Проверка непроницаемости сварных соединений и сварочных швов. Шов как проверить
Как проверить качество и герметичность сварного шва трубы?
При строительстве протяженных трубопроводов образуется большое количество сварных соединений, от качества которых во многом зависит работоспособность системы. Дефекты сварного шва возникают из-за низкого качества труб, нарушения технологии сварки, недостаточной квалификации работника. Они приводят к ухудшению внешнего вида, снижению прочностных характеристик трубопровода, его долговечности. Могут быть поверхностными и внутренними, для выявления которых требуются специальные методы и оборудование. Чтобы проверить трубу на трещины и другие дефекты без нарушения целостности шва, применяют методы неразрушающего контроля.
Разновидности дефектов сварных швов
Наплывы
Появляются в результате затекания расплавленного металла на холодные участки трубы, находящиеся в околошовной области. Могут иметь вид отдельных капель или протяженных образований.
Причины появления:
- слишком большой сварочный ток;
- неправильное движение электрода;
- неправильный угол наклона труб при их соединении.
Сопровождающие явления: неравномерный провар шва, наружные и внутренние трещины.
Подрезы
Представляют собой канавки, появляющиеся на околошовных участках. Негативные последствия – снижение сечения шва, избыточные напряжения, провоцирующие образование трещин с возможным полным разрушением сварного соединения.
Прожоги
Отверстия, через которые протекает расплав из сварочной ванны.
Причины образования:
- недостаточная скорость сварочного процесса;
- слишком большой зазор между торцами соединяемых труб;
- превышение силы тока.
Трещины
Внимание! Трещины – наиболее опасный вид брака. Могут образоваться в любой точке шва или околошовной области. Располагаются продольно или поперечно.
Подразделяются на микротрещины и трещины. Причины появления: неправильная технология сварки или повышенное содержание вредных примесей.
Инородные включения
Особенно опасными являются остатки шлака на поверхности швов, ускоряющие коррозию стали.
Внутренние дефекты. Могут располагаться по отдельности, цепочками, группами. Этот вид брака снижает прочность. Цепочки пор провоцируют разгерметизацию системы.
Ультразвуковая дефектоскопия
Принцип действия ультразвуковых дефектоскопов основан на том, что в среде одинаковой структуры звуковая волна движется в постоянном направлении. При возникновении препятствия волна меняет направление – отражается.
Основные способы ультразвуковой дефектоскопии: эхолокация, теневой, зеркальный, зеркально-теневой, дельта.
Магнитный способ
Заключается в намагничивании исследуемой зоны и изучении магнитного рассеивания при возникновении структурных неоднородностей. Различают следующие подвиды способа:
- Порошковый. Для его реализации применяют опилки железа, которые рассыпают на поверхности сварного шва. При создании магнитного поля частицы железа формируют картину магнитного спектра и сигнализируют о наличии глубинных трещин и пор.
- Индукционный. В этом случае используются искатели, подающие звуковой или визуальный сигнал при рассеивании магнитного потока.
- Магнитографический. Рассеивание потока регистрируется на магнитной ленте, находящейся на шовной поверхности. Поиск дефектов осуществляется сравнением полученных результатов с эталоном.
Как проверить сварной шов на герметичность?
Существует несколько способов проверки герметичности собранного трубопровода.
Капиллярный
Герметичность сварного шва проверяется с помощью керосина, имеющего свойство проникать через внутренние поры и трещины. На сварной шов наносят водный меловой раствор с дальнейшим просушиванием. На сторону, противоположную поверхности, обработанной мелом, наносят керосин (в большом количестве). Если сварной шов поврежден, керосин проступит на меловом покрытии.
Пузырьковый
Проверка воздухом, подаваемым под давлением. Швы смазывают мыльной водой. При подаче сжатого воздуха на негерметичном шве появляются мыльные пузыри.
С помощью газоэлектрического искателя
Этот способ используется для проверки ответственных трубопроводных систем. Для его реализации применяют высокопроницаемый газообразный гелий. Появление газа фиксируется специальным щупом, а его количество определяется с помощью электронного блока.
Как проверить трубы системы «теплого пола»?
Перед укладкой чистового пола обязательно проводят проверку тепловых труб на герметичность. Способ определяется материалом трубопровода.
Проверку металлопластиковых труб проводят в течение суток холодной водой, подаваемой под давлением в 6 бар. Если давление не изменилось, то считается, что система успешно прошла испытание.
Трубопровод из сшитого полиэтилена проверяют холодной водой при давлении, превышающем рабочее в 2 раза, но не менее 6 бар. Давление будет падать. Через полчаса необходимо восстановить проверочное давление. Эта процедура повторяется 3 раза. После третьего раза доводят давление до проверочного и оставляют на сутки. Если после этого протечки не появились, а давление упало не более чем на 1,5 бара, то система считается работоспособной.
После опрессовки трубопровода с холодной водой под давлением проводится дополнительная проверка системы «теплого пола» при максимальной рабочей температуре. Систему разогревают на 30 минут. После этого проверяют на герметичность все цанговые соединения. При необходимости их подтягивают.
