Особенности полуавтоматической и автоматической сварки. Сварка полуавтоматическая и автоматическая
Автоматическая и полуавтоматическая сварка: скорость и нюансы (видео)
Полуавтоматическая сварка и автоматическая позволяют получить высокую точность шва. Такая сварка имеет много преимуществ, нежели обычная ручная, поскольку процесс не зависит от уровня квалификации рабочего. Исходя из этого, можно проследить значительную экономию финансов, так как если работать с мастером высокой квалификации, то можно получить хорошее качество, но при этом высокую стоимость. Если же экономить на уровне квалификации, в данном случае будет страдать качество сварки.
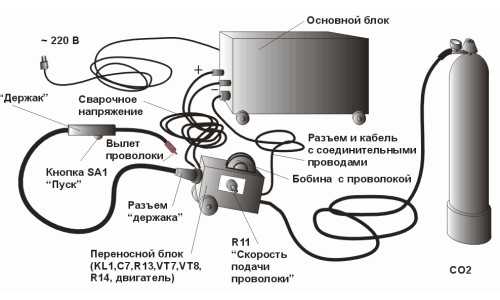
Схема устройства сварочного полуавтомата.
Сущность автоматизированного процесса состоит в механическом перемещении электрода вдоль шва и подачи электрода в дугу. Автоматически поддерживается длина дуги. Особенности полуавтоматической сварки состоят в том, что происходит механизированная подача электрода непосредственно в зону сварки, однако электрод вдоль шва перемещается вручную. Полуавтоматом работать несложно: это некая альтернатива между ручной и автоматизированной работой.
Принципы, которые вложены в работу полуавтоматической дуговой сварки, и ее особенности
Дуговая сварка встречается двух видов: это автоматическая и полуавтоматическая дуговая сварка. Автомат прекрасно подойдет для массового производства или серийного. Для мелкосерийного лучше всего использовать полуавтомат. В индивидуальном случае применяют ручную дуговую сварку. Не всегда для предметов, на которых нужно осуществить сваривание, хорошо подходит автоматический процесс. Например, сварные швы могут быть короткими или иметь достаточно сложную конфигурацию, а также могут быть неудобно расположены. Существует несколько вариантов полуавтоматической дуговой сварки:
- Сварка, которая производится с помощью лежачего электрода или наклонного.
- Шланговая сварка.
Классификация дуговой сварки.
В первом случае используется электрод, который имеет толстую смазку, ложится на предмет, который прикрыт писчей бумагой. После этого на него ложится большой прижимной брусок, который обязательно должен быть из меди. В этом бруске необходимо наличие канавки, которая позволит передвигаться электроду. К электроду подводится сварочный ток. Он крепится на свободный от смазки конец, который для удобства имеет согнутую форму.
Зажигание дуги происходит специальным зажигательным стержнем, который подносят к концу электрода, что примыкает к изделию.После загорания дуга временно становится невидимой, поскольку она ползет под брусок по электроду, расплавляя его. Таким образом, вдоль него формируется наплавленный валик. Длина самого электрода и определяет длину шва, который необходимо наплавить. Чтобы изменить ее, следует просто взять электрод необходимой длины. Он может иметь до 12 см вдоль и до 0,8 см в диаметре.
Если воспользоваться вторым вариантом, то можно изменять сечение наплавленного металла в зависимости от изменения угла. Для этого существуют определенные пределы. Что в первом, что во втором вариантах электрод опирается на изделие, при этом стержень в обоих случаях изолируется от предмета благодаря обмазке, которая выступает так называемым козырьком.
Вернуться к оглавлению
Шланговая полуавтоматическая дуговая сварка
Схема полуавтоматической шланговой сварки.
Вместе с другими видами, данный вариант сварки получил достаточно широкое распространение. Изначально в шланговых полуавтоматах использовалась уникальная система сварки: она производилась за счет электродной тонкой проволоки, которая имела диаметр 4-5 мм.
Вся работа осуществлялась на маленьких сварочных токах. Из-за того, что проволока имела большой диаметр сечения, сам шланг был тяжелым и неудобным, поскольку не мог обеспечить необходимую гибкость при работе. К тому же из-за маленькой производительности не достигался необходимый результат, поэтому предпочтение отдавали применению ручной сварки.
Созданию более удобного шланга для сварки послужило уменьшение толщины проволоки до 0,2 — 0,25 см, а также ее покрытие флюсом — это дало возможность увеличить сварочный ток. Теперь шланг стал более гибким, не таким тяжелым и удобным для работы.
Вернуться к оглавлению
Сварка под флюсом, ее основные возможности и принцип работы
Автоматическая и полуавтоматическая сварка под флюсом — это высокопроизводительный процесс, поскольку она позволяет хорошо обеспечить технологичность в производстве. Чаще всего используется для изготовления и соединения технологических трубопроводов.
Схема сварки под слоем флюса.
Принцип ее действия состоит в том, что сварочная дуга находится между предметом, который непосредственно сваривается и электродной голой проволокой. При этом она плотно прикрыта слоем сыпучего вещества, которое и называется флюсом. Он практически выполняет ту же самую роль, что и прикрытие сварочной дуги при ручной сварке. К тому же можно не прикрывать глаза защитными приспособлениями, поскольку флюс полностью закрывает источник горения, поэтому опасность их повредить сильно уменьшается.
Такой процесс осуществляется благодаря сварочной головке. В автоматическом процессе она перемещается, соответственно, автоматически, а вот при использовании полуавтомата головка вдоль шва перемещается вручную.
Подготовке кромок сварных труб для автомата и полуавтоматической сварки уделяют больше внимания, чем ручной. Это объясняется тем, что обеспечивается большая жидкотекучесть и точность в процессе, поэтому необходимо при сборке установить одинаковые зазоры и разделки фасок.
Только при таком условии можно получить идеально точный размер и толщину шва, а также отличное качество и отлаженную производительность процесса.
Благодаря тому, что повышается коэффициент наплавки, увеличивается плотность тока и растет скорость самой сварки. Полуавтоматы могут увеличивать производительность под слоем флюса практически от 2 до 5 раз больше, чем ручная сварка.
Вернуться к оглавлению
Варианты использования флюса в зависимости от характеристик стали
По характеристикам стали определяют, какую именно марку флюса нужно применить, например:
- низкоуглеродистая или малоуглеродистая сталь — применяются флюсы ФЦ-9, АН-348А, ОСЦ-45;
- высоколегированные стали — используется флюс ФЦЛ-2;
- углеродистые и легированные стали — необходим флюс неплавленный керамический КВС-19 или К-2;
Что касается всех остальных труб, то для сварки обычно используется холоднотянутая калиброванная проволока.
Диаметр такой сварочной проволоки от 0,3 до 12 мм. Однако наиболее часто используется сечение от 0,8 мм до 5 мм. Ее химический состав может быть различным.
