство, виды | CMYKom.ru
Опубликовано: Июнь 7, 2013 by admin
Оставить комментарий
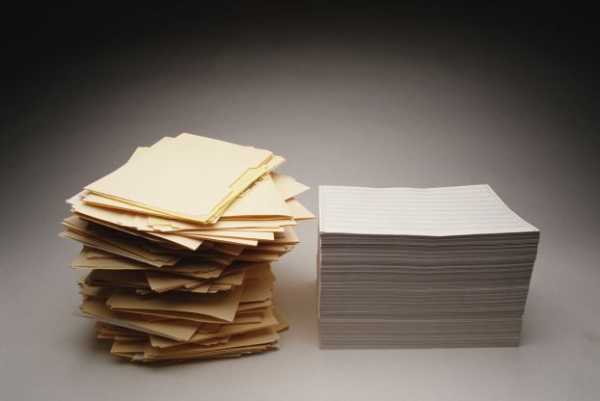
Бумага (от итал. bambagia — хлопок) — многокомпонентный материал, состоящий в основном из специально обработанных мелких растительных волокон, тесно переплетенных между собой, связанных силами сцепления различного вида и образующих тонкий лист.
Считается, что бумагу изобрели в Китае во 2 в. до н.э., а уже в 76 ее применяли для книг. Из Китая бумага проникла в Японию, а затем через Персию в Северную Африку, на Кипр, в 1154 в Испанию и затем в ряд других стран. Она постепенно стала вытеснять применявшийся до этого для письма папирус и другие материалы.
До 18 века изготовление (отлив) бумаги происходило вручную. В 1799 француз П.Л. Робер предложил механизированный отлив бумаги на непрерывно движущейся бесконечной сетке, расположенной над черпальным чаном. Позднее появилась первая бумагоделательная машина, состоящая из следующих основных частей: сеточной, прессовой, сушильной, отделочной. Для получения отдельных высококачественных видов и бумаги специального назначения до сих пор применяется ручной отлив.
Наиболее распространенный способ производства бумаги — «мокрый», который базируется, как правило, на использовании плоско- или двухсеточных бумагоделательных машин. Такая бумагоделательная машина состоит из:
- сеточной
- прессовой
- сушильной частей
- каландра (пресса, состоящего из 2–20 валов, между которыми пропускают бумагу)
- наката (устройство для наматывания бумаги в рулон)
Сеточная часть имеет одну или две бесконечно движущиеся сетки, на которую (плоскосеточные машины) или в зазор между которыми (двухсеточные машины) непрерывным потоком равномерно по всей ширине сеток поступает разбавленная водой бумажная масса. При обезвоживании бумажной массы происходит формирование бумажного полотна, которое далее обезвоживается в прессовой части и окончательно высушивается в сушильной части машины. Прессовая часть состоит из нескольких 2-вальных (иногда 3-вальных) прессов, между валами которых проходит бумажное полотно. При этом часть влаги из него отжимается. Сушильная часть состоит из 2-ярусных батарей сушильных вращающихся цилиндров, обогреваемых изнутри паром. Сырое бумажное полотно, проходя между горячими поверхностями цилиндров и сушильным сукном каждой батареи, высушивается до влажности 5–7%. В конце сушильной части имеется холодильный цилиндр (иногда два) для охлаждения бумаги. Затем бумага проходит каландр, придающий ей машинную гладкость, и наматывается в рулон на накате.
Для отделки бумаги применяются суперкаландры (система вращающихся с разной скоростью валов, между которыми пропускают увлажненное бумажное полотно), обеспечивающие более ровную гладкую поверхность и глянец. Такая бумага называется каландрированной (глазированной) и высококаландрированной (дважды пропускается через суперкаландр). Для придания бумаге глянца бумажное полотно пропускают через лощильный (или фрикционный) каландр, валы которого совершают возвратно-вращательное движение, не оказывая большого давления на бумагу.
