Нарезание резьбы резцами и гребенками. Резцы для нарезания резьбы
Нарезание резьбы резцами
Нарезание резьбы резцами осуществляется за несколько проходов. Инструмент совершает следующие движения: (Рис. 78) I. – радиальное SP (движение подачи),
П. – рабочий ход вдоль оси детали на длину резьбы (движение формообразования.
Ш. – быстрый радиальный отвод.
IV. – быстрый обратный холостой ход вдоль оси заготовки в исходное положение. Такой цикл вручную или автоматически повторяют до полного удаления припуска.
При нарезании метрических резьб при врезании используют два направления подачи: 1. Радиальное и 2. Боковое (Рис. 79).
Геометрические параметры резьбовых резцов (Рис. 80)
ε – угол при вершине. Для метрической резьбы ε = 60°; с учетом "разбивки" резьбы при нарезании рекомендуют угол ε для резцов делать равным 59° 30′.
Вершину резца делают либо плоской шириной f, либо закругленной радиусом r величины которых выбираются в зависимости от шага резьбы Р .
Боковые поверхности резьбы являются винтовыми с углом подъема τ (по наружному диаметру). Для правой резьбы задний угол у левой кромки (αл) должен быть больше угла τ, чтобы левая поверхность резца не задевала боковую поверхность резьбы (Рис. 81).
Рис. 78. Схема резания при многопроходном нарезании резьбы резцом
Рис. 79. Схемы резания при многопроходном нарезании резьбы
Рис. 80. Геометрические параметры резьбового резца
Обычно:
Задний угол α в плоскости перпендикулярной оси резьбы обычно задают α = 10 – 12°, для обработки резьб на закаленных сталях α = αл = αп = 6 °.
Передний угол γ = 0 – 25° для черновых резцов.
Для чистовых резцов γ = 0° для избежания коррекционных расчетов профиля резца.
Нарезание резьб плашками
Плашками нарезают наружные резьбы. Во время работы плашку устанавливают в плашкодержатель. Круглая плашка, подобно гайке, имеет центральное отверстие с резьбой, вокруг которого расположено несколько гладких отверстий, пересекающих центральное для образования передней поверхности. Режущие части у плашки выполнены с двух сторон. Плашками работают с теми же движениями что и метчиками.
Геометрия плашек (Рис.82)
Угол режущей части 2φ = 50°. Длина режущей части l1 = (1,5…2)Р. Задний угол α = 7 – 10°, получают затылованием зубьев на режущей части. Передний утл γ = 15 – 20°.
Элементы резания и срезаемого слоя у плашек те же, что и у метчиков.
Метчики и плашки требуют принудительного осевого движения при врезании только по 1 – 2 шага. Дальнейшее осевое движение инструмента осуществляется за счет самозатягивания.
Рис. 81. Задние углы резьбового резца
Рис. 82. Основные конструктивные элементы плашки
Фрезерование
Фрезерование является одним из наиболее распространенных видов обработки плоскостей, пазов, а также фасонных поверхностей. Главным движением при фрезеровании является вращение фрезы, а движением подачи – обычное поступательное перемещение заготовки.
Типы фрез
По своему назначению фрезы делятся на: 1. цилиндрические, 2. торцовые, 3. дисковые, 4. прорезные и отрезные, 5. концевые, 6. фасонные фрезы.
По конструктивному оформлению фрезы бывают цельными, составными и сборочными, как из быстрорежущих сталей, так и из твердых сплавов. По способу крепления фрезы бывают насадочными и с хвостовиком.
Элементы резания при фрезеровании
Рассмотрим элементы резания и срезаемого слоя при цилиндрическом и торцовом фрезеровании.
Цилиндрическое фрезерование (Рис. 83)
К элементам резания относятся:
t – глубина резания, мм ,
S – подача, мм,
V – скорость резания, м/мин,
В – ширина фрезерования, мм.
К элементам срезаемого слоя относятся:
a – толщина срезаемого слоя,
b – ширина срезаемого слоя.
Различают следующие размерности подачи:
1. Подача на 1 оборот фрезы
S0 – величина перемещения за 1 оборот.
2. Подача на зуб SZ
Рис. 83. Элементы срезаемого слоя при работе прямозубой цилиндрической фрезой
мм/зуб.
Подача минутная SM
мм/мин.
Скорость резания:
м/мин,
где D – диаметр фрезы.
Ширина фрезерования В – величина обрабатываемой поверхности, измеренная в направлении параллельной оси фрезы.
Толщина срезаемого слоя имеет переменные значения:
Толщина срезаемого слоя в любой точке дуги контакта (мгновенная толщина) определяется:
Для прямозубых фрез ширина срезаемого слоя равна ширине фрезерования b = B.
Число одновременно работающих зубьев
где Ψ – угол контакта фрезы.
ε – угловой шаг зубьев, фрезы.
Цилиндрическое (также и торцовое) фрезерование может осуществляться двумя способами: (Рис. 84)
а) встречное фрезерование,
б) попутное фрезерование.
Рис. 84. Схемы фрезерования
Рис. 85. Схема симметричного торцевого фрезерования
При встречном фрезеровании направление подачи противоположно направлению вращения фрезы.
При попутном фрезеровании направление подачи и вращение фрезы совпадают.
При встречном фрезеровании нагрузка на зуб возрастает от нуля до максимума. При этом силы стремятся оторвать заготовку от стола станка, что вызывает вибрации и ухудшается шероховатость обработки. Преимуществом встречного фрезерования является работа зубьев "из-под корки", что весьма важно при обработке отливок с коркой, загрязненной литейной землей.
При попутном фрезеровании зуб фрезы начинает работать с максимальной толщины среза. Стойкость фрез в 2 – 3 раза при попутном фрезеровании выше, чистота обработанной поверхности лучше, прижим детали силами резания осуществляется к столу станка. Однако, для этого типа фрезерования необходимо плотное соединение ходового винта и маточной гайки стола.
