Спиральные концевые фрезы из цельного твердого сплава CTA (ITALTRADE) и SISTEMI Klein (Италия). Твердый сплав фрезы
Материалы, применяемые для изготовления фрез
Категория:
Фрезерные работы
Материалы, применяемые для изготовления фрезМатериалы, применяемые для изготовления фрез, должны обладать следующими свойствами: высокой твердостью, превышающей твердость обрабатываемого материала, высокой износостойкостью и теплостойкостью, высокой механической прочностью. Для изготовле-
ния режущих инструментов и, в частности, фрез применяют углеродистые легированные инструментальные стали, быстрорежущие инструментальные стали, твердые сплавы, минерало-керамику, сверхтвердые материалы, синтетические и естественные алмазы.
Для изготовления режущего инструмента применяют инструментальные углерод-истые стали следующих марок: У7, У8, У9, У10, У11, У12, У13 (буква У указывает на то, что сталь углеродистая, а цифры показывают среднее содержание углерода в десятых долях процента). Инструментальные стали повышенного качества, имеющие минимальное количество вредных примесей, отмечают буквой А: У10А, У8А и т. д. Углеродистая инструментальная сталь обладает низкими режущими свойствами. Режущие инструменты, изготовленные из такой стали, позволяют вести обработку при температуре в зоне резания до 200—250 °С и при скоростях резания в пределах 10— 15 м/мин.
Легированная инструментальная сталь по химическому составу отличается от углеродистой инструментальной стали лишь наличием одного или нескольких легирующих элементов: хрома, вольфрама, молибдена, ванадия. Чаще всего для изготовления прорезных, фасонных и концевых фрез малых диаметров применяют следующие марки стали: ХГ, ХВ5, 9ХС и ХВГ. Легированная инструментальная сталь обладает более высокими режущими свойствами, чем углеродистая инструментальная сталь (температура в зоне резания 300—350 °С, скорость резания 20— 25 м/мин).
Быстрорежущая инструментальная стальв отличие от углеродистой и легированной инструментальной стали обладает большим сопротивлением износу и большой теплостойкостью. Она обладает красностойкостью, т. е. не теряет своих свойств при температуре красного каления (550—600 °С)
В СССР установлены единые условные обозначения (из букв и цифр) химического состава стали. Первые две цифры показывают среднее содержание углерода, буквами обозначают легированные элементы (В — вольфрам, Ф — ванадий, К — кобальт, М — молибден и т. д.), а цифрами справа от буквы — их среднее содержание (в процентах). Буквой Р обозначают быстрорежущую сталь.
В настоящее время наибольшее применение для изготовления всех видов цежущего инстру-. мента при обработке обычных конструкционных материалов применяются следующие марки стали: Р6М5, Р6МЗ и Р12. В последнее время УкрНИИспецсталь разработал новую марку быстрорежущей стали 11АРЗМЗФ2 с пониженным содержанием вольфрама (1,1% углерода, азот, ванадий, молибден).
Для обработки высокопрочных нержавею-щих сталей и сплавов в условиях повышенного j разогрева режущих кромок, а также для обработки сталей и сплавов повышенной твердости и вязкости при работе с ударами применяют I следующие марки стали: Р18КФ2, Р10К5ФЗ, Р9К5, Р6М5К5, Р12Ф2К8МЗ, Р9М4К8 и др. Эти марки часто применяются также для изготовления зуборезного инструмента.
Твердые сплавы допускают работу со скоростями резания, превышающими в 5— 10 раз скорости обработки быстрорежущими I инструментальными сталями, и не теряют режущих свойств при температуре до 80 °С и выше. Металлокерамические твердые сплавы I состоят из карбидов вольфрама, титана или тантала и кобальта, связывающего эти вещества. Различают вольфрамо-кобальтовые металлокерамические сплавы (ВК2, ВКЗ, ВКЗМ, ВК6, ВК6М, ВК5Н, ВК10, ВК10М, ВК15М, ВК8, ВК6-ОМ, ВК8-ОМ, ВКЮ-ОМ, ВК15-ОМ и др.) и титаново-вольфрамо-кобальтовые (Т5К10, Т14К8, Т15К6, Т30К4, Т60К6 и др.). Цифры после букв указывают процентное содержание в сплаве кобальта и титана.
