способ производства проволоки из алюминиевого сплава. Из алюминиевой проволоки
Производство алюминиевой проволоки – виды и характеристики
Алюминиевая проволока представляет собой длинномерное металлоизделие с круглым сечением малого размера. Производство алюминиевой проволоки востребованное. Изделия используют в пищевой, мебельной промышленности, приборостроении, машиностроении, в строительстве при проведении сварочных работ, для прокладки кабелей электролиний.
Свойства проволоки из алюминия
Алюминий – универсальный материал, которому присущи такие характеристики:
- малый вес;
- гибкость;
- прочность;
- влагоустойчивостью;
- хорошая износостойкость;
- температура плавления 660 0C;
- стойкость к агрессивным средам;
- слабые магнитные свойства;
- биологическая инертность;
- долговечность.
По сравнению с другими видами аналогичных изделий, алюминиевая проволока имеет много преимуществ. Материал устойчивый к коррозии, поэтому его применяют там, где объекты контактируют с водой. Технический алюминий легко поддается обработке. Он обладает электро- и теплопроводностью. Металл безопасный в использовании, так как соответствует необходимым санитарно-техническим требованиям.
Для изготовления профиля используют чистый алюминий разных марок и его деформируемые сплавы в виде слитков или катанки. Свойства изделия зависят от химического состава и способа производства. Диаметр готовой продукции варьируется от 0,08 до 10 мм.
Виды и марки проволоки из алюминия
Производство длинномерных алюминиевых изделий регламентируется стандартами ГОСТ. Длинномерный профиль из алюминия имеет разную классификацию, основанную на эксплуатационных характеристиках.
По химическому составу стали:
- низкоуглеродистая — с массой углерода до или выше 0,25%;
- легированная;
- высоколегированная;
- на основе особых сплавов.
По форме сечения:
- круглая, овальная;
- квадратная, прямоугольная;
- трапециевидная;
- многогранная;
- сегментная;
- клиновидная;
- зето- и иксообразная;
- периодического, специального, фасонного профиля.
По виду поверхности:
- полированная;
- шлифованная;
- травленная;
- с металлическим или неметаллическим покрытием;
- светлая;
- черная.
Каждому специалисту известно понятие «марка металла». Расшифровка символов дает сведения о химическом составе и физических свойствах материала. Сплавы маркируют буквами и цифрами, по которым определяют состав химических элементов и их количество. В соответствии с ГОСТ круглую проволоку обозначают таким образом:
- Твердая – АТ.
- Полутвердая – АПТ.
- Мягкая – АМ.
- Повышенной прочности – АТп.
По ГОСТ 14838-78 производят изделия для холодной высадки на основе технического алюминия или его сплавов. ГОСТ 7871-75 позволяет изготавливать проволоку для сварки. ГОСТ 4784-97 регулирует химический состав продукции. Согласно ГОСТ 24231-80, проводят пробы с целью определить содержание компонентов металла.
Особенности производства алюминиевой проволоки
Основой для изготовления проволоки является катанка алюминиевая диаметром от 9 до 14 мм. Ее получают тремя способами.
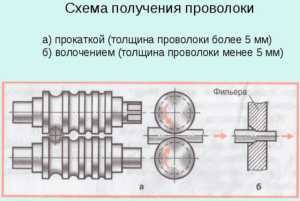
Схема получения проволоки
Прокаткой, если в качестве исходного сырья имеются алюминиевые слитки. Для этого используют проволочно-прокатный стан. Это комплекс автоматизированных механизмов, оснащенный нагревательными печами с электрическим, газовым или нефтяным обогревом.
Методом непрерывного литья и проката, если сырье представлено в виде расплавленного алюминия. Это передовой способ, который предполагает загрузку жидкой массы в кристаллизатор. Специальное вращающееся колесо с вырезом на ободе охлаждается водой. Во время движения металл кристаллизуется и передается на прокатные валки. Готовую продукцию сворачивают в катушки, помещают в полиэтиленовые пакеты.
Холодное волочение алюминиевой проволоки
На некоторых заводах, оснащенных гидравлическими прессами, электротехническую катанку изготавливают методом прессования. Нагретый слиток помещают в специальный контейнер с матрицей. На ней есть отверстие, соответствующее форме сечения изделия. Обработка давлением происходит за счет пуансона со сменной прессшайбой, которая плотно заходит в пространство контейнера.
Последний способ подходит для изготовления сложных профилей разного сечения, прутков, гладких и ребристых труб диаметром до 400 мм. Прессованная продукция, в отличие от литой, может выпускаться в виде прямолинейных отрезков от 1 до 2,5 метра.
Предварительная обработка
Чтобы алюминиевая проволока на выходе приобрела нужные свойства, ее подвергают предварительной обработке:
Закалка и старение алюминиевых сплавов сплавов
- Для крепости изделий из неупрочняемых сплавов применяют холодную деформацию. Это характерно для марок АД1, АМг3, АМг5.
- Термоупрочняемые сплавы подвергают закалке и старению: Д1П, Д16П, Д18.
- Для достижения пластичности проволоку отжигают.
- На завершающей стадии изготовления изделий с помощью специального инструмента проводится абразивная обработка. Она помогает удалить заусеницы и закруглить ребра металлического шнура.
Метод волочения
Алюминиевая проволока получается из катанки методом волочения. Заготовку диаметром от 7 до 20 мм протягивают через несколько отверстий – волок. Их размер намного меньше, чем сечение проволоки. Поскольку при горячей прокатке металл покрывается безвредной окисной пленкой, его не подвергают процедуре травления. Если катанка алюминиевая хранится долгое время, слой окислов необходимо стравливать. Для этого металл погружают в водный раствор серной кислоты.
Изготовление изделий проводят по такой схеме:
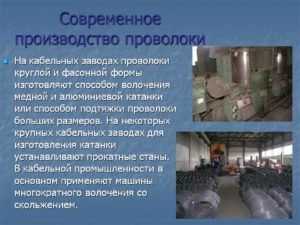
Современное производство проволоки
- Алюминий при помощи загрузчика подают в плавильную печь с рабочей температурой 700–800 0C.
- Расплавленную массу пропускают через фильеру с целью получения литой заготовки диаметром до 3,5 мм.
- Обрабатываемый материал охлаждают, кладут на индивидуальный компенсатор.
- Волочение катанки осуществляют на многократных станках без скольжения с применением густой смазки.
- С компенсатора заготовка поступает в волочильное устройство.
- Волочение заготовок меньшего диаметра производят на агрегатах со скоростью 18м/сек. и скольжением.
- Технологический процесс предполагает использованием мыльно-масляной эмульсии.
- При многократно повторяющемся волочении величину вытяжек делают на 5% меньше, чем для меди. Это снижает вероятность обрывов проволоки.
Области применения алюминиевой проволоки
Длинномерная нить из алюминия нашла широкое применение в разных сферах человеческой деятельности.
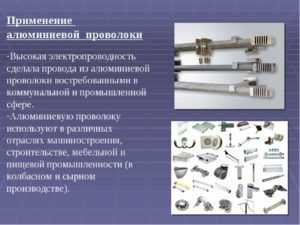
Применение алюминиевой проволоки
Круглую проволоку используют в качестве сварочного материала при ручной, дуговой, аргонной и автоматической сварке. Шов из алюминия защищает предмет от коррозии и термической деформации. При минимальном весе металл обеспечивает прочность конструкций. Данные виды работ характерны для строительства, судо-, машино- и авиастроения.
Длинномерный алюминиевый шнур является универсальным крепежным материалом. Его задействуют при изготовлении мебели. Пружины, сетки, фурнитура, заклепки, декоративные детали из алюминия – это далеко не весь перечень полезных предметов из катаного алюминия.