Торцовое фрезерование
В зависимости от расположения оси торцовой фрезы относительно оси симметрии заготовки различают симметричное и несимметричное фрезерование.
При симметричном фрезеровании ось фрезы совпадает с осью симметрии заготовки. Глубина резания t определяется так же, как и у цилиндрической фрезы: шириной фрезерования является размер обрабатываемой поверхности, в направлении, перпендикуляном подаче (Рис. 85).
Максимальное значение толщины среза равно подаче на зуб:
Мгновенная толщина срезаемого слоя определяется так же, как и для цилиндрических фрез:
Геометрические параметры фрез
По конструкции зубьев фрезы бывают с затылованными и острозаточенными зубьями.
Фрезы с острозаточенными зубьями обычно затачиваются по задним поверхностям (Рис. 86).
Фрезы с затылованными зубьями затачивают по передней поверхности. С затылованными зубьями делают только фасонные фрезы.
Основные элементы конструкции острозаточенных фрез стандартизованы. Этими элементами являются диаметр фрезы, форма зуба и впадины/ диаметр посадочного отверстия, шпоночного паза, а также размеры, посадочного хвостовика.
Форма зуба
Объем впадины и ее профиль должны обеспечивать свободное размещение и выход стружки.
Для острозаточенных фрез рекомендуются следующие формы зубьев (Рис. 87). Для мелкозубных фрез, предназначенных для чистовой обработки, рекомендуются следующие формы зуба.
Высота зуба где
Sокр – окружной шаг зубьев.
Радиус закругления у дна впадины:
r = 0,5…2,5 мм,
f = 1 – 2 мм - длина задней поверхности.
Для достаточной прочности угол η не должен быть меньше 45 – 50°. υ = 45-100°.
Геометрические параметры фрез
γ = 5 – 25°- в зависимости от обрабатываемого материала (для быстрорежущих фрез).
γ = –15 ÷ +15°- для твердосплавных фрез.
α = 12 – 20° – для быстрорежущих фрез.
α = 8 – 20° – для твердосплавных фрез.
Рис. 86. Схема заточки зуба фрезы
Рис. 87. Форма и основные геометрические параметры зубьев острозаточенных фрез
Для затылованных фрез рекомендуется следующая форма зуба. (Рис. 88)
К - величина затылования.
studfiles.net
Нарезание резьбы резцами | Токарная обработка металла
Наиболее распространенным способом нарезания резьбы на токарно-винторезных станках является нарезание резьбовыми резцами.
Конструкция резцов для нарезания резьбы. Профиль режущей части резца должен соответствовать профилю резьбы. Угол режущей части для метрической резьбы должен быть 60°, для дюймовой и трубной резьб - 55°. Чтобы избежать при нарезании резьбы искажения ее профиля, резьбовые резцы затачивают по передней поверхности с передним углом у = 0° и устанавливают вершину резца на высоте линии центров станка; на резцах для черновых проходов передний угол равен от 5 до 25° в зависимости от механических свойств обрабатываемого материала; задний угол на боковых поверхностях резца - от 5 до 10°.
Типы резцов
Различают резьбовые резцы для нарезания наружной резьбы (рис. 215, а) и резцы для нарезания внутренней резьбы (рис. 215, б). Те и другие могут быть цельными или вставными. Головка резьбового резца для внутренней резьбы должна быть
Рис. 215. Резцы для нарезания треугольной резьбы: а - наружной, б - внутренней
перпендикулярна оси стержня резца. Длина и сечение стержня зависят от диаметра отверстия.
Токарь-новатор В. К. Семинский для нарезания внутренних резьб применяет специальные резьбовые резцы. У этих резцов (рис. 216) головка повернута относительно стержня путем
Рис. 216. Резьбовой резец для нарезания внутренней резьбы конструкции В. К. Семинского
скручивания державки на 45°. Это придает резцу повышенную жесткость и обеспечивает более спокойную работу по сравнению с обычным резьбовым резцом (рис. 215, б).
Чистовой проход
Для чистовых проходов при нарезании резьб иногда применяют пружинящие державки и пружинящие резцы, позволяющие получать чистую и гладкую резьбу. Такой резец, встречая на своем пути более твердую часть металла, слегка отжимается и не портит резьбы.
Рис. 217. Пружинящая державка с резьбовым резцом
На рис. 217 показана пружинящая державка 1. Болт 2 служит для крепления вставного резьбового резца 3 в державке. Особенность этой державки в том, что она может работать и как пружинящая, и как жесткая. Это достигается при помощи винта 4: когда винт затянут, державка работает как жесткая; когда вин г отпущен, она работает как пружинящая.
Черновое нарезание производят резцом, закрепленным в жесткой державке, а чистовое - резцом, закрепленным в пружинящей державке.
Рис. 218. Установка резьбового резца: а - правильная, б - неправильная
Установка резца
Устанавливают резьбовой резец точно на высоте центров, иначе профиль резьбы получится неправильным. Кроме того, средняя линия профиля резца должна быть перпендикулярна к оси детали (рис. 218, а).
Эти требования остаются в силе при нарезании не только наружных, но и внутренних резьб. Если пренебречь этими требованиями, то профиль резьбы окажется повернутым в сторону (несимметричным), как показано на рис. 218, б.
Резьбовой резец устанавливают при помощи шаблона, как показано на рис. 219 (при нарезании наружной резьбы) и на рис. 220 (при нарезании внутренней резьбы).
Правильность установки
Правильность установки резьбового резца по шаблону проверяют так: прикладывают шаблон к цилиндрической
поверхности детали в горизонтальной плоскости точно на высоте оси детали, затем вводят резец в вырез шаблона и на просвет определяют, есть ли зазор между его режущими кромками и вырезом. Если зазор имеется, то перестановкой резца его устраняют, после чего резец прочно закрепляют в резцовой головке. При установке резца для нарезания внутренней резьбы шаблон можно устанавливать также по торцу детали (см. рис. 220).
