3.3 Проверка на самоторможение и на число витков гайки. Количество витков резьбы после гайки гост
3.3 Проверка на самоторможение и на число витков гайки
После определения диаметра резьбы необходимо проверить выбранные резьбы на самоторможение. Под самоторможением понимается обеспечение невозможности самопроизвольного движения винта под действием рабочей нагрузки (самопроизвольное раскручивание).
Для обеспечения самоторможения механизма должно выполняться условие:
,
где – приведенный угол трения;
–угол подъема винтовой линии;
–коэффициент запаса самоторможения: для самотормозящихся механизмов
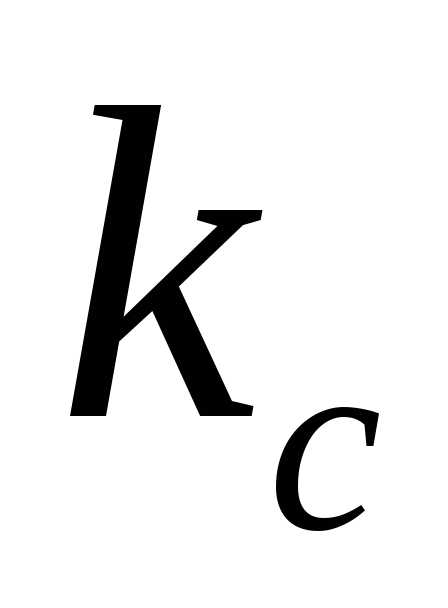
Угол подъема винтовой линии зависит от геометрии резьбы:
,
где – шаг резьбы;
–число заходов резьбы;
–средний диаметр резьбы.
Приведенный угол трения :
,
где – коэффициент трения, зависящий от шероховатостей рабочих поверхностей витков и материала гайки, выбирается по таблице 2.
Таблица 2
Класс точности | Параметры шероховатости, мкм | Коэффициент трения при материале гайки | ||||
винта | гайки | Бронза оловянная | Бронза безоловянная | Чугун | Сталь | |
2 | Ra = 1,25 | Ra = 1,25 | 0,07 | 0,08 | 0,09 | 0,10 |
3 | Ra = 2,5 | Ra = 2,5 | 0,08 | 0,09 | 0,10 | 0,12 |
| Ra = 2,5 | Rz = 20 | 0,09 | 0,10 | 0,12 | 0,15 |
–угол наклона рабочей грани витка к торцевой плоскости винта: для упорной резьбы –
=3, для трапецеидальной резьбы –
=15, для метрической резьбы –
=30;
Результаты расчета коэффициента запаса самоторможения заносятся в таблицу с подобранными резьбами (см. расчет на износостойкость). Резьбы, не обеспечивающие самоторможение, исключаются из рассмотрения. Из оставшихся выбирается резьба с наибольшим шагом, так как чем больше шаг, тем меньше потери на трение, выше КПД, быстрее осевое перемещение винта, крупная резьба меньше изнашивается, ее легче нарезать при необходимости ремонта. Но при этом следует отметить, что увеличиваются габариты резьбы и уменьшается выигрыш в силе, следовательно, в приводе потребуется рукоятка большей длины.
Для того чтобы убедиться в правильности выбора резьбы, необходимо проверить число витков гайки z:
.
Количество витков гайки z должно быть 6…12, оптимальное количество – 8…10. Если число витков z не попадает в указанный диапазон, то следует изменить коэффициент высоты гайки и снова провести расчет на износостойкость (п. 3.2).
3.4 Выбор конструкции пяты
В качестве примера рассмотрим конструкцию пяты винтового домкрата. Под пятой подразумеваем опорную поверхность, к которой прикладывается осевое усилие Q со стороны чашки домкрата (для других конструкций – со стороны других деталей). При вращении винта чашка домкрата остается неподвижной, поэтому на опорной поверхности пяты возникает трение, для уменьшения которого применяют смазку.
3.4.1 Кольцевая пята
Наиболее простой по конструкции и по способу установки будет кольцевая пята (рис. 3.1), но из-за относительно большой величины момента трения ее можно рекомендовать только для домкратов небольшой грузоподъемности (до 2 тонн). Кроме того, в некоторых механизмах, где по конструкции на конце винта требуется хвостовик для крепления маховичка (рис. 2.2, 2.7), кольцевая пята будет единственно возможным вариантом.
Диаметр можно принять, где d – наружный диаметр винта.
Диаметр находится из условия износостойкости трущихся деталей:
,
где = 25…40 МПа – допускаемое давление на поверхности пяты.
Если диаметр превышает внутренний диаметр резьбыd1, в конструкции винта необходим поясок для увеличения площади пяты (рис. 3.1б). При этом следует предусмотреть канавку между пояском и резьбой для выхода режущего инструмента. Толщину пояска можно принять , где
| |||
а | б | ||
Рис. 3.1. Кольцевая пята |
Необходимо помнить, что поясок не позволит при сборке накрутить гайку на винт, поэтому конструкция другого конца винта должна позволять свободный проход гайки до резьбовой части винта.
Высоту выступа на пяте можно принять.
Момент трения на кольцевой пяте будет равен:
,
где = 0,10…0,12 – коэффициент трения стальной чашки о стальной винт.
3.4.2 Сплошная пята
Сплошная пята (рис. 3.2а) компактнее по конструкции, чем кольцевая, обладает меньшим моментом трения на пяте (так как силы трения расположены ближе к оси вращения винта), и поэтому обеспечивает более высокий КПД механизма. Она проще в изготовлении, но крепление опорной детали сложнее. Их можно рекомендовать для механизмов средней нагрузочной способности.
Диаметр опорной поверхности пяты должен таким, чтобы давление на поверхности трения, как и на кольцевой пяте, не превышало
= 25…40 МПа, т.е.:
.
Рассчитанный диаметр должен быть
для обеспечения свободного прохода гайки, идля обеспечения прочности выступа на изгиб.
![]() | |||
а | б | ||
Рис. 3.2. Сплошная (а) и сферическая (б) пяты |
Для облегчения сборки на конце выступа выполняется фаска (0,6…1,0)×45º. Поэтому диаметр выступа под пяту мм. Сопряжение по диаметруосуществляется по посадке с гарантированным зазором.
Высоту выступа на торце винта можно принять.
Момент трения на сплошной пяте:
,
где = 0,10…0,12 – коэффициент трения стальной чашки о стальной винт.
