4.7. Условные обозначения заклепочных соединений. Заклепочные соединения гост
Заклепочные швы. Заклепки ГОСТ. Соединения деталей заклёпками. Прочные швы
Соединения деталей заклёпками представляют собой один из способов получения неразъёмного соединения. Основным отличием заклёпочных соединений от разъёмных является то, что отделение одной детали от другой возможно лишь при разрушении всех заклёпок.
Заклёпка представляет собой цилиндрический стержень, снабжённый на конце головкой. В зависимости от назначения, головкам заклёпок придают формы: полукруглую, плоско-коническую, плоскую, полупотайную, коническую и коническую с подголовком (табл. 17).
Заклёпочные швы разделяются на швы: прочные, плотно-прочные и плотные. Прочные швы находят применение, главным образом, в металлических конструкциях, фермах, мостах, колоннах, анкерных опорах и др.
Плотно-прочные швы применяются для клёпки паровых котлов и сосудов, подверженных внутреннему давлению газа, пара или жидкости. Для скрепления заклёпками в соединяемых деталях делают отверстия. Диаметр отверстий под заклёпку должен быть больше, чем диаметр заклёпки. Это необходимо для того, чтобы заклёпка в нагретом состоянии свободно входила в него. Например, при диаметре непоставленной заклёпки 19 мм диаметр отверстия под заклёпку должен быть 20 мм.
Ниже даны размеры отверстий для заклёпок диаметром от 8 до 37 мм. Диаметр заклёпки d 8 10 13 16 19 22 25 28 31 34 37 Диаметр отверстия под заклёпку d0 9 11 14 17 20 23 26 29 32 35 38
|
Замыкающая головка заклёпки образуется путём расклёпывания выступающего конца её. Клёпка производится вручную обыкновенными или пневматическими молотками, пневматическими машинами-скобами или гидравлическими прессами. Независимо от того, каким способом производится клёпка шва, заклёпки должны быть нагреты до температуры приблизительно 900—1000°С. В практике обычно подвергают нагреву заклёпки диаметром от 12 мм и выше. Заклёпки диаметром менее 12 мм ставят в холодном состоянии. Как при горячей, так и при холодной клёпке стер-
В котельных швах кромки склёпываемых листов скашивают под углом~75° для возможности подчеканки. Педчеканка возможна при толщине листов 5 мм и выше.
Если склёпываемые листы накладываются один на другой, то образуется соединение внахлёстку (фиг. 338, а). Если же склёпываемые листы примыкают один к другому кромками, то образуется соединение встык. В этом случае для скрепления листов применяются накладки, склёпываемые вместе с листами (фиг. 338, б).
Швы могут быть с одной или двумя накладками. На фиг. 338, б представлен шов с двумя накладками. Заклёпки в шве могут быть расположены в один ряд или в несколько, поэтому швы называются однорядными, двурядными (фиг. 339) и многорядными. По расположению заклёпок одного ряда по отношению к заклёпкам другого ряда различают швы: шахматные (фиг. 339) и параллельные (фиг. 338,б).
По числу срезов заклёпок плотно- прочные швы бывают одно- и двусрезные. Количество заклёпок, необходимых для образования шва, определяется расчётом на прочность и плотность по формулам курса деталей машин. Если известна толщина склёпываемых листов ?, то диаметр заклёпки d можно принимать равным ?+(6/8) мм. Расстояние между центрами заклёпок в ряду (шаг) принимается по эмпирическим формулам, приведённым на фиг. 338, 339 и 340.
Расстояние от центра заклёпки до края листа e = 1,5 d0. При вычерчивании шва должно быть показано на плане не менее двух-трёх заклёпок в одном ряду. Обрывы листов рекомендуется делать так, чтобы частично был виден нижний лист (фиг. 339).
Обрывы листов в проекциях должны быть согласованными. Размеры наносятся в числовых значениях.
На фиг. 340 дан пример стыка продольного и поперечного котельного плотно-прочного шва?
Прочные швы. Усилия, действующие на отдельные элементы заклёпочного соединения, должны быть направлены по их центру тяжести.
Поэтому следовало бы и заклёпки располагать именно по линии центра тяжести элемента. Однако во всех профилях центр тяжести проходит так близко от боковой стенки, что постановказа- клёпок становится невозможной. Это заставило распределять заклёпки по специальным линиям, называемым рисками. Положение рисок можно найти в любом справочнике по металлическим конструкциям. На фиг. 341 и 342 положение рисок определяется размером е1. В уголках до № 10 заклёпки располагают по одной риске, в уголках больших номеров— по двум рискам.
Шаг заклёпок t для прочных швов принимают в пределах t = 3/12d, где d—диаметр заклёпки. Расстояние е (фиг. 341 и 342) принимают равным 2/2,5d.
На фиг. 341 и 342 приведены примеры узлов клёпаной стропильной фермы.
Далее: Сварные швы (соединения). Электрическая сварка
www.nacherchy.ru
Заклепочные соединения металлов - Сборка металлоконструкций
Заклепочные соединения металловКатегория:
Сборка металлоконструкций
Заклепочные соединения металловСоединение деталей, образованное с помощью заклепок, называется заклепочным, а место соединения — клепаным швом.
На заклепках соединяют в основном пролетные строения мостов и конструкции промышленных зданий, работающих под динамической нагрузкой.
Заклепка — это цилиндрический стержень с головкой на конце. Ее вставляют в отверстие соединяемых деталей до упора головки и прижимают к поверхности детали. Выступающий конец осаживают пневматическим молотком или давлением специальной машины через обжимку и формируют вторую головку заклепки. Процесс формирования второй головки называется клепкой. Склепанные детали оказываются пронизанными стержнем заклепки и зажатыми между его двумя головками.
