Ручная плазменная резка: аппараты, оборудование, видео. Плазморез ручной
советы по выбору и использованию
Аппарат плазменной резки применяется для резки и сварки токопроводящих и других металлических материалов.
Используется для термообработки поверхностей, включая закалку металла, отжиг материалов для снижения твердости, зачистки верхнего слоя стали.
Для сварки цветных и черных металлов, а также для иных работ требующих интенсивного концентрированного нагрева твердых материалов.
Принцип действия аппарата плазменной резки описывают по следующей схеме: в канале сопла с узким сечением образуется электродуга, которая затем охлаждается под воздействием движущегося по каналу потока водяного пара.
В результате ионизирования пара вырабатывается струя плазмы,– температура теплового источника составляет около 60000.
При резке металла плазменным устройством, обширные участки обрабатываемого материала не накаляются, так как это происходит при разрезании металла кислородным резаком.
Назначение пара заключается в интенсивном охлаждении основных рабочих элементов горелки – сопла и катода, а также в поддержании устойчивости столба разряда тока и выдувки дуги.
Схема снабжения сопла паром представляет собой следующее действие: из резервуара плазменного аппарата пар самотеком проходит по каналам охлаждения в разрядную камеру, затем посредством канала сопла выходит в атмосферу.
Для эффективной стабилизации электродуги и ее оттискивания от стенок сопла, применяют тангенциальную или осевую схему подачи газа.
Виды аппаратов для плазменной резки металла
Отличительные технические характеристики аппаратов для плазменной резки и сварки металла, позволяют их разделить на виды.
На сегодняшний день потребительским спросом пользуются инверторные аппараты и трансформаторные источники резки.
При этом цена каждой конкретной модели зависит от мощности и продолжительности работы оборудования.
Видео:
Инверторные устройства характеризуются легким весом, компактными размерами и небольшим потреблением энергии.
Минусом использования данного типа аппаратов плазменной резки и сварки является их сверхчувствительность к сбою напряжения, из-за чего цена на подобные отечественные аппараты сравнительно невысокая.
Особенно эта проблема касается фирменных моделей, которые не приспособлены к эксплуатации в условиях наших электросетей.
При этом если из строя выйдет система защиты аппарата, без сервисного обслуживания уже не обойтись.
Кроме того инверторные устройства имеют ограничение по рабочей мощности, которое не превышает 70 А, и небольшой срок включения при большом токе.
Трансформаторные установки для резки и сварки металла считаются надежнее, чем инверторные типы.
Такие аппараты при падающем напряжении теряют рабочую мощность, но не выходят из строя. За счет чего и цена на данный тип плазморезов намного выше.
Трансформаторные устройства имеют высокий показатель продолжительности включения, при этом ПВ может доходить до 100% (при стандартной норме для ручной резки в 70 процентов).
Аппараты применяются для автоматической резки металла с применением ЧПУ.
При этом время беспрерывной эксплуатации плазмотрона намного превышает время функционирования устройства ручной резки.
Минусом трансформаторных установок являются тяжелый вес, большое энергопотребление и габариты.
Трансформаторные аппараты плазменной резки имеют между собой отличия, которые заключаются в разных технологиях охлаждения плазмотрона.
Видео:
Как правило, стационарные установки работают при водяном охлаждении, переносные аппараты – за счет воздушного охлаждения.
Устройства воздушно-плазменной резки имеют компактные размеры и небольшой вес, благодаря чему их можно беспроблемно транспортировать.
Приемлемая цена позволяет приобрести подобные модели для бытовых условий.
Функционирование аппарата воздушно плазменной резки сводится к использованию сжатого воздуха, он необходим для образования плазмы, и охлаждения.
Максимальная толщина металла, с которой воздушно плазменный аппарат может справиться, равняется 50-55 мм.
Рабочая мощность плазмореза составляет 150-180 Ампер.
Как показывает видео, аппарат плазменной резки со встроенным компрессором можно эксплуатировать на любом участке, так как устройство не зависит от пневматической сети.
Оборудование для плазменной резки металла с водяным охлаждением представляет собой мощную установку, способную разрезать твердый материал толщиной от 80 до 100 мм.
Устройства могут эксплуатироваться в составе с комплектом ЧПУ. Более подробно об особенностях их эксплуатации далее в статье и в видео сюжете.
Цена и технические параметры плазморезов
Помимо видов, плазморезы делятся на установки машинной автоматической резки и аппараты воздушно-плазменной ручной резки.
Рассмотрим возможную стоимость и технические характеристики обеих категорий.
Параметры ручных воздушно плазменных аппаратов
Ручной плазморез нашел свое применение в бытовой сфере, его также используют на маленьких предприятиях и в мастерских для вырезки и обработки различных деталей.
Ручной воздушно-плазменный резак не может обеспечить высокую производительность, так как в ходе рабочего процесса задействован труд оператора, который своими руками держит резак на весу и ведет им по линии реза.
В данном случае шов не может получить идеальную ровность.
Чтобы повысить качество результата работ, ручной воздушно-плазменный аппарат для резки дополняют вспомогательным упорным элементом.
Видео:
Упор своими руками одевают на сопло, затем его прижимают к плоскости рабочей заготовки и ведут ручной резак. При этом больше не надо контролировать определенность расстояния между соплом и изделием.
В результате образуется ровный шов, исключающий появление окалин и наплывов. Указанный рабочий процесс можно посмотреть в следующем видео сюжете.
Цена на ручной плазморез устанавливается в зависимости от возможностей аппарата, включая максимальную силу тока и толщину металлического материала, с которой удается справиться ручной модели.
Также на рынке предлагают универсальные модели, которые можно применять как для резки, так и для сварки металлов. Цена на такой ручной плазменный аппарат с дополнительной функцией сварки доходит до 550 $.
Отличить данную модель при выборе позволяет производственная маркировка.
В пример возьмем аппарат FoxWeld Plasma 43 Multi, устройство совмещает в себе:
- Воздушно-плазменная резка, маркировка – CUT;
- функция аргонодуговой сварки – TIG;
- возможность дуговой сварки посредством штучного электрода – MMA.
Параметры аппаратов машинной резки
Установки машинной резки практически всегда дополняют ЧПУ (программное обеспечение).
Станок с ЧПУ функционирует в соответствии с записанной программой, при этом исключается в рабочем процессе участие человека.
Применение установки с ЧПУ позволяет значительно повысить производительность, при этом качество резки аппарат выполняет с идеальной точностью.
После эксплуатации автоматического устройства с ЧПУ нет необходимости дополнительно обрабатывать кромки заготовок.
Оператору достаточно своими руками ввести в ЧПУ специальную схему и установка строго повторит любую геометрическую форму фигуры. Увидеть, как работает такая установка, можно в предложенном видео.
Видео:
Цена на станки с ЧПУ во много раз превышает стоимость ручного плазмореза с функцией сварки.
Оборудование состоит из мощного трансформатора и специальной поверхности, выполненной в виде стола, укомплектованного порталом и направляющими.
Цена на такое устройство с ЧПУ будет зависеть от габаритов и сложности установки. На данный момент цена на аппараты машинной резки с ЧПУ может составлять от 3000$ до 20000$.
Особенности выбора аппаратов по рабочей мощности, скорости и времени резки
Подбор номинальной рабочей мощности аппарата плазмореза рекомендуется проводить с учетом толщины и вида планируемого к обработке металла.
От типа металла будет зависеть тип рабочего потока (воздух или азот), а также величина диаметра сопла.
Если выбранный вами аппарат имеет мощность 60-90 Ампер, его можно будет применять для резки 30-ти мм металла. Данный тип установки доказывают свою пользу во многих промышленных сферах.
С его использованием можно работать в домашних и авторемонтных мастерских.
Для плазменной резки более толстых металлических изделий, рекомендуется выбирать аппарат с рабочей мощностью от 90 до 170 А.
Его применение позволит разрезать 50-ти мм металл.
Выбирая аппарат плазморез, также необходимо обратить внимание на номинальное первичное напряжение и величину силы тока.
Кроме того, стоит определиться с тем, нужен ли для вашей работы аппарат универсального типа, который можно эксплуатировать при разном напряжении.
Как правило, такие устройства можно подключать к любой электросети. Обычно это аппараты зарубежных производителей с функцией Авто-лайн.
Видео:
Упрощенные устройства могут работать только при 220V или 380V, от одно- или трехфазной сети питания.
Показатель скорости резки измеряется в сантиметрах за 1 минуту.
Существуют установки, которые могут разрезать 30-ти мм лист металла в течение 5 минут, в то время как более мощные устройства справляются с этой задачей за минуту.
Также при выборе аппарата для плазменной резки металла смотрят на продолжительность его непрерывной работы. В пример возьмем установку с ПВ непрерывной эксплуатации 60%.
Проценты говорят о том, что аппарат может работать непрерывно 6 минут, при этом для охлаждения ему понадобится 4 минуты.
Как собрать ручной плазменный резак своими руками?
Но не всем приходится по карману даже бюджетная цена плазмореза.
Видео:
Найти выход из ситуации можно, выполнив устройство своими руками, все что потребуется — это приобрести сопло и источник питания.
Аппараты плазменной резки, умело собранные своими руками, могут не уступать показателями мощности производственным устройствам.
Рабочим материалом для плазмы послужит воздух, с целью охлаждения берут воду или тосол, которые необходимо залить в емкость блока.
