Обзор методов фосфатирования металлов. Фосфатное покрытие
Фосфатирование
Фосфатирование используют для дополнительной защиты от коррозии, улучшения твердости, износостойкости, повышения электроизоляционных свойств основного покрытия на черных и цветных металлах. Суть процесса фосфатирования состоит в создании на поверхности защищаемого изделия слоя малорастворимых фосфатов железа, цинка или марганца.
Фосфатированию подвергаются: чугун, низколегированные, углеродистые стали, кадмий, цинк, медь, сплавы меди, алюминий.
Фосфатированию плохо поддаются высоколегированные стали.
Изделия, подвергшиеся фосфатированию, эксплуатируются даже в тропиках. Фосфатная пленка не боится органических масел, смазочных, горячих материалов, толуола, бензола, всех газов, кроме сероводорода.
Под воздействием щелочей, кислот, пресной, морской воды, аммиака, водяного пара покрытие довольно быстро разрушается. Непродолжительный срок службы покрытия также связан с его низкой эластичностью и прочностью.
Процесс фосфатирования нашел широкое применение в автомобильной промышленности. Фосфатная пленка – наилучший грунт. Стальной корпус автомобиля перед покраской подвергают фосфатированию, а далее окрашивают эмалями.
Фосфатное покрытие
Толщина и структура фосфатного покрытия
Толщина фосфатного слоя составляет от 2 – 8 до 40 - 50 мкм (зависит от режима фосфатирования, подготовки поверхности, состава раствора для фосфатирования). Толщина покрытия связана с его структурой. Мелкокристаллические защитные слои имеют меньшую толщину (1 – 5 мкм) и обладают более выраженной защитной способностью. В связи с этим их намного чаще используют. Получают такие покрытия из цинкфосфатных растворов, которые содержат ускорители (окисляющие элементы). Мелкокристаллические слои не используются в качестве самостоятельных защитных. После получения такого слоя поверхность подвергают дополнительной обработке лакокрасочными материалами.
Крупнокристаллические фосфатные слои более толстые, получают их из марганцевофосфатных растворов. После промасливания могут служить самостоятельными покрытиями.
Кристаллы фосфатов имеют пластинчатую структуру, благодаря чему пленка отлично впитывает различные пропитки, лаки, удерживая их в себе.
Фосфатное покрытие состоит из двух слоев. Первый, плотно прилегающий к поверхности слой, плотно связан с металлом, незначительной толщины, имеет пористую структуру, а также гладкий и достаточно эластичный. Он состоит, в большей части, с монофосфатов железа. Второй слой (наружный) – состоит из монофосфатов марганца, вторичных и третичных фосфатов. Он более хрупкий, кристаллический. Характеристиками именно наружного слоя обуславливается ценность фосфатных пленок.
Цвет фосфатного покрытия
Цвет фосфатного покрытия колеблется от светло-серого до темно серого (почти черного). Светло-серые фосфатные пленки образуются на цветных металлах и малоуглеродистых сталях. Предварительно подвергшихся пескоструйной обработке поверхностях, в растворах повышенной кислотности.
Если чугунное (либо из высоколегированной стали) изделие предварительно подвергалось травлению, и концентрация ортофосфорной кислоты больше обычного - фосфатный слой получается более темного оттенка. Фосфатное покрытие зеленоватого оттенка образуется на поверхности стали, содержащей никель и хром.
Свойства фосфатного покрытия
Полученное фосфатное покрытие может использоваться как самостоятельное защитное, но в большинстве случаев его используют как основу под лакокрасочное, смазочное, либо перед пассивированием. То, что его очень редко используют, как самостоятельное, можно объяснить тем, что оно легко разрушается под воздействием кислот и щелочей.
Фосфатное покрытие не подвергается воздействию кислорода воздуха, смазок, масел, керосина, не смачивается расплавленными металлами. Фосфатный слой может выдержать непродолжительное влияние температуры около 500 °С. Наибольшая минусовая температура, при которой не разрушается покрытие -75 °С. При длительной выдержке фосфатный слой теряет свои защитные свойства и постепенно разрушается.
Фосфатное покрытие отличается высоким электросопротивлением, может выдержать напряжение до 500 В. Чтоб повысить пробивное напряжение готового фосфатного покрытия (до 1000 В) – его дополнительно пропитывают бакелитовыми либо масляными лаками. Фосфатное покрытие по твердости мягче стали, но более твердое, чем латунь или медь.
При щелочном оксидировании стали полученный защитный слой имеет меньшую защитную способность, чем обычные фосфатные слои.
Подготовка поверхности перед операцией фосфатирования играет важную роль, т.к. от ее способа и качества во многом зависят свойства полученного покрытия, а именно – структура, адгезионная способность, толщина, цвет фосфатной пленки.
При фосфатировании заранее протравленной поверхности (с использованием HCl, h3SO4, h4PO4) образуются крупнокристаллические, рыхлые фосфатные слои, толщиной до 40 – 50 мкм. Они обладают достаточно низкими защитными свойствами, поэтому для улучшения качества пленки деталь промывают в 3 – 5 % растворе кальцинированной соды, а далее в воде и затем только фосфатируют. Или же в 1 – 2 % растворе хозяйственного мыла и 5 – 8 % растворе кальцинированной соды при температуре 55 – 60 °С.
Мелкокристаллические, тонкие (толщиной от 5 до 10 мкм) пленки образуются на поверхностях, обработанных пескоструйным методом с последующим обезжириваниям (с использованием органических растворителей или же химическим способом), также механически обработанные кругом, и т.п. Такие фосфатные пленки отличаются хорошей адгезией к поверхности и высокими защитными свойствами.
Суть процесса фосфатирования
Фосфорная кислота (h4PO4) образует три вида солей (именно на свойствах солей фосфорной кислоты и основан метод защиты): дигидрофосфаты, моногидрофосфаты, фосфаты.
Дигидрофосфаты Me(h3PO4)2 – однозамещенные соли, где Me – двухвалентный металл. Образуются сразу при первичном контакте металла с фосфорной кислотой. Взаимодействие описывается реакцией:
Me + 2h4PO4 → Me(h3PO4)2 + h3↑.
При дальнейшем взаимодействии кислоты с металлом (концентрация кислоты уменьшается) образуются двухзамещенные (моногидрофосфаты MeHPO4) и трехзамещенные (фосфаты Me3(PO4)2) соли.
Реакции образования вторичных и третичных солей:
Me(h3PO4)2 ↔ MeHPO4 + h4PO4 - продуктами реакции являются двухзамещенная соль и свободная ортофосфорная кислота;
3Me(h3PO4)2 ↔ Me3(PO4)2 + 4h4PO4 – образуется трехзамещенная соль, свободная ортофосфорная кислота.
Труднорастворимые фосфаты железа – основная составляющая часть фосфатных покрытий. Их качество определяется свободной и основной кислотностью раствора, природой катионов металла, концентрацией монофосфатов.
При введении в раствор для фосфатирования окислительных анионов (например, ClO3, NO2, NO3) процесс формирования защитной пленки значительно ускоряется.
При фосфатировании на поверхности металла наблюдается два основных процесса – осаждение фосфатов и растворение основного металла.
Фосфатирование черных металлов
Сегодня самое широкое применение получил препарат для фосфатирования Мажеф. Выпускается в виде серой массы, расфасованной по бочкам или ящикам. Отличается характерным кисловатым запахом. Название препарата произошло от первых букв его составных частей: марганец, железо, фосфорная кислота.
Фосфатная пленка при использовании данного препарата обладает хорошими защитными свойствами.
Процесс получения фосфатной пленки с использованием данного препарата имеет свои недостатки: высокие температуры, узкий рабочий интервал температур, длительность операции, наводораживание стали (из-за сильного выделения водорода). Чтоб снизить наводораживание уменьшают длительность процесса.
Фосфатирование может быть электрохимическим и химическим.
Химическое фосфатирование черных металлов, в свою очередь, подразделяется на холодное, нормальное и ускоренное.
Холодное фосфатирование
Холодное фосфатирование проводится без подогрева рабочих растворов. Фосфатное покрытие получается довольно тонким и используется в качестве основы под покраску. В основу растворов для холодного фосфатирования входят препарат Мажеф и однозамещенный фосфат цинка (Zn(h3PO4)2). NaNO2 и NaF играют роль активаторов процесса.
Составы для холодного фосфатирования:
Состав №1: 25 – 30 г/л пр. Мажеф, 35 – 40 г/л Zn(NO3)2•6h3O, 5 – 10 г/л NaF, длительность обработки 40 минут;
Состав №2: 60 – 70 г/л Zn(h3PO4)2, 80 – 100 г/л Zn(NO3)2•6h3O, 0,3 – 1.0 г/л NaNO2, продолжительность обработки 15 – 25 мин.;
Состав №3: 100 г/л Zn(h3PO4)2, 6 г/л NaF, 2 г/л NaNO2, длительность обработки 30 - 40 минут;
Состав №4: 18 – 21 г/л ZnO, 80 – 85 г/л h4PO4, 1 - 2 г/л NaNO2, продолжительность обработки 15 – 20 минут.
Если температуру раствора увеличить – можно получить мелкокристаллическое покрытие.
Растворы для холодного фосфатирования довольно быстро гидролизуются (при контакте составных веществ с водой разлагаются основные молекулы и образуются новые соединения), увеличивается свободная кислотность раствора. Это отрицательно сказывается на качестве фосфатного покрытия, т.к. слой получается пористый и с низкими защитными характеристиками. Поэтому холодное фосфатирование используется довольно редко.