Изделия, детали которых соединены с помощью заклепок, называют клепаными конструкциями.
Для различных соединений применяют заклепки, отличающиеся одна от другой формой головки. Наиболее распространены заклепки с полукруглой головкой (ГОСТ 10299—80*): они наиболее прочные. Когда на поверхности склепываемой детали не Допускаются выступы, применяют заклепки с потайной головкой (ГОСТ 10300—80*).
По назначению заклепочные соединения бывают прочные, плотные, прочно-плотные. Прочные соединения обеспечивают только прочность. Этим способом соединяют элементы ферм, балок, колонн. Плотные соединения обеспечивают герметичность. Такие соединения делают в баках, резервуарах, где нет давления. Прочно-плотные соединения обеспечивают герметичность и прочность. Такими соединениями склепывают элементы в сосудах, резервуарах, баллонах, корпусах судов, где есть значительное внутреннее или внешнее давление.
По взаимному расположению склепываемых деталей различают нахлесточные заклепочные соединения, стыковые с одной накладкой или с двумя. Кроме того, различают соединения в зависимости от расположения заклепок: однорядные и многорядные; в последних заклепки могут быть расположены параллельными рядами или в шахматном порядке.
Склепанные детали сжаты при соединении растягивающими силами. Между этими деталями возникают силы трения тем больше, чем сильней эти детали сжаты заклепками. Растягивающее усилие Р в какой-то мере воспринимается силами трения, не допускающими сдвига — скольжения одного склепанного элемента по другому. Однако при расчетах прочности заклепочного соединения силы трения склепанных деталей не принимают во внимание. Условно допускают, что склепанные детали под нагрузкой сдвигаются одна относительно другой на величину зазора стержня заклепки в отверстии и последний начинает удерживать детали от дальнейшего смещения и разрушения соединения.
Если нагрузка слишком велика, заклепочное соединение может разрушиться по одной из следующих причин: срез заклепки; смятие стенок отверстий; разрыв одной из деталей по сечению, ослабленному заклепочными отверстиями; разрушение кромки одной из деталей по сечениям аб и вг.
Рис. 1. Схема расклепывания заклепки: а — заклепка вставлена в отверстие собранных деталей, б — д — осаживание стержня и формирование второй головки (замыкающей), е — сформованная вторая головка заклепки, ж -— заклепка на поддержке, з — конец формирования обжимной головки заклепки; 1 — заклепка, 2 — склепываемые листы, 3 — поддерживающая подставка (поддержка). 4 — обжимка
Рис. 2. Заклепочные соединения: однорядные: а — нахлесточное; б — стыковое с одной накладкой, в —с двумя накладками; двухрядные: г — стыковое с шахматным расположением заклепок, д — нахлесточное с параллельным расположением заклепок, е — с шахматным расположением заклепок с двумя накладками
Диаметр заклепок, которые одинаково прочны на срез и на смятие стенок отверстия, определяется из следующего условия: d—(1,8…2,2) t, где d — диаметр заклепки, мм; t — толщина склепанной детали, мм (если детали разной толщины, то в расчет принимают меньшую).
Шаг s заклепок, одинаково прочный на разрыв детали и на срез заклепок, принимают не менее 3d.
Из условия равной прочности на срез заклепок и кромок деталей находят размер обреза е= 15 d для обрезных кромок и 1,2 d — для прокатных.
Ось заклепочных отверстий должна отстоять от кромки на 1,5 d, если не требуется герметичное уплотнение (зачеканивание) кромок, и на 1,75 d, если необходимо зачеканивание кромок; увеличение ширины полосы до кромки вызывается желанием иметь запас материала для повторных зачеканиваний.
Если заклепки расположить на расстоянии 4d и более от кромки, то последняя начинает отходить от листа, в щели проникает влага, появляется ржавчина. По той же причине шаг заклепок в листовых соединениях не должен превышать 8 d.
При расчете длины заклепочного стержня необходимо для образования замыкающей головки учитывать усадку стержня при заполнении отверстия. Расчетом установлено (ГОСТ 10299—80*), что для формирования полноценной полукруглой головки выстулающий конец стержня заклепки должен составлять (1,5… … 1,75) d. Для потайной замыкающей головки длина выступающего стержня заклепки должна быть равна 0,8d.
Рис. 3. Работа заклепок в стыковом соединении: а — схемы нагрузок на заклепочное соединение, б — смещение склепанных деталей под нагрузкой и работа заклепки на срез, в срез заклепки под нагрузкой Р, г—смятие стенок отверстия под нагрузкой Р; 1 — толщина листа. d — диаметр заклепки,
Для заклепочных соединений с одной накладкой ее толщину рекомендуется выбирать одинаковой с толщиной t склепываемых листов, т. е. равной t или на 10% больше, т. е. равной 1,1 t. Если накладок две, то толщина каждой не должна быть менее 0,6. Когда одна накладка предназначена под потайную головку (накладка с раззенковкой), то ее толщину берут не менее 0,71, а вторую под нормальную головку делают толщиной 0,6.
Общая толщина склепываемых деталей, как правило, не должна превышать 5 d: при длинных заклепках невозможны усадка стержня от удара или давления и хорошее заполнение отверстий; кроме того, при остывании очень длинных заклепок продольные напряжения в стержне могут оторвать головку, особенно при отсутствии плавного перехода стержня в головку.
При разметке отверстий в профильной стали необходимо учитывать размещение обжимки.