Пищевая промышленность: сырное и колбасное производство.
Проволока тесно связана с электротехнической промышленностью. Это антенны, разные виды кабелей и проводов для прокладки линий электропередачи, электроды, коммуникации. Из проволоки изготавливают метизы, сверла, пружины, электроды.
Металлическая нить незаменима в производстве деталей для оборудования химической промышленности и высокотехнологичных приборов.
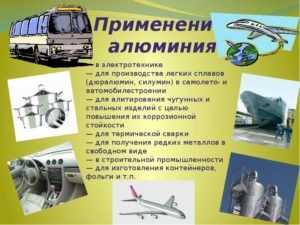
Алюминий используется в очень большом количестве различных отраслей
Алюминиевую ленту применяют в различных отраслях современного народного хозяйства: для сварки, электропроводки, сооружения конструкций, которые контактируют с влажной средой.
Проволоку используют для изготовления декоративных предметов, сувениров, украшений, которые могут быть отдельными вещами или частью интерьера. Плетение из проволоки является современным видом творчества.
Длинномерный материал нашел применение в ландшафтном дизайне, при изготовлении беседок, скамеек, оград.
Проволока из алюминия обладает уникальными техническими характеристиками. Это многофункциональный металл, который помогает реализовать инновационные проекты в науке и технике.
Видео по теме: Станок для волочения проволоки СВ 6
promzn.ru
Алюминиевая проволока: типы и области применения
Наиболее распространенным присадочным материалом для различных видов сварки является алюминиевая сварочная проволока. Данный материал широко используется в технологических процессах автоматической и полуавтоматической сварки. Непрерывность процесса, высокое качество получаемого шва, саморегуляция скорости подачи в область сварки – вот далеко не все достоинства, которыми обладает алюминиевая проволока.
Общеизвестным правилом считается то, что материал свариваемых деталей должен быть похожим по составу на используемый присадочный. Это условие становится особенно важным, поскольку именно от него зависит качество сварного шва, его долговечность и прочность.
Алюминиевая проволока зачастую используется для сваривания металлов похожего состава. К примеру, для автоматической и полуавтоматической сварки таких материалов, как легированная, углеродистая или нержавеющая сталь, а также, конечно же, алюминиево-марганцевые сплавы и алюминиевые детали. Газовая сварка наилучшим образом подходит для наплавления присадочной проволоки на шов.
Проволока сварочная алюминиевая представляет собой проволочную ленту. Это своеобразный гибкий электрод, который превосходно заменит более хрупкие и дорогостоящие элементы, которые могут применяться во время ручной обработки.
Алюминиевая проволока изготавливается из листа алюминия при помощи вытягивания и последующего нарезания на части необходимой длины. Фирмы-производители занимаются реализацией множества типов подобной продукции.
В зависимости от вида производства, алюминиевая проволока может иметь различные характеристики, к ней могут быть предъявлены различные требования. Следовательно, завод-изготовитель должен произвести необходимую продукцию. Будь то алюминиевая проволока различной длины и поперечного сечения, запросы покупателя должны быть удовлетворены.
Алюминий – универсальный материал, который характеризуется достаточной прочностью и надежностью, удобством эксплуатации и высокой степенью гибкости, обладает сравнительно низкой стоимостью и малым весом.
Выделяют следующие виды алюминиевой проволоки:
- Порошковая.
- Омедненная.
- Нержавеющая.
Каждый из этих типов имеет свои особенности применения. К примеру, порошковый тип представляет собой небольшую трубку, внутри которой находится алюминиевая смесь в виде порошка. Это предотвращает окисление и шлакообразование, а также способствует стабилизации горящей электрической дуги. Нержавеющая проволока используется для соединения хромосодержащей нержавеющей стали и никеля. В свою очередь, омедненная применяется для сваривания деталей из легированного чугуна и стали, что позволяет предотвратить разбрызгивание металла и получить сварные швы высокого качества.
Для получения высококачественного шва важен не только подобранный материал присадочной наплавки, но также и другие факторы, такие как температура зоны сварки и степень обработки поверхностей. Это значит, что температура плавления присадочного материала не должна быть больше температуры плавления свариваемых деталей, в то время как поверхность металла должна быть чистой и сухой, без каких-либо окислов, окалин и следов краски.
fb.ru
Деревья из алюминиевой проволоки | Невозможного.нет
Что удивительного можно создать из обычной алюминиевой проволоки? На этот вопрос всему миру ответил американский художник и скульптор Кевин Айрис (Kevin Iris). На протяжении уже 23-х лет Кевин мастерит очень красивые деревья из проволоки, причем все они разные: от маленьких деревцев, типа бонсай, до крупных с человеческий рост.
Деревья выполнены с высочайшей детализацией: сучки, листочки, веточки, плоды и цветки. У тех, кто впервые видит работы Кевина Айриса, как правило, создается впечатление, что это обычные деревья, которые художник заботливо вырастил, а затем покрыл серебряной краской, выдавая за проволочные. Только рассматривая удивительные деревья вблизи можно увидеть, как все эти произведения буквально сотканы витиеватыми узорами из обычной алюминиевой проволоки. Создание одного проволочного дерева занимает у мастера более четырех месяцев. В среднем, на кроне дерева получается до десяти тысяч миниатюрных листочков. Такому терпению и таланту можно только позавидовать.
Слава к мастеру пришла постепенно, только после того, как ценители искусства случайно увидели проволочные растения. А начинал скульптор с создания композиций для себя, своей семьи и друзей. Самое первое дерево из проволоки он подарил своему брату на день рождения, и оно до сих пор находится в его доме. Спустя время Кевин Айрис начал получать заказы на создание целых партий таких проволочных деревьев. При этом хочется отметить, что все его растения уникальны в той же степени, как и уникальны они в природе. Нет одинакового листочка, нет двух одинаковых кленов или сосен.
Как оказалось, создание деревьев из алюминиевой проволоки – это довольно прибыльное занятие. Одно такое дерево может стоить от 1 500 до 7 000 долларов.
[youtube]7-R3ImJvAD8[/youtube]
nevozmozhnogo.net
Алюминиевая проволока для полуавтомата — sovetskyfilm.ru
Для сварки деталей, выполненных из алюминия и сплавов на его основе, используется алюминиевая проволока, с помощью которой также выполняется наплавка заготовок из данного металла. Все работы с использованием такой проволоки осуществляются в среде защитного газа, в качестве которого чаще всего применяется аргон. Алюминиевая сварочная проволока, если она подобрана правильно, способна обеспечить высокое качество и надежность формируемого сварного шва, стабильность его механических характеристик.
Катушка алюминиевой сварочной проволоки
Алюминий, как известно, является одним из самых сложных металлов в плане выполнения сварочных работ. Этот факт, который может подтвердить любой опытный сварщик, объясняется свойствами данного металла: на его поверхности всегда присутствует тугоплавкая окисная пленка. Сам же алюминий, если не брать во внимание упомянутую пленку, имеет невысокую температуру плавления, что также вносит сложности в процесс выполнения сварки.
Оптимальным способом получения надежных соединений деталей, выполненных из алюминия и его сплавов, является механизированная дуговая сварка. Для ее осуществления используется алюминиевая проволока.
Виды алюминиевой проволоки и правила ее применения
Присадочная проволока, которая используется для соединения деталей, изготовленных из алюминия и его сплавов, может относиться к одной из двух категорий:
- Алюминиевая проволока, применяемая для выполнения технологической операции холодной высадки (требования к качественным характеристикам такой присадочной проволоки оговариваются в ГОСТ 14838-78).
- Проволока для сварки алюминия, а также сплавов на основе данного металла.
