Свойства лакокрасочных покрытий автомобиля. Покрытия лакокрасочные
Покрытие лакокрасочное: виды и способы примения
Покрытие лакокрасочное используется сегодня во множестве различных сфер, ведь оно отличается массой преимуществ. Одним из основных условий обеспечения всех этих достоинств является корректное использование, и именно поэтому важно знать, какими бывают такие покрытия, как их правильно наносить.
Что это?
Покрытие лакокрасочное представляет собой сформировавшуюся пленку лакокрасочного вещества, нанесенного на определенную поверхность. Она может образовываться на различных материалах. Сам же химический процесс, благодаря которому формируется покрытие лакокрасочное, включает в себя, в первую очередь, высыхание, а потом финишное затвердевание нанесенного материала.
Главной функцией таких покрытий является обеспечение эффективной защиты от каких-либо разрушений, а также придание любым поверхностям привлекательного внешнего вида, цвета и фактуры.
Виды
В зависимости от эксплуатационных свойств покрытие лакокрасочное может относиться к одному из следующих видов: водоустойчивые, маслобензостойкие, атмосферостойкие, термостойкие, химстойкие, консервационные, электроизоляционные, а также специального назначения. Последние включают в себя следующие подтипы:
- Противообрастающее покрытие лакокрасочное (ГОСТ Р 51164-98 и другие) представляет собой основной материал в судовой промышленности. При помощи него исключается риск обрастания подводных частей судов, а также всевозможных гидротехнических конструкций какими-либо водорослями, ракушками, микроорганизмами или другими веществами.
- Светоотражающее покрытие лакокрасочное (ГОСТ P 41.104-2002 и другие). Имеет способность к люминесценции в видимой зоне спектра при наличии воздействия облучением, светом.
- Термоиндикаторные. Позволяют изменить яркость или цвет свечения при наличии определенной температуры.
- Огнезащитные, которые препятствуют распространению пламени или же исключают возможность воздействия на защищаемую поверхность высоких температур.
- Противошумные. Обеспечивают защиту от проникновения звуковых волн через поверхность.
В зависимости от внешнего вида лакокрасочное покрытие может принадлежать к одному из семи классов, каждый из которых отличается уникальным составом, а также химической природой пленкообразователя.
Материалы
Всего принято использовать несколько типов материалов, основанных на:
- термопластичных пленкообразователях;
- термореактивных пленкообразователях;
- растительных маслах;
- модифицированных маслах.
Все перечисленные выше лакокрасочные покрытия сегодня довольно широко используются практически во всех сферах народного хозяйства, а также получили распространение в быту.
Статистика
Во всем мире производится ежегодно более 100 млн тонн лакокрасочных материалов, при этом более половины от всего этого количества используется в сфере машиностроения, в то время как четверть применяется в строительстве и ремонте.
Для изготовления лакокрасочных покрытий, которые потом применяются в отделке, используются предельно простые технологии производства, которые в основном предусматривают использование в качестве основы таких пленкообразователей, как водные дисперсии поливинилацетата, казеин, акрилаты и прочие аналогичные компоненты, основанные на жидком стекле.
В преимущественном большинстве случаев такие покрытия изготавливаются посредством нанесения специальных материалов в несколько слоев, благодаря чему достигаются максимально высокие показатели безопасности защищаемой поверхности. В основном их толщина составляет от 3 до 30 мкм, при этом из-за таких низких показателей достаточно сильно затрудняется определение толщины лакокрасочного покрытия в бытовых условиях, где нет возможности использовать специальные приборы.
Специальные покрытия
Чтобы получить многослойное защитное покрытие, принято наносить сразу несколько слоев материала различных видов, при этом у каждого слоя есть своя конкретная функция.
Прибор для проверки лакокрасочного покрытия применяется для того, чтобы убедиться в таких свойствах нижнего слоя, как обеспечение первичной защиты, адгезия к подложке, замедление электрохимической коррозии и других.
Покрытие, которое отличается максимальными защитными характеристиками, должно включать в себя несколько основных слоев:
- шпатлевка;
- грунтовка;
- фосфатный слой;
- от одного до трех слоев эмали.
В некоторых случаях, если прибор для проверки лакокрасочного покрытия показал неудовлетворительные значения, дополнительно может наноситься лак, при помощи которого обеспечиваются более эффективные защитные свойства, а также некая декоративность. При получении прозрачных покрытий лак принято наносить непосредственно на ту поверхность изделий, которой требуется обеспечение максимальной защиты.
Изготовление
Технологический процесс, с помощью которого получаются комплексные лакокрасочные покрытия, включает в себя несколько десятков различных операций, которые относятся к подготовке поверхности, нанесению лакокрасочного материала, сушке и проведению промежуточной обработки.
Выбор какого-то конкретного технологического процесса непосредственно зависит от типа используемых материалов, а также условий эксплуатации самой поверхности. Помимо этого, учитываются форма и габариты объекта, на который они наносятся. Качество подготовки поверхности перед нанесением окраски, а также правильный выбор того, какое лакокрасочное покрытие использовать, значительно определяет адгезионную прочность материала, а также его долговечность.
Подготовка поверхности включает в себя очистку с помощью ручного или же механизированного инструмента, дробеструйную или пескоструйную обработку, а также обработку с использованием различных химических средств, которая подразумевает ряд операций:
- Обезжиривание поверхности. К примеру, это касается обработки специализированными водными растворами или же смесями, в которые входят ПАВ и прочие добавки, органическими растворителями или специализированными эмульсиями, включающими в свой состав воду и органический растворитель.
- Травление. Полное удаление ржавчин, окалин, а также других продуктов коррозии с защищаемой поверхности. В преимущественном большинстве случаев данная процедура осуществляется уже после того как была проведена проверка лакокрасочного покрытия автомобиля или других изделий.
- Нанесение конверсионных слоев. Оно предусматривает изменение изначальной природы поверхности и довольно часто используется при необходимости создания комплексных лакокрасочных покрытий с большим сроком службы. В частности, сюда входит фосфатирование и оксидирование (в преимущественном большинстве случаев электрохимическим методом на аноде).
- Формирование металлических подслоев. Сюда входит цинкование и кадмирование (в основном с использованием электрохимического метода на катоде). Обработка поверхности с использованием химических средств в основном осуществляется путем окунания или же обливания изделия специализированным рабочим раствором в условиях полностью автоматизированной или механизированной конвейерной окраски. Вне зависимости от того, какие используются виды лакокрасочных покрытий, применение химических средств позволяет добиться высокого качества подготовки поверхности, но при этом предусматривает дальнейшую промывку водой и горячую сушку поверхности.
Как наносятся жидкие покрытия?
После того как выбираются необходимые материалы, а также проверяется качество лакокрасочного покрытия, выбирается способ нанесения его на поверхность, которых существует несколько:
- Ручной. Применяется для проведения окраски различных крупногабаритных изделий, а также для проведения бытового ремонта и устранения всевозможных бытовых дефектов. В основном принято использовать лакокрасочную продукцию естественной сушки.
- валковый. Механизированное нанесение, которое предусматривает использование системы валиков. Применяется для нанесения материалов на плоские изделия, такие как полимерные пленки, листовой и рулонный прокат, картон, бумага и множество других.
- струйный. Обрабатываемое изделие проводится через специальную «завесу» из соответствующего материала. При помощи такой технологии может наноситься лакокрасочное покрытие машины, различного бытового оборудования и еще целого ряда других изделий, при этом для отдельных деталей чаще используется облив, в то время как наливом обрабатываются плоские изделия, такие как листовой металл, а также щитовые элементы мебели и другие.
Методы окунания и облива в преимущественном большинстве случаев принято использовать для того, чтобы наносить слои лакокрасочного покрытия на изделия обтекаемой формы, имеющие гладкую поверхность, если нужно окрасить их в один цвет. Для получения лакокрасочных покрытий, имеющих равномерную толщину без каких-либо наплывов или подтеков, после окраски изделия в течение определенного времени выдерживают в парах растворителя, поступающих непосредственно из сушильной камеры. Здесь важно провести правильно определение толщины лакокрасочного покрытия.
Окунание в ванну
Традиционное лакокрасочное покрытие лучше всего удерживается на поверхности после того, как изделие извлекается из ванны после смачивания. Если рассматривать водоразбавляемые материалы, то здесь принято использовать окунание с хемо-, электро- и термоосаждением. В соответствии со знаком заряда поверхности изделия, которое подвергается обработке, различается като- и анофоретическое электроосаждения.
При использовании катодной технологии получаются такие покрытия, которые имеют достаточно высокую коррозийную устойчивость, в то время как использование самой технологии электроосаждения позволяет добиться эффективной защиты от коррозии кромок и острых узлов изделия, а также внутренних полостей и сварных швов. Единственной же неприятной особенностью данной технологии является то, что наносится в данном случае только один слой материала, так как первый слой, который является диэлектриком, будет препятствовать электроосаждению последующих. Также стоит отметить тот факт, что этот метод может сочетаться с предварительным нанесением специального пористого осадка, сформированного из суспензии пленкообразователя.
При хемоосаждении используется дисперсионный лакокрасочный материал, в состав которого входят всевозможные окислители. В процессе их взаимодействия с металлической подложкой на ней формируется достаточно высокая концентрация особых поливалентных ионов, что обеспечивает коагуляцию приповерхностных слоев использующегося материала.
В случае использования термоосаждения осадок создается на нагретой поверхности, и в данной ситуации в воднодисперсионный лакокрасочный материал вводится специализированная добавка, теряющая растворимость в случае нагрева.
Распыление
Данная технология также распределяется на три основные разновидности:
- Пневматическое. Предусматривает использование автоматических или же ручных пистолетообразных распылителей с лакокрасочными материалами при температуре 20-85 оС, которые подаются под высоким давлением. Применение такого метода отличается достаточно высокой производительностью, а также позволяет добиться неплохого качества лакокрасочных покрытий вне зависимости от формы поверхностей.
