Назначение и конструкция станков для резки арматуры. Станок для арматуры
Оборудование для заготовки арматуры
Строительные машины и оборудование, справочник
Категория:
Путевые и дорожные машины
Оборудование для заготовки арматурыВ состав работ, связанных с изготовлением арматуры, входит очистка, правка, резка, упрочнение и сварка арматурной стали. Со склада арматура подается в заготовительное отделение, в котором установлены правильно-отрезные станки, станки для резки и гибки арматуры, стыковые сварочные машины и точила для зачистки концов стержней.
При прохождении через правильный барабан станка для правки и резки стали прутки арматурной стали диаметром до 14 мм самоочищаются от грязи, окалины и коррозии. Для очистки стали диаметром 14—25 мм используют специальные станки с щетками, совершающими сложное движение. Очищенная арматура имеет лучшее сцепление с бетоном.
Правку и резку арматуры диаметром от 4 до 14 мм выполняют на правильно-отрезных станках и станках-автоматах (рис. 160). Проволока с бухты, пройдя ограждение, тянущими роликами протягивается через правильный барабан и поступает в направляющий лоток. Конец проволоки, упираясь в переставной рычажный упор отмеривающего устройства, включает дисковые ножи, которые отрезают пруток заданной длины. Отрезанные стержни сосредоточиваются на приемном устройстве.
Рис. 160. Принципиальная схема станка для непрерывной правки и резки арматурной стали
Правильный барабан вращается в подшипниках, установленных в корпусах и закрепленных в станине. Барабан приводится во вращение от электродвигателя через клиноременную передачу. На концах барабана по оси установлены неподвижные плашки, которые могут быть передвинуты в осевом направлении и зафиксированы винтами. В средней части барабана в стаканах установлены регулируемые плашки, которые с помощью винтов могут смещаться в радиальном направлении. Плашки устанавливают так, чтобы линия, соединяющая их центры, образовывала волну с небольшой амплитудой. При протягивании проволоки барабан с плашками вращается от двигателя, и все изгибы исправляются. В случае пробуксовки тянущих роликов величина их нажатия регулируется нажимным винтом. Привод тянущих и отрезных роликов осуществляется от электродвигателя.
Рис. 161. Станок (С-370А) для-резки арматурной стали диаметром до 40 мма — кинематическая схема; б — конструктивная схема
Скорость резания ножей соответствует скорости вращения тянущих роликов, благодаря чему обеспечивается непрерывная правка и резка проволоки. Приемное устройство служит для приема выправленного арматурного стержня и сбора отрезанных прутков. Приемное устройство имеет направляющую откидную рейку, которая автоматически открывает канал для сброса прутка. Скорость подачи проволоки в таких станках достигает 1,5 м/с и более. Мощность привода составляет 4—7 кВт. В практике находят применение также станки с периодической “подачей проволоки, где резка осуществляется ножами гильотинного типа. Арматуру диаметром от 20 до 45 мм правят на правйльных станках тяжелого типа с двигателем мощностью до 50 кВт.
В тех случаях, когда для заготовки арматуры применяют круглую сталь диаметром до 40 мм, режут ее на специальных приводных станках (рис. 161). Массивная станина 8, двигатель и передачи этого станка смонтированы на опорной раме (салазках), позволяющей перемещать его с одного места на другое. Движение от двигателя посредством клиноременной передачи трансмиссионного вала и двухступенчатого редуктора передается кулисному механизму, который вместе с подвижным ножом совершает возвратно-поступательное движение. Подвижный нож, входя в соприкосновение с неподвижным ножом, отрезает пруток арматуры. Производительность станка 32 реза в 1 мин, мощность двигателя 2,8 кВт, масса станка 0,45 т.
В настоящее время создан станок С-445М для резки, арматурной стали диаметром до 70 мм, привод станка гидравлический. Неподвижный нож крепится к поверхности рабочего цилиндра, а подвижный установлен в держателе на поршне. Станок может работать в автоматическом цикле, при котором подвижный нож совершает возвратно-поступательное движение в вертикальной плоскости и производит одиночные резы. При малых объемах для резки арматурной стали диаметром до 20 мм применяют станки с ручным приводом.
Упрочнение арматуры. Сталь, применяемую для изготовления арматуры, в большинстве случаев предварительно упрочняют, что позволяет соответственно уменьшить расход арматуры в железобетоне на 20—30%. Упрочнение арматуры производится вытяжкой, скручиванием, сплющиванием (профилированием) и волочением. В результате скручивания и сплющивания арматуре придается периодический профиль, что значительно повышает ее сцепление с бетоном. Арматуру вытягивают в холодном состоянии до появления в ней напряжения, несколько превышающего предел текучести. В результате такой вытяжки сталь получает наклеп, ее предел текучести повышается. Для целей вытяжки используют механические (грузовые), гидравлические и гидромеханические установки. Наибольшее усилие, развиваемое механической установкой, показанной на рис.162, а, достигает 25 т, что позволяет обрабатывать сталь диаметром до 22 мм. Упрочняемый пруток зажимами соединяется с тягами, одна из которых навивается на барабан лебедки, а вторая крепится к подвижной обойме полиспаста. Натя5кение полиспаста создается грузом. Скручивание арматуры производится на станках, позволяющих закручивать стержни на определенный угол при одновременной вытяжке.