Нормальное фосфатирование
Препарат Мажеф, используемый также и при нормальном фосфатировании, имеет химический состав: 2,4 – 2,5 % Fe, 14 % Mn, 46 – 52 % фосфатов, 1 % SO42-, самую малость ионов хлора и CaO, 1 – 2 % h3O.
Однозамещенные соли ортофосфорной кислоты, марганца, железа (MnHPO4, Fe(h3PO4)2, Mn(h3PO4)2) и являются основой препарата.
Наилучший результат фосфатирования дает раствор, содержащий 30 – 33 г/л препарата Мажеф. Температура – 97 – 98 °С. Если вести процесс при более высоких температурах – образуется много шлама, а при более низких – покрытие имеет кристаллическую структуру.
Длительность процесса нормального фосфатирования: время выделения водорода + выдержка около 5 – 10 минут. Кислотность раствора (общая) должна составлять около 30 точек, свободная 3 – 4 точки. (Точка – мера общей и свободной кислотности раствора. Одна точка показывает количество мм 0,2 н. раствора щелочи, израсходованного на процесс титрования 10 мл фосфатного раствора).
Если свободная кислотность превышает указанное значение – ухудшаются свойства фосфатного слоя, а сам процесс затягивается по времени. При уменьшении – полученные пленки слишком тонкие и незащитные.
При повышении концентрации препарата Мажеф до 100 – 200 г/л получают более толстые фосфатные слои с повышенными защитными свойствами и мелкокристаллической структуры. С повышением концентрации немного уменьшают температуру рабочего р-ра (до 80 – 85 °С).
При фосфатировании высоколегированных сталей количество препарата Мажеф составляет около 30 – 32 г/л. Дополнительно вводят 10 – 12 % BaCl2 для улучшения качества фосфатного слоя. Изделие выдерживают в рабочем растворе 45 – 60 минут при температуре около 100 °С.
Ускоренное фосфатирование
Ускоренное фосфатирование получило довольно широкое промышленное применение, т.к. процесс ведется быстрее, чем при нормальном, и имеет свои преимущества.
Длительность процесса ускоренного фосфатирования (с использованием препарата Мажеф) составляет 8 – 15 минут. Рабочий раствор подогревают до температуры 45 – 65 °С (или же 92 – 96 °С, если использовать электролит №2). Дополнительно вводят окислители (NaF, Zn(NO3)2 и др.), благодаря которым ускоряется процесс фосфатирования, выделяется намного меньше водорода и окисляется Fe2+ до Fe3+.
Растворы для ускоренного фосфатирования с применением препарата Мажеф:
Раствор №1: 30 – 40 г/л препарата Мажеф, 50 – 65 г/л Zn(NO3)2•6h3O, 2 – 5 г/л NaF;
Раствор №2: 30 – 40 г/л препарата Мажеф, 50 – 70 г/л Zn(NO3)2•6h3O, 4 – 5 г/л NaNO3, 0,1 – 1,0 г/л h4PO4.
После ускоренного фосфатирования изделия обрабатывают раствором бихромата калия, а далее – сушат.
Пленки, полученные при ускоренном фосфатировании, небольшой толщины и не отличаются высокими защитными свойствами, поэтому их используют как основу (грунт) для лакокрасочных покрытий.
Ускоренное фосфатирование может проводится и с использованием других растворов, например, цинкофосфатных (основа – первичный фосфат цинка).
Составы для ускоренного фосфатирования с применением цинкофосфатных растворов:
Состав №1: 8 – 12 г/л Zn(h3PO4)2, 10 – 20 г/л Zn(NO3)2•6h3O, 30 – 40 г/л Ba(NO3)2, температура 75 – 85 °С, продолжительность 3 - 10 минут;
Состав №2: 28 – 36 г/л Zn(h3PO4)2, 42 – 58 г/л Zn(NO3)2•6h3O, 9,5 – 15,0 г/л h4PO4, температура 85 – 95 °С, продолжительность 10 – 25 минут.
Покрытия, полученные в вышеописанных электролитах, состоят с Zn3(PO4)2•4h3O и Zn2Fe(PO4)2•4h3O. Большая часть фосфатов образуется на поверхности в первые минуты процесса, когда скорость нарастания фосфатов превышает скорость их растворения. При одинаковых значениях этих скоростей рост фосфатной пленки прекращается.
Ускоренное фосфатирование можно проводить как погружением в ванну с раствором, так и распылением состава на поверхность.
Для струйного ускоренного фосфатирования часто используют раствор на основе препарата Мажеф следующего состава: 30 – 60 г/л пр. Мажеф, 50 – 70 г/л Zn(NO3)2•6h3O, 2 – 4 г/л NaNO2. Температура раствора - 15 – 25 °С, рН 2,6 – 3,2.
Широко используются концентраты для фосфатирования стали (на основе первичных фосфатов), такие, как КФЭ-1, КФЭ-2, КФ-1, КФ-3.
Чтоб улучшить структуру покрытия в основной р-вор вводят оксалаты цинка (до 0,1 г/л). При фосфатировании в таком растворе с поверхности изделия удаляется ржавчина.
Частным случаем химического - является черное фосфатирование. Используется в оптическом приборостроении. Фосфатная пленка черного цвета более привлекательна на вид и более коррозионноустойчива, чем полученные другими способами. Процесс черного фосфатирования состоит с двух частей. Сначала, предварительным фосфатированием, получают черную пленку. Далее, при фосфатном пассивировании, заполняются поры начального слоя.
Электрохимическое фосфатирование
Электрохимическое фосфатирование проводят в растворах схожего состава, но с использованием постоянного либо переменного тока. Это позволяет повысить производительность процесса.
Детали развешивают на катодных штангах, анодами служат пластины (цинк или углеродистая сталь, зависит от состава электролита). Плотность тока – от 0,3 до 3 А/дм2. Продолжительность процесса – от 5 до 20 мин.
Полученные пленки используются в качестве подслоя для лакокрасочного покрытия.
Недостаток электрохимического фосфатирования – низкая рассеивающая способность электролита. Вследствии, на деталях сложной формы фосфатное покрытие ложится неравномерно.
Фосфатирование цветных металлов
Фосфатированию часто подвергают многие цветные металлы. Чаще всего это цинк, магний, алюминий, кадмий, никель, титан.
Фосфатирование титана проводят для повышения его износостойкости, антифрикционных свойств. Процесс ведется при температуре 98 – 99 °С около 10 – 30 минут. Применяемый состав: 10 – 100 г/л ортофосфорной кислоты и такое же количество фторидов (NaF, Nh5F или KF).
Магний фосфатируют в р-рах однозамещенных фосфатов для защиты от коррозии. Фосфатирование магния (как и алюминия) применяют реже, чем его оксидирование.
Для кадмия, алюминия, цинка и большинства цветных металлов фосфатная пленка используется в качестве основы перед нанесением лакокрасочного покрытия.
Алюминий фосфатируют в растворах ортофосфорной кислоты с содержанием CrO3 и NaF или HF. Пленки имеют голубовато-зеленый цвет, поэтому процесс получил название «голубое фосфатирование». Получившийся фосфатный слой тонкий (около 3 мкм), гладкий, аморфный, не отличается высокими защитными свойствами (имеет низкие прочностные характеристики). Состав покрытия таков: около 50 – 55% CrPO4, 17 – 23% AlPO4, 22 – 23% воды. После промывки в холодной воде и сушки при температуре ниже 60 °С фосфатная пленка становится более прочной, может выдержать температуру до 300 °С. Если готовое фосфатное покрытие на протяжении 10 минут обрабатывать в 10 % растворе K2Cr2O7 (при температуре 75 – 80 °С) – его коррозионная стойкость значительно увеличится.
Для фосфатирования кадмия, цинка применяют универсальный цинк-фосфатный раствор. Для получения фосфатной пленки на цинке можно использовать раствор на основе композиции Ликонда Ф1А, обработка ведется при температуре 19 – 40 °С на протяжении 5 – 10 минут. В итоге – на поверхности цинка образуется мелкокристаллическая серо-дымчатая фосфатная пленка с высокими защитными свойствами (лучше, чем при хроматировании).
Никель (его сплавы) фосфатируют только матовый, на блестящем покрытие почти не осаждается. Рекомендованный состав раствора: 15 г/л h4PO4, 13 г/л NaF, 200 г/л Zn(NO3)2. Длительность обработки – 35 – 45 минут при температуре 25 – 35 °С. рН раствора около 2,0.
Улучшение защитных свойств фосфатных пленок
Фосфатные пленки не обладают достаточными защитными свойствами из-за своей пористой структуры, поэтому после получения их еще дополнительно обрабатывают. Для этого применяют пассивирующие растворы K2Cr2O7 (калия дихромат) либо Na2Cr2O7 (натрия дихромат). Процесс ведется при температуре 70 – 80 °С. Пассивирование фосфатных пленок возможно в двух составах: 80 – 100 г/л хромата и 3 – 5 г/л. Для первого раствора время выдержки составляет 10 – 20 минут, и дополнительная промывка до сушки. Для второго – 1 – 3 минуты, после фосфатирования изделие сушат без предварительной промывки.После проведения операции пассивирования готовые изделия пропитывают минеральным маслом (горячим), а далее гидрофобизируют (3 – 5 мин). Для гидрофобизации применяют 10 % раствор в бензине кремнийорганической жидкости ГФЖ-94.Если деталь предназначена для холодной деформации – ее промывают и обрабатывают около 3 – 5 минут при 60 – 70 °С в мыльном растворе (70 – 100 г/л хозяйственного мыла).
www.okorrozii.com
Свойства и области применения фосфатных покрытий | Фосфатирование
Фосфатирование представляет собой процесс обработки металлических изделий растворами кислых фосфорнокислых солей с образованием на поверхности защитной солевой пленки из нерастворимых фосфатов. Фосфатная пленка выполняет свое основное назначение — защиту от коррозии только в сочетании с лакокрасочными покрытиями или масляной пленкой, что объясняется хорошими адгезионными свойствами, сама по себе она пориста.