Образование электродуги можно добиться посредством вольфрамового стержня, его делают из сегментов электрода.
Остальные комплектующие элементы можно отыскать в магазине, после чего руководствуясь схемой, собрать все воедино. Дополнить информацию позволит видео материал.
Видео:
rezhemmetall.ru
Ручная плазменная резка: аппараты, оборудование, видео
В настоящее время на крупных промышленных объектах и небольших предприятиях активно используется ручная плазменная резка, которая дает возможность произвести максимально точную обработку металлов практически любой толщины и конфигурации.
Еще совсем недавно для того, чтобы сделать необходимый рез на металлической поверхности, приходилось прибегать к достаточно громоздким и совершенно неудобным газовым резакам, которые к тому же не всегда могли справиться с поставленной задачей.
Современное оборудование имеет не только компактные размеры, но и обладает высокими функциональными возможностями и большим потенциалом работы.
Следует отметить и то, что аппарат для плазменной ручной резки достаточно просто освоить, а сама технология выполнения работ доступна даже не квалифицированным умельцам.
В специализированных магазинах можно найти большой выбор ручных устройств, предназначенных для плазменной резки металлов.
Несмотря на то, что цена на данное оборудование достаточно высокая, оно пользуется большим спросом, в первую очередь, из-за своих функциональных возможностей.
На видео, которое размещено ниже, можно наблюдать технологию работы на ручном устройстве для резки при помощи плазмы.
Видео:
Характерные особенности процесса резки
Ручная плазменная резка, при которой используется ручной плазменный аппарат, можно отнести к термической обработке, при которой материал плавится.
В данном конкретном случае основным режущим инструментом является поток низкотемпературной плазмы под большим давлением, которая образуется за счет некоторых специфических процессов.
Используемое для работы плазменное оборудование обязательно имеет специальный электрод, который при помощи сопла и рабочего металла создает электрическую дугу, внешняя температура которой в некоторых отдельных случаях достигает нескольких тысяч градусов по Цельсию.
В определенный момент в сопло начинает подаваться под большим давлением специальный газ, что способствует тому, что рабочая температура многократно повышается, а это, в свою очередь, приводит к ионизации газа и, соответственно, преобразование его в плазму, которую называют низкотемпературной.
Следует отметить и то, что ионизация имеет свойство при нагреве от дуги возрастать, а это делает температуру газового потока еще большей. Сам рабочий поток ярко светится и становится электропроводным.
Аппарат, используемый для обработки металла при помощи плазмы, способен локально разогревать металлическую заготовку и плавить ее непосредственно в необходимом месте реза.
Для того чтобы получить плазму, необходимо в определенных пропорциях смешать определенные виды газов.
За основу берется атмосферный воздух, который смешивается с кислородом, азотом, а также водородом и аргоном. В состав плазмы также входит водяной пар.
Для того чтобы при работе сопло не оплавилось под воздействием высоких температур, предусмотрено его специальное охлаждение за счет потока жидкости или газа.
Конечно, использовать в быту аппарат для плазменной резки достаточно проблематично, так как требуются определенные условия его эксплуатации, однако данное оборудование установлено на многих промышленных предприятиях.
Стоит отметить, что цена такого устройства достаточно высокая и для многих домашних мастеров просто не подъемная.
В настоящее время такое оборудование активно используется в самых разных сферах и дает возможность получать не только ровный, но и аккуратный рез.
Более подробно узнать о возможностях ручных аппаратов для плазменной резки можно на видео, которое размещено ниже.
Видео:
Классификация и характеристики оборудования
То оборудование, которое используется для плазменной резки металлических заготовок, можно поделить в зависимости от его действия на обрабатываемую поверхность.
Для бесконтактной резки используется оборудование косвенного действия, в свою очередь, для контактной – прямого.
Резка косвенного действия используется при необходимости провести обработку неметаллических заготовок, соответственно, второй тип резки используется исключительно для работы с металлами.
В этом случае и аппарат, и сама обрабатываемая деталь включатся в единую схему, что и приводит к образованию необходимой дуги.
Идущий из сопла ионизированный поток газа равномерно прогревается по всему участку, вплоть до самой заготовки. Для того чтобы работать с металлом, требуется оборудование, предназначенное только для прямого действия.
Используемый для плазменной резки ручной аппарат получает питание от электрической сети.
Следует отметить, что данный тип резки металлов является не только востребованным, но и экономически обоснованным, даже несмотря на то, что цена оборудования достаточно высокая.
В настоящее время резка плазмой уже стала традиционным способом обработки металлов.
Для того чтобы выполнить необходимую раскройку материалов при использовании аппарата для плазменной резки, не нужно обладать специальной подготовкой и иметь квалификацию.
Работа выполняется достаточно быстро при минимальных трудозатратах.
За счет того, что в рабочем процессе активно участвует воздух, удается сократить расход газа, однако при этом значительно увеличивается вес и габариты используемого оборудования.
Современные устройства, которые применяются для ручной резки плазмой, имеют компактные размеры и привлекательный внешний вид.
Они дополнительно для повышения удобства эксплуатации оснащаются подъемными ручками, всевозможными колесиками, а их корпуса производятся преимущественно из легких композитных материалов.
На видео ниже представлен ручной аппарат для плазменной резки.
Видео:
Конструктивные особенности
Ручное плазменное оборудование состоит из нескольких технологических элементов, которые и обеспечивают его работоспособность.
Одним из главных элементов является сам плазмотрон, функционирование которого обеспечивает источник заданного питания с определенными рабочими параметрами.
Также в состав ручного плазменного аппарата в обязательном порядке входят набор кабелей, специальных шлангов с соответствующим сечением.
Дополнительно работу плазменного аппарата обеспечивает универсальный компрессор. Стоит отметить, что плазмотрон, который и выполняет роль резака, имеет достаточно сложную конструкцию.
В его состав входят непосредственно само сопло и специальный электрод, между которыми особым образом устроен изолятор с высокими показателями термостойкости.
Именно в плазмотроне происходит преобразование дуги электричества в тепловую энергию плазмы. Скорость, а также форму потока плазмы регулирует сопло, имеющее сложную конструкцию.
При работе на ручном плазменном аппарате оператор самостоятельно контролирует ровность линии реза.
Большое значение при работе на ручном плазменном аппарате имеет опыт оператора.
Так как рабочий аппарат человек постоянно держит на весу, возможны непроизвольные движения, которые могут привести к появлению дефектов и снижению качества выполняемого раскроя.
Неопытный оператор может сделать рез не только неровным, но и с наплывами и следами рывков.
Чтобы этого не произошло, выпускаются самые разные дополнительные устройства в виде упоров и подставок.
При их использовании даже у неопытного оператора рез получается максимально ровный и качественный.
Ручной агрегат для плазменной резки металлов — это огромные функциональные возможности в области обработки металлов различной толщины и конфигурации.
Посмотреть, как производится процесс резки металлов при помощи аппарата плазменного ручного типа, можно на видео, которое размещено ниже.
Видео:
Полезные советы и рекомендации
Качество выполняемой обработки напрямую зависит от конфигурации и типа сопла, так, в частности, его диаметр может влиять на скорость образования и формирование самой дуги.
Кроме этого, этот показатель оказывает влияние на объем пропускаемого воздуха или газа, а также ширину реза.
Правильно подобранный диаметр позволяет получить на выходе чистый и качественный рез с ровными кромками.
Следует отметить то, что сопло можно в любой момент поменять на новое, а кроме этого, есть возможность увеличить его длину, что позволит несколько улучшить режущие характеристики.
Перед началом работ на ручном аппарате следует тщательно проверить всю схему подключения используемого оборудования, а также исправность кабелей и шлангов.
Не следует перегружать аппарат, так как это может привести к его поломке.
Видео:
Несмотря на то, что цена такого типа оборудования достаточно высокая, оно достаточно быстро окупается. Все же цена не должна быть определяющим фактором при выборе оборудования.
На видео, которое размещены в нашей статье, можно увидеть все достоинства плазменной резки при помощи ручного типа устройства.
rezhemmetall.ru
Плазморез своими руками из инвертора для плазменной резки металла (7 фото + 2 видео)
И специалисты, и начинающие мастера часто используют в своей работе плазменную резку. Это и понятно: ведь это – незаменимый процесс при самых разных строительных и производственных процессах. Недостаток один: выпускающимися различными фирмами устройства стоят значительных денег, не всем они по карману. Поэтому самые разные рабочие люди, будь то строительные бригады или отдельные мастера, задумываются, как создать плазморез из инвертора, полагаясь только на свои руки и на доступное оборудование, сэкономив тем самым значительную сумму.
Назначение
Видео: Самодельный плазморез,плазменный резак сделанный за месяц
Основное назначение ручного плазмореза – это резка разных типов металлов. Такие действия необходимы во время возведения различных сооружений. Ведь не нужно использовать другие инструменты. Применение всевозможных электродов, с помощью которых идёт сварочный процесс также возможно, если в наличии самодельный плазморез.
В данном агрегате основополагающий принцип, по которому происходит соединение металлов – это пайка. Именно благодаря высокой температуре припоя ручной плазморез позволяет надежно скреплять разнообразные металлы — это его основное преимущество, поэтому данное оборудование столь и необходимо многим.