- Гидравлическое. Осуществляется под давлением, которое создается специализированным насосом.
- Аэрозольное. Применяются баллончики, заполненные пропеллентом и лакокрасочными материалами. По ГОСТ лакокрасочное покрытие легковых автомобилей может наноситься и с применением такого метода, а помимо этого его активно используют при покраске мебели и еще целого ряда других изделий.
Довольно важным недостатком, которым отличаются практически все существующие методы распыления, является наличие довольно существенных потерь материала, так как аэрозоль уносится вентиляцией, оседает на стенах камеры и в используемых гидрофильтрах. При этом стоит отметить, что потери при пневмораспылении могут достигать 40%, что представляет собой довольно существенный показатель.
Чтобы хоть как-то сократить такие потери, принято использовать технологию распыления в специальном электрическом поле высокого напряжения. Частицы материала в результате коронного разряда или же контактного заряжения получают заряд, после чего оседают на окрашиваемом изделии, которое в данном случае служит электродом противоположного знака. При помощи такого метода в преимущественном большинстве случаев принято наносить различные многослойные лакокрасочные покрытия на металлы и простые поверхности, среди которых, в частности, можно выделить древесину или пластмассу с токопроводящим покрытием.
Как наносятся порошковые материалы?
Всего используется три основных метода, которыми осуществляется нанесение лакокрасочных покрытий в виде порошка:
- насыпание;
- напыление;
- нанесение в псевдоожиженном слое.
Преимущественное большинство технологий нанесения ЛКМ принято использовать в процессе окраски изделий непосредственно на поточных конвейерных линиях, благодаря чему при повышенных температурах формируются устойчивые покрытия, отличающиеся достаточно высокими потребительскими и техническими свойствами.
Также градиентные лакокрасочные покрытия получаются посредством единоразового нанесения материалов, которые включают в себя смеси порошков, дисперсий или растворов пленкообразователей, не характеризующихся термодинамической совместимостью. Последние могут самостоятельно расслаиваться в процессе испарения общего растворителя или же при нагреве пленкообразователей выше температур текучести.
За счет избирательного смачивания подложки один пленкообразователь обеспечивает обогащение поверхностных слоев лакокрасочных покрытий, в то время как второй, в свою очередь, обогащает нижние. Таким образом, создается структура многослойного покрытия.
При этом стоит отметить, что технологии в этой сфере постоянно совершенствуются и улучшаются, в то время как старые методы забываются. В частности, сегодня покрытие лакокрасочное (система 55) по ГОСТ 6572-82 уже не применяется для обработки двигателей, тракторов и самоходных шасси, хотя раньше его применение было весьма распространенным.
Сушка
Сушка нанесенных покрытий осуществляется при температуре от 15 до 25 оС, если речь идет о холодной или естественной технологии, а также может осуществляться при повышенных температурах при использовании «печных» методов.
Естественная применяется в случае использования лакокрасочных материалов, основанных на термопластичных быстровысыхающих пленкообразователях и тех, которые имеют ненасыщенные связи в молекулах, использующих в качестве отвердителей влагу или кислород, такие как полиуретаны и алкидные смолы. Также стоит отметить, что довольно часто естественная сушка встречается в случае использования двухупаковочных материалов, в которых применение отвердителя осуществляется перед нанесением.
Сушка материалов в промышленности зачастую производится при температуре от 80 до 160 оС, при этом порошковые и некоторые специальные материалы и вовсе могут сушиться при температуре до 320 оС. За счет создания таких условий обеспечивается ускоренное улетучивание растворителя, а также осуществляется термоотверждение различных реакционноспособных пленкообразователей, к примеру, меламино-алкидных, алкидных, а также феноло-формальдегидных смол.
Наиболее популярными технологиями термоотверждения покрытия стоит назвать следующие:
- Конвективные. Изделие обогревается при помощи циркулирующего горячего воздуха.
- Терморадиационные. В качестве источника обогрева используется инфракрасное излучение.
- Индуктивные. Для сушки изделие размещается в переменном электромагнитном поле.
Чтобы получить лакокрасочные покрытия, основанные на ненасыщенных олигомерах, принято использовать также технологию отверждения под воздействием ультрафиолетовых излучений или ускоренных электронов.
Дополнительные процессы
В ходе проведения сушки происходит множество химических и физических процессов, которые в итоге приводят к созданию высокозащищенных лакокрасочных покрытий. В частности, сюда входит удаление воды и органического растворителя, смачивание подложки, а также поликонденсация или полимеризация, если речь идет о реакционноспособных пленкообразователях с образованием сетчатых полимеров.
Создание покрытий из порошковых материалов включает в себя обязательное оплавление различных частиц пленкообразователя, а также слипание сформировавшихся капель и смачивание ими подложки. Также стоит отметить, что в некоторых ситуациях принято использовать термоотверждение.
Промежуточная обработка
Проведение промежуточной обработки предусматривает:
- Шлифование при помощи абразивных шкурок нижних слоев ЛКМ, чтобы удалить какие-либо посторонние включения, а также придать матовость и улучшить адгезию между несколькими слоями.
- Полировка верхнего слоя с применением специализированных паст, чтобы лакокрасочные покрытия получили зеркальный блеск. В качестве примера можно привести технологические схемы окраски, использующиеся при обработке кузовов легковых автомобилей и включающие в себя обезжиривание, фосфатирование, охлаждение, сушку, грунтование и отверждение поверхности с последующим нанесением герметизирующих, шумоизолирующих и ингибирующих составов, а также проведение еще целого ряда других процедур.
Свойства нанесенных покрытий определяются составом используемых материалов, а также структурой самого покрытия.
fb.ru
1.5. Лакокрасочные защитные покрытия
Лакокрасочные покрытия — один из самых распространенных и надежных способов защиты от коррозии. Они дешевы и доступны, имеют простую технологию нанесения на поверхность, легко восстанавливаются в случае повреждения, отличаются разнообразием внешнего вида и цвета.
Ежегодно более 80 % металлоизделий, используемых в народном хозяйстве, подвергаются окрашиванию. В 1999 г. производство лакокрасочных материалов достигло 26,7 млн.т. Это свидетельствует об огромных масштабах средств, вовлеченных в сферу производства этого вида противокоррозионной защиты.
Эффективность применения лакокрасочных покрытий, как показывают данные рис. 3, целесообразна при условии долговечности эксплуатации не более 10 лет и скорости коррозии металла до 0,05 мм/год. Если требуется повышение долговечности или скорость коррозии металла составляет 0,5-1,0 мм/год, то следует применять комбинированные покрытия. Например, цинковые плюс лакокрасочное покрытие. Такое покрытие позволяет увеличить срок защиты до 30 лет.
Защитные действия лакокрасочного покрытия заключаются в создании на поверхности металлического изделия сплошной пленки, которая препятствует агрессивному воздействию окружающей среды и предохраняет металл от разрушения.
Компонентами лакокрасочных материалов служат пленкообразующие вещества, растворители, пластификаторы, пигменты, наполнители, катализаторы (сиккативы).
Лаки — это коллоидные растворы высыхающих масел или смол в органических растворителях. Защитное твердое покрытие образуется вследствие испарения растворителя или полимеризации масла или смолы при нагревании или под действием катализатора.
Краски представляют собой суспензию минеральных пигментов в пленкообразователе.
Эмали — это раствор лака, в который введены измельченные пигменты.
Пленкообразователи — это природные масла, естественные или искусственные смолы. Масла по своему составу представляют собой сложные эфиры, т.е. являются продуктом взаимодействия кислот и спиртов. В основу классификации масел положена их способность к высыханию.
Наиболее распространенный масляный пленкообразователь — олифа. Натуральную олифу получают из высыхающих растительных масел, обработанных при 300 °С с целью частичной полимеризации. На воздухе олифа окисляется и полимеризуется до твердого состояния.
Растворители пленкообразующих веществ придают лакокрасочным покрытиям такую вязкость, при которой они легко наносятся на поверхность. В дальнейшем растворители испаряются. Растворителями могут быть: спирты, ацетон, бензин, скипидар, толуол, ксилол, этилацетат и др.
Пластификаторы или смягчители — это вещества повышающие эластичность пленок после высыхания. К ним относятся касторовое масло, каучуки, дибутилфталат, трикрезилфосфат, эфиры адипиновой кислоты.
Количество пластификаторов, вводимых в смесь, составляет 20-75 % от массы пленкообразователя.
Краски и пигменты вводят в состав лакокрасочных композиций для придания им определенного цвета. Краски растворяются в растворителях, а пигменты находятся в них в нерастворимом мелкодисперсном состоянии. Размер частиц от 0,5 до 5 мкм. В качестве пигментов используют охру, сурик свинцовый, хром свинцовый, цинковые белила, порошки металлов. Пигменты повышают твердость, атмосферную и химическую стойкость, износостойкость и т.д.
Наполнители — это инертные вещества, которые вводят в лаки и краски для снижения расхода пигментов, а также для улучшения антикоррозионных свойств пленки. К ним относятся мел, тальк, каолин, асбестовая пыль и др.
Наполнители образуют прочную основу всей пленки. Частицы наполнителя распределяются в пленке между частицами пигмента и заполняют имеющиеся в ней промежутки. Благодаря этому пленка приобретает повышенную влагостойкость и антикоррозионные свойства. Схема строения лакокрасочной пленки представлена на рис. 8.
Рис.8. Строение лакокрасочной плёнки
Сиккативы или катализаторы представляют собой магниевые и кобальтовые соли жирных органических кислот. Их вводят в состав композиций для ускорения высыхания масляных пленок.
Успешная противокоррозионная защита лакокрасочными материалами в значительной степени зависит от соблюдения технологии получения покрытий. Основными факторами, влияющими на срок службы покрытия, являются:
• способ подготовки поверхности;
• методы нанесения и отверждения лакокрасочного покрытия;
• толщина комплексного покрытия.
studfiles.net
Лакокрасочные покрытия - это... Что такое Лакокрасочные покрытия?