Рис 219. Установка резьбового резца по шаблону при нарезании наружной резьбы
Проверка шаблонами
Рис. 220. Установка резьбового резца по шаблону при нарезании внутренней резьбы
Шаблонами (см. рис. 219 и 220) проверяют также правильность заточки резьбовых резцов.
Похожие материалы
www.metalcutting.ru
Резцы для нарезания внутренней резьбы — КиберПедия
Такими резцами для токарного станка можно нарезать резьбу только в отверстии большого диаметра, что объясняется их конструктивными особенностями. Внешне они напоминают расточные резцы для обработки глухих отверстий, но не стоит их путать, так как они принципиально отличаются друг от друга.
Резцы для нарезания внутренней резьбы
Расточные резцы для обработки глухих отверстий
Расточными резцами, режущая пластина которых имеет треугольную форму (как и у подрезных), выполняют обработку глухих отверстий. Рабочая часть инструментов этого типа выполнена с изгибом.
Расточные резцы для глухих отверстий
Расточные резцы для обработки сквозных отверстий
Такими резцами, рабочая часть которых выполнена с изгибом, обрабатываются сквозные отверстия, предварительно полученные при помощи сверления. Глубина отверстия, которое можно обработать на станке при помощи инструмента данного вида, зависит от длины его державки. Слой металла, который снимается при этом, приблизительно равен величине отгиба его рабочей части.
Расточные резцы для сквозных отверстий
Сверла
Части и элементы спирального сверла
Сверление — высокопроизводительный способ обработки отверстий, однако обеспечивает невысокую точность размера (до 5 км.) и шероховатость только до третьего класса.Наиболее распространенным инструментом для сверления является спиральное сверло. Сверло состоит из рабочей части, шейки и хвостовика (картинка 1). Часть сверла, на которой расположены две режущие кромки, называется режущей частью. Угол между режущими кромками (для обработки стали и чугуна) обычно составляет 118—120°.На рабочей части сверла имеются два спиральных пера, связанные перемычкой. На наружной поверхности перьев прошлифованы узкие направляющие ленточки. Между перьями расположены две спиральные канавки. Одна из стенок каждой канавки образует переднюю поверхность режущею клипа сверла. По канавкам к режущим кромкам подается охлаждающая жидкость и по ним же стружка выходит из отверстия. Хвостовик служит для закрепления сверла. Хвостовик может иметь коническую и цилиндрическую форму. Конический хвостовик выполняется по стандарту (конус Морзе № I, 2, 3, 4, 5).
Картинка 2. Закрепление сверла при помощи переходной втулки. 1-сверло, 2-переходная втулка
Картинка 3. Патрон для закрепления сверл. а-общий вид, б-разрез, в-ключ. 1-хвостовик, 2-корпус, 3-обойма, 4-резьбовое кольцо(гайка), 5-кулачек
Конус хвостовика обеспечивает надежное центрирование сверла и удерживание ею от проворачивания. Если конус хвостовика сверла обличается по размеру (номеру) от конусного отверстия пиноли задней бабки, то применяют переходные втулки (картинка 2). Сверла с цилиндрическими хвостовиками закрепляют в пиноли задней бабки при помощи сверлильных патронов. Простейший кулачковый сверлильный патрон показан на картинке 3. а, б. В корпусе 2 патрона наклонно расположены три кулачка, имеющие наружную резьбу. На эту резьбу навертывается гайка 4, связанная с обоймой 3, которую вращают зубчатым ключом (картинка 3, в), вставляемы в отверстие корпуса патрона. При вращении ключа вращается и обойма, а с нею гайка, что заставляет кулачки перемещаться по наклонным гнездам и при этом сходиться, закрепляя сверло, или расходиться, освобождая его.
Рабочая часть сверла изготовляется из инструментальной стали, а шейка и хвостовик — из конструкционной стали; обе части соединены сваркой.
Картинка 4. Твердосплавные сверла
Картинка 5. Сверло Овчинниковас внутренними каналами для охлаждения
Для обработки твердых материалов применяют сверла, оснащенные твердым сплавом в виде впаянной пластинки (картинка 4, а) пли припаянной спиральной коронки (картинка 4, б). Твердосплавные сверла диаметром до 8 мм изготовляют цельными и впаивают в стальные хвостовики (картинка 4, в).
Высокую стойкость имеют сверла конструкции Овчинникова с внутренним подводом охлаждающей жидкости (картинка 5, а, б). В каждом пере сверла проходит сквозное отверстие, оба отверстия соединяются в хвостовике, образуя центральный канал. Через специальный патрон жидкость от насоса поступает в хвостовик сверла, затем по каналам к режущим кромкам, охлаждает и принудительно удаляет стружку из отверстия.
Развертки
Развертки – вид металлорежущего инструмента, используемого для технологического процесса обработки металла, называемого развертыванием. Развертывание применяется для растачивания подготовленных отверстий с целью получения более высокого их качества (чистоты) и точности соблюдения геометрических размеров при их обработке. За счет того, что класс точности разверток значительно выше, чем у сверл, при помощи развертывания удается получить отверстие с классом чистоты обработки поверхности 7-8 и классом точности 2-3. С помощью разверток производится однократная или, в некоторых случаях, многократная (черновая, промежуточная и чистовая) обработка цилиндрических и конических отверстий, имеющих небольшую шероховатость, с целью получения требуемых параметров точности и чистоты.
Развертки изготавливаются из быстрорежущих сталей марок 9XC, Р6М5, Р9 и Р18 (обладают лучшими качествами).
cyberpedia.su
Инструмент для нарезания резьбы: метчики, плашки, клупп, гребенка
Резьбовой тип соединения на сегодняшний день получил самое широкое распространение. Он применяется в машиностроении и других сферах производства, характеризуется высокой надежностью и простой в изготовлении. При желании можно провести нарезание витков при помощи специальных инструментов, которые характеризуются практичностью и универсальностью в применении.

