Отпуск стали. Виды отпуска. Что такое отпуск стали
Отпуск закалённой стали
Отпуск закаленных углеродистых сталей
Образующийся при закалке стали мартенсит, представляет собой неустойчивую структуру, характеризующуюся высокой твёрдостью, хрупкостью и высоким уровнем внутренних напряжений. По этой причине закалённую сталь обязательно подвергать отпуску.
Отпуском называют термическую операцию, заключающуюся в нагреве закалённой стали до температур, не превышающих точку Аc1 (т.е. не выше линии PSK), выдержке и последующем охлаждении чаще всего на воздухе. Отпуск является окончательной операцией термической обработки, в результате которой сталь получает требуемые механические свойства. Кроме того, отпуск частично или полностью устраняет внутренние напряжения, возникшие при закалке.
Окончательные свойства стали в большей степени зависят от температуры отпуска. Различают три вида отпуска стали в зависимости от температуры нагрева.
Низкий (низкотемпературный отпуск) проводят при температурах не выше 250...300°С. При таких температурах происходит частичное обезуглероживание мартенсита и выделение из него некоторого количества избыточного углерода в виде частиц е - карбида железа. Образующаяся структура, состоящая из частичного обезуглероженного мартенсита и е-карбидов, называется отпущенным мартенситом. Выход некоторого количества углерода из решетки мартенсита способствует уменьшению её искажения и снижению внутренних напряжений. При таком отпуске несколько повышается прочность и вязкость без заметного снижения твёрдости. В целом изменение свойств при низком отпуске незначительно. Так закалённая сталь с содержанием углерода 0,5... 1,3 % после низкого отпуска сохраняет твёрдость в пределах 58...63 HRC, а следовательно, обладает высокой износостойкостью. Однако такая сталь не выдерживает значительных динамических нагрузок.
Низкому отпуску подвергают режущий и мерительный инструмент из углеродистых и низколегированных сталей, работающий без значительного разогрева рабочей части, а такие детали, прошедшие поверхностную закалку или цементацию. Цель такого отпуска - некоторое снижение внутренних напряжений.
Средний (средне-температурный) отпуск выполняют при температурах 350...500°С и применяют преимущественно для рессор, пружин, некоторых видов штампов. При таких температурах происходит дальнейшее обезуглероживание мартенсита, приводящее к его превращению в обычный а-раствор,т.е. в феррит. Одновременно происходит карбидное превращение по схеме; Fe2C Fе3С,В результате образуется феррито-цементитная смесь, называемая троститом отпуска. Наблюдается снижение твёрдости до величины 40...50 HRC, а также снижение внутренних напряжений.Высокий(высокотемпературный) отпуск проводят при 500...600°С. Структурные изменения при таких температурах заключаются в укрупнении (коагуляции) частиц цементита. В результате этого образуется феррито-цементитная смесь, называемая сорбитом отпуска. Также, как итростит отпуска, эта структура характеризуется зернистым строением в отличии от пластинчатых структур тростита и сорбита закалки. Твёрдость стали после высокого отпуска снижается до 25,,,35 HRC, Однако уровень прочности при этом ещё достаточно высок , В то же время обеспечивается повышенная пластичность и особенно ударная вязкость, практически полностью снимаются внутренние напряжения,, возникшие при закалке.
Таким образом, высокий отпуск на сорбит обеспечивает наилучший комплекс механических свойств, позволяющий применять его для деталей, работающих в условиях динамических нагрузок. Такой же отпуск рекомендуется для деталей машин из легированных сталей, работающих при повышенных температурах.
Термическую обработку, состоящую из закалки на мартенсит и последующего высокого отпуска на сорбит, называют термическим улучшением. Вообще термическому улучшению подвергают детали из среднеуглеродистых (0,3...0,5%С) конструкционных сталей, к которым предъявляют высокие требования по пределу текучести, пределу выносливости и ударной вязкости. Однако износостойкость улучшенной стали вследствие её" пониженной твёрдости невысока.
Скорость охлаждения после отпуска оказывает большое влияние на величину остаточных напряжений. Чем медленнее охлаждение, тем меньше остаточные напряжения. Так охлаждение на воздухе даёт напряжения в 7 раз меньше, а охлаждение в масле в 2,5 раза меньше по сравнению с охлаждением в воде. По этой причине изделия сложной формы во избежание их деформации после отпуска следует охлаждать медленно (на воздухе), а детали из некоторых легированных сталей, склонных к отпускной хрупкости, рекомендуется охлаждать в масле (иногда даже в воде).
Легирующие элементы, входящие в состав легированных сталей, особенно такие, как Мо5 W, Cr, Ti, V и Si, сильно тормозят диффузионные процессы, происходящие при отпуске закалённой стали. Поэтому после отпуска при одинаковой температуре легированная сталь сохраняет более высокую твёрдость и прочность. Это делает легированные стали более теплостойкими, способными работать при повышенных температурах.
Также по теме:
Применение легированных сталей. Структура и свойства легированных сталей, область их применения.
Дюраль. Состав диралюминов, свойства, применение, термообработка.
svarder.ru
5 Отпуск закаленной стали
4.4 Вопросы для самоподготовки к выполнению и защите лабораторной работы
1Что такое закалка?
2Как изменяются механические свойства в результате закалки?
3Равновесные критические точки, их смысл и обозначение.
4Обозначение и отличие фактических критических точек от равно-
весных.
5Назначение нагрева, выдержки и охлаждения при закалке.
6Что такое критическая скорость закалки?
7От чего зависит и как практически определяется общее время выдержки при закалке?
8Структура доэвтектоидной закаленной стали.
9Структура заэвтектоидной закаленной стали.
