Литье колоколов. Особенности технологии. Литье колоколов
Данилов монастырь - Литье колоколов
Специалисты Центра имеют богатый опыт проектирования колоколов и создания ансамблей. Он базируется на основе результатов обмеров более ста двадцати колоколов России XII-XX вв. Оформление наших колоколов отличается хорошим художественным вкусом, воспитанным в духе декоративных стилей русского колокольного литья XVI-XX вв.
Чтобы разработать новую модель колокола в соответствии с классическими правилами и по заданным характеристикам веса и ударного тона, мы по собственной методике выполняем расчеты с привлечением акустических и геометрических данных профиля, с помощью методов математического моделирования и экспериментальных данных. Затем следует этап коррекции чертежа, поверочных расчетов и финальное проектирование оснастки.
После периода сотрудничества с различными производителями было принято решение открыть свое производство, на котором бы достаточно полно выдерживалась старинная технология литья. Уже не первый год мы сами льем колокола. Знакомьтесь с их звучанием, экстерьером и описанием модельного ряда ниже на этой же странице.
Предлагаем услуги:
• литье колоколов весом от 4 кг до 5 тонн;
• составление колокольных наборов по гармонии;
• изготовление курантов;
• дополнение существующих ансамблей;
• воссоздание утраченных колоколов по предоставленным данным;
• проектирование уникальных колоколов и ансамблей для литья на нашем или ином колокольном производстве.
Каталог стандартной колокольной продукции мастерских Данилова монастыря
Вес, кг |
Диаметр, мм |
Высота, мм |
Ударный тон, октава ( |
5 |
206 |
213 |
Си бемоль, третья |
6 |
206 |
218 |
Ля, третья |
7 |
210 |
220 |
Ля бемоль, третья |
8 |
220 |
225 |
Соль, третья |
10 |
242 |
245 |
Соль бемоль, третья |
12 |
268 |
266 |
Фа, третья |
13 |
281 |
285 |
Ми, третья |
17 |
288 |
300 |
Ми бемоль, третья |
19 |
310 |
319 |
Ре, третья |
21 |
330 |
339 |
До, третья |
25 |
340 |
345 |
Си, вторая |
33 |
379 |
379 |
Си бемоль, вторая |
36 |
386 |
384 |
Ля, вторая |
54 |
446 |
477 |
Соль, вторая |
75 |
500 |
492 |
Соль бемоль, вторая |
88 |
530 |
517 |
Фа, вторая |
100 |
540 |
545 |
Ми, вторая |
120 |
570 |
588 |
Ми бемоль, вторая |
|
630 |
616 |
Ре, вторая |
205 |
690 |
695 |
До диез, вторая |
230 |
700 |
713 |
До, вторая |
270 |
710 |
713 |
Си, первая |
320 |
815 |
810 |
Си бемоль, первая |
400 |
865 |
856 |
Ля, первая |
500 |
930 |
939 |
Соль, первая |
600 |
1000 |
1005 |
Фа, первая |
900 |
1150 |
1165 |
Ми, первая |
1050 |
1204 |
1290 |
Ре, первая |
1850 |
1452 |
1446 |
Си, малая |
Портфолио
Благовестник весом 36 тонн для Среднеуральского женского монастыря
Памятный прорезной колокол в честь лодки "Кореец"
Эскизные проекты колокола Победы и колокола "Цесаревич"
msdm.ru
Литьё колоколов | Производство колоколов | Художественное литьё
В современной России возрождается много традиций, утраченных в прежние времена по разным причинам. Повсюду строится тысяча церквей, восстанавливаются разрушенные храмы, возрождая духовность народа. В 1998 году в столице Черноземья было создано предприятие «Ясак», занимающаяся литьём колоколов. Основной нашей задачей стало возобновление традиций и старинного ремесла – это художественное литьё колоколов. Мы нашли и объединили в своем коллективе мастеров и знатоков своего дела. Возродили к жизни старинные технологии и сам процесс литья колоколов, подразумевающий даже некоторые народные приметы. Например, во время производства колокола, надо говорить о чем-то пустяковом, не упоминая главное действо. Колокола имеют множество различных форм, размеров, материалов и способ производства. Каждый колокол создавался не как предмет производства, а как нечто одухотворенное. Большие колокола употреблялись почти только при церквах, а потому именовались Божьим гласом. Колоколам, особенно встарь, давали имена: бурлила, гудь, лебедь, мотора. Каждый колокол имел как бы свой характер, свои особенности, ведь ни один не был похож на другого. По назначению и величине различали: перечасный, зазвонный, праздничный. Звон колоколов на Руси в старину имел очень большое значение. Он не только предварял или заканчивал службу в храме, но также являлся оповестителем о пожарах, нападениях врагов, стихийных бедствиях. А вместе с тем народная молва приписывала звону колокола и очищающие, лечебные свойства. Недаром в городах, где стояло много церквей, особенно почитались места, в которых было слышно пятизвонницу – звон с пяти колоколен.
Производство колоколов.
Наше предприятие занимается производством колоколов и художественным литьем с «русским» профилем. В наших изделиях обеспечивается использование лишь сертифицированных металлов и уникальных старинных профилей. Такой испытанный подход позволяет нашим изделиям высоко цениться в России и выходить на мировой рынок. По всем вопросам производства колоколов звоните по телефону, указанному на сайте.
Церковная утварь.
Ещё одно направление нашего производства – это церковная утварь. Церковной утварью называют предметы, украшения, убранство, применяемые для богослужения. Различные чаши, подсвечники, оклады икон и книги. Все это изукрашено узорами, православной тематикой. В церковную утварь часто вставляют драгоценные камни, поэтому большинство предметов церковной утвари представляют большую художественную ценность. Красочность, монументальность, праздничность богослужений в большой мере определяется окружающим убранством, что и создает особую торжественность происходящего.
Основным преимуществом церковной утвари, которую производим мы, является лучшее соотношение цены и безупречной ручной работы каждого изделия. Это определяется высокой квалификацией и мастерством рабочих, вернее сказать настоящих русский умельцев. При этом вся церковная утварь изготавливается в строгом соответствии с канонами Русской Православной церкви.
Мы принимает заказы из любой части России (Москва, Нижний Новгород, Великий Новгород, Владимир, Суздаль, Кострома, Ростов, Сергеев-Посад, Переславль Залесский, Ярославль) и стран СНГ(Киев, Минск). Для уточнения деталей и совершения заказа звоните по телефонам, указанным на сайте.
yasak-kolokola.ru
Литье колоколов. Особенности технологии — реферат
Литье колоколов. Особенности технологии.
Построение профиля колокола.
Работа мастера над будущим колоколом начинается с расчетов и построения чертежа его профиля. От решения этой первоначальной задачи будут зависеть голос, прочность и внешний вид колокола. Обычно заказчик определяет массу нужного ему колокола, но иногда задается и его основной тон. То и другое зависит от определенного соотношения размеров всех частей формы колокола. Главные параметры — это нижний диаметр, высота и толщина стенки, причем стенки колокола постепенно утоньшаются соответственно диаметру, идя снизу вверх.
Вариантов построения формы колокола множество, есть т. н. «немецкий» профиль, «французский», «английский», «русский», — но принцип всегда один: все части формы рассчитываются по единому модулю и должны быть ему кратны. Величина модуля задается толщиной стенки в месте удара, т. е. в наиболее утолщенной части, которую русские мастера назвали «бой». Рассчитывается бой в зависимости от массы и тона будущего колокола по специальным таблицам. Далее по осевой линии стенки колокола строятся линии внутреннего и наружного профиля. Вся система пропорций основана на свойствах логарифмической спирали. От соотношения толщины боя к диаметру колокола зависит и его прочность. В старинных колоколах (до XV в.) это соотношение было равно 1:12 и 1:13; у русских колоколов XIX в. — 1:15. Чем тоньше стенки колокол а, тем ниже его основной тон и пластичнее звук.
Итак, прочность и красоту звучания колокола определяет соотношение трех основных параметров: диаметра, высоты и толщины стенок. При этом существующий, выверенный многовековой практикой метод не дает точно рассчитанного способа определения верхнего диаметра колокола. В итоге каждый мастер имеет свой собственный, хранимый в тайне профиль колокола, хотя все мы пользуемся единым принципом его построения. Мой «секретный метод» могу раскрыть отчасти: из всех старых колоколов, которые привелось мне увидеть и услышать, больше других мне нравятся русские колокола XVII в. Их я внимательно изучал, обмерял и по их подобию строю профиль своих колоколов.
Когда чертеж будущего колокола готов, по нему изготавливаются два лекала: для внутреннего профиля колокола и для наружного. Далее начинается создание объемной формы колокола из кирпича и глины.
Формовка колоколов.
