Термическая обработка (термообработка) стали, сплавов, металлов. Стали 45 отпуск
№ п/п | Марка стали | Твёрдость (HRCэ) | Температ. закалки, град.С | Температ. отпуска, град.С | Температ. зак. ТВЧ, град.С | Температ. цемент., град.С | Температ. отжига, град.С | Закал. среда | Прим. |
1 | 2 | 3 | 4 | 5 | 6 | 7 | 8 | 9 | 10 |
1 | Сталь 20 | 57…63 | 790…820 | 160…200 |
| 920…950 |
| Вода |
|
2 | Сталь 35 | 30…34 | 830…840 | 490…510 |
|
|
| Вода |
|
33…35 | 450…500 |
|
|
|
| ||||
42…48 | 180…200 | 860…880 |
|
|
| ||||
3 | Сталь 45 | 20…25 | 820…840 | 550…600 |
|
|
| Вода |
|
20…28 | 550…580 |
|
|
|
| ||||
24…28 | 500…550 |
|
|
|
| ||||
30…34 | 490…520 |
|
|
|
| ||||
42…51 | 180…220 |
|
|
| Сеч. до 40 мм | ||||
49…57 | 200…220 | 840…880 |
|
|
| ||||
<= 22 |
|
|
|
| 780…820 |
| С печью | ||
4 | Сталь 65Г | 28…33 | 790…810 | 550…580 |
|
|
| Масло | Сеч. до 60 мм |
43…49 | 340…380 |
|
|
| Сеч. до 10 мм (пружины) | ||||
55…61 | 160…220 |
|
|
| Сеч. до 30 мм | ||||
5 | Сталь 20Х | 57…63 | 800…820 | 160…200 |
| 900…950 |
| Масло |
|
59…63 |
| 180…220 | 850…870 | 900…950 |
| Водный раствор | 0,2…0,7% поли-акриланида | ||
"-- |
|
|
|
| 840…860 |
|
| ||
6 | Сталь 40Х | 24…28 | 840…860 | 500…550 |
|
|
| Масло |
|
30…34 | 490…520 |
|
|
|
| ||||
47…51 | 180…200 |
|
|
| Сеч. до 30 мм | ||||
47…57 |
| 860…900 |
|
| Водный раствор | 0,2…0,7% поли-акриланида | |||
48…54 |
|
|
|
|
| Азотирование | |||
<= 22 |
|
|
|
| 840…860 |
|
| ||
7 | Сталь 50Х | 25…32 | 830…850 | 550…620 |
|
|
| Масло | Сеч. до 100 мм |
49…55 | 180…200 |
|
|
| Сеч. до 45 мм | ||||
53…59 | 180…200 | 880…900 |
|
| Водный раствор | 0,2…0,7% поли-акриланида | |||
< 20 |
|
| |
| 860…880 |
|
| ||
8 | Сталь 12ХН3А | 57…63 | 780…800 | 180…200 |
| 900…920 |
| Масло |
|
50…63 |
| 180…200 | 850…870 |
| Водный раствор | 0,2…0,7% поли-акриланида | |||
<= 22 |
|
|
|
| 840…870 |
| С печью до 550…650 | ||
9 | Сталь 38Х2МЮА | 23…29 | 930…950 | 650…670 |
|
|
| Масло | Сеч. до 100 мм |
<= 22 |
| 650…670 |
|
|
|
| Нормализация 930…970 | ||
HV > 670 |
|
|
|
|
|
| Азотирование | ||
10 | Сталь 7ХГ2ВМ | <= 25 |
|
|
|
| 770…790 |
| С печью до 550 |
28…30 | 860…875 | 560…580 |
|
|
| Воздух | Сеч. до 200 мм | ||
58…61 | 210…230 |
|
|
| Сеч. до 120 мм | ||||
11 | Сталь 60С2А | <= 22 |
|
|
|
| 840…860 |
| С печью |
44…51 | 850…870 | 420…480 |
|
|
| Масло | Сеч. до 20 мм | ||
12 | Сталь 35ХГС | <= 22 |
|
|
|
| 880…900 |
| С печью до 500…650 |
50…53 | 870…890 | 180…200 |
|
|
| Масло |
| ||
13 | Сталь 50ХФА | 25…33 | 850…880 | 580…600 |
|
|
| Масло |
|
51…56 | 850…870 | 180…200 |
|
|
| Сеч. до 30 мм | |||
53…59 |
| 180…220 | 880…940 |
|
| Водный раствор | 0,2…0,7% поли-акриланида | ||
14 | Сталь ШХ15 | <= 18 |
|
|
|
| 790…810 |
| С печью до 600 |
59…63 | 840…850 | 160…180 |
|
|
| Масло | Сеч. до 20 мм | ||
51…57 | 300…400 |
|
|
| |||||
42…51 | 400…500 |
|
|
| |||||
15 | Сталь У7, У7А | НВ <= 187 |
|
|
|
| 740…760 |
| С печью до 600 |
44…51 | 800…830 | |
|
|
| Вода до 250, масло | Сеч. до 18 мм | ||
55…61 | 200…300 |
|
|
| |||||
61…64 | 160…200 |
|
|
| |||||
61…64 | 160…200 |
|
|
| Масло | Сеч. до 5 мм | |||
16 | Сталь У8, У8А | НВ <= 187 |
|
|
|
| 740…760 |
| С печью до 600 |
37…46 | 790…820 | 400…500 |
|
|
| Вода до 250, масло | Сеч. до 60 мм | ||
61…65 | 160…200 |
|
|
| |||||
61…65 | 160…200 |
|
|
| Масло | Сеч. до 8 мм | |||
61…65 |
| 160…180 | 880…900 |
|
| Водный раствор | 0,2…0,7% поли-акриланида | ||
17 | Сталь У10, У10А | НВ <= 197 |
|
|
|
| 750…770 |
|
|
40…48 | 770…800 | 400…500 |
|
|
| Вода до 250, масло | Сеч. до 60 мм | ||
50…63 | 160…200 |
|
|
| |||||
61…65 | 160…200 |
|
|
| | Сеч. до 8 мм | |||
59…65 |
| 160…180 | 880…900 |
|
| Водный раствор | 0,2…0,7% поли-акриланида | ||
18 | Сталь 9ХС | <= 24 |
|
|
|
| 790…810 |
| С печью до 600 |
45…55 | 860…880 | 450…500 |
|
|
| Масло | Сеч. до 30 мм | ||
40…48 | 500…600 |
|
|
| |||||
59…63 | 180…240 |
|
|
| Сеч. до 40 мм | ||||
19 | Сталь ХВГ | <= 25 |
|
|
|
| 780…800 |
| С печью до 650 |
59…63 | 820…850 | 180…220 |
|
|
| Масло | Сеч. до 60 мм | ||
36…47 | 500…600 |
|
|
| |||||
55…57 | 280…340 |
|
|
| Сеч. до 70 мм | ||||
