Горячее цинкование - справка. Оцинкованная по методу сендзимира
Горячее цинкование - историческая справка Поль-Жак Малуин, Сорель, Лафольи, Кроуфурд и Сендзимир
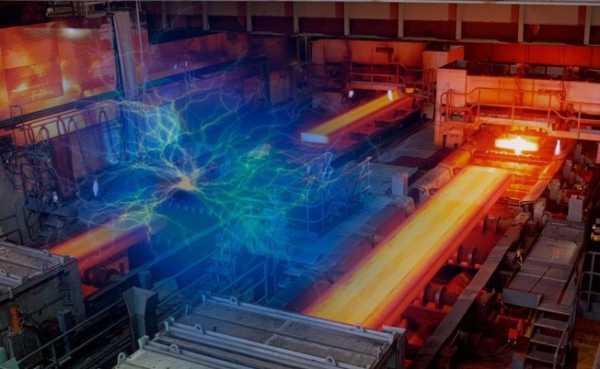
Обычно все исторические отсылки о горячем цинковании относятся к двум фамилиям – дескать, французский химик Поль-Жак Малуин (Paul-Jaques Malouin) сообщил в 1742 году на заседании французской Академии Наук о том, что при окунании куска железа в расплавленный цинк этот кусок покрылся тонким слоем металлического цинка, а другой французский химик Сорель (Stanislas Sorel) в 1836 году предложил перед такой обработкой выдерживать железный образец предварительно несколько часов в разбавленном растворе серной кислоты или в кислых отходах от производства масел, содержащих органические кислоты, а затем в растворе нашатыря.
Но никто обычно не задается вопросом – почему между этими событиями прошло почти 100 лет, и почему именно последнее событие стало толчком к широкому внедрению горячего цинкования в промышленное производство.
Сообщение, сделанное Малуином на заседании Академии, как и последующее письменное его изложение, опубликованное в ее трудах, не содержало деталей проведения опытов, и их невозможно было воспроизвести. Кроме того, со стороны академиков были высказаны мнения, что цинк является ядовитым веществом. Потребовались детальные исследования процессов, осуществленные, прежде всего, Л-Ж.де-Лафольи (Louis-Guillaume de Lafolie), что это не так (то есть цинковое покрытие не ядовито), а также требования, которые необходимо выполнять, чтобы получить цинковое покрытие необходимого качества.
Впервые использование цинковых листов в качестве кровельного материала можно отнести к 1811 году. К 1829 году можно отнести установление защитного действия цинка по отношению к металлическому железу (Михаил Фарадей). А сам термин «гальванизация» обязан открытию Луиджи Гальвани, который обнаружил возникновение электрического тока при контакте двух разнородных металлов, а цинк-углеродная батарея служит верой и правдой до настоящего времени.
Хотя принцип защиты одного металла другим был уже известен, и некоторое количество железных изделий покрывалось цинком, до реального промышленного производства дело не доходило из-за многочисленных технологических проблем. Именно с Сореля поэтому следует отсчитывать начало промышленного производства оцинкованных изделий. В 1836 году данным химиком был получен французский патент на способ покрытия железа расплавленным цинком. В течение последующих нескольких лет им было внесено до 23 усовершенствований в разработанную им технологию.
Изделия перед окунанием в расплавленный цинк выдерживались для удаления ржавчины в течение нескольких часов в разбавленной серной кислоте или в смеси органических кислот, являвшихся отходом производства растительных масел, затем промывались водой, окунались в соляную кислоту, раствор хлористого аммония, высушивались и окунались в расплавленный цинк. Для того, чтобы изделие было более блестящим, оцинкованное изделие охлаждалось окунанием в холодную воду.
Чуть позже, а именно, в 1837 году Кроуфурдом (H.W.Craufurd) был получен и английский патент, и чуть позднее (а именно, с 1843 года) в Великобритании начинается создание промышленного производства оцинкованных изделий. Уже с 1851 года производился достаточно широкий ассортимент оцинкованной продукции, начиная от водосточных труб, садовой фурнитуры и кончая даже полномасштабными строительными конструкциями.