покрытия, которые образуются в результате плёнкообразования (высыхания) лакокрасочных материалов (См. Лакокрасочные материалы), нанесённых на поверхность изделий. Основное назначение Л. п. — защита материалов от разрушения (например, металлов — от коррозии (См. Коррозия), дерева — от гниения) и декоративная отделка изделий (см. также Защитные лакокрасочные покрытия, Декоративные лакокрасочные покрытия, Отделка древесины, Малярные работы). Существуют также Л. п. специального назначения — электроизоляционные, флуоресцентные, термоиндикаторные, термостойкие, бензо- и маслостойкие и др. Применяют Л. п. во всех отраслях народного хозяйства и в быту. При правильной эксплуатации срок службы Л. п. может достигать нескольких лет, они не дороги, просто наносятся и ремонтируются, придают защищаемой поверхности красивый внешний вид. В 1972 во всём мире для получения Л. п. было израсходовано около 14,5 млн. т лакокрасочных материалов. Свойства Л. п. определяются составом лакокрасочных материалов (типом плёнкообразующих веществ (См. Плёнкообразующие вещества), пигментов (См. Пигменты) и др.), а также структурой покрытий, которые в большинстве случаев состоят из нескольких слоев. Важнейшие требования к Л. п. — прочное сцепление (Адгезия) отдельных слоев друг с другом, а нижнего слоя — также и с подложкой, твёрдость, прочность при изгибе и ударе, влагонепроницаемость, атмосферостойкость, комплекс декоративных свойств (прозрачность или укрывистость, цвет, степень блеска, узор и др.). При получении многослойных Л. п. применяют следующие материалы: Грунтовки, которые наносят непосредственно на подложку для её антикоррозионной защиты и обеспечения адгезии Л. п.; Шпатлёвки, наносимые по слою грунтовки при необходимости заполнения пор, мелких трещин и устранения др. дефектов поверхности; Краски, которые придают поверхности необходимые декоративные свойства и обеспечивают стойкость Л. п. к внешним воздействиям; Лаки, наносимые по слою краски для повышения блеска Л. п. (при получении прозрачных Л. п. лак наносят непосредственно на защищаемую поверхность). Общая толщина многослойных Л. п. составляет обычно 40—300 мкм. Технологический процесс получения Л. п. включает операции подготовки поверхности, нанесения отдельных слоев, сушку Л. п. и их отделку. Качество подготовки поверхности под окраску в значительной степени определяет адгезию Л. п. к подложке. Эффективные способы подготовки металлических поверхностей — придание им шероховатости с помощью дробеструйной или гидроабразивной обработки или создание микропористого подслоя путём оксидирования (См. Оксидирование) или фосфатирования (См. Фосфатирование).Технология нанесения лакокрасочных материалов претерпела начиная с 1920—30-х гг. существенные изменения в связи с развитием производства синтетических плёнкообразующих веществ, а также в результате разработки эффективных средств механизации и автоматизации производственных процессов. Известные издавна ручные методы нанесения лакокрасочных материалов с помощью кисти или шпателя ввиду их малой производительности и затруднений при работе с быстровысыхающими лакокрасочными материалами используются в современном производстве в ограниченных масштабах. В машиностроении наиболее распространён метод нанесения Л. п. с помощью ручных или автоматических пистолетообразных краскораспылителей. Применение этого высокопроизводительного метода позволяет получать Л. п. хорошего качества на поверхностях различной формы. В установках для пневматического распыления может быть осуществлен подогрев (до 55—70°С) как лакокрасочного материала, так и расходуемого на распыление воздуха. Это позволяет наносить высоковязкие материалы и уменьшать, таким образом число слоев, необходимых для получения Л. п. заданной толщины. Недостаток метода — большие потери лакокрасочного материала (до 50%) па рассеивание в окружающем воздухе («туманообразование»). Помимо непроизводительного расхода материалов, это создаёт тяжёлые условия работы. Поэтому лакокрасочные материалы распыляют обычно в огражденных, хорошо вентилируемых камерах. Потери на «туманообразование» могут быть существенно уменьшены (до 15—30%) при распылении лакокрасочных материалов под высоким давлением, создаваемым насосом [4—25 Мн/м2 (40—250 кгс/см2)].
Резкое сокращение потерь на «туманообразование» (до 5—10%) достигается при распылении лакокрасочных материалов в электрическом поле постоянного тока высокого напряжения (около 100 кв). В результате коронного разряда (См. Коронный разряд), создаваемого на острой кромке распылителя, частицы материала приобретают заряд (обычно отрицательный), вследствие чего они распыляются и осаждаются на противоположно заряженном и заземлённом изделии. В электрическом поле наносят многослойные Л. п. как на металлы, так и на неметаллические материалы, в частности на древесину с влажностью не менее 8%. Электрораспыление, широко применяемое для окраски деталей на конвейерных линиях, осуществляется автоматически. Единичные и разнотипные изделия окрашивают с помощью ручных электрораспылителей, изделия сложного профиля — с помощью пневмоэлектро- и гидроэлектрораспылителей, применение которых позволяет покрывать заглубленные участки поверхности. При подкраске и восстановлении внешнего вида изделий (например, автомобилей, мебели) используют метод аэрозольного распыления с помощью баллончиков, заполненных лакокрасочным материалом, разбавленным сжиженным фреоном (См. Фреоны).Однотипные изделия массового производства, имеющие обтекаемую форму, можно окрашивать методами окунания и струйного обливания; в последнем случае расходуется меньше лакокрасочного материала. Дефект Л. п., получаемых этими методами, — образование подтёков и «наплывов» — предотвращают, пропуская окрашенные изделия через туннель с парами растворителя. При этом задерживается улетучивание растворителя из нанесённого слоя, что позволяет избежать преждевременного загустения лакокрасочного материала.
Для нанесения полиэфирных лакокрасочных материалов на деревянные щитовые заготовки мебели применяют лаконаливную машину (См. Лаконаливная машина). Методом электроосаждения в ваннах на аноде (напряжение постоянного тока 30—500 в) на автоматизированных конвейерных линиях получают Л. п. из водоразбавляемых грунтовок и лаков. Под влиянием Электрофореза частицы лакокрасочного материала разряжаются на аноде и осаждаются на нём, переходя в водонерастворимую форму. Этим методом может быть нанесён только один слой Л. п. (20—25 мкм), т. к. его изолирующее действие препятствует электроосаждению последующих слоев. К числу высокопроизводительных методов нанесения Л. п. на листовые и рулонные материалы (например, металлические ленты, полосы) относится накатка с помощью валков. Сушка Л. п. бывает холодная (естественная, воздушная) или горячая (искусственная, печная). Холодную сушку применяют для быстро высыхающих лакокрасочных материалов, а также для медленно высыхающих, но наносимых на изделия, которые нельзя подвергать действию высоких температур. Горячая сушка позволяет не только ускорить улетучивание растворителя, но и отвердить Л. п. на основе реакционноспособных (превращаемых) плёнкообразователей. Один из наиболее старых методов горячей сушки — конвективный, осуществляемый в сушильных камерах; при его использовании сушка каждого слоя длится 1—3 ч. Более производителен (в 3—6 раз) метод терморадиационной сушки Л. п. под действием инфракрасных лучей. Источниками излучения служат лампы накаливания или тёмные излучатели — металлические панели или керамические плиты, нагреваемые до 400—700°С трубчатыми электронагревателями или газовыми горелками. Тёмные излучатели долговечнее, эффективнее и экономичнее ламповых (см. Инфракрасный нагрев). Быстрое высыхание Л. п. достигается при индукционном методе сушки вследствие нагрева подложки вихревыми токами. Под действием ультрафиолетового облучения или потока быстрых электронов полиэфирные лакокрасочные материалы высыхают (отверждаются) в течение долей секунды.Отделочные операции включают шлифование абразивными шкурками высушенных нижних слоев Л. п. для удаления посторонних включений и улучшения адгезии между слоями. Верхний слой Л. п. при необходимости полируют, например, с помощью полировочной пасты и полировочной воды. Шлифование и полирование могут быть осуществлены вручную, а также с помощью машинок пневматического действия или автоматических устройств.
Для контроля качества Л. п. проводят их внешний осмотр и определяют (на образцах) твёрдость, эластичность, прочность при изгибе, антикоррозионные свойства, атмосферостойкость и др. эксплуатационные характеристики.
Лит.: Любимов Б. В., Специальные защитные покрытия в машиностроении, 2 изд., М. — Л., 1965; Аронов Н. В., Оборудование и механизация цехов неметаллических защитных покрытий, М., 1969; Справочник по лакокрасочным покрытиям в машиностроении, М., 1964; Альбом оборудования окрасочных цехов, М., 1970.
М. М. Гольдберг.
dic.academic.ru
Лакокрасочные покрытия металлов - Цветные металлы
Лакокрасочные покрытия металловКатегория:
Цветные металлы
Лакокрасочные покрытия металловЛакокрасочные покрытия получают путем нанесения на детали лакокрасочных материалов; их широко применяют для предохранения летательных аппаратов и двигателей от коррозии, для улучшения аэродинамических свойств поверхности, а также в Целях маскировки.
После нанесения на покрываемую поверхность лакокрасочные материалы высыхают и образуют плотную пленку, хорошо сцепляющуюся с покрытой поверхностью, достаточно прочную и эластичную, сохраняющую связь с деталью практически при всех изменениях внешних условий в процессе хранения, транспортировки и эксплуатации.
Лакокрасочные материалы классифицируются по характеру процесса пленкообразования и по виду.
Рис. 1. Схема защиты стали анодным (а) и катодным (б) покрытиями
По характеру процесса пленкообразования, или высыхания, все лакокрасочные материалы подразделяются на две группы-материалы на основе растительных масел и материалы на основе нитроцеллюлозы и смол.
1. Материалы на основе растительных масел
Образование пленки у этих материалов происходит в результате длительного процесса физико-химического изменения растительного масла под действием воздуха, света и температуры. Происходящее при этом присоединение кислорода воздуха к молекулам масла сообщает лакокрасочной пленке высокую вязкость и достаточную прочность.