Инструмент для нарезания резьбы
Общая информация о резьбонарезании
Выбирая инструмент для нарезания резьбы следует учитывать особенности резьбовых поверхностей. К ним можно отнести следующие моменты:
- Нарезание витков проводится механическим путем при применении специального оборудования. При снятии металла образуются канавки и витки, которые идеально сочетаются с поверхностью второго элемента.
- Все применяемые инструменты для нарезания резьбы и технологии можно условно разделить на две категории: ручные и автоматизированные. На протяжении длительного периода использовали станки токарно-винторезной группы.
- На момент использования ручных инструментов при резьбонарезании нужно использовать смазку. Она существенно продлевает срок службы приспособлений, упрощает сам процесс резьбонарезания.
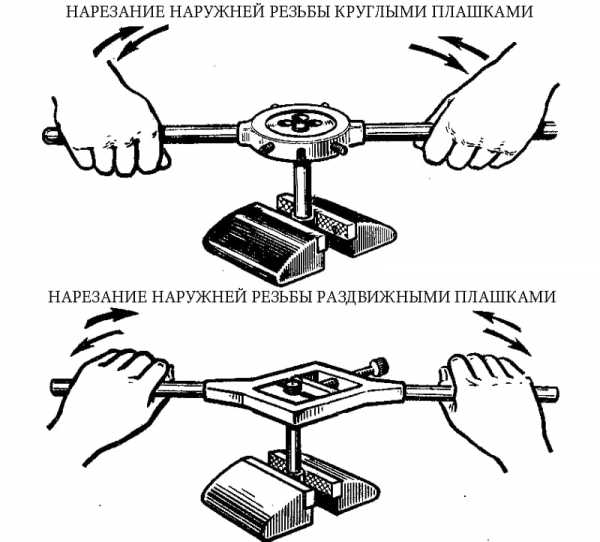
Нарезание резьбы разными видами плашек
Стоит учитывать, что ручные варианты исполнения имеют внутреннюю поверхность, которая и определяет размеры витков и шах их расположения. В случае обработки на токарно-винторезном станке, параметры будущей резьбовой поверхности определяются подачей и скоростью перемещения суппорта.
Фасонные резцы для нарезания резьбы
При использовании токарно-винторезного оборудования для нарезания резьбы следует подобрать наиболее подходящий резец. Производители выпускают специальные варианты исполнения резцов для нарезки резьбы, которые характеризуются своими определенными особенностями:
- При производстве создается режущая часть определенной формы. За счет этого образуется канавка требуемой формы.
- Режущая часть изготавливается из инструментальной стали, которая подвергается закалке. За счет этого при работе исключается вероятность быстрого износа режущей кромки.
- Применение рассматриваемого метода позволяет обрабатывать поверхности крупных заготовок.
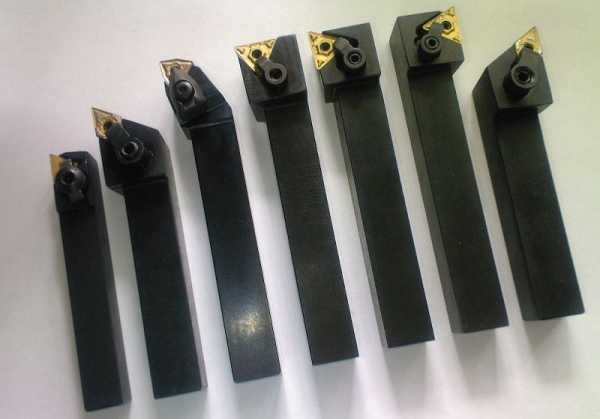
Фасонные резцы
В производственных цехах часто используется именно токарно-винторезный станок, так как плашек и метчиков для работы с заготовками большого диаметра практически нет. Кроме этого, при резьбонарезании возникает серьезная нагрузка.
Резьбовые гребенки для повышения производительности труда
Некоторые инструмент для нарезки резьбы характеризуются высокой эффективностью при применении. Примером можно назвать резьбовые гребенки, которые можно использовать для получения витков практически любых размеров. Их достоинствам можно отнести следующие моменты:
- Простая конструкция.
- Универсальность в применении.
- Высокая эффективность.
- Технологичность.
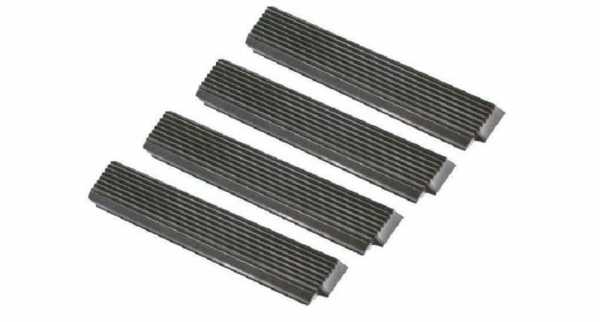
Резьбовые гребенки
Гребенки представлены многониточными фасонными резцами, которые бывают призматического, круглого и стержневого типа. Чаще всего они применяются для нарезания резьбы с мелким шагом и небольшой высотой профиля.
Метчики, плашки и головки для резьбонарезания
Наибольшее распространение получили ручные инструменты для резьбонарезания. Они могут применяться в промышленности и быту.
Наибольшее распространение получили следующие варианты исполнения:
- Подобные инструменты применяются для изготовления болтов и шпилек. Подобное изделие представляет собой шайбу круглой формы, внутри которой выступает несколько ребер. Внешняя резьба может формироваться и калиброваться всего за один проход. В продаже встречаются различные варианты исполнения инструментов, при изготовлении применяется закаленная инструментальная сталь.
- Метчики используются для получения внутренней резьбы. Он также изготавливается при применении закаленной инструментальной стали, которая характеризуется высокой износоустойчивостью. Метчик имеет форму стержня, рабочая часть которого имеет несколько впадин и выступающих граней. За счет этого существенно упрощается процесс резьбонарезания.
- Специальные головки также могут применяться для проведения рассматриваемой работы. Они могут иметь различные размеры, применяются в паре со специальной державкой.
