Методы защиты от коррозии металлов и сплавов (стр. 1 из 12). Современные способы защиты от коррозии металлов
Методы защиты от коррозии | Инструмент, проверенный временем
Современные методы предохранения от коррозии металлов и сплавов весьма разнообразны, так как причин, вызывающих ее, также очень много. Существующие методы можно разделить на следующие: легирование; применение многослойных материалов; неметаллические покрытия; протекторная защита; обработка коррозионной среды; рациональное конструирование и эксплуатация металлических сооружений и деталей.
Легирование металлов. Введение в сталь некоторых легирующих элементов повышает ее антикоррозионные свойства. Одни легирующие элементы образуют на поверхности стали устойчивые окисные пленки, которые защищают металл от коррозии; другие создают с железом твердые растворы — аустенитную структуру, обладающую высокой стойкостью и практически не корродирующую в данной среде.
Стали, содержащие 1296 Сг, с мартенситно-ферритной структурой практически не корродируют в атмосфере, в водных растворах солей, в органических кислотах и других слабоагрессивных средах при комнатной температуре.
Стали, содержащие 12—14% Сг, относятся к. мартенситно-ферритному и мартенситному классу. При более высоком содержании хрома (17- 28%) стали относятся к ферритному классу. Хромоникелевые стали (Х18Н9) имеют аустенитную структуру. Сталь Х18Н10Т, а также легированные стали аустенитного класса, содержащие хром, никель, титан, относятся к нержавеющим сталям и хорошо сопротивляются коррозии.
Двухслойные и многослойные металлы, состоящие из двух или нескольких различных металлов (сплавов), прочно соединенных между собой по всей плоскости соприкосновения, и представляющие монолитное целое. Машины и агрегаты, работающие в условиях повышенной коррозии, влажности, загрязненности атмосферы парами кислот, пылью и другими вредными веществами, особенно нуждаются в биметаллах, у которых основой являются малоуглеродистые или низколегированные стали/ а в качестве плакирующего слоя используются коррозионностойкие металлы. Наши металлургические заводы освоили многие виды проката листа, ленты, проволоки с защитными покрытиями — луженые, хромированные, оцинкованные и др. Организовано производство труб, покрытых цинком, алюминием, кремнием. Изготовление биметаллов сталь —- медь, сталь — латунь, сталь — бронза, сталь — никель и т. д. дает значительную экономию цветных металлов.
Неметаллические покрытия органического происхождения широко применяются в строительстве, машиностроении, на транспорте. К неметаллическим покрытиям относятся лакокрасочные эмали, фенолофор — мальдегидные смолы, неметаллические пленки и др.
Лакокрасочные покрытия, являясь самым распространенным методом защиты металлов от коррозии, изолируют металлические сооружения от контакта с агрессивной средой. Как известно, этот метод защиты обязателен для всех строительных металлических конструкций (мостов, ферм, колонн, магистральных трубопроводов, различных емкостей и т. д.) и некоторых машиностроительных конструкций.
Имеются лаки и краски, которые используют Для защиты металла и от электрохимической коррозии, ибо они увеличивают омическое сопротивление коррозийных пор, находящихся под слоем покрытия. Лакокрасочные покрытия, кроме химической стойкости, в условиях эксплуатации должны обладать достаточной механической прочностью, водонепроницаемостью, прилипаемостью (адгезией), не пропускать газ и защищать от подпочвенной коррозии.
Эмалированию подвергаются как черные, так и цветные металлы. Удачное сочетание химической стойкости и механической прочности позволило широко применять эмалирование в строительстве и промышленности.
Фенолоформальдегидные смолы-наиболее распространенные антикоррозионные материалы из числа пластмасс. На основе этих смол изготавливают следующие химически стойкие сложные композиционные материалы: фаолит, текстолит, текстофолит. Кроме того, применяют вяжущие лаки, арзалиты и некоторые специальные мастики.
Получение покрытий напылением другого металла с целью изоляции от агрессивной среды называют металлизацией. Така я защита сейчас широко применяется.
Различают два типа металлических покрытий — анодное и катодное. Для анодного покрытия используют металлы, обладающие более отрицательным электродным потенциалом, чем основной металл. В процессе коррозии анодные покрытия растворяются и предохраняют металл от разрушения. Эти покрытия не боятся царапин и других внешних нарушений слоя, так как при этом разрушаются преимущественно сами покрытия. Анодным покрытием для железных сплавов являются цинк, кадмий и др.
Для катодного покрытия выбирают металлы, имеющие меньшее отрицательное значение электродного потенциала, чем основной металл. Пока катодное покрытие полностью изолирует металл от контакта с агрессивной средой, он не подвергается коррозии. При нарушении сплошности катодного покрытия (царапины, механические повреждения и т. п.) его защитное действие прекращается, поскольку основной металл легче будет разрушаться от действия электролита. Катодными покрытиями служат медь, олово, свинец, никель и др. Всякое защитное металлическое покрытие должно быть сплошным. Металлические покрытия наносят горячим методом, гальваническим и способом металлизации. При металлизации на поверхность изделий наносят мельчайшие капли расплавленного металла при помощи пистолета.
Металлизаци я — один из методов предотвращения коррозии. Химические, механические и физические свойства покрытий, получаемых металлизацией путем напыления, часто резко отличаются от свойств металлов и сплавов, подвергаемых металлизации. Одним из наиболее важных факторов, определяющих практическую возможность применения металлизации, является прочность сцепления наносимого слоя с поверхностью основного металла. Это сцепление имеет чисто механический характер и основано на адгезии, т. е. вызвано избыточной энергией поверхностного слоя. Это определяет относительно невысокую прочность сцепления металлических покрытий с основной поверхностью. Металлизированный слой представляет хаотическое нагромождение отдельных распыленных металлических частиц размером от 1 до 4мкм. В последнее время производят плазменное напыление, сущность которого-заключается в расплавлении металла электрической дугой, последующим его подогреве быстродвижущейся высокотемпературной плазмой и осаждении на рабочую поверхность. Все эти процессы протекают в плазменной горелке.
Диффузионное покрытие осуществляют, насыщая поверхностные слои защищаемого металла атомами наносимого металла с диффузией последнего в глубину основного металла. Этот процесс протекает при высоких температурах.