Читать далее:
Болтовые соединения металлов
Статьи по теме:
pereosnastka.ru
4.7. Условные обозначения заклепочных соединений
При выполнении чертежей заклепочного соединения ГОСТ 2.313–82 «Условные изображения и обозначения неразъемных соединений» допускает применять упрощения. Размещение заклепок указывают на чертеже условным знаком «+». Все конструктивные элементы и размеры шва клепаного соединения указывают на чертеже (рис. 4.11).
В разрезе заклепки изображаются условными символами, приведенными в табл. 4.4.
Таблица 4.4
Условные изображения соединений, получаемых клепкой (по гост 2.313–82)
Вид соединения | Изображение | Условное обозначение | |
в сечении | на виде | ||
1 | 2 | 3 | 4 |
1. Заклепка с полукруглой головкой и с полукруглой замыкающей головкой | |||
2. Заклепка с потайной головкой и с полукруглой замыкающей головкой | |||
3. Заклепка с потайной головкой и с потайной замыкающей головкой |
1 | 2 | 3 | 4 |
4. Заклепка с полупотайной головкой и с потайной замыкающей головкой | |||
5. Заклепка специальная (вытяжная) |
Если предмет, изображенный на чертеже, имеет ряд однотипных соединений с заклепками одного типа и с одинаковыми размерами, то заклепки, входящие в соединение, следует показать условно в одном-двух местах каждого соединения, а в остальных – центровыми или осевыми линиями (рис. 4.11).
Рис. 4.11. Условное изображение на чертеже однотипных заклепок
Если на чертеже необходимо показать несколько групп заклепок различных типов и размеров, то рекомендуется отмечать одинаковые заклепки одним и тем же условным знаком (рис. 4.12а) или одинаковыми буквами (рис. 4.12б).
а б
Рис. 4.12. Условное изображение на чертеже разнотипных заклепок
Условное обозначение заклепки приводят в технических требованиях чертежа или на полке линии-выноски, проведенной непосредственно от изображения заклепки, записью по типу: «Заклепка 2 × 8 ГОСТ 10299–80», которая указывает, что заклепка с полукруглой головкой имеет диаметр стержня d = 2 мм и длину L = 8 мм [14–18].
4.8. Контрольные вопросы
1. Поясните сущность процесса клепки.
2. Из каких материалов изготавливаются заклепки?
3. Перечислите основные виды заклепок.
4. Перечислите основные виды заклепочных соединений, дайте им краткую характеристику.
5. Перечислите и поясните основные этапы выполнения заклепочного соединения.
6. Какие инструменты необходимы для осуществления процесса клепки?
7. Перечислите основные виды брака при выполнении заклепочного соединения.
8. Поясните основные способы изготовления ювелирных заклепок.
9. Каким образом обозначаются и изображаются заклепочные соединения на чертежах и в документации?
Список использованной литературы
1. Стильная штучка // Jewel. – 2008. – №4. – С. 60.
2. Гримвейд М.Ф. Руководство по пайке и другим техникам соединения в производстве ювелирных изделий из золота: пер. с англ. / Марк Ф. Гримвейд. – Омск: Дедал-Пресс, 2007. – 64 с.
3. Новиков В.П. Ручное изготовление ювелирных украшений / В.П. Новиков, В.С. Павлов. – Л.: Политехника, 1991. – 208 с.
4. Технология сплавов благородных металлов: учебник для вузов / С.Н. Бошин, В.А. Гусев, В.П. Калашник [и др.]; под редакцией проф. С.Н. Бошина. – Кострома: Изд-во Костром. гос. технол. ун-та, 2002. – 222 с.
5. Бреполь Э. Теория и практика ювелирного дела / Э. Бреполь. – СПб.: Соло, 2000. – 528 с.
6. ГОСТ 19248–90. Припои. Классификация и обозначения. – М.: Изд-во стандартов, 1990.
7. Новиков В.П. Практикум по ювелирному делу / В.П. Новиков. – СПб.: Континент, 2005. – 944 с.
8. ГОСТ 30649–99. Сплавы на основе благородных металлов ювелирные. Марки. – М.: Изд-во стандартов, 1999.
9. Галанин С.И. Художественное материаловедение: неметаллические материалы: в 2 ч. Часть 2. Стекло, керамика, композиционные и древесные материалы, флюсы: учебное пособие / С.И. Галанин. – Кострома: Изд-во Костром. гос. технол. ун-та, 2009.– 128 с.
10. Мак Крайт Т. Полное руководство по обработке металлов для ювелиров. Иллюстрированный справочник: пер. с англ. / Тим Мак Крайт. – Омск: Издательский дом «Дедал-пресс», 2006.– 206 с.
11. Аппараты микропайки «Mig-O-Mat» // Ювелирное обозрение. – 2008. – Февраль. – С. 23.
12. Пламя из воды // Ювелирное обозрение. – 2011. – Июнь. – С. 31.
13. Без кислоты, но травят не кисло // Ювелирное обозрение. – 2008. – Апрель. – С. 27.
14. ГОСТ 2.313–82. Условные изображения и обозначения неразъемных соединений. – М.: Изд-во стандартов, 1982.
15. Куликов В.П. Стандарты инженерной графики: учебное пособие / В.П. Куликов. – 2-е изд., испр. и доп. – М.: ФОРУМ, 2008. – 240 с.
16. Чекмарев А.А. Справочник по машиностроительному черчению / А.А. Чекмарев, В.К. Осипов. – 7-е изд., перераб. – М.: Высшая школа, 2007. – 493 с.
17. Левицкий В.С. Машиностроительное черчение и автоматизация выполнения чертежей: учебник для втузов / В.С. Левицкий. – 8-е изд., перераб. и доп. – М.: Высшая школа, 2007. – 435 с.