Рекомендуемые марки проволок для сварки алюминиевых сплавов
Выбирая сварочную проволоку для сварки алюминиевых сплавов с различным химическим составом, лучше остановить свой выбор на универсальных типах такого расходного материала. Кроме высокой надежности получаемого соединения, такая проволока позволяет обеспечить:
- устойчивость сварного шва к образованию горячих трещин;
- высокую прочность формируемого шва;
- пластичность полученного соединения;
- способность сварного шва успешно противостоять коррозионным процессам.
Специальная порошковая проволока позволяет сваривать заготовки без газа. Предлагаемый видеоролик поможет разобраться в целесообразности использования этой технологии.
Правильно подобранная алюминиевая проволока – не единственное условие, позволяющее получить качественное и надежное сварное соединение. Очень большое значение также имеет правильная подготовка соединяемых деталей, которая заключается в тщательной очистке их поверхностей и удалении с них тугоплавкой оксидной пленки. Важно выполнить такую процедуру непосредственно перед началом сварки, так как алюминиевая поверхность под воздействием окружающей среды быстро покрывается оксидной пленкой.
По этой же причине проволока, предназначенная для сварки алюминия, после вскрытия упаковки, в которой она поставляется с завода, должна быть использована достаточно быстро. Иначе ее поверхность будет подвергнута активному окислению. В этом случае качественные характеристики проволоки будут значительно ухудшены, что скажется и на характеристиках формируемого с ее помощью сварного соединения.
Временное хранение вскрытой катушки с алюминиевой проволокой
Проволока, которая применяется для сварки алюминиевых деталей полуавтоматом, может иметь различный химический состав. Для такой сварки используются в основном проволоки, изготовленные на основе алюминия в сочетании с марганцем, кремнием и магнием. Выбор конкретного типа зависит от того, какие элементы входят в химический состав свариваемых деталей.
Особенности подающих механизмов для алюминиевой сварочной проволоки
Стандартный подающий механизм полуавтомата не слишком подходит для работы с алюминиевой проволокой. Объясняется это такими характеристиками данного металла, как высокая пластичность и теплопроводность.
Подающий механизм стандартного полуавтомата для сварки, в котором применяются два ролика, может смять мягкую алюминиевую проволоку, что приведет к ее застреванию в механизме. Именно поэтому при использовании в полуавтомате алюминиевой проволоки необходимо оснащать его подающим механизмом, состоящим из 4 роликов, каждый из которых имеет U-образный профиль рабочей канавки.
Механизм подачи проволоки с четырьмя роликами
Для работы с полуавтоматом, в котором будет использоваться проволока из алюминия, необходимо оснащать его подающим шлангом минимальной длины (до 3 метров). В противном случае мягкая проволока будет просто застревать в длинном подающем шланге. Данную проблему помогает решить использование подающего канала из тефлона, что даст возможность значительно уменьшить трение проволоки о стенки такого канала.
Чтобы избежать застревания алюминиевой проволоки, которая отличается высоким коэффициентом теплового расширения, в наконечнике полуавтомата для сварки, следует подбирать наконечник таким образом, чтобы отверстие в нем было несколько больше (на 1–2 мм), чем диаметр самой проволоки.
Комплект различных наконечников облегчает подбор нужного отверстия для проволоки
Подающий механизм полуавтомата, на котором планируется использовать проволоку из алюминия, должен работать без перебоев, которые являются частой причиной застревания проволоки в канале подачи. Перебои в работе такого механизма чаще всего возникают по причине нестабильной работы тормозного устройства катушки. Чтобы в процессе выполнения сварки таких проблем не возникало, необходимо отрегулировать усилие, создаваемое катушкой: оно должно иметь возможность уменьшения до минимума. В то же время такого усилия должно быть достаточно для того, чтобы предотвращать поворот катушки.
Правильный выбор проволоки для выполнения полуавтоматической сварки алюминиевых деталей в среде аргона, а также параметров выполнения такого технологического процесса позволяет не только получать качественные, надежные и красивые сварные швы, но и минимизировать риск возникновения брака при их выполнении. К таким параметрам относятся не только диаметр используемой проволоки и ее химический состав, но и скорость ее подачи, а также значения сварочного тока и полярность его подключения.
Объем сварочных работ в домашней мастерской обычно не требует большого расхода алюминиевой проволоки, но маленькие катушки подходят не ко всем аппаратам. Установить бобину небольшого размера поможет смекалка, как показано на видео.
- Содержимое:
- Проволока для сварки нержавейки
- Проволока для сварки алюминия
- Какая должна быть скорость подачи проволоки
- Какая проволока лучше
Согласно ГОСТ 2246-70 выпускается около 76 видов проволоки для проведения сварочных работ с помощью полуавтомата. Дополнительно производится еще несколько десятков наименований продукции, соответствующей определенным ТУ.
Сварочная проволока для полуавтомата позволяет обеспечить максимально прочное соединение деталей, тяжело поддающихся термической обработки, сократить негативное воздействие на поверхность детали и шва.
Наиболее востребованными остаются расходные материалы, предназначенные для работ с нержавеющей сталью и алюминием.
Проволока для сварки нержавейки
Сварочная проволока для полуавтомата по нержавейке производится на основе высоколегированной стали. В результате получаемый шов становится прочным и устойчивым к воздействию влаги, имеет антикоррозионные свойства.
Чтобы добиться высоких прочностных характеристик крайне важно, чтобы наплавляемый металл во время сварки нержавеющей стали, полуавтоматом не вступал в химическую реакцию с водой, кислородом и азотом. С этой целью используется защитный газ, обычно аргон.
Для полуавтоматов используется порошковая сварочная проволока, позволяющая выполнить сварочные работы без применения углекислоты и других защитных газов. По своему строению стержень порошковой проволоки напоминает полую трубку, наполненную присадками, гранулами металла и шлакообразующими материалами.
Под воздействием высокой температуры, проволока для сварки полуавтоматом без газа раскаляется, внутренняя смесь испаряется, в результате образуется защитное облако газа. По мере остывания, на поверхности шва появляется защитный шлак, предотвращающий образование пор и растрескивание соединения.
Флюсовая проволока применяется не только для нержавейки, широкое распространение получило ее использование для получения качественного шва при работах с углеродистыми и низкоуглеродистыми сталями и практически любыми видами цветных металлов, включая титан.
Проволока для сварки алюминия
Алюминий считается одним из самых тяжелых в обработке металлов. Алюминий быстро нагревается, хорошо передает тепло, что в результате обеспечивает большое количество прогораний.
Алюминиевая проволока для сварных работ должна обеспечить надлежащее качество шва. Основными требованиями, предъявляемыми к электродным материалам, являются:
- Равномерная толщина. Механизм подачи проволоки может давать сбои в скорости движения электрода при резком изменении объема материала. Качество расходных материалов должно быть проверено с помощью скальпирования.
- Стабильность скорости подачи проволоки при полуавтоматической сварке независимо от расстояния.
- Качественный равномерный шов с отличным показателем смачиваемости кромок.
- Отсутствие в получаемых соединениях расколов и пор.
Так как диаметр электрода может варьироваться от 0,8 до 2,4 мм, чтобы обеспечить равномерную скорость подачи, наконечник проволоки выбирается по диаметру расходного материала.
Сварочная проволока для сварки алюминия используется при выполнении работ полуавтоматом в среде защитных газов Ar, He, или смеси Ar/He. Допускается применение специальных порошковых электродов.
Какая должна быть скорость подачи проволоки
В большинстве полуавтоматоматических станков и оборудовании с программным управлением, присутствует функция саморегулирования дуги, это несколько облегчает выбор скорости и других параметров.
