Литьё цветных металлов в металлические формы - кокили (стр. 1 из 8). Литье алюминия в кокиль
Гравитационное (классическое) литьё алюминия в кокиль
Для крупносерийного выпуска алюминиевой продукции используются многочисленные методы получения отливок. Традиционным и широко распространенным на литейном производстве является метод гравитационного (классического) литья алюминия. Почему он называется гравитационным, в чем особенности и основные достоинства данного метода?
Гравитационное литьё сплавов из алюминия
Для выпуска изделий требуемых параметров используют специальную емкость — кокиль, в которую заливается расплавленная масса металла. После полного охлаждения готовую деталь можно легко извлечь и отправить на последующую механическую обработку. Кокиль обычно изготовлен из чугуна, благодаря чему допустимо его многоразовое применение до 10 тысяч циклов.
Если же речь идет о мелкосерийной или единичной продукции, в ход идут пластиковые и даже деревянные емкости, а также изготовленные из песка и глины с добавлением пластификаторов. Кокиль — это один из элементов литейной оснастки, кроме него требуются также различные стержни, модельные плиты и шаблоны, необходимые для производства деталей из алюминия со сложной геометрией.
Расплавленный металл под действием силы гравитации заполняет все полости оснастки, полностью копируя форму заданного изделия. После его извлечения на поверхности могут быть шероховатости или другие изъяны, избавиться от которых можно путем дальнейшей механической обработки.
Основные этапы классического литья
Кокиль нашел широкое распространение на литейных производствах по той простой причине, что алюминий относится к мягким пластичным металлам. Вылитые из него детали широко используются практически во всех сферах промышленности, например в машиностроении.
Сам процесс производства состоит из определенных стадий:
- подготовка оснастки;
- установка стержней;
- заливка жидкого металла;
- охлаждение и извлечение.
Изготовление оснастки является одним из наиболее ответственных этапов, так как форма должна с максимальной точностью повторять линии готового изделия. К счастью, сегодня есть достаточно функциональные программы и сложное оборудование для 3D моделирования и получения нужных форм.
Чтобы готовое изделие можно было легко извлечь из кокиля, его стенки тщательно очищают, а затем покрывают специальной облицовкой. Наличие малейших неровностей может привести к образованию дефектов.
Преимущества гравитационного литья
Почему именно данный способ нашел наибольшее распространение? Причин можно привести множество, но основная из них — относительная простота и дешевизна по сравнению с другими способами. А это отображается и на конечной стоимости отливок.
Из других достоинств отметим:
- точность, низкий уровень шероховатости;
- толщина стенок от 4 мм и более;
- выпуск деталей практически любых размеров;
- быстрое остывание алюминиевых сплавов.
Благодаря всем этим факторам можно значительно снизить себестоимость готовой продукции. Кроме того, все изделия полученные данным методом, проходят строгую систему ОТК, любой брак отправляется на переработку.
Кокили
Классификация конструкций кокилей
В производстве используют кокили различных конструкций. В зависимости от отсутствия или наличия поверхности разъема кокили бывают неразъемные (вытряхные) или разъемные.
Неразъемные, или вытряхные, кокили применяют в тех случаях, когда конструкция отливки позволяет удалять ее вместе с литниками из полости кокиля без его разъема. Обычно эти отливки имеют достаточно простую конфигурацию.
В случае разъемных кокилей расположение и число разъемов определяются необходимостью реализовать рациональное положение отливки в кокиле при заливке, разместить технологические элементы (литниковую систему, прибыли и др.), собрать форму и извлечь из нее без разрушения готовую отливку конкретной конструкции. В свою очередь, разъемы кокиля предопределяют выбор кокильной машины с соответствующим количеством и расположением механизмов, которые обеспечивают перемещение подвижных частей кокиля при его сборке и разборке.
По числу рабочих полостей (гнезд), определяющих возможность одновременного (с одной заливки) изготовления того или иного числа отливок, кокили разделяют на одноместные и многоместные.
В зависимости от способа охлаждения различают кокили с воздушным (естественным и принудительным), жидкостным (водяным, масляным) и комбинированным (водовоздушным и т.д.) охлаждением. Если воздушное охлаждение используют для малотеплонагруженных кокилей, то водяное охлаждение обычно применяют для высокотеплонагруженных кокилей, а также для повышения скорости охлаждения отливки или ее отдельных частей. Вода подается раздельно в обе половины кокиля, нижнюю плиту и верхнюю крышку.
Элементы конструкции кокилей
Конструктивное исполнение основных элементов кокилей – полуформ, плит, металлических стержней, вставок – зависит от конфигурации отливки и от особенностей установки кокиля на кокильную машину.
К основным элементам конструкции кокилей относят: формообразующие элементы – половины кокилей, нижние плиты (поддоны), вставки, стержни; конструктивные элементы – толкатели, плиты толкателей, системы нагрева и охлаждения кокиля и отдельных его частей, вентиляционная система, центрирующие штыри и втулки.
Корпус кокиля или его половины выполняют коробчатым с ребрами жесткости. Ребра жесткости на тыльной (не рабочей) стороне кокиля делают невысокими, толщиной 0,7 – 0,8 толщины стенки кокиля, сопрягая их галтелями с корпусом. Толщина стенки кокиля зависит от состава заливаемого сплава и его температуры, размеров и толщины стенки отливки, материала, из которого изготовляется кокиль, и его конструкции. Толщина стенки кокиля должна быть достаточной, чтобы обеспечить заданный режим охлаждения отливки, необходимую жесткость кокиля и минимальное его коробление при нагреве отводимой теплотой залитого расплава, а также стойкость против растрескивания.
