Токарное дело и его история. Токарное дело
Токарное дело и его история
Среди рабочих специальностей профессия токаря была и остаётся одной из самых востребованных. Обработка древесины и металла – сфера применения токарного ремесла. Для оптимизации труда, точности и скорости изготовления деталей существует множество станков и иного оборудования, которое постоянно совершенствуется, позволяя выполнять мастеру сложнейшие и точнейшие операции.
Специфика термина
Токарное дело прошло долгий путь развития, прежде чем обрело те формы производства, которые мы знаем сейчас. На современном этапе к нему относятся резка металлических и неметаллических материалов и сплавов, нанесение резьбы разных типов на детали, вытачивание отдельных элементов оборудования и нанесение на них различных насечек, канавок и т.д., обтачивание деревянных болванок для придания им нужной формы. Конечные продукты производства – знакомые нам болты и гайки, клапаны и переходники, заглушки и многая другая фурнитура, а также разные корпуса и прочие детали.
Токарное дело тесно связано с токарным производством. Под это понятие подходит, в принципе, любое предприятие, где установлены соответствующие станки и прочие орудия для работы с разным материалом от единичных заказов до целой серии или линии. Для того чтобы уметь выполнять нужные действия и разбираться в каждом этапе операций, необходимо хорошо знать свойства термообработок материалов, ориентироваться в чертежах и обладать многими другими знаниями. Поэтому токарное дело считается наукой сложной, самым тесным образом взаимодействующей со смежными.
История и традиции
Если вернуться в далёкое прошлое, то можно вспомнить, что наши предки пользовались посудой, которую долбили, вырезали и вытачивали из дерева, равно как и предметы домашнего обихода, мебель и даже игрушки. Делалось это сначала грубым способом и подручными средствами, а затем на приспособлениях, напоминавших токарные станки и ставших их прообразами. Так появились обточенные братины, миски, чашки. Следовательно, именно оттуда современное токарное дело берёт свои истоки. И по сей день в декоративном искусстве, народных промыслах точёные детали и целые изделия находят широкое применение. Например, различные кухонные аксессуары: подставки под горячие чайники, кастрюли и сковородки, разделочные доски и т.д.; аксессуары дизайна интерьера: деревянные «занавесы» из отшлифованных кругляшков из древесины или палочек, сувенирные скульптуры и статуэтки. Токарные станки обрабатывают практически любую породу дерева быстро и аккуратно, со всей необходимой точностью. При этом размер изделия особой роли не играет. Обточить можно и миниатюрную нэцкэ, указав даже мельчайшие детали, и крупное изделие. Особую красоту и выразительность таким предметам прида
С развитием промышленности, активным использованием в производстве железа зародилось и токарное дело по металлу, близкое технически к деревообрабатывающему. Сейчас без него не обходится ни один производственный процесс. Сложнейшие механизмы в основе своей сделаны из деталей, созданных на токарных станках. Поэтому токарь, особенно фрезеровщик, всегда востребован на предприятиях. А обучение токарному делу ведётся во всех специализированных профтехучилищах и на многих крупных заводах и фабриках.
Резюме
Профессия токаря, интересная и трудная, требует большой самодисциплины, аккуратности и постоянного самосовершенствования. Это одна из тех специальностей, на которых держатся самые сложные высокотехнологичные процессы.
fb.ru
Токарное дело
ТЕХНИКА БЕЗОПАСНОСТИ ПРИ РАБОТЕ НА ТОКАРНОМ СТАНКЕ
Техника безопасности – это система организационных и технических мероприятий и средств, предотвращающих воздействие на работающих опасных и вредных производственных факторов. Основное содержание мероприятий по технике безопасности и производственной санитарии заключается в профилактике травматизма, т. е. предупреждении несчастных случаев на производстве, и в частности в период прохождения учебной практики.
Каждый студент должен получить инструктаж о технике безопасности, производственной санитарии и противопожарной охране.
Инструктаж на рабочем месте проводится перед допуском к работе всех вновь прибывших на практику учащихся, а также переведенных.
До начала работы.
1) Надеть спецодежду; застегнуть рукава; спрятать волосы под головной убор.
2) Проверить наличие и надёжность крепление защитных ограждений и соединение защитного заземления с корпусом станка.
3) Расположить инструменты и заготовки в определённом порядке на приставной тумбе.
4) Прочно закрепить резец и обрабатываемую деталь. Вынуть ключ из патрона и установить на установленное место.
5) Проверить работу станка на холостом ходу и исправность пусковой коробки путём выключения кнопок и рычагов управления.
Во время работы.1) Строго выполнять технологию операций.
2) Во избежание травм запрещается:
· наклонять голову близко к патрону или режущему инструменту.
· предавать или принимать предметы через вращающие части станков.
· облокачиваться или опираться на станок, класть на него инструменты или заготовки.
· измерять обрабатываемую деталь, чистить и убирать стружку со станка до полной его остановки.
· охлаждать режущий инструмент или обрабатываемою деталь с помощью тряпки.
· останавливать станок путём торможения рукой патрона.
· отходить от станка не выключив его.
· поддерживать и ловить рукой отрезанною деталь.
3) Зачистку детали на станке производить напильником или шкуркой прикрепленной оправе. Рукоятка оправы должна быть с предохранительным кольцом. При работе держать левой рукой.
4) При выключение станка необходимо отвести резец от обрабатываемой детали.
5) При работе в центрах проверить надёжно ли закреплена задняя бабка и следить, чтобы засверловка была достаточна, и угол ее соответствовал углу центров.
6) Пользоваться ключами, соответствующими гайками и головками болтов.
7) Обрабатываемый пруток не должен выступать за пределы станка
8) При выключении тока в сети, во время работы, немедленно выключить машину.
По окончанию работы. 1) Отключить суппорт, выключить электродвигатель.2) Удалить стружку со станка при помощи щётки, из пазов станины крючками. Сдувать стружку ртом или сметать рукой запрещается.
3) Протереть станок, смазать, привести в порядок инструменты и индивидуальные средства защиты. Сдать станок преподавателю.
РЕЖУЩИЕ ИНСТРУМЕНТЫ
Режущим инструментом,применяемым на токарных станках, являются резцы. По виду обработки резцы делятся на: проходные, подрезные, отрезные, прорезные, гантельные, резьбовые, фасонные и расточные; расточные, в свою очередь, делятся на резцы для обработки сквозных отверстий, обработки в упор глухих отверстий, расточки канавок, нарезания резьбы. По направлению подачи резцы делятся на правые и левые. Правыми резцами называются такие, у которых при наложении на них сверху ладони правой руки главная режущая кромка оказывается расположенной на стороне большого пальца. При работе такими резцами на токарном станке они перемещаются справа налево. По форме головки и ее расположению относительно оси тела резцы бывают прямые. Рационально выбранные геометрические параметры резца и форма передней поверхности для заданных условий резания должны обеспечивать наибольшую стойкость инструмента или наибольшую скорость резания. Такая геометрия называется оптимальной и выбирается из соответствующих справочников по режимам резания и конструированию режущего инструмента. Материалом для резцов служат быстрорежущая сталь (сварные резцы) и металлокерамический твердый сплав (резцы с напаянными или привернутыми пластинами).
ОБРАБОТКА ДЕТАЛЕЙ НА ТОКАРНЫХ СТАНКАХ
Токарная обработка – один из самых распространенных видов обработки металлов резанием, осуществляемый на станках токарной группы. Детали, обрабатываемые на этих станках, делятся на три класса: валы, диски, втулки. Детали обрабатываются на специализированных станках, налаженных для обработки определенных простых и средней сложности заготовок или выполнения отдельных операций: нарезание наружную и внутреннюю треугольную и прямоугольную резьбы метчиками и плашками. Пользуются универсальными и специальными приспособлениями, многомерным и одномерным инструментом.
