УМК ВиН correp / КЛ / Лекция 3. Основные понятия о посадках. Натяги и зазоры
Лекция 3. Основные понятия о посадках
Третья лекция
2. Основные понятия о посадках (сопряжениях)
План лекции
Понятия зазора и натяга.
Виды посадок.
Образование посадок в системе отверстия и в системе вала.
Ранее были введены понятия вала и отверстия как соответственно наружного охватываемого и внутреннего охватывающего элементов. При сопряжении этих элементов, принадлежащих двум разным деталям, получают ту или иную посадку.
Посадка – характер соединения двух деталей, определяемый значениями получающихся в этом соединении зазоров и натягов.
Зазор – разность между размерами отверстия и вала до сборки:
S = D – d.
Зазор характеризует свободу относительного перемещения соединяемых деталей. Чем больше зазор – тем большая свобода относительного перемещения элементов сопряжения. Можно вспомнить еще термин люфт (нем. – Luft), обозначающий зазор между сопряженными поверхностями деталей узла.
Если размер вала больше размера отверстия, в соединении получается положительный натяг. Натяг – разность размеров вала и отверстия до сборки:
N = d – D.
И зазор и натяг можно, вообще говоря, рассматривать как величины алгебраические, считая, что S = - N.
Понятие «посадка» относится к совокупности пар сопрягаемых элементов, размер каждого из которых является случайной величиной. Поле рассеивания данной случайной величины ограничено заданными предельными отклонениями. Поэтому получающиеся при сборке зазоры (натяги) – также случайные величины.
Характер сопряжения (то есть посадки) удобно представлять на схеме полей допусков отверстия и вала [1]. В геометрической интерпретации полем допуска является часть плоскости, ограниченная сверху и снизу линиями предельных размеров (отклонений). Отклонения ES и EI (es и ei) на схемах полей допусков (рис. 2.1) откладывают от линии номинального размера – нулевой линии - в мкм.
Рис. 2.1
Конкретное содержание приведенной схемы полей допусков может быть лучше понято из рис. 2.2, где показан этот же характер соединения.
Рис. 2.2
В зависимости от взаиморасположения полей допусков сопрягаемых элементов посадки бывают трех видов:
- с гарантированным зазором, P(S > 0) = 1;
- с гарантированным натягом, P(S < 0) = 1 или P(N > 0) = 1;
- переходные, то есть 0 < P(s) < 1.
Разумеется, P(S > 0) + P(N > 0) = 1.
Мера точности соединения – допуск посадки. Подобно тому как допуск размера есть разность его максимального и минимального предельных значений, допуск посадки находится как разность наибольшего и наименьшего зазоров:
TS = S max – S min = D max – d min – (D min – d max) = TD + Td .
Полученное соотношение иллюстрирует простую мысль: высокая точность соединения может быть обеспечена только при соответствующей высокой точности размеров сопрягаемых элементов.
Посадки назначаются, как правило, либо в системе отверстия либо в системе вала.
Слово «система» означает порядок, закономерность. Закономерность, прежде всего, выражается в том, что поле допуска одной из деталей сопряжения имеет вполне определенное постоянное расположение относительно линии номинального размера. Такая деталь именуется основной [2]. Постоянная определенность расположения поля допуска основной детали – в том, что оно соприкасается с нулевой линией и опрокинуто «в материал детали» (так называемый принцип «экономии металла»).
Посадки в системе отверстия получаются сочетанием различных полей допусков наружных охватываемых элементов соединений (валов) с полем допуска основного отверстия (рис. 2.3):
Рис. 2.3
Здесь верхнее отклонение отверстия для всех сопряжений постоянно и равно допуску размера отверстия (ES = TD = const), а нижнее отклонение отверстия равно нулю (EI = 0). Предельные же отклонения сопрягаемого с этим отверстием вала выбираются соответственно характеру назначаемого сопряжения.
Рис. 2.4
Здесь es = 0, ei = - Td; в зависимости же от требуемого характера соединения выбирают предельные отклонения отверстия (ES, EI).
Предпочтительнее применение системы отверстия: изготовление внутреннего элемента (отверстия) зачастую сложнее и дороже; для обработки отверстий обычно используется мерный режущий инструмент (например, развертки, протяжки), номенклатуру которого следует снижать.
В отдельных случаях [3] выгоднее система вала:
- применения стандартизованных комплектующих, наружные элементы которых надо различным образом (то есть с образованием разных посадок) сопрягать с отверстиями других деталей;
- использования одного и того же вала для получения нескольких различных сопряжений с охватывающими внутренними элементами других деталей;
- использования для изготовления деталей стандартных калиброванных прутков без их механической обработки.
Литература
Белкин В.М. Допуски и посадки (Основные нормы взаимозаменяемости). – М.: Машиностроение, 1992.- 528 с.
Дунин-Барковский И.В. Взаимозаменяемость, стандартизация и технические измерения. – М.: Издательство стандартов, 1987. - 352 с.
Анухин В.И. Допуски и посадки: Учебное пособие. – СПб.: Питер, 2008. – 207 с.
studfiles.net
Посадки, зазор и натяг - Измерения
Посадки, зазор и натягКатегория:
Измерения
Посадки, зазор и натягВзаимное соединение парных деталей называется посадкой. Посадки подразделяются на подвижные и неподвижные. Различие между ними состоит в том, что у подвижных посадок должна быть обеспечена возможность взаимного перемещения деталей, а у неподвижных, наоборот, жесткое и прочное соединение.
В подвижных посадках диаметр отверстия должен быть больше диаметра вала. Если в собранном механизме вал сидит в отверстии свободно и может в нем вращаться, это означает, что диаметр отверстия больше диаметра вала. Свободное пространство между поверхностями отверстия и вала, равное разности между их диаметрами, называется зазором. Посадка одной детали в другую с зазором называется свободной или подвижной.
Если вал сидит в отверстии туго, то есть запрессован в нем и не может вращаться, такая посадка называется неподвижной. Она возможна в том случае, если диаметр отверстия несколько меньше диаметра вала. Превышение диаметра вала над диаметром отверстия называется натягом. В зависимости от размеров соединяемых деталей зазор и натяг изменяются от наименьшей величины до наибольшей. Поэтому различаются: наибольший зазор и наименьший зазор, наибольший натяг и наименьший натяг (рис. 1).
Рис. 1. Графическое изображение зазора и натяга
Наибольший зазор — разность между наибольшим предельным размером отверстия и наименьшим предельным размером вала.
Наименьший зазор—разность между наименьшим предельным размером отверстия и наибольшим предельным размером вала.
Наибольший натяг — разность между наибольшим предельным размером вала и наименьшим предельным размером отверстия.
Наименьший натяг — разность между наименьшим предельным размером вала и наибольшим предельным размером отверстия.
Допуск зазора или натяга — разность между наибольшими и наименьшими зазорами или между наибольшими и наименьшими натягами. Допуск зазора или натяга равен сумме допусков вала и отверстия.
При соединении деталей неподвижной посадкой необходимо приложить некоторое усилие, зависящее от требуемой плотности соединения. Одни детали соединяются от руки, другие — ударом свинцового или деревянного молотка, третьи — при помощи пресса и т. д. Плотность посадки зависит от назначения соединяемых деталей.
Напряженная — Н Плотная — П
Горячая посадка (Гр) применяется для неразъемного соединения деталей. Перед сборкой деталь с отверстием нагревают. Под влиянием нагрева деталь расширяется, диаметр отверстия увеличивается и деталь свободно насаживается на холодный вал, плотно обхватывая его после остывания. Для этой же цели применяют холод, сильно охлаждая вал, в результате чего он свободно входит в отверстие.
Прессовую (Пр) и легкопрессовую (Пл) по с a flit и применяют в тех случаях, когда нужно жестко соединить детали без закрепления их шпонками, шпильками или стопорами. Эта посадка осуществляется под значительным давлением при помощи прессов. Прибегают к ней при установке зубчатых венцов на ободы зубчатых колес, втулок в подшипниках, пальцев в кривошипах и т. д.
Глухая посадка (Г) применяется для частей, которые плотно сидят в соединении и редко разбираются. Производится она давлением пресса или ударами молотка; чтобы не допустить проворачивания (например втулок в корпусах подшипников, соединительных муфт на концах валов, упорных колец), в соединяемых частях ставят шпонки и шпильки.
Тугая посадка (Т) применяется для получения прочных, но более или менее часто разбираемых соединений. Проворачивание и сдвиг соединяемых деталей предотвращаются шпонками, шпильками, стопорами. Тугой является посадка шкивов, зубчатых колес, колец шарикоподшипников.
Напряженная посадка (Н) применяется в тех случаях, когда детали должны быть соединены прочно, но в то же время должна быть обеспечена возможность собирать их в соединение или разбирать полученное соединение с незначительными усилиями. Этим способом осуществляют посадку зубчатых колес, фланцев, соединительных муфт, маховичков, рукояток.