18. Гжиров Р.И. Краткий справочник конструктора: справочник / Р.И. Гжиров. – Л.: Машиностроение, Ленинградское отд-ние, 1983. – 464 с.
19. ГОСТ 19249–73. Соединения паяные. Основные типы и параметры. – М.: Изд-во стандартов, 1973.
20. Виноградов В.М. Основы сварочного производства: учебное пособие для вузов / В.М. Виноградов, А.А. Черепахин. – М.: Академия, 2008. – 272 с.
21. ГОСТ 2601–84. Сварка металлов. Термины и определения основных понятий. – М.: Изд-во стандартов, 1984.
22. ГОСТ 19521–74. Сварка металлов. Классификация. – М.: Изд-во стандартов, 1974.
23. Аппараты точечной электросварки // Ювелирное обозрение. – 2008. – Апрель. – С. 22–23.
24. Инструмент. Оборудование. Технологии // http://www.sapphire.ru.
25. Специально для ювелиров // Ювелирное обозрение. – 2011. – Февраль. – С. 41.
26. Лазер в мастерской ювелиров // Ювелирное обозрение. – 2011. – Июнь. – С. 32.
27. Кузнецов И. Синтерирование – технология XXI века / И. Кузнецов // Ювелирное обозрение. – 2005. – Март. – С. 42–43.
28. Миджетт С. Мокуме гане. Полный обзор: пер. с англ. / Стив Миджетт. – Омск: Дедал-Пресс, 2005. – 160 с.
29. ГОСТ Р ИСО 17659–2009. Сварка. Термины многоязычные для сварных соединений. – М.: Изд-во стандартов, 2009.
30. ГОСТ 2.312–72 ЕСКД. Условные изображения и обозначения швов сварных соединений. – М.: Изд-во стандартов, 1972.
31. Ковачич Л. Склеивание металлов и пластмасс: пер. со словац. / Л. Ковачич; под ред. А.С. Фрейдина. – М.: Химия, 1985. – 240 с.
32. Шилдз Дж. Клеящие материалы: справочник: пер. с англ. Ю.А. Гаращенко [и др.] / Дж. Шилдз; под ред. В.П. Батизата. – М.: Машиностроение, 1980. – 368 с.
33. Халилов И. Особенности облагораживания ювелирных камней / Ибрагим Халилов // Ювелирное обозрение. – 2008. – Май. – С. 24–26.
ПРИЛОЖЕНИЕ 1
studfiles.net
Соединения заклёпочные
Соединения при помощи заклепок являются неразъемными соединениями (см. фиг. 498). Заклепка представляет собой цилиндрический стержень, на одном конце которого находится головка.
При склепывании деталей заклепки располагают рядами. Совокупность рядов составляет заклепочный шов.Различают следующие типы заклепочных соединений:а) Внахлестку (фиг. 500), когда склепываемые элементы накладывают один на другой.
б) В стык с одной (фиг. 501) или двумя накладками (фиг. 502).
Головки заклепок могут быть вычерчены по относительным размерам в зависимости от диаметра стержня заклепки (фиг. 503).
1. Размеры заклепок. При выборе размеров заклепок в зависимости от толщины склепываемого материала можно руководствоваться табл. 34 - 37 и фигуры 504, 505.
Размеры заклепок в мм Таблица №34.
Толщина скрепляемого материала в мм Таблица №35.
Размеры заклепок в мм Таблица №36.
Толщина скрепляемого материала в мм (Таблица №37).
2. Расположение заклепок. В прочных заклепочных швах (балках, фермах, рамах и т. д.):а) При рядовом расположении заклепок шаг заклепок t ≥ Зd;б) При шахматном расположении расстояние между центрами заклепок по диагонали ta ≥ 3,5dв) Расстояние от центра заклепки до свободной кромки по направлению действия силы t1 ≥ 2d при необрезных кромках и t1 = 1,5d при обрезных;г) Расстояние до свободной кромки в направлении, перпендикулярном к действию силы: t2 ≥ 1,5d при необрезных кромках и t2 ≥ 1,2d при обрезных кромках (фиг. 506).
В крайнем ряду при наличии окаймляющего уголка и в среднем ряду t ≤ 16d или t ≤ 24S при растяжении, t ≤ 12d или t ≤ 16S при сжатии (фиг. 507).
В крайнем ряду при отсутствии окаймляющего уголка t ≤ 8d или t ≤ 12S при растяжении и сжатии. Наибольшее расстояние центра заклепки от края листа t2 ≤ 4d или t2 ≤ 8d при растяжении и сжатии (фиг. 508).
В таблицах 38 - 40 приведены данные размещения осей заклепок для прочных швов в прокатных профилях.
Размещение осей заклепок в уголках (фиг. 509) Таблица №38.
Размещение осей заклепок по стенке двутавров и швеллеров (фиг. 510) Таблица №39.
Размещение осей заклепок по полкам двутавров и швеллеров (фиг. 511) Таблица №40.
3. Условное изображение заклепок на чертежах. В тех случаях, когда на чертежах не требуется указывать диаметры заклепок, а необходимо показать форму головок, следует заклепки изображать условно в соответствии с таблицей 41. Для указания только размещения заклепок следует применять условное изображение в виде знака.
Условные изображения заклепок Таблица №41.
Если заклепки имеют различные диаметры и длины, то на чертеже следует указывать:а) Для наиболее распространенных размеров подписью по типу: Все заклепки d X Ɩ кроме оговоренных', например, Все заклепки 13 X 45, кроме оговоренных.б) Для заклепок с оговариваемыми размерами указать и их размеры около изображения по типу фиг. 512.