20 | Сталь Х12М | 61…63 | 1000…1030 | 190…210 |
|
|
| Масло | Сеч. до 140 мм |
57…58 | 320…350 |
|
|
| |||||
21 | Сталь Р6М5 | 18…23 |
|
|
|
| 800…830 |
| С печью до 600 |
64…66 | 1210…1230 | 560…570 3-х кратн. |
|
|
| Масло, воздух | В масле до 300…450 град., воздух до 20 | ||
26…29 | 780…800 |
|
|
|
| Выдержка 2…3 часа, воздух | |||
22 | Сталь Р18 | 18…26 |
|
|
|
| 860…880 |
| С печью до 600 |
62…65 | 1260…1280 | 560…570 3-х кратн. |
|
|
| Масло, воздух | В масле до 150…200 град., воздух до 20 | ||
23 | Пружин. сталь Кл. II |
|
| 250…320 |
|
|
|
| После холодной навивки пружин 30-ть минут |
24 | Сталь 5ХНМ, 5ХНВ | >= 57 | 840…860 | 460…520 |
|
|
| Масло | Сеч. до 100 мм |
42…46 |
|
|
| Сеч. 100..200 мм | |||||
39…43 |
|
|
| Сеч. 200..300 мм | |||||
37…42 |
|
|
| Сеч. 300..500 мм | |||||
НV >= 450 |
|
|
| Азотирование. Сеч. св. 70 мм | |||||
25 | Сталь 30ХГСА | 19…27 | 890…910 | 660…680 |
|
|
| Масло |
|
27…34 | 580…600 |
|
|
|
| ||||
34…39 | 500…540 |
|
|
|
| ||||
"-- |
|
|
|
| 770…790 |
| С печью до 650 | ||
26 | Сталь 12Х18Н9Т | <= 18 | 1100…1150 |
|
|
|
| Вода |
|
27 | Сталь 40ХН2МА, 40ХН2ВА | 30…36 | 840…860 | 600…650 |
|
|
| Масло |
|
34…39 | 550…600 |
|
|
|
| ||||
28 | Сталь ЭИ961Ш | 27…33 | 1000…1010 | 660…690 |
|
|
| Масло | 13Х11Н2В2НФ |
34…39 | 560…590 |
|
|
| При t>6 мм вода | ||||
29 | Сталь 20Х13 | 27…35 | 1050 | 550…600 |
|
|
| Воздух |
|
43,5…50,5 | 200 |
|
|
|
| ||||
30 | Сталь 40Х13 | 49,5…56 | 1000…1050 | 200…300 |
|
|
| Масло |
|
infotables.ru
Отпуск закаленных сталей. Температура закалки и отпуска сталей таблица
твердость, режимы, время, температура, технология
При сильном нагреве практически все материалы изменяют свои физические характеристики. В некоторых случаях нагрев проводится целенаправленно, так как подобным образом можно улучшить некоторые эксплуатационные качества, к примеру, твердость. Термическая обработка на протяжении многих лет используется для повышения твердости поверхности стали. Выполнять закалку следует с учетом особенностей металла, так как технология повышения твердости поверхности создается на основании состава материала. В некоторых случаях провести закалку можно в домашних условиях, но стоит учитывать, что сталь относиться к труднообрабатываемым материалам и для придания пластичности нужно проводить сильный нагрев до высоких температур при помощи определенного оборудования. В данном случае рассмотрим особенности нагрева стали 40Х для повышения пластичности и проведения закалки или отпуска.
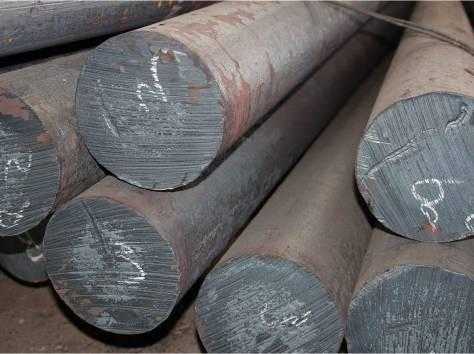
Круг из стали 40Х
Сталь 40Х
Как ранее было отмечено, для правильного проведения закалки и отпуска стали следует учитывать ее состав и многие другие особенности. Выбрать правильно режимы термической обработки можно с учетом следующей информации:
- Рассматриваемая сталь относится к конструкционной легированной группе. Легированная группа характеризуется содержанием большого количества примесей, которые определяют изменение эксплуатационных качеств, в том числе твердости.
- Используется в промышленности при создании валов, осей, штоков, оправок, реек, болтов, втулок, шестерней и других деталей.
- Показатель твердости до проведения термической обработки HB 10-1 = 217 Мпа.
- Температура критических точек определяет момент, при котором сталь 40Х начинает терять свои качества из-за термической обработки: c1= 743 , Ac3(Acm) = 815 , Ar3(Arcm) = 730, Ar1 = 693.
- При температуре отпуска 200 °С HB = 552.
Расшифровка стали 40Х говорит о том, что в составе материала находится 0,40% углерода и 1,5% хрома.
Скачать ГОСТ 4543-71 «Прокат из легированной конструкционной стали 40Х»
Процесс закалки
Процесс обработки высокой температурой стали 40Х и иного сплава называют закалкой. Стоит учитывать, что нагрев выполняется до определенной температуры, которая была определена путем многочисленных испытаний. Время выдержки, после которого проводится охлаждение, а также другие моменты можно узнать из специальных таблиц. Провести нагрев в домашних условиях достаточно сложно, так как в рассматриваемом случае нужно достигнуть температуры около 800 градусов Цельсия.
