Устройство для доворота и фиксации шпинделя в заданном угловом положении. Фиксация шпинделя что это
Что я знаю о шуруповертах: mux22
Шуруповертом можно очень быстро и точно крутить почти весь гитарный крепеж, сверлить любые отверстия в дереве и небольшие - в металле, зенковать их, полировать небольшие детали и делать кучу других вещей. И все это без проводов. Классическая электродрель существенно уступает шуруповерту на "гитарных" масштабах и в мелкой столярке вообще, поэтому заводить такую для мастерской нет никакого смысла. Электроотвертка, в свою очередь, не умеет сверлить и слабовата для крупного крепежа (попробуйте-ка ей нормально прикрутить гриф к фендеру).
На что смотреть при покупке:
- Аккумуляторы: только литиевые, минимум две штуки в комплекте. Вас будут пугать, что они дорогие - не верьте. Хороший литиевый аккум живет много лет и не умеет парить мозги. Инструменты с никелевыми аккумуляторами выпускаются для глупых и жадных людей. И еще для тех, кто много работает на морозе.
- Напряжение (и размер): по моему опыту и на моих задачах, 10,8 хватает для всего. Тяжелые аппараты хороши на стройке. Чем мельче инструмент, тем приятнее и легче им пользоваться.
- Патрон: только трехкулачковый. Максимальный диаметр от 10 мм.
- Блокировка шпинделя: важнейшая штука. Позволяет в любой момент спокойно откручивать-закручивать патрон одной рукой, без проворота. Сейчас такими обзавелись все приличные шуруповерты, кроме хитачи.
- Скорость: чем больше максимальная, тем лучше. На моем боше 1350, на соседском деволте 1500 - и я хорошо ощущаю разницу, когда сверлю дерево или кручу длинные винты. Это не самый важный момент, но при прочих равных его надо учитывать.
- Минимальный крутящий момент: очень важный параметр, о котором мало кто знает. Дело в том, что у многих шуруповертов "единичка" трещотки выдает такой момент, что шуруповерт играючи срывает резьбу в дереве вокруг мелких шурупчиков. Правило такое: шуруповерт на максимальной скорости и на минимальном крутящем моменте должен очень легко останавливаться. Типа, от зажима патрона двумя пальцами. Цифр на эту тему вы, скорее всего, не найдете, большинство производителей указывает только максимальный крутящий момент. Остается ехать в магазин и сравнивать руками.
- Китайский хлам: не покупать никогда. Бренды с большим запасом доверия: макита, деволт, метабо, синий бош, хилти, фестул. Выходить за пределы этого списка не стоит, инфа 100%.
К шуруповерту непременно купить много 50-мм бит Ph2 и Ph3 (половина потеряется), тарелочку с липучкой для полировки, а также переходник на квадрат 1/4" для торцевых головок. Знаете, как круто колки шуруповертом ставить? Вжж, вжж. Двадцать секунд на все шесть. Пит-стоп.
А тарелка с липучкой используется, например, так:
С тем же успехом для этой цели можно использовать сверлильный станок, конечно.
Время от времени с помощью шуруповерта делается что-то совсем странное - например, на фото ниже я стачиваю с анкерной гайки часть толщины, вращая ее по движущейся ленте гриндера. Почти токарный станок. Похожим способом снимаются фаски с обрезанных по длине винтов, а также уменьшается диаметр их шляпок.
И последнее. Нажимать на кнопочку шуруповерта лучше всего не указательным, а средним пальцем. При таком хвате указательный и большой пальцы перемещаются предельно близко к центру аппарата (и поэтому лучше его контролируют), а заодно молниеносно переключают направление вращения, так как лежат ровно на нужном месте. Такой хват работает на большинстве шуруповертов, и он гораздо удобнее "пистолетного". Попробуйте, удивитесь.
mux22.livejournal.com
Устройство фиксации шпинделя металлорежущих станков различного назначения
Устройство предназначено для управления шпиндельным механизмом в виде вращающегося шпинделя со шкивом для сверлильно-фрезерно-расточных работ, зафиксированного шпинделя для токарных работ, и сменой инструмента и содержит корпус и штыри для фиксации шпинделя. Для расширения технологических возможностей оно снабжено планкой, на которой установлены штыри, пневмоцилиндром, предназначенным для перемещения планки со штырями, толкателем и пружиной для возврата толкателя и штырей. При этом штыри предназначены для взаимодействия с пазами, выполненными на шкиве, установленном на шпинделе. 2 ил.
Изобретение относится к области станкостроения и может быть использовано в металлорежущих станках сверлильно-фрезерно-расточной группы для выполнения сверлильно-фрезерно-расточных и токарных операций на вращающемся столе.
Известны конструкции шпиндель-моторов [1, 2], в компоновке которых предусмотрено устройство, позволяющее фиксировать фрезерный шпиндель в заданной позиции для производства токарных операций. Недостатками такого устройства являются невозможность изменения мощности и крутящего момента главного двигателя, а также необходимость установки на станок гидростанции и подвода гидравлики к устройству.
Цель изобретения - создание устройства, позволяющего управлять шпиндельным механизмом - вращающимся шпинделем для сверлильно-фрезерно-расточных работ, фиксированным положением шпинделя для токарных работ и сменой инструмента. Установка устройства фиксации шпинделя в корпусе шпиндельной бабки позволяет устанавливать различные двигатели главного движения и шкивы для передачи крутящего момента от двигателя к шпиндельному устройству для получения необходимых выходных характеристик станка без изменения конструкции шпиндельной бабки.
На фиг.1 представлена установка устройства фиксации шпинделя в корпусе шпиндельной бабки станка.
На фиг.2 представлена компоновка узла фиксации шпинделя.
Корпус 1 устройства фиксации шпинделя устанавливается на корпусе 2 шпиндельной бабки. Перемещение подвижных частей устройства осуществляется при помощи пневмоцилиндра 3 (при движении вниз) и встроенной в устройство пружины (при движении вверх). Фиксация шпинделя 4 осуществляется по пазам фланца 5 шкива 6 ременной передачи, установленного в шпиндельном устройстве 7.