Благодаря хорошей адгезии фосфатирование широко применяют для грунтования под лакокрасочные покрытия в различных областях машиностроения — автомобильной, судостроительной, сельскохозяйственной и др. Иногда фосфатированию подвергают различные крепежные детали с последующим пропитыванием смазочными веществами, поскольку фосфатирование не приводит к изменению размеров.
Фосфатные покрытия не смачиваются расплавленными металлами; это свойство нередко используется в металлургической промышленности и машиностроении. Кроме того, эти покрытия обладают электроизоляционными свойствами, что позволяет применять фосфатированные изделия в электропромышленности и приборостроении.
Ограничившись этим далеко неполным перечнем областей применения фосфатирования, необходимо добавить, что его осуществление не связано с затратой дорогих материалов, с привлечением квалифицированной рабочей силы и какого-либо сложного оборудования. Особенно ценным является способность фосфатной пленки заменять роль грунта под лакокрасочные покрытия. Все это делает процесс относительно дешевым и объясняет его широкое распространение.
Фосфатирование осуществляется методом погружения в раствор кислых солей фосфорнокислого железа и марганца, иногда цинка. Соль эта известна под названием МАЖЕФ (марганец, железо, фосфор). Ниже приводится примерный состав соли МАЖЕФ, %:
Водный раствор этой соли подвергается гидролизу Me (h3PO4)2 ↔ Me НPO4 + h4PO4.
При нагревании до температуры кипения гидролиз идет дальше 5Ме(h3PO4)2 ↔2МеНPO4 + Ме3(PO4)2 + 6h4PO4.
Как известно, при взаимодействии железа с фосфорной кислотой образуются одно-, двух- и трехзамещенные фосфаты и выделяется водород: Fe + 2h4PO4→Fe(h3PO4)2 + h3, Fe + Fe (h3PO4)2 → 2FeHPO4 + h3, Fe + 2FeHPO4 → Fe3(PO4)2 + h3.
Параллельно может идти диссоциация 3Fe(h3PO4)2 ↔ Fe3(PO4)2 + 4h4PO4.
Однозамещенные фосфаты хорошо растворимы в воде, двухзамещенные трудно растворяются, а трехзамещенные практически не растворяются. Последние два соединения и являются основой фосфатной пленки, формирующейся на поверхности обрабатываемых изделий.
Для предотвращения диссоциации однозамещенного фосфата и выпадения нерастворимого трифосфата раствор должен содержать свободную фосфорную кислоту. При погружении в раствор железо взаимодействует с фосфорной кислотой и концентрация ее у поверхности металла уменьшается, равновесие реакции нарушается и на металле выделяется осадок двух- и трехзамещенных фосфатов. Образовавшаяся при диссоциации монофосфата фосфорная кислота восстанавливает кислотность раствора у поверхности металла, что создает условия для дальнейшего протекания процесса. По мере роста фосфатного слоя поверхность металла изолируется от воздействия раствора, скорость фосфатирования через некоторое время уменьшается и процесс заканчивается, что заметно по прекращению выделения пузырьков водорода.
Процесс фосфатирования протекает особенно эффективно при температуре 90—100° С. Ускорение процесса достигается при введении азотнокислых или азотисто-кислых солей, являющихся деполяризаторами; при этом резко сокращается доля процесса, протекающего с выделением водорода.
Защитная способность фосфатных пленок, полученных в присутствии ускорителей (так называемых ускоренным фосфатированием), ниже, чем пленок, полученных без ускорителей. Поэтому ускоренное фосфатирование преимущественно применяют для создания (замены) грунта под лакокрасочные покрытия, или для получения электроизоляционных фосфатных пленок.
Холодное фосфатирование можно осуществлять путем увеличения концентрации свободной фосфорной кислоты и введения солей азотной, азотистой и плавиковой кислот.
Толщина фосфатных пленок зависит от режима и состава раствора, а также от способа подготовки поверхности обрабатываемых изделий. На полированной стали в обычных растворах образуются мелкокристаллические пленки толщиной 2—4 мкм. При крупнокристаллическом строении обеспечивается более продолжительный доступ раствора к металлу и формируются пленки толщиной 10—15 мкм, а иногда и больше. В растворах для холодного фосфатирования получаются пленки толщиной до 6 мкм. Размер фосфатируемых изделий меняется незначительно по той причине, что наряду с ростом пленки размеры несколько уменьшаются в результате травления в фосфорной кислоте и в кислых фосфорнокислых солях.
Чаще и с лучшим эффектом фосфатируются изделия из углеродистой и малолегированной стали и чугуна. Высоколегированные стали фосфатируются с трудом, цветные металлы фосфатируются сравнительно редко.
www.stroitelstvo-new.ru
Фосфатирование металла: преимущества и методы обработки
Проблема защиты металлов и сплавов от коррозионных процессов встала еще с тех пор, как люди научились добывать металл из руды. Технологии производства значительно изменились и стали более современными, однако коррозия все равно разрушает изделия и конструкции. Для защиты металлических поверхностей применяют покрытие цинком, но это не обеспечивает максимальной защиты. Современная промышленность применяет более совершенный способ защиты от неблагоприятных воздействий – фосфатирование металла. С помощью данной технологии можно не только сберечь изделие или поверхность, но и получить повышенную износостойкость материала.
Что такое фосфатирование
Технология предполагает обработку металлических поверхностей специальными растворами, в основе которых лежат фосфорнокислые соли. В результате образуется прочная защитная пленка. Среди видов фосфатирования наиболее популярный метод – нанесение фосфатирующих грунтов. Также применяют и гидроабразивную, и химическую обработку металлов.
Фосфатная пленка позволяет в несколько раз улучшить защитные характеристики и срок эксплуатации лакокрасочного покрытия. За счет низкой электропроводности пленка также улучшает адгезию и препятствует подпленочным коррозионным процессам. Нередко технология применяется на изделиях перед покраской по порошковой технологии.
Фосфатная пленка легко выдерживает воздействия органических веществ – это различные масла, смазочные и горячие материалы, любые газы, кроме сероводорода.
Данная технология позволяет обрабатывать чугун, низколегированные, а также углеродистые стали. Фосфатные покрытия могут наноситься на цинк, кадмий, медные сплавы, алюминий. Фосфатируют и высокоуглеродистую сталь. Но, несмотря на свои высокие защитные качества фосфатное покрытие может разрушиться под воздействием щелочей, морской воды, пара воды, кислоты, пресной воды, а также водяного пара.
Защитная пленка образуется за счет окунания изделия в специальную ванну, где находится фосфатирующий раствор. Также можно наносить покрытие методом распыления в струйной камере. В зависимости от состава растворов, на поверхности могут образовываться фосфаты с хорошо выраженной кристаллической решеткой или же без нее.
Кристаллическая пленка оседает из раствора с катионами тяжелых металлов, а аморфную пленку получают из раствора кислых фосфатов щелочных металлов или кислого фосфата аммония.
С помощью фосфатирования металлы можно длительно эксплуатировать в тяжелых условиях, таких как:
- условия повышенной влажности;
- при воздействии горюче-смазочных материалов;
- в средах органических растворителей;
- под напряжением до 1000 В.
Основные методы обработки
Получить защитную фосфатную пленку можно разными способами, а выбор конкретного метода очень зависит от детали, которую нужно обработать, а также от области применения детали или конструкции. В промышленности чаще всего применяются следующие способы фосфатирования:
- при помощи препаратов «Мажеф»;
- с применением фосфорной кислоты;
- с помощью монофосфата цинка;
- с помощью фосфатирующей пасты.
Препаратом «Мажеф»
Это не что иное, как химическое фосфатирование, при котором деталь окунается в ванну со специальным раствором. Химической обработке подвергают низкоуглеродистые стали. Чаще всего данный способ применяется для подготовки металлоконструкций и изделий под покраску для получения надежных антикоррозийных грунтов.
Мажеф — это сочетание марганца, железа и фосфора. Продукт напоминает соль или порошок зеленоватого цвета.
Концентрация раствора в ванне – не более 40 г на 1 л. Чтобы получить пленку химическим методом, изделие помещается в готовый состав, который подогревают и доводят до температуры кипения. Рекомендуется периодическое помешивание. Кипятят ванну в течение 15-20 минут. Этого вполне хватит, чтобы сталь покрылась слоем защитной пленки.
Чтобы при помощи химического способа получить высококачественную пленку, толщина которой составляет от 5 до 10 мкм, необходимо предварительно тщательно подготовить поверхность при помощи абразивной очистки или с использованием пескоструйного аппарата.
Состав рекомендуется готовить с некоторым избытком, так как в процессе нагревания часть его испарится. Общая кислотность устанавливается при помощи титрования по фенолфталеину. Уровень свободной кислотности можно выяснять при помощи индикаторов метилоранжа.
На видео: фосфатирование солью Мажеф.