Колокола формуются обыкновенно по способу вольной глиняной мазки, при помощи шаблонов, и только небольшие колокольчики формуются в опоках. Мазку производят или в литейном чану, или же внутри сушильной камеры, если таковая имеется надлежащих размеров. На отечественных колокольных заводах формовка колоколов производится так: сначала приготовляют сердечник. На него наносится временная рубашка, и уже по этой последней выделывается кожух. Сушка формы производится на месте сжигания горючего материала, внутри пустой формы сердечника. Формовку начинают тем, что в центре литейного чана устанавливают временную стойку, которая своим нижним концом может вращаться в гнезде, закопанной в землю доски, а в верхнем - в бруске, уложенном на верхние края чана. На стойку наколачивают временный шаблон и по круговой линии, описываемой им, выкладывают цоколь из кирпича с замком и затем приблизительную форму сердечника, до половины его высоты. Для кладки цоколя употребляются обыкновенные кирпичи и в стенках его делают каналы, для притока воздуха, необходимого для сжигания горючего материала. Самый сердечник выкладывается из сырцовых кирпичей, формованных из тощей формовочной глины и высушенных на воздухе или слегка прожаренных в сушилке. Когда кладка дойдет до половины высоты сердечника, стойку с шаблоном снимают. В кладку сердечника заделывают железный крест с коническим гнездом посередине и в это гнездо вставляют нижнюю пятку железного шпинделя. Верхний конец последнего помещают в скобу, приделанную к лежащему на чане брусу; передвигая последний, устанавливают шпиндель в отвесное положение, после чего брус закрепляют. Затем на шпинделе надевают шаблонную доску с начерченным на ней контуром стенок колокола и несколькими параллельными контурами, которые постепенно урезываются. Сначала урезывают шаблон по первому контуру сердечника, выкладывают тело его и наносят на него слой тощей шишечной глины, сначала обыкновенной, а затем смешанной с мелкоистолченным и просеянным кирпичем и формовочным песком. Изготовив окончательно контур сердечника, обмазывают его с помощью кисти пеплом, разболтанным в мыльной воде для образования изолирующего слоя. На шаблоне имеется выступ, которым вырезается в верхней части сердечника коническое гнездо, для помещения короны колокола. После сердечника приступают к мазке рубашки, постепенно урезывая шаблон до второго контура. На сердечник наносят слой пластической жирной глины, а для того, чтобы не получились трещины при сушке, в массу закладывают волокна льна. После окончательного выглаживания наружного слоя рубашки по второму контуру, дают ей просохнуть; огонь внутри формы тушат и дают ей охладиться. Затем наносят на глиняную поверхность кистью слой жидкой смеси из сала, мыла и воска, проглаживают и дают просохнуть на воздухе. Когда все это сделано, накладывают на поверхность рубашки, в соответствующих местах, рельефные украшения - пояски, надписи, изображения святых и т.п. Эти части формируются отдельно из воска в гипсовых формах и, слегка подогретые, прилепляются к составу, покрывающему рубашку.
Укрепив украшения, приступают к мазке кожуха, урезывая шаблон по третьему контуру. Обливают поверхность формы жидким составом из тонкого, просеянного сквозь сито, порошка формовочной глины, смешанного с конским калом, также пропущенном и просеянном, коровьей шерстью и рубленым льном. Эту операцию повторяют несколько раз, пока получится слой толщиной в 5-7 мм, причем жидкая масса проникает во все углубления рельефных украшений колокола и плотно, отчетливо их заполняет.
После просушки нескольких таких слоев, снова разводят огонь внутри формы и начинают смазку наружных слоев кожуха их жирной глины. По мере разогревания формы, восковые украшения, нанесенные на рубашку, плавятся, частью стекают, частью всасываются глиной, оставляя на их месте пустоты, которые при отливке заполняются металлом. Для того, чтобы предохранить кожух от растрескивания во время сушки, в его массу вмазывают льняные волокна или телячью шерсть, а для сообщения кожуху устойчивости в глину заделывают железные ребра и обручи, к которым ребра привязывают проволокой. Этот железный каркас заменяет опоку. На поверхность законченного кожуха накладывают такие же, но более толстые ребра, верхние концы которых выгнуты в виде крючьев для подцепки подъемным краном; нижние же их концы загнуты под нижнюю крышку кожуха. Кроме того, поверх ребер загоняются железные обручи и стягиваются болтами.
После этого кожух снимают, устанавливают его на козлах и тщательно осматривают его поверхность, исправляют рельефные украшения, затирают трещинки, покрывают чернилами и просушивают, сжигая солому. Одновременно острым ножом разрезают рубашку и удаляют ее по частям с сердечника. После удаления рубашки, осматривают сердечник, заглаживают неровности и трещины и приступают к окончанию верхней части сердечника. Для этого необходимо, прежде всего, удалить шпиндель (шаблонодержатель) и положив в центральную пустоту горючий материал, зажигают его. Одновременно на края сердечника накладывают железную решетку или чугунную плиту, на которой из кирпича выкладывают форму свода колокола и заканчивают ее пористой тощей глиной. Через оставленное в голове сердечника отверстие засыпают внутреннюю его пустоту сухим песком для удаления воздуха, и затем отверстие заделывается. На законченный сердечник наставляют исправленный и отделанный кожух, причем, благодаря замку, смыкание их произойдет правильно. Модель короны колокола отливается из смеси воска и сала в гипсовую разборную форму. Саму модель обмазывают пластической массой, а затем наносят на ее жирную пластическую глину несколько слоев. В глину заделывают железные ребра и, кроме того, два железных прута, выпускаемые концами наружу для удобства поднятия и переноски формы. Литники и выпары устраиваются на самой модели, приливая их к ней из легкоплавкого сплава. Более крупные короны формуют по частям и затем соединяют в одно целое. Собрав кожух на сердечнике и вставив в гнездо форму короны, замазывают швы глиной, связывают проволокой и производят заливку, пока форма не потеряла жара, сообщенного ей огнем, и не успела впитать в себя сырости. Пустое пространство между стенками формы и литейного чана надо засыпать песком и гарью и утрамбовать. Заливку бронзой производят без помощи ковшей, а дорожкой, проведенной от печи, для чего форму погружают в литейный чан.
Колокольная бронза.
Мало кто знает, что церковный колокол изготавливают из смеси: бронзы, меди, олова, при очень большой температуре плавления. Такой состав обеспечивает эхо и громкий звук готового изделия: колебания диаметра-это низкая октава и толщины-это высокая октава. Под общим названием бронзы в технике известно несколько составов меди с оловом, с преобладанием первого из этих металлов. Медь и олово могут сплавляться в весьма различных пропорциях, но для отливки изделий применяются только некоторые определенные сплавы. Примесь к меди олова для образования бронзового сплава увеличивает твердость меди, делая ее звонкой и легкоплавкой, но в то же время и хрупкой. При содержании олова не превышающем 25%, бронза будет иметь желто-красный цвет и сохраняет присущую чистой металлической меди степень вязкости и тягучести. При увеличении содержания олова вязкость и тягучесть заменяются хрупкостью, причем цвет бронзы из красноватого переходит в стально-серый. Таким образом содержание олова в бронзе не должно превышать предельных 25% без риска уменьшить к худшему свойства сплава. Так сплав из 65 частей меди и 35 частей олова обладает наибольшей степенью твердости, но в то же время хрупок. Затем, с увеличением в сплаве содержания олова до 50% , сплав делается мягким, приближаясь по своим свойствам к металлическому олову. Бронза на воздухе окисляется быстрее металлической меди, покрываясь зеленоватым налетом окиси. Таким налетом бывают покрыты все античные бронзовые статуи и другие предметы, отлитые из этого сплава, открываемые в земле как археологические находки. Кроме основных составных частей меди и олова в бронзовых отливках всегда можно открыть присутствие других примесей, составляющих или следствие недостаточной очистки сырых материалов, употребленных для переплавки, или же введенных в сплав для сообщения ему специальных качеств и, главным образом, для его удешевления. К таким примесям относятся: железо, марганец, никель, свинец, цинк, фосфор, мышьяк, сера и сурьма. Примесь к бронзе цинка придает сплаву красный, желтоватый оттенок. Цинк в небольших дозах, до 2%, подмешанный к бронзе, действует благоприятно, повышая способность бронзы отчетливо заполнять формы и уменьшая склонность к образованию раковин. При содержании цинка более нормального количества, бронза теряет свойственные ей характеристики, сообщая металлу характер латуни.
Свинец ухудшает физические свойства бронзы, а железо повышает твердость и увеличивает температуру плавления, но зато способствует получению доброкачественных отливок. Никель увеличивает твердость и уменьшает вязкость бронзы. Примеси мышьяка, сурьмы, серы и фосфора, даже в самых малых дозах, делают бронзу хрупкой, а потому не должны быть допускаемы. Независимо от состава сплава, получение хороших отливок зависит также от способа обращения с металлом при плавке и разливке в формы, а также и физических изменений, которые произойдут в вылитом в форму сплаве. Добротность отливок много зависит от быстроты охлаждения металла в форме. При быстром охлаждении металла отливка будет иметь мелкозернистое сложение, которое служит признаком крепости и плотности сплава. Поэтому, если для отливки будет употреблена металлическая форма, то бронза может быть более перегрета, чем при отливке в земляные сухие формы.
Металлические формы, как обладающие большей теплопроводностью, быстро охлаждают металл и не дают сплаву распадаться на отдельные части. Массивная же форма, при большом перегреве металла, не в состоянии предотвратить это нежелательное явление. Усадка бронзы больше чугуна и почти равна стали. Что касается мер, которые должны быть приняты против большой усадки, то они общие с теми, которые принимаются при отливке чугуна и стали. Получение неплотных и нечистых отливок может произойти по причине химических реакций, происходящих в сплаве во время его переплавки и остывании. Так при переплавке меди и олова, последнее, обладая большим сродством с кислородом, выгорает быстрее меди. Вот почему при составлении сплава необходимо брать олова значительно больше против теоретического расчета. Бронза в расплавленном состоянии имеет свойство поглощать значительное количество кислорода и затем снова освобождает его при остывании. При быстром остывании отливки, сплав принимает густую консистенцию, вследствие чего пузырьки кислорода не могут пробиться сквозь него и выйти из формы, причем образуется множество мельчайших раковин. Вот почему необходимо как при разливке, так и при остывании бронзы защищать ее от действия кислорода, посыпая расплавленный металл порошком угля. Так как олово окисляется быстрее меди, то при составлении бронзового сплава сначала плавят медь, и когда она совсем разжижается, бросают в ванну олова, стараясь поднять возможно выше температуру ванны для поддержания сплава в весьма жидком состоянии, способствующем более тесному перемешиванию обоих металлов. Быстрота ведения плавки до некоторой степени понижает возможность окисления металлов, т.е. угар их. Поэтому печи для плавки надо устраивать так, чтобы они доводили сплав до требуемой температуры в возможно кратчайший срок. Тем не менее, несмотря на все предосторожности, совершенно избежать окисления металлов при переплавке нельзя; угар бывает от 4 до 10%. Колокольная бронза содержит на 80 ч. меди 20 ч. олова. Она должна удовлетворять следующим требованиям: издавать при ударе полный и чистый звук и обладать значительной крепостью и упругостью. Хороший колокольный металл отличается плотным, мелкозернистым изломом, серовато-белого цвета.