Регулировка скорости подачи проволоки, сварочного полуавтомата осуществляется следующим образом:
- Горелка отводится от конструкции, подключенной к заземлению аппарата. Зажимается курок, устанавливается скорость, с помощью механического регулятора подачи проволоки, поворачиваемого до значения 100-120 мм/сек. Ток сварки взаимосвязан с интенсивностью движения электрода, поэтому регулировать его не нужно.
- Регулируем напряжение на дуге.
- Подключаем СО². Расход смеси устанавливается на уровне 8-12 л/мин. Если планируется сварка полуавтоматом порошковой проволокой без газа, следует установить меньшую скорость движения электрода.
- Делаем пробный шов на образце. Если аппарат не варит, добавляем напряжение, при этом расход сварочной проволоки не увеличиваем, оставляем прежним. В результате этого эксперимента можно заранее получить и записать значения необходимые при сварке проволокой с флюсом, проведения работ с нержавейкой и алюминием.
Какая проволока лучше?
На вопрос, какая проволока лучше, самозащитная, с флюсом, или общего сечения, не существует прямого ответа. Все зависит от используемого оборудования, условий выполнения работ и других факторов.
К примеру, технология сварки порошковой проволокой позволяет выполнять работы в потолочном положении, хорошо справляется с необходимостью в обратном формировании шва.
Недостаток использования проволоки с флюсовой прослойкой, то, что для качественного шва требуется безупречная схема протяжки проволоки в аппарате. Пока таким механизмом может похвастаться только оборудование, изготовленное в странах ЕС. В качестве минуса можно рассматривать высокую стоимость материала и узкий диапазон сварки.
При условии наличия качественного полуавтомата, лучше поменять проволоку общего сечения на порошковую. При работе с алюминием и нержавейкой, использование флюса помогает улучшить качество шва.
Алюминиевая проволока для полуавтомата обладает высокой пластичностью, поэтому для обеспечения оптимальных условий ее использования рекомендуется применять подающие устройства с четырьмя роликами. Они позволяют равномерно распределить прижимное усилие и не допустить повреждения поверхности проволоки, приводящее к образованию оксида алюминия, значительно ухудшающего качество сварочного шва.
В этом разделе каталога предлагаются образцы легированной алюминиевой проволоки, цена которой позволяет выгодно купить продукт в необходимом количестве:
- алюминиевая сварочная проволока AlMg5 диаметром от 0,8 до 1,6 мм, легированная магнием с предельной концентрацией до 5%. Она предназначена для полуавтоматической сварки постоянным током в среде аргона нелегированного алюминия или его сплавов с содержанием магния не более 3%. Область применения: авиационная промышленность, машиностроение, автомобильное хозяйство, пищевая и химическая отрасли. При увеличенной толщине свариваемых деталей (от 6 до 10 мм) и необходимости повышения температуры плавления рекомендуется использовать смесь аргона и гелия.
- сварочная проволока на основе сплава алюминия и кремния AlSi5 диаметром от 0,8 до 1,6 мм с предельной концентрацией химически чистого кремния до 6%. Она может использоваться при полуавтоматической сварке постоянным током в среде аргона и гелия литейных алюминиевых сплавов на основе кремния и магния, например, блоков цилиндров или деталей корпусов двигателей. Область применения: машиностроение, химическая и энергетическая отрасли.
- Высокое качество сварочной проволоки и полное соответствие ГОСТ 10543-75 гарантировано известной торговой маркой БАРС. На сайте компании «СВАРБИ» можно купить алюминиевую проволоку в розницу, но гораздо выгоднее приобрести ее по оптовой цене с прогрессивной скидкой. При выборе продукта необходимо учесть, что для получения качественного сварочного шва химические составы свариваемых металлов и проволоки должны иметь минимальные отличия.
Даже дети знают, что алюминий обычно вариться вольфрамовым электродом в среде аргона (TIG сварка). Но, то что люминьку можно сваривать полуавтоматом известно не всем.Для такого процесса нужен мощный полуавтомат, с такой же протяжкой. Моя самоделка подходит по всем параметрам www.drive2.ru/l/288230376152884642/. Кстати, уже пять лет без единой серьезной поломки этот агрегат трудится в моей мастерской, каждый день, на благо автомобилей клиентов, уничтожая иногда по 5 кг проволоки за 2 дня:)Также желательная тефлоновая вставка в рукав, продается в сварочных магазинах, хотя я работаю без проблем без нее. Наконечник под алюминий берем на 0.2 мм больше чем диаметр проволоки. Если проволока 0,8 мм то наконечник нужно брать 1 мм, если проволока 1 мм тогда наконечник 1,2 и т. д. Либо купить специально наконечник под алюминиевую проволоку. Защитным газом для нашего вида сварки будет не углекислота или смесь а чистый аргон. Ну и как вы поняли сама проволока тоже должна быть из алюминия, хотя я видел попытки «умельцев9quot; варить алюминий обычной стальной СВ08Г2С:).
Для штампованных и литых деталей нужно использовать разные виды проволоки ER 5356 и ER4043 соответственно, точно также как и при TIG сварке.
Полуавтоматическая сварка, конечно, не дотягивает до ювелирности TIGa, но по продуктивности превосходит его намного. Когда нужно что-то наплавить, или заварить зазор то тут полуавтомат лидирует с отрывом. На заводах из-за высокой продуктивности используют именно MIG.Например ремонт клапанной крышки от ВАЗ 2105, которую я специально для этой записи сначала повредил молотком заняла не более 3 мин.
На поры не смотреть и тапками не кидать от масла не чистил, просто хотел показать продуктивность:)
Сварка алюминия является достаточно сложным технологическим процессом, который требует масштабной предварительной подготовки, а также наличия специализированных средств. Дело в том, что данный металл очень сложен в сваривании, так как у него быстро образуется оксидная пленка, а также наблюдается повышенная текучесть, что в особенности сказывается на присадочном материале. Проволока сварочная легированная может быстро стекать вниз при расплавлении в вертикальном или потолочном положении, так и не заполняя шов. Во время работы с полуавтоматом это очень важный момент, поэтому, нужно обращать внимание, какие виды сварочной проволоки здесь используются.
Проволока для сварки алюминия
Проволока сварочная высоколегированная требует дополнительной защиты, так что здесь лучше всего подходит аргонодуговая сварка, которая минимизирует негативные эффекты от воздействия негативной среды за счет отличной изоляции, которую обеспечивает данный газ. Здесь требуется специальная алюминиевая проволока, которая будет подаваться полуавтоматом на место, где находится сварочная ванна, с заданной скоростью. Скорость подачи должна соответствовать скорости плавления металла. Если сравнивать со сталью или медью, то скорость подачи здесь будет выше, так как сам алюминий является мягким металлом с низкой температурой плавления. Проволока сварочная легированная диаметром 4 мм.
Проволока сварочная легированная диаметром 4 мм
Естественно, что работа ведется не всегда с чистым металлом. В промышленности зачастую применяются разнообразные сплавы, которые при сохранении низкого веса добавляют крепости металлу. Таким образом, требуется подбирать специальную проволоку, которая бы соответствовала нюансам сплава. В данном случае соблюдается основной принцип, по которому присадочный материал, к примеру, сварочная проволока СВ 08ГНМ, должна максимально соответствовать составу сплава. Выбор защитного газа также является важным моментом, но здесь зачастую все сводится к использованию аргона, так как сложности с работой алюминия он замечательно убирает все негативные моменты. В качестве замены можно использовать ацетилен, но он с данной функцией будет справляться хуже, так что проволока сварочная легированная диаметром 2 мм не сможет полностью проявить все свои преимущества. В связи с большой ответственностью применения, к стандартам изготовления выдвигаются большие требования. Производится проволока сварочная легированная по ГОСТ 7871-75.