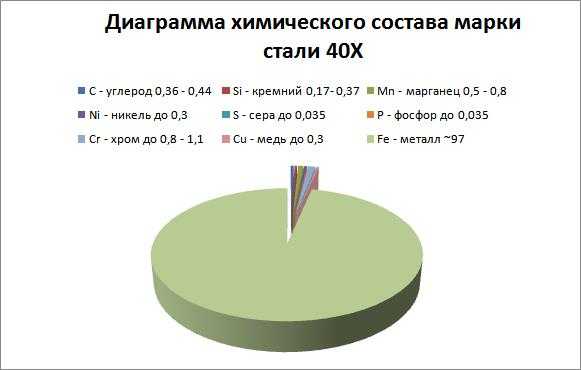
Химический состав стали 40Х
Результатом сильного нагрева и выдержки металла 40Х на протяжении определенного времени с последующим резким охлаждением в воде становится пов
pellete.ru
Отпуск стали | Мир сварки
Отпуск стали
Отпуск заключается в нагреве закаленной стали до температур ниже Ас1 выдержке при заданной температуре и последующем охлаждении с определенной скоростью. Отпуск является окончательной операцией термической обработки, в результате которой, сталь получает требуемые механические свойства. Кроме того, отпуск полностью или частично устраняет внутренние напряжения, возникающие при закалке. Эти напряжения снимаются тем полнее, чем выше температура отпуска. Так, например, осевые напряжения в цилиндрическом образце из стали, содержащей 0,3 % С, в результате отпуска при 550 °С уменьшаются с 60 до 8 кгс/мм2. Так же сильно уменьшаются тангенциальные и радиальные напряжения.
Наиболее интенсивно напряжения снижаются в результате выдержки при 550 °С в течение 15–30 мин. После выдержки в течение 1,5 ч напряжения снижаются до минимальной величины, которая может быть достигнута отпуском при данной температуре.
Скорость охлаждения после отпуска также оказывает большое влияние на величину остаточных напряжений. Чем медленнее охлаждение, тем меньше остаточные напряжения. Быстрое охлаждение от 600 °С создает новые тепловые напряжения. По этой причине изделия сложной формы во избежание их коробления после отпуска при высоких температурах следует охлаждать медленно, а изделия из легированных сталей, склонных к обратимой отпускной хрупкости, после отпуска при 500–650 °С во всех случаях следует охлаждать быстро.
Основное влияние на свойства стали оказывает температура отпуска. Различают три вида отпуска.
Низкотемпературный отпуск стали
Низкотемпературный (низкий) отпуск проводят с нагревом до 150–200 °С, реже до 240–250 °С. При этом снижаются внутренние напряжения, мартенсит закалки переводится в отпущенный мартенсит, повышается прочность и немного улучшается вязкость без заметного снижения твердости. Закаленная сталь (0,5–1,3% С) после низкого отпуска сохраняет твердость в пределах HRC 58–63, а следовательно, высокую износостойкость. Однако такое изделие (если оно не имеет вязкой сердцевины) не выдерживает значительных динамических нагрузок.
Низкотемпературному отпуску подвергают поэтому режущий и измерительный инструмент из углеродистых и низколегированных сталей, а также детали, претерпевшие поверхностную закалку, цементацию, цианирование или нитроцементацию. Продолжительность отпуска обычно 1–2,5 ч, а для изделий больших сечений и измерительных инструментов назначают более длительный отпуск.
Среднетемпературный отпуск стали
Среднетемпературный (средний) отпуск выполняют при 350–500 °С и применяют главным образом для пружин и рессор, а также для штампов. Такой отпуск обеспечивает высокие предел упругости, предел выносливости и релаксационную стойкость. Структура стали (0,45–0,8 % С) после среднего отпуска – троостит отпуска или троостомартенсит с твердостью HRC 40–50. Температуру отпуска надо выбирать таким образом, чтобы не вызвать необратимой отпускной хрупкости.
Охлаждение после отпуска при 400–450 °С следует проводить в воде, что способствует образованию на поверхности сжимающих остаточных напряжений, которые увеличивают предел выносливости пружин.
Высокотемпературный отпуск стали
Высокотемпературный (высокий) отпуск проводят при 500–680 °С. Структура стали после высокого отпуска – сорбит отпуска. Высокий отпуск создает наилучшее соотношение прочности и вязкости стали.
Закалка с высоким отпуском по сравнению с нормализованным или отожженным состоянием одновременно повышает пределы прочности и текучести, относительное сужение, и особенно ударную вязкость (таблица 1). Термическую обработку, состоящую из закалки и высокого отпуска, называют улучшением.
Улучшению подвергают среднеуглеродистые (0,3–0,5 % С) конструкционные стали, к которым предъявляются высокие требования к пределу текучести, пределу выносливости и ударной вязкости. Однако износостойкость улучшенной стали вследствие ее пониженной твердости не является высокой.
Отжиг при 880 °С | 55 | 35 | 20 | 59 | 9 |
Закалка с 880 °С (охлаждение в воде) и отпуск при 300 °С | 130 | 110 | 12 | 35 | 3 |
Закалка с 880 °С (охлаждение в воде) и отпуск при 600 °С | 62 | 43 | 22 | 55 | 14 |
* Заготовка диаметром 12 мм. |
Улучшение значительно повышает конструктивную прочность стали, уменьшая чувствительность, к концентраторам напряжений, увеличивая работу пластической деформации при движении трещины (работу развития трещины) и снижая температуру верхнего и нижнего порога хладноломкости.
Отпуск при 550–600 °С в течение 1–2 ч почти полностью снимает остаточные напряжения, возникшие при закалке. Чаше длительность высокого отпуска составляет 1–6 ч – в зависимости от габаритных размеров изделия.
weldworld.ru
Отпуск сталей
Отпуск - это процесс термической обработки, заключающийся в нагреве закаленной стали до температур ниже точки Ас1, c целью получения равновесной структуры и заданного комплекса механических свойств.
