Свойства легированной стали. Какие стали называются легированными
Низколегированные стали: классификация и применение
Легированными сталями называют такие стали, которые получают свои улучшенные свойства за счет:— одного или нескольких специальных легирующих элементов;— более высокого содержания, чем в обычных углеродистых сталях таких элементов как магний и кремний.
Легированные стали содержат марганец, кремний и медь в более высоких концентрациях, чем это допускается для обычных углеродистых сталей (1,65 % по марганцу; 0,60 % по кремнию и 0,60 % по меди).
Легирующие элементы повышают механические и технологические свойства сталей. Обычно легированные стали делят на три группы по суммарному содержанию легирующих элементов (не считая углерода):— низколегированные стали – менее 5 %;— среднелегированные стали – от 5 до 10 %;— высоколегированные стали – более 10 %.
Низколегированные стали
Низколегированные стали образуют группу сталей, которые проявляют более высокие механические свойства по сравнению с обычными углеродистыми сталями. Это является результатом добавок таких легирующих элементов как никель, хром и молибден. Для многих низколегированных сталей главная функция легирующих элементов заключается в увеличении прокаливаемости стали, чтобы оптимизировать затем прочностные и вязкие свойства средствами термической обработки. В некоторых случаях, однако, легирующие элементы применяют для того, чтобы повысить сопротивление стали каким-либо специфическим воздействиям.
Низколегированные стали , в свою очередь, разделяют:
- по химическому составу на базе основных легирующих элементов: никелевые, хромоникелевые, молибденовые, хромомолибденовые и тому подобные стали;
- по термической обработке: закаленные и отпущенные (мартенситные), нормализованные и отпущенные, отожженные и так далее;
- по свариваемости.
Стали могут иметь огромное разнообразие химических составов и, кроме того, одни и те же стали могут получать различные термические обработки. Поэтому существуют определенные «нахлесты» в той классификации низколегированных сталей, которая представлена выше.
По этой причине низколегированные стали чаще делят на четыре больших группы, такие как:
- низколегированные мартенситные (улучшаемые) стали;
- среднеуглеродистые высокопрочные стали;
- шарикоподшипниковые стали;
- теплостойкие хромомолибденовые стали.
Низколегированные мартенситные стали
Низколегированные мартенситные стали характеризуются относительно высокой прочностью с минимальным пределом текучести 690 МПа и хорошей ударной вязкостью и пластичностью, коррозионной стойкостью и свариваемостью. Их также называют низколегированными улучшаемыми сталями, имея в виду улучшение термической обработкой. Из этих сталей изготавливают плиты, листы, прутки, профили и кованые изделия. Они широко применяются для изготовления сосудов под давлением, землеройного и шахтного оборудования, а также ответственных элементов больших стальных конструкций.
Среднеуглеродистые высокопрочные стали
Среднеуглеродистые высокопрочные стали являются конструкционными и имеют очень высокую прочность. Минимальный предел текучести сталей этого класса достигает 1380 МПа.
ГОСТ 4543-71 разбивает эти сплавы на пять групп – по возрастанию степени легирования. По мере увеличения степени легирования возрастает размер сечения изделия, на котором может быть достигнута сквозная прокаливаемость. Самые прочные стали из пятой группы легируются 1,2-1,5 % хрома; 3,0-3,4 % никеля; 0,35-0,45 % молибдена и 0,1-0,2 % ванадия.
Примером такой стали может служить хромомолибденовая сталь 30ХМ из третьей группы по ГОСТ 4543-71 (аналог знаменитой стали 4130, из которой за рубежом делают велосипедные рамы). Минимальные предел текучести стали 30ХМ составляет 735 МПа, минимальный предел прочности – 930 МПа, а минимальная ударная вязкость KCU – 78 Дж/см2.
Шарикоподшипниковые стали
Шарикоподшипниковые стали должны обладать высокой твердостью. Поэтому они обычно имеют содержание углерода около 1 %. Для хорошей прокаливаемости при закалке в масле эти стали имеют от 0,4 дл 1,65 % хрома. Иногда применяют низколегированную подшипниковую сталь (0,10-0,20 % углерода). В этом случае высокой твердости поверхности добиваются цементованием.
Хромомолибденовые теплостойкие стали
Хромомолибденовые теплостойкие стали содержат 0,5-9 % хрома, 0,5-1,0 % молибдена и обычно менее 0,20 % углерода. Их подвергают различным термическим обработкам: нормализации с отпуском, закалке с отпуском или отжигу. Эти стали применяют в нефтегазовом оборудовании, химической промышленности, оборудовании обычных и атомных электростанций для изготовления труб, теплообменников и сосудов высокого давления.
Источники:Steel Heat Treatment: Metallurgy and Technologies, ed. G. E. Totten, 2006Гуляев А. П. Металловедение, 1986.
steel-guide.ru
Легированная сталь
Легированные стали используют для изготовления тяжелонагруженных деталей ответственного назначения, так как они обладают значительно более высокими механическими характеристиками. При легировании у стали можно получать заданные свойства, в том числе отсутствующие у углеродистых сталей (например, коррозионную стойкость, жаропрочность).
Легированные стали обладают более глубокой прокаливаемостью деталей тех же размеров, чем из углеродистых сталей. Многие их марки прокаливаются насквозь даже при больших сечениях деталей. Чем больше в стали легирующих элементов (до определенной концентрации), тем выше ее прокаливаемость. Большинство легирующих элементов снижают температуру мартенситного превращения и улучшают качество остаточного аустенита в структуре.
В зависимости от суммарного содержания легирующих элементов стали делятся на низколегированные (содержание легирующих элементов до 2.5%), среднелегированные (от 2.5 до 10%) и высоколегированные (свыше 10%).
В легированных сталях Fe должно быть не менее 50%, при меньшем количестве Fe получаются сплавы с особыми свойствами. Стали считаются легированными, если они содержат Si более 0.8% и Mn более 1%.
По назначению легированные стали делятся на конструкционные, инструментальные, стали и сплавы с особыми свойствами.
В конструкционные легированные стали для улучшения их служебных свойств вводят такие химические элементы, как Cr, Ni, W, Mo, V, B и другие, а также Mn и Si в количествах, превышающих их обычное содержание в углеродистых сталях.