К диффузионным процессам относятся алитирование (покрытие алюминием), хромирование (покрытие хромом), силицирование (покрытие кремнием) и т. д. Широко применяют покрытие оловом (лужение) и цинком (для кровельного железа, водопроводных труб и других изделий).
При гальваническом способе покрытия изделие из основного металла опускают в электролизеры (ванны), где под действием постоянного электрического тока на поверхности защищаемого металла осаждается никель, хром, цинк или другой металл. Защищаемый металл помещают в ваниу в качестве катода и подключают к отри — 7*
цатсльпому полюсу источника тока, а анодами служат пластины металла покрытия, которые присоединяют к положительному заряду источника тока. Металл анода растворяется, выделяясь затем на катоде.
Гальванические покрытия равномерно распределяются по поверхности защищаемого металла и обеспечивают неограниченную толщину покрытия; однако последние пористы и это существенный недостаток данного способа, ограничивающий его применение.
Защита протекторами — один из способов электрохимической защиты и в некоторых случаях полностью предохраняет металл от коррозии. При контакте двух различных металлов, погруженных в электролит, металл с более низким электродным потенциалом служит анодом и растворяется, защищая от коррозии тот металл, который является катодом. Этот метод — эффективный и экономически выгодный способ защиты от коррозии металлических конструкций в морской воде, почве и других, в том числе нейтральных, средах; здесь в качестве протектора применяют чистый цинк, реже алюминиево-цинковый сплав или сплавы на основе магния.
Катодная защита внешним током магистральных трубопроводов, котлов и других паросиловых установок заключается в том, что от источника постоянного тока через катод подводится ток к защищаемому металлическому изделию, а анодом служат дополнительные пластины, опущенные в электролит. В результате основное изделие становится катодом и перестает корродировать (рис. 61).
Обработка коррозионной среды производится с целью уменьшения ее агрессивного воздействия на металл или сплав. Некоторые вещества сильно замедляют скорость коррозии и служат замедлителями (ингибиторами) коррозии. Ингибиторы по характеру их действия можно разделить на анодные (т. е. тормозящие анодные процессы), катодные (тормозящие катодные процессы) и смешанные — тормозящие оба процесса. Кроме того, коррозионную активность среды можно уменьшить, удаляя из нее некоторые составляющие, вызывающие коррозию.
Наконец, при конструировании необходимо выбирать также формы изделий, при которых в пазах, углах, на стыках не задерживается агрессивная жидкость (рис. 61,6).
Кроме того, необходимо, чтобы сопрягающиеся детали и изделия изготовлялись из сплавов, близких по коррозионным характеристикам (нормальным электродным потенциалам).
Раздел третий
hssco.ru
Методы защиты от коррозии
Современная защита металлов от коррозии базируется на следующих методах:
- повышение химического сопротивления конструкционных материалов,
- изоляция поверхности металла от агрессивной среды,
- понижение агрессивности производственной среды,
- снижение коррозии наложением внешнего тока (электрохимическая защита).
Эти методы можно разделить на две группы. Первые два метода обычно реализуются до начала производственной эксплуатации металлоизделия (выбор конструкционных материалов и их сочетаний еще на стадии проектирования и изготовления изделия, нанесение на него защитных покрытий). Последние два метода, напротив, могут быть осуществлены только в ходе эксплуатации металлоизделия (пропускание тока для достижения защитного потенциала, введение в технологическую среду специальных добавок-ингибиторов) и не связаны с какой-либо предварительной обработкой до начала использования.При применении первых двух методов не могут быть изменены состав сталей и природа защитных покрытий данного металлоизделия при непрерывной его работе в условиях меняющейся агрессивности среды. Вторая группа методов позволяет при необходимости создавать новые режимы защиты, обеспечивающие наименьшую коррозию изделия при изменении условий их эксплуатации. Например, на разных участках трубопровода в зависимости от агрессивности почвы можно поддерживать различные плотности катодного тока или для разных сортов нефти, прокачиваемой через трубы данного состава, использовать разные ингибиторы.Однако в каждом случае приходится решать каким из средств, или в каком их сочетании можно получить наибольший экономический эффект.
Широко применяются следующие основные решения защиты металлических конструкций от коррозии:
1. Защитные покрытия
Металлические покрытия.
По принципу защитного действия различают анодные и катодные покрытия. Анодные покрытия имеют в водном растворе электролитов более отрицательный электрохимический потенциал, чем защищенный металл, а катодные – более положительный. Вследствие смещения потенциала анодные покрытия уменьшают или полностью устраняют коррозию основного металла в порах покрытия, т.е. оказывают электрохимическую защиту, в то время как катодные покрытия могут усиливать коррозию основного металла в порах, однако ими пользуются, т.к. они повышают физико-механические свойства металла, например износостойкость, твердость. Но при этом требуются значительно большие толщины покрытий, а в ряде случаев дополнительная защита.Металлические покрытия разделяются также по способу их получения (электролитическое осаждение, химическое осаждение, горячее и холодное нанесение, термодиффузионная обработка, металлизация напылением, плакирование).
Неметаллические покрытия
Данные покрытия получают нанесением на поверхность различных неметаллических материалов – лакокрасочных, каучуковых, пластмассовых, керамических и др.Наиболее широко используются лакокрасочные покрытия, которые можно разделить по назначению (атмосферостойкие, ограниченно атмосферостойкие, водостойкие, специальные, маслобензостойкие, химически стойкие, термостойкие, электроизоляционные, консервационные) и по со составу пленкообразователя (битумные, эпоксидные, кремнийорганические, полиуретановые, пентафталевые и др.)
Покрытия, получаемые химической и электрохимической обработкой поверхности Эти покрытия представляют собой пленки нерастворимых продуктов, образовавшихся в результате химического взаимодействия металлов с внешней средой. Поскольку многие из них пористы, они применяются преимущественно в качестве подслоев под смазки и лакокрасочные покрытия, увеличивая защитную способность покрытия на металле и обеспечивая надежное сцепление. Методы нанесения – оксидирование, фосфатирование, пассивирование, анодирование.
2. Обработка коррозионной среды с целью снижения коррозионной активности.
Примерами такой обработки могут служить: нейтрализация или обескислороживание коррозионных сред, а также применение различного рода ингибиторов коррозии, которые в небольших количествах вводятся в агрессивную среду и создают на поверхности металла адсорбционную пленку, тормозящую электродные процессы и изменяющую электрохимические параметры металлов.