С 1950-х гг. в производстве бумаги находят применение полимерные пленки и синтетические волокна, на основе которых выпускают синтетическую бумагу. Такая бумага отличается высокой механической прочностью в сухом и влажном состоянии, хорошей стабильностью линейных размеров при увлажнении, долговечностью, высокой эластичностью.
В качестве основных компонентов композиционного состава бумаги используют волокна растительного происхождения, выделяемые из древесины хвойных и лиственных пород, из стеблей однолетних растений, семенных коробочек и листьев некоторых растений. В зависимости от метода производства, выхода гемицеллюлоз (веществ, сходных с целлюлозой, но с меньшей молекулярной массой) и лигнина (инкрустирующего вещества), получают различные полуфабрикаты: древесную массу, полухимическую массу (полуцеллюлозу), небеленую, беленую и облагороженную целлюлозу.
Для снижения гидрофильности и гигроскопичности (впитывания при смачивании и поглощения воды из воздуха) бумагу проклеивают смолами с водоотталкивающими свойствами (гидрофобные) и парафинами. Для повышения прочности, гладкости (уменьшения ворсистости), стойкости к выщипыванию и истиранию наиболее эффективна поверхностная проклейка в клеильных прессах крахмальным, карбоксиметилцеллюлозным и др. клеями. В зависимости от степени проклейки различают бумагу слабоклееную, клееную и высококлееную. В бумажную массу вводят наполнители — белые порошкообразные, нерастворимые в воде минеральные вещества: каолин, сернокислый барий, тальк, двуокись титана и др. Они повышают белизну, гладкость и непрозрачность бумаги, делают ее более мягкой, легко деформируемой (пластичной), но и менее прочной.
Повышенное содержание наполнителей (зольность) необходимо бумаге для высокой печати, т.к. повышенная пластичность позволяет снизить давление для хорошей пропечатки оттиска, а для глубокой печати — лучшего впитывания и снижения растекаемости жидкой краски на оттисках. По содержанию наполнителей различают мало-, среднезольную, повышенной зольности и высокозольную бумагу.
Важнейшие показатели бумаги:
- масса бумаги площадью 1 м2
- толщина
- плотность
- прочность
- гладкость
- пористость
- белизна
- непрозрачность,
- оттенок и др.
Листовая и рулонная бумага для печати выпускается с массой площади 40–250 г/м2. Ниже приведены характеристики некоторых видов бумаг, применяемых в издательском деле и полиграфии.
Типографская (для высокой печати) — 50–70 г/м2, на основе древесной целлюлозы или с добавлением 20–75% древесной массы, белая, малоклееная, среднезольная или повышенной зольности, машинной гладкости, каландрированная или высококаландрированная. Предназначена для печати текстовой и иллюстрационно-текстовой продукции. Бумага с массой площади 40- 50 г/м2, чистоцеллюлозная или с небольшим добавлением древесной массы, повышенной зольности, малоклееная, каландрированная, с органической прозрачностью предназначена для печатания справочников и других книг с большим количеством текста.
Для глубокой печати — белая 60–220 г/м2, чистоцеллюлозная, слабоклееная, высокозольная, обладающая ровной сомкнутой (мелкопористой) поверхностью, каландрированная. Предназначена для печатания иллюстрационно-текстовых изданий и изобразительной продукции.
Офсетная — 60–250 г/м2, чисто целлюлозная или с содержанием до 75% древесной массы, белая, клееная, с хорошей стойкостью поверхности к выщипыванию, низкой деформацией при увлажнении, машинной гладкости или каландрированная. Предназначена для печатания иллюстрационно-текстовых изданий и изобразительной продукции офсетным способом. Офсетную бумагу используют для изготовления блокнотов, блоков для записей, кубариков ( кубиков для записей).
Газетная — 45–49 г/м2, низкозольная, неклееная, машинной гладкости, в композиции преобладает древесная масса. Предназначена для печатания газет и приложений к ним, массовых брошюр способами высокой и офсетной печати.