Помимо стандартной строительной деятельности используют этот удобный инструмент так же и при кузнечных работах. Ведь при его непосредственном участии можно производить различные манипуляции, как с цветными, так и с черными металлами. Помимо их сваривания: ещё и термическую чистку, и закаливание, и отжиг. По данной причине наличие ручного плазмореза при подобных работах является обязательным, этим обеспечивается и качество продукции и значительно экономия времени.
Конструкция её особенности
Прежде чем начинать самостоятельно собирать плазморез из инвертора, необходимо точно определить его комплектацию и как он будет устроен. Следует понять, что отдельные детали будущего устройства лучше приобрести уже готовыми, нежели собирать самостоятельно, т.к. такая сборка будет сопряжена с определенными трудностями.
Обычно собранный аппарат состоит из следующих основных компонентов, без которых работа его невозможна: это воздушный компрессор, пакет шланго-кабельного типа, источник питания и резак, который официально называют плазмотроном.
Своеобразное «сердце» ручного плазмореза – это источник питания. Именно он подаёт ток необходимой мощности. Технические характеристики агрегата определяются именно этой составляющей.
Если сравнивать используемый на данном устройстве резак (или «плазмотрон»), то видно, что его конструкция значительно отличается от аналогичных компонентов, применяемых в сварочных агрегатах. Тем ни менее, он является не менее важным, чем источник питания. Именно резак (плазморез), является той деталью, самостоятельное создание которой из инвертора сопряжено со значительными проблемами. Приобрести резак лучше уже готовым, в магазине. В дальнейшем это избавит от многих проблем.
В мощных агрегатах для горячей резки металла необходимы функции внутреннего охлаждения. Там для этого применяются различные газовые смеси. Необходимо охлаждение и в ручном плазморезе, но здесь достаточно только своевременной подачи воздуха. С этой целью задействуют компрессор, для работы которого нужен ток силой в пределах 200 А.
Соединительная часть, сквозь которую на резак и идет ток от источника, а также нагоняется посредством компрессора воздух – это кабеле-шланговый пакет.
Об использовании транформатора либо инвертора
Чаще всего при когда планируется собрать плазморез, в роль источника питания берут либо инвертор, либо особый трансформатор. У каждого из этих вариантов имеются свои преимущества, но чтобы понять, какой именно подойдёт, надо точно знать, какие технические характеристики должны получиться у вашего плазмореза, соответственно, надо знать и особенности инвертора и трансформатора.
Преимущества у плазмореза, изготовленного на основе инвертора следующие: в среднем его КПД на треть выше, чем у аналогов, в которых присутствует трансформатор, они наиболее эффективны и экономны. Такое устройство обеспечивает стабильность дуги. К недостаткам относится то, что работа проводится исключительно с материалами незначительной толщины.
Если же за основу взят трансформатор, то такой агрегат наверняка будет громоздким и потребует дополнительную площадку для использования. Но значительным плюсом является то, что он позволяет проводить работы с довольно массивными и толстыми деталями. Такие устройства ставят либо в специально оборудованных для них помещениях либо на передвижных платформах.
Поэтому, если не планируется проводить резку особо крупных объектов, то рекомендуется использовать именно плазморез созданный из инвертора. Принцип прост: надо соединять уже находящийся в вашем распоряжении источник питания и прочие детали, соблюдая определенную последовательность.
Какое оборудование понадобится
Конечно, прежде чем приступать непосредственно к сборке устройства для плазменной резки металла, потребуется приобрести все детали, которые и составят конечный продукт. Но если вы хотите, чтобы предполагаемые функции выполнялись на высоком уровне, без поломок, то некоторые из составляющих надо покупать уже в готовом виде.
Инвертор
Это «сердце» нашего будущего агрегата, и взять его можно из какого-либо сварочного аппарата. В большинстве случаев, это и есть главное материальное вложение в описываемый проект. Для того, чтобы выбрать подходящий инвертор надо точно знать, какие работы будут производиться плазморезом, их объем и т.д. Тогда уже не сложно будет подобрать и мощность инвертора.
Приходится слышать, что некоторые народные умельцы собирают инвертор и своими силами. Для этого кропотливо подбирают детали, используют материалы имеющиеся в их распоряжении. Но на практике оказывается, что такие самодельные конструкции менее надежны, чем покупные варианты. К тому же в домашних условиях трудно обеспечить те же стандарты, что и на производстве. Поэтому предпочтительнее все же покупной вариант инвертора.
Резак
Когда мастера или любители делают своими силами плазморез, то зачастую ошибаются, пытаясь полностью собрать и резак с подачей электричества и воздуха. Составные части резака это: сопло, элементы подвода и ручка. Причем ручка, вследствие её интенсивного использования, изнашивается за короткий период времени и приходится часто её заменять. Поэтому лучшим выбором будет покупка заводского сопла, а вот остальные составляющие можно собрать своими силами. Но вполне обоснованным также является и мнение о том, что затрата большого количества средств и усилий на самостоятельную сборку этой составляющей не продуктивно. Лучше купить заводское изделие.
Компрессор
По инструкции использование компрессора подразумевает, что будет применяться кислород, либо инертный газ. На практике же чаще его подключают к баллонам, в которых – специальная смесь. Именно такая смесь обеспечивает сильный пучок плазмы при достойном охлаждении. Если жеплазморез используется в быту, то для экономии и простоты дела рекомендуют использовать простой компрессор. Эту составляющую вполне можно собрать своими силами, где роль ресивера будет выполнять обычный баллон. Компрессор же часто берут из холодильника, либо из машины ЗИЛ. Важно не ошибиться с регулированием давления. Делается это опытным путем, мастерами, на начальном этапе работ.
Кабель–шланговый пакет
Эту составляющую плазмореза можно купить как по отдельности, так и вместе с основным оборудованием. Главное знать некоторые характеристики агрегата, а именно: какое при работе будет давление, а также какое сечение у кабеля – от этого зависят и характеристики шлангов. Проводник подбирается под силу инвертора. В другом случае он перегреется и может загореться и даже возможно поражение током.
Процесс сборки
Это довольно простая последовательность сборки. Сопло плазмореза соединяется с инвертором и компрессором. Для подобных целей и нужен кабель-шланговой пакет. Потребуются набор клемов и зажимов. С их помощью можно оперативно собирать, а также и разбирать плазморез. Если все сделано грамотно, то на выходе получится устройство весьма компактных параметров. Его легко транспортировать на место, где будет проводиться очередная работа.
Что советуют специалисты
- Прежде всего, вы должны позаботиться о том, чтобы в наличии были запасные прокладки в достаточном количестве. Ведь происходит плазменая резка при использовании газа, а прокладки необходимы для подключения шлангов. И если агрегат планируется достаточно часто перевозить, то без данного элемента никак не обойтись, более того – отсутствие прокладок может стать причиной остановки всей работы.
- Особо высокие температуры воздействуют на сопло резака. Поэтому, в перспективе длительного использования аппарата, именно эта деталь изнашивается скорее других. Так что в наличии должно быть и запасное сопло.
- Диапазон цен на инверторы весьма велик: от весьма дешёвых и до действительно дорогих. Главное, что влияет на цену – это мощность инвертора. Так что, прежде чем покупать, определитесь с тем, какая вам потребуется мощность. И уж отталкиваясь от своих реальных потребностей, выбирайте ту или иную модель. Так и деньги сэкономите и создадите плазморез, который подходит именно для вашей работы.
- Не обойтись без электродов изготовленных из тугоплавких металлов. На рынке выбор достаточно велик. Например, изделия изготовленные из циркония, бериллия или тория. Но при значительном нагреве из определенных металлов происходит выделение опасных компонентов. Наиболее безопасным, а значит и предпочтительным считаются электроды, изготовленные из гафния.
- Во время проведения работ плазма в таком аппарате раскаляется до 30 тысяч градусов. А это значит, что требуется соблюдений всех мер безопасности. Без этого возможно возгорание, либо же может быть нанесён вред, как сварщику, так и окружающим. По этой причине новичкам, не прошедшим никакого обучения нельзя работать на подобном оборудовании. В идеале должен работать специалист со значительным стажем.
- Причина, по которой специалисты рекомендуют применять при работах только изготовленные на заводах резаки, это то, что самодельные вариации могут вносить нарушения в вихревой поток воздуха. А это недопустимо, т.к. возможно образование 2-х дуг, которые станут причиной поломки изделия. Поэтому лучше один раз потратиться, чем потом вкладывать дополнительные средства и силы в починку агрегата.
- Если с помощью инвертора планируется производить работы только одного типа, то в него возможно внесение некоторых модификаций призванных облегчить именно такой тип работ. Например, некоторые умельцы вводят собственные доработки в сопло или создают особый кожух для защиты рук. Главный принцип любого такого дополнения: они не должны идти в разрез с правилами безопасности.
Выводы
Итак, ознакомившись с этим материалом, становится ясно, что для сборки плазмореза с инвертором потребуется приобрести уже готовые составляющие от разных производителей. А что касается изготовления плазмореза, то это простая сборка. Но все же подбор отдельных деталей позволить сэкономить, т.к. если брать полный готовый комплект у одного производителя, то это выйдет гораздо дороже.
