Большая Энциклопедия Нефти и Газа. Прессование литьевое
Процесс - литьевое прессование - Большая Энциклопедия Нефти и Газа, статья, страница 1
Процесс - литьевое прессование
Cтраница 1
Процесс литьевого прессования состоит в том, что пресс-материал поступает в загрузочную камеру предварительно замкнутой пресс-формы. Нагревание материала происходит за счет стенок загрузочной камеры. Материал, приобретший пластичность, выдавливается пуансоном в оформляющую часть пресс-формы по литниковым каналам. Метод литьевого прессования лишен недостатков, свойственных обычному прессованию, хотя и связан с повышенным расходом пресс-материала, а литьевые пресс-формы значительно сложнее и дороже пресс-форм для обычного прессования. [1]
Процесс литьевого прессования реактопластов осуществляется с высоким градиентом скорости и большим удельным давлением на материал. [2]
В процессе литьевого прессования после заполнения пресс-формы давление сохраняется некоторое время на постоянном уровне, затем после отверждения или охлаждения материала в литниковых каналах начинается постепенное снижение давления из-за усадки материала. Гидравлические сопротивления, которые имеют место при литьевом прессовании, включают в себя сопротивления в загрузочной камере ( при входе материала в литник), сопротивления в литниковых каналах, а также местные сопротивления в рабочей полости пресс-формы. [3]
Как показано на рис. IX-10, процесс литьевого прессования осуществляется следующим образом. Сначала прессформу закрывают и на ней устанавливают загрузочную камеру, в которую помещают таблетированный материал. [5]
Отличие процесса литья под давлением от процесса литьевого прессования состоит в том, что первый рассчитан на переработку термопластических материалов, а второй - термореактивных, но может быть использован и при переработке термопластов. Соответственно свойствам применяемых материалов, пресс-формы для литья под давлением непрерывно охлаждаются, пресс-формы для литьевого прессования, наоборот, только обогреваются. [6]
В обычном, или одноступенчатом, процессе литьевого прессования, рассмотренном выше, прессматериал на своем пути из загрузочной камеры в прессформу продавливается через узкий канал - литник - только один раз. В процессе продавлнвания через узкие отверстия прессматериал хорошо прогревается и перемешивается, поэтому в последние годы начинает развиваться метод двуступен-чатого процесса литьевого прессования, предусматривающий двукратное продавливание материала через узкие каналы. Это дает следующие преимущества: быстрый и равномерный нагрев, хорошее перемешивание прессматериала, регулирование влажности пресс-материала. [7]
Кроме компрессионного прессования на гидропрессах, может быть осуществлен процесс литьевого прессования в специальных формах. В этих формах тигель для размягчения полимера и формующая изделие часть составляют одно целое. В формах для пресс-литья тигель подходит к форме только в момент ее заполнения. [9]
Заусенец ( грат) на изделии при литьевом прессовании оказывается незначительным благодаря тому, что в процессе литьевого прессования матрица вначале плотно смыкается, после чего в ее загрузочную камеру всыпается материал. [10]
Хороший внешний вид изделия получается благодаря тому, что материал в процессе литьевого прессования лучше и равномернее прогревается. Вследствие этого ликвидируются бугорки и помутнения на поверхности изделий. Скорость прохождения нагретого материала через канал достигает 20 - 50 м / сек. [11]
В обычном, или одноступенчатом, процессе литьевого прессования, рассмотренном выше, прессматериал на своем пути из загрузочной камеры в прессформу продавливается через узкий канал - литник - только один раз. В процессе продавлнвания через узкие отверстия прессматериал хорошо прогревается и перемешивается, поэтому в последние годы начинает развиваться метод двуступен-чатого процесса литьевого прессования, предусматривающий двукратное продавливание материала через узкие каналы. Это дает следующие преимущества: быстрый и равномерный нагрев, хорошее перемешивание прессматериала, регулирование влажности пресс-материала. [12]
Процесс компрессионного прессования состоит в следующем. В рабочую полость нагретой прессформы загружается определенное количество пластмассы, которая под действием давления пуансона заполняет рабочую полость прессформы; после выдержки при 150 - 160 С в течение 0 5 - 2 мин на 1 мм толщины стенок детали прессформу раскрывают и готовая деталь выталкивается из прессформы. Прессформы обогреваются электричеством или паром. Процесс литьевого прессования осуществляется на обычных гидравлических прессах, в которых загрузочная камера прессформы находится вне формующей рабочей полости. В этой камере пресс-материал нагревается и в полужидком состоянии под давлением прессующего пуансона перетекает по литникам в рабочую полость прессформы. [13]
Процесс изготовления изделий литьем под давлением имеет принципиальное отличие: полимерный материал поступает в сомкнутую форму из загрузочной камеры через литниковые каналы. Излишек материала при таком способе изготовления в форму не поступает, а остается в загрузочной камере. Поэтому литье под давлением обеспечивает получение изделий без облоя; последующей механической обработки не требуется. Конструктивно машина для процесса литьевого прессования более сложна. [14]
Страницы: 1
www.ngpedia.ru
Литьевое прессование - Реферат | Litsoch.ru
СЕВЕРНЫЙ ГОСУДАРСТВЕННЫЙ МЕДИЦИНСКИЙ УНИВЕРСИТЕТ
МУ « 1 ГОРОДСКАЯ СТОМАТОЛОГИЧЕСКАЯ ПОЛИКЛИНИКА »
Г. АРХАНГЕЛЬСКА
Кафедра ортопедической стоматологии
Ортопедическое отделение
ИЗГОТОВЛЕНИЕ СЪЁМНЫХ ПРОТЕЗОВ
ЛИТЬЕВЫМ ПРЕССОВАНИЕМ
Докладчик:
Мёрзлая Е.Г.
Научный руководитель:
ассистент кафедры
ортопедической стоматологии,
кандидат медицинских наук
Лёвкин Владимир Андреевич.
Архангельск – 2002
Важность и актуальность улучшения технологии изготовления зубных протезов обусловлены значительной распространённостью патологии зубо-челюстной системы.
Ортопедическая стоматологическая заболеваемость (нуждаемость в протезировании) взрослого населения в различных регионах нашей страны
составляет около 60% (А.И. Рыбаков, Г.В. Базиян, 1973; Н.И. Колегов, 1973; Г.Н. Гадулин, 1973; и др.), на промышленных предприятиях от 32,3% (Р.И. Пеккер, 1966 и др.) до 80-85% (М.В. Бекметов, 1961; И.М. Флейшер, В.Н. Федчишин, 1982).