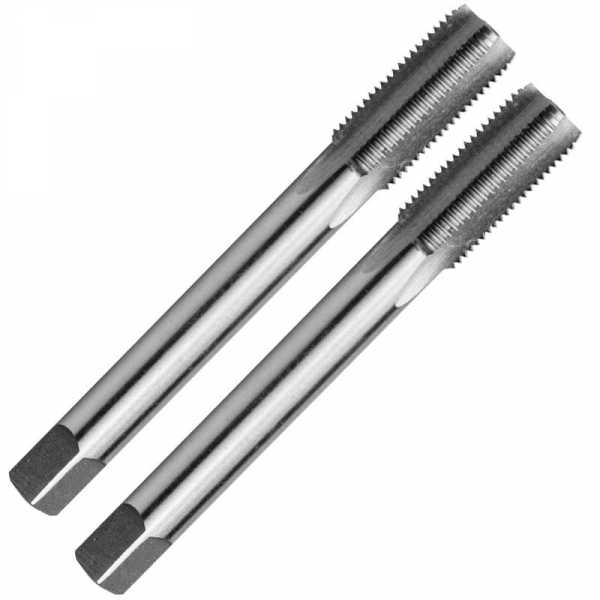
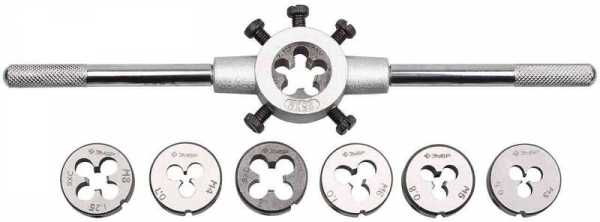
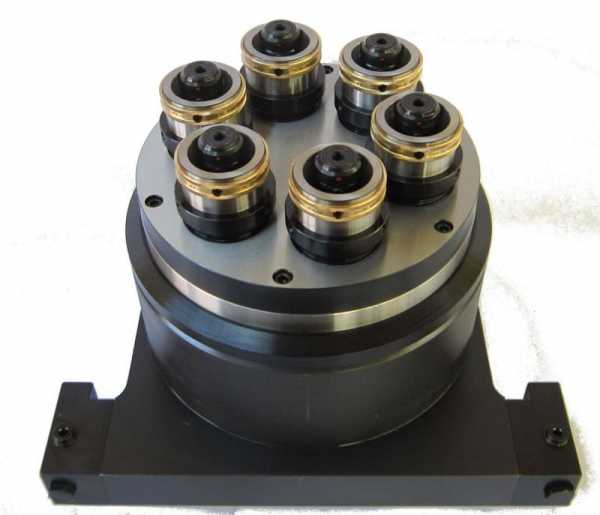
Стоимость ручных инструментов невысокая, при этом они характеризуются высокой эффективностью в применении.
Как правильно нарезать витки на водопроводной трубе
Рекомендации по нарезанию витков на водопроводной трубе во многом связаны с тем, какая именно технология применяется. Ручной инструмент для нарезания наружной резьбы должен применяться с учетом следующей информации:
- Нужно применять смазывающие вещества, которые добавляются в зону резания для снижения степени износа режущей кромки.
- На момент работы нужно следить за тем, чтобы инструмент был расположен строго перпендикулярно заготовке. При его смещении витки могут быть расположены друг относительно друга неправильно.
- При резьбонарезаии уделяется внимание тому, чтобы с зоны резания своевременно удалялась стружка.
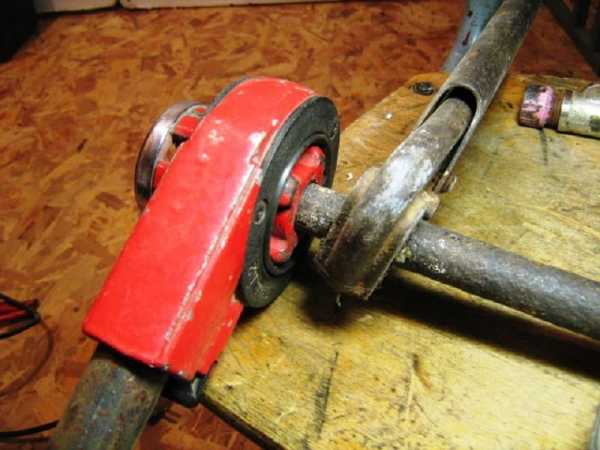
Нарезание резьбы на водопроводной трубе
Рассматриваемая работа может проводится и в бытовых условиях.
Работа плашкой
Плашки применяются для обработки наружной цилиндрической поверхности. Среди особенностей ее применения можно отметить следующие моменты:
- Заготовка закрепляется в тисках. Во время работы она должна находится в неподвижном состоянии.
- Перед применением инструмента режущая кромка и обрабатываемая поверхность смазываются маслом.
- Как правило, на торцевой поверхности создается небольшая фаска. Она упрощает процесс навинчивания плашки на обрабатываемую поверхность.
- Во время работы нужно уделить внимание тому, чтобы плашка не смещалась. Из-за этого резьба может нарезаться неравномерно, ход плашки становится более тяжелым.
- На 2-3 витка по ходу резьбы делается один оборот в обратном направлении. Подобным образом обеспечивается удаление стружки с зоны обработки, повышается качество получаемой поверхности.
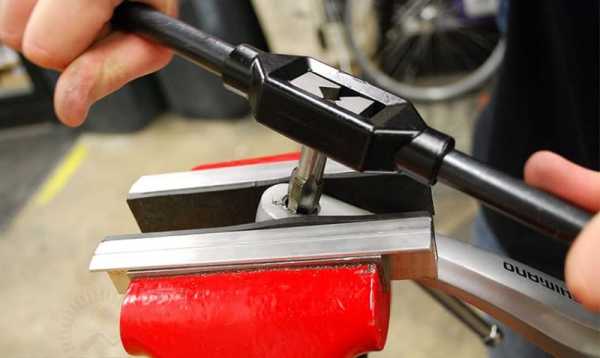
Работа плашкой
После завершения работы проверяется качество рабочей поверхности. Для этого достаточно накрутить гайку, у которой должен быть свободный ход.