Размеры и конструкция частей кокиля должны позволять размещать и закреплять его на плитах кокильной машины.
Стержни в кокилях могут быть песчаными и металлическими. Песчаные стержни для кокильных отливок должны обладать пониженной газотворностью и повышенной поверхностной прочностью. Первое требование обусловлено трудностями удаления газов из кокиля, второе – взаимодействием знаковых частей стержней с кокилем, в результате чего отдельные песчинки могут попасть в полость кокиля и образовать засоры в отливке. Стержневые смеси и технологические процессы изготовления песчаных стержней могут быть различными – сплошные и оболочковые стержни из холоднотвердеющих смесей и т.д. В любом случае использование песчаных стержней в кокилях вызывает необходимость организации дополнительной технологической линии для изготовления стержней в кокильном цехе. Однако, в конечном счете использование кокилей в комбинации с песчаными стержнями в большинстве случаев экономически оправдано.
Использование металлических стержней зависит от конструкции отливки и технологических свойств сплава. Их использование дает возможность повысить скорость затвердевания отливки, сократить продолжительность цикла ее изготовления, в отдельных случаях повысить механические свойства и плотность (герметичность) отливки. Однако при использовании металлических стержней возрастают напряжения в отливках, увеличивается опасность появления в них трещин из-за затруднения усадки.
Для надежного извлечения стержней из отливки они должны иметь ук-лоны 1 – 5о, хорошие направляющие во избежание перекосов, а также быть надежно зафиксированы в форме.
Во многих случаях металлические стержни делают водоохлаждаемыми изнутри. Водяное охлаждение стержня обычно включают после образования в отливке прочной корочки. При охлаждении размеры стержня сокращаются и между ним и отливкой образуется зазор, благодаря которому уменьшаются усилия при извлечении стержня из отливки.
Вентиляционная система должна обеспечивать направленное вытеснение воздуха из кокиля расплавом. Для выхода воздуха используют открытые выпоры, зазоры по плоскости разъема и между подвижными частями кокиля и специальные вентиляционные каналы. По плоскости разъема делают газоотводные каналы, направленные по возможности вверх. В местных углублениях формы при заполнении их расплавом могут образовываться воздушные мешки. В этих местах в стенке кокиля устанавливают вентиляционные пробки. При выборе места установки вентиляционных пробок необходимо учитывать последовательность заполнения формы расплавом.
Центрирующие элементы – контрольные штыри и втулки – предназначены для точной фиксации половин кокиля при его сборке. Обычно их количество не превышает двух и располагают их в диагонально противоположных углах кокиля.
Закрытие и запирание кокилей, устанавливаемых на машинах, осуществляется пневматическим или гидравлическим приводом подвижной плиты машины. Системы нагрева и охлаждения кокиля предназначены для поддержания заданного температурного режима процесса. Применяют электрический и газовый обогрев. Первый используется для общего нагрева кокиля, второй более удобен для общего и местного нагрева.
Материалы для кокилей
В процессе эксплуатации в кокиле возникают значительные термические напряжения как результат чередующихся резких нагревов при заливке, а также при затвердевании отливки и охлаждений при раскрытии кокиля и извлечении отливки, нанесении на рабочую поверхность огнеупорного покрытия. Кроме знакопеременных термических напряжений под действием переменных температур в материале кокиля могут протекать структурные изменения и химические процессы. Поэтому материалы, предназначенные для изготовления кокиля, особенно его частей, непосредственно соприка-сающихся с расплавом, должны хорошо противостоять термической устало-сти, иметь высокие механические свойства и претерпевать минимальные структурные превращения при температурах эксплуатации, обладать повышенной ростоустойчивостью и окалиностойкостью, характеризоваться минимальной диффузией отдельных элементов при циклическом воздействии температур, хорошо обрабатываться, быть недефицитными и недорогими.
Производственный опыт показывает, что для изготовления рабочих стенок кокилей пригодны следующие материалы, в достаточно полной мере соответствующие указанным требованиям:
- чугуны СЧ20, СЧ25 и др. – кокили для мелких и средних отливок из алюминиевых, магниевых, медных сплавов, чугуна, а также кокили с воздушным и водовоздушным охлаждением;
- чугуны ВЧ40, ВЧ45 и др. – кокили для мелких, средних и крупных отливок из чугунов: серого, высокопрочного, ковкого, кокили с воздушным и водовоздушным охлаждением;
- стали 10, 20, Ст3, стали 15Л, 15ХМЛ и др. – кокили для мелких, средних, крупных и особо крупных отливок из чугуна, стали, алюминиевых, магниевых, медных сплавов;
- медь и ее сплавы, легированные стали и сплавы с особыми свойствами – вставки для интенсивного охлаждения отдельных частей отливок, тонкостенные водоохлаждаемые кокили, массивные металлические стержни для отливок из разных сплавов;
- силумины АЛ9, АЛ11 и др. — водоохлаждаемые кокили с анодированной поверхностью для мелких отливок из алюминиевых и медных сплавов.