Отверстия для заклепок, которые должны быть просверлены при монтаже, следует пояснять надписью: Сверлить по месту, Сверлить при монтаже и т. д. Если отверстия имеют различные размеры, необходимо на чертеже дать соответствующие указания. При изображении на чертежах отверстий и заклепок, оси которых параллельны плоскостям проекций, допускается выполнять их в виде осевых линий (фиг. 513).
На выносках могут быть указаны их размеры и другие данные. На фигуре 514 приведен пример чертежа узла, детали которого соединены при помощи заклепок.
Зубчатые передачи.....
www.viktoriastar.ru
Заклепочное соединение
Неразъемные соединения должны обеспечивать точность взаимного расположения деталей и сохранение этого расположения в рабочих условиях прибора.
Заклепочные соединения осуществляют с помощью заклепок или непосредственным расклепыванием цапф деталей.
Заклепочные соединения в приборостроении на прочность не рассчитывают. Основным типом является заклепка с полукруглой головкой, применяемая в тех случаях, когда можно допустить выступающую головку. Заклепки с потайной и полупотайной головками применяют там, где толщина деталей позволяет производить зенковки под головку. Заклепки с плоской и полупотайной головками применяют при соединении деталей, изготовленных из непрочного материала, например, из кожи, текстолита, эбонита, дерева.
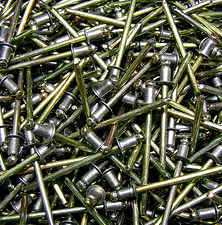
Заклепки пустотелые (и трубчатые тип I) применяют для соединения деталей в тех случаях, когда образование головки обычным путем невозможно. Область применения их ограничивается непрочными материалами. Заклепки с засверленными концами (и трубчатые тип II) могут применяться в тех же случаях, что и обычные. Выбор длин заклепок (с учетом стандартных длин) для образования полукруглой и полупотайной головок в зависимости от толщины склепываемых деталей и отверстия под заклепки. Кроме стандартных материалов для заклепок могут быть применены серебро, платино-иридиевый сплав для контактов и другие цветные металлы, назначение которых рассматривается в каждом конкретном случае.
Примеры условных обозначений заклепок согласно шифрам материалов и покрытий приведены ниже:
- 1) Заклепка диаметром 3 мм, длиной 12 мм по ГОСТ 10299—68 (с полукруглой головкой) из материала подгруппы 01, с покрытием по группе 1 обозначается:«Заклепка ЗХ 12—011 ГОСТ 10299—68».
- 2) Заклепка диаметром 2 мм, длиной 6 мм по ГОСТ 10303—68 (с плоской головкой) из материала подгруппы 62, с покрытием по группе 3 обозначается:«Заклепка 2X 6—623 ГОСТ 10303—68».
- 3) Заклепка диаметром 4 мм, длиной 20 мм по ГОСТ 10301—68 (с полупотайной головкой) из материала подгруппы 70, без покрытия обозначается:«Заклепка 4X 20—700 ГОСТ 10301—68».
Соединения заклепками относятся к типу А — болтовое соединение. Головки, образующиеся при непосредственном расклепывании цапф и выступов, имеют различную форму, например, потайную, полукруглую и т. п. При расклепывании квадратной или цилиндрической цапфы головка обычно приобретает плоскую форму. Для надежного и прочного соединения при непосредственном расклепывании цапф деталей прибегают к увеличению длины выступа с последующей зачисткой расклепанного места.
metiz-bearing.ru
ГОСТ 10304-80
ГОСТ 10304-80
Группа Г34
МКС 21.060.40
Дата введения 1981-01-01
1. РАЗРАБОТАН И ВНЕСЕН Министерством станкостроительной и инструментальной промышленности СССР
2. УТВЕРЖДЕН И ВВЕДЕН В ДЕЙСТВИЕ Постановлением Государственного комитета СССР по стандартам от 06.05.80 N 2011
3. Стандарт полностью соответствует СТ СЭВ 1329-78
4. Взамен ГОСТ 10304-70
5. ССЫЛОЧНЫЕ НОРМАТИВНО-ТЕХНИЧЕСКИЕ ДОКУМЕНТЫ
________________* ТУ, упомянутые здесь и далее по тексту, не приводятся. За дополнительной информацией обратитесь по ссылке. - Примечание изготовителя базы данных.
6. Ограничение срока действия снято по протоколу N 5-94 Межгосударственного совета по стандартизации, метрологии и сертификации (ИУС 11-12-94)
7. ИЗДАНИЕ (ноябрь 2004 г.) с Изменениями N 1, 2, 3, утвержденными в мае 1982 г., апреле 1985 г., июне 1990 г. (ИУС 8-82, 7-85, 10-90)
Настоящий стандарт распространяется на заклепки общемашиностроительного применения, классов точности В и С, предназначенные для работы при температуре от плюс 300 до минус 60°С.Стандарт полностью соответствует СТ СЭВ 1329-78.
1. ТЕХНИЧЕСКИЕ ТРЕБОВАНИЯ
1.1. По форме, размерам, предельным отклонениям, не указанным в настоящем стандарте, заклепки должны соответствовать стандартам на технические условия.(Измененная редакция, Изм. N 3).
1.2. Схема построения условных обозначений заклепок приведена в приложении 1.
1.3. Марки материалов и их условные обозначения должны соответствовать указанным в табл.1.
Таблица 1
________________* Сведения о материалах приведены в приложении 2.Допускается применять другие материалы с временным сопротивлением не ниже указанного в табл.2.