10Что такое мартенсит?
11От чего зависят свойства мартенсита?
12Основная структурная составляющая закаленной стали.
13Влияние массовой доли углерода на закаливаемость стали.
14В чем сущность мартенситного превращения?
15Почему размер аустенитных зерен влияет на размер пластин мар-
тенсита?
16Каковы условия получения крупноигольчатого и мелкоигольчатого мартенсита?
17Чем отличается мартенситное превращение от перлитного?
18Чем вызывается образование закалочных напряжении?
19До каких температур нагревают до- и заэвтектоидные стали под за-
калку?
Закаленная сталь характеризуется по сравнению с другими состояниями максимальными значениями твердости и прочности и минимальными значениями пластичности и вязкости. Кроме того, в результате закалки в стали возникают большие остаточные закалочные напряжения, которые сами по себе, без приложения внешних нагрузок, могут приводить к трещинообразованию и разрушению детали.
Поэтому для уменьшения хрупкости и снятия закалочных напряжений закаленные детали подвергают отпуску.
Отпуском называется термическая обработка, заключающаяся в нагреве закаленной стали до температуры ниже критической точки Ас1, выдержке
ипоследующем охлаждении.
Взависимости от температуры нагрева различают три вида отпуска:
− низкий отпуск от 150 °С до 250 °С;
15
−средний отпуск от 350 °С до 450 °С;
−высокий отпуск от 500 °С до 650 °С.
Выбор температуры отпуска зависит от того, в каких условиях будет работать изделие и, следовательно, какими свойствами оно должно обладать.
5.1 Превращения при отпуске, структура свойства отпущенной стали
Основным превращением, происходящим при отпуске является распад мартенсита закалки на феррито-карбиднуюсмесь.
С повышением температуры отпуска увеличивается диффузионная подвижность атомов и, как следствие этого, увеличивается скорость и полнота процесса распада мартенсита. Кроме температуры на превращения при отпуске оказывает влияние время выдержки при температуре нагрева. Однако, определяющее воздействие оказывает температура отпуска.
При низком отпуске в результате частичного распада мартенсита закалки образуется мартенсит отпуска, в котором наблюдается перераспределение углерода с начальным образованием карбидов. При этом практически не снижается твердость и износостойкость, но снимается часть закалочных напряжений и снижается хрупкость. Низкий отпуск применяется для режущих инструментов и деталей, подвергнутых поверхностной закалке, а также цементированных деталей.
Средний отпуск приводит к завершению распада мартенсита на мелкодисперсную феррито-цементитнуюсмесь, называемуютрооститом отпуска. Твердость его в пределах HRC 40 – 50 для сталей, содержащих от 0,45 % до 0,8 % С. При этом сохраняются высокие упругие свойства и происходит дальнейшее (относительно низкого отпуска) снятие закалочных напряжений. Средний отпуск применяется для пружин и рессор.
В результате высокого отпуска происходит коагуляция (укрупнение) цементитных частиц и, образующаяся при этом феррито-цементитнаясмесь с более крупными, чем у троостита отпуска цементитными частицами, называетсясорбитом отпуска. Твердость его находится в пределах HRC15 – 25 для сталей, содержащих от 0,40 % до 0,60 % С. Эта структура обладает хорошим сочетанием прочности и пластичности. Поэтому высокий отпуск применяется для многих деталей машин (коленчатые и распределительные валы, шестерни и т.п.), работающих в условиях циклических знакопеременных и динамических нагрузок.
Комплекс термической обработки, состоящей из полной закалки и высокого отпуска конструкционных сталей, называется улучшением. Таким образом, отпуск является заключительной термической обработкой, формирующей конечную структуру и придающей изделиям требуемые условиями эксплуатации свойства.
16
Для достижения этих свойств температуру отпуска необходимо назначать исходя из следующих закономерностей: при повышении температуры отпуска понижаются твердость и прочность и повышаются пластичность и ударная вязкость сталей.
Технология проведения отпуска состоит из нагрева образца до температуры соответствующего отпуска и выдержки при этой температуре. Таким образом, общее время нахождения образца в печи (τобщ.) определяется:
τобщ. =τH +τB,
где τобщ – время нахождения образца в печи, мин.; τH – время нагрева образца, мин;
τB – время выдержки образца, мин.
Данные τH, и τB выбирают из таблицы 5.
Таблица 5 – Продолжительность нагрева и выдержки при термической обработке
Температура печи, °С | Продолжительность (мин.) нагрева и выдержки |
| на 1 мм поперечного сечения образца |
900 | 1,3 – 1,8 |
800 | 1,5 – 2,0 |
700 | 0,7 – 0,9 |
600 | 0,9 – 1,1 |
500 | 1,0 – 1,2 |
400 | 1,1 – 1,3 |
300 | 1,3 – 1,6 |
200 | 1,5 – 1,8 |
Примечания 1 Времянагревадотемпературот200 °Сдо700 °Суказанабезвременивыдержки.
2 Примерноевремявыдержкипритемпературеотпускасоставляет0,5 временинагрева.
5.2 Задание и порядок выполнения работы
Рассмотреть процессы, протекающие при отпуске закаленной стали. Дать характеристику структур получаемых после отпуска стали.
Для исследуемых образцов закаленных сталей выполнить низкий, средний или высокий отпуск, исследовать микроструктуру полученных образцов пользуясь 350-500кратным увеличением и измерить твердость. Установить связи между строением, механическими свойствами и классификационными признаками.
Нарисовать микроструктуры предложенных образцов с указанием структурных составляющих.