Для уменьшения износа, и, следовательно, увеличения срока службы опорную поверхность пяты целесообразно подвергнуть поверхностной или объемной закалке до твердости HRC 40…45 – HRC 50…55 , или запрессовать в чашку закаленный вкладыш – подпятник 1 (рис. 3.2а). Это также позволит увеличить допускаемое давление
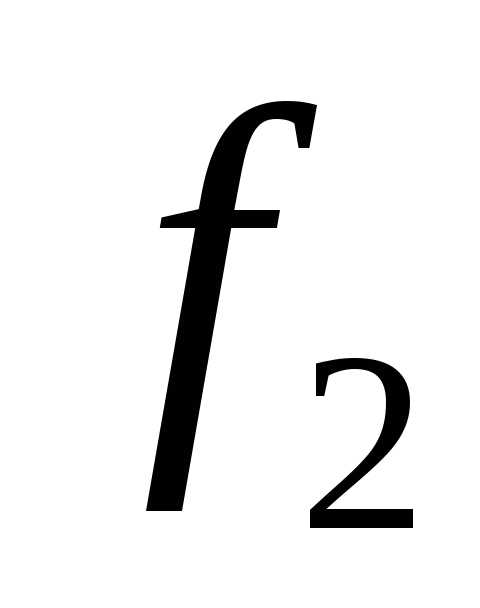
3.4.3 Сферическая пята
Сферическая пята (рис. 3.2б) обеспечивает еще меньший момент трения за счет значительно меньшей площади трения. Она обладает наибольшей нагрузочной способностью, но дороже в изготовлении. Кроме того, сферическая пята обеспечивает центральное нагружение винта даже при неперпендикулярности опорной поверхности подпятника относительно оси винта. Сферическую пяту можно рекомендовать для механизмов с сильно нагруженными винтами, где требуется более высокий КПД и для механизмов, при работе которых возможны перекосы опорных деталей (чашек, прижимов и т.д.).
Рабочая поверхность пяты и подпятника должны иметь твердость HRC 40…45 – HRC 50…55. Радиус сферы R находится из условия контактной прочности рабочих поверхностей:
,
где – приведенный модуль продольной упругости; для стальных деталей
= 2,1105 МПа;
допускаемое контактное напряжение ,
где – предел контактной выносливости, соответствующий базовому числу циклов;
–коэффициент долговечности: для рассматриваемых деталей, отличающихся небольшим числом циклов нагружения за весь срок службы
= 2,4;
–коэффициент запаса контактной прочности.
Величина зависит от твердости
в случае объемной закалки деталей (HRC 40-55):
(МПа), =1,1;
при поверхностной закалке (HRC 40-55):
(МПа), =1,2.
Твердость закалки внутри указанных выше диапазонов задается:HRC 40…45, HRC 45…50 или HRC 50…55. В формулу подставляется среднее значение диапазона:
= 42,5, 47,5 или 52,5.
Диаметр круговой площадки контакта, получающийся в результате деформации сжимаемых тел определяется по формуле:
.
Момент трения в сферической пяте:
,
где – коэффициент трения :
= 0,08…0,10.
Диаметр выступа под пяту на торце винта можно принять.Высота выступа .
3.4.4 Крепление опорных устройств на пяте
На рисунке 3.1 показано крепление чашки домкрата на кольцевой пяте с помощью торцевой шайбы и гайки. Вместо гайки можно использовать винт, если предусмотреть на торце резьбовое отверстие. Зазор a должен быть минимальным, но достаточным для обеспечения свободного вращения чашки домкрата.
На рисунке 3.2а показано крепление опорного устройства на сплошной пяте с помощью установочного винта 2 (по ГОСТ 1478-93, ГОСТ 1482-93). Винт вкручивается в отверстие таким образом, чтобы выступающая часть винта (без резьбы) полностью находилась в канавке. Форма канавки выбирается в зависимости от формы конца установочного винта. Винт не должен касаться дна канавки, чтобы обеспечить свободное вращение опорной детали.
Зазор a служит для компенсации износа опорной поверхности пяты. При отсутствии зазора в случае износа пяты нагрузка с опорного устройства будет передаваться на винт не через пяту, а через установочный винт.
При использовании установочного винта для крепления опорного устройства на сферической пяте (рис. 3.2б), которая допускает некоторый перекос, установочный винт выставляется по центру канавки. Зазор a необходим для обеспечения возможности поворота опорной детали и зависит от величины радиального зазора между выступом и стенкой отверстия:
,
где – суммарный зазор между выступом и стенкой отверстия (разница диаметра отверстия и
).
Другие способы крепления опорных устройств на пяте представлены на рисунках 3.3 и 3.4.
| | |
а | б | в |
Рис. 3.3. Крепление опорных устройств на пяте |
Опорное устройство можно закрепить с помощью шайбы с прорезью (рис. 3.3а) или двух полуколец (рис. 3.3б).
Простым способом будет использование запорного кольца по МН 470-61 (рис. 3.3в), которое представляет собой пружинное кольцо круглого сечения. Канавки на пяте и опорном устройстве имеют форму кольца. Одну из канавок делают глубже, чтобы кольцо утопало при установке опорного устройства. Благодаря фаске на конце выступа на пяте такая пята легко монтируется, но ее демонтаж будет затруднен, если кольцо будет слишком жестким. Для облегчения разборки можно предусмотреть прорезь в опорной детали (рис. 3.4г).
На рисунках 3.4а-в опорная деталь крепится с помощью полуколец, фиксируемых с помощью накидной гайки (рис. 3.4а), внутренней гайки (рис. 3.4б) или плоского пружинного кольца по ГОСТ 13941-86 или ГОСТ 13943-86 (рис. 3.4в).
На рисунке 3.4д опорная деталь фиксируется с помощью двух цилиндрических штифтов, устанавливаемых с натягом в корпус опорной детали. При этом штифты позволяют ей свободно вращаться вокруг винта. На рисунке 3.4е опорная деталь крепится с помощью проволоки из мягкой стали, заводимой в канавку круглого сечения. Данный способ довольно простой при сборке, но связан с трудностями при разборке. Более удобным способом для разборки будет применение пружинной скобы (рис. 3.4ж).
Простой способ крепления показан на рисунке 3.4з. Выступ пяты и отверстие в опорном устройстве имеют наружную и внутреннюю резьбу. Резьба должна иметь левое направление, а вес опорного устройства должен быть относительно небольшим.
| | | |||
а | б | в | |||
| | | | ||
г | д | е | ж | ||
| | | |||
з | и | к | |||
Рис. 3.4. Крепление опорных устройств на пяте |
На рисунке 3.4и опорное устройство держится с помощью пальца, концы которого находятся в кольцевой проточке. Для сборки и разборки необходимы отверстия, закрываемые резьбовыми заглушками.
На рисунке 3.4к показано соединение с помощью шариков, заводимых через боковое отверстие. В отличие от остальных конструкций, показанных ранее, это соединение может передавать большие силы в оба направления при минимальном сопротивлении вращению.
studfiles.net
ГОСТ 1759.0-87 Болты, винты, шпильки и гайки. Технические условия
ГОСТ 1759.0-87
МЕЖГОСУДАРСТВЕННЫЙ СТАНДАРТ
БОЛТЫ, ВИНТЫ, ШПИЛЬКИ И ГАЙКИ
Технические условия
Москва Стандартинформ 2006 |
МЕЖГОСУДАРСТВЕННЫЙ СТАНДАРТ
Дата введения 01.01.89
Настоящий стандарт распространяется на болты, винты, шпильки и гайки с метрической резьбой по ГОСТ 24705*диаметром от 1 до 48 мм.
1.1. Конструкция, размеры и шероховатость поверхности болтов, винтов, шпилек и гаек установлены в стандартах на продукцию.
1.2. Допуски размеров, формы и расположения поверхностей болтов, винтов, шпилек и гаек - по ГОСТ 1759.1.