2. Материалы на основе нитроцеллюлозы и смол
Быстровысыхающие лакокрасочные материалы изготовляются на основе нитроцеллюлозы, глифталевой, перхлорвиниловой и других смол. Образование пленок у этих материалов происходит за счет испарения растворителей из жидкого слоя лака или краски. Оставшаяся при этом нитроцеллюлоза или смола образует пленку с необходимыми защитными свойствами.
По виду лакокрасочные материалы подразделяются на четыре группы:
1. Грунт, предназначающийся для непосредственной защиты изделия от коррозии и обеспечения прочной связи основной лакокрасочной пленки с поверхностью изделия.
2. Шпаклевка, служащая для выравнивания покрываемой поверхности.
3. Краска, применяемая для получения основного слоя покрытия, защищающего деталь от внешней среды.
4. Лак, используемый для получения последнего, отделочного слоя покрытия, придающего поверхности детали гладкость и хорошую обтекаемость.
На рис. 2 представлен разрез полного лакокрасочного покрытия, включающего все описанные слои.
Рис. 2 Схема разреза полного лакокрасочного покрытия
Пленкообразователи служат основой лакокрасочных материалов, из них образуются защитные пленки лакокрасочного подпития’. В качестве пленкообразователей применяются растительные масла, эфиры целлюлозы и смолы.
Из растительных масел применяются древесное (тунговое), льняное, конопляное, подсолнечное и другие. Основным качеством этих масел является способность их высыхать, характеризуемая йодным числом, показывающим ненасыщенность масла и, следовательно, способность его окисляться и высыхать. Йодным числом называется число граммов иода, присоединяющегося к 100 г масла. У высыхающего льняного масла оно равно 190, а у невысыхающего касторового —всего лишь 85.
Для лакокрасочных материалов применяют не сами масла, а олифы, представляющие собой масла, уплотненные (частично окисленные) выдержкой при повышенной температуре и, следовательно, более густые. Кроме того, в олифу вводят ускорители сушки.
Ускорители сушки (сиккативы) представляют собой вещества, каталитически ускоряющие процесс высыхания масел. Они выполняют роль передатчиков кислорода. В качестве сиккативов используются высшие окислы кобальта, марганца и свинца.
Льняное масло без сиккатива высыхает через 70 час, то же масло со свинцовым сиккативом высыхает через 21 час, с марганцевым — через 4 час, а с кобальтовым — через 2,5 час.
Нитроцеллюлоза, а также глифталевая, перхлорвиниловая, эпоксидная и кремнийорганическая смолы также являются плен-кообразователями. Они образуют прочные и стойкие в различных средах защитные пленки. Высыхание и отвердевание их происходит вследствие испарения растворителя. Поэтому введение в них ускорителей сушки — сиккативов не требуется.
Пигменты и красители вводятся в лакокрасочные материалы для увеличения прочности и защитной способности пленки, а также для придания ей определенной окраски. Красящие вещества, не растворяющиеся в связующем, называются пигментами, растворяющиеся — красителями.
Пигменты представляют собой тонко размолотые минеральные вещества.
По цвету пигменты можно разделить на две группы:1. Ахроматические пигменты: белые, представляющие собой в основном различные белила — цинковые, свинцовые, титановые; серые — алюминиевая пудра, цинкоЬая пыль; черные — сажа, жженая кость.2. Хроматические пигменты: желтые — охра, цинковый и свинцовый крон; красные — свинцовый и железный сурик, киноварь и мумия; зеленые — окись хрома, медянка; синие — уль рамарин, берлинская лазурь.
Пластификаторы представляют собой вещества, вводимые нитроцеллюлозные лаки для сохранения эластичности пленки q течением времени, предупреждения отслаивания ее от поверхно сти металла, растрескивания, морщения и для понижения во пламеняемости пленки. Предполагается, что пластификатор внедряясь между макромолекулами нитроцеллюлозы, облегчает скольжение их друг относительно друга. В качестве пластифика торов применяются фталаты (эфиры фталевой кислоты), фос фаты (эфиры фосфорной кислоты) и касторовое масло.
Наполнители представляют собой тонко размолотые мел, тальк, каолин и другие порошки, вводимые в грунты и шпаклев ки для придания им соответствующих химических и физико-ме ханических свойств.
Растворители представляют собой органические летучие жид кости, применяемые для растворения пленкообразователей, улетучивающиеся в процессе образования пленки.
До недавнего времени не было общепринятой классификации и системы обозначения лакокрасочных материалов; по этой причине их названия носят случайный характер. В настоящее время ГОСТ 9825—61 предусмотрена единая классификация и маркировка лакокрасочных материалов. Обозначения лакокрасочных материалов определяются основной смолой или эфиром целлюлозы, введенными в состав пленкообразующего вещества и группой, к которой отнесен данный лакокрасочный материал.
Для смол, эфиров целлюлозы и масел приняты обозначения, главные из которых приведены ниже: битумы — БТ; глифтали — ГФ; пентафтали — ПФ; фенольные — ФЛ; меламинные — МЛ; кремнийорганические — КО; эпоксидные — ЭП; перхлорвинило-вые — ХВ; нитроцеллюлоза — НЦ; ацетилцеллюлоза — АЦ; масла растительные — МА.
По назначению лакокрасочные материалы делятся на восемь групп, обозначенных в таблице 38.
Обозначение (марка) лаков, грунтовок и шпаклевок состоит из пяти групп знаков, следующих одна за другой слева направо.
Первая группа определяет вид лакокрасочного материала, например: «лак», «эмаль», «грунтовка», «шпаклевка».
Вторая группа определяет основную смолу, входящую в состав пленкообразующего вещества. Между второй и третьей группой знаков ставится тире; третья группа определяет преимущественное значение материала и обозначается цифрой согласно таблице 38.
Четвертая группа определяет порядковый номер, присвоенный данному лакокрасочному материалу в группе, к которой он отнесен.
Пятая группа — относится в основном к эмалям и определяет их цвет — «красная», «синяя» и т. п.
Ниже приведены примеры обозначения лаков, эмалей и грунтовок.
Грунтовка коричневая на основе фенолформальдегидной смолы: грунтовка ФЛ—013 коричневая.
Эмаль голубая нитроцеллюлозная для внутренних работ: эмаль НЦ—25 голубая.
Лак глифталевый электроизоляционный: лак ГФ—95.
Обозначения масляных красок также состоят из пяти групп знаков, например: краска МА—11 коричневая, что означает — краска масляная для наружных (1) работ; (для внутренних работ первая цифра правее тире — 2). Для красок часто вместо слова «краска» указывается пигмент, например «белила цинковые», «охра» и т. п.
Основными лакокрасочными материалами, применяемыми для покрытия летательных аппаратов и двигателей, наземных транспортных средств, наземного оборудования и конструкций, являются грунты, шпаклевки, краски, эмали и лаки.
Грунты предназначаются для нанесения первого слоя лакокрасочного покрытия и могут изготавливаться на основе растительных масел, смол или нитроцеллюлозы.
Наряду с этим в качестве грунта под лакокрасочное покры тие в ряде случаев используются неметаллические неорганиче ские покрытия, например фосфатные на стали и окисные на алю минии.
Грунты для металлов делятся на пять групп: изолирующие; с пигментами основного характера; пассивирующие; протекторные и фосфатирующие.
Изолирующие грунты изготовляются на основе инертных пигментов. К ним относятся, например, грунты с железным суриком. Для покрытия дюралюминиевых и магниевых деталей применяется лаковый желтый грунт АЛГ-1 ‘) на основе масляного лака и цинкового крона.
Для стальных деталей применяется глифталеЕый коричневый грунт № 138 на основе глифталевого лака и железного сурика или свинцового крона. Покрытия этим грунтом отличаются хорошими антикоррозионными свойствами, хорошей адгезией, эластичностью и механической прочностью.
Для деталей из легких сплавов и дерева применяются нитро-грунты, состоящие из нитроцеллюлозы, смолы, пластификаторов, пигментов и растворителей. Для легких сплавов используются грунты АГ-10с и АГ-ЗА, для деталей из дерева — желтый грунт дд-пз.
Грунт с пигментами основного характера (свинцовый сурик, цинковые белила) отличается повышенной водостойкостью в результате образования сложных комплексных соединений при взаимодействии пигмента с пленкообразователем.
Пассивирующие грунты отличаются пассивирующими свойствами и содержат хроматы металлов: цинковый крон, хромат свинца и другие.
Протекторные грунты включают порошкообразный металлический пигмент, имеющий более низкий электродный потенциал по сравнению с покрываемым металлом. Примером таких грунтов могут служить цинковые протекторные грунты ПС.
Фосфатирующие грунты (ФХЛ) содержат хромовый ангидрид и фосфорную кислоту, способные фосфатировать поверхность стальных деталей, улучшать адгезию и защиту от коррозии.
Шпаклевка наносится на слой грунта до полного выравнивания поверхности. По составу шпаклевки могут быть масляные (лаковые) и нитрошпаклевки.
Шпаклевка представляет собой густую пасту, состоящую примерно из 80% пигментов и наполнителей (железный сурик, цинковые белила, охра, мел и другие), затертых на различных пленкообразующих веществах.
Для покрытия по грунту № 138 наружных поверхностей применяется шпаклевка ЛШ-1.
Выравнивание и сплошное покрытие поверхностей деталей из легких сплавов по грунту АЛГ-1 осуществляется коричневой шпаклевкой № 175 на глифталевом лаке.
Деревянные детали покрываются желто-зеленой нитрошпак-левкой АШ-30, содержащей 7% нитроцеллюлозы, 5% смолы, 45о/0 пигмента, небольшое количество амилацетата в качестве растворителя и остальное наполнитель. Расход ее до 300 г/м2.