Вернуться к оглавлению
Сварочный пост и его конструкция
Схема соединения сварочного поста.
Сварочный пост — это рабочее место мастера. Оно оснащено различными инструментами и еще целым комплектом технологического приспособления, которое необходимо для работы сварщику. Они могут быть двух видов: передвижные и стационарные.
Передвижной пост обычно применяется в том случае, если необходимо осуществить сварку на большом изделии. Обычно он расположен на свободном пространстве, при этом закрыт навесом во избежание попадания светового излучения. Еще могут использоваться защитные щиты.
Стационарный пост — это кабинка, которая имеет размер 2000х2500х2000, она не имеет крыши. Стенки ее изготавливают из нескольких материалов: брезента, тонкой стали или фанеры. Однако перед установкой нужно обязательно обработать огнеустойчивой смесью или раствором квасцов. Это позволит обезопасить работу сварщика. Пол обязан состоять из огнестойкого материала. Освещенность кабинки не может быть меньше 80 лк. Обеспечивается хорошая вентиляционная система. Отсос воздуха должен быть расположен таким образом, чтобы при сварке полученные газы были отведены от работника.
Сам процесс выполняется на столе высотой 500-700 мм при наличии чугунной крышки, которая должна быть 20-25 мм толщиной. Нельзя пренебрегать техникой безопасности, поскольку сварка может быть очень опасна, если не соблюдаются все положенные правила.
В кабине сварщика имеется магнитный пускатель или рубильник, который непосредственно обеспечит доступ тока при сварке.
expertsvarki.ru
Автоматическая и полуавтоматическая сварка
Автоматы и их основные узлы. Автоматом для дуговой сварки называют устройство, механизирующее возбуждение и поддержание дуги, перемещение ее вдоль линии соединения и подачу сварочных материалов в зону плавления.
Подавляющее большинство автоматов предназначено для сварки плавящимся электродом – проволокой. Такой автомат (рисунок 16) представляет собой укрепленную на основании стойку 1, по которой в вертикальном направлении может перемещаться рейка 2. Эта рейка имеет возможность поворачиваться относительно оси стойки. По реке 2 перемещается каретка 5, к которой подводится шланг 4, подводящий сварочную проволоку и углекислый газ в зону сварки. Углекислый газ подается в шланг из баллона 7 через редуктор 8. Необходимость применения редуктора обусловлена тем, что давление газа в баллоне порядка 200 ати, а для сварочного процесса достаточно давления в 0.2 ати. Проволока при помощи механизма подачи сматывается с барабана 3. Механизм подачи проволоки представляет собой пару или несколько последовательно стоящих пар роликов, вращаемых электромотором через редуктор. Ролики зажимают проволоку, вытягивают ее с катушки и проталкивают в мундштук. Расстояние от места подвода тока к проволоке до дуги не превышает нескольких сантиметров. Поэтому потери напряжения из-за сопротивления проволоки малы и можно работать на гораздо больших плотностях тока, чем при ручной сварке. Так, сварку проволокой диаметром 1 мм выполняют токами до 450 А, то есть значительно большими, чем при ручной сварке электродами диаметром 5 мм. Вследствие этого, производительность и глубина проплавления при автоматической сварке гораздо больше, чем при ручной. Немаловажно также, что время подготовки сварщика для работы на автомате гораздо меньше, чем для ручной дуговой сварки.
Автоматы, в которых перечисленные узлы установлены на самоходной тележке с приводом от электромотора, которая перемещается автоматически вдоль свариваемого стыка, называются самоходными. Автоматы, перемещающиеся непосредственно по изделию или по направляющим, укладываемым на изделие или рядом с ним, называются сварочными тракторами. Прочие самоходные автоматы перемещаются только по направляющим сварочной установки. Конструкция направляющих зависит от формы стыка. Для сварки прямолинейных швов часто применяют консольные направляющие. Они позволяют сваривать и кольцевые поворотные швы: каретка стоит неподвижно, а изделие под ней поворачивают.
Несамоходные (подвесные) сварочные автоматы перемещаются вдоль шва механизмами, входящими в состав сварочного станка или установки.
Механизмы подачи электродной проволоки. Во время работы автомата режим сварки необходимо поддерживать постоянным, чтобы обеспечить постоянство геометрических размеров и качество шва. Другими словами, сварочный ток, напряжение и длина дуги должны быть неизменными. Поэтому любой механизм подачи электродной проволоки должен подавать ее со скоростью точно равной скорости плавления. Неравенство этих скоростей приводит к удлинению и обрыву дуги или к короткому замыканию (проволока упрется в изделие). Равенство скоростей плавления и подачи проволоки в сварочных автоматах обеспечивают двумя способами:
а) скорость плавления проволоки, т. е. сварочный ток, поддерживают постоянным, а скорость подачи проволоки в процессе сварки регулируют. Такие автоматы называют автоматами с регулируемой скоростью подачи проволоки;
б) проволоку подают с постоянной скоростью, а сварочный ток, т. е. скорость плавления, регулируют в процессе сварки. Такие автоматы называются автоматами с постоянной скоростью подачи проволоки.
Работа автоматов с регулируемой скоростью подачи проволоки основана на линейной зависимости напряжения дуги от ее длины при заданном токе:. Значит, постоянство напряжения на дуге обеспечивает постоянство ее длины. В механизме подачи проволоки таких автоматов используют электромотор постоянного тока с двумя обмотками возбуждения. Одна обмотка (независимая) питается от выпрямителя, вторая обмотка (дуговая) через выпрямительный блок подключена параллельно дуге. Магнитные потоки обмоток направлены встречно, причем, чем больше поток дуговой обмотки, тем больше скорость подачи проволоки. Магнитный поток независимой обмотки препятствует подаче проволоки. Если скорость плавления проволоки по каким-то случайным причинам окажется больше скорости подачи, то длина дуги увеличится, в результате возрастут напряжение на дуге, ток в дуговой обмотке и повысится скорость подачи проволоки. Если же длина дуги уменьшится, то напряжение дуги и магнитный поток дуговой обмотки уменьшатся, замедляя подачу проволоки и восстанавливая заданную длину дуги. Задают длину дуги изменением тока независимой обмотки с помощью реостата.
