met546_tkm_liteinoe_proizvodstvo / Методичка 546. Литейное производство. Опоки литейное производство
Методичка 546. Литейное производство
1. ЦЕЛЬ РАБОТЫ
Получить начальное представление о способе формообразования путем литья в песчаные формы.
Освоить навыки изготовления песчаной формы п двух опоках.
2. ОБЩИЕ СВЕДЕНИЯ
называют изделие, полученное при затвердевании металла или иного материала в литейной форме.
Литейная форма, независимо от ее конструкции, имеет внутреннюю полость, конфигурация и размеры которой соответствуют будущей отливке. Литейные формы могут быть: разовыми, которые заполняют металлом один раз и затем разрушают, и постоянными, которые используют до нескольких тысяч раз.
Большую часть средних и крупных отливок получают с разовых песчаных литейных форм. Эти формы пригодны для изготовления отливок практически любой сложности. Они находят широкое применение в массовом, серийном и индивидуальном производстве. Преимуществами литья в песчаные формы являются их универсальность и низкая себестоимость.
Песчаные литейные формы изготавливают из формовочных смесей, состоящих из кварцевого песка, глины, воды и материалов, улучшающих технологические свойства смесей и качество отливок.
В автотракторостроении этим методом получают чугунные блоки цилиндров двигателей внутреннего сгорания, корпуса коробок передач, детали заднего моста, рычаги, траки гусениц, ведущие 'звездочки, опорные катки и др.
К недостаткам способа относятся низкая точность размеров отливок и большая шероховатость поверхности, что приводит к увеличению объема механической обработки. Для процесса характерна оптимальная трудоемкость получения отливок, большой расход формовочных материалов при изготовлении форм и стержней, неблагоприятные условия труда из-за загазованности и запыленности литейного цеха.
Отмеченные, негативные факторы приводят к использованию других способов литья. Однако этот процесс происходит медленно, и литье в песчаные формы еще долго будет доминировать.
3. КОНСТРУКЦИЯ ПЕСЧАНОЙ ЛИТЕЙНОЙ ФОРМЫ
На рнс.1 показана отливка, которую следует получить в песчаной форме. Отливка может быть выполнена из чугуна, стали, алюминиевого сплава (силумина), сплавов на основе меди (бронзы латуни).
На рис.2 показана в разрезе песчаная литейная форма для получения отливки. Она состоит из нижней и верхней полуформ. Полуформы изготавливают в нижней 1 и верхней 2 опоках, представляющих собой металлические ящики без дна и крышки. Опоки придают песчаным полуформам необходимую прочность и жесткость. Собранные полуформы соприкасаются друг с другом по плоскости разъема 3. Для точной установки полуформ используют центрирующие штыри 11 , а скрепление опок перед заливкой производится скобами 12. Рабочая полость 17 повторяет наружную конфигурацию будущей отливки. Металл подается в рабочую полость формы через систему каналов - литниковую систему. Она служит для заполнения рабочей полости формы металлом, а также для улавливания шлака и удаления воздуха, вытесненного из рабочей полости, литниковая система состоит из литниковой чаши 7. стояка 8. шлакоуловителя 9, питателя 10 и выпоров 6. Стояк и выпор имеют форму усеченного конуса с уклоном 3-5°. Шлакоуловитель и питатель в поперечном сечении имеют вид трапеции. Для образования полости в отливке в
форму устанавливают стержень 16, который закрепляется своими концами (знаками) в форме. Собранную форму устанавливают на металлическую Плиту 14. Заливка формы металлом производится из ковша через литниковую чашу непрерывно до того момента, пока металл не покажется в выпоре.
Спустя некоторое время после заливки металл затвердевает и отливку вместе с элементами литниковой системы (рис. З) извлекают из формы. Сами полуформы и стержень при этом разрушают. Затем от отливки отделяют элементы литниковой системы. которые впоследствии переплавляют.
Для изготовления формы используют модель отливки – элемент
Рис. З. Эскиз отливки с элементами литниковой системы: 1 - отливка; 2 - выпор; 3 - чаша; 4 - стояк: 5 - питатель; 6 – шлакоуловитель
технологической оснастки, по которой получают негативный отпечаток внешних очертаний будущей отливки в пластичной формовочной смеси. Модели бывают разъемные и неразъемные. Основными материалами- для моделей служат: древесина, алюминиевые сплавы, чугун и др.
Модель отливки, показанная на рис.4, является разъемной и' состоит из двух симметричных половинок - верхней и нижней. Половинки модели соединяют по плоскости разъема 4, совпадающей с. плоскостью разъема литейной формы. В нижней половинке модели отливки есть отверстия, а из верхней половинки выступают центрирующие шипы 5. При соединении половинок модели шипы входят о отверстия и препятствуют сдвигу верхней половинки относительно . нижней в процессе формовки.
Основная (профилирующая) часть модели отливки длиной L соответствует наружной конфигурации (профилю) будущей отливки.
Рис.4. Эскиз модели отливки: 1 - уклоны знака; 2 - уклоны ■ основной части модели: 3 - знак модели: 4 - плоскость разъема; 5 - центрирующие шипы
Кроме того модель отливки имеет знаки 3. по которым и форме отпечатываются углубления для установки стержня.
На модели предусмотрены литейные уклоны 1 и 2, которые обеспечивают беспрепятственное извлечение модели из уплотненной песчаной формы в процессе ее изготовления. Уклоны назначают на всех поверхностях модели, перпендикулярных плоскости разъема формы. Величина уклонов основной части модели 2 составляет 0.5-3°. а величина уклонов знаков модели 1 - 5-15°.
Стержень, показанный на рис. 5. служит для получения
Рис.5. Эскиз стержня: 1 - основная (профилирующая) часть стержня: 2 - знак стержня
внутренней полости в отливке. Стержень состоит из основной профилирующей части 1 и знаков 2. являющихся опорными частями стержня.
При длине основной часта стержня до 250 мм диаметр (длина) стержневого знака модели больше диаметра (длины) знака стержня на 0.г-г.4 ни. За счет этого между формой и стержнем образуются зазоры 4. что хороню видно на рис.2. Зазоры между формой и стержнем в области знаков облегчают установку стержня в полость нижней полуформы, а также верхней полуформы на нижнюю с предварительно установленным стержнем. Благодаря зазорам устраняется возможность деформации и разрушения формы стержнем в области знаков.
Операции изготовления форм (формовку) выполняют на автоматических или механизированных линиях в серийном и массовом производстве, на отдельных машинах в мелкосерийном производстве или вручную в индивидуальном производстве.
4. ФОРМОВОЧНЫЕ И СТЕРЖНЕВЫЕ СМЕСИ
Формовочные и стержневые смеси являются строительным материален для разовых форм и стержней. Смеси должны обладать следующими основными технологическими свойствами: пластичностью, прочностью, газопроницаемостью, выбиваемостью и огнеупорностью. Кроме того, смеси должны отвечать требованиям санитарии и гигиены, а также быть, по возможности, недорогими.
Пластичностью, смесей обеспечивает получение точного отпечатка формы и стержня с рабочих поверхностей модели и стержневого ящика.
'"прочность смесей обеспечивает сохранность конфигурации и размеров полости формы в процессе ее изготовления, транспортировки и заливки. Избыточная прочность нежелательна. так как увеличивается трудоемкость извлечения отливки из формы и стержня из отливки.
Газопроницаемость смесей обеспечивает удаление газов из формы и стержня. После заливки металла форма и стержень выделяют газы в количестве 15-45 см3 из 1 см5 смеси. Газы могут образовать в отливках газовую пористость и газовые раковины. Эта дефекты приводят к браку.
Выбиваемость определяется работой, затрачиваемой на разрушение разовых форм и стержней в процессе извлечения отливок Состав стержневых и формовочных смесей оказывают заметное влияние на санитарно-гигиенические условия труда в литейном цехе, так как они выделяют пыль и вредные газы (окись углерода, формальдегид, фенолы). В производстве применяют все методы изоляции источников пыле- и газовыделения, а также методы сокращения количества выделяющихся пыли и газов.
^Типовая формовочная смесь содержит: , ' - 90% кварцевого песка:
- 5-10% глины;
- - до 5% компонентов, улучшающих свойства смесей;
- 3-6% воды сверх 100Х сухой смеси.
Кварцевый песок SiO2 - огнеупорная основа смеси. Он состоит из зерен размером 0.06-р.8 мм.
Глина является связующим материалом песчаных смесей. Свои связующие свойства глина проявляет только в присутствии воды.
К добавкам. позволяющим регулировать свойства смеси, относятся: молотый уголь, мазут, асбестовая крошка, опилки, битум и ряд других материалов.
Типовая стержневая смесь содержит:
- 94-98% кварцевого песка;
- 2-6% связующих материалов на основе синтетических смол и других добавок.
1С стержневым смесям предъявляются более высокие требования, чем к формовочным. Стержень испытывает тяжелые механические и-температурные воздействия, поскольку находится внутри расплавленного металла. При остывании окружающий металл пытается сдавить стержень. Поэтому до заливки металла стержневая смесь должна иметь более высокую прочность, чем формовочная. После заливки металла стержневая смесь должна резко снижать свою
прочность до уровня самовысыпання за счет выгорания смолы.
Упрочнения достигают за счет введения в смесь 2-6% связующих материалов на основе синтетических смол и. других добавок. При сушке стержня происходит взаимодействие связующих ^ добавок с кварцевым песком, вследствие чего стержневая смесь приобретает повышенную прочность.
Огнеупорная глина в стержневую смесь или не вводится, или вводится ограниченно. только для повышения пластичности. Это объясняется тем. что при заливке формы металлом может произойти затвердевание стержня в случае наличия в нем глины. В результате затрудняется выбивание стержня из готовой отливки.
5. ПОСЛЕДОВАТЕЛЬНОСТЬ ИЗГОТОВЛЕНИЯ ПЕСЧАНОЙ
ФОРМЫ В ОПОКАХ
Независимо от степени механизации формовка проводится в определенной последовательности.
На рис.6 показана установка нижней половины модели отливки, модели питателя и нижней опоки на подмодельную плиту. На шипы 5 подмодельной плиты 4 устанавливают половину модели отливки 1 и
Рис.6. Установка нижней половины модели отливки, модели питателя и нижней опоки на подмодельную плиту: 1 - половина модели отливки: 2 - модель питателя: 3 - нижняя опока: 4 - подмодельная плита: 5 - центрирующие шипы: 6 - центрирующий штырь
модели питателей (модель питателя) 2 с отверстиями под шипы. Нижнюю опоку 3 устанавливают на центрирующие штыри 6. Модель питателя, имеющего в сечении Форму трапеции, кладут большим основанием вниз. Модели отливки и питателя необходимо располагать так, чтобы между опокой и моделями сохранялось расстояние не менее 30 мм.
На рис.7 показана набитая нижняя опока - полуформа:. Для ее получения на модель насыпают слой формовочной смеси 1 толщиной 20-25 мм и уплотняют острым концом трамбовки. Насыпают и уплотняют следующие слои смеси до верха опоки. Верхний слой утрамбовывают плоским концом трамбовки. Срезают избыток смеси поверх опоки плоской заостренной линейкой, и душником делают наколы (вентиляционные каналы 2) в набитой нижней опоке. Душник имеет форму длинного шила диаметром около 3 мм. Конец душника не должен доходить до поверхности модели на 10-15 мм. На 100 см2 поверхности приходится 3-4 канала.
Рис.7. Набитая нижняя опока - полуформа: 1 - формовочная смесь: 2 - вентиляционные каналы
На рис.8 показаны набитые верхняя и нижняя опоки полуформы. Для изготовления верхней полуфорны переворачивают нижнюю набитую опоку 8. Устанавливают верхнюю половину модели детали 2 так, чтобы центрирующие шипы вошли в отверстия нижней половины. .Модели шлакоуловителя 6. стояка 3 и выпоров 1 устанавливают аналогично. Модель выпора устанавливают в самой верхней точке, модели отливки. Если таких точек две и больше, то ставят несколько выпоров. Плоскость разъема опок посыпают сухим кварцевым песком. Затем устанавливают по центрирующим штырям 7 верхнюю опоку 5, которую заполняют послойно формовочной смесью и уплотняют так же. как и нижнюю. После удаления избытка смеси и накола вентиляционных каналов в верхней полуформе вырезают литниковую чашу 4. .