ГОСТом предусмотрены следующие буквенные обозначения легирующих элементов, входящих в состав сталей: Mn – Г, Si – С, Cr- Х, Ni - Н, Mo - М, W- В, V- Ф, Al - Ю, Ti - Т, B - Р, Cu - Д, Nb - Б. Эти буквы, сочетаясь с цифрами, указывают на состав легированной стали, например: 45Х, 12ХН3А, ХВ5, 9ХС. Цифры, стоящие перед буквами, указывают на содержание углерода в сотых долях процента, - если две цифры и в десятых долях процента, - если одна цифра. Отсутствие впереди букв цифр означает, что сталь содержит углерода 1% и больше. Цифры, стоящие за буквами, указывают на среднее содержание данного легирующего элемента в процентах. Отсутствие за буквой цифры означает, что данного элемента содержится до 1%. Стоящая в конце маркировки буква А свидетельствует о высококачественной стали, с пониженным содержанием S и P (менее0.02% каждого). Например, марка 12Х2Н4А обозначает, что это хромоникелевая высококачественная сталь с содержанием углерода 0.12%, Cr – 2%, Ni – 4%.
Из 90 стандартных марок конструкционных легированных сталей большинство являются среднеуглеродистыми (0.25-0.45% углерода). Используют их после улучшения свойств путем закалки и отпуска, поэтому называют улучшенными. Наиболее распространенные среди них являются стали: хромистые (30Х, 38Х, 40Х, 45Х, 50Х), марганцевые (30Г, 35Г, 40Г, 45Г, 35Г2, 40Г2), кремнистые (55С2, 60С2), хромоникелевые (30ХН3А, 40ХН, 45ХН), хромокремнистые (33ХС, 38ХС), хромомарганцевые (35ХГ2, 4ХГ), хромомарганцевокремнистые (30ХГС, 30ХГСА, 35ХГСА). Эти стали используются в производстве нагруженных и сильнонагруженных деталей машин.
Конструкционные легированные стали в сравнении с углеродистыми обладают более высокими вязкостно-прочностными свойствами. Это объясняется тем, что: 1) все они (кроме марганцевых сталей) имеют мелкозернистую структуру; 2) глубже прокаливаются; 3) закаливаются не в воде, а в масле (а некоторые на воздухе), благодаря чему у них образуется очень малые закалочные напряжения, и поэтому они имеют более высокие пластичность и вязкость; 4) при их отпуске требуется более высокая температура и время выдержки, чем для углеродистых сталей, вследствие чего в них полнее снимаются закалочные напряжения и вязкость оказывается выше.
Инструментальные легированные стали применяют для изготовления мерительного, режущего и ударно-штамповочного инструментов. Эти стали должны быть твердыми и износостойкими, сохранять геометрические размеры в течение длительного времени. Указанные свойства достигаются в результате относительно высокого содержания углерода (0.8-1.0%) и при наличии карбидообразующих элементов, главным образом Cr. Образующаяся у них после закалки и низкого отпуска структура обеспечивает высокие режущие свойства инструмента.
Наиболее часто для изготовления режущего инструмента используют следующие марки легированной инструментальной стали: Х (для резцов), 9ХС и ХВСГ (для сверл, разверток, метчиков, плашек, фрез). В маркировке этих сталей содержание углерода указывается в десятых долях процента. Отсутствие цифры указывает на содержание углерода в количестве около 1%. Отсутствие цифры после символов таких элементов, как Cr, Si, W, означает, что их содержание может достигать до 1.5%.
Высоколегированные инструментальные стали, содержащие до 1% углерода и до 25% W, Cr, V, способны сохранять высокую твердость и резать металл при разогреве режущей кромки инструмента до 580-650 ° С. Благодаря этим качеством они обеспечивают высокую скорость резания при точении, сверлении, фрезеровании и называются быстрорежущими сталями. Например, в стали марки Р18 - буквой Р обозначают быстрорежущую сталь.
Еще более высокой твердостью и режущей способностью обладают твердосплавные пластины, которыми оснащают режущий инструмент. Они превосходят быстрорежущую сталь по скорости резания и теплостойкости, которая достигает 900-1000° С . Пластины получают методом спекания при температуре 1500° С. Изготавливают их из порошков карбидов вольфрама, титана, тантала и кобальта; кобальт используют в качестве пластичной связки.
Коррозионностойкими ( нержавеющими) называют стали стойкие к действию химической и электрохимической коррозии, т.е. обладающие стойкостью к разрушающему воздействию атмосферных условий, речной и морской воды, растворов солей, кислот и щелочей. Основным легирующим элементом всех марок нержавеющих сталей является Cr. На металлическом изделии при содержании Cr не менее 12% образуется тонкая сплошная плотная пленка окисла хрома Cr2O3, которая и предохраняет сталь от коррозии. Стойкость к коррозии хромистых сталей повышается при введении в их состав Ni. Поэтому различают нержавеющие стали хромистые и хромоникелевые. Например, хромистые стали ОХ13, 12Х13, 40Х13 и хромоникелевые стали Х18Н10, ОХ18Н10, ООХ18Н10. В маркировке «О» указывает, что содержание углерода не должно превышать 0.08%, «ОО» - не более 0.04%. Стали марок Х17, ОХ17Т, Х28 используют для изготовления оборудования предприятий химической и пищевой промышленности. Хромоникелевые стали марок ОХ18Н10 и ОХ18Н9 применяют для изготовления деталей сваркой; они работают в особо агрессивной среде.
Для защиты металла от коррозии используют также оксидирование и фосфатирование, цинкование, хромирование, кадмирование и др.
Сплавы
Окружающие нас металлические предметы редко состоят из чистых металлов. Только алюминиевые кастрюли или медная проволока имеют чистоту около 99,9%. В большинстве же других случаев люди имеют дело со сплавами. Сплавы - это системы, состоящие из двух или нескольких металлов, а также из металлов и неметаллов, обладающие свойствами, присущи металлическому состоянию. Так, различные виды железа и стали содержат наряду с металлическими добавками незначительные количества углерода, которые оказывают решающее влияние на механическое и термическое поведение сплавов. Все сплавы имеют специальную маркировку, т.к. сплавы с одним названием (например, латунь) могут иметь разные массовые доли других металлов.