Основные отклонения резьбы должны назначаться по ГОСТ 16093**в зависимости от требуемой толщины покрытия. Поля допусков резьбы указываются для изделий без покрытия. После нанесения покрытия требования к резьбе в соответствии с ГОСТ 16093.
_______
* С 1 июля 2005 г. введен в действие ГОСТ 24705-2004.
** С 1 июля 2005 г. введен в действие ГОСТ 16093-2004 (здесь и далее).
(Измененная редакция, Изм. № 1).
1.3. По требованию потребителя допускается изготовлять болты, винты и шпильки с увеличенной или уменьшенной длиной резьбовой части.
1.4. По соглашению между изготовителем и потребителем допускается изготовлять:
болты, шпильки и гайки с левой резьбой;
болты с одним контровочным отверстием в головке.
1.5. Допускаемые отклонения формы, от установленной в стандартах на конструкцию болтов, винтов, шпилек и гаек всех классов точности, должны соответствовать указанным в приложении 5.
2.1 Внешний вид
2.1.1. Поверхность болтов, винтов, шпилек и гаек должна быть чистой, без следов коррозии и механических повреждений.
2.1.2. Допускаемые дефекты поверхности болтов, винтов и шпилек - по ГОСТ 1759.2.
2.1.3. Допускаемые дефекты поверхности гаек - по ГОСТ 1759.3.
2.2. Механические свойства и материалы
2.2.1. Механические свойства болтов, винтов (кроме установочных) и шпилек из углеродистых нелегированных и легированных сталей - по ГОСТ 1759.4.
2.2.2. Механические свойства установочных винтов и аналогичных крепежных изделий, не работающих на растяжение, из углеродистых нелегированных и легированных сталей - по ГОСТ 25556.
2.2.3. Механические свойства гаек из углеродистых нелегированных и легированных сталей - по ГОСТ 1759.5.
2.2.4. Механические свойства болтов, винтов, шпилек и гаек из коррозионно-стойких, жаропрочных, жаростойких и теплоустойчивых сталей, а также рекомендуемые марки сталей - по табл. 1 и 2.
2.2.5. Механические свойства болтов, винтов, шпилек и гаек из цветных сплавов, а также рекомендуемые марки сплавов - по табл. 3 и 4.
2.2.6. Допускается изготовлять болты, винты, шпильки и гайки из материалов и сплавов, не предусмотренных в табл. 1 - 4. При этом их механические свойства должны быть не ниже указанных для соответствующих групп.
2.2.7. По требованию потребителя крепежные изделия из латуни, изготовленные холодной высадкой, должны подвергаться термической обработке для снятия внутренних напряжений.
2.3. Покрытия
2.3.1. Болты, винты, шпильки и гайки должны изготовляться с одним из видов покрытий по табл. 5 или без покрытий.
Допускается применять другие виды покрытий - по ГОСТ 9.303.
2.3.2. Выбор толщины покрытий - по ГОСТ 9.303.
2.3.3. Технические требования к покрытиям - по ГОСТ 9.301.
Таблица 1
Механические свойства болтов, винтов и шпилек из коррозионно-стойких, жаропрочных, жаростойких и теплоустойчивых сталей при нормальной температуре
Условное обозначение группы |
Временное сопротивление σв, Н/мм2 |
Предел текучести, σт (σ0,2), Н/мм2 |
Относительное удлинение δ5, % |
Ударная вязкость KCU, Дж/см2 |
Напряжение от пробной нагрузки σп, Н/мм2 |
Сталь |
|
|
Марка |
Обозначение стандарта |
|||||||
Не менее |
|
|||||||
21 |
510 |
195 |
35 |
Не регламентируется |
175 |
12Х18Н10Т |
ГОСТ 5632 |
|
12Х18Н9Т |
||||||||
10Х17Н13М2Т |
||||||||
10Х17Н13М3Т |
||||||||
06ХН28МДТ |
||||||||
22 |
590 |
345 |
20 |
60 |
310 |
12X13 08Х21Н6М2Т |
|
|
23 |
690 |
540 |
12 |
60 |
485 |
20X13 14Х17Н2 |
|
|
24 |
880 |
540 |
8 |
30 |
485 |
10Х11Н23Т3МР |
|
|
25 |
735 |
10 |
30 |
660 |
13Х11Н2В2МФ |
|
||
25Х1МФ; 25Х2М1Ф 20Х1М1Ф1ТР |
ГОСТ 20072 |
|
||||||
26 |
1080 |
835 |
10 |
50 |
750 |
07Х16Н6 |
ГОСТ 5632 |
|
Таблица 2
Механические свойства гаек из коррозионно-стойких, жаропрочных, жаростойких и теплоустойчивых сталей при нормальной температуре
Условное обозначение группы |
Напряжение от пробной нагрузки sF, Н/мм2, не менее |
Сталь |
|
Марка |
Обозначение стандарта |
||
21 |
510 |
12Х18Н10Т, 12Х18Н9Т 10Х17Н13М2Т 10Х17Н13М3Т 06ХН28МДТ |
ГОСТ 5632 |
22 |
590 |
12X13 08Х21Н6М2Т |
|
23 |
690 |
20X13, 14Х17Н2 |
|
24 25 |
880 |
10Х11Н23Т3МР 13Х11Н2В2МФ |
|
25Х1МФ, 25Х2М1Ф 20Х1М1Ф1ТР |
ГОСТ 20072 |
||
26 |
1080 |
07Х16Н6 |
ГОСТ 5632 |
Таблица 3
Механические свойства болтов, винтов, шпилек из цветных сплавов при нормальной температуре
Условное обозначение группы |
Временное сопротивление σв, Н/мм2 |
Предел текучести σт (σ0,2), Н/мм2 |
Относительное удлинение δ5, % |
Твердость по Бринеллю НВ |
Марка материала или сплава |
Обозначение стандарта |
Не менее |
||||||
31 |
260 |
120 |
15 |
Не регламентируется |
АМг5П АМг5 |
ГОСТ 4784 |
32 |
310 |
Не регламентируется |
12 |
75 |
Латунь Л63, Латунь ЛС59-1 |
ГОСТ 15527 ГОСТ 12920 |
33 |
Латунь ЛС59-1 антимагнитная Латунь Л63 антимагнитная |
|||||
34 |
490 |
Не регламентируется |
Бронза Бр. АМц9-2 |
ГОСТ 18175 |
||
35 |
370 |
195 |
10 |
Д1, Д1П, Д16, Д16П |
ГОСТ 4784 |
Таблица 4
Механические свойства гаек из цветных сплавов при нормальной температуре
Таблица 5
Вид покрытия |
Обозначение покрытия |
|
по ГОСТ 9.306 |
цифровое |
|
Цинковое, хроматированное |
Ц. хр |
01 |
Кадмиевое, хроматированное |
Кд. хр |
02 |
Многослойное: медь - никель |
М. Н |
03 |
Многослойное: медь - никель - хром |
М. Н. X. б |
04 |
Окисное, пропитанное маслом |
Хим. Окс. прм |
05 |
Фосфатное, пропитанное маслом |
Хим. Фос. прм |
06 |
Оловянное |
О |
07 |
Медное |
М |
08 |
Цинковое |
Ц |
09 |
Окисное, наполненное хроматами |
Ан. Окс. нхр |
10 |
Окисное из кислых растворов |
Хим. Пас |
11 |
Серебряное |
Ср |
12 |
Никелевое |
Н |
13 |
2.4. Маркировка
2.4.1. Общие правила маркировки
2.4.1.1. Болты с шестигранной головкой, винты с цилиндрической головкой и шестигранным углублением под ключ, шпильки и гайки шестигранные следует маркировать знаком класса прочности (или группы материала) и клеймом (товарным знаком) завода-изготовителя, а изделия с левой резьбой дополнительно знаком левой резьбы.