Фиксацию шпиндельного устройства 7 обеспечивают два штыря 8, установленные на планке 9, которые при перемещении вниз входят в пазы фланца 5 и фиксируют шпиндель 4 для токарных работ. Для отжима инструмента из конуса шпинделя 4 используется толкатель 10. Возврат штырей 8 и толкателя 10 в исходное (верхнее) положение осуществляется за счет усилия пружины 11. При отжиме инструмента осуществляется обдув инструментального конуса шпинделя 4 через полый толкатель 10 устройства фиксации и полый шток 12 устройства зажима инструмента, расположенного в шпинделе 4.
Работа устройства фиксации шпинделя осуществляется следующим образом:
а) для выполнения сверлильно-фрезерно-расточных работ толкатель 10 и штыри 8 занимают крайнее верхнее положение, давая возможность шпинделю 4 беспрепятственно вращаться;
б) для выполнения токарных работ фланец 5 шкива 6 шпинделя сориентирован пазами по штырям 8; шток пневмоцилиндра 3 перемещает планку 9 вниз; штыри 8 входят в зацепление с пазами фланца 5 шкива 6 шпинделя и фиксируют шпиндель 4 для токарной обработки; по окончании работы толкатель 10 под действием пружины 11 возвращается в исходное положение, перемещая планку 9 с установленными на ней штырями 8; штыри 8 выходят из зацепления с фланцем 5 шкива 6, освобождая шпиндель 4;
в) при отжиме инструмента фланец 5 шкива шпинделя сориентирован пазами перпендикулярно штырям 8; шток пневмоцилиндра 3 перемещает планку 9 вниз; толкатель 10 преодолевает свободный ход и перемещает шток 12 механизма зажима инструмента, что приводит к освобождению хвостовика инструмента 13; одновременно происходит обдув инструментального конуса шпинделя 4.
Ориентацию шпинделя к устройству фиксации, управление пневмоцилиндром и обдувом инструментального конуса шпинделя осуществляет ЧПУ станка.
Литература
1. Dr. Karl Gebert, Motor Spindles-Solutions for packing machines-Siemens., www.automation.siemens.com/mc.
2. Tool turret - SAUTER., www.directindustry.com.
Устройство фиксации шпинделя металлорежущих станков различного назначения, предназначенное для управления шпиндельным механизмом в виде вращающегося шпинделя со шкивом для сверлильно-фрезерно-расточных работ, зафиксированного шпинделя для токарных работ и сменой инструмента и содержащее корпус и штыри для фиксации шпинделя, отличающееся тем, что оно снабжено планкой, на которой установлены штыри, пневмоцилиндром, предназначенным для перемещения планки со штырями, толкателем и пружиной для возврата толкателя и штырей, при этом штыри предназначены для взаимодействия с пазами, выполненными на шкиве, установленном на шпинделе.
Устройство для доворота и фиксации шпинделя в заданном угловом положении
Союз Советских
Социалистически)(Республик
ОПИСАНИЕ
ИЗОБРЕТЕНИЯ
К АВТОРСКОМУ СВИДЕТЕЛЬСТВУ () )) 971612 (61) Дополнительное к авт. санд-ву (51)М. Кл.
В 23 6 5/20 (22) Заявлено 18.05.81 (2I ) 3288440/25-08 с присоединением заявки ЭЙ
Ркударстпееь(й кпиптпт
СССР (23)Ilриоритет по аплаи пзебретеккк к открытий
Опубликовано 07.1 1.82. Ьтоллетенв Ме 41 (53) УДК 62.589 (088.8) /
Дата опубликования описания 09.1 1.82
В. Х. Подойницын, Е. И. Горелик и IO. А. Никуленко,, ) И!t н( :в . „1 " (т)ьт.и4(((. /, °
-" 0 ГЕ, (, 1
Барановичское специальное конструкторское бюро автомат линий им. 60»летия Великого Октября (72) Авторы изобретения (7I) Заявитель (54) УСТРОЙСТВО ДЛЯ ИОВОРОТА И ФИКСАЦИИ
ШПИНДЕЛЯ B ЗАДАННОМ УГЛОВОМ ПОЛОЖЕНИИ
Изобретение относится к области станкостроения, в более конкретно тс устройствам для доворота и фиксации шпинделя в заданном угловом положении.
Известны устройства дпя доворота и фиксации штптнделя в заданном угловом положении, содержащие корпус, в котором размещен ротор гидропривода, выполненный в виде кольца с лопастью, и фиксагор, взаимодействующий со шпинделем (1).
Недостатком известнь(х устройств является их недостаточная надежность.
Пель изобретения - повышение надежности устройства в работе.
Для этого устройство снабжено дополнительными ротором и фиксатором, идентичными первым, причем роторы установлены с возможностью встречного поворота на угол 1 80, а фикса т оры расположены в лопастях роторов таким образом, что в крайних положениях последних лежат
20 в одной плоскости.
На фиг. 1 кзображено устройство в се чении по оси шпи(щеля; на фиг. 2 - раз2 рез А-А на фиг. 1; на фиг. 3 - разрез
Б-Б на фиг. 1; на фиг. 4 «частичный поперечный разрез устройства в момент начала поворота роторов.
Устройстве содержит корпус 1 с цьлиндрическими расточками в которых вы1 полнены перемычки 2. В расточках корпуса 1 смонтированы роторы 3,4 с лопастями 5, 6. Между перемычками 2 и лопастями 5,6 образованы рабочие полости 7-10. В лопастях 5, 6 выполнены ступенчатые расточки, в которых смонтированы фиксаторы, выполненные в виде поршней 11 со штоками 12. Фиксаторы отжаты в нерабочее положение плоскими пружинами 13, закрепленными в отверстиях лопастей 5, 6. Через осевые отверс тия роторов 3,4 пропущен шпиндель 14, в котором выполнен шлицевой паз 15.
Устройство работает следующим обре зом.
В нерабочем положении роторы 3,4 с лопастями 5,6 отведены в крайние положения. Поршни ll со штоками 12 удер
3 97181 живаются пружинами 13 в нерабочем положении. Подачей рабочей жидкости в полости 7, 9 поршни 11 со штоками 12 пе ремещиатся в сторону шпинделя 14 и рабочими торцами прижимаются к шпинделю, после чего начинается поворот роторов
3,4 с лопастямц5, 6. При этом полости
8,10 соединенй со сливом. После того, как один иэ штоков 12 совпадает со шли цевым пазом 15 и входит в паз рабочим >0 концом, начинается доворот шпинделя 14;
На конечном участке доворота конец второго штока 12 также входит в паз 15.