Видео: Как превратить инвертор для ручной сварки в полуавтомат
Другие статьи:
nlo-mir.ru
Плазморез своими руками
Плазменная резка – достаточно востребованная операция, особенно, когда дело касается резки толстых металлических деталей или заготовок. Процесс происходит быстро, кромки металла остаются ровными. Но такой аппарат стоит недешево. Поэтому многие умельцы изготавливают для себя плазморез своими руками из разных видов оборудования, соединив их в одну конструкцию. Схема соединения их проста, главное – правильно подобрать приборы по необходимым техническим характеристикам.
Основы плазменной резки
В основе плазменной резки лежит ионизированный газ, который вылетает из сопла горелки с большой скоростью. Этот газ и есть та самая плазма. Что она делает.
- По сути, это ионизированная среда является отличным проводником электрического тока, который от электрода поступает к металлической заготовке.
- Плазма нагревает металл до необходимой температуры.
- Она же сдувает расплавленный металл, освобождает пространство реза.
Значит, чтобы создать плазму, необходим газ и источник электроэнергии. И эти две составляющие должны соединиться в одном месте. Поэтому оборудование плазменной резки состоит из баллона с газом, источника электроэнергии повышенной силы и резака, в котором установлен электрод.
Конструкция резака изготовлена таким образом, чтобы вокруг электрода проходил газ и в нагретом от электрода виде вырывался наружу через небольшое отверстие. Небольшой диаметр отверстия и давление газа создают необходимую скорость плазме. При изготовлении самодельной плазменной резки нужно просто приобрести готовый резак и не думать над его созданием. Потому что в нем уже все продумано, плюс заводской вариант – это гарантия безопасности.
Что касается газа, то от всех вариантов давно уже отказались, оставив сжатый воздух. Получить его можно сегодня очень просто – приобрести и установить компрессор.
Есть определенные условия, которые гарантируют качество резки плазмой.
- Сила тока на электроде не должна быть меньше 250 А.
- Сжатый воздух должен подаваться на резак со скоростью в пределах 800 м/сек.
Как сделать плазморез своими руками
Основы плазменной резки понятны, конструкция плазмореза тоже ясна, можно приступать к его сборке. Кстати, для этого не нужны специальные чертежи.
Итак, что будет необходимо.
- Нужно найти источник электроэнергии. Самый простой вариант – это сварочный трансформатор или инвертор. По многим причинам инвертор лучше. К примеру, у него стабильное значение тока, без перепадов. Он экономичнее в плане потребления электроэнергии. Обратить внимание придется на ток, который выдает сварочный аппарат. Его значение не должно быть меньше 250 ампер.
- Источник сжатого воздуха. Здесь без изменений – компрессор. Но какой? Основной параметр – давление воздуха. На него и надо будет обратить внимание. 2,0-2,5 атм. – будет нормально.
- Резак можно приобрести в магазине. И это будет идеальным решением. Если есть в наличии резак для аргонной сварки, то и его можно переделать под плазменную резку. Для этого из меди придется сделать насадку в виде сопла, которая вставляется в резак аргонной сварки.
- Комплект шлангов и кабелей, для соединения всех частей самодельного плазмореза. Опять-таки комплект можно приобрести в магазине, как единый соединяющий элемент.
Вот четыре элемента, с помощью которых собирается самодельный плазморез.
Вспомогательные элементы и материалы
На что еще необходимо обратить внимание, собирая аппарат плазменной резки своими руками. Как уже было сказано выше, основная характеристика плазменного резака – это диаметр его отверстия. Каких размеров он должен быть, чтобы качество реза было максимальным. Специалисты считают, что диаметр в 30 мм – оптимальный размер. Поэтому, покупая резак в магазине, нужно обратить внимание, есть ли в его комплекте сопло с таким отверстием.
К тому же надо подбирать сопло со значительной длиной. Именно этот размер дает возможность струе сжатого воздуха набрать необходимую скорость. От чего рез металла получается аккуратным, а сам процесс резки быстрым и легким. Но не стоит приобретать сопло уж очень большой длины. Такое приспособление быстро разрушается под действием высоких температур.
Что касается выбора электрода для плазмореза, то тут необходимо обратить внимание на сплав, из которого он изготовлен. К примеру, если в сплав входит бериллий, то это радиоактивное вещество. Работать с такими электродами долго не рекомендуется. Если в сплав входит торий, то при высоких температурах он выделяет токсичные вещества. Идеальный электрод для плазменной резки, в сплав которого входит гафний.
Проверка плазмореза
Итак, шланги соединяют резак и компрессор, кабель резак и инвертор. Теперь необходимо проверить, а работает ли собранная конструкция. Включаются все агрегаты, на резаке нажимается кнопка подачи электроэнергии на электрод. При этом образуется дуга с температурой 6000-8000С. Она проскакивает между металлом электрода и сопла.
После этого начинает подаваться в резак сжатый воздух. Проходя через сопло и нагреваясь от электрической дуги, он резко расширяется в десять раз и при этом приобретает токопроводящие свойства. То есть, получается ионизированный газ.
Он проходит через суженное сопло, при этом приобретая скорость в пределах 2-3 м/сек. А вот температура плазмы повышается до 25000-30000С. Самое важное, что дуга, с помощью которой был разогрет сжатый воздух и превращен в плазму, гаснет, как только плазма начинает воздействовать на металлическую заготовку, подготовленную к резке. Но тут же включается вторая, так называемая рабочая дуга, которая на металл действует локально. Именно в зону реза. Поэтому металл режется только в этой зоне.
Если при проверке работы плазменного резака у вас получилось разрезать металл толщиною не меньше 20 мм, то все элементы новой конструкции, собранной своими руками, были подобраны правильно. Необходимо обратить внимание, что заготовки толщиною более 20 мм плазморез из инвертора не режет. У него просто не хватает мощности. Чтобы резать металл большей толщины, придется использовать трансформатор.
Внимание! Любые работы, связанные с использование плазменной резки, должны проводиться в защитной одежде и перчатках.
Полезные советы
Существует много моментов, которые обязательно сказываются на работе агрегата.
- Приобретать, например, большой компрессор нет необходимости. Но 2-2,5 атмосфер при большом объеме работ может не хватить. Выход из положения – установить на компрессоре ресивер. Он работает, как аккумулятор, накопляющий давление в сжатом воздухе. Для этого дела можно приспособить, к примеру, болоны от тормозной системы большегрузных машин. Вариант на самом деле простой. Объем у баллона большой, и его должно хватить на длительный промежуток времени.
- Чтобы давление воздуха было стабильным и одинаковым, на выходе ресивера нужно установить редуктор.
- Конечно, оптимальное решение – приобрести компрессор в комплекте с ресивером. Стоит он дороже обычного, но если этот агрегат использовать и для других дел, к примеру, для покраски, то можно увеличить его функциональность и тем самым покрыть затраты.
- Чтобы сделать мобильную версию станка, можно изготовить тележку небольших размеров. Ведь все элементы плазмореза – небольшие по габаритам приспособления. Конечно, о мобильности придется забыть, если станок изготовлен на основе сварочного трансформатора. Слишком он большой и тяжелый.
- Если нет возможности купить готовый комплект шланг-кабель, то можно его сделать самостоятельно. Нужно сварочный кабель и шланг высокого давления объединить в один рукав и поместить их в единую оболочку. К примеру, в обычный шланг большего диаметра. Сделанный таким образом комплект просто не будет мешаться под ногами, что очень важно при проведении резки металлов.
Сделать свой собственный плазморез совсем несложно. Конечно, надо будет получить необходимую информацию, изучить ее, обязательно рекомендуется посмотреть обучающее видео. И после этого правильно подобрать все элементы точно под необходимые параметры. Кстати, собранный плазморез на основе серийного инвертора дает возможность не только проводить плазменную резку металлов, но и плазменную сварку, что увеличивает функциональность агрегата.
Поделись с друзьями
2
0
0
1
svarkalegko.com
Плазморез своими руками
Главная страница » Своими руками » Плазморез
Раскрой металла – это одна из основных операций на всех металлообрабатывающих предприятиях. Статистика показывает, что почти 90% всего разрезаемого металла имеют толщину ≤ 25 мм. Именно для такого материала учёные и инженеры разработали плазменный метод резки.
На предприятиях, в зависимости от объёмов и уровня производства, применяется самое разнообразное оборудование: от мобильного ручного до портальных станков плазменной резки. Но, даже самые маломощные, аппараты имеют высокую стоимость и будут «не по карману» многим домашним умельцам. И они задаются вопросом: как сделать плазморез своим руками? Для них мы и расскажем, как изготовить такой плазморез.
Принцип действия плазмореза
Что бы было всё понятно, начнём с описания плазменной резки .
Несколько слов посвятим терминологии. Аппарат для плазменной резки называется плазморез, а главный инструмент в нём – плазмотрон. Именно он создаёт поток ионизированного воздуха, в среде которого образуется плазма.
Плазменная резка заключается в следующем. Формируется поток ионизированного воздуха. Кардинальное отличие этого воздуха от обычного заключается в том, что он не является электроизолятором, и его электропроводность равна аналогичному параметру разрезаемой заготовки. В плазмотроне от импульса тока происходит поджиг этого потока. Образуется электродуга в плотном потоке плазмы, температура последней достигает 5000…30000°С. Эта дуга осуществляет рез заготовки, если она элктропроводна. Если заготовка не пропускает электроток, то рез осуществляется потоком плазмы. Образующиеся на поверхности разрезаемой заготовки металлические капли сдуваются потоком воздуха из сопла.