По данным сотрудников кафедры ортопедической стоматологии АГМИ (А.Л. Рожков с соавторами, 1983, В.А. Лёвкин Н.В. Скрипова, 1982, 1985 гг.) в ортопедическом лечении нуждается от 67,35-71,6% рабочих промышленных предприятий г. Архангельска.
Если учесть, что средний срок пользования съёмными зубными протезами определяется в 4 года, то фактическая динамическая нуждаемость окажется значительно большей.
Зубные протезы следует оценивать с биологической и технологической позиции. С биологической точки зрения – влияние на организм, с технологической – процесс изготовления.
Анализ состояния полости рта у больных, использующих съёмные протезы, базис которых изготовлен из акриловых пластмасс, позволяет утверждать, что указанные пластмассы нередко вызывают воспалительные изменения в слизистой оболочке. Его определяют в клинике как акриловый или «протезный стоматит». Причиной воспалительных изменений в большинстве случаев считают повторные выделения мономера из базисов протезов и его токсико-аллергическое местное и общее воздействие на организм. Поэтому с биологической позиции актуальной является разработка способов, позволяющих уменьшить содержание мономера в базисах протезов.
Методы формовки порошковых пластмасс в тестообразном состоянии в промышленности разделяют на 2 вида: компрессионное (КП) и литьевое прессование (ЛП).
КП – заключается в том, что формуемый материал помещают в форму и сжимают контр-штампом; ЛП – когда формуемый материал вводят в закрытую форму через литниковый канал; следовательно, есть основание считать термины «КП» и «ЛП» применительными и в зубопротезной технике.
Анализ технологии изготовления большинства съёмных протезов даёт основание утверждать, что КП является причиной изменения формы протеза, снижение прочности, образования пор и повышению содержания мономера. КП имеет существенные технологические недостатки, которые особенно отрицательно проявляются в процессе замены воска на пластмассу. При КП по окончании формирования на базисный материал, находящийся в форме, давление не оказывается. Поэтому не представляется возможным уплотнить пластмассу, чтобы уменьшить её усадку при полимеризации и исключить возникновение пор. При КП во время сближения штампа и контрштампа излишки пластмассы вытесняются между ними и препятствуют их соприкосновению. Образуется грат. Для изменения слоя грата в промышленности штампы и контрштампы изготовляют из твёрдых сплавов и применяют высокое давление. Гипс – материал не прочный и создать большое давление нельзя, т.к. неизбежно разрушение формы и увеличение слоя грата. Грат, образующийся при обратной гипсовке протезов, в кювете приводит к завышению прикуса и утолщению базиса протеза с оральной стороны, т.к. искусственные зубы, находящиеся в контрштампе, образно говоря, не возвращаются на прежний уровень, а остаются выше его на толщину грата. Таким образом, кламмеры тоже оказываются смещёнными, если они были при загипсовке переведены в контрштамп. По данным Седунова А.А. (1972 г.), при фиксации протезов во рту на коррекцию окклюзионной поверхности пластмассовых зубов в частичном протезе с 7 и более зубами врач затрачивает 20 минут. Во время коррекции фактически заново создаётся окклюзионное соотношение зубов и, следовательно, напрасно затрачивается значительная часть рабочего времени при постановке искусственных зубов и времени врача и больного. При проверке конструкции протеза, возникает вопрос, почему врач фактически заново формирует уровень жевательной поверхности зубов, после их установки техником и проверки конструкции протеза в клинике.
Критически оценивая метод формовки базисного материала путём КП, можно сказать, что в технологию КП заложена неизбежность изменения формы протеза.
В мире более 80% пластмасс перерабатывается только методом ЛП. Преимущество ЛП по сравнению с КП, в том, что излишки материала остаются в литниковой системе и получаются детали точного размера. Кроме того, форма не испытывает столь большого деформирующего воздействия, и через канал можно оказывать на пластмассу постоянное давление до её полного отверждения, что позволяет компенсировать усадку во время полимеризации.
Убеждённость, что метод КП в зуботехническом процессе – неудовлетворительный этап, являлась для многих стимулом к разработке метода ЛП. Детальные исследования в этом вопросе провёл В.Н. Копейкин. Им был создан оригинальный шприц-пресс, позволяющий формировать группу протезов и приходится сожалеть, что до сих пор не внедрён в производство. Сейчас признано, что литьевое формирование – это эффективный способ устранения усадки формуемого материала. Для формирования предлагаются специальные, так называемые, литьевые пластмассы. Созданный в СССР литьевой материал МСН-У находится в стадии промышленной разработки. Сделанный совершенно чёткие выводы о том, что изготовление базисов протезов методом ЛП позволяет получить более точную форму протеза и исключить применение в окклюзионном соотношении искусственных зубов, улучшить однородность и качество пластмассы и в значительной степени сократить расход материала.
ОБОРУДОВАНИЕ И МЕТОДИКА ИЗГОТОВЛЕНИЯ ПРОТЕЗОВ.
Э.Я. Варесом (1984-1986) предложен комплект шприц-кювет для литьевого прессования. Комплект состоит из одно-, двух- и четырёхместных кювет и одного прилагаемого к ним поршневого устройства. Двухместная шприц-кювета состоит из следующих деталей: 2 прямоугольные рамки с внутренними размерами 70×140 мм, с наклонными под 30° сторонами. Рамки сварены, их полосы шириной 25 мм и толщиной 4 мм. К нижней рамке с обеих сторон в торцовой части приварены вертикальный стойки , высотой 45 мм, диаметром 8 мм, с резьбой у свободного края. Камера представляет собой цилиндр высотой 70 мм с внутренними диаметрами 36 мм и толщиной стенок 2 мм. Прижимная пластина имеет на боковых сторонах 2 отверстия диаметром 9 мм. Поршневое устройство включает дугообразную рамку, винт и резиновый
поршень. Составные части кюветы удерживают в рабочем положении при помощи барашковых гаек.По общепринятой методике отливаются модели (лучше из супергипса). Нижняя рамка устанавливается на ровную (лучше резиновую) поверхность и избирается оптимальный вариант расположения моделей с восковыми формами протезов. Модели следует располагать как можно ближе друг к другу, чтобы литниковые каналы были короче и не имели изгибов. Восковая форма протезов должна отстоять от края рамки кюветы. Изыскивая оптимальный вариант расположения моделей, их следует подрезать так, что боковые стенки сходились к основанию. При подготовке гипса для нижней челюсти в кюветы следует брать гипс с песком в соотношении 3:2. добавление песка экономит расход гипса и упрочняет его на сжатие, но главное – облегчает выемку протеза из кюветы. Погружая модели в гипс, надо следить, чтобы искусственные зубы располагаясь не выше 12 мм от уровня кюветы.