Например, сплав Т14К8 состоит из 14% карбида титана, 8% кобальта и 78% карбида вольфрама.
Выпускают трехкарбидные твердые сплавы, состоящие из кобальта (связки) и карбидов вольфрама, титана, тантала. Эти сплавы характеризуются высокой прочностью. Твердый сплав марки ТТ7К12 допускает работу в 1,5—2 раза большими подачами на зуб, чем сплав Т5К10. Твердые сплавы выпускаются в виде пластинок стандартных форм и размеров.
Вольфрамо-кобальтовые сплавы применяют для обработки хрупких материалов: чугуна, бронзы, закаленной стали, пластмасс, фарфора и т. п. Твердые сплавы титано-вольфрамовой группы предназначены главным образом для обработки сталей. Сплав ТТ20К9 специально предназначен для фрезерования стали (например, для фрезерования глубоких пазов). Он отличается повышенным сопротивлением тепловым и механическим циклическим нагрузкам. Наиболее прочными сплавами при черновой обработке стали являются сплавы марок ТТ7К12 и Т5К12Б.
С уменьшением размеров зерен карбидов вольфрама износостойкость и твердость сплава увеличиваются. Эту закономерность используют при создании сплавов различного назначения с требуемыми свойствами. Первыми мелкозернистыми сплавами были сплавы марок ВКЗМ и ВК6М. В последнее время разработаны твердые сплавы с особо мелкозернистой (ОМ) структурой — ВК6-ОМ, ВКЮ-ОМ и ВК15-ОМ.
Стойкость твердосплавного инструмента повышается при нанесении на его поверхность изностойких слоев (5—15 мкм) карбидов (титана, ниобия), боридов, нитридов и др.
Минерал о керамическ ие спла-в ы приготовляют на основе окиси алюминия А/203 (корунда) путем тонкого размола, прессования и спекания. Выпускают их, как и твердые сплавы, в виде пластинок стандартных форм и размеров. В настоящее время промышленное применение имеют две марки минеральной керамики: ЦМ-332 и ВЗ. Минеральная керамика марки ВЗ обладает большей (в 1,5—2 раза) прочностью по сравнению с керамикой марки ЦМ-332. В состав керамики марки ВЗ помимо окиси алюминия входят сложные карбиды тугоплавких металлов.
Минералокерамические пластинки обладают большей теплостойкостью и износостойкостью, чем некоторые твердые сплавы. Однако они имеют пониженную по сравнению с твердыми сплавами прочность и повышенную хрупкость. Минералокерамика находит применение при чистовом и тонком фрезеровании торцовыми фрезами (головками) с неперетачиваемыми пластинками.
Сверхтвердые материалы (СТМ) являются поликристаллическим образованием на основе кубического нитрида бора. В эту группу входят композит 01 (эльбор-Р), композит 05 и композит 10 (гексанит-Р), ПТНБ (поликристалл твердого нитрида бора), «зубр», «бел-бор» и др.
Сверхтвердые материалы значительно превосходят минеральную керамику и твердые сплавы по термоусталостной прочности. Эль-бор-Р, гексанит-Р, ПТНБ и др. применяют для оснащения резцов, фрез, а также при изготовлении абразивного инструмента для заточки металлического (лезвийного) инструмента.
Сверхтвердые материалы для металлического инструмента выпускаются в виде цилиндрических вставок диаметром от 4 до 8 мм и длиной от 4 до 8 мм.
Сверхтвердые материалы на основе нитрида бора химически инертны к черным металлам, а материалы на основе углерода (алмазы) к ним химически активны. Это различие и определяет область их применения: сверхтвердые материалы применяются для обработки сталей, чугу-нов, ряда труднообрабатываемых сплавов; поликристаллические алмазы — для обработки цветных металлов, титановых сплавов, стеклопластиков и др. Для обработки сверхтвердых материалов можно применять только алмазы, которые превосходят их по твердости.