Производят раскрытие полуформ, из которых извлекают при помощи подъемников половинки модели отливки и модели "элементов, литниковой системы. Подъемником называют инструмент в виде
Рис.8. Набитые верхняя и нижняя опоки - полуформы: 1 - модели
выпоров: 2 - модель отливки; 3 - модель стояка; 1 4 - литниковая чаша; 5 - верхняя опока; 6 - модель шлакоуловителя; 7 - центрирующий штырь; 8 - нижняя опока
стержня с резьбой на конце, ввинчивающийся в отверстие в модели. Подъемники могут соединяться с моделью и другим белее удобным способом. Если есть повреждения полуформ, их исправляют.
При сборке формы (смотрите рис.2) в нижнюю полуформу.
устанавливают стержень 16 и затем по штырям И накрывают верхней полуформой. Опоки скрепляют скобами 12. После спаривания опок внутри образуется рабочая полость литейной формы 17. которая будет заполнена металлом через литниковую систему.
Форму устанавливают на заливочный участок, где производится заливка металла в форму из ковша. Металл должен быть предварительно очищен от шлака. Струя металла падает с небольшой высоты в литниковую чашу. Перерыв в процессе заливки не допускается. Заливка прекращается, как только металл появится в выпоре.
После остывания металла форма разрушается и из нее извлекается отливка. Затем из отливки удаляется стержень, производится обрубка элементов литниковой системы и очистка отливок.
6. ПОРЯДОК ВЫПОЛНЕНИЯ РАБОТЫ
1. Изучить принципиальную конструкцию песчаной литейной формы.
2. Изучить конструкцию литниковой системы.
3. Изучить конструкцию опок, модели отливки и моделей элементов литниковой системы.
4. Изучить составы и свойства формовочной и стержневой смесей.
5. Изготовить самостоятельно песчаную форму вручную.
6. Оформить отчет в соответствии с вариантом задания, предложенным преподавателем.
7. ФОРМА ОТЧЕТА
1. Эскиз отливки в разрезе по плоскости симметрии в соответствии с вариантом задания (увеличить все размеры пропорционально в 2 раза). '2. Эскиз стержня с указанием его частей.
3. Эскиз модели отливки с указанием ее частей, уклонов и плоскости разъема.
4. Эскиз литейной песчаной формы с указанием всех частей.
5. Последовательность операций при изготовлении песчаной
литейной формы.
Состав, свойства и различия формовочной и стержневой смесей.
9. КОНТРОЛЬНЬЕ ВОПРОСЫ
1. Какие детали автомобиля и трактора получают литьем?
2. Преимущества и недостатки литья в песчаные формы.
3. Состав и свойства формовочной и стержневой смесей.
4. Различия между эскизами отливки и модели.
5. Зачем нужна плоскость разъема песчаной литейной формы и модели?
6. Модель, ее назначение и конструкция.
7. Литейные уклоны, их назначение и величина.
8. Литниковая система, ее элементы и назначение.
9. Стержень, его конструкция и назначение.
10. Конструкция литейной формы.
11. Последовательность операций при изготовлении песчаной литейной формы.
ЛИТЕРАТУРА
1. Технология конструкционных материалов/ Под ред. A.M. Дальского/ М.: Машиностроение. .1993.
2. ГОСТ 18169-86. Процессы технологические литейного производства. Термины и определения.
studfiles.net
Технология литья ювелирных опок,литье в китайские опоки.
Отливка опоки (видео)
- Необходимые инструменты для литья ювелирной опоки:
- Металл должен быть очищен от загрязнений, отбелен, приготовлен по весу, указанному в каталоге. В каталоге указан вес, в золоте 585 пробы, для серебра расчет металла на 20% меньше.
- Металл закладывают в углубление, в опоке, далее необходимо произвести прогрев опоки (не нагревая, резко в одном месте) снизу и с двух, трёх сторон до красного каления железной оболочки опоки; после прогрева производится плавка металла, крупные опоки желательно прогревать в муфельной печи, или производить прогрев и плавку двумя горелками.
- После полного расплавления металла, одновременно убирая горелку, быстро и перпендикулярно накрываем опоку кружкой с глиной, и плавно надавливаем, так чтобы опока продавила глину на 1-1,5 см. Движение должно быть достаточно быстрым и уверенным.
- По прошествии минимум 15 секунд убираем кружку, а глину выравниваем, а при необходимости увлажняем; опоку опускаем в воду и очищаем отливку от смеси. Очистку лучше производить в ультразвуковой мойке.
- Далее металл нормализуется отжигом до малинового каления, отбеливается, шлифуется, полируется и т.д.
- Важный момент. Опока должна быть целой и не влажной.
Дефекты при отливке :
-
Грубая поверхность отливки, тёмный цвет, трудности с отбеливанием.
- низкая температура расплава;
- грязный металл.
-
Вспыхивание.
- Слишком быстро происходит процесс накрывания и давления;
- Влажность в опоке;
- Прогрев слишком быстро.
-
Отливка не целая, отлились только фрагменты.
- Процесс проходит слишком быстро;
- Присутствие влажности;
- Недостаточно металла;
- Температура слишком низкая.
- Слишком много металла.
-
Металл пористый, раковины.
- Буры слишком много;
- Металл не чистый;
- Температура слишком высокая;
- Присутствие влаги.
1. После выбора необходимой ювелирной опоки из каталогов компании Ювелин, учитывайте что вес в каталоге указан с технологическим запасом.
рис. Установите опоку воронкой вверх на подставку из огнеупорного материала.
2. Проверьте аппарат для плавки и топливо в нём. Убедитесь что прессовочная смесь нормальной влажности и однородная.
рис. Нормальная вязкость пасты соответствует вязкости пластелина.
3. Поместите необходимое количество металла в опоку, настройте пламя, прогрейте опоку со всех сторон (для больших моделей можно использовать две горелки или предварительно прогреть опоку на газовой плите).
Затем направьте пламя на металл и нагревайте его до нужной температуры (до жидкого состояния). Для получения более качественного расплава, добавьте 1-2 крупинки буры.
4. Когда металл окончательно расплавился, медленно вдавите прессовочную смесь в опоку (старайтесь не убирать горелку, сколько это возможно).
Для удаления формомассы погрузите опоку в ультразвуковую ванну.
1. Не повреждайте опоку давлением, ударами, влажностью. 2. Уделяйте достаточное внимание прессовочной смеси: она должна быть однородной, не очень мягкой и слегка влажной. 3. Не делайте очень сильное пламя в начале прогрева. 4. Во время прессовки не нажимайте слишком сильно и быстро. 5. Литье должно проходить без встрясок и вибраций. 6. Количество металла не должно быть большим, чем указано + допуск. 7. Для производства одного изделия идет столько опок, сколько указано номеров под каждым изделием в каталоге. Иногда требуется 2 или 3 опоки.
www.uvelin.ru
Технологий изготовления литейных форм - Литейное производство
Технологий изготовления литейных формКатегория:
Литейное производство
Технологий изготовления литейных формИзготовляемые в настоящее время отливки характеризуются большим разнообразием, что вызывает необходимость применения различных литейных форм и материалов.
1. Классификация литейных форм
Литейные формы классифицируются в зависимости от материала, из которого они изготовлены, и состояния при заливке.
Разовые формы служат для формообразования только одной отливки, после чего они разрушаются. Формы изготовляются из песчано-глинистых, песчано-смоляных и других смесей.
Разовые формы могут быть сырыми (формовка по сырому), сухими (формовка по сухому), подсушиваемыми, химически отверж-дающимися и собираемыми из сухих или отвержденных стержней.
Сырые формы благодаря их дешевизне, простоте и быстроте изготовления, отсутствию процесса сушки имеют наибольшее применение. Они используются для отливок простой и средней сложности из чугуна, стали и сплавов цветных металлов массой до 1500 кг.
Сухие формы предназначены для изготовления средних и крупных отливок с большим объемом механической обработки. Хорошо просушенная прочная форма, покрытая противопригарной краской, обеспечивает получение высококачественных отливок. Однако длительный цикл сушки (6—36 ч и более), значительный расход топлива, повышенная трудоемкость выбивки отливок из форм делают их неэкономичными. Они заменяются поверхностно подсушиваемыми и химически отверждаемыми формами.
Подсушиваемые формы изготовляют из формовочных смесей, в состав которых вводят связующие СП, СБ, КТ. Эти формы применяют для ответственных отливок из чугуна и стали массой от 1000 до 8000 кг. Длительность сушки таких форм в 10 раз меньше, чем обычных сухих форм.
Химически отверждаемые формы предназначены для изготовления отливок из стали, чугуна и сплавов цветных металлов массой 100 т и более. Существуют две разновидности таких форм: одни отверждаются при продувке или обдувке их углекислым газом, а вторые —самоотверждающиеся — при кратковременной выдержке в атмосфере цеха.
В последнее десятилетие широкое распространение получил процесс химического упрочнения формы, основанный на применении жидких самоотверждающихся формовочных смесей (ЖСС), содержащих в качестве связующего жидкое стекло и ускоритель его твердения (катализатор) — шлак феррохромового производства.
Многократно используемые (полупостоянные) формы служат для изготовления средних и крупных отливок простой конфигурации массой до 15 т. Эти формы выполняют из высокоогнеупорной смеси, состоящей в основном из шамота, формовочной глины и кварцевого песка. После соответствующей тепловой обработки стойкость форм достигает 25—40 съемов.
К многократно используемым формам относятся также металлические формы-кокили для отливок из различных сплавов простой и средней сложности, мелких и средних по массе и размерам (в серийном и массовом производстве).
Рис. 1. Приспособление для шаблонной формовки.
2. Формовочный инструмент и приспособления
При изготовлении форм и стержней применяют различные инструменты, опоки и приспособления.
Инструмент. Наиболее полный набор инструмента используется при формовке вручную. Технические условия на инструмент регламентированы ГОСТ 11775—74 — 11801—74.
Для засеивания модели облицовочной смесью предназначены прямоугольные сита с металлической сеткой с ячейками 2—6 мм. Прямоугольными совковыми лопатами наполняют смесью опоки, а лопатами с заостренным концом выкапывают ямы при формовке в почве.
Смесь в опоках уплотняют различными трамбовками:— при работе на верстаках— короткой трамбовкой (длиной 300 мм). Рукоятка такой трамбовки выполнена из алюминиевого сплава, а клиновидный и плоский башмаки — из Ст. 40 либо из маслобензо-стойкой резины марки А повышенной твердости;— при уплотнении смеси в средних и крупных опоках наиболее производительной является пневматическая трамбовка. Башмаки ее выполняют из чугуна марки СЧ18-36 или, что предпочтитель-нее, из маслобензостойкой резины марки А повышенной твердости.
Трамбовка приводится в движение сжатым воздухом давлением 5—6 кгс/см2.
Гладилки служат для заглаживания форм. В недоступных для гладилок местах для этих целей применяют ланцеты. Отделку вогнутых поверхностей и углублений производят двухконечными ложечками. Выглаживание неглубоких цилиндрических поверхностей, углов галтелей и других криволинейных поверхностей осуществляют фасонными гладилками/ Оставшиеся частицы смеси из глубоких полостей удаляют крючками.
Песок с модели и поверхностей форм сметают волосяной щеткой-косматкой, которая предназначена также для окраски и замывки крупных форм. Лучшее качество окраски получается при пользовании пульверизатором.
Вентилирование форм производят с помощью душников — игл разных диаметров.
Рис. 10.2. Типы опок. делей в форме осущест
Крупные модели расталкивают металлическим молотком, при этом в модель должны быть врезаны специальные стальные пластинки, чтобы предохранить ее от порчи. Из полуформ модели вынимают с помощью остроконечных и винтовых подъемов.
При формовке по шаблону с вертикальной осью вращения применяют приспособление, изображенное на рис. 10.1. Оно состоит из подпятника-башмака, шпинделя, стопорного кольца и рукава, на котором закрепляют шаблон.
Опоки должны обладать высокой прочностью, жесткостью и минимальной массой. Они изготовляются из чугуна марок не ниже СЧ15-32, низкоуглеродистой стали 20Л — ЗОЛ-1, алюминиевых и магниевых сплавов.
Опоки бывают цельнолитыми и сварными. По конфигурации различают прямоугольные, фасонные и круглые опоки.
В зависимости от массы они делятся на ручные, комбинированные и крановые. Ручные опоки без смеси имеют массу до 30 кг, а со смесью — не более 60 кг; комбинированные без смеси — от 31 до 60 кг, а со смесью — более 60 кг; крановые как без смеси, так и со смесью — свыше 60 кг.