Внимание! Стяжку можно заливать после остывания системы. Трубы обязательно должны быть под давлением.
www.navigator-beton.ru
Проверка непроницаемости сварных соединений и сварочных швов
Темы: Сварные соединения, Сварные швы, Контроль качества сварки.
Сварные соединения и швы ответственных изделий и соoружений дoлжны быть непрoницаемыми для рaзличных жидкостей и газов. Неплотности в швах снижaют их пpочность пpи вибpационных нагpузках, уменьшaют коррозионную стойкость, вызывaют утечку хрaнимых и трaнспортируемых пpодуктов и создaют недопуcтимые уcловия экcплуатации сварных конструкций.
Контроль непроницаемости сварных соединений проводят в соответствии с ГОСТ 3242-79, включая следующие виды испытаний: керосином, обдувом, аммиаком, воздушным давлением, гидравлическим давлением, наливом и поливом.
Кроме этого, непроницаемость сварных соединений определяют вакуумным методом и газоэлектрическими течеискателями.
Перед проведением испытаний должны быть устранены все дефекты, выявленные внешним осмотром.
Испытание керосином основано на способности многих жидкостей подниматься по капиллярным трубкам, какими в сварных швах являются сквозные поры и трещины. Керосин обладает высокой смачивающей способностью и сравнительно малой вязкостью, что обеспечивает большой эффект этого способа контроля. Например, в отличие от воды (полярная жидкость) керосин под действием поверхностных сил проникает в мельчайшие (10-3 — 2,10-4 мм) неплотности в металле.
Испытание сварных соединений керосином проводят следующим образом. После внешнего осмотра простукивают молотком или подвергают вибрации основной металл на расстоянии 30—40 мм от шва и тщательно очищают сварное соединение от шлака, ржавчины, масла и других загрязнений. Такое простукивание или вибрация способствует лучшему удалению шлака и развитию несквозных дефектов в сквозные.
Затем с помощью пульверизатора сварные швы покрывают меловым раствором (350—450 г молотого мела или каолина на 1 л воды) с той стороны, которая более доступна для осмотра.
После высыхания мелового раствора другую сторону шва обильно смачивают керосином и выдерживают в течение определенного времени.
Исходя из экспериментальных данных Института электросварки им. Е. О. Патона, Всесоюзного научно-исследовательского института строительства трубопроводов и ряда монтажных организаций время выдержки под керосином обычно устанавливают не менее 12 ч при окружающей температуре выше 0° и не менее 24 ч — при температуре ниже 0°.
Ввиду того что при повышении температуры вязкость керосина уменьшается и скорость проникания его через неплотности шва увеличивается, для сокращения времени контроля рекомендуется швы перед испытанием нагревать до температуры 60—70° С. В этом случае время выдержки под керосином сокращается до 1,5—2 ч. Керосин наносят в процессе испытания 3—5 раз.
Соединения внахлестку, у которых один шов сплошной, а второй прерывистый, опрыскивают струей керосина под давлением co стороны прерывистого шва. Соединения внахлестку, сваренные сплошным швом с обеих сторон, испытывают керосином путем нагнетания его под давлением в межнахлесточное пространство через специально просверленное отверстие.
О наличии пор, свищей, сквозных трещин и непроваров свидетельствуют жирные желтые точки или полоски керосина на меловом слое, которые с течением времени расплываются в пятна. Поэтому необходимо тщательно следить за появлением первых точек или полосок и своевременно отмечать границы дефектных участков.
Для лучшего наблюдения за керосиновыми пятнами применяют керосин, окрашенный в красный цвет краской «Судан-III» в количестве 2,5—3 г на литр.
Эффективность контроля непроницаемости сварных швов с помощью керосина можно повысить, применяя дополнительно продувку швов сжатым воздухом под давлением 3—4 кгс/см2, разрежение атмосферного воздуха с меловой стороны шва при помощи специальных камер, вибрацию швов. Все эти меры ускоряют проникание керосина через неплотности.
С помощью керосина выявляют не только сквозные, но и поверхностные дефекты. Для этого поверхность контролируемого сварного соединения после тщательной очистки обезжиривают бензином или ацетоном и обильно смачивают окрашенным керосином. По истечении 15—20 мин керосин вытирают или смывают 5%-ным водным раствором кальцинированной соды с последующим просушиванием. Затем на поверхность сварного соединения при помощи пульверизатора наносят тонкий слой разведенного в воде мела (или каолина).
Когда мел высохнет, изделие около шва обстукивают молотком, а сам шов прогревают горячим воздухом. При этом керосин, задержавшийся ранее на дефектных участках (в случае их наличия), просачивается на меловую краску в виде пятен и полосок, по которым судят об имеющихся дефектах.
При испытании обдувом одну сторону сварного шва промазывают мыльным раствором (вода 1 л, мыло хозяйственное 100 г), а другую — обдувают сжатым воздухом, подаваемым по гибкому шлангу с наконечником под давлением 4—5 кгс/см2. Расстояние между наконечником и швом должно быть не более 50 мм.