17
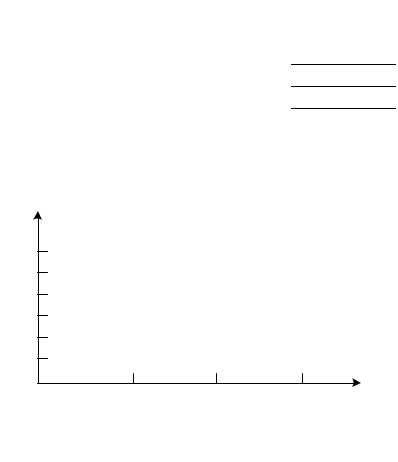
5.3 Содержание отчета
Отчет по лабораторной работе должен содержать следующие пункты:
–название работы;
–цель работы;
–исходные данные образцов и результаты закалки представить в форме таблиц 6 и 7, приведенных ниже;
Таблица 6 – Результаты закалки образцов
|
| , |
| Режим закалки |
| Результаты закалки | ||||
Маркастали | Массовая доля углерода, % | Диаметробразца | мм | t, °С | Времянагрева, | мин. |
| Охлаждающая среда | ТвердостьHRC | Структура |
|
|
|
|
|
|
|
|
|
| |
|
|
|
|
|
|
|
|
|
|
|
|
|
|
|
|
|
|
|
|
|
|
|
|
|
|
|
|
|
|
|
|
|
Таблица 7 – Режим и результаты отпуска закаленной стали.
|
| Вид отпуска |
| Результаты отпуска | |
Вид отпуска | t, °С | Время на- | Охлаждаю- | Твердость | Структура |
|
| грева, мин. | щая среда | HRC |
|
|
|
|
|
|
|
|
|
|
|
|
|
|
|
|
|
|
|
– зависимость твердости от результатов отпуска стали выстроить на координатной сетке, как показано на рисунке 7;
Рисунок 7 – Зависимость твердости от результатов отпуска стали
– выводы.
18
studfiles.net
Отпуск (в сталях) - это... Что такое Отпуск (в сталях)?
Отпуск (в сталях)Влияние отпуска на прочность и пластичность стали
О́тпуск — технологический процесс, заключающийся в термической обработке закалённого на мартенсит сплава или металла, при которой основными процессами являются распад мартенсита, а также полигонизация и рекристаллизация.
Отпуск проводят с целью получения более высокой пластичности и снижения хрупкости материала при сохранении приемлемого уровня его прочности. Для этого изделие подвергается нагреву в печи до температуры от 150°C-260°C до 370°C-650°C с последующим медленным остыванием.
Низкотемпературный отпуск
Проводят при температурах до 250 °С. Закалённая сталь сохраняет высокую износостойкость, однако такое изделие (если оно не имеет вязкой сердцевины) не выдержит высоких динамических нагрузок. Такому отпуску подвергают режущие и измерительные инструменты из углеродистых и низколегированных сталей.
Среднетемпературный отпуск
Проводят при температурах 350-500 °С и применяют главным образом для пружин и рессор, а также для штампов. Такой отпуск обеспечивает высокие пределы упругости и выносливости, а также релаксационную стойкость. Охлаждение после отпуска проводят при температурах 400-500 °С в воде, после чего возникают сжимающие остаточные напряжения, которые увеличивают предел выносливости пружин.
Высокотемпературный отпуск
Проводят при температурах 500—680 °С. При этом остается высокая прочность и пластичность, а также максимальная вязкость. Высокому отпуску подвергают детали, воспринимающие ударные нагрузки (зубчатые колеса, валы).
Стадийность
Общий принцип: Сначала заканчивается распад мартенсита, а затем начинается полигонизация и рекристаллизация. В зависимости от соотношения стадий различают:
- низкий отпуск — распад идет незначительно;
- средний отпуск — распад заканчивается, полигонизация не начинается;
- высокий отпуск — идет полигонизация или рекристаллизация.
См. также
- Металлургические процессы
- Отжиг
Литература
- Ю.М. Лахтин, В.П. Леонтьева "Материаловедение" Москва издательство "Машиностроение" 1990.
Wikimedia Foundation. 2010.
- Отправитель
- Отоманская Империя
Смотреть что такое "Отпуск (в сталях)" в других словарях:
Отпуск (металлов) — Отпуск металлов, вид термической обработки, заключающийся в нагреве закалённого сплава до температуры ниже нижней критической точки, выдержке и последующем охлаждении. Термин «О.» применяют главным образом к сталям. Процессы распада… … Большая советская энциклопедия
ОТПУСК (металлов) — ОТПУСК металлов, термическая обработка (см. ТЕРМИЧЕСКАЯ ОБРАБОТКА) закаленных сплавов, в которых превращение при закалке имело мартенситный характер. Термин «отпуск» применяют главным образом к сталям. Отпуск, как и старение (см. СТАРЕНИЕ… … Энциклопедический словарь
Отпуск — I Отпуск в СССР ежегодное время отдыха, гарантированное Конституцией СССР (ст. 119), в течение которого за работником сохраняется место работы (должность) и средний заработок. Наряду с О. для отдыха законодательство предусматривает О. по… … Большая советская энциклопедия
Высокий отпуск — Для улучшения этой статьи желательно?: Найти и оформить в виде сносок ссылки на авторитетные источники, подтверждающие написанное … Википедия
ЖЕЛЕЗА СПЛАВЫ — металлич. системы, одним из компонентов к рых (как правило, преобладающим) служит железо. Различают сплавы железа с углеродом (нелегир. и легир. чугуны и стали), сплавы с особыми физ. хим. св вами и ферросплавы. Система железо углерод. Наиб.… … Химическая энциклопедия
Сталь — (Steel) Определение стали, производство и обработка стали, свойства сталей Информация об определении стали, производство и обработка стали, классификация и свойства сталей Содержание Содержание Классификация Характеристики стали Разновидности… … Энциклопедия инвестора
Быстрорежущая сталь — Быстрорежущие стали легированные стали, предназначенные, главным образом, для изготовления металлорежущего инструмента, работающего при высоких скоростях резания … Википедия
Термическая обработка — металлов, процесс обработки изделий из металлов и сплавов путём теплового воздействия с целью изменения их структуры и свойств в заданном направлении. Это воздействие может сочетаться также с химическим, деформационным, магнитным и др.… … Большая советская энциклопедия
Легирование — Не следует путать с с лигированием в медицине и биохимии. Легирование (нем. legieren «сплавлять», от лат. ligare «связывать») добавление в состав материалов примесей для изменения (улучшения) физических и химических… … Википедия
Легировка — Легирование (нем. legieren сплавлять, от лат. ligo связываю, соединяю) введение в расплав или шихту дополнительных элементов (например, в сталь хрома, никеля, молибдена, вольфрама, ванадия, ниобия, титана), улучшающих механические, физические … Википедия
dic.academic.ru
Высокий отпуск стали — ПЗТО
Высокий отпуск стали - метод термической обработки, при котором металл нагревается до температуры не выше нижнего порога интервала превращений Ас1, выдерживается при ней и медленно или быстро охлаждается. Скорость охлаждения зависит от сложности форм деталей, в случае с легированными сталями важен фактор отпускной хрупкости. Отпуск является заключительным этапом термообработки металлов. От правильности его выполнения во многом зависит конечное качество готовой детали. Когда высокий отпуск проводится после закалки, применим термин "улучшение стали".