Работа автоматов с постоянной скоростью подачи проволоки основана на явлении саморегулирования дуги, открытом в 1942 г. В. И. Дятловым. Суть его в следующем. При увеличении длины дуги точка пересечения статической характеристики дуги с внешней характеристикой источника питания смещается в сторону уменьшения тока (рисунок 17). При увеличении длины дуги эта точка пересечения смещается в сторону уменьшения тока. Таким образом, возрастание длины дуги приводит к снижению скорости плавления проволоки, а уменьшение длины дуги к увеличению скорости плавления. Если в исходный момент скорость плавления была равна скорости подачи проволоки, то при случайных отклонениях длины дуги скорость плавления самопроизвольно меняется в сторону восстановления исходной длины дуги. Если используют источник питания с крутопадающей характеристикой, то абсолютные изменения скорости плавления при изменении длины дуги малы, и практически не ощутимы. Если же источник питания имеет пологопадающую или жесткую характеристику, то малейшее изменение длины дуги приводит к значительному изменению сварочного тока и быстрому восстановлению длины дуги. Эффективность саморегулирования тем больше, чем больше плотность тока и чем больше изменение тока при колебаниях длины дуги, то есть чем меньше крутизна внешней характеристики источника.
Как правило, в приводе механизмов подачи проволоки с постоянной скоростью используют асинхронные двигатели переменного тока. Скорость подачи проволоки устанавливают предварительно, меняя коэффициент передачи редуктора. Длина дуги и сварочный ток самоустанавливаются в процессе сварки сообразно скорости подачи проволоки и внешней характеристике источника питания. Автоматы с постоянной скоростью подачи проволоки конструктивно проще и надежнее в эксплуатации, чем автоматы с регулируемой скоростью проволоки. Поэтому автоматов с постоянной скоростью подачи проволоки большинство. Но установлено, что саморегулирование дуги достаточно эффективно только при токах, превышающих минимальные для данного диаметра проволоки – выше кривой А на рисунке 18. При сварочных токах в интервале между кривыми А и Б восстановление режима после случайных изменений недопустимо затягивается. Ниже кривой Б устойчивость дуги недостаточна для нормальной работы и нужны автоматы с регулируемой скоростью подачи проволоки. Кроме того, автоматы с регулируемой скоростью проще настраивать при сварке разных изделий.
Шланговые полуавтоматы. Автоматическая сварка не всегда осуществима и целесообразна. Она выгодна при выполнении длинных прямолинейных и круговых швов, а также при выполнении коротких швов на небольших массовых изделиях, подкладываемых под автомат. В противном случае время на перестановку и настройку автомата перекрывает выигрыш в производительности автоматической сварки по сравнению с ручной.
Достоинства автоматической сварки (производительность и глубокий провар) в сочетании с гибкостью ручной в значительной степени сочетает сварка с помощью шланговых полуавтоматов, В них механизм подачи электродной проволоки принципиально такой же, как в сварочных автоматах, проталкивает проволоку по гибкому шлангу в горелку, которую держит в руке сварщик. Таким образом, шланговый автомат подачу сварочной проволоки в дугу, а перемещение дуги вдоль шва сварщик производит вручную. Для первичной ионизации в горелку подают углекислый газ, который попутно защищает сварочную ванну от взаимодействия с кислородом воздуха или устанавливают на ней воронку с флюсом, который выполняет те же функции.
Подавляющее большинство горелок комплектуют шлангами длиной 3 м (предельная длина шлангов 4 – 5 м) Шланг состоит из направляющей трубки (сплошной полимерной или стальной спиральной), защитных слоев, токоведущих гибких жил, трех проводов управления и, наконец, наружного защитного слоя.
Сварку выполняют тонкой проволокой – сплошной диаметром 0,8 – 2 мм, порошковой – диаметром до 3,5 мм, которая не ухудшает гибкость шланга. Плотность тока при сварке велика – до 200 А/мм2, поэтому саморегулирование длины дуги идет очень быстро. Это позволяет при ручном перемещении горелки использовать механизмы подачи проволоки с постоянной скоростью. Случайные колебания длины дуги из-за ручного ведения горелки легко компенсируются саморегулированием дуги.
Источниками питания при полуавтоматической сварке обычно служат сварочные трансформаторы и выпрямители на номинальные токи от 300 до 500 А. Механизмы подачи полуавтоматов гораздо меньше и легче, чем у автоматов, так как рассчитаны на проволоку только малого диаметра. Масса их для разных отечественных полуавтоматов колеблется в пределах 12 – 25 кг – их легко переносить или перевозить на тележке. Для сварки на монтаже в небольших количествах выпускают ранцевые полуавтоматы, масса механизма подачи которых составляет 5 – 7 кг. Их сварщик надевает на спину как рюкзак. Сварочные провода позволяют относить механизм подачи на расстояния примерно до 50 м от источника питания.
Производительность полуавтоматической сварки плавящимся электродом в 2 – 3 раза превышает производительность ручной сварки покрытыми электродами.
studfiles.net
Автоматическая и полуавтоматическая сварка - Виды сварки и их общие характеристики - Сварные соединения
Принцип автоматической сварки заключается в том, что электрод подается к месту сварки автоматически при непрерывном разматывании бухты специальной электродной проволоки. Электрод подается автоматической (сварочной) головкой, которая выполняет те же функции, что рука сварщика при ручной сварке.
Схема автоматической сварки под слоем флюса
Вместо обмазки применяется сыпучий материал определенного химического состава (флюс), которым засыпается конец электрода. Флюс полностью изолирует место сварки от воздуха, так как горение дуги происходит под слоем флюса. В результате получается однородный, плотный, с глубоким проваром шов, обладающий высокими механическими показателями.
Таблица Механические свойства образцов сварных соединений и наплавленного металла шва.
Вследствие большой силы тока, применяемого при автоматической сварке (600 — 3 000 а), производительность ее в 3 — 5раз (а иногда даже в десятки раз) выше, чем при ручной сварке.
Автоматическая сварка угловых швов балок сварочными тракторами
При проектировании конструкций, соединения которых должны быть выполнены автоматической сваркой, необходимо предусматривать такие конструктивные решения, которые не мешали бы проходу автоматической головки. Автоматическая сварка может осуществляться на стационарной установке или при помощи сварочных тракторов1.
Автоматическая сварка
Автоматическая сварка угловых швов в нижнем положении:
а — «в лодочку»; б — наклонным электродом; в — способом оплавления.
Обычно эту сварку выполняют при нижнем положении швов, применяя для этого вращающиеся кондукторы. При этом швы формируются свободно.
В последнее время Институтом электросварки АН УССР разработан метод сварки с принудительным формированием швов (для металла толщиной от 10 до 24 — 30 мм), предназначенный главным образом для наложения вертикальных швов. Схема такой сварки показана на фигуре.
Вращающийся кондуктор для сварки балок
Схема автоматической сварки
Схема автоматической сварки с принудительным формированием шва:
1 — охлаждающая вода; 2 — ползун; 3 — мундштук; 4 — задняя прокладка; 5 — электрод; б — расплавленный флюс; 7 — ванна; 8 — шов.
Для сварки элементов толщиной больше 24 — 30 мм применяется метод бездуговой сварки, названной электрошлаковой. Для этого вида сварки, с помощью которой можно сваривать детали большой толщины (200 — 300 мм), характерно, что ток проходит через расплавленный шлак (флюс) с выделением тепла, достаточного для плавления основного и электродного материала.
