Закалка стали – способы, температура, правила
- Какой бывает закалка металла
- Как избежать образования окалины и обезуглероживания при закалке
- Охлаждение стали при закалке
- Выполнение закалки и отпуска стальных деталей в домашних условиях
Одним из наиболее распространенных способов термообработки металлов является закалка стали. Именно при помощи закаливания формируются требуемые характеристики готового изделия, а ее неправильное выполнение может привести к излишней мягкости металла (непрокаливание) или к его чрезмерной хрупкости (перекаливание). В нашей статье речь пойдет о том, что такое правильная закалка и что нужно сделать, чтобы ее выполнить.
Закалка стали
Какой бывает закалка металла
О том, что воздействие высокой температуры на металл может изменить его структуру и свойства, знали еще древние кузнецы и активно использовали это на практике. В дальнейшем уже научно было установлено, что закалка изделий, изготовленных из стали, предполагающая нагрев и последующее охлаждение металла, позволяет значительно улучшать механические характеристики готовых изделий, значительно увеличивать срок их службы и даже в итоге уменьшать их вес за счет увеличения прочности детали. Что примечательно, закалка деталей из недорогих сортов стали позволяет придать им требуемые характеристики и успешно использовать вместо более дорогостоящих сплавов.
Смысл процесса, который называется закалка изделий из стальных сплавов, заключается в нагреве металла до критической температуры и его последующем охлаждении. Основная цель, которая преследуется такой технологией термообработки, заключается в повышении твердости и прочности металла с одновременным уменьшением его пластичности.
Существуют различные виды закалки и последующего отпуска, отличающиеся режимами проведения, которые и определяют конечный результат. К режимам закалки относятся температура нагрева, время и скорость его выполнения, время выдержки детали в нагретом до заданной температуры состоянии, скорость, с которой осуществляется охлаждение.
Наиболее важным параметром при закалке металлов является температура нагрева, при достижении которой происходит перестройка атомной решетки. Естественно, что для сталей разных сортов значение критической температуры отличается, что зависит, в первую очередь, от уровня содержания в их составе углерода и различных примесей.
После выполнения закалки повышается как твердость, так и хрупкость стали, а на ее поверхности, потерявшей значительное количество углерода, появляется слой окалины. Толщину этого слоя обязательно следует учитывать для расчета припуска на дальнейшую обработку детали.
Диаграмма состояний железо-углерод
При выполнении закалки изделий из стальных сплавов, очень важно обеспечить заданную скорость охлаждения детали, в противном случае, уже перестроенная атомная структура металла может перейти в промежуточное состояние. Между тем, слишком быстрое охлаждение тоже нежелательно, так как оно может привести к появлению на детали трещин или к ее деформации. Для того, чтобы избежать образования таких дефектов, скорость охлаждения после падения температуры нагретого металла до 200 градусов Цельсия, несколько замедляют.
Для нагрева деталей, изготовленных из углеродистых сталей, используют камерные печи, которые могут прогреваться до 800 градусов Цельсия. Для закалки отдельных марок стали критическая температура может составлять 1250–1300 градусов Цельсия, поэтому детали из них нагреваются в печах другого типа. Удобство закалки сталей таких марок заключается в том, что изделия из них не подвержены растрескиванию при охлаждении, что исключает необходимость в их предварительном прогреве.
Очень ответственно следует подходить к закалке деталей сложной конфигурации, имеющих тонкие грани и резкие переходы. Чтобы исключить растрескивание и коробление таких деталей в процессе нагрева, его следует проводить в два этапа. На первом этапе такую деталь предварительно прогревают до 500 градусов Цельсия и лишь затем доводят температуру до критического значения.
Нагрев стали при закалке токами высокой частоты
Для качественной закалки сталей важно обеспечить не только уровень нагрева, но и его равномерность. Если деталь отличается массивностью или сложной конфигурацией, обеспечить равномерность ее нагрева можно только в несколько подходов. В таких случаях нагревание производится с двумя выдержками, которые необходимы для того, чтобы достигнутая температура равномерно распределилась по всему объему детали. Увеличивается суммарное время нагревания и в том случае, если в печь одновременно помещаются сразу несколько деталей.
Как избежать образования окалины и обезуглероживания при закалке
Многие детали из стали проходят закалку уже после того, как была выполнена их финишная обработка. В таких случаях недопустимо, чтобы поверхность деталей была обезуглерожена или на ней образовалась окалина. Существуют способы закалки изделий из стали, которые позволяют избежать таких проблем. Закалка, выполняемая в среде защитного газа, который нагнетается в полость нагревательной печи, может быть отнесена к наиболее передовому из таких способов. Следует иметь в виду, что используют такой метод лишь в том случае, если печь для нагрева полностью герметична.
На фото виден момент гидросбива на стане горячей прокатки — удаление окалины
Более простым способом, позволяющим избежать обезуглероживания поверхности металла при закалке, является применение чугунной стружки и отработанного карбюризатора. Для того чтобы защитить поверхность детали при нагревании, ее помещают в специальную емкость, в которую предварительно засыпаны эти компоненты. Для предотвращения попадания в такую емкость окружающего воздуха, который может вызвать процессы окисления, снаружи ее тщательно обмазывают глиной.
Если после закалки металла его охлаждают не в масле, а в соляной ванне, ее следует регулярно раскислять (не менее двух раз за смену), чтобы избежать обезуглероживания поверхности детали и появления на ней окисла. Для раскисления соляных ванн могут быть использованы борная кислота, бурая соль или древесный уголь. Последний обычно помещают в специальный стакан с крышкой, в стенках которого имеется множество отверстий. Опускать такой стакан в соляную ванну следует очень осторожно, так как в этот момент на ее поверхности вспыхивает пламя, которое затухает через некоторое время.
Существует простой способ, позволяющий проверить качество раскисления соляной ванны. Для этого в такой ванне нескольких минут (3–5) нагревают обычное лезвие из нержавеющей стали. После соляной ванны лезвие помещают в воду для охлаждения. Если после такой процедуры лезвие не гнется, а ломается, то раскисление ванны прошло успешно.
Объемная закалка толстостенных заготовок
Охлаждение стали при закалке
Основу большинства охлаждающих жидкостей, используемых при закалке изделий из сталей, составляет вода. При этом важно, чтобы такая вода не содержала в своем составе примесей солей и моющих средств, которые могут значительно повлиять на скорость охлаждения. Емкость, в которой содержится вода для закалки изделий из металла, не рекомендуется использовать в других целях. Важно также учитывать и то, что для охлаждения металла в процессе закалки, нельзя использовать проточную воду. Оптимальной для охлаждающей жидкости считается температура в 30 градусов Цельсия.
Закалка изделий из стали с использованием для их охлаждения обычной воды, имеет ряд существенных недостатков. Самый главный из них — это растрескивание и коробление деталей после их охлаждения. Как правило, таким способом охлаждения пользуются, когда выполняется цементирование металла, поверхностная закалка стали или термическая обработка деталей простой конфигурации, которые в дальнейшем будут подвергаться финишной обработке.
Для изделий сложной формы, изготовленных из конструкционных сталей, применяют другой тип охлаждающей жидкости – 50%-й раствор каустической соды, нагретый до температуры 60 градусов Цельсия. После охлаждения в таком растворе закаленная сталь приобретает светлый оттенок.
Очень важно при работе с каустической содой соблюдать технику безопасности, обязательно использовать вытяжку, размещаемую над ванной. При опускании раскаленной детали в раствор образуются пары, очень вредные для здоровья человека.
Закалка стали в муфельной печи
Лучшей охлаждающей жидкостью для тонкостенных деталей из углеродистых сталей и изделий, выполненных из легированных сплавов, являются минеральные масла, которые обеспечивают постоянную (изотермическую) температуру охлаждения, вне зависимости от условий окружающей среды. Главное, чего следует избегать при использовании такой технической жидкости, — это попадания в нее воды, что может привести к растрескиванию деталей в процессе их охлаждения. Однако, если в такую охлаждающую жидкость все же попала вода, ее можно легко удалить из нее, нагрев масло до температуры, превышающей температуру кипения воды.
У закалки стали с использованием масла в качестве охлаждающей жидкости есть ряд существенных недостатков, о которых обязательно стоит знать. При контакте масла с раскаленной деталью выделяются пары, вредные для человеческого здоровья, кроме того, масло в этот момент может загореться. У масляной ванны есть и такое свойство: после ее использования на детали остается налет, а сама охлаждающая жидкость со временем теряет свою эффективность.
Все эти факторы следует учитывать при выполнении закалки металлов в масляной среде и принимать следующие меры безопасности:
- погружать детали в масляную ванну при помощи щипцов с длинными ручками;
- все работы выполнять в специальной маске из закаленного стекла и в перчатках, изготовленных из толстой ткани с огнеупорными свойствами или из грубой кожи;
- надежно защищать плечи, шею, грудь рабочей одеждой, изготовленной из толстой огнеупорной ткани.
Охлаждение в масляной ванне
Для закалки сталей отдельных марок охлаждение осуществляют при помощи потока воздуха, создаваемого специальным компрессором. Очень важно, чтобы охлаждающий воздух был совершенно сухим, так как содержащаяся в нем влага может вызвать растрескивание поверхности металла.
Существуют способы закалки стали, при которых используют комбинированное охлаждение. К ним обращаются для охлаждения деталей из углеродистых сталей, имеющих сложный химический состав. Суть таких способов закалки заключается в том, что сначала нагретую деталь помещают в воду, где за короткое время (несколько секунд) ее температура снижается до 200 градусов, дальнейшее охлаждение детали проводят уже в масляной ванне, куда ее следует переместить очень оперативно.
Выполнение закалки и отпуска стальных деталей в домашних условиях
Термическая обработка металлических изделий, в том числе поверхностная закалка стали, не только увеличивает твердость и прочность сплава, но и значительно повышает внутренние напряжения в его структуре. Чтобы снять эти напряжения, способные в процессе эксплуатации детали привести к ее поломке, необходимо отпустить изделие из стали.
Следует иметь в виду, что такая технологическая операция приводит к некоторому снижению твердости стали, но увеличивает ее пластичность. Для выполнения отпуска, суть которого состоит в постепенном уменьшении температуры нагретой детали и ее выдерживании при определенном температурном режиме, используются печи, соляные и масляные ванны.
Закалка и отпуск стали в домашних условиях
Температуры, при которых выполняется отпуск, отличаются для различных сортов стали. Так, отпуск быстрорежущих сплавов проводится при температуре 540 градусов Цельсия, а для сталей с твердостью на уровне HRC 59-60 достаточно и 150 градусов. Что характерно, при отпуске быстрорежущих сплавов их твердость даже возрастает, а во втором случае ее уровень понижается, но значительно повышается показатель пластичности.
Закалка и отпуск изделий из стали, в том числе и нержавеющих сортов, вполне допустима (и, более того, часто практикуется) и в домашних условиях, если в этом возникла необходимость. В таких случаях для нагрева изделий из стали можно использовать электроплиты, духовки и даже раскаленный песок. Температуры, до которых следует нагревать стальные изделия в таких случаях, можно подобрать по специальным таблицам. Перед закалкой или отпуском стальных изделий, их необходимо тщательно очистить, на их поверхности не должно содержаться грязи, следов масла и ржавчины.
После очистки изделие из стали следует нагреть так, чтобы оно равномерно раскалилось докрасна. Для того чтобы раскалить его до такого состояния, необходимо выполнять нагрев в несколько подходов. После того, как требуемое состояние достигнуто, нагреваемое изделие следует охладить в масле, а затем сразу поместить в духовку, предварительно разогретую до 200 градусов Цельсия. Затем необходимо постепенно снизить температуру в духовке, доведя ее до отметки в 80 градусов Цельсия.
Данный процесс занимает обычно час. Дальнейшее охлаждение следует проводить на открытом воздухе, исключение составляют лишь изделия из хромоникелевых сталей, для снижения температуры которых используются масляные ванны.
Обусловлено это тем, что стали таких марок при медленном охлаждении могут приобрести так называемую отпускную хрупкость.
Закалка стали
Закалка стали
Закалкой стали называется операция термической обработки, заключающаяся в нагреве её по крайней мере выше критической точки Ac1(T.e. до аустенито-ферритного, аустенитного или аустенито-цементитного), выдержке и последующем охлаждении в различных средах с целью получения при комнатной температуре неустойчивых продуктов распада аустенита, а следовательно, повышения твёрдости и прочности.