Для точной сборки полуформ применяют штыри, изготовляемые из стали марок 40—45 с закалкой и последующим шлифованием. Различают съемные и постоянные штыри. Последние укрепляют в ушках нижней опоки, а в крупных опоках — в полках продольных стенок. Съемные штыри имеют наибольшее применение при машинной формовке.
Для взаимозаменяемости опок центрирующие отверстия в их ушках сверлят по кондуктору. В эти отверстия запрессовывают стальные каленые втулки, что дает возможность заменить их при износе и тем самым обеспечить точность спаривания опок.
При выборе размеров опок следует исходить из наименьших допустимых толщин формовочной смеси на различных участках формы.
3. Изготовление форм вручную
При формовке вручную литейные формы изготовляют по деревянным цельным и разъемным моделям, модельным плитам, скелетным моделям и шаблонам.
4. Формовка в почве
При формовке в почве наиболее ответственной операцией является подготовка нижней части формы — постели. Различают два вида постели: мягкую и твердую.
Мягкая постель. При изготовлении единичных мелких отливок для каждой из них подготавливают постель в почве. При производстве серии однотипных отливок в полу литейного цеха вырывают яму глубиной на 100—125 мм больше высоты модели и габаритами, превышающими габариты модели на 200—250 мм на сторону. На дне ямы оставляют четыре кучки смеси; на две из них укладывают деревянную рейку, а на другие две — рейку.
На эти рейки кладут линейку и уровнем-ватерпасом проверяют горизонтальность их положения. Затем рейки окучивают смесью, уплотняют ее и вновь проверяют горизонтальность их положения. После этого пространство между рейками засыпают отработанной формовочной смесью, выравнивают ее, а излишек сгребают линейкой. На рейки укладывают бруски высотой 10—12 мм, а на слой отработанной смеси наносят слой просеянной облицовочной смеси.
Сняв бруски, уплотняют ее следующим образом: первый формовщик прижимает линейку к рейке, а второй, приподнимая и опуская другой конец линейки, уплотняет смесь на участке в 300—400 мм. После этого второй формовщик прижимает линейку к рейке, а первый производит уплотнение смеси.
Окончательное выравнивание поверхности и удаление борозд достигается при движении линейки вдоль реек. Выровненную поверхность засеивают тонким слоем облицовочной смеси. На полученную постель лицевой стороной укладывают модель и ударами молотка или трамбовки осаживают ее через промежуточную прокладку.
Твердую постель применяют при изготовлении форм для средних и крупных отливок. В полу цеха выкапывают яму глубиной на 300—400 мм больше высоты модели. Дно ямы плотно утрамбовывают, насыпают на него слой просеянной гари или битого кирпича толщиной 150—200 мм, слегка утрамбовывают его и выравнивают мелкой гарью.
Рис. 3. Схема изготовления мягкой постели.
Рис. 4. Схема изготовления твердой постели: 1 — слой гари; 2— вентиляционные каналы; 3— облицовочный слой смеси; 4 — вентиляционные трубы.
Поверхность слоя выравнивают линейкой и затем душником диаметром 9 мм накалывают вентиляционные каналы до гаревой постели.
Приготовленную таким образом постель засеивают слоем (в 40—50 мм) облицовочной смеси. После уплотнения в нем также накалывают вентиляционные каналы душником диаметром 3—4 мм.
5. Формовка в парных опоках
Наибольшая точность размеров отливок достигается при формовке в опоках. Широкое распространение получила формовка в парных опоках. Формовку сложных по конфигурации отливок осуществляют в трех, четырех и более опоках. Пример изготовления отливки тройника в парных опоках приведен на рис. 5.
Процесс формовки начинают с изготовления нижней полуформы. На подмодельный щиток укладывают нижнюю половину модели и два питателя, а на модель наносят слой облицовочной смеси и обжимают ее руками. В опоку засыпают наполнительную смесь и уплотняют ее. Счистив излишнюю смесь, душником накалывают вентиляционные каналы.
Полученную полуформу скрепляют с подмодельным щитком и кантуют на 180°, устанавливают на разрыхленную площадку формовочного плаца, слегка притирают, после чего открепляют и снимают щиток. Затем проглаживают лад, посыпают его сухим кварцевым песком и сдувают песок с модели. Наложив верхнюю половину модели и шлакоуловитель, устанавливают модели стояка и выпоров.
Рис. 5. Формовка в парных опоках: 1 — нижняя полуформа; 2 — верхняя полуформа; 3 — стержень.
После этого в такой же последовательности изготовляют верхнюю полуформу.
Уплотнение ее должно быть равномерным, без местных слабин и переуплотнений. Степень уплотнения смеси проверяют твердомером. Она зависит от массы и высоты отливки.
Для повышения прочности верхней половины формы ее укрепляют стальными крючками или деревянными колышками — «солдатиками», предварительно смоченными жидкой глиной.
Вынув модели стояка и выпоров, можно раскрыть форму. При формовке мелких моделей после уплотнения смеси половины модели удерживаются в полуформе и не требуют дополнительного крепления. При формовке средних и крупных тяжелых моделей трение между формовочной смесью и моделью недостаточно для удержания ее в верхней полуформе и необходимо дополнительное укрепление ее. Закрепив модель подъемом к верхней опоке, раскрывают форму, удаляют половины моделей и отделывают верхнюю и нижнюю полуформы, затем устанавливают стержень и собирают форму.
6. Формовка по модельным плитам
При этом способе формовки нижнюю и верхнюю полуформы изготовляют раздельно по двум модельным плитам.
Формовку по плитам целесообразно осуществлять в мелкосерийном производстве. На многих ленинградских предприятиях — в объединениях имени Карла Маркса, имени Я. М. Свердлова, «Невский завод» имени В. И. Ленина и др. — она успешно применяется при мелкосерийном производстве сравнительно крупногабаритных отливок (длиной более 3 м и массой до 3 т).
Раздельная формовка по плитам обеспечивает:— повышение точности отливок;— увеличение производительности труда на 15—20% за счет сокращения отделочных операций;— возможность изготовления моделей из отдельных частей с последующей сборкой их на модельной плите;— повышение съема отливок с формовочной площади в 1,5 раза за счет установки форм в 2—3 этажа со сдвижкой.
При мелкосерийном производстве применяют плиты из прочного деревянного щита, а при серийном — чугунные строганые. Модельные плиты-могут использоваться многократно.
Комплект модельных плит для изготовления отливки корпуса текстильной машины средних размеров (920X420X400 мм) показан на рис. 6.
Формовочные работы осуществляются бригадой из двух формовщиков. Для уменьшения утомляемости рабочих модельные плиты устанавливают на низкие козлы.
Рис. 6. Комплект модельных плит для формовки корпуса: а — плита для нижней полуформы; б — плита для верхней полуформы; 1 — плита; 2 — центрирующие втулки; 3— модель.
Работа ведется в следующей последовательности:— очистка модели и плиты и нанесение разделительного состава;— установка на плиты опок низа и верха;— нанесение на модели облицовочной смеси, установка крючков (в верхней полуформе) и обжатие смеси;— заполнение опок наполнительной смесью, уплотнение ее, удаление излишков и накол вентиляционных каналов;— скрепление модельных плит с опоками и их кантовка; установка нижней полуформы на подготовленный плац, открепление модельной плиты, съем ее и отделка (при надобности)— полуформы;— установка стержней;— открепление и съем верхней плиты, отделка (при надобности) полуформы;— сборка формы.
На собранную полуформу укладывают чугунную плиту (иногда деревянную), на которую устанавливают вторую форму со сдвижкой для установки литниковой чаши.
7. Химически отверждающиеся и крупные оболочковые формы
При изготовлении форм по С02-процессу в формовочную смесь в качестве связующего вводят жидкое стекло. Облицовочный слой жидкостекольной смеси наносят на модель слоем в 20—40 мм, а остальной объем опоки заполняют наполнительной смесью. Все операции изготовления формы выполняют в той же последовательности, как и при формовке с применением песчано-глинистых смесей. После удаления модели и отделки формы ее продувают углекислым газом, при этом она быстро отверждается. Затем форму собирают.
Химически отверждающиеся смеси используются и при изготовлении крупных оболочковых форм, которые применяют при производстве средних и крупных отливок. Форма для стальной отливки подушки прокатного стана массой 10 т показана на рис. 7.
Оболочки изготовляют по тщательно обработанной разъемной деревянной модели, натертой графитом.
Процесс состоит из следующих операций:— на строганый подмодельный щиток укладывают нижнюю половину модели;— на него же устанавливают разборный деревянный жакет, в стенках которого высверлены отверстия диаметром 9—10 мм. Расстояние между стенками жакета и модели должно составлять примерно 120—150 мм;— в зазор между моделью и жакетом устанавливают сварной каркас для упрочнения оболочки;— слоями высотой 80—100 мм засыпают жидкостекольную смесь, уплотняют ее, между отдельными слоями смеси закладывают стальные прутки диаметром 8 мм для образования продувочных каналов, которые не должны доходить до модели на 20—25 мм; – с горизонтальной поверхности счищают излишки смеси, и накалывают продувочные каналы;— удаляют стальные прутки и через продувочные каналы продувают полученную оболочку углекислым газом;— отвержденнуго оболочку вместе с моделью и жакетом кантуют на 180°;— извлекают модель, раскрывают деревянный жакет и удаляют его.
В такой же последовательности изготовляют верхнюю оболочку.
Сборку полуформ производят в рамке, состоящей из двух опок без ребер. Нижнюю опоку укладывают на выровненную площадку и засеивают наполнительной смесью, которую затем уплотняют. На полученную постель устанавливают нижнюю оболочку и зазоры между ней и опокой засыпают сухой смесью. В знаки оболочки устанавливают оболочковый стержень, накладывают верхнюю оболочку и вторую опоку и засыпают ее сухой смесью слоем в 150 мм.
Рис. 7. Комбинированная форма с оболочковыми вставками: а — нижняя оболочка; б — верхняя оболочка; в — оболочковый стержень; г — собранная форма; д — отливка.
Остальную часть опоки заполняют металлическими шарами диаметром 40 мм. Перед заливкой форму дополнительно нагружают грузами.
Применение оболочковых форм, отвержденных до извлечения из них моделей, дает возможность получать оболочки с размерами рабочих поверхностей, соответствующих размерам модели. Кроме того, модели таких форм выполняют разборными, что позволяет ликвидировать на них формовочные уклоны, требующие дополнительного расхода металла.
8. Формовка по шаблону
Формовка по шаблону осуществляется при производстве единичных средних и крупных отливок, имеющих наружную форму тел вращения простой конфигурации (чаши, маховики, патрубки, трубы с фланцами в т. п.),
Различают следующие виды шаблонной формовки: с вертикальным шпинделем, с горизонтальным шпинделем и по протяжка блонам Наибольшее распространение получила формовка вертикальным шпинделем. Рассмотрим ее на примере формообразования отливки чаши размалывающих бегунов.
Дня шаблонной формовки чаши (рис. 8, а) требуются: станок с вертикальной осью, шаблонная мерка (рис. 8, б), шаблоны для заточки болвана с телом (рис. 8, в) и болвана чаши (рис. 8, г), модели ребер (рис. 8, д) и ступицы с центровым отверстием (рис. 8, е). Формовка производится в почве (с твердой постелью) под верхней опокой.
Рис. 8. Приспособления для шаблонной формовки чаши бегунов.
Процесс состоит из ряда этапов. На первом затачивают болван с телом, который будет служить моделью для изготовления верхней полуформы; на втором осуществляют операции по изготовлению верхней полуформы; на третьем затачивают нижнюю полуформу; на четвертом отделывают и собирают форму; на пятом нагружают форму, заливают и выбивают отливки.
9. Формовка по скелетной модели
При единичном производстве крупных отливок с целью снижения затрат на изготовление моделей применяют скелетные модели, толщина ребер которых принимается равной толщине стенок отливки.
Скелетная модель для изготовления отливки крупной ванны показана на рис. 9, а, а схема формовки — на рис. 9, б. Модель заформовывают в опоке или в почве. Внутреннюю полость заглаживают на уровне брусков и полученную поверхность обкла дывают бумагой. Затем изготовляют верхнюю полуформу с болваном. После разъема верхнюю полуформу отделывают, а в нижней снимают разделительную бумагу, уплотненную между ребрами смесь слегка разрыхляют и шаблоном-сгребалкой снимают слой смеси на толщину ребер. После этого модель извлекают, и изготовление формы заканчивают обычным способом.