Для изготовления сплавов применяют различные металлы. Самое большое значение среди всех сплавов имеют стали различных составов. Простые конструкционные стали состоят из железа относительно высокой чистоты с небольшими (0,07—0,5%) добавками углерода. Так, чугун, получаемый в доменной печи, содержит около 10% других металлов, из них примерно 3% составляет углерод, а остальные — кремний, марганец, сера и фосфор. А легированные стали получают, добавляя к железу кремний, медь, марганец, никель, хром, вольфрам, ванадий и молибден.
Никель наряду с хромом является важнейшим компонентом многих сплавов. Он придает сталям высокую химическую стойкость и механическую прочность. Так, известная нержавеющая сталь содержит в среднем 18% хрома и 8% никеля. Для производства химической аппаратуры, сопел самолетов, космических ракет и спутников требуются сплавы, которые устойчивы при температурах выше 1000 °С, то есть не разрушаются кислородом и горючими газами и обладают при этом прочностью лучших сталей. Этим условиям удовлетворяют сплавы с высоким содержанием никеля. Большую группу составляют медно-никелевые сплавы.
Сплав мельхиор содержит от 18 до 33% никеля (остальное медь). Он имеет красивый внешний вид. Из мельхиора изготавливают посуду и украшения, чеканят монеты («серебро»). Похожий на мельхиор сплав - нейзильбер -содержит, кроме 15% никеля, до 20% цинка. Этот сплав используют для изготовления художественных изделий, медицинского инструмента. Медно-никелевые сплавы константан (40% никеля) и манганин (сплав меди, никеля и марганца) обладают очень высоким электрическим сопротивлением. Их используют в производстве электроизмерительных приборов. Характерная особенность всех медно-никелевых сплавов - их высокая стойкость к процессам коррозии - они почти не подвергаются разрушению даже в морской воде. Латуни благодаря своим качествам нашли широкое применение в машиностроении, химической промышленности, в производстве бытовых товаров. Для придания латуням особых свойств в них часто добавляют алюминий, никель, кремний, марганец и другие металлы. Из латуней изготавливают трубы для радиаторов автомашин, трубопроводы, патронные гильзы, памятные медали, а также части технологических аппаратов для получения различных веществ.
Для деталей машин используют сплавы меди с цинком, оловом, алюминием, кремнием и др. (а не чистую медь) из-за их большей прочности: 30-40 кгс/мм2 у сплавов и 25-29 кгс/мм2 у технически чистой меди.
Медные сплавы (кроме бериллиевой бронзы и некоторых алюминиевых бронз) не принимают термической обработки, и их механические свойства и износостойкость определяются химическим составом и его влиянием на структуру. Модуль упругости медных сплавов (900-12000 кгс/мм2 ниже, чем у стали).
Основное преимущество медных сплавов - низкий коэффициент трения (что делает особенно рациональным применением их в парах скольжения), сочетающийся для многих сплавов с высокой пластичностью и хорошей стойкостью против коррозии в ряде агрессивных сред и хорошей электропроводностью.
Марки обозначаются следующим образом.
Первые буквы в марке означают: Л - латунь и Бр. - бронза. Буквы, следующие за буквой Л в латуни или Бр. В бронзе, означают: А - алюминий, Б - бериллий, Ж - железо, К - кремний, Мц - марганец, Н - никель, О - олово, С - свинец, Ц - цинк, Ф. - фосфор. Цифры, помещенные после буквы, указывают среднее процентное содержание элементов. Порядок расположения цифр, принятый для латуней, отличается от порядка, принятого для бронз.
В марках латуни первые две цифры (после буквы) указывают на содержание основного компонента - меди. Остальные цифры, отделяемые друг от друга через тире, указывают среднее содержание легирующих элементов.
Эти цифры расположены в том же порядке, как и буквы, указывающие присутствие в сплаве того или иного элемента. Таким образом, содержание цинка в наименовании марки латуни не указывается и определяется по разности. Например, Л86 означает латунь с 68% Cu (в среднем) и не имеющую других легирующих элементов, кроме цинка; его содержание составляет (по разности) 32%. ЛАЖ 60-1-1 означает латунь с 60% Cu , легированную алюминием (А) в количестве 1% , с железом (Ж) в количестве 3% и марганцем (Мц) в количестве 1%. Содержание цинка (в среднем) определяется вычетом из 100% суммы процентов содержания меди, алюминия, железа и марганца.
В марках бронзы (как и в сталях) содержание основного компонента - меди - не указывается, а определяется по разности. Цифры после букв, отделяемые друг от друга через тире, указывают среднее содержание легирующих элементов; цифры расположенные в том же порядке, как и буквы, указывающие на легирование бронзы тем или иным компонентом. Например, Бр.ОЦ10-2 означает бронзу с содержанием олова (О) ~ 4% и цинка (Ц) ~ 3%.Содержание меди определяется по разности (из 100%). Бр.АЖНЮ-4-4 означает бронзу с 10% Al , 4% Fe и 4% Ni (и 82% Cu). Бр. КМц3-1 означает бронзу с 3% Si , и 1% Mn (и 96% Cu).
studfiles.net
Легированные стали
Легированными называют стали, в которые вводятся специальные легирующие элементы, способные улучшать механические, технологические, эксплуатационные свойства, а в некоторых случаях придавать стали особые физические или химические свойства.
Легирующие элементы могут растворяться в феррите, аустените., цементите, образовывать специальные карбиды (карбиды легирующих элементов в отличии от карбида железа) или интерметаллидные соединения с железом и между собой, например, FeCr, FeV и т.д.
Растворяясь в аустените или феррите, легирующие элементы упрочняют эти фазы, делают их более устойчивыми против распада при нагреве и охлаждении, изменяя температуры фазовых превращений и структуру сталей.