Для углеродистых сталей точка Ас1 соответствует линии на диаграмме «железо-цементит» и составляет 727°С, В связи с тем, что нагрев ниже этой температуры не приводит к изменению исходной отожженной структуры стали, последующее охлаждение с любой скоростью так же не изменяет ни структуры, ни свойств стали. Следовательно такая операция не является закалкой.
В большинстве случаев основная цель закалки — повышение твёрдости и прочности — достигается превращением аустенита в одну из самых прочных структур — мартенсит. Его образование требует быстрого охлаждения с температуры закалки.
Выбор температуры закалки.
В зависимости от температуры нагрева закалка может быть полной и неполной.
В случае, если нагрев производится выше линии GSE диаграммы (точки асз и Аcm), то полученная при этом однофазная структура аустенита при охлаждении со скоростью больше некоторой критической превращается в чистый мартенсит. Такую закалку называют полной.
При неполной закалке нагрев стали осуществляется выше линии РSК(точка Ac1), но ниже линии GSE. При этом в доэвтектоидных сталях образуется структура аустенит + феррит, а в заэвтектоидных — аустенит + цементит. В таком случае даже охлаждение с очень высокой скоростью не может обеспечить чисто мартенситной структуры, так как избыточные фазы (феррит или цементит) сохраняются в структуре без изменений, В результате в доэвтектоидных сталях получается структура мартенсит + феррит, а в заэвтектоидных – мартенсит + цементит.
Твёрдость мартенсита, представляющего собой пересыщенный твёрдый раствор углерода в -железе, зависит от содержания в нём углерода (рис 1). В среднеуглеродистых и высокоуглеродистых сталях она составляет 55…65 НRС или 550…680НВ.
Феррит одна из самых мягких и малопрочных фаз в сталях. Его твёрдость не превышает 80…100 НВ. Цементит же — весьма твёрдая фаза (около 1000 HV или более 700 НВ). Следовательно присутствие избыточного феррита в структуре закалённой стали резко снижает её твёрдость, в то время как цементит способствует получению более высокой твёрдости.
Рис. 1 Зависимость твёрдости мартенсита от содержания углерода в стали.
Таким образом, для доэвтектоидных сталей целесообразно производить полную закалку на чистый мартенсит, а для заэвтектоидных — неполную, которая кроме мартенсита сохраняет в структуре некоторое количество цементита. Для эвтектоидной стали возможна только полная закалка.
Следует иметь в виду, что нагрев стали при закалке до температур, значительно превышающих критические точки Ac3 и Аcm, вообще не желателен, так как может привести к сильному обезуглероживанию и окислению поверхности деталей, укрупнению зерна аустенита и увеличению внутренних напряжений. В итоге после закалки с таких температур твёрдость поверхности оказывается заниженной, наблюдается повышенная деформация детали, получающийся мартенсит имеет грубое строение и обладает повышенной хрупкостью.
Всё это позволяет придти к выводу, что в зависимости от состава стали её нагрев под закалку целесообразно осуществлять до температур, лежащих на 30… 50 0С выше линии GSK (рис 2)
Рис. 2. Оптимальный интервал температур нагрева под закажу углеродистых сталей.
Скорость охлаждения при закалке
Структура и свойства закаленной стали в большей степени зависят не только от температуры нагрева, но и от скорости охлаждения. Получение закалочных структур обусловлено переохлаждением аустенита ниже линии PSK, где его состояние является неустойчивым. Увеличивая скорость охлаждения, можно обеспечивать его переохлаждение до весьма низких температур и превратить в различные структуры с разными свойствами. Превращение переохлажденного аустенита может идти как при непрерывном охлаждении, так и изотермически, в процессе выдержки при температурах ниже точки Ar1 (т. е. ниже линии PSK).
Влияние степени переохлаждения на устойчивость аустенита и скорость его превращения в различные продукты представляют графически в виде диаграмм в координатах «температура-время». В качестве примера рассмотрим такую диаграмму для стали эвтектоидного состава (рис 3). Изотермический распад переохлажденного аустенита в этой стали происходит в интервале температур от Ar1 (727 °С) до Мн (250 °С), где Мн -температура начало мартенситного превращения. Мартенситное превращение в большинстве сталей может идти только при непрерывном охлаждении.
Рис.3 Диаграмма распада аустенита для стали эвтектоидного состава.
На диаграмме (см. рис 3) нанесены две линии, имеющие форму буквы «С», так называемые «С-кривые». Одна из них (левая) указывает время начало распада переохлажденного аустенита при разных температурах, другая (правая) — время окончания распада, В области, расположенной левее линии начала распада, существует переохлажденный аустенит. Между С-кривыми имеется как аустенит, так и продукты его распада. Наконец, правее линии конца распада существуют только продукты превращения.
Превращение переохлажденного аустенита при температурах от Ar1 до 550 0С называют перлитным. Если аустенит переохлажден до температур 550…Mн, — его превращение называется промежуточным.
В результате перлитного превращения образуются пластинчатые структуры перлитного типа, представляющие собой феррито-цементитные смеси различной дисперсности. С увеличением степени переохлаждения в соответствии с общими законами кристаллизации возрастает число центров. Уменьшается размер образующихся кристаллов, т.е. возрастает дисперсность феррито-цементитной смеси. Так если превращение происходит при температурах, лежащих в интервале Ar1…650°C, образуется грубая феррито-цементитная смесь, которую называют собственно перлитом. Структура перлита является стабильной, т.е. неизменяемой с течением времени при комнатной температуре.
Все остальные структуры, образующиеся при более низких температурах, т.е. при переохлаждениях аустенита, относятся к метастабильным. Так при переохлаждении аустенита до температур 650…590°С он превращается в мелкую феррито-цементитную смесь, называемую сорбитом.
При ещё более низких температурах 590… 550 °С образуется тростит -весьма дисперсная феррито-цементитная смесь. Указанные деления перлитных структур в известной степени условно, так как дисперсность смесей монотонно возрастает с понижением температуры превращения. Одновременно с этим возрастают твёрдость и прочность сталей. Так твёрдость перлита в эвтектовдной стали составляет 180…22- НВ (8…19 HRC), сорбита — 250…350 НВ (25…38 НRС), тростита — 400…450 НВ (43…48HRC).
При переохлаждении аустенита до температур 550…МН он распадается с образованием бейнита. Это превращение называется промежуточным, так как в отличие от перлитного оно частично идет по так называемому мартенситному механизму, приводя к образованию смеси цементита и несколько пересыщенного углеродом феррита. Бейнитная структура отличается высокой твёрдостью 450…550 НВ.
Рис.4 Диаграмма распада аустенита для доэвтектоидной (а) и заэвтектоидной (б) сталей.
На диаграммах распада аустенита для доэвтектоидных и заэвтектоидных сталей (рис.4.) имеется дополнительная линия, показывающая время начала выделения из аустенита избыточных кристаллов феррита или цементита. Выделение этих избыточных структур происходит только при небольших переохлаждениях. При значительном переохлаждении аустенит превращается без предварительного выделения феррита или цементита, В этом случае содержание углерода в образовавшейся смеси отличается от эвтектоидного.
В случае непрерывного охлаждения аустенита с различной скоростью его превращение развивается не при постоянной температуре, а в некотором интервале температур. Для того, чтобы определить структуры, получающиеся при непрерывном охлаждении, нанесём на диаграмму распада аустенита кривые скорости охлаждения образцов углеродистой эвтектоидной стали (рис.5.).
Из этой диаграммы видно, что при очень малой скорости охлаждения V1 которая обеспечивается охлаждением вместе с печью (например, при отжиге), получается структура перлита. При скорости V2 (на воздухе) превращение идёт при несколько более низких температурах. Образуется структура перлит, но более дисперсный. Такая обработка называется нормализацией и широко применяется для малоуглеродистых сталей (иногда и для среднеуглеродистых) взамен отжига в качестве смягчающей.
Рис.5. Кривые распада аустенита при непрерывном охлаждении эвтектоидной стали.
При скорости V3 (охлаждение в масле) превращение аустенита идёт при таких температурах, которые обеспечивают получение сорбитной структуры, а иногда и троститной.
Если аустенит охлаждать с очень большой скоростью (V4), то он переохлаждается до весьма низкой температуры, обозначенной на диаграммах, как Мн. Ниже этой температуры происходит бездиффузионное мартенситное превращение, приводящее к образованию структуры мартенсита. Для углеродистых сталей такую скорость охлаждения обеспечивает, например, вода
В общем случае минимальная скорость охлаждения, при которой весь аустенит переохлаждается до температуры Мн и превращается в мартенсит, называется критической скоростью закалки. На рис.5, она обозначена, как Vкр и является касательной к С-кривой. Критическая скорость закалки — важнейшая технологическая характеристика стали. Она определяет выбор охлаждающих сред для получения мартенситной структуры.
Величина критической скорости закалки зависит от химического состава стали и некоторых других факторов. Так, например, у некоторых легированных сталей даже охлаждение на воздухе обеспечивает скорость больше критической.
При закалке на мартенсит необходимо учитывать, что эта структура имеет большой удельный объём и её образование сопровождается как заметным увеличением объёма закаливаемого изделия, так и резким увеличением внутренних напряжений, которые в свою очередь приводят к деформации или даже к образованию трещин. Всё это в сочетании с повышенной хрупкостью мартенсита требует проведения дополнительной термической обработки закалённых деталей — операции отпуска.
Также по теме:
Отпуск стали. Термообработка, обычно проводящаяся после закалки.
Свойства легированных сталей. Структура, свойства и применение.
Сталь с воздушной закалкой – свойства и определение
Сталь с воздушной закалкой относится к стали, которая подвергается процессу закалки на воздухе. Эта естественная закалка часто используется для обработки сталей группы А инструментальных сталей, таких как А2, А3, А4, А6 и А10. Однако также известно, что он используется для сталей таких марок, как D2.
Закалка – это процесс, используемый для упрочнения стали и изменения ее прочности и свойств упрочнения. Закалка стали может производиться с использованием различных сред, таких как масло и вода. Хотя в этой статье мы рассмотрим охлаждение металла с использованием воздуха или воздуха с такими добавками, как газ.
При использовании воздуха в качестве закалки рекомендуется учитывать, что охлаждение стали на естественном воздухе является наименее контролируемым методом. Вместо этого было бы лучше, если бы вы поместили его в атмосферную или вакуумную печь, чтобы обеспечить полный контроль над процессом закалки.
Важность закалки стали на воздухе
Закалка на воздухе, как правило, является важным процессом, используемым для термической обработки сталей, которые, как было установлено, должны быть закалены на воздухе. Эти стали, которые не закаливаются на воздухе, не обладают дополнительными свойствами прочности и твердости, которые позволяют использовать их в сложных условиях. Например, такие конечные продукты, как ножи для резки, калибры, штампы и пуансоны, не будут служить долго без этого процесса термообработки.
При закалке воздухом ваш производитель стали порекомендует, заключается ли процесс в простом охлаждении металла до комнатной температуры или следует продуть его сжатым воздухом. Если производитель рекомендует струйную очистку воздухом, это можно сделать разными способами, включая простой баллончик со сжатым воздухом или использование оборудования, специально предназначенного для управления воздухом.
Свойства стали воздушной закалки
Свойства инструментальной стали, относящейся к закалке на воздухе, включают стали с содержанием углерода в пределах от 0,5% до 2%. Способность к закалке на воздухе означает, что эти типы стали обладают дополнительными свойствами, такими как молибден, хром и марганец.
AISI | C | Mn | Si | Cr | Ni | Mo | W | V |
---|---|---|---|---|---|---|---|---|
A2 | 1.00 | 1.00 | 0.50 | 5.00 | 0.30 | 1.00 | – | 0.15-0.50 |
A3 | 1.30 | 0.60 | 0.50 | 5.50 | 0.30 | 1.40 | – | 1.40 |
A4 | 1.05 | 2.![]() | 0.50 | 2.20 | 0.30 | 1.40 | – | – |
A6 | 0.75 | 2.50 | 0.50 | 1.20 | 0.30 | 1.40 | – | – |
A10 | 1.50 | 2.10 | 1.50 | – | 2.05 | 1.75 | – | – |
Advantages of air quenching
The advantages этой закалочной среды включает в себя возможность полного контроля над скоростью охлаждения и конечным результатом твердости. Например, регулирование давления и воздействия воздуха на сталь означает, что вы можете контролировать скорость ее охлаждения и, следовательно, желаемые свойства. Это важно для производителей инструментов, которые хотят использовать продукт в условиях, требующих чрезвычайной прочности и долговечности, поскольку известно, что закалка на воздухе позволяет получать прочные и долговечные металлы, способные выдерживать даже самые сложные условия.