ТИПЫ ТОКАРНЫХ СТАНКОВ
Станоксостоит из станины, установленной на тумбах, передней (шпиндельной) бабки, суппорта с резцедержателем и фартуком, задней бабки. Станина является основанием и служит для монтажа всех основных узлов станка. По направляющим станины перемещаются каретка суппорта и задняя бабка. Передняя бабка имеет внутри коробку скоростей со шпинделем, на переднем конце которого закрепляется патрон или планшайба для установки, обрабатываемой заготовки. Суппорт предназначен для крепления резцов в резцедержателе и перемещения их в продольном, поперечном и угловом направлениях. Для перемещения инструмента суппорт имеет трое салазок (кареток): продольные, поперечные и верхние. Коробка подач и гитара сменных зубчатых колес служат для налаживания станка на необходимую подачу или шаг нарезаемой резьбы. От коробки подач движение на суппорт поступает через ходовой винт, при нарезании резьбы, или через ходовой вал, когда необходимо осуществить движение продольной и поперечной подачи при обтачивании заготовок. Задняя бабка служит для поддержания свободного конца длинных заготовок. Она состоит из трех основных частей: корпуса, пиноли и плиты. В коническое отверстие пиноли устанавливают центр или инструмент (сверло, зенкер и т. п.). Корпус задней бабки можно смещать в поперечном направлении для обтачивания конусных поверхностей. Токарные станки оснащены устройствами для ускоренной подачи суппорта и механизма для быстрой остановки вращения шпинделя и автоматического отключения подачи суппорта при перегрузке. На передней бабке станка помещены указатели положения рукояток настройки и таблицы частот вращения шпинделя.
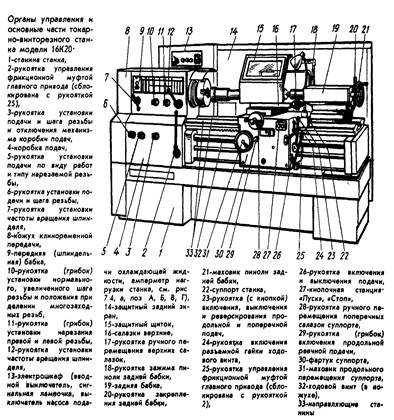
ОБРАБОТКА ЦИЛИНДРИЧЕСКИХ И ТОРЦОВЫХ ПОВЕРХНОСТЕЙ
Для обработки цилиндрическойповерхности заготовки полностью за одну установку необходимо вместо поводкового патрона и хомутика применить специальный передний центр (рифленый, плавающий с рифленым поводком, самозажимной или обратный) и заднийцентр - вращающийся.
Подрезание торцов заготовок заключается в выполнении приемов, предусмотренных в предыдущих упражнениях (установка патрона, резца и заготовки, настройка станка на требуемую частоту вращения шпинделя). Заготовку закрепить в патроне с вылетом из кулачков не более 40... 50 мм. Обработку выполнять тифозным торцовым отогнутым резцом с углом j = 90° или проходным отогнутым резцом с углом j =45°. Обработку торца заготовки выполнять в такой последовательности: коснуться вершиной головки резца торца заготовки и отвести резец от заготовки на себя; установить резец на требуемый размер срезаемого слоя (глубину резания или припуск по торцу), перемещая его влево, подать резец ручной поперечной подачей, уменьшая значение подачи при подходе вершины резца к оси заготовки. Для подрезки второго торца заготовки открепить заготовку, измерить ее длину, определить оставшийся припуск для обработки 2-го торца, закрепить заготовку в патроне другим концом. Переместить резец, отсчитывая перемещение по лимбу винта верхних салазок (или по лимбу продольной подачи каретки суппорта) от торца заготовки, оставив 0,1 ... 0,2 мм на окончательное подрезание.
Подрезать торец путем перемещения резца к центру поперечной ручной подачей. Отвести резец от заготовки в исходное положение. По лимбу винта верхних салазок суппорта подать резец влево на оставшийся припуск и подрезать второй торец окончательно. При подрезке торцов проходным отогнутым резцом с углом j= 45° предварительный проход выполнять перемещением резца от наружной поверхности заготовки к центру, окончательный проход — перемещением от центра к наружной поверхности заготовки. Прямолинейность торца заготовки после обработки проверить измерительной линейкой. Выпуклость торца не допускается. Все приведенные выше упражнения по обтачиванию цилиндрических поверхностей и подрезке торцов повторить несколько раз, после чего обработать заготовки, необходимые для проведения следующих занятий или изготовления деталей для продукции, выпускаемой учебными мастерскими.
Подрезание торца заготовки выполняют в такой последовательности: касаются вершиной головки резца торца заготовки и отвести резец от заготовки на себя; установить резец на требуемой размер (глубину резания или припуск по торцу), перемещая его влево; подать резец ручной поперечной подачей, уменьшая значение подачи при проходе вершины резца к оси заготовки.
СВЕРЛЕНИЕ И РАСТОЧКА ОТВЕРСТИЙ
Обработку отверстий на токарных станках выполняют различными режущими инструментами, выбор которых зависит от ваших заготовок, формы отверстия, точности и шероховатости поверхности отверстия. Заготовки крепят в шпинделе станка и сообщают им вращательное движение, а режущие инструменты — в пиноли задней бабки и сообщают им поступательное движение — подачу. В зависимости от формы и размеров заготовку крепят в трехкулачковом самоцентрирующемся патроне, в четырехкулачковом патроне, на планшайбе с помощью планок и болтов или другими способами. Обработку отверстий в сплошном металле заготовки производят спиральными сверлами. Когда длина отверстия превышает 5...10 диаметров, при так называемом глубоком сверлении, применяют специальные сверла (ружейные, пушечные,шпиндельные, кольцевые, центровочные и др.). Спиральные сверла диаметром до 10мм с цилиндрическим хвостовиком закрепляют в трехкулачковом сверлильном патроне, который устанавливают непосредственно в коническое отверстие пиноли задней бабки. Если конус хвостовика сверлильного патрона меньше конуса конического отверстия пиноли, то необходимо использовать переходную коническую втулку. Спиральные сверла диаметром более 10 мм с цилиндрическим хвостовиком закрепляют в двухкулачковом сверлильном патроне, обладающем большей силой зажима Спиральные сверла с коническими хвостовиками устанавливают непосредственно в коническом отверстии пиноли задней бабки танка, а когда конус сверла меньше конического отверстия пиноли, то с помощью одной или нескольких переходных втулок. Различают предварительное и окончательное сверление. При предварительном сверлении диаметр сверла подбирают меньше окончательного диаметра на размер припуска, оставленного для окончательной обработки. После предварительного сверления может быть проведено рассверливание, т. е. сверление сверлом большего диаметра, зенкерование, развертывание или растачивание отверстия резцом. Выбор вида дальнейшей обработки зависит от точности обрабатываемого отверстия. Обработку центровых отверстий на торцовых поверхностях для установки заготовок в центрах станков осуществляют или последовательно сверлом и зенковкой, или за один прием комбинированным центровочным сверлом.
mirznanii.com
Токарное дело
ТЕХНИКА БЕЗОПАСНОСТИ ПРИ РАБОТЕ НА ТОКАРНОМ СТАНКЕ
Техника безопасности – это система организационных и технических мероприятий и средств, предотвращающих воздействие на работающих опасных и вредных производственных факторов. Основное содержание мероприятий по технике безопасности и производственной санитарии заключается в профилактике травматизма, т. е. предупреждении несчастных случаев на производстве, и в частности в период прохождения учебной практики.
