Как выполнить ремонт гидронасосов своими руками. Ремонт шестеренчатых насосов своими руками
Вид неисправности гидронасоса и видимое проявление отказа | Возможная причина | Способ обнаружения и устранения неисправности |
Повышенная вибрация насосной установки. | 1.Ослабление крепления насоса к установочному кронштейну или самого кронштейна 2.Несоосность валов насоса и электродвигателя. 3.Повреждение приводной муфты(большой износ или разрушение эластичных элементов). | 1.На ощупь, при выключенном электродвигателе.Подтянуть винты крепления и обеспечить их контровку. 2.Определить биение полумуфт с помощью индикаторной стойки.Выставить насос так, что бы биение полумуфт не превышало 0,2мм ( одной относительно другой). 3. При выключенном электродвигателе определить наличие углового люфта между полумуфтами. Заменить эластичные элементы. |
Повышенный шум механического происхождения и повышенная температура корпуса насоса. | 1.Ослабление закрепления насоса и электродвигателя. 2. Износ подшипников или задиры на их поверхностях. Контакт шестерен с расточкой корпуса. | 1.На ощупь, при выключенном электродвигателе.Подтянуть винты крепления насоса электродвигателя, кожуха электродвигателя, проверить отсутствие контакта вентилятора с кожухом. 2.Наличие в масле мелкой металлической пыли из материала корпуса.Разобрать насос и заменить новым. |
Повышенный шум гидравлического происхождения.Резкие колебания давления на выходе насоса. | 1. Низкий уровень жидкости в гидробаке. 2.Засорение или негерметичность всасывающей магистрали, эрозионный износ деталей из-за кавитации. | 1.Наличие пены на поверхности масла в баке. Долить масло до верхней отметки уровня.Заливка масла другой марки не допускается! 2.Вибрация нагнетательной трубы, шум высокого тона.Наличие в масле металлической пыли из материала пластин или крышек. Подтянуть элементы крепления трубопровода.Разобрать всасывающий трубопровод, проверить целостность уплотнений, отсутствие посторонних предметов в нем.Разобрать насос и осмотреть детали для проверки их состояния.Заменить насос новым. |
Отсутствие подачи в нагнетательную магистраль. Отсутствие перемещения рабочих органов машины. | 1.Поломка приводной муфты или вала насоса. 2.Непроходимость или негерметичность всасывающей магистрали насоса. | 1.Провести несколько кратковременных запусков электродвигателя, наблюдая за вращением вала насоса.При отсутствии вращения или прерывистом вращении, демонтировать насос, осмотреть муфту и вал.Заменить муфту или насос. 2.Давление на выходе насоса отсутствует. Подтянуть элементы крепления всасывающего трубопровода. Разобрать трубопровод, проверив целостность уплотнений, трубы или рукава, проверить проходимость трубопровода.После разборки уплотнения заменить новыми. |
Наружная течь масла. | 1.Износ уплотнительного узла вала. 2.Ослабление крепления нагнетательного трубопровода, разрушение уплотнений. | 1.Визуально уточнить место течи.Разобрать соединение в месте течи, проверить состояние деталей и уплотнений.Уплотнения заменить новыми. 2.Подтянуть элементы крепления трубопровода. |
Снижение подачи насоса, замедленное перемещение рабочих органов машины. | 1.Износ деталей качающего узла насоса,торцевых поверхностей крышек или пластин, опорных втулок. 2.Чрезмерно высокая температура масла. | 1.Определяемое на ощупь повышение температуры корпуса насоса по сравнению с обычной. Разобрать насос и проверить состояние деталей.При незначительных повреждениях и следах износа на торцах шестерен и пластин или втулок исправить их путем притирки.Замена насоса новым. 2.При температуре масла выше 65-79˚С определить причину повышения температуры и устранить (неправильная настройка клапана, отказ теплообменника и т.д.) |
www.metalstanki.com.ua
Ремонт шестеренчатых насосов | Гидропривод
На потерю производительности, развиваемой шестеренчатым насосом при определенных давлениях, особенно большое влияние оказывает увеличение торцовых зазоров между шестернями 1 и 4 и опорными втулками 3 (рис. 52). Утечки через торцевые зазоры примерно в 3 раза больше, чем через радиальные зазоры при равном значении этих зазоров, так как при вращении шестерен создается сопротивление течению масла по радиальным зазорам между выступами зубьев и расточенным отверстием в корпусе; кроме того, путь движения масла по радиальным зазорам из полости нагнетания в полость всасывания значительно больше, чем по торцовым зазорам. В то же время вращение шестерен содействует утечке масла через торцовые зазоры по ходу их вращения.
Таким образом, увеличение торцовых зазоров является основной причиной уменьшения производительности и снижения давления масла насосов.
Износ деталей
При разборке насоса после длительной его эксплуатации обычно обнаруживается износ корпуса 5 в зоне шестерен 1 и 4 по всей поверхности валиков 2 и 8 и опорных втулок 3. Фланцы насоса 9 и 10 износу практически не подвергаются. Особенно сильно изнашиваются соприкасающиеся торцы шестерен и опорных втулок, на поверхностях которых образуются кольцевые задиры, волнистость и др.
Рис. 52. Шестеренчатый насос
Капитальный ремонт насоса, связанный с реставрацией корпуса и заменой шестерен, целесообразно производить только в хорошо организованных ремонтных хозяйствах. Однако и в этом случае при ремонте обычно не восстанавливают изношенную внутреннюю поверхность корпуса, так как радиальный зазор со стороны нагнетательного отверстия после замены изношенных шестерен и подшипников почти равен зазору у нового насоса, а увеличенный из-за насоса зазор со стороны всасывающего отверстия не будет оказывать существенного влияния на нормальную работу насоса.
Ремонт шестерен насоса зависит от характера их износа. Износ торцов зубьев устраняют шлифованием при соблюдении параллельности плоскостей торцов и их перпендикулярности к оси зубчатого колеса в пределах 0,015 мм. Шестерни с изношенным профилем зубьев заменяют новыми.
Обычно шестерни изготовляют из стали 45 или из стали 40Х с закалкой при нагреве токами высокой частоты. Вновь изготовленные или реставрированные шестерни должны удовлетворять следующим техническим условиям: торцевое биение шестерни - не более 0,01 мм; непараллельность торцов - не более 0,015 мм; биение наружной поверхности относительно отверстия - 0,015-0,02 мм; конусность и овальность по наружной поверхности - не более 0,02 мм.
Изношенные в посадочных местах подшипников валики шестерен заменяют новыми, реже восстанавливают. Валики изготовляют из стали 20Х, цементируют на глубину до 1,2 мм и закаливают до твердости HRС 60-62. Шейки валиков, которые являются поверхностями качения игл, тщательно шлифуют и доводят до шероховатости Rа = 0,10 мкм.
Опорные валики игольчатых подшипников восстанавливают или заменяют новыми. При восстановлении опорных втулок их изношенные торцы шлифуют для устранения следов износа. После шлифования торцов необходимо восстановить канавки для прохода масла между зубьями. Отверстия опорных втулок расшлифовывают до диаметра, необходимого для установки ближайшего по размеру стандартного игольчатого подшипника, учитывая при этом диаметр шейки восстановленного или замененного валика.
Для обеспечения нормальной работы шестерен насоса опорные втулки шлифуются попарно в один размер, при этом параллельность торцов должна быть в пределах 0,01 мм. Биение наружной цилиндрической поверхности втулки относительно оси ее отверстия допускается до 0,01 мм, а биение торцов относительно оси отверстия на наибольшем диаметре должно быть не более 0,01 мм. Соблюдение этих условий гарантирует отсутствие защемления шестерен при малых торцевых зазорах.
После восстановления или замены шестерен и опорных втулок определяется их общая ширина. С учетом этого размера шлифуют один из торцов корпуса, чтобы длина посадочного отверстия в корпусе (размер А, рис. 52) была на 0,06-0,08 мм больше общего размера по ширине шестерни и двух опорных втулок. При шлифовке корпуса непараллельность его торцов должна быть обеспечена в пределах 0,01-0,02 мм. Равномерность и величина обеспеченного торцевого зазора между шестернями и торцами втулок является основным критерием качества ремонта насоса. В отдельных случаях требуемый торцевой зазор может быть обеспечен с помощью прокладок из фольги, которые устанавливаются между торцами корпуса и фланцами. Однако этот метод регулировки недостаточно надежен и рекомендуется только в отдельных случаях до очередного планового ремонта.