3. Электрохимическая защита металлов.
Путем катодной или анодной поляризации от постороннего источника тока или присоединением к защищаемой конструкции протекторов, потенциал металла смещается до значений, при которых сильно замедляется или полностью прекращается коррозия.
4. Разработка и производство новых металлических конструкционных материалов повышенной коррозионной устойчивости путем устранения из металла или сплава примесей, ускоряющих коррозионный процесс (устранение железа из магниевых или алюминиевых сплавов, серы из железных сплавов и т.д.), или введения в сплав новых компонентов, сильно повышающих коррозионную устойчивость (например, хрома в железо, марганца в магниевые сплавы, никеля в железные сплавы, меди в никелевые сплавы и т.д.).
5. Переход в ряде конструкций от металлических к химически стойким материалам (пластические высокополимерные материалы, стекло, керамика и др.).
6. Рациональное конструирование и эксплуатация металлических сооружений и деталей (исключение неблагоприятных металлических контактов или их изоляция, устранение щелей и зазоров в конструкции, устранение зон застоя влаги, ударного действия струй и резких изменений скоростей потока в конструкции и др.).Вопросам проектирования антикоррозионной защиты строительных конструкций уделяют серьезное внимание как у нас в стране, так и за рубежом. Западные фирмы при выборе проектных решений тщательно изучают характер агрессивных воздействий, условия эксплуатации конструкций, моральный срок службы зданий, сооружений и оборудования. При этом широко используются рекомендации фирм, производящих материалы для антикоррозионной защиты и располагающих лабораториями для исследования и обработки защитных систем из выпускаемых ими материалов.Актуальность решения проблемы противокоррозионной защиты диктуется необходимостью сохранения природных ресурсов, защиты окружающей среды. Эта проблема находит широкое отражение в печати. Издаются научные труды, проспекты, каталоги, устраиваются международные выставки с целью обмена опытом между развитыми странами мира.Таким образом, необходимость исследования коррозионных процессов является одной из наиболее важных проблем.
www.domzzz.ru
Методы защиты от коррозии металлов и сплавов
Основным условием противокоррозийной защиты металлов и сплавов является уменьшение скорости коррозии. Уменьшить скорость коррозии можно, используя различные методы защиты металлических конструкций от коррозии. Основными из них являются:
1 Защитные покрытия.
2 Обработка коррозионной среды с целью снижения коррозионной активности (в особенности при постоянных объемах коррозионных сред).
3 Электрохимическая защита.
4 Разработка и производство новых конструкционных материалов повышенной коррозионной устойчивости.
5 Переход в ряде конструкций от металлических к химически стойким материалам (пластические высокомолекулярные материалы, стекло, керамика и др.).
6 Рациональное конструирование и эксплуатация металлических сооружений и деталей.
1. Защитные покрытия
Защитное покрытие должно быть сплошным, равномерно распределенным по всей поверхности, непроницаемым для окружающей среды, иметь высокую адгезию (прочность сцепления) к металлу, быть твердым и износостойким. Коэффициент теплового расширения должен быть близким к коэффициенту теплового расширения металла защищаемого изделия.
Классификация защитных покрытий представлена на рис. 43
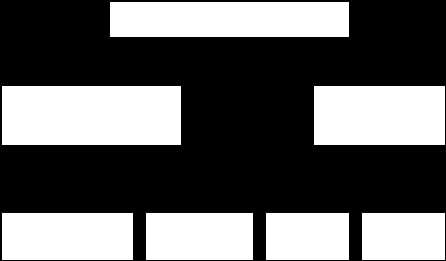
Защитные покрытия
Неметаллические Металлические покрытия покрытияНеорганическиеОрганическиеКатодныеАнодные
Рисунок 43 - Схема классификации защитных покрытий
1.1 Металлические покрытия
Нанесение защитных металлических покрытий – один из самых распространенных методов борьбы с коррозией. Эти покрытия не только защищают от коррозии, но и придают их поверхности ряд ценных физико-механических свойств: твердость, износоустойчивость, электропроводность, паяемость, отражательную способность, обеспечивают изделиям декоративную отделку и т.д.
По способу защитного действия металлические покрытия делят на катодные и анодные.
Катодные покрытия имеют более положительный, а анодные - более электроотрицательный электродные потенциалы по сравнению с потенциалом металла, на который они нанесены. Так, например, медь, никель, серебро, золото, осажденные на сталь, являются катодными покрытиями, а цинк и кадмий по отношению к этой же стали – анодными покрытиями.
Необходимо отметить, что вид покрытия зависит не только от природы металлов, но и от состава коррозионной среды. Олово по отношению к железу в растворах неорганических кислот и солей играет роль катодного покрытия, а в ряде органических кислот (пищевых консервах) служит анодом. В обычных условиях катодные покрытия защищают металл изделия механически, изолируя его от окружающей среды. Основное требование к катодным покрытиям – беспористость. В противном случае при погружении изделия в электролит или при конденсации на его поверхности тонкой пленки влаги обнаженные (в порах или трещинах) участки основного металла становятся анодами, а поверхность покрытия катодом. В местах несплошностей начнется коррозия основного металла, которая может распространяться под покрытие (рис. 44 а).
Рисунок 11 Схема коррозии железа с пористым катодным (а) и анодным (б) покрытием
Анодные покрытия защищают металл изделия не только механически, но главным образом электрохимически. В образовавшемся гальваническом элементе металл покрытия становится анодом и подвергается коррозии, а обнаженные (в порах) участки основного металла выполняют роль катодов и не разрушаются, пока сохраняется электрический контакт покрытия с защищаемым металлом и через систему проходит достаточный ток (рис.4 б). Поэтому степень пористости анодных покрытий в отличие от катодных не играет существенной роли.
В отдельных случаях электрохимическая защита может иметь место при нанесении катодных покрытий. Это происходит, если металл покрытия по отношению к изделию является эффективным катодом, а основной металл склонен к пассивации. Возникающая анодная поляризация пассивирует незащищенные (в порах) участки основного металла и затрудняет их разрушение. Такой вид анодной электрохимической защиты проявляется для медных покрытий на сталях 12Х13 и 12Х18Н9Т в растворах серной кислоты.
Основной метод нанесения защитных металлических покрытий – гальванический. Применяют также термодиффузионный и механотермический методы, металлизацию распылением и погружением в расплав.Разберем каждый из методов более подробно.