Каждый студент должен получить инструктаж о технике безопасности, производственной санитарии и противопожарной охране.
Инструктаж на рабочем месте проводится перед допуском к работе всех вновь прибывших на практику учащихся, а также переведенных.
До начала работы.
Надеть спецодежду; застегнуть рукава; спрятать волосы под головной убор.
Проверить наличие и надёжность крепление защитных ограждений и соединение защитного заземления с корпусом станка.
Расположить инструменты и заготовки в определённом порядке на приставной тумбе.
Прочно закрепить резец и обрабатываемую деталь. Вынуть ключ из патрона и установить на установленное место.
Проверить работу станка на холостом ходу и исправность пусковой коробки путём выключения кнопок и рычагов управления.
Во время работы.
Строго выполнять технологию операций.
Во избежание травм запрещается:
наклонять голову близко к патрону или режущему инструменту.
предавать или принимать предметы через вращающие части станков.
облокачиваться или опираться на станок, класть на него инструменты или заготовки.
измерять обрабатываемую деталь, чистить и убирать стружку со станка до полной его остановки.
охлаждать режущий инструмент или обрабатываемою деталь с помощью тряпки.
останавливать станок путём торможения рукой патрона.
отходить от станка не выключив его.
поддерживать и ловить рукой отрезанною деталь.
Зачистку детали на станке производить напильником или шкуркой прикрепленной оправе. Рукоятка оправы должна быть с предохранительным кольцом. При работе держать левой рукой.
При выключение станка необходимо отвести резец от обрабатываемой детали.
При работе в центрах проверить надёжно ли закреплена задняя бабка и следить, чтобы засверловка была достаточна, и угол ее соответствовал углу центров.
Пользоваться ключами, соответствующими гайками и головками болтов.
Обрабатываемый пруток не должен выступать за пределы станка
При выключении тока в сети, во время работы, немедленно выключить машину.
По окончанию работы.
Отключить суппорт, выключить электродвигатель.
Удалить стружку со станка при помощи щётки, из пазов станины крючками. Сдувать стружку ртом или сметать рукой запрещается.
Протереть станок, смазать, привести в порядок инструменты и индивидуальные средства защиты. Сдать станок преподавателю.
РЕЖУЩИЕ ИНСТРУМЕНТЫ
Режущим инструментом, применяемым на токарных станках, являются резцы. По виду обработки резцы делятся на: проходные, подрезные, отрезные, прорезные, гантельные, резьбовые, фасонные и расточные; расточные, в свою очередь, делятся на резцы для обработки сквозных отверстий, обработки в упор глухих отверстий, расточки канавок, нарезания резьбы. По направлению подачи резцы делятся на правые и левые. Правыми резцами называются такие, у которых при наложении на них сверху ладони правой руки главная режущая кромка оказывается расположенной на стороне большого пальца. При работе такими резцами на токарном станке они перемещаются справа налево. По форме головки и ее расположению относительно оси тела резцы бывают прямые. Рационально выбранные геометрические параметры резца и форма передней поверхности для заданных условий резания должны обеспечивать наибольшую стойкость инструмента или наибольшую скорость резания. Такая геометрия называется оптимальной и выбирается из соответствующих справочников по режимам резания и конструированию режущего инструмента. Материалом для резцов служат быстрорежущая сталь (сварные резцы) и металлокерамический твердый сплав (резцы с напаянными или привернутыми пластинами).
ОБРАБОТКА ДЕТАЛЕЙ НА ТОКАРНЫХ СТАНКАХ
Токарная обработка – один из самых распространенных видов обработки металлов резанием, осуществляемый на станках токарной группы. Детали, обрабатываемые на этих станках, делятся на три класса: валы, диски, втулки. Детали обрабатываются на специализированных станках, налаженных для обработки определенных простых и средней сложности заготовок или выполнения отдельных операций: нарезание наружную и внутреннюю треугольную и прямоугольную резьбы метчиками и плашками. Пользуются универсальными и специальными приспособлениями, многомерным и одномерным инструментом.
ТИПЫ ТОКАРНЫХ СТАНКОВ
Станок состоит из станины, установленной на тумбах, передней (шпиндельной) бабки, суппорта с резцедержателем и фартуком, задней бабки. Станина является основанием и служит для монтажа всех основных узлов станка. По направляющим станины перемещаются каретка суппорта и задняя бабка. Передняя бабка имеет внутри коробку скоростей со шпинделем, на переднем конце которого закрепляется патрон или планшайба для установки, обрабатываемой заготовки. Суппорт предназначен для крепления резцов в резцедержателе и перемещения их в продольном, поперечном и угловом направлениях. Для перемещения инструмента суппорт имеет трое салазок (кареток): продольные, поперечные и верхние. Коробка подач и гитара сменных зубчатых колес служат для налаживания станка на необходимую подачу или шаг нарезаемой резьбы. От коробки подач движение на суппорт поступает через ходовой винт, при нарезании резьбы, или через ходовой вал, когда необходимо осуществить движение продольной и поперечной подачи при обтачивании заготовок. Задняя бабка служит для поддержания свободного конца длинных заготовок. Она состоит из трех основных частей: корпуса, пиноли и плиты. В коническое отверстие пиноли устанавливают центр или инструмент (сверло, зенкер и т. п.). Корпус задней бабки можно смещать в поперечном направлении для обтачивания конусных поверхностей. Токарные станки оснащены устройствами для ускоренной подачи суппорта и механизма для быстрой остановки вращения шпинделя и автоматического отключения подачи суппорта при перегрузке. На передней бабке станка помещены указатели положения рукояток настройки и таблицы частот вращения шпинделя.
ОБРАБОТКА ЦИЛИНДРИЧЕСКИХ И ТОРЦОВЫХ ПОВЕРХНОСТЕЙ
Для обработки цилиндрической поверхности заготовки полностью за одну установку необходимо вместо поводкового патрона и хомутика применить специальный передний центр (рифленый, плавающий с рифленым поводком, самозажимной или обратный) и задний центр - вращающийся.
Подрезание торцов заготовок заключается в выполнении приемов, предусмотренных в предыдущих упражнениях (установка патрона, резца и заготовки, настройка станка на требуемую частоту вращения шпинделя). Заготовку закрепить в патроне с вылетом из кулачков не более 40... 50 мм. Обработку выполнять тифозным торцовым отогнутым резцом с углом j = 90° или проходным отогнутым резцом с углом j =45°. Обработку торца заготовки выполнять в такой последовательности: коснуться вершиной головки резца торца заготовки и отвести резец от заготовки на себя; установить резец на требуемый размер срезаемого слоя (глубину резания или припуск по торцу), перемещая его влево, подать резец ручной поперечной подачей, уменьшая значение подачи при подходе вершины резца к оси заготовки. Для подрезки второго торца заготовки открепить заготовку, измерить ее длину, определить оставшийся припуск для обработки 2-го торца, закрепить заготовку в патроне другим концом. Переместить резец, отсчитывая перемещение по лимбу винта верхних салазок (или по лимбу продольной подачи каретки суппорта) от торца заготовки, оставив 0,1 ... 0,2 мм на окончательное подрезание.