Сплющивание (профилирование) производится прокатыванием гладких стержней арматуры между профилированными валками (см. рис. 162,6). Роль тянущих роликов здесь выполняют сами профилированные валки, за которыми устанавливается правйльное устройство, устраняющее местные изгибы. Отрезают стержни отрезными роликами.
Волочением арматуру упрочняют на волочильных . станках, позволяющих протягивать проволоку диаметром от 7 до 22 мм через постепенно суживающееся отверстие в волоке-фильере (см. рис. 162, в).
Станки для гнутья арматуры. Хомуты, крюки и другие изделия из арматурных стержней гнут на различных гибочных станках, рабочим органом которых является вращающийся диск (рис. 163, а) с укрепленными на нем изгибающим роликом и центральным пальцем. Арматурный стержень в исходном положении укладывают в промежутке между упорным и изгибающим роликами, расположенными с одной стороны, и центральным пальцем — с другой. При повороте диска изгибающий ролик изгибает стержень вокруг пальца и образует нужный профиль. Диск поворачивают вручную или механическим приводом.
Станки с ручным приводом предназначены для гнутья арматуры диаметром до 25 мм при небольших объемах работ. Приводные станки могут быть однодисковыми для гнутья арматуры диаметром до 40 мм и двухдисковыми (см. рис. 163,6). Меньший диск 6 двухдискового станка изгибает арматуру диаметром до 40 мм, больший 7 — до 90 мм. Привод станка осуществляется от электродвигателя мощностью 10 кВт. Вращение от двигателя через цилиндрический и червячный редукторы передается валу, на котором закреплен меньший диск. Больший диск закреплен на валу, который вращается зубчатой парой. Для уменьшения динамических нагрузок в кинематической цепи привода предусмотрены эластичные муфты. Диск для гнутья арматуры больших диаметров может выключаться автоматически конечным выключателем, на который воздействует кулачок рабочего вала.
Рис. 162. Схемы упрочнения арматурной стали
Рис. 163. Схемы станков для гнутья арматурыа — схема рабочего органа; б — кинематическая схема двухдискового станка
Рис. 164. Схемы машин для сварки арматурных стержней а — точечным методом; б — стыковым методом
Сварку арматуры производят при необходимости получения стержней большой длины или при изготовлении сеток и пространственных каркасов. В настоящее время для этой цели в основном применяют контактную электросварку (точечную и стыковую). Для увеличения площади контакта свариваемые поверхности предварительно обрабатывают (зачищают).
Одноточечная контактная сварочная машина (рис. 164, а) состоит из станины, механизма сжатия электродов, пружины механизма сжатия, регулируемой гайкой, собачки, которой включается и выключается ток, однополюсного механического контактора, нажимной педали, электродов, винта для закрепления электрододержателя, трансформатора с переключателем ступеней, нижнего неподвижного хобота и верхнего подвижного хобота. Концы вторичной обмотки трансформатора соединены с электродами нижнего и верхнего хоботов гибкими шинами. При нажатии на педаль электроды сближаются и зажимают детали, которые при прохождении через них тока расплавляются и свариваются. Машины точечной сварки обеспечивают сварку стержней диаметром до 30 мм. При сварке крупногабаритных каркасов и сеток, подача которых к стационарным машинам невозможна, применяют передвижные сварочные машины (сварочные клещи). Помимо передвижных машин, для точечной сварки существуют также подвесные машины, все оборудование которых для удобства работы находится в подвешенном состоянии.
Машина для стыковой сварки (см. рис. 164,6) работает по принципу разогрева свариваемых стержней до светло-красного каления и последующего сжатия (высаживания), в результате чего происходит окончательное сваривание. Машина состоит из зажимного устройства, подающе-осадочного устройства, сварочного трансформатора с первичной обмоткой, переключателя ступеней и автоматического прерывателя, сблокированного с рычагом подающе-осадочного устройства. Ток через плиты подается к электродам, прижимающимся к свариваемым стержням прижимными устройствами. Свариваемые стержни закрепляются в губках зажимных устройств, к которым подведены полюса вторичной обмотки трансформатора через гибкие шины.
Сварку осуществляют сближением стержней при помощи подающе-осадочного устройства, привод которого может быть ручным, пневмогидравлическим и моторным. Зажим стержней в губках зажимных устройств может осуществляться ручным и пневмогидравлическим приводами. Для соединения стержней, работающих на растяжение, можно использовать сварку трением. Стержни с чисто обработанными торцами быстро вращаются навстречу друг другу, при сближении которых в результате трения выделяется большое количество тепла, нагревающее их до светло-красного каления. Сварку стержней заканчивают нажатием их друг на друга с большим усилием.
Читать далее: Вибраторы
Категория: - Путевые и дорожные машины
Главная → Справочник → Статьи → Форум
stroy-technics.ru
Оборудование для изготовления напрягаемой арматуры
Строительные машины и оборудование, справочник
Категория:
Машины в производстве стройматериалов
Оборудование для изготовления напрягаемой арматурыНапряженно-армированные железобетонные изделия изготовляют методом предварительного напряжения бетона путем натяжения арматуры до его укладки и формования или методом последующего напряжения бетона путем натяжения арматуры с передачей усилия натяжения на затвердевший бетон. Предварительное напряжение конструкций осуществляют следующими способами: механическим (натяжением), электротермическим (натяжением при нагреве и последующем охлаждении), электромеханическим (сочетание механического и электротермического), физико-химическим (применение специального цемента, расширяющегося при твердении) и гидравлическим (гидравлическое расширение гибкого сердечника). При использовании механического, электротермического и электротермоме-ханического способов натяжения арматуру с помощью анкерных устройств закрепляют в упорах форм или стенда.