Одновременно с производством оцинкованных изделий по данному методу другими авторами был получен ряд патентов по несколько иному способу – сначала осуществлялось окунание в ванну с расплавленным оловом, затем с расплавленным цинком.
Примерно через десять лет появились близкие производства в других странах Европы, а также в Америке и в Австралии. Постепенно расширяется и масштаб произведенной продукции. Так, в 1850 году в Англии производилось около 10 тысяч тонн оцинкованной продукции.
Среди культовых строений того времени – открытие в 1883 году бруклинского моста, стальные канаты которого были изготовлены из оцинкованной проволоки. Через сто лет службы моста была произведена ревизия, которая показала их хорошее состояние.
Оцинкованная проволока впервые была использована для проводного телеграфа в 1850 году; для трансатлантического подводного кабеля она же была использована в 1856 году; для этой цели было задействовано производство с мощностью 10 тонн оцинкованной проволоки в неделю. В 1860 году было создано устройство для непрерывного цинкования проволоки.
Вообще производство оцинкованной продукции в середине 19 века оказалось очень востребованным, поскольку вследствие промышленной революции резко возросли потребности человечества в гигиене – и именно оцинкованная продукция дала возможность наладить вынос отходов жизнедеятельности человека за пределы городов, их последующую переработку и доставку населению городов воды питьевого качества.
Развитие технологии горячего цинкования
По мере развития потребности в оцинкованном металле различного назначения постепенно улучшается и развивается технология горячего цинкования. Появляются и обобщающие труды по технологиям горячего цинкования. Некоторые труды до нас не дошли, но из монографии «Hot dip galvanizing and tinning” от 1900 г. К началу двадцатого века уже применялись технологии, которые с небольшими уточнениями применяются и сейчас. В конце 19-го или начале 20-го века (автором данного обзора не установлено, когда) для улучшения внешнего вида изделий было предложено добавлять алюминий в ванну с расплавом. Было известно и о влиянии примесей в сталях на скорость их растворения в расплаве.
Недостатки технологий того времени связаны с ограниченной возможностью получения материалов нужного качества. Так, хотя было известно, что для изготовления ванн необходим металл повышенной чистоты, металлургия того времени не была способна его дать. Так же дело обстояло и с материалом для изготовления ванн подготовки поверхности изделий – в то время не было ни современных органических материалов, ни прочных защитных покрытий, поэтому ванны для технологических растворов изготавливались из дерева. Кстати, ванны такого типа из-за их высокой устойчивости к кислым растворам дожили и до наших дней – на одном из предприятий автор видел такие деревянные ванны длиной до 6 метров. По-видимому, до 20-х годов не существовало и отдельных ванн обезжиривания, хотя в упомянутой выше монографии упоминается использование ванн со щелочным раствором.
Сами ванны для расплава изготавливались из листов металла наивысшей достигнутой к тому времени чистоты, но она была недостаточной, поэтому нередки были аварийные ситуации, связанные с течью ванн. Для уменьшения последствий аварии в последних предусматривались либо краны для слива цинка, либо специальный под из огнеупорного кирпича – поэтому, как только появлялась течь, жидкий цинк сливали либо в специальные приемники, либо в пространство, окруженное песчаным барьером.
Метод Сендзимира
Невозможность изготовления ванн большого размера в 20-30-х годах являлась определенным тормозом развития промышленности горячего цинкования. Была большая потребность в кровельных материалах, но размер получаемых оцинкованных листов был недостаточным. Поэтому настоящим прорывом в производстве оцинкованного листа стало предложение американца польского происхождения Тадеуша Сендзимира получать непрерывный оцинкованный лист путем пропускания его через расплав по направляющим роликам. Для этого непрерывный лист пропускался сначала через специальную печь с восстановительной атмосферой, где с него удалялись следы органических загрязнений (смазки), а окалина восстанавливалась в атмосфере водорода. Метод был реализован в 1936 году, а получение непрерывной оцинкованной полосы, кроме расширения производства устойчивого к коррозии кровельного материала, позволило создать еще одно направление в технологии – получение тонкостенных профилей для быстровозводимых зданий и сооружений.