Назначение проведения высокого отпуска металла
Основная цель обработки металла методом высокого отпуска - придание ему максимальной вязкости в условиях сохранения достаточных упругости и предела прочности металла. В процессе проведения высокого отпуска сталь приобретает наивыгоднейшее сочетание механических свойств с вязкостью и пластичностью. Также, при условии медленного охлаждения, практически полностью устраняются внутренние напряжения металла, возникающие после закалки. Используется для снятия напряжений после правки.
Термообработку в виде высокого отпуска применяют к деталям из среднеуглеродистых и конструкционных сталей - к ним предъявляются повышенные требования относительно пределов ударной вязкости, выносливости и текучести. Повышается конструктивная прочность стали, происходит понижение верхнего и нижнего порогов хладноломкости, сводится к минимуму возможность развития трещин.
Методика улучшения стали, как правило, применяется для деталей различных станков и машин.
Режим проведения высокого отпуска
Температурный режим, в условиях которого возможен полный отпуск - выше 500° С и ниже точки Ас1 - нижнего предела интервала превращений. Таким образом, интервал температур находится в пределах 500 - 600° С, для легированных сталей - до 700° С. Время выдержки по достижении требуемых температур - 0,5 - 1 час. В роли охлаждающих сред могут фигурировать воздушная и масляная среды. Что касается скорости охлаждения, детали сложных форм охлаждаются медленно для исключения коробления, изделия из легированных сталей во избежание хрупкости охлаждают быстро. Скорость охлаждения также в значительной мере влияет на снятие внутренних напряжений в металле - чем медленнее идет процесс охлаждения, тем меньше остается внутренних напряжений.
Высокий отпуск стали на нашем заводе проводится в камерной отпускной электропечи современного образца, оборудованной системой принудительной циркуляции атмосферы внутри печи. Среди достоинств нашего оборудования:
-
контроль температуры
-
конвекция
-
регулировочные приборы высокой точности
-
равномерное распределение температуры в различных точках печи
-
графики-режимы термообработки изделий
Процесс термической обработки металла с помощью такого оборудования проходит в условиях строгого соблюдения технологических требований. Изделия, прошедшие высокий отпуск на нашем оборудовании, отличаются высоким качеством металла и улучшенными характеристиками.
Структурные изменения в результате проведения высокого отпуска стали
В ходе высокого отжига происходит процесс рекристаллизации (приводящей вещество в состояние большей термодинамической устойчивости) в сочетании со сфероидизацией цементита. Частицы цементита приобретают округлую форму размером от 0,5 до 2 мкм., приобретается структура сорбита отпуска с зернистой формой. Сорбит отпуска наделяет сталь повышенной ударной вязкостью. Легированные стали приобретают структуру зернистого перлита. Обеспечивается структурная стабильность, снимается внутреннее напряжение.
Технологические процессы на нашем заводе проводятся в современном компьютеризированном оборудовании под управлением квалифицированного персонала. Это помогает добиться самых высоких показателей в области химико-термической обработки металлов. У нас практикуется индивидуальный подход к каждому клиенту и каждому заказу.
Заказать услугу по высокому отпуску металла Вы можете, воспользовавшись формой обратной связи или по телефонам нашего сайта.
pzto.pro
Отпуск стали. Виды отпуска
Отпуску подвергают закаленную сталь с целью повышения ее ударной вязкости и пластичности, уменьшения твердости и внутренних напряжений. Для отпуска сталь нагревают до температуры ниже точки Ас1(линия PSK) и затем охлаждают обычно на воздухе.
В зависимости от температуры нагрева различают отпуск низко-, средне- и высокотемпературный.
Низкотемпературный (низкий) отпуск проводят с нагревом до 150…200 °С. При низком отпуске несколько снижаются внутренние напряжения. Твердость остается высокой (58…62 HRC). Структура стали после низкого отпуска состоит из мартенсита отпуска. Этот вид отпуска применяется, в основном, для режущих и измерительных инструментов, для изделий, подвергаемых поверхностной закалке, цементации, нитроцементации. Низкий отпуск рекомендуется для деталей из малоуглеродистых легированных сталей, так как малоуглеродистый мартенсит отпуска имеет высокий комплекс механических свойств.