Так осуществляется доворот и жесткая фиксация шпинделя 14 в заданном угло- 15 вом положении. При условии, когда доворот шпинделя 14 происходит эа счет фрикционного зацепления с одним из штоков
12, то с пазом 15 взаимодействует второй шток 12 и доворачивает шпиндель 14 2î во встречном направлении к направлению перемещения первого штока 12. Расцепление штоков 12 со шпинделем 14 осуществляется соединением полостей 7, 9 со сливом и перемещением поршней 11 25 со штоками 12 с помощью пружин 13.
Подачей рабочей жидкости в полости 8, 2 1
10 роторы 3,4 с лопастями 5,6 воэвра щаются в исходное положение.
Такое конструктивное выполнение позволит повысить надежность устройства в работе.
Формула изобретения
Устройство для доворота и фиксации шпинделя в заданном угловом положении, содержащее корпус, в котором размещен ротор гидропривода, выполненный в виде кольца с лопастью, и фиксатор, взаимодействующий со шпинделем, о т л и ч а юшийся тем, что, с целью повышения надежности в работе, устройство снабжено дополнительными ротором и фиксатором, идентичными первым, причем роторы установлены с возможностью встречного поворота на угол 180, а фиксаторы расположены в лопастях роторов таким образам, что в крайних положениях послед« них лежат в одной плоскости.
Источники информации, принятые во внимание при экспертизе
1. Авторское свидетельство СССР
rro заявке % 2988737/25-08, кл. В 23 Gl 5/ О, 8,10.80.
071 () 12
Фиг. У
Q 9
Г31111ИГ1И Заказ 8821/25
Тираж 7 0 11одписное
Филиал Ц11Ц "Патент °, ? >K t ()1) of 1, v;1. (1р >е к т и " ÿ, 1
Я
Фиг. Ф
www.findpatent.ru
Выбор схемы фиксации шпинделя — МегаЛекции
Важное значение для работоспособности шпиндельного узла имеет выбор оптимальной схемы его радиальной и осевой фиксации.
Все многообразие конструкций шпиндельных узлов принципиально можно свести к трем основным схемам фиксации (рис. 24):
Рис.24. Схемы фиксации шпинделей.
В первой схеме радиальная и двухсторонняя осевая фиксации шпинделя выполнены в передней опоре. Задняя опора - плавающая, позволяет компенсировать линейные тепловые деформации шпинделя. В конструкции передней опоры использованы специальные конструкции подшипников: двухрядный с цилиндрическими роликами серии 3182100 и два упорных подшипника серии 8000. Следует отметить, что данная схема характеризуется повышенной сложностью передней опоры и большим тепловыделением в ней, что отрицательно сказывается на технологичности изготовления и сборки, а также на точности обработки. Кроме того из-за существенного различия в радиальной жесткости подшипников серий 3182100 и 8000 в конструкции опоры должна быть предусмотрена раздельная регулировка предварительного натяга этих подшипников, что требует больших осевых габаритных размеров и особой тщательности регулировки.
Поэтому эта схема преимущественно применяется в сверлильных, фрезерных, расточных и токарных станках средних размеров. Следует отметить, что использование в передней опоре упорных подшипников существенно снижает быстроходность (d×n) шпиндельного узла. Поэтому в шпинделях легких и скоростных станков взамен упорных подшипников устанавливают радиально-упорные серий 36000, 46000 и др., имеющие более высокую быстроходность.
Перенос упорных (или радиально-упорных) подшипников в заднюю опору (схема 2) существенно упрощает конструкцию передней опоры и снижает тепловыделение в ней, но при этом резко возрастают температурные деформации переднего конца шпинделя, что для высокоточных станков недопустимо. Поэтому схему 2 можно рекомендовать для токарно-операционных, сверлильных, агрегатных, шлифовальных и других станков с невысокими требованиями к точности осевых размеров.
Шпиндельные узлы спроектированные по третьей схеме имеют достаточно высокую радиальную и осевую жесткость. Однако этой схеме присущ общий недостаток с первой схемой: необходимость раздельной регулировки предварительного натяга подшипников и ограниченная быстроходность. С целью увеличения быстроходности и снижения температурных деформаций можно рекомендовать использование в схеме радиально-упорных подшипников серии 46000 и выбора малого межопорного расстояния. Схему можно применять в станках средних размеров (в том числе с ЧПУ), с малым межопорным расстоянием или с использованием осевых пружинных компенсаторов для выбора зазоров в подшипниках.
Конструирование шпиндельных опор в основном выполняется по первым двум схемам. В качестве примера рассмотрим вариант конструкции шпиндельного узла токарного станка, выполненного по второй схеме (рис. 25).
Рис. 25. Опора шпинделя с радиальным двух рядным роликовым подшипником.
В этой конструкции радиальный зазор подшипника 2 регулируется с помощью гайки 1 путем смещения внутреннего кольца подшипника до упора в дистанционное кольцо 3. Для удобства монтажа и демонтажа кольцо 3 выполняется разъемным, состоящим из двух полуколец. Гайка 4 предназначена для обеспечения демонтажа кольца 2 с целью уменьшения предварительного натяга. Для этой же цели используется отверстие 6, в которое принудительно под высоким давлением нагнетается масло для гидроразжима кольца 2. Подпружиненный фикатор 7 служит для предотвращения самопроизвольного отвинчивания гайки 1.
Необходимая величина натяга обеспечивается подшлифовкой кольца 3. Следует отметить, что коническая поверхность А шпинделя не обеспечивает высокой точности базирования, вследствие чего возможен перекос внутреннего кольца подшипника и потеря геометрической точности вращения шпинделя. Для исключения этого недостатка рекомендуется базирование по конусу дополнять базированием по торцу внутреннего кольца с помощью длинной дистанционной втулки 5, имеющей посадку Н6/n6. Длинная втулка совместно с посадкой Н6/n6 обеспечивает хорошее осевое направление кольца.
