Большая Энциклопедия Нефти и Газа. Хим никель покрытие. Никель покрытие
Свойства и область применения никелевых покрытий | Никелирование
Никель является металлом подгруппы железа, который получил в гальванотехнике наиболее широкое применение.
По сравнению с меднением, латунированием, серебрением и др. никелирование получило промышленное применение значительно позднее, но уже с конца XIX столетия этот процесс стал наиболее распространенным методом «облагораживания» поверхности металлических изделий. Лишь в двадцатые годы текущего столетия широкое применение получил другой процесс — хромирование, который, казалось, вытеснит никелирование. Однако оба эти процесса — никелирование и хромирование для защитно-декоративных целей применяются комбинированно, т. е. изделия сперва никелируют и затем покрывают тонким слоем хрома (десятые доли микрона). Роль никелевого покрытия при этом не умаляется, напротив к нему предъявляются повышенные требования.
Широкое распространение никелирования в гальванотехнике объясняется ценными физико-химическими, свойствами электролитически осажденного никеля. Хотя в ряде напряжений никель стоит выше водорода, вследствие сильно выраженной склонности к пассивированию, однако он оказывается достаточно стойким против атмосферного воздуха, щелочей и некоторых кислот. По отношению к железу никель имеет менее электроотрицательный потенциал, следовательно, основной металл — железо — защищается никелем от коррозии лишь при отсутствии пор в покрытии.
Никелевые покрытия, полученные из растворов простых солей, имеют весьма тонкую структуру, и так как в то же время электролитический никель прекрасно принимает полировку, то покрытия могут быть доведены до зеркального блеска. Это обстоятельство позволяет широко применять никелевые покрытия для декоративных целей. При введении в электролит блескообразователей удается получать в слоях достаточной толщины блестящие никелевые покрытия без полировки. Структура нормальных никелевых осадков чрезвычайно тонка, и ее трудно выявить даже при сильном увеличении.
Чаще всего при никелировании преследуют две цели: защиту основного металла от коррозии и декоративную отделку поверхности. Такие покрытия широко применяют для наружных частей автомобилей, велосипедов, различных аппаратов, приборов, хирургических инструментов, предметов домашнего обихода и т. д.
С электрохимической точки зрения никель может быть охарактеризован как представитель металлов группы железа. В сильнокислой среде осаждение этих металлов вообще невозможно — на катоде выделяется почти один водород. Мало того, даже в растворах, близких к нейтральным, изменение рН влияет на выход по току и свойства металлических осадков.
Явление отслаивания осадка, больше всего присущее никелю, также в сильной степени связано с кислотностью среды. Отсюда и вытекает первейшая забота о соблюдении надлежащей кислотности и регулировании ее при никелировании, так же как выбор надлежащей температуры для правильного ведения процесса.
Первые электролиты для никелирования готовили на основе двойной соли NiSO4(Nh5)2SO4·6h3O. Эти электролиты были впервые исследованы и разработаны профессором Гарвардского университета Исааком Адамсом в 1866 г. По сравнению с современными высокопроизводительными электролитами с высокой концентрацией никелевой соли электролиты с двойной солью допускают плотность тока, не превышающую 0,3—0,4 А/дм2. Растворимость двойной никелевой соли при комнатной температуре не превышает 60—90 г/л, в то время как семиводный сульфат никеля при комнатной температуре растворяется в количестве 270—300 г/л. Содержание металлического никеля в двойной соли 14,87%, а в простой (сернокислой) соли 20,9%.
Процесс никелирования весьма чувствителен к примесям в электролите и в анодах. Совершенно очевидно, что малорастворимую в воде соль легче освободить в процессе кристаллизации и промывки от вредных примесей, например сульфатов меди, железа, цинка и др., чем более растворимую простую соль. В значительной степени по этой причине электролиты на основе двойной соли имели доминирующее применение во второй половине XIX и в начале XX столетия.
Борная кислота, которая в настоящее время рассматривается как весьма существенный компонент для буферирования электролита никелирования и электролитического рафинирования никеля, была впервые предложена в конце XIX — начале XX в.
Хлориды были предложены для активирования никелевых анодов в начале XX столетия. К настоящему времени в патентной и журнальной литературе предложено большое разнообразие электролитов и режимов для никелирования, по-видимому, больше, чем по какому-либо другому процессу электроосаждения металлов. Однако без преувеличения можно сказать, что большая часть современных электролитов для никелирования представляет собой разновидность предложенного в 1913 г. профессором Висконзинского университета Уоттсом на основании детального исследования влияния отдельных компонентов и режима электролита. Несколько позднее в результате усовершенствования им было установлено, что в концентрированных по никелю электролитах, при повышенной температуре и интенсивном перемешивании (1000 об/мин) можно получать удовлетворительные в толстых слоях никелевые покрытия при плотности тока, превышающей 100 А/дм2 (для изделий простой формы). Эти электролиты состоят из трех основных компонентов: сульфата никеля, хлорида никеля и борной кислоты. Принципиально возможна замена хлорида никеля хлоридом натрия, но, по некоторым данным, такая замена несколько снижает допустимую катодную плотность тока (возможно из-за уменьшения общей концентрации никеля в электролите). Электролит Уоттса имеет следующий состав, г/л: 240 — 340 NiSO4 · 7h3O, 30—60 NiCl2 · 6h3O, 30 — 40 h4ВO3.
Из других электролитов, которые в последнее время все больше привлекают к себе внимание исследователей и находят промышленное применение, следует назвать фторборатные, позволяющие применять повышенную плотность тока и сульфаматные, обеспечивающие возможность получения никелевых покрытий с меньшими внутренними напряжениями.
В начале тридцатых годов текущего столетия, и в особенности после второй мировой войны, внимание исследователей было приковано к разработке таких блескообразователей, которые позволяют получать блестящие никелевые покрытия в слоях достаточной толщины не только на отполированной до блеска поверхности основного металла, но и на матовой поверхности.
Разряд ионов никеля, как и других металлов подгруппы железа, сопровождается значительной химической поляризацией и выделение этих металлов на катоде начинается при значениях потенциалов, которые намного отрицательнее соответствующих стандартных потенциалов.
Выяснению причин этой повышенной поляризации посвящено много исследований и было предложено несколько далеко не совпадающих объяснений. По одним данным, катодная поляризация при электроосаждении металлов группы железа резко выражена лишь в момент начала выделения их, при дальнейшем повышении плотности тока потенциалы меняются незначительно. С повышением температуры катодная поляризация (в момент начала выделения) резко снижается. Так, в момент начала выделения никеля при температуре 15° С катодная поляризация равна 0,33 В, а при 95° С 0,05 В; для железа катодная поляризация снижается с 0,22 В при 15° С до нуля при 70° С, а для кобальта с 0,25 В при 15° С до 0,05 В при 95° С.
Высокую катодную поляризацию в момент начала выделения металлов группы железа объясняли выделением этих металлов в метастабильной форме и необходимостью затраты дополнительной энергии для перехода их в устойчивое состояние. Такое объяснение не является общепризнанным, имеются и другие взгляды на причины большой катодной поляризации, при которой происходит выделение металлов группы железа, и связанную с поляризацией мелкокристаллическую структуру.
Другие последователи приписывали особую роль водородной пленке, образующейся в результате совместного разряда ионов водорода, затрудняющей процесс агрегации мелких кристаллов и приводящей к образованию мелкодисперсных осадков металлов группы железа, а также защелачиванию прикатодного слоя и связанным с этим выпадением коллоидных гидроокисей и основных солей, которые могут соосаждаться с металлами и затруднять рост кристаллов.
Некоторые исходили из того, что большая поляризация металлов группы железа связана с большой энергией активации при разряде сильно гидратированных ионов, расчеты других показали, что энергия дегидратации металлов группы железа примерно такая же, как энергия дегидратации таких двухвалентных ионов металлов как медь, цинк, кадмий, разряд ионов которых протекает с незначительной катодной поляризацией, примерно в 10 раз меньшей, чем при электроосаждении железа, кобальта, никеля. Повышенную поляризацию металлов группы железа объяснили и сейчас объясняют адсорбцией чужеродных частиц; поляризация заметно снижалась при непрерывной зачистке катодной поверхности.
Этим не исчерпывается обзор различных взглядов на причины повышенной поляризации при электроосаждении металлов группы железа. Можно, однако, принять, что за исключением области малых концентраций и высоких плотностей тока, кинетика этих процессов может быть описана уравнением теории замедленного разряда.
Вследствие большой катодной поляризации при сравнительно небольшом перенапряжении водорода процессы электроосаждения металлов группы железа чрезвычайно чувствительны к концентрации ионов водорода в электролите и к температуре. Допустимая катодная плотность тока тем выше, чем выше температура и концентрация ионов водорода (чем ниже водородный показатель).
Для электроосаждения металлов группы железа нет нужды прибегать к растворам комплексных солей — эти металлы вполне удовлетворительно кристаллизуются на катоде из растворов простых солей, чаще всего сернокислых или хлористых, более доступных и более экономичных, чем комплексные соли.
www.stroitelstvo-new.ru
Никелирование в домашних условиях своими руками: технология, советы
Никелирование, которое является достаточно распространенной технологической операцией, выполняют для того, чтобы нанести на поверхность металлического изделия тонкий слой никеля. Толщина такого слоя, величину которого можно регулировать, используя различные приемы, может варьироваться от 0,8 до 55 мкм.
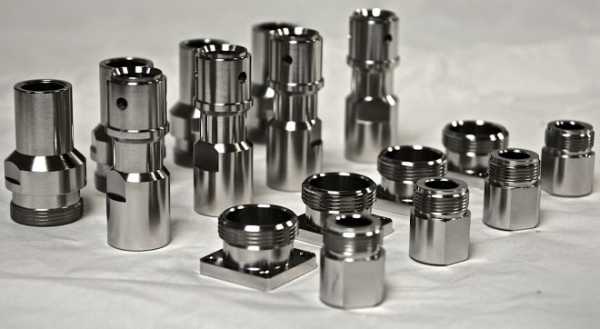
Никелирование используется в качестве защитно-декоративного покрытия, а также для получения подслоя при хромировании
Чаще всего никелированию подвергаются:
- изделия из металла, которые будут эксплуатироваться на открытом воздухе;
- кузовные детали мото- и автотранспортных средств, в том числе и те, для изготовления которых был использован алюминиевый сплав;
- оборудование и инструменты, применяемые в общей медицине и стоматологии;
- изделия из металла, которые длительное время эксплуатируются в воде;
- ограждающие конструкции, изготовленные из стали или алюминиевых сплавов;
- изделия из металла, подвергающиеся воздействию сильных химических веществ.
Существует несколько используемых как в производственных, так и в домашних условиях методов никелирования металлических изделий. Наибольший интерес в практическом плане представляют способы никелирования металлических деталей, не требующие применения сложного технологического оборудования и реализуемые в домашних условиях. К таким способам относится электролитическое и химическое никелирование.
Свойства гальванического и химического покрытия никелем
Электролитическое никелирование
Суть технологии электролитического никелирования металлических деталей, имеющей и другое название – «гальваническое никелирование», можно рассмотреть на примере того, как выполняется омеднение поверхности изделия из металла. Такую процедуру можно проводить как с применением электролитического раствора, так и без него.
Деталь, которая будет в дальнейшем обрабатываться в электролитическом растворе, подвергается тщательной обработке, для чего с ее поверхности при помощи наждачной бумаги удаляют оксидную пленку. Затем обрабатываемое изделие промывается в теплой воде и обрабатывается содовым раствором, после чего снова промывается водой.
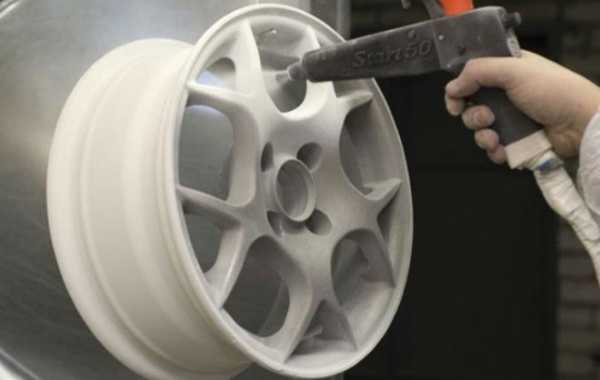
Крупные детали лучше очищать пескоструйным аппаратом
Сам процесс никелирования выполняется в стеклянной емкости, в которую заливается водный раствор (электролит). В составе такого раствора содержится 20% медного купороса и 2% серной кислоты. Обрабатываемую деталь, на поверхность которой необходимо нанести тонкий слой меди, в растворе электролита помещают между двумя анодами из меди. Чтобы запустить процесс омеднения, на медные аноды и обрабатываемую деталь необходимо подать электрический ток, величину которого рассчитывают, исходя из показателя 10–15 мА на один квадратный сантиметр площади детали. Тонкий слой меди на поверхности изделия появляется уже через полчаса его нахождения в растворе электролита, причем такой слой будет тем толще, чем дольше будет протекать процесс.
