Ацетиленовый резак: устройство, принцип работы, особенности. Работа резаком
Газовая резка – технология обработки металла + Видео
Газовая резка, также нередко называемая автогенной либо кислородной, представляет собой процесс разрезания металлических заготовок посредством воздействия на них кислородного потока, подаваемого из специального агрегата.
1 Техника автогенной резки и ее ключевые положения
Данный вид обработки металла эксплуатируется весьма активно. На сегодняшний день он является популярным методом резки стальных и металлических изделий. Его суть состоит в том, что материал в зоне обработки доводится до температуры зажигания (горения) посредством смеси газа и кислорода, а затем на него наводят поток чистого кислорода.
Рекомендуем ознакомиться
Указанные действия приводят к сгоранию металла и удалению из зоны резки оксидов, которые образуются в ходе выполнения операции.
При горении поверхностного слоя заготовки отмечается выделение существенных объемов кислоты, в результате чего нагреваются нижние слои металла. Благодаря этому процесс горения охватывает деталь на всю глубину, формируется отверстие сквозного вида. Через него кислородная струя, выполняющая функцию режущего инструмента, пробивает заготовку полностью и выходит наружу. Передвигая с заданной скоростью приспособление для кислородной резки, получают точный разрез.
По сути, описываемый процесс включает в себя несколько основных этапов. Сначала металл подогревают, затем при помощи кислорода его сжигают, а на финальной стадии из полости реза происходит выдувание шлака, находящегося в расплавленном состоянии. В связи с тем, что при горении в кислороде железа выделяется сравнительно мало теплоты, тушения подогревательного пламени не производят. Это позволяет возмещать большие утраты тепла на участке обработки металла.
Если пламя потушить, металлическая заготовка очень быстро охлаждается, реакция горения затухает, и операция резки прекращается. Кислородная резка дает возможность вырезать сложные по форме изделия, а также без проблем осуществлять разрезание металлических деталей толщиной до 200 сантиметров. Отметим, что далеко не все сплавы и стали допускается подвергать автогенной резке. Она используется для металлов, которые соответствуют некоторым важным условиям. О них речь пойдет далее.
2 Условия для проведения кислородной резки
Газовая резка металла будет успешной только в том случае, если его температура плавления выше температуры воспламенения. Данному условию полностью отвечают сплавы с малым содержанием углерода. Плавятся они при температуре 1500 градусов, а воспламеняются при 1300 градусах. Средне- и высокоуглеродистые стали поддаются газовой обработке намного хуже, так как повышенное содержание углерода в них приводит к уменьшению температуры плавления и увеличению температуры воспламенения.
Также теплопроводность металлических композиций должна быть не очень высокой. Если подобное условие не выполняется, фиксируется активное отведение от зоны реза нагретого шлака и подогревающего пламени, что становится причиной неустойчивости операции. Она может прекратиться практически в любой момент резки. "Нужный" для проведения рассматриваемой в статье операции показатель теплопроводности отмечается исключительно у сталей, являющихся техническим сплавом железа, и непосредственно у железа. Автогенная резка прочих металлов в большинстве случаев невозможна.
Кроме того, должны выполняться и другие условия для резки:
- При сгорании в кислородной струе металла количество теплоты обязано быть таким, чтобы операция проходила непрерывно. Стоит помнить, что лишь 30 процентов теплоты образовывается от работы пламени резака, остальные же 70 процентов выделяются при сгорании металла.
- Температура расплавления металла должна быть выше температуры, при которой начинают плавиться металлические оксиды. В тех случаях, когда данное требование не соблюдается, операция резки нарушается из-за того, что кислородный поток не способен качественно выдуть тугоплавкие окислы. В связи с этим автогенная резка не рекомендуется для алюминия (его оксиды плавятся при температуре порядка 2050 градусов) и сталей с большим содержанием хрома (температура плавления их оксидов составляет около 2000 градусов). Впрочем, выход есть. Резать алюминий и высокохромистые сплавы допускается при помощи флюсов со специально подобранным составом.
- Жидкотекучесть шлаков, которые появляются в процессе резки, должна иметь высокие показатели, обеспечивающие простую выдувку шлаков из места выполнения операции.
3 Виды кислородной резки и их краткое описание
Резка с использованием газового оборудования бывает ручной и машинной, поверхностной и разделительной. При поверхностной разрезание металлической детали сопровождается формированием круглых по форме канавок, а при разделительной резке на поверхности появляются разрезы сквозного типа.
Разделительная ручная операция обычно назначается для обработки скрапа, профильных поковок и листов из углеродистой стали. Такая резка предполагает применение природного газа, смеси бутана и пропана, ацетилена в качестве горючей составляющей процесса. Как правило, используется ацетилен, так как он обеспечивает быстрый подогрев обрабатываемого изделия.
Ручная резка также применяется для вырезки отверстий и участков с теми или иными изъянами в трубопроводах, для обрезки под последующую газовую сварку концов трубных изделий. И листы, и трубы, и поковки режутся во всех пространственных положениях. При этом на качество процесса большое влияние оказывает квалификация специалиста, осуществляющего операцию, и наличие у него опыта работы резчиком.
Для повышения эффективности точности ручной прямолинейной резки рекомендуется производить процесс по направляющим и заранее нанесенным отметкам на изделии. Кроме того, нужно использовать и дополнительные приспособления (уголок, направляющие линейки, специальный циркуль для обработки отверстий и фланцев и так далее), которые дают возможность:
- четко выдерживать требуемую дистанцию между поверхностью заготовки и резаком;
- передвигать резак максимально равномерно;
- вовремя запускать кислородную струю.
Поверхностная резка (и машинная, и ручная) подразумевает удаление струей кислорода слоя металла определенной толщины. Ее отличие от распределительной состоит в том, что резак при поверхностной обработке передвигается быстро, причем под некоторым углом по отношению к металлической поверхности.