1.2 Гальванические покрытия.
Гальванический метод осаждения защитных металлических покрытий получил очень широкое распространение в промышленности. По сравнению с другими способами нанесения металлопокрытий он имеет ряд серьезных преимуществ: высокую экономичность (защита металла от коррозии достигается весьма тонкими покрытиями), возможность получения покрытий одного и того же металла с различными механическими свойствами, легкую управляемость процесса (регулирование толщины и свойств металлических осадков путем изменения состава электролита и режима электролиза), возможность получения сплавов разнообразного состава без применения высоких температур, хорошее сцепление с основным металлом и др.
Недостаток гальванического метода – неравномерность толщины покрытия на изделиях сложного профиля.
Электрохимическое осаждение металлов проводят в гальванической ванне постоянного тока (рис 45). Покрываемое металлом изделие завешивают на катод. В качестве анодов используют пластины из осаждаемого металла (растворимые аноды) или из материала, нерастворимого в электролите (нерастворимые аноды).
Обязательный компонент электролита – ион металла, осаждающийся на катоде. В состав электролита могут также входить вещества, повышающие его электропроводность, регулирующие протекание анодного процесса, обеспечивающие постоянство рН, поверхностно-активные вещества, повышающие поляризацию катодного процесса, блескообразующие и выравнивающие добавки и др.
Рисунок 5 Гальваническая ванна для электроосаждения металлов:
1 – корпус; 2 – вентиляционный кожух; 3 – змеевик для обогрева; 4 – изоляторы; 5 – анодные штанги; 6 – катодные штанги; 7 – барботер для перемешивания сжатым воздухом
В зависимости от того, в каком виде ион разряжающегося металла находится в растворе, все электролиты делятся на комплексные и простые. Разряд комплексных ионов на катоде происходит при более высоком перенапряжении, чем разряд простых ионов. Поэтому осадки, полученные из комплексных электролитов, более мелкозернисты и равномерны по толщине. Однако у этих электролитов ниже выход металла по току и более низкие рабочие плотности тока, т.е. по производительности они уступают простым электролитам, в которых ион металла находится в виде простых гидратированных ионов.
Распределение тока по поверхности изделия в гальванической ванне никогда не бывает равномерным. Это приводит к разной скорости осаждения, а следовательно, и толщине покрытия на отдельных участках катода. Особенно сильный разброс по толщине наблюдается на изделиях сложного профиля, что отрицательно сказывается на защитных свойствах покрытия. Равномерность толщины осаждаемого покрытия улучшается с увеличением электропроводности электролита, ростом поляризации с ростом плотности тока, уменьшением выхода металла по току при повышении плотности тока, увеличении расстояния между катодом и анодом.
Способность гальванической ванны давать равномерные по толщине покрытия на рельефной поверхности называется рассеивающей способностью. Наибольшей рассеивающей способностью обладают комплексные электролиты.
Для защиты изделий от коррозии используют гальваническое осаждение многих металлов: цинка, кадмия, никеля, хрома, олова, свинца, золота, серебра и др. Применяют также электролитические сплавы, например Cu – Zn, Cu – Sn, Sn – Bi и многослойные покрытия.
Наиболее эффективно (электрохимически и механически) защищают черные металлы от коррозии анодные покрытия цинком и кадмием.
Цинковые покрытия применяются для защиты от коррозии деталей машин, трубопроводов, стальных листов. Цинк – дешевый и доступный металл. Он защищает основное изделие механическим и электрохимическим способами, так как при наличии пор или оголенных мест происходит разрушение цинка, а стальная основа не корродирует.
Покрытия из цинка занимают доминирующее положение. С помощью цинка защищают от коррозии примерно 20 % всех стальных деталей, и около 50% производимого в мире цинка расходуется на гальванические покрытия.
В последние годы получили развитие работы по созданию защитных гальванических покрытий из сплавов на основе цинка: Zn – Ni (8 – 12% Ni), Zn – Fe, Zn – Co (0,6 – 0,8% Co). При этом удается повысить коррозионную стойкость покрытия в 2-3 раза.
mirznanii.com
Современные способы защиты металлов от коррозий
Коррозия поверхностей металлов является вполне естественным природным процессом, от которого трудно уберечь металлические изделия, если не провести необходимую защитную обработку. Разнообразные металлы по разному реагируют на окисление под воздействием воздуха и других естественных факторов. Помимо этого, оказывает высокое влияние тип окружающей среды. То есть, на открытом воздухе, окисление и последующие разрушающие процессы на поверхности металлических изделий проходят крайне медленно и почти незаметно. Но в условиях высоких температур или повышенного давления, как это обычно бывает с металлическими канализационными или водопроводными трубами, темпы коррозии увеличиваются.
Сам термин «коррозия» является собирательным и описывает все негативные процессы, которые отражаются на состоянии металлов разных видов. Самое простое и известное всем проявление коррозии — ржавчина. Это процесс внешней коррозии, так как ржавчина появляется на поверхности металла. Чтобы уберечь металл от ржавчины, достаточно покрыть его защитным слоем. Например, эмаль ХВ-785, создана специально для защиты металлических, железобетонных и бетонных строительных конструкций от коррозии. Стоит отметить, что проблемой коррозии металлов люди озаботились еще очень давно, во времена, когда металл не играл столь важной роли в строительных процессах. Так, например, в Древней Греции применяли разнообразные масла, чтобы продлить эксплуатацию и улучшить свойства различных металлических конструкций.
В наши дни существуют куда более эффективные средства. Благодаря достижениям в химии и физике, мы может защищать любые строительные конструкции из металла в разы эффективные. И не только строительные. Так, например, эмаль ХС-510 предназначена, в первую очередь, для нанесения на поверхности надстроек и надводного борта судов. Все для той же защиты от коррозии металлов. Аналогично, для защиты металла в условиях морской воды, применяется и эмаль ХС-717. Использование эмали для защиты металлических конструкций относится к способу защиты, который называется — применение изоляционной пленки. Сюда же относится оксидирование и металлизация. Помимо этих типов защит существуют также и другие варианты. Например легирование металлов, то есть добавление в металлический сплав веществ, которые делают его более устойчивым к процессам окисления. Существует и электрохимическая защита с использованием электрического тока, пропускаемого через металл с целью уменьшения его химической активности. Иногда, чтобы защитить от коррозии металлические конструкции, воздействуют не на сам металл, а на среду, которая его окружает. Этот способ называется ингибированием и имеет смысл на производственных объектах.