Плотная посадка (П) применяется для соединения деталей, которые не должны смещаться сами собой, но должны легко поддаваться сборке или разборке от руки или ударам деревянного молотка; применяется она для сменных зубчатых колес, съемных маховичков, рукояток, установочных колец.
Скользящая посадка (С) применяется для соединения деталей, которые должны плотно входить одна в другую и при смазанных поверхностях легко передвигаться от руки, но иметь точное направление. Скользящую посадку используют для сменных колес на валах, для шпинделей задней бабки, рукояток, маховичков и т. п.
Посадка движения (Д) — самая точная из подвижных посадок, применяемая для соединения деталей с небольшим зазором, например для подшипников станков, передвижных зубчатых колес и т. п.
Ходовая посадка (X) применяется для соединения деталей, которые должны перемещаться одна в другой с заметным зазором. Пример: валы в червячных передачах, распорные кольца, фрикционные муфты, ползуны в направляющих.
Легкоходовая посадка (Л) применяется для соединения деталей, которые должны перемещаться одна в другой со значительным зазором (ходовые винты суппортов, валы с несколькими подшипниками).
Широкоходовая посадка (Ш)—наиболее свободная, с большими зазорами, применяемая во всех случаях соединения деталей, сильно нагревающихся при работе.
Перечисленные выше посадки относятся к первому и ко второму классам точности (см. ниже). При посадках первого клас-1 я предъявляются особенно высокие требования к чистоте поверхности и качеству соединения.
Существуют еще посадки третьего, четвертого и пятого классов точности. Третий класс охватывает шесть посадок, из них три прессовые (однотипные с посадками второго класса) и три подвижные: скользящая, ходовая и широкоходовая.
Скользящая посадка (С3) применяется для соединения деталей, которые должны свободно входить одна в другую и легко перемещаться одна в другой (например установочные кольца в трансмиссиях, съемные рукоятки, распорные втулки).
Ходовая посадка (Х3) применяется для соединения деталей, которые должны входить одна в другую и перемещаться одна относительно другой со значительным зазором (например подшипники насосов, холостые канатные шкивы, кулисные камни, соединительные муфты).
Широк оводовая посадка (Ш3) применяется для соединения деталей, которые должны перемещаться одна в другой с большим зазором (детали сельскохозяйственных машин, холостые шкивы, длинные валы).
Подвижные посадки четвертого и пятого классов точности применяются в машиностроении для соединения деталей с большими зазорами.
Читать далее:
Классы точности
Статьи по теме:
pereosnastka.ru
ОПРЕДЕЛЕНИЕ ЗАЗОРОВ И НАТЯГОВ В СОЕДИНЕНИЯХ
Стр 1 из 4Следующая ⇒Введение
Одним из основных условий, способствующих повышению качества изготовления и ремонта машин при наименьших затратах, является внедрение в производство принципов взаимозаменяемости, прогрессивных технологий и методов контроля.
Метрология, стандартизация и квалиметрия, изучает на основе системы стандартов вопросы количественной оценки качества технических изделий, обеспечения точности их геометрических и функциональных параметров как необходимого условия обеспечения взаимозаменяемости, надежности и долговечности, является научно–методическим фундаментом качества проектирования, производства, эксплуатации и ремонт машин и оборудования.
![]() |
ОПРЕДЕЛЕНИЕ ЗАЗОРОВ И НАТЯГОВ В СОЕДИНЕНИЯХ
В данном задании определяем предельные размеры, допуски, зазоры(натяги) для трех посадок: с зазором, с натягом и переходной:
Исходные данные: номинальный размер d = 55 мм соединения посадки с зазоромН7/с8 , с натягом Н7/r6, переходная k7/6
1.1 По СТСЭВ 144-75 (приложение 4-7.[4]) находим значения предельных отклонений размеров соединенных деталей и определяются их предельные размеры и допуски:
1.1.1 Для соединения с зазором:
а) для отверстия D max = DH + ES = 55+0.030 = 55,030 мм;
Dmin = DH + EI = 55+0 =55 мм;
TD = D max - Dmin = ES – EI = 55,030+55,0 = 0,030 мм;
б) для вала dmax = dн +es = 55- 0,060 = 54,940 мм;
dmin = dн + ei = 55-0,106=54,894 мм;
Td = dmax - dmin = es-ei = 54,940+54,894 =0,046 мм.
1.1.2 Для соединения с натягом:
а) для отверстия
D max = DH + ES = 55+0.030 = 55,030 мм;
Dmin = DH + EI = 55+0 =55 мм;
TD = D max - Dmin = ES – EI = 55,030+55,0 = 0,030 мм;
б) для вала dmax = dн +es = 55 + 0,060 =55,060 мм;
dmin = dн + ei = 55+ 0,041 = 55,041 мм;
Td = dmax - dmin = es-ei = 55,041– 55,041 = 0.019 мм;
1.1.3 Для переходного соединения:
а) для отверстия D max = DH + ES = 110+0.010 = 110.010 мм;
Dmin = DH + EI = 110 – 0.025 = 109.975 мм;
TD = D max - Dmin = 0.010+0.025 =0.035мм;
б) для вала dmax = dн +es = 110+0 = 110 мм;
dmin = dн + ei = 110 – 0.022 = 109.978 мм;
Td = dmax - dmin = es-ei = 0+ 0.022 = 0.022мм;
1.2 Определяем предельные и средние зазоры (натяги) и допуски пасадок
а) посадки с зазором
Smax = Dmax– dmin = ES – ei = 55,030+54,894 = 0,136 мм;
Smin = Dmin – dmax = EI – es = 55,0+54,940 = 0,060 мм;
Sс = 0.5(Smax+ Smin) =0.5(0,136+0,060) = 0,098 мм;
TS = Smax – Smin = TD + Td = 0,030 +0,046 =0,076 мм;
б) для посадки с гарантированным натягом
Nmax = dmax – Dmin =es – EI = 55 –0 = 0.076 мм;
Nmin = dmin – Dmax = ei –ES = 0.054– 0.035 = 0.019 мм;
Nc = 0.5(Nmax + Nmin) = 0.5(0.076 + 0.019) = 0.0475 мм;
TN = Nmax+ Nmin = TD + Td = 0.035+0.022 = 0.057 мм;
в) для переходной посадки
Nmax = dmax – Dmin = es – EI = 0 + 0.025 = 0.0025 мм;
Smax = Dmax– dmin = ES – ei = 0.010 +0.022 = 0.032 мм;
TN(S) = TD +Td = 0.035 + 0.022 = 0.057 мм;
1.3 Выбираем шероховатость соприкосаемых поверхностей (приложение 10) и вид окончательной механической обработки деталей (приложение 11)
а) для соединения с зазором .
Шероховатость поверхности отверстия 3,2 мкм;
Вид механической обработки: развертывание чистовое.
Шероховатость прочности вала 3.2 мкм;
Вид механической обработки: обмачивание продольной подачей чистовое
б) для соединения с натягом.
Шероховатость поверхности отверстия 3.2 мкм;
Вид механической обработки: развертывание чистовое
Шероховатость поверхности вала 1.6 мкм;
Вид механической обработки: полирование обычное
в) для переходного соединения
Шероховатость поверхности отверстия 3,2 мкм;.
Вид механической обработки: развертывание чистовое
Шероховатость поверхности вала 1.6 мкм;
Вид механической обработки: полирование обычное
1.4 Строим схемы расположения полей допусков отверстия и вала с указанием на них номинальных размеров, предельных отклонений, предельных и средних зазоров и натягов.
Схемы расположений допусков.
посадки с зазором посадки с натягом переходной посадки
![]() |
Рисунок 1. Схема расположения полей допусков посадки с зазором
1.5 Вычерчиваем эскизы соеденении и проставляем условные обозначения и цифровые значения расположенная полей допусков и шероховатостей поверхностей (рисунок 4–6).
Эскизы соединения с зазором и соединяемых деталей
![]() |
Эскизы соединения с натягом и соединяемых деталей
Эскизы переходного соединения и соединяемых деталей
Рисунок 2. Эскизы соединения и соединяемых деталей
РАСЧЕТ И ВЫБОР ПОСАДОК
РАСЧЕТ РАЗМЕРНОЙ ЦЕПИ
Основное положения
При выполнении задачи необходимо по чертежу узла, а также задонному номинальному размеру и предельным отклонениям замыкающего звена (таблица 9 и рисунок 2,3 приложение 32 [4]) составить линейную размерную цепь, изобразить ее схему и рассчитать допуски и предельные отклонения всех составляющих звеньев (прямая задача). Расчет следует произвести методом полной взаимозаменяемости (метод максимума – минимума) и вероятностным методом.