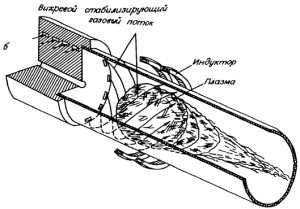
Формирование воздушного потока
Из чего состоит плазморез
Плазморез состоит из нескольких узлов:
Плазмотрон
Есть два пути изготовления плазмотрона:
В обоих случаях, следует обратить особое внимание на соблюдение принципа плазменного резания металла.
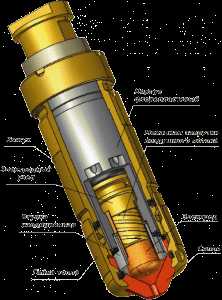
Плазматрон (узнать подробнее про его устройство можно тут)
Блок электропитания
Источником электропитания плазмореза может быть:
Таким образом, можно самостоятельно намотать трансформатор необходимой мощности и его использовать.
Осциллятор
Плазмотрон в плазморезе образует и формирует горящий поток ионизированного воздуха. Поджиг этого потока осуществляется устройством, которое называется осциллятор.
Компрессор
Компрессор, как следует из названия, подает воздух. Но не просто воздух. Он должен обеспечивать вихревую подачу воздуха, которая заставит катодное пятно плазменной дуги располагаться точно по центру электрода. Если этого не будет, то возможны проблемы с дугой.
Компрессор лучше купить специализированный, иначе в стандартном придётся монтировать систему очистки воздуха.
Узнать подробнее про компрессоры для плазменной резки
Таким образом, можно построить самодельный плазморез. При тщательной настройке вы добьётесь хорошего качества реза при существенной экономии материальных средств.
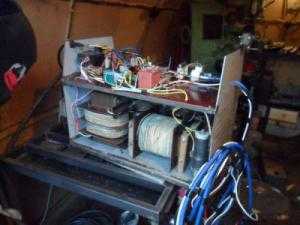
Самодельный плазморез
Плазморез своими руками
Самодельный осциллятор
Осциллятор для плазмореза — это устройство для бесконтактного возбуждения дуги и стабилизации её горения. Эти опции он получает благодаря преобразованию параметров электроэнергии. Подробнее в статье: «Осциллятор для плазмореза своими руками».
Самодельный кабель-шланговый пакет
Видео
Посмотрите полезный видеоролик, где умелец показывает, как сделать кабель-шланговый пакет своими руками:
Как сделать из сварочного трансформатора
Более подробная информация про плазморез из трансформатора сварочного здесь.
Самодельный трансформатор для плазмореза
Один из возможных источников питания аппарата плазменной резки — это самодельный трансформатор для плазмореза. Он обладает рядом достоинств:
- не чувствителен к перепадам напряжения;
- позволяет резать толстый металл.
Но, вместе с тем, у него имеется несколько минусов: низкий КПД и большая масса.
Подготовка
Подберите для самоделки сварочный трансформатор, который сможет обеспечить работу вашего плазмореза в удобных для вас условиях. Бытовая однофазная электропроводка может выдерживать нагрузку до 25А, соответственно трёхфазная – до 60А. Удобнее всего использовать трёхфазную с плавной регулировкой исполнительных параметров:
- изменением размеров воздушного промежутка между первичной и вторичной обмотками;
- согласованным изменением числа витков первичной и вторичной обмоток;
- применением подмагничиваемого шунта и т. п.
Необходимо проверить и отрегулировать все органы настройки. Если демонтировалась вторичная обмотка, то, будет не лишним, намотать дополнительную первичную обмотку и предусмотреть возможность её подключения при необходимости настройки режима реза. Это позволит получать ровные и гладкие стенки. Кроме того следует предусмотреть несколько ответвлений во вторичной обмотке по той же причине.
Полезное видео:
Посмотрите ролик плазмореза, где используется самодельный трансформатор:
Эксплуатация самодельного трансформатора для плазмореза
Эксплуатация такого трансформатора не вызывает каких-либо трудностей. Положительная особенность таких гаджетов – они легко переносят токовые перегрузки. Недостатком (кроме неподъёмного веса) является необходимость частого применения осциллятора. Но, и этот «недостаток» очень быстро, с приобретением опыта, проходит.
Где купить комплектацию для плазмотрона
Контакты продавцов смотрите на этой странице.
Узнать больше:
Плазменная резка металла
Оборудование для плазменной резки металла
Ручная плазменная резка металла (оборудование)
Установка плазменной резки металла
plazmen.ru
Плазменная резка своими руками | Строительный портал
Плазменная резка представляет собой способ резки металлов с применением вместо резца в качестве режущего инструмента струи плазмы. Между электродом и соплом аппарата или поверхностью разрезаемого металла зажигается электрическая дуга. В сопло аппарата в свою очередь подается под давлением газ, который превращается в плазму под воздействием электрической. Плазма нагревается до 5 - 30 тысяч градусов, а скорость работы составляет пределах 500-1 500 метров в секунду.
Содержание:
- Понятие плазменной резки
- Достоинства плазменной резки
- Принцип работы аппарата плазменной резки
- Выбор аппарата плазменной резки
- Использование аппарата плазменной резки
Понятие плазменной резки
Различают поверхностную и разделительную плазменную резку металла. Широкое распространение на практике нашла именно вторая методика. Сама резка может осуществляться двумя способами: плазменной струей или дугой. При резке металла плазменной дугой включается разрезаемый металл в электрическую цепь. Дуга образуется между изделием и вольфрамовым электродом. При резке плазменной струей в электрическую цепь изделие не включается. Дуга в резаке возникает между двумя электродами.
Обычно плазменную резку проводят в атмосфере. Резка при применении дополнительной среды выступает дальнейшим усовершенствованием - при помощи такой среды ограничивается длина дуги. При толщине металлического листа в пару миллиметров и использовании кислорода как параллельность обработанных поверхностей сопоставима с данным параметром при лазерной резке. Получение параллельных поверхностей возможно при резке листов, которые имеют толщину вплоть до 10 миллиметров.
При плазменной резке низколегированных и мягких сталей предпочтительнее использовать в качестве режущего газа кислород. Расплавленное железо отличается пониженную вязкость, поэтому разжиженный материал из паза легче удаляется. В результате кромки образуются практически без заусенцев. Ещё одним преимуществом применения кислорода является уменьшенное содержание в обработанных кромках азота.
Как режущий газ иногда используется азот. При этом для резки аналогичной толщины листа требуется меньшая сила электротока и тратятся меньшие термические нагрузки на электроды, срок службы которых существенно увеличивается. Если не уменьшать нагрузки, то возможно возрастание содержания азота в кромке, что отрицательно сказывается при выполнении дальнейшей работы. Иногда как более дешевый газ используется воздух, но он уменьшает срок службы сопел и электродов, а также повышает содержание на порезанных кромках азота по сравнению кислородом.
Достоинства плазменной резки
С помощью оборудования для плазменной резки вы можете обрабатывать почти любые металлы – черные и цветные, а также тугоплавкие. Посредством плазменной резки можно обрабатывать металлы в несколько раз быстрее газовой резки. Технология плазменной резки позволяет получать заготовки без каких-то ограничений по геометрической форме. Возможен и процесс сложной фигурной резки.
Подобная технология позволяет разрезать металл точно и быстро, причем процедура эффективна при работе с металлом разной толщины — близко 0,5 - 50 миллиметров. Методика плазменной резки в отличие от кислородной технологии резки позволяет разрезать железосодержащие материалы и материалы, что железа не содержат. Применение плазменной технологии для резки металла, не содержащего железа, является более быстрой, безопасной и эффективной альтернативой механической резке.
Плазменная резка металла по техническим характеристикам и скорости резки является особенно эффективной для прямых резов, к примеру, для резания листов и зачистки кромок, для обработки профилей. Серьёзным преимуществом по сравнению с лазерной резкой является возможность обработки более широких листов металла, резки листов под углом для будущей сварки и получения деталей с небольшими дефектами на поверхности, окалинах и загрязнениях.
При плазменной резке получаются намного меньшие затраты на метр длины металла. Поэтому данная методика в последнее время получила широкое распространение на крупных производствах. При использовании дополнительной среды плазменная резка может применяться на воздухе и даже под водой. Именно вода, попадающая между соплом и плазмой, выступает дополнительной средой при резке алюминия и легированных сталей, обработке низколегированных и мягких сталей.
Принцип работы аппарата плазменной резки
Аппарат для плазменной резки предназначается для высокотемпературного местного нагрева струей плазмы поверхностей материалов, которые имеют малую толщину, в процессе термической обработки. Применение аппарата плазменной резки — резка электропроводного и неэлектропроводного материала, пайка и сварка высокотемпературными припоями, поверхностная термообработка (закалка, местный отжиг, огневая зачистка), сварка черного и цветного металла и другие работы, которые связаны с высокотемпературным местным нагревом.
Реализуется в плазменной горелке технология получения из водяного пара плазмы. Принцип плазменной резки металла в общих чертах можно описать так: в узком канале сопла зажигается электрическая дуга, через этот канал продувается водяной пар, интенсивно охлаждая дугу. Водяной пар при этом ионизируется, и в результате чего создается плазменная струя, которая имеет температуру порядка 6000 градусов.
