Диффузионное насыщение неметаллами. Насыщение поверхностного слоя углеродом называется
Диффузионное насыщение неметаллами - Химико-термическая обработка - Химико-термическая и термомеханическая обработки
Поверхностное насыщение стали углеродом и азотом или совместно этими элементами — наиболее широко используемые процессы химико-термической обработки.
Углерод и азот растворяются в железе по способу внедрения и поэтому могут быстро диффундировать на значительную глубину. Активные среды, содержащие эти элементы, дешевы, а фазы, образующиеся с участием углерода и азота в процессе насыщения или при последующей термообработке, резко изменяют механические и физико-химические свойства стали.
Науглероживание (цементация)
Цементации подвергают изделия из сталей с низким содержанием углерода (обычно до 0,25%).
При цементации в твердом карбюризаторе изделия укладывают в ящики, куда засыпают и утрамбовывают древесный уголь, смешанный с 20 — 26% ВаСO3.
При нагревании углерод древесного угля, соединяясь с кислородом воздуха, находящегося в цементационном ящике между частицами карбюризатора, образует окись углерода:
В контакте с железом окись углерода дает атомарный углерод:
Этот активный углерод (in statu nascendi) поглощается аустенитом и диффундирует в глубь изделия. Добавка ВаСО3 сильно интенсифицирует процесс цементации, поставляя дополнительное количество окиси углерода и соответственно активного углерода:
Для газовой цементации в качестве карбюризатора используют природный газ (состоит в основном из СН4), контролируемые атмосферы, получаемые в специальных генераторах, а также жидкие углеводороды (керосин, бензол и др.), каплями подаваемые в герметичное рабочее пространство печи, где они образуют активную газовую фазу. Основной поставщик углерода в газообразных карбюризаторах — метан:
В искусственно полученной контролируемой атмосфере таким поставщиком является окись углерода.
Газовая цементация — основной процесс при массовом производстве, а цементацию в твердом карбюризаторе используют в мелкосерийном производстве.
Глубина цементации в зависимости от назначения изделия и состава стали обычно находится в пределах 0,6 — 2,0 мм.
Цементацию проводят при 910 — 930 °С, а иногда, для ускорения, при 1000 — 1050 °С. С повышением температуры уменьшается время достижения заданной глубины цементации. Так, при газовой цементации науглероженный слой толщиной 1,0 — 1,3 мм получают при 920 °С за 15 ч, а при 1000 °С — за 8 ч. Чтобы предотвратить сильный перегрев (рост аустенитного зерна), высокотемпературной цементации подвергают наследственно мелкозернистые стали.
Концентрация углерода в поверхностном слое изделия обычно составляет 0,8 — 1,0% и не достигает предела растворимости яри температуре цементации. Следовательно, сетка FeC при температуре цементации не образуется, и поверхностный слой, как и сердцевина, находится в аустенитном состоянии.
После медленного охлаждения цементованный слой с переменной концентрацией углерода состоит из феррита и цементита и характеризуется гаммой структур, типичных для заэвтектоидной, эвтектоидной и доэвтектоидной стали (смотрите рисунок Участок диаграммы состояния Fe — С).
Цементация является промежуточной операцией, цель которой — обогащение поверхностного слоя углеродом. Требуемое упрочнение поверхностного слоя изделия достигается закалкой после цементации. Закалка должна не только упрочнить поверхностный слой, но и исправить структуру перегрева, возникающую из-за многочасовой выдержки стали при температуре цементации.
После цементации в твердом карбюризаторе ответственные изделия подвергают двойной закалке, так как содержание углерода в сердцевине и на поверхности изделия разное, а оптимальная температура нагрева под закалку зависит от содержания углерода в стали (смотрите рисунок Интервал температур нагрева под закалку углеродистых сталей).
Первую закалку проводят с нагревом до 850 — 900 °С (выше точки А3 сердцевины изделия), чтобы произошла полная фазовая перекристаллизация с измельчением аустенитного зерна в доэвтектоидной стали. В углеродистой стали из-за малой глубины прокаливаемости сердцевина изделия после первой закалки состоит из феррита и перлита.
Вместо первой закалки к углеродистой стали можно применять нормализацию. В прокаливающейся насквозь легированной стали сердцевина изделия состоит из низкоуглеродистого мартенсита. Такая структура обеспечивает повышенную прочность и достаточную вязкость сердцевины.
После первой закалки цементованный слой оказывается перегретым и содержащим повышенное количество остаточного аустенита. Поэтому применяют вторую закалку с температуры 760 — 780 °С, оптимальной для заэвтектоидных сталей. После второй закалки поверхностный слой состоит из мелкоигольчатого высокоуглеродистого мартенсита и глобулярных включений вторичного карбида.
При газовой цементации чаще всего применяют одну закалку с цементационного нагрева после подстуживания изделия до температур 840 — 860 °С. После закалки цементованные изделия всегда нагревают до 160 — 180 °С для уменьшения закалочных напряжений.
Цементацию широко применяют в машиностроении для повышения твердости и износостойкости изделий с сохранением высокой вязкости их сердцевины. Удельный объем закаленного науглероженного слоя больше, чем сердцевины, и поэтому в нем возникают значительные сжимающие напряжения. Остаточные напряжения сжатия в поверхностном слое, достигающие 40 — 50 кгс/мм2, повышают предел выносливости изделия.
Низкое содержание углерода (0,08 — 0,2 : 5%) обеспечивает высокую вязкость сердцевины. Цементации подвергают качественные стали 08, 10, 15 и 20 и легированные стали 12ХНЗА, 18ХГТ и др.
Основное назначение легирования здесь — повышение прокаливаемости и соответственно механических свойств сердцевины изделий из цементуемой стали.
«Теория термической обработки металлов»,И.И.Новиков
Азотирование стальных изделий проводят в аммиаке, который при нагревании диссоциирует, поставляя активный атомарный азот: В системе Fe — N при температурах азотирование могут образовываться следующие фазы: α-раствор азота в железе (азотистый феррит), γ-раствор азота в железе (азотистый аустенит), промежуточная γ-фаза переменного состава с г. ц. к. решеткой (ей приписывают формулу Fe4N) и промежуточная ε-фаза с…
Металлы растворяются в железе и других металлах по способу замещения и потому медленнее, чем неметаллы, диффундируют в изделие. Как правило, диффузионное насыщение металлами проводят при более высоких температурах, чем насыщение неметаллами. Типичные примеры — алитирование и хромирование. Алитирование (алюминирование) применяют для повышения окалиностойкости сталей и реже чугунов. Алитируют также литые лопатки газотурбинных двигателей из жаропрочных…
В промышленности применяют множество способов химико-термической обработки, различающихся диффундирующими элементами, типом и составом внешней среды, химизмом процессов в ней, техникой исполнения и другими признаками. В зависимости от агрегатного состояния внешней среды, в которую помещают обрабатываемое изделие, различают химико-термическую обработку в твердой, жидкой и газовой средах. Атомы диффундирующего элемента поступают из твердого вещества в местах прямого…
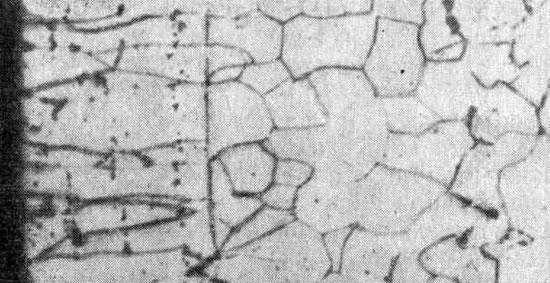
Диффузионную зону на шлифе можно выявить травлением благодаря измененному химическому составу поверхностного слоя. В однофазной зоне концентрация плавно изменяется от поверхности в глубь изделия (смотрите рисунок Распределение концентрации в однофазной зоне), и поэтому под микроскопом граница такой зоны размыта или чаще вообще не выявляется. Если диффузия сопровождается фазовыми превращениями, то строение диффузионной зоны резко отличается…
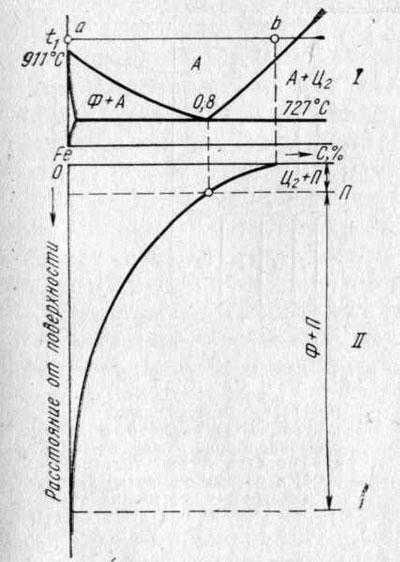
В однофазной диффузионной зоне при охлаждении изделия с температуры химико-термической обработки могут протекать фазовые превращения: полиморфное превращение твердого раствора, эвтектоидное превращение, выделение избыточной фазы и др. Допустим, что во время науглероживания железа при температуре t1 (выше 911 °С) концентрация углерода на поверхности изделия возрастает от точки а (чистое железо) до точки b, не достигая границы…
www.ktovdome.ru
Lektsia_19_Pokrytia
22
Лекция 19.