Преимущества
- Дает высокие результаты качества соединения при работе с алюминием;
- Существует широкое разнообразие выбора, благодаря которому можно подобрать подходящий вариант практически под любой сплав;
- Обладает высокой коррозионной стойкостью даже при температурной обработке;
- Легко можно определиться с толщиной требуемой проволоки, согласно толщине заготовке;
- Одинаково хорошо подходит как для ручной, так и для полуавтоматической сварки;
- Дополнительные легирующие элементы помогают лучше бороться с негативными моментами сварки алюминия.
Недостатки
- Как сам основной материал, так и проволока к нему покрывается оксидной пленкой, что требует обработки перед процессом соединения, иначе будет падать уровень качества;
- Из-за большого ассортимента порой сложно выбрать наиболее подходящую модель проволоки, тем более, что не всего известно с каким сплавом приходится работать;
- Обязательно нужно использовать инертный защитный газ, что делает себестоимость сварки достаточно высокой и сложно осуществимой для домашних условий;
- Требуется точная регулировка параметров подачи из-за высокой скорости плавления материала проволоки.
Физико-химические свойства
Химические свойства проволоки во многом определяются ее составом. С учетом того, что алюминий является одним из основополагающих металлов, которые содержит сварочная проволока СВ06Х14, а также другие марки, то и большинство свойств она получает от него. Материал плохо взаимодействует с другими металлами, так что вкрапления легирующих элементов здесь минимальные. Сохраняется высокая подверженность влиянию оксидов, что требует предварительную обработку растворителями. При всем этом шов сохраняет высокую коррозионную стойкость даже после термической обработки.
Сварочная проволока 18ХМА
Помимо этого проволока сварочная 18ХМА обладает высокой пластичностью и низкой температурой плавления. Это помогает работать с металлом, не подвергая его сильному температурному воздействию. При нагревании расходный материал не меняет цвет, что слегка затрудняет визуальный контроль, но при работе с полуавтоматом все будет зависеть только от правильного режима. Стоит также отметить, что проволока не портит электропроводность алюминия, которая оказывается выше, чем у меди, поэтому, ее применяют и при ремонте электроприборов.
Технические характеристики
Особенности выбора
Подбирая присадочный материал для полуавтомата, следует в первую очередь определиться с тем, с каким металлом будет происходить сваривание. Это один из самых главных моментов, так как состав основного и присадочного материала должен быть максимально похож.
Если же неизвестно точный состав, изделия, которое нужно сваривать, то выбирается нейтральный вариант, которым может выступить сварочная проволока СВ 08ГА.»
Вторым параметром является толщина, с которой придется столкнуться. Здесь все максимально просто, так как чем больше толщина свариваемой заготовки, тем толще должна быть проволока. Для алюминия, который достаточно быстро плавится, нужно аккуратно выбирать режимы, чтобы не испортить основной металл. Из-за сложностей в свариваемости, газовая сварка и аргонодуговая применяется даже при большой толщине, только для этого может потребоваться разделка кромок.
Схема газовой сварки алюминия
Многие производители выпускают проволоку в бухтах различного объема. Для длительной однообразной работы требуется большой запас материала, так что выгоднее покупать бухты с максимальной длиной проволоки. Для частной сферы такой необходимости нет, поэтому, можно остановиться на более простых вариантах.
Алюминиевая проволока для полуавтомата
При выборе нужно обращать внимание, чтобы расходный материал и основной металл имели примерно одинаковую температуру плавления. Из-за дополнительных элементов в составе сплава значения могут достичь критических значений, так что шов либо не сможет создать нормальное крепкое соединение, либо же основной металл перепалится, а проволока так и не достигнет нужного состояния для сваривания.
Особенности сварки алюминия проволокой на полуавтомате
Когда используется сварочная проволока 09Г2С, или другая марка, требуется учитывать повышенную расположенность металла к короблению, так как у него большая величина коэффициента линейного расширения. Сам металл и проволока из него обладает низкой упругостью, что приводит к деформации. Во время работы на полуавтомате, требуется жестко фиксировать детали при помощи дополнительного груза, пресса или других доступных способов
Перед каждым началом процесса сваривания обязательно нужно проводить химическую очистку, чтобы убрать оксиды и прочие негативные скопления на поверхности. Во время самого сваривания должна быть обеспечена защита. Даже при работе на полуавтомате возникает большая вероятность появления трещин, которые появляются от перепада температур и попаданий кислорода и водорода в шов. Все вышеуказанные процедуры помогают снизить этот риск.
Производители
Внимание, только СЕГОДНЯ!sovetskyfilm.ru
Технологический процесс изготовления проволоки из цветных металлов и сплавов :: Технология металлов
- ОБЩИЕ СВЕДЕНИЯ
Технологический процесс изготовления проволоки — это ряд последовательных операций (травление, термообработка, волочение и другие), при осуществлении которых происходит уменьшение сечения заготовки и достигаются необходимые свойства проволоки.
Качество изделия и экономические показатели производства проволоки зависят от технического уровня процесса. Важным условием снижения трудовых затрат в производстве проволоки является сокращение циклов. Это достигают путем волочения проволоки с максимально возможными суммарными обжатиями (табл. 1).
Таблица 1
Допустимые суммарные обжатия
Сплав или металл | Максимальное суммарное обжатие, % | Сплав или металл | Максимальное суммарное обжатие, % |
Медь M1 | 99,9 | Константан | 99 |
Л80 | 95—99 | Никель | 99 |
Л62 | 80—96 | Алюмель | 80-90 |
ЛС 59-1 | 40—50 | Хромель | 80—90 |
БрБ-2 | 35-85 | Монель-металл | 80-95 |
БрКМцЗ-1 | 80—90 | Алюминий | 99,9 |
БрОЦ4-3
| 80—99 | Цинк | 99,9 |
Манганин
| 99 | Титан (ВТ1) | 45-60 |
Они зависят главным образом от пластичности металла и диаметра обрабатываемой проволоки. Чем меньше диаметр, тем больше допустимое суммарное обжатие. Например, при волочении проволоки бериллиевой бронзы из катанки 7,2 мм в начале процесса до размера 4,5 мм допускаются обжатия между отжигами, равные 30—40%, а из заготовки диаметром 1,0—0,5 мм волочение ведется с суммарным обжатием 75—85%.
Важным фактором, определяющим технологию производства проволоки, является заготовка и способ ее получения. От диаметра заготовки, ее качества зависит трудоемкость производства и качество проволоки.
2. ЗАГОТОВКА ДЛЯ ПРОВОЛОКИ
Заготовку для изготовления проволоки получают следующими способами:
1. Прокаткой слитков на проволочно-прокатном стане до диаметра 6,5—19 мм. Этот способ является наиболее производительным и широко используется для получения заготовки из меди, медных сплавов, алюминия, никеля, никелевых и медно-никелевых сплавов, латуней (Л62, Л68, ЛА85-0,5), цинка, бронз (ОЦ4-3, КМЦ-3-1, ББ2), титана и титановых сплавов.
2. Горячим прессованием на гидравлических прессах. Этим способом можно получить заготовку диаметром 5,5—20 мм и выше с высоким качеством поверхности. Однако этот метод менее производителен, чем прокатка, и связан с получением значительных геометрических отходов — от 10 до 25%. В то же время при прокатке эти отходы составляют 2—4%. Прессованием получают заготовку из сплавов, сортовая прокатка которых затруднена, например латуни ЛС59-1, ЛС63-3 и др., а также при необходимости получения проволоки с высоким качеством поверхности и сложным профилем.
3. Разрезкой холоднокатаных дисков по спирали специальными ножницами на прямоугольную заготовку (например, размером 6x8 мм). Этот способ применяется для сплавов, не выдерживающих горячей деформации. К таким сплавам относится фосфористая бронза.