Для нормальной работы насоса необходимо, чтобы торец бурта втулки 6 (см. рис 52) по всей поверхности прилегал к грундбуксе 7. При ремонте грундбуксу шлифуют по плоскости до устранения следов износа. Торец бурта втулки тоже шлифуют, выдерживая перпендикулярность торца к оси отверстия втулки; биение торца не должно превышать 0,01 мм.
Сборка и испытания
Перед сборкой все детали ремонтируемого насоса необходимо промыть в керосине и смазать тонким слоем минерального масла, а игольчатые подшипники промыть в бензине и смазать солидолом. Плоскости корпуса, крышек и втулок не должны иметь забоин и царапин. Сборку насоса необходимо вести так, чтобы изношенная внутренняя поверхность корпуса была со стороны всасывающего отверстия, т. е. слева, если смотреть со стороны приводного вала, а дренажные каналы на втулках были выведены в ту же сторону.
Во избежание зажима и перекоса валов и шестерен винты крепления фланцев необходимо завертывать попеременно и до отказа, при этом легкость вращения валиков проверяют от руки.
Отремонтированный насос подвергают испытанию на специальном стенде для определения производительности и объемного коэффициента полезного действия (к. п. д.).
Объемный к. п. д. представляет собой отношение производительности насоса при определенном давлении к его же производительности без давления. Он характеризует качество ремонта насоса. Чем точнее и с меньшими зазорами изготовлены сопрягаемые детали, тем меньше внутренние утечки в насосе и тем большее значение объемного к. п. д.
Похожие материалы
www.metalcutting.ru
Способ ремонта шестеренного насоса
Изобретение относится к машиностроению и может применяться для ремонта шестеренных насосов. Способ ремонта шестеренного насоса включает шлифование наружного диаметра и торцов шестерен и рабочих поверхностей платиков до выведения следов износа. Производят замену резиновых уплотнительных элементов. Производят при помощи ступенчатого цилиндрического притира одновременную доводку радиальной уплотняющей и опорной поверхностей поджимной обоймы. Большой диаметр ступенчатого притира изготавливают равным наружному диаметру отшлифованной шестерни, а меньший диаметр равным диаметру цапфы шестерни. После чего производят доводку отшлифованных торцов шестерен при помощи дискового притира и производят обработку торцевых поверхностей, примыкающих к радиальной уплотняющей поверхности. Затем доводят рабочую поверхность платиков на притирочной плите. Под резиновые уплотнительные элементы подкладывают металлические шайбы, толщина которых равна толщине слоя металла, снятого при шлифовке торцов шестерен. Изобретение направлено на разработку способа ремонта шестеренных насосов, в которых уплотнение радиального и торцевого зазоров происходит со стороны, близкой к зоне нагнетания, а также на увеличение ресурса работы насоса после ремонта за счет уменьшения нагрузки на подшипники и увеличение подачи путем снижения радиальных и торцевых утечек. 8 ил.
Изобретение относится к машиностроению и может применяться для ремонта шестеренных насосов.
Известен способ ремонта шестеренного насоса внешнего зацепления, содержащего корпус и торцовые уплотнительные пластины (SU 1263910 А1, 23.02.1989). Согласно этому способу производят шлифование наружного диаметра и торцов шестерен и поверхности торцовых уплотнительных пластин до выведения следов износа. Торцовые поверхности корпуса обрабатывают для того, чтобы ширина корпуса была равна ширине венца шестерен. Колодцы корпуса растачивают радиусом, равным наружному радиусу наибольшей из шлифованных шестерен у приемной полости на части окружности длиной не менее π D/Z со смещением осей расточек в сторону приемной полости, где D - диаметр шестерни, a Z - число зубьев. При сборке в корпусе устанавливают шестерни наибольшего и наименьшего диаметров с обеспечением в зоне их сопряжения с поверхностью расточки зазора не более номинального. Способ прост в применении и позволяет снизить утечки рабочей жидкости после ремонта насоса как по торцам шестерен, так и по наружному диаметру шестерен. Однако уплотнение радиальных зазоров между шестернями и расточками корпуса происходит только в районе приемной полости (в зоне всасывания), это приводит к увеличению нагрузки на подшипники и, как следствие, к снижению ресурса работы насоса, так как увеличивается площадь поверхности шестерен, на которые воздействует давление рабочей жидкости. Другим недостатком этого способа является несколько большие утечки рабочей жидкости по радиальному зазору по сравнению с новым насосом, что снижает подачу насоса. Еще одним недостатком этого способа является невозможность полностью его применить при ремонте шестеренных насосов внешнего зацепления, в которых уплотнение радиального и торцовых зазоров происходит со стороны, близкой к зоне нагнетания (например, НШ-67К).
Задачей, на решение которой направлено данное предлагаемое изобретение, является разработка способа ремонта шестеренных насосов, в которых уплотнение радиального и торцового зазоров происходит со стороны, близкой к зоне нагнетания, а также увеличение ресурса работы насоса после ремонта за счет уменьшения нагрузки на подшипники и увеличения подачи путем снижения радиальных и торцовых утечек.
Для решения поставленной задачи предлагается способ ремонта шестеренного насоса, включающий шлифование наружного диаметра и торцов шестерен и рабочих поверхностей платиков до выведения следов износа. Производят замену резиновых уплотнительных элементов и при помощи ступенчатого цилиндрического притира одновременную доводку радиальной уплотняющей и опорной поверхностей поджимной обоймы, причем большой диаметр ступенчатого притира изготавливают равным наружному диаметру отшлифованной шестерни, а меньший диаметр равным диаметру цапфы шестерни, после чего производят доводку отшлифованных торцов шестерен при помощи дискового притира. Производят обработку торцевых поверхностей, примыкающих к радиальной уплотняющей поверхности, а затем доводят рабочую поверхность платиков на притирочной плите, под резиновые уплотнительные элементы подкладывают металлические шайбы, толщина которых равна толщине слоя металла, снятого при шлифовке торцов шестерен.
Замена резиновых уплотнительных элементов позволяет уменьшить протечки рабочей жидкости.
Одновременная доводка радиальной уплотняющей и опорных поверхностей сохраняет высокую соосность этих поверхностей, устраняет задиры, позволяет уменьшить зазор до минимума между отшлифованными наружным диаметром шестерни и радиальной уплотняющей поверхностью.
Доводка отшлифованных торцов шестерен при помощи дискового притира увеличивает точность обработки шестерен по ширине и снижает шероховатость поверхностей, что приводит к снижению торцовых утечек.
Доводка рабочей поверхности платиков на притирочной плите значительно повышает точность поверхности, снижает шероховатость, улучшает прилегание поверхности платиков к торцам шестерен, тем самым снижаются торцовые утечки.
Обработка торцевых поверхностей, примыкающих к радиальной уплотняющей поверхности прижимной обоймы, восстанавливает соотношение между шириной шестерни, отшлифованной по торцам, и шириной уплотняющей поверхности.
Осуществление способа поясняется на примере ремонта шестеренного насоса НШ-67К.
На фиг.1 изображен общий вид шестеренного насоса модели НШ-67К; на фиг.2 - разрез А-А на фиг 1; на фиг.3 изображена поджимная обойма шестеренного насоса; на фиг.4 - разрез Б-Б на фиг.3; на фиг.5 - технология одновременной доводки радиальной уплотняющей и опорных поверхностей насоса; на фиг.6 - технология фрезерования торцевых поверхностей, примыкающих к радиальной уплотняющей поверхности; на фиг.7 - технология доводки отшлифованных торцов шестерен при помощи дискового притира; на фиг.8 - доводка рабочей поверхности платиков на притирочной плите.
Шестеренный насос НШ-67К состоит из корпуса 1, крышки 2, поджимной 3 и подшипниковой 4 обойм, ведущей 5 и ведомой 6 шестерен, а также уплотнительных и крепежных деталей. Ведущая 5 и ведомая 6 шестерни расположены в подшипниковой обойме 4, выполненной в виде полуцилиндра с четырьмя подшипниковыми гнездами. Радиальное уплотнение осуществляется с помощью поджимной обоймы 3, опирающейся на цапфу 7 шестерен 5 и 6 опорными поверхностями 8. Резиновый уплотнительный элемент 9 формирует камеру давления, в которой создается усилие поджима обоймы к зубьям шестерен. По мере износа опорных поверхностей 8 поджимная обойма 3 компенсирует радиальный зазор между своей уплотняющей поверхностью 10 и зубьями шестерен. Уплотнение торцов шестерен достигается с помощью двух платиков 11, поджим которых осуществляется усилием из камер давления, ограниченных резиновыми уплотнительными элементами 12.