Технологические процессы формирования заданных физико-механических и эксплуатационных свойств поверхностных слоев.
Химико-термическая обработка металлов и сплавов.
Общие закономерности.
В процессе эксплуатации наиболее интенсивно подвергаются температурно-силовым воздействиям поверхностные слои деталей и инструмента, поэтому структура и свойства поверхностных слоев оказывает важное влияние на их работоспособность. С этой точки зрения представляет интерес повышение износостойкости деталей машин и инструмента методами химико-термической обработки
Химико-термической обработкой (ХТО) называют технологические процессы, приводящие к диффузионному насыщению поверхностного слоя деталей различными элементами. При этом изменяется химический состав, микроструктура и свойства поверхностного слоя материала.
Изменение химического состава поверхностных слоев происходит в результате их взаимодействия с окружающей средой (твердой, жидкой, газообразной и плазменной), в которой реализуется нагрев. В результате изменения химического состава поверхностного слоя изменяются его фазовый состав и микроструктура. Основными параметрами химико-термической обработки являются температура нагрева и время выдержки. В основе любой разновидности химико-термической обработки лежат процессы диссоциации, адсорбции, диффузии.
Диссоциация – получение насыщающего элемента в активированном атомарном состоянии в результате химических реакций, а также испарения.
Адсорбция – захват поверхностью детали атомов насыщающегося элемента. Адсорбция – всегда экзотермический процесс, приводящий к уменьшению свободной энергии.
Диффузия – перемещение адсорбированных атомов вглубь изделия.
Цель: повышение твердости, износостойкости, сопротивления усталости и контактной выносливости, а также для защиты от электрохимической и газовой коррозии.
Различают три стадии ХТО:
На первой стадии протекают химические реакции в исходной (окружающей) среде, в результате которых образуются активные диффундирующие элементы в ионизированном состоянии.
На второй стадии процесса они усваиваются насыщаемой поверхностью металла – происходит адсорбция (лат. Поглощение вещества из раствора или газа поверхностным слоем жидкости или твѐрдого тела) диффундирующих элементов, в результате чего тончайший поверхностный слой насыщается диффундирующим элементом (абсорбция – тоже поглощение, но в отличие от адсорбции происходит во всѐм объѐме поглотителя), возникает градиент концентрации – движущая сила для следующей стадии процесса.
Третья стадия – диффузионное проникновение элементов в глубь насыщаемого металла, которое сопровождается образованием твѐрдых растворов или фазовой перекристаллизацией.
Третья стадия определяет скорость процесса ХТО. Толщина диффузионного слоя при постоянной температуре и времени выдержки процесса диффузии тем больше, чем выше концентрация диффундирующего элемента на насыщаемой поверхности.
Существует множество способов ХТО, однако наибольшее распространение в промышленности получили процессы диффузионного насыщения из активных жидких и газовых сред.
Виды химико-термической обработки
Методами химико-термической обработки металлов достигается изменение свойств поверхности, обеспечивается поверхностное упрочнение металлов и сплавов (повышение поверхностной твердости, износостойкости, усталостной прочности, теплостойкости и т. д.), а также повышение стойкости металлов и сплавов против воздействия внешних агрессивных сред при нормальных и повышенных температурах (коррозионной стойкости в атмосферных условиях, стойкости к кавитационной эрозии, кислотостойкости, жаростойкости, окалиностойкости и т. д.).
Из методов химико-термической обработки наиболее распространены методы насыщения поверхности металлических изделий неметаллами.
Такими неметаллами являются углерод, азот, бор, сера. Поэтому способы химико-термической обработки металлов и сплавов получили следующие названия: науглероживание (цементация), азотирование, борирование, сульфидирование. Насыщение может проводиться одним неметаллом, комплексно двумя или тремя неметаллами.
Насыщение металлами включает следующие процессы: алитирование (насыщение алюминием), хромирование (диффузионное насыщение хромом), силицирование (насыщение поверхности кремнием).
Насыщение проводят путем нагрева обрабатываемых изделий в химически активной среде, содержащей насыщающий компонент. В результате нагрева во внешней среде образуется насыщающий элемент в атомарной форме, он адсорбируется насыщаемой поверхностью и диффундирует в глубь изделия, приводя к его упрочнению.
Диффузионное насыщение углеродом и азотом.
Углерод и азот легко усваиваются поверхностью стали, образуют с железом твѐрдые растворы внедрения и сравнительно быстро диффундируют в стали, образуя слой значительной толщины.
Цементация стали – технологический процесс диффузионного насыщения углеродом. Концентрация углерода на поверхности стальной детали доводится до 0,8 – 1%. Сердцевина детали, содержащая 0,08 – 0,25%С, остаѐтся вязкой, а поверхности, не подлежащие цементации, защищаются гальваническим омеднением. Толщина медного слоя составляет 0,02 – 0,05 мм.
Цементации обычно подвергают такие детали машин, которые должны иметь износостойкую рабочую поверхность и вязкую сердцевину: зубчатые колѐса, валы и пальцы, распределительные валики, кулачки, червяки и т.д.
Цементации обычно подвергают углеродистые и легированные стали с малым содержанием углерода (как правило, не более 0,20–0,25 %). После цементации и окончательной термической обработки обеспечивается получение поверхностной твердости 56–64 НRC при сохранении вязкой сердцевины (рис. 12.3), что определяет высокую конструктивную прочность изделий, благоприятное сочетание износостойкости поверхности с высокой сопротивляемостью динамическим разрушениям.
Рис. 12.3. Толщина цементованного слоя зубчатого колеса
Цементацию проводят в твердом карбюризаторе, в газовых средах и иногда в расплавах солей (жидкостная цементация).
Поверхностный слой после цементации еще не обладает высокой твердостью и износостойкостью. Для создания этих качеств требуется окончательная термическая обработка (закалка и отпуск).