Наиболее широко для изготовления кокилей применяют серый и высокопрочный чугуны, так как эти материалы в достаточной мере удовлетворяют основным технологическим требованиям и сравнительно дешевы. Эти чугуны должны иметь феррито-перлитную структуру. Графит в серых чугунах должен иметь форму мелких изолированных включений. В этих чугунах не допускается присутствие свободного цементита, так как при нагревах кокиля произойдет распад цементита с изменением объема материала, в результате в кокиле возникнут внутренние напряжения, способствующие короблению, образованию сетки разгара, снижению его стойкости. В состав чугунов для кокилей с целью повышения их стойкости вводят до 1 % никеля, меди, хрома, а содержание вредных примесей (серы и фосфора) в них должно быть минимальным. Например, для изготовления кокилей с высокой теплонагруженностью рекомендуется серый чугун следующего химического состава, мас. %: 3,0 – 3,2 С, 1,3 –1,5 Si, 0,6 – 0,8 Мn, 0,7 – 0,9 Сu, 0,3 – 0,7 Ni, 0,08 – 0,1 Тi, не более 0,12 S, не более 0,1 Р.
Для изготовления кокилей широко используют также низкоуглеродистые стали марок 10, 20, а также стали, легированные хромом и молибденом, например, сталь марки 15ХМЛ. Эти материалы обладают высокой пластичностью, поэтому хорошо сопротивляются растрескиванию при эксплуатации.
Кокили для мелких отливок из алюминиевых сплавов иногда изготавливают также из алюминиевых сплавов (АЛ9 и АЛ11). Такие кокили анодируют, в результате чего на их рабочей поверхности образуется тугоплавкая износостойкая пленка оксида алюминия толщиной до 0,4 мм, температура плавления которой составляет около 2000оС. Высокая теплопроводность стенок кокиля из алюминия способствует быстрому отводу теплоты от отливки. Эти кокили обычно делают водоохлаждаемыми.
Медь также часто используют для изготовления рабочих стенок водоохлаждаемых кокилей. Из меди делают отдельные вставки, вкладыши в местах, где необходимо ускорить отвод тепла от отливки и тем самым управлять процессом ее затвердевания.
Стержни простой конфигурации изготовляют из конструкционных углеродистых сталей, а стержни сложной конфигурации – из легированных сталей. Для прочих деталей – осей, валов, болтов и т.д. – используют конструкционные стали.
Стойкость кокилей и пути ее повышения. Данный показатель измеряется числом отливок требуемого качества, полученных в данном кокиле до выхода его из строя. Приблизительная стойкость кокилей приведена в таблице 3.1.
Таблица 3.1 – Приблизительная стойкость кокилей
Основной причиной разрушения кокиля являются сложные термохимические процессы в материале кокиля, вызываемые неравномерным циклическим нагревом и охлаждением его рабочей стенки во всех трех ее измерениях (по толщине, длине и ширине). Это приводит к появлению неоднородного, изменяющегося с изменением температуры поля напряжений в стенке кокиля, вызывающего ее упругие и пластические деформации. Для последних характерны остаточные деформации и напряжения. Теоретически показано, что в поверхностном слое кокиля нереализованная термическая деформация обычно в 2 раза превосходит деформацию, соответствующую пределу текучести материалов при определенной температуре. Поэтому в каждом цикле термического нагружения (заливка – удаление отливки) деформация сжатия сменяется дефор-мацией растяжения, что приводит к термической усталости материала кокиля. Термические напряжения возникают также вследствие структурных превращений и роста зерна материала кокиля, протекающих тем интенсивнее, чем выше температура его нагрева. Способность кокиля выдерживать термические напряжения зависит от механических свойств его материала при рабочих температурах кокиля. Эти свойства резко снижаются при нагреве. Например, предел текучести стали 15 при нагреве до температуры 600оС уменьшается приблизительно в 3 раза.
Уровень возникающих в кокиле напряжений зависит также от конструкции кокиля – толщины его стенки, конструкции ребер жесткости и т.д. Например, тонкие ребра жесткости большой высоты приводят к появлению трещин на рабочей поверхности кокиля, а низкие ребра могут не обеспечить жесткость кокиля и привести к короблению.
Стойкость кокилей обеспечивается конструктивными, технологическими и эксплуатационными методами.
Конструктивные методы основаны на правильном выборе материалов для кокилей в зависимости от преобладающего вида разрушения, разработке рациональной конструкции кокиля.
Термические напряжения, приводящие к снижению стойкости кокиля, являются следствием нереализованной термической деформации: менее нагретые части кокиля (слои рабочей стенки, прилегающие к внешней нерабочей поверхности, ребра жесткости) препятствуют расширению нагревающейся металлом отливки части кокиля. Уменьшить напряжения можно, если термическая деформация нагретой части происходит беспрепятственно. Этого можно достичь, если расчленить рабочую стенку кокиля на отдельные элементы в продольном или поперечном направлениях. Тогда вследствие зазоров между элементами кокиля каждый из них при нагреве расширяется свободно.
Для повышения стойкости кокилей используют сменные вставки, оформляющие рабочую полость кокиля. Благодаря зазорам между корпусом и вставкой, термическая деформация вставки протекает свободно, возникающие в ней напряжения снижаются, стойкость кокиля возрастает. Наиболее эффективно использование сменных вставок в многоместных кокилях.