Эмали и краски предназначаются для нанесения основного слоя лакокрасочного покрытия. Краски представляют собой суспензии мелкорастертых пигментов в пленкообразователе. Эмали или эмалевые краски в отличие от обычных красок при высыхании образуют твердую блестящую пленку с хорошим лаковым глянцем, напоминающим эмали ‘).
По эксплуатационной стойкости краски и эмали подразделяются на атмосферостойкие, химически стойкие, термостойкие и жаростойкие.
Атмосферостойкими являются масляные краски 4БО (ГОСТ 5786—51) защитного цвета, приготовленная на олифе, а также зеленая масляная эмаль А24г, светло-коричневая А21 и другие. Высокой атмосферостойкостью отличаются также эмали на основе перхлорвиниловых материалов, например защитная эмаль ПХВ-715Т серая, голубая, коричневая и другие.
Химически стойкие предназначаются для эксплуатации в кислотах, щелочах и других агрессивных средах. К ним относятся материалы на основе перхлорвиниловой смолы. Так, например, для защиты от серной, азотной, фосфорной и других кислот, а также от щелочей и растворов солей предназначаются грунты ХСГ, эмали ХСЭ и лаки ХСЛ.
Термостойкие лакокрасочные покрытия под действием высоких температур не изменяют внешнего вида, защитных и физи-ко-химических свойств. Они получаются преимущественно на алкидно-масляной или кремнийорганической основе в сочетании с пигментами: железным суриком, графитом, алюминиевой пудрой и другими. Термостойкая эмаль черная 4-1 стойка при температурах 200—250° в течение 200 часов; срок службы в атмосферных условиях — около года. Эмаль жаростойкая АЛ-70 отличается стойкостью при температурах до 350° в течение 350 — 400 часов, срок службы в атмосферных условиях около 18 месяцев.
Жаростойкие покрытия получаются при использовании лакокрасочных материалов на основе кремнийорганических и перхлорвиниловых смол. Примером может служить композиция, состоящая из жаростойкого лака ФГ-9, представляющего собой смесь кремнийорганической смолы Ф-9 и полуфабриката ФХ-02, растворенных в толуоле и смешанных с алюминиевой пудрой. Эта эмаль применяется для деталей, работающих при температуре до 500° в течение 300 часов.
Для окраски трубопроводов и агрегатов систем летательных аппаратов и двигателей применяются глифталевые эмали различных цветов. Для нанесения опознавательных знаков и окраски противопожарной аппаратуры применяется красная пентаф-талевая эмаль марки А67.
Нитроэмали представляют собой растворы нитроцеллюлозы в летучих органических растворителях, смешанные с наполнителями, пигментами, смолами и пластификаторами.
Для окраски изделий, не подвергающихся непосредственному действию атмосферы, широкое применение находят нитроэмали марки ДМ различных цветов.
Окраска шкал и стрелок приборов, указателей и надписей осуществляется композициями, содержащими наряду с обычными составляющими светящиеся вещества — люминофоры. При изготовлении светящейся краски на один литр лака добавляется 400 г цинкового, цинково-кадмиевого или щелочно-земельного светосостава.
Лаки служат главным образом для защиты лакокрасочных покрытий, а также для окончательной отделки окрашенной поверхности. Применяются масляные, смоляные и эфироцеллюлоз-ные лаки.
Масляные лаки представляют собой сплавы смол с олифами, растворенные в скипидаре. В зависимости от соотношения количества масла и смолы эти лаки подразделяются на жирные, полужирные и тощие. Жирные лаки по сравнению с тощими образуют более плотную и эластичную пленку.
Жирный масляный лак марки 17А применяется для сталей и алюминиевых сплавов. Для декоративной отделки приборов применяется лак марки ЛМ-33, так называемый лак-кристалл «Мороз».
Смоляные лаки представляют собой растворы смол в растворителях. Примером их могут служить бакелитовые лаки, представляющие собой растворы резольных смол в этиловом спирте.
Эфироцеллюлозные лаки являются растворами нитроцеллюлозы, ацетилцеллюлозы и других эфиров целлюлозы. Главное применение получили нитролаки.
Читать далее:
Защита пленками сложного химического состава
Статьи по теме:
pereosnastka.ru
Покрытия лакокрасочные долговечность - Справочник химика 21
Повышение защитных свойств и долговечности лакокрасочного покрытия автомобиля, гаражей и т.п. за счет предварительного фосфатирования поверхности окрашиваемого металла [c.51]ГОСТ 9.083-78 ЕСЗКС. Покрытия лакокрасочные. Ме-годы ускоренных испытаний па долговечность в жидких агрессивных средах. [c.84]
ЕСЗКС, Покрытия лакокрасочные. Методы ускоренных испытаний на долговечность в жидких агрессивных средах ЕСЗКС. Покрытия лакокрасочные. Методы испытаний на стойкость к статическому воздействию жидкостей [c.233]
Все это приводит к ухудшению защитных свойств покрытия. Между долговечностью нанесенных покрытий и степенью очистки поверхности защищаемого металла существует четко проявляющаяся зависимость. Чем выше степень очистки поверхности металла, тем дольше сохраняется защитное действие покрытия. Например, срок службы лакокрасочного покрытия на стали, очищенной с помощью пескоструйной обработки, в 3—6 раз больше, чем на стали, обработанной с помощью только одного крацевания. Причина этого состоит в том, что при крацевании не удаляются плотно прилегающие к поверхности слои ржавчины и окалины. [c.124]ГОСТ 9.083—78 ЕСЗКС. Покрытия лакокрасочные. Методы ускоренных испытаний на долговечность в жидких агрессивных средах ГОСТ 9.104—79 ЕСЗКС. Покрытия лакокрасочные. Группы условий эксплуатации [c.618]
Однако за простотой этого дела скрываются и некоторые не всем известные тонкости, знание которых позволяет сделать окрашивание делом еще более простым, более дешевым, а лакокрасочное покрытие — более долговечным. [c.8]
Лакокрасочные покрытия имеют значительные преимущества перед другими видами защитных покрытий более долговечны, их можно наносить на большие поверхности, что затруднительно, а иногда и невозможно для других видов покрытий. [c.7]
Эффективность применения лакокрасочных покрытий, как показывают данные рис. 9.1, целесообразна при условии долговечности эксплуатации не более 10 лет и скорости коррозии металла до 0,05 мм/год. Если требуется повышение долговечности или скорость коррозии металла составляет 0,5-1,0 мм/год, то следует применять комбинированные покрытия. Например, цинковые плюс лакокрасочное покрытие. Такое покрытие позволяет увеличить срок защиты до 30 лет. [c.282]
По сравнению с металлическими покрытиями, нанесенными лужением, никелированием, хромированием и т. д., лакокрасочные покрытия более долговечны, для их нанесения не требуется сложное оборудование, и они легче возобновляются. Поэтому такие покрытия широко применяются во всех отраслях промышленности, на транспорте, в строительстве и в быту. В машиностроении, например, лакокрасочные покрытия составляют более 60% всех защитных покрытий. [c.5]
По сравнению с металлическими покрытиями, нанесенными лужением, никелированием, хромированием и т. п., лакокрасочные покрытия более долговечны, для их нанесения не требует ся сложное оборудование и они легче возобновляются. Поэтому такие покрытия широко применяются во всех отраслях промыт- [c.3]
Адгезия. Если бы вдруг силы адгезии перестали действовать, произошла бы катастрофа. Разрушились бы кирпичные кладки, скрепленные цементом, потеряли прочность детали автомобилей и самолетов, развалилась мебель, отвалились клееные подошвы у сапог и ботинок и, конечно, отслоились бы все лакокрасочные покрытия. Хорошее качество покрытия, его долговечность зависят не только от условий, при которых покрытие получают, но также от того, насколько прочно оно связано с подложкой, Т е. от адгезии. [c.48]
При разрушении лакокрасочного покрытия нарушается эстетический вид изделия, однако бывают случаи, когда в результате абразивного разрушения покрытия ухудшается техническая характеристика изделия — происходит его коррозия, уменьшается прочность. Таким образом от эрозионной стойкости покрытия зависит долговечность изделия. [c.143]
Для анализа и учета необходимо, чтобы свойства продукции могли быть измерены (сравнимы), например ходимость шин, долговечность (срок службы) лакокрасочного покрытия, срок службы катализаторов и др. Такие показатели являются обобщенными, они отражают наиболее важный признак качества продукции как потребительной стоимости. Для повышения качества продукции изучают динамику изменения обобщенного показателя, например изменение во времени того или иного свойства качества. [c.103]
В настоящее время уже определились основные направления наиболее целесообразного использования полимеров в строительстве. Рулонные и плиточные материалы все шире применяются для покрытия полов (например, на основе поливинилхлорида), а на основе вспененных полимеров могут быть изготовлены новые виды тепло- и звукоизоляционных материалов для утепления зданий. Большое значение имеют синтетические лакокрасочные материалы, бумажно-слоистые пластики, пленки, моющиеся обои для отделки стен. Перспективно использование при крупнопанельном строительстве долговечных латексных кровельных покрытий, мастичных и профильных материалов на основе синтетических каучуков. Внедрение древесностружечных и древесноволокнистых плит позволяет изготовлять встроенную мебель и шкафы, перегородки, а также высококачественные дверные блоки. Полимерные материалы будут находить и в дальнейшем самое широкое применение при производстве различных санитарно-технических изделий и канализационных труб, в качестве связующего при производстве стеклопластика и других строительных материалов. [c.414]
Синтетические смолы в лакокрасочных покрытиях стали применяться в связи с развитием производства пластмасс, до этого применялись высыхающие растительные масла в виде олиф или такие природные смолистые вещества, как шеллак, канифоль и пр. С течением времени растительные масла и дефицитный шеллак стали частично вытесняться более дешевыми и высококачественными синтетическими смолами, хотя в связи с быстрым развитием производства лаков и красок растительные масла еще по-прежнему применяются для этих целей и даже в абсолютном выражении еще в больших количествах. В 1957 г. в СССР 80% лакокрасочных покрытий было получено на основе растительных масел, теперь потребление растительных масел для этих целей значительно ниже, но абсолютный расход еще велик. Лакокрасочные покрытия на синтетических лаковых смолах " не только дешевле, но и значительно более долговечны, чем на раститель- ных маслах, и быстрее высыхают. За 1959—1965 гг. производство синте- тических лаковых смол в нашей стране увеличилось в несколько раз. [c.141]