Схема электрошлаковой сварки
Схема электрошлаковой сварки:
1 — кромки изделия; 2 — охлаждаемые ползуны; 3 — ванна расплавленного шлака; 4 — металлическая ванна; 5 — электрод, погруженный в шлак.
Полуавтоматическая сварка
Полуавтоматическая сварка:
а — установка для полуавтоматической сварки: 1 — сварочный трансформатор; 2 — аппаратный ящик; 3 — бухта проволоки; 4 — подающие ролики; 5 — гибкий шланг; 6 — держатель и бункер флюса; 7 — свариваемое изделие;
б — держатель ДШ-5: 1 — трубчатый мундштук; 2 — воронка для флюса; 3 — заслонка; 4 — ручка с кнопками управления.
Для наложения швов, неудобных для автоматической сварки, может применяться шланговая полуавтоматическая сварка под флюсом. Идея этого вида сварки заключается в том, что тонкая электродная проволока диаметром 2 мм подается к месту сварки по гибкому шлангу механизированным способом, а движение вдоль шва производится вручную.
Флюс подается непосредственно из воронки держателя, на котором находятся также кнопки управления. На фигуре показана приварка полуавтоматом ребер жесткости сварной балки.
Полуавтоматическая сварка ребер жесткости балок
Другие виды сварки
Точечная электросварка. За последние годы появились машины, сваривающие пакеты листов общей толщиной до 30 мм при помощи сплавления их в отдельных точках. Для этого свариваемые листы помещают между двумя обжимающими их медными электродами, через которые пропускают ток большой силы.
Точечная сварка в строительных стальных конструкциях в настоящее время не получила заметного распространения из-за невозможности обеспечить стабильные показатели прочности для толстых деталей.
Газовая сварка. Сгорание ацетилена в струе кислорода дает высокую температуру (3200°), в результате чего расплавляются и свариваются основной металл и присадочный материал в виде проволоки, которая вводится в газовое пламя. Газовая сварка мало производительна и поэтому применяется редко, преимущественно в ремонтном деле.
1 Д. П. Шиловцев, Изготовление стальных конструкций, Государственное издательство литературы по строительству и архитектуре, 1954.
«Проектирование стальных конструкций»,К.К.Муханов
www.ktovdome.ru
преимущества над ручными моделями, разновидности и управление
К сварочным полуавтоматам относят устройства, осуществляющие электродуговую сварку металлов, использующие проволочный электрод с непрерывной автоматической подачей.
В процессе выполнения сварочных работ такие процедуры, как возбуждение и поддержание электрической дуги, выбор ее оптимальной длины и визуальный контроль качества образующегося шва, выполняются сварщиком в ручном режиме.
По степени автоматизации процесса, сварка полуавтоматом занимает промежуточное положение между ручной дуговой сваркой, использующей сменяемые штучные электроды, и автоматической сваркой, полностью выполняемой без участия сварщика. Таким образом, автоматическая и полуавтоматическая сварка, выполняется, соответственно, с полной или частичной автоматизацией процесса.
Режимы работы
Еще одной отличительной чертой сварочных полуавтоматов является использование в процессе сварки среды защитных газов. Сварка может осуществляться как в инертной среде (обычно это аргон), так и в активной (углекислый газ). В первом случае, процесс носит название MIG (metal inert gas), во втором – MAG (metal active gas).
Канал подачи газа в зону сварки располагается в рукаве вместе с трубкой, в которой перемещается проволочный электрод. Рукав соединяет корпус сварочного полуавтомата с горелкой, которую сварщик удерживает в руке.
Название «горелка» закрепилось за этим аналогом держателя электрода ручной сварки из-за его внешнего сходства с горелками, применяемыми в газосварочном оборудовании. Функционально, это совершенно разные устройства.
Управление подачей газа, проволочного электрода и включением источника сварочного тока осуществляется нажатием одной кнопки, удобно расположенной на рукоятке горелки, под пальцем сварщика.
Значительно реже применяется режим работы сварочного полуавтомата без использования защитного газа. В этом случае используется специальная проволока, представляющая собой тонкую трубку, внутренняя полость которой заполнена флюсом.
Так как флюс имеет порошкообразную структуру, такую сварочную проволоку в обиходе часто называют порошковой. При плавлении стальной оболочки в процессе сварки сгорающий флюс обильно выделяет газ, образующий необходимую защитную среду.
Типы конструкции
Основой конструкции полуавтомата является источник сварочного тока или блок питания. Этот узел может быть построен по одному из двух принципов. Классический вариант представляют устройства, в основе которых обычный понижающий трансформатор.
Но превалируют на рынке аппараты, в основе конструкции которых лежат инверторные преобразователи. Сварочное оборудование, построенное на основе этой инновационной технологии, уверенно теснит классику уже не первый год, и тому есть веские причины.
Преимущества инверторных полуавтоматов очевидны и подтверждены неоднократно проводимыми тестированиями. Среди важных достоинств инверторов особо следует выделить:
- высокую стабильность горения электрической дуги, обеспечиваемую даже при пониженных значениях питающего напряжения;
- более высокий КПД по сравнению с трансформаторными устройствами;
- относительно маленький вес и небольшие габариты аппаратов.
К положительным чертам трансформаторных полуавтоматов можно отнести только простоту конструкции, и то, что в случае возникновения неисправности, починить его сможет электрик, не обладающий очень высокой квалификацией.
Конструкции полуавтоматов различаются по используемому напряжению питания. Аппараты, ориентированные на бытового потребителя, питаются от однофазной сети 220 Вольт.
Устройства, предназначенные для промышленного применения, чаще выпускаются в трехфазном варианте. Такие полуавтоматы способны выполнять сварку более высокими токами, с использованием более толстой проволоки и в более нагруженном режиме.
Механизм подачи проволоки
Еще одна важная деталь устройства сварочного полуавтомата – это механизм подачи сварочной проволоки, намотанной на вращающейся бобине. Устройство механизма может быть толкающим, тянущим, или комбинированным.
Выбор типа устройства зависит от длины рукава, соединяющего корпус полуавтомата с горелкой. Обычно, при длине рукава до 3 метров, применяется толкающий механизм, если длина превышает этот уровень, используется тянущий или комбинированный привод.
Толкающий привод располагается внутри корпуса сварочного аппарата, тянущий привод – в ручке горелки.
Конструкция механизма подачи проволоки в полуавтомате очень проста. Основными его элементами являются одна или две пары роликов, один из которых играет роль ведущего, второй является прижимным.
Бобина с проволокой может располагаться внутри корпуса, а может находиться снаружи, на специальной подставке. Первый вариант, безусловно, более компактный, но сварочная проволока поставляется с заводов на бобинах разного размера, а крупную катушку удобнее расположить вне корпуса.