Читайте еще, вам понравится
blitz-remont.ru
Коррозия металлов и защита от не
Коррозией ( от лат. «corroder – разъедать» ) называется самопроизвольное разрушение металлических материалов, происходящее под химическим воздействием окружающей среды. Общая масса металлических материалов, используемых в виде различных изделий в мировом хозяйстве, очень велика. Поэтому, несмотря на то, что обычно скорость коррозий мала, ежегодно из–за коррозии теряется безвозвратно огромное количество металла. По ориентировочным подсчетам безвозвратные потери металла от коррозии составляют 10 – 15 % мировой продукции стали. Но еще больший вред связан не с потерей металла, а с порчей изделий, вызываемой коррозией. Затраты на ремонт или на замену деталей судов, автомобилей, аппаратуры химических производств, трубопроводов, приборов, во много раз превышают стоимость металла, из которого они изготовлены. Наконец, существенными бывают косвенные потери, вызванные коррозией. К ним можно отнести, например, утечку различных продуктов ( нефть, газ, вода, пар) из подвергшихся коррозии трубопроводов, порчу продуктов питания, потерю здоровья, иногда и жизни людей в тех случаях, когда это вызвано коррозией представляет собой важную проблему, а на защиту от коррозии тратятся большие средства. К основным видам коррозии относятся химическая и электрохимическая коррозии.
Химическая коррозия металлов.
Коррозия металлов может протекать при взаимодействии металлов с сухими газами или растворами не электролитов. Такая коррозия называется химической. Взаимодействие металлов с газами ( газовая коррозия ) происходит при повышенных температурах, когда конденсация влаги на поверхности металла невозможна. Газовой коррозии подвергаются арматура печей, детали двигателей внутреннего сгорания, лопатки газовых турбин и т.д. Газовую коррозию претерпевает также металл, подвергаемый термической обработке.
Например, сталь при температурах выше 200 о С начинает интенсивно коррозировать в присутствии многих других газов ( хлора, оксидов азота, углерода, серы ), но главным реагентом для стали является кислород. Медь активно взаимодействует с окислами углерода и серы, содержащимися в атмосфере. Из цветных металлов устойчив к газовой коррозии в воздушных средах никель, а его сплавы с хромом устойчивы к коррозии даже при температурах, превышающих 1000 о C. Отдельной проблемой выступает коррозия энергетических трубопроводов, предназначенных для транспортировки воды и пара. Металл трубопровода подвергается коррозии (окислению) под воздействием растворенного в ней (или конденсате) кислорода. Так как большинство современных систем водоснабжения такие, где обеззараживание воды достигается с помощью хлорсодержащих компонентов, материал трубопровода подвергается интенсивному воздействию ионов хлора. При взаимодействии образуются двух – и трехвалентные хлориды железа, очень трудно растворимые в воде, которые разрушают металл стенки трубопровода и в дальнейшем приводят к его разрушению (образованию свищей, разрушению сварных швов, порывов стенки трубопровода и т.п. ). Отдельным видом коррозии металлов является электрохимическая коррозия. К электрохимической коррозии относятся все случаи коррозии в водных растворах. Электрохимической коррозии подвергаются, например, подводные части судов, паровые котлы, проложенные в земле трубопроводы. Коррозия металла, находящегося во влажной атмосфере, также представляет собой электрохимическую коррозию. В результате электрохимической коррозии окисление металла может приводить как к образованию нерастворимых продуктов (например, ржавчины), так и к переходу металла в растворе в виде ионов.
Однако, физические и химические свойства отдельных металлов (алюминия) являются одним из защитных средств от коррозии. Так, оксиды алюминия образуют на стенке металла химически прочный продукт, который плохо реагирует с кислородом и другими окислителями. Пленка оксида, образующаяся на стенках алюминиевых деталей, препятствует разрушению металла стенки и является одним из способов защиты от коррозий. К важным случаям электрохимической коррозии относятся коррозия в природных водах, в растворах, атмосферная коррозия, коррозия в грунте, коррозия при неравномерной аэрации, контактная коррозия. Атмосферная коррозия – коррозия во влажном воздухе при обычных температурах. Поверхность металла, находящегося во влажном воздухе, бывает покрыта пленкой воды, содержащей различные газы, и в первую очередь – кислород. Скорость атмосферной коррозии зависит от ряда условий. В частности, на нее влияет влажность воздуха и содержание в нем газов образующих с водою кислоты (CO 2, SO2, и др.). Большое значение имеет также состояние поверхности металла: скорость атмосферной коррозии резко возрастает при наличии на поверхности шероховатостей, микрощелей, пор, зазоров и других мест, облегчающих конденсацию влаги.
Коррозия в грунте ( почвенная коррозия ) приводит к разрушению проложенных под землей трубопроводов, оболочек кабелей, деталей строительных сооружений. Металл в этих условиях соприкасается с влагой грунта, содержащей растворенный воздух. В зависимости от состава грунтовых вод, а также от структуры и минералогического состава грунта, скорость этого вида коррозии может быть весьма различной.
Коррозия при неравномерной аэрации – наблюдается в тех случаях, когда деталь или конструкция находится в растворе, но доступ растворенного кислорода к различным ее частям неодинаков. При этом те части металла, доступ кислорода к которым минимален, коррозируют значительно сильнее тех частей, доступ кислорода к которым больше. Локализация процесса окисления приводит к местной коррозии – интенсивному разрушению металла на отдельных участках. Местная коррозия приводит к появлению на поверхности металла углублений («язв»), которые со временем могут превращаться в сквозные отверстия. Этот вид коррозии особенно опасен для обшивки судов, для промышленной химической аппаратуры и в ряде других случаев.
Современные методы защиты металлов от коррозии
Для предупреждения коррозии и защиты от нее применяются многие способы, которые включают в себя изменение коррозионных свойств металла, изменение свойств коррозионной среды.
К электрохимическим методам защиты металлов относятся катодная защита, протекторная защита и др. При катодной защите защищаемая конструкция или деталь присоединяется к отрицательному полюсу источника электрической энергии и становится катодом. В качестве анодов используется куски железа или специально изготовленные сплавы. И протекторы и катодная защита применимы в средах, хорошо проводящих электрический ток, например, в морской воде. В частности, протекторы широко применяются для защиты подводных частей морских судов. Следующим методом защиты от коррозии является изменение коррозионных свойств металла, которое достигается его легированием или нанесением на поверхность металла защитных покрытий.