Работа клуппом
Для проведения рассматриваемой работы может использовать клупп. Он напоминает плашку, но при этом имеет большие размеры. Зачастую он применяется для нарезания резьбы на трубах, поставляется в специальных наборах с рукоятками. Среди особенностей применения отметим:
- Клуппом характеризуется высокой эффективностью, поэтому процесс нарезания витков упрощается.
- Инструкция по использованию плашки и клуппа практически идентична, разница заключается лишь в том, какое усилие нужно прикладывать для получения требуемого результата.
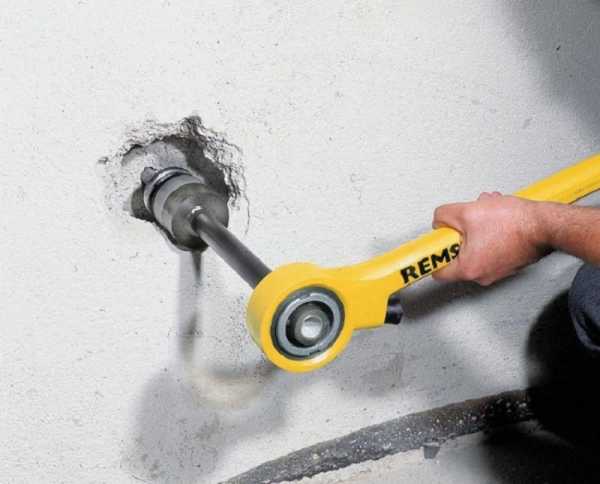
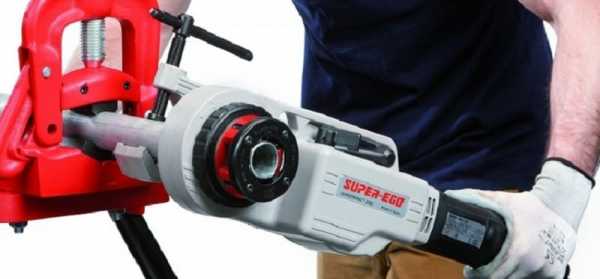
Набор для нарезания резьбы зачастую представлен сочетанием насадок различных диаметров. При изготовлении рабочей части также используется износостойкий материал, который не тупится при длительном применении.
Если вы нашли ошибку, пожалуйста, выделите фрагмент текста и нажмите Ctrl+Enter.
stankiexpert.ru
Нарезание резьбы резцами
Наиболее распространенным способом нарезания резьбы на токарно-винторезных станках является нарезание резьбовыми резцами.
Конструкция резцов для нарезания резьбы. профиль режущей части резца должен соответствовать профилю резьбы. Угол режущей части для метрической резьбы должен быть 60°, для дюймовой и трубной резьб - 55°. Чтобы избежать при нарезании резьбы искажения ее профиля, резьбовые резцы затачивают по передней поверхности с передним углом γ=0° и устанавливают вершину резца на высоте линии центров станка; на резцах для черновых проходов передний угол равен от 5 до 25° в зависимости от механических свойств обрабатываемого материала; задний угол на боковых поверхностях резца - от 5 до 10°.
Различают резьбовые резцы для нарезания наружной резьбы (рис. 215, а) и резцы для нарезания внутренней резьбы (рис. 215, б). Те и другие могут быть цельными или вставными. Головка резьбового резца для внутренней резьбы должна быть перпендикулярна оси стержня резца. Длина и сечение стержня зависят от диаметра отверстия.
Токарь-новатор В.К. Семинский для нарезания внутренних резьб применяет специальные резьбовые резцы. У этих резцов (рис. 216) головка повернута относительно стержня путем скручивания державки на 45°. Это придает резцу повешенную жесткость и обеспечивает более спокойную работу по сравнению с обычным резьбовым резцом.
Для чистовых проходов при нарезании резьб иногда применяют пружинящие державки и пружинящие резцы, позволяющие получать чистую и гладкую резьбу. Такой резец, встречая на своем пути более твердую часть металла, слегка отжимается и не портит резьбы.
На рис. 217 показана пружинящая державка 1. Болт 2 служит для крепления вставного резьбового резца 3 в державке. Особенность этой державки в том, что она может работать и как пружинящая, и как жесткая. это достигается при помощи винта 4: когда винт затянут, державка работать как жесткая; когда винт отпущен, она работает как пружинящая.
Устанавливают резьбовой резец точна на высоте центров, иначе профиль резьбы получится неправильным. Кроме того, средняя линия профиля резца должна быть перпендикулярно к оси детали (рис. 218, а). Эти требования остаются в силе при нарезании не только наружных, но и внутренних резьб. Если пренебречь этими требованиями, то профиль резьбы окажется повернутым в сторону (несимметричным), как показано на рис. 218, б.
Резьбовой резец устанавливают при помощи шаблона, как показано на рис. 219 (при нарезании наружной резьбы) и на рис. 220 (при нарезании внутренней резьбы).
Правильность установки резьбового резца по шаблону проверяют так: прикладывают шаблон к цилиндрической поверхности детали в горизонтальной плоскости точно на высоте оси детали, затем вводят резец в вырез шаблона и на просвет определяют, есть ли зазор между его режущими кромками и вырезом. Если зазор имеется, то перестановкой резца его устраняют, после чего резец прочно закрепляют в резцовой головке. При установке резца для нарезания внутренней резьбы шаблон можно устанавливать также по торцу детали (см. рис. 220).