Все модели сварочных полуавтоматов имеют функцию регулирования скорости подачи проволоки.
Технология сварки
Одной из отличительных черт, которой обладает сварка полуавтоматом (особенно это относится к аппаратам инверторного типа) является простота выполнения операций.
Даже человек, никогда не имеющий дела со сваркой, в состоянии очень быстро освоить основные правила работы и научиться выполнять качественные соединения.
Вначале надо проверить все комплектующие полуавтомата, необходимые для выполнения работ. Комплект оборудования должен быть таким:
- собственно полуавтомат;
- горелка с рукавом для присоединения к основному корпусу;
- катушка с проводом требуемой марки;
- баллон с газом, который предполагается использовать;
- соединительные провода требуемого сечения, чтобы подключить электрическое питание.
Первое, о чем следует позаботиться прежде, чем начать работу, это выбрать сварочную проволоку требуемого диаметра из нужного материала. На выбор влияет металл, который предстоит сваривать и его толщина.
Существуют разновидности сварочной проволоки, имеющие диаметр от 0,6 мм до 1,2 мм. Очень удобно пользоваться специальными таблицами, содержащими необходимые данные для выбора типа сварочной проволоки, ее диаметра, скорости подачи и величины сварочного тока. Так, например, для сварки стальных изделий применяется стальная проволока, для сварки алюминия – алюминиевая.
Правила выполнения соединений различного вида с использованием автоматической и полуавтоматической сварки регламентируются ГОСТ 11533-75. Сварщику-любителю, решившему использовать сварочный полуавтомат для выполнения ремонтных работ в собственном доме или на даче, неплохо перед этим заглянуть в этот документ.
Что же касается сварщиков-профессионалов, то все сварочные работы на производственных предприятиях должны выполняться в соответствии с проектом, на основании которого технологами составляется технологическая карта процесса, где учитываются все требования ГОСТ.
Выбор оборудования
Перед тем как купить полуавтоматический аппарат, в первую очередь внимание следует обратить на его технические характеристики.
Основной характеристикой полуавтомата является рабочий ток, на котором может вестись сварка. Эта характеристика напрямую связана с толщиной металла, сварку которого можно осуществлять на этом аппарате.
Хорошо, если максимальный ток выбранного экземпляра на 20 – 30% превышает требуемый. Этот запас обеспечит более надежную и длительную работу устройства.
Еще одна важная характеристика – так называемая продолжительность включения. Эту величину принято выражать в процентах. Она показывает, какую часть 10-ти минутного промежутка времени полуавтомат находится в работе.
Например, автоматические сварочные аппараты, работающие на сборочных конвейерах машиностроительных предприятий, должны обеспечивать продолжительность включения до 100%.
Для выполнения ремонтных работ на бытовом уровне, вполне удовлетворительным можно считать значение этого показателя на уровне 20%. Этот параметр является основным, по которому сварочные полуавтоматы относятся к категории профессиональных или любительских. Также, его значение в большой степени определяет цену прибора.
Что касается напряжения питания, безусловно, в быту более практичными являются модели с однофазным питанием, подключить которые можно практически в любых условиях – в квартире, доме, на даче, в гараже.
Значение производителя
Важным фактором при решении вопроса, какой сварочный полуавтомат выбрать, является выбор производителя. Здесь трудно давать рекомендации, ведь бывают ситуации, когда изделия никому не известных производителей безотказно работают годами, а продукция мировых брендов не отрабатывает гарантийный срок эксплуатации.
Не смотря на это, лучше все же отдавать предпочтение именитым производителям. Главным образом потому, что они при реализации продукта, обычно создают сеть сервисных центров, обеспечивающих обслуживание, и если понадобится, гарантийный ремонт аппарата.
Особенно важно обращать на это внимание, если приобретается инверторный сварочный полуавтомат, для ремонта которого требуется специально обученный, высококвалифицированный персонал.
svaring.com
Автоматическая и полуавтоматическая сварка труб под флюсом
Инженеры уже давно думали об автоматизации сварки, которая бы посодействовала ускорению многих работ на производстве. Один из изобретенных вариантов — автоматическая сварка под флюсом. Этот метод был внедрен в промышленность в 1939 году благодаря разработкам академика Патона Е.О. и его команды при институте электросварки. Как осуществляется дуговая сварка под флюсом? В чем ее преимущества? Какое используется оборудование для автоматической сварки?
Суть процесса и варианты
Автоматическая сварка под слоем флюса, называемая в международной системе SAW, основана на горении электрической дуги, плавящей кромки металла. Для этого в зону сварки подается проволока, (ГОСТ 16130-72 или с иными составами), между кончиком которой и изделием возбуждается дуга. Сварочный трактор, параллельно с этим, подает в зону соединения специальный порошок — флюс, который покрывает расплавленную часть шва, защищая от воздействия внешних газов. Дополнительно, слой флюса содействует лучшей вплавляемости легирующих элементов в шовную структуру, и уменьшает разбрызгивание металла.
Плавящийся конец проволоки удерживается головкой сварочного автомата на определенном расстоянии от изделия. Сварочный станок может работать неподвижно, когда его используют для сварки труб, которые вращаются на роликах, приводящихся в движение редуктором. Или же головка аппарата может двигаться по заданной траектории, благодаря наличию шаблона, соответствующего форме соединения. Оператор установки только настраивает режимы сварки и запускает процесс. Технология автоматической сварки под флюсом требует человеческого контроля над работой и корректировки режимов, а также периодической оценки качества результата. Модели, называемые сварочный трактор, передвигаются самостоятельно на собственных шасси, вдоль линии соединения. Все основные узлы такой машины двигаются вместе с ней.
По ГОСТ 8713-79 различают следующие виды работ, которые может выполнять сварочный станок:
- сваривать изделия на весу, без поддержек для обратной стороны шва;
- на специальной медной подкладке, предохраняющей от протекания и наплывов;
- на подушке из порошка;
- на медном ползуне, сопровождающем движение головки аппарата.
В некоторых случаях требуется накладывать предварительный корневой шов, по которому сварочный трактор будет вести свою работу. В других технологиях необходимо производить подварочные швы с обратной стороны изделия.
Применение сварочного метода
Автоматическая дуговая сварка соответствует параметрам ГОСТ 8713-79. Благодаря высокой скорости работы она успешно применяется для нанесения ровных швов в продольном положении. Для обеспечения прямого движения головки, сварочный станок снабжается шаблонами, вдоль края которых двигается электродная проволока и горит дуга. Таким методом быстро соединяются толстые листы железа, используемые для промышленных конструкций. Возможны и фигурные движения головки аппарата. Для этого устанавливают соответствующий шаблон.
Сварочные трактора для сварки под флюсом способны выполнять все швы, обозначенные ГОСТ 11533-75. Они хорошо подходят для соединений: встык, внахлест, угловых и тавровых. Шов получается ровный и хорошо расплавленный, без перерасхода присадочного материала.