Язык колокола при литье изготавливают из мягких сортов стали. Он должен при звоне, бить точно в само ударное кольцо колокола, потому что, если будет подвешен выше, то он не озвучит всех обертонов звука, а ниже – возможен полный раскол колокола. Как видите не простая эта работа-литье колокола.
Литье колоколов.
После долгих недель работы над формой колокола, поиск наилучшего для него профиля, подбор и изготовление икон, декора и надписей. Настал великий момент — день отливки колокола.
В подовой печи разводят огонь и закладывают медь, которая плавится в течение 5-6 часов. Мастер все это время постоянно следит, чтобы пламя не ослабевало и медленно, постепенно температура приближалась к точке плавления меди (1083 °С). Далее температуру быстро поднимают до 1200-1300 °С и вбрасывают нужное количество олова. Полученный сплав тщательно перемешивают длинными деревянными шестами, раскисляя металл. Сплав охлаждают до температуры 1080 °С и вышибают снаружи печи пробку. Жидкий металл, стремительно вырываясь из отверстия, течет по желобу и наполняет форму. До этого момента от загрузки олова в печь должно пройти не более 10 минут, иначе олово выгорит. Если температура будет меньше 1080 °С, тело колокола выйдет пористым, если больше — будет чересчур большой процент угара, а сплав в наиболее толстых участках стенки колокола выйдет неоднородным: легкое олово разделится с тяжелой медью, что окажет вредное влияние на звук.
Готовность сплава, кроме точного определения температуры, можно определить старинным способом: опустить в него деревянную палочку. Если бронза готова, она застывает на ней в виде стеклообразной корки. При правильном заполнении формы металл глухо журчит (более резкие звуки говорят о пузырях в сплаве, что ведет к раковинам в колоколе). Колокол стынет несколько дней, затем его вынимают из ямы, очищают от пригоревшей глины изнутри и снаружи, а затем тщательно обрабатывают каждый сантиметр поверхности. Теперь колокол можно приподнять и попробовать звук. На моем заводе колокола ни в коем случае не обтачиваются, что часто делается на других предприятиях для «подправления звука».
На основе вышеописанного способа существуют различные способы литья колоколов: 1. Литье в керамику, самое качественное, быстрое и дорогое . 2. Литье в гипсовые формы, требует принудительной сушки, и качество уступает керамике. 3. Литье в глиняные формы, самый дорогой способ.
Колоколов, полностью соответствующих всем требованиям качества, к сожалению, выпускается крайне мало. Даже наиболее известные на сегодняшний день изготовители регулярно допускают недоработки. С другой стороны, в системе государственного механизма России отсутствуют ГОСТы, технические требования, стандартизация а, соответственно, и правовые основания, позволяющие четко определять критерии качества при приемке колоколов. Оценка возможна только по внешним признакам, например, качество сырья или точность соблюдения технологии. Но такая оценка не гарантирует главного - красивого традиционного звучания. А это самое главное требование к колоколам. Существующий пробел в регулировании данного вопроса восполняется проведением экспертной оценки. |
referat911.ru
РЕМЕСЛЕННАЯ ТЕХНОЛОГИЯ. ЛИТЬЕ ПУШЕК И КОЛОКОЛОВ
Этап ремесленной литейной технологии начался с бурного освоения чугунолитейного производства, которое стало возможным с изобретением мощных воздуходувных устройств, позволивших создать более производительные печи для восстановления железа из руды. Кроме того, возрос спрос на чугунные ядра и чугунные пушки.
Изготовление пушек представляло довольно сложный трудоемкий технологический процесс (рис. 1.5).
Сначала выполняли глиняную модель на деревянном стержне. На этот стержень первоначально наматывали соломенный канат, который обмазывали глиной. С помощью шаблона формировали наружную поверхность модели, диаметр которой должен был быть на 20—25 мм меньше внешнего диаметра готовой пушки. Когда глина подсыхала, на модель наносили последний слой, состоящий из воска и сала, к которым для твердости примешивали толченый уголь. Украшения (гербы, над-, писи и т. д.) делали отдельно в гипсовых стержневых ящиках и прикрепляли ,к телу модели.
Изготовление самой литейной формы начиналось с нанесения кистью слоя тощей глины, смешанной с углем и волокнистыми материалами (соломой, паклей). Толщина слоя составляла примерно 15 мм, а число -таких слоев достигало 25—30. Затем наносили слои жирной глины, пока общая толщина глиняной обмазки не достигала 120—150 мм в зависимости от диаметра орудия. После этого накладывали поперечные обручи, а на них — ряд продольных брусьев. По окончании обмазывания н подсушивания (при этом восковой слой вытапливался) удаляли деревянный стержень. Далее вставляли керамический стержень. Прикрепляли отдельно изготовленную форму казенной части и приступали к заливке.
Уникальным памятником литейного искусства XVI века является Царь-пушка — выдающееся творение русского мастера Андрея Чехова.
Согласно надписи на пушке она была отлита по указанию царя Федора Иоанновича в 1586 г. Масса ее — более 2400 пудов (40 т), длина — 5,34 м, калибр — 89 см. По замыслу создателей вес ядра составлял 120 пудов, масса одного порохового заряда — 30 пудов.
Царь-пушка славится не только своими размерами, но и художественными достоинствами. Пушку украшают тонко выполненные изящные барельефы. На правой стороне дульной части изображен царь Федор в полном царском облачении, со скипетром, едущий верхом. Царь-пушка была создана как боевое орудие для обороны Кремля, но из нее не было сделано ни одного выстрела.
Особой областью литейного искусства является литье колоколов. Оно достигло расцвета в средние века, однако основные технологические приемы накапливались тысячелетиями.
Колокольный набат извещал о нашествии врагов, мятеже, пожаре, эпидемии чумы. Под колокольный звон казнили людей. По сигналу колокола новгородцы собирались на вече. В деревнях России в пургу днем и ночью звонили колокола, чтобы путники находили дорогу. Колокола, устанавливаемые на кораблях или в опасных местах побережья, в туман предохраняли корабли от столкновений и крушений. Трезвон церковных колоколов, то радостный и заливистый, то торжественно-плавный, то томительно-скорбный, сопровождал человека в течение всей его жизни.
Колокол должен был обладать громким, звучным и чистым голосом, мелодичным и определенного тембра.
Для звучания буддийских колоколов характерна камерность. Их звон не сигнал бедствия, не призыв к действию. Это — голос, взывающий к богам. На боковой стороне колокола есть литое пятно, в которое ударяют бревном, подвешенным на веревках или цепях. Звук получается мягким, приглушенным. Сам колокол должен быть хорошим аккумулятором и резонатором звука, чтобы возникший через несколько секунд после удара и нарастающий гул казался ответом «небожителей», которому дает истолкование монах.
На колоколах, как правило, выполняли всевозможные надписи. Первоначально они содержали сведения о времени изготовления колокола, религиозные тексты. Позднее их форма и содержание усложнились, появились посвящения различным историческим событиям, государям.
Особенно часто надписи встречаются на восточных колоколах. На поверхности пекинского колокола «Та-гжун» отлито несколько буддийских канонов — более 200 тысяч иероглифов, что соответствует китайской книге среднего формата объемом около 300 страниц.
Ранние колокола имели тюльпановидную или бочкообразную форму, которая сохранилась в некоторых восточных колоколах, а также в колокольчиках, гирлянды которых вешают на шею верблюдам.
Со временем форма менялась довольно существенно. Мастера разных стран вырабатывали свой определенный стиль.
Европейские колокола приобрели заметно расширяющуюся нижнюю часть, что сохранилось до наших дней. Для этих колоколов
характерна тщательная обработка поверхности, которую украшали рисунками и надписями, сначала выдавленными, а позднее выпуклыми (украшения выполняли, прикрепляя на форму восковые элементы).
Восточные колокола отличаются от европейских. Китайские, например, по форме часто напоминают цветы колокольчика. В Китае колокола издавна отливались из чугуна. Чугунная отливка не подвергалась механической обработке, о чем говорят сохранившиеся заливы металла в стыках форм. Литейные формы китайских колоколов, в отличие от европейских цельных, были составными.
По мере развития техники литья увеличивались размеры и масса колоколов. Литье колоколов стало своеобразной демонстрацией мощи. Кто умел лить колокола, мог лить и пушки.
Крупные колокола обычно формовали в ямах недалеко от плавильных печей, чтобы заливать металл самотеком.
В яме выкладывали из обычного кирпича цоколь. В центре цоколя помещали деревянную стойку, к которой крепился временный шаблон для изготовления нижней части пустотелого болвана (рис. 1.6, а). Затем шаблонную систему заменяли постоянной металлической для окончательной формовки болвана (рис. 1.6, б). Внутренняя полость болвана представляла собой топку, в которой сжигали дрова или уголь для сушки болвана. Последние слои болвана делали из песка и глины, разведенной на квасном сусле. Высушенный болван окрашивали смесью, состоящей из молотой золы, которую разводили в мыльной воде или пиве, а затем болван смазывали салом.
На готовый болван с помощью шаблона наносили глиняную рубашку — место будущего тела колокола (рис. 1.6, в). Рубашку подсушивали и покрывали составом, приготовленным из мыла, сала и воска. На обработанную поверхность наносили различные рельефные изображения: надписи, орнаменты, рисунки. Эти изображения готовили из смеси воска, канифоли, сурика и сажи.
Приготовленный болван служил в дальнейшем как бы моделью колокола. По нему готовили верхнюю опоку с каркасами и другими приспособлениями (рис. 1.6, г).
После подсушки кожух снимали, удаляли глиняную рубашку, доделывали литниковую системы и другие элементы формы и окончательно собирали ее под заливку (рис. 1.6, д).
Заливка металла, как уже говорилось выше, обычно происходила самотеком.