4 Особенности автогенной обработки металлов
Технология газовой резки предусматривает необходимость качественной очистки поверхности металлической детали от грязи, коррозии, окалины и лакокрасочных покрытий. При ручном разделении листов рекомендуется обдуть область реза на ширину не более 3–5 сантиметров (использовать пламя резака), после чего при помощи щетки из металла зачистить эту область.
При машинной резке, как правило, осуществляют очистку стальных листов на специальных агрегатах по дробеструйной либо химической методике. Дополнительно выполняют правку металлических заготовок на вальцах.
К ключевым характеристикам режима резки относят:
- давление кислорода;
- мощность пламени;
- скорость выполнения операции.
Качество и производительность операции зависит именно от этих показателей. Давление кислородной струи зависит от чистоты используемого газа, формы сопла на режущем инструменте и толщины изделия, подвергаемого разрезанию. При увеличении давления выше нормативных величин отмечается ухудшение качества поверхности и скорости процедуры, что, естественно, приводит к повышенному расходу кислорода.
Мощность пламени зависит от состояния сплава (поковка либо обычный прокат), его состава и толщины металла. Машинная резка выполняется на минимальном пламени, а вот для ручной его мощность необходимо повышать в 1,5–2 раза. Еще важный момент – при обработке изделий толщиной более 40 сантиметров следует использовать науглероживающее пламя (то, в котором имеется "лишний" ацетилен). В остальных случаях применяется стандартная мощность.
Скорости окисления металлической детали и процесса резки должны соответствовать друг другу. Чрезмерная скорость резки сопровождается искрами, она чревата тем, что металл может не прорезаться.
tutmet.ru
Как правильно резать металл кислородно-пропановым резаком?
По сравнению с газосварочными работами резка газом требует от человека гораздо меньших навыков. Поэтому овладеть газовым резаком не так уж сложно. Достаточно понять, как это правильно делать. Наибольшее распространение в наше время получили пропановые резаки. В них применяются совместно пропан и кислород, так как их смесь дает наибольшую температуру горения.
ПРЕИМУЩЕСТВА И НЕДОСТАТКИ
Преимущества резки металла пропаном перед другими способами очевидны:
- Применяется газовая резка, когда нужно разрезать довольно толстый металл или что-то вырезать по шаблонам, когда требуется криволинейный рез, который попросту невозможно сделать той же болгаркой. Газовый резак незаменим, если возникла необходимость вырезать диск из толстого металла или пробить глухое отверстие на 20-50 мм.
- Малый вес и удобство в использовании газового резака - еще одно неоспоримое достоинство. Кто работал с бензиновыми аналогами, знает, насколько они тяжелы, неповоротливы и шумны, сильно вибрируют, заставляя оператора прилагать значительные усилия при работе. Газовые модели лишены всех этих недостатков.
- Кроме того, резка металла газом позволяет работать в 2 раза быстрее, нежели при использовании устройства с двигателем на бензине.
- Пропан стоит гораздо дешевле не только бензина, но и других газов. Поэтому его выгодно использовать при больших объемах работ, например, при резке стали на металлолом.
- Кромка среза при пропановой резке немного хуже, чем при использовании ацетиленовых резаков. Тем не менее срез получается гораздо чище, чем у бензиновых горелок или болгарки.
Единственным минусом газовых резаков (пропановых в том числе) можно считать ограниченность спектра металлов, которые с их помощью можно резать. Им под силу только низко- и среднеуглеродистые стали, а так же ковкий чугун.
Резать газом высокоуглеродистые стали невозможно, потому что температура их плавления довольно близка к температуре пламени. В результате окалина не выбрасывается в виде столпа искр с обратной стороны листа, а смешивается с расплавленным металлом по краям разреза. Это не дает кислороду добраться вглубь металла, чтобы его прожечь. При резке чугуна процессу мешают форма зерен и графит между ними. (Исключение составляет ковкий чугун). Алюминий, медь и их сплавы газовой резке тоже не поддаются.
Следует напомнить, что к низкоуглеродистым сталям относятся марки от 08 до 20Г, к среднеуглеродистым - марки от 30 до 50Г2. В обозначениях же марок углеродистых сталей впереди всегда ставится буква У.
НЕОБХОДИМОЕ ОБОРУДОВАНИЕ
Для резки металла газом необходимо иметь по одному баллону пропана и кислорода, шланги высокого давления (кислородные), сам резак и мундштук нужного размера. На каждом баллоне должен располагаться редуктор, позволяющий регулировать подачу газа. Учтите, на баллоне с пропаном резьба обратная, поэтому навернуть на него другой редуктор невозможно.
Конструкция газового оборудования для резки металла разных производителей отличается незначительно. Обычно на всех них есть 3 вентиля: первый из них для подачи пропана, за ним идет вентиль регулирующего кислорода, после - вентиль режущего кислорода. Чаще всего кислородные вентили синие, те же, что открывают пропан, красные либо желтые.
Металл режут под воздействием струи горячего пламени, которая генерируется резаком. Во время работы аппарата в специальной смесительной камере пропан соединяется с кислородом, образуя горючую смесь.
Пропановый резак способен раскроить металл толщиной до 300 мм. Многие детали этого аппарата сменные, поэтому устройство в случае его поломки можно быстро отремонтировать прямо на рабочем месте.
Очень важно правильно выбрать мундштук. При его подборе стоит исходить из толщины металла. Если предмет, который необходимо разрезать, состоит из частей разной толщины, которая варьируется от 6 до 300 мм, понадобится несколько мундштуков с внутренними номерами от 1 до 2 и с внешними - от 1 до 5.