Подрезать торец путем перемещения резца к центру поперечной ручной подачей. Отвести резец от заготовки в исходное положение. По лимбу винта верхних салазок суппорта подать резец влево на оставшийся припуск и подрезать второй торец окончательно. При подрезке торцов проходным отогнутым резцом с углом j= 45° предварительный проход выполнять перемещением резца от наружной поверхности заготовки к центру, окончательный проход — перемещением от центра к наружной поверхности заготовки. Прямолинейность торца заготовки после обработки проверить измерительной линейкой. Выпуклость торца не допускается. Все приведенные выше упражнения по обтачиванию цилиндрических поверхностей и подрезке торцов повторить несколько раз, после чего обработать заготовки, необходимые для проведения следующих занятий или изготовления деталей для продукции, выпускаемой учебными мастерскими.
Подрезание торца заготовки выполняют в такой последовательности: касаются вершиной головки резца торца заготовки и отвести резец от заготовки на себя; установить резец на требуемой размер (глубину резания или припуск по торцу), перемещая его влево; подать резец ручной поперечной подачей, уменьшая значение подачи при проходе вершины резца к оси заготовки.
СВЕРЛЕНИЕ И РАСТОЧКА ОТВЕРСТИЙ
Обработку отверстий на токарных станках выполняют различными режущими инструментами, выбор которых зависит от ваших заготовок, формы отверстия, точности и шероховатости поверхности отверстия. Заготовки крепят в шпинделе станка и сообщают им вращательное движение, а режущие инструменты — в пиноли задней бабки и сообщают им поступательное движение — подачу. В зависимости от формы и размеров заготовку крепят в трехкулачковом самоцентрирующемся патроне, в четырехкулачковом патроне, на планшайбе с помощью планок и болтов или другими способами. Обработку отверстий в сплошном металле заготовки производят спиральными сверлами. Когда длина отверстия превышает 5...10 диаметров, при так называемом глубоком сверлении, применяют специальные сверла (ружейные, пушечные, шпиндельные, кольцевые, центровочные и др.). Спиральные сверла диаметром до 10 мм с цилиндрическим хвостовиком закрепляют в трехкулачковом сверлильном патроне, который устанавливают непосредственно в коническое отверстие пиноли задней бабки. Если конус хвостовика сверлильного патрона меньше конуса конического отверстия пиноли, то необходимо использовать переходную коническую втулку. Спиральные сверла диаметром более 10 мм с цилиндрическим хвостовиком закрепляют в двухкулачковом сверлильном патроне, обладающем большей силой зажима Спиральные сверла с коническими хвостовиками устанавливают непосредственно в коническом отверстии пиноли задней бабки танка, а когда конус сверла меньше конического отверстия пиноли, то с помощью одной или нескольких переходных втулок. Различают предварительное и окончательное сверление. При предварительном сверлении диаметр сверла подбирают меньше окончательного диаметра на размер припуска, оставленного для окончательной обработки. После предварительного сверления может быть проведено рассверливание, т. е. сверление сверлом большего диаметра, зенкерование, развертывание или растачивание отверстия резцом. Выбор вида дальнейшей обработки зависит от точности обрабатываемого отверстия. Обработку центровых отверстий на торцовых поверхностях для установки заготовок в центрах станков осуществляют или последовательно сверлом и зенковкой, или за один прием комбинированным центровочным сверлом.
www.coolreferat.com
Бруштейн Б. Е. и Дементьев В. И. Токарное дело. Учебник для проф.-техн. училищ. Изд. 6-е, переработ, и доп. М., «Высш. школа», 1967, 448 с. с илл. // Библиотека технической литературы
В книге рассмотрена технология обработки деталей на токарных станках; приведены сведения об оборудовании, инструментах, приспособлениях и выборе наиболее рациональных режимов резания; освещены вопросы механизации и автоматизации процессов обработки деталей на токарных станках, а также вопросы техники безопасности при работе на этих станках; приведены примеры работы токарей-новаторов.Книга предназначена в качестве учебника для подготовки токарей в городских профессионально-технических училищах и может быть использована в сети индивидуального и бригадного обучения на промышленных предприятиях.
Размер: 10,8 МбФормат: djvuСкачать книгу с depositfiles.comСкачать книгу с rapidshare.comСкачать книгу с dropbox.comНе работает ссылка? Напишите об этом в комментарии.
Оглавление:
Предисловие к шестому изданию.Введение.Раздел первый. Краткие сведения о токарном деле.Глава I. Основные понятия об устройстве токарно-винторезного станка.§ 1. Назначение токарных станков.§ 2. Типы токарных станков.§ 3. Основные узлы токарно-винторезного станка.§ 4. Станина.§ 5. Передняя бабка.§ 6. Механизмы подачи.§ 7. Суппорт.§ 8. Фартук.§ 9. Задняя бабка.§ 10. Правила ухода за токарным станком.
Глава II. Основы процесса резания металлов.§ 1. Элементы резания при обработке на токарных станках§ 2. Процесс образования стружки.§ 3. Смазочно-охлаждающие жидкости.§ 4. Материалы, применяемые для изготовления резцов и других режущих инструментов.§ 5. Токарные резцы.§ 6. Заточка резцов.
Глава III. Краткие сведения о технике безопасности.§ 1. Значение техники безопасности.§ 2. Техника безопасности в механических цехах.§ 3. Правила пожарной безопасности.
Глава IV. Обтачивание наружных цилиндрических поверхностей.§ 1. Резцы для продольного обтачивания.§ 2. Установка и закрепление резца.§ 3. Установка и закрепление деталей в центрах.§ 4. Установка и закрепление деталей в патронах.§ 5. Навинчивание и свинчивание кулачковых патронов§ 6. Приемы обтачивания гладких цилиндрических поверхностей.§ 7. Приемы обтачивания цилиндрических поверхностей с уступами§ 8. Элементы режима резания при обтачивании.§ 9. Уход за резцом.§ 10. Измерение деталей при обтачивании цилиндрических поверхностей§ 11. Брак при обтачивании цилиндрических поверхностей и меры его предупреждения.§ 12. Техника безопасности при обтачивании цилиндрических поверхностей.
Глава V. Обработка торцовых поверхностей и уступов.§ 1. Резцы, применяемые при обработке торцовых поверхностей и уступов, и их установка.§ 2. Приемы подрезания торцовых поверхностей и уступов§ 3. Приемы измерения торцовых поверхностей и уступов.§ 4. Техника безопасности при подрезании торцовых поверхностей и уступов.§ 5. Брак при подрезании торцовых поверхностей и уступов и меры его предупреждения.
Глава VI. Вытачивание наружных канавок и отрезание.§ 1. Резцы для вытачивания канавок и отрезания, их установка.§ 2. Приемы вытачивания канавок и отрезания.§ 3. Измерение канавок.§ 4. Брак при вытачивании канавок и отрезании и меры его предупреждения.
Глава VII Сверление и рассверливание цилиндрических отверстий.§ 1. Сверла.§ 2. Затачивание спиральных сверл.§ 3. Закрепление сверл.§ 4. Приемы сверления..§ 5 Элементы режима резания при сверлении.§ 6. Рассверливание.§ 7. Особенности конструкций некоторых типов сверл.§ 8. Замена ручной подачи механической.§ 9. Брак при сверлении и меры его предупреждения.
Глава VIII. Центрование.§ 1. Назначение и формы центровых отверстий.§ 2. Разметка центровых отверстий.§ 3. Приемы центрования.§ 4. Брак при центровании и меры его предупреждения.