Таблица 2
Материал заклепок | Вид термообработки | Временное сопротивление срезу, МПа(кгс/мм), не менее | |
Наименование | Марка | ||
Сталь | Ст2, Ст3 | Отжиг | 250 (25) |
10, 15 | |||
10кп, 15кп | |||
09Г2 | Без термической обработки | 380 (38) | |
12Х18Н9Т,12Х18Н10Т | Закалка | 430 (43) | |
Латунь | Л63 | Отжиг | - |
Л63(антимагнитная) | |||
Медь | М3, МТ | 190 (19) | |
Алюминиевые сплавы | АМг5П | Без термической обработки | 160 (16) |
АД1 | 60 (6) | ||
Д18 | Закалка и естественное старение | 190 (19) |
(Измененная редакция, Изм. N 1, 2, 3).
1.3а. Заклепки должны изготовляться с покрытиями или без покрытий. Виды покрытий и их условные обозначения - по ГОСТ 1759.0. Выбор толщины покрытий - по ГОСТ 9.303.
(Измененная редакция, Изм. N 3).
1.4. Технические требования к покрытиям - по ГОСТ 9.301.
1.5. Временное сопротивление срезу заклепок должно соответствовать указанному в табл.2.
1.6. Допускается изготовлять заклепки без термической обработки.
1.7. Заклепка должна выдерживать испытание в холодном состоянии на прочность соединения головки со стержнем. Изгиб головки по отношению к стержню на угол 15° должен происходить без возникновения поперечных надрывов.
1.8. Конец стержня или металла, подготовленного для изготовления заклепок, должен выдерживать испытание на расклепываемость без появления в образованной головке трещин и надрывов. Испытанию на расклепываемость допускается не подвергать заклепки, изготовленные методом холодной штамповки, и термообработанные заклепки.
1.7, 1.8. (Измененная редакция, Изм. N 3).
1.9. Поверхность заклепок должна быть чистой, без грата, трещин, надрывов, расслоений материала, пузырей, раковин и отделяющейся окалины.
На поверхности допускаются:
поверхностные дефекты, допускаемые стандартами на проволоку и прутки, из которых изготовляют заклепки, в том числе дефекты, измененные в результате деформирования материала при высадке. Глубина измененных дефектов на головках должна быть не более 0,2 мм;
следы инструмента и закаты, находящиеся в пределах допустимых отклонений размеров заклепок;
заусеницы на головке, если их величина не превышает половины поля допуска на диаметр головки заклепки; для заклепок с диаметром стержня >16 мм заусеницы на головках не более 1 мм;
неотделяющийся цветной налет окисей. (Измененная редакция, Изм. N 2, 3).
1.9а. Шероховатость поверхности заклепок не должна превышать: =6,3 мкм для класса точности В,=50 мкм для класса точности С.Шероховатость поверхностей заклепок, изготовленных методом холодной штамповки, и шероховатости торца стержня не контролируются.(Введен дополнительно. Изм. N 3).
1.10. Поля допусков и предельные отклонения размеров заклепок должны соответствовать указанным в табл.3.
Таблица 3
Наименование параметра | Поля допусков и предельные отклонения | |
Класс точности В | Класс точности С | |
Диаметр стержня | ||
Диаметр головки | ||
Длина заклепки | ||
Высота головки >1 мм |
1.11. Допускаемые отклонения формы и расположения поверхностей не должны превышать следующих значений:косой срез стержня (черт.1): =3° для диаметров от 1 до 16 мм; =5° " " свыше 16 мм;допуск перпендикулярности опорной и торцовой поверхностей головок относительно оси стержня (черт.1) ; =0,0175 для класса точности В и =0,0349 для класса точности С;
Черт.1
высота цилиндрического пояска и недопрессовка на вершине головок в виде площадок (черт.2) - согласно табл.4.
Черт.2
Таблица 4
мм
До 3 | Св. 3 до 6 | Св. 6 до 10 | Св. 10 до 18 | Св. 18 до 30 | Св. 30 до 50 | Св. 50 | |
, не более | 0,3 | 0,4 | 0,6 | 1,5 | 2,0 | 2,5 | 3,0 |
, не более | 0,5 | 0,6 |
Для заклепок диаметром стержня до 6 мм по согласованию между изготовителем и потребителем допускается увеличение значений , указанных в табл.4 на 0,1 мм;допуск соосности оси головки относительно оси стержня (черт.2) - согласно табл.5.
Таблица 5
мм
От 1 до 1,6 | Св. 1,6 до 2,5 | Св. 2,5 до 5 | Св. 5 до 8 | Св. 8 до 18 | Св. 18 до 24 | Св. 24 до 36 | |
0,2 | 0,32 | 0,4 | 0,6 | 1,0 | 2,0 | 3,0 |
уменьшение диаметра стержня, измеренное на расстоянии, равном диаметру стержня от конца заклепки, - согласно табл.6.
Таблица 6
мм
От 1 до 10 | Св. 10 до 13 | Св. 13 до 18 | Св. 18 до 30 | Св. 30 до 36 | |
Уменьшение диаметра конца стержня | В пределах нижнего отклонения | - 0,7 | - 0,8 | - 1,0 | - 1,4 |
1.10, 1.11. (Измененная редакция, Изм. N 3).
2. ПРИЕМКА
2.1. Правила приемки заклепок - по ГОСТ 17769.
2.2. Каждая партия заклепок должна сопровождаться документом о качестве с указанием:наименования или товарного знака завода-изготовителя;условного обозначения заклепок;перечня и результатов проведенных испытаний;массы нетто партии;средств временной противокоррозионной защиты и срока защиты.Примечание. Допускается вкладывать документ о качестве заклепок в тару или контейнер, при этом должна обеспечиваться сохранность его при транспортировании.Разд.2. (Измененная редакция, Изм. N 3).