Синтетические алмазы (типа «карбонадо» и «баллас») выпускаются в виде порошков и кристаллов. Из синтетических
алмазных порошков изготовляют алмазно-абразивные инструменты. Круги из синтетических алмазов успешно применяются при заточке и доводке твердосплавных режущих инструментов (в том числе и фрез), а также для шлифования и доводки драгоценных камней, в том числе и самого алмаза. Алмазные резцы и фрезы применяют в основном в качестве чистового (отделочного) инструмента при резании цветных металлов, сплавов и неметаллических материалов.
Читать далее:
Износ и стойкость фрез
Статьи по теме:
pereosnastka.ru
WS40PM – универсальный фрезерный твёрдый сплав с жаропрочной начинкой решает проблемы
История и традиции
Первым в мире твёрдым сплавом для режущего инструмента был сплав «WIDIA», изобретённый на заводе Krupp в г. Эссен (Германия) в 1925 году. Он был «твёрд как алмаз» (WIe DIAmant) по сравнению с основным применяющимся в то время инструментальным материалом – быстрорежущей сталью, что значительно повысило скорость обработки деталей на заводах Европы, а спустя несколько лет – когда твёрдый сплав научились изготавливать и другие инструментальные компании – и всего мира.
Став самостоятельной структурой, WIDIA разрабатывала и приносила миру металлообработки всё больше и больше новых инструментальных решений – первую универсальную модульную систему инструментальной оснастки, передовые конструкции корпусных фрез для обработки шеек коленчатых валов, фрезы для обработки блоков цилиндров и многие другие инновации, но никогда не забывала о совершенствовании структуры самого твёрдого сплава.
Жаропрочность
Наибольшую сложность в обработке среди всех материалов представляют сплавы на никелевой и титановой основе (группы ISO S, сплавы типа ХН77ТЮР, ХН68МБТЮ, ВТ6, ВТ22, ВТ23, Ti5553), благодаря сложной высокопрочной структуре, карбидным включениям, и низкой теплопроводности. А с всё большим применением их в технике, прежде всего, авиационной, повышаются требование и к материалу режущей части инструментов, которые должны позволять станкам обрабатывать данные материалы быстрее, использовать возможности станка на 100%.
При механической обработке данных материалов тепло не уходит со стружкой (как это происходит при обработке стали, например), а остаётся в зоне резания и воздействует на режущую кромку, приводя к её преждевременному износу.
«Клин клином вышибают»
После скрупулёзного анализа проблемы и долгой исследовательской работы инженеры по фрезерным твёрдым сплавам WIDIA совершили то, что все от WIDIA в первую очередь и ждали, — изобрели новый твёрдый сплав для фрезерования труднообрабатываемых материалов под названием WS40PM. Но не простой, а жаропрочный!
Инженеры поработали над оптимизацией химического состава карбидов и связки, а также подобрали оптимальное износостойкое покрытие PVD AlTiN-TiN последнего поколения.
Результат работы позволил новому сплаву долго сохранять свои свойства при высоких температурах. И теперь можно применять на повышенных скоростях резания как на черновой (область применения S40), получистовой (S20-S30), так как чистовой обработке (S10-S15). Тоже самое касается и обработки нержавеющих сталей.
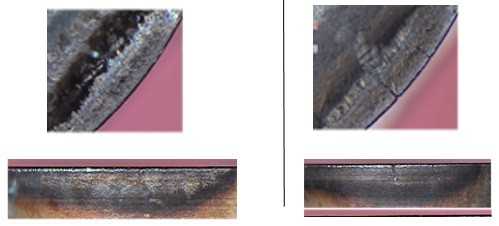
Износ после часа работы: слева – сплав с оптимизированной структурой, справа – с обычной
Режущие пластины из WS40PM отлично сопротивляются как ударам, нестабильным условиям резания при черновой обработке, так и высоким температурам. Это позволило значительно повысить стойкость. Разница в стойкости с обычными сплавами ещё больше увеличивается при работе с большой шириной фрезерования – когда режущая кромка зуба фрезы дольше остаётся в металле и сильнее нагревается.