4. Металлокерамическим способом — путем спекания порошков в длинные прямоугольные заготовки и последующей ковки их на ротационно-ковочных машинах. Этот способ применяется для тугоплавких металлов (молибден, вольфрам и др.).
3. ИЗГОТОВЛЕНИЕ ПРОВОЛОКИ ИЗ МЕДИ
Заготовкой для волочения медной проволоки служит катанка диаметром 7,2—19 мм или прямоугольного сечения. Для изготовления проволоки сложного профиля применяется прессованная заготовка соответствующего профиля. Заготовку травят в 8—12%-ном водном растворе серной кислоты, подогретом до 40—50 °С. Волочение катанки диаметром 7,2 мм, предварительно сваренной встык, производят на машинах со скольжением типа ВМ-13 на размер 1,79—1,5 мм. Для смазки и охлаждения применяется мыльно-масляная эмульсия. Далее волочение ведут на 22-кратной машине на размер 0,38—0,2 мм, скорость волочения до 18 м/сек. Затем волочение на 18-кратных машинах на диаметры 0,15—0,05 мм. На последнем переделе волочения применяют алмазные волоки. Угол рабочего конуса волок 16—18°.
Проволоку диаметром 0,15—0,05 мм изготавливают без промежуточного отжига. При необходимости проводится безокислительный отжиг, как правило, на готовых размерах в конвейерных электропечах с водяным затвором или в шахтных электропечах без доступа воздуха.
На некоторых заводах кабельной промышленности эксплуатируются волочильные машины с совмещенным отжигом медной проволоки. Применение таких машин позволяет снизить трудоемкость изготовления проволоки и повысить степень автоматизации производства. В настоящее время работают над улучшением качества отжига проволоки на этих машинах.
4. ИЗГОТОВЛЕНИЕ ПРОВОЛОКИ ИЗ АЛЮМИНИЯ
Алюминиевую проволоку изготавливают из катаной заготовки диаметром 7—19 мм. При горячей прокатке алюминий покрывается очень тонким слоем окислов, влияние которого на процесс волочения незначителен, поэтому горячекатаную заготовку обычно не травят. Но при длительном хранении на металле образуется слой окислов, который рекомендуется стравливать. В этом случае производят травление в водном растворе, содержащем 8—12% h3SO4 .
Изготовление алюминиевой проволоки средних и тонких размеров проводится по следующей схеме.
Волочение катанки диаметром 7,2 мм на 1,8 мм осуществляется на многократных машинах без скольжения типа ВМА-10/450. Далее волочение на размер 0,47—0,59 мм проводится на 15 волочильных машинах со скольжением; скорость волочения до 18 м/сек.
На машинах без скольжения применяется густая смазка, на машинах со скольжением — мыльно-масляная эмульсия.
При многократном волочении алюминиевой проволоки в целях снижения обрывности принимают величину вытяжек на 5% ниже, чем для меди. Волоки применяются с углом рабочего конуса, равным 24—26°.
5. ИЗГОТОВЛЕНИЕ ПРОВОЛОКИ ИЗ ЦИНКА
Цинковая проволока изготавливается из цинка марок ЦО и Ц1. Заготовкой для волочения служит катанка диаметром 7,2 мм, ее протягивают на размер 3,7 мм на 6-кратной машине со скольжением типа 6/480. Смазкой служит мыльно-масляная эмульсия, приготовленная из пасты Ц4 с добавкой серного цвета. Далее волочение на машинах со скольжением типа 8/250, 10/250 с диаметра 3,7 мм на готовые размеры 1,5—2 мм. Смазка та же, что и для предыдущего передела волочения. При волочении цинковой проволоки особое внимание должно уделяться подготовке смазки и волок. Для снижения усилий на преодоление трения рекомендуется уменьшить площадь контактирования проволоки в очаге деформации, для чего угол рабочего конуса волоки увеличивают до 24—26°, а длину рабочего пояска уменьшают до 0,3 диаметра готовой проволоки.
Цинковую катанку обычно не подвергают травлению, так как тонкий слой окислов, покрывающий ее, не оказывает влияния на процесс волочения.
6. ИЗГОТОВЛЕНИЕ ПРОВОЛОКИ ИЗ ТИТАНА
Заготовкой для волочения проволоки из титана служит катанка диаметром 8 мм. Волочение ведут на однократных или многократных машинах без скольжения в твердосплавные металлокерамические волоки. Для смазки применяют сухой порошкообразный графит. Скорость волочения от 20 до 50 м/мин. Допустимые суммарные обжатия при волочении проволоки из титана марки ВТ1 — от 45 до 60%. После такой деформации проводится отжиг в электропечах при температуре 620—640°С, выдержка при данной температуре 20 мин.
Отожженные бухты проволоки погружают в соляноизвестковый раствор следующего состава: 100—150г/л гашеной извести (СаО) и 80—100 г/л поваренной соли (NaCl). Температура раствора 80—90 °С. После обработки в растворе бухты просушивают в токе теплого воздуха. Полученный на поверхности проволоки известковый слой способствует лучшему захвату сухого порошкообразного графита.
Готовую проволоку травят для снятия альфированного слоя. После травления проволоку подвергают вакуумному отжигу для повышения пластичности и снижения содержания водорода. Температура отжига 750— 800 °С, время выдержки 4—6 ч, охлаждение в печи до 250 °С. В печи поддерживается вакуум от 13,3 до 6,65 мн/м2 (от 1 · 10-4 до 5 10-5 мм рт. ст.).
По указанной технологии изготавливается проволока из титана марки BT1 диаметром от 1,2 до 7 мм. Волочение ведут в твердосплавные металлокерамические волоки с углом рабочего конуса 8—10°.
Проволоку из титановых сплавов изготавливают по этой же технологии, но с большим количеством промежуточных отжигов, так как допустимое суммарное обжатие при обработке сплавов снижается до 30—40%.
7. ИЗГОТОВЛЕНИЕ ПРОВОЛОКИ ИЗ НИКЕЛЯ И ЕГО СПЛАВОВ
Проволоку из никеля и его сплавов изготавливают из катаной заготовки. Поверхность катанки из никелевых сплавов и заготовка после отжига имеют весьма плотную окисную пленку, препятствующую процессу волочения, поэтому в производстве проволоки особое внимание уделяется подготовке поверхности. С этой целью применяется комбинированное щелочно-кислотное и кислотно-солевое травление, известково-солевое покрытие поверхности заготовки .
Волочение проволоки из никелевых и медно-никелевых сплавов, обладающих высокой твердостью и прочностью, связано с повышенным износом волок, поэтому в процессе производства этой проволоки вопросу стойкости волок также уделяется большое внимание. С этой целью повышается качество подготовки поверхности металла, подготовки волок и смазки, внедряется волочение проволоки в условиях жидкостного трения. В настоящее время волочение проволоки из никеля, кремнистого никеля, никеля марганцовистого, константана, хромеля на многократных машинах без скольжения ведется в так называемые сборные волоки , создающие условия жидкостного трения.
Проволоку из никеля и его сплавов отжигают в электропечах шахтного типа без доступа воздуха, а также в протяжных электропечах. Для получения светлой поверхности рекомендуется вести отжиг в среде генераторного газа, диссоциированного и неполностью сожженного аммиака, содержащего 5% водорода, или в чистом осушенном водороде. Отжиг термоэлектродной проволоки на готовых размерах ведется в окислительной среде для получения надежной окисной пленки, которая в значительной мере определяет свойства проволоки (стабильность т. э. д. с).