ПОДГОТОВКА К РАБОТЕ
Перед работой обязательно требуется осмотреть устройство, чтобы убедиться в том, что резак полностью исправен. Затем проделайте следующие шаги:
- Далее проверьте разъемные соединения на герметичность. Обнаружив утечку, подтяните гайки или смените уплотнители.
- Не забудьте проконтролировать, насколько герметичны крепления газовых редукторов и исправны ли манометры.
ПРИСТУПАЕМ К РАБОТЕ
Выставляем на кислородном редукторе 5 атмосфер, на газовом - 0,5. (Обычно соотношение газа к кислороду 1:10.) Все вентили резака следует поставить в закрытое положение.
Берется резак, сначала немного открываем пропан (на четверть или чуть больше), поджигаем. Упираем сопло резака в металл (под наклоном) и медленно открываем регулирующий кислород(не перепутайте с режущим). Поочередно регулируем эти вентили, чтобы добиться пламени нужной нам силы. При регулировке открываем попеременно газ, кислород, газ, кислород. Сила (или длина) пламени подбирается с расчетом толщины металла. Чем лист толще, тем сильнее пламя и расход кислорода с пропаном больше. Когда пламя отрегулировано (оно приобретает синий цвет и коронку), можно резать металл.
Подносится сопло к краю металла, держится он в 5 мм от разрезаемого предмета под углом 90°. Если лист или изделие необходимо прорезать в середине, разогревать металл следует начинать с той точки, от которой пойдет разрез. Разогреваем верхнюю кромку до 1000-1300° в зависимости от металла (до температуры его возгорания). Визуально это выглядит так, словно поверхность начала немного «мокнуть». По времени разогрев занимает буквально несколько секунд (до 10). Когда металл воспламеняется, открываем вентиль режущего кислорода, и на лист подается мощная узконаправленная струя.
Вентиль резака следует открывать очень медленно, тогда кислород зажжется от разогретого металла самостоятельно, что позволит избежать обратного удара пламени, сопровождающегося хлопком. Не спеша ведем кислородной струей вдоль заданной линии. В этом деле очень важно правильно выбрать угол наклона. Он должен составлять сначала 90°, затем иметь небольшое отклонение на 5-6° в сторону, обратную направлению резки. Однако если толщина металла превышает 95 мм, можно допустить отклонение в 7-10°. Когда металл уже прорезан на 15-20 мм, необходимо изменить угол наклона на 20-30°.
НЮАНСЫ РЕЗКИ ПО МЕТАЛЛУ
Резать метал нужно с правильной скоростью. Определить оптимальную скорость можно визуально по тому, как разлетаются искры. Поток искр при верной скорости вылетает под углом примерно 88-90° к разрезаемой поверхности. Если поток искр полетел в сторону, противоположную движению резака, это означает, что скорость резки слишком мала. Если же угол потока искр меньше 85°, это сигнализирует о превышении скорости.
При работе всегда необходимо ориентироваться на то, какой толщины металл. Если свыше 60 мм, лучше расположите листы под наклоном, чтобы обеспечить сток шлаков, и выполните работу наиболее точно.
Резка толстого металла имеет свои особенности. Перемещать резак раньше, чем металл будет разрезан на всю толщину, нельзя. К концу процесса резки необходимо плавно уменьшить скорость продвижения и сделать угол наклона резака больше на 10-15°. Останавливаться в процессе резки не рекомендуется. Если же работа по какой-то причине была прервана, не продолжайте резать с той точки, на которой остановились. Необходимо заново начать резать и только в новом месте.
Завершив резку, сначала перекрываем режущий кислород, затем отключаем регулирующий кислород, в последнюю очередь отключаем пропан.
ПОВЕРХНОСТНАЯ И ФИГУРНАЯ РЕЗКА
Иногда возникает необходимость прорезать металл не насквозь, а лишь создать на поверхности рельеф, прорезая на листе канавки. При этом методе резки металл будет нагреваться не только за счет пламени резака. Расплавленный шлак так же послужит источником тепла. Растекаясь, он будет подогревать нижние слои металла.
Поверхностная резка, как и обычная, начинается с того, что нужный участок прогревается до температуры воспламенения. Включив режущий кислород, вы создадите очаг горения металла, а равномерно перемещая резак, обеспечите процесс зачистки вдоль заданной линии разреза. Резак в этом случае нужно расположить под углом 70-80° к листу. При подаче режущего кислорода нужно наклонить резак, создавая угол в 17-45°.
Размеры канавки (ее глубину и ширину) регулируйте скоростью резки: увеличив скорость, уменьшаете размеры углубления и наоборот. Глубина выреза увеличится, если возрастет угол наклона мундштука, если уменьшится скорость резки и повысится давление кислорода (конечно же, режущего). Ширина канавки регулируется диаметром режущей кислородной струи. Помните, что глубина канавки должна быть меньше ее ширины примерно в 6 раз, иначе на поверхности появятся закаты.
Вырезать фигурное отверстие в металле можно следующим образом. Сначала намечаем на листе контур (при разметке окружности или фланцев следует отметить еще и центр окружности). До начала самой резки следует сделать пробивку отверстий. Начинать резку всегда необходимо с прямой линии, это поможет получить на закруглениях чистый рез. Начинать резать прямоугольник можно в любом месте, кроме углов. В самую последнюю очередь следует вырезать наружный контур. Это поможет вырезать деталь с наименьшими отклонениями от намеченных контуров.
МЕРЫ ПРЕДОСТОРОЖНОСТИ
Резка металла газом сопряжена с некоторым риском, поэтому необходимо строго придерживаться правил безопасности. Начнем с защитной одежды, которая должна включать в себя: огнеупорный костюм и краги для рук с такой же пропиткой; маску сварщика, сделанную из негорючего пластика с наголовником; рабочую обувь с высокими бортами. Также рекомендуется надевать респиратор. Зачем дышать дымами и пылью? Все эти меры придуманы не случайно, и не стоит ими пренебрегать. Например, может возникнуть ситуация, когда толстый металл сразу не продуется, и расплавленные брызги будут попадать на вас.