Там где требуется проложить трубопровод особенно успешно применяется автоматическая сварка кольцевых швов. Сущность метода заключается во вращении изделия под неподвижной головкой сварочного аппарата. Благодаря повышенной силе тока, работы ведутся быстрее, чем в ручном режиме. Швы получаются высокого качества. Автоматическая сварка труб может проводиться на большом участке, соединяя секции в одну линию. Размер таких заготовок достигает 25 метров. Реальны и большие соединения, но это зависит от возможности транспортировки трубы к месту укладки. Дополнительно, задействуют тягачи или железнодорожная техника. При помощи крана трубы укладываются в магистраль, а заключительный стыковой шов выполняет сварщик вручную. Это значительно ускоряет процесс прокладки трубопроводов.
Преимущества автоматического метода
Сварочный станок, работающий в автоматическом режиме, отличается рядом преимуществ перед другими видами сварки. А именно:
- высокая производительность выполнения работ за счет увеличенной силы тока и скорости ведения шва, которая может превышать показатели других методов в 15 раз;
- хорошее качество соединения благодаря стабильность подачи присадки и постоянной скорости прохода всей линии;
- глубокое проплавление;
- работа с трубами больших диаметров;
- задействование меньшего количества сварщиков на одинаковый объем работ;
- более благоприятные условия труда для сварщика и меньший вред для здоровья, ввиду удаленности от источника излучения и дыма.
Быстрые режимы автоматической сварки под флюсом достигаются и за счет использования порошка, который подается в зону горения дуги из специального бункера по трубке. Количество высыпания регулируется широтой открытия заслонки. Внешне, флюс похож на круглые светлые шарики, мелкого гранулирования. Посыпание зоны сварки флюсом имеет следующие преимущества:
- исключает разбрызгивание металла сварочной ванны и присадочного элемента;
- придает стабильности дуге;
- задерживает процесс остывания сварочного шва, что улучшает его физические свойства;
- защищает сварочную ванну от взаимодействия расплавленного металла с кислородом;
- раскисляет металл и помогает качественней вплавляться легирующим элементам.
Сварочный трактор плавит часть порошка электрической дугой от проволоки, вследствие чего образуется небольшая корка на поверхности соединения. Другая часть порошка так и остается в виде гранул. После завершения шва требуется удаление слоя шлака молотком и щеткой по металлу. Очищенное изделие готово к покраске или обработке антикоррозийными составами.
Разновидности автоматической сварки
Автоматический сварочный аппарат, создающий дугу подачей тока на проволоку, и защищающий сварочную ванну слоем флюса, может иметь несколько вариантов исполнения. Это могут быть станки с подвижной головкой, выполняющие ровные или шаблонные линии швов. Для трубопроводов используют неподвижные головки, под которыми изделие вращается на роликах. Тракторы сами ездят по изделию, перевозя аппарат и одновременно ведя сварку. Во всех моделях применяется плавящийся электрод (проволока ГОСТ 16130-72). За последующее время, после внедрения в промышленность этих методов, были разработаны и другие устройства, позволяющие автоматизировать сварочные работы. Некоторые принципы работы таких установок похожи, а другие отличаются в корне.
В среде аргона
Одной из разновидностей является автоматическая аргонодуговая сварка неплавящимся электродом. В качестве последнего выступает стержень из вольфрама с некоторыми добавками. Между ним и изделием возбуждается электрическая дуга, а аргоновый состав газовой смеси, подаваемый через сопло головки аппарата, не дает углероду вырываться через поверхность шва. Благодаря этому соединение получается крепким и ровным. Сварка в среде защитных газов может выполняться стационарно закрепленной головкой устройства, под которой изделие проворачивается, так и движущейся частью по линии соединения. Аргонно-дуговой метод активно применяется при работе с нержавеющими трубами и емкостями.
Порошковой проволокой
Еще одним вариантом является автоматическая сварка порошковой проволокой. Аппарат подает плавящийся электрод в зону сварки по роликам. Напряжение на конце проволоки создает дугу. Но для защиты расплавленного металла используется не порошок из бункера, а флюс, находящийся в самой проволоке. Для этого последняя изготавливается трубчатой формы и укладывается в бобины. Такой расходный материал стоит дороже, но облегчает подготовку к сварочному процессу. Сварочный станок не требует загрузки флюса в бункер. Наплавленный шов, как и в случае с насыпным порошком, нуждается в очистке. Аппараты могут работать перемещаясь на самом изделии или неподвижно, с прокруткой свариваемых частей под ними.
Плазменная сварка
Для быстрого соединения легированных сталей была разработана автоматическая плазменная сварка. В подобных устройствах электрическая дуга горит между двумя электродами в головке горелки. Аргон или гелий, подающиеся под высоким давлением и закрученный завихрителем, содействует ионизации пламени дуги, и усилению ее температуры. Плазменная сварка устанавливается на кронштейны, которые могут вращаться по оси. Расстояние от центра до головки может изменяться, что делает удобным это оборудование для круговых автоматических швов днищ емкостей. В зависимости от толщины металла и требуемой высоты шва, устройство может снабжаться дополнительным блоком подающим присадочную проволоку.
Кроме вышеперечисленных агрегатов встречаются их полуавтоматические версии, где сварщику требуется направлять сварочную головку или руководить движением трактора. Автоматическая и полуавтоматическая сварка востребованы не только на крупных предприятиях, но в небольших фирмах. Ведь таким способом можно значительно повышать производительность и доходность. Некоторые умельцы смогли сделать самодельный аппарат на основе полуавтомата, который способен передвигаться по заданной траектории.
Режимы и особенности
Сваривание автоматическим методом происходит на повышенных токах. Это обеспечивает высокую скорость и эффективность процесса. Рекомендуемые параметры следующие:
Диаметр проволоки, мм | Сила тока, А |
2 | 200-300 |
3 | 350-500 |
4 | 400-700 |
5 | 500-1000 |
Кроме этого, на каждый вид работы при задействовании автоматической сварки на трубопроводе, составляется технологическая карта, в которой указывается весь комплекс усилий и ресурсов, чтобы соединить один километр трубы. Сюда входят: трудоемкость (наличие определенного числа человек и дней на выполнение), выработка за одну смену, необходимость в кране (количество машин на смену), затрачиваемость энергетических ресурсов (тока и горючего), конкретные требования по сборке и сварке изделий, техника безопасности.
Благодаря автоматизации сварочного процесса ускорилось выполнение многих работ. Эти машины облегчают монтаж трубопроводов и других конструкций. А высокое качество швов позволяет использовать их на ответственных соединениях.