Впоследствии метод Сендзимира постоянно усовершенствовался, создавались установки для производства листа все большей ширины и толщины металла; разрабатывались и альтернативные способы, в частности, метод Кука-Нортмана производства непрерывной оцинкованной полосы. В настоящее время агрегаты непрерывного цинкования имеют годовую производительность в несколько сотен тысяч тонн при ширине полосы до 1,8 м и толщиной до 6 мм.
Следующий этап совершенствования технологии горячего цинкования приходится на 60-е годы прошлого столетия. Связано это с новыми возможностями, которые открыла как металлургия, так и промышленность полимерных материалов. Во-первых, вместо мартеновских печей стали внедряться электрические печи, что позволяло получать сталь заметно большей чистоты и тем самым повлияло на продолжительность жизни изготавливаемых из нее ванн. Успехи в области новых методов сварки привели к тому, что сварные места не стали причиной преждевременного выхода ванн из строя. Донный нагрев углем был заменен на более передовые методы – на системы газового обогрева боковых поверхностей ванн, что уменьшило как интенсивность теплопередачи через поверхность (площадь дна ванны значительно меньше площади боковых стенок), так и интенсивность перемешивания расплава, что обеспечило более эффективное осаждение образующегося в результате реакции оцинкования гартцинка. Стало возможным еженедельное удаление гартцинка со дна ванны, что позволило уменьшить потери цинка при извлечении из ванны отходов.
Большую лепту в дело совершенствования процесса внесла и промышленность органических материалов. Создание устойчивых к кислым средам эпоксидно-полиэфирных покрытий, каучуков холодного отверждения, полимеризуемых непосредственно на ваннах, наконец, создание пластмасс, устойчивых не только к средам, но и к ударным нагрузкам, позволило заменить дерево на более удобные материалы. Так что современный цех – это синтез достижений современной промышленности.
Сложности горячего цинкования
Вместе с тем достижения в металлургии создали и немало сложностей технологиям горячего цинкования. Переход от конверторного и мартеновского производства к технологиям непрерывной разливки стали вызвал дополнительные сложности в технологиях горячего цинкования при получении изделий с контролируемой толщиной покрытия. Дело в том, что в 1940 году немецкий исследователь Санделин обнаружил эффект, названный его именем и заключающийся в следующем. Если в низкоуглеродистой стали (а именно такие стали подвергаются горячему цинкованию) содержание кремния и фосфора находится в некоторых нехороших пределах (а именно, для кремния – это содержание от 0,07 до 0,12% масс.), то получается для технологических времен, используемых при горячем цинковании, грубое покрытие толщиной часто более 200 мкм (при цинковании оптимальным считается покрытие менее 100 мкм, лучше в интервале 60-80 мкм), со слабой адгезией, отслаивающееся при ударе. Раньше этот эффект практически не наблюдался, поскольку прежние металлургические технологии давали т.н. «кипящие» стали. После введения технологии непрерывной разливки стали в производстве различных конструкций с последующим цинкованием возросла доля сталей с заметным содержанием кремния, причем в значительном количестве с содержанием кремния именно в этом «неприятном» интервале. Дело в том, что по технологиям непрерывной разливки сталь раскисляется именно кремнием, и вероятность того, что его остаточное содержание в стали окажется именно в этом концентрационном интервале, велико.
Данная проблема потребовала буквально «мозгового штурма» от металлургов, в результате чего были предложены технологии, в значительной степени нивелирующие этот эффект.