Карбюризатор – исходная среда для цементации (науглероживание). В основном применяют два способа цементации:
В твѐрдом карбюризаторе: древесный уголь + добавки углекислого бария.
Газовый карбюризатор: разбавленный природный газ (состоящий почти полностью из метана: СН4 → 2Н2 + С), а также жидкие углеводороды (керосин, бензол и др.), каплями подаваемые в герметичное рабочее пространство печи, где они образуют активную газовую среду.
Структура цементованного слоя. Наружная часть слоя, содержащая более 0,8%С, имеет структуру заэвтектойдных сталей – перлит и вторичный цементит в виде сетки по границам зѐрен. Средняя часть слоя, имеющая эвтектойдную концентрацию, состоит из перлита. Далее по направлению к сердцевине концентрация углерода уменьшается, структура соответствует доэвтектойдной стали, причѐм количество перлита уменьшается при приближении к сердцевине.
Эффективная толщина цементованного слоя обычно составляет 0,5 – 1,8 мм и в исключительных случаях достигает 6 мм при больших контактных нагрузках на цементованную поверхность.
Надо помнить, что структура после цементации получается крупнозернистой в связи с длительной выдержкой деталей при температуре науглероживания. Длительность изотермической выдержки при цементации зависит от заданной толщины слоя и марки цементируемой стали.
Цементацией называется технологический процесс диффузионного насыщения поверхности стальных изделий углеродом. Цементация применяется для деталей, работающих в условиях трения и высоких контактных давлений (например, зубчатые колеса, валы, пальцы, распределительные валики, кулачки, червяки и т. д.). Обработке подвергаются детали с припуском на шлифование из низкоуглеродистых сталей, содержащих 0,1...0,25 % углерода, и низколегированных сталей типа 20Х, 15ХР, 20ХН, 18ХГТ, 12ХНЗ, 18Х2Н4 и др. Глубина цементованного слоя колеблется от 0,5 до 4 мм. После цементации изделия подвергаются закалке и низкому отпуску. В результате такой обработки твердость поверхностного слоя достигает 58...62 НRСэ при сохранении вязкой сердцевины детали. В основном применяют два вида цементации: твердую и газовую.
При твердой цементации карбюризатором, т. е. науглероживающим веществом, служит смесь древесного угля и углекислых солей. Углекислые соли добавляют к древесному углю в количестве 10...30 % в качестве катализаторов. Детали укладывают в металлические ящики и пересыпают твердым карбюризатором так, чтобы они не соприкасались друг с другом, со стенками и дном ящика. Сверху ящик закрывают крышкой и щели замазывают огнеупорной глиной. Ящики устанавливают в печь и нагревают до температуры 910...950°С. При такой температуре уголь взаимодействует с кислородом воздуха, сохранившегося в порах засыпки.
Цементация в твердом карбюризаторе — длительная операция, скорость которой составляет 0,10...0,12 мм/ч при температуре 930°С, а длительность зависит от толщины требуемого цементованного слоя. Для получения цементованного слоя глубиной 1 мм при температуре 930°С длительность процесса составляет около 10 ч.
После окончания цементации ящики вынимают из печи, охлаждают на воздухе, а затем распаковывают и вынимают детали.
Цементация в твердом карбюризаторе— малопроизводительный процесс, который применяется только при мелкосерийном и индивидуальном способе производства.
Газовая цементация наиболее широко применяется в массовом производстве. Основной реакцией, обеспечивающей выделение свободного атомарного углерода, является диссоциация метана и оксида углерода.
В качестве карбюризатора используют разбавленный Природный газ (метан), контролируемые атмосферы, получаемые в специальных генераторах, а также пары жидких углеводородов.
В зависимости от состава газовой смеси и содержания углерода в стали атмосфера в рабочем пространстве печи может иметь различную науглероживающую способность. Скорость газовой цементации составляет 0,12...0,15 мм/ч при температуре 930...950°С, а толщина диффузионного слоя достигает 1,7 мм.
Газовая цементация осуществляется в стационарных или периодических конвейерных печах. При газовой цементации можно получить заданную концентрацию углерода в слое, сократить длительность процесса (отпадает необходимость прогрева ящиков, наполненных плохо проводящим тепло карбюризатором), обеспечить возможность полной механизации и автоматизации процесса, проводить закалку непосредственно от температуры цементации.
Для получения необходимых свойств детали после цементации обязательно подвергают термической обработке. Обычно после цементации структура стали крупнозернистая, что связано с выдержкой при высокой температуре. Для таких деталей проводятся двойная закалка и отпуск. Первая закалка (или нормализация) проводится с температур 880...900 °С с целью измельчения структуры сердцевины и устранения цементитной сетки в поверхностном слое. Вторую закалку проводят с нагревом до 760...780 °С для устранения перегрева цементованного слоя и придания ему высокой твердости.
Для наследственно мелкозернистых сталей применяют закалку с температур выше Ac1. После газовой цементации такие изделия часто закаливают без повторного нагрева, непосредственно из печи с температурой 840...860°C после подстуживания с целью уменьшения коробления обрабатываемых изделий.
После закалки цементованные детали во всех случаях подвергают низкому отпуску при температуре 160... 180°С для уменьшения закалочных напряжений и повышения сопротивления хрупкому разрушению.
Термическая обработка после цементации. В зависимости от условий работы, а также от выбранной для изготовления детали стали и получения заданного комплекса свойств после цементации режим упрочняющей термической обработки может быть различным:
Для тяжелонагруженных трущихся деталей машин, испытывающих в условиях работы динамическое нагружение, в результате термической обработки нужно получить не только высокую поверхностную твѐрдость, но и высокую прочность (например, для зубчатых колес – высокая прочность на изгиб) и высокую ударную вязкость. Для обеспечения указанных свойств требуется получить мелкое зерно как на поверхности детали, так и в сердцевине. В таких ответственных случаях цементованные детали подвергают сложной термической обработке, состоящей из двух последовательно проводимых закалок и низкого отпуска.
При первой закалке деталь нагревают до температуры на 30-50оС выше температуры А3 цементируемой стали. Это обеспечит перекристаллизацию сердцевины детали с образованием мелкого аустенитного зерна, что в свою очередь обеспечит мелкозернистость продуктов распада.
При второй закалке деталь нагревают до температуры на 30-50оС выше температуры А1. в процессе нагрева мартенсит, полученный в результате первой закалки, отпускается, что сопровождается образованием глобулярных карбидов, которые в определѐнном количестве сохраняются после неполной закалки в поверхностной заэвтектойдной части слоя, увеличивая его твѐрдость. Вторая закалка обеспечивает также мелкое зерно в науглероженном слое.
Окончательной операцией термической обработки является низкий отпуск при 160-200оС, уменьшающий остаточные напряжения и не снижающий твѐрдости стали.
Структура после двойной закалки и низкого отпуска – отпущенный мартенсит с включениями глобулярных карбидов. Структура сердцевины детали зависит от легированности стали. В углеродистых сталях в сердцевине получается сорбитная структура. В легированных сталях, в зависимости от количества легирующих элементов, может получиться бейнит или низкоуглеродистый мартенсит. Во всех случаях из-за низкого содержания углерода будет обеспечена достаточно высокая ударная вязкость.
Детали менее ответственного назначения после цементации подвергают более простой термической обработке, состоящей из одной закалки и низкого отпуска.
Если для цементации выбирают природно мелкозернистые стали и содержание углерода на поверхности близко к эвтектойдному, то и при одной закалке получают удовлетворительные свойства, как в сердцевине, так и в цементованном слое. Однократная закалка широко используется на заводах массового производства, где цементацию ведут в газовом карбюризаторе.