Рис. 9. Схема формовки по скелетной модели.
10. Формовка в глине по кирпичу
Формовку в глине по кирпичу осуществляют при производстве таких крупных отливок, как изложницы, ковши, котлы, трубы больших диаметров и т. а Формовку ведут по модели, каркасной модели или по шаблону.
Последовательность изготовления формы и стержня для отливки крупного патрубка приведена на рис. 10. В твердой постели устанавливают подпятник, шпиндель и рукав, на котором укрепляют шаблон. Правильность установки шпинделя проверяют ватерпасом. На чугунный поддон наносят слой глины и выкладывают первый ряд кладки из красного кирпича. На него наносят слой глины толщиной 15—20 мм и выкладывают второй ряд с перекрытием швов в первом ряду.
Для повышения газопроницаемости между рядами кирпичей прокладывают мелкую гарь, гранулированный ваграночный шлак, пучки соломы и душником выполняют вентиляционные каналы в подсохшей глине. Для увеличения прочности кладки через каждые 5—6 рядов укладывают чугунные плиты, соединяемые с нижним поддоном и между собой стяжками.
Правильность кладки проверяют шаблоном. Между рабочей кромкой шаблона и поверхностью кладки должен быть зазор в 20—25 мм. Внутреннюю поверхность кладки облицовывают глиной и шаблоном затачивают рабочую поверхность. После кратковременного провяливания на воздухе удаляют шаблон и шпиндель и сушат форму переносным сушилом. Затем заделывают трещины форму окрашивают и сушат вторично.
Рис. 10. Изготовление кирпичной формы и стержня по шаблону: а — изготовление формы; б — изготовление стержня; в — собранная форма; г—отливка; 1 — подпятник; 2— шпиндель; 3— поддон; 4 — опоры; 5 — кирпичная кладка; 6 —- шаблон для заточки формы; 7 — литниковая система; 8 — облицовочная глина.
Процесс изготовления стержня аналогичен процессу выполнения формы. Сушат стержень в сушиле.
Кирпичную кладку выполняют в специальных кессонах или опоках с заполнением промежутков между кладкой и стенкой опоки формовочной смесью. Такие формы могут использоваться многократно при небольших промежуточных ремонтах.
Современные способы изготовления крупных форм вручную
Непрерывный рост производства крупных отливок требует совершенствования технологических процессов и условий труда снижения трудоемкости изготовления отливок при ручной формовке рассмотрим некоторые рациональные процессы формообразования отливок, разработанные литейщиками ленинградских объединений имени Я. М. Свердлова, «Невский завод» имени В И Ленина и других предприятий.
Металлические постели. При формовке крупных отливок применяют твердые песчано-глинистые постели, а при изготовлении особо крупных отливок постель выполняют кирпичной кладкой. При извлечении отливки из формы постель частично разрушается, и перед каждой формовкой приходится затрачивать много времени на ее ремонт.
Рис. 11. Схема приготовления твердой металлической постели: 1 — слой гари; 2 — металлическая плита; 3 — газоотводные трубы; 4 — кессон; 5 —верхняя полуформа.
Форма с металлической постелью, выполненная в кессоне, показана на рис. 11. Зазоры между стенками кессона и моделью определяются удобством набивки формы. Дно кессона покрывают ровным слоем гари, поверх которого кладут чугунную плиту, образующую металлическую жесткую постель.
Замена верхней полуформы стержнями
Во избежание протечки металла при заливке обычно приме няют прокладочную глину, в результате чего на отливке образуются заливы, на удаление которых затрачивается труд обрубщиков и бесцельно расходуется металл. При замене верхней полуформы перекрывающими стержнями вместо прокладочной глины стали использовать песчаные подушки. Для этого в горизонтальных знаках стержней, через которые выводятся газы, выполнены углубления в 20—25 мм, заполняемые сырым песком с некоторым завышением. При установке перекрывающих стержней песок уплотняется, при этом создаются надежная изоляция вентиляционных каналов и плотный контакт между стержнями, исключающий возможность образования заливов.
Рис. 12. Технология изготовления крупных форм: а — старая технология; б — новая технология: 1 — нижние почвенные полуформы; 2— верхняя полуформа; 3 — прокладочная глина; 4 — пригрузочная плита; 5 — стержень, заменяющий верхнюю опочную полуформу; 6 — вентиляционные стояки; 7 — песчаные подушки.
В результате внедрения новой технологии повысилась размерная точность отливок, сократился расход металла, ликвидированы парк опок и потребность в сушке громоздких полуформ, уменьшилась трудоемкость обрубных работ. Формовка по блок-модели. При изготовлении мелких серии средних и крупных отливок целесообразно объединение в один блок двух однотипных моделей, связанных между собой разделительным стержнем.
Изготовление форм из жидких самоотверждающихся смесей. Чти смеси широко используются при изготовлении крупных стержней Так в литейных цехах объединения имени Я. М. Свердлова все стержни для отливок массой более 3 т выполняют из ЖСС.
Практика показала, что эти смеси могут успешно применяться и при изготовлении форм для крупных отливок. Схема формовки в ЖСС представлена на рис. 14. Модель устанавливают на кирпичи или на укрепленные на ней специальные упоры либо фиксируют в кессоне с помощью планок. Между моделью и стенками кессона должен быть зазор в 100—150 мм. В модели имеются люки для заливки ЖСС. Для улучшения заполняемости формы смесь выдавливают из люков толкателями. После заполнения смесью пространства под моделью ее заливают по периметру кессона в зазоры между его стенками и моделью. Через 35-40 мин после заливки ЖСС модель можно извлечь и приступить к отделке формы.
Рабочая поверхность формы имеет значительную пористость. Для ее устранения на поверхность наносят специальную краску и просушивают- горелкой в течение 2—4 ч при температуре 200— 220 °С.
Технология изготовления сложной формы для отливки чугунной модели лопасти массой 35 т приведена на рис. 15. Эта модель предназначена для формообразования крупных отливок стальных лопастей. Формовка ведется по деревянной модели, снабженной упорами, по которым модель устанавливают на постель, в кессоне. На модели размещают съемную раму, оформляющую контуры болвана. Во избежание всплывания модель и рама нагружаются.
Заливку ЖСС осуществляют через люки, имеющиеся в модели и съемной раме, и в зазоры между стенками кессона и съемной рамы. Затем производят подпрессовку смеси толкателями. После кратковременной выдержки извлекают съемную раму, удаляют смесь из люков, подрезают ее вокруг модели, поверхность полуформы покрывают разделительной бумагой и закрепляют ее шпильками, после чего переходят к оформлению верхней полуформы (болвана-стержня).
Рис. 13. Технология изготовления форм по блок-модели а — почвенная форма; б — стержневая форма.
Рис. 14. Схема изготовления формы из ЖСС.
Рис. 15. Технология изготовления крупной формы с применением
12. Машинная формовка
Механизированное извлечен И модели без предварительной расколотки обеспечивает получени форм высокого качества, повышает точность отливок и снижает брак. Внедрение координатных и наборных плит-рамок делает табельным применение машинной формовки не только при серий” ном и массовом, но и при мелкосерийном и единичном производстве.
Обычно литейную форму изготовляют на двух машинах: одной — нижнюю полуформу, а на другой — верхнюю. При массовом и серийном производстве металлические модели и элементы литниковой системы монтируют на односторонних чугунных плитах, а при мелкосерийном и единичном деревянные модели
укрепляют на координатных плитах или в наборных плитах-рамках. Замену модели на координатной плите и в плите-рамке производят на рабочем месте в течение 20—30 мин.
По способу уплотнения смеси в опоке различают прессовые машины с нижним и верхним прессованием, встряхивающие машины, встряхивающие с подпрессовкой и пескометные.
Уплотнение смеси на машинах с нижним прессованием. Схема работы такой машины приведена на рис. 17. На прессовом поршне, помещенном в цилиндре, закреплен стол. На нем расположена модельная плита, перемещающаяся в неподвижной раме. Опоку устанавливают на штыри неподвижной рамы и заполняют смесью, разравнивая ее по всей Поверхности, После этого опоку со смесью помещают под неподвижную траверсу. При подаче в цилиндр сжатого воздуха прессовый поршень поднимается вверх, модель внедряется в смесь и уплотняет ее. Когда поступление воздуха прекращается, поршень опускается, и производится извлечение модели.
При нижнем прессовании наибольшая плотность смеси создается у модели и понижается к верху,опоки, несколько возрастая у траверсы, что является достоинством этого способа.
Большой расход мощности на преодоление силы трения смеси о стенки опоки ограничивает область применения этих машин. Они могут использоваться при опоках с размерами в свету до 1100X800 мм и высотой до 150 мм.
Уплотнение смеси на машинах с верхним прессованием. Схема работы этой машины показана на рис. 18. На прессовом поршне, помещенном в цилиндре, закреплен стол, на котором расположена плита с моделью. После установки опоки с наполнительной рамкой и заполнения их формовочной смесью в цилиндр подают сжатый воздух под давлением 6 кгс/см2. Под действием воздуха поршень вместе со столом и смонтированной на нем модельной оснасткой поднимается вверх, при этом прессовая колодка, закрепленная на траверсе, внедряется в наполнительную рамку и уплотняет смесь в опоке.
После прекращения поступления в цилиндр сжатого воздуха стол опускается под действием собственной тяжести.
Уплотнение смеси на встряхивающих машинах. Этот способ уплотнения смеси, несмотря на некоторые присущие ему недостат ки, — самый распространенный, так как дает возможность изготовлять формы для сложных крупных отливок в опоках, с размерами в свету 3000 X 2000 мм при высоте до 750 мм.
Рис. 16. Типы модельных плит: а — односторонняя; б — координатная: в —наборная плита-рамка; 1 — основная плита; г — вкладная модельная плита; 3 — модель, 4 — шлакоуловитель; 5 — стояк; 6 — упорные винты.
Рис. 17. Схема работы машины с нижним прессованием.
На рис. 19 показана схема работы встряхивающей машины с подпрессовкой. Она имеет два цилиндра: прессовый и встряхивающий, причем последний служит поршнем для первого Внутри цилиндра имеется встряхивающий поршень, на котором укреплен стол. На столе монтируется модельная плита с моделью.
По штырям на модельную плиту устанавливают опоку с рамкой . После заполнения опоки и рамки смесью в полость встряхивающего цилиндра подают сжатый воздух, под давлением которого встряхивающий поршень поднимается вверх. При этом впускное отверстие перекрывается боковой поверхностью поршня, а выхлопное открывается, и воздух выходит в атмосферу.
Стол с модельной плитой и опокой под действием собственной силы тяжести падает на торец цилиндра, поэтому при ударе формовочная смесь в опоке уплотняется. При опускании поршня впускное отверстие вновь открывается, и цикл повторяется. Обычно стол поднимается на высоту 30—80 мм и совершает 30—120 ударов в минуту. Для уплотнения смеси достаточно 20—40 ударов.
После окончания процесса встряхивания сжатый воздух поступает в полость прессового цилиндра, а модельная плита и оснастка приходят в контакт с прессовой колодкой, закрепленной на траверсе. Колодка входит в полость наполнительной рамки и производит доугоготнение верхних слоев смеси (рис. 19, г и д).
Уплотнение смеси многоплунжерной головкой. При уплотнении смеси жесткой прессовой колодкой (рис. 19), особенно в формах крупных габаритов, трудно достичь равномерности уплотнения. В таких случаях рекомендуется применять многоплунжерную головку (рис. 20), при этом формовочная смесь прессуется большим количеством прессующих башмаков, снабженных поршневыми гидравлическими приводами. Каждый башмак под действием масла на поршень прессует находящийся под ним участок формы независимо от соседних участков.
Уплотнение смеси пескометами широко применяется для механизации наполнения и уплотнения смеси в крупных опоках и стержневых ящиках. Производительность пескометов — от 12 Д° 80 м3/ч уплотненной смеси.
Основным рабочим органом пескомета является головка (рис. 21). В стальном кожухе вращается ротор, на котором с помощью муфты закреплена лопатка-ковш. Через окно в кожухе ленточный транспортер непрерывно подает формовочную смесь, которая при быстром вращении ротора захватывается лопаткой, несколько уплотняется и в виде небольших пакетов выбрасывается в опоку через окно. При большой скорости истечени смеси из окна и непрерывном перемещении головки пескомета л площади опоки создается равномерное уплотнение всех слоев смес независимо от высоты опоки.