Структура легированных сталей в нормализованном состоянии
Легированные стали в зависимости от структуры, получаемой после нагрева до 900°С и охлаждения на воздухе (т.е. после нормализации), подразделяются на пять классов;
1. перлитный;2. мартенситный;3. аустенитный;4. ферритный;5. карбидный,
По мере увеличения содержания легирующих элементов устойчивость аустенита в интервале температур перлитного превращения возрастает, а температурная область мартенситного превращения понижается. Это схематично отражено на диаграмме распада аустенита (рис.1)
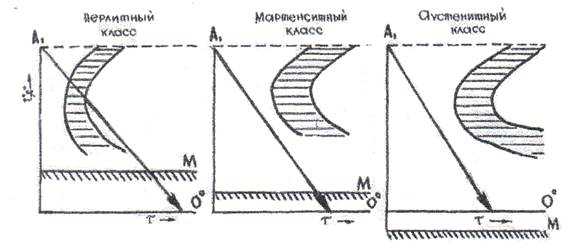
Рис.1. Диаграмма изотермического распада аустенита для сталей трёх классов (схема).
В зависимости от содержания легирующих элементов и углерода при заданной скорости охлаждения (на воздухе) можно получить разную структуру.Стали перлитного класса характеризуются небольшим содержанием легирующих элементов (менее 5...7%). Для них, как и для углеродистых сталей, кривая скорости охлаждения при нормализации будет пересекать С-кривые перлитного распада. Следовательно, будут получаться структуры перлитного типа: перлит, сорбит, тростит.Стали мартенситного класса содержат большее количество легирующих элементов (обычно 7... 15 %). В присутствии никеля, даже при общем количестве легирующих элементов около 5 %, сталь может относиться к мартенситному классу. Содержание углерода в сталях мартенситного класса обычно не превышает 055 %, Область перлитного распада в этих сталях сдвинута вправо, поэтому охлаждение на воздухе приводит к переохлаждению аустенита до температур мартенситного превращения, где и происходит образование мартенсита.
Стали аустенитного класса содержат более 15 % легирующих элементов, в том числе не менее 8 % никеля или около 13 % марганца. В большинстве этих сталей содержание углерода не превышает 0,2 %. Легирующие элементы (особенно никель), растворяясь в аустените, очень сильно повышают его устойчивость. При этом не только сдвигается вправо область перлитного распада, но и точка начала мартенситного превращения снижается в область отрицательных температур. В результате сталь, охлажденная на воздухе до комнатной температуры, сохраняет аустенитную структуру.
Стали ферритного класса содержат от 17 до 30 % хрома или не менее 2,5% кремния. Это малоуглеродистые стали, в которых процент углерода не превышает 0,2. Растворяясь в феррите, хром очень сильно повышает его устойчивость. Такие стали практически не имеют фазовых превращений при нагреве вплоть до плавления, то есть сохраняют ферритную структуру во всех интервалах температур.
К сталям карбидного (ледебуритного) класса относятся высокоуглеродистые (более 0,7 % С), легированные большим количеством карбидообразующих элементов, преимущественно вольфрамом, ванадием, молибденом, хромом. Легирующие элементы образуют с углеродом большое количество специальных карбидов. Уже в процессе кристаллизации стали образуются карбиды, входящие в состав эвтектики, напоминающей ледебурит. При охлаждении на в сталях карбидного класса, подобно сталям мартенситного класса, основа структуры получается мартенситной.
Микроструктура сталей различных классов в нормализованном состоянии показана на рис.2.
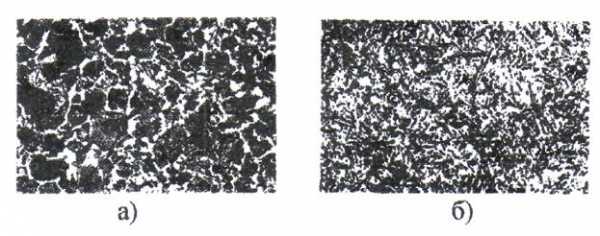
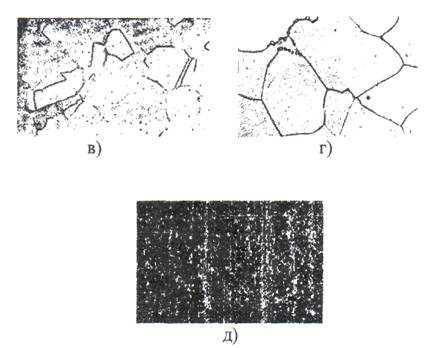
Риc.2. Микроструктуры сталей различных классов в нормализованном состоянии, увеличение 100:
а) перлит и феррит;б) мартенсит игольчатый;в) аустенит;г) феррит;д) бесструктурный мартенсит и карбиды.
Рассмотренная классификация легированных сталей условна и относится к случаю охлаждения на воздухе образцов небольших сечений. Меняя условия охлаждения можно в одной и той же стали получать различные структуры и свойства.
Свойства и применение легированных сталей
По назначению легированные стали разделяются на конструкционные, инструментальные и стали с особыми свойствами.
Стали перлитного класса с различным содержанием углерода нашли широкое применение как конструкционные материалы для изготовления различных конструкций и деталей машин. Для изготовления конструкций применяют преимущественно низколегированные стали с невысоким содержанием углерода, что обеспечивает им хорошую свариваемость.
Стали предназначенные для изготовления деталей машин и приборов, разделяют в зависимости от применяемой к ним термообработки на цементуемые (содержат не более 0,25 %С) и улучшаемые (0.25... 0,5%С). Детали из цементуемых сталей подвергают цементации, закалке и низкому отпуску. В результате получается твёрдая, износостойкая поверхность (HRC 56... 62), со структурой высокоуглеродистого мартенсита и более мягкая, вязкая сердцевина (НЕС 15...45) со структурой малоуглеродистого мартенсита.
Детали из улучшаемых сталей подвергают закалке в масле и высокому отпуску. Такая термообработка называется улучшением. Закалка даёт мартенситную структуру. Мартенсит при высоком отпуске распадается на сорбит., сочетающий достаточную прочность с повышенной вязкостью. Такие детали хорошо работают в условиях динамических нагрузок.
Стали, легированные кремнием, марганцем и некоторыми другими элементами и содержащие 0,5...0,65 %С, используются для изготовления пружин и рессор. Они подвергаются закалке и среднему отпуску на тростит, который обеспечивает хорошую упругость и прочность.