Выгодно и удобно закалку проводить с температур цементации.
Цементованные детали подвергают шлифованию.
Азотирование стали – процесс диффузионного насыщения азотом поверхностной зоны деталей.
Азотированием называется технологический процесс диффузионного насыщения поверхности стальных изделий азотом, в результате которого повышается твердость, износостойкость и предел выносливости ответственных деталей машин (например, коленчатых валов, гильз цилиндров, червяков, валов и др.). Азотированию подвергают детали из среднеуглеродистых сталей, которые прошли чистовую обработку, закалку и высокий отпуск. После азотирования детали шлифуют или полируют.
Азотирование – поверхностное насыщение стали азотом применяется, как и цементация, преимущественно для повышения поверхностной твердости, износостойкости деталей машин и механизмов.
Азотирование ведут путем нагрева заготовок в газовой среде аммиака, который под воздействием температур процесса разлагается и таким образом обеспечивает насыщение поверхности заготовок азотом.
Кроме того, азотирование обеспечивает повышение коррозионной стойкости материала, а также теплостойкость упрочненного поверхностного слоя. Характер упрочнения в результате азотирования принципиально иной по сравнению с цементацией. Высокая твердость и износостойкость слоя достигается при образовании сплошной зоны нитридов легирующих элементов, содержащихся в стали на внешней поверхности изделия.
Для повышения коррозионной стойкости азотированию подвергают углеродистые стали. Для повышения поверхностной твердости и износостойкости используют комплексно-легированные стали, содержащие хром, молибден, алюминий и другие компоненты, например 30ХМЮА, 38ХЮА, 34ХН1М и др. Азотированию подвергают наиболее ответственные детали: гильзы цилиндров двигателей внутреннего сгорания, шестерни, детали топливной аппаратуры. Азотирование также проводят для нержавеющих сталей ферритного или аустенитного класса: 30Х1З, 40Х13, 40Х14Н14В2М и др.
Изделия после азотирования без дополнительной термической и механической обработки сразу подаются на сборку. Размеры изделий при азотировании не изменяются, поэтому азотированию подвергаются готовые детали без припусков на окончательную механическую обработку. В связи с этим свойства, которыми должна обладать сердцевина изделия, должны быть сформированы до азотирования. Поэтому заготовки для изготовления азотируемых деталей подвергают предварительной термической обработке (улучшению), включающей закалку и высокотемпературный отпуск.
Цель: повысить износостойкость и предел выносливости деталей машин (коленчатые валы, гильзы цилиндров, червяки, валики и др.).
Детали, подвергаемые азотированию, укладываются в герметичные камеры, куда с определенной скоростью подается аммиак, который при нагреве разлагается с образованием атомарного азота.
Азотирование— длительная операция. Для получения слоя толщиной 0,5 мм требуется порядка 60 ч при температуре азотирования 500...520°С. С целью ускорения процесса азотирование проводят по двухступенчатому режиму: при 500...520 °С в течение 12...15 ч и при 540...600 °С в течение 20...25 ч. Вторая стадия ускоряет диффузионные процессы и общая длительность процесса сокращается в 1,5...2 раза.
До азотирования детали подвергают закалке и высокому отпуску (улучшению) и чистовой обработке. После азотирования детали шлифуют или полируют.
Обычно азотирование проводят при температуре 500-600оС в муфелях или контейнерах, через которые пропускается диссоциирующий (лат. диссоциация – распадение молекул на несколько более простых частиц) аммиак.
Вероятно, что на стальной поверхности происходит реакция диссоциации аммиака с выделением ионов азота, которые адсорбируются поверхностью детали, а затем диффундируют в глубь.
2NН3 → N2 + 3Н2 при нагреве
Азотированная сталь, имеющая на поверхности слой έ-фазы, коррозионностойка в воде и в атмосферных условиях. Высокие твѐрдость и износостойкость получаются после азотирования комплексно-легированных сталей. Например: сталь 38Х2МЮА – твердость азотированного слоя достигает 1200НV. Молибден также устраняет отпускную хрупкость, которая может возникнуть при медленном охлаждении от температуры азотирования.
Процесс азотирования – весьма длительная операция. Требуется от 40 до 55 час. Для получения диффузионной зоны толщиной около 0,5 мм.
Надо помнить: по сравнению с цементованными азотированные слои легированных сталей имеют более высокие твѐрдость и износостойкость. Однако азотирование используют реже, чем цементацию, из-за большой длительности процесса и меньшей толщины упрочненного слоя, что ограничивает величину контактных нагрузок на поверхность детали.
Методы совместного насыщения азотом и углеродом
Совместное насыщение поверхности деталей азотом и углеродом предусматривает возможность реализации принципиально различающихся способов в зависимости от того, какой из этих элементов является основным, а какой − дополнительным. В соответствии с этим различают цианирование и нитроцементацию. Цианирование ведут в жидких средах – расплавах солей, а нитроцементацию − в газовой среде.
Цианирование и нитроцементация обеспечивают получение слоя, аналогичного, получаемому при цементации. Азот увеличивает прочностные свойства слоя, его износостойкость. Основное применение низкотемпературного цианирования – дополнительное упрочнение режущего и штампового инструмента, изготовленного из быстрорежущих и других теплостойких сталей. Инструменты после окончательной термической обработки на максимальную твердость и после шлифовки и заточки насыщают углеродом и азотом, при этом формируется тонкий (0,04–0,09 мм) карбонитридный слой высокой твердости и износостойкости, увеличивающий режущую стойкость инструмента в 1,5–2,0 раза. Термообработки после насыщения, как и после азотирования, не требуется.
Цианирование
Цианирование сталей заключается в поверхностном насыщении стальных изделий одновременно углеродом и азотом из расплавленных цианистых солей NaCN с добавками солей NaCl, BaCl и др. При нагреве в ванне, образующиеся атомарный азот и углерод диффундируют в сталь. Детали нагревают в расплавленных солях до температуры 820. ..860°С и выдерживают 0,5...1,5 ч.
При этом толщина диффузионного слоя достигает 0,16...0,35 мм и в нем содержится примерно 0,7% углерода и 0,1% азота.
После цианирования детали закаливают непосредственно из цианистой ванны и подвергают низкому отпуску при 180...200 °С. Твердость цианированного слоя после термической обработки 58...62 HRCЭ.
Цианированный слой по сравнению с цементованным обладает более высокой износостойкостью. Его структура состоит из тонкого поверхностного слоя карбонитридов Fe2(C,N), Fe3(C,N), после чего следует слой азотистого мартенсита.
Цианированию подвергают коленчатые валы, шестерни, режущий инструмент, штампы, пресс-формы и др. Основным недостатком цианирования является его ядовитость. Соли NaCl и BaCl добавляют для повышения температуры плавления ванны, что несколько уменьшает испарение дорогих и ядовитых цианистых солей при рабочих температурах. Этих недостатков лишен процесс газового цианирования, получивший название нитроцементации.
Одновременное насыщение поверхности стали углеродом и азотом (нитроцементация).
Исследования показали, что в ряде случаев совместное диффузионное насыщение стали азотом и углеродом позволяет получить определенные преимущества. Например: азот способствует диффузии углерода, поэтому можно понизить температуру диффузионного насыщения до 850оС и получить такое же науглероживание, как при цементации. В этом случае уменьшится рост зерна аустенита и последующую закалку можно проводить сразу же после некоторого подстуживания.