8. ИЗГОТОВЛЕНИЕ ПРОВОЛОКИ ИЗ ВОЛЬФРАМА
Заготовкой для вольфрамовой проволоки служат вольфрамовые штабики квадратного сечения 15X 15 мм, длиной около 0,5 м, полученные металлокерамическим способом.
Перед волочением штабики проковывают на ротационно-ковочных машинах на диаметр 2,5—3,0 мм. Кованую заготовку протягивают на диаметр 1 мм на цепных волочильных станах длиной до 30 м. Волочение горячее, для чего стан оборудован газовой печью. Перед задачей в волоку конец прутка заостряют путем нагрева до вишнево-красного цвета и погружения в коробку с сухим азотнокислым калием или натрием. Под действием высокой температуры соль растворяется и равномерно растворяет концы вольфрамовых прутков на длине 100—120 мм. Следует избегать попадания азотнокислого калия или натрия в канал волоки во избежание его порчи. После заострения с конца прутка смывают остатки азотнокислого калия или натрия водой и смазывают его коллоидно-графитовым препаратом марки B-1. Заостренный конец нагревают в печи и затягивают в волоку на длину до 200 мм. Затем конец прутка прогревают вместе с волокой, быстро устанавливают в волокодержатель и протягивают.
Волочение ведется на скорости 0,1—0,15 м/сек. Волоки твердосплавные с углом рабочего конуса 8—10 град. Перед волочением волоку нагревают до температуры 500 °С, а проволоку до 1000—850 °С в зависимости от диаметра (с уменьшением диаметра снижается температура).
Таким образом процесс повторяют 7—8 раз до диаметра 1 мм, после чего проволоку сворачивают в моток.
Далее волочение на размер 0,5—0,55 ведут на однократных волочильных машинах в 6 протяжек. С фигурки проволока проходит через смазочную коробку с коллоидно-графитовым препаратом марки В-1, разбавленным дистиллированной водой в соотношении 1:1, попадает в газовую печь, где нагревается до температуры 800—750 °С, протягивается в победитовую волоку со скоростью 0,16—0,20 м/сек и принимается на барабан диаметром 500 мм.
Волочение на более тонкие размеры проводится по этой же схеме с приемом проволоки на барабаны диаметром 200 мм или на катушки. Скорость волочения до 0,3—0,4 м/сек. Для смазки применяют препарат марки В-1, разбавленный дистиллированной водой в соотношении 1 : 2. Волочение проволоки диаметром 0,34—0,32 мм и ниже ведется в алмазные волоки типа Т, которые нагревают перед волочением до 400 °С.
9. ИЗГОТОВЛЕНИЕ ПРОВОЛОКИ ИЗ БЛАГОРОДНЫХ И РЕДКИХ МЕТАЛЛОВ
Для изготовления проволоки из серебра применяют катаную или прессованную заготовку диаметром 7—8 мм. Волочение заготовки ведут без промежуточного отжига до размера 0,26 мм по следующей схеме. До диаметра 3—3,5 мм применяют однократное волочение. В качестве смазки используют хозяйственное мыло. Волочение на этом переделе можно вести на многократных волочильных машинах со скольжением типа ВМ-13 или СМВ-П-9. Волочение до размера 1,2 мм ведут на 15-кратной машине со скольжением типа 15/250, затем на машине типа 22/200 до диаметра 0,26 мм. На этом размере проводится отжиг в камерной электропечи при температуре 250 °С, выдержка 30 мин.
Дальнейшее волочение на тончайшие размеры до 0,02 мм проводится на 18 волочильных машинах со скольжением без промежуточного отжига. На машинах со скольжением смазкой служит мыльная эмульсия. Волоки твердосплавные металлокерамические с углом рабочего конуса 16—18 град. Для тончайшего волочения применяют алмазные волоки типа М.
В процессе обработки серебряной проволоки заготовка и промежуточные размеры после отжига травлению не подвергаются. Особое внимание уделяется чистоте рабочего места, качеству поверхности проволоки, подготовке производства с целью исключения обрывности и потерь металла.
Для получения проволоки тончайших диаметров (до 0,001 мм) из золота, платины и сплавов благородных металлов применяют волочение в медной рубашке, для чего пруток из благородных металлов или сплавов диаметром до 2 мм закладывают в .медную трубку диаметром 10 мм и с толщиной стенки 4 мм. Такую биметаллическую заготовку подвергают волочению до расчетного размера.
Так, для получения платиновой проволоки диаметром 0,01 мм волочение биметаллической заготовки ведут до диаметра 0,05 мм, для получения диаметра 0,005 мм — волочение до 0,025 мм, для диаметра 0,004 мм — волочение до 0,02 мм и т. д. Перед применением проволоки из благородных металлов с нее стравливают верхний слой металла (медную рубашку) раствором азотной кислоты в дистиллированной воде в соотношении 1:1.
Проволоку из бериллия и его сплавов диаметром от 1 до 0,12 мм производят волочением при температурах 420—450 °С. Обжатие за проход составляет 25%. В качестве смазки используют коллоидный графит в масле, а также смесь графита с дисульфидом молибдена. После каждого третьего прохода проволоку подвергают промежуточному отжигу при 800 °С в течение 6 ч 30 мин. Очистку поверхности проволоки производят ультразвуковым методом, так как травление снижает ее механические свойства.
10. ИЗГОТОВЛЕНИЕ ПРОВОЛОКИ ИЗ ЛАТУНЕЙ
Пластичность латуней ниже пластичности меди, поэтому в процессе обработки они быстрее нагартовываются и требуются промежуточные отжиги. По пластичности латуни можно условно разделить на три группы: 1) пластичные латуни, содержащие выше 78—80% меди. К ним относятся латуни Л80, ЛА85-0,5, Л90 и др.; 2) латуни средней пластичности, содержащие 60—70% меди. К ним можно отнести Л62, Л68; 3) латуни низкой пластичности. К ним относятся латуни марок ЛС59-1, ЛО60-1.
Изготовление проволоки толстых и средних размеров из латуней первой группы можно вести без промежуточного отжига; тонких размеров—с одним промежуточным отжигом и тончайших—с двумя отжигами.
Из латуней второй группы изготовление проволоки толстых размеров ведется без промежуточных отжигов; средних размеров— с одним и двумя промежуточными отжигами; тонких размеров — с тремя отжигами и тончайших — с четырьмя промежуточными отжигами.
Проволока из латуней третьей группы диаметром выше 5 мм производится из прессованной заготовки соответствующего диаметра без промежуточных отжигов. Проволоку диаметром ниже 5 мм изготовляют с промежуточными отжигами через каждые 30—40% обжатия.
С улучшением технологии подготовки поверхности металла перед волочением, повышением качества волочильного инструмента и смазки, а также улучшением качества заготовки суммарные обжатия при волочении латунной проволоки могут быть повышены и, следовательно, сокращено количество промежуточных отжигов.
В связи с большой градацией латунной проволоки по механическим свойствам термическая обработка в технологическом процессе ряда марок латунной проволоки (Л62, Л68 и др.) имеет важное значение, определяющее качество проволоки (механические свойства) и условия ее дальнейшей обработки. В процессе производства латунной проволоки особое внимание должно уделяться отжигу, с точки зрения его равномерности, и подготовке поверхности проволоки после отжига для дальнейшей обработки. Многократное волочение латунной проволоки средних и тонких диаметров ведется с частными обжатиями 17—18%. Желательно работать на меньших обжатиях, если позволяет машина.
Травление заготовки проволоки и промежуточных размеров после отжига проводится в 5—15%-ном водном растворе серной кислоты. Удовлетворительное качество травления латунной проволоки получается при условии погружения ее в раствор на приспособлении, обеспечивающем равномерное травление каждой бухты .