Одним из основных преимуществ использования воздуха в качестве охлаждающей жидкости является стоимость. Воздух предоставляется бесплатно, и если не используются дорогостоящие климатические камеры, вы можете значительно сэкономить на затратах, используя воздух для закалки стали.
Недостатки закалки на воздухе
При закалке стали на воздухе часто возникают проблемы с металлом, если она выполняется неправильно. Основная проблема, которая может возникнуть, — это трещины при охлаждении из-за быстрого охлаждения стальной детали. Однако вы можете легко предотвратить эту проблему, используя вакуумные печи и соответствующие методы закалки.
Инструментальная сталь D-2 для воздушной закалки
Инструментальная сталь D-2 представляет собой универсальную высокоуглеродистую, высокохромистую инструментальную сталь для воздушной закалки, которая характеризуется относительно высокой достижимой твердостью и многочисленными крупными сплавами с высоким содержанием хрома. в микроструктуре. Эти карбиды обеспечивают хорошую стойкость к износу при скользящем контакте с другими металлами и абразивными материалами. Хотя доступны другие стали с повышенной ударной вязкостью или улучшенной износостойкостью, D-2 обеспечивает эффективное сочетание износостойкости и ударной вязкости, производительности инструмента, цены и большого разнообразия форм изделий.
Категория*
FlatRoundsFollow BarOther
Толщина/внутренний диаметр*
Ширина/внешний диаметр*
Длина*
Другое Примечания углеродистая, высокохромистая, закаливаемая на воздухе инструментальная сталь, характеризующаяся относительно высокой достижимой твердостью и многочисленными, крупными, богатыми хромом сплавными карбидами в микроструктуре. Эти карбиды обеспечивают хорошую стойкость к износу при скользящем контакте с другими металлами и абразивными материалами. Хотя доступны другие стали с повышенной ударной вязкостью или улучшенной износостойкостью, D-2 обеспечивает эффективное сочетание износостойкости и ударной вязкости, производительности инструмента, цены и большого разнообразия форм изделий.
Analysis:
C | CO | CR | It increases the rate of carbon-penetration in carburizing.»> MN | MO | NI | P | It decreases weldability, impact toughness and ductility.»> S | SI | V | W |
---|---|---|---|---|---|---|---|---|---|---|
1.40 – 1.60 | 11.00 – 13.00 | 0.10 – 0.60 | 0.70 – 1.20 | 0.![]() | 0.50 – 1.10 |
Size Availability :
Плоские • Полые • Метрические • Нестандартные • Круглые • Квадратные • Стандартные
Применение:
Штампы для вырубки | Инструменты для полировки | Штампы для чеканки |
Drawing Dies | Extrusion Dies | Forming Rolls |
Gauges | Knurls | Lamination Dies |
Lathe Centers | Master Parts | Punches |
Seaming Rolls | Shear Blades | Бобинорезательные станки |
Плашки обжимные | Плашки резьбовые накатные | Матрицы обрезки |
Обозначения:
DIN 1.2379-Германия
B.S. BD 2-Великобритания
ASTM A681-US
FED QQ-T-570-US
SAE J437-US
SAE J438-US
UNS T30402-US
AISI D2 Инструментальная сталь для закалки на воздухе-US
Диапазон температур | Охлаждение/закалка | Примечания | |||||||||||||||||||||||||||||||||||||||||||||||||||||||||||||||||||||||||||||||||||||||||||||||||||||||||||||||||||||||||||||||||||||||||||||||||||||||||||||||||||||||||||||||||||||||||||||||||||||||||||||||||||||||||||||||||||||||||||||||||||||||||||||||||||||||||||||||||||||||||||||||||||||||||||||||||||||||||||||||||||||||||||||||||||||||||||||||||||||||||||||||||||||||||||||||||||||||||||||||||||||||||||||||||||
---|---|---|---|---|---|---|---|---|---|---|---|---|---|---|---|---|---|---|---|---|---|---|---|---|---|---|---|---|---|---|---|---|---|---|---|---|---|---|---|---|---|---|---|---|---|---|---|---|---|---|---|---|---|---|---|---|---|---|---|---|---|---|---|---|---|---|---|---|---|---|---|---|---|---|---|---|---|---|---|---|---|---|---|---|---|---|---|---|---|---|---|---|---|---|---|---|---|---|---|---|---|---|---|---|---|---|---|---|---|---|---|---|---|---|---|---|---|---|---|---|---|---|---|---|---|---|---|---|---|---|---|---|---|---|---|---|---|---|---|---|---|---|---|---|---|---|---|---|---|---|---|---|---|---|---|---|---|---|---|---|---|---|---|---|---|---|---|---|---|---|---|---|---|---|---|---|---|---|---|---|---|---|---|---|---|---|---|---|---|---|---|---|---|---|---|---|---|---|---|---|---|---|---|---|---|---|---|---|---|---|---|---|---|---|---|---|---|---|---|---|---|---|---|---|---|---|---|---|---|---|---|---|---|---|---|---|---|---|---|---|---|---|---|---|---|---|---|---|---|---|---|---|---|---|---|---|---|---|---|---|---|---|---|---|---|---|---|---|---|---|---|---|---|---|---|---|---|---|---|---|---|---|---|---|---|---|---|---|---|---|---|---|---|---|---|---|---|---|---|---|---|---|---|---|---|---|---|---|---|---|---|---|---|---|---|---|---|---|---|---|---|---|---|---|---|---|---|---|---|---|---|---|---|---|---|---|---|---|---|---|---|---|---|---|---|---|---|---|---|---|---|---|---|---|---|---|---|---|---|---|---|---|---|---|---|---|---|---|---|---|---|---|---|---|---|---|---|---|---|---|---|---|---|---|---|---|---|---|---|---|---|---|---|---|---|---|---|---|---|---|---|---|---|---|---|---|---|---|---|---|---|---|---|---|---|---|---|---|---|---|---|
Ковка | 2000-2100°F | Медленно.![]() | Медленно и равномерно нагревайте. Не подделывайте ниже 1700°F. Охладить в вермикулите или другом изоляционном материале. | ||||||||||||||||||||||||||||||||||||||||||||||||||||||||||||||||||||||||||||||||||||||||||||||||||||||||||||||||||||||||||||||||||||||||||||||||||||||||||||||||||||||||||||||||||||||||||||||||||||||||||||||||||||||||||||||||||||||||||||||||||||||||||||||||||||||||||||||||||||||||||||||||||||||||||||||||||||||||||||||||||||||||||||||||||||||||||||||||||||||||||||||||||||||||||||||||||||||||||||||||||||||||||||||||||
Отжиг | 1545-1600°F | Медленное охлаждение со скоростью 25°F в час до 1000°F. | |||||||||||||||||||||||||||||||||||||||||||||||||||||||||||||||||||||||||||||||||||||||||||||||||||||||||||||||||||||||||||||||||||||||||||||||||||||||||||||||||||||||||||||||||||||||||||||||||||||||||||||||||||||||||||||||||||||||||||||||||||||||||||||||||||||||||||||||||||||||||||||||||||||||||||||||||||||||||||||||||||||||||||||||||||||||||||||||||||||||||||||||||||||||||||||||||||||||||||||||||||||||||||||||||||
Снятие напряжения | 1020-1200°F | Медленно охладить в печи до 930°F. Затем на воздухе. | Снятие напряжения после черновой обработки | ||||||||||||||||||||||||||||||||||||||||||||||||||||||||||||||||||||||||||||||||||||||||||||||||||||||||||||||||||||||||||||||||||||||||||||||||||||||||||||||||||||||||||||||||||||||||||||||||||||||||||||||||||||||||||||||||||||||||||||||||||||||||||||||||||||||||||||||||||||||||||||||||||||||||||||||||||||||||||||||||||||||||||||||||||||||||||||||||||||||||||||||||||||||||||||||||||||||||||||||||||||||||||||||||||
Предварительный нагрев | 1450-1500° F | Время предварительного нагрева в печи ¾ часа. на дюйм толщины. Нагрев до температуры как можно медленнее | |||||||||||||||||||||||||||||||||||||||||||||||||||||||||||||||||||||||||||||||||||||||||||||||||||||||||||||||||||||||||||||||||||||||||||||||||||||||||||||||||||||||||||||||||||||||||||||||||||||||||||||||||||||||||||||||||||||||||||||||||||||||||||||||||||||||||||||||||||||||||||||||||||||||||||||||||||||||||||||||||||||||||||||||||||||||||||||||||||||||||||||||||||||||||||||||||||||||||||||||||||||||||||||||||||
Закалка | 1800-1900°F | На воздухе. | Отпуск сразу после закалки. Дайте остыть до 125-150 ° F перед темперированием. Время выдержки составляет 15 минут на дюйм толщины. Минимум 30 минут. | ||||||||||||||||||||||||||||||||||||||||||||||||||||||||||||||||||||||||||||||||||||||||||||||||||||||||||||||||||||||||||||||||||||||||||||||||||||||||||||||||||||||||||||||||||||||||||||||||||||||||||||||||||||||||||||||||||||||||||||||||||||||||||||||||||||||||||||||||||||||||||||||||||||||||||||||||||||||||||||||||||||||||||||||||||||||||||||||||||||||||||||||||||||||||||||||||||||||||||||||||||||||||||||||||||
Закалка | (см. таблицу) | Для получения хороших результатов необходимо полное выравнивание температуры по всему инструменту.![]() Как сверло вставить в дрель: Как вставить сверло в дрель? Как вытащить и поменять сверло без ключа, чтобы пользоваться дрелью? Как его открутить и снять, если застряло?Как вставить сверло в дрель и перфораторОпубликовано: Нередко могут возникать трудности и проблемы в работе с перфоратором или дрелью. Главным образом, проблема может заключаться в неумении правильно работать со сверлами. Для начала рассмотрим некоторые отличия патронов и сверл. Содержание
РазновидностиРазновидности патронов Сверла подразделяются на применяемые по:
Разновидности сверл Сверла могут быть:
Также сверла отличаются и своим наконечником. Они специально изготавливаются для ударной и обычной дрели, а по форме напоминают цилиндр. Что касается самих патронов, то здесь также имеются отличия. Например, некоторые используются для ударной дрели, а другие для обычной дрели или перфоратора. В каждом отдельном случае закрепить сверло можно по разному.
Патрон кулачковый для дрели Патроны в свою очередь также могут быть двух видов:
Ключевой патрон требует специального ключа для установки сверла. Техника замены патрона представлена в видеоматериале: Двухмуфтовый патрон имеет две муфты, одна из них зажимается, второй рукой крутится другая муфта. Если говорить об одномуфтовых патронах, то патрон зажимается одной рукой. Замена сверл в таком патроне происходит гораздо быстрее в отличие от ключевого. Но что касается фиксации сверла, то оно значительно слабее держится при таком варианте. Устройство патрона
Итак, как вставить сверло в перфоратор или дрель правильно? Как вставить сверлоСмазка для сверла Чтобы этот процесс прошел гладко, важно соблюсти некоторые последовательные шаги:
Все зависит от используемого вами патрона. Но как быть, если после работы не получается извлечь сверло из патрона? Что делать, если сверло застрялоЗастряло сверло Обычно изъятие сверла из патрона не составляет особенных проблем. Например, в ключевом патроне достаточно ключ повернуть против часовой стрелки. В быстрозажимном патроне все действия происходят также просто. Для этого муфта крутится против часовой стрелки. Например, дрель можно зажать в левой руке и вскользь ударить по нижней части патрона внутренней стороной ладони. Обычно после таких действий сверло легко вынимается. Если патрон металлический, то также можно слегка постучать по патрону молотком. Постукивать необходимо до тех пор, пока хвостик не появится из патрона. Если и так не получается, то можно воспользоваться газовым ключом.