Обязательной маркировке подлежат:
болты с шестигранной головкой классов прочности 4.6, 5.6, 6.6, 8.8, 9.8, 10.9, 12.9;
винты с цилиндрической головкой и шестигранным углублением под ключ и шпильки классов прочности 8.8, 9.8, 10.9, 12.9;
гайки классов прочности 05, 8, 9, 10, 12.
(Измененная редакция, Изм. № 1).
2.4.1.2. Изделия, не указанные в п. 2.4.1.1 и неуказанных классов прочности, а также изделия, изготовленные методом резания, маркируют по соглашению между изготовителем и потребителем.
2.4.1.3. Знаки маркировки могут быть выпуклыми или углубленными.
2.4.1.4. При маркировке классов прочности допускается не ставить точку, разделяющую первое и второе число знака класса прочности.
При использовании для изделий класса прочности 10.9 низкоуглеродистых мартенситных сталей, знак класса прочности должен быть подчеркнут: 10.9 или 109.
(Измененная редакция, Изм. № 1).
2.4.1.5. Размеры знаков маркировки устанавливает завод-изготовитель.
2.4.2. Маркировка болтов с шестигранной головкой и винтов с цилиндрической головкой и шестигранным углублением под ключ
2.4.2.1. Маркировке подлежат болты и винты с диаметром резьбы d ³ 6 мм.
2.4.2.2. Знаки маркировки наносят на торцевой или боковой поверхности головки болта или винта (черт. 1). Знаки на боковой поверхности головки должны быть углубленными.
Черт. 1
2.4.2.3. При маркировке выпуклыми знаками допускается увеличение наибольшей предельной высоты головки болта или винта на:
0,1 мм - для изделий с диаметром резьбы d £ 8 мм;
0,2 мм – » » » » 8 мм < d £ 12 мм;
0,3 мм » » » » d > 12 мм.
2.4.3. Маркировка шпилек
2.4.3.1. Маркировке подлежат шпильки с диаметром резьбы d ³ 12 мм. Допускается маркировать шпильки с диаметром резьбы d ³ 8 мм с применением заменительных знаков:
○ - для класса прочности 8.8;
+ » » » 9.8;
□ » » » 10.9;
D » » » 12.9.
2.4.3.2. Знаки маркировки наносят на торце гаечного конца шпильки.
2.4.4. Маркировка шестигранных гаек
2.4.4.1. Маркировке подлежат гайки с диаметром резьбы d ³ 6 мм.
2.4.4.2. Знаки маркировки наносят на одной из торцевых поверхностей. В технически обоснованных случаях допускается наносить знаки маркировки на боковых поверхностях гаек (черт. 2). Знаки должны быть углубленными.
2.4.4.3. Допускается применение циферблатной маркировки гаек (черт. 3). В этом случае маркировка наносится на фасках выпуклыми или углубленными знаками или на торцевой поверхности углубленными знаками.
Черт. 2
2.4.5. Маркировка болтов, шпилек и гаек с левой резьбой
2.4.5.1. Знаком левой резьбы является стрелка, указывающая направление ввинчивания болтов, шпильки и навинчивания гайки.
Черт. 3
2.4.5.2. Знак левой резьбы наносят на торцевой поверхности головки болта, на одной из торцевых поверхностей гайки (черт. 4а), на конце гаечного конца шпильки. В технически обоснованных случаях допускается наносить знак левой резьбы на боковых поверхностях гайки и головках болтов (черт. 4б). В этом случае знаки должны быть углубленными.
2.4.5.3. Знак левой резьбы для болтов и гаек может заменяться надрезами на ребрах шестигранников (черт. 4в).
Черт. 4
3.1. Правила приемки болтов, винтов, шпилек и гаек - по ГОСТ 17769.
3.2. Каждая партия крепежных изделий должна сопровождаться документом о качестве с указанием:
наименования или товарного знака завода - изготовителя;
условного обозначения изделия;
перечня и результатов проведенных испытаний;
массы нетто партии;
средств временной противокоррозионной защиты и срока защиты.
Примечания: 1. Допускается вкладывать документ о качестве изделий в тару или конвейер, при этом должна обеспечиваться сохранность его при транспортировании.
2. До 01.01.92 обязательными испытаниями являлись:
по ГОСТ 1759.4 для классов прочности 8.8 - 12.9 определение временного сопротивления и определение ударной вязкости; для классов прочности 4.8; 5.8; 6.8 испытание на прочность соединения головки со стержнем;
по ГОСТ 1759.5 для классов прочности 8 - 12 испытание пробной нагрузкой.
Остальные испытания проводят по требованию потребителя.
(Измененная редакция, Изм. № 1).
4.1. Контроль внешнего вида болтов, винтов, шпилек и гаек должен производиться без применения увеличительных приборов.
Допускается в спорных случаях использовать лупу с увеличением 2,5 - 3х.
4.2. Контроль дефектов поверхности болтов, винтов и шпилек - по ГОСТ 1759.2.
4.3. Контроль дефектов поверхности гаек - по ГОСТ 1759.3.
4.4. Контроль размеров болтов, винтов, шпилек и гаек - по ГОСТ 1759.1.
4.5. Притупление углов квадратного подголовка должно проверяться в контрольной матрице с квадратным отверстием, выполненным по 1-му ряду ГОСТ 16030. Под головкой болта должна устанавливаться плоская шайба с отверстием диаметром большим диаметра описанной окружности подголовка и толщиной 0,5 высоты подголовка.
Проворачивание подголовка в отверстии контрольной втулки или шаблона не допускается.
4.6. Шероховатость поверхностей болтов, винтов, шпилек и гаек должна проверяться путем сравнения с образцами шероховатости по ГОСТ 9378.
Допускается осуществлять контроль шероховатости поверхности при помощи измерительных приборов.
Шероховатость поверхности изделий, изготовленных методом холодной штамповки и шероховатость торца стержней кроме установочных винтов не контролируется.
4.7. Шероховатость резьбы болтов, винтов и шпилек должна проверяться на боковых поверхностях профиля.
Шероховатость резьб, полученных накаткой, и шероховатость резьбы гаек не контролируется и должна обеспечиваться технологией изготовления и инструментом.
4.8. Методы проверки качества и толщины покрытий - по ГОСТ 9.302.
4.9. Методы испытаний и программы испытаний болтов, винтов и шпилек из углеродистых нелегированных и легированных сталей - по ГОСТ 1759.4.