Содержание
После закалки сталь имеет структуру на основе мартенсита с тетрагональной искаженной кристаллической решеткой и остаточного аустенита, количество которого зависит от химического состава стали. При нагреве закаленной стали в ее структуре происходят фазовые превращения, которые можно показать в виде схемы.
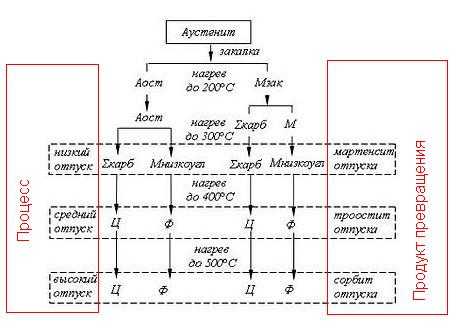
Схема фазовых превращений при отпуске сталей
Низкий отпуск сталей
Низкий отпуск стали делают при температуре до 250°С. При этом процессе из мартенсита выделяется часть избыточного углерода с образованием мельчайших карбидных частиц (ε-карбидов). ε-карбиды выделяются в виде пластин или стержней и они когерентно связаны с решеткой мартенсита. Распад остаточного аустенита при низком отпуске происходит по механизму бейнитного превращения: образуется гетерогенная смесь кристаллов низкоуглеродистого мартенсита и дисперсных карбидов. Продуктом низкого отпуска является мартенсит отпуска, который отличается от мартенсита закалки меньшей концентрацией углерода и наличием в нем карбидов (ε-карбидов), которые когерентно связаны с решеткой мартенсита.
При температуре около 250°С начинается превращение карбида в цементит; при этом когерентность решеток α-твердого раствора мартенсита и карбидов нарушается.
Низкому отпуску подвергают инструментальные железоуглеродистые материалы (режущий и мерительный инструмент), а также стали, которые подвергались цементации, нитроцементации. Часто низкий отпуск делают для сталей после термообработки токами высокой частоты.
Средний отпуск
Средний отпуск проводится при температурах 350–400 °С. При этом из мартенсита выделяется весь избыточный углерод с образованием цементитных частиц. Тетрагональность (степень тетрагональности) решетки железа уменьшается, она становится кубической. В результате вместо мартенсита остается феррит. Такая феррито-цементитная смесь называется трооститом отпуска, а процесс, приводящий к таким изменениям, среднетемпературным отпуском. При среднем отпуске снижается плотность дислокаций и уменьшаются внутренние напряжения в стали.
Средний отпуск применяется при термообработке упругих деталей: рессор, пружин и др.
Высокий отпуск
Во время высокого отпуск (450-550°С и выше) в углеродистых сталях происходят изменения структуры, не связанные с фазовыми превращениями: изменяются форма, размер карбидов и структура феррита. С повышением температуры происходит коагуляция – укрупнение частиц цементита. Форма кристаллов постепенно становится сферической – этот процесс называется сфероидизацией.
Коагуляция и сфероидизация карбидов начинают происходить более интенсивно с температуры 400°С. Зерна феррита становятся крупными, и их форма приближается к равноосной. Феррито-карбидная смесь, которая образуется после отпуска при температуре 400–600 °С, называется сорбитом отпуска. При температуре, близкой к точке А1, образуется достаточно грубая феррито-цементитная смесь – перлит.
Высокий отпуск с температур 450-550°С применяется для большинства конструкционных сталей. Его широко используют при термообработке различных втулок, опор, крепежных изделий, работающих на растяжение-сжатие и других изделий, которые испытывают статические нагрузки.
Явление отпускной хрупкости
При отпуске некоторых сталей возможно протекание процессов, которые снижают ударную вязкость стали не меняя остальные механические свойства. Такое явление называется отпускной хрупкостью и наблюдается в температурных интервалах отпуска при 250–400ºС и 500–550ºС. Первый вид хрупкости называется отпускной хрупкостью Ι рода и является необратимым, поэтому стоит избегать отпуска сталей при этих температурах. Данный вид присущ практически всем сталям, легированным хромом, магнием, никелем и их сочетанием, и обусловлен неоднородным выделением карбидов из мартенсита. Второй вид отпускной хрупкости - отпускная хрупкость ΙΙ-го рода является обратимым. Отпускная хрупкость ΙΙ-го рода проявляется при медленном охлаждении легированной стали при температуре 500–550°С. Данная хрупкость может быть устранена повторным отпуском с большой скоростью охлаждения (в воде или масле). В этом случае устраняется причина этой хрупкости – выделение карбидов, нитридов, фосфидов по границам бывших аустенитных зерен. Устранение отпускной хрупкости легированных сталей возможно введением в них малых добавок молибдена (0,2–0,3 %) или вольфрама (0,5–0,7 %).
Графически эти виды хрупкости выглядят, как показано на рисунке.
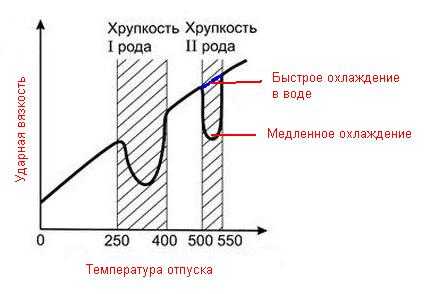
Проявление отпускной хрупкости в сталях при отпуске
Практически все стали подчиняются закону: повышение температуры отпуска — снижение прочностных характеристик и повышение пластических, как показано на рисунке ниже.
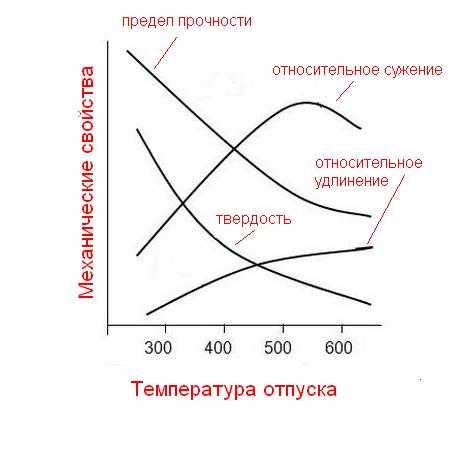
Влияние температуры отпуска на механические свойства стали
Такая закономерность не касается быстрорежущих инструментальных легированных карбидообразующими элементами сталей.