Более того, стало возможно успешно обрабатывать материалы типа Hardox 400 и материалы деталей турбокомпрессоров. А после массовых испытаний в цехах предприятий оказалось, что фрезы с пластинами из сплава WS40PM показывают высокую стойкость не только на материалах групп S и M, но и на обычных углеродистых и легированных сталях. Это позволяет успешно применять данное решение как широкоуниверсальное и считать его полноценной заменой легендарному универсальному фрезерному сплаву WIDIA TN6540.
Повышенная жаропрочность нового сплава позитивно сказалась на результатах во фрезеровании как всех видов титановых и никелевых сплавов (группа S1-S4), так и нержавеющих сталей (группы M1, M2, M3) и позволяет поднять скорость резания на 20%, а стойкость – в 2 и более раз по сравнению со сплавами аналогичной группы применения (M40, S40).
«На предприятии в Англии нам поставили задачу увеличить стойкость инструмента при фрезеровании плоскостей заготовок, изготовленных из Inconel 625 (аналог ХН75МБТЮ). На тот момент стойкость используемого инструмента была равна 1,5 детали. Мы применили фрезу для работы на высоких подачах M1200HF с пластинами 12-ю режущими кромками из нового WS40PM. При подаче 0,5 мм/зуб и скорости резания 45 м/мин удалось достичь впечатляющего результата – 6 деталей. А благодаря превосходству по количеству режущих кромок стойкость на пластину возросла в 18 раз!», говорит Майк Сперхаке, региональный продукт менеджер.
Где найти, как применить и решить задачу
Из сплава WS40PM изготавливаются режущие пластины для большинства современных серий фрез WIDIA:
- M1200 бестселлер для обработки плоскостей и фрезерования на высоких подачах
- M640 для обработки плоскостей на маломощных станках
- VSM11, VSM17, VSM490 и M690 для обработки прямоугольных уступов, универсальные
- M100 и M200 – с круглыми пластинами для контурного фрезерования и обработки плоскостей
- M370 для обработки на высоких подачах
Перечень пластин из сплава WS40PM, а также режимы резания, показаны в каталоге по новым продуктам WIDIA – «Достижения 2018».
Сами же фрезы под них указаны в следующих каталогах:
Больше информации о фрезах с пластинами из сплава WS40PM Вы сможете найти, связавшись с ближайшим авторизованным дистрибьютором WIDIA по ссылке https://www.widia.com/ru/distributor.html, либо позвонив по телефону 8 (800) 333-49-36 (звонок бесплатный).
Владимир Жеребцов,
Региональный продукт менеджер,
WIDIA Восточная и Юго-Восточная Европа,
Также советуем прочитать:
Нет связанных записей.
Понравилась статья? Поделитесь:
tverdysplav.ru
Материалы, применяемые для изготовления фрез, должны обладать следующими свойствами: высокой твердостью, превышающей твердость обрабатываемого материала, высокой износостойкостью и теплостойкостью, высокой механической прочностью. Для изготовления режущих инструментов и, в частности, фрез применяют углеродистые легированные инструментальные стали, быстрорежущие инструментальные стали, твердые сплавы, минералокерамику, эльборы, синтетические и естественные алмазы. Для изготовления режущего инструмента применяют инструментальные углеродистые стали следующих марок: У7, У8, УО, У10, У11, У12, У13 (буква У указывает на то, что сталь углеродистая, а цифры показывают среднее содержание углерода в десятых долях процента). Инструментальные стали повышенного качества, имеющие минимальное количество вредных примесей, отмечают буквой А: У10А, У8А и т. д. Углеродистая инструментальная сталь обладает низкими режущими свойствами. Режущие инструменты, изготовленные из такой стали, позволяют вести обработку при температуре в зоне резания до 200 - 250°С и при скоростях резания в пределах 10 - 15м/мин. Легированная инструментальная сталь по химическому составу отличается от углеродистой инструментальной стали лишь наличием одного или нескольких легирующих элементов: хрома, вольфрама, молибдена, ванадия. Чаще