Основное превращение при отпуске - распад мартенсита, т.е. выделение углерода из пересыщенного твердого раствора в виде мельчайших кристалликов карбида железа.
Распад мартенсита завершается при температуре около 400 °С, образовавшуюся ферритоцементитную высокодисперсную механическую смесь называют трооститом отпуска. При более высокой температуре нагрева происходит коагуляция кристаллов карбида железа, дисперсность ферритоцементитной смеси снижается и при температуре 500…650 °С образуется сорбит отпуска. Помимо описанных превращений в интервале температур 200… 300 °С происходит распад остаточного аустенита с образованием отпущенного мартенсита.
В зависимости от температуры нагрева различают три вида отпуска.
Низкий отпуск производится при 120…150 °С (отпуск на отпущенный мартенсит). Его применяют после закалки инструментов, цементованных и цианированных изделий, а также после поверхностной закалки. При низком отпуске уменьшаются остаточные закалочные напряжения, твердость практически не снижается.
Средний отпуск (отпуск на троостит) происходит при нагреве до температур 350…450 °С. При этом снижается твердость. Средний отпуск рекомендуется для пружин и рессор.
Высокий отпуск (отпуск на сорбит) производится при температуре 500…650 °С. Применяют в машиностроении для изделий из конструкционной стали с целью обеспечения достаточной прочности, вязкости и пластичности. Сочетание закалки с высоким отпуском на сорбит называется улучшением. Эту операцию применяют для среднеуглеродистых сталей (0,35…0,6 % С).
После закалки (при охлаждении в воде) углеродистой стали (0,4 % С) и отпуске при 300 °С sв = 1300 МПа, d = 12 %,y = 35 %, а при отпуске 600 °С sв = 620 МПа, d = 22 %, y = 55 %.
Химико-термическая обработка сталей
Химико-термической обработкой называют технологический процесс, заключающийся в диффузионном насыщении поверхностного слоя деталей различными элементами с целью изменения его состава, структуры и свойств.
Химико-термическую обработку применяют для повышения твердости, износостойкости, сопротивления усталости и контактной выносливости, а также для защиты от электрохимической и газовой коррозии.
Проведение любой химико-термической обработки деталей включает следующие стадии:
1) диссоциацию химических соединений, в состав которых входит насыщающий элемент, с образованием активных атомов диффундирующего элемента;
2) адсорбцию диффундирующих элементов на поверхности металла, в результате чего тончайший поверхностный слой насыщается диффузионно-активным элементом;
3) собственно диффузию - проникновение элемента в глубь металла.
В результате образуется диффузионный слой, на поверхности которого концентрация легирующего элемента максимальна, а по мере удаления от нее - снижается.
Цементация сталей
Цементацией называется процесс насыщения поверхности изделия углеродом. Цель цементации - придание поверхности твердости при сохранении мягкой сердцевины. Обычно цементации подвергают детали из низкоуглеродистой стали, содержащей не более 0,25 % С (сталь марок 10, 15, 20, А12, 15Х, 25ХГМ и др.), работающие в условиях переменных ударных нагрузок и подвергающиеся износу, например зубья автомобильных зубчатых колес, шестерни, втулки, поршневые пальцы и т.д. Температура цементации 900…970 °С. Толщина цементованного слоя от 0,1 до 3…4 мм.
В поверхностном слое содержание углерода составляет 0,8…1,0 %. Цементацию проводят в твердых, жидких и газообразных средах, называемых карбюризаторами. В качестве твердого карбюризатора применяют древесный уголь в смеси с другими компонентами.
Газовую цементацию проводят в атмосфере метана, керосина, бензола и др. Применяют для массового производства мелких деталей. Жидкие карбюризаторы (смесь цианистого калия с бурой, содой и другими веществами) применяют в тех случаях, когда нужно получить тонкий цементованный слой с высоким содержанием углерода.
Для придания твердости наружному слою производят закалку с температур 820…850 °С и низкий отпуск при 150…170 °С. После термической обработки твердость поверхностного слоя 60…64 HRC. Чтобы получить заданную структуру и свойства материала сердцевины изделия, проводят нормализацию (880…900 °С) и для поверхностного слоя - закалку (760…780 °С) с низким отпуском.
Газовая цементация наиболее широко применяется в массовом производстве. Основной реакцией, обеспечивающей выделение свободного атомарного углерода, является диссоциация метана и оксида углерода по реакции:
СН4 ® 2Н2 + Сат,
2СО ® СО2 + Сат.
В качестве карбюризатора используют разбавленный природный газ (метан), контролируемые атмосферы, получаемые в специальных генераторах, а также пары жидких углеводородов.
При газовой цементации можно получить заданную концентрацию углерода в слое, сократить длительность процесса, обеспечить возможность полной механизации и автоматизации процесса, проводить закалку непосредственно от температуры цементации.
Содержание углерода в поверхностном слое при данной температуре обычно составляет 1,1…1,2 % и быстро убывает по толщине детали, поэтому после охлаждения структура различна по глубине и твердости.
После закалки цементованные детали во всех случаях подвергают низкому отпуску при температуре 160…180 °С для уменьшения закалочных напряжений и повышения сопротивления хрупкому разрушению.