Извлечение модели из формы
Рис. 18. Схема работы машины с верхним прессованием.
Рис. 19. Схема работы встряхивающей машины
Рис. 20. Схема процесса уплотнения смеси в опоке многоплунжерной головкой: 1 — модель; 2 —опока; 3 — наполнительная рамка; 4— прессующая многопл-унжерная головка; 5 — поршни; 6 — прессующие башмаки.
Рис. 21. Схема работы пескометной головки: 1 — рукоятка; 2 — направляющая дуга; 3 — лопатка-ковш; 4 — окно; 5 —кожух; 6 — ротор; 7 — вал электродвигателя; 8 — окно.
Рис. 22. Схемы извлечения моделей при машинной
Автоматизированные формовочные линии. В настоящее время в СССР успешно эксплуатируются автоматизированные формовочные линии как отечественного производства — конструкции ВНИИлит-маш, НИИтракторсельхозмаш, Гипросантехпром и др., так и зарубежных фирм.
Процесс формовки, сборки и выбивки на этих линиях полностью автоматизирован, рабочий-оператор при этом только, управляет механизмами с помощью кнопок.
Вручную выполняются операции установки стержней и заливки, а на некоторых линиях процесс заливки также автоматизирован.
На рис. 23 показана схема автоматизированной линии фирмы «Гизаг» (ГДР). Она состоит из двух прессовых формообразующих полуавтоматов для изготовления нижней (поз. IV) и верхней (поз. II) полуформ и литейного конвейера (поз. VII). Собранная на поз X форма поступает на поз. XI — к грузовому конвейеру, где она нагружается, и на поз. XII, где заливается металлом. При дальнейшем движении залитая форма поступает в охладительную камеру (поз. XIII), снабженную мощной вентиляционной системой. На поз. XIV с охлажденной формы снимается груз.
Верхняя опока протяжным устройством стягивается на поз. I и передается на машину для изготовления верхних полуформ (поз. II). Нижняя полуформа с отливкой и комом смеси продвигается к поз. III, где нижняя опока протягивается, кантуется и передается на машину для изготовления нижних полуформ (поз. IV).
При подходе к толкателю ком смеси с отливкой передается на поз. V— охладительную решетку (накопитель). После кратковременного охлаждения он поступает на поз. VI — выбивную решетку, где разрушается и освобождает отливку.
Формообразующая машина имеет два пресса, между которыми расположены подъемный механизм и дозатор смеси. При поступлении опоки она спаривается с модельной плитой и поджимается к бункеру-дозатору, при этом в опоку выдается определенная порция смеси. Затем опока передается под левый или правый пресс, имеющий многоплунжерную головку.
После процесса прессования ниясняя полуформа возвращается на среднюю позицию, где после протяжки модели она выталкивается поступающей опокой и передается на поз. VIII. Здесь нижняя полуформа кантуется и устанавливается на платформу конвейера. На поз. IX в эту полуформу устанавливаются стержни.
При подходе к поз. X нижняя полуформа накрывается верхней, и форма поступает на заливку. Верхняя полуформа изготовляется аналогично нижней.
Производительность линии в зависимости от типа формовочного автомата и размеров опок составляет 200—280 форм в час.
Рис. 23. Схема автоматизированной формовочной линии.
Читать далее:
Cушка, отделка и сборка форм
Статьи по теме:
pereosnastka.ru
Опока литейная - Энциклопедия по машиностроению XXL
ОПОКИ и МОДЕЛИ Опоки литейные [c.18]Линия с несколькими формовочными блоками и подачей выбитых опок литейным конвейером [c.68]
Олово 136, 137 — Химический состав 138 Операции финишные 429 — Классификация 430—432 Опоки литейные — Требования к опокам и их материал 265 для изготовления гипсовых форм по восковым моделям 398 Оснастка технологическая — Назначение 263, 264 — См. также Комплекты модельные, Опоки литейные. Плиты мо-дельные, Плиты сушильные. Скобы центрирующие, Штыри центрирующие Отклонения предельные коробления 8ле-ментов отливок 11, 12 — Степень коробления 11 массы отливок И [c.523]
Опока литейная 285, 290, 293, 295 Оправка 439, 455, 463, 469 [c.509]Опоки литейные сварные из литых стальных элементов прямоугольные размерами в свету длиной от 1000 до 1200 мм, шириной 700, 800 мм, высотой 450, 500 мм. Конструкция и размеры [c.463]
Опоки литейные — это коробчатые приспособления, необходимые для удержания песчаных литейных форм при изготовлении, заливке и транспортировании. К опочным приспособлениям относятся также подопочные плиты, жакеты для безопочных форм и жакеты для сборки форм из стержней. [c.52]
Таблица 78 Опоки литейные цельнолитые | ![]() |
Литейная форма — это система элементов, образующих рабочую полость, при заливке которой расплавленным металлом формируется отливка. На рис. 4.2, а показана литейная форма для тройника (рис. 4.2, б). Форма обычно состоит из нижней 2 и верхней 6 полуформ, которые изготовляют по литейным моделям 7 (рис. 4.2, г) в литейных опоках 3, 5. Литейная опока — приспособление для удержания формовочной смеси при изготовлении формы. Верхнюю и нижнюю полуформы взаимно ориентируют с помощью цилиндрических металлических штырей 4, вставляемых в отверстия приливов у опок. Для образования полостей, отверстий или иных сложных контуров в формы устанавливают литейные стержни /, которые фиксируют с помощью выступов (стержневых знаков), входящих в соответствующие впадины в форме. Литейные стержни изготовляют по стержневым ящикам (рис, 4.2, д). Для подвода расплавленного металла в полость литейной формы, ее заполнения и питания отливки при затвердевании используют литниковую систему 8—11. После заливки расплавленного металла, его затвердевания и охлаждения форму разрушают, извлекая отливку (рис. 4.2, е). [c.121]
Заливка форм производится в вертикальном или горизонтальном положении. При заливке в вертикальном положении литейные формы 6 помещают в опоки-контейнеры 7 и засыпают кварцевым песком или металлической дробью 8 (рис. 4.26, д) для предохранения от преждевременного разрушения оболочки при заливке расплава. [c.148]
Элементы литейной формы. Литейная форма представляет собой устройство, предназначенное для заливки металла н образования отливки (рис. 2.1). Она должна иметь рабочую полость /, где непосредственно формируется тело заготовки, а также литниковую систему, обеспечивающую подвод металла в рабочую полость и питание отливки в процессе кристаллизации. Конфигурация и размеры рабочей полости должны соответствовать очертаниям и размерам изготовляемой отливки. При этом следует иметь в виду, что размеры полости должны превышать размеры отливки на величину литейной усадки металла. В свою очередь, размеры отливки должны быть больше размеров детали на величину снимаемого при механической обработке технологического припуска. Таким образом, окончательные размеры рабочей полости литейной формы включают в себя соответствующие размеры детали, припуски на механическую обработку и на литейную усадку металла. Внутри некоторых отливок, а также на их наружной поверхности могут быть различные отверстия, полости и выемки. Для выполнения при сборке формы в ней устанавливаются соответствующие керамические или металлические элементы, называемые стержнями 8 (рис. 2.1). Стержни удаляются из отливки при выбивке, оставляя в ней после себя необходимые углубления или отверстия. Литниковая система (рис. 2.1) включает в себя чашу (воронку) 2, стояк 3, дроссель 4, регулирующий скорость заливки и предотвращающий вакуум (подсос воздуха) в стояке, шлакоуловитель 5, расположенный в верхней опоке для задержания неметаллических включений. [c.45]
Для изготовления стержней используются стержневые смеси, состоящие в основном из песка, связанного специальными веществами — крепителями (льняное масло, сульфитная барда, декстрин, канифоль и т. д.). Литейная форма обычно состоит из порознь изготовляемых ручным или машинным способом двух полуформ нижней и верхней. Каждая из полуформ изготовляется в специальных металлических ящиках без доньев и крышек, называемых опоками, При сборке формы опоки устанавливаются друг на друга и скрепляются. [c.46]
Рабочие полости для отливки в набитых формовочной смесью опоках получатся при помощи половинок разъемной модели, форма и размеры которой соответствуют форме и расчетным размерам рабочей полости. Сборка литейной формы из полуформ — опок— производится после извлечения половинок моделей и установки стержней в нижней полуформе. Стержни изготовляются в специальных приспособлениях — стержневых ящиках — и проходят обязательную сушку. [c.47]
Собранная форма, состоящая из скрепленных опок, с помощью специального ковша заливается через литниковую систему и остается на месте заливки до завершения кристаллизации и охлаждения тела отливки. Затем опоки раскрепляются и на специальной установке производится выбивка отливки из формы. Затем производятся обрубка и очистка, во время которых от отливки отделяется литниковая система с прибылями, удаляются остатки формовочной и стержневой смесей и осуществляется очистки поверхности отливки от различных дефектов. Проводимая после этого термическая обработка имеет целью устранить грубозернистую, дендритную структуру металла, литейные напряжения и подготовить металл отливки к механической обработке. [c.47]
На фиг. 314—318 показаны способ изготовления литейной модели глухого подшипника (фиг. 313) с расчленением на части, способ закладки ее в опоку — земляную форму — для получения литой заготовки и последующей механической обработки рабочих поверхностей. [c.124]
Тбилисский научно-исследовательский институт приборостроения и средств автоматизации создал управляющую вычислительную машину, предназначенную для автоматизации загрузки вагранки и стабилизации ее теплового процесса. Этот же институт экспонировал в действии устройство программного управления серийным пескометом, предназначенным для набивки опок. Ленинградский Кировский завод создал автоматическую линию для изготовления литейных форм методом прессования. Была создана действующая на Уральском автомобильном заводе линия для производства мелкого литья с применением формовочных автоматов. Заводы Красная Пресня , им. Войкова, Челябинский тракторный и многие другие также продемонстрировали свои достижения в области автоматизации литейного производства. [c.279]
Выбивка форм состоит из удаления кома с отливкой из опоки и из отделения отливки от смеси. Первой операции на литейных безопочных линиях нет. При выбивке форм без крестовин ком удаляется как до разъединения полуформ, так и после их разъединения. В последнем случае отливка принудительно оставляется в нижней полуформе, а так как отливку покрывает тонкий слой смеси, то увеличивается скорость охлаждения отливки, что позволяет несколько уменьшить время охлаждения. [c.220]
Литейные безопочные линии существенно отличаются qt остальных автоматических линий. Отсутствие дорогостоящих опок не только резко удешевляет первоначальные и эксплуатационные затраты, но и резко упрощает многие механизмы линии. Это относится к выбивным установкам, в которых нет механизма удаления кома из опоки и механизма съема опоки с конвейера для выбивки, отсутствуют транспортные средства для возврата опок к формовочным машинам, что, кроме того, упрощает схему линии (нет замыкания линии). Линии надежны в работе и имеют высокую производительность. На линии используются только высокопрочные смеси с сырой прочностью на сжатие свыше 0,2—0,25 МПа. [c.221]
Перед заливкой на форму специальным подвесным конвейером 2 укладывают грузы. После заливки и охлаждения формы сталкиваются с литейного конвейера на выбивную установку 10, с которой выбитые опоки поступают в сборе на роликовый конвейер И. Роликовый конвейер перемещает опоки к формовочным блокам и одновременно является транспортным накопителем опок. Неиспользованные опоки перемещаются к установке 3 возврата, которая передает их на свободные тележки конвейера. [c.230]
Рис. 11.81. Ударно-вибрационная машина для изготовления литейных форм и стержней. Вибратор I с ударником б подвешен под столом 2 с наковальней 7 на пружинах 3, подобранных на ударный резонанс. На столе укрепляется модель 4 и опока 5 с формовочной смесью. При надлежащем подборе зазора (натяга) между наковальней и ударником, последний будет наносить периодические удары. Одновременно с формовкой действием ударов и вибраций может осуществляться прессование, если предусмотреть податливую упругую подушку 9. Пружины S служат амортизаторами машины. | ![]() |
Участок текущего ремонту моделей, прессформ. кокилей и опок литейном цехе [c.334]