Отпуск быстрорежущих инструментальных сталей
Основными легирующими элементами быстрорежущих сталей (Р18, Р6М5 и др.) являются вольфрам, молибден, кобальт и ванадий — элементы, обеспечивающие теплостойкость и износостойкость при эксплуатации. Быстрорежущие стали относятся к карбидному (ледебуритному) классу. Под закалку эти стали нагревают до температуры выше 1200°С (Р18 до температуры 1270°С, Р6М5 — до 1220°С). Высокие температуры закалки необходимы для более полного растворения вторичных карбидов и получения аустенита высоколегированного хромом, молибденом, вольфрамом, ванадием. Это обеспечивает получение после закалки теплостойкого мартенсита. Даже при очень высоком нагреве растворяется только часть карбидов. Для этих сталей характерно сохранение мелкого зерна при высоких температурах нагрева.
Железо и легирующие элементы "быстрорезов" имеют сильно отличающиеся свойства теплопроводности, поэтому при нагреве, для избежания трещин, следует делать температурные остановки. Обычно при 800 и 1050°С. При нагреве крупного инструмента первую выдержку делают при 600°С. Время выдержки составляет 5-20 мин. Выдержка при температуре закалки должна обеспечить растворение карбидов в пределе их возможной растворимости. Охлаждение инструмента чаще всего делают в масле. Для уменьшения деформации применяют ступенчатую закалку в расплавах солей с температурой 400-500°С. Структура "быстрорезов" после закалки состоит из высоколегированного мартенсита, содержащего 0,3-0,4%С, нерастворенных избыточных карбидов и остаточного аустенита. Чем выше температура закалки, тем ниже положение точек Мн, Мк и тем больше остаточного аустенита. В стали Р18 присутствует примерно 25-30% остаточного аустенита, в стали Р6М5 — 28-34%. Для уменьшения аустенита можно сделать обработку холодом, но как правило этого не требуется.
После закалки следует отпуск при 550 — 570°С, вызывающий превращение остаточного аустенита в мартенсит и дисперсионное твердение за счет частичного распада мартенсита и выделения дисперсных карбидов легирующих элементов. Это сопровождается увеличением твердости (вторичная твердость). В процессе выдержки при отпуске из остаточного аустенита выделяются карбиды, что уменьшает его легированность, и поэтому при последующем охлаждении он претерпевает мартенситное превращение (Мн~150°С). В процессе однократного отпуска только часть остаточного аустенита превращается в мартенсит. Чтобы весь аустенит перешел в мартенсит применяют двух и трехкратный отпуск. Время выдержки обычно составляет 60 минут.При назначении режима нужно учитывать химические свойства элементов и периодичность выделения карбидов в зависимости от температуры. Например максимальная твердость стали Р6М5 получается за счет 3-х стадийного отпуска. Первый отпуск при температуре 350°С, последующие два при температуре 560-570°С. При температуре 350°С выделяются частицы цементита, равномерно распределенные в стали. Это способствует однородному выделению и распределению спецкарбидов М6С при температуре 560-570°С.
heattreatment.ru
Термическая обработка (термообработка) стали, сплавов, металлов.
Термическая обработка (термообработка) — это технологический процесс изменения структуры сталей, сплавов и цветных металлов посредством широкого диапазона температур: поэтапных нагреваний и охлаждении с определенной скоростью. Такая обработка очень сильно изменяет свойства сталей, сплавов, металлов в сторону улучшения показателей, но при этом не изменяя их химический состав. Можно сказать, что основная цель термической обработки – это улучшение свойств и характеристик изделий из него.
Виды (стадии) термической обработки стали
Отжиг — термическая обработка (термообработка) металла, представляющая собой процесс нагревания до заданной температуры, а затем процесс медленного охлаждения. Отжиг бывает разных видов в зависимости от уровня температур и скорости процесса.
Нормализация — термообработка, принципиально похожая на отжиг. Основное отличие в том, что процесс отжига предполагает печь, а при нормализации охлаждение стали проходит на воздухе.
Закалка — этап термообработки, основанный на нагревании сырья до такого уровня температуры, который является выше критического (перекристаллизация стали). После выдержки в такой температуре в заданном интервале времени происходит охлаждение, быстрое, с заданной скоростью. Закаленной стали (сплавам) свойственна неравновесная структура и поэтому применяется такой вид термообработки как отпуск.
Отпуск — стадия термообработки, необходимая для снятия в стали и сплавах остаточного напряжения или максимального его снижения. Снижает хрупкость и твёрдость металла, увеличивает вязкость. Проводится после стадии закалки.
Старение — иначе еще называется дисперсионное твердение. После стадии отжига металл опять нагревают, но до более низкого уровня температур и с медленной скоростью остужают. Цель такой термообработки в получении особенных частиц упрочняющей фазы.
От степени необходимой глубины обработки различают термообработку поверхностную, которая затрагивает лишь поверхность изделий, и объемную, когда термическому воздействию подвергается весь объем сырья.
В отраслевой промышленности, в частности – в машиностроении, термическую обработку чаще всего проходит сталь следующих марок:
- сталь 45 (замещаемость 40Х, 50, 50Г2)
- сталь 40Х (замещаемость 38ХА, 40ХР, 45Х, 40ХС, 40ХФ, 40ХН)
- сталь 20 (замещаемость 15, 25)
- сталь 30ХГСА (замещаемость 40ХФА, 35ХМ, 40ХН, 25ХГСА, 35ХГСА)
- сталь 65Г
- сталь 40ХН
- сталь 35
- сталь 20Х13
Термообработка стали 45
Конструкционная углеродистая. Этап предварительной термической обработки называется нормализация, проходит на воздухе, а не в печи. довольно легко проходит механическую обработку. Точение, фрезеровку и т. д. Получают детали, например, типа вал-шестерни, коленчатые и распределительные валы, шестерни, шпиндели, бандажи, цилиндры, кулачки.