По мере кристаллизации поверхность гипса обрабатывается, устраняются ретенционные пункты. После кристаллизации устанавливается литниковая система по принципу увеличения диаметра.
На восковую форму полного съёмного протеза верхней челюсти, как правило устанавливается вертикально в центре нёбной поверхности один основной литник диаметром 4,5 мм. Высота его должна быть на 10 мм выше верхнего конца кюветы. На восковую форму нижнего протеза или восковую форму протеза верхней челюсти, состоящую из 2-х, 3-х сёдел, следует установить вертикально входящий литник диаметром 4-4,5 мм и от него наклонно три ил четыре впускных литника диаметром 5 мм. Литники устанавливаются в тех местах восковой формы протезов, где толщина их не менее 2 мм. Выводные литники ставятся на наиболее выступающих частях воскового базиса. Создав подводящую систему литников, нижнюю рамку кюветы опускают в воду для изоляции поверхности гипса. Лучше применять для изоляции 3% раствор воска в бензине. Бензин испарится, а воск остаётся. После этого надевают верхнюю рамку и заполняют верхнюю часть кювет. Для заполнения верхней части подготавливают 1/3 объёма резиновой чашки прочного гипса и наносят его на поверхность восковой формы и литников. При этом жёсткой кисточкой удаляют поры воздуха около шеек искусственных зубов. Получается своеобразная рубашка. Не ожидая кристаллизации, замешивают гипс с песком и заполняют остальную часть кювет на 1 мм выше края. Без промедления устанавливают загрузочную камеру и укрепляют к кювете. После кристаллизации гипса загрузочную камеру с прижимной пластиной осторожно снимают и обрабатывают поверхность гипса, входящую в загрузочную камеру. Обработав кювету, опускают в кипящую воду для выплавления воска, тщательно промывают каналы литников, проверяют фиксацию зубов и наносят изоляционный слой изокола. Слой изокола следует наносить 2 раза. Первый раз наносят тотчас же после выплавления воска, а спустя 7 минут – второй слой. Далее одним из способов определяют объём полостей и подготавливают загрузочную камеру. Подготовка заключается в создании изоляционного слоя из полиэтиленовой пленки перекрытия входа в литниковый канал (для избежания преждевременного поступления пластмассы в литники). Лучшим материалом является фольга. После установки изоляционной пластинки кювету с загрузочной камерой помещают в холодильник на 20-30 минут. Охлаждённый порошок и мономер в определённом объёме помещают в охлаждённый стакан и перемешивают в течение 40-60 сек.
Охлаждение кюветы, порошка, мономера препятствует ранней полимеризации.
После того, как пластмасса приобретает консистенцию сметаны, стаканчик помещают в чашку Петри с водой и покрывают вторым стаканчиком (тем самым создают водный затвор для предупреждения испарения мономера) и помещают в холодильник. Спустя 2 мин пластмассу выливают в загрузочную камеру. Края изоляционного полиэтиленового цилиндра загибают внутрь и осторожно вставляют поршень. В загрузочной камере продолжается набухание пластмассы. В течение 1,5 минуты из пластмассы вверх перемещаются крупные пузырьки воздуха. По истечении указанного времени над поршнем устанавливают поршневое устройство и приступают к формированию. Быстрым вращением винта поршень погружают в камеру. Ограничительная мембрана лопается и пластмасса поступает в полости кюветы. О заполнении судят по появлению пластмассы в выводных литниках.
Далее следует этап уплотнения формуемой пластмассы путём периодического подкручивания винта. При этом происходит сжатие резинового поршня, что создаёт относительную непрерывность создаваемого давления. Уплотнение производится с целью выжима мономера, удаления воздушных пор и спрессования частиц порошка. Спустя 8-10 мин после уплотнения делают ещё ½ оборота для деформации резинового поршня с целью создания резервного давления и приступают к полимеризации.
Полимеризация пластмассы производится в 2 этапа:1) направленную при температуре до 100° С, а затем 2) общую в сушильном шкафу при температуре 120-130°С. Для проведения направленной полимеризации шприц-кювету нижней частью помещают в горячий песок, находящийся в низкооборотном лотке на нагревательном приборе с температурой подогрева до 100°С. Гипс в кювете прогревается снизу постепенно и пластмасса, находившаяся в загрузочной камере под давлением, продолжает поступать в кювету, компенсируя полимеризационную усадку. Экспозиция кюветы в песке 15-20 мин. А после этого проводится полимеризация в сухожаровом шкафу в течение 1,5 часов. Охлаждение кюветы необходимо проводить при комнатной температуре. Последующие клинико-лабораторные этапы не отличаются от традиционных.
В настоящее время, несмотря на то, что оборудование промышленностью страны ещё не выпускается, ведётся внедрение данной технологии изготовления протезов в практику ортопедической стоматологии.
В Архангельске и в области такие протезы пока не делаются. Сотрудники кафедры ортопедической стоматологии СГМУ постановили своей целью апробировать эту технологию и применять участие по внедрению её в практику ортопедических отделений г. Архангельска.
Для изготовления съёмных протезов нами использовалась 2-х местная кювета, выполненная по чертежам ассистента кафедры ортопедической стоматологии СГМУ к.м.н. Лёвкина В.А. с применением базисных пластмасс горячего отверждения – «Этакрила» и «Фторакса».
Технология апробирована на кафедре ортопедической стоматологии СГМУ и внедрена в МУ «1 городская стоматологическая поликлиника» г. Архангельска.
Нами на студенческом приеме оказана ортопедическая помощь 39 пациентам, преимущественно с полным отсутствием зубов на обеих челюстях.
В настоящее время технология литьевого прессования используется в сочетании с объёмным моделированием при изготовлении полных съёмных пластиночных протезов.
Анализ технологии изготовления съёмных протезов литьевым прессованием даёт основание утверждать следующее:
1) не образуется грат, что сокращает время выполнения клинического этапа припасовки и наложения протезов с пришлифовкой искусственных зубов;
2) повышается прочность протезов;
3) исключается образование пор;
4) значительно сокращается содержание свободного мономера;
5) в меньшей степени проявляется выраженная реактивность тканей протезного ложа.
www.litsoch.ru
Литьевое прессование пластмасс - это... Что такое Литьевое прессование пластмасс?