Рис. 2.30. Основные типы анкеров и упоров дли креплении арматуры в формах:а — коротыш; б — головка; в — спрессованная шайба; г — упор с пазом; д — петля; е — штыревой упор
Для анкеровки натягиваемой арматуры применяют съемные цанговые или клиновые зажимы, а также постоянные анкеры: обжимные (шайбы, спирали), приварные (шайбы, петли, коротыши, резьбовые хвостовики) и высаженные на стержнях анкерные головки (рис. 2.30).
Широкое применение получил полуавтоматический съемный анкерный зажим конструкции НИИЖБа (рис. 2.31), предназначенный для образования концевых анкеров и закрепления проволочной и прядевой арматуры в упорах.
Зажим состоит из корпуса, трех зажимных губок, толкателя и хвостовика. Закрепление зажима с проволокой или прядью обеспечивается путем заклинивания их внутри конической втулки-корпуса с помощью конических губок. При натяжении проволоки корпус зажима упирается в опорную поверхность упоров стенда или формы. После затвердения бетонной смеси через толкатель хвостовиком отводят зажимные губки, и зажим свободно снимается с концов проволоки.
Рис. 2.31. Полуавтоматический анкерный зажим НИИЖБ:а — в сборе; б — детали зажима
Для равномерного снятия натяжения и передачи его с упоров форм на бетон применяют механические устройства для отпуска арматуры. По условиям обеспечения безопасной работы в случаях обрыва анкера со стороны одного из упоров приваривают защитные ограждения.
Технологический процесс напряженного армирования железобетонных конструкций включает заготовку мерной арматуры, устройство анкеров, натяжение арматуры, отпуск натяжения и обрезку выпусков (рис. 2.32).
Оборудование для заготовки и натяжения арматуры
Линия СМЖ-213А (рис. 2.33) предназначена для заготовки мерных стержней проволочной и прядевой арматуры длиной 6, 12, 18 и 24 м из высокопрочной арматурной проволоки диаметром 5 … 6 мм и прядей диаметром 7,5; 12 и 15 мм, собираемых в пакеты и используемых для предварительного натяжения железобетонных изделий. Линия состоит из бухтодержателя, направляющих роликов, механизма подачи, механизма резки проволоки и пряди, приемного стола.
Рис. 2.32. Схема технологического процесса напряженного армирования железобетонных конструкций
Механизм резки проволоки имеет корпус с обоймой, в котором смонтированы неподвижная разрезная втулка-нож и поворотный с приводом от пневмоцилиндра стакан с подвижной втулкой-ножом. Режущая кромка подвижной втулки смещается относительно неподвижной втулки за счет эксцентриситета стакана.
Механизм резки прядей состоит из кронштейна со шпинделем и дисковой пилой. Зажатая в тисках с помощью пневмопривода прядь разрезается дисковой пилой, приводимой от электродвигателя и прижимаемой пневмоци-линдром. Автоматически подаваемая из бухтодержателя проволока или прядь проходит по каналу приемного стола до упора, нажимающего на конечный выключатель, после чего подача прекращается, арматура зажимается, включается нож, производятся резка, открытие приемного стола, сброс мерной арматуры и закрытие стола.
Установка СМЖ-524 (рис. 2.34) предназначена для заготовки напрягаемой стержневой арматуры в виде плетей с высаженными анкерными головками на концах и для заготовки ненапряга-емой арматуры.
Установка состоит из питателя, заднего механизма подачи с поджимом, сварочной стыковой машины, подъемных роликов, механизма подачи с захватом, станка для резки арматурной стали, приемного роликового конвейера, упора, приемных секций и шкафа-пульта.
На раме питателя расположены лоток для приема стержней, вал для отбора стержня из пакета и ролик со склизами и упорами для приема стержня и подачи его на сварку. На сварной раме механизма подачи смонтированы двигатель, тормоз, клиноременная передача, червячный редуктор и механизм поджима стержня. На конце тихоходного вала редуктора размещено подающее колесо. По обе стороны его на раме установлены поддерживающие ролики.
Станок (СМЖ-133А) для резки арматурной стали имеет автономные привод и систему управления.
На сварочной машине (МС-200В) установлены сдвоенные пневмоци-линдры, обеспечивающие усилие осадки 60 кН при давлении 0,5 МПа. Для управления работой пневмоци-линдрами в процессе высадки на раме машины установлены краны, кнопки и пневмоаппаратура. Машина снабжена съемным пуансоном для высадки анкера.
В зависимости от длины заготовляемых плетей роликовый конвейер 3 комплектуют секциями, соединенными между собой и с рамой приемного конвейера. На раме и на секциях устанавливают уноры с конечным выключателем.
Для сбрасывания стержня внутри рамы смонтирован рычажный механизм.