В процессе работы не забывайте следить за показанием редукторов на баллонах. Помните, что нельзя приступать к резке, если на шлангах есть трещины, разрывы или стыки. Некоторые умельцы соединяют стыки трубкой из алюминия или латуни. Однако лучше не рисковать. Примите во внимание, что железные трубки использовать с этой целью нельзя категорически, так как железо может дать искру.
Самое главное, что необходимо знать при работе с газовыми резаками: пропан огнеопасен, кислород же маслоопасен. При контакте кислорода с любым маслом произойдет взрыв. Во избежание беды, не прикасайтесь к кислородному баллону в испачканных маслом рукавицах или одежде. Не оставляйте рядом промасленные тряпки.
Помните, что баллоны должны располагаться на расстоянии 10 м от рабочего места и в 5 м друг от друга. Весь газ из баллона расходовать никак нельзя.
Иногда в процессе работы возникают внештатные ситуации. Не теряйтесь. Например, если у вас во время резки слетел со штуцера или оборвался кислородный шланг, не пугайтесь. Обычно испуг возникает из-за того, что случается это неожиданно и громко. Необходимо тут же перекрыть на резаке подачу пропана, затем закрыть оба баллона. Случается, что при розжиге пламени и настройки резака неожиданно исчезает пламя, издав хлопок. Просто закрываете вентили резака и разжигаете пламя заново.
metall-rostov.ru
Газорезка и необходимые знания при выборе газорезательного инструмента
В данной статье мы поговорим о газовых резаках. Для чего нужен газовый резак? Как ни странно, но он нужен для резки металла. Для этого сначала нужно нагреть метал до температуры плавления, а затем подать туда струю кислорода для того, чтобы металл начал гореть, и таким образом, осуществляется резка.
Для этого чаще всего используют два типа горючего газа:
- Пропан
- Ацетилен
Обычно на газорезке, предназначенной для резки с пропаном в наименовании имеется буква "П" в ацетиленовой версии используется буква "А".
Газорезки могут делиться по толщине реза:
Резаки с пометкой "Р1" способны резать металл до 100 миллиметров.
С пометкой "Р3" способны резать металл до 300 миллиметров.
Сейчас, к сожалению, не все производители соблюдают это требование. К примеру, на рынке могут встретиться резаки, помеченные индексом "Р3", и потребители думают, что они могут осилить металл до 300 миллиметров, но это оказывается не так.
Также резаки делятся между собой по принципу смешения газа:
Инжекторный резак. Они имеют 2 трубки. Горючий и подогревающий кислород движется на выход по одной трубке, а режущий кислород по другой.
Есть ещё и резаки с тремя трубками. Они называются "С внутрисопловым смешиванием газа". Все 3 вида газа идут по отдельной трубке и смешиваются на выходе в отдельной установке, под названием "Сопля". Поэтому этот вид газорезки называется внутрисопловое смешивание.
По типу подачи режущего кислорода резаки делятся на вентильные и рычажные:
Вентильные резаки имеют специальный вентиль, с помощью которого газорезчик может увеличивать и уменьшать подачу кислорода.
Рычажный. Исходя из названия, можно понять, что он имеет специальный рычаг, по нажатию на который происходит подача режущего кислорода.
Как выбрать газовый резак для газорезки?
Здесь пойдёт речь о том, как правильно выбрать резак? Р1 или Р3? Как выбрать резак по внешнему виду?
Прежде всего, нужно отметить, что невозможно сделать выбор глядя на какую-то рекламу или картинку. Для того, чтобы правильно выбрать резак его нужно как минимум взять в руки.
Для начала нужно определиться с тем, для каких целей вы хотите приобрести резак? Если вам нужен резак чтобы резать металл до 100 миллиметров, то нужно приобретать резак с пометкой Р1. Если же нужно резать металл до 300 миллиметров, соответственно это будет приспособление с пометкой Р3. Далее, нужно обратить внимание на внешний вид резака и из чего изготовлен наружный мундштук резака. Для хорошей и безопасной работы с устройством нужно приобретать резак с мундштуком, изготовленным из хромистой бронзы или из материала не уступающим ей по своим физико-механическим свойствам. Например, это может быть медь.
Также необходимо обратить внимание на то, из чего изготовлена внутренняя часть мундштука. Для безопасного и долгосрочного использования газорезки — внутренний мундштук должен изготавливаться из хромистой бронзы или меди. Различить их можно по цвету.
Из чего должен быть изготовлен резак?
Изготовление резаков допускается из латуни, она имеет жёлтый цвет. Из меди, она будет иметь цвет меди. Или из нержавеющей стали, серого цвета. Приобретать резаки, изготовленные из других материалов – не рекомендуется.
Для долгосрочной работы рекомендуется приобретать разобранный резак. Он должен иметь разъёмные соединения на тот случай, если, допустим, из строя вышел наконечник, износилась головка или прогорела трубка. Такие газорезки можно легко разобрать и без особого труда и усилий заменить испорченную делать.
Желаем сделать вам удачный выбор, руководствоваться данной статьёй и следить за безопасностью своей жизни и жизни своего помощника - резака.
weldering.com
Правила обращения с резаками
Подробности Подробности Опубликовано 27.05.2012 13:44 Просмотров: 16046Перед началом работы резаком необходимо проверить все его соединения на плотность и исправность инжектора. Проверка работы инжектора производится так же, как это описано выше для горелки. Для проверки плотности соединений поступают следующим образом. Выходные отверстия в мундштуке заглушают, закрывают ацетиленовый вентиль, присоединяют к кислородному ниппелю шланг, по которому в каналы резака подается кислород или воздух под давлением 10 кг)см2—для проверки кислородных каналов и 3 кг/см2 — для проверки каналов горючего и горючей смеси. Затем резак погружают в воду.