Литьевое прессование пластмасс трансферное прессование, метод изготовления изделий различной формы из реактопластов (См. Реактопласты), при котором материал размягчается (пластицируется) в литьевом цилиндре (тигле), откуда нагнетается в пресс-форму (рис.), где, отверждаясь, принимает конфигурацию и размеры изделия. В некоторых случаях в тигель может загружаться пластицированный материал из экструдера. Л. п. п. осуществляют на универсальных прессах с одним рабочим плунжером для замыкания пресс-формы и нагнетания в неё материала или на специализированных прессах, у которых замыкание пресс-формы осуществляется одним плунжером, а нагнетание материала — другим. Л. п. п. применяют для формования изделий сложной конфигурации, повышенной точности, с тонкой арматурой и глубокими отверстиями, с большой разницей в толщине стенок. По технологии и оборудованию Л. п. п. занимает промежуточное место между прессованием полимерных материалов (См. Прессование полимерных материалов) и литьём под давлением (См. Литьё под давлением) полимерных материалов.
Лит.: Завгородний В. К., Механизация и автоматизация переработки пластических масс, 3 изд., М., 1970.
В. К. Завгородний.
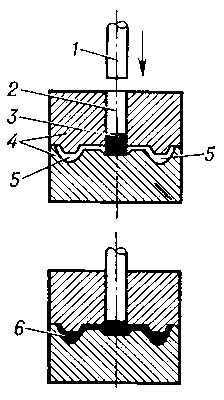
Схема литьевого прессования пластмасс: 1 — плунжер; 2 — литьевой цилиндр; 3 — нагретый материал; 4 — замкнутая форма; 5 — оформляющая полость формы; 6 — изделие.
Большая советская энциклопедия. — М.: Советская энциклопедия. 1969—1978.
- Литургия (христ. богослужение)
- Литьё
Смотреть что такое "Литьевое прессование пластмасс" в других словарях:
Прессование полимерных материалов — компрессионное, метод изготовления изделий из пластических масс и резиновых смесей в Пресс формах, установленных на Прессе (чаще всего гидравлическом). В зависимости от температуры процесса П. и. м. подразделяют на высокотемпературное… … Большая советская энциклопедия
ЛИТЬЕ — ЛИТЬЕ, изготовление предметов посредством литья расплавленного металла в форму с последующим охлаждением и затвердеванием. Формы для отливки часто делают из песка или глины. Имеется много специальных разновидностей этого процесса, таких как… … Научно-технический энциклопедический словарь
ПЛАСТМАССЫ — (пластические массы, пластики). Большой класс полимерных органических легко формуемых материалов, из которых можно изготавливать легкие, жесткие, прочные, коррозионностойкие изделия. Эти вещества состоят в основном из углерода (C), водорода (H),… … Энциклопедия Кольера
Пластик — (Plastic) История пластмасс, основная классификация Производство пластмасс, система маркировки, АБС пластик Содержание Содержание Раздел 1. История . Раздел 2. Классификация. Подраздел 1. Термопласты. Подраздел 2. Реактопласты. Подраздел 3.… … Энциклопедия инвестора
ПОЛИМЕРНЫХ МАТЕРИАЛОВ ПЕРЕРАБОТКА — комплекс технол. операций и приемов, с помощью к рых из полимерных материалов изготовляют (формуют) изделия с заданными формой, размерами и св вами. Ниже рассматриваются осн. вопросы переработки разл. полимерных материалов (П. м.), в т. ч.… … Химическая энциклопедия
dic.academic.ru
Литьевое прессование пластмасс
трансферное прессование, метод изготовления изделий различной формы из реактопластов (См. Реактопласты), при котором материал размягчается (пластицируется) в литьевом цилиндре (тигле), откуда нагнетается в пресс-форму (рис.), где, отверждаясь, принимает конфигурацию и размеры изделия. В некоторых случаях в тигель может загружаться пластицированный материал из экструдера. Л. п. п. осуществляют на универсальных прессах с одним рабочим плунжером для замыкания пресс-формы и нагнетания в неё материала или на специализированных прессах, у которых замыкание пресс-формы осуществляется одним плунжером, а нагнетание материала — другим.
Л. п. п. применяют для формования изделий сложной конфигурации, повышенной точности, с тонкой арматурой и глубокими отверстиями, с большой разницей в толщине стенок. По технологии и оборудованию Л. п. п. занимает промежуточное место между прессованием полимерных материалов (См. Прессование полимерных материалов) и литьём под давлением (См. Литьё под давлением) полимерных материалов.
Лит.: Завгородний В. К., Механизация и автоматизация переработки пластических масс, 3 изд., М., 1970.
В. К. Завгородний.
Схема литьевого прессования пластмасс: 1 — плунжер; 2 — литьевой цилиндр; 3 — нагретый материал; 4 — замкнутая форма; 5 — оформляющая полость формы; 6 — изделие.
Поделитесь на страничкеslovar.wikireading.ru
Литьевое прессование
СЕВЕРНЫЙ ГОСУДАРСТВЕННЫЙ МЕДИЦИНСКИЙ УНИВЕРСИТЕТ
МУ « 1 ГОРОДСКАЯ СТОМАТОЛОГИЧЕСКАЯ ПОЛИКЛИНИКА »
Г. АРХАНГЕЛЬСКА
Кафедра ортопедической стоматологии
Ортопедическое отделение
ИЗГОТОВЛЕНИЕ СЪЁМНЫХ ПРОТЕЗОВ
ЛИТЬЕВЫМ ПРЕССОВАНИЕМ
Докладчик:
Мёрзлая Е.Г.
Научный руководитель:
ассистент кафедры
ортопедической стоматологии,
кандидат медицинских наук
Лёвкин Владимир Андреевич.
Архангельск – 2002
Важность и актуальность улучшения технологии изготовления зубных протезов обусловлены значительной распространённостью патологии зубо-челюстной системы.
Ортопедическая стоматологическая заболеваемость (нуждаемость в протезировании) взрослого населения в различных регионах нашей страны
составляет около 60% (А.И. Рыбаков, Г.В. Базиян, 1973; Н.И. Колегов, 1973; Г.Н. Гадулин, 1973; и др.), на промышленных предприятиях от 32,3% (Р.И. Пеккер, 1966 и др.) до 80-85% (М.В. Бекметов, 1961; И.М. Флейшер, В.Н. Федчишин, 1982).
По данным сотрудников кафедры ортопедической стоматологии АГМИ (А.Л. Рожков с соавторами, 1983, В.А. Лёвкин Н.В. Скрипова, 1982, 1985 гг.) в ортопедическом лечении нуждается от 67,35-71,6% рабочих промышленных предприятий г. Архангельска.
Если учесть, что средний срок пользования съёмными зубными протезами определяется в 4 года, то фактическая динамическая нуждаемость окажется значительно большей.
Зубные протезы следует оценивать с биологической и технологической позиции. С биологической точки зрения – влияние на организм, с технологической – процесс изготовления.