После затвердевания металла форму разрушали, отливку извлекали, очищали и производили отделочные работы — чеканили, шлифовали.
Нигде в мире колокола не достигли такого совершенства, как в России. Русские колокола поражают не только своей формой и искусством исполнения, но и красотой звука. Части колоколов так соразмерены, что дают три тона: первый — в месте удара, второй (полутон верхнего) — на середине колокола, третий (на целую октаву ниже) — вверху.
Первые колокола появились на Руси в X веке. Но наибольшего совершенства мастерство литейщиков достигло к началу XIV века.
При Иване Грозном осваивается литье чугунных колоколов. К XIV веку в Москве насчитывалось не меньше 5000 колоколов.
Первым из колокольных дел мастеров в летописях упоминается московский мастер Борис (1342 г.).
К XVI веку мастерство русских литейщиков достигло такого уровня, что они смогли приступить к отливке колоколов-гигантов.
Московский мастер Николай Немчинов отливает в 1532—1533 гг. два колокола, один весом 500, а другой — 1000 пудов.
Андрей Чохов, бывший в течение 64 лет придворным литейщиком и прославившийся изготовлением Царь-пушки отливает во времена Бориса Годунова колокол «Реут» весом больше 2000 пудов, почти равный одному из крупнейших в то время пекинскому колоколу.
При царе Алексее Михайловиче было задумано отлить колокол невиданных размеров массой 10 000 пудов. Иностранные мастера брались изготовить этот колокол за 5 лет. А выполнил царский заказ в 1654 г. менее чем за один год русский мастер Емельян Данилов, представитель знаменитой московской семьи литейщиков Даниловых.
В 1655 г. всего за 10 месяцев Александром Григорьевым был отлит Успенский колокол — «отец» Царь-колокола, по массе почти равный своему знаменитому «потомку». О масштабах работ говорят следующие цифры. Чтобы выплавить металл, построили 5 печей, вмещавших 2500 пудов каждая. Для загрузки только одного куска шихты требовалось одновременно 40—50 стрельцов. Металл плавили в печах три дня, а заливали в форму почти сутки. Отливка остывала в течение нескольких дней. Верх формы снимали с помощью 16 блоков. Для выбивки отливки из формы потребовалось по 70—80 стрельцов на каждый из шестнадцати блоков.
Колокол поражал очевидцев своей красотой. На нем были искусно изображены царь, царица, патриарх Никон и херувимы. Сирийский путешественник Павел Алеппский утверждал: «Ничего подобного этой редкости, великой, удивительной, единственной в мире нет, не было и не будет: она превосходит силы человеческие». А звук его он сравнивал с громом.
Успенский колокол, как и его предшественники-гиганты, не сохранился до наших дней. Через 46 лет он стал жертвой большого московского пожара. Его лом пошел на изготовление Царь-колокола, единственного уцелевшего свидетельства искусства русских литейщиков.
Иван Моторин, создавший шедевр колокольного литья, принадлежал к одной из знаменитых династий литейщиков. Царь-колокол оказался лебединой песней Ивана Моторина.
При изготовлении уникального колокола Иван Моторин показал себя не только талантливым литейщиком-художником, но и отличным организатором. Однако из-за того что ему то и дело приходилось обращаться за помощью в сенат, пуск печей затянулся на несколько
месяцев. При плавке произошли две аварии После второй аварии И Моторин умер, так и не увидев своего детища.
Литье самого крупного в мире колокола (256 т) завершил его сын и помощник Михаил. 25 ноября 1735 г была произведена заливка. Колокол из литейной ямы не вынимали, над ним устроили деревянное сооружение Во время пожара строение загорелось, колокол раскалился и, когда его начали заливать водой, треснул — откололся кусок весом 11,5т.
В 1836 году Царь-колокол установили на постаменте около колокольни Ивана Великого в Кремле.
В дореволюционной России признанным центром колокольного дела был город Валдай Здесь отливали тысячепудовые колокола для главных храмов Москвы и Петербурга. Но особой известностью и любовью
заслуженно пользовались валдайские колокольчики По чистоте голоса и мелодичности они не уступали колокольцам из бельгийского города Мехелен-Малин, от которых пошло выражение «малиновый звон».
К сожалению, в наши дни только ростовские звоны напоминают о гармоничном согласии колоколов, которое было характерной приметой русской жизни в XVI—XVII веках Впоследствии гармоническая слаженность колоколов отошла на задний план, а главными стали ритмические достоинства Это повлияло на технологию, еще больше отдалив форму русских колоколов и технические приемы их литья от европейских.
Сегодня колокола звучат не только в храмах Ведущие оперные театры страны имеют достаточно большой набор колоколов, без которых нельзя почувствовать всю глубину замысла композитора и красоту многих музыкальных произведений В Мариинском театре Санкт-Петербурга во время оперных спектаклей звучат голоса до 18 колоколов, больших и маленьких, массой от 3 т до 5 кг Колокольный звон включали в свои произведения почти все русские композиторы — от Глинки до Стравинского В Мариинском театре есть набор не совсем обычных по форме, чашкообразных колоколов, звучание которых составляет хроматическую гамму (рис. 1.7).
1.3. СКУЛЬПТУРНОЕ ЛИТЬЕ В XVII—XIXВЕКАХ
Европа, как уже указывалось, наследовала традиции скульптурного литья, заложенные древними греками и этрусками Начиная с эпохи Возрождения античные статуи стали классическими образцами, на которых учились и которым подражали многие поколения ваятелей.
Широкое знакомство России с античным искусством происходит в царствование Петра I Изготовление литых статуй требовало особых, весьма сложных приемов, поэтому в XVII веке в России литье скульптур превращается в самостоятельную область литейного производства
Если в допетровской Руси в честь выдающихся событий — побед, чудесных исцелений и т д — воздвигались храмы, монастыри, либо часовни, то с начала XVIII века под влиянием «просвещенной Европы» получают распространение мемориальные сооружения в виде скульптурных памятников Они очень быстро завоевали самую широкую популярность Именно в памятниках лучшие художники-скульпторы смогли проявить и русский размах, и чувство прекрасного.
Скульптуры делают из различных материалов, устойчивых к атмосферным воздействиям Материалами, сочетающими в себе высокую пластичность, прочность и достаточную стойкость против коррозии и эрозии с декоративными свойствами, являются бронза, чугун, сталь.
Литые памятники имеются почти в каждом городе, они украшают площади, скверы, парки Некоторые из них настолько слились с архитектурным ансамблем городов и окружающим ландшафтом, что стали
их неотделимой частью, их символическим выражением. Таким символом для Киева стал памятник Богдану Хмельницкому (скульптор М. Микешин, 1888 г.). Новгород трудно себе представить без памятника 1000-летию России (скульптор М. Микешин, 1862 г.). С Одессой неразрывно связан памятник дюку Ришелье (скульптор И. Мартос, 1823 г.). Каждому, кто бывал в Архангельске, наверняка запомнился памятник Ломоносову (скульптор И. Мартос, 1829 г.).
Особенно богат памятниками Санкт-Петербург — северная столица России.
Первыми произведениями русского скульптурного литья были статуи Петра I.
В 1747 г. К. Б. Растрелли создал конную статую Петра I в стиле барокко, но она не понравилась императрице Екатерине II, поскольку не соответствовала новому стилю — раннему классицизму. Лишь в 1800 г. статую установили перед Инженерным замком.
Создание новой конной статуи было поручено парижскому ваятелю Э. М. Фальконе. Его произведение, которое вслед за А. С. Пушкиным стали называть «Медным всадником», явилось шедевром мирового искусства.
Талантливый художник, беззаветно преданный любимому делу, работал над своим детищем 12 лет, терпеливо снося помехи, придирки и даже нарочитые унижения со стороны именитых сановников.
Вначале вызвала бурю негодования гипсовая модель памятника — «полураздетый, босой царь, на взбесившемся жеребце, накрытом звериной шкурой вместо седла». Но Екатерина II утвердила проект.
Много неприятностей доставил Фальконе президент Российской академии художеств И. И. Бецкий, вообразивший себя автором проекта.
Возникли трудности с изготовлением литейной формы. Фальконе сам взялся за ремесло литейщика, используя помощь русских мастеров.
При изготовлении отливки произошло две аварии, которые едва не привели к полному провалу. Первый раз во время вытапливания воск загорелся, а дежуривший подмастерье уснул. Форму спас сам скульптор, проверявший ночью ход работы. Вторая авария произошла во время заливки, когда из формы прорвался металл. И только благодаря мужеству литейщика Хайлова заливка была закончена благополучно.
В отливке, имеющей максимальный размер больше Эми толщину стенок 7,5 мм, практически не было раковин и недоливов. Лишь в головах всадника и лошади образовались намывы металла в результате пожара во время вытапливания воска. Фальконе, считавший, что «еще не было лучшей отливки», нашел удачные решения, позволившие исправить эти дефекты литья.
В ноябре 1777 г. работа над статуей завершилась. Но у скульптора кончилось терпение. Не выдержав травЛи, сплетен, козней, так и не дождавшись установки статуи на постамент, Фальконе уехал на родину.
Памятник Петру I был торжественно открыт 7 августа 1782 г. Он увековечил не только память о выдающемся государственном деятеле,
но и славу русских умельцев-литейщиков и великого скульптора Э. М. Фальконе.
В 1873 г. перед зданием Александрийского театра был открыт памятник Екатерине II, созданный по проекту М. Микешина скульпторами М. Чижовым и А. Опекушиным.
На Исаакиевской площади в 1859 г. поставлен конный памятник Николаю I (проект О. Монферрана). Фигуры коня и всадника с большим искусством выполнил П. Клодт. Талантливый ваятель мастерски решил трудную техническую задачу установки конной статуи лишь на двух точках опоры.
В 1909 г. в торжественной обстановке на Знаменской площади Петербурга (теперь площадь Восстания) был открыт памятник императору Александру III. Он сооружался в течение 9 лет. Наверное, немного на свете памятников с такой незадачливой судьбой, какая выпала на долю этого шедевра Паоло Трубецкого. Долгие споры и резкая критика сопровождали создание памятника и не смолкали после его открытия. Среди немногих И. Е. Репин оценил художественные достоинства скульптуры и поставил ее в один ряд с «Медным всадником» Фальконе.