Установка работает следующим образом. При заготовке напрягаемой арматуры стержни из питателя 9 подаются на сварочную машину 6 при помощи механизма подачи 8. На передний конец первого стержня надевается специальная упорная шайба и производится горячая высадка анкерной головки. Затем первый стержень при помощи механизма подачи подается вперед таким образом, чтобы анкерная головка с шайбой оказались за роликами заднего механизма 4 подачи, а конец этого стержня находился в зажимных губках сварочной машины. Далее подается следующий стержень и производится стыковая сварка стержней.
11ри продвижениисвареннойстержне-вой плети или первого стержня с шайбой периодически с пульта включают подъемные ролики.
Когда пердний анкер достигает упора с конечным выключателем, подача плети прекращается. Расстояние между упором и плоскостью реза определяет мерную длину заготовки. Производится резка. Далее упор отводится в сторону, а сварная плеть продвигается механизмом подачи так, что ее задний конец попадает в губки сварочной машины. Перед высадкой заднего анкера, а стержень надевают вторую упорную шайбу.
Машина СМЖ-525 (рис. 2.35) предназначена для механического упрочнения стержневой арматуры из стали класса A-IIIB путем вытяжки. Упрочненную стержневую арматуру используют в качестве напрягаемых элементов при изготовлении предварительно напряженных железобетонных конструкций.
Стержни вытягиваются гидродомкратом СМЖ-84А. Силовую раму собирают из отдельных секций в зависимости от исполнения по длине. Всего имеется семь исполнений для стержней длиной 6000 … 24 ООО мм.
В каждой секции установлены рычаги, соединенные тягой. На рычагах имеются фасонные конические ролики для загрузки стержней с наклонного стеллажа внутрь силовой рамы. Тяга перемещается двумя пнев-моцилиндрами, установленными в начальной и концевой секциях рамы.
Концевая секция заканчивается анкерной плитой, в которой на тяге монтируется захват для анкерной головки стержня. Анкерная плита оборудована предохранительной скобой.
Машина комплектуется промежуточной анкерной плитой, устанавливаемой на раме для упрочнения стержней меньшей длины.
На переднем конце начальной секции размещена анкерная плита с силовым гидроцилиндром домкрата, шток которого проходит через отверстие в плите. На конце штока смонтирован подвижный захват, усилие которого определяется с помощью манометра, а удлинение — с помощью линейки и указателя на захвате.
Машина работает следующим образом. Заготовленные стержни подаются на наклонный стеллаж силовой рамы до упоров. В ряде случаев такая подача осуществляется с установки СМЖ-524, которую размещают рядом с машиной СМЖ-525. Затем включают механизм укладки стержней. При подъеме фасонных роликов очередной упрочненный стержень сбрасывается в бункер, а передний стержень на наклонном стеллаже приподнимается над упорами. При опускании рычагов с фасонными роликами стержень укладывается по оси натяжения. При этом анкерные стержни должны попасть в подвижпыи и неподвижный захваты. После включения насосной станции осуществляется натяжение стержня.
Рис. 2.35. Машина СМЖ-525 длн упрочнения стержней
Рис. 2.36. Установка СМЖ-129Б
В начале натяжения выбираются все зазоры, и при давлении 1,0 МПа гидроцилиндр отключается и начинается отсчет удлинения. После достижения необходимого удлинения производится выдержка в течение не менее 2 мин, обеспечиваемая соответствующей регулировкой реле давления на насосной станции.
После выдержки производится отпуск натяжения.
Установка СМЖ-129Б (рис. 2.36) предназначена для удлинения методом электронагрева горячекатаной арматуры периодического профиля, используемой при производстве предварительно напряженных железобетонных изделий. Установка состоит из подвижного и неподвижного контактов, рамы, поддерживающей опоры и электрооборудования.
Сжатый воздух подается через пне-вмораспределитель в передние полости пневмоцилиндров зажима и подтяжки. Зажимные рычаги занимают крайнее верхнее положение, а подвижный контакт — исходное положение для подтяжки. В контактные губки укладываются два арматурных стержня, подлежащих удлинению. При подаче воздуха в нижние полости пневмоцилиндров производится зажим стержней с последующей их подтяжкой.
После соответствующей выдержки подается ток. Нагреваясь при прохождении электрического тока, стержни удлиняются и перемещают подвижный контакт 6. Наличие подтяжки обеспечивает точную фиксацию исходного положения подвижного контакта и исключает искривление арматуры на участке между контактами, что позволяет стабилизировать расчетное удлинение арматуры.
Необходимое удлинение стержня регулируется нажимным винтом. При достижении требуемого удлинения винт нажимает на штифт микропереключателя 7. При этом нагрев прекращается, нажимные рычаги поднимаются, и подвижный контакт перемещается в исходное положение. Нагретые стержни снимаются за концы и укладываются в упоры поддона. На этом цикл работы установки заканчивается.
Рис. 2.37. Машина СМЖ-128Б для высадки анкеров
Машина СМЖ-128Б (рис. 2.37) предназначена для высадки анкерных головок на стержнях из стали классов A-IIIB, A-1V, A-V, A-VI и термически упрочненных сталей классов Ат-V и At-VI с предварительным нагревом осаживаемых концов арматурных стержней.