Как уже говорилось ранее, научное сопровождение технологий горячего цинкования в середине 80-х годов была буквально уничтожено в России. Если не считать чудом сохранившихся небольших установок при судостроительных предприятиях, приходится данную отрасль промышленности создавать с нуля. Но этот факт также дает и возможность выхода на передовые рубежи. Если в условиях Европы и Америки перевооружение цехов горячего цинкования приходится проводить в стесненных условиях существующего производства, то у нас создающиеся предприятия размещаются практически всегда на свободных территориях, с учетом существующего зарубежного опыта. Желательно только не экономить на оборудовании, а в случае нехватки финансирования просто предусматривать площади под установку соответствующего оборудования в дальнейшем.
Возможно Вас так же заинтересуют следующие статьи: comments powered by HyperCommentsecm-zink.ru
Обработка поверхности кабельных лотков - Домашнее Радио
В наше время наиболее используемым металлом является сталь. Существует много методов защиты стальных изделий от коррозии. На выбор необходимого метода обработки поверхности влияет естественным образом та среда, в которой будет использоваться изделие. Классификацию степени коррозийной стойкости различных сред по категориям в соответствии со стандартом SFS-EN ISO 12944-2 и правила обработки поверхности, которые применимы в различных случаях, можно найти по данной ссылке.
Горячеоцинкованная тонколистовая сталь (оцинковка по методу Сендзимира)
Изделия из горячеоцинкованной тонколистовой стали изготавливаются из уже оцинкованного (по методу Сендзимира) листа стали. О таких изделиях говорят, что они предварительно оцинкованы.
Мека использует горячеоцинкованную тонколистовую сталь с покрытием цинка около 20 мкм. Сталь оцинкована в соответствии требованиями стандарта EN 10327, ASTMA 875 и DIN 17162.
Из горячеоцинкованной тонколистовой стали изготавливаются профильные лотки KS20, KS30 и KS35, листовые лотки KRA, KRB, и KRC, а также коробы МЕК для электропроводки и подвески светильников.
Изделия из горячеоцинкованной тонколистовой стали подходят для применения в помещениях, относящихся по степени воздействия окружающей среды к категориям С1 и С2. Типичными объектами применения изделий являются сухие помещения – офисные и коммерческие здания, торговые центры, супермаркеты, школы, больницы, промышленные цеха, склады, спортивные залы и т.д.
Горячая оцинковка методом погружения (глубокое цинкование)
Горячеоцинкованные изделия изготавливаются из необработанной тонколистовой стали. После изготовления изделия предварительно обрабатываются и погружаются в ванну с расплавленным цинком. О таких изделиях говорят, что они оцинкованы методом погружения (глубокое цинкование). Слой цинка толщиной около 55 мкм покрывает изделия полностью, включая обрезные кромки и сварные швы. Методом погружения оцинковываются профильные лотки Мека серии KS80, KSF80, KSE80 и относящиеся к ним принадлежности. Горячеоцинкованные изделия оцинкованы по стандарту SFS-EN 1461 (соответствует прежним стандартам SFS 2765 и DIN 50976) и подходят для применения в помещениях, относящихся по степени воздействия окружающей среды к категориям С1, С2, С3 и С4. Типичными объектами применения изделий являются объекты под открытым небом, производственные и промышленные помещения с высокой степенью влажности и загрязненности.
Покрытие РЕХ (обработка «Дуплекс»)
При обработке «Дуплекс» горячеоцинкованное изделие очищается на этапе предварительной обработки, затем покрывается порошковой краской, и в конце погружается в печь для придания краске тведости. При помощи обработки «Дуплекс» горячеоцинкованное изделие получает дополнительную защиту, которая может быть необходима в агрессивных средах. Кроме этого, обработка «Дуплекс» дает возможность выбора цвета по желанию клиента из цветовой палитры RAL. Стандартный цвет изделия PEX - белый RAL9010.