К перлитному классу принадлежат и шарикоподшипниковые стали. Это высокоуглеродистые стали, легированные небольшим количеством хрома (не более 1,5 %). Закалка и низкий отпуск обеспечивают им мартенситную структуру, прочность и износостойкость.
Кроме деталей машин из легированных сталей перлитного класса с высоким содержанием углерода (более 0,8 %) изготавливают режущий и мерительный инструмент. Такой инструмент подвергается неполной закалке и низкому отпуску. Приобретая высокую твёрдость и износостойкость, инструмент, однако, не обладает достаточной теплостойкостью. Некоторые марки перлитных сталей используют для изготовления инструмента для горячего деформирования. Пониженное по сравнению с другими инструментальными сталями содержание углерода (от 0,3 до 0,7%) позволяет получить достаточную вязкость, т.к. такой инструмент часто работает с ударными нагрузками.
Легирующие элементы в сталях перлитного класса не оказывают существенного влияния на структуру. В основном они способствуют увеличению прокаливаемости и тем самым дают возможность получить высокие механические свойства в деталях больших сечений.
Среди сталей мартенситного класса широкое применение находят стали, содержащие около 13 % хрома и до 0,4 % углерода. При содержании хрома более 12,5 % сталь становится коррозионностойкой. Стали этой группы хорошо сопротивляются атмосферной коррозии и коррозии в среде водяного пара, т.е. являются нержавеющими из них изготавливают различные детали машин, требующие повышенной прочности и коррозионной стойкости, а также некоторые виды инструмента. Упрочнение достигается закалкой в масле или на воздухе на структуру мартенсита. Отпуск в зависимости от назначения может быть высоким (для деталей машин) или низким (для инструмента).
Набольшее применение среди сталей аустенитного класса находят хромоникелевые стали, содержащие около 18 % хрома и 8.., 10 % никеля (углерода не более 0,2 %). Эти стали имеют более высокую коррозионную стойкость, чем хромистые стали мартенситного класса. В нормализованном состоянии эти стали имеют структуру, состоящую из аустенита и небольшого количества карбидов типа (FeCr)23C6. При нагреве под закалку (так называемая аустенизацня) карбиды растворяются в аустените, и при резком охлаждении в воде фиксируется однофазная аустенитная структура. Однофазные структуры характеризуются более высокой коррозионной стойкостью, т.к. в этом случае уменьшается вероятность образования микрогальванических пар, вызывающих электрохимическую коррозию. Закалка аустенитных сталей не является упрочняющей операцией.
Аустенитные стали используются как кислотостойкие для изготовления химической аппаратуры, а также для деталей машин и криогенного оборудования, работающего при температурах до -253 С. Стали этого класса могут использоваться и как жаростойкие, жаропрочные материалы.
Наиболее известными сталями ферритного класса являются высокохромистые стали, содержащие 17...30 % хрома и не более 0,2 % углерода. Они хорошо сопротивляются как электрохимической так и газовой коррозии при высоких температурах, т.е. являются кислотостойкими и жаростойкими (окалиностойкими). Недостатком этих сталей является низкая прочность и возникающая при перегреве (например, при сварке) крупнозернистость, которая не устраняется термической обработкой, Крупнозернистость придаёт сталям повышенную хрупкость. Используются эти стали преимущественно в отожженном состоянии.
Рассмотренные стали мартенситного, аустенитного и ферритного класса относятся с особыми свойствами.
Стали карбидного класса по назначению являются инструментальными. Они отличаются повышенной износостойкостью и теплостойкость (красностойкостью). Благодаря этому их используют для изготовления режущего инструмента, работающего при высоких скоростях резания. Наилучшие режущие свойства стали приобретают после сложной термической обработки. Отожженные заготовки имеют структуру сорбитообразного перлита и карбидов. После механической обработки заготовок и придания инструменту необходимой формы он подвергается закалке и трёхкратному отпуску. Схема режимов термической обработки приведена.
С целью выравнивания температуры по всему сечению инструмента и в избежании его деформации производится подогрев до температуры около 800°С, а затем окончательный нагрев в расплавах солей до температур 1260... 1290 °С (для стали Р18). Высокие температуры закалки необходимы для более полного растворения карбидов и получения при нагреве высоколегированного аустенита. Это обеспечивает получение после закалки в масле (или на воздухе) высоколегированного мартенсита, обладающего высокой устойчивостью против отпуска, т.е. теплостойкостью. Часть карбидов, не растворившихся при нагреве, препятствуют росту зерна аустенита.
В процессе охлаждения часть аустенита превращается в мартенсит. Кроме того в структуре сохраняются не растворенные карбиды и некоторое количество остаточного аустенита, т.к. точка Мк лежит ниже нуля градусов и мартенситное превращение не заканчивается. Остаточный аустенит понижает твёрдость и режущие свойства, поэтому его присутствие в структуре недопустимо.
После закалки следует отпуск при температуре около 560 °С, при котором происходит превращение остаточного аустенита в мартенсит с выделением дополнительного количества дисперсных карбидов. Это сопровождается увеличением твёрдости. Чтобы весь остаточный аустенит превратился в мартенсит, отпуск проводят 3 раза подряд с выдержкой по одному часу. Для инструмента простой формы можно делать после закалки обработку холодом и однократный отпуск при 560°С.
Твёрдость стали после закалки составляет HRC 62...63, а после трёхкратного отпуска HRC 64...65. Высокая твёрдость сохраняется при последующих нагревах в процессе работы до температур до 600 "С, что обеспечивает теплостойкость инструмента.
Также по теме:
Про дюралюмины. Состав и применение сплавов на основе Al-Cu-Mg.
Дилатометрия. Дилатометрические кривые.
svarder.ru
Свойства легированной стали.
Поиск ЛекцийХарактеристика легированных сталей
Легированная сталь представляет собой сталь, которая кроме обычных примесей оснащена еще и дополнительными добавочными веществами, которые необходимы для того, чтобы она соответствовала тем или иным химическим и физическим требованиям.