Наличие не плотностей обнаруживается по выходящим через них пузырькам газа.
Зажигание резака производят в такой последовательности. Открывают немного вентиль для подогревающего кислорода и создают разрежение в ацетиленовых каналах. Затем открывают ацетиленовый вентиль и поджигают горючую смесь, выходящую из мундштука. Далее необходимо отрегулировать подогревательное пламя резака с помощью соответствующих вентилей, после чего пустить режущий кислород. Струя режущего кислорода должна располагаться в центре подогревательного пламени.
В резаке могут иметь место следующие неисправности: не плотности в соединениях, неправильная установка, износ деталей, засорение каналов, наличие в каналах рисок, заусенцев и др. Если при зажигании горючей смеси в резаке возникают хлопки, то это указывает на пропуск режущего кислорода в месте посадки внутреннего мундштука в головку. В этом случае посадочные поверхности мундштука и головки следует притереть и тем устранить не плотность их соединения. Неправильная установка внутреннего мундштука в головке вызывает отклонение режущей струи от центра подогревающего пламени. При наличии заусенцев и царапин на кромках каналов мундштуков форма подогревательного пламени искажается. Заусенцы и царапины удаляются с помощью шлифовки.
При работе с керосинорезом надо тщательно следить за плотностью всех соединений. Перед заливкой в бачок керосин необходимо фильтровать через слой войлока и каустической соды для очистки от механических примесей, смолистых веществ и влаги.
Необходимо следить, чтобы горючее не проникало в кислородные каналы резака и кислородный шланг, что может привести к обратному удару. Давление кислорода должно быть всегда больше давления воздуха в бачке, а при перерывах в работе нужно укладывать керосинорез головкой вниз во избежание затекания керосина в кислородный шланг.
Для получения пламени керосинореза его испаритель сначала нагревают пламенем другого резака, горелки, паяльной лампы или зажженных обтирочных концов.
Затем открывают вентиль для подогревающего кислорода и вентиль подачи горючего, поджигают выходящую из мундштука горючую смесь и регулируют пламя, которое должно иметь слегка колоколообразную форму.
Прогрев ведется до исчезновения блестков в пламени, что говорит о полном испарении горючей жидкости в испарителе.
Прекращая работу, прежде всего нужно закрыть вентиль режущего кислорода, затем прекратить поступление горючего и, наконец, закрыть вентиль подогревающего кислорода. После этого снять давление в бачке с помощью спускного вентиля.
Испаритель резака нужно регулярно прочищать от нагара, асбестовую оплетку промывать бензином, а если она сильно уплотнилась, то заменить новой.
В работе керосинореза могут быть следующие неисправности.
1. Хлопки пламени в результате засорения мундштука или недостаточного поступления горючего и кислорода. Для устранения хлопков необходимо прочистить сопло или увеличить подачу газов.
2. Засорение мундштука для подогрева испарителя, в результате чего пламя, подогревающее испаритель, гаснет. Необходимо прочистить мундштук медной иглой.
3. Изменение формы и угасание подогревающего пламени вследствие тугой асбестовой оплетки, которая плохо пропускает горючее, или утечки воздуха из бачка. В этом случае необходимо устранить утечку воздуха из бачка или сменить оплетку. Смену оплетки необходимо производить также и в случае ее пересыхания или ослабления, так как при этом подача горючего происходит неравномерно и пламя начинает гореть неравномерно.
При работе керосинореза на бензине применяются меньшие диаметры каналов сопла для подогрева испарителя.
Читайте также
Добавить комментарий
electrowelder.ru
Ацетиленовый резак: устройство, принцип работы, особенности
Одним из самых востребованных металлообрабатывающих приборов является газовый резак, который позволяет раскраивать изделия из железа и стали в соответствии с утвержденным проектом. Действие таких устройств основано на нагревании материала до высоких температур, его сгорании в кислородной струе и удалении той же струей продуктов горения из зоны реза.
На крупных производственных объектах особой популярностью пользуется ацетиленовый резак, который способен разрезать стальные листы и изделия металлопроката толщиной 300 миллиметров и более. Одновременно с этим увеличивается производительность предприятия, улучшается качество обработки изделий и ускоряется производственный процесс.
Устройство ацетиленовых резаков
Любой газокислородный резак состоит их трех основных частей – газовых баллонов, ствола и наконечника. Ствол представляет собой рукоятку с ниппелями, которые служат для присоединения газовых рукавов с кислородом и ацетиленом. На корпусе также имеется три клапана, с помощью которых регулируют подачу режущего и подогревающего кислорода, а также рабочего газа (ацетилена).
Одним из основных элементов, входящих в ацетиленовый резак, является инжектор – ускоритель заряженных частиц. Сразу к нему присоединена камера смешения, в которой образуется горючая смесь из ацетилена и химически чистого кислорода. Камера смешения плавно переходит в трубку подачи подогревающего кислорода.
Перед самым инжектором на стволе имеется ответвление – трубка режущего кислорода. На ней расположен вентиль, регулирующий подачу химически чистого кислорода. Торцы трубок подачи подогревающей смеси и режущего кислорода присоединены к наконечнику. Он состоит из внутреннего и наружного мундштуков, которые помещены в специальную головку резака.
Принцип действия ацетиленового резака
Как и любой другой газокислородный нож, ацетиленовый резак обрабатывает металлические изделия одновременным воздействием высокой температурой и направленной кислородной струей. После присоединения газовых рукавов к ниппелям кислород направляется в двух направлениях. Одна часть газа, через специальное ответвление, попадает в трубку режущего кислорода, а другая – в инжектор.