Анализ состояния полости рта у больных, использующих съёмные протезы, базис которых изготовлен из акриловых пластмасс, позволяет утверждать, что указанные пластмассы нередко вызывают воспалительные изменения в слизистой оболочке. Его определяют в клинике как акриловый или «протезный стоматит». Причиной воспалительных изменений в большинстве случаев считают повторные выделения мономера из базисов протезов и его токсико-аллергическое местное и общее воздействие на организм. Поэтому с биологической позиции актуальной является разработка способов, позволяющих уменьшить содержание мономера в базисах протезов.
Методы формовки порошковых пластмасс в тестообразном состоянии в промышленности разделяют на 2 вида: компрессионное (КП) и литьевое прессование (ЛП).
КП – заключается в том, что формуемый материал помещают в форму и сжимают контр-штампом; ЛП – когда формуемый материал вводят в закрытую форму через литниковый канал; следовательно, есть основание считать термины «КП» и «ЛП» применительными и в зубопротезной технике.
Анализ технологии изготовления большинства съёмных протезов даёт основание утверждать, что КП является причиной изменения формы протеза, снижение прочности, образования пор и повышению содержания мономера. КП имеет существенные технологические недостатки, которые особенно отрицательно проявляются в процессе замены воска на пластмассу. При КП по окончании формирования на базисный материал, находящийся в форме, давление не оказывается. Поэтому не представляется возможным уплотнить пластмассу, чтобы уменьшить её усадку при полимеризации и исключить возникновение пор. При КП во время сближения штампа и контрштампа излишки пластмассы вытесняются между ними и препятствуют их соприкосновению. Образуется грат. Для изменения слоя грата в промышленности штампы и контрштампы изготовляют из твёрдых сплавов и применяют высокое давление. Гипс – материал не прочный и создать большое давление нельзя, т.к. неизбежно разрушение формы и увеличение слоя грата. Грат, образующийся при обратной гипсовке протезов, в кювете приводит к завышению прикуса и утолщению базиса протеза с оральной стороны, т.к. искусственные зубы, находящиеся в контрштампе, образно говоря, не возвращаются на прежний уровень, а остаются выше его на толщину грата. Таким образом, кламмеры тоже оказываются смещёнными, если они были при загипсовке переведены в контрштамп. По данным Седунова А.А. (1972 г.), при фиксации протезов во рту на коррекцию окклюзионной поверхности пластмассовых зубов в частичном протезе с 7 и более зубами врач затрачивает 20 минут. Во время коррекции фактически заново создаётся окклюзионное соотношение зубов и, следовательно, напрасно затрачивается значительная часть рабочего времени при постановке искусственных зубов и времени врача и больного. При проверке конструкции протеза, возникает вопрос, почему врач фактически заново формирует уровень жевательной поверхности зубов, после их установки техником и проверки конструкции протеза в клинике.
Критически оценивая метод формовки базисного материала путём КП, можно сказать, что в технологию КП заложена неизбежность изменения формы протеза.
В мире более 80% пластмасс перерабатывается только методом ЛП. Преимущество ЛП по сравнению с КП, в том, что излишки материала остаются в литниковой системе и получаются детали точного размера. Кроме того, форма не испытывает столь большого деформирующего воздействия, и через канал можно оказывать на пластмассу постоянное давление до её полного отверждения, что позволяет компенсировать усадку во время полимеризации.
Убеждённость, что метод КП в зуботехническом процессе – неудовлетворительный этап, являлась для многих стимулом к разработке метода ЛП. Детальные исследования в этом вопросе провёл В.Н. Копейкин. Им был создан оригинальный шприц-пресс, позволяющий формировать группу протезов и приходится сожалеть, что до сих пор не внедрён в производство. Сейчас признано, что литьевое формирование – это эффективный способ устранения усадки формуемого материала. Для формирования предлагаются специальные, так называемые, литьевые пластмассы. Созданный в СССР литьевой материал МСН-У находится в стадии промышленной разработки. Сделанный совершенно чёткие выводы о том, что изготовление базисов протезов методом ЛП позволяет получить более точную форму протеза и исключить применение в окклюзионном соотношении искусственных зубов, улучшить однородность и качество пластмассы и в значительной степени сократить расход материала.
ОБОРУДОВАНИЕ И МЕТОДИКА ИЗГОТОВЛЕНИЯ ПРОТЕЗОВ.
Э.Я. Варесом (1984-1986) предложен комплект шприц-кювет для литьевого прессования. Комплект состоит из одно-, двух- и четырёхместных кювет и одного прилагаемого к ним поршневого устройства. Двухместная шприц-кювета состоит из следующих деталей: 2 прямоугольные рамки с внутренними размерами 70×140 мм, с наклонными под 30° сторонами. Рамки сварены, их полосы шириной 25 мм и толщиной 4 мм. К нижней рамке с обеих сторон в торцовой части приварены вертикальный стойки , высотой 45 мм, диаметром 8 мм, с резьбой у свободного края. Камера представляет собой цилиндр высотой 70 мм с внутренними диаметрами 36 мм и толщиной стенок 2 мм. Прижимная пластина имеет на боковых сторонах 2 отверстия диаметром 9 мм. Поршневое устройство включает дугообразную рамку, винт и резиновый поршень. Составные части кюветы удерживают в рабочем положении при помощи барашковых гаек.
По общепринятой методике отливаются модели (лучше из супергипса). Нижняя рамка устанавливается на ровную (лучше резиновую) поверхность и избирается оптимальный вариант расположения моделей с восковыми формами протезов. Модели следует располагать как можно ближе друг к другу, чтобы литниковые каналы были короче и не имели изгибов. Восковая форма протезов должна отстоять от края рамки кюветы. Изыскивая оптимальный вариант расположения моделей, их следует подрезать так, что боковые стенки сходились к основанию. При подготовке гипса для нижней челюсти в кюветы следует брать гипс с песком в соотношении 3:2. добавление песка экономит расход гипса и упрочняет его на сжатие, но главное – облегчает выемку протеза из кюветы. Погружая модели в гипс, надо следить, чтобы искусственные зубы располагаясь не выше 12 мм от уровня кюветы.
По мере кристаллизации поверхность гипса обрабатывается, устраняются ретенционные пункты. После кристаллизации устанавливается литниковая система по принципу увеличения диаметра.