Расчет вероятностным методом выполняется при условии рассеяния размеров всех звеньев по нормальному закону, при котором риск выхода размеров за пределы допуска составляет 0.27% . При этом коэффициенты относительной асимметрии звеньев равны нулю, т.е. математические ожидания размеров совпадает с серединами полей допусков.
Исходные данные: Es0 = 0.10; Ei0 = –0.20; [A0] =2;
7.2 Методика решения прямой задачи методом взаимозаменяемости
7.2.1 По заданным значениям номинального размера [A0] и предельных отклонений [ES0], [EI0] исходного (замыкающего) звена определяем его предельные размеры ([A0max], [A0min]), координата середины поля допуска [Δc0] и допуск [T0].
[A0max] = [A0] + [ES0] = 2 + 0.10 = 2.10 мм;
[A0min] = [A0] + [EI0] = 2 – 0.20 = 1.80 мм;
[T0] = [A0max] – [A0min] = 2.10 – 1.80 = 0.300 мм;
7.2.2 Определяем номинальное расчетное значение исходного звена. Если выполняется условие то размерная цепь составлена правильно.
A0 = [A0] = 2 = 2 – цепь составлена правильно.
7.2.3 Определяем среднее число единиц допуска зависимых звеньев:
7.2.4 По полученному значению ас определяем квалитет изготовления зависимых звеньев и их допуски (приложение 1,2 [4]). Если расчетное значение ас не совпадает с табличным ат и ас имеет какое–то промежуточное значение, то на часть звеньев, более сложных в изготовлении, можно назначить допуски по ближайшему грубому квалитету, а на остольные – по более точному. Допуски на зависимые звенья берем по 9 квалитету IT9 (приложения 1,2 [4]).
3IT9 T = 0.020мм; ;
4IT9 T = 0.03 мм; ;
29IT9 T = 0.050 мм; ;
300≤300 – условие выполняется.
7.2.5 Предельное отклонения для охватывающих размеров рекомендуется определять кА для основного отверстия (Н), для охватываемых – как для основного вала (h0, для свободных размеров (глубина отверстия, ширина уступа, межцентровое расстояние) их принимают симметричными (Js).
7.2.6 Определяем среднее и предельное отклонения и предельные размеры замыкающего звена.
7.2.7 Проверяем правильность назначения предельных отклонений из выполнения условия:
7.2.8 Уловия не выполняется прибегаем к решению размерной цепи с корректирующим звеном в следующей последовательности:
а) на все зависимые соотношение звенья, кроме корректирующего, оставляют принятые значения предельных отклонений;
б) определяем допуск корректирующего звена:
в) определяем среднее и предельное отклонения корректирующего звена:
Выбирае посадку на корректирующие звено е8 с предельным отклонением es = –40 мкм; ei = –73 мкм;
;
;
7.2.9 задачи размерных расчетов считается решенные
достигнуто соотношение.
7.2.10 Результаты расчетов размерной цепи методом полной взаимозаменяемости занесем в таблицу 7.1.
Таблица 7.1
Результаты расчетов размерной цепи
(Метод взаимозаменяемости)
Обозначение звеньев | Нормальный размер, мм | Поле допуска | Передаточное отношение | Допуск, мм | Предельные отклонения, мм | |
ES | EI | |||||
A1 | Js | +1 | 0.020 | +10 | -10 | |
A2 | Js | -1 | 0.03 | +15 | -15 | |
A3 | H | +1 | 0.050 | +40 | -73 | |
А0 | - | -1 | 0.300 | +275 | -25 |
БИБЛИОГРАФИЧЕСКИЙ СПИСОК
1.Допуски и посадки: Справочник: В 2 ч. /В. Д. Мягков, М. А. Палей, А. Б. Романов, В. А. Брагинский. Л.: Машиностроение, 1983.
2.Допуски и посадки: Справочник: В 2 ч. /М. А. Палей, А. Б. Романов, В. А. Брагинский Л.: Политехника, 1991.
3.Серый И. С. Взаимозаменяемость, стандартизация и техническое изделие. М.: Агропомиздат, 1987. 367.
4. Курсовое проектирование по метрологии, стандартизации и квалитрии: Учеб. Пособие / П. В. Сенин. – Саранск: Изд–во Мордов. ун–та, 1997. –80 с. – ISBN 5 – 7103 – 0352 –6.
Реферат
Данная курсовая работа содержит 36 страницы, 17 рисунков, 1 схему, 7 таблиц, библиографический список состоит из 4 источников.
РАЗМЕР, ПОСАДКА, ДОПУСК, ОТКЛОНЕНИЕ, ОТВЕРСТИЕ, ВАЛ.
Цель курсовой работы: систематизация, закрепление и расширение теоретических знаний и их применение для решения конкретных научно-технических и производственных задач.
Полученные результаты: определены зазоры и натяги в соединениях, рассчитаны и выбраны посадки с зазором и натягом, рассчитаны и выбраны посадки для соединений с подшипником качения, выбраны посадки шпоночных соединений, шлицевых соединений, рассчитаны исполнительные размеры рабочих калибров и выбраны универсальные средства измерений, рассчитана размерная цепь.
Содержание
Введение ………………………………………………………………….……
1. Определение зазоров и натягов в соединениях……………………..5
2. Расчет и выбор посадок……………………………………………….11
Расчет и выбор посадок с зазором……………………………….11
Расчет и выбор посадок с натягом……………………….………13
Выбор переходных посадок и определение вероятности
появления соединений с натягом и зазором………..….……….16
3. Расчет и выбор посадок для соединений с подшипником качения.. 18
4. Выбор посадок шпоночных соединений…………………….………21
5. Выбор посадок шлицевых соединений……………………….……..23
6. Расчет исполнительных размеры рабочих калибров и выбор
универсальных средств измерений……………………………….…26
7. Расчет размерной цепи……………………………………………….30
Библиографический список…………………………………………………..36
Введение
Повышение качества продукции – одно из главных условий подъема экономики. Успешное решение проблему повышения качества продукции определяется рядом технических, организационных, экономических факторов. Сегодня , когда для производства одной машины необходимо взаимодействие между несколькими предприятиями различных отраслей промышленности, вопросы качества продукции требуют для своего решения дальнейшего развития и совершенствования системы стандартизации.
Одним из основных условий, способствующих повышению качества изготовления и ремонта машин при наименьших затратах, является внедрение в производство принципов взаимозаменяемости, прогрессивных технологий и методов контроля.
Взаимозаменяемость требует определенного уровня измерительной техники, также являющейся объектов стандартизации. Поэтому подготовка современного инженера включает освоение широкого круга вопросов, связанных со стандартизацией, взаимозаменяемостью и сертификацией.
Введение
Одним из основных условий, способствующих повышению качества изготовления и ремонта машин при наименьших затратах, является внедрение в производство принципов взаимозаменяемости, прогрессивных технологий и методов контроля.
Метрология, стандартизация и квалиметрия, изучает на основе системы стандартов вопросы количественной оценки качества технических изделий, обеспечения точности их геометрических и функциональных параметров как необходимого условия обеспечения взаимозаменяемости, надежности и долговечности, является научно–методическим фундаментом качества проектирования, производства, эксплуатации и ремонт машин и оборудования.
![]() |
ОПРЕДЕЛЕНИЕ ЗАЗОРОВ И НАТЯГОВ В СОЕДИНЕНИЯХ
В данном задании определяем предельные размеры, допуски, зазоры(натяги) для трех посадок: с зазором, с натягом и переходной:
Исходные данные: номинальный размер d = 55 мм соединения посадки с зазоромН7/с8 , с натягом Н7/r6, переходная k7/6
1.1 По СТСЭВ 144-75 (приложение 4-7.[4]) находим значения предельных отклонений размеров соединенных деталей и определяются их предельные размеры и допуски:
1.1.1 Для соединения с зазором:
а) для отверстия D max = DH + ES = 55+0.030 = 55,030 мм;
Dmin = DH + EI = 55+0 =55 мм;
TD = D max - Dmin = ES – EI = 55,030+55,0 = 0,030 мм;
б) для вала dmax = dн +es = 55- 0,060 = 54,940 мм;
dmin = dн + ei = 55-0,106=54,894 мм;
Td = dmax - dmin = es-ei = 54,940+54,894 =0,046 мм.