Бывают и другие случаи, когда сверло застревает в стене. В таком случае сверло прокручивается в патроне. Для его изъятия потребуется навесу разжать патрон и удалить сверло из стены. Итак, как мы рассмотрели с вами все возможные ситуации, которые могут возникнуть в работе с перфоратором и дрелью при смене сверла. ВидеоСмотрите, как правильно вставлять сверло в дрель:
Помогла ли вам статья? Как вставить сверло в дрель: особенности эксплуатации инструментаПрактически у каждого домашнего мастера есть разный электроинструмент вроде шуруповерта, дрели, перфоратора. Основное их назначение — сделать круглое отверстие в разных материалах. И если шуруповерт служит средством для вкручивания крепежных элементов (саморезы, винты, шурупы и т. д.), то электрические дрели представляют собой более мощное оборудование. У таких инструментов развивается больший крутящий момент, и они способны выдавать более высокие обороты. Главное — знать основные правила работы с ними — к примеру, как вставить сверло в дрель Метабо, Интерскол, Зубр, Бош. От того, насколько грамотно мастер сможет установить сверло в патрон, зависит качество работы и собственная безопасность. Содержание
Как вставлять сверло в дрель Разновидности патронов для дрелиПатрон любой дрели — это обязательный элемент, который предназначен для закрепления хвостовика, а также прочих типов насадок для электродрели. При этом хвостовая часть зажимается цанговым механизмом, а надежное крепление обеспечивается ее обхватом кулачками в патроне. Обычно их не более 3 штук и поэтому механизм зовется трех кулачковым. Сами патроны могут быть 2 основных типов:
Крутящий момент передается от электромотора дрели через систему шестерен на вал с патроном, что и обеспечивает вращение последнего. Поэтому крайне важно, чтобы зажимной механизм был высокого качества исполнения.
Зубчато-венцовый патронЧтобы понять, как вставить насадку в дрель, стоит рассмотреть, что представляет собой такой механизм. Основная особенность данного механизма кроется в наличии специального зажимного ключа, за счет чего патрон и называется ключевым. Это самый распространенный вариант для электродрелей Bosch, Sparky, Makita, Hammer, Dewalt в силу того, что обеспечивается высокое качество зажима хвостовика сверла. В такое устройство поместятся насадки диаметром 1-16 мм. Сам ключ выглядит как стержень с рычажком, на который насажено зубчатое колесико. На самом патроне предусмотрено специальное отверстие, рассчитанное под вал ключа, а также есть круговая зубчатая коронка, что соответствует ключевому профилю. Зубчато-венцовый патрон Для разведения и сведения кулачков с целью закрепить или ослабить хвостовик сверла, ключ помещается в паз, одновременно с этим шестерни колеса насаживаются на зубья коронки. Далее остается вращать стержень в том или ином направлении. Как правило, ключи имеют идентичное строение, а потому подходят ко многим ручным инструментам. Однако есть исключение из правил — ряд производителей, которые поставляют на рынки дорогую продукцию, делают оригинальные ключи, отличающиеся по размеру и профилю.
Такое устройство патрона удобно в использовании, однако есть высокий риск потери ключа, а без него невозможно как поставить, так и вынуть элемент конструкции. По этой причине большинство мастеров привязывают его к ручке дрели. Быстрозажимной механизмКак поменять насадку на дрель? В этом случае тоже нужно понимать устройство механизма. Есть патроны с одной или двумя муфтами. В случае одномуфтового механизма операции выполняются одной рукой. В отношении второго типа задействуются обе руки — одной нужно удерживать одну муфту (ближнюю к корпусу), а другой вращать вторую муфту. Зная такие тонкости, можно легко понять, как менять сверла. Как сверло вставляется в дрельПроцедура очень простая и выполняется быстро, а в умелых руках мастера это может занять считанные секунды. Однако ряд правил следует соблюдать неукоснительно, чтобы обезопасить себя от непредвиденных случаев. Пошаговый алгоритм:
Как сверло вставляется в дрель Подбор расходников зависит от самого электроинструмента — есть разнообразные модели, которые отличаются между собой многообразием технического оснащения и функционала. Есть модели, которые не приспособлены для сверления металла, в другие электродрели можно установить насадки диаметром 0,8-10 мм или 1,5-15 мм. Теперь о качестве самих сверл — не рекомендуется приобретать дешевые изделия, поскольку они делаются из материала низкого качества, а потому долго не прослужат. Как из дрели вытащить сверлоКогда нужно убрать сверло в случае его поломки либо, чтобы сменить его на другое изделие, исходя из характера работ, процедура уже выполняется еще легче и быстрее. В этом случае имеется своя инструкция. Для начала необходимо выключить инструмент от электрической сети и обесточить его. Далее действовать, исходя из вида патрона — рукой либо ключом повернуть муфту в направлении против движения часовой стрелки. В результате кулачки начнут раздвигаться, ослабляя сверло. Его лучше пока не касаться, так как после работы оно остается горячим. Когда сверло будет извлечено из патрона, остается вставить другое изделие и продолжать работу или убрать оборудование на хранение. Далеко не всегда получается повернуть ключ или муфту с первого раза. Торопиться в ближайшую мастерскую пока не стоит — нужно приложить больше усилий. Возможные проблемные ситуацииВ некоторых случаях домашние мастера отдают электроинструмент в сервис для решения той или иной проблемы. Замена сверлаТеперь о том, как поменять сверло в дрели — вся процедура выполняется по схеме описанной выше — то есть сначала достается старое сверло и ставится новое. При этом, чтобы заменить элемент в быстрозажимном патроне зачастую приходится сталкиваться с рядом трудностей. В отдельных случаях бывает, что сверло в механизме настолько прочно засело, что не удается повернуть муфту. Следует использовать кусок ткани, что обеспечит крепкое сцепление с муфтой и попробовать покрутить еще раз.
Когда все это не помогает, следует крепко зафиксировать инструмент одной рукой, а ладонью другой ударять по патрону в направлении раскручивания. Как поменять сверло в дрели Удаление сверла без ключаЦенное достоинство ключевых конструкций в очень прочной фиксации сверла. Подойдет гвоздь, крестообразная отвертка, шуруп. К другой половине нужно приложить усилие для раскручивания патрона и таким образом пробовать вытащить сверло, обойдясь без ключа. Если вручную не получается, можно использовать тиски либо большой газовый ключ. Если застряло сверлоВ ряде случаев, когда работа закончена, вынуть сверло не получается раскручиванием патрона руками либо ключом. Не помогает даже режим реверс. Тогда придется использовать кардинальные способы:
Если застряло сверло Тем не менее, если ничего из рассмотренного не помогает, остается полностью открутить патрон. После чего крепить его в тисках и выбить сверло каким-нибудь металлическим стержнем или подходящей отверткой. Как вставить сверло в дрель (ключ + ключ без ключа)Узнайте, как пользоваться электродрелью и как менять сверло! Мы рассмотрим сверлильный патрон, патрон без ключа, сетевые и аккумуляторные дрели, сверла, отвертки и многое другое! Как пользоваться электродрелью Готовы научиться пользоваться электродрелью и заменять сверло? Это так просто, и я покажу вам шаг за шагом, как это сделать. Мы рассмотрим различные типы дрелей, таких как сетевые и аккумуляторные. Вам также может понравиться 10 инструментов, необходимых начинающим для деревообработки Этот пост содержит партнерские ссылки на расходные материалы или инструменты, которые я использовал для завершения этого проекта. Покупки, сделанные по этим ссылкам, помогают поддерживать веб-сайт Saws on Skates и позволяют мне делиться другими проектами, сделанными своими руками. и советы DIY с вами. Вы не платите за использование этих ссылок. Нажмите здесь, чтобы ознакомиться с политикой моего сайта. Прежде чем мы перейдем к как пользоваться электродрелью и как заменить сверло , не забудьте нажать кнопку подписки в нижней части этой страницы, чтобы подписаться на мой БЕСПЛАТНЫЙ еженедельный информационный бюллетень, содержащий полезные хитрости с отверстиями для карманов , экономящие место идеи мастер-классов , умные советы по самостоятельному изготовлению и многое другое! Содержание
Что такое дрель? Википедия определяет дрель как «инструмент, используемый в основном для проделывания круглых отверстий или забивания крепежных деталей. Вернуться к оглавлению Типы дрелей Существует несколько типов дрелей, таких как ручные дрели, электрические дрели и аккумуляторные дрели. В этом уроке мы сосредоточимся на электрических и аккумуляторных дрелях. Вернуться к оглавлению Сетевая дрель Для работы сетевую дрель необходимо подключить к электрической розетке. Электрический шнур соединяет дрель с розеткой. Это означает, что сетевая дрель может работать вечно, пока она подключена к розетке. Но есть недостаток. Этот недостаток — длина шнура. Другими словами, если шнур имеет длину шесть футов, мы можем использовать дрель только в пределах шести футов от электрической розетки. В противном случае нам понадобится удлинитель, чтобы увеличить радиус действия дрели. Сетевая дрель — это моя любимая дрель для предотвращения разрывов при сверлении карманных отверстий с помощью приспособления Kreg Jig. Связанный: Как подключить вилку Вернуться к оглавлению Аккумуляторная дрель-шуруповерт Аккумуляторная дрель-шуруповерт отличается от сетевой дрели тем, что не имеет шнура и не подключается к электрической розетке. . Вместо этого беспроводная дрель питается от аккумулятора. Для работы дрели необходимо зарядить аккумулятор. Одной из лучших особенностей аккумуляторной дрели является то, что ее можно использовать практически где угодно, поскольку она не ограничена длиной шнура. Еще одно различие между сетевой дрелью и аккумуляторной дрелью заключается в том, что аккумуляторная дрель не может работать вечно. Когда батарея аккумуляторной дрели начинает разряжаться, дрель начинает работать медленнее. СОВЕТ: Всегда следите за тем, чтобы второй аккумулятор был заряжен или заряжался при использовании аккумуляторной дрели. Нет ничего хуже, чем ждать, пока зарядится аккумулятор, когда вы находитесь в процессе создания проекта! Постоянное питание сетевой дрели будет поддерживать ее работу с постоянной скоростью, независимо от того, сверлим мы одно отверстие или сто отверстий. Аккумуляторная дрель перестанет работать, когда батарея полностью разрядится. Опять же, сетевая дрель может работать вечно, поэтому она не перестанет работать, если ее не отключить от электрической розетки. Я предпочитаю удобство аккумуляторной дрели почти для всех своих проектов, потому что я не ограничен длиной шнура. Связанный: Как сделать стеллаж для хранения аккумуляторных дрелей своими руками Вернуться к оглавлению Сверлильный станок Википедия определяет сверлильный станок как «дрель, которая может быть установлена на подставке или прикручена болтами к полу или верстаку». Рабочий конец сверлильного станка устанавливается над головой и может опускаться в заготовку. Сверлильный станок отлично подходит для сверления повторяющихся отверстий в заготовках. Я использовал сверлильный станок, чтобы просверлить отверстия, чтобы сделать эти фоторамки для коллажей своими руками. Вернуться к оглавлению Как пользоваться электродрелью Основными частями электродрели являются двигатель, рукоятка, пусковой переключатель, кнопка направления и патрон. Дрель вращается благодаря двигателю. Захват — это место, где мы держим руку, чтобы держать дрель. Ниже мы рассмотрим более подробно спусковой крючок, кнопку направления и патрон. Вернуться к оглавлению Средства индивидуальной защиты Перед тем, как включить дрель, нам нужно подумать о личной безопасности. Мы должны защитить ваши глаза защитными очками. Нам нужно защитить наши уши средствами защиты органов слуха, если мы собираемся бурить в течение длительного периода времени. Нам нужно защитить наши легкие качественным респиратором, если наш буровой проект будет создавать много пыли. Вернуться к оглавлению Триггерный переключатель Триггерный переключатель включает и выключает дрель. Большинство триггеров имеют переменную скорость. Это означает, что чем сильнее мы нажимаем на курок, тем быстрее будет вращаться дрель. Вернуться к оглавлению Кнопка направления Сверло вращается как в прямом, так и в обратном направлении. Кнопка используется для изменения направления вращения сверла. Кнопка «вперед/назад» обычно находится рядом с триггерным переключателем. Направление