На восковую форму полного съёмного протеза верхней челюсти, как правило устанавливается вертикально в центре нёбной поверхности один основной литник диаметром 4,5 мм. Высота его должна быть на 10 мм выше верхнего конца кюветы. На восковую форму нижнего протеза или восковую форму протеза верхней челюсти, состоящую из 2-х, 3-х сёдел, следует установить вертикально входящий литник диаметром 4-4,5 мм и от него наклонно три ил четыре впускных литника диаметром 5 мм. Литники устанавливаются в тех местах восковой формы протезов, где толщина их не менее 2 мм. Выводные литники ставятся на наиболее выступающих частях воскового базиса. Создав подводящую систему литников, нижнюю рамку кюветы опускают в воду для изоляции поверхности гипса. Лучше применять для изоляции 3% раствор воска в бензине. Бензин испарится, а воск остаётся. После этого надевают верхнюю рамку и заполняют верхнюю часть кювет. Для заполнения верхней части подготавливают 1/3 объёма резиновой чашки прочного гипса и наносят его на поверхность восковой формы и литников. При этом жёсткой кисточкой удаляют поры воздуха около шеек искусственных зубов. Получается своеобразная рубашка. Не ожидая кристаллизации, замешивают гипс с песком и заполняют остальную часть кювет на 1 мм выше края. Без промедления устанавливают загрузочную камеру и укрепляют к кювете. После кристаллизации гипса загрузочную камеру с прижимной пластиной осторожно снимают и обрабатывают поверхность гипса, входящую в загрузочную камеру. Обработав кювету, опускают в кипящую воду для выплавления воска, тщательно промывают каналы литников, проверяют фиксацию зубов и наносят изоляционный слой изокола. Слой изокола следует наносить 2 раза. Первый раз наносят тотчас же после выплавления воска, а спустя 7 минут – второй слой. Далее одним из способов определяют объём полостей и подготавливают загрузочную камеру. Подготовка заключается в создании изоляционного слоя из полиэтиленовой пленки перекрытия входа в литниковый канал (для избежания преждевременного поступления пластмассы в литники). Лучшим материалом является фольга. После установки изоляционной пластинки кювету с загрузочной камерой помещают в холодильник на 20-30 минут. Охлаждённый порошок и мономер в определённом объёме помещают в охлаждённый стакан и перемешивают в течение 40-60 сек.
mirznanii.com
Прессование литьевое трансферное - Справочник химика 21
Существуют две разновидности этого метода трансферное и инжекционное литьевое прессование. Схема трансферного литьевого прессования показана на рис. 1. Оно производится на прессе с верхним гидроцилиндром. Усилие пресса передается на пуансон, который продавливает прессматериал через литниковые каналы в форму. [c.106]Разновидностью литьевого прессования является трансферное прессование. Его отличие состоит лишь в конструктивном оформлении оборудования и пресс-форм (рис. 2, в). Трансферное прессование производят как на специальных прессах с верхним и нижним давлением, так и на обычных с использованием усилия выталкивателя для литья. При помощи гидравлического цилиндра верхнего давления производится смыкание пресс-формы, а затем под действием нижнего гидравлического цилиндра пресс-материал, заранее уложенный в загрузочную камеру, заполняет оформляющую полость пресс-формы. После отверждения материала пресс-форма размыкается, и изделие выталкивается из матрицы пресс-формы толкателями. Как и при литьевом прессовании, используются пресс-материалы с коротковолокнистым наполнителем, обладающие высокой текучестью. Метод позволяет изготавливать изделия сложной формы. [c.19]
В соответствии с ГОСТ 8200-87 изготовляют гидравлические прессы шести типоразмеров с номинальным усилием от 400 до 4000 кН. Для каждого из этих типоразмеров ГОСТом регламентируются следующие параметры ход ползуна, наибольщее расстояние между столом и ползуном, размеры стола, скорости холостого и рабочего ходов ползуна, номинальное усилие, ход выталкивателя, скорость рабочего хода выталкивателя. Прч этом прессы могут быть двух исполнений 1 — с одной ступенью рабочей скорости ползуна и выталкивателя 2 — с двумя ступенями рабочих скоростей ползуна для режима компрессионного (прямого) прессования и выталкивателя для режима трансферного (литьевого) прессования. [c.373]Литьевое (трансферное) прессование заключается в том, что прессматериал нагревается до вязкотекучего состояния в загрузочной камере (тигле) и впрыскивается через узкое сопло в оформляющие гнезда, в которых он отверждается при нагревании. [c.55]
Второй, более производительный метод переработки реактопластов известен как трансферное (литьевое) прессование, или пресс-литье, иногда называемое плунжерным прессованием. [c.40]
Прессование пластмассовых изделий осуществляется при воздействии давления на материал, помещенный в нагретую пресс-форму. Основными разновидностями прессования являются прямое (компрессионное) и литьевое (трансферное). При прямом прессовании материал загружается в нагретую до заданной температуры пресс-форму (рис. 8.5), под действием развиваемого прессом давления растекается по полости формы, а затем затвердевает, приобретая конфигурацию изделия. Процесс прямого прессования ускоряется, а качество изделий улучшается при предварительном подогреве материала. По оборудованию и технологии литьевое прессование занимает промежуточное место между прессованием и литьем поД давле- [c.110]
Процесс прессования, при котором материал загружается непосредственно в полость пресс-формы, называется прямым или компрессионным прессованием. В том случае, когда материал загружается не в полость пресс-формы, а в специальную загрузочную камеру, в которой он нагревается, а затем в вязкотекучем состоянии выдавливается в оформляющую полость формы, процесс называется литьевым (трансферным) прессованием. [c.83]
Литьевое прессование на трансферных прессах (трансферное прессование) [c.11]
Прессование осуществляют двумя основными способами прямым (компрессионным) и литьевым (трансферным) —рис. 3.1. При первом способе (см. рис. 3.1, а) давление воздействует непосредственно на материал в полости пресс-формы, во втором (см. рис. 3.1, б) — в загрузочной камере, из которой по литниковым каналам расплав выдавливают в полость пресс-формы. Прямому прессованию отдают предпочтение при изготовлении несложных изделий, при переработке высоконаполненных материалов, в производстве изделий максимально чистого цвета (особенно белого) и изделий массой более 1 кг. Литьевое прессование рационально применять для изготовления армированных изделий сложной конфигурации, с тонкими стенками, при повышенных требованиях к точности раз.меров. [c.58]
Способу формования литьем под давлением посвящена гл. 12. Теперь рассмотрим трансферное прессование, получившее широкое распространение в производстве массовых изделий небольших размеров, Суть его заключается в том, что на одной из частей формы, например на верхней, смонтирован небольшой по высоте литьевой цилиндр (напорная камера), плунжер которого жестко прикреплен к верхней нагревательной плите (рис. 15.1, б). Резиновая смесь закладывается в литьевой цилиндр и после смыкания полуформ вы- [c.319]