Глава IX. Зенкерование, развертывание и растачивание цилиндрических отверстий. Вытачивание внутренних канавок.§ 1. Зенкерование цилиндрических отверстий.§ 2. Развертывание цилиндрических отверстий.§ 3. Растачивание цилиндрических отверстий.§ 4. Приемы растачивания сквозных и глухих цилиндрических отверстий.§ 5. Брак при обработке цилиндрических отверстий и меры его предупреждения.§ 6. Приемы подрезания внутренних торцовых поверхностей и вытачивания внутренних канавок.§ 7. Измерение цилиндрических отверстий, внутренних канавок и выточек.
Глава X. Токарная обработка несложных деталей.§ 1. Токарная обработка штыря.§ 2. Токарная обработка гладких и ступенчатых валов.
Глава XI. Основные принципы построения технологических процессов обработки деталей на токарных станках.§ 1. Понятие о технологическом и производственном процессах§ 2. Элементы технологического процесса.§ 3. Типы производств в машиностроении.§ 4. Принципы разработки технологического процесса механической обработки.§ 5. Понятие об установочных базах и их выбор.
Раздел второй. Обработка конических поверхностей. Обтачивание фасонных поверхностей. Отделка поверхностей. Нарезание треугольной резьбы.Глава XII. Обработка конических поверхностей.§ 1. Понятие о конусе и его элементах.§ 2. Способы получения конических поверхностей.§ 3. Обтачивание конических поверхностей поперечным смещением корпуса задней бабки.§ 4. Обтачивание конических поверхностей поворотом верхней части суппорта.§ 5. Обработка конических поверхностей с применением конусной линейки.§ 6. Обработка конических поверхностей широким резцом.§ 7. Растачивание и развертывание конических отверстий.§ 8. Измерение конических поверхностей.§ 9. Брак при обработке конических поверхностей и меры его предупреждения.
Глава XIII. Обтачивание фасонных поверхностей.§ 1. Фасонные резцы, их установка и работа ими.§ 2. Обтачивание фасонных поверхностей проходными резцами.§ 3. Обработка фасонных поверхностей по копиру.§ 4. Брак при обтачивании фасонных поверхностей и меры его предупреждения.
Глава XIV. Отделка поверхностей.§ 1. Шероховатость обработанной поверхности.§ 2. Тонкое точение.§ 3. Доводка или притирка.§ 4. Обкатывание поверхности роликом.§ 5. Накатывание.
Глава XV. Нарезание резьбы.§ 1. Общее сведения о резьбах.§ 2. Типы резьб и их назначение.§ 3. Измерение и контроль резьбы.§ 4. Нарезание треугольной резьбы плашками.§ 5. Нарезание треугольной резьбы метчиками.§ 6. Нарезание резьбы резцами.§ 7. Резьбовые гребенки.§ 8. Настройка токарно-винторезного станка для нарезания резьбы§ 9. Примеры подсчета сменных зубчатых колес.§ 10. Приемы нарезания резьбы резцами.§ 11. Высокопроизводительные методы нарезания резьбы.§ 12. Брак при нарезании резьбы резцами и меры его предупреждения.
Раздел третий. Токарные станки. Механизация и автоматизация процессов обработки деталей на токарных станках.Глава XVI. Устройство токарных станков.§ 1. Краткий исторический обзор развития токарного станка.§ 2. Основные типы станков токарной группы.§ 3. Условное обозначение токарных станков.§ 4. Основные характеристики токарно-винторезных станков отечественного производства.§ 5. Приводы токарных станков.§ 6. Кинематическая схема станка.§ 7. Механизмы коробок скоростей и подач.§ 8. Суппорт токарно-винторезного станка.§ 9. Фартук.§ 10. Токарно-винторезный станок модели 1К62.§ 11. Станки токарной группы.
Глава XVII. Проверка токарно-винторезного станка на точность.§ 1. Инструмент для проверки станков на точность.§ 2. Основные методы проверки токарного станка.
Глава XVIII. Механизация и автоматизация процессов обработки деталей на токарных станках.§ 1. Устройства, механизирующие процесс обработки на токарных станках.§ 2. Устройства, автоматизирующие процесс обработки на токарных станках.§ 3. Станки с программным управлением.§ 4. Автоматические линии.
Раздел четвертый. Основы учения о резании металлов.Глава XIX. Общие сведения о резании.§ 1. Краткий исторический обзор.§ 2. Материалы, применяемые для изготовления режущих инструментов.§ 3. Углы резца.§ 4. Установка резца.
Глава XX. Основные процессы резания.§ 1. Процесс образования стружки.§ 2. Основные сведения о силах, действующих на резец.§ 3. Теплота резания.§ 4. Стойкость резца.§ 5. Охлаждение инструмента.§ 6. Влияние различных факторов на выбор скорости резания.
Раздел пятый. Высокопроизводительное резание металлов. Выбор наивыгоднейших режимов резания.Глава XXI. Высокопроизводительное резание металлов.§ 1. Сущность скоростного резания металлов.§ 2. Геометрия резцов для скоростного резания.§ 3. Современные конструкции высокопроизводительных резцов.§ 4. Требования, предъявляемые к станкам для скоростного точения.§ 5. Приспособления, применяемые при скоростном резании.§ 6. Приспособления для отвода стружки.§ 7. Неполадки при скоростном точении.§ 8. Основные правила работы резцами, оснащенными пластинками из твердых сплавов.
Глава XXII. Выбор наивыгоднейших режимов резания.§ 1. Понятие о производительности труда.§ 2. Понятие о мощности при точении.§ 3. Крутящий момент.§ 4. Паспорт токарного станка.§ 5. Выбор наивыгоднейших режимов резания.Раздел шестой. Сложные токарные работы.
Глава XXIII. Нарезание прямоугольной и трапецеидальной резьб.§ 1. Общие сведения о резьбах для передачи движения.§ 2. Нарезание прямоугольной и трапецеидальной резьб.§ 3. Способы нарезания многозаходных резьб.§ 4. Деление многозаходных резьб на заходы.§ 5. Высокопроизводительные методы нарезания многозаходных.§ 6. Основные сведения о нарезании резьбы вращающимися резцами.
Глава XXIV. Токарная обработка деталей со сложной установкой.§ 1. Обработка деталей в люнетах.§ 2. Обработка деталей на планшайбе.§ 3. Обработка деталей на угольниках.§ 4. Обработка деталей на оправках.§ 5. Обработка эксцентриковых деталей.
Раздел седьмой. Организация рабочего места и труда токаря. Технологический процес обработки деталей на токарных станках.Глава XXV. Организация рабочего места и труда токаря.§ 1. Организация рабочего места токаря.§ 2. Планировка рабочего места токаря.§ 3. Порядок и чистота на рабочем месте.§ 4. Организация труда на рабочем месте.§ 5. Многостаночная работа.
Глава XXVI. Рациональные методы токарной обработки.§ 1. Технологические приемы, применяемые токарями-новаторами.§ 2. Сокращение основного (машинного) времени.§ 3. Сокращение вспомогательного времени.§ 4. Комплексный метод сокращения штучного времени.
Глава XXVII. Технологический процесс обработки деталей на станках.§ 1. Общие сведения о разработке технологического процесса обработки деталей.§ 2. Порядок составления технологического процесса обработки деталей.§ 3. Метод групповой обработки деталей.§ 4. Карты технологического процесса обработки деталей на станках§ 5. Технологическая дисциплина.
Глава XXVIII. Технологические процессы обработки деталей на токарных станках.§ 1. Технологический процесс токарной обработки втулок.§ 2. Технологический процесс токарной обработки дисков.§ 3. Технологический процесс токарной обработки стаканов.