Фосфорной кислотой
Фосфорную кислоту используют для получения покрытия холодным методом. Чтобы процесс фосфатирования протекал максимально стабильно, температура раствора должна находиться в диапазоне 18-25 градусов. Чтобы добиться покрытий с высоким качеством и прочностью, нужно четко соблюдать количество действующих ингредиентов. В промышленности применяется следующая концентрация:
- 40 г/л фосфорной кислоты;
- азотнокислый цинк – 200 г на 1 л;
- сернокислого натрия 8 г на 1 л;
- окиси цинка – 15 г на 1 л.
В данном растворе деталь или конструкции из металлов обрабатывают в течение 30 минут. Этого вполне достаточно, чтобы на поверхности образовались фосфаты.
Технология подойдет для обработки больших деталей посредством струйного метода. Данный вариант по сравнению с фосфатированем в ваннах дает возможность значительно снизить продолжительность процесса, а также уменьшить расход материала.
Метод с монофосфатами цинка
Данная технология применяется для защиты металлов, которые будут применяться в электрической отрасли, а также на машиностроительных производствах. Поверхность или деталь помещают в раствор из следующих веществ:
- монофосфат цинка в количестве 20 г на 1 л;
- нитрат натрия – 35 г. на 1 л.
Процесс фосфатирования проходит при температуре раствора 60 градусов. Для покрытия металлов плотной фосфатной пленкой необходимо около 20 минут. Для проведения процесса также нужна ванна.
Что касается качества покрытия, то фосфатные пленки аналогичны по характеристикам тем, которые получают с использованием раствора Мажефа. Так можно обеспечить высокую степень защиты любому металлу.
Для обработки оцинкованных сталей лучше применять раствор, в котором используется сернокислый цинк, азотный цинк, фосфорная кислота, фтористый натрий. Процесс проводят при температурах около 60 градусов, а длительность его составляет до 20 минут. В данном растворе можно обрабатывать цинк, углеродистые стали, никель.
Обработка фосфатирующими пастами
В данном случае применяются специальные фосфатирующие грунты. Преимущество в том, что можно выполнять фосфатирование стали и других сплавов при комнатной температуре. Смесь наносится на поверхность детали с помощью обычной кисти. Для обработки не нужны ванны, а это значит, что такому фосфатированию можно подвергать материалы в домашних условиях. Этот способ часто используют автовладельцы и автопроизводители.
В составе грунта металлический пигмент, а также растворитель, в основе которого лежит ортофосфорная кислота. В краске чаще всего содержится цинк. При взаимодействии с ортофосфорной кислотой продукты коррозии укрепляются, создавая прочный защитный фосфатный слой.
Фосфатирующая паста широко применяется для обработки поверхностей деталей из черных и цветных сплавов любых размеров. Прогрунтованные поверхности пассивируются, что также улучшает их адгезионные качества.
Фосфатирование в домашних условиях
Нередко появляется нужда в фосфатировании различных деталей в домашних условиях. Чаще всего используется фосфатирование алюминия, но также можно обрабатывать разные виды сталей и не только. Технология домашнего получения фосфатных покрытий немного отличается от промышленной – полноценная химическая обработка для многих недоступна. Преимущественно используется электрохимическая обработка.
Для получения защитных пленок нужен постоянный либо переменный ток. В роли электролита используются растворы фосфорной кислоты или раствор «Мажеф». Деталь, которую нужно покрыть фосфатами, ставят на электрод, опущенный в ванну с кислотой. В качестве анода применяются цинковые стержни, к которым также подсоединяют электрический ток.
Чтобы получить качественный результат, достаточно напряжения в 25 В. Процесс получения пленки займет около 30 минут. Метод идеально подойдет для различных деталей прямолинейной формы. Объемные геометрические изделия таким методом обрабатывать сложнее, так как на сложную деталь слой ляжет неравномерно, что снизит ее защитные качества.
С помощью технологии фосфатирования можно надежно защитить металлические изделия от разрушительного воздействия коррозии. Многие способы доступны в домашних условиях, что очень важно – дома многие работают с различными металлами и хотят, чтобы детали имели большой срок службы.
Получение состава из подручных средств (1 видео)
Разные материалы для антикоррозийной защиты (18 фото)
gidpokraske.ru
Фосфатирование металла - методы и составы
Фосфатирование — это обработка металла специальными средствами на основе фосфорнокислых солей, в результате чего на поверхности появляется защитная пленка. Среди вариантов защиты металла от коррозии методом фосфатирования наиболее известна фосфатирующая грунтовка. Также применяются гидроабразивное фосфатирование и химическая обработка металла. Помимо защиты металла, пленка обеспечивает повышенную адгезию (сцепляемость) металла с лакокрасочными материалами.
Гидроабразивное фосфатирование
Гидроабразивная обработка считается одним из лучших способов защиты металла. Состав для обработки металла приготавливается на основе мягкой воды. Детали окунают на 10-15 минут в 10% раствор бихромата калия. Температура жидкости — от 70 до 80 градусов по Цельсию.
Далее проводится гидрофобизация пленки, для чего изделие на 7 минут кладется в 10% раствор кремнийорганической жидкости в бензине. После этого парам бензина дают испариться на открытом воздухе и отправляют металл на высушивание при 100 градусной температуре в течение часа.
Фосфатирующие грунтовки
Для защиты металла может использоваться фосфатирующая грунтовка, на 9/10 состоящая их металлических пигментов, а также растворителя на основе ортофосфорной кислоты. При взаимодействии с электролитом краска с содержанием цинка укрепляется продуктами коррозии и образует плотную пленку.
Фосфатирующие грунты используются для обработки изделий из черных и цветных металлов любых размеров (от крупных конструкций до резьбы одной детали). Прогрунтованная поверхность приводит к пассивации металла, а также улучшению адгезионных качеств материала.
Химическая обработка стали
Химическое фосфатирование — это окунание металла в специальные химические составы, в результате чего на его поверхности появляется защитная пленка.
Кладем в ванну соль МАЖЕФ, исходя из пропорции 35 граммов на литр воды. Заливаем жидкость, доводим ее до кипения и держим в таком состоянии 20 минут. Далее снимаем емкость с огня для определения и правки (в случае необходимости) уровня кислотности.
Состав изготавливается с избытком, так как в ходе нагревания часть его улетучивается. Уровень общей кислотности устанавливается методом титрования по фенолфталеину. Для титрования 10 миллилитров раствора уйдет 30 миллилитров децинормального состава гидроксида натрия. Свободная кислотность выяснятся при наличии индикатора метилоранжа.
Для титрования 10-миллилитровой пробы нужно 4 миллилитра децинормального раствора гидроксида натрия. Количество щелочи, затраченной на титрование, обозначается в точках. Показатели нормы кислотности: общая — 28-30 точек, свободная — 3-4 точки (то есть соотношение разных видов кислотности между собой может колебаться от 7 до 10).
Фосфатирование осуществляется при температуре 98 градусов по Цельсию в течение 1-2 часов.
Работу можно считать законченной, когда прекращается пузырение водорода. Далее металл выдерживается в емкости на протяжении 10-15 минут. Это нужно, чтобы произошла кристаллизация пленки.
Норма расхода МАЖЕФ на фосфатирование квадратного метра поверхности может колебаться от 120 до 140 граммов. Уровень кислотности корректируется водой или добавлением соли МАЖЕФ. Конкретное количество соли, необходимое для достижения показателя кислотности на уровне 30 точек, можно рассчитать по формуле:
A (кг) = (30-n)*V/1000
Переменная V означает объем, а n — количество точек раствора. Если в стали имеется большая доля легирующих компонентов (меди, хрома, ванадия), получить пленку надлежащего качества не получится. Снижает качество работы присутствие в растворе компонентов алюминия, свинца, мышьяка, а также хлоридных и сульфидных примесей. Доля ионов хлора не должна превышать 0,3%.
Если пленка получилась низкокачественной, ее можно удалить при помощи 15% раствора соляной кислоты или подогретого 20% раствора гидроксида натрия. Следует иметь в виду, что в случае повторного фосфатирования пленка будет иметь более крупнокристаллическую структуру с меньшими защитными качествами.
Ускоренная обработка солью МАЖЕФ
Фосфатирование низколегированных и электротехнических марок стали производиться с помощью смесей, включающих в себя следующие компоненты (граммов на литр воды):
Вариант №1
- препарат МАЖЕФ — 30-40;
- цынк азотнокислый Zn(NO3)26Н2O — 50-60.
Вариант №2
- препарат МАЖЕФ — 45-50;
- цынк азотнокислый Zn(NO3)26Н2O — 70-80:
- натрий фтористый NaF.
Фосфатирование осуществляется всего за 10-15 минут при условии температуры жидкости 97-98 градусов по Цельсию для раствора №1 и раствора №2. Без очищения поверхности процедуру можно произвести методом добавления в состав оксалата цинка. Это вещество уберет следы коррозии в ходе возникновения пленки.
Содержание раствора (граммов на литр):
- цинковый монофосфат — 35;
- азотнокислый цинк — 53;
- фосфорная кислота — 14;
- оксалат цинка — 0,1.
Допустимый уровень общей кислотности — 70-80 точек, свободная кислотность — 12-15 точек, температура жидкости – 92-98 градусов по Цельсию, время фосфатирования — 20-40 минут.