Машина состоит из рамы, неподвижного и подвижного высадочно-зажимных устройств и загрузочно-выгрузочного устройства с пневмо-цилиндром. На высадочных устройствах установлены подвижная и неподвижная траверсы. Зажимают стержни пневмоцилиндром. На подвижной траверсе установлен высадочный пуансон, перемещаемый пневмоцилиндром.
Машина работает следующим образом. Из загрузочного устройства арматурный стержень укладывается в зажимные губки и зажимается в них, к торцам стержня подводятся высадочные пуансоны, включается трансформатор и концы стержня нагреваются. По достижении необходимой температуры срабатывает фотоэлектронный пирометр, выключая трансформатор и включая подачу воздуха в гшевмоцилиндры для высадки головок. По окончании высадки пуансоны автоматически отводятся, губки разжимаются и стержень с высаженными на концах анкерными головками сбрасывается.
Автомат СМЖ-484 (рис. 2.38) предназначен для мерной резки стержневой арматуры, высадки анкерных головок на концах стержней, электронагрева и укладки нагретых стержней в упоры поддона при использовании электротермического способа натяжения арматуры. Автомат применяют при изготовлении предварительно напряженных железобетонных изделий.
Автомат состоит из блока резки и высадки, блока высадки и подтяжки, питателя, передаточной платформы и упора.
Работа на автомате производится в следующем порядке. После выдачи с конвейера поддона на передаточную платформу из пакета отбирается очередной стержень, включается привод передвижения, и платформа на большой скорости перемещается к первой позиции укладки стержня. При подходе к первой позиции скорость платформы снижается, привод передвижения платформы выключается и срабатывают фиксаторы.
Включается рабочий ход механизма захвата, при этом передний конец стержня должен попасть в вилки захвата за отсекателем. При нахождении захвата с концом стержня в исходном
положении срабатывает механизм отбора стержней, и стержень отделяется от пакета. Когда оба конца отобранного стержня находятся на одной оси, а механизм отбора оказывается в конце рабочего хода, включается механизм сброса стержня. При движении на сброс одновременно с подачей всего стержня механизм одним из своих рычагов отводит через систему рычагов вал-отсекатель вилок захвата,и передний конец стержня свободно выходит из вилок захвата. Отобранный стержень поступает на позицию резки. Рычаги механизма сбрасывания стержня возвращаются в исходное положение.
Положение стержня на позиции резки контролируется конечными выключателями. В конце хода подачи включается гидрораспределитель цилиндра резки стержня. Одновременно производятся поперечный зажим концов стержня и подвод пуансонов, включаются трансформаторы, производится импульсный нагрев. Температура нагрева под высадку контролируется фотодатчиками, включающими пуансоны высадки анкерных головок. В конце процесса высадки отключаются трансформатор нагрева и прекращается подача воздуха под высоким давлением в пневмоцилиндры приводов пуансонов.
Включается трансформатор нагрева стержня. Стержень нагревается и удлиняется при сильном воздействии пневмоцилиндра подтяжки. При достижении заданного удлинения нагрев стержня прекращается, губки разжимаются и пуансон отводится от левого конца стержня, доступ воздуха в рабочую полость пневмоцилиндра подтяжки прекращается. Левый конец стержня укладывается в упор поддона.
При нахождении в нижнем положении левого механизма укладки снова подается воздух в рабочую полость пневмоцилиндра подтяжки для перемещения до упора анкерной головки левого конца стержня в упор поддона. Затем губки разжимаются и пуансон отводится от правого конца стержня, доступ воздуха в рабочую полость пневмоцилиндра подтяжки снова прекращается. Правый конец стержня укладывается в упор поддона. Механизм
укладки концов стержня, фиксаторы поддона и механизм подтяжки возвращается в исходное положение. Па этом цикл натяжения одного стержня заканчивается.
После укладки и натяжения последнего стержня платформа с поддоном на высокой скорости возвращается на конвейерную линию формования.
Для натяжения арматуры получили применение одно- и двухпроволочные, многопроволочные и стержневые; одностороннего и двойного действия, работающие с перехватом арматуры; передвижные, подвесные, переносные; универсальные и специальные гидравлические домкраты (рис. 2.39).
Гидродомкрат СМЖ-81 (рис. 2.39, б) двойного действия предназначен для одновременного натяжения пуков проволоки, закрепляемых после натяжения путем запрессовки клиновой пробки. Гидродомкрат имеет два цилиндра — для натяжения и запрессовки проволок.
По этому же принципу работают унифицированные гидродомкраты, предназначенные для изготовления железобетонных конструкций для мостостроения (типа МДГ-70У, МДГ-150У, МДГ-240У и МДГ-400), имеющие усилие натяжения прядей соответственно 700, 1500, 2400 и 4000 кН).
Гидродомкрат СМЖ-84А предназначен для натяжения пучков проволоки. Он имеет основной гидроцилиндр, внутри которого помещен второй, выполняющий роль поршня. На основном цилиндре размещена обойма с клиновыми пазами, в которых с помощью клиньев попарно закреплены натягиваемые проволоки. Для закрепления натянутой проволоки служит гидроцилиндр, помещенный внутри передней упорной части домкрата. После закрепления в обойме домкрата пучок проволок натягивается и фиксируется путем заклинивания клиновой пробки в анкерном кольце; тянущий цилиндр и поршень запрессовки возвращаются в исходное положение.