Выходя из инжектора, кислород развивает высокую скорость и создает зону разряжения в смесительной камере. Из-за разницы давления в камеру начинает «подсасываться» ацетилен, который равномерно смешивается с О2. Полученная смесь газов на высокой скорости движется дальше и вырывается через зазор между внутренним и внешним мундштуками, одновременно воспламеняясь.
Так образуется подогревающее пламя, которое доводит материал до аморфного (полужидкого/полутвердого) состояния. Через установленный на ацетиленовый резак наконечник вырывается также струя режущего кислорода, которая своей высокой скоростью «сдувает» расплавленный металл.
Особенности ацетиленового резака
Все особенности ацетиленового резака обусловлены рабочим газом – ацетиленом. В отличие от других видов топлива он способен разогреваться до температуры порядка 3100 градусов по Цельсию. Именно благодаря этому обеспечивается:
- Наивысшая производительность – при помощи ацетиленового газокислородного ножа можно разрезать материал толщиной более 300 мм.
- Низкая доля окислительных процессов – структурные связи в молекулах мгновенно разрушаются без образования соединений с кислородом.
- Высокое качество резки.
На рынке в широком ассортименте представлен резак ацетиленовый «Маяк». Модели отличаются главным образом либо конструкцией ствола, либо его заменяемой частью – мундштуком, от которого зависит интенсивность, а также размер газовой струи.
Универсальные резаки
В некоторых случаях использовать резак газовый ацетиленовый экономически нецелесообразно. При этом иметь два резака, работающих на разных типах топлива, неразумно. Поэтому на крупных производственных объектах особой популярностью пользуются универсальные газокислородные ножи. Их главная особенность заключается в способности работать от разных видов топлива.Подавляющее большинство универсальных агрегатов используется для ручной резки нелегированных изделий или сталей с низким процентом углерода в их составе. Наибольшее распространение получил пропановый/ацетиленовый резак. Первый тип газа используется для обработки материалов толщиной до 200 мм, а второй – свыше 300 мм.
fb.ru
условия эксплуатации ножей, инжекторные устройства
Газовая резка металла предусматривает использование высоких температур для его нагревания, стимулируя процесс плавления или возгорания. Обширный диапазон применения газового резака позволяет использовать его для работы в ручном режиме. Устройство газового резака применяется для создания из металлических листов сложных конструктивных форм.
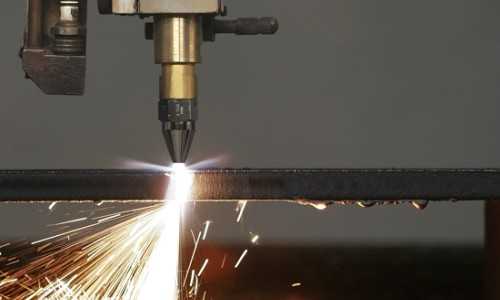
Устройство газового резака используется для создания сложных конструктивных форм из металлических листов.
Зачем нужен газовый резак?
Благодаря достоинствам газовая резка металла используется очень часто. Она проводится без применения сложного оборудования, не требует большого количества источников энергии, простая в исполнении. Наиболее часто она применяется в сельском хозяйстве, при проведении ремонтных работ в промышленности.
Резак используют при работе с изделиями из алюминия, чугуна, латуни, бронзы. В процессе эксплуатации применяют 2 вида газа — кислород и пропан. Резка пропаном используется для стальных листов с содержанием углерода выше 0,8%.
Использование смеси пропана и кислорода для работы газового ножа
Схема газового резака.
В процессе разрезания металла формируется газовое облако с высокой температурой. Наблюдается окисление продуктов сгорания за счет влияния кислорода.
Для работы с применением пропана используют несколько видов горелок:
- индукторные;
- модели с камерами;
- камерно-вихревые.
При кислородной резке металла применяют горючие жидкости, образующие температуру смеси до 1800°C. Чистота кислорода для работы составляет 98,5-99,5%.
В процессе осуществления мероприятий под водой используют резак с бензиново-кислородным горением, а легированные стали разрезают кислородно-флюсовой резкой.
Газовый нож для ручной резки с применением ацетилена разъединяет металл толщиной 60 мм, образуя шов шириной от 2,0 до 4,5 м.
Подготовленный материал обрабатывается при помощи смеси, находящейся в корпусе ножа, предназначенного для разрезания вручную. Устройства для разъединения материалов подразделяют на следующие виды:
Схема кислородного резака.
- по характеру используемой смеси;
- по функциональным признакам.
Инжекторные ножи изготавливают по ГОСТ 5191-796. Они имеют несколько мощностей, зависящих от толщины металла.
Конструкция газового ножа обязана удовлетворять такому требованию, как наличие ствола, состоящего из специальных запорных вентилей, способных подогревать пламя. Обязательно присутствие крепления из двух ниппелей и гаек согласно ГОСТ 9356-75.
К газовому ножу прилагается наконечник с трубкой и сменные мундштуки. Дозирующее устройство оснащено удлинительной трубкой. Работа газового ножа осуществляется с применением газов, имеющих величину сгорания 16,9 МДж/м³.
Следует использовать для работы детали ножей, изготовленные из латуни. Для создания ствола резака используют алюминиевые материалы, не влияющие на работу газового ножа.
Для изготовления мундштуков используют бронзу марки БрХ1. Особое внимание уделяют созданию деталей смесительной емкости. Они изготавливаются из сплавов, содержащих медь не более 70%. Общая длина газового ножа составляет 700 мм.