После закалки, которая является конечной стадией термообработки, детали достигают высокого уровня прочности и отличных показателей износостойкости. Подвергаются шлифовке. Высокое содержание углерода (0,45%) обеспечивает хорошую закаливаемость и, соответственно, высокую твёрдость поверхности и прочность изделия. Сталь 45 калят «на воду», когда после калки деталь охлаждают в воде. После охлаждения деталь подвергается низкотемпературному отпуску при температуре 200-300 градусов по Цельсия. При такой термообработке стали 45 достигает твердость порядка 50 HRC.
Изделия: Кулачки станочных патронов, согласно указаниям ГОСТ, изготовляют из сталей 45 и 40Х. Твёрдость Rc = 45 -50. В кулачках четырёх-кулачных патронов твёрдость резьбы должна быть в пределах Rс = 35-42. Отпуск кулачков из стали 45 производится при температуре 220-280°, из стали 40Х при 380-450° в течение 30-40 мин.
Расшифровка марки стали 45: марка 45 означает, что в стали содержится 0,45% углерода,C 0,42 - 0,5; Si 0,17 - 0,37;Mn 0,5 - 0,8; Ni до 0,25; S до 0,04; P до 0,035; Cr до 0,25; Cu до 0,25; As до 0,08.
Термообработка стали 40Х
Легированная конструкционная сталь. Для деталей повышенной прочности такие как оси, валы, вал-шестерни, плунжеры, штоки, коленчатые и кулачковые валы, кольца, шпиндели, оправки, рейки, зубчатые венцы, болты, полуоси, втулки и прочих деталей повышенной прочности. Сталь 40Х также часто используется для производства поковок, штампованных заготовок и деталей трубопроводной арматуры. Однако последние перечисленные детали нуждаются в дополнительной термической обработке, заключающейся в закалке через воду в масле или просто в масле с последующим отпуском в масле или на воздухе.
Расшифровка марки стали 40Х. Цифра 40 указывает на то, что углерод в стали содержится в объеме 0,4 %. Хрома содержится менее 1,5 %. Помимо обычных примесей в своем составе имеет в определенных количествах специально вводимые элементы, которые призваны обеспечить специально заданные свойства. В качестве легирующего элемента в данном случае используется хром, о чем говорит соответствующая маркировка.
Термообработка стали 20
Термообработка стали 20 - сталь конструкционная углеродистая качественная. Широкое применение в котлостроении, для труб и нагревательных трубопроводов различного назначения, кроме того промышленность выпускает пруток, лист. В качестве заменителя стали 20 применяют стали 15 и 25.
По требованиям к механическим свойствам выделяют пять категорий.
- I категория: сталь всех видов обработки без испытания на ударную вязкость и растяжение.
- II категория: образцы из нормализованной стали всех видов обработки размером 25 мм проходят испытания на ударную вязкость и растяжение.
- III категория: испытания на растяжение проводят на образцах из нормализованной стали, размером 26-100 мм.
- IV категория: образцы для испытаний на растяжение и ударную вязкость изготавливают из термически обработанных заготовок размером не более 100 мм. Требования третьей и четвертой категории предъявляют к калиброванной, горячекатаной и кованной качественной стали.
- V категория. Испытания механических свойств на растяжение проводят на образцах из калиброванных термически обработанных (высокоотпущенных или отожженных) или нагартованных сталей.
Химический состав стали 20: углерод (C) - 0.17-0.24 %, кремний (Si) - 0,17-0,37%, марганец (Mn) - 0,35-0,65 %;содержание меди (Cu) и никеля (Ni) допускается не более 0,25%, мышьяка (As) - не более 0,08%, серы (S) - не более 0,4%, фосфора (Р) - 0,035%.Структура стали 20 представляет собой смесь перлита и феррита. Термическая обработка стали 20 позволяет получать структуру реечного (пакетного) мартенсита. При таких структурных преобразованиях прочность возрастает, и пластичность уменьшается. После термического упрочнения прокат из стали 20 можно использовать для изготовления метизной продукции (класс прочности 8.8).
Технологические свойства стали 20: Температура начала ковки стали 20 составляет 1280° С, окончания - 750° С, охлаждение поковки - воздушное. Сталь 20 нефлокеночувствительна и не склонна к отпускной способности. Свариваемость стали 20 не ограничена, исключая детали, подвергавшиеся химико-термической обработке. Рекомендованы способы сварки АДС, КТС, РДС, под газовой защитой и флюсом.
Сталь 20 применяют для производства малонагруженных деталей ( пальцы, оси, копиры, упоры, шестерни) , цементуемых деталей для длительной и весьма длительной службы (эксплуатация при температуре не выше 350° С) , тонких деталей, работающих на истирание. Сталь 20 без термической обработки или после нормализации используется для производства крюков кранов, вкладышей подшипников и прочих деталей для эксплуатации под давлением в температурном диапазоне от -40 до 450°С . Сталь 20 после химико-термической обработки идет на производство деталей, которым требуется высокая поверхностная прочность ( червяки, червячные пары, шестерни) . Широко применяют сталь 20 для производства трубопроводной арматуры, труб, предназначенных для паропроводов с критическими и сверхкритическими параметрами пара, бесшовных труб высокого давления, сварных профилей прямоугольного и квадратного сечения и т. д.
Термообработка стали 30ХГСА
Относится к среднелегированной конструкционной стали. Сталь 30ХГСА проходит улучшение – закалку с последующим высоким отпуском при 550-600 °С, поэтому применяется при создании улучшаемых деталей (кроме авиационных деталей это могут быть различные корпуса обшивки, оси и валы, лопатки компрессорных машин, которые эксплуатируются при 400°С, и многое другое), рычаги, толкатели, ответственные сварные конструкции, работающие при знакопеременных нагрузках, крепежные детали, работающие при низких температурах.
Сталь 30ХГСА обладает хорошей выносливостью, отличными показателями ударной вязкости, высокой прочностью. Она также отличается замечательной свариваемостью.