Нитроцементованный слой хорошо сопротивляется износу и коррозии. Нитроцементацию широко применяют на автомобильных и тракторных заводах для упрочнения поверхностей нешлифуемых деталей.
Существенный недостаток цианирования – ядовитость цианистых солей (ионов СN-), что требует принятия специальных мер по охране труда и окружающей среды.
Для информации: разработаны низкотемпературные процессы насыщения азотом и углеродом из расплавов нетоксичных солей – цианатов и карбонатов. Такие процессы известны под названием «Карбонитрация» (Россия), «Тенифер» (Германия) и «Мелонайт» (США).
Специальными мерами (продувка ванны воздухом, охлаждение деталей в расплаве едкого натра и нитрита натрия) добиваются ликвидации образования ионов [CN-].
Для повышения стойкости быстрорежущего инструмента после закалки и высокого отпуска проводят карбонитрацию.
В зависимости от вида инструмента режим процесса устанавливают в следующих пределах: температура расплава 530-570оС, время выдержки 5-30 мин.
При нитроцементации совмещают процессы газовой цементации и азотирования и используют смесь СО, СО2, Н2, СН4, Nh4. Температура и состав атмосферы контролируются и зависят от марки стали, требуемой структуры и глубины насыщаемого слоя детали.
Высокотемпературная нитроцементация осуществляется для деталей из конструкционных сталей при температурах 830...950°С и из легированных —при 850...870°С. Процесс длится 4...10 ч, так как диффузия углерода существенно ускоряется в присутствии азота.
Низкотемпературная нитроцементация проводится для инструмента из быстрорежущей стали при температурах 550...570°С. Процесс длится 1,5...3 ч, толщина нитроцементованного слоя 0,02...0,04 мм, а его твердость 900... 1200 НV. Износостойкость инструмента повышается в 1,5...2 раза. Перед низкотемпературной нитроцементацией детали подвергают закалке и высокому отпуску.
После нитроцементации осуществляют закалку с 800...825°С (после подстуживания) и низкий отпуск при 160... 180°С. Твердость достигает 56...62 HRCЭ, а толщина нитроцементованного слоя составляет 0,2...0,8 мм.
Преимуществами нитроцементации по сравнению с цианированием являются безопасность процесса (отсутствуют ядовитые вещества), его низкая стоимость и возможность более точного регулирования толщины и состава поверхностного слоя. Преимущества по сравнению с цементацией заключаются в меньшей длительности и стоимости процесса, более простой термической обработке, меньшей деформации и более высокой износостойкости и усталостной прочности.
Диффузионное насыщение сплавов металлами и неметаллами.
Насыщение металлами
Металлами можно насыщать стали и чугуны, алюминиевые и медные сплавы, а также многие другие металлические или керамические материалы.
studfiles.net
Цементация металла – виды цементации стали и нюансы процесса
Цементация, осуществляемая в различных средах и исключительно под воздействием высоких температур, является очень распространенным методом химико-термической обработки металла, успешно применяемым уже не один десяток лет.
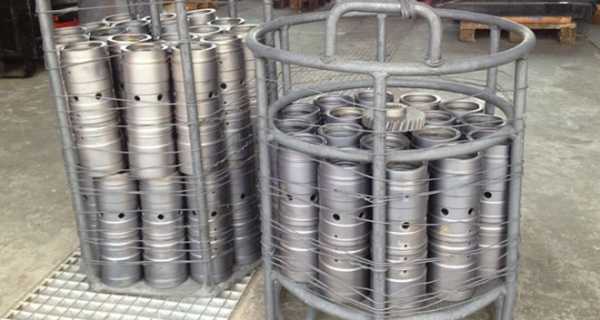
Подготовка деталей для цементации
Сущность процесса цементации
Смысл любых методов химико-термической обработки металлов, к числу которых относится и цементация стали, заключается в том, что изделие нагревают до высокой температуры в специальной среде (жидкой, твердой или газообразной). Такое воздействие приводит к тому, что меняется химический состав металла – поверхность обрабатываемого изделия насыщается углеродом, в итоге становится более твердой и износостойкой. Что важно, сердцевина обработанных деталей остается вязкой.
Добиться желаемого эффекта после такого воздействия на металл можно лишь в том случае, если обработке подвергают низкоуглеродистые стали, в составе которых углерода содержится не более 0,2%. Для того чтобы выполнить цементацию, изделие нагревают до температуры 850–950 градусов Цельсия, а состав среды подбирают таким образом, чтобы она при нагреве выделяла активный углерод.
Если цементацию стали проводить квалифицированно, можно не только изменить химический состав металлического изделия, но также преобразовать его микроструктуру и даже фазовый состав. В результате удается значительно упрочнить поверхностный слой детали, придать ему характеристики, сходные со свойствами закаленной стали. Для того чтобы добиться таких результатов, необходимо правильно подобрать параметры химико-термической обработки металла – температуру нагрева и время выдержки обрабатываемого изделия в специальной среде.
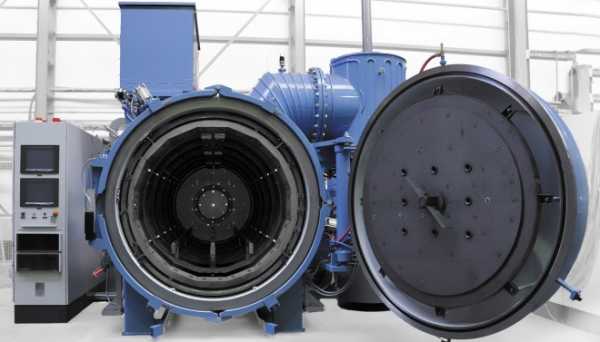
Оборудование для вакуумной цементации стали
Данная технологическая операция является достаточно продолжительной по времени, так как процесс насыщения поверхностного слоя стали углеродом проходит очень медленно (0,1 мм за 60 минут). Учитывая тот факт, что упрочненный поверхностный слой для большинства изделий должен составлять не менее 0,8 мм, можно рассчитать, что на выполнение цементации металла необходимо будет затратить не менее 8 часов. Основными типами сред для выполнения цементации металла (или, как их правильно называют, карбюризаторами) являются:
- газообразные среды;
- растворы электролитов;
- пастообразные среды;
- кипящий слой;
- твердые среды.
Наиболее распространенными являются газообразные и твердые карбюризаторы.
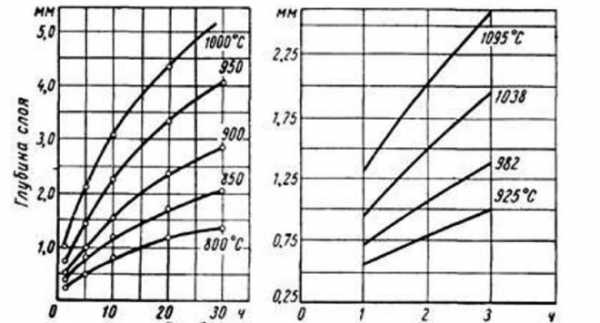
Зависимость толщины цементованного слоя от времени и температуры обработки
Проведение цементации стали в твердой среде
Чаще всего для выполнения цементации металла в твердой среде используется смесь, состоящая из углекислого натрия, бария или кальция и березового или дубового древесного угля (70–90%). Перед этим все компоненты такой смеси измельчаются до фракции 3–10 мм и просеиваются, что необходимо для удаления слишком мелких частиц и пыли.
После того, как компоненты смеси для химико-термической обработки металла подготовлены, их можно смешать несколькими способами.