После Октябрьской революции отношение официальных властей к памятнику было резко отрицательным. С легкой руки Демьяна Бедного к нему пристало прозвище «пугало». В 1937 г. власти города решили, что «ворота города» — площадь у Московского вокзала —явно неподходящее место для памятника. Его перевезли во двор Русского музея. Было дано несколько указаний переплавить памятник. Но к чести сотрудников музея этого не произошло. Во время Великой Отечественной войны памятник перевезли в Михайловский сад и засыпали песком. Эта насыпь оказалась такой надежной, что предохранила скульптуру от разрушения при прямом попадании фугасной бомбы 7 октября 1941 г.
После долгих споров памятник Александру III в ноябре 1994 г был перевезен к Мраморному дворцу и установлен на пьедестале, который когда-то занимал «броневик Ленина».
Одному из авторов этого учебника было поручено оценить состояние памятника (вся документация оказалась утраченной) (рис 1 8) В результате обследования установлено, что памятник состоит из пяти частей плинт, голова коня, передняя часть коня, задняя часть коня, фигура Александра 111 Такое расчленение памятника резко упростило технологический процесс литья, исключило развитие ликвационных процессов (как, например, в «Медном всаднике») и обеспечило высокое качество литой скульптуры Создание такой конструкции оказалось возможным благодаря особой механической обработке крупных отливок (части памятника соединены полуфланцами и скреплены болтами) (рис 1 9), а также завариванию (копыта присоединены к постаменту штырями и заварены) Последней операцией было сочленение головы коня шпильками, срезанными заподлицо по окончании закрепления
Памятник имеет незначительное число литейных дефектов — небольшие раковины на сапоге всадника, на руке и в верхней части кулака Обнаружены следы небольшой ужимины в нижней части руки Все эти дефекты со стороны не заметны.
Памятник Александру III отлит из так называемой зеленой художественной бронзы (8% олова, 8% цинка, 1 % свинца, остальное медь) Сплав имеет структуру, характерную для этого класса бронз, и состоит из твердого раствора с включениями эвтектоида (Cu31 Sng + a)
Дореволюционная Москва была несколько беднее Петербурга городскими скульптурами.
Цельнолитыми выполнены бронзовые статуи героев освободительной войны 1612 г. Минина и Пожарского. Этот первый скульптурный памятник Москвы создал скульптор И. Мартос. Отлил памятник в 1818 г. знаменитый русский литейщик В. Екимов.
Изготовление колоссальной и сложной восковой модели — серьезная техническая задача, требующая высокого мастерства литейщиков. Восковую группу установили на фундаменте с решеткой, вокруг соорудили сложную литниковую систему.
Готовую модель и литниковую систему 45 раз покрывали мастикой из молотого кирпича и пива (рис. 1.10). Затем их обложили сырой глиной. Всю конструкцию укрепили кирпичной стенкой и железными обручами. Для вытапливания воска было зажжено 16 печей. Выжигание продолжалось месяц. Чтобы форму не разрушило давление жидкого металла, ее дополнительно укрепили обручами. Форму залили через общую литниковую чашу и разветвленные каналы. Окончательная отделка скульптур проводилась чеканщиками.
В 1880 г. на народные пожертвования Москва поставила первый в России памятник Пушкину, талантливо исполненный скульптором А. Опекушиным. В 1909 г., тоже на народные пожертвования, на Арбатской площади воздвигнут памятник Гоголю (скульптор Н. Андреев). В тот же год Москва получила еще одну превосходную скульптуру — памятник первопечатнику Ивану Федорову (скульптор С. Волнухин).
1.4. ЛИТЬЕ ОГРАД И РЕШЕТОК
Одной из разновидностей художественного литья являются ограды и решетки. Нельзя представить себе Петербург без чугунного кружева, которое не только удачно дополняет архитектурный ансамбль города, но и является его органической частью, гармонично связанной с дворцами, парками, набережными и мостами.
Чугунные решетки в России появились во времена Петра I и получили особенно широкое распространение в период с первой половины XVIII века до последней четверти XIX века. Железные кованные решетки и деревянные ограды почти повсеместно сменялись чугунным литьем.
Поскольку требования к качеству решеток и оград сводятся к отсутствию на поверхности грубых дефектов (раковин, засоров, заливов), для их изготовления применяли наиболее простую технологию — литье в сырые песчаноглинистые формы, точнее, разновидность этого метода, называемую почвенной формовкой.
В полу литейной мастерской делали яму, заполняли ее формовочной смесью и вдавливали модель в эту смесь.
Различали почвенную формовку по мягкой постели и по твердой постели.
В первом случае глубина ямы превышала высоту модели на 150—200 мм. Ширина и длина ямы были несколько больше соответствующих размеров модели.
При формовке по твердой постели глубина ямы была на 300—5ОО мм больше высоты модели. На дно ямы в этом случае насыпали слой крупного шлака или песка, укладывали рогожу или солому для отвода газов при заливке металла. Иногда для этих целей дополнительно устанавливали вентиляционные трубы. Затем яму заполняли формовочной смесью (рис. 1.11) и утрамбовывали ее.
Формовка в почве может быть открытой и закрытой.
Открытая формовка производилась, как правило, по мягкой постели. На предварительно уплотненную и выровненную формовочную смесь укладывали модель и ударами молотка осаживали ее. Так изготавливали отливки, у которых одна сторона была плоской.
При закрытой формовке после осаждения модели устанавливали и затем заформовывали верхнюю опоку.
В современных условиях почвенная формовка для изготовления решеток и оград применяется относительно редко. Такое литье сейчас изготавливают в двух опоках.
Ажурные ограды были призваны не скрывать усадьбы от нескромных взоров или отмежевать личные владения — они подчеркивают цельность и законченность композиции архитектурного сооружения.
В числе лучших кружевных произведений из чугуна встречаются работы всемирно известных архитекторов.
По проекту Растрелли создаются: решетка Смольного, чугунная ограда, отделяющая дворец графа М. И. Воронцова от Садовой улицы.
Чертежи решетки Летнего сада разработали Е. Фельтен и П. Егоррв, ограды Екатерининского и Александровского парков г. Пушкина — Ч. Камерон и Д. Кваренги.
Один из крупнейших представителей классицизма в русской архитектуре И Е. Старое спроектировал для ансамбля Таврического дворца чугунную ограду. Ее художественное решение подчинено общему замыслу зодчего- простой и спокойный рисунок решетки выдержан в строгом классическом стиле. Много чугунных литых решеток создано по рисункам А. Н. Воронихина К ним относятся изящная ограда с венками и гирляндами в Павловске, литые решетки в Стрельне, Гатчине, Петергофе, у Александровского дворца в г Пушкине. Одно из лучших его творений — чугунная ограда Казанского собора, созданная в 1811 г. Ее литая чугунная решетка, отличающаяся красотой и сложностью композиции, имеет величественный вид.
Но, пожалуй, наиболее значителен вклад К И. Росси и В. П. Стасова, творцов позднего ампира. По рисункам К И. Росси отлиты кружевные решетки Аничкова, Елагина, Михайловского и других дворцов. Наверное, самое удачное создание Росси — монументальная ограда у главного фасада здания Михайловского дворца. Четкий рисунок решетки, изящные контрформы, удачные пропорции ставят эту ограду в число лучших в Петербурге. Украшением Петербурга стали решетки многочисленных мостов и набережных. Их создатели нашли удачные формы и рисунки для пролетов низких решеток. Вытянутость линий, простота и прозрачность рисунка превращают решетки на фоне водной глади в тончайшие литые кружева (рис. 1.12). Длина художественных решеток на мостах города достигает 11 км.
В архитектурном убранстве Москвы ограды не играли такой огромной роли, как в Петербурге. Застройка велась веками и без единого плана. Усадьбы и дворцы разбросаны на большой территории, так что отдельные участки ограды никак не могли образовать сплошного кружевного полотна. По времени создания московские чугунные решетки относятся в основном к концу XIX века.
Обращает на себя внимание решетка особняка Морозова («Испанского подворья»). Сам дом являет собой типичный пример эклектического архитектурного стиля конца XIX — начала XX веков. В ограде строгость вертикального рисунка гармонично сочетается с барочной динамичностью растительного орнамента. Чтобы увязать рисунок ограды с оформлением стен особняка, ее декорировали накладными рельефами в виде раковин. Эти рельефы выполнены весьма искусно, но выглядят все-таки чужеродными элементами.
ИСКУССТВО ЛИТЬЯ В XX ВЕКЕ
Как уже говорилось выше, к началу XX века на смену ремесленной технологии пришла промышленная. Создаются новые сплавы, новые технологии, новое оборудование.