1.1.2 Для соединения с натягом:
а) для отверстия
D max = DH + ES = 55+0.030 = 55,030 мм;
Dmin = DH + EI = 55+0 =55 мм;
TD = D max - Dmin = ES – EI = 55,030+55,0 = 0,030 мм;
б) для вала dmax = dн +es = 55 + 0,060 =55,060 мм;
dmin = dн + ei = 55+ 0,041 = 55,041 мм;
Td = dmax - dmin = es-ei = 55,041– 55,041 = 0.019 мм;
1.1.3 Для переходного соединения:
а) для отверстия D max = DH + ES = 110+0.010 = 110.010 мм;
Dmin = DH + EI = 110 – 0.025 = 109.975 мм;
TD = D max - Dmin = 0.010+0.025 =0.035мм;
б) для вала dmax = dн +es = 110+0 = 110 мм;
dmin = dн + ei = 110 – 0.022 = 109.978 мм;
Td = dmax - dmin = es-ei = 0+ 0.022 = 0.022мм;
1.2 Определяем предельные и средние зазоры (натяги) и допуски пасадок
а) посадки с зазором
Smax = Dmax– dmin = ES – ei = 55,030+54,894 = 0,136 мм;
Smin = Dmin – dmax = EI – es = 55,0+54,940 = 0,060 мм;
Sс = 0.5(Smax+ Smin) =0.5(0,136+0,060) = 0,098 мм;
TS = Smax – Smin = TD + Td = 0,030 +0,046 =0,076 мм;
б) для посадки с гарантированным натягом
Nmax = dmax – Dmin =es – EI = 55 –0 = 0.076 мм;
Nmin = dmin – Dmax = ei –ES = 0.054– 0.035 = 0.019 мм;
Nc = 0.5(Nmax + Nmin) = 0.5(0.076 + 0.019) = 0.0475 мм;
TN = Nmax+ Nmin = TD + Td = 0.035+0.022 = 0.057 мм;
в) для переходной посадки
Nmax = dmax – Dmin = es – EI = 0 + 0.025 = 0.0025 мм;
Smax = Dmax– dmin = ES – ei = 0.010 +0.022 = 0.032 мм;
TN(S) = TD +Td = 0.035 + 0.022 = 0.057 мм;
1.3 Выбираем шероховатость соприкосаемых поверхностей (приложение 10) и вид окончательной механической обработки деталей (приложение 11)
а) для соединения с зазором .
Шероховатость поверхности отверстия 3,2 мкм;
Вид механической обработки: развертывание чистовое.
Шероховатость прочности вала 3.2 мкм;
Вид механической обработки: обмачивание продольной подачей чистовое
б) для соединения с натягом.
Шероховатость поверхности отверстия 3.2 мкм;
Вид механической обработки: развертывание чистовое
Шероховатость поверхности вала 1.6 мкм;
Вид механической обработки: полирование обычное
в) для переходного соединения
Шероховатость поверхности отверстия 3,2 мкм;.
Вид механической обработки: развертывание чистовое
Шероховатость поверхности вала 1.6 мкм;
Вид механической обработки: полирование обычное
1.4 Строим схемы расположения полей допусков отверстия и вала с указанием на них номинальных размеров, предельных отклонений, предельных и средних зазоров и натягов.
Схемы расположений допусков.
посадки с зазором посадки с натягом переходной посадки
![]() |
Рисунок 1. Схема расположения полей допусков посадки с зазором
1.5 Вычерчиваем эскизы соеденении и проставляем условные обозначения и цифровые значения расположенная полей допусков и шероховатостей поверхностей (рисунок 4–6).
Эскизы соединения с зазором и соединяемых деталей
![]() |
Эскизы соединения с натягом и соединяемых деталей
Эскизы переходного соединения и соединяемых деталей
Рисунок 2. Эскизы соединения и соединяемых деталей
РАСЧЕТ И ВЫБОР ПОСАДОК
Читайте также:
lektsia.com
Типы посадок. Предельные зазоры и натяги. Допуск посадки. 1 страница
⇐ ПредыдущаяСтр 8 из 36Следующая ⇒Вследствие колебания размеров деталей при изготовлении значения зазоров и натягов при сборке деталей также будут колебаться. Действительным зазором или действительным натягом называются соответственно зазор или натяг, определяемый разностью действительных размеров отверстия и вала. Действительный зазор или натяг должны находиться между двумя предельными значениями, называемыми наименьшим и наибольшим зазором или натягом. При этом наибольший и наименьший зазор обозначается Smax и Smin, а наибольший и наименьший натяг - Nmax и N min.
Предельные зазоры или натяги чертежами непосредственно не устанавливаются. Для того чтобы обеспечить независимое изготовление деталей соединения, а на сборке получить зазоры и натяги в требуемых пределах без дополнительной пригонки или регулировки деталей, необходимо назначить посадку в виде определенного сочетания полей допусков отверстия и вала.
При назначении посадок номинальный размер для отверстия и вала, составляющих соединение, является общим и называется номинальным размером соединения или посадки.
В зависимости от расположения полей допусков отверстия и вала различают посадки 3х типов: с зазором; с натягом; переходные.
В посадке с зазором поле допуска отверстия расположено над полем допуска вала.
S max = D max – d min = ES-ei, S min = D min – d max = EI-es,S с=(S max + S min)/2
T s= S max – S min = (ES-ei)-(EI-es)=T D+T d
Рис.1.3 Схема Полей допусков посадки с зазором.
Значение S min называют “ гарантированным зазором “.
К посадкам с зазором относятся также так называемые скользящие посадки, в которых нижняя граница поля допуска отверстия совпадает с верхней границей поля допуска вала.
Рис. 1.4. Схема скользящей посадки.
Посадкой с натягом называют посадку, когда поле допуска отверстия расположено под полем допуска вала.
N max = d max – d min = es-EI
N min = d min – d max = ei-ES
N с=(N max + N min)/2
T N= N max – N min =(es-EI)-(ei-ES)=T D+T d
Рис. 1.5. Схема полей допусков посадки с натягом.
Переходной посадкой называется посадка, при которой возможно получение как зазора, так и натяга. При такой посадке поля допусков отверстия и вала частично перекрывают друг друга. Она характеризуется наибольшими значениями натяга и зазора.
N max = es - EI.
S max = ES- ei
Рис.1.6. Схема полей допусков переходной посадки.
Наибольший зазор переходной посадки часто представляют в виде отрицательного наименьшего натяга: -N min = S max = ei-ES.
Допуск T N= Ts = N max - N min = S max – S min =(ES-EI)+(es - ei)= T D +T d.
Т.о. для любой посадки, независимо от ее типа, допуск посадки есть сумма допусков отверстия и вала, составляющих соединение.
При расчете и выборе посадок нас могут интересовать не только предельные зазоры или натяги, но и средние, обычно наиболее вероятные, зазоры и натяги.
, (1.1.)
или
, (1.2.)
(1.3.)
В переходных посадках средний натяг рассчитывается по формуле:
(1.4.)
(результат со знаком « - » означает, что среднее значение для посадки соответствует зазору).
Здесь Ес и ei – средние отклонения.
(1.5.)
Вследствие различных причин действительные значения геометрических, механических и других параметров деталей и изделий могут отличаться от расчетных, т.е. могут иметь погрешность.
Погрешность Δx – это разность между действительным значением Хr и расчетным Храсч размерами: .
Расчетным размером для валов считают наибольший предельный размер, для отверстий – наименьший предельный размер, т.е. переходный предел.
При таких условиях годный вал может иметь только отрицательные погрешности, не превышающие по абсолютному значению допуск, годные отверстия – только положительные и также не превышающие допуск.
Точностью изготовления называют степень приближения действительных значений геометрических или иных параметров деталей и изделий и их заданным значениям, указанным на чертежах или в ТУ.
Различают нормированную точность, т.е. совокупность допускаемых отклонений от расчетных значений и действительную точность, т.е. совокупность действительных отклонений, определенных в результате измерения (с допускаемой погрешностью).
Достичь заданной точности – значит изготовить деталь, у которой погрешность находится в установленных пределах.
Допуск.
Допуском Т называют разность между наибольшим и наименьшим допускаемыми значениями того или иного параметра. Допуском размера называется разность между наибольшим и наименьшим предельными размерами или абсолютное значение алгебраической разности между верхним и нижним отклонениями. Допуск всегда положителен. Он определяет допускаемое поле рассеяния действительных размеров годных деталей в партии, т.е. заданную точность изготовления. С увеличением допуска качество детали, как правило, ухудшается, но стоимость изготовления уменьшается.
Для упрощения допуски можно изображать графически в виде полей допусков. При этом ось изделия всегда находится под схемой. Поле допуска – поле, ограниченное верхним и нижним отклонениями. Поля допуска определяются значением допуска и его положением относительно номинального размера.
При графическом изображении поле допуска заключено между двумя линиями, соответствующими верхнему и нижнему отклонениям относительно нулевой линии. Нулевая линия – линия, соответствующая номинальному размеру, от которой откладывают отклонения размеров при графическом изображении допусков и посадок. Если нулевая линия расположена горизонтально, положительные отклонения откладывают вверх от нее, а отрицательные – вниз.
Систематизация допусков включает отсчет и закономерности построения рядов допусков. Закономерности построения рядов допусков устанавливают функциональные зависимости допусков от значений параметров и их комплексов, эталоны сравнения точности, градации уровней точностей к конкретным деталям типовых соединений.