Обычная сталь состоит из железа, углерода и примесей, без которых невозможно себе представить данный материал. В легированную сталь добавляются дополнительные вещества, которые получили название легирующих. Они используются для того, чтобы сталь стала обладать такими свойствами, которые необходимы в тех или иных ситуациях.
Начало формы
Конец формы
В большинстве случаев в качестве легирующих элементов к железу, примесям и углероду добавляются: никель, ниобий, хром, марганец, кремний, ванадий, вольфрам, азот, медь, кобальт. Также не редко в таком материале отмечаются такие вещества, как молибден и алюминий. Для придания прочности материалу в большинстве случаев добавляется титан.
Такой вид стали имеет три основные категории. Отношение легированной стали к той или иной группе обусловлено тем, сколько в ней содержится стали и примесей, а также легированных добавок.
Виды легированной стали
Есть три основных вида стали с легирующими элементами:
- Низколегированная сталь.
Она характеризуется тем, что в ней содержится около двух с половиной процентов легирующих дополнительных элементов.
- Среднелегированная сталь.
Данный материал имеет в своем составе от 2.5 до 10 процентов легирующих дополнительных веществ.
- Высоколегированная сталь.
К данному виду относятся стальные материалы, количество легирующих добавок в которых превышает десяти процентов. Количество этих компонентов в такой стали может
достигать пятидесяти процентов.
Назначение легированной стали
Легированную сталь широко применяют в современной промышленности. Она обладает высоким уровнем прочности, что позволяет изготовлять из нее оборудование для резки и рубки металлического проката самых разных видов.
По своему назначению стали легированного типа могут быть представлены большим количеством групп.
Основными из них являются:
- конструкционная легированная сталь,
- инструментальная легированная сталь,
- легированная сталь с особыми химическими и физическими свойствами.
Характеристики легированных сталей могут быть разнообразными. Они их приобретают благодаря соотношению основных элементов. Стали такого типа являются в любом случае более прочными и устойчивыми к образованию коррозии.
Свойства легированной стали.
Свойства легированных сталей являются разнообразными. Они главным образом определяются теми добавками, которые применяются в качестве легирующих при производстве отдельных видов стальных материалов.
В зависимости от добавленных легирующих компонентов сталь приобретает следующие качества:
- Прочность. Данное свойство приобретает после добавления в ее состав хрома, марганца, титана, вольфрама.
- Устойчивость к образованию коррозии. Это качество появляется под воздействием хрома, молибден.
- Твердость. Сталь становится боле твердой благодаря хрому, марганцу и другим элементам.
Внимание: Стоит отметить, что для того, чтобы легированная сталь была более прочной и устойчивой к внешнему влиянию окружающей среды необходимое содержание хрома не должно быть менее двенадцати процентов.
Сталь легированного типа при правильном процентном соотношении всех входящий в нее элементов не должна менять свои качестве при температуре нагревания до шестисот градусов Цельсия.
poisk-ru.ru
Легированная сталь
Легированная сталь или специальная сталь - сталь, содержащая добавки других металлов с целью придания ей тех или иных свойств. Как легирующие элементы чаще всего применяют хром, никель, марганец, кремний, вольфрам, молибден и ванадий, значительно реже - кобальт, титан, бериллий и другие металлы. В большинстве случаев легирующие элементы добавляются в незначительных количествах - десятые доли процента, но некоторые из них - от нескольких до 10-15% и даже больше. Названия легированных сталей происходят от названий легирующих элементов.
По степени легирования стали разделяют на низколегированные с содержанием легирующих элементов до 2,5%, среднелегированные - 2,5-10% и высоколегированные, где содержание легирующих элементов превышает 10%.
1. Цель легирования
Главная цель легирования подавляющего большинства сталей - повышение прочности за счет растворения легирующих элементов в феррите и аустените, образования карбидов и увеличения прогартовуваности. Кроме того, легирующие элементы могут повышать устойчивость против коррозии, теплостойкость, жаростойкость (окалиностийкисть), жаропрочность и т.д.. Такие элементы как хром, марганец, молибден, вольфрам, ванадий, титан образуют карбиды, а никель, кремний, медь, алюминий карбидов не образуют. Марганец и никель снижают критические точки А 1 и А 3, а остальные - повышают. Кроме того, легирующие элементы уменьшают критическую скорость охлаждения при закалке, что необходимо учитывать при назначении режимов закалки (температуры нагрева и среды для охлаждения). При значительном количестве легирующих элементов может существенно измениться структура, что приводит к образованию новых структурных классов по сравнению с углеродистыми сталями.
2. Влияние легирующих элементов на свойства стали
- Все легирующие элементы повышают прочность.
- Легирующие элементы, которые образуют карбиды, измельчают зерно при кристаллизации.
- Коррозионной стойкости, жаростойкости (окалиностийкости), жаропрочности, теплостойкости легирующие элементы оказывают лишь при значительном количестве в сталях (хром 8-13%, никель 8-12%, вольфрам, молибден более 5%).
- Отдельные химические элементы:
3. Маркировка легированных сталей
Легированные стали маркируют с помощью букв и цифр. Легирующие элементы обозначаются буквами: Н - никель, Х - хром, К - кобальт, М - молибден, Г - марганец, Д - медь, Р - бор, Б - ниобий, С - кремний, В - вольфрам, Т - титан, Ф - ванадий, П - фосфор, А - азот.
Первые две или три цифры в начале маркировки показывают среднее содержание углерода в сотых долях процента, а если одна цифра - то в десятых долях. Цифры, стоящие после букв, указывают на среднее содержание легирующего элемента сказывается этой буквой в процентах. Если углерода или легирующего элемента содержится около 1%, то цифры не относятся. Буква А в конце маркировки обозначает, что данная сталь относится к высококачественным.
Например:
- сталь 35Х2ГСА имеет 0,35% углерода, 2% хрома, 1% марганца, 1% кремния. А - означает, что эта сталь высококачественная;
- сталь 110Г13 содержит 1,10% углерода, 13% марганца;
- сталь ХВ5 имеет 1% углерода, 1% хрома, 5% вольфрама;
- сталь 9ХС содержит 0,9% углерода, 1% хрома, 1% кремния.