Неограниченные возможности чугунного литья были продемонстрированы литейщиками Каслинского завода на Всемирной выставке в Париже в 1900 г. Было выставлено множество скульптур, ажурных
тарелок, полочек, кресел, огромных чанов, тончайших изящных цепочек Истинным шедевром чугунолитейного искусства был павильон, в котором размещалась коллекция отливок Он поражал изяществом и красотой (рис 113)
Павильон спроектировал архитектор Е Е Баумгартен в 1898 г Современники считали Баумгартена не более чем талантливым компилятором, подражателем Тем не менее архитектору удалось в одном произведении представить все жанры художественного литья кабинетную скульптуру, тонкие горельефы, филигранный сквозной орнамент, архитектурные детали, барельефы и т п Декоративные приемы древнерусского искусства гармонично сочетаются с архитектурным решением павильона, выдержанным в византийском стиле
Огромный, почти пятиметровый павильон кажется воздушным Мотивы причудливой чугунной вязи невероятно разнообразны Павильон состоит из множества деталей, каждая из которых — законченное
художественное произведение Вместе с тем он не оставляет впечатления мешанины, нагромождения орнаментальных мотивов и художественных стилей
На Всемирной выставке павильон завоевал золотую медаль В настоящее время он экспонируется в специальном зале Екатеринбургской картинной галереи
Развитие литейной технологии не ограничивалось совершенствованием традиционных методо^в Немало усилий было затрачено на освоение новых материалов Наглядным примером может служить разработка технологии литья титановых сплавов
Производство титановых сплавов представляло серьезную проблему Прошло полтора века после открытия этого металла (1791 г), прежде чем началось его промышленное производство Первоначально из титановой губки путем вакуумно-дугового переплава изготавливали слитки Получать фасонные отливки мешала, в первую очередь, чрезвычайно высокая химическая активность титана в расплавленном состоянии Оказалось, что в природе не существует такого огнеупорного материала, с которым не реагировал бы жидкий титан
Проблему помогла решить гарнисажная плавка, при которой достаточно большая порция жидкого металла выплавляется в гарнисаже — скорлупе из того же металла (см гл 4)
В качестве огнеупорных материалов для изготовления литейных форм были использованы электрокорунд, диоксид циркония, магнезит, а позднее и графит, обладающие достаточной огнеупорностью и химической инертностью применительно к титановому литью
Первые фасонные отливки из титана были изготовлены в Москве под руководством профессора С Г Глазунова и К К Ясинского Почти одновременно литые заготовки несколько больших размеров были отлиты в Ленинграде под руководством Л В Буталова и Ю А Филина
Поскольку титан и его сплавы обладают хорошими декоративными качествами, напоминают по цвету никель или старинное серебро, было решено опробовать этот металл в качестве материала для художественного литья
Первую художественную отливку из титана изготовили в 1961 г под руководством профессора О Н Магницкого Это был сувенирный вариант копии Медного всадника (рис 1 14) Восковые модели сделали на заводе «Монументскульптура» В качестве огнеупорного материала керамических форм выбрали электрокорунд, который в минимальной степени взаимодействует с титаном и обеспечивает хорошее качество литой поверхности
Дальнейшее освоение промышленного производства титановых сплавов показало, что они могут с успехом анодироваться Цвет и интенсивность получаемых покрытий определяются продолжительностью травления
Художественные титановые отливки гармонично сочетаются с такими декоративными полудрагоценными камнями, как малахит, яшма, родонит и др , применяемыми для изготовления подставок
Высокие декоративные свойства и коррозионная стойкость позволили использовать титан в качестве материала для памятников, монументов, обелисков.
Первой в мировой практике монументальной литой скульптурой из титана является памятник Юрию Гагарину (рис. 1.15) на площади его имени в Москве.
Фигура Гагарина высотой 14м изготовлена из 239 блоков. Размеры литых блоков выбраны исходя из технологических возможностей вакуумного литейного оборудования. Формы изготавливали из графитовой смеси методом кусковой формовки. Плавка производилась в гарни-сажных печах с тиглями вместимостью 400 кг. Отдельные блоки сое-
диняли между собой болтами, изготовленными также из титанового
сплава.
Руководил выполнением всего комплекса сложных технологических процессов профессор Г. Л. Ходоровский.
Монументальная бронзовая скульптура по-прежнему запечатлевает на века разные исторические события. В Москве в дни празднования пятидесятилетия победы в Великой Отечественной войне установлен памятник.легендарному полководцу Г. К. Жукову (рис. 1.16). Это событие отмечено также открытием мемориала на Поклонной горе, органической частью которого являются монументальные литые фигуры.
В течение последних лет в Санкт-Петербурге установлено несколько работ скульптора М. Шемякина, подаренных художником городу. Достоинство этих скульптур служит предметом споров. Кое-какие из них
кажутся тенденциозными, несущими сугубо политическую нагрузку, например сфинкс на набережной Невы, напротив тюрьмы «Кресты». Посетители Петропавловской крепости невольно сравнивают работу Шемякина с «Медным всадником» Фальконе. Некоторые объясняют подчеркнутую уродливость фигуры Петра I сложностью натуры императора, в судьбе которого были не только взлеты, символически запечатленные Фальконе, но и мрачные, даже кровавые периоды, которые в своеобразной форме представил Шемякин. Заслуживает благодарности увековечивание Шемякиным в бронзе памяти о великих художниках, сформировавших облик северной столицы (комплекс Сампсониев-ской церкви).
Слово «памятник» обычно ассоциируется с чем-то монументальным и величественным, невольно представляешь «бронзы многопудье» (выражение Маяковского). Но в последнее время в Санкт-Петербурге появились памятники, которые должны вызвать не благоговейный трепет, а улыбку. Например, на Фонтанке есть теперь памятник Чижику-пыжику из известной песенки. Теперь гости северной столицы приходят к Чижику и бросают монеты в воды Фонтанки, чтобы вновь посетить прекрасный город.
Поиски новых путей и форм нередко принимают самое неожиданное направление. Так, в Москве, в мастерской МГТУ им. Баумана, под руководством профессора В. А. Васильева отлито несколько стилизованных человеческих фигурок, обладающих, по словам создателей, чудодейственным свойством влиять на психику человека В процессе
изготовления отливки подвергались воздействию биополя экстрасенса. Предполагается, что полученный ими заряд уменьшает или даже полностью снимает психическое напряжение. На рис. 1.17 показана такая биологически заряженная отливка — настольная миниатюра «Женщина-огонь». Она воплощает одну из легенд о сотворении мира, по которой Бог создал женщину из огня.
Высокое совершенство ювелирного литья демонстрирует созданная в той же мастерской бронзовая отливка паучка (рис. 1.18). Моделью для отливки служил усыпленный эфиром живой паук. Мелкие детали строения реального паучка воспроизведены с такой удивительной точностью, что их можно оценить при помощи очень сильной лупы. После окончательной отделки к лапкам паучка была припаяна серебряная нить — паутина.
Глава 2 ЛИТЕЙНЫЕ СПЛАВЫ
Чистые металлы для изготовления художественных отливок практически не применяются, главным образом из-за неудовлетворительных физико-химических и технологических свойств (чрезвычайно высокой пластичности золота и серебра, низкой коррозионной стойкости железа, низких механических свойств меди и т. д.) Легирование существенно изменяет эти свойства и позволяет значительно разнообразить цветовую гамму изделий, а стало быть, повысить их эстетическую ценность.
Тем не менее чтобы составить полное представление о свойствах литейных сплавов, влияющих на качество изделий, надо знать, какими физическими химическими и механическими свойствами обладают чистые металлы. Поэтому в первой части настоящей главы дана характеристика основных свойств тех металлов, сплавы которых применяются для художественного литья, а во второй части рассматриваются литейные свойства сплавов.
2.1. МЕТАЛЛЫ ^2.1.1. КЛАССИФИКАЦИЯ МЕТАЛЛОВ
Металл — слово греческого происхождения. Первоначально оно означало: рудник, руда, шахта, раскопки, материал, добытый из-под земли. М. В. Ломоносов металл определил как «светлое тело, которое ковать можно».
В средневековом трактате упоминаются семь известных европейцам металлов:
infopedia.su
Литье колоколов
Исторически первое описание технологии колокольного литья дал монах Теофил, живший на рубеже XI-XII в.в. Изготовление колоколов расценивалось как священнодействие и с VI в., с основания ордена бенедиктинцев, находилось во введении состоящих в нем монахов.
В XVI веке появилась книга В.Бирингуччо “Пиротехния” на многие века вперед предопределившая технологию колокольного литья. Вот суть этого процесса. Колокол льют в литейной яме. Форма будущего колокола состоит из двух частей: глиняной болванки и верхней части – кожуха из железных прутьев, обмазанных глиной. Болванку и кожух обмазывают жиром, обжигают. Кожух поднимают. Мастер входит под кожух и на внутренней его стороне накладывает надписи, орнаменты. Кожух ставится на место. Пустота между кожухом и болваном заливается расплавленной бронзой. Вся форма при этом засыпается землей, чтобы ее не разорвало. На краях ямы устраиваются плавильные печи. По желобам жидкий металл заливается в форму. Остывает колокол около недели. Потом колокол освобождают от земли, снимают кожух, вынимают из ямы, шлифуют и отделывают.
Технология литья не изменилась и в XX веке. В начале XX века на заводе братьев Усачевых в Валдае колокола отливали следующим образом. “Процесс создания колокола сложен и стар. Механизация не коснулась этого производства. Как 300 лет назад лили, так и теперь льют.
Прежде всего, на кирпичном фундаменте выкладывается угловатая кирпичная форма, по размерам близкая к будущему колоколу. В середине – довольно широкое отверстие. Сверху форма обмазывается глиной и приглаживается лекалом – это будет внутренняя часть колокола – ступа. После основательной сушки и обмазки жиром, мастер начинает покрывать форму жидкой глиной до тех пор, пока новый слой не достигнет нужной толщины, а именно, толщины будущих стенок “тела” колокола. Сушка. “Тело” готово. Надо его еще украсить и дать внешность. Для орнаментов заготовлены деревянные доски-трафареты. Накатывая на них массу (смесь воска, смолы и др.) получают выпуклые отпечатки орнаментов на восковых лентах. Эти ленты украшений подкрепляются на глиняное “тело” так же, как и надписи. Украшение окончено, и, после смазки формы салом, ее густо облепляют толстым слоем глины - “кожухом”. Всю форму хорошо просушивают, разводя костер под фундаментом. От тепла тает воск, но отпечатки украшений остаются на внутренней стороне кожуха. Кожух снимается и толщина “тела” легко отбивается. Так получаются две формы: ступа – для внутренней части колокола, и кожух для наружной, а между ними – полое пространство, которое заполнится металлом. Форма готова для спуска в литейную яму. После опускания формы к ней приделывают глиняную трубку (по ней потечет металл) и плотно забивают яму землей. К выходящей на поверхность трубке проводят кирпичный желоб от выходного отверстия. Тем временем печь уже накалила металл до 1200 градусов. На краю желоба в ряд ставят чугунные гири, чтобы напор металла не разнес желоб. Тяжелым обухом выбивается глиняная замазка, и из выходного отверстия печи вырывается жидкий металл, льется по желобу, уходит в форму. Два-три дня форма охлаждается в земле. На третий день ее выкапывают, разбивают глиняный кожух, выбивают ступу и тускло-красный колокол извлекается из ямы. Шлифовка, отделка занимают день, два. Затем наступает решительный момент: пробуют звон”.
www.novgorod.ru
ЛИТЬЕ ЗВУЧАЩЕГО МЕТАЛЛА (4) | АРТконсервация
Из-за бюрократических проволочек изготовление формы, постройка печей и другие подготовительные работы были начаты лишь в январе 1733 г. Все работы проводились на Ивановской площади Кремля вблизи колокольни Ивана Великого. Технологический процесс был подобен описанному ранее, по Бирингуччо, выполняемый с особой тщательностью, диктуемой огромной массой изделия.