Гидродомкрат СМЖ-82А (рис. 2.39, в) предназначен для натяжения стержневой арматуры. Он состоит из цилиндра, поршня со штоком, захвата со сменными гайками и упора. Цилиндр с одной стороны имеет крышку со штуцером, а с другой—две стойки с упорной плитой. На конце штока, имеющем головку, помещен захват для арматуры со сменной гайкой. Гайка навинчивается на резьбовой конец арматуры. После подачи масла в цилиндр со стороны штока происходит натяжение арматуры. Усилие натяження контролируется по манометру. В натянутом положении стержневая арматура фиксируется навинчиваемой на нее анкерной гайкой. Далее направление масла изменяется, гайка захвата отвинчивается и шток возвращается в исходное положение.
Самоходная арматурно-намоточная машина типа 3269/1 (рис. 2.40) предназначена для непрерывного армирования плоских железобетонных конструкций. Машина выполнена в виде самоходного портала, перемещающегося с помощью привода 6 по рельсовому пути с колеей 4,5 м вдоль ряда стационарно установленных форм. На портале смонтированы бухтодержатель, механизм натяжения, поперечно перемещаемая от привода каретка с пинолью. Механизм натяжения снабжен грузовой клетью, а также системой электронагрева.
Закрепленная на штыре формы арматурная проволока с помощью пиноли, перемещающейся в вертикальном направлении, а также в продольном с порталом и поперечном с кареткой, наматывается с заданным усилием в продольном, поперечном, диагональном направлениях, создавая арматурный каркас требуемой формы. При этом усилие натяжения арматуры создается как механическим путем с помощью грузовой клети, так и электротермическим при электронагреве участка арматуры.
Рис. 2.39. Конструктивные схемы гидравлических домкратов для натяжения арматуры:а — однопроволочного; б — двойного действия СМЖ-81; в — стержневого СМЖ-82; г — стержневого с перехватом СМЖ-84; 1 — цилиндр; 2 — поршень со штоком; 3,5 — Цанговые зажимы; 6 — упор; 7 — штуцер; 8 — поршень заклинивания; 9 — анкерная шайба; 10 — анкерная пробка; 11 — кольцо крепления; 12 — захватное устройство; 13 — гайка; 14 — стержневая арматура; 15 — анкерная гайка; 16, 17 — клиновые зажимы
Арматурно-навивочная машина СМЖ-360А (рис. 2.41) предназначена для навивки напряженной арматуры на затвердевшие бетонные сердечники квадратного сечения, которые представляют собой объемные элементы сборных элеваторов.
Машина состоит из бухтодержателей, направляющего устройства, механизма подачи, механизма натяжения каретки с пантографом, механизма 6 навивки и электрооборудования. Бухтодержатель имеет раздвижные упоры и два исполнения для возможности установки бухты проволоки или бухты пряди.
Механизм подачи представляет собой электропривод с коническим диском, на который в начале работы машины наматываются несколько витков проволоки. Чтобы проволока не перехлестывалась, снизу к поверхности диска поджимается ролик. Предварительная подтяжка свободного конца проволоки создается механизмом торможения, состоящим из пяти последовательно расположенных роликов.
Механизм натяжения имеет грузовую клеть, подвешенную на натягиваемой проволоке. Натягивание создается под действием силы тяжести клети и регулируется съемными грузами.
Проволока нагревается от сварочного трансформатора. Ток пропускается через проволоку на участке от механизма подачи до пантографа. Все детали на этом участке, соприкасающиеся с проволокой, изолированы диэлектрическими прокладками и втулками. Степень нагрева регулируется реостатом с пульта управления. Для мягкой посадки грузовой клети внизу установлены четыре амортизационные пружины.
На раме на пути перемещения клети размещены конечные выключатели, верхний и нижний из которых являются аварийными. Второй выключатель сверху включает подачу проволоки, второй выключатель сверху включает подачу проволоки, второй выключатель снизу отключает подачу проволоки. Со стороны выхода проволоки к раме прикреплен пантограф, состоящий из подвижной каретки, направляющей балки, ходового винта и редуктора. Подвижная каретка, перемещаясь по направляющей балке сверху вниз, укладывает проволоку по высоте. Каретка состоит из двух щек, на которых прикреплены четыре пары направляющих роликов, фиксирующих каретку на направляющей балке. Сбоку между щеками установлен поворотный выдающий блок.
Для временного опускания проволоки при наложении косого витка установлен отжимной ролик, закрепленный в поворотной рамке. Ролик приводится в движение пневмоцилинд-ром. Ходовой винт имеет две рабочие скорости — одну при навивке проволоки одного пучка, вторую — при переходе от одного пучка к другому. Кроме того, винт имеет одну вспомогательную скорость для возврата каретки в исходное положение после окончания навивки очередного сердечника.
Ходовой винт приводится от поворотной платформы через редуктор, имеющий два входных вала, одновременно, вращающихся с разными скоростями. Ходовой винт к одному из входных валов подключается с помощью кулачковых муфт с электромагнитным приводом. В зависимости от того, к какому валу присоединен ходовой винт, может быть выполнена быстрая или медленная подача подвижной каретки. Редуктор, кроме того, имеет и третий привод от электродвигателя 23, который возвращает каретку в исходное положение. На направляющей балке пантографа установлены два конечных выключателя, ограничивающие ход подвижной каретки.