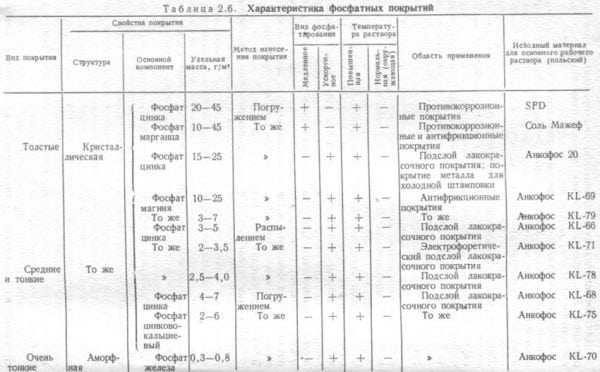
Оксалат цинка приготавливается из щавелевокислого натрия и азотнокислого цинка. При объединении растворов на дне емкости образуется осадок щавелевокислого цинка, который нужно убрать с помощью фильтра. Далее осадок высушивается и используется для создания фосфатирующего раствора.
Ускоренная обработка цинковыми солями
Обработка металла в растворе цинковых солей позволяет обеспечить лучшую защиту поверхности в сравнении с солью МАЖЕФ.
Компоненты состава (граммов на литр):
- монофосфат цинка — 37;
- азотнокислый цинк — 54;
- фосфорная кислота — 16.
В ходе фосфатирования понадобится корректировка состава. Для этого нужно добавить концентрат, в который входят 500 граммов азотнокислого цинка, 480 граммов монофосфата цинка, 180 граммов фосфорной кислоты и литр воды.
Пленка черного цвета с повышенными защитными характеристиками получается за счет последовательного окунания деталей в два состава. Один из них содержит 1 грамм кальцинированной соды, 23 грамма фосфорнокислого закисного железа, 8 граммов цинковой окиси, 32 грамма ортофосфорной кислоты (все количества указаны на литр воды). Общая кислотность состава — от 56 точек, а свободная — от 9 до 14 точек. Температура жидкости — от 92 до 97 градусов по Цельсию.
После окунания в вышеуказанном растворе изделие на 5 минут кладут в 9% раствор хромпика калия при температуре от 80 до 95 градусов по Цельсию. Далее деталь вновь промывается в мыльно-содовом растворе, а затем в горячей воде и кладется в емкость для повторного фосфатирования. На этот раз смесь включает 150 граммов азотнокислого цинка, 30 граммов МАЖЕФ, 3 грамма углекислой кислоты. Показатель кислотности — от 80 точек, свободной кислотности — от 2 до 4 точек. Температура состава — от 50 до 60 градусов по Цельсию, период фосфатирования — от 10 до 20 минут. Далее изделие кладется в мыльно-содовый раствор на 2 минуты. Завершается процесс высушиванием пленки и обработкой ее минеральным маслом.
Холодный процесс
Холодное фосфатирование подразумевает обработку материала при температуре от 20 до 40 градусов по Цельсию. Можно использовать один из двух видов раствора.
Для работы понадобятся следующие компоненты (из расчета граммов на литр):
Раствор №1. Загружаем в ванну соответствующее объему воды количество соли МАЖЕФ. Доливаем в раствор прокипяченный и настоянный фтористый натрий, и азотнокислый цинк. Чтобы увеличить уровень кислотности раствора, на каждую точку добавляем 1,5 грамма соли МАЖЕФ, 2-3 грамма азотнокислого цинка и 2-3 миллиграмма фтористого натрия.
Раствор №2. Для создания раствора используем концентрат, который включает в себя 80 граммов цинкового монофосфата, 750 граммов азотнокислого цинка, 160 граммов фосфорной кислоты, 40 граммов кальцинированной соды и 1 литр воды.
Чтобы приготовить 100 литров рабочего раствора, к 85 литрам воды добавляем 12 литров концентрата едкого натра (300 граммов на литр), а затем доливаем воду до уровня 100 литров. Также засыпаем 40 граммов азотисто-кислого натрия. Если показатель кислотности оказывается меньше необходимого, понемногу добавляем едкий натр.
Фосфатирование в домашних условиях
Процесс фосфатирования можно осуществить и самостоятельно. Проще всего это сделать быстрым способом. Для этого понадобится сделать раствор на основе соли МАЖЕФ и азотнокислого цинка. После смешивания компонентов и нагрева жидкости до температуры кипения металлическое изделие на 15 минут размещается в емкости со смесью.
Обратите внимание! Окрашивать фосфатированную поверхность можно только лишь после ее окончательного высыхания.
Хотя фосфатирование можно провести вне производственных условий, для проведения работ все же нужны определенные знания и квалификация. Поэтому, если нет уверенности в своих силах, лучше поручить этот процесс специалистам, которые окажут такую услугу быстро и качественно.
kraska.guru
Фосфатное покрытие - Большая Энциклопедия Нефти и Газа, статья, страница 1
Фосфатное покрытие
Cтраница 1
Фосфатные покрытия представляют собой пленки фосфорнокислой соли железа и марганца. Фосфатные пленки вследствие пористости обладают недостаточной коррозионной стойкостью, поэтому применение фосфатных покрытий аффективно только в атмосферных условиях или в сочетании с лакокрасочными покрытиями. [1]
Фосфатные покрытия устойчивы в атмосферных условиях, в смазочных маслах и органических растворителях, но разрушаются в кислотах и щелочах. [2]
Фосфатные покрытия сами по себе не обеспечивают надежной коррозионной защиты. Их используют преимущественно как основу под окраску, которая обеспечивает хорошее сцепление краски со сталью и уменьшает коррозионные разрушения в местах царапин или других дефектов. Иногда фосфатные покрытия пропитывают маслами или воском - это обеспечивает более высокую степень защиты от коррозии, особенно если в них ввести ингибиторы коррозии. [4]
Фосфатные покрытия используют и как электроизоляцмлшыс. Они характеризуются высоким электросопротивлением и выдерживают напряжение 300 - 1000 В. [5]
Фосфатные покрытия без труда наносят на изделия из углеродистых и низколегированных сталей, чугуна, ряда цветных мета-шов и металлических покрытий Высоколегированные стали, особенно хромо-вольфрамовые, хромоваиадиевые, легированные медью, фосфатнруются с трудом и образуют пленку низкого качества Коррозионностойкие стали не поддаются фосфатировакию. [6]
Фосфатное покрытие легко удаляется в серной или соляной кислотах, применяемых для травления деталей. В случае неоднократного удаления пленки рекомендуется перед повторным фос-фатированием обдуть поверхности отработанным песком. [7]
Фосфатные покрытия возникают в виде пленки на очищенной поверхности металла и в зависимости от метода получения их толщина колеблется от 1 до 20 мкм. Фосфатные покрытия используются для защиты стальных, алюминиевых и цинковых поверхностей. [8]
Фосфатные покрытия могут применяться, кроме того, как антифрикционная твердая смазка При холодной пластической обработке металлов и в качестве электроизолирующих слоев. [9]
Фосфатные покрытия получают осаждением из растворов солей. Присутствующие в растворах первичные фосфаты при нагревании и в присутствии металла превращаются в малорастворимые вторичные и третичные соли, которые осаждаются на металле. [10]
Фосфатные покрытия получают обработкой поверхности изделий растворами однозамещенных солей ортофосфорной кислоты. Получающиеся водонерастворимые пленки двух - и трехзамещенных фосфатов железа и марганца или железа и цинка окрашены в серый цвет и имеют кристаллическую структуру, отличающуюся большой пористостью. Толщина пленки может достигать 30 - 40 мк; чаще получают пленки толщиной 5 - 8 мк. Размеры деталей увеличиваются сравнительно мало - на 5 - 6 мк, так как пленка образуется за счет частичного растворения верхнего слоя металла. [11]
Фосфатные покрытия применяют также в сочетании со смазками для уменьшения трения при обработке металлов давлением, волочением, для лучшей приработки трущихся деталей и для покрытия болтов, гаек и других крепежных деталей. Фосфатные пленки изолируют электрический ток и имеют пробивное напряжение до 250 в, а после пропитки электроизоляционным лаком - до 1000 в. В связи с этим их применяют для электроизоляции трансформаторных, ста-торных и роторных пластин. Магнитные свойства металла при фос-фатировании не изменяются. Пленка не поддается пайке. По твердости она превосходит медь и латунь, но уступает стали. [12]
Фосфатные покрытия получают обработкой поверхности изделий растворами однозамещенных солей ортофосфорной кислоты. Получающиеся водонерастворимые пленки двух - и трехзамещенных фосфатов железа и марганца или железа и цинка окрашены в серый цвет и имеют кристаллическую структуру, отличающуюся большой пористостью. Толщина пленки может достигать 30 - 40 мк; чаще получают пленки толщиной 5 - 8 мк. Размеры деталей увеличиваются сравнительно мало - на 5 - 6 мк, так как пленка образуется за счет частичного растворения верхнего слоя металла. [13]
Фосфатные покрытия применяют также в сочетании со смазками для уменьшения трения при обработке металлов давлением, волочением, для лучшей приработки трущихся деталей - и для покрытия болтов, гаек и других крепежных деталей. Фосфатные пленки изолируют электрический ток и имеют пробивное напряжение до 250 в, а после пропитки электроизоляционным лаком - до 1000 в. В связи с этим их применяют для электроизоляции трансформаторных, ста-торных и роторных пластин. Магнитные свойства металла при фос-фатировании не изменяются. Пленка не поддается пайке. По твердости она превосходит медь и латунь, но уступает стали. [14]
Фосфатные покрытия с достаточно высокой коррозионной стойкостью образуются в растворе, содержащем 30 - 35 г / л препарата мажеф и 50 - 70 г / л азотнокислого цинка. Время выдержки деталей в растворе 10 - 15 мин. Снижение температуры ванны до 70 - 80 и значительное сокращение времени выдержки является большим преимуществом этого раствора по сравнению с обычным составом для фосфатирования. [15]
Страницы: 1 2 3 4
www.ngpedia.ru
Фосфатные покрытия - Справочник химика 21