Устройство ручного газового ножа
Основная задача устройства для резки состоит в подаче режущей струи в центральное отверстие мундштука. Нож имеет ствол, соединенный резинотканными рукавами с ниппелем, а через него с правой резьбой для подачи кислорода. Соединение через штуцер с левой резьбой обеспечивает подачу ацетилена и других газов.
Устройство ручного газового ножа.
Небольшое количество кислорода попадает в инжектор, а затем в емкость перед смесительной камерой. В ней горючий газ смешивается с кислородом из-за создания разреженного пространства.
Смесь транспортируется в промежуток между гильзой и соплом, а часть кислорода поступает в центральный канал. С помощью вентилей происходит регулировка интенсивности подогревающего пламени.
Основное устройство состоит из инжектора и смесительной емкости. От ее функционирования зависит работа газового ножа. Сбой в работе происходит при изменении размеров зазора между концом инжектора и самой камерой.
Ствол содержит маркировку вида ножа, на смесителе обозначают вид используемого топлива.
Схема инжекторного газового резака.
Ножи средней мощности пригодны для разъединения листов металла толщиной до 200 мм. Устройства, обладающие большей мощностью, работают на смеси сжиженного или природного газа. Комплектующие ножи к аналогичным модификациям горелок отличаются между собой наличием соединительных деталей. Ножи включают в свой состав корпус, несколько мундштуков, рычаг пуска, вентили. Используется рабочее давление газа не ниже 0,8-1,2 Мпа при общем его расходе-74 м³/г. Масса ножа составляет 2 кг.
Резка металлов осуществляется не только с применением газового ножа, но и с использованием плазменных аппаратов. Современный плазморез вместо рабочего газа использует сжатый воздух. Универсальность аппарата позволяет производить не только резку, но и создание дуги между электродами.
Условия эксплуатации газовых ножей
Работа с устройством для разъединения материалов требует от газорезчика собранности и внимания. Прежде всего, мастеру нужно проверить нож, найти видимые повреждения. Он проверяет соединение между рукавами и резаком. Рукав продувают с помощью газа. Осматривают механизм взаимодействия рукава и штуцера.
До подключения левого рукава устанавливают наличие давления в ноже. Используя данные инструкции, крепят два мундштука. При слабом подсосе требуется прочистить инжектор.
Устанавливают герметичность в соединениях ножа. Одновременно подтягивают крепления сальника до упора или полностью заменяют кольца уплотнителя смесительной камеры. Контролируют уровень жидкости в водяном затворе.
После проведения процедуры проверки необходимо отрегулировать пламя в газовом ноже. До начала процесса устанавливают запас ацетилена. При возникшей необходимости ликвидации пламени закрывают вентиль емкости с ацетиленом, а затем — кислородный кран.
Ручной газовый резак имеет эргономичный дизайн, удобен при обслуживании, пригоден для использования горючих газов.
moyasvarka.ru
Резка металла резаком: виды, технология
Ручные резки металла резаком пользуются большой популярностью по той причине, что можно быстро и качественно разрезать материал (например, при прокладке трубопроводов), не повредив поверхность.
Использование резака позволяет резать металл любой толщины с минимальными затратами средств и времени (например, при прокладке трубопроводов).
С помощью данной ручной резки осуществляется резка цветных сплавов, чугуна, высокохромистых сталей.
Существует несколько видов резаков, которые нужно знать, чтобы выбрать подходящий вариант для больших и маленьких толщин любого металла, особенно чугуна.
В целом резаки для обработки металла подразделяются на две категории: газовые и воздушно-дуговые.
Газовые резаки
Основой газовой (кислородной) резки является сгорание металлосплавов в потоке чистого кислорода. Перед резкой материал нагревается до температуры горения и окисления.
Таким образом, кислородная резка состоит из двух этапов:
- нагрев материала до необходимой температуры;
- резка кислородом.
Для нагревания металлического листа, чтобы воспользоваться кислородной резкой, применяются такие горючие газы, как ацетилен, достигающий максимальной температуры сгорания более 3000° (используется для резки рельсов), природный газ, водород, керосин, пары бензина и др.
В таком случае используются резаки небольшой и средней толщины, имеющие конструкцию кислородной горелки.
Газовые резаки включают в себя следующие процессы:
- соединение паров жидкости, кислорода и горючих газов;
- создание огня для нагрева;
- подача кислорода.
Ручную резку сплавов больших толщин кислородом не во всех случаях возможно сделать резаком.
Для кислородной вариации резки важно правильно выбрать металл с точки зрения температуры плавления, показатель которой не должен превышать температуру возгорания кислорода.
Часто возникают проблемы с газовой резкой материала, содержащего большое количество углерода, например, чугуна.
Одной из разновидностей газовой резки является кислородно-флюсовая, с помощью которой осуществляется обработка нержавеющих хромоникелевых и хромистых сплавов, цветных металлов, чугуна и многого другого. Чаще всего ее применяют для трубопроводов и пр.
Суть заключается в том, что на место кислородной резки специальные приспособления беспрерывно подают порошкообразный флюс вместе с кислородом.
Флюс сгорает и образуются оксиды, после чего оксиды начинают плавиться и жидкие текущие шлаки вытекают. В качестве флюса используется мелкогранулированный железный порошок.
А при кислородной резке чугуна еще добавляется доменный феррофосфор. Кислородно-флюсовая резка чугуна и других материалов представлена на видео.
Видео:
При ручной кислородной резке качество работ зависит от правильно расположенного резака над поверхностью металла. Нужно соблюдать угол наклона и скорость, так как при неправильно установленной скорости получается неровный срез.
При резке металла больших толщин до 5 см (как при прокладке трубопроводов) пламя должно направляться непосредственно на кромку, что наглядно представлено на видео.
Мундштук располагается перпендикулярно обрабатываемого материала так, чтобы нагревающее пламя и кислород были вдоль вертикальной грани.