Технологические методы направлены на повышение стойкости поверхностного слоя рабочей полости, имеющего наибольшую температуру при работе кокиля. Для этого используют поверхностное легирование, алитирование, силицирование, термическую обработку различных видов, наплавку, напыление на рабочую поверхность материалов, повышающих стойкость кокиля. Каждый из этих способов предназначен для повышения стойкости кокиля к разрушениям определенного вида.
Рисунок 3.4 – Зависимость стойкости кокиля kзал от темпа работы m
Таблица 3.2 – Температура нагрева кокилей перед заливкой
uas.su
Литье в кокиль - проверенная и точная технология производства отливок из алюминия.
Литье в кокиль (многоразовую металлическую форму) – это достаточно дорогостоящая, но проверенная и точная литейная технология, применяемая Компанией «ПРАКТИК плюс» при производстве отливок из алюминиевых сплавов.
Несмотря на высокую первоначальную стоимость оснастки, технология литья в кокиль имеет ряд основных преимуществ, по сравнению с другими технологиями, а именно:
- отливки получают с более плотной структурой;
- значительно улучшается внешний вид отливок и чистота поверхности;
- повышается точность отливок и идентичность их размеров;
- уменьшается металлоемкость отливки и стоимость механической обработки за счет уменьшения литейных припусков;
- увеличивается выход годного литья;
- устраняются операции с формовочными смесями;
- при крупносерийном производстве снижается себестоимость продукции;
- значительно повышается производительность труда литейщиков.
Для изготовления кокилей специалисты «ПРАКТИК плюс» в основном применяют серый или высокопрочный чугун, а также углеродистые или легированные стали. Серый чугун, применяемый для кокилей, стойкий к тепловым нагрузкам, недорогой и легко обрабатываемый материал. Стальные кокили более дорогие в изготовлении, но более «живучие» чугунных, так как они не боятся ударных нагрузок. Металлические стержни, направляющие и толкатели для раскрытия кокиля и выталкивания отливок всегда изготавливают из стали, так как они испытывают повышенные растягивающие напряжения.
Основной показатель кокиля — его стойкость. При работе рабочие поверхности кокилей подвергаются быстрому нагреву и охлаждению, в следствие чего в них возникают термические напряжения, приводящие к короблению и поверхностным трещинам – разгарам. Стойкость чугунных и стальных кокилей при получении отливок из алюминиевых сплавов составляет 50—100 тыс. заливок. Для повышения стойкости кокилей рабочие поверхности покрывают красками. С помощью красок устраняется также приваривание металла к стенкам кокиля, обеспечивается получение качественных поверхностей и регулируется направленность затвердевания отливок. При соприкосновении с металлом краска возгоняется, создается газовая и сажистая прослойка между жидким металлом и кокилем, которая предотвращает приваривания жидкого металла к кокилю. Краску наносят кистью или пульверизатором один-два раза в смену, в зависимости от конструкции и режима работы, на подогретый до 100—200 °C кокиль.
В процессе литья очень важным технологическим параметром является температурный режим кокиля. Для получения качественного литья из алюминиевых сплавов температура кокиля должна поддерживаться в пределах 200—350 °C. Разогрев и поддержание температуры кокиля (разгон кокиля) специалисты «ПРАКТИК плюс» осуществляют подогревом с помощью газовых горелок, а контроль температурного режима осуществляют инфракрасными термометрами (пирометрами) или термопарами. Охлаждение кокиля осуществляется путем естественной передачи тепла в окружающую среду через стенки кокиля. При необходимости наши специалисты спроектируют и изготовят кокили, охлаждаемые снаружи водой (водоохлаждаемые) по специально предусмотренным каналам. Стойкость водоохлаждаемых кокилей выше, чем неводоохлаждаемых.
При литье сложных по конфигурации отливок специалисты «ПРАКТИК плюс» применяют различные подвижные металлические стержни и вставки. Подвижность нужна для своевременного удаления стержня из отливки. Если внутренние контуры отливки сложные, то стержни делают составными из нескольких частей. Также для получения отливок со сложной внутренней конфигурацией нами применяются песчаные стержни. Их устанавливают в форму каждый раз перед заливкой при сборке формы с помощью знаковых частей.
В «ПРАКТИК плюс» изготавливают кокили либо литыми, либо из поковок проката путем механической обработки. Литые кокили дешевле, поскольку требуется минимальная механическая обработка. Разъем (раскрытие) кокилей осуществляют ручным или механизированным способом с помощью механических, пневматических и гидравлических приводов, которые также проектируют и изготавливают специалисты «ПРАКТИК плюс». Поверхности разъемов обрабатывают по 6-му классу точности. Отдельные части кокиля центрируют с помощью штырей и втулок. Для вывода газа и воздуха из полости кокиля предусматриваются вентиляционные каналы.
Компания "ПРАКТИК плюс" рассматривает заказы на производство литья из алюминия любой конфигурации и серийности, массой до 50 кг.
Цена отливки зависит от сложности детали и рассчитывается индивидуально.
За дополнительной информацией обращайтесь по тел.: (067) 437-90-70, (050) 921-30-09 или по контактам, указанным на сайте.
praktikp.com.ua
Литье алюминия в кокиль
Завод «Zavod-Litja.ru» оказывает услуги по литью алюминия в кокиль. Наше предприятие в год выполняет объём литья в размере 80 тонн. Отливки, которые можно заказать на нашем заводе находятся в диапазоне от 0,5 кг до 160 кг. Наш завод готов предоставить как черновую продукцию, так и последующую механическую обработку изделий. При литье мы используем следующие технологии:
- литьё в кокиль (в пределах до 15кг.),
- литьё в модели из ХТС (до 160кг.)