Способ осуществляется следующим образом.
Производят осмотр шестеренного насоса, в результате которого обнаруживается, что сильно «задрались» торцы и наружный диаметр шестерен 5 и 6, образовались глубокие риски на радиальной уплотняющей поверхности 10 поджимной обоймы 3, износились рабочие поверхности платиков 11. Далее производят на круглошлифовальном станке с одной установки шлифование двух торцов и наружного диаметра шестерен 5 и 6 до выведения следов износа. При шлифовании торцов шестерен стараются добиться, чтобы разность шестерен по ширине не превышала 0,01 мм. Если до шлифовки шестерни 5 и 6 имели наружный диаметр 77 мм, ширину 30 мм, а диаметр цапф 7 был равен 40 мм, то после шлифования наружный диаметр стал равен 76,9 мм, а ширина шестерен 29,8 мм. Затем изготавливают ступенчатый притир 12, у которого больший диаметр будет равен 76,9 мм, а два меньших диаметра будут равны диаметру цапф 7 шестерен 5 и 6, то есть 40 мм. С помощью ступенчатого притира 13 производят вручную доводку двух опорных поверхностей 8 и радиальной уплотняющей поверхности 10 поджимной обоймы 3, сначала, например, для ведущей шестерни 5, затем для ведомой 6. Поджимную обойму 3 при этом закрепляют в тисках, алмазную притирочную пасту наносят на опорные 8 и радиально уплотняющие 10 поверхности поджимной обоймы 3. Притиру 13 придают вращательное возвратно-поступательное движение, прижимая притир вручную к доводимым поверхностям. В начальный момент доводки (притирки) съем металла будет производиться только с опорных поверхностей 8, так как наружный диаметр шестерен 5 и 6 после операции шлифования стал меньше, а больший диаметр ступенчатого притира 13 равен наружному диаметру шестерен 5 и 6. Для доводки используют алмазную пасту. Доводку производят до исчезновения следов износа на радиальной уплотняющей поверхности 10 поджимной обоймы 3. Затем на плоскошлифовальном станке шлифуют рабочие поверхности платиков 11 до выведения следов износа и доводят отшлифованную поверхность на притирочной плите 14 при помощи алмазной пасты. Далее шестерни 5 и 6 закрепляют за цапфы 7 на патроне токарного станка, шпинделю придают обороты 350-450 об/мин и при помощи дискового притира 15 доводят торцы шестерен, используя пасту АСМ 28/20, при этом стараются, чтобы разность по ширине шестерен 5 и 6 не превышала 2 микрона. Дисковый притир 15 имеет при этом следующие параметры - наружный диаметр на 2-3 мм больше диаметра шестерен 5 и 6, внутренний диаметр притира 15 на 3-4 мм больше диаметра цапф 7, ширина притира 10-15 мм. При доводке дисковый притир 15 прижимают к торцу шестерен, удерживая в руке, слегка притормаживая и создавая максимальный эксцентриситет, который позволяет внутренний диаметр притира. Притир 15 будет вращаться в ту же сторону, что и шестерни 5 и 6, только с меньшими оборотами. Далее фрезеруют на горизонтально-фрезерном станке торцевые поверхности 16, примыкающие к радиальной уплотняющей поверхности 10 прижимной обоймы 3. При этом добиваются, чтобы ширина отфрезерованных поверхностей 16 была максимально точно равна ширине доведенных шестерен. При сборке насоса, для того, чтобы сохранить первоначальный поджим платиков 11 к торцам шестерен 5 и 6, под резиновые уплотнительные элементы 12 подкладывают металлические шайбы, толщина которых равна толщине слоя металла, снятого при шлифовании торцов 5 и 6. Этим обеспечивается силовая уравновешенность насоса.
Предлагаемый способ ремонта внедрен в ОАО «КАМА3-Металлургия» в ремонтно-механическом цехе на участке ремонта гидроаппаратуры при ремонте шестеренных насосов моделей НШ-32-2Л, НШ-50-2, НШ-67К, НШ-98К.
Способ ремонта шестеренного насоса, включающий шлифование наружного диаметра и торцов шестерен и рабочих поверхностей платиков до выведения следов износа, отличающийся тем, что производят замену резиновых уплотнительных элементов, производят при помощи ступенчатого цилиндрического притира одновременную доводку радиальной уплотняющей и опорной поверхностей поджимной обоймы, причем большой диаметр ступенчатого притира изготавливают равным наружному диаметру отшлифованной шестерни, а меньший диаметр равным диаметру цапфы шестерни, после чего производят доводку отшлифованных торцов шестерен при помощи дискового притира и производят обработку торцевых поверхностей, примыкающих к радиальной уплотняющей поверхности, а затем доводят рабочую поверхность платиков на притирочной плите, под резиновые уплотнительные элементы подкладывают металлические шайбы, толщина которых равна толщине слоя металла, снятого при шлифовке торцов шестерен.
www.findpatent.ru
Способ ремонта корпусов шестеренных насосов и устройство для его осуществления
Использование: ремонт корпусов шестеренных насосов, используемых в различных отраслях промышленного производства. Сущность изобретения: осуществляют подготовку изношенных поверхностей - расточку, обезжиривание, нанесение полимерного композиционного материала и сушку. Расточку, обезжиривание, нанесение полимерного покрытия осуществляют по изношенным поверхностям колодцев корпуса, а также по поверхностям впускного и нагнетательного патрубков. Нанесение покрытия осуществляют запрессовкой одновременно с вакуумированием. Устройство для реализации способа содержит формообразующие фланцы, крышки уплотнения, вставки для впускного и нагнетательного патрубков. Уплотняющие фланцы выполнены с каналами для удаления воздуха. 2 с.п. ф-лы, 2 ил.
Изобретение относится к способам и устройствам для ремонта корпусов шестеренных насосов и может быть использовано в различных отраслях промышленного производства.
Известен способ ремонта, при котором изношенные поверхности колодцев корпусов насосов при малых износах при величине от 0,1 до 0,3 мм (задиры, риски на поверхности) восстанавливают растачиванием под увеличенный размер, например, на специальном двухшпиндельном расточном станке типа 2705 или на фрезерных станках повышенной точности. Требуемые номинальные зазоры между вершинами зубьев качающих шестерен и стенками расточенных колодцев достигаются смещением отверстий под цапфы валов-шестерен в опорных втулках. Смещение осей шестерен должно быть не меньше разности радиусов головок зубьев шестерен и колодцев корпуса. Использование растачивания при ремонте корпусов шестеренных насосов со смещением базовых отверстий во втулках ограничено величинами износов и требуемой степенью точности сборки конструкции. Забоины, задиры, риски в корпусе, не проходящие через посадочные места и не захватывающие обработанные поверхности, длиной до 3 мм и шириной не более 1 мм и глубиной до 0,2 мм устраняют зачисткой. Количество дефектов в одном колодце не должно превышать десяти. Эллипсность колодцев после расточки должна быть не более 0,01 мм, а конусность не более 0,02 мм, непараллельность осей колодцев не более 0,02 мм, несовпадение плоскостей днищ колодцев не более 0,02 мм. Размер комплекта опорных втулок и шестеренок при сборке по высоте должен быть таким, чтобы они выступали не более чем на 0,1 мм или утопали не более, чем на 0,14 мм от плоскостей выточки корпуса. Комплекс операций по механической обработке поверхностей с высокой степенью точности их исполнения при малых полях допусков, а также малые поля допусков при сборке существенно ограничивают использование данного метода. Операции механической обработки весьма трудоемки и себестоимость работ с высокой степенью точности значительна. Поэтому использование данного метода ремонта не всегда возможно и экономически оправдано. Известен способ ремонта, когда при больших износах боковых поверхностей колодцев, а также при третьем ремонте корпуса нагревают в печи и подвергают пластической деформации обжатию в горячем состоянии. Для этого корпуса помещают в электронагревательную печь с автоматическим регулированием температуры и выдерживают 30 мин при температуре 500oC. Затем корпус устанавливают в матрицу приспособления и обжимают на прессе с усилием 500 кН в специальной пресс-форме. Обжатие завершают при температуре не ниже 430oC. Обжатый корпус подвергают термической обработке: нагревают и выдерживают в течение 30 мин при температуре 520oC, закаливают в воде при температуре 60 -100oC и отпускают в течение 4 6 ч при температуре 170 180oС. Затем у обжатого корпуса фрезеруют поверхности: верхнюю под крышку и торец днища под табличку для маркировки. С помощью специального кондуктора засверливают в корпусе базовые отверстия, растачивают колодцы на токарном или фрезерном станке и восстанавливают резьбовые отверстия под болты крышки корпуса и фланцев трубопроводов [2] Рассмотренный способ также весьма трудоемок, требует