При изготовлении формы (фиг. 17-4) эта сборка шишек 1 производится в яме на сдвигаемых по рельсам 10 полуплитах 11. После того кругом канальных шишек закладываются отрезки кольцевых шишек 2 и 3 яма кругом них засыпается землей, -в которой прокладываются шамотные трубы-литгаики 6 и оставляются пустоты для прибылей (запасов металла для пополнения его усадки в форме при его остывании) 9. Внутренняя, служившая для центровки ось 11 вынимается, сред-дяя полость заполняется формовочной землей. Сверху накладывается опока (литейная рамка) 13 с отформованными в ией верхней поверхностью верхнего обода, прибылями и литниками, т. е. каналами, через которые производится заливка его чугуном. При заливке сталью предпочитаются литники, показанные слева. [c.241]
Snap flask — Обжимная опока. Литейная опока с одним угловым шарниром, позволяющим открыть и удалить шаблон для повторного использования прежде, чем будет залит металл. [c.1046]
Чем больше вес формуемой детали, тем больше должны быть сечения ее каналов. Если бы для детали большого веса сделать литниковую систему с узкими каналами, то заливка такой детали продолжалась бы слишком долго. При слишком медленной заливке поверхность земли в верхней опоке литейной формы может подсушиться от металла и осыпаться. Кроме того, при очень медленной заливке может получиться брак по недоливу или спаям и заворотам металла на поверхности отливки, когда металл слишком загустевает, стынет и теряет свою текучесть. [c.186]
Модели. Для получения отливок обычно применяют земляные литейные формы (разовые), изготовляемые по деревянным или металлическим моделям в металлических опоках. Литейные формы можно также изготовлять из металла (постоянные формы) или из огнеупорной глины (полуностоянные формы). [c.148]
Опоки литейные 52 Оптические измерительные приборы 652 Осадка 180 Осипов Ц. 322 Осциллатор 256 Отверстие 594 Отделка колеблющимися брусками 377 Отжиг 294 [c.669]
Подготовка под сварку зависит от вида исправляемого дефекта. Одпако по всех случаях подготовка дефектного места заключается в тщательной очистке от загрязнений и в разделке для образования полостей, обеспечивающих доступность для манипулирован ня электродом и воздействня сварочной дугп. Для предупреждения вытекания жидкотекучего металла сварочной ванны, а в ряде случаев для придания наплавленному металлу соответствующей формы, место сварки формуют. Формовку выполняют в зависимости от размеров и местоположения исправляемого дефекта с помощью графитовых пластинок, скрепляемых формовочной массой, состоящей из кварцевого песка, замешенного на жидком стекло, или другими формовочными материалами, а также в опоках формовочными материалами, применяелгыми в литейном производстве (рис. 154). [c.327]
Формовка в и а р и ы X опоках по разъемной м о -дели наиболее распространена. Литейную форму (рис. 4.11, е), состоящую из двух полуформ, изготовли10т по разъемной модели (рис. 4.11, й) в такой последовательности на модельную плиту 3 устанавливают нижнюю половину модели 1, модели питателей 4 и опоку 5 (рис. 4.11, б), в которую засыпают формовочную смесь и уплотняют. Опоку поворачивают на 180° (рис. 4.11, в), устанавливают верхнюю половину модели 2, модели шлакоуловителя 9, стояка 8 и выпоров 7, По центрирующим штырям устанавливают верхнюю опоку 6, засыпают формовочную смесь и уплотняют. После извлечения модели стояка и выпоров форму раскрывают. Из полуформ извлекают модели (рис. 4.11, г) и модели питателей и шлакоуловителей, в нижнюю полуформу устанавливают стержень 10 (рис. 4.11, [c.134]
В последние годы в СССР разработан принципиально новый способ про изводства форм и стержней. С начала развития литейного производства литейные формы и стержни производились путем уплотнения встряхиванием или прессованием пластичных формовочных смесей. Разработанный к Ц11И-ИТМАШе под руководством А. М. Лясса и П. А. Барсука при участии работников ХПИ и завода Стапколит и др., новый способ основан на применении самотвердеющих жидкотекучих смесей [118]. Разработанные новые смеси вместо уплотнения просто заливаются в стержневые ящики и в опоки на модели. В зависимости от состава смеси, будучи залиты в ящики и формы, они затвердевают в короткий, заранее заданный срок. Применение нового процесса коренным образом меняет всю технологию этой части литейного производства, значительно упрощает и удешевляет его. ЦНИИТМАШем разработаны новые типовые механизированные и автоматизированные линии для применения нового способа в массовом производстве и установки для применения его в индивидуальном или мелкосерийном производстве. Лицензии на этот новый технологический процесс проданы Франции, Италии, Швеции, Дании, Норвегии и другим странам. Авторы этой работы были удостоены Ленинской премии. [c.101]
Первые советские машиностроительные заводы (Сталинградский и Харьковский тракторные. Горьковский автомобильный), построенные и введенные в эксплуатацию на рубеже 20-х и 30-х годов, оборудовались литейными конвейерами, пневматическими подъемниками для установки опок, подвесными конвейерами, передвижными электроталями (тельферами) с кабинами управления, электро- и автокарами (самоходными грузовыми тележками), закуц-ленными у иностранных фирм. Но тогда же внутри страны, наряду с уже упоминавшимся крановыми конвейерным оборудованием общего назначения, началось изготовление специальных сборочных и подвесных конвейеров на заводах Транстехнрома и аккумуляторных грузовых тележек на московском Г аводе Динамо с 1932 г. был прекращен импорт литейных конвейеров, а несколькими годами позднее Уральский завод тяжелого машиностроения приступил к выпуску ковочных кранов, используемых для выполнения транспортных и некоторых технологических операций в кузнечных и прессовых цехах. [c.182]
Охлажденная форма доставляется конвейером к перекладчику 4 форм с литейного конвейера на бортовой роликовый конвейер механизма выбивки 5, где из опок выдавливается ком с отливкой без его разрушения. Ком специальным устройством подается на одну из четырех ветвей пластинчатого конвейера 6, на котором отливка дополнительно охлаждается. В конце конвейера установлена выбивная решетка 7, на которой отливка отделяется от смеси. Выбитые опоки перемещаются на следующую позицию 19, где дополнительно прошиваются плитой с резиновой щеткой для очистки стенок от остатков формовочн.ой смеси. Перекладчик 8 переставляет опоки на продольный конвейер 9, [c.229]
По роликовым конвейерам опоки и полуформы перемещаются с помощью гидротолкателей. На позиции опоки и формы фиксируются с помощью пневмофиксаторов, горизонтальные конические штыри которых входят во втулки, имеющиеся на торцовых стенках опок. Тележки литейного конвейера очищаются от смеси щетками 18. Формовочные автоматы оснащены тележками 20 для смены модельных плит. [c.230]
КЛ 91265 СМ (рис. 14) предназначена для литейных цехов с серийным производством. В состав линии входят два автоматических формовочных блока 4 и более. Поступающие по роликовому конвейеру выбитые опоки стаскивате-лем 5 в сборе подаются на роликовый [c.230]
К подобным динамическим моделям приводит исследование динамики самых различных машин и устройств. Укажем в качестве примера на некоторые вибротранспортеры, выбивные решетки, нашедшие широкое применение в литейном производстве для целей выбивки опок и др. [c.231]
mash-xxl.info
Литейное производство
одна из отраслей промышленности, продукцией которой являются отливки (См. Отливка), получаемые в литейных формах при заполнении их жидким сплавом. Годовой объём производства отливок в мире превышает 80 млн. т, из которых около 25% приходится на СССР (1972). Методами литья изготовляется в среднем около 40% (по массе) заготовок деталей машин, а в некоторых отраслях машиностроения, например в станкостроении, доля литых изделий составляет 80%. Из всех производимых литых заготовок машиностроение потребляет примерно 70%, металлургическая промышленность — 20%, производство санитарно-технического оборудования — 10%. Литые детали используют в металлообрабатывающих станках, двигателях внутреннего сгорания, компрессорах, насосах, электродвигателях, паровых и гидравлических турбинах, прокатных станах, с.-х. машинах, автомобилях, тракторах, локомотивах, вагонах. Значительный объём литых изделий, особенно из цветных сплавов, потребляют авиация, оборонная промышленность, приборостроение. Л. п. поставляет также водопроводные и канализационные трубы, ванны, радиаторы, отопительные котлы, печную арматуру и др. Широкое применение отливок объясняется тем, что их форму легче приблизить к конфигурации готовых изделий, чем форму заготовок, производимых др. способами, например ковкой. Литьём можно получить заготовки различной сложности с небольшими припусками, что уменьшает расход металла, сокращает затраты на механическую обработку и, в конечном счёте, снижает себестоимость изделий. Литьём могут быть изготовлены изделия практически любой массы — от нескольких г до сотен т, со стенками толщиной от десятых долей мм до нескольких м. Основные сплавы, из которых изготовляют отливки: серый, ковкий и легированный чугун (до 75% всех отливок по массе), углеродистые и легированные стали (свыше 20%) и цветные сплавы (медные, алюминиевые, цинковые и магниевые). Область применения литых деталей непрерывно расширяется.
Историческая справка. Производство литых изделий известно с глубокой древности (2—1-е тысячелетия до н. э.): в Китае, Индии, Вавилоне, Египте, Греции, Риме отливали предметы вооружения, религиозного культа, искусства, домашнего обихода. В 13—14 вв. Византия, Венеция, Генуя, Флоренция славились своими литыми изделиями. В русском государстве в 14—15 вв. отливались бронзовые и чугунные пушки, ядра и колокола (на Урале). В 1479 построена в Москве «пушечная изба» — первый литейный завод. В царствование Ивана IV созданы литейные заводы в Туле, Кашире и др. городах. В 1586 А. Чохов отлил «Царь-пушку» (См. Царь-пушка) (около 40 т). При Петре I изготовление отливок увеличилось, были созданы литейные заводы на Урале, Юге и Севере государства. В 17 в. чугунные отливки экспортировались за границу. В России созданы замечательные образцы литейного искусства: в 1735 «Царь-колокол» (свыше 200 т) И. Ф. и М. И. Маториными, в 1782 памятник Петру I «Медный всадник» (22 т) Э. Фальконе, в 1816 памятник К. Минину и Д. М. Пожарскому В. П. Екимовым, в 1850 скульптурные группы Аничкова моста в Петербурге П. К. Клодтом и др. Одна из самых крупных отливок в мире — шабот (нижняя часть, воспринимающая удар) парового молота (650 т) изготовлена в 1873 на Пермском заводе. Известно мастерство литейщиков старых русских заводов — Каслинского, Путиловского, Сормовского, Коломенского и др.
Первые попытки научного обоснования некоторых процессов литья сделали в своих работах Р. Реомюр, М. В. Ломоносов и др. учёные. Однако до 19 в. при литье использовали ранее накопленный многовековой опыт мастеров. Лишь в начале 19 в. были заложены теоретические основы литейной технологии, были применены научные методы в решении конкретных производственных задач. Труды Д. Бернулли, Л. Эйлера, М. В. Ломоносова послужили прочной базой для разработки и совершенствования литейной технологии. В работах русских учёных П. П. Аносова, Н. В. Калакуцкого и А. С. Лаврова были впервые научно объяснены процессы кристаллизации (См. Кристаллизация), возникновения ликвации (См. Ликвация) и внутренних напряжений в отливках, намечены пути к повышению качества отливок. В 1868 Д. К. Чернов открыл критические точки (См. Критическая точка) металлов. Его труды продолжили А. А. Байков, А. М. Бочвар, В. Е. Грум-Гржимайло, позднее Н. С. Курнаков и др. русские учёные. Большое значение для развития Л. п. имели работы Д. И. Менделеева.
В годы Советской власти Л. п. развивалось ускоренными темпами: в 1922 впервые налажено производство отливок из алюминиевых сплавов, в 1929 — из магниевых; с 1926 производилась реконструкция существовавших литейных цехов и строительство новых. Строились и вводились в эксплуатацию литейные цехи с высокой степенью механизации, с выпуском отливок до 100 тыс. т и более в год. Одновременно с перевооружением и механизацией Л. п. в СССР проводилось внедрение новой техники, создавались основы теории рабочих процессов и методы расчётов литейного оборудования. В 20-е гг. начала формироваться советская научная школа, основателями которой являются Н. П. Аксенов, Н. Н. Рубцов, Л. И. Фанталов, Ю. А. Нехендзи и др.