всего для изготовления прорезных, фасонных и концевых фрез малых диаметров применяют следующие марки стали: ХГ, ХВ5, ОХС и ХВГ. Легированная инструментальная сталь обладает более высокими режущими свойствами, чем углеродистая инструментальная сталь (температура в зоне резания 300 - 350°С, скорости резания 20 - 25 м/мин). Быстрорежущая инструментальная сталь в отличие от углеродистой и легированной инструментальной стали обладает большим сопротивлением износу и большей теплостойкостью. Она обладает красностойкостью, т. е. не теряет своих свойств при температуре красного каления (550 - 600°С). Быстрорежущие стали делятся на стали нормальной производительности (Р18, Р12, РО, Р18М, РОМ, Р6М5, Р18Ф2) и стали повышенной производительности (Р18Ф2К5, РОФ2К5, РОФ2К5, РОФ2К10, РОФ5, Р14Ф4, Р6МЗ, Р10Ф5К5 и др ), легированные кобальтом (К), ванадием (Ф) и молибденом (М). Из быстрорежущих сталей нормальной производительности лучшей является сталь Р18, которая легко обрабатывается шлифованием и малочувствительна к прижогам. Стали повышенной производительности обладают более высокими красно- стойкостью и режущими свойствами. Быстрорежущая сталь нормальной производительности может работать при скоростях резания до 60 м/мин и выше, а повышенной производительности до 100 м/мин и выше. Термическая обработка быстрорежущей стали. Закалка применяется для повышения твердости и сопровождается уменьшением вязкости. Оптимальная температура при закалке быстрорежущей стали Р18 для тонких изделий (5 - 8 мм) - 1260°, для изделий толщиной более 10 - 15 мм - 1280°. Быстрорежущая сталь медленно прогревается, высокий нагрев приводит к обезуглероживанию и образованию трещин, поэтому изделия из быстрорежущей стали медленно нагревают при закалке до температуры 820 - 850°. Окончательный нагрев лучше всего производить в соляных ваннах, так как это позволяет избежать обезуглероживания стали. Выдержка при температуре закалки измеряется долями минуты. Быстрорежущая сталь после закалки обязательно должна быть подвергнута многократному отпуску. Оптимальная температура отпуска для стали Р18 - 580°, а для стали P9 - 560°. Быстрорежущие стали повышенной производительности требуют тщательного соблюдения режимов термообработки. Отступление от рекомендуемых режимов (особенно при обработке кобальтовых сталей) может привести к понижению твердости и сильному обезуглероживанию). Твердые сплавы допускают работу со скоростями резания, превышающими в 5 - 10 раз скорости обработки быстрорежущими инструментальными сталями, и не теряют режущих свойств при температуре до 850°С и выше. Металлокерамические твердые сплавы состоят из карбидов вольфрама, титана или тантала и кобальта, связывающего эти вещества. Различают вольфрамо-кобальтовые металлокерамические сплавы (ВК2, ВКЗ, ВК6, ВК4В, ВК6В, ВК6М, ВК8, ВК10, ВК10М, ВК15М и др.) и титано-вольфрамо-кобальтовые (Т5К10, Т14К8, Т15К6, ТЗОК4, Т60К6 и др.). Цифры после буквы К указывают процентное содержание в сплаве кобальта, после буквы Т - карбидов титана; остальное составляют карбиды вольфрама. Например, сплав Т14К8 состоит из 14% карбида титана, 8% кобальта и 78% карбида вольфрама. В настоящее время выпускают трех-карбидные твердые сплавы марок Т5К12В, ТТ7К12, ТТ7К5, ТТ10К8Б и др., состоящие из карбидов вольфрама, титана, тантала, кобальта. Эти сплавы характеризуются высокой прочностью. Твердый сплав марки ТТ7К12 допускает работу с 1,5 - 2 раза большими.подачами на зуб, чем сплав Т5К10. Твердые сплавы выпускаются в виде пластинок стандартных форм и размеров Вольфрамо-кобальтовые сплавы применяют для обработки хрупких материалов: чугуна, бронзы, закаленной стали, пластмасс, фарфора и т. п. Твердые сплавы титано-вольфрамовой группы предназначены главным образом для обработки сталей. При выборке марок твердого сплава можно руководствоваться данными табл. 24.