В процессе резки металла плазма не нагревает обширные участки металла. Материал, который разрезается плазменным резаком, способен охлаждать намного быстрее, чем металл, что разрезан кислородной резкой. Функция пара рабочей жидкости сведена к охлаждению самых нагруженных частей горелки – катода и сопла, стабилизации столба разряда и выдуванию из сопла дуги. Система подачи пара действует по «открытой схеме»: из резервуара самотеком пар попадает по каналам охлаждения в разрядную камеру и выбрасывается через сопло в атмосферу.
Стабилизация дуги относительно оси центра сопла обеспечивается соосношением сопла и катода специальной конструкции и спирального потока пара при помощи тангенциальной подачи в камеру. В резервуаре горелки размещен запас рабочей жидкости. В резервуаре горелки находится капиллярно-пористый влаговпитывающий материал, который служит для транспортировки рабочей жидкости к поверхности нагревателя с помощью капиллярного эффекта. Источник питания на катоде имеет отрицательный потенциал и на сопле положительный.
Выбор аппарата плазменной резки
Если вы решили прикупить такое оборудование, для начала стоит тщательно проанализировать некие параметры, которые будут влиять на качество работы аппарата плазменной резки. Есть опции, которые являются принципиально важными для резака, есть – дополнительные, которые в ваших условиях работы могут попросту не понадобиться.
Виды аппаратов плазменной резки
Аппараты плазменной резки делятся на две разновидности: инверторные и трансформаторные.К достоинствам инверторных аппаратов плазменной резки металла относят такие параметры, как компактность, малое потребление энергии, привлекательный дизайн и небольшой вес. К недостаткам причисляют невысокую продолжительность включения особенно на большом токе и ограничение по максимальной мощности - не больше 70 Ампер. Но главным недостатком выступает то, что инверторные плазморезы являются очень чувствительными к перепадам напряжения.
К достоинствам трансформаторных аппаратов плазменной резки относят высокое продолжение включения и значительную надежность. К тому же при падении напряжения поломки аппарата не происходит, только уменьшается его мощность. Установки с продолжением включения больше 70% можно применять для автоматической резки, где длительность непрерывной работы плазмотрона намного больше, чем при ручной резке. К недостаткам относят размеры и вес, который является значительно большим, чем у плазменных инверторов, а также высшее энергопотребление.
Мощность аппарата
Подбирать номинальную мощность аппарата необходимо зависимо от толщины и вида разрезаемого металла. Толщину металла определяет тип газового потока (азот, воздух) и диаметр сопла. Определите, какой вы будете резать металл, и проверьте мощность вашего оборудования. К примеру, аппарат, который имеет входную мощность 60 или 90 Ампер, способен резать металл, что отличается толщиной до 30 миллиметров.
Аппарат подобного типа предназначен для использования в разных отраслях промышленности, при проведении работ в автомобильных ремонтных и домашних мастерских. Если вы желаете резать толстый металл, то стоит выбрать аппарат с номинальной мощностью 90 или 170 Ампер, как на фото плазменной резки металла на нашем сайте. Используя данный аппарат, вы сможете порезать металл, который имеет толщину до 50 миллиметров.
Обязательно стоит проверить первичное напряжение и силу тока, что необходима для источника питания. Также стоит определить, нужен ли вам универсальный аппарат, что способен работать с разным током и напряжением. Некоторые аппараты могут работать только с напряжением 380 или 220 Вольт, однофазным или трехфазным током питания. В некоторых аппаратах зарубежного производства предусмотрена функция Auto-Line, что позволяет подсоединять оборудование к любой электрической сети.
Скорость и время резки
Перед покупкой аппарата сварочной резки нужно проверить скорость резки данного оборудования. Обычно этот показатель измеряется сантиметрами в минуту. Некоторые аппараты могут перерезать металл, который имеет толщину 30 миллиметров, на протяжении 5 минут, другие – за одну минуту. Скорость резки является очень важной характеристикой, особенно когда нужно уменьшать расходы времени.
При покупке аппарата плазменной резки нужно обратить внимание на продолжительность его работы - время, на протяжении которого аппарат может работать без перегрева. Если длительность работы составляет 60 %, то аппарат может работать без перерыва 6 минут, а в течение 4 минут ему нужно охлаждаться. Очень важна высокая продолжительность для выполнения длинных разрезов или использования аппарата при повышенной температуре.
Продолжительность работы указывается, как правило, для максимальной мощности аппарата. Если вы будете использовать оборудование с меньшей мощностью, то продолжительность его работы соответственно увеличится. Температура среды, где эксплуатируется аппарат плазменной резки, также влияет на этот показатель.
Плазменная горелка
Выбирать плазматрон необходимо в зависимости от особенностей продуктов или материалов, которые вы будете резать. Плазменная горелка всегда должна иметь достаточную мощность для обеспечения качественной резки в тяжелых условиях и быть стойкой к ударам при интенсивной эксплуатации. Вы можете использовать плазматроны различной конструкции.
Плазматроны с медным соплом являются более прочными, чем аппараты с керамическим соплом, практически не бьются, имеют воздушное охлаждение. Рукоятки могут комплектоваться дополнительными элементами, что крепятся к плазматрону и поддерживают наконечники на необходимом расстоянии от рабочей поверхности - 1,6-3 миллиметра. Посмотрите видео о плазменной резке металла - это существенно облегчает работу оператора.
Длина дополнительного элемента, то есть расстояние между плазменной горелкой и рабочей поверхностью, зависит от необходимой силы тока и толщины разрезаемого металла. При использовании малых токов можно прикоснуться соплом к поверхности металла. При использовании большого тока (больше 60 Ампер) расстояние между поверхностью металла и плазматроном должно быть минимум 1,6-4,5 миллиметров.
При выборе плазменной горелки рекомендуется выяснить, для какой цели она будет служить, потому что возможны разные конструкционные решения. Если горелка будет использоваться только в пределах малых токов и разрезать исключительно тонкие листы металла, то защитный газ для охлаждения плазматрона не требуется, и в горелку будет подаваться только воздух, что необходим для резки. Если вы используете плазматрон для резки толстого листового металла, то нужен больший ток, и желательно в плазматрон подавать азот, а не воздух.
Внешние параметры аппарата
Для плазменной резки необходим сжатый воздух и другие комплектующие – электроды для резки и сопло горелки. Поврежденные и изношенные запчасти влияют на качество резки. Низкий уровень квалификации оператора, высокая влажность воздуха, процесс резки толстого листа металла с применением интенсивного режима ускоряют износ таких комплектующих частей. Посмотрите видео о ручной плазменной резке металла - оптимального качества резки можно достичь только при одновременной замене электрода и сопла.
Если вам нужен переносной аппарат, очень важными факторами выступают его размеры и вес. Можно купить небольшой переносный агрегат, который весит меньше 40 килограмм. Также в продаже имеются мощные аппараты, которые весят больше, они служат стационарными постами резки и способны качественно выполнять резку металлов, что отличаются толщиной до 50 миллиметров.
Использование аппарата плазменной резки
Ручную плазменную резку металла при помощи специального оборудования может проводить даже человек без сварочного опыта. Имея аппарат плазменной резки в домашнем обиходе, вы можете осуществлять резку металла и других материалов - пластика, древесины, керамической плитки. Но иногда не по карману купить готовый аппарат, потому что его стоимость, а поэтому и цена плазменной резки слишком высока. В этом случае можно изготовить плазменный резак самостоятельно, купив блок питания и сопло.
Плазменные резаки, созданные своими руками, не уступают по мощности заводским. В качестве рабочего материала для плазмы используют в самодельных аппаратах воздух. Для охлаждения применена жидкая система: полость анодного блока принято заполнять тосолом или обычной водой. Дугу в сопле можно получить при помощи вольфрамового стержня, для изготовления которого берут кусочек электрода. Остальные части продаются в магазинах в качестве комплектующих. Остается только собрать их воедино.
Работая с аппаратами плазменной резки, нужно строго придерживаться правил безопасности, потому что при этой работе имеет место большое число факторов, которые представляют опасность для человека: температура, высокое напряжение, расплавленный металл и ультрафиолетовое излучение. Рекомендуется носить одежду сварщика и под рукой иметь сварочный щиток с затемненными стеклами.
Перед началом процесса плазменной резки металла своими руками необходимо осмотреть защитный щиток, электрод и сопло! Нельзя начинать работу, если электрод или сопло недостаточно закреплены. Не желательно стучать плазматроном для удаления брызг металла, потому что можно его повредить. Для экономии материалов нужно избегать обрыва и частого зажигания плазменной дуги.
При подготовке к работе аппарата плазменной резки в него подается сжатый воздух. Можно выбрать один из трех источников сжатого воздуха: подключение к системе сжатого воздуха, которая имеется на заводе, баллоны сжатого воздуха или воздушный компрессор. Львиная доля аппаратов имеют регулятор, который необходим для подачи и распределения воздуха в системе.
При расчете определенного тока и скорости резки рекомендуется выполнить несколько пробных разрезов при высоком токе. При необходимости, зависимо от скорости резки, вы можете уменьшать ток. Если он является слишком высоким или скорость резки выступает маленькой, разрезаемый металл будет перегреваться и может возникать окалина. Правильно определив ток и скорость резки, вы сможете получить чистый разрез, на котором практически не возникает окалины, а разрезаемый металл не деформируется.