Надежность и долговечность антикоррозионного лакокрасочного покрытия определяются способностью материала, из которого оно изготовлено, длительно сохранять свои свойства в условиях эксплуатации защищаемого сооружения, правильным выбором системы покрытия и точным соблюдением технологии его нанесения. Покрытие должно выполняться из водоустойчивого материала, обладающего высокими адгезионными и диэлектрическими свойствами, эластичностью, устойчивостью к истиранию и динамическим воздействиям, коррозионной стойкостью, химической инертностью по отношению к металлу трубы и биостойкостью [16—18]. [c.21]
Роль лакокрасочной защиты возрастает в связи с тем, что постоянно повышается качество лакокрасочных материалов, возрастает долговечность защитных покрытий, снижается благодаря новым технологическим приемам нанесения стоимость окрасочных работ. [c.8]
ПУТИ ПОВЫШЕНИЯ НАДЕЖНОСТИ И ДОЛГОВЕЧНОСТИ ЛАКОКРАСОЧНЫХ ПОКРЫТИЙ [c.61]
Исследователями из Ростова-на-Дону установлено, что если для приготовления этого лака вместо масла взять инден-кумароновую смолу (коксохимический продукт) и отход масло-жирового производства, то образующийся лакокрасочный материал приобретает заметные преимущества он высыхает за,5 часов (вместо 24 часов для лака БТ-577), а покрытия из него проявляют более высокие защитные свойства и долговечность. [c.80]
В-третьих, и на это нам хотелось бы обратить особое внимание, долговечность лакокрасочного покрытия, сформированного на внешней поверхности трубы, значительно выше, чем на плоской поверхности традиционных прокатных профилей, так как усадочные явления в по- крытии при высыхании краски в данном случае приводят к обжатию трубы, к возрастанию адгезии, в то время как на плоской поверхности — к отслаиванию покрытия. [c.85]
Эти примеры показывают, каким могучим фактором повышения долговечности лакокрасочного покрытия, снижения трудоемкости его нанесения может быть разумное конструирование. [c.86]
Повышение долговечности при скорости коррозии металла 0,5-1,0 мм/год может быть достигнуто путем применения комбинированных металлизационных лакокрасочных покрытий. Папример, горячее цинкование плюс лакокрасочное покрытие, ручная металлизация плюс лакокрасочное покрытие. Использование этого вида защиты позволяет увеличить продолжительность защиты до 30 лет и более. [c.262]
Существуют противоречивые мнения по вопросу выбора толщины защитного лакокрасочного покрытия. По некоторым данным защитные свойства покрытия пропорциональны его толщине, по другим — повышение толщины не всегда приводит к увеличению его долговечности. Поэтому в каждом отдельном случае подбирается оптимальная толщина лакокрасочного покрытия. [c.284]
Лаки на основе каменноугольной смолы (или пека) обладают высокой водостойкостью и широко используются для защиты подводных сооружений и подземных трубопроводов. Недостаток битумных покрытий — их низкие атмосферостойкость и маслостойкость и относительно быстрое ухудшение физико-механических свойств при старении. Лакокрасочные материалы на основе эпоксидно-пековых смол лишены этих недостатков. Высокие защитные свойства и долговечность эпоксидно-пековых покрытий, особенно в условиях воздействия морской и пресной воды, можно объяснить тем, что при введении в эпоксидный состав битума не только повышается адгезия при соответствующем снижении внутренних напряжений, водонабухаемости, водопроницаемости, но за счет ряда соединений, входящих в состав каменноугольной смолы, обеспечивается дополнительное защитное действие. [c.78]
До 1930 г при производстве лакокрасочных материалов преимущественно использовались продукты переработки растительных масел и природные смолы, а также минеральные пигменты природного происхождения С тех пор лакокрасочная промышленность прошла большой путь развития Использование синтетических пленкообразующих веществ и пигментов дало возможность значительно расширить сырьевую базу, а также создать новые, более совершенные лакокрасочные материалы для получения долговечных атмосферо-, термо- и химически стойких покрытий с высокими декоративными характеристиками [c.8]
Таким образом, варьируя состав не только пленкообразующих компонентов лакокрасочной системы, но и состав различных добавок, можно существенно влиять на долговечность покрытия [c.53]
Акриловые лакокрасочные материалы обладают рядом ценных свойств, в том числе атмосфере- и светостойкостью, устойчивостью к воздействию воды и щелочей Они прекрасно сохраняют глянец и отличаются повышенной стойкостью к старению и долговечностью (срок службы покрытия 8—10 лет) [c.164]
Высокое качество кирпича и тщательность его укладки, а также плотность швов в конструкции — важные средства повышения долговечности трубы. Противокоррозионная защита внутренней поверхности ствола трубы обеспечивается лакокрасочными покрытиями и шпаклевками из полимерных материалов. Такая защита необходима при слабоагрессивных газах с температурой 80—150° С. При средней и сильной агрессивности газов с температурой менее 80° С пользуются полиизобутиленом, который при двухслойном покрытии и тщательном выполнении работ является эффективной противокоррозионной защитой. [c.372]
Использование малоизученных, непроверенных, некачественных или с превышенным сроком хранения лакокрасочных и вспомогательных материалов, отклонение от технологического регламента при проведении работ, отсутствие или проведение формального окончательного контроля готового покрытия приводит, как правило, к резкому снижению (иногда в 2...4 раза) долговечности покрытия. Различают следующие виды контроля [c.65]
Эффективными заменителями лакокрасочных покрытий, а в некоторых случаях и других видов покрытий являются металлизационные и металлизационно-лакокрасоч-ные (комбинированные) покрытия. Зарубежный и отечественный опыт промышленного применения таких покрытий показывает, что они не только во много раз долговечнее лакокрасочных, но и выгоднее их. Срок службы металлизационных и металлизационно-лакокрасочных покрытий во много раз выше срока службы лакокрасочных покрытий. Благодаря долговечности стоимость металлизационных покрытий, отнесенная к реальному сроку службы в 20 лет, оказывается в 2— 2,5 раза меньше стоимости лакокрасочных покрытий [19]. Результаты длительных испытаний комбинированных металлизационно-лакокрасочных покрытий показали, что срок службы их в 4—5 раз превышает срок службы лакокрасочных покрытий, наиболее стойких в сравниваемых условиях эксплуатации,. [c.266]
Анализ текущего состояния промысловых трубопроводов Южно-Ягунского и Ватьеганского месторождений, а также месторождений ТПП Урайнефтегаз показал, что для обеспечения долговечности трубопроводов системы ППД и нефтепроводов, кроме существующих противокоррозионных мероприятий (лакокрасочные и футеровочные покрытия и химические реагенты) следует использовать методы физического и физико-химического воздействия на свойства транспортируемых жидкостей. Целесообразность применения магнитного воздействия на свойства жидкостей подтверждается опытом его использования как в теплоэнергетике, так и в нефтедобыче. [c.157]
Таким образом, во влажных субтропиках применяемые гальванические покрытия не обеспечивают длительную защиту. Поэтому следует применять комбинированные покрытия (гальванические и лакокрасочные). Такие покрытия отличаются большей долговечностью по сравнению с гальваническими. При исследовании цинкового покрытия по Ст. 45 толщиной 60 мкм и комбинированных покрытий толщиной 30 мкм после 6 месяцев хорошие результаты были получены из девяти схем комб инированных покрытий на семи, в то время как все девять схем гальванических покрытий имели коррозионные поражения. [c.94]
Окрашивание фасадов памятников архитектуры, исторических зданий относится к отделочным работам и кроме декоративной выполняет защитную функцию. Материалы для окрашивания фасадов должны бьпь долговечными. Из современных лакокрасочных материалов для этой цели используют известковые, органосиликатные (ВН-30, ОСМ-5), кремнийорганические (КО-174) эмали, перхлорвиниловые фасадные краски (ХВ-161), фасадные краски на основе хлорсульфированного полиэтилена (ХП-71Ф), эмульсионные казеиновые краски. Вощюдиспер-сионные краски применять не рекомендуется в связи с их низкой атмо-сферостойкостью. Не следует применять также алкидно-акриловые краски с органическими пигментами, так как происходит быстрое выгорание пигментов, а покрытия притягивают пьшь и быстро загрязняются. [c.97]
Некоторые соединения свинца защиш ают металл от коррозии не в условиях агрессивных сред, а просто на воздухе. Эти соединения вводят в состав лакокрасочных покрытий. Свинцовые белила — это затертая на олифе основная углекислая соль свинца 2РЬСОз РЬ(ОН)г. Хорошая кроюш ая способность, прочность и долговечность образуемой пленки, устойчивость к действию воздуха и света — вот главные достоинства свинцовых белил. Но есть и антидостоинства высокая чувствительность к сероводороду, и главное — токсичность. Именно из-за нее свинцовые белила применяют сейчас только для наружной окраски судов и металлоконструкций, [c.263]
Учитывая, что коррозионная стойкость стали резко возрастает при введении в сплав уже незначительных количеств легирующих элементов, применение низколегированных сталей в качестве строительных и конструкционных материалов, эксплуатируемых в атмосферных условиях, является экономически весьма выгодным долговечность сооружения может быть при этом псвышена по крайней мере в 2—3 раза. При этом необходимо иметь в виду, что низколегированные стали ведут себя лучше, чем малоуглеродистые, и в условиях, когда на их поверхности нанесены лакокрасочные покрытия. [c.275]
chem21.info
ЛАКОКРАСОЧНЫЕ ПОКРЫТИЯ