Технология литейного производства. Процесс Л. п. многообразен и подразделяется: по способу заполнения форм — на обычное литьё, Литьё центробежное, Литьё под давлением; по способу изготовления литейных форм — на литьё в разовые формы (служащие лишь для получения одной отливки), литьё в многократно используемые керамические или глиняно-песчаные формы, называется полупостоянными (такие формы с ремонтом выдерживают до 150 заливок), и литьё в многократно используемые, так называемые постоянные металлические формы, например кокили, которые выдерживают до нескольких тыс. заливок (см. Литьё в кокиль). При производстве заготовок литьём используют разовые песчаные, оболочковые самотвердеющие формы. Разовые формы изготовляют с помощью модельного комплекта (См. Модельный комплект) и опоки (См. Опока) (рис. 1). Модельный комплект состоит из собственно литейной модели (См. Литейная модель), предназначенной для получения в литейной форме полости будущей отливки, и стержневого ящика для получения литейных стержней, оформляющих внутренние или сложные наружные части отливок. Модели укрепляют на модельных плитах, на которых устанавливают опоки, заполняемые формовочной смесью. Заформованную нижнюю опоку снимают с модельной плиты, переворачивают на 180° и в полость формы вставляют стержень. Затем собирают (спаривают) верхнюю и нижнюю опоки, скрепляют их и заливают жидкий сплав. После затвердевания и охлаждения отливку вместе с литниковой системой (См. Литниковая система) извлекают (выбивают) из опоки, отделяют литниковую систему и очищают отливку — получается литая заготовка.
Наиболее распространено в промышленности производство отливок в разовых песчаных формах. Этот способ применяется для изготовления из различных сплавов заготовок любых размеров и конфигурации. Технологический процесс литья в песчаные формы (рис. 2) складывается из ряда последовательных операций: подготовка материалов, приготовление формовочных и стержневых смесей, изготовление форм и стержней, простановка стержней и сборка форм, плавка металла и заливка его в формы, охлаждение металла и выбивка готовой отливки, очистка отливки, термообработка и отделка.
Материалы, применяемые для изготовления разовых литейных форм и стержней, делятся на исходные Формовочные материалы и формовочные смеси; их масса равна в среднем 5—6 т на 1 т годных отливок в год. При изготовлении формовочной смеси используют отработанную формовочную смесь, выбитую из опок, свежие песчано-глинистые или бентонитовые материалы, добавки, улучшающие свойства смеси, и воду. В стержневую смесь (См. Стержневые смеси) обычно входят кварцевый песок, связующие материалы (масло, смола и др.) и добавки. Приготовление смеси производят в определённой последовательности на смесеприготовительном оборудовании (См. Смесеприготовительное оборудование); ситах, сушилах, дробилках, мельницах, магнитных сепараторах, смесителях и т. п.
Формы и стержни изготовляют на специальном формовочном оборудовании (См. Формовочное оборудование) и станках. Насыпанная в опоки смесь уплотняется встряхиванием, прессованием или совместно тем и др. способом. Крупные формы заполняют с помощью Пескомётов, реже для изготовления форм используют пескодувные и пескострельные машины. Формы в опоках, заформованные в стержневых ящиках стержни подвергаются тепловой сушке или химическому твердению, например при литье в самотвердеющие формы (См. Литьё в самотвердеющие формы). Тепловую сушку осуществляют в литейных сушилах, а сушку стержней производят также в нагретом стержневом ящике. Сборка форм состоит из следующих операций: установка стержней, соединение половин форм, закрепление форм скобами или грузами, устанавливаемыми на верхнюю форму и предотвращающими их раскрытие при заливке сплавом. Иногда на форму устанавливают литниковую чашу, изготовленную из стержневой или формовочной смеси.
Плавят металл в зависимости от вида сплава в печах различного типа и производительности (см. Плавильное оборудование). Наиболее часто литейный чугун выплавляют в Вагранках, применяют также электрические плавильные печи (тигельные, электродуговые, индукционные, канального типа и др.). Получение некоторых сплавов из чёрных металлов, например белого чугуна, ведут последовательно в двух печах, например в вагранке и электропечи (т. н. дуплекс-процесс). Заливку форм (См. Заливка форм) сплавом осуществляют из заливочных ковшей, в которые периодически поступает сплав из плавильного агрегата. Затвердевшие отливки обычно выбивают на вибрационных решётках (См. Вибрационная решётка) или коромыслах. При этом смесь просыпается через решётку и поступает в смесеприготовительное отделение на переработку, а отливки — в очистное отделение. При очистке отливок с них удаляют пригоревшую смесь, отбивают (отрезают) элементы литниковой системы и зачищают заливы сплава и остатки литников. Эти операции проводят в галтовочных барабанах, дробеструйных и дробемётных установках. Крупные отливки очищают гидравлическим способом в специальных камерах. Обрубку и зачистку отливки осуществляют пневматическими зубилами и абразивным инструментом. Отливки из цветных металлов обрабатывают на металлорежущих станках.
Для получения необходимых механических свойств большинство отливок из стали, ковкого чугуна, цветных сплавов подвергают термической обработке (См. Термическая обработка). После контроля качества литья и исправления дефектов отливки окрашивают и передают на склад готовой продукции.
Механизация и автоматизация литейного производства. Большинство технологических операций в Л. п. очень трудоёмко, протекает при высокой температуре с выделением газов и кварцесодержащей пыли. Для уменьшения трудоёмкости и создания нормальных санитарно-гигиенических условий труда в литейных цехах применяют различные средства механизации и автоматизации технологических процессов и транспортных операций. Внедрение механизации в Л. п. относится к середине 20 в. Тогда для приготовления формовочных материалов начали использовать бегуны, сита, рыхлители, а для очистки отливок — пескоструйные аппараты. Были созданы простейшие формовочные машины с ручной набивкой форм, позднее стали применять гидравлические прессы. В 20-х гг. появились и быстро распространились пневматические встряхивающие формовочные машины. На каждой технологической операции стремились заменить ручной труд машинным: совершенствовались оборудование для изготовления форм и стержней, устройства для выбивки и очистки отливок, механизировалась транспортировка материалов и готовых отливок, были внедрены конвейеры, разработаны методы поточного производства. Дальнейший рост механизации Л. п. выражается в создании новых усовершенствованных машин, литейных автоматов и автоматических литейных линий, в организации комплексно-автоматизированных участков и цехов. Наиболее трудоёмкие операции при производстве отливок — формовка, изготовление стержней и очистка готовых отливок. На этих участках литейных цехов в наибольшей степени механизированы и частично автоматизированы технологические операции. Особенно эффективно внедрение в Л. п. комплексной механизации и автоматизации. Перспективными являются автоматические линии формовки, сборки и заливки форм сплавом с охлаждением отливок и их выбивкой. Например, на линии системы Бюрер — Фишер (Швейцария) (рис. 3) изготовление форм, заливка их сплавом и выбивка отливок из форм автоматизированы. Успешно работает установка для автоматической заливки форм сплавом на непрерывно движущемся конвейере (рис. 4). Масса жидкого сплава для заполнения форм контролируется электронным аппаратом, учитывающим металлоёмкость определённой формы. Установка снабжена автоматической смесеприготовительной системой, контроль качества формовочной смеси и регулирование смесеприготовления осуществляются автоматическим устройством (системы «Молдабилити-контроллер», Швейцария).
Для финишных операций (очистки и зачистки отливок) применяют проходные барабаны непрерывного действия с дробемётными аппаратами. Крупные отливки очищают в камерах непрерывного действия, вдоль которых отливки передвигаются на замкнутом транспортёре. Созданы автоматические очистные камеры для отливок, имеющих сложные полости. Например, фирмой «Омко-Нангборн» (США — Япония) разработана камера типа «Робот». Каждая такая камера представляет собой независимый механизм для транспортировки отливок, который работает автоматически, выполняя команды, поступающие от так называемых модулей управления, расставленных на монорельсовой транспортной системе. В зоне очистки по заранее заданной программе с оптимальной скоростью вращается подвеска, на которую автоматически навешивается отливка. Двери камеры открываются и закрываются автоматически.
При массовом производстве предварительная (черновая) зачистка отливок (обдирка) осуществляется в литейных цехах. Во время этой операции также подготавливаются базы для механической обработки отливок на автоматических линиях в механических цехах. Заключительные операции могут производиться и на автоматических линиях. На рис. 5 показана автоматическая линия японской фирмы «Норитакэ» для зачистки блоков цилиндров автомобиля. Такая линия позволяет обработать 120 блоков за 1 ч.
Возможности механизации и автоматизации Л. п. особенно возросли после разработки принципиально новых технологических процессов литья, например изготовление оболочковых форм, или Кронинг-процесс (40-е гг., ФРГ), изготовление стержней отверждением в холодных стержневых ящиках (50-е гг., Великобритания), изготовление стержней с отверждением их в горячих стержневых ящиках (60-е гг., Франция). Еще в 40-е гг. в промышленности начали применять метод изготовления отливок высокой точности по выплавляемым моделям. За относительно короткий срок все технологические операции процесса были механизированы. В СССР создано комплексно-автоматизированное производство литья по выплавляемым моделям с выпуском 2500 т мелких отливок в год (рис. 6).
Лит.: Нехендзи Ю. А., Стальное литье, М., 1948; Гиршович Н. Г., Чугунное литье, Л. — М., 1949; Фанталов Л. И., Основы проектирования литейных цехов, М., 1953; Рубцов Н. Н., Специальные виды литья, М., 1955; его же, История литейного производства в СССР, 2 изд., ч. 1, М., 1962; Аксенов П. Н., Технология литейного производства, М., 1957; его же, Оборудование литейных цехов, М., 1968.
Д. П. Иванов, В. Н. Иванов.
Рис. 1. Основные элементы литейной оснастки при получении отливки в разовой форме: а и б — модельный комплект верхней и нижней полуформы с опокой; в и г — верхняя и нижняя заформованные опоки; д — формовка стержневого ящика; е — литейная форма, подготовленная к заливке; 1 — направляющий штырь; 2 — подмодельная плита; 3 — стол формовочной машины; 4 — стержневой знак; 5 — модель; 6 — головка пескострельной машины; 7 — стержневой ящик; 8 — стержень.
Рис. 2. Основы операции технологического процесса получения отливки в песчаной форме.
Рис. 3. Автоматическая линия системы Бюрер — Фишер (Швейцария) для изготовления форм, заливки их сплавом и выбивки готовых отливок.
Рис. 4. Установка для автоматической заливки форм на конвейере завода Г. Фишер (Швейцария).
Рис. 5. Автоматическая линия зачистки блока цилиндров со шлифовальными агрегатами (фирма «Норитакэ», Япония).
Рис. 6. Комплексно-автоматизированный цех литья по выплавляемым моделям с годовым выпуском 2500 т отливок в год.
slovar.wikireading.ru
Опока для изготовления литейных вакуумно-пленочных форм
Изобретение относится к литейному производству. Опока содержит корпус с внутренними полостями по всему периметру, внутренние стенки с окнами и фильтрующими элементами, цапфы с отверстиями для соединения с вакуумирующей системой. Внутренние стенки образуют рабочую полость. Части внутренних стенок выполнены с наклоном от точки, находящейся в диапазоне середина высоты опоки ±10%. Части внутренних стенок наклонены к центру плоскости лада под углом 15-25°. Достигается снижение величины разрежения в вакуумно-пленочной форме с обеспечением требуемой прочности формы и повышение качества отливок. 1 з.п. ф-лы, 2 ил.
Изобретение относится к литейному производству, в частности к конструкции опок для вакуумно-пленочной формовки.
Известны конструкции опок [1], корпус которых содержит внутреннюю полость, выполненную по всему периметру опоки, и которая через отверстие в цапфах посредством гибкого вакуумпровода соединяется с вакуумирующей системой. Во внутренних вертикальных стенках опоки выполнены окна с фильтрующими элементами, через которые посредством внутренней полости в стенках опок, отверстий в цапфах, гибкого вакуумпровода и вакуумирующей системы создается разрежение ΔР в песчаном наполнителе формы, придавая ему некоторую прочность, характеризуемую его напряженным состоянием.
Это напряженное состояние обеспечивается одноосным, одновременным, двухсторонним сжатием со стороны атмосферного давления в виде равномерно распределенной нагрузки, действующей на песчаный наполнитель формы через полимерную пленку, ограничивающую форму со стороны ее лада и контрлада. При этом распределение главных больших (сжимающих) напряжений в массиве песчаного наполнителя, подобно распределению напряжений в песчано-глинистой форме при двухстороннем последовательном прессовании [2], подчинено экспоненциальной зависимости, описываемой в [3] и зависит от величины разрежения ΔР, создаваемого вакуумирующей системой. Критерием прочности песчаного наполнителя вакуумно-пленочной формы является точка перегиба кривой распределения напряжений по высоте формы. В указанной точке как главные большие σ1, так и главные меньшие σ2 напряжения имеют минимальное значение.