Поделись с друзьями
0
0
0
0
svarkalegko.com
Автоматическая и полуавтоматическая дуговая сварка — Мегаобучалка
Одновременно с разработкой методов улучшения качества сварного шва развитие сварочной техники шло в направлении повышения производительности и автоматизации процесса.Производительность процесса дуговой сварки зависит от мощности дуги. Значительное увеличение напряжения дуги невозможно по соображениям техники безопасности. Попытки же поднять мощность путем увеличения силы тока ограничивались двумя обстоятельствами. Во-первых, при увеличении силы тока происходит нагрев стержня электрода ввиду того, что тек подводится от держателя к концу электрода, а электрическое сопротивление стержня достаточно велико. Во-вторых, большое тепловыделение в дуге вызывает интенсивное кипение сварочной ванны, разбрызгивание металла и совершенно неудовлетворительное формирование шва.Некоторое время назад стремились достигнуть повышения производительности увеличением диаметра электрода, при котором удавалось увеличить силу тока без перегрева стержня. Применялись электроды диаметром 8, 10 и 12 мм. Однако работать столь большими электродными стержнями было очень неудобно. Применение скользящих электрических контактов для подвода тока к концу электрода вблизи дуги оказалось конструктивно сложным и все равно не устраняло разбрызгивания.
Таким образом, создался как бы технологический предел повышения производительности дуговой сварки. Автоматизация процесса, т. е. механизированная подача проволоки в дугу и перемещение последней вдоль соединения, не исправляла положения. Применение автоматов в этих условиях было бесполезным, так как не обеспечивало основного условия - повышения производительности труда.Коренное решение вопроса о повышении производительности электросварки было получено в 1936-1937 гг., когда в США, а затем и в СССР был применен метод автоматической электросварки закрытой дугой, т. е. под слоем флюса.Схема современного метода автоматической сварки под флюсом. Сварочная проволока подается в дугу специальным механизмом (головкой) из бухты. Флюс засыпается из бункера. Дуга (невидимая для глаза) горит под слоем флюса, расплавляет часть флюса и образует в нем пузырь, заполненный газами и парами веществ, испаряемых дугой. Питание дуги электрическим током осуществляется от специального источника (трансформатора с дросселем или генератора постоянного тока).
Автоматическая сварка под флюсом имеет следующие преимущества перед ручной сваркой.1. Достигается резкое повышение производительности сварки (иногда в 10-20 раз) благодаря:а) применению больших сил тока без увеличения диаметра электрода; ток подводится вблизи конца электрода, и поэтому, несмотря на повышение плотности тока, не происходит перегрева электрода; наличие флюса, оказывающего давление на зону дуги и ванну (около 6-9 г/см2), предотвращает разбрызгивание металла при большой плотности тока и обеспечивает правильное формирование шва;б) уменьшению количества наплавленного металла вследствие более глубокого проплавления основного металла и увеличения его доли в формировании шва;в) возможности сваривать швы большого сечения за один проход.2. Экономится электродная проволока благодаря отсутствию потерь на огарки и резкому снижению потерь на угар и разбрызгивание.3. Экономится электроэнергия, что обусловлено высокими режимами сварки и лучшим использованием тепла дуги.При автоматической сварке под флюсом может быть получено более высокое качество металла шва, чем при ручной сварке, благодаря лучшей защите наплавленного металла от вредного действия кислорода и азота воздуха, отсутствию пор, шлаковых включений и непроваров, и большей плотности металла. Кроме того, при сварке под флюсом устраняется вредное действие излучения дуги. Снижаются требования в отношении квалификации сварщиков.
Дальнейшим развитием и видоизменением способа сварки закрытой дугой явилась полуавтоматическая сварка под флюсом. При полуавтоматической сварке перемещение дуги вдоль шва осуществляется вручную, а подача проволоки - автоматически. По предложению В. П. Демянцевича и И. А. Блоха применяется проволока малого диаметра (1,2-2 мм), которая подается в дугу по гибкому шлангу. Используется повышенная плотность тока.Флюс засыпается в зону дуги из бункера, укрепленного на конце шланга. Бункер с рукояткой и наконечником, направляющим проволоку, представляет собой единый электрододержатель. Существуют установки и с пневматической подачей флюса от отдельно стоящего бункера по второму параллельному шлангу.Благодаря малому диаметру проволоки обеспечиваются достаточная гибкость шланга и большая маневренность. Относительно небольшая сила тока позволяет использовать компактные источники питания (такие же, как при ручной дуговой сварке). Полуавтоматическая сварка под флюсом находит в судостроении весьма широкое распространение, главным образом, для сварки угловых швов, протяженность которых в корпусных конструкциях наиболее велика.В области применения автоматической и полуавтоматической сварки под флюсом Советский Союз занимает ведущее место. Автоматической сваркой свариваются сотни тысяч тонн металлоконструкций. Объем применения автоматической и полуавтоматической сварки в судостроении достиг сейчас 60-70% от общего объема сварочных работ.В 1949 г. Г. З. Волошкевичем был предложен метод автоматической дуговой сварки с принудительным формированием для выполнения швов в вертикальном или наклонном положении. При обычной автоматической сварке со свободным формированием вследствие относительно большого объема сварочной ванны сварка на вертикальной плоскости, очевидно, невозможна, так как жидкий металл вытекает из сварочной ванны. Для того, чтобы предотвратить вытекание сварочной ванны, необходимо искусственно охлаждать ее с поверхности, прижимая медными ползунами или диском.Процесс ведется проволокой малого диаметра (как правило 3 мм) автоматом, перемещающимся вместе с ползуном по зубчатой рейке, укрепленной параллельно свариваемому шву.
В настоящее время создаются автоматы для сварки даже в потолочном положении (например, неповоротных стыков трубопроводов больших диаметров). Удержание сварочной ванны от вытекания производится в них при помощи медного диска. Электрошлаковая сварка. Электрошлаковая сварка - дальнейшее развитие метода автоматической сварки с принудительным формированием. При электрошлаковом процессе, в отличие от других способов сварки, источником нагрева служит тепло, выделяющееся в жидкой шлаковой ванне при прохождении через нее электрического тока. Ванна расплавленного шлака создается между кромками двух деталей и поддерживается от вытекания охлаждаемыми медными планками или специальной формой. В шлаковую ванну погружается плавящийся электрод. Электрический ток, проходя через расплавленный шлак, вследствие сопротивления последнего разогревает ванну. Благодаря высокой температуре шлаковой ванны в ней расплавляется погруженный электрод и оплавляются кромки деталей. Жидкая металлическая ванна из расплавленного электродного и основного металла располагается внизу, под шлаком. По мере плавления электрода сварочная ванна и находящийся над ней шлак постепенно поднимаются вверх, а затвердевающий в нижней части металл образует сварной шов. При большой толщине свариваемого металла в ванну может подаваться не один, а несколько параллельных электродов в виде прутков (иногда в виде пластин).