Рекомендуемые страницы:
Воспользуйтесь поиском по сайту:
megalektsii.ru
Устройство для фиксации инструмента на шпинделе
Устройство позволяет зажать инструмент на шпинделе станка и облегчает отсоединение инструмента от шпинделя без помощи дополнительных инструментов. Устройство включает дистальные средства, которые могут быть захвачены тяговым стержнем станка с возможностью отсоединения от него, а также средства для сцепления с инструментом с возможностью отцепления от него. Технический результат: уменьшение времени простоя станка при смене инструмента. 7 з.п. ф-лы, 4 ил.
Область техники, к которой относится изобретение
Настоящее изобретение относится к станочному оборудованию, в частности металлорежущим станкам, и устройствам для фиксации инструмента на шпинделе станка.
Уровень техники
При обработке изделий на станках, в частности металлообработке, к примеру в ходе операций резки и/или шлифования для изготовления зубчатых колес и других зубчатых изделий, вращательный инструмент (к примеру, торцевую фрезу, червячную фрезу, шлифовальный круг) обычно закрепляют и фиксируют на шпинделе станка с помощью одного или более резьбовых болтов (то есть стопорных болтов), которые проходят через наружную поверхность шпинделя.
В некоторых случаях вращательный инструмент фиксируют на шпинделе станка, продевая осевой резьбовой зажимной болт через головку инструмента и вставляя его в шпиндель, где конец центрального болта сцепляют с тяговым стержнем станка. Тяговый стержень выдвигают для сообщения осевому болту растягивающего усилия, чтобы привести инструмент в соприкосновение со шпинделем и зафиксировать инструмент на шпинделе.
При использовании средств соединения вышеописанного типа могут потребоваться определенные инструменты, такие как ручной инструмент или пневматический инструмент (к примеру, гайковерт), для затягивания и/или ослабления зажимных болтов. Как только болты ослаблены и, если необходимо, тяговый стержень вдвинут, для отсоединения вращательного инструмента от шпинделя станка может потребоваться ослабить контакт между инструментом и шпинделем с помощью дополнительных инструментов и/или ослабляющих винтов. Такие операции зажима и/или ослабления могут отнимать достаточно много времени, что ведет к значительным простоям станка.
Учитывая стремления к увеличению производительности и снижению простоев станков, необходима технология фиксации инструмента на шпинделе, которая отнимает меньше времени и задействует меньше дополнительных инструментов, чем технологии по нынешнему уровню техники.
Раскрытие изобретения
Настоящее изобретение относится к устройству для фиксации инструмента, которое позволяет зажать инструмент в шпинделе станка и может облегчить отсоединение инструмента от шпинделя без помощи дополнительных инструментов. Такое устройство для фиксации инструмента включает в себя дистальные средства, которые могут быть захвачены тяговым стержнем станка с возможностью отделения от данного стержня, а также средства для контакта с инструментом с возможностью отделения от него.
Краткое описание чертежей
Фиг.1 - вид сбоку устройства для фиксации инструмента, соответствующего настоящему изобретению.
Фиг.2 - осевой разрез устройства для фиксации инструмента, соответствующего настоящему изобретению.
Фиг.3 - осевой разрез устройства для фиксации инструмента, соответствующего настоящему изобретению и установленного на шпинделе вместе с инструментом.
Фиг.4 - увеличенный фрагмент фиг.3.
Осуществление изобретения
Прежде чем будут подробно описаны любые признаки и, по меньшей мере, одна конструкция настоящего изобретения, следует учесть, что настоящее изобретение не сводится к особенностям конструкции и компоновке компонентов, раскрытым в нижеследующем описании или проиллюстрированным чертежами. Изобретение допускает и другие конструкции и может применяться или быть реализовано различным образом. Подразумевается также, что используемая в настоящем документе фразеология и терминология носит описательный характер и их не следует считать ограничительными.
На фиг.1 изображено устройство 2 для фиксации инструмента, соответствующее настоящему изобретению. Устройство 2 содержит продолжающийся аксиально главный участок 4, который имеет в целом круглое поперечное сечение и включает в себя проксимальный фланцеобразный участок или головку 6, тело 8 и дистальную захватную головку 10. Вдоль заданного отрезка длины тела 8 расположена серия, предпочтительно три или более шаров 12 (к примеру, стальных шаров), которые находятся в продолжающихся радиально отверстиях 17, разнесенных по окружности тела 8, предпочтительно на одинаковые расстояния. Шары 12 удерживаются в устройстве 2 для фиксации инструмента надвижной гильзой 14.
Далее, устройство 2 для фиксации инструмента включает в себя внутренний шток 16 (фиг.2-4), к концу которого крепится нажимно-вытяжная ручка 18, предпочтительно через резьбу. Шток 16 может перемещаться между различными позициями в продолжающемся аксиально внутреннем канале главного участка 4 устройства 2 для фиксации инструмента, при этом шары 12 проталкиваются в свою радиально внешнюю позицию или возвращаются назад за счет различных диаметров участков штока 16, расположенных вблизи его другого конца. А именно, шток может находиться во вдвинутом положении (фиг.1-4), при котором соответствующий участок имеет первый диаметр d1 и шары 12 протолкнуты в радиально внешнюю позицию, и выдвинутом положении (не показано), при котором тот же участок имеет меньший второй диаметр d2 и шары 12 могут переместиться из радиально внешней позиции вовнутрь, вдавшись, по меньшей мере, частично в образованную таким образом полую область 15.
Кроме того, внутренний шток 16 может содержать прокладку 20 (к примеру, уплотнительное кольцо), расположенную вблизи боковой поверхности его верхнего участка, при этом прокладка 20 может располагаться в первом стопорном пазу 22 канала 5, когда шток 16 находится во вдвинутом положении, и втором стопорном пазу 24 канала 5, когда шток 16 находится в выдвинутом положении. Может быть предусмотрено стопорное кольцо 26 для предотвращения случайного выхода штока 16 из канала 5, а также проникновения любых побочных продуктов обработки (к примеру, текучих сред или металлической стружки) в канал 5.