Глава XXIX. Примеры составления технологических процессов обработки деталей на токарных станках.§ 1. Обработка ступенчатого валика.§ 2. Обработка нажимной гайки.
Приложение I. Паспорт токарно-винторезного станка модели 1К12.Приложение II. Классификатор переходов.Приложение III. Операционная карта механической обработки.Приложение IV. Технологическая карта механической обработки ступенчатого валика.Приложение V. Технологическая карта механической обработки нажимной гайки.
techlib.org
Описание специальности токарное делоТокарное дело и токарная обработка - это обработка резанием на токарном оборудовании с применением различных операций: резание металлов, неметаллов и сплавов, нарезание резьб различной сложности, обточка и расточка различных профилей, точение конусов, канавок, сфер и многое другое. Токарные работы - это годная или можно сказать окончательная продукция получаемая путем обработки на станках токарной группы, к ним можно отнести: корпуса различной сложности, клапана, плунжера, болты, гайки, мелкие пружины, крышки, заглушки, переходники, трубы, шнеки и многие другие работы. Токарное производство - к токарному производству можно отнести мелкое предприятие с небольшим участком и крупный завод с несколькими цехами. Как такового понятия токарное производство не существует, но можно классифицировать это понятие как: предприятие или завод принимающий заказы по обработке различных материалов и сплавов на токарном оборудовании от штучного заказа до серийного. Токарное дело это целая наука состоящая из большого количества материала и для освоения этой профессии необходимы знания и навыки работы. В токарное дело входят науки о резании, термообработки, материаловедение, черчение, сопромат и много других наук. Для молодых рабочих могу сказать: придя на предприятие или обучение на дому, учебных организациях осваивайте побольше теории и вникайте в суть процесса. Не торопитесь освоить все полностью, у вас это не получится, так как даже токаря с большим навыком работы и большим знанием теории не совершенны в своем деле (век живи век учись), не спорю такие токаря многое умеют и знают. Начинайте освоение с общих положений, техники безопасности, организации рабочего места, токарного станка, чертежей, допусков и посадок, правильной заточки инструмента (углы), измерительные приборы, металлы и сплавы, режимы резания после чего можно делать другой шаг. Не старайтесь в первый же день встать за станок, для новичков это может быть опасно. В процессе обучения смотрите внимательно за работой наставника (подготовка к работе, настройка станка, непосредственно сам процесс, замеры, уборка оборудования), чаще спрашивайте его о работе. Изучите мерительный инструмент, правила замера и попробуйте сделать несколько замеров для закрепления. После получения базовых теоретических знаний под руководством наставника попробуйте практически поработать, чтобы понять сам процесс. Для быстрого освоения профессии старайтесь побольше работать практически и не забывайте о теории. После получения теоретических и практических навыков работайте над скоростью изготовления продукции и качеством. Беритесь за изготовление сложных деталей, корпусов, клапанов, плунжеров, распределителей, поршней, шнеков и многих других. Старайтесь разрабатывать инновации в области резания и заточки режущего инструмента. Посещайте форумы, читайте о новинках токарного дела, развивайтесь и не стойте на одном месте, и только в этом случае вы достигните больших успехов в этой профессии. Город Красноярск имеет множество различных учебных заведений обучающие токарному делу, а так же есть предприятия и крупные заводы принимающие молодых рабочих для обучения токарного дела. |
www.tokar-work.ru
Оглавление: | Предисловие к шестому изданию [3]Введение [4]Раздел первый. Краткие сведения о токарном деле Глава I. Основные понятия об устройстве токарно-винторезного станка [7] § 1. Назначение токарных станков [7] § 2. Типы токарных станков [7] § 3. Основные узлы токарно-винторезного станка [8] § 4. Станина [10] § 5. Передняя бабка [10] § 6. Механизмы подачи [12] § 7. Суппорт [15] § 8. Фартук [17] § 9. Задняя бабка [19] § 10. Правила ухода за токарным станком [20] Глава II. Основы процесса резания металлов [22] § 1. Элементы резания при обработке на токарных станках [22] § 2. Процесс образования стружки [25] § 3. Смазочно-охлаждающие жидкости [26] § 4. Материалы, применяемые для изготовления резцов и других режущих инструментов [27] § 5. Токарные резцы [30] § 6. Заточка резцов [35] Глава III. Краткие сведения о технике безопасности [38] § 1. Значение техники безопасности [38] § 2. Техника безопасности в механических цехах [39] § 3. Правила пожарной безопасности [41] Глава IV. Обтачивание наружных цилиндрических поверхностей [41] § 1. Резцы для продольного обтачивания [42] § 2. Установка и закрепление резца [43] § 3. Установка и закрепление деталей в центрах [45] § 4. Установка и закрепление деталей в патронах [49] § 5. Навинчивание и свинчивание кулачковых патронов [52] § 6. Приемы обтачивания гладких цилиндрических поверхностей [53] § 7. Приемы обтачивания цилиндрических поверхностей с уступами [56] § 8. Элементы режима резания при обтачивании [59] § 9. Уход за резцом [60] § 10. Измерение деталей при обтачивании цилиндрических поверхностей [60] § 11. Брак при обтачивании цилиндрических поверхностей и меры его предупреждения [64] § 12. Техника безопасности при обтачивании цилиндрических поверхностей [65] Глава V. Обработка торцовых поверхностей и уступов [68] § 1. Резцы, применяемые при обработке торцовых поверхностей и уступов, и их установка [68] § 2. Приемы подрезания торцовых поверхностей и уступов [70] § 3. Приемы измерения торцовых поверхностей и уступов [73] § 4. Техника безопасности при подрезании торцовых поверхностей и уступов [73] § 5. Брак при подрезании торцовых поверхностей и уступов и меры его предупреждения [75] Глава VI. Вытачивание наружных канавок и отрезание [76] § 1. Резцы для вытачивания канавок и отрезания, их установка [76] § 2. Приемы вытачивания канавок и отрезания [79] § 3. Измерение канавок [83] § 4. Брак при вытачивании канавок и отрезании и меры его предупреждения [84] Глава VII. Сверление и рассверливание цилиндрических отверстий [85] § 1. Сверла [85] § 2. Затачивание спиральных сверл [88] § 3. Закрепление сверл [89] § 4. Приемы сверления [90] § 5 Элементы режима резания при сверлении [91] § 6. Рассверливание [92] § 7. Особенности конструкций некоторых типов сверл [93] § 8. Замена ручной подачи механической [96] § 9. Брак при сверлении и меры его предупреждения [97] Глава VIII. Центрование [98] § 1. Назначение и формы центровых отверстий [98] § 2. Разметка центровых отверстий [100] § 3. Приемы центрования [101] § 4. Брак при центровании и меры его предупреждения [103] Глава IX. Зенкерование, развертывание и растачивание цилиндрических отверстий. Вытачивание внутренних канавок [103] § 1. Зенкерование цилиндрических отверстий [103] § 2. Развертывание цилиндрических отверстий [106] § 3. Растачивание цилиндрических отверстий [109] § 4. Приемы растачивания сквозных и глухих цилиндрических отверстий [113] § 5. Брак при обработке цилиндрических отверстий и меры его предупреждения [115] § 6. Приемы подрезания внутренних торцовых поверхностей и вытачивания внутренних канавок [116] § 7. Измерение цилиндрических отверстий, внутренних канавок и выточек [117] Глава X. Токарная обработка несложных деталей [121] § 1. Токарная обработка штыря [121] § 2. Токарная обработка гладких и ступенчатых валов [125] Глава XI. Основные принципы построения технологических процессов обработки деталей на токарных станках [130] § 1. Понятие о технологическом и производственном процессах [130] § 2. Элементы технологического процесса [131] § 3. Типы производств в машиностроении [132] § 4. Принципы разработки технологического процесса механической обработки [134] § 5. Понятие об установочных базах и их выбор [134]Раздел второй. Обработка конических поверхностей. Обтачивание фасонных поверхностей. Отделка поверхностей. Нарезание треугольной резьбы Глава XII. Обработка конических поверхностей [138] § 1. Понятие о конусе и его элементах [138] § 2. Способы получения конических поверхностей [141] § 3. Обтачивание конических поверхностей поперечным смещением корпуса задней бабки [141] § 4. Обтачивание конических