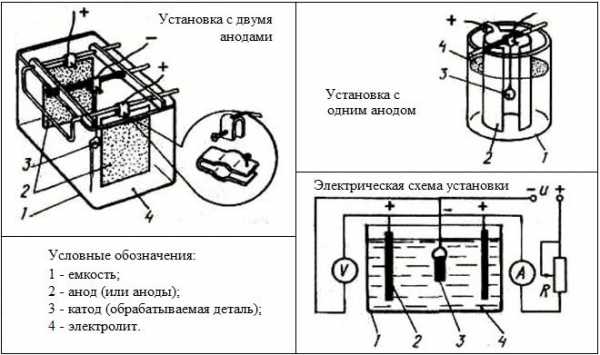
Схема установки для электролитического никелирования
Нанести медный слой на поверхность изделия можно и по другой технологии. Для этого необходимо изготовить кисточку из меди (можно использовать многожильный провод, предварительно сняв с него изоляционный слой). Такую кисточку, сделанную своими руками, надо зафиксировать на деревянной палочке, которая будет служить ручкой.
Изделие, поверхность которого предварительно зачищают и обезжиривают, помещают в емкость из диэлектрического материала и заливают электролитом, в качестве которого можно использовать насыщенный водный раствор медного купороса. Самодельную кисточку подключают к плюсовому контакту источника электрического тока, а обрабатываемую деталь – к его минусу. После этого приступают к процедуре омеднения. Заключается она в том, что кисточкой, которую предварительно обмакивают в электролит, проводят над поверхностью изделия, не прикасаясь к ней. Наносить покрытие, применяя такую методику, можно в несколько слоев, что позволит сформировать на поверхности изделия слой меди, на котором практически отсутствуют поры.
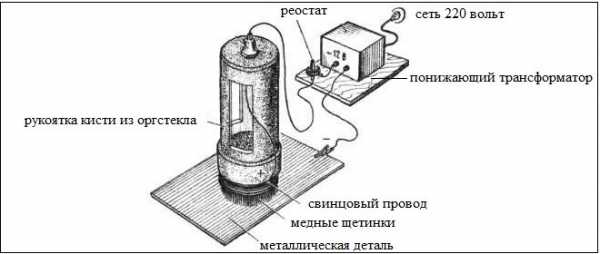
Схема простого приспособления для нанесения покрытия
Электролитическое никелирование выполняется по схожей технологии: при его осуществлении тоже используется раствор электролита. Так же, как и в случае с омеднением, обрабатываемое изделие располагают между двумя анодами, только в данном случае они изготовлены из никеля. Аноды, помещенные в раствор для никелирования, подключаются к плюсовому контакту источника тока, а изделие, подвешенное между ними на металлической проволоке, – к минусовому.
Для осуществления никелирования, в том числе и выполняемого своими руками, используются электролитические растворы двух основных типов:
- водный раствор, включающий в свой состав сернокислый никель, натрий и магний (14:5:3), 2% борной кислоты, 0,5% поваренной соли;
- раствор на основе нейтральной воды, содержащий в своем составе 30% сульфата никеля, 4% хлорида никеля, 3% борной кислоты.
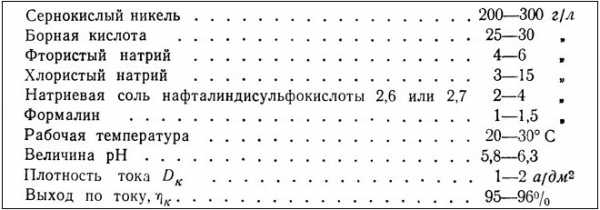
Электролит блестящего никелирования с добавкой органических блескообразователей (натриевых солей)
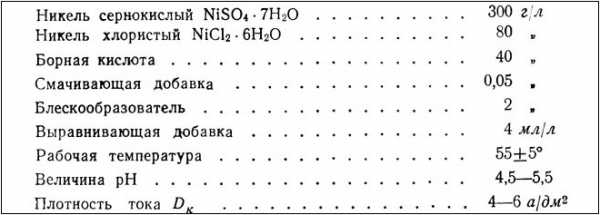
Выравнивающий электролит блестящего никелирования. Подходит для поверхностей с низким классом очистки
Чтобы приготовить электролитический раствор, сухую смесь из вышеуказанных элементов заливают одним литром нейтральной воды и тщательно перемешивают. Если в полученном растворе образовался осадок, от него избавляются. Только после этого раствор можно использовать для выполнения никелирования.
Обработка по данной технологии обычно длится полчаса, при этом используют источник тока с напряжением 5,8–6 В. Результатом является поверхность, покрытая неравномерным матовым цветом серого цвета. Чтобы она стала красивой и блестящей, необходимо ее зачистить и выполнить ее полировку. Следует иметь в виду, что такая технология не может быть использована для деталей, отличающихся высокой шероховатостью поверхности или имеющих узкие и глубокие отверстия. В таких случаях покрытие поверхности металлического изделия слоем никеля следует выполнять по химической технологии, которую также называют чернением.
Электролит для осаждения черного никеля
Суть технологической операции чернения заключается в том, что на поверхность изделия сначала наносится промежуточное покрытие, основой которого может быть цинк или никель, а на верхней части такого покрытия формируется слой черного никеля толщиной не более 2 мкм. Покрытие никелем, выполненное по технологии чернения, смотрится очень красиво и обеспечивает надежную защиту металла от негативного воздействия различных факторов внешней среды.
В отдельных случаях металлическое изделие одновременно подвергают сразу двум технологическим операциям, таким как никелирование и хромирование.Химическое никелирование
Процедуру химического никелирования изделий из металла выполняют по следующей схеме: обрабатываемую деталь на некоторое время погружают в кипящий раствор, в результате чего на ее поверхности оседают частички никеля. При применении такой технологии электрохимическое воздействие на металл, из которого изготовлена деталь, отсутствует.
Результатом использования такой технологии никелирования является формирование на поверхности обрабатываемой детали никелевого слоя, который прочно связан с основным металлом. Наибольшей эффективности такой способ никелирования позволяет добиться в тех случаях, когда с его помощью обрабатываются предметы, изготовленные из стальных сплавов.
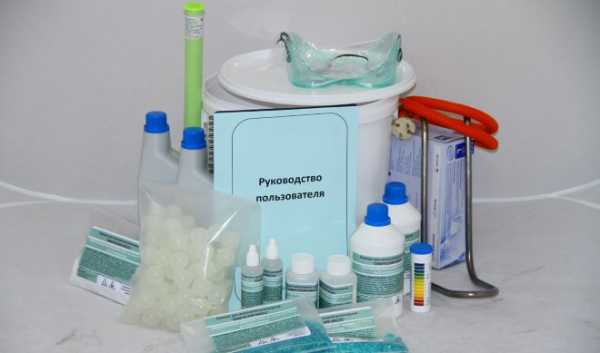
Комплект для нанесения никелированного покрытия химическим способом
Выполнять такое никелирование в домашних условиях или даже в условиях гаража нетрудно. При этом процедура никелирования проходит в несколько этапов.
- Сухие реактивы, из которых будет приготовлен электролитический раствор, смешиваются с водой в эмалированной посуде.
- Полученный раствор доводят до кипения, а затем в него добавляют гипофосфит натрия.
- Изделие, которое необходимо подвергнуть обработке, помещают в электролитический раствор, причем делают это так, чтобы оно не касалось боковых стенок и дна емкости. Фактически надо изготовить бытовой аппарат для никелирования, конструкция которого будет состоять из эмалированной емкости соответствующего объема, а также диэлектрического кронштейна, на котором будет фиксироваться обрабатываемая деталь.
- Продолжительность кипения электролитического раствора в зависимости от его химического состава может составлять от одного часа до трех.
- После завершения технологической операции уже никелированная деталь извлекается из раствора. Затем ее промывают в воде, в составе которой содержится гашеная известь. После тщательной промывки поверхность изделия подвергается полированию.
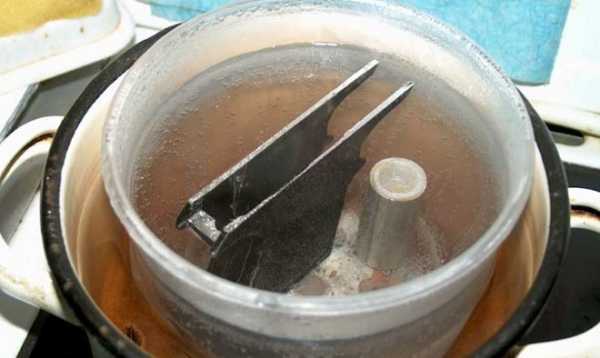
Процесс никелировки в домашних условиях
Электролитические растворы для выполнения никелирования, которому можно подвергать не только сталь, но также латунь, алюминий и другие металлы, обязательно содержат в своем химическом составе следующие элементы – хлористый или сернокислый никель, гипофосфит натрия различной кислотности, какую-либо из кислот.
Чтобы увеличить скорость никелирования изделий из металла, в состав для выполнения этой технологической операции добавляют свинец. Как правило, в одном литре электролитического раствора выполняют никелевое покрытие поверхности, площадь которой составляет 20 см2. В электролитических растворах с более высокой кислотностью проводят никелирование изделий из черных металлов, а в щелочных обрабатывают латунь, осуществляют никелирование алюминия или деталей из нержавеющей стали.
Некоторые нюансы технологии
Выполняя никелирование латуни, изделий из стали различных марок и других металлов, следует учитывать некоторые нюансы этой технологической операции.
- Пленка из никеля будет более устойчивой, если она нанесена на предварительно омедненную поверхность. Еще более устойчивой никелированная поверхность будет в том случае, если готовое изделие будет подвергнуто термической обработке, заключающейся в его выдержке при температуре, превышающей 450°.
- Если никелированию подвергаются детали из закаленных сталей, то нагревать и выдерживать их можно при температуре, не превышающей 250–300°, иначе они могут утратить свою твердость.
- При никелировании изделий, отличающихся большими размерами, возникает потребность в постоянном перемешивании и в регулярной фильтрации электролитического раствора. Такая сложность особенно характерна для процессов никелирования, выполняемых не в промышленных, а в домашних условиях.
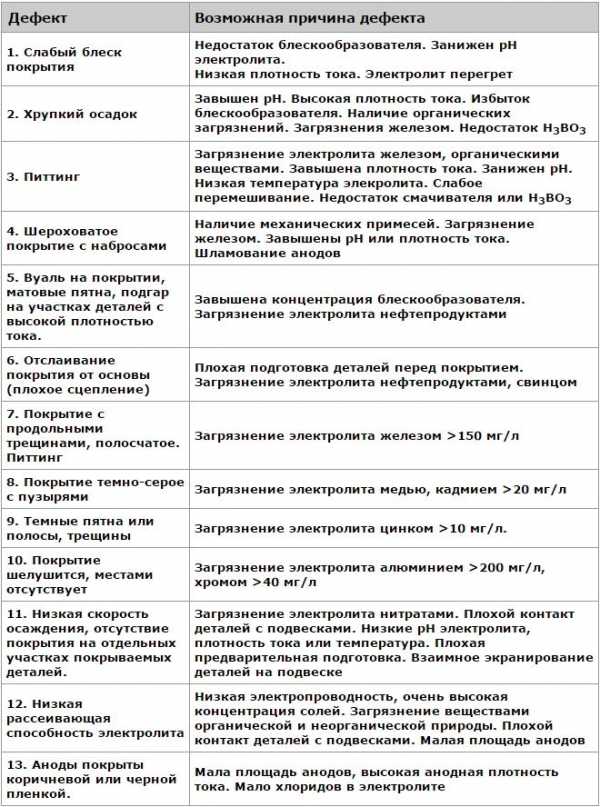
Причины дефектов никелирования
По сходной с никелированием технологии можно покрыть латунь, сталь и другие металлы слоем серебра. Покрытие из данного металла наносят, в частности, на рыболовные снасти и изделия другого назначения, чтобы предотвратить их потускнение.
Процедура нанесения слоя серебра на сталь, латунь и другие металлы отличается от традиционного никелирования не только температурой проведения и временем выдержки, но также тем, что для нее применяют электролитический раствор определенного состава. При этом выполняют данную операцию в растворе, температура которого составляет 90°.