|
machinetools.aggress.ru
Черновая фреза 10мм (твердый сплав)
Инструмент был куплен 2 года назад в количестве 1 шт., на пробу, для неответственной задачи — обдирки, где его не жалко и где от него не зависит качество итогового изделия.Как показало время, инструмент показал себя… очень неплохо и теперь в работе еще немного инструмента китайского происхождения.
Пост будет о лени… а лень это двигатель прогресса. Основное правило — надо чтобы все делалось и при этом совершать минимум телодвижений без ущерба качеству — профессиональная лень. Cпойлеров тоже не будет, лишние телодвижения открывать их…
Заказан:
Размеры
4 зубая, обдирочная. для черновой обработки
Режущая кромка выполнена гребенкой, чтобы стружка была не полосками а зернышками— более компактная стружка— легче вымывается, реже убирать рабочую зону (лень убирать)— более безопасная стружкаИз просторов интернета, чтобы подтвердить эти пункты:
Видео можно не смотреть (хоть оно и ускоренно в 8 раз), ниже основные картинки, полное видео тут
На черновой обработке как раз и идёт большой съем металла, и остаётся припуск 0.2 мм для чистового прохода. И инструмент этот больше подвержен износу, но нас это не волнует, у нас всегда будет чистовой минимальный съем фрезой, которая садится от такой работы не будет, а это позволяет меньше думать о чистовых размерах (лень напрягаться)
Изначально фрезу не жаловал, вообще была мания ввалить режимы (лень время тратить) чтобы она сломалась, но у меня не получилось, на нержавейке уже жесткости станка не хватало, трясло.
В итоге фреза выстояла, так и стоит вкрученная в свой патрон эти 2 года и всегда на ковыряние стали она в деле.
А теперь немного пофрезеруем:
Решено было сделать крепление тисков, чтобы было одно резьбовое соединение и чтобы можно было использовать шестигранный ключ. Вот старое крепление:
Результат:
вот какое у фрезы состояние режущей кромки было до и после, ничего не поменялось поэтому фото одно:сколоты кончики гребешков в самой рабочей частиза этой черновой всю обработку подчищает о
mysku.me
Журнал «Твердый сплав» - Твердосплавный металлорежущий инструмент: промышленный, импортный, режущий инструмент
Эксперт в области режущего инструмента и инструментальных систем Sandvik Coromant выпустил три новых сплава для популярного сверла CoroDrill® 870 со сменными головками.
Сплавы GC4344, GC3334 и GC2334 разработаны для повышения стойкости инструмента и получения прогнозируемого износа при сохранении высокой минутной подачи и производительности.
Новые сплавы производятся с использованием уникальной технологии нанесения PVD-покрытия Zertivo™. Читать полностью …
В октябре Sandvik Coromant — эксперт в области режущего инструмента и инструментальных систем, обновил ассортимент продукции.
Компания подготовила ряд решений для автомобильной, нефтегазовой и аэрокосмической промышленностей.
Так, новые керамические концевые фрезы CoroMill® Plura и фрезерные головки CoroMill® 316 с напаянной керамической режущей частью оптимизированы для обработки деталей авиационных двигателей из жаропрочных сплавов на основе никеля. CoroMill® 316 для титана предназначены для фрезерования глубоких карманов на деталях аэрокосмического назначения. Читать полностью …
В соревновании на максимальный объем снятого материала новые кукурузные фрезы от Kennametal занимают первое место.Представьте себе, как режущий инструмент за минуту превращает в стружку 1000 см3 титанового сплава Ti-6Al-4V. Это можно было наблюдать в ходе недавнего испытания новой фрезы с винтовым расположением зубьев HARVI™ Ultra 8X от Kennametal. Кукурузная фреза диаметром 80 мм обрабатывала титановый сплав с шириной фрезерования 95 мм, глубиной – 20 мм и минутной подачей 423 мм/мин в течение трех минут без перерыва. Читать полностью …
Эксперт в области режущего инструмента и инструментальных систем Sandvik Coromant представит рынку два новых сплава для прерывистой токарной обработки материалов высокой твёрдости: CB7125 и CB7135.