Для построения систем допусков устанавливают единицу допуска i (I), которая, отражая влияние технологических, конструктивных и метрологических факторов, выражает зависимость допуска от номинального размера, ограничиваемого допуском, и является мерой точности. На основании исследований точности механической обработки цилиндрических деталей из металла установлены следующие единицы допуска:
для размеров до 500 мм
; (1.6)
для размеров свыше 500 до 10000 мм
, (1.7)
где - среднее геометрическое крайних размеров каждого интервала, мм;
- единица допуска, мкм.
Второй член в этих уравнениях учитывает погрешность измерения.
Допуск для любого квалитета
. (1.8)
где - число единиц допуска, зависящее от квалитета и независящее от номинального размера.
В каждом изделии детали разного назначения изготовляют с различной точностью. Для нормирования требуемых уровней точности установлены квалитеты (степени точности для резьбовых соединений, зубчатых передач и др.) изготовления деталей и изделий. Под квалитетом ( франц. - точность) понимают совокупность допусков, характеризуемых постоянной относительной точностью (определяемой коэффициентом ) для номинальных размеров данного диапазона (например, от 1до 500). Точность в пределах одного квалитета зависит только от номинального размера. Для размеров до 500 мм в системе ИСО и е ЕСДП по величине допуска установлено 19 квалитетов:01,0,1,2,…17 (самые точные квалитеты 01 и 0 введены после введения квалитета 1). Для размеров от 500 до 3150 мм установлено 18 квалитетов. Количество квалитетов определялось потребностью различных отраслей промышленности, перспективами повышения точности изделий, границами достижимой точности, а также функциональными и технологическими факторами и принятым значением знаменателя геометрической прогрессии φ, по которой изменяется допуск при переходе от одного квалитета к другому. Квалитет определяет допуск на изготовление, а, следовательно, и соответствующие методы и средства обработки и контроля деталей машин. Допуски системы ИСО обозначаются ; ; . Буквы означают «допуск ИСО». Выше указанные формулы предназначены для определения допусков квалитетов 5 – 17. Число единиц допуска для этих квалитетов соответственно равны: 7, 10, 16, 25, 40, 64, 1200, 160, 250, 400, 640, 1000 и 1600. Значения для квалитетов 6 и грубее образуют геометрическую прогрессию со знаменателем φ = 1,6. Это значит, что при переходе от одного квалитета к следующему, более грубому, допуски возрастают на 60%. Через каждые пять квалитетов допуски увеличиваются в 10 раз. В квалитетах точнее 5 допуски определяют по специальным формулам.
Для размеров менее 1 мм допуски по квалитетам 14…17 не назначают.
Основные отклонения для образования посадок.
Для образования посадок с различными зазорами и натягами в системах ИСО и ЕСДП для размеров до 500 предусмотрено 27 вариантов основных отклонений валов и отверстий. Основное отклонение – это одно из двух (верхнее или нижнее) отклонение, ближайшее к нулевой линии, и определяющее положение поля допуска относительно номинального размера (нулевой линии). Основные отклонения отверстий обозначают прописными буквами латинского алфавита, валов – строчными буквами. Основное отверстие обозначают буквой , основной вал . Отклонения предназначены для образования полей допусков в посадках с зазором; отклонения - в переходных посадках; отклонения в посадках с натягом.
Каждая буква обозначает ряд основных отклонений, значения которых зависят от номинального размера. Абсолютные значения и знак каждого основного отклонения вала определяется по эмпирическим формулам. Основное отклонение вала не зависит от квалитета.
Основные отклонения отверстия построены так, чтобы обеспечить посадки в системе вала, аналогичные посадкам в системе отверстия. Они равны по абсолютной величине и противоположны по знаку основным отклонениям валов, обозначаемых той же буквой. Общее правило определения основных отклонений отверстий:
при основных отклонениях от до ;
при основных отклонениях от до .
Это правило формулируется следующим образом: основное отверстие должно быть симметрично относительно нулевой линии основному отклонению вала, обозначенному той же (но строчной) буквой. Из этого правила сделано исключение для отверстий размером свыше 3 мм с отклонениями до квалитета 8 и с отклонениями до квалитета 7 включительно. Для них установлено специальное правило: , где - разность между допуском рассматриваемого квалитета (с которым сочетается данное основное отклонение) и допуском ближайшего точного квалитета.
Специальное правило формулируется так: две посадки в системе отверстия и в системе вала, в которых отверстие данного квалитета соединяется с валом ближайшего точного квалитета, должны иметь одинаковые зазоры или натяги (например, Ø и Ø ).
Только для отверстий, определяемых по указанному специальному правилу, основные отклонения зависят от сочетаемого с ним квалитета. Во всех остальных случаях основные отклонения, обозначенные данной буквой, остаются неизменными при сочетании с различными квалитетами (изменяется лишь второе предельное отклонение).
У отверстий с отклонениями и у валов с отклонениями (не имеющих основного отклонения) оба предельных отклонения определяются исходя только из допуска соответствующего квалитета. Для отклонений и поле допуска симметрично относительно нулевой линии.
Значения основных отклонений валов и отверстий для размеров до 500 мм приведены соответственно в табл. 7 и 8, значения основных отклонений валов и отверстий для размеров от 500 до 3150 мм – в табл.15 ГОСТ 25346-82.
Поля допусков.
Поле допуска образуется сочетанием одного из основных отклонений с допуском по одному из квалитетов. В соответствии с этим, поле допуска обозначают буквой основного отклонения и номером квалитета, например, для вала а для отверстия
Поле допуска ограничено горизонтальной линией, соответствующей значению основного отклонения. Второе предельное отклонение можно определить по основному отклонению и допуску принятого квалитета. Если основное отклонение верхнее, то нижнее отклонение: для вала ; для отверстия . Если основное отклонение нижнее, то верхнее отклонение: для вала ; а для отверстия (отклонения берут с учетом знака).
Ряды полей допусков для размеров менее 1 мм характеризуются большим набором полей и смещением их в сторону более точных квалитетов по сравнению с основными рядами полей допусков для размеров от 1 до 500 мм (табл. 1 и 2 ГОСТ 25347 – 82). Это отражает высокие точностные требования в приборостроении.
Для размеров свыше 500 до 10000 мм установлено сокращенное число полей допусков, и они смещены в сторону более грубых квалитетов.
В соответствии с рекомендациями ИСО и практикой изготовления деталей и узлов из основных рядов полей допусков для размеров от 1 до 500 мм выделены предпочтительные поля допусков. Они обеспечивают 90…95% посадок общего применения, и это способствует повышению уровня унификации изделий, сокращает номенклатуру режущего и мерительного инструмента, создает благоприятные условия для кооперирования и организации специализированного производства.
Для размеров более 500мм и менее 1 мм предпочтительные поля допусков не выделены.
В отдельных технически обоснованных случаях возможно применение полей допусков, не вошедших в основные ряды. В этом случае поля допусков и соответствующие им числовые значения предельных отклонений для размеров от 1 до 500 мм выбираем в Приложении 3 ГОСТа 25347-82.
Рис.1.7. Основные отклонения валов и отверстий.
Рис.1.8. Расположение полей допусков отверстий и валов в системе основного отверстия (а) и основного вала (б).
Единые принципы построения систем допусков и посадок для типовых соединений деталей машин и других соединений.
Системой допусков и посадок называют совокупность рядов допусков и посадок, закономерно построенных на основе опыта, теоретических и экспериментальных исследований и оформленных в виде стандартов. Она предназначена для выбора минимально необходимых, но достаточных для практики вариантов допусков и посадок типовых соединений изделий машиностроения.
Системы допусков и посадок разрабатываются по отдельным типам соединений, в том числе для гладких цилиндрических поверхностей, для резьбовых, шпоночных и шлицевых сопряжений. Есть также системы допусков углов, формы и расположения поверхностей и ряд других.
Там, где необходимо нормирование сопряжений поверхностей разрабатывают системы допусков и посадок, в противных случаях ограничиваются только системой допусков.
Особую роль в системах допусков играет принциппредпочтительности. Этот принцип проявляется многообразно в качественном отношении (ряды предпочтительности допусков и посадок) и в количественном аспекте (использование рядов предпочтительных чисел в системах).
Два следующих принципа направлены на обеспечение инвариантности (invariantis — не изменяющийся — свойство неизменности по отношению к какому-либо преобразованию, условию, или совокупности преобразований) требований систем допусков и посадок. Принцип измерений при нормальных условиях обеспечивает единообразие информации, получаемой при многократных, независимых измерениях одних и тех же параметров. Принцип ограниченияпредельных контуров необходим для соблюдения единообразия при решении вопроса о годности детали по контролируемому параметру. Несоблюдение этих принципов исключает возможность применения систем допусков и посадок, что видно на примерах возникновения конфликтных ситуаций при нарушениях нормальных условий измерений из-за небрежного или неграмотного подхода, или при произвольной трактовке годности.