вперед используется для сверления отверстий и заворачивания шурупов. Обратное направление используется для удаления сверл из заготовок и для удаления винтов из заготовок. Сверла или дрели устанавливаются или вставляются в патрон дрели. Сверлильный патрон в основном представляет собой зажим, который удерживает биты и драйверы в дрели. Сверла используются для выполнения круглых отверстий в заготовках. Вернуться к оглавлению Сверлильный патрон Сверлильный патрон представляет собой зажим. Патрон имеет кулачки, которые удерживают или зажимают сверла и драйверы в дрели. Часто встречаются патроны двух типов. Один использует ключ патрона, чтобы заблокировать патрон, а второй — патрон без ключа. СОВЕТ : «Зажать сверло» или «зажать дрель» означает вставить сверло или отвертку в патрон. Вернуться к оглавлению Ключ для сверлильного патрона Ключ для патрона используется для затягивания и ослабления патрона. Чтобы использовать этот тип сверлильного патрона, в дрель вставляется сверло или отвертка. Важно убедиться, что сверло находится по центру кулачков патрона. Затем ключ поворачивают по часовой стрелке, чтобы затянуть патрон и удерживать биту или отвертку на месте. Чтобы снять сверло или отвертку, ключ поворачивают против часовой стрелки, чтобы ослабить патрон. СОВЕТ: Ключи от патрона легко потерять. Если у вашей сетевой дрели есть ключ для патрона, прикрепите его к шнуру, чтобы не потерять. Вернуться к оглавлению Быстрозажимной патрон Бесключевой патрон не требует ключа для затягивания или ослабления патрона. Вместо этого мы можем просто повернуть патрон по часовой стрелке, чтобы затянуть, и против часовой стрелки, чтобы ослабить. Преимущество бесключевого патрона в том, что нам не нужно беспокоиться о потере ключа. В моей сетевой дрели используется двухсекционный быстрозажимной патрон. Нижняя часть удерживает патрон на месте. Верхнюю часть можно повернуть, чтобы затянуть или ослабить патрон. Для использования этого быстрозажимного патрона в дрель вставляется сверло или отвертка. Важно убедиться, что сверло находится по центру кулачков патрона. Чтобы снять сверло или отвертку, возьмитесь за нижнюю часть патрона и поверните верхнюю часть против часовой стрелки, чтобы ослабить. В моей аккумуляторной дрели используется цельный быстрозажимной патрон. Все, что мне нужно сделать, это повернуть, чтобы затянуть или ослабить патрон. Мне нравится эта функция. С ним так легко менять биты! Для использования этого быстрозажимного патрона в дрель вставляется сверло или отвертка. Важно убедиться, что сверло находится по центру кулачков патрона. Затем удерживайте дрель и поверните патрон по часовой стрелке, чтобы затянуть. Чтобы снять сверло или отвертку, удерживайте сверло и поверните патрон против часовой стрелки, чтобы ослабить его. Вернуться к оглавлению Муфта Муфта сверла предотвращает дальнейшее закручивание шурупа в заготовку, когда сверло встречает определенное сопротивление. Я всегда устанавливаю муфту на дрель при заворачивании шурупов. Винты с карманами нужно закручивать только до тех пор, пока они не будут плотно прилегать, чтобы создать прочное соединение. По сути, мы хотим перестать закручивать винт, когда начинаем чувствовать некоторое сопротивление. Чрезмерное затягивание винта с потайной головкой может повредить отверстие в потайной головке, что может привести к ослаблению соединения. Чрезмерная затяжка может даже привести к тому, что винт пройдет сквозь другую заготовку. Я установил муфту на свою дрель, чтобы избежать чрезмерного затягивания карманных винтов. Для забивания шурупов с карманом в мягкую древесину, например, в сосну, моя дрель DEWALT хорошо работает, если установить сцепление на 3. Как заменить сверло: быстрые действия
Вернуться к оглавлению Что такое сверло? Проще говоря, сверло делает круглые отверстия. Спиральный хвостовик сверла удаляет материал, проходя через заготовку. Сверла специально разработаны для сверления отверстий в различных материалах, таких как дерево, металл, бетон и т. д. Сверло с зенковкой Зенковка выполняет две функции. Во-вторых, сверло с зенковкой создает V-образную форму или зенковку на поверхности заготовки. Эта V-образная или утопленная область позволяет вкручивать винт с потайной головкой заподлицо с поверхностью заготовки. Я часто использую зенковки, потому что они придают моим проектам аккуратный профессиональный вид. Сверло Форстнера Сверло Форстнера просверливает отверстия с гладкими, чистыми сторонами и плоским дном. Я часто использую зенкеры, потому что они также придают моим проектам аккуратный профессиональный вид. Кольцевая пила Кольцевая пила используется для изготовления больших круглых отверстий. Например, сверление отверстий для дверной ручки. Вернуться к оглавлению Что такое драйвер? Сверло входит в головку крепежного изделия, как винт. Это то, что мы будем использовать либо для ввинчивания винта в заготовку, либо для удаления его из заготовки. Обычные отвертки, которые мы можем видеть, это отвертки с плоской головкой, отвертки с крестообразным шлицем, квадратные отвертки и отвертки со звездочкой. Вернуться к оглавлению Как установить сверло в патрон с ключом Расходные материалы
Инструменты
Шаг 1. Отключите питание Отсоедините дрель от розетки или аккумулятор от дрели. Шаг 2. Откройте кулачки патрона Откройте кулачки патрона, повернув ключ против часовой стрелки. Шаг 3. Вставьте биту или отвертку в патрон. Закройте кулачки патрона, повернув ключ патрона по часовой стрелке. Обязательно держите биту по центру челюстей. Шаг 4. Подключите питание Подключите дрель к электрической розетке или установите аккумулятор в дрель. При необходимости просверлите отверстия или вверните винты. Шаг 5. Снимите сверло Выполните эти шаги в обратном порядке, чтобы снять сверло или отвертку. Пожалуйста, будьте осторожны. Сверла нагреваются при использовании. Вернуться к оглавлению Как установить сверло в двухсекционный быстрозажимной патрон Расходные материалы
Инструменты
Шаг 1. Отключите питание Отсоедините дрель от розетки или аккумулятор от дрели. Шаг 2. Откройте кулачки патрона Откройте кулачки патрона, удерживая нижнюю часть патрона и поворачивая верхнюю часть патрона против часовой стрелки. Шаг 3. Вставьте биту Вставьте биту или отвертку в патрон. Закройте кулачки патрона, удерживая нижнюю часть патрона и поворачивая верхнюю часть патрона по часовой стрелке. Обязательно держите биту по центру челюстей. Шаг 4. Подключите питание Подключите дрель к электрической розетке или установите аккумулятор в дрель. При необходимости просверлите отверстия или вверните винты. Шаг 5. Удалите бит Выполните эти действия в обратном порядке, чтобы снять сверло или отвертку. Пожалуйста, будьте осторожны. Сверла нагреваются при использовании. Вернуться к оглавлению Как установить сверло в цельный быстрозажимной патрон Расходные материалы
Инструменты
Шаг 1. Отсоедините дрель от розетки или аккумулятор от дрели. Шаг 2. Откройте кулачки патрона Откройте кулачки патрона, удерживая сверло и поворачивая патрон против часовой стрелки. Шаг 3. Вставьте биту Вставьте биту или отвертку в патрон. Закройте кулачки патрона, удерживая сверло и поворачивая патрон по часовой стрелке. Обязательно держите биту по центру челюстей. Шаг 4. Подключите питание Подключите дрель к электрической розетке или установите аккумулятор в дрель. При необходимости просверлите отверстия или вверните винты. Шаг 5. Снимите сверло Выполните эти шаги в обратном порядке, чтобы снять сверло или отвертку. Пожалуйста, будьте осторожны. Сверла нагреваются при использовании. Вернуться к оглавлению ВИДЕО: Как вставить сверло в дрель Посмотрите это краткое видео, чтобы узнать, как заменить сверло в дрели с ключевым патроном, двухсекционным бесключевым патроном и цельный быстрозажимной патрон. Вернуться к оглавлению Заключительные мысли Теперь вы знаете, как пользоваться дрелью и как менять сверло. Мы рассмотрели сетевые и аккумуляторные дрели. Мы видели, как использовать сверлильный патрон. И мы узнали о сверлах, шуруповертах и многом другом! Спасибо, что заглянули. Если вы нашли эту информацию полезной, не могли бы вы прикрепить ее к Pinterest? Другие мастера были бы признательны, и я тоже! Спасибо – Скотт 216 Что делать, если сверло не крутится ровноСо мной такое случается постоянно. Запускаю дрель, а сверло крутится не ровно. Вместо этого он вращается по слишком большому кривому кругу. К счастью, в большинстве случаев это легко решаемая проблема. Наиболее распространенная причина, по которой сверло не вращается прямо, заключается в том, что сверло неправильно отцентровано в патроне. Ниже приведены более подробные инструкции по правильной установке сверла, а также еще несколько причин, по которым ваша дрель не будет вращаться прямо! Примечание. Этот блог содержит партнерские ссылки. Если вы нажмете и совершите покупку, я могу получить компенсацию (без дополнительных затрат для вас). Убедитесь, что сверло правильно вставленолегко случайно зажать сверло неправильно. Вот как это выглядит: Чтобы сверло правильно отцентрировалось в патроне, поворачивайте патрон до тех пор, пока доступное отверстие не станет слишком маленьким для вставки сверла. Затем медленно открывайте отверстие, пока оно не станет достаточно большим, чтобы в него можно было вставить сверло. Поместите биту полностью в отверстие. Затяните и зафиксируйте биту на месте. Этот метод требует точного центрирования сверла, поскольку отверстие никогда не бывает достаточно большим, чтобы сверло могло перемещаться и неправильно ориентироваться. После того, как вы вставили сверло таким образом, проверьте сверло. Есть ли еще проблемы? Продолжай читать. Проверьте сверло. Это Бент?Сверла изгибаются при нагревании до высоких температур, что часто происходит во время использования. Если вы использовали сверло раньше, стоит убедиться, что проблема не в нем, поскольку, если ваше сверло погнуто, оно будет странно вращаться. Если вы считаете, что причиной может быть погнутое сверло, проверьте дрель с другим сверлом. Попробуйте несколько разных размеров — сверло большего размера с меньшей вероятностью погнется. Чтобы убедиться, что проблема не в сверле, вы также можете проверить дрель с новым сверлом. Если у сверла все еще есть проблемы, то, вероятно, дело не в сверле. Проверка патронаПредыдущие два раздела должны были устранить возможность ошибки пользователя, поэтому пришло время немного поближе взглянуть на саму дрель. Во-первых, если ваша дрель совершенно новая, подумайте о том, чтобы вернуть ее в магазин. Если у вас уже давно есть дрель, попробуйте подтянуть патрон. После продолжительного использования патрон может расшататься, что приведет к раскачиванию сверла во время использования. Чтобы затянуть патрон, извлеките аккумулятор и выберите среднее положение «выключено» переключателя направления вращения. Затем откройте кулачки патрона настолько, насколько это возможно, и вставьте в патрон шестигранный ключ. Затяните патрон вокруг шестигранного ключа. Поворот ключа вручную приведет к повороту патрона. Чтобы действительно затянуть патрон, возьмите молоток и сильно ударьте шестигранным ключом по часовой стрелке, чтобы повернуть его. Это затянет патрон на шпинделе. Удалите шестигранный ключ и проверьте свою дрель. Теперь сверло крутится прямо? Если это не решит вашу проблему, рассмотрите возможность замены патрона. Вертикально сверлильный станок 2н135: 2Н135 станок вертикально-сверлильный универсальный одношпиндельный. Паспорт, схемы, описание, характеристикиВертикально-сверлильный станок 2н135 ценаПроизводитель: Вертикально-сверлильный станок 2н135 используется для установки на предприятиях, занимающихся мелкосерийным производством изделий, а также может быть применен для благоустройства ремонтных мастерских. Функциональные возможности данного вида оборудования варьируются в зависимости от типа инструментов и приспособлений, которыми оно дополнено. Именно поэтому станок вертикально-сверлильный 2н135, цена на который доступна, по праву можно назвать оптимальным выбором. В стандартном исполнении вертикально-сверлильный станок 2н135 имеет следующие характеристики:
Отличающееся высокой степенью надежности и функциональности данное оборудование отвечает мировым стандартам качества. На станок вертикально-сверлильный 2н135 цена указана в онлайн-каталоге компании «Русстанко».
Технические характеристики станка сверлильного 2н135
назначение и применение, технические характеристики и принцип действияСверлильный станок — это приспособление, которое предназначено для формирования отверстий определённого диаметра в деталях из разнообразных материалов.