Мелованная — с пигментированно-клеевым покровным слоем (мелованным), нанесенным на волокнистую чистоцеллюлозную или содержащую древесную массу бумагу — основу для получения микропористой и микрошероховатой поверхности. Различают одно- и двукратного мелования с одно- и двусторонним покрытием мелованным слоем. Предназначена для печатания одно- и многокрасочной изобразительной продукции, различных иллюстрационно-текстовых изданий способами высокой, офсетной и глубокой печати. Разновидность — тонкая мелованная бумага 60–70 г/м2, предназначена для издания массовой иллюстрационно-текстовой продукции способами офсетной и глубокой печати. В листовом офсете используется мелованная бумага плотностью от 90 г/м2. Для изготовления бумажных пакетов используют мелованную бумагу плотностью от 170 г.
Обложечная — светопрочная, чистоцеллюлозная или с содержанием до 40% древесной массы, клееная, малозольная бумага с небольшими усадкой и скручиваемостью при одностороннем увлажнении, каландрированная и машинной гладкости. Предназначена для изготовления обложек (140–200 г/м2) и склейки переплетных крышек (80–120 г/м2).
Форзацная — клееная, среднезольная бумага 80–160 г/м2, чистоцеллюлозная, машинной гладкости или каландрированная, отличается повышенным сопротивлением излому, ограниченной скручиваемостью после одностороннего увлажнения. Предназначена для изготовления форзацев книг.
Писчая — белая или цветная, 45–80 г/м2, чистоцеллюлозная (с добавлением целлюлозы из хлопкового линта) или содержащая небольшую часть древесной массы, клееная, машинной гладкости или каландрированная. Предназначена для изготовления бланков, унифицированных систем документации, бумажно-беловых изделий, бумаг потребительских форматов, школьных тетрадей и т.п.
Документная — на основе льнопеньковых и хлопковых волокон, малозольная, высококлееная, иногда с водяными знаками, долговечная, стойкая к механическим воздействиям. Предназначена для печатания денежных знаков, облигаций, банковских чеков и других документов.
Афишная и билетная — белая или цветная, малозольная, слабоклееная, машинной или односторонней гладкости. Предназначена для печати афиш, билетов, абонементных талонов, бланков способом высокой печати.
Картографическая — 85–160 г/м2, композиция на основе древесной целлюлозы и из хлопкового линта (отхода хлопкового производства), малозольная, клееная, машинной гладкости или каландрированная, прочная в сухом и влажном состоянии, повышенной белизны. Предназначена для печатания гидро-, топо-, географических и других карт и атласов офсетным способом.
Баритованная — используется в качестве основы фотобумаги. Белая или подцвеченная красителем толстая бумага с баритовым (из сернокислого бария) покровным слоем, нанесенным на чистоцеллюлозную, малозольную, высококлееную основу повышенной белизны для улучшения качества поверхности.
Ватманская (ватман) — белая чертежная высокосортная ручного отлива на основе механически обработанного тряпья (тряпичной полумассы) с поверхностной проклейкой. Отличается большим сопротивлением к истиранию и шероховатой поверхностью. Предназначена для чертежных работ, выполняемых карандашом, тушью и акварельными красками.
Верже — белая или цветная чистоцеллюлозная высокосортная с водяными знаками в виде близко расположенных узких полос, иногда пересеченных, под прямым углом к машинному направлению, редко расположенными полосами. Предназначена для изготовления подарочных изданий, а также форзацев и суперобложек книг.
Этикеточная — 45–120 г/м2, малоклееная или клееная, одно- или двусторонней гладкости, односторонне мелованная, с ограниченной поверхностной впитываемостью, линейной деформацией при увлажнении и скручиваемостью при одностороннем смачивании водой. Предназначена для печатания этикеток способами высокой и офсетной печати.
Крафт-бумага — особый вид оберточной бумаги на основе очень крепкой, так называемой, крафт-целлюлозы. Отличается высокой механической прочностью. Предназначена для обертки, упаковки.
← ManRoland на выставке China Print 2013 Новинка от Heidelberg: вкладочно-швейно-резальный агрегат Stitchmaster ST 200 Compact →cmykom.ru