Фосфатные покрытия сами по себе не обеспечивают надежной коррозионной защиты. Их используют преимущественно как основу под окраску, которая обеспечивает хорошее сцепление краски со сталью и уменьшает коррозионные разрушения в местах царапин или других дефектов. Иногда фосфатные покрытия пропитывают маслами или воском — это обеспечивает более высокую степень защиты от коррозии, особенно если в них ввести ингибиторы коррозии. [c.246] Защитная способность фосфатных покрытий против коррозии повышается при дополнительной обработке маслами, лаками и красками. [c.931]Для предотвращения коррозии создают на защищаемой поверхности защитную пленку окислов железа (оксидирование) или фосфатов марганца и железа (фосфатирование). При отсутствии влаги оксидная пленка обладает хорошей химической стабильностью, но во влажной среде ее защитные свойства невысоки. Защитная способность фосфатных покрытий значительно выше, чем у оксидных, однако фосфатные пленки довольно хрупкие. При контакте с маслами фосфатные покрытия хорошо ими пропитываются и защитные свойства покрытий повышаются. [c.99]
Толщина фосфатного покрытия в зависимости от подготовки и технологии нанесения может быть от 5—10 до 30—40 мк [c.931]
Подготовка поберхностей под покрытия без удаления ржавчины Такая подготовка заключается в обработке поверхностей различными химическими соединениями, которые получили название преобразователей (модификаторов) ржавчины. В состав большинства из них входит фосфорная кислота. Кислота разрушает ржавчину и одновременно фосфатирует металлическую поверхность. Химически разрушенная ржавчина становится нанелнителем фосфатного покрытия. Рецептуры некоторых преобразователей ржавчины приведены в табл. 7. [c.91]
Фосфатные покрытия представляют собой плёнки фосфорнокислой соли железа и марганца. Так как фосфатные плёнки вследствие пористости обладают недостаточной коррозионной стойкостью, применение фосфатированных изделий допустимо только в атмосферных условиях. [c.46]
ОКСИДНЫЕ И ФОСФАТНЫЕ ПОКРЫТИЯ [c.215]
Оксидно-фосфатные покрытия но сравнению с оксидными, полученными в щелочных растворах, обладают рядом преимуществ, в 2—3 раза сокращается продолжительность процесса прн увеличении ро столько 1е раз коррозионной стойкости пленки, увеличивается механическая прочность пленкн, повышенная ее износостойкость к антифрикционные [c.217]
Фосфатные покрытия устойчивы в атмосферных условиях, в смазочных маслах и органических растворителях, но разрушаются в кислотах и щелочах. [c.254]
Окисно- фторидное ОКИСНО фосфатное Алюминий и его сплавы Обладают эластичностью, хорошей адгезией с металлом окисно-фосфатное покрытие неэлектропроводно, является хорошим грунтом под окраску Декоративная отд 1Ка и защита от коррозии [c.373]
Оксидно фосфатное покрытие на кадмии получают в растворе состава, гД г гидрофосфат цннка 8—10, иитрат цннка 30—40, нитрат барня 30—40 прн 75—85 С, т=3- 10 мнн. [c.262]
Высоким защитным действием обладает фосфатное покрытие, содержащее соли цинка и железа. Эти соли, взаимодействуя с ингредиентами ЛКП, после его нанесения, образуют слой, являющийся барьером для проникновения агрессивной среды (например, метаболитов грибов или влаги) к поверхности подложки, предотвращая коррозию металла. Целесообразно применять комбинированные покрытия, в состав которых входит ЛКП с биоцидным грунтом, нанесенным по фосфатному покрытию. [c.81]
ФОСФАТНЫЕ ПОКРЫТИЯ. Так называемое фосфатирование осуществляют, нанося на чистую стальную поверхность кистью или напылением холодные или горячие разбавленные растворы ортофосфатов марганца или цинка (например, 2пНР04 + Н3РО4). [c.245]
Качество фосфатных плеиок заметно улучшается при фосфатированни в ультразвуковом поле Фосфатные покрытия при этом получаются мелкокристаллическими, менее пористыми, с повышенной коррозионной стой костью [15] [c.258]
Ниже приведены выдержки капельной пробы фосфатных покрытий [c.280]
Фосфатные покрытия применяются, в основном, при подготовке стальных изделий перед окраской. Распространены три способа нанесения фосфатных покрытий медленное фосфатирование, ускоренное и фосфатирование при комнатной температуре. [c.129]
По методу погружения дета-дн прн комнатной температуре помещают в раствор на определенное время, после чего промывают и сушат На контролируемой поверхности за это время не должно быть следов коррозии (фосфатные покрытия), контактного выделения меди (оксидные покрытия). [c.280]
Фосфатные покрытия используют и как электроизоляционные. Они характеризуются высоким электросопротивлением и выдерживают напряжение 300—1000 В. [c.254]
Так как все органические растворители в той или иной степени токсичны, то ведутся интенсивные исследования способов обезжиривания поверхности водными растворами. Положительный опыт в этом направлении имеется во ВНИИГ им. Б. Е. Веденеева, где установлена эффективность применения 0,5%-ного водного раствора ПАВ ОП-7 при подготовке поверхности под нанесение фосфатных покрытий. Технические характеристики оборудования для подготовки поверхности приведены в 13. [c.99]
ЗАЩИТА СТАЛЕЙ ФОСФАТНЫМИ ПОКРЫТИЯМИ [c.128]
В некоторых случаях растворенный кислород благоприятствует замедлению коррозионного процесса. Усиленный доступ кислорода уменьшает скорость коррозии железа в фосфате натрия вследствие образования фосфатного покрытия, а также в 0,1 н. растворе хлорида натрия при относительно высоких скоростях движения раствора в результате пассивирования. [c.79]
Вследствие хорошей смачиваемости фосфатированных металлов жидкими лакокрасочными материалами и их развитой поверхности достигается высокая адгезия покрытий, в том числе и тех, которые в обычных условиях плохо адгезируют. Фосфатные покрытия в зависимости от состава имеют термостойкость от 150 до 220 °С обладают хорошими диэлектрическими свойствами цвет покрытий — от светло- до темно-серого. [c.149]
Некачествениые фосфатные покрытия удаляют химическим путем в растворе соляной кислоты 100—150 г/л прн 18—28 °С ичи ссрной кнс лоты 100—150 г/т при 18—25 С нли едкого натра 150—200 i/л прн во—SO [c.266]
Грунт для достижения лучшего сцепления следует наносить на сухую поверхность металла как можно быстрее после его очистки. Еще лучше создать предварительно на поверхности металла фосфатный слой (см. разд. 14.4). В этом случае грунт, при необходимости, можно наносить с некоторой задержкой во времени. Фосфатное покрытие обеспечивает лучшее сцепление ЛКП с металлом и эффективно предотвращает подтравливание слоя краски в местах царапин и других дефектов, в которых образуется ржавчина. В противном случае коррозионные процессы развиваются и под слоем полимерного покрытия. Уже многие годы является общепринятой практикой фосфатированне автокузовов и электроприборов перед покраской. [c.254]
Фосфатирование широко применяют для защиты изделий от коррозии и для подготовки поверхности перед нанесением лакокрасочны покрытий При нанесении на фосфатную пленку сокращается расход де- фицит тых, дорогостоящих лакокрасочных материалов. Защитные свойства фосфатных покрытий выше, чем оксидных, полученных в щелочных растворах. [c.254]
Для контроля сплошности оксидных и фосфатных покрытий на сталн используют соответственно растворы I н 4 (см табл. 158). оксядных покрытий на алюминии раствор состава- сульфат медн 20 г/л, соляная кислота (п.потностью 1,19) 20 ыл/л [c.281]
Фосфатные покрытия на стали получают из растворов ортофос-форной кислоты и ортофосфатов марганца или цинка (например, пНР04 + Н3РО4). При реакции образуется пористый кристалличе- [c.220]
Фосфатные покрытия на сталь, чугуи наносят химическими и электрохн мическими способами. Большинство фосфатных пленок наносят химическим способом [c.254]
Фосфатные покрытия на стали получают из растворов орто-фосфорной кислоты и ортофосфатов марганца или цинка (например, гпНР04-(-Н3РО4). При реакции образуется пористый кристаллический фосфат металла, хорошо сцепленный с поверхностью стали. Сами по себе фосфатные покрытия не обеспечи- [c.237]
Оксидно-фосфатные покрытия образуются в растворах, содержащих перв11чкыс фосфаты железа, цинка нлн ортофосфорную кислоту, а также окислители — нитраты барня, кальция, пероксид марганца Оптимальная концентрация ортофосфориой кнелоты 2—10 г/л [c.217]
Фосфатные покрытия наносят в виде специальных паст, метоЛ груження или струйным [c.255]
Растворы для ианесення химических фосфатных покрытий деляются на три основные группы — горячего, ускоренного и фосфатироваиия [c.255]
Изменяя состав растворов фосфатироваиия, проводя специальные операции, можно получать декоративные фосфатные покрытия. [c.258]
Осазкдают фосфатные покрытия как прн постоянном, так и при переменном токе В табл 147 приведеиы составы электролитов и режимы осаждения фосфатных покрытий [19, 391 [c.259]
Защитные свойства фосфатных пленок значительно увеличиваются прн придании им гидрофобных свойств Коррозионная стойкость гндро-фобизированных фосфатных покрытий значительно выше, чем прн про-ыаслищанни [c.264]
Оксидные и фосфатные покрытия контролируют до пропитки, ано-лдаационпые оксидные покрытия на алюминии н его сплавах с наполни телями — не позднее, чем через 3 ч после наполнения. [c.279]
Для нанесения лакокрасочных и фосфатных покрытий мбгут быть использованы следующие компрессорные установки 0-16А, 0-39А, 0-38М и С-728, создающие давление воздуха от 0,4 до 0,7 МПа. Для очистки воздуха, подаваемого [c.106]