3. МЕТОДЫ КОНТРОЛЯ
3.1. Контроль механических свойств заклепок должен производиться на соответствие требованиям табл.2.
3.2. Контроль качества покрытий - по ГОСТ 9.302.
3.3. Внешний вид заклепок (п.1.9) проверяют визуально без применения увеличительных приборов.Для заклепок диаметром менее 3 мм допускается применение увеличительных средств (до 3).
3.4. Шероховатость поверхности проверяют сравнением с образцами шероховатости по ГОСТ 9378 или приборами.Шероховатость поверхности заклепок, изготовленных методом холодной высадки, не контролируется.
3.5. Отклонения размеров и расположения поверхностей заклепок проверяют предельными калибрами, шаблонами, контрольными матрицами, универсальными измерительными приборами или инструментом.Длина заклепок при косом срезе конца должна проверяться по короткой стороне стержня.
3.6. Высоту потайных и полупотайных головок заклепок проверяют с помощью контрольной матрицы и шаблона по схеме, указанной на черт.3.Высоту полупотайных головок заклепок Н контролируют по размеру (Н+h) с допуском, равным по величине допуску на размер H, черт.4. Допускаются другие методы контроля высоты головок.
Черт.3
Черт.4
3.5, 3,6. (Измененная редакция, Изм. N 3).
3.7. Отклонение от перпендикулярности опорной поверхности головки к оси стержня проверяют угловым шаблоном или щупом по просвету между опорной поверхностью головки и торцевой поверхностью контрольной матрицы.
3.8. Прямолинейность стержня заклепок проверяют по свободному вхождению заклепки в контрольную матрицу, диаметр отверстия которой соответствует максимальному диаметру стержня заклепки.Поле допуска отверстия матрицы - Н14.
3.9. Отклонение от соосности головки относительно стержня заклепок определяют разностью размеров и (черт.5), измеренных с помощью штангенглубиномера или микрометрического глубиномера. Допускаются другие методы контроля.
Черт.5
(Измененная редакция, Изм. N 1, 3).
3.10. Значения величины угла и радиуса скругления плоской головки, радиуса под головкой, перпендикулярности опорной и торцовой поверхностей головок к оси стержня, прямолинейности стержня, косой срез стержня и соосность головки относительно оси стержня допускается не контролировать в готовых заклепках при условии обеспечения этих геометрических параметров инструментом.(Измененная редакция, Изм. N 2, 3).
3.11. Прочность соединения головки со стержнем испытывают в контрольной матрице по схеме, указанной на черт.6 ударами по головке заклепки до соприкосновения ее опорной поверхности с плоскостью матрицы.
Черт.6
Диаметр отверстия матрицы должен выбираться из 2-го ряда ГОСТ 11284.Надрывы под головкой не допускаются.Испытанию не подлежат заклепки с потайной и полупотайной головками, отожженные и изготовленные горячей штамповкой.
3.12. Испытание на расклепываемость стержня заклепок - по ГОСТ 8818.Допускается проводить испытание стальных заклепок с диаметром стержня более 10 мм в горячем состоянии (при температуре 850°С-950°С).
3.13. Испытание заклепок на срез стержня проводят по требованию потребителя по методике, согласованной между изготовителем и потребителем.При определении значения временного сопротивления срезу расчет ведется по действительному диаметру заклепок.Допускается вместо заклепок подвергать испытанию образцы проволоки из бухты, которая была использована для высадки заклепок (при условии, что эти образцы термообработаны одновременно с представленными на испытание заклепками).(Введен дополнительно, Изм. N 1).
3.14. Методика контроля покрытий - по ГОСТ 9.302.(Введен дополнительно, Изм. N 3).
4. ТРАНСПОРТИРОВАНИЕ И ХРАНЕНИЕ
Упаковка заклепок, маркировка тары, транспортирование и хранение - по ГОСТ 18160. Разд.4. (Введен дополнительно. Изм. N 3).Разд.5. (Исключен, Изм. N 1).
ПРИЛОЖЕНИЕ 1 (обязательное). Схема построения условного обозначения заклепок
ПРИЛОЖЕНИЕ 1Обязательное
1 - класс точности. Класс точности В не указывается; 2 - диаметр стержня; 3 - длина; 4 - условное обозначение марки (группы) материала; 5 - марка материала. Указывается для групп 01, 03, 21, 38 и для материала, не предусмотренного в настоящем стандарте. Допускается не указывать марку материала для групп 01, 03, 21, 38; 6 - условное обозначение вида покрытия. Отсутствие покрытия не указывается; 7 - толщина покрытия; 8 - обозначение стандарта на конкретный вид заклепок.Пример условного обозначения заклепки класса точности С, диаметром d=8 мм, длиной L=20 мм, из материала группы 38, марки меди М3, с никелевым покрытием толщиной 6 мкм:
Заклепка С 820.38.М3.136 ГОСТ...
ПРИЛОЖЕНИЕ 1. (Измененная редакция, Изм. N 2, 3).
ПРИЛОЖЕНИЕ 2 (справочное). Материалы для изготовления заклепок
ПРИЛОЖЕНИЕ 2Справочное
Кроме стандартных материалов, приведенных в табл.1, для изготовления заклепок применяют следующие марки стали: Ст2, Ст3 по ОСТ 14-2-188 и ОСТ 14-15-193; сталь марок 10, 15 по ТУ 3-80.ПРИЛОЖЕНИЕ 2. (Введено дополнительно. Изм. N 3).Электронный текст документаподготовлен АО "Кодекс" и сверен по:официальное изданиеМ.: ИПК Издательство стандартов, 2005
docs.cntd.ru
Заклепочные соединения
Заклепочными называют неразъемное соединение деталей (обычно листовых) с помощью заклепки – сплошного или полого цилиндрического стержня с закладной головкой.