специального оборудования, включает много финишных операций механической обработки с требуемой высокой точностью изготовления и поэтому не всегда рентабелен. Известен также способ ремонта колодцев корпусов запрессовкой в них гильз из латуни или бронзы с последующей расточкой внутренних поверхностей до номинальных размеров. Для этого внутренние поверхности колодцев вначале растачивают и при необходимости фрезеруют. На обезжиренные поверхности гильз и корпусов наносят клеевой эпоксидный состав и запрессовывают гильзы. После запрессовки корпус в течение 2 ч высушивают в сушильном шкафу при температуре 180 200oC [3] Рассмотренный способ, кроме выполнения ряда предварительных работ, требует выполнения комплекса финишных операций с точным базированием и высокой степенью точности механической обработки, зачастую не обеспечивая требуемую точность сборки по соосности валов, что вызывает повышенный износ опорных втулок, самих шестерен и уплотнений, возникают утечки и насосы зачастую не достигают требуемой величины производительности 90% от расчетной даже при стендовых испытаниях. Наиболее близким к описываемому является способ ремонта корпусов шестеренных насосов, заключающийся в восстановлении изношенных поверхностей полимерным композиционным покрытием, основанным на эпоксидных смолах. Восстановление корпусов насосов нанесением состава на основе эпоксидной смолы состоит в следующем. На тщательно обезжиренные поверхности колодцев корпуса шпателем наносится слой эпоксидного клеевого состава, который при температуре 18 20oC выдерживают 1 -2 ч, а затем еще 2 ч в сушильном шкафу при температуре 180 220oC. Клеевой состав включает: 100 мас.ч смолы ЭД-6, 20 мас.ч. алюминиевой пудры или 160 мас. ч. железного порошка, 15 мас. ч. дибутилфталата. Перед применением дополнительно вводят отвердитель полиэтиленполиамин. Затем колодцы корпусов растачивают под номинальные или уменьшенные ремонтные размеры. Уменьшенные ремонтные размеры используются в случае сборки отремонтированных корпусов насосов с изношенными шестернями, которые не подвергались при их ремонте восстановлению наплавкой, а лишь шлифовались или калибровались [3] Известный способ ремонта корпусов также содержит ряд операций финишной механической обработки поверхностей, требующих высокой точности исполнения на специальных станках. Кроме того, не гарантируется надежность эксплуатации отремонтированных этим способом насосов, т.к. велика вероятность отказов из-за отслоений покрытий, вызываемых запрессовкой масла, находящегося под высоким давлением до 1,4 1,6 МПа в камерах проточной части, в дефекты покрытия (поры и микротрещины), обнажающиеся после механической обработки. Масло запрессовывается также и между слоем покрытия и поверхностью корпуса на стыках колодцев с впускным и нагнетательным патрубками. Известно устройство для ремонта корпусов шестеренных насосов при больших износах боковых поверхностей колодцев пластической деформацией обжатием в горячем состоянии. Оно представляет собой матрицу со специальной пресс-формой [2] Известное устройство предназначено для реализации способа ремонта пластической деформацией корпусов, требует специального оборудования и сложно в устройстве. В качестве ближайшего аналога выбрано устройство для реализации способа ремонта корпусов шестеренных насосов нанесением полимерногокомпозиционного покрытия на изношенные поверхности, содержащее формообразующие вставки в колодцах, уплотняющие фланцы, крышки и уплотнения, препятствующие оплыванию покрытия до полного его отверждения [3] Конструкция устройства предназначена для реализации конкретного способа и не обеспечивает требуемого качества покрытия без его дополнительной трудоемкой механической обработки. Известный способ ремонта корпусов шестеренных насосов и устройство для его реализации не позволяют: обеспечить требуемую надежность отремонтированных насосов, обеспечить качество формуемого полимерного покрытия, сократить трудоемкость выполнения ремонта. Техническая задача, на решение которой направлено описываемое изобретение, обеспечение качества и упрощение технологии ремонта корпусов шестеренных насосов. Указанная техническая задача решается тем, что в известном способе ремонта корпусов шестеренных насосов, включающем подготовку изношенных поверхностей расточку и обезжиривание, нанесение полимерного композиционного материала и сушку, расточку и покрытие производят не только по изношенным поверхностям колодцев корпуса, но и по поверхностям впускного и нагнетательного патрубков. Кроме того, нанесение полимерного композиционного покрытия производят запрессовкой одновременно с вакуумированием. Устройство для реализации предлагаемого способа ремонта корпусов, содержащее формообразующие вставки колодцев, уплотняющие фланцы, крышки и уплотнения, выполнено с дополнительными вставками, расположенными во впускном и нагнетательном патрубках, а уплотняющие фланцы содержат каналы для удаления воздуха. Указанная совокупность признаков позволяет придать объекту новые свойства и получить новый технический результат. Выполнение процесса ремонта корпусов шестеренных насосов восстановлением изношенных поверхностей полимерным композиционным покрытием, основанным на эпоксидных смолах, с помощью расточки и обезжиривания и покрытия не только изношенных поверхностей колодцев корпусов, но и поверхностей впускных и нагнетательных патрубков, позволяет обеспечить требуемую надежность эксплуатации отремонтированных этим способом насосов. Сплошное композиционное полимерное покрытие всех поверхностей проточных частей насосов исключает вероятность эксплуатационных отказов из-за возможных его отслоений, вызываемых, как правило, запрессовкой масла на ребрах поверхностей между полимерным покрытием и металлической поверхностью корпусов в местах переходов из впускных патрубков в колодцы и из колодцев в нагнетательные патрубки. Нанесение полимерного композиционного материала запрессовкой одновременно с вакуумированием позволяет обеспечить качество формуемого полимерного покрытия. Исключается возможность образования дефектов формования поверхности - микротрещин и пор и, соответственно, возможность запрессовки масла в них под давлением и отслоений в процессе работы. Сокращается трудоемкость выполнения ремонта за счет исключения финишной механической обработки восстановленных поверхностей колодцев и патрубков, т.к. способ позволяет сразу получить требуемое качество поверхности покрытия с номинальными размерами в пределах полей допусков с требуемой шероховатостью каналов проточных частей корпусов. Применение устройства для выполнения способа ремонта корпусов шестеренных насосов с дополнительными вставками, расположенными во впускных и нагнетательных патрубках, и с фланцами, содержащими каналы для удаления воздуха, позволяет реализовать способ, а также обеспечить требуемое качество покрытия. Дополнительные вставки формируют покрытие каналов всасывающих и нагнетательных патрубков корпусов насосов, обеспечивая его форму, размеры, сплошность и отсутствие микротрещин и пор. Каналы во фланцах также способствуют получению требуемого качества поверхности проточной части, облегчая процессы растекания композиционного материала и формования полимерного покрытия. Удаление воздуха из зазоров между вставками и расточенными поверхностями снижает сопротивление течению воздушной пробки, обеспечивает сплошное заполнение пазух между расточенными поверхностями и всеми вставками. Сплошное покрытие всех каналов проточной части корпуса шестеренного насоса исключает возможность его отслоения из-за запрессовки масла в стыки и прочие дефекты получаемой поверхности. На фиг.1 2 изображены фронтальный и горизонтальный разрезы ремонтируемого корпуса насосов в сборе с устройством. Способ ремонта корпусов 1 шестеренных насосов осуществляют следующим образом. Подготавливают поверхности путем расточки изношенных поверхностей колодцев и поверхностей патрубков и их обезжиривания, затем наносят полимерный композиционный материал 2 на основе эпоксидного связующего и по изношенным поверхностям колодцев корпусов и по поверхностям впускного и нагнетательного патрубков запрессовкой одновременно с вакуумированием и осуществляют финишную сушку изделия. Изношенные поверхности колодцев корпусов 1, всасывающий и нагнетательный патрубки растачивают на фрезерном или токарном станке с нанесением канавок, например, типа "ласточкин хвост" на глубину до 1 мм и обезжиривают. Внутри корпусов размещают необходимые детали устройства для реализации способа, заливают требуемые объемы композиции и запрессовывают