При электрошлаковой сварке тепло используется, главным образом, для плавления основного и присадочного материала, так как флюса расплавляется очень мало. Расход электроэнергии на 1 кг наплавленного металла получается низким.Благодаря большой силе тока, доходящей до 6000 а, обеспечивается высокая производительность процесса, причем его эффективность особенно высока при сварке металла больших толщин (100-200 мм и выше). Одним из преимуществ процесса является то, что не требуется точная обработка и подгонка кромок под сварку. При больших толщинах такая обработка очень трудоемка и ее исключение дает значительную экономию. Существуют различные варианты электрошлаковой сварки в зависимости от конструкции шлакоудерживающих устройств: например, с подвижными охлаждаемыми ползунами, ванношлаковая в неподвижной форме и др. Схемы электрошлаковой сварки разделяются также по количеству, форме и способу подачи электродов (проволочными электродами, пластинчатыми электродами, плавящимся мундштуком и др.). Дуговая сварка в защитных газах. Защита металла шва при дуговой сварке может осуществляться не только применением слоя флюса, но и путем создания газовой оболочки. Для этого газ по шлангу подают в зону дуги или производят сварку в замкнутом сосуде, наполненном газом. В качестве защитных газов используются нейтральные газы (гелий или аргон), углекислый газ, азот или водород. Наиболее распространена сварка в струе аргона, обеспечивающей надежную защиту от окисления и, благодаря этому, получение высоких механических свойств металла шва. Могут быть применены как неплавящиеся (вольфрамовые), так и плавящиеся электроды. В частности, последний способ с применением алюминиевой проволоки, подаваемой в дугу полуавтоматом, широко используется для сварки судовых конструкций из алюминиевых сплавов. Полуавтоматическая и автоматическая сварка стали в среде углекислого газа была разработана в 1950-1952 гг. К. В. Любавским и Н. М. Новожиловым. Этот процесс особенно перспективен благодаря высокой экономичности. Схема процесса незначительно отличается от схемы аргоно-дуговой сварки. Процесс ведется плавящимся электродом, подаваемым в горелку автоматом или полуавтоматом. Применяется электродная проволока диаметром 1-2 мм с повышенным содержанием элементов-раскислителей (марганца и кремния).
Вибродуговая наплавка. Автоматическая дуговая наплавка вибрирующим электродом в среде электролита разработана в СССР в 1951 г. Этот способ служит для нанесения на поверхность детали твердых и тонких поверхностных слоев без значительных структурных изменений и деформирования деталей.Сущность способа состоит в том, что между изделием и электродом, конец которого колеблется специальным вибратором, возникают кратковременные дуги. При этом на поверхности детали постепенно наплавляются частицы электродного материала. Для охлаждения металла в зону сварки все время подается жидкость.Электродуговая резка. Электрическая дуга может быть использована не только для сварки, т. е. соединения металлов, но и для их резки. Электродуговая резка осуществляется металлическим или угольным электродом на больших силах тока, чтобы обеспечить максимальную глубину проплавления. Расплавляющийся металл должен удаляться из места разреза. Для этого резку начинают с кромки или же прожигают отверстие: расплавленный металл из места разреза стекает вниз. Применяют дуговую резку черных и цветных металлов. Дуговую резку алюминия и его сплавов осуществляют вольфрамовым электродом в защитной среде аргона либо дуговой плазменной головкой.Одной из разновидностей дуговой резки является воздушно-дуговая строжка. Сущность ее состоит в том, что удаляемый слой металла расплавляется электрической дугой, а затем выдувается из зоны дуги сильной воздушной струей, направляемой сбоку из шланга. Чтобы не вводить лишнего электродного материала, резка ведется угольным электродом. Процесс весьма производителен и широко используется при подготовке канавок с обратной стороны шва (для подварочного шва), при удалении дефектных швов и т. д.
20.Автоматическое регулирование процесса контактной сварки.
megaobuchalka.ru
Полуавтоматическая сварка – принцип работы, отличие от автоматической сварки
Теперь же, поговорим о полуавтоматической сварке. Создавать о ней отдельный раздел не стоит, так как между автоматической и полуавтоматической сваркой существует небольшое количество отличий. Основное из них – это наличие или отсутствие процесса механизации во время работы.Так, если автоматическая сварка предполагает автоматическое перемещение сварочной проволоки, то полуавтоматическая сварка требует перемещения этой проволоки вручную. Однако назревает вопрос – зачем вообще нужна полуавтоматическая сварка, если есть возможность делать все на автомате, без присутствия человеческого фактора? На самом деле, все очень просто.Автоматическая сварка очень популярна и распространена при массовом производстве. Так, сварочные аппараты настраиваются под определенную программу, и по мере поступления изделий для сварки, аппараты включаются без вмешательства человека в процесс. Однако, в широком ряде случаев необходимо, чтобы направление шва и формирование его качества, происходило только при содействии человека. Поэтому, такой сваркой и стала полуавтоматическая сварка.Такая сварка предусматривает собой простую конструкцию. В ней есть специальный автоматический механизм подачи электродной проволоки, которая подается в специальный гибкий шланг, на сварочный держатель. Так, проволока подается автоматически, а сварщик, глядя на общую картину изделия, направляет наконечник в ту сторону, где необходимо сделать шов и сварное соединение. Именно потому, что проволока подается автоматически, а дуга перемещается вручную, процесс и получил название полуавтоматической сварки.Происходить полуавтоматическая сварка может как с применением флюса, так и без него. Применение же флюса, позволило использовать полуавтоматическую сварку при толщине, выше 2-2,5 мм. Также, использование флюса позволило заметно увеличить величину сварочного тока, что в свою очередь, поспособствовало улучшению устойчивости дуги и резкому повышению производительности сварки. Кроме того, использование флюса позволило сократить диаметр проволоки, которая используется для сварки, и тем самым, снизить габариты шланги и сварочного аппарата.
Процесс подачи электродной проволоки Как правило, используется проволока, диаметром от 1,6-2 мм. Она смотана в бухту, которая находиться в специальной кассете, установленной в сварочном аппарате. Там же, расположился проталкивающий механизм, который подает проволоку через гибкий шланг, непосредственно в держатель, который держит сварщик в руках. Далее, подается сварочный ток на держатель через специальный гибкий шланг, подключенный к сварочному трансформатору. Этот ток, воздействует на электродную проволоку, и при контакте с поверхностью металла, возникает дуга, при помощи которой и выполняется сварка. Таким образом, полуавтоматическая сварка удобней тем, что с ее помощью можно четко контролировать процесс сварки, и выполнять провары там, где сварщик посчитает нужным. А автоматический процесс подачи проволоки, намного облегчает весь процесс.Статья подготовлена по материалам сайта: http://www.vse-o-svarke.org/publ/avtomaticheskaja_dugovaja_svarka/princip_raboty_poluavtomaticheskoj_svarki/6-1-0-44
profilgp.ru