поверхностей поворотом верхней части суппорта [144] § 5. Обработка конических поверхностей с применением конусной линейки [145] § 6. Обработка конических поверхностей широким резцом [148] § 7. Растачивание и развертывание конических отверстий [148] § 8. Измерение конических поверхностей [150] § 9. Брак при обработке конических поверхностей и меры его предупреждения [154] Глава XIII. Обтачивание фасонных поверхностей [155] § 1. Фасонные резцы, их установка и работа ими [155] § 2. Обтачивание фасонных поверхностей проходными резцами [159] § 3. Обработка фасонных поверхностей по копиру [160] § 4. Брак при обтачивании фасонных поверхностей и меры его предупреждения [162] Глава XIV. Отделка поверхностей [163] § 1. Шероховатость обработанной поверхности [163] § 2. Тонкое точение [165] § 3. Доводка или притирка [169] § 4. Обкатывание поверхности роликом [170] § 5. Накатывание [171] Глава XV. Нарезание резьбы [173] § 1. Общее сведения о резьбах [173] § 2. Типы резьб и их назначение [176] § 3. Измерение и контроль резьбы [178] § 4. Нарезание треугольной резьбы плашками [181] § 5. Нарезание треугольной резьбы метчиками [182] § 6. Нарезание резьбы резцами [185] § 7. Резьбовые гребенки [188] § 8. Настройка токарно-винторезного станка для нарезания резьбы [190] § 9. Примеры подсчета сменных зубчатых колес [193] § 10. Приемы нарезания резьбы резцами [196] § 11. Высокопроизводительные методы нарезания резьбы [198] § 12. Брак при нарезании резьбы резцами и меры его предупреждения [200]Раздел третий. Токарные станки. Механизация и автоматизация процессов обработки деталей на токарных станках Глава XVI. Устройство токарных станков [202] § 1. Краткий исторический обзор развития токарного станка [202] § 2. Основные типы станков токарной группы [205] § 3. Условное обозначение токарных станков [206] § 4. Основные характеристики токарно-винторезных станков отечественного производства [206] § 5. Приводы токарных станков [207] § 6. Кинематическая схема станка [208] § 7. Механизмы коробок скоростей и подач [208] § 8. Суппорт токарно-винторезного станка [215] § 9. Фартук [217] § 10. Токарно-винторезный станок модели 1К62 [222] § 11. Станки токарной группы [232] Глава XVII. Проверка токарно-винторезного станка на точность [238] § 1. Инструмент для проверки станков на точность [239] § 2. Основные методы проверки токарного Станка [240] Глава XVIII. Механизация и автоматизация процессов обработки деталей на токарных станках [244] § 1. Устройства, механизирующие процесс обработки на токарных станках [245] § 2. Устройства, автоматизирующие процесс обработки на токарных станках [248] § 3. Станки с программным управлением [256] § 4. Автоматические линии [263]Раздел четвертый. Основы учения о резании металлов Глава XIX. Общие сведения о резании [268] § 1. Краткий исторический обзор [268] § 2. Материалы, применяемые для изготовления режущих инструментов [269] § 3. Углы резца [274] § 4. Установка резца [279] Глава XX. Основные процессы резания [282] § 1. Процесс образования стружки [282] § 2. Основные сведения о силах, действующих на резец [287] § 3. Теплота резания [291] § 4. Стойкость резца [291] § 5. Охлаждение инструмента [293] § 6. Влияние различных факторов на выбор скорости резания [293]Раздел пятый. Высокопроизводительное резание металлов. Выбор наивыгоднейших режимов резания Глава XXI. Высокопроизводительное резание металлов [303] § 1. Сущность скоростного резания металлов [303] § 2. Геометрия резцов для скоростного резания [303] § 3. Современные конструкции высокопроизводительных резцов [308] § 4. Требования, предъявляемые к станкам для скоростного точения [313] § 5. Приспособления, применяемые при скоростном резании [314] § 6. Приспособления для отвода стружки [321] § 7. Неполадки при скоростном точении [323] § 8. Основные правила работы резцами, оснащенными пластинками из твердых сплавов [325] Глава XXII. Выбор наивыгоднейших режимов резания [326] § 1. Понятие о производительности труда [326] § 2. Понятие о мощности при точении [328] § 3. Крутящий момент [330] § 4. Паспорт токарного станка [332] § 5. Выбор наивыгоднейших режимов резания [332]Раздел шестой. Сложные токарные работы Глава XXIII. Нарезание прямоугольной и трапецеидальной резьб [337] § 1. Общие сведения о резьбах для передачи движения [337] § 2. Нарезание прямоугольной и трапецеидальной резьб [339] § 3. Способы нарезания многозаходных резьб [345] § 4. Деление многозаходных резьб на заходы [346] § 5. Высокопроизводительные методы нарезания многозаходных резьб [347] § 6. Основные сведения о нарезании резьбы вращающимися резцами [348] Глава XXIV. Токарная обработка деталей со сложной установкой [351] § 1. Обработка деталей в люнетах [351] § 2. Обработка деталей на планшайбе [355] § 3. Обработка деталей на угольниках [357] § 4. Обработка деталей на оправках [358] § 5. Обработка эксцентриковых деталей [362]Раздел седьмой. Организация рабочего места и труда токаря. Технологический процесс обработки деталей на токарных станках Глава XXV. Организация рабочего места и труда токаря [368] § 1. Организация рабочего места токаря [368] § 2. Планировка рабочего места токаря [368] § 3. Порядок и чистота на рабочем месте [370] § 4. Организация труда на рабочем месте [370] § 5. Многостаночная работа [372] Глава XXVI. Рациональные методы токарной обработки [374] § 1. Технологические приемы, применяемые токарями-новаторами [374] § 2. Сокращение основного (машинного) времени [378] § 3. Сокращение вспомогательного времени [379] § 4. Комплексный метод сокращения штучного времени [382] Глава XXVII. Технологический процесс обработки деталей на станках [383] § 1. Общие сведения о разработке технологического процесса обработки деталей [383] § 2. Порядок составления технологического процесса обработки деталей [384] § 3. Метод групповой обработки деталей [385] § 4. Карты технологического процесса обработки деталей на станках [387] § 5. Технологическая дисциплина [387] Глава XXVIII. Технологические процессы обработки деталей на токарных станках [388] § 1. Технологический процесс токарной обработки втулок [388] § 2. Технологический процесс токарной обработки дисков [394] § 3. Технологический процесс токарной обработки стаканов [399] Глава XXIX. Примеры составления технологических процессов обработки деталей на токарных станках [403] § 1. Обработка ступенчатого валика [403] § 2. Обработка нажимной гайки [408]Приложение I. Паспорт токарно-винторезного станка модели 1К12 [412]Приложение II. Классификатор переходов [421]Приложение III. Операционная карта механической обработки [423]Приложение IV. Технологическая карта механической обработки ступенчатого валика [426]Приложение V. Технологическая карта механической обработки нажимной гайки [434] |
www.nehudlit.ru
ТОКАРНОЕ ДЕЛО
ТОКАРНОЕ ДЕЛО
Рукоятки: 1 — выбора и величины или шага резьбы (управление накидным зубчатым колесом конуса и блоками множительного механизма), 2 — выбора подачи или резьбы, 3, 20 — фрикционной муфты, 4, 7— уста
Новки чисел оборотов в минуту шпинделя, 5 — выбора увеличенного и нормального шага резьбы (управление блоком звена увеличения шага), 6 — настройки станка на нарезание правой или левой резьбы (управление механизмом трензеля), 8 — отключения реечного зубчатого колеса от рейки при нарезании резьбы, 9 — переме-
Щения поперечного суппорта, 10— поворота и зажима резцедержателя, 11 — перемещения верхних салазок суппорта, 13 — включения продольной и поперечной подач суппорта, 14 — зажима пинали задней бабки, 15 — крепления задней бабки, 21 — управления разъемной гайкой ходового винта; кнопки: 12—включения ускоренной подачи каретки и суппорта (включение и выключение электродвигателя и механизма ускоренного хода), 22 — пуска и остановки двигателя главного движения; маховички: 16 — подачи пиноли задней бабки, 23 — перемещения каретки; выключатели; 17 — местного освещения; 18 — общий; 19 — насоса подачи охлаждающей жидкости
Без машин немыслима жизнь человека в современном обществе. Уголь, руда, нефть добываются с помощью угольных комбайнов, врубовых машин, шагающих экскаваторов, буровых установок. Тепловозы, электровозы, теплоходы, самолеты, автомашины, мотоциклы перевозят людей и грузы, связывают самые отдаленные точки земного шара. Для изготовления различных видов оборудования применяют машины-орудия: молоты, прессы, металлорежущие станки.