ее с помощью вставок в патрубках в зазоры между формообразующими деталями и стенками корпусов при одновременном вакуумировании полости формования. После отверждения композита корпуса подвергают окончательной сушке для упрочнения покрытия. Устройство для ремонта корпусов 1 шестеренных насосов полимерными композиционными покрытиями 2 содержит расположенные в колодцах формообразующие вставки 3, установленные на боковых торцах уплотняющие фланцы 4, снабженные уплотнениями 5, верхние крышки 6 и 7, размещенные над вставками 3 и снабженные уплотнениями 8 и 9. Во впускном и нагнетательном патрубках размещены дополнительные вставки 10, снабженные уплотнениями 11. Формообразующие вставки колодцев 3 закреплены своими цапфами (не показаны) в нижних вкладышах 12 и верхних крышках 7, отделенных от вставок 3 прокладками 13 и 14. Уплотняющие фланцы 4 содержат каналы для отвода из зоны формования полимерного покрытия 2, отделенные от нее тонкими бумажными фильтрами 15 и снабженные штуцерами 16 для присоединения шлангов вакуумного насоса (не показаны). Внутри колодцев корпуса 1 последовательно размещают: нижние вкладыши 12, прокладку 14, смазанные техническим вазелином формообразующие вставки 3, прокладку 13, уплотнение 9, верхние крышки 7, уплотнение 8 и прижимают крышкой 6. Уплотняющие фланцы 4 с размещенными в них уплотнениями 11 и с тонкими фильтрами 15 присоединяют к боковым торцам ремонтируемого корпуса 1 и штуцеры 16 подключают к шлангам вакуумного насоса (не показаны). Дополнительная вставка 10 со смазанным до уплотнения 11 участком рабочей поверхности вводится до упора с формообразующими вставками 3 внутрь одного из уплотняющих фланцев 4. Корпус насоса с устройством поворачивают на 90 градусов и размещают с верхним расположением второго патрубка. Подготовленный объем композиции заливают в верхний патрубок через отверстие в уплотняющем фланце 4 устройства, затем в последний вводят вторую дополнительную вставку 10 (также с предварительно смазанным участком рабочей поверхности), которую плавно запрессовывают до соприкосновения с формообразующими вставками 3. Параллельно с этим производят вакуумирование посредством отсоса воздуха из зоны формования через штуцеры 16 вакуумным насосом. Корпус насоса с устройством оставляют под прессом до отверждения, а затем подвергают термообработке в сушильном шкафу при температуре 120oС в течение 2 ч. Выполнение расточки и покрытия не только по изношенным поверхностям колодцев корпуса, но и по поверхностям впускного и нагнетательного патрубков обеспечивает требуемый уровень надежности работы отремонтированных насосов, гарантируя сплошность покрытия и отсутствие стыковых поверхностей в проточной части насоса на линиях перехода между колодцами и всасывающими и нагнетательным патрубками, исключая тем самым возможность запрессовки масла, находящегося под большим давлением, под слой покрытия. Нанесение полимерного композиционного материала на подготовленные поверхности запрессовкой одновременно с вакуумированием позволяет обеспечить требуемое качество формуемого покрытия проточной части корпуса насоса - отсутствие пузырьков в слое материала, микротрещин на поверхности и снизить пористость поверхности покрытия. Сочетание вакуумирования зоны заполнения с запрессовкой полимерного материала позволяет улучшить процесс заполнения пазух между поверхностями вставок и корпусом насоса, снижает сопротивление растеканию по поверхностям, улучшает внутреннюю структуру полимерного покрытия за счет удаления пузырьков воздушных включений. Применение в устройстве формообразующих вставок колодцев с номинальными или увеличенными ремонтными диаметрами позволяет, кроме того, исключить финишную механическую обработку поверхностей полимерного покрытия колодцев корпусов, снижая себестоимость их ремонта. При этом сохраняется качество восстановленной поверхности покрытия, достигнутое формованием, и гарантируется качество сборки насосов.Формула изобретения
1. Способ ремонта корпусов шестеренных насосов, включающий подготовку поверхности колодцев корпуса путем расточки и обезжиривания, нанесение на подготовленные поверхности полимерного композиционного покрытия и последующую сушку, отличающийся тем, что дополнительно расточку, обезжиривание и нанесение покрытия производят по поверхностям впускных и нагнетательных патрубков корпуса, при этом нанесение покрытий осуществляют запрессовкой одновременно с вакуумированием. 2. Устройство для ремонта корпусов шестеренных насосов, содержащее формообразующие вставки колодцев, уплотняющие фланцы, крышки и уплотнения, отличающееся тем, что оно снабжено дополнительными вставками для впускного и нагнетательного патрубков корпуса, а уплотняющие фланцы выполнены с каналами для удаления воздуха, соединенными со штуцерами, установленными в корпусах уплотняющих фланцев.РИСУНКИ
Рисунок 1, Рисунок 2www.findpatent.ru
Ремонт насосов - Ремонт промышленного оборудования
Ремонт насосовКатегория:
Ремонт промышленного оборудования
Ремонт насосовНасосы в гидросистемах
Нясосы, нагнетающие масло в рабочие цилиндры, являются основными механизмами гидроприводов. В гидроприводах промышленного оборудования применяются шестеренчатые, лопастные (пластинчатые), поршневые и другие насосы
Шестеренчатые насосы состоят из двух зубчатых колес (преимущественно наружного зацепления), вращающихся с малыми зазорами в корпусе.
Масло захватывается вращающимися зубчатыми шестернями из всасывающей зоны впадинами зубьев; выступы зубьев, входя в зацепление, выталкивают масло из впадин зубьев в зону нагнетания. Для устранения излишнего давления, возникающего между зубьями, в месте заклинивания жидкости, на торце корпуса (или вкладышей), выполнена специальная канавка, отводящая запираемое масло в зону нагнетания. Этот процесс происходит непрерывно.
Шестеренчатый насоо состоит из корпуса, к торцам которого прикреплены фланцы. На приводном валу помещена ведущая шестерня, соединяемая с ведомой. Обе шестерни соединены с валиками и посредством шпонок по скользящей посадке. От осевого смещения валики удерживаются пружинными кольцами. Цапфы валиков вращаются на игольчатых подшипниках в комплектом иголок. На стыках корпуса и крышек поставлены прокладки из тонкой бумаги, обеспечивающие герметичность соединения. Для предотвращения утечки масла по приводному валику через отверстие в крышке предусмотрен сальник.
Конструктивные особенности шестеренчатых насосов весьма разнообразны. Они различаются по производительности, давлению опорами качения и скольжения, по способу монтажа и др.
Рис. 1. Общий вил шестеренчатого насоса ГП-22
Ремонт шестеренчатых насосов
В шестеренчатом насосе изнашиваются по торцам и наружному диаметру зубчатые колеса, а также сопрягающиеся с ними внутренние поверхности корпуса и другие детали насоса. Зубчатые колеса испытывают одностороннее давление жидкости, направленное из полости нагнетания в сторону всасывания. Поэтому сопрягающиеся с ними внутренние поверхности корпуса получают односторонний износ, тем больший, чем выше давление жидкости. Когда же работа ведется на загрязненном масле, усиливается износ зубьев зубчатых колес, а также подшипников и поверхности приводного вала, сопрягающейся с сальниковой набивкой
Рис. 2. Схема к ремонту шестеренчатых насосов пластмассовыми композициями
Изношенные шестеренчатые насосы работают неровно. Их производительность значительно снижается и давление падает из-за повышенного протекания масла между зубьями колес и внутренними поверхностями корпуса.
Внутренние поверхности корпуса при ремонте растачивают, снимая слой металла желательно не больше 0,2 мм, затем их шлифуют. Старые зубчатые колеса заменяют новыми — корригированными с припуском по торцам для последующего шлифования торцов (при сборке) и с диаметром выступов, увеличенным на глубину расточки корпуса.
Можно восстанавливать корпус шестеренчатого насоса пластмассовыми композициями. Для этого растачивают отверстие так, чтобы образовался зазор 2—3 мм, и изготовляют специальные вставки, диаметр которых равен наружному диаметру устанавливаемых зубчатых колес. Вставки устанавливают в отверстия для подшипников валов насоса и вместе с крышками и скрепляют с корпусом. Из пластилина делают воронки, закрывают пластилином отверстия всасывания и нагнетания и заполняют пространство между вставками и корпусом насоса пластмассовой композицией, образуя втулки.
После отвердевания пластика отвинчивают центрирующие винты, очищают от пластилина, снимают крышки и и удаляют приливы пластика. Этим способом восстанавливают насосы, работающие с давлением до 2,5 МПа (25 кгс/см2).