Микробиологические повреждения лакокрасочных покрытий — одни из часто встречающихся случаев биоповреждений. Характерные признаки их проявления — серо-зеленые, бурые, темные и другие окрашенные пятна и налеты плесени мицелия грибов и бактериальной слизи на окрашенных поверхностях в местах с повышенной влажностью, растрескивание и отслаивание покрытий, образование бугров и отверстий и другие повреждения. Биоповреждения лакокрасочных покрытий обычно сочетаются с повреждающим воздействием на них других факторов внешней среды — атмосферной влаги с растворенными в ней агрессивными химическими веществами, воздействием солнечного света, повышенных температур и т. д. Эти процессы, относящиеся к процессам атмосферного старения полимерных материалов, могут предшествовать биоповреждениям, протекать одновременно с ними или же! после них. Сочетание процессов старения и биоповреждений затрудняет изучение их и разработку средств защиты и требует тесного сотрудничества биологов с химиками. Основными агентами микробиологических повреждений лакокрасочных покрытий являются плесневые грибы. Бактериальные поражения встречаются реже, они характеризуются появлением бесцветного или окрашенного слизистого налета. Под слоем краски встречаются микробиоценозы сложного состава, включающие бактерии и грибы. Среди микроорганизмов, повреждающих лакокрасочные покрытия, часто встречаются грибы родов Аsреrgillus, Penicillium, Fusarium, Trioderma, Alternaria, Серhalosporium, бактерии родов Pseudomonas, Flavobacterium. Повреждения покрытий грибами происходят либо за счет компонентов, входящих в состав покрытия, либо за счет веществ, загрязняющих поверхность покрытия, под действием метаболитов, выделяемых мицелием, который растет за счет загрязняющих покрытия веществ. Видовой состав грибов, повреждающих лакокрасочные покрытия, специфичен для различных почвенно-климатических зон. Он формируется из видов, составляющих сообщество, характерное для почв той или иной зоны. Один и тот же вид гриба может поражать покрытия различного состава. Биоповреждения лакокрасочных покрытий чаще встречаются в условиях влажного тропического и субтропического климата, а также в сооружениях и помещениях с повышенной влажностью и температурой (предприятия мясомолочной и консервной промышленности, животноводческие фермы, бассейны, бани и т. п.). Здесь они могут причинять наибольший ущерб. Однако и в районах с умеренным климатом также приходится сталкиваться с повреждениями покрытий грибами, правда, меньшей интенсивности, если это только не связано с нарушением условий эксплуатации (протечки, застои влажного воздуха и т. п.). В районах с сухим климатом такие повреждения встречаются очень редко. Биостойкость лакокрасочных покрытий зависит как от состава и свойств лакокрасочных материала (пленкообразователя и пигмента), так и частично от материала, на который наносится покрытие (подложки). Так, покрытия на древесине сохраняются лучше, чем на металле или силикатных строительных материалах. На черных металлах они бывают часто менее биостойкими, чем на цветных. Важную роль играет правильный подбор системы покрытия, включающей, например, грунт, антикоррозионное защитно-декоративное или противообрастающее покрытие. Во многих случаях за счет правильного подбора компонентов лакокрасочного материала, системы покрытия и учета свойств подложки удается обеспечить требуемую биостойкость, не прибегая к использованию специальных лакокрасочных материалов, в которые вводятся фунгициды. Пленкообразующие вещества. Решающее значение для биостойкости лакокрасочных покрытий имеет химический состав пленкообразующего полимера и физические свойства полученной из него пленки покрытия (набухаемость, твердость, пористость, гидрофоб-ность и др.). Синтетические пленкообразующие полимеры (термопластичные и термореактивные) менее склонны к повреждению микроорганизмами, чем природные. Грибостойкость этих покрытий уменьшается в следующем ряду: эпоксидные, полиуретановые, меламиноалкидные, кремнийорганические, пентафталевые. Повышению грибостойкости способствует увеличение скорости отверждения пленкообразующего вещества, уменьшение водопоглощеиия, шероховатости и пористости пленки. Гладкие блестящие ровные пленки более биостойки из-за того, что на них трудеее адсорбируются споры грибов и они меньше загрязняются. Среди природных пленкообразователей наиболее распространенными являются высыхающие масла — масла растительного происхождения (льняное, хлопковое, конопляное, подсолнечное, талловое и др.). Все они обладают сравнительно невысокой грибостойкостью. Для повышения биостойкости из растительных масел рафинированием удаляют воду, белковые продукты и другие примеси. Характерными признаками повреждения растительных масел микроорганизмами являются снижение их вязкости, повышение кислотности, ухудшение полимеризационной способности. Одним из биостойких пленкообразующих веществ лакокрасочных материалов природного происхождения является канифоль. Биостойкость канифоли связывают с присутствием в ее составе терпенов, обладающих фун-гицидными свойствами, и образованием кислых продуктов в пленке в процессе формирования защитного покрытия. Применяемые в качестве пленкообразователей битумы имеют недостаточную биостойкость. Для повышения биостойкости в состав битумных лаков и битумных защитных покрытий добавляют фенольные, малеиновые и другие синтетические смолы. Термопластичные синтетические смолы на основе хлорированного каучука, сополимеров стирола с бутадиеном и винилхлорида с винилацетатом, применяемые для производства быстросохнущих лаков и необрастающих лакокрасочных покрытий, характеризуются высокой биостойкостью. Широко распространенным полимерным связующим является поливинилацетатная дисперсия. Изготавливаемые на ее основе краски, покрытия, мастики, грунтовки и другие материалы негрибостой-ки. Непластифицированные дисперсии поражаются грибами сильнее, чем пластифицированные. Небиостойки не только покрытия из поливинилацетатных красок, но и сами жидкие краски, которые в процессе хранения поражаются грибами и бактериями, при этом снижается их вязкость, образуются газообразные продукты и т. д. Термореактивные синтетические смолы (глифталевые, пентафталевые, эпоксидные, силиконовые, мочевиноформальдегидные и др.), применяемые в составе лаков и эмалей горячего и холодного отверждения, обладают высокой биостойкостью, причем некоторые из них проявляют даже фунгицидные свойства. Покрытия из них отличаются высокой твердостью, гладкостью и малой проницаемостью, что способствует росту биостойкости. Водорастворимые пленкообразующие вещества, в качестве которых используют производные целлюлозы, белковые соединения (декстрин, камеди, желатин, альбумин, казеин и др.) повреждаются плесневыми грибами. Пониженная биостойкость водорастворимых пленкообразователей органического происхождения связана с их гигроскопичностью, способностью к набуханию. Во влажных условиях Нередко встречаются случаи повреждения казеиновых, декстриновых и других водоэмульсионных клеевых красок плесневыми грибами. В отличие от органических водорастворимых пленкообразователей неорганические пленкообразователи обладают высокой биостойкостью. Примером таких пленкообразователей является жидкое стекло. Пигменты. Вторым важным компонентом, от которого зависит биостойкость лакокрасочного покрытия, является пигмент. Пигменты придают краске нужный цвет и кроющую способность, регулируют вязкость, улучшают стойкость к солнечной радиации и водостойкость покрытия. Благодаря повышенной твердости частицы пигмента- механически затрудняют рост и развитие мицелия. Они могут оказывать также токсическое действие на плесневые грибы и другие микроорганизмы. Оксид цинка, оксид меди (I), метаборат бария и некоторые другие пигменты обладают фунгицидными свойствами и поэтому повышают биостойкость содержащих и лакокрасочных покрытий. Вместе с тем такие пигменты, как мел, желтый крон, двуокись титана, алюминиевая пудра, оксид хрома, сажа, сами не обладают биоцидными свойствами, однако масляные краски на их основе об ладают повышенной грибостойкостью. Меньшей грибостойкостью отличаются масляные краски с пигментами окислов сурьмы, свинца, литопоном. Ряд неорганических пигментов и наполнителей, например, тальк, графит, слюда-мусковит, снижают стойкость к повреждению грибами. Защита от биоповреждений лакокрасочных покрытий осуществляется прежде всего подбором систем покрытий с учетом условий эксплуатации и особенностей окрашиваемого объекта без применения специальных красок, содержащих биоциды. В условиях повышенной опасности микробиологических повреждений рекомендуется использовать антисептированные краски, т. е. краски, содержащие в составе биоциды. Защитно-декоративные и электроизоляционные лакокрасочные покрытия с добавками биоцидов рекомендованы для использования в некоторых видах радиоэлектронной аппаратуры, оптико-механических и других приборов, особенно поставляемых в страны с тропическим климатом. Антисептированные краски применяют для окраски помещений с повышенной влажностью и температурой (бассейны, бани, некоторые предприятия пищевой промышленности и др.). В качестве биоцидов для лакокрасочных покрытий общего назначения, предназначенных для наружного и внутреннего применения, могут применяться следующие соединения: 1) неорганические пигменты — оксид цинка, оксид меди (I), метаборат бария и др.; 2) органические фунгициды — 8-оксихинолят меди (окрашивает от желто-зеленого до коричневого цвета, может применяться в пищевой промышленности из-за низкой токсичности), салициланилид, бромтан, «-нитрофенол, тетра- и пентахлорфенол, фталан (трихлор-метилтиофталимид) и др.; 3) металлорганические фунгициды — оловоорганические (гексабутилдистанноксан, трибутилоловоакрилат), мышьякорганические (хлорфеноксарсин), ртутьорганические (фенилмеркуролеат и др.), последние из-за высокой летучести и токсичности для человека имеют ограниченное применение. Лакокрасочные покрытия для защиты от обрастания в водной среде. Основным способом защиты от обрастания является нанесение на защищаемую