Конструктивные формы заклепок:
а) с полукруглой головкой;
б) с потайной головкой;
в) с плоской головкой;
г) с полукруглой головкой;
д) с полупотайной головкой;
е) пустотелая.
Соединение собирают путем установки заклепок в предварительно подготовленные отверстия в деталях и последующей осадки клепки специальным инструментом второй замыкающей головки (рис. 23.1).
Соединения применяют в основном в авиа и судостроении, металлоконструкциях и других изделиях, в которых внешние нагрузки действуют параллельно плоскости стыка, а применение сварки, пайки и склеивания оказывается невозможным по конструктивным или технологическим соображениям.
По назначению различают прочные, плотные (герметичные) и прочноплотные соединения.
Прочными называют соединения, основная задача которых состоит в передаче нагрузки.
Плотные соединения должны обеспечивать главным образом герметичность конструкции (например, топливные баки).
Прочноплотные соединения служат как для передачи нагрузки, так и для обеспечения герметичности конструкции.
По конструкции различают соединения:
1. Внахлестку (рис. 23.2)
d=S+8 мм;
t=2d+8 мм;
l=1,35d.
2. Встык с одной прокладкой (рис. 23.3)
d=S+8 мм;
t=2d+8 мм;
l=1,35d…1,5d;
S1=1…1,25S.
3. Встык с двумя накладками (рис. 23.4)
d=S+(5…6) мм;
t=2,6d+10 мм;
l=1,35d;
l1=3d;
S1=(0,6…0,7)S.
Заклепки в соединении располагают рядами или в шахматном порядке. Основные недостатки соединений связаны с невысокой технологичностью и высокой трудоёмкостью изготовления, а также сложностью контроля качества.
Заклепки изготавливают из пластичных (d³15%) сталей 15, 20, 09Г2, 20ХМА, 20ГА и др. алюминиевых сплавов В65, АД-1, АМг5Г, и др. титановых сплавов ОТ4, ВТ16 и др.
Расчет соединений при симметричном нагружении
Принимают, что нагрузка равномерно распределяется между всеми одиночными соединениями. В нахлесточных и стыковых соединениях с одной накладкой, называемых односрезными, заклепки работают на срез и изгиб из-за несовпадения плоскостей действия сил F, то есть под действием момента M= F a (рис. 23.5). Момент возрастает с увеличением толщины листов; он воспринимается стержнем и головками заклепки, вызывая их деформации (сдвиг и изгиб). В результате контактные напряжения sk между листами и стержнем заклепки, уравновешивающие силы F, будут неравномерно распределяться по высоте заклепки и в окружном направлении, концентрируясь вблизи стыка листов.
Характер распределения нагрузки по высоте заклепки будет зависеть от соотношения изгибных податливостей головки и стержня. При податливой головке нагрузка по длине соединения распределяется так, что часть изгибающего момента воспринимается головкой. В заклепке с очень податливой головкой последняя не воспринимает изгибающего момента. Изгиб головки вызывает концентрацию напряжений в зоне сопряжения её со стержнем, а также концентрацию контактных напряжений на опорных поверхностях. Это создает угрозу усталостного обрыва головки (опасное сечение показано волнистой линией) и возникновения фреттинг-коррозии и трещин в зонах контакта. Отверстия в соединяемых листах являются источником значительной концентрации ( в точке В) и причиной возникновения усталостных трещин и разрушения листов (опасное сечение показано волнистой линией). Наиболее распространены повреждения заклепочных соединений, связанные со срезом заклепок, обрывом головок, смятием стенок отверстий возникновением и развитием трещин вблизи отверстий, приводящих к разрушению листов.
Расчет заклепок
Разрушение стержня заклепки нахлесточного соединения и стыкового соединения с одной накладкой происходит в результате среза по сечению, лежащему в плоскости стыка соединяемых деталей.
Для определения размеров заклепки проводят условные расчеты на срез и смятие. Для упрощения принимают, что стяжка пакета и трение на стыке листов отсутствуют, а вся внешняя нагрузка воспринимается заклепками. Приближенный характер расчетов учитывается при назначении допускаемых напряжений. Номинальные напряжения среза (касательные напряжения) будут одинаковыми во всех точках сечения и условие прочности стержня заклепки по допускаемым напряжениям примет вид
,
где F – срезывающая сила в плоскости стыка; А– суммарная площадь поперечного сечения и заклепок с диаметром стержня d; - допускаемое напряжение при срезе.
Откуда требуемый диаметр заклепки
.
В соединениях с двумя накладками, соединение может разрушаться путем среза по двум сечениям, совпадающим с плоскостями контакта накладок с соединяемыми деталями. Такие соединения называют иногда двухсрезными. При их расчете принимают, что сила, приходящаяся на одно сечение, вдвое меньше общей силы.
Смятие стержня заклепки может привести к преждевременному выходу из строя соединения, если заклепка изготовлена из менее прочного материала, чем соединяемые детали. Действительные контактные напряжения, вызывающие смятие стержня заклепки, неравномерно распределены по его поверхности. Однако расчетные значения этих напряжений находят по приближённой формуле и сопоставляют с допускаемыми напряжениями на смятие материала заклепки
, отсюда .
Из двух найденных расчетами на срез и на смятие значений диаметра d заклепки принимают большее.
Похожие статьи:
poznayka.org