Новые сплавы предназначены для точения сталей твёрдостью от 58 до 62 HRC и позволяют выполнять операции средне- и высоконагруженного прерывистого резания, снимать упрочнённый слой на деталях из стали после цементации и индукционной закалки с глубиной резания до 2 мм. CB7125 и CB7135 повышают стойкости инструмента, обеспечивают высокий уровень качества обработанной поверхности и строгую размерную точность. Читать полностью …
Веб-сайт компании:
http://mefexport.com/ru
Наша компания помогает клиентам найти поставщиков в Европе. Мы будем вашим партнером в вопросах закупки и консолидации груза. Возьмем на себя все вопросы логистики до склада вашей транспортной компании. Читать полностью …
Новые торцевые фрезы Seco Double Quattromill® 22 значительно увеличивают скорость съема металла и позволяют использовать все возможности станков для фрезерования. Новая фреза для черновой и получистовой обработки имеет восемь пластин с несколькими режущими кромками, которые позволяют увеличивать глубину резания, экономить средства и достигать высокой производительности. Читать полностью …
CoroDrill® 865 от Sandvik Coromant – сверло с новой геометрией, которая гарантирует повышенную производительность и стабильность при сверлении масляных каналов глубиной до 25xØ. CoroDrill® 865, оптимизированное для обработки коленчатых валов из чугуна и стали, обеспечивает высокие минутные подачи, превосходную повторяемость и высокую надежность процесса обработки. Читать полностью …
С 10 по 15 сентября ведущий глобальный поставщик инструмента и инновационных решений для металлообрабатывающей отрасли, компания Sandvik Coromant примет участие в выставке IMTS в Чикаго. Читать полностью …
ПРОИЗВОДИТЕЛИ ИНСТРУМЕНТАВеб-сайт компании:
http://spinstrument.ru/index.htm
ООО «Новая инструментальная технология» основано в 2015 году на базе ОАО «Специнструмент», которое свыше 25-ти лет разрабатывало и производило импортозамещающий металлорежущий инструмент с механическим креплением сменных режущих пластин для обработки металла путем точения, фрезерования, сверления, резьбонарезания.
Предлагаем свои услуги для инструментального решения технических задач всех вопросов имеющих отношение к обработке металлов резанием. Читать полностью …
Sandvik Coromant / НовостиС 18 по 22 сентября в Штутгарте состоится выставка AMB, где Sandvik Coromant под девизом «Формируем будущее вместе», продемонстрирует, как заказчики и партнеры могут достигнуть более высокого уровня производительности, гибкого процесса обработки и устойчивого производства.
Читать полностью …
Эксперт в области в области режущих инструментов и инструментальных систем Sandvik Coromant представила два новых сплава пластин из керамики, обеспечивающих надежное высокоскоростное точение деталей из труднообрабатываемых жаропрочных сплавов.
Использование керамики CC6220 и CC6230, позволяет обрабатывать материалы, которые тяжело поддаются обработке керамикой с нитевидными кристаллами и сиалоновой керамикой. Способность работать с высокой скоростью резания снижает затраты на производство детали, а надежность обработки гарантирует качество выпускаемых деталей. Читать полностью …
Sandvik Coromant / НовостиВ Москве завершилась международная специализированная выставка «Металлообработка-2018», в рамках которой компания провела специальное мероприятие – «День Sandvik Coromant».
16 мая в зале «Панорама» на территории выставочного пространства «Экспоцентр» состоялось специальное мероприятие компании – «День Sandvik Coromant». Посетители выставки проявили наибольший интерес к теме цифровой трансформации предприятий: от разработки и планирования до непосредственно производства и аналитики. Новинки компании в области дигитализации представил директор по стратегическим связям региона продаж Sandvik Coromant Северная Европа Джеймс Рис-Девис.