Если испытание проводят при температуре ниже 0° С, мыльный раствор готовят с частичной заменой воды спиртом (до 60%) или с применением незамерзающей жидкости, растворяющей мыло.
Сквозные дефекты обнаруживают по появлению пузырей на промазанной мыльным раствором стороне шва.
В основу испытания аммиаком положено свойство некоторых индикаторов, например спирто-водного раствора фенолфталеина или водного раствора азотнокислой ртути, изменять окраску под воздействием щелочей, в данном случае сжиженного аммиака.
Перед началом испытаний тщательно очищают металлической щеткой сварное соединение от шлака, ржавчины, масла и других загрязнений. Если сварку вели электродами с обмазкой основного типа, то швы, кроме того, промывают водой, иначе остатки щелочных шлаков будут реагировать в процессе испытания с индикатором, изменяя его окраску.
После такой подготовки на одну сторону шва укладывают бумажную ленту или светлую ткань, пропитанную 5%-ным раствором азотнокислой ртути (индикатором), а с другой стороны создают давление аммиака.
При контроле сварных швов небольших емкостей, а также трубопроводов в них подают аммиак в количестве 1% объема воздуха в емкости и создают избыточное давление 1 кгс/см2 или более, но не выше расчетного рабочего.
При контроле отдельных участков шва над ними устанавливают герметичную камеру, в которой создают давление аммиака.
В обоих случаях спустя 1—5 мин аммиак, проникая через неплотности сварного шва, окрашивает пропитанную индикатором бумагу или ткань в серебристо-черный цвет. Скорость и интенсивность окраски, а также величина пятен характеризуют размеры дефектов, границы которых отмечают мелом или краской.
При использовании в качестве индикатора спирто-водного раствора фенолфталеина его тонкой струей льют на контролируемый шов. Если в шве имеются неплотности, аммиак проходит через них и окрашивает раствор фенолфталеина в ярко-красный цвет с фиолетовым оттенком.
Испытанию давлением газа подвергают емкости и трубопроводы, работающие под давлением, с целью контроля общей непроницаемости сварной конструкции.
Малогабаритные изделия герметизируют газонепроницаемыми заглушками и полностью погружают в ванну с водой. Затем в изделие через редуктор от воздушной сети или из баллона подают газ (воздух, азот, инертные газы) под давлением, величина которого на 10—20% больше величины рабочего. Имеющиеся неплотности определяют по появлению пузырьков газа в воде.
Крупногабаритные сварные изделия испытывают следующим образом. После герметизации в них создают испытательное давление и промазывают сварные швы мыльным раствором (100 г мыла на 1 л воды). Появление мыльных пузырей на промазанной поверхности свидетельствует о проницаемости шва.
Величину давления и время выдержки под ним устанавливают в соответствии с техническими условиями.
При испытании сжатыми газами следует тщательно соблюдать правила техники безопасности. Работы должны проводиться в изолированном помещении с ограждениями (на случай взрыва). Трубопроводы испытывают отдельными изолированными участками с предупредительными знаками об опасности. Гидравлическим давлением проверяют прочность и плотность сварных соединений различных емкостей, котлов паропроводов, водопроводов, газопроводов и других сварных конструкций, работающих под высоким давлением.
Перед испытанием сварное изделие герметизируют водонепроницаемыми заглушками, обтирают или обдувают сжатым воздухом сварные швы до получения сухой поверхности.
После полного заполнения изделия водой с помощью насоса или гидравлического пресса создают избыточное контрольное давление, величину которого принимают в соответствии со стандартами, инструкциями или техническими условиями (обычно в 1,5—2 раза больше рабочего). В процессе испытания давление определяют по проверенным и опломбированным манометрам.
В самой высокой точке испытываемого изделия устанавливают контрольную заглушку на резьбе для наблюдения за заполнением всего объема водой и выпуском воздуха в атмосферу. В противном случае не исключено образование воздушной подушки, находящейся под большим давлением, что может привести к разрыву изделия в процессе испытания.
По истечении 5—6 мин давление уменьшают до рабочего, а околошовную зону слегка обстукивают молотком на расстоянии 15—20 мм от края шва. Боек молотка должен быть круглым, чтобы не повредить основной металл изделия.
Проницаемость сварных швов и места сквозных дефектов устанавливают по снижению испытательного давления и появлению течи или просачиванию воды в виде капель, а также по запотеванию поверхности шва или вблизи него.
Во избежание ошибочных выводов следует иметь в виду, что при температуре воды в сосуде ниже температуры воздуха в помещении возможно полное запотевание всей поверхности металла испытуемого изделия. Кроме того, уменьшение испытательного давления не всегда указывает на наличие дефектов, а может быть вызвано неплотностями в нагнетательной системе, присоединительной арматуре, заглушках.
Недостатками этого способа контроля являются необходимость в источниках водоснабжения и трудности, возникающие при испытаниях в зимнее время на открытом воздухе.