поверхность противообрастающего (необрастающего) лакокрасочного покрытия. Отличительной особенностью таких покрытий является то, что в них находятся добавки токсичных для гидробионтов-обрастателей веществ — биоцидов (альгицидов, моллюскицидов). Эти добавки постепенно вымываются морской водой из покрытия и, поражая гидробионтов-обрастателей в пограничном с корпусом судна слое, предохраняют его от обрастания. Применение необрастающих покрытий с биоцидами наряду с определенными достоинствами имеет и существенные недостатки, в частности, при скоплении большого числа морских судов в портах морская вода может загрязняться токсичными веществами, вымываемыми из противообрастающих покрытий. Поэтому в настоящее время к таким покрытиям предъявляются жесткие экологические требования. Прежде всего запрещено или резко ограничено применение наиболее токсичных и стойких к морской воде органических соединений, содержащих ртуть, свинец, хлор. Среди биоцидов в противообрастающих покрытиях наиболее широкое применение находит оксид меди (I). Этот препарат имеет довольно широкий спектр защитного действия, обладает умеренной растворимостью в морской воде, не представляет большой опасности как загрязнитель морской воды. Эффективными биоцидами являются органические соединения олова (гексабутилдистанноксан или бистрибутилоловооксид), мышьяка (бисдигидрофенарсазиноксид или n-оксид). Эти препараты применяются в современных необрастающих красках «контактного» действия, в которых в качестве пленкообразователя используют перхлорвиниловую смолу или сополимеры винилацетата с винилхлоридом. Контактные покрытия действуют по указанному механизму — находящиеся на поверхности покрытия биоциды растворяются в пограничном слое и, по мере их растворения, в результате диффузии из глубины покрытия на его поверхность перемещаются новые частицы биоцида. В процессе эксплуатации покрытия в результате истощения запасов биоцида в пограничный слой диффундирует биоцид с меньшими скоростями. В результате этого даже если биоцид полностью не израсходовался из глубинных слоев покрытия, в пограничный слой: он поступает в количестве, не достаточном для защиты от обрастания. Одним из путей преодоления этого недостатка является введение в состав покрытия добавок водорастворимых веществ, в частности канифоли. Постепенное растворение частиц канифоли создает микропоры в покрытии и облегчает диффузию биоцида на поверхность. Другим типом противообрастающих покрытий являются покрытия с применением водорастворимых полимерных пленкообразующих веществ, содержащих в макромолекуле полимера боковые функциональные группировки с биоцидными свойствами. В таком полимере совмещаются свойства связующего и биоцида. Примером такого пленкообразующего вещества является сополимер трибутилоловоакрилата и малеината. Биоцидные боковые группировки трибутилолова в результате гидролиза в морской воде отщепляются от макромолекулы полимера и обеспечивают защиту от обрастания. Оставшийся полимер приобретает повышенную растворимость в морской воде и переходит в раствор, обнажая новый слой, содержащий в макромолекуле биоцидные группировки. Таким образом обеспечивается равномерное растворение биоцида в пограничном слое морской воды по мере растворения макромолекул полимерного связующего. Срок службы такого покрытия зависит от толщины покрытия и скорости растворения. Современные покрытия растворимого типа наносятся слоем толщиной 200—300 мкм и при скорости растворения 8—10 мкм в месяц обеспечивают надежную защиту от обрастания в течение 2—3 лет. Достоинством покрытий с растворимым полимерным связующим является еще и то, что в процессе его растворения сглаживаются выступающие неровности на окрашенной поверхности корпуса судна и происходит, как говорят, «самополирование» покрытия. Поэтому покрытия такого типа называют самополирующимися или «сополимерными покрытиями самополирующимися» (СПС). К числу достоинств покрытий типа СПС относится то, что в результате «самополирования» поверхности корпуса судна снижается гидродинамическое сопротивление воды движению судна и наблюдается эффект, обратный вызываемому обрастанием, — снижение расхода топлива при сохранении постоянной скорости судна или повышение скорости при сохранении постоянного расхода топлива (мощности двигателя).
|
biocides.ru
Cвойства лакокрасочных покрытий автомобиля
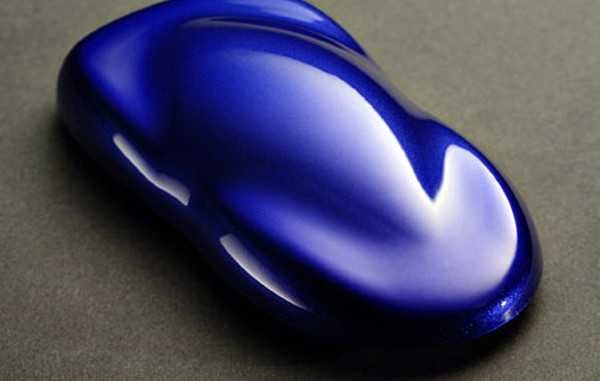
Приветствую Вас на блоге kuzov.info!
В этой статье подробно рассмотрим свойства лакокрасочных покрытий. Какие условия нанесения краски должны соблюдаться? Как должна быть подготовлена поверхность? Что такое адгезия ЛКП? Почему важна определённая толщина плёнки ЛКП? Что такое эластичность, прочность и абразивостойкость лакокрасочного покрытия? На все эти вопросы Вы найдёте ответы в этой статье. Итак, приступим.
Адгезия лакокрасочного покрытия
Лакокрасочное покрытие должно иметь хорошую адгезию, чтобы быть эффективным. Нет какой-то определённой теории, которая описывает свойства адгезии, но есть несколько механизмов, которые могут определить её. Когда речь заходит о лакокрасочном покрытии, адгезия обеспечивается, в основном, тремя механизмами: впитываемостью, химической и механической сцепляемостью.
Долговечность и эксплуатационные качества краски зависят от связанности её молекул и адгезии к подложке. Сцепка молекул краски между собой придаёт внутреннюю силу плёнки покрытия. Для такой характеристики существуют тесты на растяжимость плёнки. Для долговечности лакокрасочного покрытия имеет значимость и прочность молекулярной связи внутри плёнки и его адгезия к подложке.
Краска при нанесении должна быть достаточно жидкой, чтобы впитываться в каждую риску и неровность. Это создаст хорошую связь лакокрасочного покрытия с поверхностью.
Адгезия лакокрасочного покрытия представляет собой осуществление связи между, собственно, покрытием и поверхностью, на которое оно наносится. Если говорить по-простому, то это прилипание. Хорошая адгезия лакокрасочного покрытия к поверхности зависит от нескольких условий.
Важно правильно подготовить поверхность. Это осуществляется механическим или химическим путём. Перед покраской автомобиля поверхность матируется. Создаются мелкие риски, за которые краска и будет держаться.
Структура и толщина лакокрасочного покрытия
На адгезию влияет и толщина плёнки лакокрасочного покрытия. Смысл такой, что чем плёнка тоньше, тем она лучше держится за подложку. Таким образом, толщина покрытия не должна быть толще определённой нормы. Один толстый слой получается менее прочным, чем несколько тонких, формирующих ту же толщину.
Для подготовки поверхности к окрашиванию сначала металл покрывается грунтом. Далее наносится базовый слой краски, который придаёт декоративные свойства покрытию. Последним слоем наносится прозрачный лак, смешанный с отвердителем. Лак придаёт всему покрытию защитные свойства. Если поверхность окрашивается без лака, то сама краска является защитным слоем и имеет более толстый слой, чем базовой покрытие, закрываемое лаком.
Лак, являясь защитным покрытием, имеет самую большую толщину. Его толщина у разных производителей автомобилей варьируется и доходит до 100 микрон. 1 микрон = 1/1000 мм. Из данных на иллюстрации можно понять, что общая толщина лакокрасочного покрытия совсем не большая. Для защиты лакокрасочного покрытия необходимо правильно наносить воск и специальные защитные полироли и синтетические герметики.
Механические свойства лакокрасочного покрытия
Прочность плёнки определяет защитную функцию лакокрасочного покрытия. Это свойство зависит от молекулярной структуры плёнки. Также, влияние оказывает условия, при которых лакокрасочное покрытие отвердевало.
Твёрдость ЛКП
Твёрдость покрытия проявляется в способности противостоять деформациям и разрушению. Если сравнивать твёрдость лакокрасочного покрытия с твёрдостью других защитных покрытий, к примеру, керамического, то она значительно уступает, но всё же является достаточной для выполнения своих функций. На твёрдость плёнки влияет то, в какой степени она затвердела. На затвердевание, кроме окружающих условий и отвердителя, могут влиять пигменты краски, их количество и тип. Некоторые типы пигментов могут снижать скорость отвердевания и конечную твёрдость покрытия.
Со временем твёрдость увеличивается, так как испаряются остатки летучих веществ, а также протекают процессы старения внутри плёнки.
Нужно понимать, что твёрдость плёнки не является единственным показателем качественного лакокрасочного покрытия. Слишком твёрдое покрытие имеет плохую эластичность и может разрушаться при незначительных воздействиях на него.
Эластичность ЛКП
Эластичность покрытия помогает сохранять целостность и не отслаиваться при воздействии на него. Это же свойство помогает не разрушаться лакокрасочной плёнке при изгибе и деформации подложки (к примеру, при несильных ударах по пластиковому бамперу).
Эластические характеристики влияют как на прочность, так и на адгезию с подложкой. Эластичная плёнка будет при деформациях подложки повторять её профиль и оставаться целой.
Абразивостойкость ЛКП
Абразивостойкость определяет стойкость лакокрасочного покрытия к истиранию. Покрытия с высокой абразивостойкостью, как правило эластичные и прочные, но не слишком твёрдые. Они имеют, как правило, имеют хорошую адгезию к поверхности.
Водонепроницаемость ЛКП
Важным свойством лакокрасочного покрытия является низкая газо- и водопроницаемость. Во время эксплуатации автомобиля вода постоянно действует на кузов. Нужно знать, что не существует полностью водостойких лакокрасочных покрытий. В плёнке лакокрасочного покрытия есть микроскопические поры. Это связано со структурой самой плёнки. Между отдельными её элементами и молекулами есть промежутки. Также, на наличие пор влияют дефекты, возникающие при нанесении, формировании и сушке покрытия. Краска и лак должны быть правильно разведены перед нанесением. Распылённые капли должны хорошо растекаться по поверхности и заполнять все неровности подготовленной поверхности. Это снизит вероятность возникновения пор.
Печатать статью
Ещё интересные статьи:
kuzov.info