Станки для сверления позволяют создавать в деталях из различного материала глухие или сквозные отверстия. Эти технологические операции выполняются при помощи сверла — инструмента, вращательное движение которого обеспечивает удаление стружки с материала обработки. Большинство оборудования этого типа составляет промышленное сверлильное оборудование. Промышленные предприятия, выпускающие продукцию мелкими сериями или единичными экземплярами, чаще всего оснащены вертикально-сверлильными станками 2Н135. Применяя эти станки, можно одинаково успешно проводить рассверливание, сверление и развёртывание отверстий, а также зенкерование и подрезку торцов, деталей практически из любого материала. Назначение и применение сверлильного станка 2Н135Станок базовой модели 2135 представляет собой оборудование одно шпиндельного типа выпуск которого был освоен ещё в 1945 году на заводе города Стерлитамак. После этого, опираясь на данные по разработке и эксплуатации, были проделаны работы по технологической модернизации станков такого типа. Производство модели 2Н135 было запущено в 1965 году. Станки одно шпиндельные 2Н135 применяются в основном на промышленных предприятиях, которые занимаются единичным или мелкосерийным изготовлением различных деталей. В массовом выпуске изделий такие станки практически не используются. Это универсальное оборудование способно решать многие производственные задачи, такие как сверление, зенкерование, развёртывание или подрезка торцов. Оператор оборудования самостоятельно может выбирать режим подачи шпинделя и число оборотов необходимых для обработки в оптимальном режиме конкретного материала или сверления отверстия. Станок 2Н135 способен производить обработку деталей из разных материалов в огромном диапазоне габаритов. Особо высокую производительность можно достичь при работе с инструментом из высокоуглеродистой стали. Оператор имеет возможность нарезать резьбу из метчиков, осуществляя подачу шпиндельного устройства ручным способом, так как станок укомплектован реверсивной системой электрического двигателя. МодификацииБольшая популярность этого оборудования в промышленном и бытовом применении, стала первой причиной выпуска огромного количества модификаций. К таким моделям относятся:
Конструктивные особенностиКонструкция сверлильного станка состоит:
Станина агрегата сделана в виде монолитной, массивной, чугунной конструкции. Положение производительной поверхности выполняется оператором по несущей колонне вручную, путём отжима фиксирующего устройства и поворота штурвала, выполняющего функцию регулировки положения шпинделя. Для движения поверхности стола на колонне сделаны специальные направляющие пазы. А также чугунной является и опорная плита. Она имеет пустотелую конструкцию, внутри которой находится ёмкость для хранения жидкости охлаждения. Там же расположен отстойник для металлических крупных загрязнений и устройство фильтрации. На самой опорной колонне располагается электрический насос мощностью 120 Вт, который отвечает за подачу жидкости. Силовой агрегат станка располагается на верху корпуса. Шпиндельный блок и коробка передач станка располагаются в корпусе. Кинематическая схема оборудования имеет простое конструктивное решение, при котором силовой агрегат и скоростная коробка соединены прямым валом. Механическая регулировка скоростей осуществляется с помощью рукоятки, размещённой на фронтальной стороне сверлильной головки. Регулировка скорости производится вручную. Коробка осуществляет передачу скорости вращения шпинделя на двенадцати частотах. Смазка работающих элементов агрегата осуществляется с помощью плунжерного насоса в автоматическом режиме. Оператору понадобится только контролировать по датчику, который расположен на фронтальной панели, уровень количества масла. На этой модели установлена система ручной подачи шпинделя. Эта система включает в себя:
Принцип действияЭксплуатация станка в действующем режиме происходит по следующему принципу. Обрабатываемую заготовку, необходимо установить и надёжно зафиксировать на рабочей поверхности координатного стола. Шпиндель с установленным инструментом должен располагаться в крайнем положении снизу. Используя систему продольного смещения рабочего стола, шпиндель необходимо отцентрировать. Затем нужно убедиться в соосном расположении торца детали, предназначенной для обработки, и шпинделя. Исходя из кинематической возможности, в коробке скоростной передачи выбираем скорость вращения, подходящую для обработки. Включаем вертикальный электрический двигатель главного привода. После настройки кинематической схемы, осуществляется движение инструментальной головки к торцу обрабатываемого изделия, и выполняют нужную технологическую операцию. Технические характеристикиХарактеристики станка указывают на его хорошую универсальность. С помощью станка 2Н135 можно выполнять технологические операции с заготовками из разнообразных материалов, причём с размерами довольно широкого диапазона. Благодаря применению инструментов, изготовленных из быстрорежущих сталей и сплавов, имеющих высокие показатели твёрдости, это оборудование способно выполнить различные работы. Основными техническими характеристиками, от которых зависит функциональность любого оборудования, являются: ход шпинделя; наибольший диаметр сверления; максимальный промежуток между рабочим столом и шпинделем; количество оборотов в минуту; размер рабочей поверхности. Для станка 2Н135 эти параметры выглядят так:
Этот станок, как и всё другое оборудование, собранное в производственных цехах станкостроительного завода города Стерлитамак, сделан с умом и на совесть. Пластмассовые детали, которые широко используются современными производителями для удешевления своей продукции, в конструкции этого станка полностью отсутствуют. Этот фактор даёт полную гарантию, что ремонт оборудования можно будет произвести при любой его поломке. Причём обойдётся ремонт не очень дорого из-за широкого ассортимента запасных частей на рынке. Конечно, этот станок по многим техническим характеристикам уступает современному оборудованию. Сверлильные станки хороших производителей по скорости проведения операций, точности сверления, эргономичности и удобстве работы превосходят 2Н135. Основные преимущества этого оборудования — долговечность, выносливость и простой ремонт. Машинный парк — Турбоэнергоремонт : ТурбоэнергоремонтМашинный паркЧисленность станков Есть: • станки токарные с обработкой диаметром до 1000 мм и длиной до 5 м, в том числе с ЧПУ • станки токарно-карусельные с размером патрона 1200 и 2500 мм • буровое оборудование, в том числе радиальное с диаметром сверления до 50 мм • расточные станки с размером стола до 1600×1600 и высотой подъема шпиндельной бабки до 2000, а также координатно-расточные станки с размером стола до 1000 мм • станки фрезерные и долбежные, в том числе станки станочные фрезерные с размером стола 1000×4000 мм Комплектация и количество используемого оборудования, машин и работ:
Численность станков:
Станок вертикально-сверлильный 2Н135 продам на www.
Объявления
Bizator Тип предложения: SALEPOBOBLOD: 09.04.2020
Machines universal vertical drilling 2Н135, with conventional drilling diameter 35 mm, are used at на предприятиях с индивидуальным и мелкосерийным производством и предназначен для выполнения следующих операций: сверления «высверливания» зенкерования, зенкерования, развертывания и подрезания концов ножей. Длина/ширина/высота: 1030/825/2335 мм Вес: 1200 кг Производитель: Завод. Ленина Стерлитамак Год выпуска: 1971 Отправить себе/другу Версия для печатиПожаловаться
9271 Добавить в избранное Что такое файл cookie?Файл cookie — это небольшой текстовый файл, который сохраняется на вашем компьютере/мобильном устройстве, когда вы посещаете веб-сайт. Этот текстовый файл может хранить информацию, которая может быть прочитана веб-сайтом, если вы посетите его позже. Некоторые файлы cookie необходимы для правильной работы веб-сайта. Другие файлы cookie полезны для посетителя. Файлы cookie означают, что вам не нужно вводить одну и ту же информацию каждый раз при повторном посещении веб-сайта. Почему мы используем файлы cookie? Мы используем файлы cookie, чтобы обеспечить вам оптимальный доступ к нашему веб-сайту. Для защиты ваших персональных данных и предотвращения потери информации или противоправных действий применяются соответствующие организационные и технические меры. Почему мы используем файлы cookie сторонних поставщиков?Мы используем файлы cookie сторонних поставщиков, чтобы иметь возможность оценивать статистическую информацию в коллективных формах с помощью аналитических инструментов, таких как Google Analytics. Для этой цели используются как постоянные, так и временные файлы cookie. Постоянные файлы cookie будут храниться на вашем компьютере или мобильном устройстве не более 24 месяцев. Как отключить файлы cookie? Вы можете просто изменить настройки своего браузера, чтобы отключить все файлы cookie. Акустический метод неразрушающего контроля: Методы неразрушающего контроля | ГЕО-НДТАКУСТИЧЕСКИЙ КОНТРОЛЬ • Большая российская энциклопедияАвторы: А. Л. Ремизов АКУСТИ́ЧЕСКИЙ КОНТРО́ЛЬ (акустическая дефектоскопия), метод неразрушающего контроля, основанный на применении упругих колебаний (волн), возбуждаемых или возникающих в контролируемом объекте. Используются колебания в широком диапазоне частот, гл. обр. УЗ-волны, поэтому акустич. контроль часто называют ультразвуковым контролем. Для А. к. применяют пьезоэлектрич. (реже электромагнитоакустич.) преобразователи и лазеры, излучающие волны, распространяющиеся по поверхности или внутри контролируемого изделия. Параметры (или способы распространения) волн зависят от акустич. характеристик материала в месте дефекта, нарушения однородности или сплошности, наличия постороннего включения и т. п. В процессе контроля анализируется амплитуда волн, прошедших через изделие и отражённых от поверхностей изделия или дефекта, их фаза, частота, скорость распространения и др. Различают активную и пассивную группы А. к. Активный А. к. представлен рядом методов, основанных на излучении (отражении) и приёме упругих волн. В эхоимпульсном методе проводится анализ параметров волн, отражённых от дефектов и поверхностей объекта при его сканировании, с последующей регистрацией времени и интенсивности эхо-сигнала. В теневом методе предусмотрен анализ распространения волны, прошедшей через изделие, амплитуда которой уменьшается при наличии дефекта. В зеркально-теневом методе анализируют изменение амплитуды сигнала, отражённого от донной поверхности, после двукратного или многократного прохождения волн через контролируемый объект. Методы пассивного А. к. основаны на анализе процессов и (или) явлений, происходящих в контролируемом изделии, напр. вибраций или акустич. шумов, возникающих при работе объекта (вибрационно-диагностич. и шумодиагностич. методы), параметров испускаемых объектом акустич. волн (акустико-эмиссионный метод). Виды неразрушающего контроляВиды и методы неразрушающего контроля классифицируют по следующим признакам:
Основные виды неразрушающего контроля:
Кроме названных, применяется емкостный метод для контроля диэлектрических или полупроводниковых материалов. Метод электрического потенциала применяют для контроля проводников с целью определения глубины несплошности вблизи поверхности проводника. Что такое акустико-эмиссионное тестирование? Полное руководство Испытания на акустическую эмиссию (AE) — это метод неразрушающего контроля (NDT), который обнаруживает и контролирует выброс ультразвуковых волн напряжения от локализованных источников, когда материал деформируется под нагрузкой. Содержание
Нажмите здесь, чтобы посмотреть наши последние технические подкасты на YouTube .