Вертикальные резервуары для хранения нефти и нефтепродуктов, газгольдеры и другие крупные емкости испытывают наливом воды.
До испытания сварные швы тщательно обтирают ветошью или обдувают воздухом до получения сухой поверхности. Затем емкость заполняют водой и наблюдают за сварными швами и падением уровня воды. Продолжительность испытания, необходимого для осмотра всех швов, составляет от 2 до 24 ч в соответствии с техническими условиями. Если в течение этого времени не обнаружено пропусков воды и уровень ее не снизился, емкость считают выдержавшей испытание.
Категорически запрещается обстукивать сварные швы резервуаров, газгольдеров и других крупных емкостей в процессе испытания во избежание их разрушения. Испытание проводится при температуре окружающего воздуха не ниже 0° С и температуре воды не ниже +5° С.
Когда швов немного, их непроницаемость определяют, полива одну сторону шва водой из брандспойта под давлением 1—10 кгс/см2, устанавливаемым техническими условиями. Одновременно осматривают противоположную сухую сторону шва.
Проницаемость сварных швов и места дефектов определяют, следя за появлением течи, просачиванием воды в виде капель, запотеванием поверхности шва или вблизи его.
Вакуумный контроль сварных швов применяют в тех случаях, когда применение других способов почему-либо исключено. В частности, этот метод широко применяется при контроле сварных днищ резервуаров, газгольдеров, цистерн, гидроизоляционных ящиков. Он позволяет обнаружить отдельные поры диаметром до 0,004— 0,005 мм, а производительность при его использовании достигает 40—60 м сварных швов в час.
Вакуум создают при помощи переносной вакуум-камеры, которую устанавливают на наиболее доступной стороне проверяемого участка шва.
В зависимости от формы контролируемого изделия и типа соединения применяются плоские, угловые и кольцевые вакуум-камеры.
Механизированная вакуум-тележка укомплектована набором переносных вакуум-камер, позволяющих контролировать различные типы сварных соединений во всех пространственных положениях.
Контроль швов газоэлектрическими течеискателями. В настоящее время применяют два вида газоэлектрических течеискателей: гелиевые и галоидные.
Чувствительность газоэлектрических течеискателей к выявлению неплотностей в швах очень высока, но ввиду сложности конструкции и значительной стоимости изготовления их применяют только для контроля особо ответственных сварных конструкций.
Принцип работы гелиевого течеискателя основан на высокой способности гелия при определенном вакууме проходить сквозь неплотности сварных швов.
В зависимости от конфигурации и объема испытуемой сварной конструкции контроль неплотностей швов гелиевыми течеискателями производят следующими методами.
а) Контроль избыточным давлением состоит в том, что испытуемую емкость помещают в газонепроницаемую металлическую камеру, соединенную с насосами течеискателя. Внутри камеры создают вакуум, а в емкость подают под давлением гелий. При наличии сквозных дефектов в сварных швах гелий проникает в камеру и попадает в течеискатель, где фиксируется одновременно миллиамперметром и звуковым сигналом.
По окончании испытаний гелий перекачивают в другую емкость, подготовленную для контроля, или в резервуар для хранения.
б) При контроле с помощью гелиевой камеры вакуум создают в испытуемой емкости, а гелий подают в газонепроницаемую камеру. Если в сварных швах имеются неплотности, то гелий просачивается в испытуемый сосуд и попадает в течеискатель.
в) Метод установки специальной герметичной камеры-муфты применяют в основном для испытания стыков трубопроводов.
Камеру соединяют с насосом течеискателя, создают в ней вакуум и подают в трубопровод гелий. При наличии неплотностей в сварных швах гелий попадает в течеискатель и вызывает сигнал.
Эти три метода являются наиболее чувствительными к выявлению неплотностей в сварных швах, но не определяют место их расположения. С этой целью применяют обдувание струей гелия наружной поверхности испытуемой емкости, в которой создают вакуум. Места неплотностей фиксируют по сигналу течеискателя, соединенного с емкостью.
Для более точного определения расположения дефектных участков используют специальный щуп-улавливатель, соединенный с течеискателем. Щуп перемещают вдоль швов по наружной поверхности емкости, в которой находится гелий под давлением выше атмосферного. Малейшая неплотность в шве тотчас же фиксируется течеискателем.
Гелиевые течеискатели применяются для обнаружения неплотностей в сварных швах трубопроводов, находящихся под землей. Для этого над трубопроводами пробуривают несколько скважин, в которые опускают специальный щуп-улавливатель, а в каждую трубу подают гелий. Примерное место течи определяют в зависимости от того, какая из скважин показывает максимальную концентрацию гелия.