Наш завод оборудован кокильными станками с использованием вертикальной оси разъёма. Производительность до 5 тонн в час обеспечивается наличием шнекового смесителя OMEGA. В цеху нашего завода также имеется специальная площадь для производства отливок с помощью технологии ХТС. Механическая обработка изделий производится с помощью наждачных, фрезерных и сверлильных станков и дробеметного барабана.
Пришлите ваши чертежи или эскизы на [email protected]
Либо звоните 8-800-250-88-72. Доставка по России и СНГ!!!
Мы предлагаем все виды литья из черных и цветных металлов от 1кг и литьё в кокиль, так как этот способ наиболее целесообразный при создании отливок, который доводит объём производства до максимума и сберегает точность изделий. Подобный метод литья создаёт отливки с минимальным припуском, что позволяет экономить металл и сокращать время на мехобработку.
Литьё цветных металлов выгодно и удобно совершать с помощью кокиля. Точность полученных изделий соответствует 4-6 классу точности. Произведенные отливки могут быть совершенно тонкими: до 3 мм.
Литье алюминия в кокиль
Существуют разнообразные способы литья алюминия в кокиль позволяющие избежать дефектов и деформации при литье. Так, на нашем производстве для этого используют расширяющиеся литники. Применяется также многоярусное, щелевое и нижнее подведение расплавленного металла в кокиль, что обеспечивает его хорошее распределение и последующее качественное отделение шлака. Также применяется подпитка места подвода, и определённое расположение системы литников вдоль линии разъёма кокиля.
Для того чтобы контролировать скорость движущегося расплава применяются фильтры и изогнутые стояки, по которым он движется. Контролируя скорость можно добиться качественного заполнения сечений любого диаметра и избежать недоливов, в случае, когда был недостаточно выведен газ или воздух. Литьё в кокиль и литье корпусов из алюминия не предполагает чрезмерно высокой скорости движения расплава. Выдержка, которой подвергается отливка зависит от того как быстро затвердевает данный металл, какова температура кокиля и как быстро была произведена заливка.
Чтобы металл не прилипал к форме существуют определённые смазывающие жидкости. Извлечение изделия из формы напрямую зависит от угла заливки. Поэтому наружные поверхности заливают под углом 3º, а внутренние — 6º. Кокильная форма, которая отвечает за наружную поверхность изделия, создаётся из чугуна. Её толщина определяется тем, какой толщина должна быть сама отливка. Чтобы создать внутренние полости у отливки используют стержни из песка или стали. Песочные стержни обычно применяются при литье алюминия в кокиль более сложных конструкций.
Преимущества нашего завода
Завод «Zavod-Litja.ru» создаёт только качественную продукцию. Литейное оборудование нашего предприятия автоматизировано, что позволяет после создания опытного образца, устранив все его дефекты, наладить производство качественных отливок в авральные сроки. Пресс-формы, оснастка для моделей создаётся на высокоточных станках. Опытные инженеры и технологи нашего завода с использование современного литейного оборудования совершают плавку шестого класса точности (максимального). Наш завод отличается адекватными ценами и условиями оплаты. Работа с заявками поступившими ведётся оперативно. Доставка готовых изделий производиться по всем городам России и СНГ.
Базовые этапы технологического процесса
Подготовка кокиля к литью
Происходит его очистка от загрязнений, ржавчины и масла. Проверяется функционирование подвижных частей и их центровка, затем создаются прессформы для литья алюминия. Проверяется надёжность креплений.
Пришлите ваши чертежи или эскизы на [email protected]
Либо звоните 8-800-250-88-72. Доставка по России и СНГ!!!
На втором этапе происходит подготовка поверхностей. Кокиль и его стержни обрабатываются огнеупорным покрытием. Для этого поверхность кокиля нагревают до температуры 430-455 градусов и с помощью пульверизатора наносят огнеупорное покрытие в виде водного раствора.
Его состав определяется маркой металла, из которого будет производиться литьё, а также скоростью охлаждения изделия. Огнеупорное покрытие выполняет также сберегающую функцию, предотвращая резкое повышение температуры кокиля и схватывание его с отливкой.
На третьем этапе литья алюминия в кокиль происходит покрытие огнеупорной краской, разогревают до 600 градусов – рабочей температуры. Температура нагревания зависит от металла, из которого будет производиться литьё, размеров отливки и толщины её стенок. На этом этапе в кокиль, по мере необходимости, устанавливаются стержни в зависимости от того какая именно деталь должна быть произведена. После чего кокиль закрывается, а его половины скрепляются зажимами и специальными механизмами.
На четвёртом этапе в кокиль заливается расплав. Залитый в кокиль металл постепенно начинает затвердевать и охлаждаться. Первыми извлекаются по мере остывания из кокиля стержни. Частичное изъятие стержней из недостаточно затвердевшей отливки диктуется необходимостью, противостоять усадке металла.
На пятом этапе кокиль открывается, окончательно извлекаются стержни, и вынимается отливка. После чего из неё выбиваются песочные стержни, отрезаются литники, выпоры, прибыли, т.е. приспособление отвечающие за качество отливки.