Если для шестеренчатого насоса изготовляют новые зубчатые колеса то заготовки колес перед нарезанием зубьев обязательно прошлифо-вывают по наружному диаметру, имея в виду, что зазор между головками зубьев и внутренней поверхностью корпуса не должен превышать 0,02 мм. Изготовляют зубчатые колеса из цементируемой стали и закаливают до твердости HRC52—58. Точность изготовления должна быть такой, чтобы биение колес не превышало 0,04 мм, а отклонение от параллельности между зубьями и осью отверстия — 0,03 мм.
При ремонте зубчатых колес с небольшим износом по профилю зубьев и их наружному диаметру (между зубьями сцепляющихся колес проходит щуп толщиной до 0,1 мм) ограничиваются шлифованием торцов колес; так же шлифуют до устранения следов износа сопрягающиеся с ними торцы вкладышей. Колеса со значительным износом обычно заменяют новыми. Вместе с ними сменяют также приводной валик, подшипники и уплотнение.
Отремонтированные насосы хорошо работают, если в них соблюдены установленные зазоры между колесами, корпусом и прокладками. Суммарные зазоры между торцами колес и вкладышами, а также между головками зубьев колес и сопряженной с ними внутренней поверх, ностью корпуса допускаются 0,03—0,05 мм.
Проверку зазоров осуществляют линейкой и щупом, определяют разность высоты между торцом зубчатого колеса и корпусом насоса, щупом проверяют зазор между рабочими профилями зубьев и зазор между сопряженными поверхностями зубчатых колес и корпуса насоса.
При сборке насосов применяют для уплотнения бумажные прокладки, которые рекомендуется пропитать нитролаком. Если шестеренчатый насос собирают без таких уплотняющих прокладок, нужно тщательно пригнать (шабрением, шлифованием или другими способами) сопрягаемые поверхности деталей, обеспечивая надежную герметичность соединений между корпусом и крышками.
Ремонт пластинчатых (лопастных) насосов
Пластинчатые насосы выпускают различных типов и размеров, отличаются они по производительности и давлению от до 12,5 МПа (от 50 до 125 кгс/см2). На рис. 58 показан насос, предназначенный для подачи чистых минеральных масел в гидросистемы оборудования под Давлением 125 кгс/см2. Насос типа БГ12-2 постоянной производительности представляет собой объемную ротационную машину пластинчатого типа двойного действия.
Устроен насос следующим образом. В чугунном корпусе и крышке установлен статор, имеющий внутри криволинейную профилированную поверхность, по которой скользят десять сдвоенных лопаток, свободно перемещающихся в радиальных пазах ротора. Ротор посажен на шлицы вала, свободно вращающегося на шарикоподшипниках.
Для распределения потоков масла и уплотнения торцов ротора и статора служат плоский диск и диск с шейкой. Плоский диск имеет два основных всасывающих окна для всасывания рабочей жидкости в камеры между лопатками и два вспомогательных окна для всасывания рабочей жидкости в камеры под лопатками. Для увеличения площади всасывающие окна соединяются отверстиями, сделанными в статоре, с глухими основными и вспомогательными всасывающими окнами диска с шейкой, за счет чего обеспечивается всасывание рабочей жидкости с двух сторон ротора.
Рис. 3. Пластинчатый насос типа БГ12-2
Диск с шейкой плавающего типа имеет кроме всасывающих еще основные окна для нагнетания рабочей жидкости из камер между лопатками и вспомогательные для нагнетания рабочей жидкости из-под лопаток. Плоский диск помимо всасывающих окон имеет еще глухие основные и вспомогательные нагнетательные окна, так что нагнетание производится с двух сторон ротора. Ввиду того, что в полости всасывания пространство под лопатками соединяется с линией всасывания, обеспечивается разгрузка лопаток от гидравлического усилия, прижимающего лопатки к статору. Прижим лопаток к статору в полости всасывания осуществляется центробежной силой. В начале работы прижим диска с шейкой осуществляется пружинами 10, а в процессе работы — и давлением масла.
Для предотвращения утечек в насосе применена манжета во фланце и круглые кольца.
Нарушение нормальной работы лопастных насосов проявляется в снижении их производительности, произвольных падениях и подъемах давления подаваемой жидкости и появлении повышенного шума и стука. Наибольшему износу обычно подвергаются ротор, лопатки, диски, а также шарикоподшипники, манжета и др.
Статорные кольца особенно сильно изнашиваются в местах перехода от одного радиуса к другому, где образуются ступени и задиры. Ремонт статорных колес сводится к шлифованию их внутреннего профиля. Так как после установки отремонтированных этим способом колец падает производительность насосов, стремятся заменять изношенные статорные кольца новыми. Новые кольца изготовляют из стали ШХ15 или стали ХВГ. Термообработкой им придают твердость до HRC60-64.
Изношенный ротор целесообразно не заменять, а ремонтировать, так как изготовление нового ротора сопряжено со значительными трудностями. Ремонт заключается в восстановлении параллельности стенок пазов, шлифовании изношенных шеек и торцов.
Пазы с износом не более 0,05 мм ремонтируют вручную при помощи абразивного порошка с последующей доводкой шлифовальной пастой. Предельная допустимая непараллельность стенок пазов 0,02 мм. При большем износе стенок пазов их параллельность восстанавливают обработкой тонким абразивным кружком на станке с доводкой вручную. Следует иметь в виду, что при значительном возрастании ширины пазов приходится увеличивать ширину лопаток и в результате повышается давление лопаток на статор, ускоряя его износ.
Изношенные шейки ротора восстанавливают хромированием. Шейки можно ремонтировать и шлифованием, компенсируя уменьшение их размеров установкой дисков (изготовляются из бронзы ОФЮ-1, АЖ9-4 и др.), тщательно подгоняемых к прошлифованным шейкам.
Одновременно с шейками шлифуют торцы ротора. При этом выдерживают допуск на соосность шеек не больше 0,02 мм. Допустимое биение торцов 0,015—0,02 мм на радиусе в 40 мм.
Значительно изношенные лопатки заменяют новыми, изготовленными в соответствии с техническими условиями.
Таким образом, ремонт лопастных насосов является достаточно трудоемким и поэтому во многих случаях бывает более выгодно заменить изношенные насосы новыми. Ремонт целесообразно производить только при необходимости устранения незначительных дефектов, например, когда ослабляется сальниковое уплотнение или когда нужно сменить шарикоподшипники.
Отремонтированный насос, испытывают на стенде или непосредственно на станке, обкатывая его на холостом ходу в течение -20 мин. При отсутствии неисправности испытывают насос под нагрузкой, постепенно повышая давление до номинального и затем превышая на 30%. При этом максимальном давлении проверяемый насос должен работать не более 3—5 мин. При испытании насоса замеряют производительность при различных давлениях и тем самым определяют К п’Д., используя для этого специальное приспособление.
Читать далее:
Сборка гидроприводов
Статьи по теме:
pereosnastka.ru
Ремонт гидронасосов делаем правильно | Мой колодец
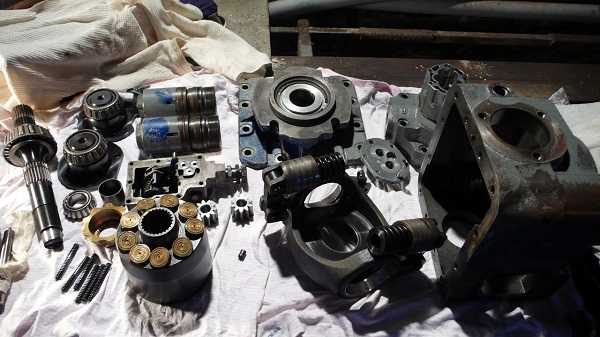
Ремонт гидронасоса
Ремонт гидравлических насосов часто необходим при возникновении проблем с такой специальной техникой. Часто, подобная ситуация не требует вмешательства квалифицированных специалистов и при наличии небольших определенных знаний можно своими руками ее исправить.
С наиболее распространенными неисправностями и способами их устранения предлагается познакомиться из статьи.
Разновидности и классификация гидронасосов
Работа любого гидронасоса основана на принципе всасывания и нагнетания жидкости.
Основные элементы конструкции:
- Камера всасывания.
- Камера нагнетания.
Между ними перемещается жидкость, которая при заполнении камеры нагнетания, начинает давить на поршень, вытесняя его, сообщая рабочему инструменту перемещение.
Основные рабочие параметры всех типов гидронасоса:
- Частота вращения вала двигателя, измеряется в об/мин.
- Рабочее давление в цилиндре, в Бар.
- Объем рабочей жидкости, в см³/об или количество жидкости, вытесняемое насосом за один оборот вала двигателя.