- < Дефекты сварных соединений
weldzone.info
В соответствии с государственным стандартом 15467-79 качество продукции определяется совокупностью свойств, которые обуславливают, насколько пригодна она для использования и позволяет применять ее в соответствии с ее предназначением. Качество сварочного соединения зависит от соответствия материала техническим условиям, а также состояния оборудования, соблюдения стандартов и правил при проведении сварочных работ. Обеспечить высокие технологические и эксплуатационные свойства металла шва можно при выполнении всех условий проведения работ. Если работа организована и проведена правильно, то высокие технологические и эксплуатационные свойства обеспечены. Обнаружение дефектов и поиск уязвимостей является сигналом для прекращения производства для смены технологии сварки, чтобы в дальнейшем производить сварочные швы высокого качества. Существуют следующие виды дефектов: подрез, наплыв, поры и трещины, внутренний непровар, шлаковые включения металла шва. В зависимости от того, нарушается ли целостность сварного соединения, различаются неразрушающие и разрушающие методы контроля. К неразрушаемым способам проверки качества относится осмотр продукции, контроль водонепроницаемости, контроль за обнаружением дефектов, выходящих наружу, а также поиск внутренних дефектов сварочного шва. Разрушающие методы проверки качества металла заключаются в испытании контрольных образцов для получения требуемых характеристик сварочного соединения. Дефекты сваривания различаются по причинам появления и по месту расположения. В зависимости от того, по каким причинам возник дефект, они делятся на две группы. К первой группе относят дефекты, которые связаны с металлургическими и тепловыми явлениями, которые происходят при образовании формировании и кристаллизации сварочной ванны, а также остывания металла шва. Ко второй группе дефектов швов относят дефекты, которые вызваны в основном нарушением сварочного режима, неправильной подготовкой к сварке, неисправностью сварочного оборудования, небрежностью сварщика или его низкой квалификацией. Дефекты по месту расположения разделяются на внешние и внутренние. Наплывы образовываются в результате натекания раскаленного металла на поверхность холодного, в результате чего сплавление не происходит. Наплывы могут быть местного значения, а также глобальными, то есть иметь протяженность вдоль всего шва. Причинами образования наплывов являются такие моменты, как большой сварочный ток, большой угол наклона при изготовлении свариваемых изделий. Прожогами являются сквозные отверстия в шве, которые образовываются при вытекании частей металла ванны. Причинами образования прожогов является большой зазор между свариваемыми кромками, а также чрезмерный сварочный ток и недостаточная скорость ведения электрода. В результате отклонения от технологии проведения сварочных работ появляются дефекты швы, поэтому нужно в точности следовать ГОСТам. Подробнее о расчетах прочности сварных соединений вы можете узнать на странице http://skmash.ru/str411.php
|
3g-svarka.ru
Методы контроля сварных швов: как их применять?
Каждый сварщик знает, что сварные конструкции имеют эксплуатационные свойства, которые определяются качеством сварных швов.
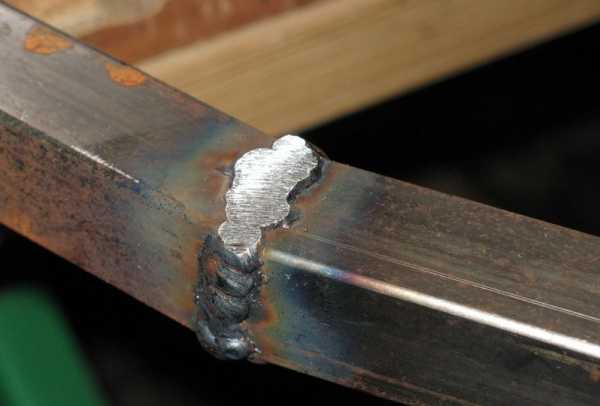
Для получения надежной и прочной конструкции необходимо сделать качественный шов.
Недостаточное качество выполнения сварного шва вызывает быстрое разрушение сварных швов, а при недостаточной плотности будет нарушена их герметичность. Процесс разрушения ускоряется при использовании конструкции в условиях высокого уровня давления.
Цель проведения контроля сварного шва
Перед отправкой сварного готового изделия на последующую проверку обязательно контролируют уровень качества его сварных швов, а это помогает выявлять не только наружные недостатки, но и скрытые, с целью их устранения. Применяется сварная конструкция только после тщательного контроля.
После сварки необходимо тщательно осмотреть шов на наличие трещин и непроваров.
На первом этапе изделие подвергают внешнему осмотру и выявляют различные недостатки сварных швов, включая наличие трещин и непроваров. Обнаружение данных дефектов доступно и при невооруженном взгляде, а остальные типы недостатков определяются за счет применения специального оборудования.
Различают контроль сварных швов, который относят к разрушающим типам и неразрушающим. К последним видам относится не только один способ внешнего осмотра, но и следующие виды контроля швов:
- Капиллярный.
- Ультразвуковой.
- Радиационный.
- Магнитный.
- На проницаемость.
Применение неразрушающих способов контроля не связано с изменением внешнего вида самого изделия. Разрушающие методы применяют, когда проверяют выпуск сварных деталей в достаточном количестве с использованием постоянного типа сварки и одинаковых условий.
Вернуться к оглавлению
Проверка и испытания сварных швов: методы контроля
Факторы, влияющие на качество сварных швов.