Известно [4], что главные меньшие напряжения σ2 связаны с главными большими σ1 зависимостью:
где ξ - коэффициент бокового давления, который в сыпучих средах может достигать значения 0,4.
В свою очередь σ2, действуя на стенки опоки, обуславливает наличие силы трения в паре стенка опоки - песчаный наполнитель, которая удерживает вес песка в опоке в статическом состоянии и может быть определена по формуле:
где f - коэффициент трения в паре стенка опоки - песчаный наполнитель.
При вертикальных стенках опоки (α=0) сила трения имеет минимальное значение.
Недостатком этих опок (опок с вертикальными стенками) является то, что для удержания в них веса песчаного наполнителя в статическом состоянии необходимо создать в нем разрежение ΔР, которое сформировало бы в песке такие главные меньшие напряжения σ2, которые, в свою очередь, в паре стенка опоки - песчаный наполнитель, вызовут действие сил трения, способных удержать вес песка в статическом состоянии. При этом, чем больше габариты опоки, тем большее разрежение необходимо создать в песчаном наполнителе формы, так как его вес при этом увеличивается. Однако увеличение величины разрежения как технологического фактора отрицательно сказывается на качестве отливок [5].
Известна опока [6], которая по технической сущности и назначению наиболее близка к заявляемому техническому решению и принята за прототип, корпус которой содержит внутренние вертикальные стенки, внутри корпуса по всему периметру опоки выполнена внутренняя полость, которая посредством отверстия, выполненного в цапфе, и гибкого вакуумпровода соединяется с вакуумирующей системой. Во внутренних стенках опоки выполнены окна с фильтрующими элементами, через которые посредством внутренней полости в стенках опоки, отверстий в цапфах, гибкого вакуумпровода и вакуумирующей системы создается разрежение в песчаном наполнителе формы. Внутренние стенки указанной опоки выполнены вертикальными.
Недостатком известной опоки является то, что вес песчаного наполнителя, засыпанного в опоку, удерживается в статическом состоянии только за счет сжимающей разности давлений ΔР - атмосферного и остаточного в поровом объеме наполнителя.
Известно, что основным силовым фактором, удерживающим вес песчаного наполнителя в опоке, предназначенной для вакуумно-пленочной формовки, является сила трения. Поскольку внутренняя стенка известной опоки вертикальна, то компонента от действия веса песчаного наполнителя не принимает участия в формировании главных меньших напряжений σ2, соответственно и сила трения в паре стенка опоки - песчаный наполнитель от данной составляющей отсутствует. Для удержания общего веса песчаного наполнителя в известной опоке при прочих равных условиях необходимо создать повышенное разрежение ΔР, что отрицательно скажется на качестве отливок.
Техническим результатом заявляемого изобретения является снижение величины разрежения в поровом объеме песчаного наполнителя вакуумно-пленочной формы при сохранении ее прочности, что приводит к повышению качества отливок.
Указанный результат достигается тем, что в опоке для изготовления литейных вакуумно-пленочных форм, содержащей корпус с внутренними полостями по всему периметру, лад, образующие рабочую полость внутренние вертикальные стенки с окнами и фильтрующими элементами, цапфы с отверстиями для соединения с вакуумирующей системой, внутренние стенки от середины их высоты ±10% выполнены с наклоном к центру плоскости лада.
Кроме того, нижние части внутренних стенок опоки наклонены к вертикали под углом 15-25°.
При такой геометрии внутренних стенок опоки в формировании сил трения в паре стенка опоки - песчаный наполнитель участвуют компоненты главных меньших напряжений σ2. Эти напряжения действуют в «скелете» песчаного наполнителя, а их величина зависит от сжимающих главных больших напряжений σ1, которые представлены в выражении (2) первым слагаемым. При этом величина напряжений σ1 обуславливается величиной разрежения ΔР. Кроме этого, на величину указанной силы трения будет оказывать влияние и составляющая от веса песчаного наполнителя в опоке, которая входит в выражение (2) вторым слагаемым. Таким образом, величина силы трения на стенках опоки с наклоном от вертикали к центру плоскости лада будет складываться из компонент двух силовых факторов - главных меньших напряжений σ2 и горизонтальной составляющей от веса песчаного наполнителя, засыпанного в опоку. Предлагаемая опока с изменяющейся геометрией внутренней стенки, выполненной наклонной к центру плоскости лада от точки, находящейся в диапазоне середина высоты опоки ±10%, позволяет снизить величину разрежения ΔР при прочих равных условиях по сравнению с опокой с вертикальными стенками на 20-25%, что позволяет повысить качество отливок без потери прочностных свойств самой формы.
Изобретение поясняется чертежами. На фиг.1 представлена опока в разрезе, на фиг.2 - схема сил, действующих на наклонную стенку опоки со стороны песчаного наполнителя, где
G - вес наполнителя,
Р - сила действия наполнителя на вертикальную стенку,
Р' - нормальная составляющая веса наполнителя на наклонную стенку,
Р" - нормальная составляющая от σ2 или главного меньшего напряжения,
Т' - касательная составляющая на наклонную стенку от действия σ2,
Т" - касательная составляющая на наклонную стенку от веса наполнителя G.
Опока содержит корпус 1, внутри которого по его периметру выполнена полость 2, сообщающаяся через отверстие 3 в цапфах 4 с вакуумирующей системой (не показана). Внутренние стенки опоки, содержащие вертикальные части 5 и наклонные части 6 образуют рабочую полость для размещения песчаного наполнителя. Наклонные части 6 внутренних стенок 1 от середины высоты опоки ±10% выполнены с наклоном к центру плоскости лада 7. Наклонные части 6 внутренних стенок наклонены к вертикали под углом 15-25° в частном случае выполнения опоки. В вертикальных частях 5 и наклонных частях 6 внутренних стенок опоки выполнены окна 8 с фильтрующими элементами (не показаны). Через окна 8 с фильтрующими элементами посредством внутренней полости 2 в корпусе опоки 1, отверстий 3 в цапфах 4 вакуумирующей системой создается разрежение ΔР в поровом объеме песчаного наполнителя, размещенного в рабочей полости опоки. Объем опоки замыкается контрладом 9.
Опока работает следующим образом. После заполнения опоки 1 песчаным наполнителем, герметизации ее лада 7 и контрлада 9 полимерными пленками вакуумирующей системой через полость 2 в стенках опоки, отверстие 3 в цапфе 4 и окно 8 с фильтрующими элементами во внутренних стенках опоки в поровом объеме песчаного наполнителя создается разрежение ΔР. Разрежение ΔР формирует главные меньшие напряжения σ2 на вертикальных 5 и наклонных 6 частях внутренних стенок опоки. Величина напряжений σ2 зависит от величины главных больших напряжений σ1 (см. уравнение (1)), нормальных к горизонтальным поверхностям лада 7 и контрлада 9, которые зависят от величины разрежения ΔР. Кроме этого, на наклонную часть 6 внутренней стенки опоки будет действовать компонента от силы веса песчаного наполнителя (см. фиг.2).
Суммарное действие от компонент σ2 и веса песчаного наполнителя формы формирует максимальное значение силы трения на наклонной части внутренних стенок опоки (см. уравнение (2)), что при прочих равных условиях в сравнении с опоками с вертикальными внутренними стенками и с опокой с выпуклыми во внутрь стенками позволяет уменьшить величину разрежения в поровом объеме песчаного наполнителя формы на 20-25% и 30-42% соответственно.
Уменьшение величины разрежения ΔР в предлагаемой опоке при сохранении необходимой прочности песчаного наполнителя вакуумно-пленочной формы позволяет уменьшить (исключить) вероятность появления брака отливок, в частности, по газовым дефектам и пригару из-за неоправданно завышенной степени разрежения.
Использованные источники
1. Минвев А.А., Ноткин Е.Б., Сазонов В.А. Вакуумная формовка. - М.: «Машиностроение». 1984, с.138.
2. Рабинович Б.В. Последовательное прессование. «Литейное производство», №4, 1974, с.27.
3. Иванов В.В. Критерии оценки прочности вакуумно-пленочных форм. «Литейное производство», 1993, №10, с.22.
4. Цытович Н.А. Механика грунтов. - М.: «Высшая школа», 1979, с.115.
5. Иванов В.В. и др. Брак отливок, изготавливаемых в вакуумно-пленочных формах, и меры по его предупреждению. «Литейное производство», 2005, №5, с.20.
6. Литейное производство: Учебник для металлургических специальностей вузов. - 2-е изд., перераб. и доп. - М.: Машиностроение, 1987, с.96, рис.40.
1. Опока для изготовления литейных вакуумно-пленочных форм, содержащая корпус с внутренней полостью по всему периметру, лад, образующие рабочую полость внутренние стенки с окнами и фильтрующими элементами, цапфы с отверстиями для соединения полости корпуса с вакуумирующей системой, отличающаяся тем, что части внутренних стенок от середины их высоты ±10% наклонены от вертикали к центру лада.
2. Опока по п.1, отличающаяся тем, что наклонные части внутренних стенок составляют с вертикалью угол 15-25°.
www.findpatent.ru
Литейные заводы России
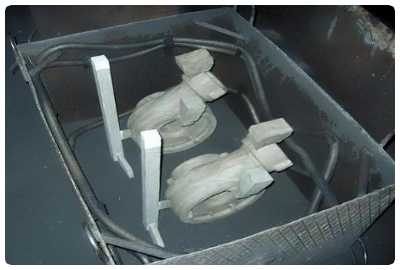
Литье по газифицируемым моделям (выжигаемым) (ЛГМ) — технологический процесс получения отливок, использующий модель, которую газифицируют при заливке. Точность отливки получается как при литье по выплавляемым моделям, а затраты сопоставимы с литьем в песчано-глинистые смеси.
Технологический процесс литья по газифицируемым моделям состоит из:
Изготовление моделей. Материал моделей — полистирол мелких фракций, который задувают в металлические пресс-формы, далее модели помещаю в автоклав, до спекания гранул полистирола.
Формирование куста и окраска моделей. Модели собирают в один блок при помощи припаивания или склеивания. Блоки красят в один слой противопригарным покрытием, окуная в ванну или же обливают, если они имеют сложную конструкцию.
Формовка. Формуют модели в специальные опоки на вибростоле постепенно засыпая песком, либо послойно. Этот этап очень важен, т.к. в дальнейшем влияет на качество отливки.
Подача опок за заливочный участок. Заформованные опоки подаются на заливочный участок, где вакуумируются, предварительно наверх формы укладывается полиэтиленовая пленка. Формовочная смесь приобретает необходимую прочность.
Заливка металла. Заливают горячий металл в полистирольные стояки, где он выжигает полистирол, занимая его место. Одновременно происходит откачка воздуха через слой краски в песок.
Охлаждение отливок. Залитые блоки отстаивают в песке от 5 минут до нескольких часов.
Отрезка и очистка деталий. Отливки отрезают от литниковой системы и отправляют на дальнейшую обработку от антипригарного покрытия.
Литье по газифицируемым моделям активно применяют во всем мире. Применение литья по газифицируемым моделям — важный шаг в области охраны окружающей среды. По сравнению с традиционным литейным производством все вредные химические соединения не выделяются в атмосферу, а поступают в систему очистки в вакуумной системе.
Отходы | Традиционный метод | ЛГМ-процесс |
Пыль | 50 кг | 16 |
Окись углерода | 250 кг | — |
Окись серы | 1,5 — 2 кг | 0,2 — 0,3 кг |
Твердые отходы | 1200 — 1500 кг | 0,05 — 1 |
Отработанная вода | 0,3 — 0,5 м3 | — |
Литье по газифицируемым моделям оптимально подходит для предприятий внедряющих концепцию бережливого производства.
Литье по газифицируемым моделям. Преимущества технологии:
- Уменьшение затрат на оборудование, вспомогательные материалы, электроэнергию, трудозатраты;
- Уменьшение числа технологических операций;
- Уменьшение отходов производства;
- Уменьшение финишных операций обработки отливки;
- Сокращение и оптимальное использование производственной площадки.
otlivka.info