На фиг.3 и 4 изображено устройство 2 для фиксации инструмента, находящееся в позиции фиксации вращательного инструмента 30 (к примеру, резца, шлифовального круга) на инструментальном шпинделе 32 станка (к примеру, зубообрабатывающего станка), способном вращаться вокруг оси Т инструмента. В инструментальном шпинделе 32 расположен тяговый стержень 34, который может перемещаться в шпинделе 32 аксиально и соединен на своем внутреннем конце с серией зажимных пальцев 36, расположенных в корпусе 38, закрепленном на передней части шпинделя 32. В качестве альтернативы шпиндель 32 и корпус 38 могут быть выполнены заодно целое. Каждый зажимной палец 36 имеет головку 40, нижняя поверхность которой приводится в соприкосновение с радиальной поверхностью 11 захватной головки 10 при зажатии инструмента.
Тяговый стержень 34 может перемещаться между своим исходным вдвинутым положением, в котором головки 40 зажимных пальцев 36 находятся за внутренним торцом 39 корпуса 38 по отношению к его продольной оси, что позволяет зажимным пальцам 36 раскрыться в радиальном направлении, обеспечив прохождение захватной головки в корпус 38, и выдвинутым положением. При перемещении тягового стержня 34 во выдвинутое положение зажимные пальцы 36 заталкиваются в корпус 38, что приводит к радиальному сближению между собой зажимных пальцев, при этом нижняя поверхность головки 40 каждого зажимного пальца 36 приводится в соприкосновение с поверхностью 11 захватной головки 10.
Далее изложен примерный принцип действия настоящего изобретения. Когда вращательный инструмент 30 установлен на/приставлен к инструментальному шпинделю 32 и/или корпусу 38 и тяговый стержень 34 находится в исходном вдвинутом положении, устройство 2 для фиксации инструмента, шток 16 которого находится в выдвинутом положении (то есть участок с диаметром d2 непосредственно примыкает к шарам 12), вставляют в центральное отверстие 42 и продвигают через центральный канал 44 вращательного инструмента 30, так чтобы нижняя поверхность 7 фланцеобразного участка 6 прилегла к внешней поверхности 46 плеча 48. Таким образом, захватная головка 10 оказывается вставленной в корпус 38. После вставки устройства 2 ручку 18 и вместе с ней шток 16 вдвигают во вдвинутое положение (то есть в котором участок с диаметром непосредственно примыкает к шарам 12), чтобы протолкнуть шары 12 радиально к периферии в позицию, в которой они не смогут пройти через центральный канал 44, то есть устройство 2 для фиксации инструмента не сможет выйти из вращательного инструмента 30. Затем тяговый стержень 34 перемещают в выдвинутое положение, чтобы зажимные пальцы 36 обхватили захватную головку 10 и вращательный инструмент 30 прижался к инструментальному шпинделю 32 и/или корпусу 38.
При снятии вращательного инструмента 30 тяговый стержень 34 перемещают в исходное вдвинутое положение, чтобы освободить захватную головку 10 от зажимных пальцев 36. Тяговый стержень 34 можно продолжать перемещать вперед, пока передняя поверхность 50 стержня не соприкоснется с дистальной торцевой поверхностью 13 захватной головки 10, что позволит отделить или извлечь вращательный инструмент 30 из инструментального шпинделя 32 и/или корпуса 38. Отделение вращательного инструмента 30 произойдет за счет того, что устройство 2 для фиксации инструмента не может перемещаться относительно вращательного инструмента 30, когда шары 12 находятся в радиально внешней позиции благодаря своему контакту с участком диаметром d1.
Устройство 2 для фиксации инструмента может быть снято с вращательного инструмента 30 путем оттягивания ручки 18, так чтобы участок штока с меньшим диаметром d2 непосредственно примкнул к шарам 12; благодаря меньшему второму диаметру d2 соответствующего участка шары 12 могут переместиться из радиально внешней позиции вовнутрь, вдавшись, по меньшей мере, частично, в полую область 15. После этого устройство для фиксации инструмента может быть вытянуто из вращательного инструмента 30, поскольку любой контакт шаров 12 с плечом 48 вызовет перемещение шаров 12 вовнутрь, после которого они смогут беспрепятственно пройти через центральный канал 44.
Подразумевается, что в качестве альтернативы устройство 2 для фиксации инструмента может быть размещено во вращательном инструменте до его установки на/прикладывания к инструментальному шпинделю и/или корпусу зажима инструмента.
В соответствии с настоящим изобретением, чтобы закрепить устройство 2 для фиксации инструмента на инструментальном шпинделе или отсоединить такое устройство от шпинделя, не требуется никаких дополнительных инструментов. Кроме того, не требуется дополнительных инструментов, чтобы отделить вращательный инструмент от инструментального шпинделя и/или корпуса зажима инструмента или извлечь инструмент из них.
Настоящее изобретение описано в отношении предпочтительных вариантов его осуществления, однако подразумевается, что настоящее изобретение не сводится к их особенностям. Предполагается, что изобретение включает в себя модификации, которые будут очевидны специалистам в области техники, к которой относится объект настоящего изобретения, без отступления от существа и объема прилагаемой формулы изобретения.
1. Устройство для фиксации инструмента на шпинделе станка без помощи дополнительных инструментов, содержащее:продолжающийся аксиально главный участок, который включает в себя проксимальный фланцеобразный участок и дистальный захватный участок, причем указанный главный участок содержит продолжающийся аксиально внутренний канал;серию продолжающихся радиально отверстий, которые разнесены вокруг указанного главного участка и расположены на указанном главном участке между указанным фланцеобразным участком и указанным захватным участком;шары, которые расположены по одному в каждом из указанных отверстий с возможностью перемещения между радиально внешней позицией и радиально внутренней позицией;внутренний шток, который расположен в указанном канале и с возможностью перемещения в нем между вдвинутым положением и выдвинутым положением;при этом находясь в указанном вдвинутом положении, указанный шток на уровне своего контакта с указанными шарами имеет первый диаметр, благодаря чему указанные шары протолкнуты в указанную радиально внешнюю позицию, а находясь в указанном выдвинутом положении, указанный шток на уровне указанных шаров имеет второй диаметр, благодаря чему указанные шары могут переместиться в указанную радиально внутреннюю позицию.
2. Устройство по п.1, в котором указанный захватный участок имеет радиальную контактную поверхность.
3. Устройство по п.1, в котором указанный шток имеет первый конец и второй конец, причем на указанном первом конце расположена ручка, а вблизи указанного второго конца расположены участки с указанными первым и вторым диаметрами.