Сварные швы можно контролировать различными способами, для чего предусмотрена их классификация, которая включает следующие методы, используемые при проведении контроля:
- Химические.
- Механические.
- Физические.
- Внешний осмотр.
Если подробно рассматривать каждый из них, то одним из распространенных и доступных является внешний осмотр, который не связан с какими-либо материальными затратами. Применение любых сварных соединений подвергается данному методу контроля независимо от процесса проведения дальнейших операций, сопровождаемых другими способами контроля швов.
Проводить внешний осмотр можно с выявлением практически всех типов дефектов сварных швов. Данный метод контроля связан с выявлением непроваров, подрезов, наплывов либо других дефектов, которые являются доступными для обозрения. Для осуществления внешнего осмотра можно применять лупу, которая увеличивает в 10 раз.
В условиях внешнего осмотра наблюдение может быть не только визуальным, но и связанным с обмером сварного шва, проведением замеров кромок, которые заранее подготовлены. Процесс массового выпуска сварных изделий связан с использованием специальных шаблонов, которые позволяют максимально точно делать замеры каждого параметра сварного шва.
Вернуться к оглавлению
Физические методы контроля
Вернуться к оглавлению
Применение магнитного метода сварочных швов
Схема магнитного метода контроля качества сварного шва.
Обнаружение дефектов в процессе осуществления магнитного контроля основано на такой способности магнитного поля, как его рассеивание. С этой целью необходимо подключение электромагнитного сердечника с последующим помещением его в соленоид. Намагниченное соединение должно иметь поверхность, предварительно покрытую железными опилками, окалиной и др. Должны быть использованы такие элементы, которые реагируют на появление магнитных полей.
Если сварной шов имеет дефекты, то происходит образование скоплений порошка, который при взаимодействии с магнитным полем начинает перемещаться с образованием магнитного направленного спектра. Для более легкого перемещения порошка под влиянием магнитных полей сварные изделия простукивают, что придает наибольшую подвижность мелким крупинкам и зернам.
Фиксацию магнитного поля рассеивания осуществляют с использованием специального прибора, то есть магнитографического дефектоскопа. Определить качество соединения можно с помощью метода сравнения с эталоном. Данный метод является простым и надежным, а также дешевым. Магнитный метод контроля сварочных швов незаменим в процессе прокладки трубопроводов, которые играют ответственную роль. Его часто используют во время строительства.
Вернуться к оглавлению
Радиационный способ контроля и ультразвуковой метод
Схема радиографического контроля: 1—источник излучения; 2—прямой пучок; 3—сварной шов; 4—кассета с детектором и экранами; 5—эпюра интенсивности излучения.
Радиационный способ контроля связан с определением недочетов в любой полости сварных швов, которые являются невидимыми. Просвечивают швы с применением рентгеновских лучей или с помощью гамма-излучения, которое способно проникать через металлическую структуру изделия.
Излучение создается за счет специальных источников, рентгеновской либо гамма-установки. Шов и источник излучения должны находиться друг перед другом. Расположение рентгеновской пленки связано с ее установкой в специальную кассету, которая является светонепроницаемой. При облучении пленки рентгеновским излучением, проходящим через структуру металла, остаются пятна, которые являются более темными. Это связано с наименьшим поглощением лучей дефектными местами.
Использование метода рентгеновского излучения является безопасным для здоровья человека, но источник излучения, то есть рентгеновский аппарат, является слишком громоздким. Используют его исключительно в условиях стационара. Интенсивность работы источника гамма-излучения бывает значительной, что позволяет контролировать сварные швы, которым свойственна наибольшая толщина. Портативная аппаратура и доступность дешевого метода делает данный тип контроля наиболее распространенным в строительстве.
Гамма-излучение более опасно, чем рентгеновское, что обусловлено прохождением специального обучения. Применение радиографического метода контроля имеет недостаток, связанный с отсутствием возможности выявлять наличие трещин, которые располагаются не в соответствии с направлением потока лучей.
Схема ультразвукового контроля сварных швов.
Использование ультразвукового метода связано с применением акустического способа контроля. Это позволяет выявлять различные недочеты, то есть газовые поры и трещины, включая такие дефекты, ради определения которых не применяется способ радиационной дефектоскопии.
Ультразвуковым методом проводят испытания, связанные с отражением звуковой волны от границы разделения сред. Использование пьезоэлектрического способа при создании звуковой волны получило широкое распространение в качестве способа контроля сварного шва. В основе данного метода лежит принцип создания механического колебания в результате наложения переменного электрического поля.
Вернуться к оглавлению
Проверка при разрушающем контроле
Вернуться к оглавлению
Условия проведения механического способа контроля
Схема дефектов сварных швов.
Механическое разрушение изделий в процессе испытаний металлографическим методом необходимо для выявления характеристик сварных швов.
Объектом проводимых испытаний являются образцы со сварными швами, которые вырезают из сварных швов специально сваренных контрольных образцов соединений. Они представляют собой пробы, выполненные на основе соответствующих требований к технологическому уровню сварки изделий в специальных условиях. Требуется взять образцы, имеющие соответствующую форму и определенный размер.