Азотирование стали
Азотированием называют процесс насыщения стали азотом. Цель азотирования - придать поверхности высокую твердость, износостойкость, устойчивость против коррозии и усталостную прочность. Процесс заключается в воздействии на сталь аммиака (газовое азотирование) при температуре 500…600 °С. Образовавшийся свободный азот, находящийся в атомарном состоянии, воздействует на сталь и образует с элементами, входящими в ее состав (Cr, Fe, Al и др.), различные нитриды, обладающие высокой твердостью (до 70 HRC). Азотированный слой сохраняет свою твердость до 400…600 °С, в то время как твердость цементированного слоя с мартенситной структурой сохраняется лишь до 200…250 °С. Толщина азотированного слоя 0,25…0,75 мм. Азотированию подвергают легированные стали, например 35ХМЮА, 18ХГТ, 40ХНМА, 38Х2МЮА и др.
Перед азотированием детали подвергают закалке и высокому отпуску (600…675 °С) с целью улучшения их механических свойств. Для ускорения процесса сначала производят азотирование при 500…520 °С, а затем при 560…600 °С. Повышение температуры ускоряет процесс диффузии и почти не сказывается на твердости поверхностного слоя.
Достоинством процесса азотирования по сравнению с цементацией является незначительное изменение размеров и отсутствие коробления вследствие низкой температуры нагрева. Азотированные поверхности имеют большую химическую стойкость на воздухе, а также в пресной и соленой воде.
Азотирование в жидких средах производится при температуре 570 °С в расплавленных цианистых солях в течение 0,5…3 ч. Общая толщина слоя 150…500 мкм, твердость HV 600…11000. Жидкое азотирование повышает сопротивление износу и предел выносливости. Недостатком его является токсичность и высокая стоимость процесса. Его используют для обработки деталей автомобиля (коленчатые валы, шестерни и т.д.), а также штампов, пресс-форм и др.
Цианирование сталей
Цианированием называют насыщение поверхности изделий одновременно углеродом и азотом в расплавленных цианистых слоях при температуре 820…950 °С.
При низкотемпературном цианировании детали нагревают до 820…860 °С в расплавленных солях, содержащих NaCN, в течение 0,5…1,5 ч, при этом получают слой толщиной 150…350 мкм. Затем производят закалку непосредственно с температуры цианирования с последующим низкотемпературным отпуском (180…200 °С). Твердость после термической обработки составляет 58…62 HRC. Такой обработке обычно подвергают детали из среднеуглеродистых сталей и инструменты из быстрорежущих сталей.
Для получения более толстого слоя (500…2000 мкм) применяют высокотемпературное цианирование при 930…950 °С со временем выдержки 1,5…6 ч. После такой обработки детали охлаждают на воздухе, производят закалку и низкотемпературный отпуск.
Нитроцементация
Нитроцементация представляет собой процесс насыщения поверхностного слоя одновременно углеродом и азотом в газовой среде азота 40 %, водорода 40 % и оксида углерода 20 % при температуре 850…870 °С в течение 4…10 ч. Назначение - повышение износостойкости, предела выносливости при изгибе, твердости и коррозионной стойкости. После закалки и низкого отпуска (160…180 °С) твердость поверхностного слоя составляет НRC 58…60 и толщина слоя 0,2…0,8 мм; они зависят от температуры и времени выдержки.
Нитроцементацию широко используют в автомобильном и автотракторном производстве. Нитроцементация имеет определенные преимущества по сравнению с газовой цементацией - более низкая температура процесса, снижение деформации и коробления и др.
Борирование
Борирование заключается в насыщении поверхностного слоя изделий из низко- и среднеуглеродистых сталей 20, 40, 40Х, 30ХГС и других бором при нагревании в боросодержащей среде. Борирование применяют для повышения твердости, износостойкости, коррозионной стойкости и окалиностойкости тяжело нагруженных деталей (нефтяное оборудование, штампы, пресс-формы и др.). Процесс проводится при температуре 850…950 °С в течение 2…6 ч. Поверхностный слой состоит из боридов, толщина слоя 0,1…0,2 мм твердость его 1800…2000 HV.
stydopedia.ru
ОТПУСК СТАЛИ
СЛЕСАРНОЕ ДЕЛО
55. Что такое отпуск углеродистой стали?
Отпуск — это термическая операция, которой подвергают стальные изделия, предварительно закаленные. Она заключается в нагревании изделий до определенной температуры ниже критической точки Лсг, выдерживании при этой температуре и последующем постепенном охлаждении на воздухе. Отпуск на цвет побежалости производится в интервале температур 230—330° С (табл. 26) с последующим замачиванием в воде.
56. Какова цель отпуска?
Цель отпуска — уменьшение или полное снятие внутренних напряжений в изделии, появившихся во время закалки, улучшение пластических свойств, уменьшение хрупкости и некоторое снижение твердости (степень твердости будет зависеть от температуры отпуска), увеличение вязкости.
57. Назвать способы отпуска закаленной стали.
Применяют три способа отпуска закаленной стали: низкий при температуре 150—250° С; средний — при 350— 450° С и высокий при температуре 450—650° С.
Название цвета | Температура, ° с | Изделия, подвергающиеся отпуску при данной температуре |
Светло-соломенный | 230 | Гравировальные иглы, долото для обработки камня, мелкие режущие инструменты |
Соломенный | 240 | Фрезы, токарные резцы, развертки, резцы для долбления, пробойники, небольшие пуансоны |
Темно-соломенный | 250 | Сверла, плашки, метчики, фигурные фре» зы, молотки |
Красно-бурый | 2G0 | Матрицы, режущие части ножниц, долота пневматических молотков и зубила, инструмент для обработки древесины |
Пурпурный | 270 | Большие пробойники, пневматические рубильные молотки, матрицы, столовые ножи |
Свекольно- фиолетовый | 280 | |
Темно-голубой | 2% | Пилы, пневматические молотки, большие штампы, пружины, ножовки, хирургический инструмент |
Васильковый | 300 | |
Голубой | 310 | Некоторые пружины, детали инструментов, которые должны обладать высокой сопротивляемостью ударам |
Серо-голубой | 320 | |
Серо-зеленый | 330 |
Температуру отпуска для определенных марок стали (а также разных изделий) и вид охлаждающей среды определяют по специальным таблицам.