Для получения светлой поверхности проволоки после отжига в отдельных случая проводится травление в растворе, содержащем 2 ч. серной кислоты, 1 ч. азотной кислоты и 6 ч. воды с последующим пассивированием в водном растворе, содержащем 150 г/л хромпика и 400—450 г/л серной кислоты. После пассивирования производится нейтрализация в щелочном растворе. Латунная проволока отжигается в шахтных электропечах без доступа воздуха и в протяжных электропечах.
Наиболее равномерный отжиг получается в протяжных электропечах, а также в шахтных электропечах с принудительной циркуляцией воздуха. Хорошие результаты по равномерности отжига проволоки Л62 получены в шахтных электропечах колодцевого типа, оборудованных автоматическим регулированием температур по зонам с учетом тепловой инерции печи. При этом достигнуты узкие пределы механических свойств проволоки в одной партии: предел прочности от 400 до 460 Мн/м2 (40— 46 кгс/мм2), а в одном мотке колебания не превышают 30 Мн/м2 (3 кгс/мм2) (проволока была изготовлена из латуни марки Л62 с содержанием меди 62—63%).
Для волочения латунной проволоки применяют твердосплавные металлокерамические волоки с углом рабочего конуса 14— 18 град. Проволоку диаметром ниже 0,2 мм протягивают в алмазные волоки типа П.
Источник:Хаяк Г.С. Волочение проволоки из цветных металлов и сплавов,Металлургия, 1967.
markmet.ru
способ производства проволоки из алюминиевого сплава - патент РФ 2101107
Изобретение предназначено для производства проволоки электротехнического назначения. Непрерывно-литую бесконечную заготовку прокатывают в проволоку и сматывают. При кристаллизации заготовки из сплава и при прокатке заготовку связывают с устройством заземления и с элементом цепи. Разница потенциалов на элементе составляет 0,1-500 В. 1 табл. Изобретение относится к способам производства проволоки методом непрерывной прокатки литых бесконечных заготовок. Известен способ получения условно-бесконечного формованного материала, включающий непрерывное литье из сплава во вращающемся разливочном кристаллизаторе и отведение получаемой бесконечной заготовки на последующую переработку [1] Указанный способ не решает проблемы обеспечения переработки заготовки в проволоку-катанку. Известен способ обработки условно-бесконечных материалов, включающий непрерывный многопроходный транспорт бесконечной детали [2] Указанный способ не решает проблемы совмещения многопроходного транспорта с непрерывным формированием детали. Прототипом изобретения является способ получения проволоки из алюминиевого сплава, включающий непрерывное литье алюминиевого сплава во вращающемся разливочном колесе-кристаллизаторе с желобом по ободу и с прижатой к ободу бесконечной лентой, охлаждение кристаллизуемой бесконечной заготовки по мере поворота колеса-кристаллизатора, отведение получаемой бесконечной заготовки от обода колеса-кристаллизатора, непрерывную многопроходную прокатку бесконечной заготовки в проволоку и сматывание проволоки [3] Ввиду поддержания заготовки согласно указанному способу в состоянии электрической нейтральности не обеспечивается управление вредными и полезными электростатическими явлениями при трении, имеющих место процессах и деформации. Задачей изобретения является снижение ресурсозатратности производственных процессов при одновременном повышении качества проволочной продукции. Сущность изобретения состоит в том, что в способе производства проволоки из алюминиевого расплава, включающем непрерывное литье алюминиевого сплава во вращающемся разливочном колесе-кристаллизаторе с желобом по ободу и с прижатой к ободу бесконечной лентой, охлаждение кристаллизуемой бесконечной заготовки по мере поворота колеса-кристаллизатора, отведение получаемой бесконечной заготовки от обода колеса-кристаллизатора, непрерывную многопроходную прокатку бесконечной заготовки в проволоку и сматывание проволоки, предусмотрено связывание заготовки в процессе кристаллизации из расплава и в процессе дальнейшей прокатки как элемента электрической цепи через заземляющую ветвь цепи с устройством заземления, а также с элементом, разница потенциалов на котором составляет 0,1-50,0 В. Пример 1. Взяли алюминиевый сплав марки А5Е. Сплав был образован алюминиевой основой, включающей легирующие добавки и примеси, мас. 0,35 железа; 0,08 цинка; 0,02 меди; 0,03 титана. Из сплава составили шихту. Шихту расплавили за счет нагрева до 725-730oC. Расплавленную шихту подвергали рафинированию с проведением продувки расплава техническим азотом. Продувка шла до приобретения жидкой металлической фазой удельного объемного сопротивления 20,1 Омсм3. После этого осуществили непрерывное литье алюминиевого сплава во вращающемся разливочном колесе-кристаллизаторе. Колесо-кристаллизатор имел желоб по ободу и прижатую к желобу бесконечную ленту. Угол обхвата бесконечной ленты обода устанавливали равным 180oC. Осуществляя литье, провели охлаждение до 480-500oC кристаллизуемой бесконечной заготовки. Охлаждение шло по мере поворота колеса-кристаллизатора. По ходу производимого литья осуществляли отведение получаемой бесконечной заготовки от обода колеса-кристаллизатора. Обеспечивающие указанное отведение манипуляции совместили с непрерывной многопроходной прокаткой бесконечной заготовки в проволоку и со сматыванием проволоки. Прокатку вели с использованием 17 последовательно установленных прокатных клетей. Каждая из применяемых клетей имела по 3 материалодеформационных валка диаметром 280 мм. Валки в клетях были обращены к оси заготовки, их ориентировали соответственно лучам 3-конечной звезды. Производительность процесса прокатки установили равной 7,3 м/с. Заготовку в процессе кристаллизации из расплава и дальнейшей прокатки связывали как элемент электрической цепи. Связывание шло через заземляющую ветвь цепи. Выход этой ветви был соединен с входом устройства заземления, а также с элементом малого сопротивления. Разница потенциалов на этом элементе составляла 0,1 В. Достигнутые результаты отражены в таблице. Пример 2. Реализующий предложенный способ технологический процесс вели при наличии соответствия определяющих режимов и параметров данным примера 1, за исключением того, что разницу потенциалов на сопряженном с устройством заземления элементе заземляющей ветви электрической цепи устанавливали равной 50,0 В. Достигнутые результаты отражены в таблице. Пример 3. Реализующий предложенный способ технологический процесс вели при наличии соответствия определяющих режимов и параметров данным примера 1, за исключением того, что разницу потенциалов на сопряженном с заземляющим устройством элементе заземляющей ветви электрической цепи устанавливали равной 10,0 В. Достигнутые результаты отражены в таблице. Техническим преимуществом предложенного способа по сравнению с прототипом является пониженная энергозатратность. Источники Информации: 1. Патент РФ N 2027544, кл. B 22 D 27/02. 2. Клюквин Т.И. Электростатические явления при трении и резании металлов. М. Наука, 1969. 3. Берин И.Ш. и др. Производство медной и алюминиевой проволоки. М. Металлургия, 1975.ФОРМУЛА ИЗОБРЕТЕНИЯ
Способ производства проволоки из алюминиевого сплава, включающий непрерывное литье алюминиевого сплава во вращающемся разливочном колесе-кристаллизаторе с желобом по ободу и с прижатой к ободу бесконечной лентой, охлаждение кристаллизуемой бесконечной заготовки по мере поворота колеса-кристаллизатора, отведение получаемой бесконечной заготовки от обода колеса-кристаллизатора, непрерывную многопроходную прокатку бесконечный заготовки в проволоку и сматывание проволоки, отличающийся тем, что заготовку в процессе кристаллизации из сплава и дальнейшей прокатки связывают, как элемент электрической цепи через заземляющую ветвь цепи, с устройством заземления, а также с элементом, разница потенциалов на котором составляет 0,1 500 В.www.freepatent.ru