После извлечения отливки, кокиль готов к новому циклу. Перед началом литья его вновь рассматривают, исследуют плоскость разъёма и рабочую поверхность. В тех местах, где огнеупорное покрытие повредилось, его наносят повторно. За одну смену достаточно двух покрытий кокиля огнеупорной смесью.
Подготовленную поверхность кокиля начинают снова разогревать, поскольку для извлечения тонкостенных отливок и точного литья алюминия из определённых металлов он доходит до полного охлаждения. В случае, когда отливалась массивная деталь, то кокиль наоборот охлаждается, поскольку даже после извлечения крупной отливки кокиль долго сберегает её температуру. Для этого в кокиле наличествуют определённые устройства охлаждения.
zavod-litja.ru
Литье в кокиль (кокильное литье) | Специальные методы литья
Литье в кокиль (кокильное литье), или литье в металлическую форму многоразового использования, является одним из прогрессивных методов производства. Оно предназначено для получения отливок из чугуна, стали, алюминиевых, магниевых, цинковых, медных и других сплавов. Наиболее широко применяется литье в кокиль при применении цветных металлов. Кокильное литье повышает формовочную площадь (в 2—6 раз), производительность труда (в 1,5—6 раз), точность исполнения отливки, выход годного литья благодаря уменьшению припусков. При этом методе литейного производства снижаются количество брака (особенно, если отливки подвергаются гидропробе) и себестоимость продукции.
Отливки, затвердевшие в металлической форме, имеют более плотную мелкозернистую структуру и более высокие механические свойства. Значительно улучшаются санитарно-гигиенические условия работы. Недостатками кокильного литья являются невысокая стойкость форм, высокая стоимость их изготовления при отливке чугунных и стальных деталей, отбел и неоднородность структуры металла по сечению отливки. Для ликвидации отбела применяют защитные покрытия в виде обмазок, красок, припыленного ферросилиция, наносимых перед заливкой на рабочую поверхность кокиля, а также выбивку горячих деталей при температуре более 700 °С и перенос их в условия медленного охлаждения (печь, колодец, песок), отжиг в печи.
Стойкость кокиля является наиболее важным фактором, определяющим рентабельность и области применения данного способа. Стойкость форм при литье цинка, алюминия и магния измеряется сотнями тысяч отливок, количество отливок из чугуна составляет 1500—2000 шт., из стали — 600—700 шт. Если для цветных сплавов выгодно изготовлять металлические формы сложной конфигурации, то для отливок из чугуна и стали следует ограничиваться выбором несложных деталей, так как в противном случае значительные затраты и высокая стоимость кокилей приводят к нерентабельности литья. Наиболее выгодным является кокильное литье алюминиевых сплавов, так как оно, улучшая структуру отливок, является эффективным методом борьбы с газовой и усадочной пористостью этих сплавов.
Большое влияние на свойства чугуна и других металлов оказывает температура заливки кокиля. С повышением температуры заливки увеличивается жидкотекучесть металла, лучше заполняются тонкостенные формы, но снижается стойкость кокиля, усиливаются его коробление и разгар. Изменение температуры заливки влияет на скорость кристаллизации и охлаждения отливок. Чем ниже температура заливки, тем больше скорость охлаждения и более мелкозернистой получается структура металла. Но наряду с положительным влиянием увеличение скорости охлаждения повышает отбел чугуна вследствие образования цементита. Для чугуна желательная высокая температура заливки. Это способствует разогреву кокиля, замедлению процесса кристаллизации, уменьшению отбела и удалению растворимых газов. Рекомендуемая температура заливки серого чугуна в кокиль составляет 1350—1260 °С в зависимости от толщины стенок отливки.
www.stroitelstvo-new.ru
Методы литья алюминия - «РОСАЛ»
15 Сен Методы литья алюминия
Posted at 12:52h in Технология литья by adminАлюминий за счет низкой цены, малого веса и превосходных характеристик пользуется популярностью и применяется в производстве деталей для всевозможных конструкций, кухонной утвари, электропроводов, различных красок и д.р.
В зависимости от запросов заказчика этот металл подвергается разным способам обработки для придания ему требуемых свойств. Часто в производстве используются разные сплавы алюминия, потому что в чистом виде этот материал довольно податливый и не всегда обладает требуемыми свойствами.
Пресс — литьё алюминия
Изготовление деталей на заказ из сплава алюминия методом пресс — литья. Процесс производства происходит в прочных стальных разборных матрицах при помощи специальных поршневых машин. Высокое давление создаётся гидравлическим прессом или специальным поршнем, который работает под давление сжатого газа или масляного состава, горячим или холодным способом.
Большая темп прессования и качество готовых деталей обуславливается давлением в 100 — 200 атм., под действием которого отливки получают 3 — 5 класс точности и стабильно ровную поверхность характеризуемую по 5 — 8 классу.
Из-за высокой точности отливки готовые детали не нуждаются в дополнительной обработке, а их качество позволяет применять эти детали на важных участках, где большое значение придается их точность. Таким образом отливаются детали сложных форм, с тонкими стенками, а также те из них, которые предназначены для сложных конструкций. Отличные технические характеристики деталей из сплава алюминия, произведённых методом горячего пресс — литья, позволяют использовать их для отливки комбинированных упрочненных деталей с армированием из другого, более прочного металла.
Литьё алюминия под давлением это экономически выгодный и экологически безопасный способ.