4.10. Испытания болтов, винтов и шпилек из коррозионно-стойких, жаропрочных, жаростойких и теплоустойчивых сталей, а также из цветных сплавов должны проводиться по требованию потребителя в соответствии с табл. 6 по методике ГОСТ 1759.4.
Таблица 6
Механические характеристики |
Вид испытаний |
Группы материалов |
||||
21 |
22, 23, 24, 25, 26 |
31, 35 |
34 |
32, 33 |
||
Временное сопротивление |
Испытание на растяжение |
´ |
´ |
´ |
´ |
´ |
0 |
0 |
0 |
0 |
0 |
||
Предел текучести |
Испытание на растяжение |
´ |
´ |
´ |
- |
- |
Относительное удлинение |
Испытание на растяжение |
´ |
´ |
´ |
´ |
´ |
Твердость по Бринеллю |
Измерение твердости |
|
|
|
|
´ |
0 |
||||||
Ударная вязкость |
Испытание ударной вязкости |
|
´ |
|
|
|
0 - для болтов, винтов и шпилек с резьбой d £ М 5 или длиной > 3d;
´ - для болтов, винтов и шпилек с резьбой d > М 5 и длиной ³ 3d.
Разрушающие нагрузки приведены в приложении 2, пробные нагрузки - в приложении 4.
Другие испытания болтов, винтов и шпилек проводятся по соглашению между изготовителем и потребителем.
(Измененная редакция, Изм. № 1).
4.11. Методы испытаний гаек из углеродистых нелегированных и легированных сталей - по ГОСТ 1759.5.
4.12. Испытания гаек из коррозионно-стойких, жаропрочных, жаростойких и теплоустойчивых сталей, а также гаек из цветных сплавов пробной нагрузкой должны проводиться по требованию потребителя по методике ГОСТ 1759.5.
Пробные нагрузки приведены в приложении 3.
4.13. При изготовлении болтов, винтов и шпилек резанием, без последующей термообработки, допускается проводить испытание механических свойств на исходном металле или изготовленных из него образцах.
Временная противокоррозионная защита изделий, упаковка, маркировка тары, транспортирование и хранение - по ГОСТ 18160.
files.stroyinf.ru
ГОСТ 1759.0-87* «Болты, винты, шпильки и гайки. Технические условия»
ГОСУДАРСТВЕННЫЙ СТАНДАРТ СОЮЗА ССР
БОЛТЫ, ВИНТЫ, ШПИЛЬКИ И ГАЙКИ
ТЕХНИЧЕСКИЕ УСЛОВИЯ
ГОСТ 1759.0-87 (СТ СЭВ 4203-83)
ГОСУДАРСТВЕННЫЙ КОМИТЕТ СССР ПО СТАНДАРТАМ Москва
СОДЕРЖАНИЕ
ГОСУДАРСТВЕННЫЙ СТАНДАРТ СОЮЗА ССР
БОЛТЫ, ВИНТЫ И ШПИЛЬКИ Технические условия Bolts, screws and nuts. Specifications |
ГОСТ 1759.0-87 (СТ СЭВ 4203-83) |
Срок действия с 01.01.89 до 01.01.94
Настоящий стандарт распространяется на болты, винты, шпильки и гайки с метрической резьбой по ГОСТ 24705-81 диаметром от 1 до 48 мм.
1.1. Конструкция, размеры и шероховатость поверхности болтов, винтов, шпилек и гаек установлены в стандартах на продукцию.
1.2. Допуски размеров, формы и расположения поверхностей болтов, винтов, шпилек и гаек - по ГОСТ 1759.1-82.
Основные отклонения резьбы должны назначаться по ГОСТ 16093-81 в зависимости от требуемой толщины покрытия. Поля допусков резьбы указываются для изделий без покрытия. После нанесения покрытия требования к резьбе в соответствии с ГОСТ 16093-81.
(Измененная редакция. Изм. № 1).
1.3. По требованию потребителя допускается изготовлять болты, винты и шпильки с увеличенной или уменьшенной длиной резьбовой части.
1.4. По соглашению между изготовителем и потребителем допускается изготовлять:
болты, шпильки и гайки с левой резьбой;
болты с одним контровочным отверстием в головке.
1.5. Допускаемые отклонения формы, от установленной в стандартах на конструкцию болтов, винтов, шпилек и гаек всех классов точности, должны соответствовать указанным в обязательном приложении 5.
2.1. Внешний вид
2.1.1. Поверхность болтов, пиитов, шпилек и гаек должна быть чистой, без следов коррозии и механических повреждений.
2.1.2. Допускаемые дефекты поверхности болтов, винтов и шпилек - по ГОСТ 1759.2-82.
2.1.3. Допускаемые дефекты поверхности гаек - по ГОСТ 1759.3-83.
2.2. Механические свойства и материалы
2.2.1. Механические свойства болтов, винтов (кроме установочных) и шпилек из углеродистых нелегированных и легированных сталей - по ГОСТ 1759.4-87.
2.2.2. Механические свойства установочных винтов и аналогичных крепежных изделий, не работающих на растяжение, из углеродистых нелегированных и легированных сталей - по ГОСТ 25556-82.
2.2.3. Механические свойства гаек из углеродистых нелегированных и легированных сталей - по ГОСТ 1759.5-87.
2.2.4. Механические свойства болтов, винтов, шпилек и гаек из коррозионно-стойких, жаропрочных, жаростойких и теплоустойчивых сталей, а также рекомендуемые марки сталей - по табл. 1 и 2.
2.2.5. Механические свойства болтов, винтов, шпилек и гаек из цветных сплавов, а также рекомендуемые марки сплавов - по табл. 3 и 4.
2.2.6. Допускается изготовлять болты, винты, шпильки и гайки из материалов и сплавов, не предусмотренных в табл. 1-4. При этом их механические свойства должны быть не ниже указанных для соответствующих групп.
2.2.7. По требованию потребителя крепежные изделия из латуни, изготовленные холодной высадкой, должны подвергаться термической обработке для снятия внутренних напряжений.
2.3. Покрытия
2.3.1. Болты, винты, шпильки и гайки должны изготовляться с одним из видов покрытий по табл. 5 или без покрытий.
Допускается применять другие виды покрытий - по ГОСТ 9.303-84.
2.3.2. Выбор толщины покрытий - по ГОСТ 9.303-84.
2.3.3. Технические требования к покрытиям - по ГОСТ 9.301-86.