Материал передвигается исключительно после прорезывания всей толщины детали.
При резке материала больших толщин до 20 см, например, рельсов или трубопроводов, чугуна, резак располагается под углом 75° к горизонтали, как на видео.
Скорость нужно выставить выше средней. Чистота и величина среза зависят от толщины материала.
Если нужно разрезать изделие круглого сечения, то угол наклона резака должен быть большим, а в процессе резки угол нужно постоянно уменьшать до перпендикулярно расположения резака.
При обработке фигурных изделий больших или малых толщин резак должен располагаться исключительно перпендикулярно относительно поверхности металла.
Видео:
Перед использованием кислородного резака поверхность обрабатываемого материала необходимо настроить и подготовить: тщательно очистить от грязи и коррозии.
Для резки используется кислород в баллонах, которые имеют редуктор для регулировки давления.
Кислород и горючий газ поступают в резак по отдельным шлангам. Чтобы не взорвался генератор, который питает резак, на нем должен быть водяной затвор, который наполняется водой до начала работы.
Генератор без водяного затвора использовать запрещено. Кислородная резка представлена на видео в разделе.
Конечно, газовая резка имеет некоторые недостатки, например: неравномерный нагрев металла приводит к деформации, поэтому при прокладке трубопроводов необходимо доверить такую работу специалисту.
Во избежание повреждения рекомендуется придерживаться следующих правил:
- резка начинается с самой длинной кромки, а заканчивается короткой;
- в первую очередь вырезаются мелкие детали;
- во избежание сильного нагревания кромок, нужно, чтобы скорость резки была достаточно высокой;
- во время резки обрабатываемые изделия охлаждаются водой.
Также довольно часто применяется поверхностная кислородная резка, с помощью которой можно вырезать канавки на поверхности металла в виде рельефа.
Поверхностная резка производится резаками моделей РАП-62, РПА-62, РПК-62.
Еще одной разновидностью кислородной резки является разделительная, которая применяется для разреза листового материала, вырезания заготовок и иных работ, связанных с разделением материала на несколько частей.
Для ручной разделительной резки используются такие резаки, как «Пламя-62», РГС-60М.
Плазменный резак
Ручной газовый резак, работающий по типу воздушно-дуговой резки (плазменной), является довольно популярным, особенно в промышленности.
Принцип плазменной резки заключается в следующем: материал плавится между электродом и обрабатываемым листом металла, после чего металл выдувается сжатым воздухом.
Технология плазменной резки доступна не только профессиональным сварщикам.
Если обработка металла выполняется ручным способом, то воздушно-плазменная резка является самым экономичным вариантом, но редко применяемым для прокладки тех же трубопроводов.
Достоинствами воздушно-дуговой обработки являются:
- компактное оборудование;
- низкие энергозатраты;
- качественный рез разных видов металла;
- высокая скорость;
- наличие защиты от перегрева и воздушного охлаждения;
- простое включение оборудования.
Такая резка часто применяется для обработки металла малых и средних толщин до 35 мм. Часто применяется для обработки отливов, устранения дефектов на швах, токопроводящих металлов и т.д.
Плазменной резкой производится не только прямолинейная резка, но и фигурная, как гласит технологическая карта.
Плазменные резаки представлены в виде машины с плазмотроном – рабочей насадкой, в которой размещается электрод. В процессе резки в электрод подается плазмообразующий газ, например, сжатый воздух.
Под воздействием выработки сварочного тока электрод нагревается и зажигается дуга, в результате чего газ превращается в плазму с температурой до 30000°.
Видео:
Так как металл быстро нагревается дугой плазмореза, поэтому происходит плавление только места среза, а другие участки материала не нагреваются.
Благодаря этому, поверхность не деформируется в результате теплового воздействия. Применение плазменной резки позволяет не обрабатывать кромки дополнительно.
Качество ручной плазменной резки напрямую зависит от сопла, находящегося в плазмотроне. Сопло оказывает влияние на скорость, ширину и чистоту среза.
Сопло является деталью, которая часто нуждается в замене, а если длина сопла будет увеличена, то данное обстоятельство улучшит качество резака.
Особенностью работы плазменного резака является длительное непрерывное время работы более получаса. По истечении данного времени оборудование требуется отключить для остывания.
Воздушно-дуговой резак может работать от трансформаторов и инверторов.
Использование трансформаторов позволяет резать металлы больших толщин до 40 мм, а инверторы для металла меньших толщин — до 30 мм.
Для ручной резки рекомендуется использовать инверторы, так как они более эффективны для работы с нержавеющими сталями, чугуном и мягкими сплавами. Подробно процесс плазменной резки можно посмотреть на видео. При желании можно найти несколько руководств в видео-формате, где рассказан процесс и показана сварка трубопроводов.
Видео:
Плазменная резка используется для обработки цветных сплавов, однако существуют определенные нюансы такой обработки.
Нержавеющие стали не рекомендуется резать с использованием сжатого воздуха. Лучше использовать чистый азот или смешать его с аргоном – это будет зависеть от толщины металла.
Также следует иметь в виду, что нержавейка может деформироваться под воздействием переменного тока, а это, в свою очередь, приведет к небольшому сроку эксплуатации.
Для резки алюминия толщиной до 70 мм применяется сжатый воздух.
При меньшей плотности материала толщиной до 20 мм резка осуществляется чистым азотом, при толщине 70-100 мм используется азот с водородом.
Использование резака для резки металла (например, при прокладке трубопроводов) позволяет быстро и качественно выполнить обработку материала. К тому же все работы можно сделать своими руками, зная технологию резки.
Подробно весь процесс представлен на видео, изучение которого позволит правильно использовать резак. Важна также и технологическая карта, в которой даны инструкции о том, как правильно пользоваться тем или иным инструментом.
rezhemmetall.ru