В высокоуглеродистых инструментальных сталях цифры, которые показывают содержание углерода, вообще упускаются, например марка Х12М означает сталь с содержанием 1,5 ... 1,7% С, 12% хрома и 0,5% молибдена. Некоторые легированные стали выделены в отдельные группы и обозначаются буквами: Ш - шарикоподшипниковые, Р - быстрорежущие, Е - для постоянных магнитов.
4. Классификация легированных сталей
4.1. По структуре в состоянии отжига
- доэвтектоидной, с легированным ферритом и евтектоидом в структуре: стали 20ХНЗА; 18ХГТ; 40Х.
- эвтектоидная, со структурой лишь евтектоиду: сталь 80Х.
- заэвтектоидные, с евтектоидом и вторичными карбидами в структуре: стали 9ХС, ШХ15, ХВГ.
- ледебуритного (карбидные): со структурой евтектоиду, эвтектических (первичных) и вторичных карбидов: стали Р18, Р14Ф4, Х12М.
- аустенитные - структура легированный аустенит: стали 110Г13, 12Х18Н10Т.
- ферритных - структура легированный феррит: стали 10Х17, 10х25.
4.2. По назначению
По назначению легированные стали подразделяются на конструкционные, инструментальные и стали с особыми свойствами.
- Конструкционные - применяют для изготовления деталей машин, при этом в этих сталях содержится хрома, марганца, кремния до 2%, никеля до 4%. Примеры конструкционных сталей:
- Инструментальные стали применяют для различного инструмента. Они должны иметь высокую твердость и износостойкость.
Стали для инструмента:
Низкой теплостойкости (до 250 ? C): ХГ, 9ХС, ХВГ, ХВСГ. Повышенной до 600 ? C теплостойкости ( быстрорежущие): Р9, Р6М5, Р9К5, Р14Ф4.Стали для измерительного инструмента. Эти стали должны иметь высокую твердость, износостойкость и сохранять постоянство размеров. Для изготовления плиток, калибров, шаблонов применяют высокоуглеродистые хромистые стали, например, ХВГ, ХВ5. Чаще всего такие стали после закалки обрабатывают холодом (для полного превращения остаточного аустенита в мартенсит).
Стали для штампов:
Холодного деформирования средних размеров: 9ХС, Х6ВФ. Холодного деформирования разных размеров, особенно высокоточных: Х12М, Х12Ф. Горячего деформирования средних размеров: 5ХНТ, 5ХНВ. Горячего деформирования больших размеров тяжелонагруженных: 4Х2В5МФ, 5Х3В3МФС.- Специальные стали (стали с особыми свойствами) применяют для работы в агрессивных средах, при высоких температурах, ударных нагрузках и т.д..
Коррозионно-стойкие стали имеют высокую коррозионную стойкость в химически активных газовых и жидких средах. Это достигается за счет большого содержания хрома (более 13%). Титан вводят в сталь для предотвращения межкристаллитной коррозии. Коррозионно-стойкие стали подразделяются на:
Хромистые 10х13, 40Х13, 10х25 (ферритной). Хромоникелевые (аустенитные): 12Х18Н9, 10Х18Н10Т.Жаростойкие и жаропрочные стали обладают способностью стали сопротивляться газовой коррозии при повышенных температурах и сохранять достаточную прочность при высоких температурах.
Жаростойкость обеспечивается легированием сталей хромом, кремнием и алюминием, которые образуют защитные пленки (Fe, Cr) 2 О 3, SiO 2, Al 2 O 3. К жаростойких сталей относятся легированные стали 25Х6С10, 40Х9С2, 15Х25Т, 12Х18Н10Т.
Жаропрочность достигается легированием тугоплавкими химическими элементами (хром, никель, молибден). Как правило, жаропрочные стали имеют и жаростойкость. Это стали 15Х2МФС, 15Х11МФ, 40Х10С2М, 10Х18Н10Т, 40Х15Н7Г7Ф2МС.
Износостойкая (аустенитная) сталь 110Г13Л ( сталь Гадфильда) используется для изготовления деталей, работающих в условиях абразивного трения и высокого давления и ударов (например, траки гусеничных машин, детали дробилок, крестовины железнодорожных и трамвайных путей, черпаки землеройных машин). Характерная особенность марганцевого аустенита - способность сильно наклепуватись и превращаться в мартенсит, что приводит к повышению твердости и сопротивления износа.
5. Примеры использования
Примером высоколегированных сталей может служить вольфрамо-хромо-ванадиевая сталь с содержанием 18% W, 4% Cr и 1% V. Эту сталь называют швидкоpизальною, поскольку из нее производят режущие инструменты. Особенностью этой стали является то, что она не теряет своей твердости и прочности даже при 600 ? C.
Хромо-никелевая сталь с содержанием 18% Cr и 8% Ni в атмосфере воздуха не поддается коррозии. Эту сталь называют нержавеющей. Из нее делают нержавеющие ножи, ложки, вилки и т.д..
Знание химического состава, структуры и влияния легирующих элементов позволяет объективно оценить эксплуатационные свойства сталей, их рациональное применение и назначить необходимую термическую обработку.
Источники
- Ф. А. Деркач "Химия" Л. 1968
- В. Попович Технология конструкционных материалов и материаловедение. Львов. 2000.
См.. также
nado.znate.ru
Легированная сталь — Мегаэнциклопедия Кирилла и Мефодия — статья
Леги́рованная сталь, углеродистая сталь, в которую специально введены легирующие элементы с целью улучшения ее эксплуатационных и технологических свойств (см. Легирование). Различают низколегированную (суммарное содержание легирующих элементов до 2, 5%), среднелегированную (2, 5-10%) и высоколегированную (свыше 10%) сталь. Легирующие элементы вводятся в сталь в различных количествах и в разных сочетаниях — по 2, по 3 и более элементов. Легированные стали используют для изготовления тяжелонагруженных деталей ответственного назначения, так как они обладают более высокими механическими характеристиками.Легированные стали могут быть классифицированы по структуре, по составу и по назначению.