Испытания на акустическую эмиссию проводятся путем установки небольших датчиков на испытуемый компонент. Датчики преобразуют волны напряжения в электрические сигналы, которые передаются на компьютер для сбора данных для обработки. Волны фиксируются, когда компонент подвергается внешнему воздействию, например, высокому давлению, нагрузке или температуре. По мере роста повреждения в компоненте происходит большее выделение энергии. Частоты обнаружения акустической эмиссии, активность и интенсивность акустической эмиссии, громкость контролируются и используются для оценки структурной целостности и контроля состояния компонентов. Акустическая эмиссия может рассматриваться как крошечные землетрясения, происходящие в материале. Существует два метода тестирования АЭ: переходный и непрерывный. Метод переходных процессов захватывает всплески АЭ, которые превышают пороговое значение (уровень громкости), и извлекает такие характеристики, как пиковая амплитуда, энергия сигнала и продолжительность всплеска. Затем эти функции используются для оценки состояния тестируемого компонента. Этот метод хорошо подходит для проверки конструкций на наличие таких дефектов, как трещины. Непрерывный метод фиксирует все АЭ в течение заданного периода времени, например, 1/10 секунды. Затем извлекаются такие характеристики, как средний уровень сигнала и среднеквадратичное значение (RMS). Испытания на акустическую эмиссию можно проводить в лаборатории, а также в полевых условиях как в течение относительно короткого времени, например, несколько часов, так и в течение более длительного времени, например, несколько месяцев. Методы беспроводной передачи данных позволяют анализировать данные удаленно. Акустическая эмиссия имеет много преимуществ перед другими методами. К ним относятся:
Однако у метода есть и некоторые ограничения:
Акустическая эмиссия может быть применена к целому ряду приложений и материалов. Конструкции
Машины
Процессы
Испытания на акустическую эмиссию: руководство Испытания на акустическую эмиссию — это метод контроля, в котором для выявления дефектов материалов используется испускание ультразвуковых волн напряжения. Испытания на акустическую эмиссию также называются акустической эмиссией (AE), акустическими испытаниями (AT, Acoustic NDT или AE Testing). В этом руководстве мы будем использовать эти термины взаимозаменяемо. распространенные и полезные методы неразрушающего контроля (т. е. испытания, которые позволяют инспекторам собирать данные о материалах, не повреждая их) Основные преимущества акустико-эмиссионных испытаний заключаются в том, что они позволяют инспекторам проверять всю историю нагрузки материала, не повреждая его. Исторически АЭ использовался только для осмотра и обслуживания дорогостоящих конструкций из-за высоких затрат, связанных с ним. Но новые разработки помогли снизить стоимость оборудования АЭ, и оно становится более доступным для множества задач контроля. [Неразрушающий контроль акустической эмиссии — это лишь один из методов неразрушающего контроля, который используют инспекторы. Вот меню, которое поможет вам ориентироваться в этом руководстве:
Как работает акустико-эмиссионное тестирование? При испытании на акустическую эмиссию инспектор регистрирует упругие ультразвуковые волны, проходящие через поверхность твердого материала, с помощью одного или нескольких датчиков. Когда акустическая волна распространяется по поверхности объекта или через нее, любой дефект, с которым она сталкивается, может изменить эту волну как с точки зрения ее скорости, так и с точки зрения ее амплитуды. И инспекторы ищут эти изменения, чтобы выявить наличие брака. Диапазон ультразвука, обычно используемый для испытаний на акустическую эмиссию, составляет 20 килогерц (кГц) и 1 мегагерц (МГц). (Один килогерц равен одной тысяче герц, или циклов в секунду; один мегагерц равен одному миллиону герц, или циклов в секунду). Вот несколько определений терминов, которые мы будем использовать в этой статье:
Откуда возникает акустическая эмиссия?Акустическая эмиссия возникает, когда материал находится под нагрузкой, либо из-за большой нагрузки, либо из-за экстремальных температур. Эти выбросы обычно связаны с каким-либо дефектом или повреждением конструкции, излучающей их, и именно это повреждение ищут инспекторы, когда проводят тест АЭ. Источники акустической эмиссии могут включать:
История акустико-эмиссионного контроляПо сравнению с другими методами неразрушающего контроля, такими как магнитопорошковый контроль или дефектоскопия с помощью красителя, акустико-эмиссионный контроль является относительно новым. Впервые он был использован в начале 1980-х годов для проверки инспекторами композитов с полимерной матрицей (ПМК). В датчиках, используемых для регистрации акустической эмиссии, используется пьезоэлектрический материал. Пьезоэлектричество — это производство электрических зарядов путем введения механического напряжения. Представьте, что вы с помощью крана устанавливаете гранитную плиту на крышу автобуса. Тяжелый гранит будет давить на автобус, вызывая напряжение и электрические разряды. Пьезоэлектричество было впервые открыто в 1880 году двумя братьями по имени Пьер Кюри и Поль-Жак Кюри. Но до начала 19 века он почти ни для чего не использовался.20-е годы, когда изобретатель по имени Уолтер Кэди экспериментировал с использованием пьезоэлектричества для стабилизации электронных генераторов. Примерно шестьдесят лет спустя исследователи начали тестировать пьезоэлектричество для выявления дефектов в композитах с полимерной матрицей. Сегодня датчики, используемые для тестирования акустической эмиссии, называются пьезоэлектрическими датчиками акустических волн, потому что они применяют колеблющееся электрическое поле для генерации механической волны. Затем эта волна проходит через материал и становится электрическим полем, которое может измерить инспектор. Хотя АЭ является многообещающим методом неразрушающего контроля, он все еще находится в зачаточном состоянии, и потребуются годы исследований и разработок, прежде чем он станет полностью надежным, автономным методом контроля. Одно интересное новое приложение для AE использует его для обнаружения землетрясений до того, как они действительно произойдут, но это приложение также находится на ранней стадии разработки. Общие приложения и отрасли дляИнспекторы обычно используют AE для поиска:
В частности, для волокна АЭ обычно используется для проверки на растрескивание, коррозию, расслоение и разрывы. Вот некоторые из наиболее распространенных применений акустических испытаний:
Акустико-эмиссионный контроль и ультразвуковой контроль Хотя и акустический, и ультразвуковой контроль используют ультразвук, они являются разными методами контроля. При неразрушающем контроле с помощью акустической эмиссии инспекторы «прислушиваются» к акустической эмиссии от дефектов, присутствующих в материале. AE-тестирование особенно полезно для определения того, перегружена ли конструкция, и это единственный метод неразрушающего контроля, который можно использовать во время производства. Он не требует использования какой-либо внешней энергии (в отличие от ультразвукового контроля), поскольку испытуемый материал или конструкция сама по себе испускает акустическую эмиссию. С другой стороны, при ультразвуковом контроле инспекторы посылают ультразвуковые волны через структуру материала из внешнего источника. Если волны прерываются, это свидетельствует о наличии дефекта в месте прерывания. См. наше руководство по ультразвуковому контролю, чтобы узнать, как это работает. Плюсы и минусы акустической эмиссии .Вот список плюсов и минусов акустико-эмиссионного неразрушающего контроля: Плюсы
Минусы Одним из недостатков АЭ является то, что он не всегда надежен, отчасти потому, что это относительно новый метод НК. Вот основные недостатки акустического контроля как метода неразрушающего контроля:
Метод акустической эмиссии Чтобы использовать АЭ-тестирование, инспекторы начинают с тщательной очистки поверхности объекта, который они хотят проверить. После очистки они помещают датчики акустической эмиссии на конструкцию или материал, которые они хотят проверить. Датчики должны быть установлены на конструкции с соответствующим связующим веществом, т. е. средой, способствующей передаче акустического сигнала. Для этой цели обычно используются клеи или смазка. После прикрепления датчики будут преобразовывать любые волны напряжения, присутствующие в материале, в электрические сигналы, чтобы инспектор мог их прочитать. Инспекторы передают данные с датчиков на монитор с помощью экранированных коаксиальных кабелей, отображая информацию в виде как читаемых результатов, так и необработанных данных. Как только данные доступны, инспекторы интерпретируют их, чтобы определить, где на объекте, который они проверяют, есть напряжение, и ищут возможные места дефектов, вызванных этим напряжением. Определение количества датчиков, которое потребуется инспектору для данной конструкции, производится в соответствии с несколькими факторами, включая:
Эффект Кайзера Эффект Кайзера относится к отсутствию акустической эмиссии в объекте до тех пор, пока не будет превышен уровень напряжения, приложенного к нему ранее. Этот эффект был впервые обнаружен в 1950 году, когда исследователь по имени Кайзер обнаружил, что металлы могут «запоминать» максимальную нагрузку, которой они подвергались ранее. Из-за эффекта Кайзера конструкция может находиться под разрушающим напряжением, которое инспекторы не могут определить с помощью АЭ, если это напряжение не превышает предшествующую величину нагрузки, которую испытала конструкция. Оборудование для испытаний на акустическую эмиссиюНиже приведены типы оборудования для акустической эмиссии, используемые в акустическом неразрушающем контроле. Преобразователи/сенсоры/тензодатчикиЭти устройства собирают необработанные данные акустической эмиссии. Их также называют:
Датчик, используемый на сборочной линии Наиболее распространенный набор датчиков для тестирования АЭ состоит из двух наборов встречно-штыревых датчиков, которое представляет собой устройство, состоящее из двух взаимосвязанных гребенчатых массивов металлических электродов, расположенных в виде молния. Один из преобразователей преобразует энергию электрического поля в энергию механических волн, а другой преобразователь преобразует энергию механических волн обратно в электрическое поле. Вот некоторые из различных типов акустических датчиков NDT:
Малошумящие предусилителиМалошумящий предусилитель усиливает выходной сигнал датчиков, чтобы инспекторы могли его прочитать. Эти устройства в сочетании с соответствующей подготовкой позволяют инспекторам определять местонахождение дефектов в материале, которые могут быть невидимы невооруженным глазом. Малошумящий предусилитель (источник: Stanford Research Systems) Стандарты и нормы для испытаний на акустическую эмиссию В связи с тем, что испытания на акустическую эмиссию недороги и просты, инспекторы часто используют их в информационных целях, т. е. для проверок, которые не должны соответствовать определенному кодексу или набору стандартов. Акустические испытания также широко используются для проверок на основе норм. Для этих инспекций инспекторы должны следовать определенным шагам в проведении испытаний, включая требование соблюдения письменной процедуры и того, чтобы лицо, проводящее испытания, было сертифицировано соответствующим органом по стандартизации. Вот некоторые из наиболее широко используемых кодов акустических испытаний: ASME (Американское общество инженеров-механиков)
ASTM (Американское общество испытаний и материалов)
CEN (Европейский комитет по стандартизации)
. Диск для резки металлочерепицы: Чем резать металлочерепицу: инструменты — диск, насадка на дрель, сверчокЧем резать металлочерепицу: инструменты — диск, насадка на дрель, сверчокМеталлочерепица – это современный листовой кровельный материал, который широко используется при самостоятельном монтаже покрытия для крыши. Изделие обладает множеством положительных качеств, среди которых можно отметить долговечность, прочность, надежность, атмосферостойкость, множество размеров листов металлочерепицы и богатое дизайнерское разнообразие, позволяющее получить строение с высокими эстетическими характеристиками. Именно здания, отделанные металлочерепицей можно сравнить со старинными постройками, так как крыша домов внешне напоминает кровли, покрытые классическим вариантом штучной керамической черепицы. При этом листы из металла, производимые сегодня по новым технологиям, намного легче постелить на кровлю любой конфигурации собственными силами, не обладая профессиональными навыками кровельщика. Конечно, как и в любом строительном мероприятии, установка металлочерепицы требует определенных знаний и, в первую очередь, пользователи, планирующие самостоятельный монтаж, должны знать, как правильно резать металлочерепицу. Особенности металлочерепицыЛисты металлочерепицы хоть и имеют в составе металлическую составляющую, но все же это композитный материал, который состоит из следующих слоев:
Чтобы получить листовую металлическую черепицу, производители профилируют готовый рулонный тонколистовой металл по методу холодного давления. Инструменты для раскроя металлочерепицыНесмотря на то что листовая металлическая черепица появилась на строительном рынке довольно давно, до сих пор даже профессиональные строители не пришли к единому мнению какими инструментами можно разрезать изделие, а какими категорически запрещено. Итак, резка металлочерепицы – это довольно непростой вопрос. Ведь от неправильного подбора инструментария может пострадать вся кровельная система. Дело в том, что в местах разреза могут образоваться еле заметные сколы, которые в дальнейшем приведут к тому, что покрытие утратит свою устойчивость к негативным факторам среды. Также следует знать, что существует список инструментов, рекомендованный производителем, и если его не придерживаться, то гарантия на металлочерепицу становится недействительной. Конечно, всегда можно заказать раскрой на оборудовании компании-производителя, однако, стоимость такой работы может значительно увеличить весь бюджет, а кроме того, не всегда заранее можно точно знать, какого размера понадобятся те или иные кровельные элементы. Чтобы не повредить покрытие и сохранить его защитный слой, стоит правильно разрезать листы. Прежде всего, необходимо избегать любых деформаций материала, повреждений лакового или полимерного слоя, появления трещин на поверхности декоративного покрытия, а также попадания искр на полимер, от которых он легко может расплавиться. Наиболее безопасными для работы с металлочерепицей будут следующие инструменты:
Именно перечисленные инструменты отлично режут металлочерепицу и при этом не повреждают ее. Также можно отметить, что этот перечень рекомендован большинством производителей черепицы из металла. Как можно заметить, угловая шлифовальная машина или иначе говоря болгарка, в данный список не вошла. Как правильно резать черепицу из металлаЧтобы понять, какой инструмент выбрать для резки металлочерепицы, стоит определиться со схемой кроя. То есть знать заранее потребуется ли делать множество разрезов или их будет минимум. Чем больше объем работы, тем более мощное оборудование для разрезания понадобиться. Альтернативой дисковой пиле может стать электролобзик. Это мобильный инструмент, с которым можно работать даже на высоте. Однако, стоит иметь в виду, что потребуется запастись большим количеством пилок с мелкими зубьями. Увеличенный расход связан с тем, что зубья очень активно истираются при взаимодействии с металлом. Кроме того, делать криволинейные разрезы будет довольно проблематично. Более доступным вариантом может стать насадка на дрель для резки металлочерепицы, которую также называют сверчком. Принцип работы ее схож с вырубными ножницами, то есть специальный пуансон оказывает давление на обрабатываемый участок и как бы прибивает или вырубает себе ход, в результате чего и производится разрезание. Работа требует от мастера определенной сноровки, поэтому прежде чем приступить к основному объему, стоит потренироваться на небольшом участке металлочерепицы, читайте также: расчет металлочерепицы на крышу. Подводя итог, можно отметить, что какой бы инструмент не был выбран, очень важно следить за тем, чтобы на листах черепицы не образовывались сколы, трещины, царапины, подпалины и прочие дефекты. Если же все-таки такие участки появились, то стоит обработать их специальным средством или фасадной краской в тон материала. Кроме того, желательно разрезать изделие таким образом, чтобы место среза скрывалось под другими кровельными элементами, а не находилось на открытом воздухе. Страница не найдена «
Последние посты
На сегодняшний день мебельный рынок имеет огромный выбор. На первый взгляд, даже у самого требовательного покупателя не должно возникнуть проблем […]
Далее >>
Небольшие дома часто заставляют задуматься о покупке многофункциональной мебели.