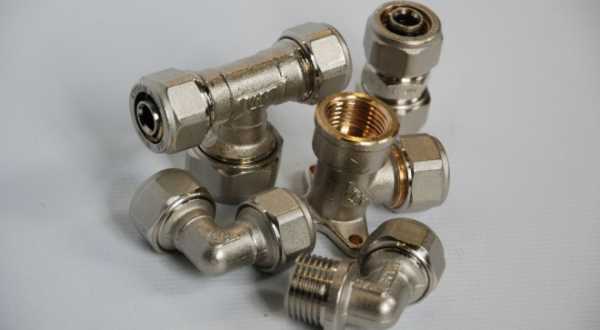
Никелированные латунные фитинги
Чтобы своими руками приготовить раствор, при помощи которого на сталь, латунь и другие металлы наносится слой серебра, достаточно выполнить ряд несложных действий.
- В 10%-й водный раствор соли добавляют аптечный ляпис.
- Осадок серебра, выпавший в растворе, промывают, смешивают с 2%-м гипосульфитом и фильтруют.
- Полученную смесь смешивают с меловой пылью и доводят до сметанообразного состояния.
Такой смесью, которая может храниться только в течение нескольких суток, натирается поверхность металлического изделия, пока на ней не сформируется тонкий слой серебра.
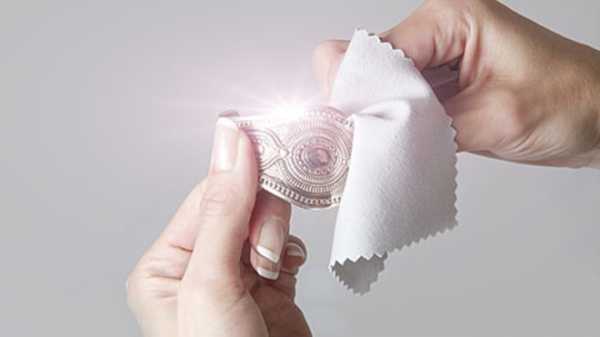
Полученное покрытие легко полируется до блеска
Можно приготовить порошок для серебрения, который не утратит своих характеристик в течение полугода. Для получения такого порошка необходимо смешать 15 граммов ляписа, 55 граммов лимонной кислоты и 30 граммов хлористого аммония. Все компоненты после перемешивания следует перетереть в пыль. Хранится полученный порошок в сухом виде.
Достаточно сложным является никелирование такого металла, как алюминий. Компоненты, входящие в состав электролитического раствора для никелирования изделий из данного металла, дорогостоящие, но даже их использование не дает гарантии того, что сформированный на изделии слой никеля не пойдет пузырями. Блестящее никелирование, если ему подвергают алюминий, может порвать готовое покрытие, поэтому в домашних условиях такую обработку выполняют в условиях слабой адгезии.
Оценка статьи:
Загрузка...Поделиться с друзьями:
met-all.org
Никелирование в домашних условиях | Строительный портал
Никель широко применяется в машиностроении и приборостроении, а также в разных отраслях. В пищевой промышленности никель заменяет оловянные покрытия, а в области оптики он распространился благодаря процедуре чёрного никелирования металла. Никелем покрывают детали, изготовленные из цветных металлов и стали, для повышения сопротивления изделий механическому износу и защиты от коррозии. Присутствие фосфора в никеле делает пленку по твердости близкой к пленке хрома!
Содержание:
- Процедура никелирования
- Виды никелирования
- Ванны никелирования
- Тонкости никелирования
- Снятие никелевого покрытия
Процедура никелирования
Никелирование представляет собой нанесение на поверхность детали никелевого покрытия, которое обычно имеет толщину от 1 до 50 мкм. Покрытия никелем бывают блестящими или матовыми черными, но не зависимо от этого, обеспечивают надежную защиту металлу в агрессивных средах (кислоты, щелочи) и в условиях повышенной температуры.
Перед процессом никелирования изделие должно быть подготовлено. Его обрабатывают наждачной бумагой для удаления оксидной пленки, протирают щеткой, промывают водой, обезжиривают в горячем содовом растворе и промывают еще раз. Никелевые покрытия способны с течением времени терять свой первичный блеск, поэтому зачастую покрывают слой никеля более устойчивым слоем хрома.
Никель, который нанесен непосредственно на сталь, является катодным покрытием и защищает материал исключительно механическим путем. Несплошность защитного покрытия способствует возникновению коррозионных пар, в которых растворимым электродом выступает именно сталь. В результате этого под покрытием образуется коррозия, разрушающая стальную подложку и провоцирующая отслаивание никелевого покрытия. Для предупреждения этого металл всегда нужно покрывать толстым слоем никеля.
Никелевые покрытия можно наносить на железо, медь, их сплавы, а также на вольфрам, титан и прочие металлы. Нельзя покрывать с помощью химического никелирования такие металлы, как свинец, кадмий, олово, свинец, сурьму и висмут. При никелировании стальных изделий принято наносить подслой меди.
Покрытия никелем используют в разных отраслях промышленности для специальных, защитно-декоративных целей, а также в качестве подслоя. Технологию никелирования используют для восстановления изношенных автозапчастей и деталей машин, покрытия химической аппаратуры, медицинского инструмента, измерительных инструментов, предметов домашнего обихода, деталей, что эксплуатируются с небольшими нагрузками в условии сухого трения или воздействия крепких щелочей.
Виды никелирования
Практике известны две разновидности никелирования - электролитическое и химическое. Последний способ является несколько дороже электролитического, однако способен обеспечить возможность создания равномерного по качеству и толщине покрытия на любых участках поверхности, если выполнено условие доступа к ним раствора.
Электролитическое никелирование
Электролитические покрытия характеризуются некоторой пористостью, зависящей от тщательности подготовки основы и толщины защитного покрытия. Для организации качественной защиты от коррозии требуется полное отсутствие пор, для этого принято предварительно производить меднение детали из металла или наносить многослойное покрытие, что является надежнее однослойного даже при равной толщине.
Для этого нужно приготовить электролит. Возьмите 30 грамм сульфата никеля, 3,5 грамма хлорида никеля и 3 грамма борной кислоты на 100 миллилитров воды, данный электролит налейте в емкость. Для никелирования стали или меди требуются никелевые аноды, которые следует опустить в электролит.
Между никелевыми электродами следует подвесить на проволочке деталь. Проволочки, идущие от никелевых пластинок, необходимо соединить вместе. Детали подключают к отрицательному полюсу источнику тока, а проволочки - к положительному. Затем нужно включить реостат в цепь для регулировки тока и миллиамперметр. Выберите источник постоянного тока, который имеет напряжение не больше 6 В.
Ток необходимо включать приблизительно на двадцать минут. Затем деталь нужно вынуть, промыть и просушить. Изделие покрыто матовым слоем никеля сероватого цвета. Чтобы защитное покрытие приобрело блеск, его необходимо отполировать. Однако при работе помните о существенных недостатках электролитического никелирования в домашних условиях — неравномерности осаждения на рельефной поверхности никеля и невозможности покрытия глубоких и узких отверстий, а также полостей.
Химическое никелирование
Помимо электролитического способа можно использовать еще один, весьма несложный способ для покрытия железа или полированной стали тонким, но прочным слоем никеля. Принято брать 10-процентный раствор хлористого цинка и постепенно добавлять к раствору сернокислого никеля до тех пор, пока жидкость не станет ярко-зеленой. После этого жидкость нужно нагреть до кипения, лучше для этого использовать фарфоровый сосуд.
При этом появляется характерная муть, однако на процесс никелирования деталей она никакого влияния не оказывает. Когда вы доведете жидкость до кипения, следует в неё опустить предмет, который подлежит никелированию. Предварительно очистите деталь и обезжирьте. Изделие должно кипеть в растворе близко часа, время от времени добавляйте дистиллированную воду по мере ее выпаривания.
Если вы заметите во время кипения, что жидкость поменяла цвет из ярко-зеленого на слабо-зеленый, то нужно добавить немного сернокислого никеля для получения первоначального окраса. По истечении указанного времени достаньте изделие из раствора, промойте в воде, в которой распущено немного мела, и тщательно просушите. Сталь или полированное железо, покрытое подобным способом никелирования, это защитное покрытие держит весьма прочно.
В основе процедуры химического никелирования находится реакция восстановления никеля из водного раствора его солей при помощи гипофосфита натрия и прочих химических реактивов. Растворы, которые применяются для химического никелирования, бывают кислыми с уровнем рН 4-6,5 и щелочными с показателем рН выше 6,5.
Кислые растворы целесообразно использовать для покрытия черных металлов, латуни и меди. Щелочные предназначены для нержавеющих сталей. Кислый раствор по сравнению с щелочным дает на полированной детали более гладкую поверхность. Еще одной немаловажной особенностью кислых растворов считается меньшая вероятность саморазряда при превышении порога рабочей температуры. Щелочные растворы гарантируют более надежное сцепление пленки никеля с основным металлом.
Все водные растворы для никелирования своими руками являются универсальными, то есть пригодными для всех металлов. Для химического никелирования берут дистиллированную воду, однако вы можете использовать и конденсат из бытового холодильника. Химические реактивы подойдут чистые – с обозначением на этикетке «Ч».
Последовательность изготовления раствора такова. Все химические реактивы, за исключением гипофосфита натрия, нужно растворить в воде, используя эмалированную посуду. Потом разогрейте раствор до рабочей температуры, растворите гипофосфит натрия и поместите детали в раствор. С помощью одного литра раствора можно отникелировать детали, которые имеют площадь их поверхности до 2 дм2.
Черные покрытия
Никелевые покрытия черного цвета применяются со специальной и декоративной целью. Их защитные свойства являются очень низкими, поэтому их принято наносить на подслой из обычного никеля, цинка или кадмия. Стальные изделия нужно предварительно оцинковать, а медь и латунь — никелировать.
Черное никелевое покрытие является твердым, но хрупким, особенно при значительной толщине. В практике останавливаются на значении толщины в 2 мкм. Никелевая ванна для нанесения подобных покрытий, как правило, содержит большое количество роданида и цинка. В покрытии присутствует близко половины никеля, а остальные 50% составляют сера, азот, цинк и углерод.
Ванны черного никелирования алюминия или стали принято готовить, растворяя в теплой воде все составляющие и фильтруя с помощью фильтровальной бумаги. Если при растворении борной кислоты возникают трудности, то ее отдельно растворяют в воде, что нагрета до 70 градусов по Цельсию. Получение глубокого черного цвета зависит от правильного выбора значения плотности тока.
Ванны никелирования
В мастерских широко применяется ванна, которая состоит из 3 основных компонентов: борной кислоты, сульфата и хлорида. Сульфат никеля является источником ионов никеля. Хлорид значительно влияет на работу анодов из никеля, его концентрация в ванне точно не нормируется. В безхлоридных ваннах совершается сильное пассивирование никеля, после чего содержание в ванне никеля уменьшается, а результатом является снижение выхода по току и падение качества покрытий.
Аноды в присутствии хлоридов растворяются в достаточном количестве для нормального протекания процесса никелирования меди или алюминия. Хлориды увеличивают проводимость ванны и её функционирование при загрязнениях цинком. Борная кислота помогает поддерживать рН на определенном уровне. Эффективность подобного действия зависит в большой степени от концентрации борной кислоты.
В качестве хлорида можно использовать хлорид натрия, цинка или магния. Повсеместно применяются сульфатные ванны Уоттса, которые содержат в качестве добавки электропроводные соли, которые повышают электропроводность ванн и улучшают внешний вид защитных покрытий. Наиболее применяем среди этих солей сульфат магния (близко 30 грамм на литр).
Сульфат никеля принято чаще всего вводить в концентрации порядка 250—350 грамм на литр. В последнее время наметились тенденции к ограничению сульфата никеля - меньше 200 г/л, что помогает заметно снизить потери раствора.
Концентрация борной кислоты составляет 25—40 грамм на литр. Ниже 25 г/л увеличиваются тенденции к быстрому защелачиванию ванны. А превышение допустимого уровня считается неблагоприятным из-за возможной кристаллизации борной кислоты и оседания кристаллов на стенках никелевой ванны и анодах.
Никелевая ванна работает в разном диапазоне температур. Однако технология никелирования в домашних условиях редко применяется при комнатной температуре. От покрытий, которые нанесены в холодных ваннах, часто отслаивается никель, поэтому ванну необходимо нагревать хотя бы до 30 градусов по Цельсию. Плотность тока выбирают экспериментально, чтобы не происходил прижог покрытий.