Плазменную резку листового металла принято начинать, размещая горелку близко к краю разрезаемого металла. Дальше нужно нажать кнопку выключателя горелки, после этого зажжется дежурная дуга, а потом режущая дуга. После того, как режущая дуга зажглась, нужно медленно двигать горелку вдоль желаемой линии разреза. Регулировать скорость движения необходимо так, чтобы искры виднелись с обратной стороны листового металла. Дугу направляется под прямым углом к металлу и вниз.
Если на обратной стороне металла не заметно искр, то металл насквозь не прорезался. Это может совершаться из-за чрезмерно большой скорости движения, малого тока или направления струи плазмы к поверхности металла не под углом 90 градусов. По окончании резки горелку следует слегка наклонить в сторону конца разреза или остановится на время, чтобы закончить процесс резки. После того, как была отпущена кнопка выключателя на горелке, воздух для охлаждения горелки некоторое время подаваться ещё будет.
Проплавить отверстие в металле получится, если угол наклона горелки достигнет 40 градусов. Необходимо нажать кнопку выключателя горелки аппарата плазменной резки. Когда загорелась режущая дуга, следует наклонить горелку таким способом, чтобы угол ее наклона достигал 90 градусов. Только тогда дуга сможет насквозь проплавить основной металл. Рекомендуется руководствоваться следующим правилом: данным способом вы сможете проплавить металл толщиной не больше самой высокой толщины разрезаемого металла, что указана в паспорте аппарата плазменной резки.
Таким образом, если нужно раскроить металл или сделать отверстие в цельном металлическом изделии, лучшим вариантом для проведения подобных работ является по технологии и стоимости плазменная резка металла. Для осуществления данной процедуры необходим специальный резак, отличительная особенность которого кроется в том, что резка происходит не благодаря электрической дуге, а за счет образования потока раскаленной плазмы.
strport.ru
Плазменная резка » Портал инженера
Плазменная резка широко используется в различных отраслях промышленности: машиностроении, судостроении, изготовлении рекламы, коммунальной сфере, изготовлении металлоконструкций и в других отраслях. К тому же, в частной мастерской плазморез тоже может пригодиться. Ведь с помощью него можно быстро и качественно разрезать любой токопроводящий материал, а также некоторые нетокопроводящие материалы – пластик, камень и дерево. Разрезать трубы, листовой металл, выполнить фигурный рез или изготовить деталь можно просто, быстро и удобно с помощью технологии плазменной резки. Рез выполняется высокотемпературной плазменной дугой, для создания которой нужен лишь источник тока, резак и воздух. Чтобы работа с плазморезом давалась легко, а рез получался красивым и ровным, не мешает узнать принцип работы плазмореза, который даст базовое понятие, как можно управлять процессом резки.
Аппарат под названием «плазморез» состоит из нескольких элементов: источника питания,плазменного резака/плазмотрона, воздушного компрессора и кабель-шлангового пакета.
Источник питания для плазмореза подает на плазмотрон определенную силу тока. Может представлять собой трансформатор или инвертор.
Трансформаторы более увесисты, потребляют больше энергии, но зато менее чувствительны к перепадам напряжения, и с помощью них можно разрезать заготовки большей толщины.
Инверторы легче, дешевле, экономнее в плане энергопотребления, но при этом позволяют разрезать заготовки меньшей толщины. Поэтому их используют на маленьких производствах и в частных мастерских. Также КПД инверторных плазморезов на 30 % больше, чем у трансформаторных, у них стабильнее горит дуга. Пригождаются они и для работы в труднодоступных местах.
Плазмотрон или как его еще называют «плазменный резак» является главным элементом плазмореза. В некоторых источниках можно встретить упоминание плазмотрона в таком контексте, что можно подумать будто «плазмотрон» и «плазморез» идентичные понятия. На самом деле это не так: плазмотрон – это непосредственно резак, с помощью которого разрезается заготовка.
Основными элементами плазменного резака/плазмотрона являются сопло, электрод, охладитель/изолятор между ними и канал для подачи сжатого воздуха.
Схема плазмореза наглядно демонстрирует расположение всех элементов плазмореза.
![]() |
Внутри корпуса плазмотрона находится электрод, который служит для возбуждения электрической дуги. Он может быть изготовлен из гафния, циркония, бериллия или тория. Эти металлы приемлемы для воздушно-плазменной резки потому, что в процессе работы на их поверхности образуются тугоплавкие оксиды, препятствующие разрушению электрода. Тем не менее, используют не все эти металлы, потому что оксиды некоторых из них могут нанести вред здоровью оператора. Например, оксид тория – токсичен, а оксид бериллия – радиоактивен. Поэтому самым распространенным металлом для изготовления электродов плазмотрона является гафний. Реже – другие металлы.
Сопло плазмотрона обжимает и формирует плазменную струю, которая вырывается из выходного канала и разрезает заготовку. От размера сопла зависят возможности и характеристики плазмореза, а также технология работы с ним. Зависимость такая: от диаметра сопла зависит, какой объем воздуха может через него пройти за единицу времени, а от объема воздуха зависят ширина реза, скорость охлаждения и скорость работы плазмотрона. Чаще всего сопло плазмотрона имеет диаметр 3 мм. Длина сопла тоже важный параметр: чем длиннее сопло, тем аккуратнее и качественнее рез. Но с этим надо быть поаккуратнее. Слишком длинное сопло быстрее разрушается.
Компрессор для плазмореза необходим для подачи воздуха. Технология плазменной резки подразумевает использование газов: плазмообразующих и защитных. В аппаратах плазменной резки, рассчитанных на силу тока до 200 А, используется только сжатый воздух, и для создания плазмы, и для охлаждения. Такого аппарата достаточно для разрезания заготовок 50 мм толщиной. Промышленный станок плазменной резки использует другие газы – гелий, аргон, кислород, водород, азот, а также их смеси.
Кабель-шланговый пакет соединяет источник питания, компрессор и плазмотрон. По электрическому кабелю подается ток от трансформатора или инвертора для возбуждения электрической дуги, а по шлангу идет сжатый воздух, который необходим для образования плазмы внутри плазмотрона. Более детально, что именно происходит в плазмотроне, расскажем ниже.
Принцип работы плазмореза
Как только нажимается кнопка розжига, источник питания (трансформатор или инвертор) начинает подавать на плазмотрон токи высокой частоты. В результате внутри плазмотрона возникает дежурная электрическая дуга, температура которой 6000 – 8000 °С. Дежурная дуга зажигается между электродом и наконечником сопла по той причине, что образование дуги между электродом и обрабатываемой заготовкой сразу – затруднительно. Столб дежурной дуги заполняет весь канал.
После возникновения дежурной дуги в камеру начинает поступать сжатый воздух. Он вырывается из патрубка, проходит через электрическую дугу, вследствие чего нагревается и увеличивается в объеме в 50 – 100 раз. Помимо этого воздух ионизируется и перестает быть диэлектриком, приобретая токопроводящие свойства.
Суженное к низу сопло плазмотрона обжимает воздух, формирует из него поток, который со скоростью 2 – 3 м/с вырывается из сопла. Температура воздуха в этот момент может достигать 25000 – 30000 °С. Именно этот высокотемпературный ионизированный воздух и является в данном случае плазмой. Ее электропроводимость примерно равна электропроводимости металла, который обрабатывается.
В тот момент, когда плазма вырывается из сопла и соприкасается с поверхностью обрабатываемого металла, зажигается режущая дуга, а дежурная дуга гаснет. Режущая/рабочая дуга разогревает обрабатываемую заготовку в месте реза – локально. Металл плавится, появляется рез. На поверхности разрезаемого металла появляются частички расплавленного только что металла, которые сдуваются с нее потоком воздуха, вырывающегося из сопла. Это самая простая технология плазменной резки металла.
![]() |
Катодное пятно плазменной дуги должно располагаться строго по центру электрода/катода. Чтобы это обеспечить, используется так называемая вихревая или тангенциальная подача сжатого воздуха. Если вихревая подача нарушена, то катодное пятно смещается относительно центра электрода вместе с плазменной дугой. Это может привести к неприятным последствиям: плазменная дуга будет гореть нестабильно, может образовываться две дуги одновременно, а в худшем случае – плазмотрон может выйти из строя.
Если увеличить расход воздуха, то скорость плазменного потока увеличится, также увеличится и скорость резки. Если же увеличить диаметр сопла, то скорость уменьшится и увеличится ширина реза. Скорость плазменного потока примерно равна 800 м/с при токе 250 А.
Скорость реза – тоже важный параметр. Чем она больше, тем тоньше рез. Если скорость маленькая, то ширина реза увеличивается. Если увеличивается сила тока, происходит то же самое – ширина реза увеличивается. Все эти тонкости относятся уже непосредственно к технологии работы с плазморезом.
Параметры плазмореза
Все аппараты плазменной резки можно разделить на две категории: ручные плазморезы и аппараты машинной резки.
Ручные плазморезы используются в быту, на маленьких производствах и в частных мастерских для изготовления и обработки деталей. Основная их особенность в том, что плазмотрон держит в руках оператор, он ведет резак по линии будущего реза, держа его на весу. В итоге рез получается хоть и ровным, но не идеальным. Да и производительность такой технологии маленькая. Чтобы рез получился более ровным, без наплывов и окалины, для ведения плазмотрона используется специальный упор, который одевается на сопло. Упор прижимается к поверхности обрабатываемой заготовки и остается только вести резак, не переживая за то, соблюдается ли необходимое расстояние между заготовкой и соплом.