Сварка стали 30ХГСАтоже имеет свои особенности. Она осуществляется с предварительным подогревом материала до 250-300 °С с последующим медленным охлаждением. Данная процедура очень важна, поскольку могут появиться трещины из-за чувствительности стали к резким перепадам температуры после сварки. Поэтому по завершении сварных работ горелка должна отводиться медленно, при этом осуществляя подогрев материала на расстоянии 20-40 мм от места сварки. Также, не более, чем спустя 8 часов по завершении сварки сварные узлы стали 30ХГСА нуждаются в закалке с нагревом до 880 °С с последующим высоким отпуском. Далее изделие охлаждается в масле при 20-50 °С. Отпуск осуществляется нагревом до 400 - 600 °С и охлаждением в горячей воде. Сварку же необходимо выполнять максимально быстро, дабы избежать выгорания легирующих элементов.
После прохождения термомеханической низкотемпературной обработки сталь 30ХГСА приобретает предел прочности до 2800 МПа, ударная вязкость повышается в два раза (в отличии от обычной термообработки стали 30хгса), пластичность увеличивается.
Термообработка стали 65Г
Сталь конструкционная рессорно-пружинная. Используют в промышленности пружины, рессоры, упорные шайбы, тормозные ленты, фрикционные диски, шестерни, фланцы, корпусы подшипников, зажимные и подающие цанги и другие детали, к которым предъявляются требования повышенной износостойкости, и детали, работающие без ударных нагрузок. (заменители: 70, У8А, 70Г, 60С2А, 9ХС, 50ХФА, 60С2, 55С2).
Термообработка стали 40
Сталь конструкционная углеродистая качественная. Использование в промышленности: трубы, поковки, крепежные детали, валы, диски, роторы, фланцы, зубчатые колеса, втулки для длительной и весьма длительной службы при температурах до 425 град.
Термообработка стали 40ХН
Сталь конструкционная легированная Используется в отраслевой в промышленности: оси, валы, шатуны, зубчатые колеса, валы экскаваторов, муфты, валы-шестерни, шпиндели, болты, рычаги, штоки, цилиндры и другие ответственные нагруженные детали, подвергающиеся вибрационным и динамическим нагрузкам, с предъявляемыми требованиями повышенной прочности и вязкости. Валки рельсобалочных и крупносортных станов для горячей прокатки металла.
Термообработка сталь 35
Сталь конструкционная углеродистая качественная. Используется в отраслевой промышленности. Это детали невысокой прочности, подвергающиеся невысокому уровню напряжения: оси, цилиндры, коленчатые валы, шатуны, шпиндели, звездочки, тяги, ободы, траверсы, валы, бандажи, диски и другие детали.
Термообработка стали 20Х13
Сталь коррозионно-стойкая жаропрочная. Используется в энергетическом машиностроении и печестроении; турбинные лопатки, болты, гайки, арматура крекинг-установок с длительным сроком службы при температурах до 500 град; сталь мартенситного класса Сталь марки 20Х13 и другие стали мартенситного класса: жаропрочные хромистые стали мартенситного класса применяют в различных энергетических установках, они работают при температуре до 600° С. Из них изготовляют роторы, диски и лопатки турбин, в последнее время их используют для кольцевых деталей больших толщин. Существует большое количество марок сталей данного класса. Общим для всех является пониженное содержание хрома, наличие молибдена, ванадия и вольфрама. Они эффективно упрочняются обычными методами термообработки, которая основана на у - a-превращении и предусматривает получение в структуре мартенсита с последующим улучшением в зависимости от требований технических условий. (заменители: 12Х13, 14Х17Н2)
Пресс-служба группы компаний ВоКа
17 сентября 2016г
metizmsk.ru
45. Виды отпуска стали. Свойства стали после отпуска
1) низкий – нагрев детали до температуры 150 – 200 град, образуется структура – мартенсит отпуска. Твердость остается неизменной – 60 – 64 HRC. Снижаются закалочные напряжения, повышается предел прочности и текучести. Низкий отпуск применяется для обработки – режущих инструментов, штампы, подшипники, детали после закалки ТВЧ, цементованные детали. 2) средний – нагрев детали до температуры 350 – 400 град, образуется структура – троостит отпуска. Снижается твердость до 40 – 48 HRC, а также предел прочности. Сильно повышается предел упругости, выносливости. Средний отпуск применяется для обработки – пружин, рессор. 3) высокий – нагрев детали до температуры 500 – 650 град, образуется структура – сорбит отпуска. Снижается твердость до 30 HRC, предел прочности и упругости. Возрастает пластичность и ударная вязкость. Применяется для большинства деталей машин. Закалка + высокий отпуск – улучшение.
44. Способы, закалки, их достоинства и недостатки
1. Закалка в одном охладителе (v1).
Нагретую до нужной температуры деталь переносят в охладитель и полностью охлаждают. В качестве охлаждающей среды используют:
воду – для крупных изделий из углеродистых сталей;
масло – для небольших деталей простой формы из углеродистых сталей и изделий из легированных сталей.
Основной недостаток – значительные закалочные напряжения.
2. Закалка в двух сферах или прерывистая
Нагретое изделие предварительно охлаждают в более резком охладителе (вода) до температуры ~ 3000C и затем переносят в более мягкий охладитель (масло).
Прерывистая закалка обеспечивает максимальное приближение к оптимальному режиму охлаждения.
Применяется в основном для закалки инструментов.
Недостаток: сложность определения момента переноса изделия из одной среды в другую.
3. Ступенчатая закалка
Нагретое до требуемой температуры изделие помещают в охлаждающую среду, температура которой на 30 – 50oС выше точки МН и выдерживают в течении времени, необходимого для выравнивания температуры по всему сечению. Время изотермической выдержки не превышает периода устойчивости аустенита при заданной температуре.
В качестве охлаждающей среды используют расплавленные соли или металлы. После изотермической выдержки деталь охлаждают с невысокой скоростью.
Способ используется для мелких и средних изделий.
4. Изотермическая закалка
Отличается от ступенчатой закалки продолжительностью выдержки при температуре выше МН, в области промежуточного превращения. Изотермическая выдержка обеспечивает полное превращение переохлажденного аустенита в бейнит.При промежуточном превращении легированных сталей кроме бейнита в структуре сохраняется аустенит остаточный. Образовавшаяся структура характеризуется сочетанием высокой прочности, пластичности и вязкости. Вместе с этим снижается деформация из-за закалочных напряжений, уменьшаются и фазовые напряжения.