Натриевая ванна надежно работает в широком диапазоне рН. Раньше поддерживали рН на уровне 5,4—5,8, мотивируя меньшей агрессивностью и высшими кроющими способностями ванны. Однако высокие значения рН провоцируют значительный рост напряжений в никелевом покрытии. Поэтому в большинстве ванн рН составляет 3,5—4,5.
Тонкости никелирования
Сцепление пленки никеля с металлом является сравнительно низким. Данную проблему можно решить с помощью термической обработки пленок никеля. Процедура низкотемпературной диффузии состоит в нагреве отникелированных изделий до температуры 400 градусов по Цельсию и выдержке деталей на протяжении одного часа при этой температуре.
Но помните, что если детали, которые покрыты никелем, были закалены (рыболовные крючки, ножи и пружины), то при температуре 400 градусов они могут отпуститься, теряя твердость - их основное качество. Поэтому низкотемпературную диффузию в подобной ситуации проводят при температуре близко 270-300 градусов с выдержкой до 3 часов. Подобная термообработка способна повышать и твердость покрытия никелем.
Современные ванны никеля требуют специального оборудования для никелирования и перемешивания водного раствора для интенсификации процедуры никелирования и уменьшения риска питтинга – возникновения небольших углублений в покрытии. Перемешивание ванны за собой влечет необходимость создания непрерывной фильтрации для устранения загрязнений.
Перемешивание при помощи подвижной катодной штанги не является настолько эффективным, как использование для этой цели сжатого воздуха, и помимо всего прочего, требует наличия специального ингредиента, который исключает пенообразование.
Снятие никелевого покрытия
Никелевые покрытия на стали принято удалять в ваннах с разбавленной серной кислотой. Добавьте к 20 литрам холодной воды порциями 30 литров концентрированной серной кислоты при постоянном перемешивании. Контролируйте, чтобы температура не превышала 60 градусов по Цельсию. После охлаждения до комнатной температуры ванны ее плотность должна достигать 1,63.
С целью уменьшения риска затравливания материала, из которого выполнена подложка, добавляют в ванну глицерин в количестве 50 грамм на литр. Ванны принято изготовлять из винипласта. Изделия навешивают на средней штанге, которая соединена с плюсом источника тока. Штанги, на которых закреплены свинцовые листы, соединяются с минусом источника тока.
Следите, чтобы температура ванны не превышала 30 градусов, так как горячий раствор на подложку действует агрессивно. Плотность тока должна составлять 4 А/дм2, но допускается изменение напряжения в пределах 5—6 Вольт.
Добавьте через определенное время концентрированную серную кислоту, чтобы поддержать плотность, равной 1,63. Для предупреждения разбавления ванны погружайте изделия в ванну после проведения их предварительной сушки. Контроль процесса особого труда не представляет, потому что плотность тока в момент удаления никеля резко падает.
Таким образом, никелирование является самым популярным гальванотехническим процессом. Покрытие никеля отличается твердостью, большой коррозионной стойкостью, сносной ценой никелирования, хорошими отражательными способностями и удельным электрическим сопротивлением.
strport.ru
Химическое никелирование деталей – всё о процессе и особенностях + Видео
Никелирование химическое - это сложный процесс, позволяющий покрыть изделия из практически любого металла тонким защитным слоем никеля, повысить при этом коррозионную стойкость и придать поверхности блестящий вид и твердость.
1 Процесс химического никелирования деталей
Свойство никеля создавать на своей поверхности тонкую оксидную пленку, устойчивую к действию кислот и щелочей, позволяет использовать его для антикоррозионной защиты металлов.
Основной метод, применяющийся в промышленности - гальваническое никелирование, но оно требует наличия достаточно сложного оборудования и подразумевает работу с кислотами и щелочами, пары которых выделяются во время работы и могут сильно навредить здоровью человека. Для покрытия стали, алюминия, латуни, бронзы и других металлов может быть применен химический способ, так как он прост в использовании, и этот процесс можно проводить в домашних условиях.
На сегодняшний день существует два основных метода покрытия металлических деталей никелем: гальваническое и химическое. Первый метод требует наличия источника постоянного тока - электролитической ванны с электродами и большого количества химических реактивов. Второй способ намного проще. Для его проведения требуется наличие мерной посуды и эмалированной емкости для нагрева реактивов. Несмотря на всю кажущуюся простоту, это довольно сложный процесс, который требует большого внимания и соблюдения правил безопасности. По возможности проводите реакции в хорошо проветриваемом помещении. Идеальным вариантом будет оборудование рабочего места вытяжкой, ни в коем случае не соединенной с общедомовой вентиляцией. При работе пользуйтесь защитными очками, не оставляйте емкость с реактивами без присмотра.
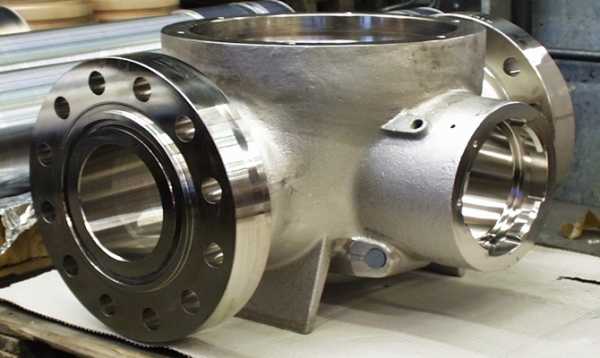
Покрытие металлических деталей никелем
Рекомендуем ознакомиться
Основные стадии для произведения химического никелирования следующие:
- Для того чтобы никель покрыл поверхность тонким и равномерным слоем, изделие предварительно шлифуют и полируют.
- Обезжиривание. Поскольку даже тончайшая пленка жира на поверхности обрабатываемого изделия может вызвать неравномерное распределение никеля по площади детали, последнюю обезжиривают в специальном растворе, состоящем из 25-35 г/л NaOH или KOH, 30-60 г кальцинированной соды и 5-10 г жидкого стекла.
- Деталь или изделие, которое необходимо покрыть никелем, промывают в воде, после чего на 0,5-1 минуту погружают в 5% раствор HCl. Данный шаг предпринимается для того, чтобы удалить с поверхности металла тонкий слой окислов, который будет значительно снижать адгезию между материалами. После протравки деталь снова промывают в воде, затем немедленно переносят в емкость с раствором для покрытия никелем.
Собственно никелирование производят при помощи кипячения металлического изделия в специальном растворе, который готовят следующим образом:
- берут воду (желательно - дистиллированную) из расчета 300 мл/дм2 площади поверхности детали, включая как внутреннюю, так и внешнюю;
- воду нагревают до 60°С, после чего растворяют в ней 30 г хлористого никеля (NiCl2) и 10 г уксуснокислого натрия (Ch4COONa) на 1 л воды;
- температуру поднимают до 80°С и добавляют 15 г гипосульфита натрия, затем в емкость с раствором погружают обрабатываемую деталь.
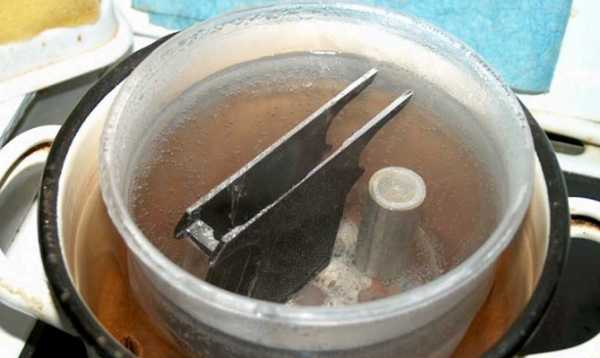
Кипячение металлического изделия
После погружения детали, раствор нагревают до 90-95°С и поддерживают температуру на таком уровне в течение всего процесса никелирования. Если вы увидели, что количество раствора сильно уменьшилось, можно добавить в него предварительно нагретую дистиллированную воду. Кипячение должно проходить не менее 1-2 часов. Иногда для получения многослойного покрытия, изделия из металла подвергают серии коротких (20-30 минут) кипячений, после каждого из которых деталь достают из раствора, промывают и высушивают. Это дает возможность получить слой никеля из 3-4 прослоев, которые суммарно имеют большую плотность и качество, чем одинарный слой той же мощности.
Особенность покрытия стальных изделий в том, что никель осаждается самопроизвольно вследствие каталитического воздействия железа. Для осаждения защитного слоя на цветных металлах используется другой состав.
2 Никелирование цветных металлов и сплавов
Химическое никелирование цветных металлов позволяет создавать защитную пленку на поверхности латуни, меди и бронзы. Для этого деталь сначала обезжиривают раствором, состав которого указан в первом способе, причем снимать оксидную пленку с металла не обязательно. Раствор для никелирования готовят следующим образом: в эмалированную емкость наливают 10% раствор хлористого цинка (ZnCl2), который более известен под названием «паяльная кислота». К нему понемногу добавляют сернокислый никель (NiSO4) до такой концентрации, при которой раствор окрашивается в зеленый цвет. Состав доводят до кипения, после чего погружают деталь в него на 1,5-2 часа. После того как реакция закончится, изделие достают из раствора и помещают в емкость с меловой водой (готовится способом добавления 50-70 г мела в порошке на 1 литр воды), а затем промывается.
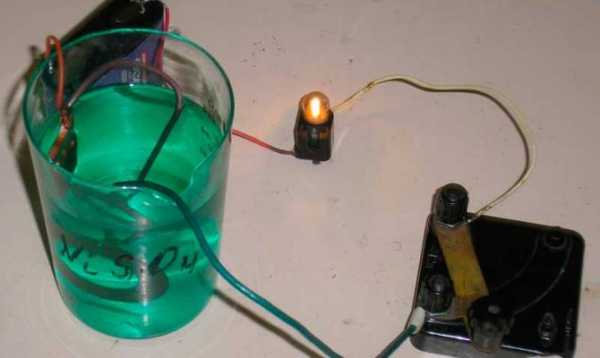
Раствор сернокислого никеля
Никелирование алюминия проходит по схожей технологии, но состав раствора немного другой:
- 20 г сернокислого никеля;
- 10 г натрия уксуснокислого;
- 25 г натрия фосфорноватистокислого;
- 3 мл тиомочевины концентрацией 1 г/л;
- 0,4 г фтористого натрия;
- 9 мл уксусной кислоты.
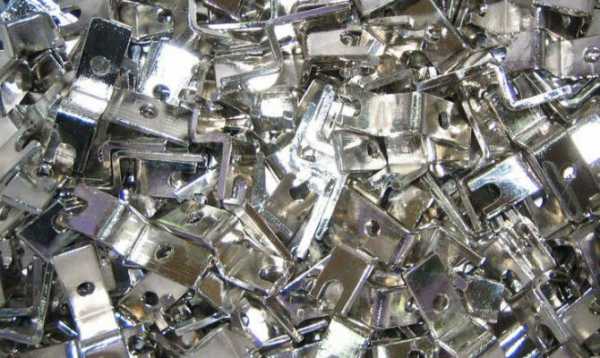
Обработка деталей из алюминия
Перед обработкой изделия из алюминия погружают в раствор каустической соды, концентрацией 10-15%, и нагретом до температуры 60-70°С. При этом происходит бурная реакция с выделением водорода, пузырьки которого очищают поверхность от окислов и загрязнения. В зависимости от степени загрязненности, детали выдерживают в очищающем растворе от 15-20 секунд до 1-2 минут, после чего промывают в проточной воде и погружают в никелирующий раствор.
3 Применение никелированных изделий
Вследствие никелирования значительно повышаются физико-механические и декоративные свойства металлических изделий. Никель имеет серебристо-белый цвет, на воздухе быстро покрывается незаметной человеческому глазу пленкой окислов, которые практически не меняют его внешнего вида, но при этом надежно защищают от дальнейшего окисления и реакций с агрессивной средой. Никелирование используется для защиты сталей, бронзы, латуни, алюминия, меди и других материалов.
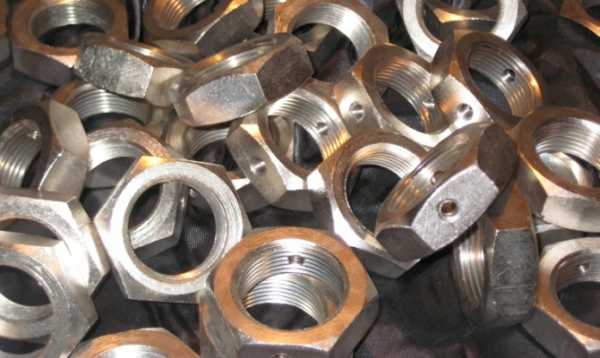
Защита металлических изделий от окисления
Является катодной защитой. Это значит, что при повреждении целостности покрытия, металл начинает реагировать с внешней средой. Для повышения механических свойств защитного слоя, нужно наносить его, точно придерживаясь технологии и последовательности действий. Никель, нанесенный на поверхность со следами загрязнения и ржавчины, с большим количеством неровностей, может начать вспучиваться и отслаиваться в процессе эксплуатации.