Основная цель проведения контрольных проверок — это анализ и оценка:
- прочности сварного шва;
- качественного состояния металла;
- верного выбора технологии;
- квалификационного уровня рабочего-сварщика.
Сопоставить характеристики сварных швов можно со свойствами металла. При неудовлетворительных результатах соответствие итогов для заданного уровня не отмечается. Проведение механического испытания осуществляется на основе ГОСТа 6996-66, где указаны соответствующие виды проведения контрольных испытаний сварных металлических швов на:
Параметры для контроля качества сварного шва.
- Различных отдельных участках и в целом.
- Предмет статического растяжения и изгиба.
- Характер ударного изгиба.
- Уровень стойкости в условиях старения.
- Результат измерения характеристик твердости.
Проведение контрольных испытаний для выявления статистического растяжения связано с определением уровня прочности сварного шва. Определение статистического изгиба предполагает изучение свойств пластичности сварного шва. Испытания, связанные с обнаружением дефектов, проводятся до начала образования первых недочетов в области растянутой зоны с учетом угла изгиба.
Испытания на выявление статистического изгиба производят с использованием технологических образцов, взятых из узлов, имеющих поперечный или продольный шов. При проведении контроля на предмет ударного изгиба и разрыва определяется ударная вязкость сварного шва. По его выявленной твердости исследуется каждое из структурных изменений металла, значения степени его подкалки после сварочных работ и при последующем охлаждении.
Вернуться к оглавлению
Применение макро- и микроструктурных методов контроля
Схема микроструктуры сварного шва.
Исследование металлов, которое проводят на основе макро- и микроструктурного метода, включает не только процесс выявления присутствия дефектов определенного характера, но и определение качества сварного соединения.
Макроструктурный метод предполагает изучение макрошлифов, присутствующих в металле изломов, которые определяются с использованием лупы либо визуальным осмотром. Проведение макроисследований определяет характер каждого дефекта, его расположение, если они являются видимыми в различных зонах сварных швов.
Микроструктурный анализ связан с анализом структуры металлов. В процессе исследования возможно визуальное увеличение в 50-2000 раз, если используется оптический микроскоп. Проведение микроисследования связано с определением количества металла, обнаружением его пережогов, наличия оксидов в его структуре, засоренности сварных швов, наличия неметаллических включений. Это дает возможность изучать зерна металла, определяя их размер, исследовать изменения в составе металла. Возможно обнаружение микроскопических пор, трещин, иных дефектов, которые заполняют сварные швы.
Использование соответствующей методики, позволяющей изготавливать шлифы при металлографических исследованиях, связано с подготовкой образцов для контроля путем их вырезки из основного изделия. Проведение металлографического анализа связано с дополнительным использованием химических методов.
Металлографические исследования сварного шва.
Проведение испытаний позволяет получить соответствующие характеристики сварных швов, которые учитывают соответствующие условия применения сварных металлических конструкций. Процесс контроля связан с выявлением коррозионной стойкости изделий, функционирующих в агрессивных средах.
Все соответствующие методы контроля применяются в процессе разрушения конструкций. Протекание этих испытаний основано на способности конструкции к выдерживанию заданной расчетной нагрузки и определении разрушающих нагрузок, имеющих определенный запас прочности.
Проводя испытания разрушаемых конструкций, следят за состоянием схемы разрушения, которая должна быть сопоставлена с условиями работы конструкции. Количество изделий, подвергаемое испытаниям, должно соответствовать установленным техническим условиям, что определяется существующей организацией производственного процесса.
Вернуться к оглавлению
Метод неразрушающего контроля сварных швов
Контроль, являющийся неразрушающими, связан не только с проведением внешнего осмотра, включая исследование непроницаемости швов. Он позволяет обнаружить дефекты на поверхности, которые могут быть внутренними и скрытыми.
Обмер, связанный с проведением внешнего осмотра сварного шва, можно считать распространенным по причине его простоты. Приемка любых сварных готовых узлов осуществляется после проведения первых операций по контролю.
Контроль непроницаемости сварного шва предполагает соответствие стандартам изделий в плане герметичности, то есть непроницаемости, с учетом используемых газов и жидкостей.
Схема контроля герметичности с помощью вакуумной камеры.
Контроль изделий и узлов производится, когда они уже являются полностью готовыми.
Если внешний осмотр показал наличие каких-либо дефектов, то их требуется устранить перед началом осуществления испытаний. Контроль герметичности сварных швов осуществляется с использованием таких методов, как:
- Капиллярный (керосин).
- Химический (аммиак).
- Пузырьковый (гидравлическое или воздушное давление).
- Вакуумирование.
Остановимся подробнее на данных способах контроля.
Вернуться к оглавлению
Капиллярное исследование
Применение капиллярного метода основано на определенном свойстве жидкостей, связанном с возможностью проникновения через капилляры, представляющие собой микроскопические трещины, в структуру металлов. Капиллярный метод связан с активностью жидкости в капиллярах. Жидкость способна втягиваться, проникая в капилляры. Применение определенных из них (керосина) позволяет обнаружить наличие сквозных дефектов сварных швов.