Оксидные и фосфатные покрытия в определенной степени эа-ццни ают стальные детали от коррозионного растрескивания в нейтральных и щелочшхх средах при сравнительно невысоких уровнях нагружения. Особенно перспективно в этом случае [c.128]
chem21.info
Фосфатное покрытие на железе - Справочник химика 21
Для предотвращения коррозии создают на защищаемой поверхности защитную пленку окислов железа (оксидирование) или фосфатов марганца и железа (фосфатирование). При отсутствии влаги оксидная пленка обладает хорошей химической стабильностью, но во влажной среде ее защитные свойства невысоки. Защитная способность фосфатных покрытий значительно выше, чем у оксидных, однако фосфатные пленки довольно хрупкие. При контакте с маслами фосфатные покрытия хорошо ими пропитываются и защитные свойства покрытий повышаются. [c.99] Фосфатные покрытия представляют собой плёнки фосфорнокислой соли железа и марганца. Так как фосфатные плёнки вследствие пористости обладают недостаточной коррозионной стойкостью, применение фосфатированных изделий допустимо только в атмосферных условиях. [c.46]Высоким защитным действием обладает фосфатное покрытие, содержащее соли цинка и железа. Эти соли, взаимодействуя с ингредиентами ЛКП, после его нанесения, образуют слой, являющийся барьером для проникновения агрессивной среды (например, метаболитов грибов или влаги) к поверхности подложки, предотвращая коррозию металла. Целесообразно применять комбинированные покрытия, в состав которых входит ЛКП с биоцидным грунтом, нанесенным по фосфатному покрытию. [c.81]
В реставрационной практике для черных металлов широко применяют фосфатирование как один из надежных способов защиты поверхности металла. Фосфатирование приводит к образованию на поверхности металла тонкой (5—50 мкм) мелкокристаллической пленки, состоящей из нерастворимых солей железа, марганца или цинка. В зависимости от условий образования цвет фосфатных покрытий от серого до черного Фосфатный слой обладает хорошими изоляционными свойствами что препятствует возникновению на поверхности металла электрохими ческой коррозии. Фосфатный слой имеет хорошее сцепление с поверх ностью металла, но является достаточно пористым, что позволяет нано сить на него защитные лаковые или восковые покрытия. Фосфатирование не нарушает отделку предмета - воронение, чернение, меднение, золочение при этой обработке сохраняются. [c.161]
В некоторых случаях растворенный кислород благоприятствует замедлению коррозионного процесса. Усиленный доступ кислорода уменьшает скорость коррозии железа в фосфате натрия вследствие образования фосфатного покрытия, а также в 0,1 н. растворе хлорида натрия при относительно высоких скоростях движения раствора в результате пассивирования. [c.79]
Положительное влияние органических хроматов даже в незначительных концентрациях на защитные свойства органических фосфатов можно, по-видимому, объяснить тем, что фосфаты образуют нерастворимые соединения с железом, покрывающие основную часть поверхности, а роль хроматов заключается в пассивации пор в фосфатном покрытии. Не исключено также, что в результате совместного действия хроматов и фосфатов изменяется структура защитных слоев. [c.181]
Фосфатные покрытия находят применение для защиты от коррозии некоторый изделий, не Требующих декоративной поверхности, а также для создания электроизоляции на поверхности роторных и статорных пластин и трансформаторного железа взамен лакирования. [c.96]
Из средств противокоррозионной защиты были изучены (Шкловским) медные, оловянные, свинцовые, цинковые и фосфатные покрытия. В сероводороде, насыщенном влагой, а также в смеси воздуха с сероводородом (5% НзЗ), насыщенном влагой, цинковое покрытие оказалось вполне устойчивым, и железо предохранялось им от коррозии. [c.197]
Оловянное покрытие в сероводороде, насыщенном влагой, а также в смеси сероводорода с воздухом при 100%-ной влажности, является устойчивым. Аналогичным же образом ведет себя и свинцовое покрытие. Оба эти покрытия являются катодами по отношению к железу и с возникновением коррозии основного металла, из-за дефектов в покрытиях, начинают отслаиваться. Медные и фосфатные покрытия разрушаются с первых же дней и защитой служить не могут. [c.197]
Кроме того, ингибиторы повышают прочность (особенно после светостарения) масляных и алкидных пленок при сохранении их гибкости, а также увеличивают паро-проницаемость ингибированных покрытий. Благотворное влияние незначительных концентраций органических хроматов на защитные свойства органических фосфатов объясняется тем, что фосфаты образуют нерастворимые соединения с железом, покрывающие основную часть поверхности, а роль хроматов заключается в пассивации пор в фосфатном покрытии. [c.601]
Протекание реакций, учитывая низкое значение величины произведения растворимости фосфатов железа и марганца, приводит через непродолжительное время к пересыщению раствора в слое, граничащем с поверхностью изделия, и последующей кристаллизации двух и трехзамещенных фосфатов железа и марганца на поверхности железа, т. е. к образованию фосфатного покрытия по реакциям [c.186]
Фосфатирование в последнее время нашло широкое применение вследствие способности фосфатного покрытия предотвращать распространение подпленочной коррозии при наличии царапин, плохо прокрашенных кромок и других дефектов покрытия. Тип и толщину фосфатного покрытия можно по желанию изменять, модифицируя процесс режим фосфатирования выбирается, исходя из целевого назначения деталей. Для придания максимальной коррозионной стойкости используют толстые покрытия фосфата железа или марганца. Применение фосфата цинка в сочетании с окислителями дает возможность ускорить образование тонкослойных фосфатных покрытий с улучшенной кристаллической структурой. [c.80]
Фосфатная защитная пленка обладает и другим существенным достоинством — она препятствует коррозии и н случае повреждения. Даже под поврежденной пленкой коррозия не распространяется, а напротив, продукты начавшейся здесь коррозии быстро закрывают поврежденное место и защищают его от дальнейшего разрушения. Свойства фосфатного покрытия можно улучшить, если после фосфатной ванны обработать металл раствором, содержащим пассивирующее вещество, которое пассивирует железо под фосфатной пленкой. Фосфатная пленка препятствует и вредному действию локальных элементов, так как является хорошим электрическим изолятором. Ее изоляционные свойства выгодны и с точки зрения электротехники во многих случаях они делают излишним применение специальных изоляторов (например, эмали или бумаги). [c.281]
Проведенное Шустером послойное исследование химического состава фосфатного покрытия на железе показало, что содержание последнего в слое, непосредственно прилегающем к металлу, является максимальным. По мере удаления от поверхности железа содержание его в слое быстро уменьшается [366, 367]. Таким образом, прочная связь фосфатной пленки с металлической поверхностью частиц карбонильного железа обусловлена структурным соответствием. [c.193]
Вместо грунтовки иногда проводят фосфатирование поверхности металла. Для этого на чистую поверхность кистью или напылителем наносят растворы ортофосфатов железа(П1), марганца (П) или цинка(II), содержащих и саму ортофосфорную кислоту Н3РО4. В нашей стране для этой цели применяют 3 %-ный раствор смеси кислых солей Ре(НгР04)з и Мп(НгР04)2 с добавками КЫОз или Си (N03)2 в качестве ускорителей. В заводских условиях фосфатирование ведут при 97—99 °С в течение 30—90 мин. В образование фосфатного покрытия вносят вклад металл, растворяющийся в фосфатирующейся смеси, и оставшиеся на его поверхности оксиды. [c.141]
Для получения фосфатных покрытий применяют нагретые до кипения разбавленные растворы первичных фосфатов двухвалентных металлов марганца, железа, цинка и кадмия. При растворении [c.405]
Фосфатное покрытие не имеет декоративного значения и может защищать железо (сталь) от коррозии после последующего нанесения слоя специальной смазки, краски или лака. Фосфатирование обычно применяется как промежуточная обработка перед лакированием и окраской. [c.51]
Оксидно-фосфатные покрытия образуются в растворах, содержащих перв11чкыс фосфаты железа, цинка нлн ортофосфорную кислоту, а также окислители — нитраты барня, кальция, пероксид марганца Оптимальная концентрация ортофосфориой кнелоты 2—10 г/л [c.217]
Фосфатирование перед склеиванием должно тщательно контролироваться. Очень толстые слои неорганических фосфатов — структуры фосфата железа или, в случае нанесения цинка, смешанные композиты железа и цинка — могут обладать меньшей силой сцепления, чем адгезив, соединяющий резину с металлом. Другими словами, плохо нанесенные неорганические (минеральные) фосфаты могут действовать как слабые приповерхностные слои. В таких случаях прочность склеенного соединения ограничивается силой, необходимой для начала отслаивания в слое конверсионного (химически взаимодействующего с металлом) фосфатного покрытия. [c.338]
Железо-фосфатное покрытие применяют для изделий, из металлов группы I. [c.185]
Фосфатные покрытия образуются при реакции фосфорной кислоты с обрабатываемой металлической поверхностью. Чаще всего применяются растворы для фосфатирования, содержащие фосфорнокислые соли цинка и железа или марганца и железа. Раствор реагирует с металлом до тех пор, пока поверхность не закроется кристаллическим фосфатным слоем. Чтобы ускорить образование покрытия, вводится окислитель [1], препятствующий образованию водородной пленки на поверхности металла. [c.935]