Изделия, покрытые никелем, почти ни в чем не уступают хромированным - имеют похожий блеск и твердость. При больших размерах емкостей для химической реакции никелем можно покрывать довольно большие детали, например, автомобильные диски.
4 Основные выводы по теме
Никелирование придает металлу красивый блестящий вид, высокую коррозионную стойкость и повышает твердость поверхности. Детали, покрытые никелем, можно использовать для украшения столбов ограды, если такую предусматривает проект участка. Красиво выглядят и имеют длительный срок эксплуатации различные метизы - крепежные болты, скобы, элементы мебельной фурнитуры. Они могут быть использованы в условиях повышенной влажности, температуры и нагрузки - в местах, где сталь быстро ржавеет и теряет свойства.
Химическое никелирование можно произвести собственноручно, в условиях хорошо проветриваемого гаража или мастерской.
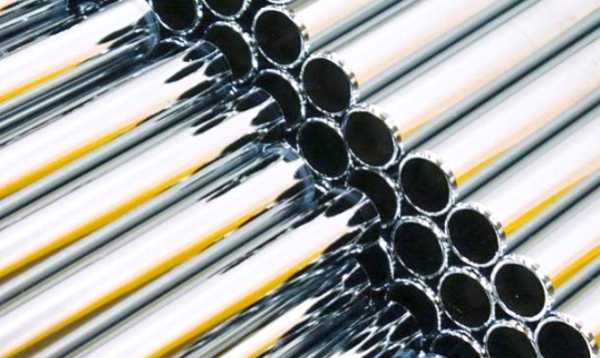
Красивый блестящий вид поверхности
Нежелательно делать описанные технологические операции на кухне, так как испарения любых химических веществ могут быть опасными для здоровья.
Покрытие никелем с помощью химических реактивов не требует высоких энергозатрат, в отличие от гальванического, но позволяет получить достаточно качественное, блестящее и твердое покрытие.
tutmet.ru
Свойства и применение никелевых покрытий
Никелирование — самый популярный гальванотехнический процесс. Привлекательный вид, высокая коррозионная стойкость и механические свойства говорят в пользу более широкого применения никеля с декоративно-защитными и функциональными целями.
Никель, нанесенный непосредственно на сталь, носит характер катодного покрытия и, следовательно, защищает только механическим путем. Несплошность покрытия способствует образованию коррозионных пар, в которых сталь является растворимым электродом. В результате этого возникает коррозия под покрытием, которая разрушает стальную подложку и приводит к отслаиванию никелевого покрытия. С целью предупреждения этого явления сталь необходимо покрывать плотным без пористости толстым слоем никеля.
Никелевые покрытия являются основой многослойных декоративно-защитных систем Ni—Сг и Сu-Ni—Сг. Применение ванн с блескообразователями значительно упрощает технологию нанесения многослойных покрытий.
Из-за высоких механических свойств никель применяют для восстановления изношенных деталей машин, гальванопластического изготовления инжекционных форм, и конструкционных элементов, которые трудно или даже невозможно изготовить обычными механическими методами. В химической промышленности толстым слоем никеля покрывают детали, подверженные воздействию крепких щелочей.
Ванны никелирования
Широко применяется в мастерских ванна, состоящая из трех основных компонентов: сульфата никеля, борной кислоты и хлорида, например, никеля.
Сульфат никеля — источник ионов никеля. Хлорид (никеля) существенно влияет на работу никелевых анодов. В безхлоридных ваннах происходит сильное пассивирование никеля, вследствие чего уменьшается содержание никеля в ванне, а результат — снижение выхода по току и ухудшение качества покрытий. В присутствии хлоридов аноды растворяются в степени, достаточной для нормального протекания никелирования. Хлориды повышают проводимость ванны и “работоспособность” ванны при загрязнениях цинком. Борная кислота облегчает поддержание рН на одном уровне. Эффективность этого действия в значительной степени зависит от концентрации борной кислоты (на практике преимущественно ~30 г/л).
Применения хлорида никеля не всеми признается желательным. Из-за высокой его цены, и часто, трудности приобретения. Однако необходимо учесть что, вводя в ванну хлорид никеля, мы вводим в ванну и ни-кель. В хлориде NiCl2•6Н2О теоретически содержится 24,69 % никеля и, следовательно, введя этот хлорид в количестве 40 г/л, мы увеличиваем содержание никеля в ванне примерно на 10 г/л, что уже имеет определенное значение.
Другим, часто дискутируемым вопросом является применение хлорида натрия как источника хлоридов. Известно, что многие гальванические мастерские успешно вводят в ванны блестящего никелирования NaСl.
Существует много причин плохой работы никелевых ванн, и утверждение, что причина — в использовании поваренной соли, мало обосновано. Даже хорошо известная среди гальванотехников английская фирма “Саnning” вводит в состав ванны для блестящего никелирования “NiSOL” хлорид натрия в количестве 28 г/л.Вместо хлорида натрия можно применять другой хлорид, например, как в ПНР, хлорид магния.В течение многих лет известна и повсеместно применяется сульфатная ванна Уоттса. Содержания отдельных компонентов — основы ванн Уоттса для нанесения матовых покрытий составляют, г/л: (200—350) NiS04•7Н20, (30—60) NiС12•6Н20, (25—40) h4ВО3.
Часто в состав ванны Уоттса вводят добавки так называемых электропроводных солей, повышающих электропроводность ванн и улучшающих внешний вид покрытия. Среди этих солей наиболее применяем сульфат магния (~30 г/л), в ваннах для массовой обработки мелких деталей его концентрация значительно выше.
Сульфат никеля чаще всего вводят в концентрации 250—350 г/л. В течение длительного времени считали целесообразной верхнюю границу концентрации, что позволяло проводить процесс при больших плотностях тока без опасения прижога покрытия на ребрах и на выступающих участках. В последнее время наметилась тенденция к ограничению сульфата никеля менее 200 г/л, чем заметно снижаются потери раствора.
Концентрация хлоридов в никелевой ванне точно не нормирована. В так называемых хлоридных ваннах концентрация хлорида никеля превышает 200 г/л и, следовательно, нет необходимости в добавке сульфата никеля. В условиях мастерской это не оправдывается, даже исходя из цены хлорида никеля.
Концентрация борной кислоты достигает 25—40 г/л. Ниже 25 г/л увеличивается тенденция к быстрому защелачиванию никелевой ванны. Однако превышение уровня в 40 г/л может оказаться неблагоприятным благодаря возможности кристаллизации борной кислоты в форме кристаллов, оседающих на стенках ванны и анодах. Особенно легко протекает это явление в неблагоприятных или слабо обогреваемых ваннах.
Сульфатная ванна работает в широком диапазоне температур, плотности тока и рН. При комнатной температуре никелирование применяется редко. Для покрытий, нанесенных в холодных ваннах, часто происходит при декоративном хромировании отслаивание никеля вместе с хромом. Поэтому следует нагревать ванну по крайней мере до 30 °С.
Ванна с блекообразователями работает при 50—60 °С. Плотность тока необходимо выбирать экспериментально с тем, чтобы не происходило прижога покрытий.
Сульфатная ванна работает надежно в широком диапазоне рН. Ранее в ваннах поддерживалась, как правило, величина рН = 5,4—5,8, что мотивировалось меньшей агрессивностью и лучшей кроющей способностью ванны. Однако столь высокое значение рН приводит к значительному росту напряжений в никелевых покрытиях. Поэтому в большинстве применяемых в промышленности ванн рН = 3,5—4,5.
Современные ванны требуют перемешивания, что необходимо с точки зрения интенсификации процесса никелирования и уменьшения опасности питтинга. Перемешивание ванны тянет за собой необходимость непрерывной фильтрации с целью устранения механических загрязнений.
Перемешивание с помощью подвижной катодной штанги не так эффективно, как перемешивание сжатым воздухом, и кроме того, оно требует специального ингридиента, исключающего пенообразование. Соответственно очищенный воздух служит в настоящее время в гальванических мастерских ПНР для перемешивания всех никелевых ванн, оборудованных устройствами для блестящего никелирования, изготавливаемыми в Институте точной механики.
Общая характеристика ванн блестящего никелирования.
Традиционные ванны для нанесения матовых покрытий применяются в настоящее время неограниченно. Их используют, в частности, для предварительного никелирования стальных изделий перед кислым меднением, полагая, что на матовом никеле матовое покрытие, осажденное в кислой ванне, имеет лучшую адгезию, чем на блестящем никеле. Это допущение иногда обосновано, так как в ваннах с блескообразователями накапливаются продукты распада органических добавок, приводя к пассивированию никелевых покрытий преимущественно в гальванических мастерских, работники которых пренебрегают правилами сохранения никелевых ванн, длительно эксплуатируемых без регенерации.
Однако, существует ситуация, заставляющая отказаться от никелирования в ваннах с блескообразующими добавками, по той причине, что блестящие покрытия недостаточно пластичны и разрушаются при изгибе никелированных предметов. Перед принятием решения об использовании блестящего никелирования в серийном производстве сначала необходимо проверить пригодностьэтого процесса на образцах.
Расход никелевых анодов.
Практики, занимающиеся никелированием ежедневно, знают, что расход никеля связан, в основном, с расходом никелевых анодов, обусловливающим также потребность в частом пополнении анодов; вместе с тем ванна работает целыми месяцами без надобности в добавке сульфата никеля.
Желая сэкономить на никеле, некоторые работники мастерских идут по линии наименьшего сопротивления и просто наносят тонкое покрытие, ухудшая тем самым качество изделия. Зависимость массы осажденного никеля от толщины покрытия показана в табл. 1.
ТАБЛИЦА 1
ВРЕМЯ, НЕОБХОДИМОЕ ДЛЯ ПОЛУЧЕНИЯ НИКЕЛЕВОГО ПОКРЫТИЯ ЗАДАННОЙ ТОЛЩИНЫ, S, И МАССА ОСАЖДЕННОГО НИКЕЛЯ, mNi, В ЗАВИСИМОСТИ ОТ ПЛОТНОСТИ ТОКА. ВЫХОД ПО ТОКУ НА КАТОДЕ 92,5 %
s, мкм
| mNi, г/дм2
| t, мин, при J, А/дм2 | ||||
1 | 2 | 3 | 4 | 5 | ||
2 | 0,181 | 9,3 | 4,7 | 3,1 | 2,3 | 1,9 |
5 | 0,453 | 26,5 | 13,2 | 8,9 | 6,6 | 5,1 |
7 | 0,680 | 39,7 | 19,8 | 13,3 | 9,9 | 7,9 |
10 | 0,890 | 52,8 | 26,4 | 17,6 | 13,1 | 10,6 |
15 | 1,330 | 79,5 | 39,7 | 26,5 | 19,8 | 15,8 |
20 | 1,780 | 105,8 | 52,8 | 35,3 | 26,4 | 21,2 |
25 | 2,230 | 130 | 66,1 | 43,1 | 32,9 | 26,4 |
30 | 2,670 | 155 | 77,5 | 51,6 | 38,75 | 31,0 |
40 | 3,560 | 205 | 102,5 | 68,3 | 51,25 | 41,0 |
50 | 4,500 | 262 | 131,0 | 87,0 | 65,5 | 52,4 |
Так, при толщине никелевого покрытия 10 мкм, часто используемого в качестве подслоя под декоративный хром для легких условий эксплуатации, на 1 дм2 поверхности теоретически осаждается 0,89 г никеля, но на практике его будет больше. Даже если мы примем расход никеля 2 г/дм2 и допустим, что 1 кг никеля стоит 1000 зл, то окажется, что стоимость требуемого никеля — 2 зл. Следовательно уменьшение толщины покрытия не дает большой экономии и может причинить ущерб авторитету фирмы.
Приготовление ванн никелирования.
Для приготовления ванн никелирования рекомендуется применять деминерализованную воду или в крайнем случае водопроводную. Грунтовую воду применять не следует. Рабочую и запасную ванны из стального листа футеруют изнутри твердой резиной или поливинилхлоридом. Обе ванны тщательно промывают и заполняют водой, добавляя серную кислоту ~5 г/л.