58. Перечислить способы нагревания стали при отпуске.
Нагрев при отпуске производится в масляных, селитровых или щелочных ваннах, а также в газовых, мазутных ила электрических печах с воздушной атмосферой. В ряде случаев применяется нагрев в горне или на разогретой металлической плите. Общее время пребывания изделия в печи при отпуске составляет примерно 2—3 мин на I мм наименьшего сечения детали, но не менее, чем 30—40 мин.
59. Какие свойства приобретает сталь при каждом из перечисленных способов отпуска?
В результате низкотемпературного отпуска при температуре 150—250° С уменьшаются внутренние напряжения и хрупкость стали, незначительно снижается твердость, несколько увеличивается вязкость. Низкому отпуску подвергаются изделия, которые должны иметь высокую твердость (режущий и мерительный инструмент). Средний отпуск при температуре 350—450° С несколько снижает твердость и значительно увеличивает вязкость, сопротивляемость стали ударам, прочность и упругость. Применяется для пил, рессор-пружин, молотков, матриц, пуансонов, автомобильных деталей. Высокий отпуск при температурах 450—650° С полностью устраняет внутренние напряжения и обеспечивает наилучшее сочетание прочности и вязкости стали при достаточной ее твердости. Применяется для ответственных деталей.
60. Что такое термическое улучшение стали?
Термическое улучшение состоит из процессов закаливания и высокого отпуска. Благодаря этим процессам достигается улучшение механических свойств стали, обеспечивается возможность обработки резанием.
61. Для какого инструмента применяется двойной отпуск?
Двойной отпуск применяется для инструмента, поверхность которого должна иметь различную твердость (пуансон, вырубной штамп, прошивень, зубило). Например, зубило: первый отпуск при температуре ниже 300° С выполняют для режущей части, второй отпуск при температуре 300— 500° С — для головки зубила.
ПАЙКА, ЛУЖЕНИЕ, ЗАЛИВКА ВКЛАДЫШЕЙ, МЕТАЛЛИЗАЦИЯ И СКЛЕИВАНИЕ
262. Что такое пайка? Пайка — это процесс создания неразъемного соединения металлов с помощью присадочного связующего материала, называемого припоем, причем припой в процессе пайки доводится до жидкого состояния. Температура плавления …
ШЕРОХОВАТОСТЬ ПОВЕРХНОСТИ И ДОПУСКИ НА ИЗГОТОВЛЕНИЕ
4. Что такое шероховатость поверхности? Поверхности всех деталей после механической обработки не являются идеально гладкими, так как режущие кромки инструмента оставляют на поверхности следы в виде определенных неровностей и гребешков …
СЛЕСАРНОЕ ДЕЛО 0 ВОПРОСАХ И ОТВЕТАХ
1. Что ты знаешь о слесарном деле? Слесарное дело — это ремесло — умение обрабатывать металл в холодном состоянии при помощи ручных слесарных инструментов (молотка, зубила, напильника, ножовки и другого …
msd.com.ua
Отпуск стали. Температура отпуска стали. Режимы отпуска стали. Отпускная хрупкость. Улучшение термическая обработка.
Раздел: | Материаловедение. Металловедение. |
Отпуск является окончательной термической обработкой. Целью отпуска является повышение вязкости и пластичности, снижение твердости и уменьшение внутренних напряжений закаленных сталей (см. Закалка стали). С повышением температуры нагрева прочность обычно снижается, а пластичность и вязкость растут. Температуру отпуска выбирают, исходя из требуемой прочности конкретной детали.
Термическая обработка металла. Термическая обработка металлов и сплавов. Виды термической обработки металлов. Виды термообработки.
Различают три вида отпуска:
1. Низкий отпуск с температурой нагрева Тн = 150…300oС.
В результате его проведения частично снимаются закалочные напряжения. Получают структуру – мартенсит отпуска.Проводят для инструментальных сталей после закалки токами высокой частоты или после цементации.
2. Средний отпуск с температурой нагрева Тн = 300…450oС.
Получают структуру – троостит отпуска, сочетающую высокую твердость 40…45HRC c хорошей упругостью и вязкостью.Используется для изделий типа пружин, рессор.
3. Высокий отпуск с температурой нагрева Тн = 450…650oС..
Получают структуру, сочетающую достаточно высокую твердость и повышенную ударную вязкость (оптимальное сочетание свойств) – сорбит отпуска.Используется для деталей машин, испытывающих ударные нагрузки.Комплекс термической обработки, включающий закалку и высокий отпуск, называется улучшением.
Способы закалки. Способы закалки стали. Виды закалки стали. Технология закалки стали. Режимы закалки сталей.Закалка стали. Закалка металла. Виды закалки. Температура закалки. Закаливаемость. Прокаливаемость. Критический диаметр.
Отпускная хрупкость
Обычно с повышением температуры отпуска ударная вязкость увеличивается, а скорость охлаждения не влияет на свойства. Но для некоторых сталей наблюдается снижение ударной вязкости. Этот дефект называется отпускной хрупкостью.
Зависимость ударной вязкости от температуры отпуска
Отпускная хрупкость I рода наблюдается при отпуске в области температур около 300oС. Она не зависит от скорости охлаждения. Это явление связано с неравномерностьюпревращения отпущенного мартенсита (см. Мартенсит. Мартенситное превращение.). Процесс протекает быстрее вблизи границ зерен по сравнению с объемами внутри зерна. У границ наблюдается концентрация напряжений, поэтому границы хрупкие.