Механизм навивки состоит из сварной круглой рамы с механизмами поворотной платформы и роликового круга. В середине рамы на подшипниках установлен вращающийся центр, на который насажена шестерня. На этом же центре фиксируется поворотная платформа. Шестерня вращается от электродвигателя постоянного тока через специальный горизонтальный редуктор и вертикальный вал-шестерню. В редукторе имеется второй выходной вал для установки тормоза. Для передачи движения на пантограф предусмотрен отбор вращения от центра (меньшая скорость) и от вала-шестерни (большая скорость) посредством конических редукторов.
Шаг навивки изменяется с помощью гитары со сменными шестернями, вращение которых передается карданными валами, соединяющими сменные шестерни с коническими редукторами. Сверху на основной раме приварено опорное кольцо, на котором смонтирован роликовый круг для опоры поворотной платформы.
Рис. 2.40. Самоходная арматурно-намоточная машина типа 3269/1
Для фиксации сердечника на поворотной платформе имеются четыре упорных угольника. Сердечник не крепится к платформе, так как достаточно его собственной массы, чтобы удержать его от опрокидывания при навивке арматуры.
Арматурная проволока навивается по высоте отдельными пучками. Число пучков во всех случаях равно. Количество проволок в пучке составляет 2 … 10 в зависимости от положения пучка по высоте и диаметра навиваемой арматуры. Навивается арматура сверху вниз, переходит от одного пучка к другому косой ниткой по одной стороне квадрата. Начало проволоки закрепляется петлей, сделанной на ее конце, которая накидывается на штырь сердечника, конец обмотки закрепляется прижимными планками. Закрепление и обрезка проволоки производятся вручную.
Читать далее: Оборудование формовочных цехов
Категория: - Машины в производстве стройматериалов
Главная → Справочник → Статьи → Форум
stroy-technics.ru
Станки для резки арматуры: ручные, мобильные, стационарные
Содержание статьи:
Во время проведения строительных работ или мероприятий по сборке металлоконструкций возникает необходимость формирования арматур определенной длины. Для выполнения этой работы следует использовать специальное оборудование – станок для резки арматуры.
Принцип работы станов для резки арматуры
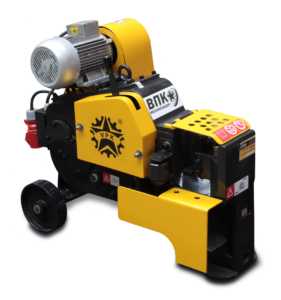
Мини-станок для резки арматуры
По сути механизм представляет собой мини-пресс, у которого вместо ровной рабочей площадки есть режущее лезвие. С помощью системы гидравлики, рычажных механизмов или электроприводов, быстро создается давление, которое передается лезвию. В результате этого происходит резание арматуры.
Для работы станка в его конструкции должна быть рабочая площадка, на которую устанавливается арматура. Обычно она имеет выемку полукруглой формы, которая облегчает фиксацию заготовки. Для обработки прутьев различных диаметров опорная площадка может быть съемной. Данный механизм позволит оперативно выполнить обработку арматуры другого диаметра.
С помощью режущего лезвия происходит процесс контролируемой деформации. В зависимости от конструктивных особенностей в качестве привода могут применяться различные механизмы. Это зависит от условий эксплуатации оборудования максимального диаметра обрабатываемого изделия:
- ручные модели. Эти станки для резки арматуры предназначены для обработки небольших по диаметру изделий. С их помощью можно выполнять рез непосредственно на металлоконструкции;
- приводные станки. Относятся к классу стационарных. В отличие от вышеописанных моделей способны за одну операцию обрезать несколько арматур. Предназначены для массовой обработки в условиях производства.
Дополнительно следует учитывать возможность функционирования без подключения к внешним источникам питания – электросети или гидравлической установки для создания давления в рабочем цилиндре. Это актуально при работе «в поле», где доступ к этим источникам ограничен.
Для привода режущей части могут использоваться гидравлические системы или кулачковые вращательные механизмы. В последнем случае габариты станка повышаются, но и при этом растет производительность.
Классификация оборудования
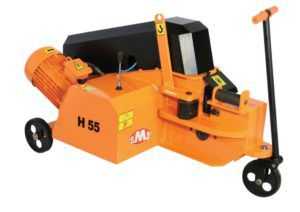
Мобильный станок для резки арматуры
В настоящее время изготавливаются различные станки для резки арматуры, которые отличаются не только техническими параметрами, но и компоновкой. Для выбора оптимальной по характеристикам модели следует изучить их классификацию и отличительные особенности.
Главным параметром является производительность устройства. Этот показатель максимален у станков с электроприводом и зависит от скорости вращения рабочего маховика. Гидравлические отличаются высокими показателями давления. С их помощью можно выполнять рез прутьев большого диаметра.
Помимо этих показателей необходимо учитывать такие конструктивные особенности оборудования:
- стационарные или мобильные модели. Первые применяются для массовой обработки арматуры. Мобильные установки целесообразно приобретать для работы на стройке или аналогичных ей объектах;
- конструкция режущих лезвий. Они не должны деформировать стальной пруток, но при этом обеспечивать должный показатель производительности.