На следующий день ванны тщательно ополаскиваются и запасная ванна на половину объема наполняется водой. Воду нагревают до 60 °С и при постоянном перемешивании растворяют сначала борную кислоту, затем сульфат и хлорид никеля.
Так как обычно для приготовления ванны применяют технические химикаты, загрязненные посторонними металлами и органическими соединениями, то необходима предварительная очистка ванны. С этой целью увеличивают рН ванны до 5,0, вводя свежеосажденный карбонат никеля, полученный из сульфата никеля.
В отдельном сосуде, заполненном до половины теплой водой, растворяют сульфат никеля и заливают его водным раствором карбоната натрия до полного исчезновения зеленого осадка карбоната никеля. Осторожно сливают воду, а оставшийся осадок добавляют в ванну малыми порциями при постоянном перемешивании до pН = 5,0. Находящийся в продаже основной карбонат никеля не так хорош, как свежеприготовленный, так как он растворяется хуже.
Некоторые упрощают процесс повышения рН, вместо карбоната никеля добавляя малыми порциями в ванну 20%-ный NаОН. В течение часа раствор необходимо интенсивно перемешивать вплоть до полного растворения зеленой взвеси карбоната никеля.
После увеличения рН до 5,0 доливают малыми порциями водный раствор перманганата калия при постоянном перемешивании, вплоть до устойчивого появления бледно-розового цвета. Затем добавляют активированный уголь “Сагbороl S-ехtга” (1 г/л) и перемешивают 2 ч. Ванну оставляют в покое до следующего дня. В таком состоянии ванна должна иметь естественный цвет сульфата никеля, если же она не имеет этого цвета, то добавляют серную кислоту до рН = 3,8—4,0; на катодную штангу до исчезновения фиолетового цвета.
Дальнейшая очистка состоит в проработке ванн при малой плотности тока. Предварительно очищенный в запасной ванне раствор перекачивают в рабочую ванну, доводят деминерализованной водой до заданного уровня, добавляют серную кислоту до рН = 3,8—4,0; на катодную штангу подвешивают максимально возможное количество волнистых стальных пластинок и включают ток плотностью сначала ~0,5 А/дм2, а после нескольких десятков минут его уменьшают до 0,2—0,3 А/дм2. Электролиз длится 6 ч при постоянном перемешивании и температуре ~ 60 °С. По доведении рН до нормы очищенная ванна готова к эксплуатации. В ней никелируют пробные загрузки с целью выбора оптимальных условий обработки. При блестящем никелировании добавляют соответствующие вещества.
Эксплуатация и регенерация никелевых ванн. Стабилизация ванн для никелирования состоит в поддержании заданных концентраций отдельных составляющих и регуляторном устранении загрязнений.
Легче всего регулировать состав, исходя из химического анализа, однако опытный гальваник решает эти проблемы самостоятельно.
Особое внимание следует обратить на контроль и корректирование рН — ежедневную обязанность персонала, отвечающего за надежную работу никелевой ванны. Заметим, что это не очень сложно, так как ванна постепенно защелачивается, и, следовательно, возникает необходимость добавки чистой серной кислоты. Готовят раствор, содержащий 25 % (объемн.) концентрированной кислоты и 75 % (объемн.) дистиллированной воды, и добавляют его малыми порциями в ванну при постоянном перемешивании. Для контроля рН достаточно иметь индикаторную бумагу ограниченного набора, например, трех — пяти диапазонов производства ПНР.
Цветовая шкала на этой бумаге не так выразительна, как на бумажках Мерка, но после определенного времени обслуживающий персонал приобретет опыт и будет делать отсчет значений рН с достаточной точностью. Несоблюдение необходимой величины рН повлечет за собой заметное ухудшение качества покрытий.
При очень большом значении рН, т. е. при недостаточной кислотности, покрытия становятся хрупкими и склонными к шелушению, а также приобретают желтый оттенок; легко также возникает прижог покрытия в местах больших плотностей тока. При рН менее 4 ослабляется блеск покрытия.Никелевая ванна легко загрязняется металлическими примесями, особенно при обработке латунных и цинковых изделий: наиболее часто — медью, цинком, железом и свинцом. Медь придает никелевому покрытию темный цвет.
Малая концентрация цинка приводит к появлению на никелевом покрытии черных точек, большая концентрация цинка проявляется в виде почернения покрытий в местах малых плотностей тока; сильное загрязнение цинком может привести к распространению черных полос по всей поверхности.
Загрязнение железом приводит к росту внутренних напряжений в покрытии, следствием чего является хрупкость никеля. Коллоидальная взвесь соединений железа, появляющаяся в никелевой ванне, может служить причиной появления сильного питтинга.
Загрязнение свинцом проявляется в виде бурого или чернобурого слоя в местах малой плотности тока. Свинец может попасть в ванну из свинцовых труб, применяемых для нагрева, или с погружаемых нагревателей, помещаемых в свинцовый кожух. Это исключительно вредно для ванн с блескообразователями.
Примесные металлы удаляют электролитически при малой плотности тока методом, описанным при составлении ванны. Время очистки зависит от степени загрязнения ванны и может длиться от нескольких часов до нескольких их десятков. Через определенное время стальные листы следует вынуть из ванны, очистить стальной щеткой и снова поместить в ванну. Не следует оставлять обесточенные листы в ванне, так как это приводит, по крайней мере, к частичному растворению в ней загрязнений.
Современные ванны для никелирования перемешиваются воздухом и, следовательно, механические загрязнения, оседающие на дне, распределяются по всему объему ванны и часть из них попадает в покрытие, придавая ему шероховатость. Таким образом возникает необходимость непрерывной фильтрации ванны, хотя в большинстве мастерских избегают этого, ограничиваясь периодической фильтрацией, и не жалуются на шероховатость покрытий. Это свидетельствует об умении поддержания ванны в надлежащей чистоте, прежде всего, о невозможности попадания анодного шлама в ванну вследствие хорошей задержки его анодным мешком.
По поводу фильтрации ванн блестящего никелирования с помощью активированного угля существуют разные мнения. Теоретически при каждой фильтрации ванны следовало бы применять уголь с целью удаления вредных органических загрязнений, к которым относят, между прочим, продукты разложения блескообразующих добавок. В действительности уголь поглощает также и некоторые необходимые для нормальной работы органические добавки, в результате чего увеличивается расход довольно дорогих препаратов, например, таких как “DF-Ьis”.
Несмотря на такую неблагоприятную ситуацию для потребителя, необходимо здесь выбирать золотую середину, заключающуюся в том, что фильтрация через свежий активированный уголь происходит раз в неделю и, наконец, частоту замены угля можно установить, исходя из собственных наблюдений. Полный отказ от угля является технической ошибкой, так как с течением времени ванна загрязняется органическими соединениями настолько сильно, что покрытия становятся хрупкими и пассивированными, что затрудняет их декоративное хромирование.
Необходимо, однако, обратить внимание на сорт активированного угля. В ПНР применяют уголь Саrbороl S-ехtга в пылеобразном виде. Случайные сорта могут принести больше вреда, чем пользы, так как они загрязнены примесными металлами, например, цинком.
Несмотря на большую заботу о никелевой ванне, она так может так загрязниться органическими веществами, что возникает необходимость капитальной регенерации с использованием перманганата калия.
Содержимое ванны, нагретой до 60 °С, перекачивают в запасную ванну и доводят рН с помощью карбоната никеля до 5,5—5,8. Растворенный в воде перманганат добавляют малыми порциями до получения бледнорозового цвета. Во время введения перманганата обязательно тщательное перемешивание.
На каждый литр таким образом обработанной ванны добавляют 3 г активированного угля и сильно перемешивают в течение нескольких часов. Затем оставляют ванну на 10—12 ч, после чего прозрачный раствор отфильтровывают осторожно в рабочую ванну, не трогая осадок на дне. Если розовый цвет остается и далее, то добавляют пергидроль, разбавленный в дистиллированной воде в соотношении 1:5 до получения нормального зеленого цвета ванны. С целью предупреждения избытка пергидроля его добавляют небольшими порциями. После корректировки рН никелируют пробные изделия, помня, что блеск будет хуже, так как часть блескообразующего раствора была уничтожена и лишь после дополнения блескообразователей будет получен желаемый декоративный вид.
Железо, загрязняющее никелевую ванну, устраняют, в основном, во время описанной выше обработки при малой плотности тока, однако, для более полного удаления этого металла поступают следующим образом:
электролит переливают в запасную ванну, нагревают до температуры 60 С и подщелачивают до рН = 6 карбонатом никеля или едким натром, причем необходимо перемешивание. Затем добавляют пергидроль в количестве 1 см3/л, перемешивают 3 ч и оставляют в покое до следующего дня. Светлый раствор отфильтровывают осторожно в рабочую ванну, наблюдая, чтобы, осадок на дне ванны не попал в чистую ванну.
После доведения рН до нормы проводят пробное никелирование и дополняют блескообразующие добавки до получения желаемого блеска.
Правильная дозировка блескообразующих веществ является основным условием успеха при блестящем никелировании. Производители блескообразователей дают приблизительный расход вещества в зависимости от прохождения количества электричества в ампер-часах, но лишь в немногих мастерских есть электросчетчики, а регистрация нагружения ванны в виде подробных записей — не столь простое дело, как кажется.
При длительной эксплуатации ванны возникают разные ситуации, которые сопровождаются значительной потерей блескообразователей, например, при регенерации ванн, описанных выше. Это происходит за пределами электричества.
Содержание блескообразователя в ванне можно определить аналитически, однако для этого надо иметь соответствующее оборудование и основательное знание лабораторной методики. Можно пользоваться услугами специальных лабораторий, однако это не всегда возможно. Следовательно, остается собственная инициатива гальваника, обслуживающего ванну, или другого более грамотного человека.
Если получим полублестящее покрытие, то это значит, что в ванне очень мало блескообразователя, На 100 л ванны можно добавить 25 см3 добавки “DF-bis”. Если это не приведет к улучшению блеска, то причина лежит в самой ванне. Следует определить рН и температуру ванны и, если после корректировки этих параметров и дальше нет улучшения, то необходимо приступить к очистке ванны с помощью активированного угля и электролиза при малой плотности тока, что подробно описано при рассмотрении ванн.
Очень трудная ситуация возникает в случае избыточного введения блескообразователей. В этом случае покрытия становятся хрупкими в местах очень малой плотности тока; например, в местах контакта изделия с подвесками образуются видимые черные пятна и может быть даже окончательный брак покрытий. Следовательно, необходимо избавиться от избытка блескообразователя, прорабатывая ванну в нормальных условиях, повесив на катодную штангу отходы стального листа, соответственно обезжирив их и протравив.
Одним из часто встречающихся дефектов никелевых покрытий является пористость — так называемый питтинг — небольшие углубления в покрытии, напоминающие наколы, возникающие при никелировании в результате прилипания пузырьков водорода к поверхности катода. Это объясняется большим поверхностным натяжением, в особенности в ваннах для никелирования. В месте расположения пузырька покрытие не образуется, возникает кратер.
Кроме водорода на поверхности катода могут оседать и пузырьки воздуха, содержащегося в ванне. Не работающая ванна охлаждается и поглощает определенное количество воздуха. При нагревании ванны воздух выделяется в виде пузырьков, часть из которых оседает на поверхности катода, приводя к питтингу. Перед началом никелирования ванну следует нагреть до температуры на несколько градусов выше обычно применяемой, выключить нагрев и подождать, пока температура не снизится до нормы. Кроме того, воздух может попасть в ванну вследствие неплотности фильтрующего насоса. Неплотность насоса, безусловно следует устранить.
Большое влияние на образование питтинга имеет также и состояние подложки, пористость которой, неметаллические включения и всякого рода загрязнения поверхности способствуют образованию питтингов. Таким же образом влияют загрязнения ванны взвесью или продуктами распада органических веществ.
С целью предупреждения образования питтинга в ванну добавляют окисляющие или смачивающие вещества. К первым относится пероксид водорода, добавляемый в обычные ванны в виде пергидроля в количествах 0,2—0,5 см3/л.
В ванны с блескообразователями пергидроль не добавляют, так как он действует разрушающе на органические вещества. В таких случаях добавляют смачивающие вещества, например, лаурилсульфат натрия, в количестве 0,1—0,2 г/л.
Пероксид водорода и смачивающее вещество не являются радикальными противопиттинговыми средствами. Устранить газовые пузырьки помогает механическое встряхивание изделий на подвесках в ванне. Подвижная катодная штанга, а еще лучше перемешивание ванны сжатым воздухом, намного облегчает борьбу с питтингом. При устойчивом питтинге следует применять очистку ванны активированным углем.