Наиболее широко применение имеют нержавеющие стали, в состав которых входит до 18 % хрома и до 10% никеля. В качестве металлов для покрытия обычно применяют металлы, образующие на своей поверхности защитные пленки. Как уже говорилось, к таким металлам относятся хром, никель, цинк, кадмий, алюминий, олово и некоторые другие. Значительно реже применяются драгоценные металлы – серебро, золото. Отдельным направлением служит сохранение металла неметаллическими методами. К ним относятся покрытия с защитными материалами: лаками, красками, грунтовками, эмалями, фенолоформальдегидными смолами. Для длительной защиты от атмосферной коррозии металлических сооружений, деталей машин, приборов чаще всего применяются лакокрасочные покрытия. Покрытия, создаваемые химической или электрохимической обработкой металла, представляют собой в основном защитные оксидные или солевые пленки. Примерами могут служить оксидирование алюминия, фосфатирование стальных изделий. Изменение свойств коррозионной среды пригодно для случаев, когда защищаемое изделие эксплуатируется в ограниченном объеме жидкости. Метод состоит в удалении из раствора, в котором эксплуатируется защищаемая деталь, растворенного кислорода ( деаэрация ) или в добавлении к этому раствору веществ, замедляющих коррозию, - ингибиторов. В зависимости от вида коррозии, природы металла и раствора применяются различные ингибиторы. Защитное действие ингибиторов обусловлено тем, что их молекулы или ионы адсорбируются на поверхности металла и каталитически снижают скорость коррозии, а некоторые из них (например, хроматы и дихроматы ) переводят металл в пассивное состояние.
biofile.ru
Министерство образования РФ Петрозаводский государственный университет Кольский филиал Кафедра: Финансы и кредит Дисциплина: Системы современных технологий Преподаватель: Доц. Цукерман В. А. КОНТРОЛЬНАЯ РАБОТА Темы: Коррозия металлов. Современные методы защиты металлов от коррозии. Основные виды полезных ископаемых и минерального сырья (на примере Баренцрегиона ). Комплексное использование минерального сырья. Студент: Кузнецова Ирина Анатольевна. Группа: СФ – 1/02 Специальность: Финансы и кредит. Факультет: экономический Отделение: заочное Снежногорск 2003 Содержание.
Комплексное использование минерального сырья….9
5. Список использованной литературы…………………16
Современное состояние мировых производительных сил и уровень технического прогресса привели к тому, что производственные процессы стали представлять собой сложные, связанные между собой технологические процессы, составляющие систему технологии, направленных на производство отдельно взятого вида продукции. Например, производство автомобилей включает в себя производство стального листа, химическое, нефтехимическое, резинотехническое производство, производство цветных металлов и сплавов, электротехническое и т.д. Производство вычислительной техники включает в себя производство полупроводников, интегральных схем с высокой степенью интеграции, производство радиокомпонентов (резисторов, конденсаторов и т.д. ), стального листа, лакокрасочное производство и т.д. Все они, вместе взятые, взаимодействуют с окружающей средой через системы технологии очистки производственных отходов и сточных вод. Рассматриваемые в настоящей работе технологии являются только частью сложной многоуровневой мировой системы современных технологий.
Коррозией ( от лат. «corroder – разъедать» ) называется самопроизвольное разрушение металлических материалов, происходящее под химическим воздействием окружающей среды. Общая масса металлических материалов, используемых в виде различных изделий в мировом хозяйстве, очень велика. Поэтому, несмотря на то, что обычно скорость коррозий мала, ежегодно из–за коррозии теряется безвозвратно огромное количество металла. По ориентировочным подсчетам безвозвратные потери металла от коррозии составляют 10 – 15 % мировой продукции стали. Но еще больший вред связан не с потерей металла, а с порчей изделий, вызываемой коррозией. Затраты на ремонт или на замену деталей судов, автомобилей, аппаратуры химических производств, трубопроводов, приборов, во много раз превышают стоимость металла, из которого они изготовлены. Наконец, существенными бывают косвенные потери, вызванные коррозией. К ним можно отнести, например, утечку различных продуктов ( нефть, газ, вода, пар) из подвергшихся коррозии трубопроводов, порчу продуктов питания, потерю здоровья, иногда и жизни людей в тех случаях, когда это вызвано коррозией представляет собой важную проблему, а на защиту от коррозии тратятся большие средства. К основным видам коррозии относятся химическая и электрохимическая коррозии. Химическая коррозия металлов. Коррозия металлов может протекать при взаимодействии металлов с сухими газами или растворами не электролитов. Такая коррозия называется химической. Взаимодействие металлов с газами ( газовая коррозия ) происходит при повышенных температурах, когда конденсация влаги на поверхности металла невозможна. Газовой коррозии подвергаются арматура печей, детали двигателей внутреннего сгорания, лопатки газовых турбин и т.д. Газовую коррозию претерпевает также металл, подвергаемый термической обработке. Например, сталь при температурах выше 200 о С начинает интенсивно коррозировать в присутствии многих других газов ( хлора, оксидов азота, углерода, серы ), но главным реагентом для стали является кислород. Медь активно взаимодействует с окислами углерода и серы, содержащимися в атмосфере. Из цветных металлов устойчив к газовой коррозии в воздушных средах никель, а его сплавы с хромом устойчивы к коррозии даже при температурах, превышающих 1000 о C. Отдельной проблемой выступает коррозия энергетических трубопроводов, предназначенных для транспортировки воды и пара. Металл трубопровода подвергается коррозии (окислению) под воздействием растворенного в ней (или конденсате) кислорода. Так как большинство современных систем водоснабжения такие, где обеззараживание воды достигается с помощью хлорсодержащих компонентов, материал трубопровода подвергается интенсивному воздействию ионов хлора. При взаимодействии образуются двух – и трехвалентные хлориды железа, очень трудно растворимые в воде, которые разрушают металл стенки трубопровода и в дальнейшем приводят к его разрушению (образованию свищей, разрушению сварных швов, порывов стенки трубопровода и т.