Таблица 1
Механические свойства болтов, винтов и шпилек из коррозионно-стойких, жаропрочных, жаростойких и теплоустойчивых сталей при нормальной температуре
Условное обозначение группы |
Временное сопротивление sв, Н/мм2 |
Предел текучести, sт (s0,2) Н/мм2 |
Относительное удлинение d5, % |
Ударная вязкость KCU, Дж/см2 |
Напряжение от пробной нагрузки sп, Н/мм2 |
Сталь |
|
|
Марка |
Обозначение стандарта |
|||||||
Не менее |
|
|||||||
21 |
510 |
195 |
35 |
Не регламентируется |
175 |
12Х18Н10Т 12Х18Н9Т 10Х17Н13М2Т 10Х17Н13М3Т 06ХН28МДТ |
ГОСТ 5632-72 |
|
22 |
590 |
345 |
20 |
60 |
310 |
12Х13 08Х21Н6М2Т |
|
|
23 |
690 |
540 |
12 |
60 |
485 |
20Х13 14Х17Н2 |
|
|
24 |
880 |
540 |
8 |
30 |
485 |
10Х11Н23Т3МР |
|
|
25 |
735 |
10 |
30 |
660 |
13Х11Н2В2МФ |
|
||
25Х1МФ; 25Х2М1Ф 20Х1М1Ф1ТР |
ГОСТ 20072-74 |
|
||||||
26 |
1080 |
835 |
10 |
50 |
750 |
07Х16Н6 |
ГОСТ 5632-72 |
|
Таблица 2
Механические свойства гаек из коррозионно-стойких, жаропрочных, жаростойких и теплоустойчивых сталей при нормальной температуре
Условное обозначение группы |
Напряжения от пробной нагрузки sF, Н/мм2, не менее |
Сталь |
|
Марка |
Обозначение стандарта |
||
21 |
510 |
12Х181-10Т, 12Х18Н9Т 10Х17Н13М2Т 10X17I-113M3T 06ХН28МДТ |
ГОСТ 5632-72 |
22 |
590 |
12Х13 08Х21Н6М2Т |
|
23 |
690 |
20Х13, 14Х17Н2 |
|
24 25 |
880 |
10Х11Н23Т3МР 13Х11Н2В2МФ |
|
25Х1МФ, 25Х2М1Ф 20Х1М1Ф1ТР |
ГОСТ 20072-74 |
||
26 |
1080 |
07Х16Н6 |
ГОСТ 5632-72 |
Таблица 3
Механические свойства болтов, винтов, шпилек из цветных сплавов при нормальной температуре
Условное обозначение группы |
Временное сопротивление sв, Н/мм2 |
Предел текучести, sт (s0,2) Н/мм2 |
Относительное удлинение d5, % |
Твердость по Бринеллю НВ |
Марка материала или сплава |
Обозначение стандарта |
Не менее |
||||||
31 |
260 |
120 |
15 |
Не регламентируется |
АМг5П Амг5 |
ГОСТ 4784-74 |
32 |
310 |
Не регламентируется |
12 |
75 |
Латунь Л63, Латунь ЛС59-1 |
ГОСТ 15527-70 ГОСТ 12920-67 |
33 |
Латунь ЛС59-1, антимагнитная Латунь Л63 антимагнитная |
|||||
34 |
490 |
Не регламентируется |
Бронза Бp. AМи9-2 |
ГОСТ 18175-78 |
||
35 |
370 |
195 |
10 |
Д1, Д1П, Д16, Д16П |
ГОСТ 4784-74 |
Таблица 4
Механические свойства гаек из цветных сплавов при нормальной температуре
Условное обозначение группы |
Напряжения от пробной нагрузки sF, Н/мм2, не менее |
Марка материала или сплава |
Обозначение стандарта |
31 |
260 |
АМг5П, АМг5 |
ГОСТ 178-1-74 |
32 |
310 |
Латунь ЛС59-1, Л63 |
ГОСТ 15527-70, |
33 |
Латунь Л63 антимагнитная Латунь ЛС59-1 антимагнитная |
ГОСТ 12920-67 |
|
34 |
490 |
Бронза Бр, АМц 9-2 |
ГОСТ 18175-78 |
35 |
370 |
Д1, Д1П, Д16, Д16П |
ГОСТ 4784-74 |
Таблица 5
Вид покрытия |
Обозначение покрытия |
|
по ГОСТ 9.306-85 |
цифровое |
|
Цинковое, хроматированное |
Ц.хр |
01 |
Кадмиевое, хроматированное |
Кд. хр |
02 |
Многослойное: медь-никель |
М.Н |
03 |
Многослойное: медь-никель-хром |
М. Н. X. б |
04 |
Окисное, пропитанное маслом |
Хим. Окс. прм |
05 |
Фосфатное, пропитанное маслом |
Хим. Фос. прм |
06 |
Оловянное |
О |
07 |
Медное |
М |
08 |
Цинковое |
Ц |
09 |
Окисное, наполненное хроматами |
ан. Окс. нхр |
10 |
Окисное из кислых растворов |
Хим. Пас |
11 |
Серебряное |
Ср |
12 |
Никелевое |
Н |
13 |
2.4. Маркировка
2.4.1. Общие правила маркировки
2.4.1.1. Болты с шестигранной головкой, винты с цилиндрической головкой и шестигранным углублением под ключ, шпильки и гайки шестигранные следует маркировать знаком класса прочности (или группы материала) и клеймом (товарным знаком завода-изготовителя, а изделия с левой резьбой дополнительно знаком левой резьбы.
Обязательной маркировке подлежат:
болты с шестигранной головкой классов прочности 4.6, 5.6, 6.6, 8.8, 9.8, 10.9, 12.9;
винты с цилиндрической головкой и шестигранным углублением под ключ и шпильки классов прочности 8.8, 9.8, 10.9, 12.9;
гайки классов прочности 05, 8, 9, 10, 12.
(Измененная редакция. Изм. № 1).
2.4.1.2. Изделия, не указанные в п. 2.4.1.1 и неуказанных классов прочности, а также изделия, изготовленные методом резания, маркируют по соглашению между изготовителем и потребителем.
2.4.1.3. Знаки маркировки могут быть выпуклыми или углубленными.
2.4.1.4. При маркировке классов прочности допускается не ставить точку, разделяющую первое и второе число знака класса прочности.
При использовании для изделий класса прочности 10.9 низкоуглеродистых мартенситных сталей знак класса прочности должен быть подчеркнут: 10.9 или 109.
(Измененная редакция. Изм. № 1).
2.4.1.5. Размеры знаков маркировки устанавливает завод-изготовитель.
2.4.2. Маркировка болтов с шестигранной головкой и винтов с цилиндрической головкой и шестигранным углублением под ключ
2.4.2.1. Маркировке подлежат болты и винты с диаметром резьбы d³6 мм.
2.4.2.2. Знаки маркировки наносят на торцевой или боковой поверхности головки болта или винта (черт. 1). Знаки на боковой поверхности головки должны быть углубленными.
Черт. 1
2.4.2.3. При маркировке выпуклыми знаками допускается увеличение наибольшей предельной высоты головки болта или винта на:
0,1 мм - для изделий с диаметром резьбы d£8 мм;
0,2 мм- » » » » 8 мм<d£12 мм;
0,3 мм- » » » » d>12 мм.
2.4.3. Mapкировка шпилек
2.4.3.1. Маркировке подлежат шпильки с диаметром резьбы d³12 мм. Допускается маркировать шпильки с диаметром резьбы d³8 мм с применением заменительных знаков:
○ - Для класса прочности 8.8;
+ - » » » 9.8;
□ - » » » 10,9;
∆ - » » » 12.9.
2.4.3.2. Знаки маркировки наносят на торце гаечного конца шпильки.
2.4.4. Маркировка шестигранных гаек
2.4.4.1. Маркировке подлежат гайки с диаметром резьбы d³5 мм.