Никелевые аноды
Никелевые аноды изготовляют в соответствии со стандартом PN-82/Н-92914 размерами 25х25х(3-8) мм и листов шириной 100—300 мм, длиной 600—1000 мм и толщиной 6—12 мм.
Химический состав анодов должен соответствовать стандарту PN-79/Н-8181, а листов — стандарту PN-79/82180. Аноды в виде листов имеют марки № 2, № 3 и № 6А. Для блестящего никелирования применяют аноды № 2.Пример обозначения анодов при размещении заказа: анод никелевый № 2 8Х300Х600 в соответствии со стандартом РН-82/Н-92914. Кубики размещаются в титановых корзинах.
Снятие никелевых покрытий
Никелевые покрытия на стали и сплавах меди, как правило, удаляются в ванне с разбавленной серной кислотой. К 20 л холодной воды добавляют при постоянном перемешивании порциями 30л концентрированной серной кислоты, наблюдая, чтобы температура не была выше 60 °С. После охлаждения ванны до комнатной температуры ее плотность должна быть ~ 1,63.
С целью снижения опасности затравливания материала подложки в ванну добавляют глицерин 50 г/л. Ванны изготовляют из винипласта. Изделия навешиваются на средней штанге, соединенной с положительным полюсом источника тока. Боковые штанги, на которых навешаны свинцовые листы, соединяют с отрицательным полюсом источника тока.Температура ванны не должна превышать 30 °С, так как горячий раствор действует агрессивно на подложку. Плотность тока достигает 4 А/дм2, но можно изменять напряжение в пределах 5—6 В.Через определенное время следует добавлять концентрированную серную кислоту для поддержания плотности, равной 1,63. С целью предупреждения разбавления ванны необходимо изделия в ванну погружать после их предварительной сушки.В случае латунных изделий контроль процесса не представляет труда, так как в момент полного удаления никеля плотность тока резко падает.
Черные никелевые покрытия
Черные никелевые покрытия применяются с декоративной и специальной целью. Их защитные свойства очень низки, поэтому их наносят на подслой из цинка, кадмия или обычного никеля. Стальные изделия предварительно оцинковывают, а латунь и медь — никелируют.
Черное никелевое покрытие твердо и хрупко особенно при большой толщине. В практике удовлетворяются обычно толщиной в 2 мкм. Ванна для нанесения таких покрытий содержит значительное количество цинка и роданида. В покрытии содержится ~50 % никеля, а остальное составляют цинк, сера, азот и углерод.Ниже приведены типичные составы ванн черного никелирования, г/л:
Ванна | 1 | 2 | 3 |
NiSO4•7h3O | 75 | — | 144 |
NiSo4•(Nh5)2SO4•6h3O | 45 | — | — |
ZnSO4•7h3O | 38 | — | — |
NaSCN•2h3O | 15 | 15 | — |
NiCl2•6h3O | — | 75 | — |
Nh5Cl | — | 30 | — |
ZnCl2 | — | 30 | — |
(Nh5)6•Mo7O24•4h3O | — | — | 30 |
h4BO3 | — | — | 23 |
Ванна 1 работает при комнатной или слегка повышенной температуре, J = 0,1—0,5 А/дм2, рН = 5,6—5,9. Ванна 2 хлоридная и, следовательно, агрессивная более сульфатной. Она работает при комнатной температуре, рН = 5,0 и J = 0,2 А/дм2. Ванна 3 содержит молибдаты и, следовательно, дороже первой и второй ванн. Ее преимуществом является большая кроющая способность и стабильность, так как она содержит борную кислоту. Недостатком является более высокая рабочая температура, как правило, выше 50 °С. Плотность тока составляет 0,2—0,5 А/дм2, рН = 4,3—4,7.
Ванны черного никелирования готовят, растворяя все составляющие в теплой воде и фильтруя через фильтровальную бумагу. Если возникают трудности растворения борной кислоты в ванне 3, то ее растворяют отдельно в воде, нагретой до 70 °С.
Стабильность ванн заключается в основном в контроле и регулировании рН посредством h3SO4 или NaОН. Получение глубоко черного цвета зависит в основном от правильного выбора плотности тока. Никелированные изделия смазывают горячим маслом.
Химическое никелирование
Этот процесс был в свое время одним из главных в технической специальной литературе, и казалось, что он создает сильную конкуренцию для традиционного электролитического никелирования. В настоящее время его оценивают более спокойно и применяют, когда для этого есть техническое и материальное обеспечение.
Основным преимуществом никелевых покрытий, нанесенных химическим путем, является однородная толщина независимо от формы изделия. Это характерно для всех процессов осаждения металла без применения тока.
Особенностью химического никелирования является непрерывное осаждение слоя, что создает возможность образования покрытий любой толщины.
Ванны для химического никелирования состоят из соли никеля, гипофосфита натрия и добавок. Основой являются соли никеля и гипофосфит натрия.
Существуют две разновидности ванн для химического никелирования — кислая и щелочная. В качестве солей никеля, в основном, применяют сульфат или хлорид никеля относительно небольшой (~5 г/л) концентрации. Содержание гипофосфита достигает 10—30 г/л. Добавки вводятся в виде комплексообразующих соединений, ускоряющих осаждение никеля, и стабилизаторов, препятствующих разложению электролита.
В качестве комплексообразующих соединений в специальной литературе упоминаются гликолевая, молочная, лимонная и аминоуксусная кислоты. Ускоряющими являются янтарная, малоновая, пропионовая, масляная, валериановая и другие кислоты. Для стабилизации служат в основном соединения свинца, тиосульфат, тиомочевина и т.д.
Ниже приведены примеры двух ванн для химического никелирования, г/л:
Ванна | 1 | 2 |
Сульфат никеля (NiS04•7Н2О) | 20 — 30 | — |
Ацетат натрия (Ch4•COONa•3h3O) | 10 — 15 | — |
Молочная кислота (Ch4CHOHCOOH) | 25 — 30 | — |
Тиомочевина (h3NCSNh3) | 0,0005 — 0,001 | — |
Гипофосфит натрия (Na2HPO2•h3O) | 15 — 20 | 15—25 |
Хлорид аммония (Nh5Cl) | — | 30—40 |
Цитрат натрия (Na3C6H5O7•5,5h30) | — | 30—50 |
Аммиак (Nh5OH) | — | 70-100 |
Хлорид никеля (NiCl2•6h3O) | — | 20—30 |
Ванна 1 кислая, лучше всего работает при рН = 4,3—4,8. Рабочая температура ванны 85—90 °С должна поддерживаться во время всего процесса никелирования. Для регулирования рН служит разбавленный (например, 5 %-ный) раствор едкого натра.
Готовят ванну 1 следующим образом: в дистиллированной воде, нагретой до температуры 60 °С, сначала растворяют ацетат натрия, затем сульфат никеля и добавляют молочную кислоту, предварительно нейтрализованную едким натром до рН = 3,5—4,0. Нагрев ванну до 85 °С, добавляют гипофосфит натрия. После этого можно приступить к никелированию.
Концентрация тиомочевины очень мала и в условиях мастерской нет возможности взвешивания с точностью до долей грамма. Так как избыток тиомочевины может привести к полной задержке процесса никелирования, лучше полностью отказаться от этого стабилизатора и воспользоваться ванной без тиомочевины.
Ванна 2 щелочная. В дистиллированной воде, нагретой до 60 °С, растворяют цитрат натрия, хлориды аммония и никеля, добавляют порциями при постоянном перемешивании раствор аммиака с целью достижения рН = 8—9. При этом происходит заметное изменение цвета раствора с зеленоватого на голубой. После подогрева до 80 °С добавляют гипофосфит и ванна готова к эксплуатации.
Приведенная информация очень общая и мало отражает практическую сторону никелирования.
При менее 80 °С эффективность ванны очень низка. При 90 °С получают в течение 1 ч слой никеля толщиной 10—20 мкм. При дальнейшем повышении температуры, например, до 95°С получают более толстые слои, но стабильность ванны снижается. В определенный момент может наступить внезапное разложение ванны, что сопровождается появлением черного порошка на дне и стенках ванны. Такая ванна непригодна для дальнейшего использования.
Серьезной проблемой является выбор соответствующих рабочих емкостей . В промышленных условиях применяют сложные установки из коррозионностойкой стали, тогда как для никелирования в малом объеме в основном служат стеклянные, фарфоровые или эмалированные емкости.
Наилучшим способом нагрева малых и средних емкостей является водяная рубашка. Опустим 5 л стеклянный сосуд в эмалированный 10 л бак с водой, мы можем получить водяную рубашку, пригодную для газо- или электронагрева ее до температуры кипения. В стеклянном сосуде можно достичь температуры 83—85 °С, достаточной для проведения процесса.
Высокая температура и сильное газовыделение на поверхности изделий фиксируется обслуживающим персоналом по сильному неприятному запаху. Очевидно, что вся установка должна находиться под вытяжкой.
Как видно, вся процедура непроста, вследствие чего применение химического никелирования ограничено теми случаями, когда неприменимы электролитические методы. Например, металлические сильфоны в виде цилиндрической гармошки, применяемые для измерения давления при пневморегулировке, невозможно никелировать электролитически из-за сложной геометрической формы. Химическое никелирование является прекрасным решением этой проблемы.
Стальные изделия можно никелировать химически без затруднений. На меди и латуни осаждение никеля начинается после кратковременного контакта с менее благородным металлом, например, железом или алюминием. Для никелирования алюминиевых сплавов обычно применяют щелочные ванны (например ванну 2).
На стенках и дне сосуда, применяемого для химического никелирования, могут оседать мелкие частички никеля, в особенности, если поверхность сосуда не очень гладка, имеет царапины. Перед дальнейшим использованием такого сосуда необходимо устранить осевшие частички никеля, растворяя их в азотной кислоте.
Свойства покрытий
Никелевое покрытие, полученное химическим путем, содержит кроме никеля в значительных количествах фосфор в зависимости от состава ванны и условий осаждения.
Установлено, что в кислых растворах получают более богатые фосфором покрытия, чем в щелочных растворах. Фосфор оказывает заметное влияние на магнитные свойства и, следовательно, определение толщины слоя никеля магнитными методами сопряжено с заметными ошибками.
Твердость свежеосажденного покрытия ~ 5 кН/мм2. Нагрев до 400 °С в течение 1 ч повышает твердость до 8—10 кН/мм2, что ненамного уступает твердости хромовых покрытий. При 400 °С химические покрытия приобретают цвет от желтого до гранатового. Во избежание этого покрытые детали следует нагревать в защитных средах.
Нагрев до 400 °С может отрицательно влиять на механические свойства подложки, поэтому некоторые применяют более низкие температуры, значительно увеличивая время обработки, например, 290 °С в течение 10 ч. Кроме того, не установлено, что максимальная твердость очень полезна, так как например, в химических покрытиях твердостью выше 9 кН/мм2 наблюдались трещины. Рекомендуется термическая обработка в температурной области 250—290 °С, что должно обеспечить твердость ~ 8 кН/мм2.
Довольно своеобразные результаты были получены при исследовании механической износостойкости. Лучшие результаты были получены на покрытиях, термически обработанных при 650 °С в течение 2 ч и, следовательно, имеющих твердость около 6 кН/мм2.
В отношении коррозионной стойкости химического никеля имеются многочисленные высказывания, отдающие предпочтение химическим покрытиям перед электролитическими. Некоторые конструкторы, подкрепленные этими высказываниями, согласились на антикоррозионную защиту стальных изделий химическим никелем толщиной 2—3 мкм. Однако такое покрытие не защищает от коррозии грубо обработанную поверхность стали.
vskproekt.ru
Никелирование в домашних условиях: технология и способы никелирования
Никель широко используется в приборостроении и машиностроении, а также в других различных отраслях. В пищевом производстве никель заменяет покрытия из олова, а в области оптики он известен за счет процесса черного никелирования металла. Никелем обрабатывают изделия, сделанные из стали и цветных металлов, для защиты от образования коррозии и увеличения сопротивления деталей механическому износу. Содержание фосфора в никеле позволяет делать пленку, по твердости схожей с пленкой хрома.
Процесс никелирования
Процедура никелирования подразумевает нанесение на поверхность изделия никелевого покрытия, которое, как правило, имеет толщину слоем 1-50 мкм. Никелевые покрытия могут быть матовыми черными или блестящими, но вне зависимости от этого, создают надежную и прочную защиту металла от агрессивных воздействий (щелочи, кислоты) и в условиях высоких температур.