п. ). Отдельным видом коррозии металлов является электрохимическая коррозия. К электрохимической коррозии относятся все случаи коррозии в водных растворах. Электрохимической коррозии подвергаются, например, подводные части судов, паровые котлы, проложенные в земле трубопроводы. Коррозия металла, находящегося во влажной атмосфере, также представляет собой электрохимическую коррозию. В результате электрохимической коррозии окисление металла может приводить как к образованию нерастворимых продуктов (например, ржавчины), так и к переходу металла в растворе в виде ионов. Однако, физические и химические свойства отдельных металлов (алюминия) являются одним из защитных средств от коррозии. Так, оксиды алюминия образуют на стенке металла химически прочный продукт, который плохо реагирует с кислородом и другими окислителями. Пленка оксида, образующаяся на стенках алюминиевых деталей, препятствует разрушению металла стенки и является одним из способов защиты от коррозий. К важным случаям электрохимической коррозии относятся коррозия в природных водах, в растворах, атмосферная коррозия, коррозия в грунте, коррозия при неравномерной аэрации, контактная коррозия. Атмосферная коррозия – коррозия во влажном воздухе при обычных температурах. Поверхность металла, находящегося во влажном воздухе, бывает покрыта пленкой воды, содержащей различные газы, и в первую очередь – кислород. Скорость атмосферной коррозии зависит от ряда условий. В частности, на нее влияет влажность воздуха и содержание в нем газов образующих с водою кислоты (CO 2 , SO2 , и др.). Большое значение имеет также состояние поверхности металла: скорость атмосферной коррозии резко возрастает при наличии на поверхности шероховатостей, микрощелей, пор, зазоров и других мест, облегчающих конденсацию влаги. Коррозия в грунте ( почвенная коррозия ) приводит к разрушению проложенных под землей трубопроводов, оболочек кабелей, деталей строительных сооружений. Металл в этих условиях соприкасается с влагой грунта, содержащей растворенный воздух. В зависимости от состава грунтовых вод, а также от структуры и минералогического состава грунта, скорость этого вида коррозии может быть весьма различной. Коррозия при неравномерной аэрации – наблюдается в тех случаях, когда деталь или конструкция находится в растворе, но доступ растворенного кислорода к различным ее частям неодинаков. При этом те части металла, доступ кислорода к которым минимален, коррозируют значительно сильнее тех частей, доступ кислорода к которым больше. Локализация процесса окисления приводит к местной коррозии – интенсивному разрушению металла на отдельных участках. Местная коррозия приводит к появлению на поверхности металла углублений («язв»), которые со временем могут превращаться в сквозные отверстия. Этот вид коррозии особенно опасен для обшивки судов, для промышленной химической аппаратуры и в ряде других случаев. ^ коррозии. Для предупреждения коррозии и защиты от нее применяются многие способы, которые включают в себя изменение коррозионных свойств металла, изменение свойств коррозионной среды. К электрохимическим методам защиты металлов относятся катодная защита, протекторная защита и др. При катодной защите защищаемая конструкция или деталь присоединяется к отрицательному полюсу источника электрической энергии и становится катодом. В качестве анодов используется куски железа или специально изготовленные сплавы. И протекторы и катодная защита применимы в средах, хорошо проводящих электрический ток, например, в морской воде. В частности, протекторы широко применяются для защиты подводных частей морских судов. Следующим методом защиты от коррозии является изменение коррозионных свойств металла, которое достигается его легированием или нанесением на поверхность металла защитных покрытий. Наиболее широко применение имеют нержавеющие стали, в состав которых входит до 18 % хрома и до 10% никеля. В качестве металлов для покрытия обычно применяют металлы, образующие на своей поверхности защитные пленки. Как уже говорилось, к таким металлам относятся хром, никель, цинк, кадмий, алюминий, олово и некоторые другие. Значительно реже применяются драгоценные металлы – серебро, золото. Отдельным направлением служит сохранение металла неметаллическими методами. К ним относятся покрытия с защитными материалами: лаками, красками, грунтовками, эмалями, фенолоформальдегидными смолами. Для длительной защиты от атмосферной коррозии металлических сооружений, деталей машин, приборов чаще всего применяются лакокрасочные покрытия. Покрытия, создаваемые химической или электрохимической обработкой металла, представляют собой в основном защитные оксидные или солевые пленки. Примерами могут служить оксидирование алюминия, фосфатирование стальных изделий. Изменение свойств коррозионной среды пригодно для случаев, когда защищаемое изделие эксплуатируется в ограниченном объеме жидкости. Метод состоит в удалении из раствора, в котором эксплуатируется защищаемая деталь, растворенного кислорода ( деаэрация ) или в добавлении к этому раствору веществ, замедляющих коррозию, - ингибиторов. В зависимости от вида коррозии, природы металла и раствора применяются различные ингибиторы. Защитное действие ингибиторов обусловлено тем, что их молекулы или ионы адсорбируются на поверхности металла и каталитически снижают скорость коррозии, а некоторые из них (например, хроматы и дихроматы ) переводят металл в пассивное состояние.