2.4.4.2. Знаки маркировки наносят на одной из торцевых поверхностей. В технически обоснованных случаях допускается наносить знаки маркировки на боковых поверхностях гаек (черт. 2). Знаки должны быть углубленными.
Черт. 2
2.4.4.3. Допускается применение циферблатной маркировки гаек (черт. 3). В этом случае маркировка наносится на фасках выпуклыми или углубленными знаками или на торцевой поверхности углубленными знаками.
2.4.5. Маркировка болтов, шпилек и гаек с левой резьбой
2.4.5.1. Знаком левой резьбы является стрелка, указывающая направление ввинчивания болта, шпильки и навинчивания гайки.
Класс прочности |
8 |
9 |
10 |
12 |
Циферблатная маркировка гаек |
Черт. 3
2.4.5.2. Знак левой резьбы наносят на торцевой поверхности головки болта, на одной из торцевых поверхностей гайки (черт. 4а), на конце гаечного конца шпильки. В технически обоснованных случаях допускается наносить знак левой резьбы на боковых поверхностях гайки и головках болтов (черт. 4б). В этом случае знаки должны быть углубленными.
2.4.5.3. Знак левой резьбы для болтов и гаек может заменяться надрезами на ребрах шестигранников (черт. 4в).
Черт. 4
3.1. Правила приемки болтов, винтов, шпилек и гаек - по ГОСТ 17769-83.
3.2. Каждая партия крепежных изделий должна сопровождаться документом о качестве с указанием:
наименования или товарного знака завода-изготовителя;
условного обозначения изделия;
перечня и результатов проведенных испытаний;
массы нетто партии;
средств временной противокоррозионной защиты и срока защиты.
Примечание. Допускается вкладывать документ о качестве изделий в тару или контейнер, при этом должна обеспечиваться сохранность его при транспортировании.
2. До 01.01.92 обязательными испытаниями являются:
по ГОСТ 1759.4-87 для классов прочности 8.8-12.9 определение временного сопротивления и определение ударной вязкости; для классов прочности 4.8; 5.8; 6.8 испытание на прочность соединения головки со стержнем;
по ГОСТ 1759.5-87 для классов прочности 8-12 испытание пробной нагрузкой.
Остальные испытания проводят по требованию потребителя
(Измененная редакция. Изм. № 1).
4.1. Контроль внешнего вида болтов, винтов, шпилек и гаек должен производиться без применения увеличительных приборов.
Допускается в спорных случаях использовать лупу с увеличением 2,5-3´.
4.2. Контроль дефектов поверхности болтов, винтов и шпилек - по ГОСТ 1759.2-82.
4.3. Контроль дефектов поверхности гаек - по ГОСТ 1759.3-83.
4.4. Контроль размеров болтов, винтов, шпилек и гаек - по ГОСТ 1759.1-82.
4.5. Притупление углов квадратного подголовка должно проверяться в контрольной матрице с квадратным отверстием, выполненным по 1-му ряду ГОСТ 16030-70. Под головкой болта должна устанавливаться плоская шайба с отверстием диаметром большим диаметра описанной окружности подголовка и толщиной 0,5 высоты подголовка.
Проворачивание подголовка в отверстии контрольной втулки или шаблона не допускается.
4.6. Шероховатость поверхностей болтов, винтов, шпилек и гаек должна проверяться путем сравнения с образцами шероховатости по ГОСТ 9378-75.
Допускается осуществлять контроль шероховатости поверхности при помощи измерительных приборов.
Шероховатость поверхности изделий, изготовленных методом холодной штамповки и шероховатость торца стержней кроме установочных винтов, не контролируется.
4.7. Шероховатость резьбы болтов, винтов и шпилек должна проверяться на боковых поверхностях профиля.
Шероховатость резьб, полученных накаткой, и шероховатость резьбы гаек не контролируется и должна обеспечиваться технологией изготовления и инструментом.
4.8. Методы проверки качества и толщины покрытий - по ГОСТ 9.302-88.
(Измененная редакция. Изм. № 1).
4.9. Методы испытаний и программы испытаний болтов, винтов и шпилек из углеродистых нелегированных и легированных сталей - по ГОСТ 1759.4-87.
4.10. Испытания болтов, винтов и шпилек из коррозионно-стойких, жаропрочных, жаростойких и теплоустойчивых сталей, а также из цветных сплавов должны проводиться по требованию потребителя в соответствии с табл. 6 по методике ГОСТ 1759.4-87.
Разрушающие нагрузки приведены в приложении 2, пробные нагрузки - в приложении 4.
Другие испытания болтов, винтов и шпилек проводятся по соглашению между изготовителем и потребителем.
4.11. Методы испытаний гаек из углеродистых нелегированных и легированных сталей - по ГОСТ 1759.5-87.
4.12. Испытания гаек из коррозионно-стойких, жаропрочных, жаростойких и теплоустойчивых сталей, а также гаек из цветных сплавов пробной нагрузкой должны проводиться по требованию потребителя по методике ГОСТ 1759.5-87.
Пробные нагрузки приведены в приложении 3.
4.13. При изготовлении болтов, винтов и шпилек резанием, без последующей термообработки, допускается проводить испытание механических свойств на исходном металле или изготовленных из него образцах.
Таблица 6
Механические характеристики |
Вид испытаний |
Группы материалов |
||||
21 |
22, 23, 24, 25, 26 |
31, 35 |
34 |
32, 33 |
||
Временное сопротивление |
Испытание на растяжение |
´ 0 |
´ 0 |
´ 0 |
´ 0 |
´ 0 |
Предел текучести |
Испытание на растяжение |
´ |
´ |
´ |
- |
- |
Относительное удлинение |
Испытание на растяжение |
´ |
´ |
´ |
´ |
´ |
Твердость по Бринеллю |
Измерение твердости |
|
|
|
|
´ 0 |
Ударная вязкость |
Испытание ударной вязкости |
|
´ |
|
|
|
0 - для болтов, винтов и шпилек с резьбой d£M 5 или длиной <3d;
´ - для болтов, винтов и шпилек с резьбой d>M 5 и длиной ³3d.
(Измененная редакция. Изм. № 1).
Временная противокоррозионная защита изделий, упаковка, маркировка тары, транспортирование и хранение - по ГОСТ 18160-72.
Условное обозначение болтов, винтов, шпилек и гаек должно записываться по следующей схеме:
Примеры условных обозначений крепежных изделий.
Винт - по ГОСТ 17473-80 класса точности А, исполнения 2, диаметром резьбы d=12 мм с мелким шагом резьбы, с полем допуска резьбы 6е, длиной l=60, класса прочности 5.8, из спокойной сталь с цинковым покрытием толщиной 9 мкм, хроматированным
Винт A2M12´1,25-6e´60.58.C.019 ГОСТ 17473-80
Гайка - по ГОСТ 5916-70 исполнения 2, диаметром резьбы d=12 мм, с мелким шагом резьбы, с левой резьбой, с полем допуска 6Н, класса прочности 05, из стали марки 40Х, с цинковым покрытием толщиной 6 мкм, хроматированным
Гайка 2М12´1,25-LH-6Н.05.40Х.016 ГОСТ 5916-70
(Измененная редакция. Изм. № 1).