На ручной плазморез цена зависит от его характеристик: максимальной силы тока, толщины обрабатываемой заготовки и универсальности. Например, существуют модели, которые можно использовать не только для резки металлов, но и для сварки. Их можно отличить по маркировке:
- CUT – разрезание;
- TIG – аргонодуговая сварка;
- MMA – дуговая сварка штучным электродом.
Например, плазморез FoxWeld Plasma 43 Multi совмещает все перечисленные функции. Его стоимость 530 – 550 у.е. Характеристики, касающиеся плазменной резки: сила тока – 60 А, толщина заготовки – до 11 мм.
Кстати, сила тока и толщина заготовки – основные параметры, по которым подбирается плазморез. И они взаимосвязаны.
Чем больше сила тока, тем сильнее плазменная дуга, которая быстрее расплавляет металл. Выбирая плазморез для конкретных нужд, необходимо точно знать, какой металл придется обрабатывать и какой толщины. В приведенной ниже таблице указано, какая сила тока нужна для разрезания 1 мм металла. Обратите внимание, что для обработки цветных металлов требуется большая сила тока. Учтите это, когда будете смотреть на характеристики плазмореза в магазине, на аппарате указана толщина заготовки из черного металла. Если вы планируете резать медь или другой цветной металл, лучше рассчитайте необходимую силу тока самостоятельно.
Например, если требуется разрезать медь толщиной 2 мм, то необходимо 6 А умножить на 2 мм, получим плазморез с силой тока 12 А. Если требуется разрезать сталь толщиной 2 мм, то умножаем 4 А на 2 мм, получаем силу тока 8 А. Только берите аппарат плазменной резки с запасом, так как указанные характеристики являются максимальными, а не номинальными. На них можно работать только непродолжительное время.
![]() |
Станок с ЧПУ плазменной резки используется на производственных предприятиях для изготовления деталей или обработки заготовок. ЧПУ означает числовое программное управление. Станок работает по заданной программе с минимальным участием оператора, что максимально исключает человеческий фактор на производстве и увеличивает производительность в разы. Качество реза машинным аппаратом идеально, не требуется дополнительная обработка кромок. А самое главное – фигурные резы и исключительная точность. Достаточно ввести в программу схему реза и аппарат может выполнить любую замысловатую фигуру с идеальной точностью. На станок плазменной резки цена значительно выше, чем на ручной плазморез. Во-первых, используется большой трансформатор. Во-вторых, специальный стол, портал и направляющие. В зависимости от сложности и размеров аппарата цена может быть от 3000 у.е. до 20000 у.е.
Аппараты машинной плазменной резки используют для охлаждения воду, поэтому могут работать всю смену без перерыва. Так называемый ПВ (продолжительность включения) равен 100 %. Хотя у ручных аппаратов он может быть и 40 %, что означает следующее: 4 минуты плазморез работает, а 6 минут ему необходимо для того, чтобы остыть.
Плазморез своими руками
Наиболее разумно будет приобрести плазморез готовый, заводского исполнения. В таких аппаратах все учтено, отрегулировано и работает максимально идеально. Но некоторые умельцы «Кулибины» умудряются смастерить плазморез своими руками. Результаты получаются не очень удовлетворительными, так как качество реза хромает. В качестве примера приведем урезанный вариант, как можно сделать плазморез самостоятельно. Сразу оговоримся, что схема далека от идеала и лишь дает общее понятие процесса.
Итак, трансформатор для плазмореза должен быть с падающей ВАХ.
![]() |
Пример на фото: первичная обмотка – снизу, вторичная – сверху. Напряжение – 260 В. Сечение обмотки – 45 мм2, каждая шина 6 мм2. Если установить силу тока на 40 А напряжение падает до 100 В. У дросселя также сечение 40 мм2, наматывался той же шиной, всего около 250 витков.
Для работы нужен воздушный компрессор, естественно, заводского исполнения. В данном случае использовался агрегат производительностью 350 л/мин.
Самодельный плазморез – схема работы.
![]() |
Плазмотрон лучше приобрести заводской, он обойдется примерно в 150 – 200 у.е. В данном примере плазмотрон изготавливался самостоятельно: медное сопло (5 у.е.) и гафниевый электрод (3 у.е.), остальное «кустарщина». За счет чего расходники быстро вышли из строя.
![]() |
Схема работает так: на резаке находится кнопка пуск, при ее нажатии реле (р1) подает на блок управления напряжение, реле (р2) подает напряжение на трансформатор, затем пускает воздух для продувки плазмотрона. Воздух осушает камеру плазмотрона от возможного конденсата и выдувает все лишнее, на это у него есть 2 – 3 секунды. Именно с такой задержкой срабатывает реле (р3), которое подает питание на электрод для поджига дуги. Затем включается осциллятор, который ионизирует пространство между электродом и соплом, как результат загорается дежурная дуга. Далее плазмотрон подносится к изделию и загорается режущая/рабочая дуга между электродом и заготовкой. Реле геркона отключает сопло и поджиг. Согласно данной схеме, если режущая дуга внезапно погаснет, например, если сопло попало в отверстие в металле, то реле геркона снова подключит поджиг и спустя несколько секунд (2 – 3) загорится дежурная дуга, а затем режущая. Все это при условии, что кнопка «пуск» не отпускается. Реле (р4) пускает воздух в сопло с задержкой, после того, как отпустили кнопку «пуск» и режущая дуга погасла. Все эти предосторожности необходимы для того, чтобы продлить ресурс сопла и электрода.
![]() | ![]() |
Самостоятельное изготовление плазмореза в «домашних» условиях дает возможность изрядно сэкономить, но о качестве реза говорить не приходится. Хотя если за работу возьмется инженер, то результат может быть даже лучше заводского исполнения.
ЧПУ плазморез своими руками
Станок плазменной резки с ЧПУ может позволить себе не каждое предприятие, ведь его стоимость может достигать 15000 – 20000 у.е. Довольно часто такие организации заказывают выполнение работ плазменной резки на специальных предприятиях, но это тоже обходится недешево, особенно если объемы работ большие. Но ведь так хочется свой новый станок плазменной резки, а средств не хватает.
Помимо известных профильных заводов есть предприятия, которые занимаются производством станков плазменной резки, закупая лишь профильные детали и узлы, а все остальное изготавливают самостоятельно. В качестве примера мы расскажем, как делают станки плазменной резки с ЧПУ инженеры в производственном цеху.
Составляющие станка плазменной резки своими руками:
- Стол 1270х2540 мм;
- Ременная передача;
- Шаговые детали;
- Линейные направляющие HIWIN;
- Система, управляющая высотой факела THC;
- Блок управления;
- Стойка-терминал, в котором находится блок управления ЧПУ, стоит отдельно.
Характеристики станка:
- Скорость перемещения по столу 15 м/мин;
- Точность установки позиции плазмотрона 0,125 мм;
- Если использовать аппарат Powermax 65, то скорость реза будет 40 м/мин для 6 мм заготовки или 5 м/мин для заготовки толщиной 19 мм.
На подобный станок плазменной резки металла цена будет около 13000 у.е., не включая источник плазмы, который придется приобрести отдельно – 900 у.е.
Для изготовления такого станка комплектующие заказываются отдельно, а затем все собирается самостоятельно по такой схеме:
- Готовится основание для сварки стола, оно должно быть строго горизонтальным, это очень важно, лучше проверить уровнем.
- Сваривается рама станка в виде стола. Можно использовать трубы квадратного сечения. Вертикальные «ноги» необходимо усилить укосинами.
![]() |
- Рама покрывается грунтовкой и краской, чтобы защитить от коррозии.
![]() |
- Изготавливаются опоры для станка. Материал опор – дюраль, болты 14 мм, гайки лучше приварить к болтам.
- Сваривается водяной стол.
![]() |
- Устанавливаются крепления для реек и ставятся рейки. Для реек используется металл в виде полосы 40 мм.
- Устанавливаются линейные направляющие.
- Корпус стола зашивается листовым железом и окрашивается.
- Устанавливается портал на направляющие.
![]() |
- На портал устанавливается двигатель и концевые индуктивные датчики.
- Устанавливаются рельсовые направляющие, зубчастая рейка и двигатель оси Y.
![]() | ![]() |
- Устанавливаются направляющие и двигатель на оси Z.
- Устанавливается датчик поверхности металла.
![]() |
- Устанавливается кран для слива воды из стола, ограничители для портала, чтобы не съехал со стола.
- Устанавливаются кабель-каналы Y,Z и X.
- Все провода прячутся в гофру.
- Устанавливается механизированная горелка.
- Далее изготавливается терминал с ЧПУ. Сначала сваривается корпус.
- В корпус терминала с ЧПУ устанавливается монитор, клавиатура, модуль ТНС и кнопки к нему.
![]() |
Все, станок плазменной резки с ЧПУ готов.
![]() |
Несмотря на то, что плазморез имеет достаточно простое устройство, все же не стоит браться за его изготовление без серьезных познаний в сварочном деле и большого опыта. Новичку проще заплатить за готовое изделие. А вот инженеры, желающие воплотить свои знания и умения в домашних условиях, что называется «на коленке», могут попробовать создать плазморез своими руками от начала и до конца.
Источник: https://strport.ru/
ingeneryi.info