25 ноября 1735 г. литье «Царь-колокола» благополучно завершилось. До 20 мая 1737 г., дня пожара, рокового для колокола, он все еще находился в яме, где проводили отделочные работы (так и не завершенные). Часть украшений колокола осталась непрочеканенной.
История создания колокола подробно изложена в ряде изданий [13, 57, 63, 64]. Следует отметить лишь несколько моментов, характеризующих трудоемкость, а иногда и драматизм, сопровождающий порой создание таких уникальных произведений. Неприятности при литье колокола начались с плавки металла. Огромное количество его, необходимое для заливки формы, предполагалось выплавить в четырех 50-тонных печах, установленных вокруг формы. Однако в ноябре 1734 г. в процессе плавки основание трех печей приподнялось и металл стал «уходить» под печи. Затем загорелась установка, предназначенная для подъема кожуха формы, и кровля здания. Обгоревшие дубовые бревна обрушились на приготовленную форму. Пожар удалось потушить, но процесс пришлось остановить для переборки формы и ремонта печей. Новая, на сей раз удачная попытка была предпринята в ноябре 1735 г. В изготовлении колокола было занято около 200 человек разных профессий. Было использовано около 1,3 млн. кирпичей для кладки печей и формы. На изготовление болвана-стержня потребовалось 2,5 месяца, кожуха формы — 2 месяца и т.д.
Несколько раз возникали идеи поднять поврежденный колокол. Однако он пролежал в земле 101 год и 7 месяцев до тех пор, пока 23 июля 1836 г. не была реализована также грандиозная операция по извлечению колокола из ямы (рис. 156). Подъемом руководил строитель Исаакиевского собора в Санкт-Петербурге архитектор А. А. Монферран, автор проекта постамента, на который был затем установлен колокол. Для подъема построили специальное сооружение над ямой, использовали 20 воротов, каждый из которых вращали десятки солдат. За подъемом наблюдали толпы народа, чиновники и общественность города, присутствовал генерал-губернатор.
И вот, наконец, перед взорами собравшихся предстал гигант диаметром 6 м 60 см и высотой более 6 м, подлинный шедевр литейного искусства. Колокол богато украшен рельефными изображениями. На нем выполнен парадный портрет императрицы Анны Иоанновны, велевшей его отлить (рис. 157, а). Изображение царя Алексея Михайловича напоминало о том, что новый колокол был перелит из более древнего, отлитого еще в XVII в. во время его правления (рис. 157, б). На теле колокола выполнены также овальные медальоны с изображениями святых.
Очень красивы два больших картуша, внутри которых пространные надписи об истории создания колокола. Удивительно убранство колокола — это и легкий, изящный орнамент в верхней части и пояса из листьев аканта и орнамента с крупными цветочными розетками.
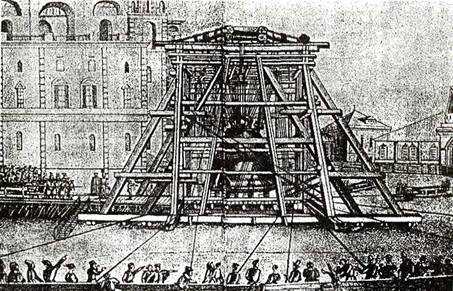
После установки колокола на постамент, его увенчали навершием, покоящимся на ушах колокола, в виде шара с золоченым крестом (см. рис. 154). На памятной доске постамента в тексте допущена неточность в дате отливки колокола.
Согласно анализу, проведенному в лаборатории минного корпуса (1832 г.) материал «Царь-колокола» содержит 84,51% меди, 13,21% олова, 1,25% серы. Выявлено также наличие около 0,036% золота и около 0,25% серебра. Повторный анализ, выполненный при реставрации колокола в 1979-1982 гг., дал несколько другие результаты: меди 81,94%, олова 17,24%. Особенно значительное различие (в 50-100 раз) в содержании примесей, например, серы 0,035%, золота 0,0025%, серебра 0,026%. Оставляя в стороне обсуждение возможной точности анализов, обусловленной техническими средствами, нужно отметить, что не следует переоценивать современные результаты для суждения об оптимальном составе колокольной бронзы. Состав металла в крупных колоколах зависит от места взятия пробы. В нижних частях содержание меди будет выше, чем в верхних, из-за ликвационных процессов. Более легкие примеси распределяются в обратном порядке.
Кроме того, и это самое главное, мы, по существу, не располагаем «эталонными» образцами древних колоколов, когда для выплавки металла использовали, в основном, чистые компоненты: медь и олово. Колокола были тем видом изделий, служба которых редко была долговечной. Их разбивали неумелые звонари, они падали с колоколен и разбивались при пожарах, их могли «наказать уничтожением» капризные цари и царицы, если не понравился тон звона или колокола звучали не вовремя (например, во время бунта).
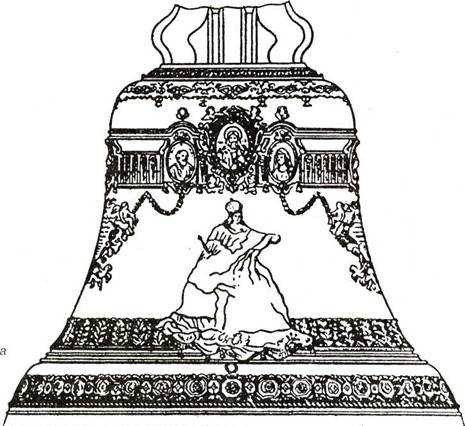
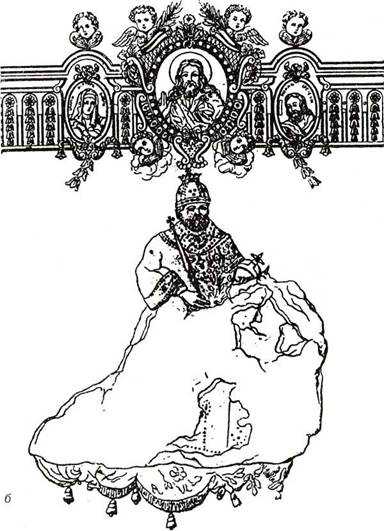
Случались, образно говоря, и «эпидемии на колокола», когда они подвергались массовому уничтожению. Бронзовые колокола переливали на пушки в Германии, Франции, России и других странах и религиозные правители, и атеисты. После поражения под Нарвой (1701 г.), когда для продолжения войны со Швецией недоставало артиллеристских орудий и не было свободного металла для изготовления пушек, Петр I повелел для этой цели взять «взаймы» часть церковных колоколов. В Москву было свезено колоколов общей массой 90 тыс. пудов.
Во время Великой Французской революции были уничтожены почти все колокола: часть металла пошла на изготовление монет, часть — на пушки для защиты революции (законы конвента 1791 — 1793 гг.) [57].
Массовое уничтожение колоколов имело место в России после Октябрьской революции. 30 июня I918 г. Совнарком постановил: «Запретить колокольный звон во всех церквях... так как он мешает трудящимся отдыхать после трудового дня»28 . Эта кампания приобрела особенно широкий размах на рубеже 20—30-х годов. По всей стране были уничтожены тысячи колоколов. Например, в Москве примерно из 200 крупных колоколов массой от 100 до 1000 пудов на месте остались два: один в Новодевичьем монастыре, другой — в Богоявленском соборе в Елохове. Металл колоколов самого крупного в Москве храма Христа Спасителя29 был использован па украшение первой очереди Московского метро, из него изготовили бронзовые барельефы известных русских писателей, установленные на фасаде нового здания Государственной библиотеки им. В. И. Ленина.
Гибли колокола во время первой и второй мировых войн. В Германии фашистский режим безжалостно уничтожал колокола как свои, так и захваченные на оккупированных территориях, используя их металл для военных нужд (рис. 158).
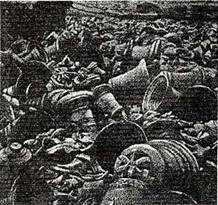
Поэтому среди сохранившихся редко встречаются колокола, отлитые до XVII в. Далеко не все из них изготовлены из материала первой плавки. Многие наиболее знаменитые колокола неоднократно переливались. Находящийся сейчас в Кремле «Успенский колокол» (окончательно установленный в 1819 г.) массой 65 т (4000 пудов) переливался шесть раз. Каждый раз при переплавке использовали металл старого колокола и добавляли лом другого литья колоколов, пушек, бытовой бронзы и т.д. Так, в металл «Царь-колокола» попали 600 мелких колоколов с Пушечного двора общей массой около 27 т и другой лом.
Следует добавить, что иногда состав бронзы, особенно по содержанию примесей, зависел от конкретно имевшихся у литейщика материалов, их месторождения, истории и других обстоятельств. Например, известно [43], что памятник Минину и Пожарскому в Москве изготовлен скорее из латуни, чем из бронзы, так как в сплаве много цинка. Однако в данном случае это связано не с особыми техническими требованиями, а скорее с финансовыми трудностями — олово дороже цинка.