Примечания:
1. В условном обозначении не указывают:
исполнение 1, крупный шаг резьбы, правую резьбу, отсутствие покрытия, а также параметры, однозначно определяемые стандартами на продукцию;
класс точности В, если стандартом на конкретное крепежное изделие предусматривается 2 класса точности (А и В).
2. Если применяется покрытие, не предусмотренное настоящим стандартом, его обозначение указывается по ГОСТ 9.306-85.
files.stroyinf.ru
Методические рекомендации и задания к контрольной работе № 3, страница 6
Гайки бывают повышенной, нормальной и грубой точности. Наибольшее распространение получили шестигранные гайки нормальной точности – ГОСТ 5915–70. Они изготовляются в двух исполнениях – с двумя (рис. 19а) или одной (рис. 19б) наружной фаской.
Рис. 19
На учебных чертежах гайка обозначается упрощенно:
Гайка 2М12 ГОСТ 5915–70,
где внутренний диаметр резьбы d= 12 мм, гайка исполнения 2, шести-гранная, нормальной степени точности (следует из номера стандарта).
2.5. Шайба
Шайба – деталь резьбового соединения в виде тонкого плоского или фасонного диска с отверстием круглой формы.
Стандартные плоские шайбы подкладывают под гайки или головки болтов (винтов) с целью предохранения свинчиваемых деталей от повреждений и для увеличения опорной поверхности гайки или головки.
Наиболее распространены плоские шайбы ГОСТ 11371–78 (рис. 20а).
Если соединение работает в условиях вибрации, то для предотвращения самоотвинчивания болтов, винтов и гаек применяются пружинные или стопорные шайбы.
Пружинные шайбы (ГОСТ 6402‑70) представляют собой виток резьбы прямоугольного профиля с левым направлением винтовой линии (рис. 20б).
Рис. 20
На учебных чертежах шайбы обозначаются упрощенно:
Шайба 18 ГОСТ 11371–78.
Это плоская шайба (следует из номера стандарта), исполнения 1, пред-назначенная для стержня с резьбой наружного диаметра d= 18 мм (действи-тельный размер отверстия шайбы равен 19 или 20 мм в зависимости от класса точности).
3. Соединение деталей крепежными изделиями
Изображения соединений деталей различными крепежными изделиями выполняются по определенным правилам. Размеры этих изделий на сборочных чертежах не наносятся. В разрезах и сечениях болты, винты, шпильки показываются нерассеченными (не штрихуются), если секущая плоскость проходит вдоль геометрической оси стержня.
Вычерчивание крепежных изделий в соединениях на учебном задании выполняется по действительным размерам, т.е. все необходимые размеры крепежных изделий нужно брать из соответствующих стандартов.
3.1. Соединение деталей болтом
Болтовое соединение состоит из болта, гайки, шайбы и скрепляемых деталей, например крышки и корпуса (рис. 21).
Характерная особенность соединения деталей болтом в том, что в крышке и корпусе выполняются отверстия без резьбы (так называемые свободные отверстия), размеры которых стандартизированы. На чертежах диаметры свободных отверстий можно выполнять по относительному размеру, равному 1,1d, гдеd– диаметр стержня крепежного изделия. Болт вставляется в отверстие крышки и корпуса, а на его свободный конец накидывается шайба и навинчивается гайка.
На шестигранной головке болта и шестигранной гайке выполнены фаски под углом 30˚ к их торцам. Следовательно, на главном виде изображения нужно построить фронтальные проекции гипербол – линий пе-ресечения конической поверхности фаски плоскостями (гранями гайки), которыми образованы шестигранники под гаечный ключ (построение и необходимые параметры показаны на рис. 22).
Принято на главном виде чертежа изображать три грани шестигранных элементов крепежных изделий (рис. 22).
Длина болта l определяется по формуле:
l= n1 + n2 + sш + m+ f,
где n1 и n2 – толщины соединяемых деталей;
sш – толщина шайбы;
m– высота гайки;
f = 3Р – длина выступающего над гайкой конца болта;
Р – шаг резьбы.
Числовые значенияs, m и Р определяют по таблицам соответствующих стандартов по номинальному диаметру резьбы d (табл. 2, 4, 5).
Полученную по формуле величину сравнивают со стандартными длинами болтов (табл. 3) и выбирают ближайшую большую стандартную длину. Это значение записывается в условное обозначение болта при составленииспецификации. По этой же таблице выбирается длина резьбы b на стержне болта.
Болты с шестигранной головкой
класса точности В по ГОСТ 7798–70 в мм
Таблица 2 Размеры в мм
vunivere.ru
Число - витки - резьба
Число - витки - резьба
Cтраница 1
Число витков резьбы в гайке крюка определяют исходя из допускаемого удельного давления в резьбе. [1]
Определив число витков резьбы, получим рабочую высоту резьбы Яр nS, где S - шаг резьбы. [2]
В Шр - число витков резьбы в гайке высотой Н, р - шаг резьбы; h - высота ( рабочая) профиля резьбы; nd2 - длина одного витка по среднему диаметру. [3]
Высота гайки Н определяется числом витков резьбы, необходимых для сопротивления разрывающим усилиям. [4]
Высота гайки h z s, где г - число витков резьбы в гайке, определенное из расчета ни смятие. [5]
Зависимость величины разрушающих нагрузок резьбового соединения от профиля и числа витков резьбы показана на рис. 1 [47], из которого видно, что прочность метрической резьбы примерно на 15 - 20 % выше прочности исследованных упорной, полукруглой и трапецеидальной резьб и на 26 - 28 % выше прочности прямоугольной резьбы. [7]
Высота гайки h z - s, где z - число витков резьбы в гайке, определенное из расчета на смятие. [8]
Высота гайки h - z - s, где z - число витков резьбы в гайке, определенное из расчета на смятие. [9]
Свинчивание и развинчивание осуществляется быстрее, так как при цилиндрических резьбах число оборотов равно числу витков резьбы, а при конических число оборотов тем меньше числа витков резьбы, чем больше ее конусность. [11]
Профиль резьбы непроходной стороны пробки также неполный: срезаны вершины резьбы, а по впадинам прорезаны канавки; число витков резьбы кольца не превышает 3 5 для того, чтобы устранить влияние возможных погрешностей наружного, внутреннего диаметров, шага и угла профиля. [12]
Профиль резьбы непроходной стороны пробки также неполный: срезаны вершины резьбы, а по впадинам прорезаны канавки; число витков резьбы кольца не превышает 3 5 для того, чтобы устранить влияние возможных погрешностей наружного, внутреннего диаметров, шага и угла профиля. [13]
Так как резьба на верхней головке делается секционной и занимает 50 % поверхности головки, то в целях равнопрочности принимаем число витков резьбы на головке в два раза больше, чем на корпусе колонны. [14]
Свинчивание и развинчивание осуществляется быстрее, так как при цилиндрических резьбах число оборотов равно числу витков резьбы, а при конических число оборотов тем меньше числа витков резьбы, чем больше ее конусность. [15]
Страницы: 1 2 3
www.ngpedia.ru