Основные разновидности оборудования:
- Ручной гидравлический гидронасос. Это простейший агрегат, работающий по принципу вытеснения жидкости.
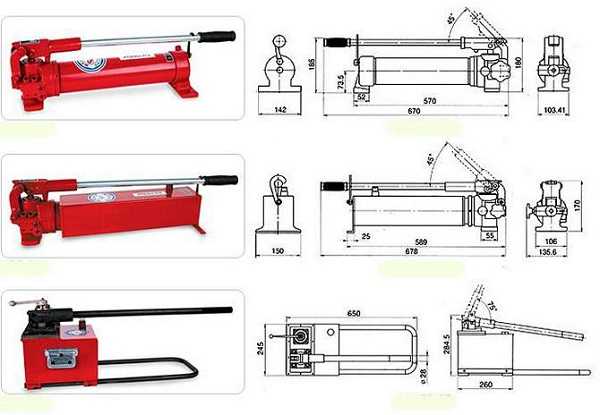
Ручной гидронасос
При нажатии ручки происходит перемещение поршня вверх, что создает силу всасывание и посредством клапана КО2 в камеру поступает жидкость, вытесняемая при поднятии рукояти.
Преимущества таких агрегатов:
- относительная простота конструкции, что облегчает ремонт при необходимости;
- надежность;
- низкая цена.
Недостаток:
- низкая производительность, по сравнению с приводными агрегатами.
- Радиально-поршневые. Способны развивать давление до 100 Бар, имеют длительный период работы. Радиально-поршневые насосы могут быть двух типов:
- роторными. В таких устройствах поршневая группа помещена внутри ротора, от его вращения поршень совершает возвратно-поступательные перемещения, поочередно стыкуясь с отверстиями для слива жидкости через золотники;
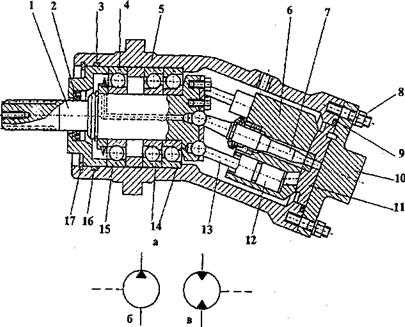
Устройство роторного радиально-поршневого насоса
- с эксцентричным валом. Его отличие — расположение поршневой группы внутри статора, такие насосы распределяют жидкость через клапана.
Преимущества оборудования:
- высокая надежность;
- работа выполняется с высоким давлением, что увеличивает производительность;
- при эксплуатации создает минимальный уровень шума.
Недостатки агрегата:
- при подаче жидкости высокий уровень пульсации:
- большая масса.
- Аксиально-поршневые. Это наиболее распространенный тип оборудования.
В зависимости от расположения оси вращения двигателя могут быть:
- наклонными;
- прямыми.
Преимущества таких насосов:
- большой КПД;
- высокая производительность.
Основной недостаток:
- высокая стоимость.
- Шестеренные насосы относятся к роторному оборудованию. Гидравлическая часть конструкции состоит из двух вращающихся шестерней, их зубья при контакте вытесняют из цилиндра жидкость. Шестеренчатые насосы могут быть:
- с внешним зацеплением;
- с внутренним зацеплением, при котором шестеренки расположены внутри корпуса.
На фото представлены типы шестеренных насосов.
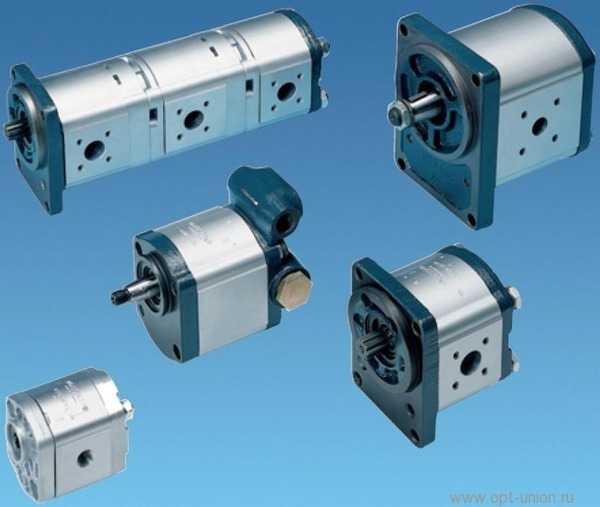
Шестеренные насосы
Шестеренные агрегаты используются в системах, где уровень рабочего давления не превышает 20 МПа. Они больше всего применяются в сельскохозяйственном и строительном оборудовании, системах подачи материалов для смазки узлов и мобильной гидравлике.
Устройства имеют:
- Простую конструкцию.
- Небольшие размеры.
- Малый вес.
Недостатки:
- Низкий КПД, до 85%.
- Небольшие обороты.
- Короткий эксплуатационный ресурс.
Основные неисправности гидронасосов и способы их устранения
Совет: Для увеличения срока службы гидронасоса необходимо строго соблюдать требования инструкции по эксплуатации.
Практически все поломки, возникающие при работе гидронасосов, являются следствием таких факторов, как:
- Несоблюдение правил управления оборудованием и пренебрежение при его техническом обслуживании:
- несвоевременной заменой масла и фильтров;
- устранением протечек в гидравлической системе.
- Ошибки при подборе гидравлической жидкости или масла.
- Использование комплектующих, которые не соответствуют режиму эксплуатации насоса.
- Неправильная настройка оборудования.
В таблице представлен список наиболее частых неисправностей и способы их устранения:
Поломка гидронасоса | Вероятная причина | Инструкция устранения неполадки |
Нестабильность при работе | Износилось или повредилось седло подшипника и поверхность люльки насоса. Зазор в тяге механизма управления. Поломались штифты седла подшипника. Загрязнился канал между золотником управления и поршнем. Задиры, полученные на поверхности поршня, препятствуют его плавному передвижению | Произвести внешний осмотр. Проверить и отремонтировать, при необходимости, гидронасос |
Задиры, возникшие на поверхности золотника управления, препятствуют плавному перемещению поршня | Познакомиться с соответствующим разделом в руководстве, выпускаемом службой контроля за гидравлическим оборудованием | |
Неисправные элементы компенсатора давления в контуре. Повысилось сопротивление гидравлической линии, расположенной между удаленными элементами компенсатора давления и пультом управления. Низкое давление управления | Проверить работу гидролинии Настроить давление управления оборудованием | |
Гидронасос выдает малый расход | Задиры или износ цилиндра и сопряженных поверхностей на тарелке клапана. Износились шлицы приводного вала. Износились или повредились башмаки поршней или сами поршни | Сравнить с соответствующими техническими характеристиками гидронасоса |
Износились поршневые отверстия блока цилиндров. Чрезмерно износились подшипники | Проверить работу гидронасоса и, при необходимости, отремонтировать | |
При низком давлении появляются вибрации | Неправильно настроен максимальный объем насоса | Выполнить регулировку максимального расхода |
Слишком приближено к рабочему давлению компенсаторное давление. Неправильно выставлен компенсатор давления. Сломался золотник механизма управления. Повредились или переломались пружины золотника управления. Образовались задиры на золотнике или в отверстии. Повредились или переломались пружины цилиндра управления. Неисправности элементов в контуре удаленного компенсатора давления | Познакомиться с соответствующим разделом в руководстве, выпускаемом службой контроля за гидравлическим оборудованием | |
Сильные перепады давления | Слишком высоко установлен компенсатор давления. Слишком большой выставлен минимальный рабочий объем оборудования. Износились или повредились опорные поверхности люльки гидронасоса и седла опорных подшипников | Познакомиться с соответствующим разделом в руководстве, выпускаемом службой контроля за гидравлическим оборудованием Проверить и если нужно отремонтировать гидронасос |
Загрязнился канал между поршнем управления и золотником, нарушилась пловность хода поршня. Загрязнился канал от выходного канала к золотнику управления | Проверить и отремонтировать гидронасос | |
Рабочее давление гидронасоса длительное время превышает номинальные или пиковые значения. В резервуаре низкий уровень рабочего состава. Низкое давление на входе в гидронасос. | Проверить уровень жидкости в емкости выше линии всасывания | |
Воздух попал в гидросистему | Ликвидировать негерметичность соединений, позволяющих воздуху проникать в жидкость | |
Насос сильно нагревается | Износились опоры поршней и блока цилиндров. Износились или повредились поверхности сопряжения между блоком цилиндров и распределителем. | Проверить и при необходимости выполнить ремонт насоса гидравлического. |
Неисправность компонента схемы: предохранительный клапан работает непрерывно или допускаются утечки жидкости под высоким давлением. Плохое охлаждение теплообменника. Необходимо осмотреть теплообменник, промыть и очистить охлаждающие поверхности. Объем бака недостаточный | Ликвидировать утечки или заменить неисправные детали | |
Насос неправильно работает под нагрузкой или остановился | Убедиться в правильности управления | |
В резервуаре низкий уровень жидкости | Проверить уровень жидкости в емкости | |
Гидронасос издает чрезмерный шум | Появился воздух при всасывании. Износилась роторная группа насоса | Ликвидировать негерметичность всасывающего трубопровода. Заменить блок цилиндров, опорные подшипники, прижимные пластины, поршни, люльку. Выполнить ремонт гидравлического насоса |
Слишком большая вязкость жидкости | Выбрать правильно вязкость рабочей жидкости | |
Входной вал насоса вращается неправильно, в другом направлении | Проконтролировать и исправить, при необходимости, направление вращения вала. |
Мелкий ремонт насосов гидравлических не является серьезной проблемой, при наличии под рукой ремкомплекта.