Изделие PEX KS20 можно использовать в помещениях, относящихся по степени воздействия окружающей среды к категориям С1, С2. Изделия PEX KS80 и KSF80 подходят для использования в помещениях категории C1, C2, C3, C4, C5-l и C5-M.
Окрашенная тонколистовая сталь
Изделия из окрашенной тонколистовой стали изготавливаются из уже оцинкованного и окрашенного листа стали. В качестве покрытия используется краска на сложных полиэфирах, которая устойчива к коррозии, изменению погодных условий, а также к износу. Изделия из окрашенной тонколистовой стали можно использовать в помещениях, относящихся по степени воздействия окружающей среды к категориям С1 и С2. Типичными объектами применения изделий являются сухие помещения – офисные и коммерческие здания, торговые центры, супермаркеты, школы, больницы, спортивные залы и т.д.
Стандартный цвет изделий - белый RAL 9010. Листовые лотки серии KRA-xxx M (белого цвета) покрыты полиэтиленовой пленкой, защищающей изделие при транспортировке и монтаже.
Нержавеющая сталь AISI 304 (RST) и кислотостойкая сталь AISI 316L (HST)
Изделия, изготовленные из нержавеющей и кислотостойкой стали, используются в очень агрессивных по степени воздействия средах, в которых горячая оцинковка не является достаточной защитой стали от коррозии. Изделия из нержавеющей и кислостойкой стали подходят для применения как внутри помещений таки и снаружи.Изделия можно использовать в помещениях, относящихся по степени воздействия окружающей среды к категориям C3, C4, C5-I и C5-M. Типичными объектами применения изделий являются предприятия химической и деревообрабатывающей промышленности, а также объекты, с повышенными требованиями к уровню гигиены - молочные фермы, скотобойни, предприятия пищевой и фармацевтической промышленности
Использование нержавеющей или кислотостойкой стали зависит от многих различных факторов. Фактор, оказывающий наибольшее влияние на выбор материала, - это химический состав окружающей среды, т.е. находящиеся в ней соединения и их процентный состав. В целом можно констатировать, что у кислотостойкого материала климатический показатель уровня сопротивления коррозии выше, и он подходит для промышленной и влажной атмосферы. Высокое содержание хлористых соединений также предполагает использование кислотостойких материалов.
housea.ru
Лестничный лоток
Листовые перфорированные лотки DKC
Система металлических перфорированных лотков S5 Combitech
Где используется данный тип лотков:Перфорированные металлические лотки подходят для тех случаев, когда необходимо организовать открытую электропроводку в фабричных и прочих индустриальных строениях, в супермаркетах и гипермаркетах, предприятиях оптовой торговли, на складах, крытых паркингах и других местах с большой площадью.
В какой среде можно использовать:
- В местах со средней концентрацией сернистых ангидридов
- На побережьях при небольшой концентрации соли
- В промышленных зданиях при высокой влажности и не очень высоком загрязнении воздуха.
Габаритные параметры:
Высота, мм | Ширина, мм | Длина, мм | Толщина, мм | Материал | |
S5-50 | 50 | 50-500 | 2000 | 0,7/0,8/1,0 | - Сталь, оцинкованная по методу Сендзимира, - Горячее цинкование, - Нержавеющая сталь. |
100-500 | 3000 | 0,7/0,8/1,0 | |||
S5-100 | 80 | 80-500 | 3000 | 0,7/0,8/1,0 | - Сталь, оцинкованная по методу Сендзимира, - Горячее цинкование, - Нержавеющая сталь. |
S5-100 | 100 | 100-500 | 3000 | 0,7/0,8/1,0 | - Сталь, оцинкованная по методу Сендзимира, - Горячее цинкование, - Нержавеющая сталь. |
Лотки ДКС отвечают всем требованиям ГОСТ 9.307-89
Листовые неперфорированные лотки DKC
Система металлических неперфорированных лотков S5 Combitech
Где используется данный тип лотков:Неперфорированные (закрытые) металлические лотки применяются в тех случаях, когда требуется смонтировать систему открытой электропроводки на фабриках, объектах тяжелой промышленности и добывающих предприятиях.