- Компоненты смеси (соль и уголь) тщательно перемешиваются в сухом состоянии. Если пренебречь этим требованием, то после окончания процесса цементации на поверхности изделия могут образоваться пятна.
- Соль растворяют в воде и полученным раствором поливают древесный уголь, после чего его просушивают до достижения влажности не более 7%.
Следует отметить, что второй способ предпочтительнее, так как позволяет получить смесь с более равномерным составом.
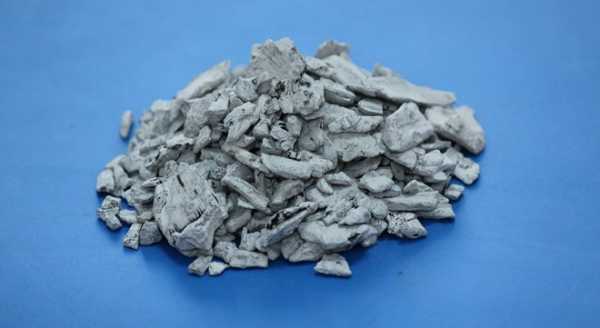
Древесноугольный карбюризатор
Как в производственных, так и в домашних условиях цементация изделий из стали выполняется в ящиках, в которые засыпан карбюризатор. Чтобы улучшить качество поверхностного слоя обрабатываемого металла, а также сократить время, идущее на прогрев ящиков, лучше всего изготавливать их максимально приближенными к размерам и формам деталей.
Оптимальные условия для протекания цементации стали можно создать, исключив утечку газов, образующихся в карбюризаторе в процессе нагрева. Для этого ящики, у которых должны быть плотно закрывающиеся крышки, тщательно обмазывают огнеупорной глиной перед помещением в печь.Естественно, использовать специально изготовленные ящики целесообразно лишь в промышленных условиях. Для цементации металла в домашних условиях применяют ящики стандартных размеров и формы (квадратные, прямоугольные, круглые), подбирая их в зависимости от количества обрабатываемых деталей и внутренних размеров печи.
Оптимальным материалом для таких ящиков является жаростойкая сталь, но может быть использована и тара из малоуглеродистых сплавов. Технологический процесс цементации изделий из металла выглядит следующим образом.
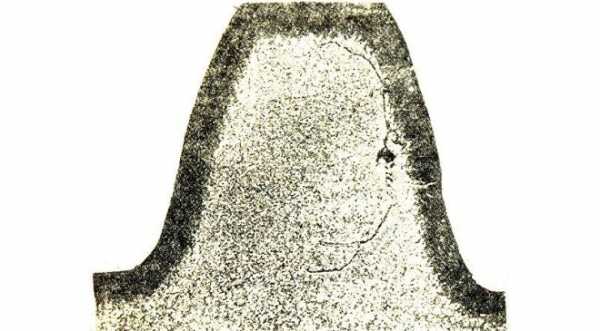
Наглядное изображение изменения структуры после цементации
- Подготовленные для обработки детали укладывают в ящики, пересыпая слоями карбюризатора.
- Наполненные ящики, обмазанные огнеупорной глиной, помещают в предварительно прогретую печь.
- Выполняют так называемый сквозной прогрев ящиков с деталями, при котором они нагреваются до температуры 700–800 градусов Цельсия. О том, что ящики хорошо прогрелись, судят по цвету подовой плиты: на ней не должно быть темных пятен в местах соприкосновения с тарой.
- Температуру в печи поднимают до 900–950 градусов Цельсия. Именно при таких значениях проводят цементацию стали.
Высокая температура и специальная среда, в которой находится металл, способствуют тому, что происходит диффузия атомов активного углерода в кристаллическую решетку стали. Следует отметить, что выполнение цементации стали возможно в домашних условиях, но часто не позволяет добиться желаемого эффекта. Объясняется это тем, что для процесса цементации необходима длительная выдержка детали при высокой температуре. Как правило, это трудно обеспечить в домашних условиях.
Цементация деталей в газовой среде
Авторами данной технологии являются С. Ильинский, Н. Минкевич и В. Просвирин, которые под руководством П. Аносова впервые использовали ее на комбинате в г. Златоусте. Суть данной технологии заключается в том, что обрабатываемые детали из металла нагреваются в среде углеродосодержащих газов, которые могут быть искусственного или природного происхождения. Чаще всего используется газ, который образуется при разложении продуктов нефтепереработки. Такой газ получают следующим способом:
- нагревают стальную емкость и подают в нее керосин, который при испарении разлагается на смесь газов;
- состав некоторой части (60%) полученного газа модифицируют (крекирование).
Полученная смесь и используется для выполнения химико-термической обработки стали.
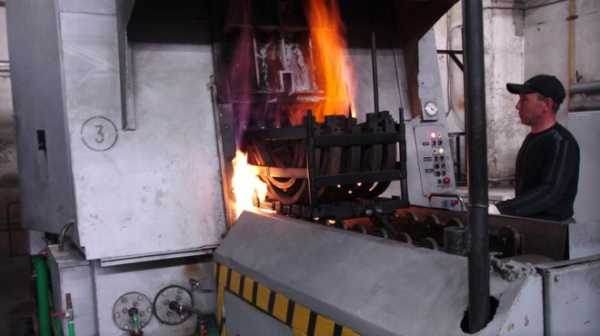
Процесс цементации стали
Если цементацию стали провести с применением только пиролизного газа, без добавления крекированного, то глубина науглероженного слоя будет недостаточной. Кроме того, в таком случае на поверхности обрабатываемой детали осядет большой слой сажи, на удаление которого может уйти много времени и сил.
Печи, которые используются для выполнения газовой цементации металла, должны герметично закрываться. На современных производственных предприятиях применяют два основных типа таких печей: методические и стационарные. Сам процесс цементации в газовой среде выглядит следующим образом. Обрабатываемые детали помещают в печь, температуру в которой доводят до 950 градусов Цельсия. В нагретую печь подают газ и выдерживают в нем детали определенное время.
По сравнению с цементацией стали с использованием твердого карбюризатора, данная технология имеет ряд весомых преимуществ:
- обеспечение лучших условий для обслуживающего персонала;
- высокая скорость достижения требуемого эффекта за счет того, что детали в газовой среде могут выдерживаться меньшее количество времени (к тому же не требуется время для приготовления твердого карбюризатора).
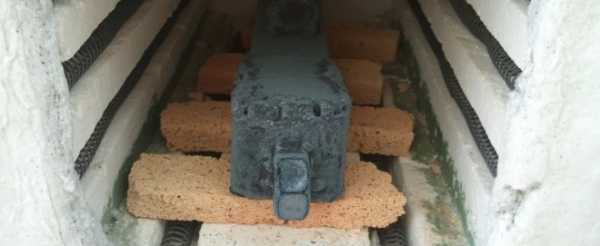
Цементация стали в домашних условиях
В каких еще средах может проводиться цементация стали
Отдельные сорта углеродистых, низкоуглеродистых и легированных сталей, в частности 15, 20, 20ХГНР, 20Х, 20Х2Н4А, 18Х2Н4ВА, 20Г, 12ХН3А и др., могут проходить цементацию в других средах.
Электролитический растворВ такой среде можно науглероживать только детали, отличающиеся небольшими размерами. Основывается данный метод на анодном эффекте, благодаря которому и происходит насыщение поверхности металла углеродом, содержащимся в растворе электролита. Для того чтобы раствор содержал достаточное количество активного углерода, в него добавляют глицерин, ацетон, сахарозу и другие вещества. Перед тем, как поместить деталь из стали в раствор, его нагревают до температуры 450–1050 градусов Цельсия (в зависимости от обрабатываемого металла и размеров детали). Для разогрева раствора используют электрический ток с напряжением 150–300 В.