Гидравлические прессы классифицируют различным образом по технологическим признакам — прессы для прямого (компрессионного) и литьевого (трансферного) прессования [c.49]
Литьевое прессование реактопластов, называемое также пресс-Литьем или трансферным прессованием, применяется при получении изделий с тонкой арматурой, которая может деформироваться при обычном компрессионном прессовании, и в других случаях, когда требуется высокая текучесть пресс-материала. Характерным отличием литьевого прессования является то, что загрузочная камера пресс-формы соединена с оформляющей полостью узким литниковым каналом. Пресс-форма замыкается перед загрузкой и расплав, образовавшийся в загрузочной камере, выдавливается через литниковый канал в оформляющую полость. [c.295]
Дальнейшим логическим развитием метода прямого прессования является метод литьевого (трансферного) прессования, при котором доза реактопласта переходит в вязкотекучее состояние в камере перед формой, затем расплав подается в форму, где происходят собственно прессование под давлением и отверждение. Схема процесса показана на рис. 10.2. [c.309]
Гидравлические прессы классифицируются по технологически признакам — прессы для прямого (компрессионного) и литьевого (трансферного) прессования по конструкции станины — колонные, рамные по степени автоматизации— прессы с ручным, полуавтоматическим и автоматическим управлением по направлению действующего усилия — вертикальные, горизонтальные, угловые по расположению рабочего цилиндра—прессы с верхним и нижним рабочими цилиндрами по числу позиций формования — одно- и многопозиционные. [c.316]
Способы прессования, применяемые в промышленности, отличаются способами нагрева материала, его ввода в форму и последующего формования прямое (компрессионное), литьевое (трансферное) и непрерывное профильное (штранг-прессование). [c.672]
Прессование —один из распространенных методов получения изделий из полимеров, в первую очередь из термореактивных материалов. Существуют следующие разновидности прессования компрессионное (прямое), литьевое (трансферное), роторное, непрерывное профильное, или штранг-прессование. Основным видам прессования является компрессионное. [c.251]
Литьевое прессование термореактивных материалов, называемое также трансферным, применяют в тех случаях, когда нельзя или нецелесообразно использовать прямое (компрессионное) прес-сование. Например, его применяют для получения изделий с тон-кой арматурой, которая может деформироваться при прямом прессовании, или же для изделий сложного профиля, требующих высокой текучести. Характерные отличия литьевого прессования от компрессионного следующие [c.98]
Одна из наиболее распространенных разновидностей прессования— литьевое прессование — известна также под названием пресс-литье или трансферное прессование. Принципиальное отличие литьевого прессования от прямого (компрессионного) прессования состоит в том, что материал загружается не в саму полость пресс-формы, где происходит формование изделия, а в загрузочную камеру ( форкамеру ), в -которой он переводится в вязкотекучее состояние, а затем по специальным литьевым каналам впрыскивается в оформляющую полость формы. При этом изделие оформляется в сомкнутой форме, а необходимое давление создается в загрузочной камере и передается через материал, поэтому давление в оформляющей полости создается только в самом конце стадии формования. Благода ря этим особенностям методом литьевого (трансферного) прессования можно изготавливать такие изделия, которые не удается получить при компрессионном формовании, — изделия сложного профиля, с большой разнотолщинностью в различных сечениях, с тонкой арматурой, сложными тонкими вставками, резьбовыми знаками и т. д. Кроме того, изготовленные этим методом изделия отличаются повышенной точностью размером (малыми допусками) и минимальным количеством грата, что в ряде случаев имеет решающее значение. [c.262]
Прессование — процесс получения из пластических масс изделий заданных размеров и конфигурации в пресс-форме под давлением пуансона. Изделия на гидравлических прессах прессуются двумя методами компрессионным (прямым) и трансферным (литьевым) компрессионное прессование может быть холодным и горячим. [c.72]
В настоящее время н,аиболее распространенными методами переработки фенопластов являются горячее компрессионное и трансферное (литьевое) прессование. В 1963 г. были созданы литьевые машины нового типа для переработки фенопластов, позволяющие сократить производственный цикл в 3—10 раз. Количество фенопластов, переработанных литьем под давлением, приведено ниже [171]- [c.223]
ТРАНСФЕРНОЕ ПРЕССОВАНИЕ — см. Литьевое [c.325]
ТРАНСФЕРНОЕ ПРЕССОВАНИЕ — см. Литьевое прессование. [c.325]
В настоящее время экструдер используется для расплавления и формования термопластичных материалов не только при экструзии, но и при переработке их другими методами. Наиболее широко применяются экструдеры в литьевых машинах, где они выполняют функции узла предваритель ной пластикации, и в машинах для трансферного прессования.. Наблюдается тенденция к замене в различных агрегатах плунжерных экструдеров червячными. Во многих случаях применение червячного экструдера означает замену периодического процесса не-прерывны.л . [c.248]
Кроме перечисленных типов прессов, применяются комбинированные прессы с одно- или разновременно действующими гидроцилиндрами верхнего и нижнего давления. К этому классу прессов, в первую очередь, можно отнести специализированные прессы для литьевого прессования (инжекционного или трансферного). Функции цилиндров прессов этого назначения (рис. IX. 20) разграничены таким образом, что с помощью одного из цилиндров осуществляется замыкание пресс-формы, с помощью второго — впрыскивание разогретого пластика в оформляющую полость уже сомкнутой формы. [c.459]
Основной недостаток компрессионного прессования (холодного и горячего) заключается в том, что полное отверждение изделий большого сечения затруднено вследствие плохой теплопроводности пластических материалов. Этот недостаток устраняется при использовании метода трансферного (литьевого) прессования. [c.73]
Следует указать, что сопоставление по производительности и экономичности литья под давлением на червячных машинах и автоматического трансферного прессования с высокочастотным подогревом материала, по-видимому, спорно вследствие различия в выборе критериев оценки и конкуренции изготовителей различных машин. Именно этим можно объяснить, что в статье [2] оспариваются преимущества червячных литьевых машин для переработки реактопластов перед автоматическими [c.58]
Прессование — процесс получения ия пластмасс изделий заданных размеров и конфигурации в пресс-форме под давлением пуансона. Изделия прессуют двумя методами компрессионным (прямым) и трансферным (литьевым). [c.102]
Конструкции трансферных пресс-форм. Трансферные пресс-формы применяют для формования изделий из реактопластов методом литьевого прессования. Основными частями пресс-формы являются формующая полость (которая [должна быть замкнута [c.294]