В какой среде можно использовать:
- В атмосферных условиях со средней концентрацией соли в воздухе,
- При повышенной влажности воздуха и агрессивной внешней среде,
- В тех местах, где влага конденсируется постоянно или в течении длительных периодов времени.
- В местах с загрязненной атмосферной средой.
Габаритные параметры:
Высота, мм | Ширина, мм | Длина, мм | Толщина, мм | Материал | |
S5-50 | 50 | 50-500 | 2000 | 0,7/0,8/1,0 | - Сталь, оцинкованная по методу Сендзимира, - Горячее цинкование, - Нержавеющая сталь. |
100-500 | 3000 | 0,7/0,8/1,0 | |||
S5-100 | 80 | 80-500 | 3000 | 0,7/0,8/1,0 | - Сталь, оцинкованная по методу Сендзимира, - Горячее цинкование, - Нержавеющая сталь. |
S5-100 | 100 | 100-500 | 3000 | 0,7/0,8/1,0 | - Сталь, оцинкованная по методу Сендзимира, - Горячее цинкование, - Нержавеющая сталь. |
Лестничные лотки DKC
Система металлических лестничных лотков L5 Combitech
Где используется данный тип лотков:Для организации открытой электропроводки в заводских и складских, административных строениях, общественных зданиях, торговых и бизнес-центрах.
Высота, мм | Ширина, мм | Длина, мм | Толщина, мм | Материал | |
L5-50 | 50 | 200-600 | 3000 | 1,20 | - Сталь, оцинкованная по методу Сендзимира |
L5-50 plus | 50 | 200-600 | 3000 | 1,50 | - Сталь, оцинкованная по методу Сендзимира |
L5-80 | 80 | 200-600 | 3000 | 1,20 | - Сталь, оцинкованная по методу Сендзимиру |
L5-80 plus | 80 | 200-600 | 3000 | 1,50 | - Сталь, оцинкованная по методу Сендзимира |
L5-100 | 100 | 200-600 | 3000 | 1,50 | - Сталь, оцинкованная по методу Сендзимира |
Проволочные лотки DKC
Система металлических проволочных лотков
Где используется данный тип лотков:
- В структурированных кабельных системах (СКС).
- Для организации открытой электропроводки в заводских и складских, административных строениях, общественных зданиях, торговых и бизнес-центрах.
- Их легко можно установить над панелями подвесных потолков или в других легкодоступных местах для внутренней разводки по офису или гаражу.
Габаритные параметры:
-
Высота, мм Ширина, мм Длина, мм Диаметр, мм Материал F5-30 30 50-600 3000 4/5 - Сталь, оцинкованная по методу Сендзимира F5-50 50 50-600 3000 4/5 - Сталь, оцинкованная по методу Сендзимира F5-80 80 80-600 3000 4/5 - Сталь, оцинкованная по методу Сендзимира F5-100 100 100-600 3000 4/5 - Сталь, оцинкованная по методу Сендзимира
Примечание (информация на заметку):Метод цинкования польского ученого и изобретателя Тадеуша Сендзимира заключается в том, что лист прокатной стали промывается специальными реагентами и просушивается в печи, где он нагревается до высокой температуры в 650-700?С. После этой процедуры лист погружают в ванну расплавленного цинка с той же температурой. Когда лист вынимается из ванны, он попадает под действие газовых ножей, которые сдувают лишний цинк с листа посредством сжатого воздуха. Все это дает равномерное и качественное цинкование стального листа.
"Рон-Электро" предлагает лестничный, оцинкованный и даже проволочный лоток производства компании ДКС, по всем вопросам вы можете обратиться по телефону, указанному в верхней части страницы.
www.ron-elektro.ru