В течении небольшого промежутка времени можно сделать много деталей, используя лишь одну матрицу. Из-за того, что при этом способе не возникает необходимости в использовании алюминиевых формовочных смесей, такое производство является менее вредным и поэтому более предпочтительным, а высокая точность конструкций уменьшает затраты на материал и в целом на предприятии.
Литье алюминия в кокиль
Второй популярный метод отливки деталей из алюминиевых сплавов называется кокилем. Это специальная цельная или неразборная форма изготовленная из металла, которая используется для формовки простых и сложных деталей из сплава алюминия. При изготовлении несложных деталей применяют цельные формы, готовые отливки просто достают из них с помощью специальных инструментов.
Разборные кокили могут быть с различными плоскостями разъемов:
• вертикальная;• горизонтальная;• криволинейная.
Кокиль с вертикальной плоскостью разъема состоит из двух половин, точность соединения которых достигается использованием втулок и штырей. Перед использованием формы нагревают до 270 — 300 градусов по Цельсию и покрывают особой огнестойкой краской, затем в него устанавливают специальные стержни, максимально точно и прочно скрепляют обе половинки формы.
Расплавленный алюминий вливают в форму — кокиль и оставляют до полного застывания. Этот метод не отличается скоростью, поэтому для производства большого количества деталей необходимо соответствующее количество форм. Точность отливки при этом способе изготовления соответствует 5 — 9 классам, неровность поверхности – 4 — 6 классу. Если сравнивать с отливкой деталей под высоким давлением, в этом варианте расход материала на припуски увеличивается на 0,5 — 2 мм. Этот метод отливки, как литье алюминия в кокиль, тоже довольно экономичен, а детали отличаются большой точностью и надёжностью. Матрицу — кокиль можно использовать многоразово.
rosalcompany.ru
Литьё цветных металлов в металлические формы
Министерство образования Российской Федерации
КУБАНСКИЙ ГОСУДАРСТВЕННЫЙ ТЕХНОЛОГИЧЕСКИЙ УНИВЕРСИТЕТ
Кафедра АПП
“Литьё цветных металлов в металлические формы (кокили)”.
Выполнил: студент
Группы 01-КТ-61
Агранович Олег
Проверил: Лецик В.И.
Краснодар 2003 год.
ОГЛАВЛЕНИЕ
ОГЛАВЛЕНИЕ.. 2
СУЩНОСТЬ ПРОЦЕССА. ОСНОВНЫЕ ОПЕРАЦИИ. ОБЛАСТЬ ИСПОЛЬЗОВАНИЯ.. 3
КОКИЛИ.. 6
Общие сведения. 6
Элементы конструкции кокилей. 7
Материалы для кокилей. 9
Изготовление кокилей. 10
Стойкость кокилей и пути ее повышения. 11
ТЕХНОЛОГИЯ ЛИТЬЯ В КОКИЛЬ.. 13
Технологические режимы литья. 13
Особенности изготовления отливок из различных сплавов. 15
Отливки из алюминиевых сплавов. 16
Отливки из магниевых сплавов. 19
Отливки из медных сплавов. 20
Финишные операции и контроль отливок из цветных сплавов. 21
Дефекты отливок из цветных сплавов и меры их предупреждения. 21
СУЩНОСТЬ ПРОЦЕССА. ОСНОВНЫЕ ОПЕРАЦИИ. ОБЛАСТЬ ИСПОЛЬЗОВАНИЯ
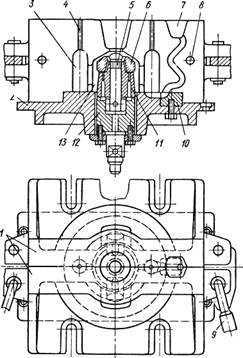
Кокиль (рис. 2.1) обычно состоит из двух полуформ 1, плиты 2, вставок 10. Полуформы взаимно центрируются штырями 8, и перед заливкой их соединяют замками 9. Размеры рабочей полости 13 кокиля больше размеров отливки на величину усадки сплава. Полости и отверстия в отливке могут быть выполнены металлическими 11 или песчаными 6 стержнями, извлекаемыми из отливки после ее затвердевания и охлаждения до заданной температуры. Расплав заливают в кокиль через литниковую систему 7, выполненную в его стенках, а питание массивных
узлов отливки осуществляется из прибылей (питающих выпоров) 3. При заполнении кокиля расплавом воздух и газы удаляются из егорабочей полости через вентиляционные выпоры 4, пробки 5, каналы 12, образующие вентиляционную систему кокиля.Основные элементы кокиля — полуформы, плиты, вставки, стержни т. д.— обычно изготовляют из чугуна или стали. Выше рассмотрен кокиль простой конструкции, но в практике используют кокили различных, весьма сложных конструкций.
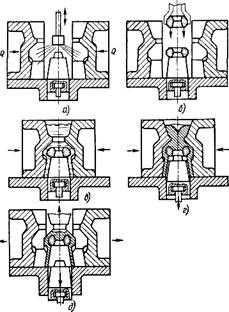
Перед нанесением огнеупорного покрытия кокиль нагревают газовыми горелками или электрическими нагревателями до температуры 423—453 К. Краски наносят на кокиль обычно в виде водной суспензии через пульверизатор. Капли водной суспензии, попадая на поверхность нагретого кокиля, испаряются, а огнеупорная составляющая ровным слоем покрывает поверхность.