Метод трансферного прессования состоит в выдавливании пресс-материала из бункера в закрытую нагретую пресс-форму (рис. VI. 41), В сравнении с прямым прессованием этот метод имеет много преимуществ, а именно большую скорость отверждения (в результате дополнительного нагревания пресс-материа-ла под влиянием внутреннего трения во время прохождения через литьевые каналы) меньшие расходы на отделку (благодаря полному отсутствию швов и заусенцев или получению очень тонких швов и заусенцев) меньший износ поверхности пресс-форм (поскольку форма соприкасается только с нагретым пласти-цированным пресс-материалом) однородность изделий по всей массе (благодаря чему их расчетная усадка более равномерна) лучший внешний вид поверхности, высокие показатели диэлектрических свойств изделий возможность формовать изделия сложной конфигурации, что не достигается при прямом прессовании. [c.189]
Точное соблюдение режима прессования в этом методе наиболее важно. Необходимо помнить, что при трансферном прессовании существует давление литья (впрыска) и давление смыкания формы. Первое зависит от метода нагревания формы и размеров изделия и составляет в среднем 1200—2000 кгс/см в пересчете на горизонтальное сечение загрузочной камеры что в 5—8 раз больше, чем при прямом прессовании. Давление смыкания формы должно быть соответственно больше, чтобы помешать открыванию формы под влиянием давления впрыска, литьевой канал — как можно короче, а пресс-форма иметь достаточное число каналов для подпрессовки . [c.189]
Литьевое (трансферное) прессование применяют гл. обр. для переработки реактопластов. Формование осуществляют в прессформах, оформляющая полость к-рых отделена от загрузочной камеры и соединяется с ней литниковыми каналами (рис. 2). В процессе прессования материал, помещенный в загрузочную камеру нагретой прессформы, переходит в вязкотекучее состояние и под давлением 60-200 МПа по литниковому каналу перетекает в оформляющую полость прессформы, где материал дополнительно прогревается и отверждается. [c.6]
Литьевое (трансферное) прессование — способ переработки термореактивных и термопластич. материалов. Особенность метода — загрузочная камера (тигель) отделена от формующей полости прессформы. Перед заполнением формы пресс-материалом формующая полость находится в замкнутом состоянии. Материал, загруженный в камеру, прогревается до вязкотекучего состояния и давлением пуансона продавливается через каналы — литники — в формующую полость прессформы, где материал дополнительно прогревается. Благодаря отделению загрузочной камеры от формующей полости их можно нагревать отдельно до различных темп-р. Этим способом можно перерабатывать термореактивные материалы при 140—200° и термопластичные при 30—45°. [c.28]
Прессование. Различают прямое (горячее, компрессионное) и литьевое (трансферное) прессование. При прямом прессовании прессматериал в виде порошка или таблеток загружается в прессформы и подвергается воздействию тепла и давления. При литьевом прессовании прессматериал нагревается до вязкотекучего состояния в загрузочной камере (тигле) и впрыскивается через узкое сопло в оформляющие гнезда. [c.76]
Прессование (обычное, прямое, компрессионное, литьевое, трансферное, шприц-гусс, с термической обработкой вне пресса, открытое, контактное и другие разновидности). [c.10]
Ненаполненные РП сравнительно редко используют как самостоят. материалы из-за высоких объемных усадок при отверждении смол и возникающих вследствие этого больших усадочных напряжений. Обычно смолы, содержащие модифицирующие добавки, служат связующими наполненных РП. Дисперсно-наполненные РП получают в виде отверждающихся масс (см. Пресспорошки, Премиксы) совмещением связующего с наполнителем в разл. смесителях такие РП перерабатывают в изделия методами компрессионного или литьевого прессования и литья под давлением, реже заливкой в формы или трансферным прессованием. Армированные РП получают в виде предвари- [c.565]
При пресслитье (трансферном, литьевом прессовании) загрузочная камера-тигель отделена от формующей полости, которая к моменту заполнения ее прессматериалом находйтся в замкнутом состоянии (рис. 1-3). [c.21]chem21.info
Литьевое прессование - Большая Энциклопедия Нефти и Газа, статья, страница 1
Литьевое прессование
Cтраница 1
Литьевое прессование позволяет получать детали сложной формы, с глубокими отверстиями, в том числе резьбовыми. Возможна установка сложной и тонкой арматуры. В процессе перетекания через литниковое отверстие пресс-материал прогревается одинаково, что обеспечивает более равномерную структуру прессуемой детали. При литьевом прессовании отпадает необходимость в подпрессовках, так как образующиеся газы могут выходить в зазор между литниковой плитой и матрицей. [1]
Литьевое прессование ( рис. 9.8, б) отличается от компрессионного тем, что пресс-материал загружается не в формующую полость формы, а в специальную загрузочную камеру 6, соединенную с оформляющей полостью 4 литниковыми каналами 9, по которым поступает размягченный пресс-материал 8 под давлением; канал 3 - вентиляционный. [2]
Литьевое прессование производится в литьевой форме ( фиг. [3]
Литьевое прессование экономичнее компрессионного ( более короткий цикл изготовления деталей) и позволяет относительно легко получать толстостенные ( до 10 мм) детали сложной конфигурации, снабженные металлической арматурой. [4]
Литьевое прессование отличается от прямого тем, что прессовочный материал загружается в специальную литьевую камеру, откуда по литниковым каналам под давлением поступает в оформляющую полость. [6]
Литьевое прессование в основном применяют для переработки термореактивных материалов, реже для термопластичных. [8]
Литьевое прессование на обычном прессе ( рис. 37, б) осуществляют следующим образом. [10]
Литьевое прессование основано на применении загрузочной ( передаточной) камеры, из которой подогретый материал после достижения нужной пластичности нагнетается в соответствующую форму. [11]
Литьевое прессование ( рис. 281, б) осуществляется только в закрытых прессформах. К прессформе, состоящей из пуансона /, матрицы 2 и выталкивателя 3, прикреплена накладная ( съемная) загрузочная камера 6 ( тигель) для разогрева прессовочного материала 4 до вязкотекучего состояния. Прессматериал загружают в обогреваемую камеру 6, где под влиянием тепла и давления от плунжера пресса через пуансон 7 загрузочной камеры материал переходит в пластичное состояние и по каналам ( литникам) перемещается из загрузочной камеры в формующую полость нагретой прессформы. [12]
Литьевое прессование основано на применении загрузочной ( передаточной) камеры, из которой подогретый материал после достижения нужной пластичности нагнетается в соответствующую форму. [13]
Литьевое прессование отличается от прямого тем, что прессовочный материал загружается в специальную литьевую камеру, откуда по литниковым каналам под давлением поступает в оформляющую полость. [14]
Страницы: 1 2 3 4 5
www.ngpedia.ru