Перед никелирования изделие необходимо подготовить. Этапы подготовки:
- деталь обрабатывают наждачкой для снятия оксидной пленки;
- обрабатывают щеткой;
- промывают под водой;
- обезжиривают в теплом содовом растворе;
- подвергают промывке еще раз.
Покрытия из никеля могут с течением времени утрачивать свой изначальный блеск, потому очень часто никелевый слой покрывают более стойким слоем хрома.
Никель, нанесенный на сталь, это катодное покрытие, которое защищает металл только механическим способом. Слабая плотность защитного слоя способствует появлению коррозионных пор, где растворимым электродом является именно стальная часть. В итоге под покрытием возникает коррозия, она разрушает стальную подложку и создает отслаивание никелевого слоя. Чтобы этого не допустить металл всегда необходимо обрабатывать толстым слоем никеля.
Покрытия из никеля наносятся на:
- медь;
- железо;
- титан;
- вольфрам и другие металлы.
Нельзя обрабатывать при помощи никелирования такие металлы, как:
- кадмий;
- свинец;
- свинец;
- олово;
- висмут;
- сурьму.
При никелировании деталей из стали необходимо делать подслой меди.
Никелевые покрытия применяют в различных сферах промышленности для специальных, декоративно-защитных целей, а также используют в роли подслоя. Технику никелирования применяют для восстановления изношенных деталей и запчастей автомобилей, покрытия медицинского инструмента, химической аппаратуры, предметов домашнего обихода, измерительных инструментов, деталей, которые подвергаются небольшим нагрузкам в условии действия крепких щелочей или сухого трения.
Разновидности никелирования
На практике существует два вида никелирования:
- Химическое;
- Электролитическое.
Первый вариант является четь дороже электролитического, но может обеспечить возможность создания равномерного покрытия по толщине и качеству на любых участках изделия, если создано условие доступа раствора к ним.
Электролитическое покрытие никелем в домашних условиях
Электролитическое никелирование отличается небольшой пористостью, она зависит от толщины защитного слоя и тщательности подготовки основания. Для создания качественной антикоррозионной защиты необходимо абсолютное отсутствие пор, для чего принято предварительно делать омеднение металлической детали или наносить несколько слоев покрытия, что намного прочней однослойного покрытия даже при одинаковой толщине.
Для чего в домашних условиях надо подготовить электролит. Необходимо 3,5 гр. хлорида никеля, 30 гр. сульфата никеля и 3 гр. борной кислоты на 100 мл. воды, этот электролит перелейте в емкость. Для никелирования меди или стали будут необходимы никелевые аноды, которые необходимо погрузить в электролит.
Деталь подвешивается на проволочке между никелевыми электродами. Проволочки, которые от никелевых пластинок, нужно соединить вместе. Детали подсоединяют к отрицательному полюсу источнику напряжения, а проволочки – к положительному. После необходимо подключить реостат в цепь и миллиамперметр для регулировки напряжения. Понадобится источник постоянного тока, с напряжением не более 6 Вольт.
Ток нужно включать примерно на 20 минут. После деталь достается, промывается и высушивается. Деталь покрыта матовым слоем никеля серого оттенка. Чтобы защитный слой получил блеск, его нужно отполировать. Но при работе не забывайте о значительных недостатках электролитического покрытия в домашних условиях — невозможности покрытия узких и глубоких отверстий и неравномерности осаждения на рельефной никелевой поверхности.
Химическое покрытие никелем в домашних условиях
Кроме электролитического способа, существует еще один, довольно несложный вариант для покрытия полированной стали или железа прочным и тонким никелевым слоем. Необходимо 10% раствор хлористого цинка и потихоньку добавлять к сернокислому раствору никеля, пока раствор не будет ярко-зеленым. Затем жидкость необходимо довести до кипения, желательно для этого взять фарфоровую емкость.
При этом образуется характерная муть, но на никелирования изделий она никак не влияет. Когда доведете раствор до кипения, надо в него опустить изделие, которое подвергается никелированию. Предварительно его надо обезжирить и почистить. Деталь должна кипеть в жидкости около часа, периодически доливайте дистиллированную воду по мере уменьшения раствора.
Если увидели при кипении, что раствор поменял цвет из ярко на слабо зеленый, то необходимо добавить чуть сернокислого никеля, чтобы получить изначальный окрас. Через указанное время достаньте деталь из жидкости, сполосните в воде, где растерто чуть-чуть мела, и хорошенько высушите. Полированное железо или сталь, покрытые таким образом, этот защитный слой удерживают довольно хорошо.
В основе процесса химического покрытия лежит реакция преобразования никеля из водяного раствора его солей с помощью гипофосфита натрия и других химических элементов. Растворы, использующиеся для химического покрытия, могут быть щелочными с рН более 6,5 и кислыми с рН 4-6,5.
Кислые растворы лучше всего применять для обработки меди, латуни и черных металлов. Щелочные используются для нержавейки. Кислый раствор, в отличие от щелочного, создает на полированном изделии более гладкую поверхность. Также важной особенностью кислых растворов является меньший шанс саморазряда при увеличении уровня рабочей температуры. Щелочные вещества гарантируют более прочное сцепление никелевой пленки с основанием металла.
Любые водные растворы для никелирования считаются универсальными, а именно подходящими для любых металлов. Для химического покрытия используют дистиллированную воду, но вы можете взять и конденсат из обычного холодильника. Химические реагенты подходят чистые – с маркировкой на упаковке «Ч».
Этапы приготовления раствора:
- Все химические вещества, кроме гипофосфита натрия, необходимо растворить в воде в эмалированной емкости.
- После разогрейте жидкость до кипячения, растворите гипофосфит натрия и разместите изделие в растворе.
- При помощи литра раствора можно покрыть никелем детали, имеющих площадь до 2 кв. дм.
Ванны для покрытия никелем
В мастерских часто используется ванна, состоящая из трех основных элементов:
- хлорид;
- сульфат;
- борная кислота.
Сульфат никеля это источник никелевых ионов. Хлорид существенно влияет на работу анодов, его пропорция в ванне точно не указывается. В безхлоридных ваннах происходит значительное пассивирование никеля, после этого количество в ванне никеля снижается, и как результат, падение качества покрытий и снижение выхода по току.
Аноды при хлоридах растворяются в необходимом количестве для достаточного протекания никелирования алюминия или меди. Хлориды повышают работу ванны при загрязнениях цинком и ее проводимость. Борная кислота поддерживает рН на необходимом уровне. Эффективность этого процесса зависит в основном от количества борной кислоты.
В роли хлорида можно выбрать хлорид магния, цинка или натрия. Повсеместно используются сульфатные ванны Воттса, содержащие в роли добавки электропроводные соли, увеличивающие электропроводность ванн и повышающие привлекательный вид защитного слоя. Наиболее часто используемый среди таких солей является сульфат магния (около 30 гр. на 1 л.).
Как правило, сульфат никеля вводить в соотношении приблизительно 220-360 гр. на 1 л. Сегодня появились тенденции к снижению сульфата никеля – менее 190 гр./л., это помогает значительно уменьшить потери раствора.
Добавление борной кислоты приблизительно 25-45 гр. на 1 л. Если менее 25 гр./л., то повышаются процессы защелачивания ванны. А превышение этого предела является неблагоприятным, по причине вероятной кристаллизации борной кислоты и выпадения осадков кристаллов на анодах и стенках ванны.
Никелевая ванна может работать в различном диапазоне температур. Но техника никелирования в домашних условиях нечасто используется при комнатной температуре. От покрытий, нанесенных в прохладных ваннах, зачастую отходит никель, потому ванну нужно прогревать минимум до 32 градусов. Плотность тока подбирают экспериментальным путем, чтобы не произошел прижег защитного слоя.
Натриевая ванна хорошо работает в большом диапазоне рН. Когда-то поддерживали рН 5,3-5,9, мотивируя слабой агрессивностью и лучшими кроющими свойствами ванны. Но высокие показатели рН провоцируют существенное увеличение напряжений в никелевом слое. Потому во многих ваннах рН равен 3,4-4,6.
Особенности никелирования
Сцепление никелевой пленки с металлом относительно низкое. Эту проблему решают при помощи термообработки пленок никеля. В основе процесса низкотемпературной диффузии находится нагрев отникелированных деталей до температуры 400 гр. и выдержке изделий в течение часа при данной температуре.
Но не забывайте, что если изделия, покрытые никелем, были закалены, то при 400 гр. они могут утратить прочность – их главное качество. Потому низкотемпературную диффузию в этих случаях делают при температуре около 260-310 гр. с выдержкой три часа. Эта термообработка может повышать и прочность никелевого покрытия.
Ванны подразумевают специальное оборудование для покрытия никелем и перемешивания водяного раствора для интенсификации процесса никелирования и снижения вероятности питтинга – появления мелких углублений в защитном слое. Перемешивание ванны влечет необходимость организации постоянной фильтрации для удаления загрязнений.
Перемешивание с помощью активной катодной штанги не настолько эффективно, как использование сжатого воздуха, и кроме этого, нуждается в наличии специального вещества, исключающего образования пены.
Удаление никелевого покрытия
Покрытия из никеля на стали принято убирать в ваннах с разведенной серной кислотой. Добавьте к 25 л. охлажденной воды частями 35 л. концентрированной серной кислоты, при этом постоянно перемешивания. Следите, чтобы температура не была не более 55 градусов. После остывания до комнатной температуры жидкости ее плотность должна быть 1,64.
Для снижения вероятности затравливания металла, из которого изготовлена подложка, в ванну добавляют глицерин в пропорции 50 гр. на 1 л. Ванны чаще всего делаются из винипласта. Детали навешивают на среднем поручне, соединенным с плюсом источника напряжения. Поручни, где прикреплены свинцовые листы, подсоединяются к минусу источника питания.
Проследите, чтобы температура ванны была не более 32 гр., потому что горячий раствор агрессивно воздействует на подложку. Плотность тока обязана быть около 4,1 А./дм. кв., но возможно изменение тока в диапазоне 4,5-6,2 Вольт.
Добавьте через некоторое время серную кислоту, чтобы выдержать плотность равной 1,64. Чтобы избежать разбавления ванны окунайте детали только после проведения их предварительной просушки.
На сегодняшний день никелирование – это наиболее популярный гальванотехнический процесс. Никелевые покрытия отличаются высокой коррозионной устойчивостью, твердостью, недорогой стоимостью никелирования, удельным электрическим сопротивлением и отличными отражательными возможностями.
Оцените статью: Поделитесь с друзьями!stanok.guru
Хим никель покрытие. 1.3. Свойства химических никелевых покрытий
Химическое никелирование | Защитные покрытия металлов
Наряду с широко применяемым электролитическим никелированием в последнее время большое внимание уделяется химическому никелированию, осуществляемому без электрического тока — при помощи химического восстановителя. Принципиально способность гипофосфористой кислоты восстанавливать металлы из растворов их солей была известна еще в середине прошлого столетия, однако промышленный метод химического никелирования был разработан в середине сороковых годов текущего столетия. Главной отличительной особенностью процесса является возможность нанесения равномерных по толщине покрытий на любые участки изделий сложного профиля. Никелевые покрытия, восстановленные гипофосфитом, содержат около 15% фосфора и по своим физико-химическим свойствам существенно отличаются от электроосажденного никеля, не содержащего фосфора. Химически восстановленный никель отличается высокой коррозионной стойкостью и твердостью, которая может быть значительно повышена в результате термической обработки.
Восстановление никеля гипофосфитом может быть представлено реакцией: NiCl2 + Nah4PO2 + h4O + Ni + Nih4PO3 + 2НCl.
Одновременно происходит гидролиз гипофосфита с выделением водорода Nah4PO2 + h4O → Nah4PO3 + h4.
Выделение никеля гипофосфитом самопроизвольно протекает на никеле, кобальте, палладии, железе и алюминии. На других металлах, например меди, требуется предварительное нанесение тонкого слоя никеля контактным методом или палладия методом погружения на несколько секунд изделий в подкисленный раствор хлористого палладия. Такие металлы, как свинец, кадмий, цинк, олово, висмут и сурьма не удается химически никелировать даже при использовании этих методов.
Скорость образования никелевого покрытия в сильной степени зависит от температуры раствора: при 98° С за 30 мин толщина покрытия равна примерно 10 мкм. В сильной степени скорость процесса определяется кислотностью, резко падая по мере повышения содержания свободной кислоты. Так как при взаимодействии никелевой соли с гипофосфитом освобождается кислота, то необходимо раствор буферировать с таким расчетом, чтобы рН поддерживать в пределах 5,0—5,5. Меньшее распространение имеют растворы со щелочной реакцией, в которых рН подд
pellete.ru