Принцип формализации допусков необходим для создания рядов допусков, которые в силу более высокого уровня абстрагирования дают возможность оперативного выбора допусков и точности технологических процессов, исходя из значений допусков вне зависимости от расположения полей.
Формирование рядов допусков в любой системе осуществляется на базе трех остальных принципов.
Принцип увязки допусков с эффективными параметрамипозволяет связать значения допусков с технологическими и (или) конструктивными факторами. Из всего множества влияющих факторов отбираются те, которые характеризуют обобщенное влияние возмущений. Эти факторы (их может быть несколько или один) названы эффективными параметрами.
Необходимость сокращения номенклатуры применяемых допусков, привела к появлению принципа группирования эффективных параметров. Группирование осуществляется так, чтобы значения допусков на краях интервалов умеренно отличались от "теоретических".
Принцип установления уровней относительной точностидает возможность выбирать по аналогии допуски и посадки, а также ориентироваться при выборе технологического оборудования для обеспечения требуемой точности обработки.
Рассмотрим предложенные принципы более подробно.
Принцип предпочтительности — один из основных принципов стандартизации. Различают качественный и количественный аспекты применения этого принципа. Качественная сторона принципа предпочтительности состоит в образовании предпочтительных рядов объектов стандартизации. Объектами могут быть конкретные изделия, детали, их конструктивные элементы и т.д.
Предпочтительных рядов может быть как минимум два, причем всегда устанавливаются уровни предпочтительности. В соответствии с этими уровнями следует выбирать стандартные объекты. Как правило, наиболее предпочтительный ряд включает наименьшее количество объектов стандартизации. Следующие, менее предпочтительные ряды, отличаются расширенной номенклатурой и могут включать объекты предыдущих рядов.
Соблюдение принципа предпочтительности позволяет добиться разумного сокращения применяемой номенклатуры стандартных объектов. В первую очередь следует применять номенклатуру наиболее предпочтительного ряда и переходить к выбору из менее предпочтительных только тогда, когда поставленная задача не имеет удовлетворительного решения.
В стандартных системах допусков и посадок обычно устанавливают ряды с несколькими уровнями предпочтения, например, предпочтительные посадки (первый уровень), рекомендуемые посадки (второй уровень), и, наконец, все стандартные посадки (третий, самый низкий уровень предпочтительности).
Количественная сторона принципа предпочтительности реализуется через использование рядов предпочтительных чисел (ряды Ренара).
Предназначение рядов предпочтительных чисел состоит в том, что их использование обеспечивает упорядочение и определенный экономический эффект при выборе числовых значений любых параметров, на которые нет конкретного нормативного документа (НД) по стандартизации.
Под обеспечением инвариантности деталей понимают такое построение систем допусков и посадок, которое гарантирует геометрическую взаимозаменяемость (инвариантность) деталей, изготовленных по одним и тем же требованиям к номинальным значениям и к точности геометрических параметров.
Чтобы система, обеспечивала инвариантность деталей, должны соблюдаться заложенные в ней условия годности деталей: единообразие трактовки годности и достоверность результатов контроля. Только при соблюдении этих условий результаты измерений можно сопоставить с моделью годной детали, которая задана чертежом, и дать объективное заключение о годности.
Единообразие трактовки годности детали обеспечивается установлением ее предельных контуров, в которые должна "вписываться" реальная деталь. Геометрические параметры контролируемой детали определяются по результатам измерений.
Достоверную информацию о параметрах детали можно получить только при измерении в нормальных условиях.
Нормальные условия подразумевают, что измерения проводят при нормальных значениях влияющих физических величин. Под влияющими величинами понимают те физические величины, которые не являются измеряемыми, но могут вызвать искажение результатов измерений из-за воздействия на сам объект измерения и (или) на применяемые средства измерений. Например, при измерении длины всегда существенное значение имеет температура контролируемой детали, от которой зависит фактическое значение размера. Понятно, что температурный фактор сказывается не только на измеряемом объекте, но и на применяемых средствах измерений.
Проблема установления номенклатуры влияющих величин и областей их нормальных значений настолько сложна, что для случая измерений линейных размеров ей посвящен специальный стандарт (ГОСТ 8.050-73). Указание в некоторых стандартах допусков и посадок значения нормальной температуры 20°С не дает необходимой информации и может служить только формальным ориентиром.
Для однозначного заключения о годности детали по результатам ее измерений в нескольких сечениях необходимо предварительно установить правила разбраковки. Формальными правилами при разбраковке деталей по размерам являются истолкования предельных контуров детали. Деталь признается годной в том случае, если ее реальные контуры, установленные по результатам измерений, не выходят за предельные. При этом экстремальные измеренные значения могут быть равны предельным размерам.
В стандартах систем допусков и посадок истолкование предельных размеров содержится в явном виде (примером может служить истолкование предельных размеров гладких цилиндрических поверхностей) или оформлено косвенно, через установление полей допусков размеров.
Формализованные значения допусков могут быть построены в соответствии с рядами предпочтительных чисел и быть организованы в виде рядов с различными структурами. Например, в стандарте допусков и посадок гладких цилиндрических сопряжении ряды допусков построены в виде массива, где числовое значение допуска установлено в соответствии с интервалом номинальных размеров и уровнем точности.
В системе допусков формы и расположения поверхностей приведены несколько массивов значений допусков, в том числе допуски, связанные со значениями номинальных параметров и уровнями точности, а также абстрактный ряд допусков, построенный в порядке возрастания их числовых значений.
Значения допусков размера необходимо увязывать с параметрами, которые будем называть эффективными или влияющими.
Увязка допуска с эффективными параметрами имеет принципиальное значение как с конструкторских, так и с технологических позиций. Технологический подход к возможным значениям допусков основывается на увязывании допусков с полем практического рассеяния размеров при обработке детали на определенном технологическом оборудовании. Поле рассеяния размеров при обработке каждой детали в партии зависит от множества факторов, которые будут сказываться на силовых и температурных деформациях в системе станок—приспособление— инструмент—деталь (система СПИД). Существенное влияние на разброс размеров в партии деталей может оказывать также износ режущего инструмента.
Понятно, что нельзя выделить один. или несколько влияющих факторов и "привязать" к ним значение допуска. Поэтому эффективные параметры, с которыми увязывают значения допуска, должны отражать некоторое обобщенное влияние множества технологических факторов.
mykonspekts.ru
Поиск Лекций
Посадка – характер соединения двух деталей, определяемый разностью их размеров до сборки [2]. Посадки в системе отверстия – посадки, в которых требуемые зазоры и натяги получаются сочетанием различных полей допусков валов с полем допуска основного отверстия [2]. Посадки в системе вала – посадки, в которых требуемые зазоры и натяги получаются сочетанием различных полей допусков отверстий с полем допуска основного вала [2]. Основной вал – вал, верхнее отклонение которого равно нулю. Основное отверстие – отверстие, нижнее отклонение которого равно нулю [2]. Посадка с зазором – посадка, при которой всегда образуется зазор в соединении, т.е. наименьший предельный размер отверстия больше наибольшего предельного размера вала или равен ему [3]. Наибольший и наименьший зазоры в посадках с зазором определяются:
Допуск посадки с зазором:
Рисунок 4.1 – Схема расположения полей допусков посадки с зазором
Переходная посадка – посадка, при которой возможно получение как зазора, так и натяга в соединении, в зависимости от действительных размеров отверстия и вала [3]. Наибольший и наименьший натяги:
Допуск переходной посадки:
Рисунок 4.2 – Схема расположения полей допусков переходной посадки
Посадка с натягом – посадка, при которой всегда образуется натяг в соединении, т.е. наибольший предельный размер отверстия меньше наименьшего предельного размера вала или равен ему [3]. Наибольший и наименьший натяги:
Допуск посадки с натягом:
Рисунок 4.3 – Схема расположения полей допусков посадки с натягом СПИСОК ЛИТЕРАТУРЫ
Приложения Таблица П.1 - Значения допусков по СТ СЭВ 145-75
Таблица П.2 – Значения единицы допуска i в зависимости от размера
Таблица П.3 – Значения числа единиц допуска k
Таблица П.4 – Ряд значений коэффициента риска t
Рисунок П.5 – Схема расположения основных отклонений |
|
poisk-ru.ru
Определение зазоров и натягов в соединениях.
Поиск ЛекцийВведение.
ФГБОУ ВПО РГАТУ |
Метрология, стандартизация, сертификация. |
Качественные показатели современных изделий машиностроения (точность, долговечность, надёжность и др.) в значительной мере зависят от правильности выбора посадок, т.е. характера сопряжения деталей, и правильность выбора допусков формы и расположения.