Шаблонами проверяют также правильность заточки резьбовых резцов.
machinetools.aggress.ru
Нарезание резьбы резцами и гребенками — Мегаобучалка
а б Рис. 71. Схемы нарезания резьбы резцами: а – наружной; б - внутренней |
Резьбовые резцы и гребенки применяются для нарезания наружных и внутренних резьб точением, являющимся самым универсальным способом изготовления резьб различных видов в широком диапазоне диаметров, шагов и обрабатываемых материалов. Схемы нарезания наружной и внутренней резьбы однониточными резцами и схемы движения резцов приведены на рис. 71.
Заготовка 1 закрепляется на шпинделе станка и получает вращение со скоростью , а резец закрепляется на суппорте 2 и получает продольную подачу (II), равную шагу нарезаемой резьбы, посредством ходового винта 4 через маточную гайку, закрепленную в фартуке станка. Предварительно резец перемещается в поперечном (радиальном) направлении (I) на 0,2…0,5 мм.
Когда резец пройдет длину нарезаемой резьбы (см. рис. 71, а), он отводится (III) от заготовки и возвращается в исходное положение (IV). Затем резец снова врезается в заготовку на несколько десятых долей миллиметра и цикл повторяется до образования полного профиля резьбы.
а б в Рис. 72. Схемы образования профиля резьбы резцами: а – радиальное врезание; б – врезание под углом; в – комбинированное врезание |
Для обеспечения возможности вывода резца из зоны резания на заготовке предварительно прорезается канавка 3.
Схемы образования профиля резьбы резцами приведены на рис. 72. Сплошными стрелками показано движение продольной подачи, пунктирными – движение врезания.
Радиальное врезание (см. рис. 72, а) применяется при чистовой обработке, а врезание под углом (см. рис. 72, б) – при черновой. При комбинированном врезании подача на предварительных проходах осуществляется под углом, а на окончательных проходах – методом радиальной подачи.
Нарезание резьбы однониточным резцом обеспечивает получение 5…6 степеней точности, что выше по сравнению с другими способами нарезания, за исключением резьбошлифования.
Резьбовые резцы изготавливаются как из быстрорежущих сталей, так и из твердых сплавов.
Однониточные резьбовые резцы бывают стержневые (рис. 73), призматические (рис. 74) и круглые (рис. 75). Стержневые резцы просты по конструкции, однако не обеспечивают более 3…5 переточек. Призматические резцы конструктивно более сложные, но позволяют выполнить большее число переточек. Более широкое распространение в промышленности получили круглые резьбовые резцы из-за простоты их изготовления и большого количества
Рис. 73. Стержневой резьбовой резец |
Рис. 74. Призматический резьбовой резец |
Рис. 75. Круглый резьбовой резец |
переточек. Передний угол на круглых резцах обеспечивается заточкой (см. рис. 75), а задний угол обеспечивается за счет установки оси резца выше оси обрабатываемой детали на величину :
; .
На рис. 76. представлена рабочая часть стержневого резьбового резца со стандартной геометрией. Заточка передней поверхности с положительным передним углом весьма затруднена. Обычно передний угол в резьбовых резцах равен 0о.
![]() |
Задние углы по вершине и боковым режущим кромкам и для обработки чугуна и стали рекомендуется принимать равными 8о. Для расточных резцов задний угол по вершине увеличивается до 12о [3]. В ряде случаев при обработке труднообрабатываемых материалов . В этом случае для получения точного профиля резьбы проводят либо коррекцию инструмента, либо имеют черновой и чистовой резцы. У чистового резца .
Рис. 77. Стержневая резьбовая гребенка |
При нарезании резьбы резцом происходит разваливание резьбы. Поэтому на резце делают угол профиля на 0,5…1о меньше, чем угол профиля резьбы. При нарезании метрической резьбы чистовой резец имеет угол .
Наряду с однониточными резьбовыми резцами широкое применение находят и многониточные резьбовые резцы, которые называют резьбовыми гребенками. На рис. 77 представлена стержневая резьбовая гребенка. Особенность гребенок – совмещение нескольких однониточных резцов, профиль которых соответствует профилю нарезаемой резьбы. Первые две-три нитки срезаются на угол , образуя режущую (заборную) часть. Остальные образуют калибрующую часть гребенки. Наличие заборной части ведет к перераспределению нагрузки в процессе резания между несколькими зубьями, что позволяет увеличить глубину резания, уменьшить число проходов и, следовательно, повысить производительность обработки.
megaobuchalka.ru
Нарезание резьбы резцами и гребенками
Треугольную резьбу часто нарезают на токарно-винторезных станках резьбовыми резцами, т. е. резцами обычного типа, заточенными под требуемым углом (60° для метрической резьбы и 55° — для дюймовой). Получение профиля резьбы обеспечивается соответствующим профилем резьбового резца, который должен быть заточен очень точно, и правильной установкой резца относительно детали: резец должен быть расположен строго перпендикулярно оси станка, так как в противном случае резьба получится косой; кроме того, передняя поверхность резца должна быть расположена на высоте центров станка. При другом ее положении резьба будет нарезана с неправильным углом.
Высокие требования, предъявляемые к заточке резцов и сохранению правильного профиля, привели к внедрению в производство фасонных резьбовых резцов — призматических (рис. 3.58, а) «круглых (дисковых) (рис. 3.58, б). У этих резцов размеры элементов профиля резьбы выдерживаются более точно, чем у обычных, так как такие резьбовые резцы затачиваются по передней поверхности, а отшлифованные при изготовлении задние (боковые) поверхности сохраняют профиль неизменным.
Для улучшения качества поверхности резьбы часто применяют пружинные державки (рис. 3.58, в). Некоторые заводы применяют многорезцовые резьбовые головки. Трехрезцовая головка, представленная на рис. 3.58, г, состоит из корпуса 3, к которому болтом прикрепляется трехрезцовая пластина (отдельно показана на рис. 3.58, д). По мере затупления одного из резцов пластина перезакрепляется так, чтобы в работе был новый, незатупившийся резец. Для этой цели в корпусе имеется штифт 2 (рис. 3.58, г), по которому пластина фиксируется своими тремя точно расположенными цилиндрическими отверстиями. Применение многорезцовых головок наиболее целесообразно в условиях серийного производства.