В современном производстве сельскохозяйственных продуктов также используют различные машины. Машины выпекают хлеб, изготовляют обувь. Нас в быту также обслуживают машины: холодильники, пылесосы, полотеры И Т. д.
Коммунистическая партия и Советское правительство уделяют большое внимание развитию машиностроения — основы технического прогресса страны. Советское машиностроение после Великой Октябрьской социалистической революции прошло большой и нелегкий путь развития. К началу тридцатых годов Коммунистическая партия взяла курс на индустриализацию нашей страны, началось строительство промышленных предприятий. Уже в 1930 г. вступил в строй первенец отечественного тракторостроения — Сталинградский тракторный завод, через три года сельское хозяйство стало получать машины Челябинского тракторного завода. В июле 1933 г. вошел в строй гигант советского тяжелого машиностроения — Уральский машиностроительный завод (Уралмаш).
В годы Великой Отечественной войны машиностроительные предприятия нашей страны внесли огромный вклад в дело победы — оснащали Советскую Армию мощной боевой техникой: самолетами, танками, артиллерией, боеприпасами и другими средствами военной техники.
За исторически короткие сроки в СССР создана мощная, технически оснащенная машиностроительная индустрия. Еще в предвоенные годы Советский Союз освободился от иностранной экономической зависимости. В настоящее время наша страна не только производит, но и экспортирует многие современные машины и оборудование. По общему объему продукции машиностроения наша страна занимает первое место в Европе и второе место в мире.
Наши успехи в машиностроении прежде всего результат самоотверженного труда миллионов рабочих, инженеров и техников машиностроительных предприятий. Образцы творческого отношения к работе показывают тысячи передовиков и новаторов производства. Труд машиностроителей по достоинству оценен Коммунистической партией Советского Союза и Советским правительством. За достижения в создании и совершенствовании машин многие из них удостоены Государственной и Ленинской премий СССР, награждены орденами и медалями СССР. Лучшим присвоено высокое звание Героя Социалистического Труда. Машиностроение имеет первостепенное значение для технического перевооружения всего нашего народного хозяйства. Но для того чтобы успешно решить эту сложную задачу, необходимо машиностроение перестроить на базе новейшей технологии, оснастить его самыми совершенными средствами производства. внедрить комплексную механизацию и автоматизацию производственных процессов. Директивы XXIV съезда КПСС по пятилетнему плану на 1971 —1975 гг. предусматривают дальнейшее развитие всех отраслей машиностроения. Выпуск промышленной продукции машиностроения возрастет в 2,5 раза.
Современный машиностроительный завод — это сложный комплекс тесно связанных между собой различных цехов, отделов, служб. Например, заготовительные цехи производят заготовки, из которых в других цехах делают детали для машины. Некоторые заготовки получают в литейных цехах заливкой жидкого металла в специальные формы, другие — штамповкой из нагретого металла на молотах или прессах или — штамповкой в холодном состоянии из листового металла, или изготовляют из проката.
Чтобы получить деталь нужной формы с требуемыми размерами и качеством поверхности (шероховатостью), заготовку подвергают обработке резанием, т. е. срезают с ее поверхности лишние слои металла. Обработку резанием осуществляют обычно на металлорежущих станках, в том числе и на токарных: универсальных (токарно-винторезные) и револьверных станках, многорезцовых полуавтоматах, одношпиндельных и многошпиндельных автоматах, лобовых и карусельных станках и др. Среди рабочих-станочников одной из широко распространенных специальностей является токарь, так как токарные станки — это самая крупная группа станков в механическом цехе. Специальность токаря необходима не только на машиностроительных заво-< дах. На любом предприятии есть цехи или мастерские, где ремонтируют машины, изготовляют детали взамен изношенных. Здесь также основным видом оборудования является токарный станок и ведущим рабочим—токарь. Чтобы стать токарем, нужно знать свойства металлов и их назначение, уметь читать чертежи, знать режущие инструменты, уметь их затачивать и правильно эксплуатировать, хорошо знать устройство, работу и наладку станка.
Кадры рабочих для машиностроения, так же как и для других отраслей народного хозяйства, готовит система профтехобразования. Учащиеся училищ профтехобразования получают необходимую теоретическую подготовку, приобретают практические навыки работы на современном оборудовании.
Программа обучения токарей в профессионально-технических училищах построена таким образом, что сначала учащиеся знакомятся с устройством и работой токарного станка и основами токарной обработки и затем, сочетая теоретическое обучение с практическими занятиями в учебных мастерских, более глубоко изучают различные виды токарной обработки, наладку станка, рациональную эксплуатацию инструментов, знакомятся с организацией и экономикой машиностроительных предприятий.
В уличище молодой рабочий получает специальность токаря второго - третьего разряда.
Это определенный минимум знаний и навыков, который нужен токарю для выполнения сравнительно несложных работ. А потом перед ним открывается широкая дорога творческого труда, дальнейшей учебы, совершенствования мастерства.
Счастливого трудового пути тебе, молодой друг!
По закону сохранения энергии энергия, затраченная на процесс резания, не может исчезнуть: она превращается в другой вид —в тепловую энергию. В зоне резания возникает теплота резания. В процессе резания больше …
Особенностью современного технического прогресса является автоматизация на базе достижений электронной техники, гидравлики и пневматики. Главными направлениями автоматизации являются применение следящих (копировальных) устройств, автоматизация управления станками и контроля деталей. Автоматическое управление …
Рассмотренные ранее правила выбора установочных баз справедливы и при изготовлении деталей с участками сложной формы. Однако не всегда такие участки удобны для использования их в качестве баз, в других случаях, …
msd.com.ua