Изделия машиностроения – не простая совокупность деталей. В собранном изделии детали находятся во взаимосвязи и взаимозависимости. По этой причине при выборе посадок, допусков размеров деталей, а также допусков формы и расположения следует учитывать: назначение деталей в сборочной единице, роль отдельных поверхностей, влияние отклонений размеров и т.п.
Качество и конкурентоспособность выпускаемой продукции находятся в прямой зависимости от точности её изготовления, от количества и качества измерений, с помощью которых контролируются как значения параметров, характеризующих эту продукцию, так и значения параметров внешних воздействующих факторов. Таким образом, возникают задачи обеспечения точности изготовления продукции и обеспечения единства измерений и достоверности испытаний, решение которых предусматривает соблюдение требований стандартов к точности изготовления и единства методов и средств измерений. Отсюда следует, что обеспечение высокого качества выпускаемой продукции возможно только при совместной деятельности в области стандартизации и её раздела взаимозаменяемости, метрологии и сертификации.
Определение зазоров и натягов в соединениях.
Контрольная работа по МСС РГСХА |
Задание 1. Определить зазоры и натяги в соединениях:
а) б) в)
Рассмотрим задание а: .
1.1. Согласно приложения 4 – 7 находим значения предельных отклонений размеров соединяемых деталей и определяем их предельные размеры и допуски:
а) для отверстия H7: 55+0,030
Dmax = DH + ES = 55 + 0,030 = 55,030 мм
Dmin = DH + EI = 55 + 0,000 = 55,000 мм
TD = Dmax – Dmin = 55,030 – 55,000 = 0,030 мм = 30 мкм
б) для вала g6:
dmax = dH + es = 55 + (–0,010) = 54,990 мм
dmin = dH + ei = 55 + (–0,029) = 54,971 мм
TD = Dmax – Dmin = 54,990 – 54,971 = 0,019 мм = 19 мкм
1.2. Определим предельные и средние зазоры и допуски посадок:
Smax = Dmax – dmin = ES – ei = 0,030 – (–0,029) = 0,059 мм = 59 мкм
Smin = Dmin –dmax = EI – es = 0,000 – (–0,010) = 0,010 мм = 10 мкм
Sc = 0,5(Smax + Smin) = 0,5(0,059 + 0,010) = 0,0345 мм = 34,5 мкм
TS = Smax – Smin = TD + Td =0,030 + 0,019 = 0,049 мм = 49 мкм
Данная посадка выполняется с зазором.
1.3. Выберем шероховатость сопрягаемых поверхностей и вид окончательной механической обработки деталей по , приложение 10 и 11.
Для отверстия H7:
- шероховатость: Rа = 3,2 мкм;
- вид обработки: чистовое протягивание.
Для вала g6:
- шероховатость: Rа = 1,6 мкм;
- вид обработки: обычное полирование.
1.4. Построим схему расположения полей допусков отверстия и вала с указанием на них номинальных размеров, предельных отклонений, предельных и средних зазоров (рис.1)
1.5. Вычертим эскизы соединений (в узле и подетально) и проставим условные обозначения и цифровые значения расположения полей допусков и шероховатостей (рис.2).
Контрольная работа по МСС РГСХА |
Рис.2. Эскизы соединения и соединяемых деталей.
Рассмотрим задание б: .
1.1 1.1. Согласно приложения 4 – 7 находим значения предельных отклонений размеров соединяемых деталей и определяем их предельные размеры и допуски:
а) для отверстия H8: 78+0,046
Dmax = DH + ES = 78 + 0,046 = 78,046 мм
Dmin = DH + EI = 78 + 0,000 = 78,000 мм
TD = Dmax – Dmin = 78,046 – 78,000 = 0,046 мм = 46 мкм
б) для вала u8:
dmax = dH + es = 78 + 0,148 = 78,148 мм
dmin = dH + ei = 78 + 0,102 = 78,102 мм
Td = dmax – dmin = 78,148 – 78,102 = 0,046 мм = 46 мкм
1.2. Определим предельные и средние натяги и допуски посадок:
Nmax = dmax –Dmin = es – EI = 0,148 –0,000 = 0,148 мм = 148 мкм
Nmin = dmin –Dmax = ei – ES = 0,102 –0,046 = 0,056 мм = 56 мкм
Nc = 0,5(Nmax + Nmin) = 0,5(0,148 + 0,056) = 0,102 мм = 102 мкм
TN = Nmax – Nmin = TD + Td =0,046 + 0,046 = 0,092 мм = 92 мкм
Данная посадка выполняется с натягом.
1.3. Выберем шероховатость сопрягаемых поверхностей и вид окончательной механической обработки деталей по , приложение 10 и 11.
Для отверстия Н8:
- шероховатость: Rа = 3,2 мкм;
- вид обработки: чистовое протягивание.
Для вала u8:
- шероховатость: Rа = 3,2 мкм;
- вид обработки: чистовое растачивание.
1.4. Построим схему расположения полей допусков отверстия и вала с указанием на них номинальных размеров, предельных отклонений, предельных и средних натягов (рис.3).
Контрольная работа по МСС РГСХА |
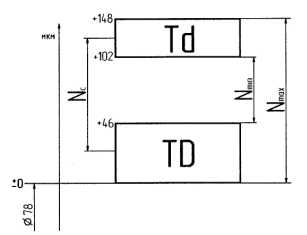
Рис. 3 Схема расположения полей и допусков посадки с натягом.
1.5. Вычертим эскизы соединений (в узле и подетально) и проставим условные обозначения и цифровые значения расположения полей допусков и шероховатостей (рис.4).
Рис. 4 Эскизы соединения и соединяемых деталей.
Рассмотрим задание в:
1.1. Согласно приложения 4 – 7 находим значения предельных отклонений размеров соединяемых деталей и определяем их предельные размеры и допуски:
а) для отверстия М7: 25-0,021
Dmax = DH + ES = 25 + 0,000 = 25,000 мм
Контрольная работа по МСС РГСХА |
Dmin = DH + EI = 25 + (–0,021) = 24,979 мм
TD = Dmax – Dmin = 25,000 – 24,979 = 0,021 мм = 321 мкм
б) для вала h6:
dmax = dH + es = 25 + 0,000 = 25,000 мм
dmin = dH + ei = 25 + (–0,013) = 24,987 мм
Td = Dmax – Dmin = 25,000 – 24,987 = 0,013 мм = 13 мкм
1.2. Определим предельные и средние зазоры (натяги) и допуски посадок:
Smax = Dmax – dmin = ES – ei = 0,000 – (–0,013) = 0,013 мм = 13 мкм
Nmax= dmax – Dmin = es – EI = 0,000 – (–0,021) = 0,021 мм = 21 мкм
Nc = 0,5(Nmax – Smax) = 0,5(0,021 – 0,013) = 0,004 мм = 4 мкм
TN(S) = Smax + Nmax = TD + Td =0,013 + 0,021 = 0,034 мм = 34 мкм
Данная посадка переходная.
1.3. Выберем шероховатость сопрягаемых поверхностей и вид окончательной механической обработки деталей по , приложение 10 и 11.
Для отверстия М7:
- шероховатость: Rа = 3,2 мкм;
- вид обработки: чистовая притирка.
Для вала h6:
- шероховатость: Rа = 1,6 мкм;
- вид обработки: чистовая притирка.
1.4. Построим схему расположения полей допусков отверстия и вала с указанием на них номинальных размеров, предельных отклонений, предельных и средних зазоров (натягов) (рис.5).
Контрольная работа по МСС РГСХА |
1.5. Вычертим эскизы соединений (в узле и подетально) и проставим условные обозначения и цифровые значения расположения полей допусков и шероховатостей (рис.6).
Рис.6 Эскизы соединения и соединяемых деталей.
Расчёт и выбор посадок.
При выборе переходных посадок необходимо учитывать то, что для них характерна возможность получения как натягов, так и зазоров. Чем больше вероятность получения натяга, тем более прочной является посадка. Для более точного центри
Контрольная работа по МСС РГСХА |
Посадки H/n, N/h являются наиболее прочными из переходных посадок. Их назначают для соединений, передающих большие усилия, при наличии ударов и вибраций, преимущественно для соединений, разбираемых редко, обычно только при капитальном ремонте изделия.
Переходные посадки предусмотрены только в квалитетах 4 – 8 . Точность отверстия в них должна быть на один квалитет ниже точности вала. Посадки повышенной точности выполняются по 4, 5, 6-му квалитетам, пониженной – по 7-му и 8-му квалитетам.
Трудоемкость сборки и разборки соединений с переходными посадками, так же как и характер последних, во многом определяется вероятностью получения в них натягов и зазоров, при расчёте которой обычно исходят из нормального закона распределения.
Задание 2. Рассчитайте и выберите переходную посадку для следующих условий: d=45 мм; детали соединения неподвижны; масса их небольшая, разборка производится редко.