Для решения этой проблемы были разработаны методы получения гомогенных фосфатных покрытий, наполненных железом, с высокоразвитой тонкой кристаллической структурой и минимальной толщиной слоя вторичного фосфата цинка. Для большей гарантии можно обработать полученный фосфатный слой слабым раствором какого-либо хромата. Получаемый при этом эффект называют эффектом закрепления , в результате кристаллы скрепляются и повышается гомогенность поверхности. [c.283]
В основе фосфатирования стальных изделий лежит процесс образования нерастворимых в воде двух- и трехзамещенных фосфатов железа, цинка и марганца, которые образуются при погружении изделий в разбавленный раствор фосфорной кислоты с добавкой одно-замещенных фосфатов вышеперечисленных металлов. В начальной стадии процесса на поверхности стального предмета образуется тонкий слой фосфорнокислого железа, при дальнейшем протекании процесса образуются смешанные кристаллы фосфатов железа, цинка и марганца. Получающееся фосфатное покрытие хорошо сцеплено с металлической основой. Однако оно имеет характерную высокую по-,ристость и не может обеспечить защиту изделия от коррозии. Его либо дополнительно обрабатывают (например, пропитывая минеральным или растительным маслом), либо используют в качестве предва- рительного покрытия перед нанесением лакокрасочных материалов, что приводит к повышению сцепления датшых материалов с основой. [c.157]
ФОСФАТЙРОВАНИЕ - создание на поверхности металлических изделий пленки из нерастворимых фосфатов. Осн. назначение Ф., к-рое сочетают, поскольку пленка пориста, с нанесением лакокрасочных или масляных покрытий,— повышение коррозионной стойкости изделий. Фосфатные покрытия термостойки до т-ры 400—500° С и выдерживают напряжение 300—500 в. Ф. осуществляют воздействием на обрабатываемые изделия (преим. стальные или чугунные малолегированные) раствора кислых солей — фосфорнокислого железа и марганца (иногда цинка) — МАН ЕФ (марганец, железо, фосфор) примерного состава 18—20% Мп 0,14-0,15% Ре2+ 2,0-2,5% Ге + 60-70% РО 1% 804 1-2% НзО [c.660]
Процесс получения фосфатного покрытия на поверхности железного образца можно интенсифицировать, добавляя в раствор для фосфатирования окислители, растворы солей металлов, более благородных, чем фосфа-тируе.мый, и т. д. Окислитель, например, нитрит натрия, добавленный в малых количествах, выступает в роли деполяризатора, ускоряя анодный процесс, пересыщение раствора фосфатами и последующую их кристаллизацию на поверхности железа. Ионы благородных металлов, например меди, осаждаясь контактно, увеличивают катодную поверхность, что повышает скорость [c.226]
Погружение в фосфатирующий раствор стальных или чугунных изделий вызывает усиление деятельности на их поверхности анодных и катодных участков. Анодные участки, разрушаясь, посылают в раствор ионы железа Ре - Ре +- -2 е, а на катодных участках совершается процесс 2 Н+-Ь 2 е- 2 Н - Н2, в результате чего слой раствора, граничащий с поверхностью фосфатируемых изделий, обогащается ионами железа, а также ионами НРОг и Р04 . Произведение растворимости кислого двухза-мещенного фосфата железа и марганца (РеНР04 и МПНРО4), а также нормальных фосфатов этих металлов (Рез(Р04)2 и Мпз(Р04)2) крайне невелики, а потому граничащий с изделиями слой раствора становится пересыщенным относительно этих солей. Последние кристаллизуются на обрабатываемой поверхности, образуя фосфатное покрытие по реакциям [c.224]
Оуверат [25] нашел, что трифосфат цинка, содержащий следы железа, является наиболее удобным фосфатирующим агентом. Он плавится при 900°С, хорошо растворим в кислотах и щелочах и, следовательно, легко удаляется с поверхности металла после штамповки. Фосфатные покрытия являются не только носителями масла. Они пластически деформируются вместе со стальной заготовкой и в сочетании со смазочным материалом предотвращают контакт металл—металл, а также уменьшают поверхностное трение и износ. Пластическая дефор-.мация фосфатного слоя во время обработки металла вызывает превращение кристаллов фосфата в стекловидную пленку, которая выполняет свою разделительную роль даже лучше, чем первоначальный кристаллический слой. [c.126]
Нормальное фосфатирование. Для получения фосфатных покрытий применяют нагретые до кипения разбавленные растворы первичных фосфатов двухвалентных металлов марганца, железа, цинка и кадмия. При растворении в горячей воде происходит гидролиз первичных фосфатов на вторичные и третичные соединения и на свободную фосфорную кислоту. При погружении в такой раствор стальных изделий железо бурно реагирует с ( сфорной кислотой и на поверхности изделия кристаллизуется слой нерастворимых фосфатов. Как только пленка станет сплошной, взаимодействие железа с раствором прекращается. Это легко установить, поскольку прекращается выделение водорода. Температура раствора при фосфатировании должна поддерживаться на уровне 96—98°. У осадков, полученных при низших температурах, грубокристаллическая структура, а при более высоких температурах покрытия загрязнены шламом. Продолжительность фосфатирования при указанной температуре составляет 0,5—2 ч. Концентрация исходной соли ддя фосфатирования [препарата Мажеф, смеси однозамещенных солей сфорной кислоты, железа и марганца Ре (НгРО г и Мп (Н РО ) а] составляет примерно 32—35 г л. [c.360]
Химическая очистка. Для удаления ржавчины и окалины издавна применяют кислотное травление. В настоящее время травление обычно производят с помощью холодных растворов соляной кислоты или горячих растворов серной кислоты с последуюи1 ей промывкой поверхности. Сравнительно недавно для травления начали применять фосфорную кислоту, а также смесь фосфорной и серной кислот при травлении по способу дуплекс . В последнем случае для удаления окалины и ржаичины металлические изделия погружают в горячий 10%-ный раствор серной кислоты с последующей промывкой холодной водой и окунанием в горячий 2%-ный раствор фосфорной кислоты, содержащий небольшое количество железа. При этом на поверхности металла образуется тонкий слой фосфатного покрытия. Для лучщего использования этого метода сталь следует окрашивать в нагретом состоянии, чтобы предотвратить конденсацию влаги на поверхности до нанесения краски. [c.522]
Основным достоннством фосфатного покрытия является его способность предотвращать распространение ржавчины при наличии царапин, плохо прокрашенных кромок и других дефектных участков лакокрасочного покрытия. Тип и толщину фосфатного покрытия можно по желанию изменять, модифицируя процесс режим фосфатирования выбирается исходя из целевого назначения детали. Для предотвращения износа поверхности и придания ей максимальной коррозионной стойкости на нее наносят толстые покрытия фосфата железа и марганца. Применение фосфата цин- [c.523]
Процесс фосфатирования солью циика по сравнению с солью железа протекает быстрее, причем его. молено еще больше ускорить с помощью таких окислителей, как нитраты, нитриты п хлораты. Окислители оказывают деполяризующее влияние на реакцию между кислотой и металлом реакция начинается на большем количестве участков поверхности и приводит к значительно более быстрому образованию сплошного фосфатного покрытия. Покрытия получаются более топкими и более мелкокристаллическими по сравиепню с покрытиями, об-разуюпиагися без ускорителей. Продолжительность процесса с одного часа со- [c.524]
Для получения фосфатных покрытий на алюминии и его сплавах можно применять растворы первичных фосфатов железа, марганца или цинка, добавив в них хромовую или плавиковую кислоты или их соли. В растворе, содержащем 300—330 г Н3РО4, 25—35 г К2СГ2О7, 2,5—2,8 г NaF, 700—750 мл Н2О, при температуре 45—50 °С и продолжительности процесса 40—60 мин, кроме чистого металла, обрабатывают сплавы АМг, АК6, АЛ4. Для электрохимического фосфатирования с применением как постоянного, так и переменного тока может быть использован электролит, содержащий (г/л) 60—65 мажефа, 60—70 Zn(N03)2, 10—15 ZnO, 7—8 NaF pH 3,0—3,2, Ко /Сс = 20ч-25. Плотность постоянного тока 0,1—0,2 А/дм , детали поляризуются катодно, анодом служит цинк плотность переменного тока 0,8—1 А/дм . [c.279]
Получение фосфатных покрытий на железе. Железные и стальные предметы часто покрываются защитным слоем фосфата железа погружением их в горячую (обыкновенно кипящую) ванну, содержащую фосфорную кислоту, насыщенную фосфатом железа часто ванна содержит фосфат марганца и иногда добавки фосфата меди или цинка, а также нитратов. Вероятно, фосфорная кислота действует на железо и превращает его поверхность в фосфат железа и, по мере того как ванна становится менее кислотной, она пересыщается фосфатами, которые затем осаждаются на уже имеющуюся пленку. Процесс варьирует сообразно с тем, предназначена ли плшка быть защитным слоем или она является только основанием для эмали или краски. В последнем случае некоторые авторитеты полагают, что какая-то степень пористости выгодна, так как в этом случае краска лучше впитывается в пленку. [c.421]
Фосфатные покрытия. Сине-серые покрытия на стали, возникающие при проведении процесса Футнера, состоят из фосфатов железа — большей частью из фосфатов закисного железа, хотя при испытании в атмосфере воз- [c.516]
chem21.info