Обычно в него входят:
- Запасные фильтры.
- Резинотехнические элементы.
- Уплотнительные втулки.
Совет: Приобретая гидронасос, необходимо проверить наличие всех комплектующих и инструкции по эксплуатации оборудования.
Как правильно выполнить ремонт насосов гидросистемы, более подробно подскажет видео в этой статье.
moikolodets.ru
Ремонт насосов и гидромоторов
Строительные машины и оборудование, справочник
Категория:
Техническое обслуживание дорожных машин
Ремонт насосов и гидромоторовОсновными ремонтируемыми узлами гидрооборудования строительных и дорожных машин являются гидронасосы и гидромоторы.
Ремонт шестеренных насосов. В шестеренном насосе изнашиваются стенки и дно колодцев корпуса, торцы шестерен и поверхности цапф, отверстия втулок под цапфу плоскости крышки, откалываются кромки буртиков крышки насоса под уплотнитель- ный сальник.
Шестеренный насос разбирают и ремонтируют, если производительность насоса меньше 60% от расчетной, т. е. когда объемный КПД (после замены уплотнения) меньше 0,6. Чтобы правильно контролировать этот показатель, необходимо различать обозначения гидравлических насосов. В маркировках НШ-10, НШ-32, НШ-46, НШ-100 цифра соответствует теоретической производительности нового насоса в кубических сантиметрах за один оборот шестерен.
При разборке насосов отвертывают болты, снимают крышку насоса и вручную вынимают детали. Съемник применяют только при снятии из гнезда нижней пары втулок. Поступивший первый раз в ремонт насос ремонтируют методом смещения шестерен концентричными втулками. Этот способ позволяет отремонтировать насос с наименьшими затратами, так как восстановление корпуса насоса сводится к одной операции — расточке колодцев на увеличенный размер. Насос собирают с эксцентриковыми втулками, величина смещения оси шестерен должна быть равна половине разности размеров головок зубьев шестерен и колодцев корпуса.
При большом износе поверхностей корпус подвергают пластической деформации — обжатию в горячем состоянии. Для этого его помещают в электронагревательную печь с автоматическим регулированием температуры и выдерживают 30 мин при температуре 500 °С. Затем корпус устанавливают в матрицу приспособления (рис. 130) и обжимают под прессом. Обжатие корпуса завершают при температуре не ниже 430 °С.
Обжатый корпус подвергают термической обработке: нагревают и выдерживают в течение 30 мин при температуре 520 °С, закаливают в воде при температуре 60—100 °С и отпускают в течение 4—6 ч при температуре 170—180 °С. У обжатого корпуса фрезеруют поверхности под табличку и крышку. Колодцы обжатого корпуса растачивают на токарном или фрезерном станке.
Для восстановления шестерен насосов шлифуют изношенные поверхности цапф, торцы и поверхности головок зубьев шестерен до ремонтных размеров на круглошлифовальном станке.
Рис. 130. Приспособление для обжатия корпуса насоса: 1— корпус насоса, 2 — выталкиватель, 3 — матрица, 4 — корпус пресс-формы, 5 — пуансон, 6 — верхняя плита
Втулки насосов ремонтируют способом пластической деформации — обжатием в холодном состоянии. Втулки и шестерни, являющиеся сопряженными деталями, подбирают по размерным группам так, чтобы длина каждой пары нижних втулок, шестерен и верхних втулок отличалась не более чем на 0,005 мм.
Резиновые уплотнительные кольца и манжету, потерявшие первоначальную упругость, заменяют. Собранный насос обкатывают и испытывают на стенде КИ-4200 или КИ-4815 на производительность. Установка шестеренного насоса на стенде КИ-4200 показана на рис. 131.
Режим обкатки: без давления — 4 мин, под давлением 2 МП а — 7 мин, 4 МПа — 5 мин, 7 МПа — 4 мин, 10 МПа — 12 мин и 13,5 МПа — пять циклов по 0,5 мин. Давление в нагнетательной магистрали регулируют дросселем.
Насосы испытывают на производительность при давлении 10 МПа и температуре масла 45—55 °С. Результаты испытаний должны соответствовать показателям, приведенным в табл. 18.
Производительность отремонтированного насоса должна быть не менее 90% расчетной, т. е. объемный коэффициент полезного действия.должен быть не менее 0,9.
Рис. 131. Установка шестеренного насоса на стенде КИ-4200: 1 — гайка, 2 — переходная плита, 3, 6 — переходные штуцера, 4 — приспособление для крепления насосов, 5— рука высокого давления, 7 — рукав низкого давления
Ремонт аксиально-поршневых гидронасосов и гидромоторов. Неисправностями гидронасосов и гидромоторов являются: износ поверхностей сфер шипа, блока цилиндров, шатуна, распределителя и ведущего вала; износ втулки блока цилиндров и износ поверхностей под подшипники; трещины на поршне и износ его диаметра. Все перечисленные детали входят в качающий узел, ремонту которого уделяется большое внимание.
В блоке качающего узла растачивают отверстия до выведения следов износа и притирают с распределителем. В распределителе качающего узла шлифуют сферическую поверхность, а затем азотируют ее и притирают с блоком качающего узла. Для узла шатун—поршень изготовляют поршень ремонтного размера, который закатывают с шатуном, шлифуют, азотируют и окончательно шлифуют; притирают сферу шатуна. В ведущем валу притирают сферические гнезда. В крышке люльки качающего узла шлифуют плоскости до выведения износа и притирают. В центральном шипе шлифуют посадочное место в распределителе на ремонтный размер и азотируют ремонтную втулку гнезда распределителя.
Поверхности под подшипники железнят и шлифуют. Втулку блока цилиндров заменяют и обрабатывают совместно с блоком цилиндров.
Поверхность полусфер ведущего вала обрабатывают на глубину 0,1 мм, торец вала — до восстановления полусфер по чертежу, которые затем притирают.
Блок цилиндров с распределителем притирают на специальном стенде, который имеет три шпинделя с опорными плитами и три механизма прижима и качания. Стенд можно использовать для притирки плоских поверхностей распределителя и крышек люльки.
Усилие прижима регулируют пружиной. Опорную плиту и привод механизма качания вращают электродвигателем через клиноременную передачу. Для притирки плоской поверхности на опорную плиту устанавливают чугунный притир диаметром 220—250 мм.
Рис. 132. Стенд для испытания насосов на герметичность: 1 — рама, 2 — электродвигатель, 3 — муфта, 4 — бак, 5 — предохранительный клапан, 6 — манометр, 7 — насос
Изношенную канавку ведущего вала фрезеруют под увеличенный размер, а при износе не более 0,2 мм зачищают стенки до выведения следов изнашивания.
Для испытания на герметичность насосов применяют специальный стенд (рис. 132). Рама стенда представляет собой сварную конструкцию и служит для установки на ней электродвигателя, насоса и бака.
Вращение вала насоса осуществляется электродвигателем через упругую муфту. В бак заливают масло, предназначенное для испытания насоса. На баке установлены фильтр, манометр 6 и предохранительный клапан, предназначенный для поддержания необходимого давления в гидросистеме при испытании насоса.
Испытуемый насос соединяют с напорной линией стенда штуцером и рукавом. Валы насоса стопорят специальными стопорами, включают электродвигатель и испытывают насос. Давление контролируют манометром.
Читать далее: Ремонт гидрораспределителей
Категория: - Техническое обслуживание дорожных машин
Главная → Справочник → Статьи → Форум
stroy-technics.ru