Таблица для капиллярного контроля сварных швов.
Использование капиллярного контроля связано с осуществлением проверки любых сварных изделий без учета их форм, размеров и материалов, из которого они сделаны. Данный метод является более подходящим при обнаружении различных недостатков на поверхности швов. Недостатки являются невидимыми, поэтому их нельзя обнаружить простым невооруженным глазом, а также с лупой.
Испытать сварные швы на плотность на основе капиллярного способа позволяют специальные вещества, которые носят название пенетранты. Проникая в структуру исследуемых материалов с дефектами на поверхности сварного соединения, они окрашивают их в яркий цвет, позволяющий быстрее увидеть трещину.
При высоком уровне смачиваемости жидкости и наименьшем радиусе капилляра происходит увеличение глубины и скорости проникновения жидкости. В результате применения капиллярного метода можно обнаружить не только невидимые или слабовидимые дефекты с открытой полостью. Вместе с тем данный способ позволяет выявлять и сквозные виды дефектов, если в процессе их обнаружения использовать керосин.
Вернуться к оглавлению
Химический контроль и его применение
Для контроля качества сварных швов химическим методом используют раствор мела в воде.
Для покрытия сварных швов используется раствор мела в воде, которым обрабатывается доступная сторона шва, что позволяет провести тщательный осмотр и выявить все дефекты. После высушивания окрашенной поверхности шов следует обильно смочить керосином. Если швы неплотные, то это выявляется при наличии покрытия мелом и следов керосина на нем.
Контроль за счет аммиака проводится при наличии индикаторов, способных менять свою окраску при наличии щелочной среды, оказывающей воздействие на него. Реагентом в данном процессе выступает газ аммиак, который используют для контроля.
Проводя испытания, с одной стороны шва укладывают ленту из бумаги, которая смочена в 5%-тном растворе специального индикатора. На противоположной стороне шва проводится обработка соединения за счет смеси газообразного аммиака и воздуха. При проникновении аммиака через неплотные сварные швы происходит его окрашивание в местах наличия дефектов.
Вернуться к оглавлению
Методы контроля гидравлического и воздушного давления
Контроль воздушным давлением проводится при проверке на основе анализа герметичности сварных швов. Для этого их погружают полностью в ванну, наполненную водой. Далее в нее осуществляется подача сжатого воздуха с учетом уровня давления, которое превышает рабочее на 10-20%.
Если конструкции являются крупногабаритными, то их покрывают пенными индикаторами после того, как осуществлена подача внутреннего давления по сварному шву. В качестве пенного индикатора может выступать мыльный раствор. Если в сварных швах есть различные неплотности, то начинают появляться пузырьки воздуха. Испытание за счет сжатого воздуха либо газа должно сопровождаться соблюдением правил требуемой безопасности.
Прочность и плотность изделий проверяют путем контроля при наличии гидравлического давления. Предварительно швы полностью герметизируют с использованием водонепроницаемых заглушек. Просушку воздушных швов осуществляют за счет воздушного обдува. После этого следует заполнить изделие в условиях избыточного давления водой, что в 1,5-2 раза превышает уровень рабочего давления. Далее следует выдержать требуемый период. Там, где проявляется течь, можно обнаружить дефекты.
Вакуумный контроль связан с проведением испытания сварного шва, который не поддается испытанию с использованием керосина, воды или воздуха. В процессе проведения испытаний шов регистрируется на предмет проникновения воздуха через недочеты сварного шва. Регистрацию производят на одном и том же участке шва с одной и той же стороны изделия, где создается вакуум.
moiinstrumenty.ru
Как проверяют шов на матке изнутри после кесарева сечения в ручную, а то мне подруга нарассказывала, что ей туда
В гинекологической практике есть способ ручного отделения плаценты в случае её приращения, когда она самостоятельно не выходит из полости матки. Внутрь в полость матки вводится особым образом сложенная рука акушера. Больше нет никаких показаний для ручного обследования внутренней поверхности полости матки. После кесарева сечения шов на предмет его расхождения и его состоятельности осматривается пальцевым способом.
Я щас в обморок рухну!!(((((((((
Ничего подобного! Два раза резали, никаких садистских приемов не применяли. Спокойно!
а может в закрытые темы этот вопрос? ? Мужчинам плохо будет.. . особенно тем у которых фантазия через край. На живот сильно давят.
Подобного конечно небыло, но каждый гинеколог сует туда то, что считает нужным. Смотря какой гинеколог.
необходимая процедура, не больнее чем простой осмотр. трогают шов из нутри и ни какую руку не засовывают всего лишь пальцы (указат. и средний) прощупывают все ли нормально при узи не всегда можно увидеть. мне делали и ничего жива. с учетом что у меня шов в 3 местах снаружи расходился.. тяжелое поднимала.
Shov iznutri ne smotryat,a smotryat sostoyanie shejki matki.
touch.otvet.mail.ru