В качестве охлаждающей среды используют расплавленные соли и щелочи.
Применяются для легированных сталей.
Дефекты, возникающие при закалке.
Закалочные трещины. В крупных деталях, например в матрицах и ковочных штампах, закалочные трещины могут появляться даже при закалке в масле. Поэтому такие детали целесообразно охлаждать до 150–200 °С с быстрым последующим отпуском.
Чтобы уменьшить скорость охлаждения при закалке легированных сталей и снизить напряжение, эти стали подвергают медленному охлаждению в масле или струе воздуха.
Деформация и коробление. Этот вид брака деталей образуется в результате неравномерных структурных и связанных с ними объёмных превращений и возникновения внутренних напряжений при охлаждении.
Обезуглероживание инструмента при нагреве в электрических печах и жидких средах (соляных ваннах) – серьёзный дефект при закалке, т.к. он в несколько раз снижает стойкость инструмента.
Мягкие пятна. При закалке на поверхности детали или инструмента образуются участки с пониженной твёрдостью. Причинами такого дефекта могут быть наличие на поверхности деталей окалины и загрязнении, участки с обезуглероженной поверхностью или недостаточно быстрое движение деталей в закалочной среде (паровая рубашка). Мягкие пятна полностью устраняются при струйчатой закалке и в подсоленной воде.
Причинами низкой твёрдости являются недостаточно быстрое охлаждение в закалочной среде, низкая температура закалки, а также малая выдержка при нагреве под закалку. Чтобы исправить этот дефект, детали или инструмент сначала подвергают высокому отпуску при температуре 600–625 °С, а затем – закалке.
Перегрев приводит к образованию крупнозернистой структуры, что ухудшает механические свойства стали. Для измельчения зерна и подготовки структуры для повторной закалки перегретую сталь необходимо подвергать отжигу.
Недогрев. Если температура закалки была ниже критических точек Ас3 (для доэвтектоидных сталей) и Ас1 (для заэвтектоидных сталей), то структура закаленной стали будет состоять из мартенсита и зерен феррита, который имеет низкую твёрдость. Недогрев можно исправить отжигом с последующей закалкой.
studfiles.net
Отпуск стали. Температура отпуска стали. Режимы отпуска стали. Отпускная хрупкость. Улучшение термическая обработка.
Отпуск является окончательной термической обработкой. Целью отпуска является повышение вязкости и пластичности, снижение твердости и уменьшение внутренних напряжений закаленных сталей (см. Закалка стали). С повышением температуры нагрева прочность обычно снижается, а пластичность и вязкость растут. Температуру отпуска выбирают, исходя из требуемой прочности конкретной детали.
Термическая обработка металла. Термическая обработка металлов и сплавов. Виды термической обработки металлов. Виды термообработки.
Различают три вида отпуска:
1. Низкий отпуск с температурой нагрева Тн = 150…300oС.
В результате его проведения частично снимаются закалочные напряжения. Получают структуру – мартенсит отпуска.Проводят для инструментальных сталей после закалки токами высокой частоты или после цементации.
2. Средний отпуск с температурой нагрева Тн = 300…450oС.
Получают структуру – троостит отпуска, сочетающую высокую твердость 40…45HRC c хорошей упругостью и вязкостью.Используется для изделий типа пружин, рессор.
3. Высокий отпуск с температурой нагрева Тн = 450…650oС..
Получают структуру, сочетающую достаточно высокую твердость и повышенную ударную вязкость (оптимальное сочетание свойств) – сорбит отпуска.Используется для деталей машин, испытывающих ударные нагрузки.Комплекс термической обработки, включающий закалку и высокий отпуск, называется улучшением.
Способы закалки. Способы закалки стали. Виды закалки стали. Технология закалки стали. Режимы закалки сталей.Закалка стали. Закалка металла. Виды закалки. Температура закалки. Закаливаемость. Прокаливаемость. Критический диаметр.
Отпускная хрупкость
Обычно с повышением температуры отпуска ударная вязкость увеличивается, а скорость охлаждения не влияет на свойства. Но для некоторых сталей наблюдается снижение ударной вязкости. Этот дефект называется отпускной хрупкостью.
Зависимость ударной вязкости от температуры отпуска
Отпускная хрупкость I рода наблюдается при отпуске в области температур около 300oС. Она не зависит от скорости охлаждения. Это явление связано с неравномерностьюпревращения отпущенного мартенсита (см. Мартенсит. Мартенситное превращение.). Процесс протекает быстрее вблизи границ зерен по сравнению с объемами внутри зерна. У границ наблюдается концентрация напряжений, поэтому границы хрупкие.
Отпускная хрупкость I рода “необратима“, то есть при повторных нагревах тех же деталей не наблюдается.
Нормализация стали. Температура нормализации стали. Процесс нормализации стали.
Отпускная хрупкость II рода наблюдается у легированных сталей при медленном охлаждении после отпуска в области 450…650oС. При высоком отпуске по границам зерен происходит образование и выделение дисперсных включений карбидов. Приграничная зона обедняется легирующими элементами. При последующем медленном охлаждении происходит диффузия фосфора к границам зерна. Приграничные зоны обогащаются фосфором, снижаются прочность и ударная вязкость. Этому деекту способствуют хром, марганец и фосфор. Уменьшают склонность к отпускной хрупкости II рода молибден и вольфрам, а также быстрое охлаждение после отпуска.
Отжиг стали. Отжиг второго рода. Полный отжиг. Неполный отжиг. Полный и неполный отжиг. Изотермический отжиг.Отжиг стали. Отжиг первого рода. Диффузионный отжиг. Отжиг рекристаллизационный. Отжиг для снятия напряжений.
Отпускная хрупкость II рода “обратима“, то есть при повторных нагревах и медленном охлаждении тех же сталей в опасном интервале температур дефект может повториться.
Стали, склонные к отпускной хрупкости II рода, нельзя использовать для работы с нагревом до 650oС без последующего быстрого охлаждения.
www.mtomd.info