Для производственных линий станок для резки арматуры дополнительно комплектуется системой подачи материала. Это позволяет максимально автоматизировать процесс обработки, повысить его точность. Однако это сказывается на габаритах установки — они значительно увеличиваются.
Система подачи помимо основной функции обеспечивает разматывание материала. Для этого в ней предусмотрена система направляющих роликов и фиксаторов. Это позволяет выполнять обработку рулонных заготовок.
Перечень технических характеристик
Производственная линия по резке арматуры
Эксплуатационные параметры являются основными критериями выбора подходящей модели. Учитывается произвольность оборудования, его потребляемая мощность и ограничения на диаметр обрабатываемой арматуры. Для полноценного анализа лучше всего сравнить эти характеристики у различных моделей.
Прежде всего обращают внимание на мощность силовой установки. Этот показатель влияет на величину создаваемого давления в рабочем режущем блоке. У моделей с гидравлическим приводом это максимальный показатель давления рабочей жидкости в поршне. Для станков с электроприводом важно знать выходную мощность силовой установки.
Перечень основных критериев выбора станка для резки арматуры:
- тип установки – стационарная или мобильная;
- рабочая ширина лезвий;
- максимальный и минимальный диаметр обрабатываемой арматуры;
- максимальный показатель усилия на рабочее лезвие;
- частота выполнения одного реза;
- наличие системы автоматической протяжки арматуры;
- габариты и масса станка;
При высокой частоте поднимания/опускания лезвия возникает проблема нагрева заготовки. Это может привести к ее деформации или созданию избыточного поверхностного натяжения. Для уменьшения вероятности проявления этих негативных факторов в конструкции станка должна быть предусмотрена система подачи охлаждающей жидкости.
Во время эксплуатации станка необходимо выполнять следующие условия:
- настройка лезвия. Проверяется величина его вылета, а также расположение. Лезвие должно находиться строго перпендикулярно заготовке;
- частота выполнения операции резания. Она зависит от модели станка и длины арматуры;
- наличие защиты от влаги. Если такая не предусмотрена в конструкции, сделать или купить защитный кожух.
После определенного цикла работ проверяется состояние режущего инструмента. В случае надобности выполняется его заточка.
С примером эксплуатации подобного оборудования можно ознакомиться в видеоматериале:
stanokgid.ru
Станок для гибки арматуры с ЧПУ и станок для протяжки (выпрямления) арматуры из бухт для полного цикла армирования :: SYL.ru
Современные станки для работы с арматурой для производственных предприятий
Железобетонные изделия являются основным материалом при строительстве жилых и промышленных зданий. Кроме них широкое распространение получила технология монолитного строительства. Бетон – пластичный материал и довольно хрупкий, поэтому для него необходим каркас из арматуры. Благодаря ему срок эксплуатации конструкции увеличивается многократно. Пространственные каркасы позволяют придавать бетону сложную форму, но для этого необходимо большое количество мелких деталей, соединяющих арматурные прутья в особую конструкцию.
Наиболее сложные объемные каркасы заказываются на заводах металлоконструкций. Специалистам этих предприятий сегодня необходимо быть готовыми к решению самых сложных проблем. По этой причине заводы комплектуются современным оборудованием для работы с арматурой. Приобрести их можно в компании «РусИнСтрой», предлагающей широкий выбор продукции ведущих производителей по доступным ценам.
Станок для гибки арматуры с ЧПУ: эффективно и выгодно
Нарезать заготовки определенной длины из стальных прутьев не сложно, но вот придать им определенную форму и сделать это идеально точно для тысяч деталей – проблематично. Справиться с задачей на очень высоком уровне поможет станок для гибки арматуры с ЧПУ, отвечающий самым строгим современным требованиям. В числе его преимуществ – способность производить серийные детали с высокой степенью идентичности. Это существенно облегчит сборку объемного каркаса, так как все его элементы будут иметь строго выверенные пропорции.
Управление станком с ЧПУ не отличается сложностью, его легко можно перепрограммировать на производство новой детали благодаря простому и понятному интерфейсу. Если есть необходимость изменить оснастку станка – то на это уйдет не более 10-15 минут. Использовать станки с ЧПУ выгодно – они позволяют выполнять сложные заказы, привлекательные с финансовой точки зрения.
Станок для протяжки арматуры: для заводов и строительных площадок
Арматура поставляется не только мерными прутьями большой длины: продукция небольшого диаметра выпускается бухтами. Работать с такой арматурной проволокой приходится и на заводах металлоконструкций и на строительных площадках, где реализуются масштабные проекты. Разматывать бухту вручную не эффективно, для этого существует станок для протяжки арматуры, позволяющий не только распрямить арматуру, но и вытянуть ее ровным прутом, который легко и просто обрабатывать.
К преимуществам станка относится небольшой вес, высокая производительность, доступная цена. Работать такое оборудование может в любых условиях, в том числе на открытой площадке зимой. Управляется одним человеком, которому не обязательно иметь высокую квалификацию. В ассортименте компании «РусИнСтрой» широкий выбор станков для протяжки арматуры, приобрести которые можно на выгодных условиях. Поставка оборудования осуществляется по всем регионам России точно в соответствие с договорными условиями.
www.syl.ru