4. Устройство по п.3, в котором указанный шток имеет прокладку, которая расположена между участком с указанным первым диаметром и указанной ручкой.
5. Устройство по п.1, в котором нижняя поверхность указанного фланцеобразного участка прилегает к инструменту, когда указанный инструмент зафиксирован на указанном шпинделе.
6. Устройство по п.1, в котором указанные шары удерживаются в указанном главном участке гильзой, которая расположена на указанном главном участке.
7. Устройство по п.1, в котором указанные отверстия разнесены на равные расстояния вокруг указанного главного участка.
8. Устройство по п.1, в котором указанный второй диаметр указанного штока формирует в указанном штоке полую область, в которую указанные шары имеют возможность, по меньшей мере, частично вдаваться, когда указанные шары находятся в указанной внутренней позиции.
www.findpatent.ru
Конструкция шпинделя и корпуса шпиндельной бабки
Хорошая конструкция — компромисс между ее достоинствами и недостатками, и решения принимаются в силу наших широты и глубины знаний, собственного опыта исследований и созидания, что и называется талантом конструктора.
Шпиндельный узел, как наиболее ответственный из всех узлов, должен обеспечивать главное функциональное качество станка — высокую точность и производительность.
Точность вращения и жесткость шпиндельного узла определяются не только высокой точностью подшипников качения, но и в значительной степени точностью обработки, качеством поверхности посадочных мест вала, корпуса и сопряженных с подшипником деталей. Точность всех этих элементов должна быть соизмерима с точностью подшипников. В целом точность шпиндельного узла, как и несущей системы станка, определяется тремя характеристиками точности.
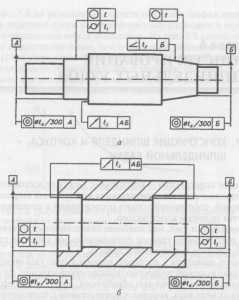
Кольца шпиндельных подшипников относительно тонкостенны и при посадке приобретают форму более жестких сопряженных поверхностей вала и корпуса. Например, сжатие внутреннего кольца подшипника диаметром 120—140 мм силой руки вызывает овальность до 10 мкм. Требуется выдерживать жесткие допуски на перпендикулярность (биение) упорных поверхностей валов, корпусов, деталей, фиксирующих подшипники в осевом направлении (гайки, втулки). На рис. 1 и в табл. 1 приводятся рекомендации по отклонению формы, расположения и шероховатости посадочных поверхностей шпинделя (вала) и корпуса при установке подшипников классов точности SP и UP и их аналогов.
Рекомендуемые допуски на форму, расположение и шероховатость вала и корпуса
Деталь | Корпус | Вал | ||
Класс точности | SP | UP | SP | UP |
Круглость t | IT2/2 | IT1/2 | IT2/2 | IT1/2 |
Цилиндричность t1 | IT2/2 | IT1/2 | IT2/2 | IT1/2 |
Конусность t2 | — | — | IT3/2 | IT3/2 |
Биение t3 | IT1 | IT0 | IT1 | IT0 |
Соосность t4 | IT4 | IT3 | IT4 | IT3 |
Диапазон d, D, мм | Шероховатость Ra, мкм | |||
d,D< 80 | 0,4 | 0,2 | 0,2 | 0,1 |
80 ≤ d,D ≤ 250 | 0,8 | 0,4 | 0,4 | 0,2 |
d,D> 250 | 1,6 | 0,8 | 0,8 | 0,4 |
Численные значения допусков на параметры круглости t, цилиндричности t1, конусности t2, биения t3, соосности t4 задаются в функции квалитетов точности ISO (IT0—IT5) — табл. 2.
Численные значения допусков на номинальный диаметр для разных квалитетов ISO
Номинальный диаметр, мм | Квалитет ISO, мкм | |||||
IT0 | IT1 | IT2 | IT3 | IT4 | IT5 | |
50-80 | 1,2 | 2,0 | 3,0 | 5,0 | 8,0 | 13,0 |
80-120 | 1,5 | 2,5 | 4,0 | 6,0 | 10,0 | 15,0 |
120-180 | 2,0 | 3,5 | 5,0 | 8,0 | 12,0 | 18,0 |
Обращает внимание высокая точность посадочных поверхностей под подшипники: круглость и цилиндричность t = t1 = 1,5 мкм, биение t3 = 2 мкм и др. для диаметров 50—80 мм и класса точности SP.
При несовпадении углов конуса шейки шпинделя и внутреннего кольца двухрядного цилиндро-роликового подшипника беговые дорожки деформируются. На рис. 2 показана деформация внутреннего кольца подшипника при уменьшении конуса шейки шпинделя на 3′. До посадки (рис. 2, а) между кольцом и шейкой шпинделя есть зазор. После посадки (рис. 2, б) кольцо деформировалось. Дорожка 1 увеличилась в диаметре на Δd1 мкм, а дорожка 2 уменьшилась на Δd2 мкм (рис. 2, в). Посадка подшипника осуществлялась осевым смещением кольца на δ0 мм вдоль оси конической шейки шпинделя.
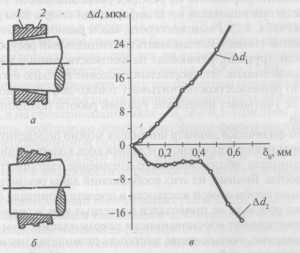
Конструкция шпинделя
Конструкция шпинделя достаточно проста и определяется числом и типом подшипников, их фиксацией, регулировкой зазора- натяга, расположением звена привода, устройством уплотнения и других элементов. Каких-либо специальных требований к конфигурации не предъявляется. При проектировании шпинделя необходимо обосновывать минимально возможные размеры при сохранении его главного функционального качества.
Расчет позволяет строго обосновать оптимальное расстояние между опорами двух- и многоопорных шпиндельных узлов и их жесткость и является главным инструментом по обоснованию конструкции шпиндельных узлов для заданных условий работы. Он позволяет на стадии проектирования учесть влияние каждого элемента шпиндельного узла: вылета шпинделя, пролетной части шпинделя, диаметральных размеров каждого подшипника передней и задней опоры шпинделя, расстояние между подшипниками на общее смещение (отжатие) шпинделя и удельное влияние каждого из них. Вылет шпинделя всегда должен быть минимальным по условиям эксплуатации станка.