Кипящий слойЦементацию стали по данной технологии проводят в среде раскаленного газового потока, формируемого при прохождении метана и эндогаза через слой нагретого мелкоизмельченного (0,05–0,2 мм) корунда.
Пастообразные составыДля науглероживания поверхности металла по данной технологии используются специальные пасты, состоящие из желтой соли, древесной пыли и сажи. Перед обработкой деталь обмазывают такой пастой и просушивают, а только затем нагревают до температуры 910–1050 градусов Цельсия при помощи токов высокой частоты.
По какой бы технологии ни была выполнена цементация стали, после ее окончания рекомендуется провести отпуск металла.Оценка статьи:
Загрузка...Поделиться с друзьями:
met-all.org
Насыщение - поверхность - изделие
Насыщение - поверхность - изделие
Cтраница 1
Насыщение поверхности изделий одновременно углеродом и азотом в расплавленной цианистой соли называют цианированием, a s газовой среде - нитроцементацчей. Соотношение углерода и азота в диффузионной зоне можно регулировать, изменяя состав среды и температуру процесса. [1]
Алитирование - насыщение поверхности изделий алюминием. Осуществляется для деталей из стали с 0 1 - 0 2 % С для повышения окалиностойкости. [2]
Термохромирование - процесс насыщения поверхности изделий из стали или чугуна хромом. Его проводят при температуре 1000 - 1500 С в смеси порошкообразного хрома или феррохрома, каолина и хлористого аммония. За это время получают слой толщиной 50 - 200 мкм. [4]
Силицирование - процесс насыщения поверхности изделий из стали или чугуна кремнием. В зависимости от температуры и времени силицирования глубина проникновения выделяющегося кремния ( 4Fe 3SiCl4 - 3Si 4FeCh) различна и составляет от 0 8 до 1 0 мм. [5]
Силицирование - процесс насыщения поверхности изделий из стали или чугуна кремнием. В зависимости от температуры и времени силицирования глубина проникновения выделяющегося кремния ( 4Fe 3SiCl4 3Si 4РеС1з) различна и составляет от 0 8 до 1 0 мм. [6]
Сущностью процесса цементации является насыщение поверхности изделий из малоуглеродистой стали углеродом до предела, обеспечивающего высокую твердость после закалки и хорошую сопротивляемость истиранию. Цементация ( например твердым карбюризатором) осуществляется следующим образом. Изделия из мягкой стали с содержанием углерода в пределах 0 15 - 0 25 % ( легированные стали содержат, кроме того, специальные элементы: хром, никель, марганец, молибден и др.) помещаются в специальные железные ящики, засыпаются веществом, содержащим углерод определенного состава, называемым карбюризатором, и герметически закрываются. Ящики с деталями и карбюризатором загружаются в печь, нагреваются до температуры 900 - 940, выдерживаются при этой температуре определенное время, затем, как правило, остывают на спокойном воздухе. Во время выдержки при высокой температуре происходит насыщение углеродом поверхностных слоев стали на определенную глубину ( в зависимости от времени выдержки), обычно на 1 - 2 мм. [7]
Диффузионная металлизация представляет собой процесс насыщения поверхности изделий из стали и других материалов алюминием, бором, хромом, титаном, кремнием и др. В результате диффузионной металлизации поверхность изделий приобретает высокую устойчивость против газовой коррозии, повышенную твердость и износоустойчивость. [8]
Диффузионная металлизация сталей заключается в насыщении поверхности изделий алюминием, кремнием, хромом, бором. Алитирование ( насыщение алюминием) осуществляется в твердой засыпке, содержащей порошок алюминия или ферроалюминия, или в жидком алюминии. Меньшее время необходимо при алитировании в расплаве. Алитированный слой, содержащий около 30 % А1, достигает толщины до 1 мм. Присутствие углерода в стали замедляет алитирование. [9]
Сущность диффузионного хромирования заключается в насыщении поверхности изделий хромом, в результате чего в поверхностных слоях получаются хромистые соединения с железом и другими элементами, входящими в состав стали. Эти соединения делают металл на поверхности легированным, очень твердым и способным сопротивляться износу и коррозии. Процесс хромирования может быть твердым и газообразным. [10]
В отличие от электрохимической, при электроэрозионной обработке структура поверхностного слоя обрабатываемого изделия меняется, так как она подвергается действию высокой температуры; кроме того, не весь расплавленный металл удаляется из межэлектродного пространства, часть его остается и застывает по окончании импульса в образовавшейся лунке. Одновременно происходит насыщение поверхности изделия продуктами испарения рабочей жидкости и электрода-инструмента, например углеродом. [11]
Такое покрытие образуется при диффузии защитного металла в защищаемый металл. Этот способ применяется для насыщения поверхности изделий цинком, алюминием, хромом. [12]
Избежать этих недостатков можно при упруго-пластическом знакопеременном циклическом деформировании изделий во время насыщения. Такое деформирование, не изменяя заметно форму и размеры обрабатываемого изделия, обусловливает значительно большую суммарную сдвиговую деформацию, чем какой-либо др. вид деформирования, дает возможность, несмотря на релаксационные процессы ( см. Релаксация), поддерживать в изделии достаточно высокую плотность несовершенств кристаллического строения, не вызывая ползучести. В одной из установок ( рис.) для насыщения поверхности изделий азотом в условиях упруго-пластического циклического деформирования реакционная камера, куда поступает аммиак, одновременно является муфелем электр. По достижении заданной т-ры нагрева к образцу прикладывают циклическую крутильную знакопеременную нагрузку. [13]
Страницы: 1
www.ngpedia.ru
Цементация | Учебные материалы
Химико-термической обработкой (ХТО) называют поверхностное насыщение стали соответствующими элементами путем их диффузии в атомарном состоянии из внешней среды при высоких температурах.
ХТО следует рассматривать как физико-химический процесс взаимодействия металла с газовой средой. Он включает три элементарные стадии:
- образование атомарного диффундирующего элемента;
- контактирование его с поверхностью стального изделия и проникновение в кристаллическую решетку;
- диффузия атомов насыщающего элемента в глубь металла.
Глубина проникновения зависит от температуры и продолжительности процессов. Диффузионные процессы протекают легче при образовании твердых растворов внедрения (углерод, азот) по сравнению с твердыми растворами замещения. В результате в поверхностном слое могу образовываться твердые растворы переменной концентрации или химические соединения.
Целью ХТО является повышение прочности, твердости, коррозионной стойкости и износостойкости поверхностного слоя. Основными видами ХТО являются цементация, азотирование, нитроцементация, цианирование, борирование.
Цементацией называется процесс насыщения поверхностного слоя стали углеродом.
Цементацию проводят при температурах выше точки Ас3 (930… 950 0С), когда аустенит может растворять углерод в большом количестве. Окончательные свойства достигаются в результате закалки и низкого отпуска, выполняемых после цементации.
Для цементации обычно используют низкоуглеродистые стали (0,10… 0,23 % С), которые практически не упрочняются закалкой. Толщина цементованного слоя обычно составляет 0,5…1,8 мм. Концентрация углерода в поверхностном слое должна составлять 0,8…1,2 %; твердость слоя 50…62 НRС.
Цементацию можно проводить в твердом и газовом карбюризаторе.