2.1. По заданным техническим и эксплуатационным требованиям, предъявляемым к соединению, по приведённым выше сведениям, согласно приложение 32 таблица 4, выбираем необходимую посадку и рассчитываем Smax, Nmax, Nc, TD, Td.
Выберем соединение .
а) для отверстия H7: 45+0,025
Dmax = DH + ES = 45 + 0,025 = 45,025 мм
Dmin = DH + EI = 45 + 0,000 = 45,000 мм
TD = Dmax – Dmin = 45,025 – 45,000 = 0,025 мм = 25 мкм
б) для вала n6:
dmax = dH + es = 45 + 0,033 = 45,033 мм
dmin = dH + ei = 45 + 0,017 = 45,017 мм
Td = dmax – dmin = 45,033 – 45,017 = 0,016 мм = 16 мкм
в) определим предельные и средние зазоры и допуски посадок:
Smax = Dmax – dmin = ES – ei = 0,025 – 0,017 = 0,008 мм = 8 мкм
Nmax= dmax – Dmin = es – EI = 0,033 – 0,000 = 0,033 мм = 33 мкм
Nc = 0,5(Nmax – Smax) = 0,5(0,033 – 0,008) = 0,0125 мм = 12,5 мкм
TN(S) = Smax + Nmax = TD + Td =0,025 + 0,016 = 0,041 мм = 41 мкм
2.2. Определим среднее квадратическое отклонение натяга и предел интегрирования :
По найденному значению находим по , приложение 14, значение функции Ф( ) и определяем вероятность появления соединений с натягом и зазором:
при ;
вероятность натяга:
;
вероятность зазора:
процент соединения с натягом:
процент соединения с зазором:
2.4. Построим дифференциальную функцию распределения натягов и зазоров (рис.7)
Контрольная работа по МСС РГСХА |
Рис.7 Распределение зазоров и натягов в соединении
poisk-ru.ru
Наибольшие значения натяга и зазора — Мегаобучалка
Nmax = dmax – Dmin = 105,011 – 105 = 0,011 мм = 11 мкм
Smax = Dmax – dmin = 105,035 – 104,989 = 0,046 мм = 46 мкм
Средний натяг
Nc = (Nmax – Smax) / 2 = (11 –46) / 2 = – 17,5 мкм
Допуски стакана и корпуса
Td = es – ei = +11 – (–11) = 22 мкм
TD = ES – EI = +35 – 0 = 35 мкм
Среднее квадратичное отклонение натяга
Предел интегрирования
Плотность вероятности случайной погрешности (по кривой Гаусса)
Вероятность натягов и вероятность зазоров
PN = 0,5 + Ф = 0,5 – 0,49 = 0,01 (1%)
PS = 0,5 – Ф = 0,5 + 0,49 = 0,99 (99%)
Наибольший вероятный натяг и зазор
2.3.11. Вероятные натяги и зазоры будут меньше предельных на величину половины разности допуска посадки (TD + Td) и поля рассеяния посадки (6sN)
Проверка
Nmin = dmin – Dmax = 104,989 – 105,035 = – 0,046 мм = – 46 мкм
Smin = Dmin – dmax = 105 – 105,011 = – 0,011 мм = – 11 мкм
TN = Nmax – Nmin = 11 – (–46) = 57 мкм
TS = Smax – Smin = 46 – (–11) = 57 мкм
TSN = TD + Td = 35 + 22 = 57 мкм
Схема расположения полей допусков стакана и корпуса
2.4 Расчёт сопряжения крышки Æ108 со стаканом по посадке с натягом по заданным значениям величин: Nmax = 95 мкм, Nmin = 25 мкм
Допуск посадки с натягом
TN = Nmax – Nmin = 95 – 25 = 70 мкм
Величина допуска, приходящаяся на каждую из сопрягаемых деталей
TD = Td = TN / 2 = 70 / 2 = 35 мкм
2.4.3. Величины допусков для Æ108, не превышающие 35 мкм [2, стр. 356]
IT6 = 22 мкм
IT7 = 35 мкм
2.4.5. Предельные отклонения стакана [2, стр. 360]
а) для IT6: ES = +22 мкмEI = 0 мкм
б) для IT7: ES = +35 мкмEI = 0 мкм
Предельные отклонения крышки
а) для IT6: esпр = EI + Nmax = 0 + 95 = + 95 мкмeiпр = ES + Nmin = +22 + 25 = + 47 мкм
б) для IT7: esпр = EI + Nmax = 0 + 95 = + 95 мкмeiпр = ES + Nmin = +35 + 25 = + 60 мкм
2.4.7. Ряд рекомендуемых посадок с натягом [2, стр. 358]
а) для IT6: , ,
б) для IT7: , , , , ,
Схема расположения полей допусков крышки и стакана для квалитетов IT6 и IT7
2.4.8. Нижнее отклонение крышки [2, стр. 368, табл. 5]
Выбираем из таблицы ряд основных нижних отклонений стакана так, чтобы было выдержано условие eiпр. £ eiтабл.:
а) для IT6: eir = + 51 мкм (r5)
б) для IT7: eis = + 71 мкм (s6)
2.4.9. Верхнее отклонение крышки [2, стр. 368, табл. 5]
а) для IT6: esr = + 66 мкм (r5)
б) для IT7: ess = + 93 мкм (s6)
Выбор посадки
Из схемы расположения полей допусков 6-го и 7-го квалитетов следует, что посадки t6, s7 и u7 могут создать натяг, превышающий Nmax функц., поэтому они не пригодны для сопряжения. Посадки, которые отвечают граничным требованиям и пригодны для использования это r5, s5 и s6. Но для посадки с гарантированным натягом для крышки целесообразней взять посадку s6, т.к. эта деталь должна быть обработана точнее, чем стакан (H7), следовательно, посадка для сопряженных поверхностей есть Æ108 H7/s6.
Допуски крышки и стакана
Td = es – ei = +93 – 71 = 22 мкм
TD = ES – EI = +35 – 0 = 35 мкм
Предельные размеры сопряженных поверхностей по выбранной посадке
а) для крышки:dmax = d + es = 108 + 0,093= 108,093 ммdmin = d + ei = 108 +0,071 = 108,071 мм
б) для стакана:Dmax = D + ES = 108 + 0,035 = 108,035 ммDmin = D + EI = 108 – 0 = 108 мм
Предельные натяги в посадке
Nmax = dmax – Dmin = 108,093 – 108 =0,093 мм = 93 мкм
Nmin = dmin – Dmax = 108,071 – 108,035 = 0,036 мм = 36 мкм
Допуск посадки с натягом
TN = Nmax – Nmin = 93 – 36 = 57мкм
Проверка
Smax = Dmax – dmin = 108,035 – 108,071 = – 0,036 мм = – 36 мкм
Smin = Dmin – dmax = 108 – 108,093 = – 0,093 мм = – 93 мкм
TS = Smax – Smin = –36 – (–93) = 57 мкм
TSN = TD + Td = 35 + 22 = 57 мкм
Схема расположения полей допусков крышки и стакана
Таблица 4. Сводная таблица гладких цилиндрических соединений
Наименование детали | Номинальный размер, мм | Система | Квалитет | Посадка | Отклонения мкм | Предельные размеры, мм | Допуск, мкм | Зазоры S, мкм | Натяги N, мкм | Допуск посадки, мкм | ||||||
ES es | EI ei | Dmax dmax | Dmin dmin | Smax | Smin | Sm | Nmax | Nmin | Nm | |||||||
Распор-ное кольцо | Æ65 | отверстия | с зазором | +30 | 65,030 | – | – | – | – | |||||||
Вал | –19 | 64,981 | ||||||||||||||
Корпус | Æ105 | отверстия | пере-ходная | +35 | 105,035 | – | – | – | -17,5 | |||||||
Стакан | +11 | –11 | 105,011 | 105,989 | ||||||||||||
Стакан | Æ108 | отверстия | с натягом | +35 | 108,035 | – | – | – | – | |||||||
Крышка | +93 | +71 | 108,093 | 108,071 | ||||||||||||
вал | Æ65 | отверстия | с натягом | -13 | 64,987 | – | – | – | – | |||||||
Внутреннее кольцо подшип. | +39 | +20 | 65,039 | 65,020 | ||||||||||||
наружное кольцо | Æ100 | отверстия | с зазором | +35 | 100,035 | – | - | - | – | |||||||
Стакан | -15 | 99,985 |
3 Расчет калибров для сопряжения Æ105 стакана и корпуса
3.1 Расчет калибра–пробки для отверстия в корпусе Æ105H7
3.1.1. Предельные отклонения отверстия в корпусе [2, стр. 360, табл. 3]
ES = + 35 мкм
EI = 0 мкм
megaobuchalka.ru