Выбор диаметра шпинделя (условно — диаметр шейки шпинделя передней опоры) до настоящего времени строго не обоснован. На наш взгляд, строго математически диаметр шпинделя можно определить формально из условия равножесткости, когда смещения шпинделя из-за деформаций опор и вала равны. Равножесткость, как и равнопрочность, позволяет в равной степени использовать потенциальный ресурс всех элементов конструкции, влияющих на жесткость шпиндельного узла: вала и подшипников. Это формальное условие выгодно использовать всегда. Но равножесткость учитывает только деформационный ресурс, но не учитывает изменение условий работы подшипников под нагрузкой.
Строго физически диаметр шпинделя можно определить из условия минимального допустимого угла перекоса колец подшипников в опорах шпинделя, обеспечивающего сохранение благоприятных условий их работы.
Однако при этом не приводятся расчетные или экспериментальные подтверждения. Тем не менее это направление, учитывающее жесткость шпинделя (диаметр в пролете) с условиями работы подшипников, верно. Необходимо учесть все факторы, вызывающие перекос колец, в том числе соосность отверстий под подшипники и жесткость опор.
На практике давно увеличивают диаметр шпинделя в пролете, если возможен монтаж подшипников с переднего и заднего концов шпинделя.
Конфигурация наружной поверхности шпинделя зависит от выбранной схемы компоновки, способов фиксации подшипников и схемы привода шпинделя.
Конфигурация и требования к внутренней поверхности шпинделя зависят от размещаемых механизмов зажима заготовки или инструмента (многоцелевые станки, одно- и многошпиндельные токарные автоматы). Максимально допустимый внутренний диаметр шпинделя dB следует назначать с учетом деформаций шпинделя в поперечном сечении от действующих на него сил. Отклонение формы сечения шпинделя под нагрузкой должно быть существенно ниже допустимого отклонения от круглости внутреннего кольца подшипника. Эта тема требует специальных исследований. Из опыта проектирования рекомендуется отношение внутреннего диаметра шпинделя dB к диаметру шейки шпинделя под передней опорой d: dB/d = (0,35—0,6). В токарных станках завода ОАО «КП» чаще всего принимается dB/d = (0,5—0,6), предельное отношение dB/d = (0,4—0,7).
При выборе диаметра отверстия в шпинделе следует учитывать изменение прогиба переднего конца шпинделя. Для шпинделя диаметром d = 100 мм и оптимальным расстоянием между опорами с увеличением dB/d от 0,5 до 0,6 прогиб увеличивается, а жесткость уменьшается с 1,3 до 4,3% при радиально-упорных шарикоподшипниках в опорах (k = 0,12 × 106 Н/мм). С увеличением жесткости опор влияние отверстия более существенно изменяет жесткость шпиндельного узла: при тех же условиях и жесткости опор k = 2,6 × 106 Н/мм жесткость узла снижается с 5,8 до 13,9%.
Из приведенного примера ясно, что при одном подшипнике в опорах для шпиндельного узла на шарикоподшипниках рекомендуется dB/d < 0,5, а на роликоподшипниках — dB/d < 0,5. При этом, как отмечалось выше, необходимо оценить отклонение формы сечения шпинделя от сосредоточенной силы.
Оформление переднего конца шпинделя чаще всего выбирают стандартным, в зависимости от способа крепления инструмента или заготовки.
При проектировании шпиндельных узлов следует уделить серьезное внимание силовым смещениям шпиндельной бабки, которые определяются собственной деформацией корпуса бабки и тангенциальными смешениями в плоскости стыка станина — шпиндельная бабка. В общем балансе силовые смещения шпиндельной бабки могут быть значительными: на долю шпиндельной бабки приходится около 30% осевых смещений (станок мод. 16К20Ф1). На рис. 3 график 1 показывает осевые смещения шпинделя, график 2 — смещения шпиндельной бабки на высоте оси шпинделя, график 3 — смещения шпиндельной бабки в плоскости стыка со станиной. Исследования большой партии станков мод. 16К20Ф1 в производственных условиях показали значительное рассеивание упругих смещений корпуса шпиндельной бабки: размах выборки составлял 21 мкм.
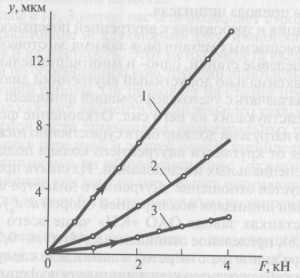
Деформация корпуса шпиндельной бабки под действием внешних сил не только увеличивает силовые смещения шпинделя и снижает жесткость узла, но и существенно влияет на деформацию посадочных поверхностей. Специально выполненный расчет силовых смещений базовых точек посадочной поверхности шпиндельной бабки станка мод. 16К20 показал следующие результаты: локальные смещения вдоль оси z шпинделя Δz = -(2,1— 5,3) мкм, радиальное смешение по оси а- в горизонтальной плоскости Δx = (0,5-3,8) мкм, радиальное смещение по оси у в вертикальной плоскости Δy = ((-0,2)-5,0) мкм.
Смешения определяли в четырех точках по окружности передней опоры методом конечных элементов с учетом закрепления шпиндельной бабки на станине при нагружении силой 4800 Н. Локальные смещения посадочной поверхности шпиндельной бабки приводят к смещению переднего конца шпинделя до 7—8 мкм.
Общий вид деформированной шпиндельной бабки после нагрузки показан на рис. 4. Обращает внимание деформация передней стенки 1 и посадочной поверхности 2 передней опоры.
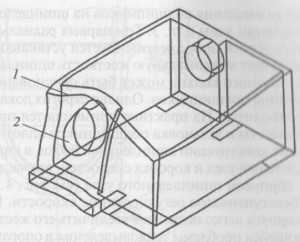
Локальные смещения посадочной поверхности под действием сил резания соизмеримы с допуском отклонения формы (см. табл. 2). Напрашивается вывод о необходимости снижения деформаций шпиндельных бабок как с целью снижения силовых смещений шпинделя относительно станины, так и с целью повышения годности вращения шпинделя в условиях силовой нагрузки. Можно также рекомендовать контроль (проверку) силовых смещений посадочных поверхностей шпиндельных бабок для каждой новой модели станка.