При нарезании резьбы одним резцом режущая кромка его вследствие быстрого притупления теряет форму, поэтому рекомендуется черновые ходы производить одним резцом с менее точным профилем, а чистовые ходы — чистовым резцом.
При нарезании резьбы на производстве широко применяются твердосплавные резьбовые резцы со специальной заточкой, значительно повышающие режимы резания.
Рисунок 3.58. Резцы для нарезания резьбы:
а — призматический; б — круглый; в — пружинная державка; г — трехрезцовая головка; д — трехрезцовая пластина
При скоростном нарезании резьбы происходит небольшое искажение ее профиля: угол профиля нарезаемой резьбы получается всегда больше угла при вершине резца на 30'—1°30'. Поэтому рекомендуется в этих условиях применять резцы с углом профиля, равным углу профиля нарезаемой резьбы, уменьшенному на 1°. Например, для нарезания метрической резьбы с углом профиля 60° угол профиля чистового резца принят 59°.
Применяют также нарезание резьбы за один проход, используя одновременно три резца, оснащенных твердым сплавом и в совокупности (рис.3.59) напоминающих гребенку; черновой резец 1 имеет угол профиля 70°, получистовой резец 2 — 65° и чистовой резец 3 — 59°.
Рисунок 3.59. Три резца для одновременного
нарезания резьбы за один проход
Нарезание резьбы резцом производится за много ходов в зависимости от требуемой точности, диаметра резьбы и твердости материала нарезаемой детали.
Необходимо заметить, что применение высоких скоростей резания при нарезании наружной и внутренней резьб в упор, в тех случаях когда на станке нет специальных автоматических упоров, ограничивающих ход суппорта, часто приводит к браку детали. Происходит это потому, что при большом числе оборотов шпинделя рабочий не всегда успевает отвести резец по окончании прохода.
Значительно облегчается работа, когда для быстрого отвода резца используются специальные устройства, особенно автоматические.
В крупносерийном и массовом производстве, а также и в специализированном серийном производстве резьбу часто нарезают на станках, работающих по автоматическому циклу.
В полуавтоматах для скоростного нарезания резьб подача на глубину, рабочий и ускоренный ход, отвод резца и подача его в исходное положение осуществляются системой кулачковых, храповых и рычажных механизмов.
Рисунок3.60 Коррекционное устройство для нарезания точной резьбы |
При нарезании точной резьбы на станках часто применяют специальные коррекционные устройства, которые компенсируют ошибки шага ходового винта. Эти устройства автоматически вводят поправки на точность ходового винта путем дополнительного поворота маточной гайки. Схема такого устройства показана на рисунке3.60. Перемещение резца 1 относительно нарезаемой детали 2 определяется перемещением маточной гайки 3 от ходового винта 4 и дополнительным поворотом ее от коррекционной линейки 5 через рейку 6 и зубчатое колесо 7.
Нарезание прямоугольной и трапецеидальной резьб является более сложной работой в сравнении с нарезанием треугольных резьб. Резьбы прямоугольного и трапецеидального профиля изготовляют как однозаходными, так и многозаходными. При нарезании таких резьб для установки резцов по углу подъема винтовой линии токари применяют специальные державки. На рис. 3.61 показана одна из таких державок, состоящая из поворотной части 2 и корпуса 5. В поворотной части имеется гнездо для резца 1, закрепляемого винтом 3. На поворотной части державки имеется буртик 4, на котором нанесена шкала с градусными делениями; с помощью этой шкалы можно отсчитывать поворот согласно углу подъема винтовой линии резьбы, не производя специальной заточки резца. При повертывании болта 7 поворотная часть 2 державки закрепляется винтом 6. Для повышения производительности труда при нарезании трапецеидальных резьб с крупным шагом применяют державку с двумя резцами (рисунок 3.62) — прорезным 1 и профильным 2, установленными один от другого на расстоянии, равном шагу нарезаемой резьбы.
Рисунок 3.62. Державка сдвумя резцами для нарезания трапецеидальной резьбы |
Рисунок3.61. Специальная державка
для нарезания прямоугольной и
трапецеидальной резьбы
На рисунке 3.63, а показано последовательное нарезание трапецеидальной резьбы тремя резцами.
На рисунке 3.63 б, в показаны приемы нарезания прямоугольной резьбы двумя и тремя резцами.
Рисунок 3.63 Приемы нарезания резьбы:
а — трапецеидальной тремя резцами; б — прямоугольной двумя резцами; в — прямоугольной тремя резцами
Применение для нарезания резьбы гребенок сокращает время нарезания и, таким образом, увеличивает производительность резьбонарезания. При нарезании резьбы гребенкой работа резания распределяется между несколькими зубьями; для этой цели концы зубьев стачиваются от одного края гребенки к другому, так что глубина резания постепенно увеличивается. Особенно целесообразно и экономично i применять гребенки при изготовлении больших партий одинаковых деталей.Гребенки нельзя применять при нарезании деталей, у которых резьба доходит до выступа или буртика, так как часть резьбы, находящаяся ближе к буртику, не получит полного профиля. Для точных резьб гребенки не применяются, так как они не могут дать высокой точности; их можно использовать только для предварительного нарезания.
Гребенки бывают плоские, тангенциальные и дисковые с кольцевыми и винтовыми канавками. Плоские гребенки применяются для нарезания треугольной резьбы с малым углом подъема: тангенциальные — для нарезания треугольной резьбы с большим углом подъема; они снабжены резьбой, обратной по отношению к резьбе обрабатываемой детали; если эта деталь должна иметь левую резьбу, то резьба гребенки — правая, и наоборот.
Круглые (дисковые) гребенки, так же как и круглые (дисковые) резцы, имеют то преимущество, что они затачиваются только по передней поверхности, допускают большое число переточек и, значит, имеют большой срок службы; благодаря этому они удобны в эксплуатации.
Похожие статьи:
poznayka.org