Читать полностью …
tverdysplav.ru
Концевые фрезы для самых твердых материалов
DHC HARDLINE дополняет линейку твердосплавных концевых фрез с переменным углом подъема винтовой канавки (Double Helix Cutters). Данная серия была разработана для решения таких проблем, как склонность к вибрации инструментов с постоянным передним углом. Особая геометрия LMT Fette обеспечивает максимальную плавность работы и стабильность процесса. Воспользуйтесь преимуществами нашего многолетнего опыта и проверьте DHC HARDLINE в работе.
Вязкий режущий материал DHC HARDLINE позволяет обрабатывать высокопрочные материалы до 1600 Н/мм2 и закаленную сталь твердостью от 45 до 55 по шкале Роквелла. Данный инструмент также может использоваться со сталями для сосудов высокого давления и показывает лучшие результаты в плане стойкости. Кроме того, фрезы DHC HARDLINE пригодны для обработки чугуна.
Преимущества
- Высочайшая надежность при обработке высокопрочных материалов
- Непревзойденная стойкость
- Один инструмент для черновой и чистовой обработки
- Максимальная плавность благодаря проверенной геометрии DHC
- Невероятные результаты при работе с мягкими сталями
В стандартном исполнении фрезы DHC имеют диаметр от 6 до 20 мм. Помимо этого, доступны различные варианты длины резания (около 1xD и 2,5xD) и типы хвостовика (гладкий; HA по DIN 6535 или Weldon; HB по DIN 6535).
Подробная информация о программе DHC:
Источник:END MILLING WITH FULL HARDNESS,LMT Tools,отдел фрезерования и нарезания резьбы
Также советуем прочитать:
Нет связанных записей.
Понравилась статья? Поделитесь:
tverdysplav.ru
Технические характеристики | Артикул | |
D 3 X B 12 X L 50 x Z 2 ( чистовая) | Т142.030R | |
D 4 X B 12 X L 50 x Z 2 ( чистовая) | Т142.040R | |
D 5 X B 17 X L 50 x Z 2 ( чистовая) | Т142.050R | |
D 6 X B 17 X L 60 x Z 2 ( чистовая) | Т142.060R | |
D 6 X B 27 X L 60 x Z 2 ( чистовая) | Т142.061R | |
D 8 X B 22 X L 80 x Z 2 ( чистовая) | Т142.080R | |
D 8 X B 35 X L 80 x Z 2 ( чистовая) | Т142.081R | |
D 10 X B 35 X L 80 x Z 2 ( чистовая) | Т142.100R | |
D 10 X B 45 X L 100 x Z 2 ( чистовая) | Т142.101R | |
D 12 X B 35 X L 80 x Z 2 ( чистовая) | Т142.120R | |
D 12 X B 45 X L 100 x Z 2 ( чистовая) | Т142.121R | |
D 12 X B 55 X L 100 x Z 2 ( чистовая) | Т142.122R | |
D 14 X B 45 X L 100 x Z 2 ( чистовая) | Т142.140R | |
D 14 X B 55 X L 100 x Z 2 ( чистовая) | Т142.141R | |
D 16 X B 45 X L 100 x Z 2 ( чистовая) | Т142.160R | |
D 16 X B 55 X L 100 x Z 2 ( чистовая) | Т142.161R | |
D 16 X B 72 X L 120 x Z 2 ( чистовая) | Т142.162R | |
D 18 X B 55 X L 100 x Z 2 ( чистовая) | Т142.180R | |
D 18 X B 72 X L 120 x Z 2 ( чистовая) | Т142.181R | |
D 18 X B 102 X L 150 x Z 2 ( чистовая) | Т142.182R | |
D 20 X B 55 X L 100 x Z 2 ( чистовая) | Т142.200R | |
D 20 X B 72 X L 120 x Z 2 ( чистовая) | Т142.201R | |
D 20 X B 102 X L 150 x Z 2 ( чистовая) | Т142.202R |
dakt.ru