Цементация твердым карбюризатором
Этот процесс проводится в древесном угле или каменноугольном полукоксе и торфяном коксе, к которым добавляют активаторы. Широко применяемый карбюризатор состоит из древесного угля, 20…35 % ВаСО3 и 3,5 % СаСО3, который добавляют для предотвращения спекания частиц карбюризатора.
Детали, подлежащие цементации, после предварительной очистки укладывают в ящики. На дно ящика насыпают и утрамбовывают слой карбюризатора толщиной 20…30 мм, на который укладывают первый ряд деталей. Их засыпают слоем карбюризатора толщиной 10…15 мм, а на него укладывают следующий слой деталей и т.д. Последний ряд деталей засыпают слоем карбюризатора толщиной 35…40 мм. Ящик закрывают крышкой, кромки которой обмазывают огнеупорной глиной или смесью глины и речного песка. После этого ящик помещают в печь. Нагрев до температуры цементации составляет от 7 до 9 мин на каждый сантиметр минимального размера ящика. Время выдержки может достигать 14 часов. После цементации ящики охлаждают на воздухе до 400…500 0С и затем открывают.
Цементация стали осуществляется атомарным углеродом. Кислород, который находится в ящике взаимодействует с углеродом карбюризатора, образуя оксид углерода СО (из-за недостатка кислорода), который в присутствии железа диссоциирует:
2СО -> СО2 + С.
Этот атомарный углерод диффундирует в аустенит. Добавление углекислых солей активизирует карбюризатор, обогащая атмосферу оксидом углерода:
ВаСО3 + С -> ВаО + 2СО.
Газовая цементация
Процесс осуществляется нагревом изделия в среде газов, содержащих углерод. В качестве карбюризатора используют природный газ, состоящий почти полностью из метана (СН4) и пропанбутановых смесей, а также жидких углеводородов (керосина, бензола), из которых пиролизом получает СО. Основными реакциями получения атомарного углерода являются диссоциация оксида углерода или метана:
2СО -> СО2 + С;
СН4 -> 2Н2 + С.
В печах непрерывного действия для цементации применяют эндотермическую атмосферу, состоящую из 95…97 % эндогаза (20 % СО, 40 % Н2 и 40 % N2) и 3…5 % природного газа.
Газовая цементация имеет ряд преимуществ по сравнению с цементацией в твердом карбюризаторе: можно получить заданную концентрацию углерода в слое; сокращается длительность процесса; обеспечивается возможность полной механизации и автоматизации процесса; значительно упрощается последующая термическая обработка деталей, так как закалку можно проводить непосредственно из цементационной печи.
dprm.ru
Насыщение - поверхность - сталь
Насыщение - поверхность - сталь
Cтраница 4
Диффузионное хромирование представляет собой процесс насыщения поверхности стали или чугуна хромом. При этом достигается высокая поверхностная твердость и сопротивляемость износу, а также повышение коррозионной стойкости и жаростойкости стальных и чугунных деталей. [46]
Силицированный слой образуется в результате насыщения поверхности стали и чугуна кремнием. [47]
Как называется обработка, состоящая в насыщении поверхности стали азотом и углеродом в газовой среде. [48]
Как называется обработка, состоящая в насыщении поверхности стали углеродом. [49]
Диффузионным хромированием ( термохромированием) называется процесс насыщения поверхности стали хромом. [50]
Описываемый способ имеет большое производственное значение и используется при насыщении поверхности стали углеродом и азотом. [51]
Диффузионное насыщение металлов - химико-термический процесс, состоящий в насыщении поверхности стали металлами ( Al, Cr, W, V, Nb, Zn и др.) и их комплексами с целью изменения ее состава и структуры. [52]
В отсутствие хлоридов в газовой фазе процесс идет очень медленно и насыщение поверхности стали осуществляется в основном только за счет контактной диффузии из порошка ферросплава. [53]
Повышение температуры процесса до 1100 С сокращает время, необходимое для насыщения поверхности стали кремнием, но при этом увеличивается пористость слоя. Аналогичное влияние оказывает предварительный подогрев др-40 С четы-реххлористого кремния, поступающего в реактор. [54]
В отсутствие хлоридов в газовой фазе процесс идет очень медленно и насыщение поверхности стали осуществляется в основном только за счет контактной диффузии из порошка ферросплава. [55]
Страницы: 1 2 3 4
www.ngpedia.ru
Насыщение - поверхностный слой - Большая Энциклопедия Нефти и Газа, статья, страница 4
Насыщение - поверхностный слой
Cтраница 4
Нитроцементация - процесс насыщения поверхностного слоя углеродом и азотом, по сравнению с газовой цементацией он имеет преимущество в скорости насыщения. Поверхностный слой обладает более высокой износостойкостью, чем при газовой цементации, благодаря наличию азота и мелкозернистой структуре с карбонитридной зоной. [46]
Борирование - процесс насыщения поверхностного слоя бором, применяется преимущественно для среднеуглеродистых нелегированных сталей. Борирование проводят в твердой, жидкой или газообразной среде. Поверхностная твердость стали после борирования и закалки достигает 1400 - 1500 HV, что обеспечивает высокую износостойкость трущихся деталей. Глубина борированного слоя составляет 0 12 - 0 85 мм. [47]
Сульфидирование - процесс насыщения поверхностного слоя сульфидами, проводят обычно в солевых ваннах. Такая обработка существенно повышает противозадирные свойства и значительно снижает коэффициент трения. Износостойкость при этом повышается в несколько раз. Аналогичный эффект достигается при сульфоцианиро-вании - одновременном насыщении поверхностей нитридами и сульфидами. [48]
Борирование - процесс насыщения поверхностного слоя бором, применяется преимущественно для среднеуглеродистых нелегированных сталей. Борирование проводят в твердой, жидкой или газообразной среде. Поверхностная твердость стали после борирования и закалки достигает 1400 - 1500 HV, что обеспечивает высокую износостойкость трущихся деталей. Глубина борированного слоя составляет 0 12 - 0 85 мм. [49]
Сульфидирование - процесс насыщения поверхностного слоя сульфидами, проводят обычно в солевых ваннах. Такая обработка существенно повышает противозадирные свойства и значительно снижает коэффициент трения. Износостойкость при этом повышается в несколько раз. Аналогичный эффект достигается при сульфоцианиро-вании - одновременном насыщении поверхностей нитридами и сульфидами. [50]
Цементацией называется процесс насыщения поверхностного слоя стали углеродом. Различают два основных вида цементации: твердыми углеродосодержащими смесями ( карбюризаторами) и газовую. При газовой цементации углеродосодержащую атмосферу создают испарением керосина, синтина или спиртов, подаваемых в печь каплями, или продувкой через печь эндотермической газовой смеси с добавками до 5 % природного газа. [51]
Цементацией называется процесс насыщения поверхностного слоя стали углеродом. Различают два основных вида цементации: твердыми углеродсодержащими смесями ( карбюризаторами) и газовую. Основной - целью цементации является получение твердой и износостойкой поверхности, что достигается обогащением поверхностного слоя углеродом до концентрации 0 8 - 1 0 % и последующей закалкой. Цементация и последующая закалка одновременно повышают предел выносливости. [52]
Цементацией называется процесс насыщения поверхностного слоя стали углеродом. Различают два основных вида цементации: твердыми утлерод-содержащими смесями ( карбюризаторами) и кгзовую. Целью цементации является получение твердой и износостойкой поверхности, что достигается обогащением поверхностного слоя углеродом и последующей закалкой с низким отпуском. Цементация и последующая термическая обработка одновременно повышают и предел выносливости. [53]
Страницы: 1 2 3 4
www.ngpedia.ru