После нанесения огнеупорного покрытия кокиль нагревают до рабочей температуры, зависящей в основном от состава заливаемого сплава, толщины стенки отливки, ее размеров, требуемых свойств.Обычно температура нагрева кокиля перед заливкой 473—623 К. Затем в кокиль устанавливают песчаные или керамические стержни (рис. 2.2, б), если таковые необходимы для получения отливки; половины кокиля соединяют (рис. 2.2, в) и скрепляют специальными зажимами, а при установке кокиля на кокильной машине с помощью ее механизма запирания, после чего заливают расплав в кокиль. Часто в процессе затвердевания и охлаждения отливки, после того как отливка приобретет достаточную прочность, металлические стержни «подрывают», т. е. частично извлекают из отливки (рис. 2.2, г) до ее извлечения из кокиля. Это делают для того, чтобы уменьшить обжатие усаживающейся отливкой металлического стержня и обеспечить его извлечение из отливки. После охлаждения отливки до заданной температуры кокиль раскрывают, окончательно извлекают металлический стержень и удаляют отливку из кокиля (рис. 2.2, д). Из отливки выбивают песчаный стержень, обрезают литники, прибыли, выпоры, контролируют качество отливки. Затем цикл повторяется.
Перед повторением цикла осматривают рабочую поверхность кокиля, плоскость разъема. Обычно огнеупорную краску наносят на рабочую поверхность кокиля 1—2 раза в смену, изредка восстанавливая ее в местах, где она отслоилась от рабочей поверхности. После этого при необходимости, что чаще бывает при литье тонкостенных отливок или сплавов с низкой жидкотекучестью, кокиль подогревают до рабочей температуры, так как за время извлечения отливки и окраски рабочей поверхности он охлаждается. Если же отливка достаточно массивная, то, наоборот, кокиль может нагреваться ее теплотой до температуры большей, чем требуемая рабочая, и перед следующей заливкой его охлаждают. Для этого в кокиле предусматривают специальные системы охлаждения,
Как видно, процесс литья в кокиль — малооперацион-н ы и. Манипуляторные операции достаточно просты и кратковре-менны, а лимитирующей по продолжительности операцией является охлаждение отливки в форме до заданной температуры. Практически все операции могут быть выполнены механизмами машины или автоматической установки, что является существенным преимуществом способа, и, конечно, самое главное — исключается трудоемкий и материалоемкий процесс изготовления формы: Кокиль используется многократно.
Особенности формирования и качество отливок. Кокиль — металлическая форма, обладающая по сравнению с песчаной значительно большей теплопроводностью, теплоемкостью, прочностью, практически нулевыми газопроницаемостью и газотвор-. ностью. Эти свойства материала кокиля обусловливают рассмотренные ниже особенности его взаимодействия с металлом отливки.
1. Высокая эффективность теплового взаимодействия между отливкой и формой: расплав и затвердевающая отливка охлаждаются в кокиле быстрее, чем в песчаной форме, т. е. при одинаковых гидростатическом напоре и температуре заливаемого расплава заполняемость кокиля обычно хуже, чем песчаной формы. Это осложняет получение в кокилях отливок из сплавов с пониженной жидкотекучестью и ограничивает минимальную толщину стенок и размеры отливок. Вместе с тем повышенная скорость охлаждения способствует получению плотных отливок с мелкозернистой структурой, что повышает прочность и пластичность металла отливок. Однако в отливках из чугуна, получаемых в кокилях, вследствие особенностей кристаллизации часто образуются карбиды, ферритографитная эвтектика, отрицательно влияющие на свойства чугуна: снижается ударная вязкость, износостойкость, резко возрастает твердость в отбеленном поверхностном слое, что затрудняет обработку резанием таких отливок и приводит к необходимости подвергать их термической обработке (отжигу) для устранения отбела.
2. Кокиль практически неподатлив и более интенсивно препятствует усадке отливки, что затрудняет извлечение ее из формы, может вызвать появление внутренних напряжений, коробление и трещины в отливке.
Однако размеры рабочей полости кокиля могут быть выполнены значительно точнее, чем песчаной формы. При литье в кокиль отсутствуют погрешности, вызываемые расталкиванием модели, упругими и остаточными деформациями песчаной формы, снижающими точность ее рабочей полости и соответственно отливки. Поэтому отливки в кокилях получаются более точными. Точность отливок в кокилях обычно соответствует 12—15-ам квалитетам по СТ СЭВ 145—75. При этом точность по 12-му квалитету возможна для размеров, расположенных в одной части формы. Точность размеров, расположенных в двух и более частях формы, а также оформляемых подвижными частями формы, ниже. Коэффициент точности отливок по массе достигает 0,71, что обеспечивает возможность уменьшения припусков на обработку резанием.
3. Физико-химическое взаимодействие металла отливки и кокиля минимально, что способствует повышению качества поверхности отливки. Отливки в кокиль не имеют пригара. Шероховатость поверхности отливок определяется составами облицовок и красок, наносимых на поверхность рабочей полости формы, и соответствует Rz = 80-10 мкм, но может быть и меньше.
4. Кокиль практически газонепроницаем, но и газотворность его минимальна и определяется в основном составами огнеупорных покрытий, наносимых на поверхность рабочей полости. Однако газовые раковины в кокильных отливках — явление не редкое. Причины их появления различны, но в любом случае расположение отливки в форме, способ подвода расплава и вентиляционная система должны обеспечивать удаление воздуха и газов из кокиля при заливке.
mirznanii.com