Отпускная хрупкость I рода “необратима“, то есть при повторных нагревах тех же деталей не наблюдается.
Нормализация стали. Температура нормализации стали. Процесс нормализации стали.
Отпускная хрупкость II рода наблюдается у легированных сталей при медленном охлаждении после отпуска в области 450…650oС. При высоком отпуске по границам зерен происходит образование и выделение дисперсных включений карбидов. Приграничная зона обедняется легирующими элементами. При последующем медленном охлаждении происходит диффузия фосфора к границам зерна. Приграничные зоны обогащаются фосфором, снижаются прочность и ударная вязкость. Этому деекту способствуют хром, марганец и фосфор. Уменьшают склонность к отпускной хрупкости II рода молибден и вольфрам, а также быстрое охлаждение после отпуска.
Отжиг стали. Отжиг второго рода. Полный отжиг. Неполный отжиг. Полный и неполный отжиг. Изотермический отжиг.Отжиг стали. Отжиг первого рода. Диффузионный отжиг. Отжиг рекристаллизационный. Отжиг для снятия напряжений.
Отпускная хрупкость II рода “обратима“, то есть при повторных нагревах и медленном охлаждении тех же сталей в опасном интервале температур дефект может повториться.
Стали, склонные к отпускной хрупкости II рода, нельзя использовать для работы с нагревом до 650oС без последующего быстрого охлаждения.
Улучшаемые стали
· Химия
Улучшаемыми сталями называют среднеуглеродистые конструкционные стали (0,3–05 % С), подвергаемые закалке и последующему высокотемпературному отпуску. После такой термической обработки стали приобретают структуру сорбита, хорошо воспринимающую ударные нагрузки. Углеродистые улучшаемые стали (стали 35, 40, 45 и 50) обладают небольшой прокаливаемостью (до 10 мм), поэтому механические свойства с увеличением сечения изделия понижаются. Для мелких деталей после термической обработки получают sв=600¸700 МПа и КСU=0,4–0,5 МДж/м2. Если от деталей требуется более высокая поверхностная твердость (шпиндели, валы, оси и т.д.), то после закалки их подвергают отпуску на твердость НRС 40–50. Для получения высокой поверхностной твердости используют закалку ТВЧ (шестерни, коленчатые валы, поршневые пальцы и т.д.).Для получения высоких механических свойств в деталях сечением более 25–30 мм применяют легированные стали, которые обладают большей прокаливаемостью, более мелким зерном, их критическая скорость закалки меньше, следовательно, меньше закалочные напряжения, выше устойчивость против отпуска. Отсюда их основное преимущество перед углеродистыми конструкционными сталями–лучший комплекс механических свойств: выше прочность при сохранении достаточной вязкости и пластичности, ниже порог хладноломкости.Большинство легированных конструкционных сталей относится к перлитному классу.При создании легированных сталей всегда учитывают стоимость легирующего элемента и его дефицитность.Основным легирующим элементом в конструкционных сталях является хром, содержание которого обычно составляет 0,8–1,1 %; марганца в сталях до 1,5 %; кремния 0,9–1,2 %; молибдена 0,15–0,45 %; никеля 1–4,5 %. Общая сумма легирующих элементов не превышает 3–5 %.Все перечисленные элементы, кроме никеля, увеличивая прочность стали, понижают ее пластичность и вязкость. Никель является исключением–он оказывает особенно положительное влияние на свойства стали, увеличивая ее прочность, не понижая пластичность и вязкость. Кроме того, никель понижает порог хладноломкости. Поэтому стали, содержащие никель, особенно ценны как конструкционный материал.Кроме названных элементов, в конструкционные стали для деталей машин вводят около 0,1 % V, Тi, Nb, Zr для измельчения зерна. Введение 0,002–0,003 % В увеличивает прокаливаемость.Улучшаемые стали можно условно разделить на несколько групп. Широко применяют стали, легированные хромом, особенно стали марок 40Х, 45Х. Для увеличения прокаливаемости в них иногда добавляют бор (сталь 40ХР). Увеличение прокаливаемости (в сечении до 40 мм) достигается и добавлением в хромистые стали около 1 % Мn: 30ХГ, 40ХГ, 40ХГР и др. Для уменьшения склонности хромистых сталей к отпускной хрупкости II рода вводят 0,15–0,25 % Мо.Хромомарганцевые стали 20ХГС, 25ХГС, 30ХГС, называемые хромансиль, легированы хромом, кремнием и марганцем, т.е. не содержат дефицитных легирующих элементов. Эти стали обладают хорошей свариваемостью и прочностью, например, сталь 30ХГС после термической обработки имеет sв=1650 МПа при КСU=0,4 МДж/м2. Недостаток этих сталей склонность к отпускной хрупкости II рода и к обезуглероживанию поверхности при нагреве.Чем больше размер детали, сложнее ее конфигурация, выше напряжения, возникающие в ней в процессе работы, тем с большим количеством никеля применяют сталь для ее изготовления: 40ХНМ, 30ХН2МФ, 38ХНЗМФ и т.д.Молибден и волъфрам вводят в состав сталей также для уменьшении склонности к отпускной хрупкости. На рис.3 приведена диаграмма, позволяющая выбрать нужную марку стали, в зависимости от заданных прочности и размеров сечения. Рис. 3.Диаграмма для выбора марок конструкционной стали в зависимости от заданной прочности и размера сечения детали:1 - 30ХН3М; 2 - 30ХН3; 3 - 34ХМА; 4 - 33ХСА; 5 - 30Н3; 6 - 35ХА; 7 - 35СГ; 8 - сталь 30
cyberpedia.su