Следует подчеркнуть, что создание жестких корпусов шпиндельных бабок более экономично достигается оптимизацией их формы, а не простым увеличением толщины стенок. В работе приводится пример расчета корпуса шпиндельной бабки станка мод. 1К62, когда только за счет перераспределения одной и той же массы по объему конструкции влияние деформаций бабки на точность шпиндельного узла удалось снизить примерно на 35%.
В пролете шпинделя или, чаще всего, на его заднем конце размещается ведомое звено шпинделя — шкив или зубчатое колесо. Их размещение, способ крепления и передача крутящего момента на шпиндель влияют на конструкцию шпинделя. Современное жесткое крепление шкива на шпинделе существенно упрощает конструкцию узла по сравнению с разгруженным шпинделем.
Три первых радиально-упорных подшипника в передней опоре рекомендуется устанавливать вплотную, что обеспечивает максимальную жесткость шпиндельного узла. Наличие проставочного кольца может быть обосновано с позиции смазки и нагревания подшипников. Однако строгих доказательств на этот счет не приводится. На практике применяются проставочные кольца разной высоты и установка подшипников вплотную.
Традиционные конструкции шпиндельной бабки, в которых совмещаются шпиндельный узел и коробка скоростей, все чаше заменяются отдельным корпусом шпиндельного узла, чему способствует бесступенчатое регулирование скорости. Компактная конструкция корпуса легко позволяет увеличить его жесткость, но не изменяет остающейся проблемы тепловыделения в опорах и тепловых деформаций подшипников и шпинделя.
Тепловые деформации в процессе работы станков поставили проблему фиксации корпуса шпиндельной бабки от поперечных смещений. По результатам исследований и опыту эксплуатации станков рекомендуется шпиндельную бабку выполнять симметричной относительно плоскости, проходящей через ось шпинделя перпендикулярно опорной поверхности бабки. Поверхность фиксации должна располагаться в плоскости симметрии.
На рис. 5, а шпиндельная бабка 1 от боковых смещений фиксируется уступом 2, к которому она прижимается винтами (станок мод. МК6801ФЗ). Шпиндельная бабка выполнена симметричной, но поверхность фиксации, уступ 2, смещен относительно плоскости симметрии. На станке мод. МК7130 (рис. 5, б) поверхность фиксации 2 расположена практически в плоскости симметрии и шпиндельная бабка 1 симметрична и прижимается к поверхности 2 клином 3. Роль фиксатора может выполнять конический подпружиненный шип 2, ось которого лежит в плоскости симметрии 1 (рис. 5, в).
Защита шпиндельных бабок от боковых тепловых смещений в станкахВ станках с несимметричной шпиндельной бабкой и смещенной от плоскости симметрии фиксирующей поверхности (осью фиксирующего шипа) поперечные тепловые смещения бабки (определялись по смещению шпинделя) больше и достигают 7,5—35 мкм у отечественных и импортных станков после работы на холостом ходу в течение 2,5—3,0 ч при частоте вращения шпинделя n = 2400 мин-1.
С целью снижения силовых и тепловых деформаций корпуса шпиндельных бабок стали часто делать в виде унифицированной конструкции цилиндрической формы, которая существенно облегчает монтаж, балансировку, регулировку зазора-натяга подшипников и испытания на нагрев. Цилиндрический корпус позволяет готовый шпиндельный узел быстро монтировать в каком-либо корпусе станка. Ранее такие конструкции применялись только для быстроходных сменных шпиндельных узлов (n = (15 000—30 000) мин-1) в целях сокращения времени монтажа и демонтажа. Сменные шпиндельные узлы хранились в инструментальной кладовой наряду с обычным инструментом.
Винты для крепления крышек, фиксирующих подшипники от осевого смещения в передней и задней опорах, могут стать причиной снижения точности вращения шпинделя. Если имеется некая толщина стенки между расточкой в корпусе под подшипник и отверстием под винты (участок пониженной жесткости), то дорожка качения наружного кольца может деформироваться из-за вспучивания посадочной поверхности. Причем вспучивание может проявляться только после затяжки винтов, т.е. после сборки узла. Предпочтительнее использовать большее число винтов, но меньшего размера, во избежание слишком сильного затягивания и вспучивания.
Также Вам будет интересно:
chiefengineer.ru
устройство фиксации шпинделя - это... Что такое устройство фиксации шпинделя?
устройство фиксации шпинделяAutomation: spindle-keylock apparatus, spindle-keylock device, spindle-keylocking apparatus, spindle-keylocking device
Универсальный русско-английский словарь. Академик.ру. 2011.
- устройство фиксации уровня
- устройство фиксации-расфиксации
Смотреть что такое "устройство фиксации шпинделя" в других словарях:
Патрон (зажимное устройство) — Современная электродрель. Ручная дрель (коловорот). Дрель ручной, пневматический или электромеханический инструмент, предназначенный для сверления отверстий при проведении строительных, отделочных, столярных, слесарных и других работ … Википедия
ГОСТ Р ЕН 1870-1-2011: Безопасность деревообрабатывающих станков. Станки круглопильные. Часть 1. Станки круглопильные универсальные (с подвижным столом и без), станки круглопильные форматные и станки круглопильные для строительной площадки — Терминология ГОСТ Р ЕН 1870 1 2011: Безопасность деревообрабатывающих станков. Станки круглопильные. Часть 1. Станки круглопильные универсальные (с подвижным столом и без), станки круглопильные форматные и станки круглопильные для строительной… … Словарь-справочник терминов нормативно-технической документации
Описание — 3.2. Описание СИЗОД фильтрующие с принудительной подачей воздуха, используемые с масками, полумасками и четвертьмасками обычно состоят из следующих элементов: а) одного или нескольких фильтров, через который (которые) проходит весь воздух,… … Словарь-справочник терминов нормативно-технической документации
Шуруповёрт — У этого термина существуют и другие значения, см. Шуруповёрт (значения). Шуруповёрт с установленным внизу ручки аккумулятором, зарядное устройство, битодержатель и две биты (насадки крестовых отвёрток) … Википедия
Бормашина — Бормашина ротационный инструмент, развивающий высокую частоту вращения шпинделя (до 400 000 об/мин) при небольшом крутящем моменте. Бормашины используются … Википедия
universal_ru_en.academic.ru