Не следует идеализировать также и качество старых колоколов. В 20-х годах выдающийся звонарь К. К. Сараджаев обследовал акустические свойства 388 колоколов 362 церквей, соборов и монастырей Москвы и ближнего Подмосковья. Из них он выделил 29,5% как достойные внимания и лишь 4,4% колоколов хорошего звучания [68].
Таким образом, любой современный, даже очень точно выполненный, но единичный анализ состава металла ранее отлитого колокола дает, по существу, случайный результат. Это лишний раз подтверждает важность исторических свидетельств, обобщающих многолетний опыт литейщиков многих поколений по выбору состава бронзы.
Изучение акустических и физических свойств сплавов системы медь-олово по современным методикам [58] показало, что их оптимальное сочетание приходится на сплавы, содержащие 17—22% олова, т.е. соответствует старым рекомендациям по «колокольной бронзе». Содержание олова меньше нижнего предела ухудшает акустические свойства, но увеличивает пластичность бронзы. Колокол из сплава, содержащего олова выше 22%, звучит чище, но очень хрупок.
Дефицит медных сплавов поощрял попытки литейщиков изготавливать колокола ил более дешевых материалов, например чугуна. Но акустические свойства таких колоколов невысоки: звук глухой, быстро затухающий. Стальной колокол звучит резко — несколько смягчает резкость бронзовый язык, и т.д. В случае же исполняющих мелодию карильонов долгое звучание колокола после удара усложняет задачу игры на них, поэтому изготавливать карильоны желательно из марганцовистой бронза с 75% меди [67].
В XIX в. производство колоколов, потребность в которых была постоянной, сосредотачивается на специализированных заводах. В России их было более 20, только в Москве находилось три колокольных завода. Наибольшей известностью пользовались Ярославский завод Оловянишникова, Петербургский Лаврова и Московский Финляндского. На последнем работало до 80 человек. За год завод расходовал до 25 тыс. пудов бронзы. В 1819 г. здесь переливали колокол массой 4000 пудов Успенского собора, вместо погибшего в 1812 г. На этом же заводе в 1877-1878 гг. были отлиты 14 колоколов для храма Христа Спасителя в Москве, общая масса которых составила 40008 пудов 38 фунтов. Главный колокол весил 1654 пуда 20 фунтов, а самый маленький — 24 фунта.
Технология изготовления форм для отливки колоколов на заводах была неизменной: для крупных колоколов формовку выполняли по шаблону в яме, для более мелких формы делали на краю ямы, а затем опускали их также в яму. Самые маленькие изготавливали в опоках по модели. Крупные формы заливали по-прежнему непосредственно из печи, мелкие — из ковшей.
Для подстройки необходимого тона и аккорда звучания некрупных колоколов иногда применяли обточку их с внутренней стороны в местах, ответственных за основные гармоники звука (рис. 145).
После десятилетий активной антирелигиозной пропаганды новый поворот в истории нашей страны начался в 1985 г. Он внес значительные изменения в положение церкви. По всей стране стали снова открываться закрытые когда-то храмы, началось восстановление разрушенных, строительство новых. Возникла потребность в большом количестве колоколов. Однако за прошедшие годы практически полностью исчезла отечественная школа этого и для современных условий непростого производства. Так, даже на одном из итальянских заводов художественного литья в первой половине 60-х годов при изготовлении колокола массой 22,5 т (примерно 1380 пудов) процесс подготовки и отливки занял около трех лет.
Возрождение производства колоколов в России потребовало времени, возникла необходимость привлечения опытных кадров литейщиков и научных работников. В частности, к решению проблемы подключился такой гигант индустрии, как ЗИЛ. Специалисты-акустики под руководством докт. техн. наук Б. Н. Нюнина провели всестороннее исследование старого колокола массой 5 пудов, отлитого на известном Московском заводе Самгина. На основе этого создана математическую модель построения формы колокола и набора колоколов с заранее заданными акустическими характеристиками.
Производством колоколов занялись и некоторые кооперативы, например «Вера» в Воронеже, объединение «Янтарь», ряд предприятий военно-промышленного комплекса, имеющих квалифицированные кадры и соответствующее оснащение. Конечно, все они вначале изготавливали относительно небольшие колокола массой до 500 кг. Однако по мере накопления опыта ассортимент их расширяется. В итоге в конкурсе на восстановление уничтоженных колоколов для храма Христа Спасителя приняло участие несколько предприятий (из 14 колоколов масса самого крупного 1654 пуда, или 27 т). Конкурс выиграли московские автозаводцы.
В марте 1996 г. Патриарх Московский и Всея Руси Алексий II освятил 10 колоколов, изготовленных на ЗИЛе. Первая партия заканчивается изготовлением колокола массой 3 т. Колокола храма Христа Спасителя (неполный комплект) звонили в Рождественскую службу 1997 г. На очереди литье и установка самых крупных колоколов: «Торжественного» массой 27 т, «Воскресного» — 16 т, «Полиелейного» — более Юти «Будничного» — более 5 т. Планируется отлить все колокола в 1997 г.
___________
28 А. Г. Лагышсв. Рассекреченный Ленин. — М.: Им-во «Март». 1996. — 336 с.
29 Храм строился на народные деньги в 1837-1883 гг., взорван по плану реконструкции Москвы в 1931 г., а ныне восстанавливается на том же месте, опять же на народные деньги к 850-летию со дня основания города.
Первоисточник:
МИР ХУДОЖЕСТВЕННОГО ЛИТЬЯ. ИСТОРИЯ ТЕХНОЛОГИИ. Бех Н.И., Васильев В.А., Гини Э.Ч., Петриченко А.М. УРСС. М., 1997art-con.ru
Священнодействие литья колоколов — Володя — Дневник — Православные знакомства «Азбука верности»
На личной страничке батюшки Виталия Тимченко, настоятеля храма Воскресения Христова (это в Ленобласти), мне нравится просматривать загружаемые им ролики на самые разные темы. Вот хочу поделиться с вами технологией отливки церковных колоколов. Насколько я понял, эта мастерская не в России, но к какой конфессии принадлежит - это неважно. Ролик всего лишь расширяет кругозор, поскольку в разных местах принцип всё равно остаётся одинаковым.
Когда я слышу звон колоколов, то иногда думаю: а что за умелые руки мастеров создали эти звуки? Одно дело благодарить звонарей, но более нужно бы помолиться о здравии литейщиков.
Вот сам фильм
А вот интересная информация, взята здесь: ссылка
Литье колоколов
Исторически первое описание технологии колокольного литья дал монах Теофил, живший на рубеже XI-XII в.в. Изготовление колоколов расценивалось как священнодействие и с VI в., с основания ордена бенедиктинцев, находилось во введении состоящих в нем монахов.
В XVI веке появилась книга В.Бирингуччо “Пиротехния” на многие века вперед предопределившая технологию колокольного литья. Вот суть этого процесса. Колокол льют в литейной яме. Форма будущего колокола состоит из двух частей: глиняной болванки и верхней части – кожуха из железных прутьев, обмазанных глиной.
Болванку и кожух обмазывают жиром, обжигают. Кожух поднимают. Мастер входит под кожух и на внутренней его стороне накладывает надписи, орнаменты. Кожух ставится на место. Пустота между кожухом и болваном заливается расплавленной бронзой. Вся форма при этом засыпается землей, чтобы ее не разорвало. На краях ямы устраиваются плавильные печи. По желобам жидкий металл заливается в форму. Остывает колокол около недели. Потом колокол освобождают от земли, снимают кожух, вынимают из ямы, шлифуют и отделывают.
Технология литья не изменилась и в XX веке. В начале XX века на заводе братьев Усачевых в Валдае колокола отливали следующим образом. “Процесс создания колокола сложен и стар. Механизация не коснулась этого производства. Как 300 лет назад лили, так и теперь льют.
Прежде всего, на кирпичном фундаменте выкладывается угловатая кирпичная форма, по размерам близкая к будущему колоколу. В середине – довольно широкое отверстие. Сверху форма обмазывается глиной и приглаживается лекалом – это будет внутренняя часть колокола – ступа. После основательной сушки и обмазки жиром, мастер начинает покрывать форму жидкой глиной до тех пор, пока новый слой не достигнет нужной толщины, а именно, толщины будущих стенок “тела” колокола. Сушка. “Тело” готово.
Надо его еще украсить и дать внешность. Для орнаментов заготовлены деревянные доски-трафареты. Накатывая на них массу (смесь воска, смолы и др.) получают выпуклые отпечатки орнаментов на восковых лентах. Эти ленты украшений подкрепляются на глиняное “тело” так же, как и надписи.
Украшение окончено, и, после смазки формы салом, ее густо облепляют толстым слоем глины - “кожухом”. Всю форму хорошо просушивают, разводя костер под фундаментом. От тепла тает воск, но отпечатки украшений остаются на внутренней стороне кожуха. Кожух снимается и толщина “тела” легко отбивается.
Так получаются две формы: ступа – для внутренней части колокола, и кожух для наружной, а между ними – полое пространство, которое заполнится металлом.
Форма готова для спуска в литейную яму. После опускания формы к ней приделывают глиняную трубку (по ней потечет металл) и плотно забивают яму землей. К выходящей на поверхность трубке проводят кирпичный желоб от выходного отверстия.
Тем временем печь уже накалила металл до 1200 градусов. На краю желоба в ряд ставят чугунные гири, чтобы напор металла не разнес желоб. Тяжелым обухом выбивается глиняная замазка, и из выходного отверстия печи вырывается жидкий металл, льется по желобу, уходит в форму.
Два-три дня форма охлаждается в земле. На третий день ее выкапывают, разбивают глиняный кожух, выбивают ступу и тускло-красный колокол извлекается из ямы. Шлифовка, отделка занимают день, два. Затем наступает решительный момент: пробуют звон”.
Если кто-то теперь захотел узнать побольше, достаточно начать с поисковой фразы "литье колоколов".
Поисковые системы помогут, а я рекомендую посетить православный сайт "Колокола.ру".
azbyka.ru