По равновесной структуре стали можно классифицировать как:
а) доэвтектоидные стали, имеющие в структуре избыточный феррит. Стали ферритного класса содержат элементы, сужающие область существования аустенита; эти стали могут сохранять структуру феррита (иногда в сочетании с карбидами) при любых температурах (вплоть до расплавления) и после охлаждения с любой скоростью;б) эвтектоидные стали, имеющие перлитную структуру;
в) заэвтектоидные стали, имеющие в структуре избыточные (вторичные) карбиды;
г) ледебуритные стали, имеющие в структуре первичные карбиды. В литом виде избыточные карбиды вместе с аустенитом образуют эвтектику — ледебурит, который при ковке или прокатке разбивается на обособленные карбиды и аустенит. Стали карбидного класса содержат повышенное количество углерода и карбидообразующих элементов.Большинство легирующих элементов влияют на диаграмму состояния C – Fe. Граница между доэвтектоидными и заэвтектоидными сталями, заэвтектоидными и ледебуритными в легированных сталях лежит при меньшем содержании углерода, чем в углеродистых.
Исходя из структуры стали, получаемой после охлаждения на воздухе, можно выделить перлитный, мартенситный и аустенитный классы сталей. Стали перлитного класса имеют структуру перлита или его разновидностей: сорбита, троостита, а также перлита с ферритом или с заэвтектоидными карбидами. Стали мартенситного класса характеризуются пониженной критической скоростью закалки и имеют после нормализации структуру мартенсита. Стали аустенитного класса имеют сильно пониженную температуру распада аустенита, который сохраняется в структуре стали даже при комнатной температуре. Получение этих классов сталей обусловлено тем, что по мере увеличения содержания легирующих элементов устойчивость аустенита в перлитной области возрастает, а температурная область мартенситного превращения понижается.В зависимости от состава — наличия в стали тех или иных легирующих примесей — легированные стали классифицируются как никелевые, хромистые, хромоникелевые и т. д.
При легировании углеродистых сталей: марганец увеличивает прочность, твердость и сопротивление стали износу; кремний и хром повышают прочность и жаростойкость; медь повышает стойкость стали к атмосферной коррозии; никель способствует улучшению вязкости без снижения прочности. Низколегированные стали имеют более высокие механические свойства, чем малоуглеродистые. Стали, содержащие никель, хром и медь, высокопластичны, хорошо свариваются, их с успехом используют для сварных и клепаных конструкций промышленных и гражданских зданий, пролетных строений мостов, нефтерезервуаров, труб и др.
В отличие от маркировки углеродистых сталей буквы в марке низколегированных сталей показывают наличие в стали легирующих примесей, а цифры — их среднее содержание в процентах. Предшествующие буквам цифры показывают содержание углерода в сотых долях процента. Для маркировки стали каждому легирующему элементу присвоена определенная буква:
С — кремний, В — вольфрам, Г — марганец, Ю — алюминий, Х — хром, Д — медь, Н — никель, К — кобальт, М — молибден, Б — ниобий, Т — титан.
Первые цифры марки обозначают среднее содержание углерода (в сотых долях процента для инструментальных и нержавеющих сталей). Буквой указан легирующий элемент и последующими цифрами — его среднее содержание, например, сталь марки 3Х13 содержит 0, 3% С и 13% Сr, сталь марки 2Х17Н2 — 0, 2 % С, 17 % Сг и 2 % Ni. При содержании легирующего элемента менее 1, 5 % цифры за соответствующей буквой не ставятся, например, 1Г2С, 12ХН3А. Буква А в конце обозначения марки указывает на то, что сталь является высококачественной, буква Ш - особо высококачественной. Например, легированная конструкционная сталь марки 1Г2С содержит 0, 1 % углерода, 2 % марганца и 1 % кремния.
Большинство марок легированных сталей приобретает высокие механические характеристики только после соответствующей термической обработки, которая сопровождается фазовыми превращениями и делает структуру сталей более мелкозернистой. Легированные стали обладают более глубокой прокаливаемостью деталей тех же размеров, чем из углеродистых сталей. Большинство легирующих элементов снижают температуру мартенситного превращения и улучшают качество остаточного аустенита в структуре.
megabook.ru
Легированная сталь - это... Что такое Легированная сталь?
Легированная сталь — сталь, которая кроме обычных примесей содержит элементы, специально вводимые в определённых количествах для обеспечения требуемых физических или механических свойств. Эти элементы называются легирующими.
Легирующие добавки повышают прочность, коррозийную стойкость стали, снижают опасность хрупкого разрушения. В качестве легирующих добавок применяют хром, никель, медь, азот (в химически связанном состоянии), ванадий и др.
Легированную сталь по степени легирования разделяют на: низколегированную (легирующих элементов до 2,5 %), среднелегированную (от 2,5 до 10 %), высоколегированную (от 10 до 50 %).
Маркировка
Легированные стали маркируются цифрами и буквами, указывающими примерный состав стали. Буква показывает, какой легирующий элемент входит в состав стали.
Стоящая за буквой цифра обозначает среднее содержание элемента в процентах. Если элемента содержится менее 1 %, то цифры за буквой не ставятся. Первые две цифры указывают среднее содержание углерода в сотых долях процента, если цифра одна, то содержание углерода в десятых долях процента.
Дополнительные обозначения в начале марки:
Р — быстрорежущая; Ш — шарикоподшипниковая; А — автоматная; Э — электротехническая;и др.
Исключения:
- содержание в шарикоподшипниковых сталях хрома в десятых долях процента(например ШХ4 — Cr 0,4 %)
- в марке быстрорежущей стали, цифра после «Р» — содержание вольфрама в %, и во всех быстрорежущих сталях содержание хрома 4 %.
Буква А в середине марки стали показывает содержание азота, а в конце — сталь высококачественная.
Пример:
- сталь 18ХГТ — 0,18 %, 1 Сr, 1 Мn, около 0,1 Тi;
- сталь 38ХНЗМФА — 0,38 %, 1,2—1,5 Сr; 3 Ni, 0,3—0,4 Мо, 0,1—0,2 V;
- сталь 30ХГСА — 0,30 %, 0,8—1,1 Сr, 0,9—1,2 Мn, 0,8—1,251 Si;
- сталь 03Х13АГ19 — 0,03 %, 13 Сr, 0,2—0,3 N, 19 Мn.
См. также
Ссылки
biograf.academic.ru