Региона). Комплексное использование. Минерального сырья. Современное развитие мировой экономики, ее глобализация являются причиной возникновения различных союзов государств как политических (ООН), военных (НАТО), так и экономических (ЕЭС). Кроме крупных мировых объединений возникли более мелкие региональные союзы ( например, Баренцрегион), созданные для решения специфических экономических вопросов региона. Основными совместно решаемыми экономическими проблемами Баренцрегиона являются:
( 60 % ) и подземных ( 40% ) способами шесть месторождений ( 70% всех запасов ). Апатитовый концентрат ( 39% P2O5) направляется на экспорт ( 25% ) и на химзаводы России ( 75% ), которые, в свою очередь, экспортируют фосфорные удобрения. Главный способ обогащения апатита – нефелиновых руд – это флотация; основными продуктами производства являются концентраты. Месторождения апатит – магнетитовых руд располагаются в районе Ковдора. Месторождение, открытое в 1932 г., эксплуатируется с 1961 года как железорудное, а с 1974 года как комплексное, апатит – бадделеит – железорудное. Рудные тела имеют штокообразную форму и вертикально погружаются на глубину. Разрабатываются они открытым способом, глубина карьера достигает 250 м. Годовая добыча руды достигает 16 млн. тонн, выработка магнетитового концентрата – 6 млн. тонн, апатитового концентрата – 1.2 млн. тонн. Из хвостов флотации извлекается бадделеит. Месторождения железных кварцитов расположены в Приимандровском районе. Железистые кварциты сложены магнетитом гематитом, а также кварцем, амфиболами, гранатом, пироксенами, слюдами и сульфидами. Руды обогащаются с помощью магнитной сепарации, извлечение магнетита достигает 91%. Получаемый магнетитовый концентрат содержит до 68 – 70% железа, который транспортируется на Череповецкий металлургический комбинат с 75% железа, используется в порошковой металлургии для получения высококачественных сталей. Месторождения сульфидных медно – никелевых руд расположены в Печенгском, Аллареченском и Мончегорском рудных полях. Никель извлекался электролитным способом. В 1963 году на комбинате «Североникель» был получен первый высокочистый карбонильный никель, а в 1978 году – первая электолитическая медь. В настоящее время из руд, помимо никеля и меди, извлекается кобальт, золото, платиноиды, селен, теллур и сера. Наиболее перспективное месторождение титановых руд расположено вблизи железнодорожной станции Африканда. Руды, помимо перовскита ( 19 – 31% ) и титаномагнетита ( 22 – 35% ), содержат оливин, пироксен, слюды, магнетит, хлорит и кальцит, Помимо титана, может извлекаться ниобий, тантал и редкие земли. В КНЦ РАН создана современная технология гидрометаллургической переработки руд. Циркониевые руды представлены бадделитовым, циркониевым и эвдиалитовым типами, из которых в настоящее время используется только первый ( Ковдорское месторождение ). В КНЦ РАН была разработана эффективная технология обогащения руд с содержанием 1.6 – 3% двуокиси циркония, которые пригодны для гидрометаллургической переработки. В последние годы на шельфе Баренцева моря открыты месторождения нефти и газа. Наиболее крупное из них, Штокмановское, расположено в 700 км к северу от г. Мурманска. Однако, добыча полезных ископаемых (особенно редкоземельных) связана со значительными технологическими трудностями. Так, например, низкий уровень технологии 30-х – 50-х годов привел к образованию очень большого количества отходов ( так называемых «хвостов» ), которые в свою очередь из – за того, что сами являются местом нахождения редких металлов на новом уровне технологий, представляют из себя значительную ценность для повторного извлечения редкоземельных металлов ( «хвосты» Заполярного, Никеля, Печенги, Мончегорска ). Развитие технологии, особенно энергоемких, а также наличие значительных гидроресурсов привело к созданию целой сети гидроэлектростанций и строительству Кольской АЭС. Отдельным моментом в деятельности стран Баренцрегиона ( Россия, Норвегия, Финляндия, Швеция ) является совместная эксплуатация природных биоресурсов ( морского зверя, рыбы, водорослей и т.д. ) Вопросы добычи биоресурсов решаются путем международных соглашений на уровне МИД стран Барецрегиона. Новый виток технического прогресса, разработка новых технологий привели к системному подходу в добыче полезных ископаемых, где принимаются во внимание не только проблемы извлечения полезных ископаемых из руд, но и проблемы сохранения и защиты окружающей среды при выполнении этих работ. Региональными усилиями стран Баренцрегиона разработаны и внедряются многие технологические программы, направленные на экономию теплоэнергоресурсов, экологическую безопасность и восстановление биопотенциала. На самом Севере Европы Россия граничит с королевством Норвегией (одной из стран Баренцрегиона). Наличие большого числа полноводных и бурных рек вывело Норвегию по запасам гидроэнергии на одно из первых мест в Западной Европе. Велики запасы цветных металлов. Месторождения титановых и молибденовых руд в Норвегии – один из крупнейших в мире. Кроме этого имеются значительные запасы пиритов, которые используются для извлечения из них меди и цинка, производства серной кислоты: а также запасы никелевых руд и месторождения сульфатных руд. Все эти природные богатства привели к развитию электрометаллургии и электрохимии. На континентальном шельфе Северного и Норвежского морей были открыты запасы нефти газа. С открытием стратегически важных и довольно крупных месторождений нефти и газа господствующее положение в экономике страны стала занимать нефтяная и газовая отрасли промышленности. Среди природных богатств Норвегии стоит отменить наличие богатых лесных массивов. Большие запасы леса в сочетании с развитой энергетикой сделали Норвегию крупнейшим экспортером целлюлозно–бумажной продукции. Наличие редких природных металлов прославило страну как крупнейшего экспортера легированных сталей, ферросплавов и цветных металлов. Среди стран – контрагентов, участвующих импорте в Мурманскую область, Норвегия занимает первое место. 35% всех товаров, импортируемых в Мурманскую область – из Норвегии. В товарной структуре экспорта преобладают алюминий и изделия из него, суда и другие плавучие средства, рыба, ракообразные и моллюски. Товарная структура экспортных поставок из Мурманской области имеет природно-сырьевую направленность. В потенциале Мурманской области по–прежнему остаются большие возможности увеличения экспорта апатитового, железорудного и бадделитового концентратов, алюминия, а также редкоземельных металлов. Экспортный потенциал акционерного общества «Апатит», Ковдорского и Оленегорского горнорудных комбинатов, предприятия «Севредмет» используется на 50 – 70%. Наибольший интерес для дальнейшего развития Кольского полуострова представляет комплексное использование руд Кольского полуострова и дальнейшее наращивание объемов переработки отходов производства горнометаллургических предприятий Мурманской области, расширение ассортимента выпускаемой на их основе продукции. При условии комплексного использования руд можно дополнительно получить около 12 млн. тонн нефелинового, 600 – 700 тыс. тонн сфенового, 400 – 500 тыс. тонн титаномагнетитового и 2,7 млн. тонн эгиринового концентрата и других товаров для внутреннего и внешнего рынков. Определенные возможности открываются в связи с использованием разведанных запасов газоконденсатного Штокмановского месторождения. 4. Заключение. Изложенное выше только в малой степени отражает место стран Баренцрегиона в мировом экономическом пространстве, а также сложность и многоуровневость мировой экономической мировой экономической системы как системы современных технологий. Можно с уверенностью сказать дальнейшее развитие технического прогресса, а также стремление мирового сообщества к совместному принятию ответственных экономических и политических решений приведет к дальнейшему усложнению технологических систем, а также к росту числа управленцев, которые будут заняты развитием и разработкой связей между отдельными технологическими системами.
|
do.gendocs.ru