Далее >>
Строительное и промышленное оборудование продается во многих специализированных магазинах. Однако найти по-настоящему качественные товары нелегко. А если и попадается качественная […]
Далее >>
На многих трубах загородного дома можно увидеть различные дымники на кирпичную трубу. Многие из них кажутся декоративными, но на самом […]
Далее >>
Профнастил представляет собой металлический лист с рифленой поверхностью (ребрами). Его получают путем холодного прессования на специальных машинах. Ребра жесткости (гофры) […]
Далее >>
Натяжные потолки представляют собой конструкции из панелей, прикрепленных к пластиковым или металлическим прямоугольникам (профилям) под основным потолком.
Далее >>
Ремонт квартир можно назвать грандиозным делом, так как в сознании владельцев рисуются необычные образы, а новые ожидания становятся все более […]
Далее >>
Эффективность очистки поверхностных сточных вод зависит от исправности и состояния дорожных поддонов, используемых для дренажа. Мало того, что дренажный лоток […]
Далее >>
В каждом загородном доме необходима чистая вода. Добиться этого можно путем бурения скважины на своем участке. На помощь в данном […]
Далее >>
Строительство объемных модульных малоэтажных жилых домов появилось в моей стране всего 10-15 лет назад.
Далее >>
»
По категориям
7-дюймовый отрезной круг по металлуВ наличии 840
В настоящее время: $39,99
Часто покупают |
Характеристика | Значение |
Подача, м³/час | 50 |
Напор, м | 32 |
Мощность электродвигателя, кВт | 7,5 |
Обороты, об/мин | 3000 |
КПД, % | 70 |
Кавитационный запас, м | <4,0 |
Утечка, л/час | <2 |
Цена: от 5600 грн
Уточняйте характеристики, цены, размеры, сроки, получайте счёт на оплату
Звоните специалистам «СЛЭМЗ», чтобы купить насос КМ 80-65-160 или немоноблочный насос К80-65-160, получить консультацию или заказать запчасти. Будем рады помочь с подбором, сервисом и доставкой.
Технические характеристики
Моноблочный насос КМ 80-65-160 – цельная конструкция. Имеет меньшие габаритные размеры, чем стандартный консольник. Используется КМ 80-65-160 на промышленных, городских, сельскохозяйственных станциях водообеспечения. Не допускается содержание в перекачиваемой воде шлака, песка, крупных примесей.
Параметры перекачиваемой воды
Интервал рабочих температур, плотности, вязкости, кислотности для насоса консольного моноблочного КМ 80-65-160.
Примеси по массе, % | Размер частиц, мм | рН | t max, ⁰С | Плотность, кг/м 3 | Вязкость, сСт |
1 | 0.2 | 6-9 | 85 | 1000 | <36 |
Чертеж с габаритно-присоединительными размерами
Схема, чертежи и присоединительные размеры взяты из оригинального паспорта консольного КМ 80-65-160.
Насос | lxBxH, мм | LxBxH, мм | L1 | L2 | l1 | l2 | l3 | B1 | B2 | h | Dd |
КМ 80-65-160 | 105х265х312 | 635х265х312 | 176 | 100 | 70 | 70 | 140 | 212 | 310 | 132 | 300 |
Подобрать КМ 80-65-160 по надежности и цене
Перед покупкой особое внимание уделяется электродвигателю – новый, неликвидный, китайский. Ниже качество двигателя — ниже цена насоса КМ 80-65-160 и ниже надежность.
Рынок Украины разбавлен центробежными КМ 80-65-160 с хранения. Цены на неликвид и бывшие в работе ниже, но покупать нужно осторожно, так как могут внешне быть похожи на новые КМ 80-65. Важно купить консольный КМ 80 65 160 у добросовестного поставщика.
Купить насос КМ 80-65-160
Звоните специалистам «Слобожанского завода», чтобы купить насос КМ 80-65-160:
- Гарантируем лучшую цену
- Удобная система оплаты
- Доставка любым перевозчиком до 48 часов
- Консультации по техническим характеристикам
- Любые запчасти в наличии и под заказ
- Профессиональный ремонт и сервисное обслуживание
продуктов | KM Speciality Pumps
ЛИНИЯ ПРОМЫШЛЕННОЙ/ГОРНОДОБЫВАЮЩЕЙ ПРОДУКЦИИ
Работаем в этой отрасли с 1982 года
Myers | Pentair
Погруженные насосы для канализации
Погружаемые насосы с ручкой
0003 Центробежные насосы с разъемным корпусом
Насосы для работы с твердыми частицами в сухих карьерах
Pentair Fairbanks Nijhuis
Полный набор средств пожаротушения, коммунального хозяйства и пожаротушения. инфраструктурные, промышленные и коммерческие продукты HVAC в линейке Fairbanks Nijhuis
Pentair Myers | Серия Aplex
Водоотливные насосы, переносные байпасные насосы, стационарные байпасные насосы, арендуемые насосы
Новая кнопка
Беркли
Центробежные насосы
Субпудные насосы
Линейные вал и насосы пропитча Погружные электронасосы KRT
Насосы сухой установки Sewatec
Погружная мешалка Amamix
CRI-MAN
Chopper pumps, mixers, screw press separators and aerobic digesters for the processing of livestock slurry, biogas and civil/industrial effluents
Borger
Rotary Lobe Sludge Pumps
In-Line Macerators
Biocrack Disintegration System
LMI Pumps
Химические дозирующие насосы и системы
Аро | Ingersoll Rand
Мембранные насосы, поршневые насосы и агрегаты, фильтрующие регуляторы, лубрикаторы, смазочное оборудование, пневматические клапаны и цилиндры
Verder
Перистальтические шланговые и трубочные насосы Verderflex® являются идеальным решением для перекачивания жидкостей и дозирования химикатов.
От небольших насосов производства оригинального оборудования (OEM) до крупнейших в мире шланговых насосов, используемых в очень тяжелых промышленных условиях.
Grindex
Компания Grindex является мировым лидером в области электрических погружных насосов для требовательных приложений, таких как строительство, горнодобывающая промышленность и тяжелая промышленность. Мы стремимся предложить насосы для любых нужд: дренажные, шламовые, шламовые, а также насосы, одобренные MSHA, для самых сложных условий, которые только можно себе представить.
TKM
TKM Industries производит высококачественные насосы-дозаторы по индивидуальному заказу для химической, сточной и горнодобывающей промышленности.
Toyo Hevvy Pumps
Hevvy Pumps — это эволюция Toyo Pumps N.A.
Hevvy Pumps — мировой лидер в области перекачки шлама, а также предлагает продукцию для горнодобывающей, нефтегазовой, дноуглубительной и энергетической отраслей.
Насос Томпсона
Водоотливные насосы, переносные байпасные насосы, стационарные байпасные насосы, арендованные насосы
American Turbine
Вертикальные и погружные турбинные насосы
National Pump Company
Полная линейка вертикальных линейных насосов, гидроструйных и погружных насосов для сельскохозяйственного, муниципального, жилого, нефтяного и промышленно-коммерческого рынков.
Sulzer
Погружные дренажные насосы, одобренные MHSA насосы, шламовые насосы
Фонтанные насосы
Насосы с закрытой муфтой, насосы с торцевым всасыванием, погружные насосы, самовсасывающие насосы, вихревые насосы, шламовые насосы, многоступенчатые насосы и насосы Canitlever
Liberty Process
Для более чем 90 Компания Process Equipment является лидером в области экономичных винтовых насосов и запасных частей винтовых насосов в Северной Америке.
Насосы MTH
Системы питания котлов, насосные агрегаты и конденсатные агрегаты
Насосы Hydroflo
Вертикальные, погружные, пропеллерные и смешанные, центробежные, обезвоживающие, напорные головки, магнитные пускатели, насосные панели, двигатели, фонтанные и воздушные диффузорные насосы
Iwaki America
Iwaki является мировым лидером в химической передаче и измерении. Различные материалы конструкции используются для потоков до 350 галлонов в минуту для передачи и 114 галлонов в час для измерения. Iwaki может помочь вам с самыми сложными задачами по обработке химикатов
Moyno
Moyno, Inc. является мировым лидером в области проектирования и разработки винтовых насосов. Его технологические достижения привели к превосходным решениям для обработки жидкостей для широкого спектра применений, включая водоподобные жидкости и жидкости, чувствительные к сдвигу, а также вязкие, абразивные, содержащие твердые частицы шламы и шламы.
Насосы BJM
Инновационная технология перекачивания сточных вод, позволяющая отказаться от заболоченной скважины.
Stancor Pumps
Полный ассортимент насосов для широкого спектра применений, от осушения угольных шахт до перекачивания растворов, смешанных с мусором, в коммунальном хозяйстве. производит комплектные насосы для сточных вод для хозяйственно-бытовых сточных вод, отвечающие самым разнообразным требованиям.
Clay-Greene
Наши насосы используются в различных отраслях промышленности, включая сталелитейную, целлюлозно-бумажную, текстильную и пищевую промышленность.
Управление/Автоматизация
Primex
Инженерные панели управления дуги Arm Armour Curnsures EcoSmart Systems Предварительно инженерные системы управления многоотправителями
SCADATA
Scadata Skadat Приложение телеметрии
, которое можно использовать практически на любом объекте в любой отрасли. Scadata с уникальным дизайном предлагает простое в использовании готовое решение SCADA/телеметрии для мониторинга, контроля, уведомления, отслеживания тенденций и анализа больших объемов данных на месте или в удаленных местах.
MJK
Инструментария для водоснабжения и канализационной промышленности: преобразователи уровня, переключатели плавания, контроль насоса, сусплентные твердые тела/мониторинг растворенного кислорода, магнитные потоки
Danfoss
.
А.Р.И. USA Inc.
Комбинированные воздушные/вакуумные клапаны Воздушные выпускные клапаны Промывочные клапаны Водоснабжение и канализация
OCV
OCV Fluid Solutions является мировым лидером в производстве и поставке автоматических регулирующих клапанов с гидравлическим приводом и мембранным приводом.
J&S Valves
Предлагаются задвижки с упругим седлом до 108 дюймов, задвижки IBBM с металлическим седлом, прокатные двухдисковые и сплошные клиновые задвижки IBBM с металлическим седлом до 108 дюймов, поворотные обратные клапаны с металлическим и упругим седлом, резиновые обратные клапаны с утконосом, с металлическим седлом Пробковые клапаны, шаровые краны с металлическим седлом от 4 до 108 дюймов, плунжерные клапаны от 8 до 72 дюймов, промышленные дисковые затворы с проушиной или вафельные бабочки от 2 до 24 дюймов, а также пожарные гидранты с мокрым или сухим стволом.
ГЕНЕРАТОРЫ
Atlas Copco
Стремясь к инновациям, наши электрогенераторы тестируются и проектируются для обеспечения долговечности. Кроме того, мы предоставляем специальный сервис, который гарантирует вам душевное спокойствие.
Multiquip
Multiquip является одним из крупнейших и наиболее диверсифицированных производителей и поставщиков качественных продуктов и решений мирового класса для строительства, промышленности, телекоммуникаций, государственных, некоммерческих, аэрокосмических, развлекательных и нефтегазовых рынков. .
Широкий ассортимент продукции Multiquip включает легкое и среднее строительное оборудование, электрогенераторы и освещение.
ДОПОЛНИТЕЛЬНЫЕ ИЗДЕЛИЯ
Kuriyama of America
Промышленные шланги из термопластика Tigerflex™, термопластиковые шланги/трубки Kuri Tec®, резиновые шланги/промышленные шланги для воздуха/воды Alfagomma®, муфты и аксессуары Tec, выпускные шланги Металлический шланг, шланг для воздуховодов, TigerDuct™, Tigerflex®, Neo-Duct®, гидравлический шланг/фитинги Alfagomma®, термопластичный гидравлический шланг/фитинги Piranhaflex™, листовая резина промышленного назначения, шланги Piranha для канализации и струйной/боковой линии
FIT Tear Covers
Обложки изоляции клапана
Фланцевые крышки изоляции
Изоляционные покрытия
Изоляция насоса
Изоляция потока. Оборудование, датчики прогиба и другие инструменты и принадлежности.
Reel Craft
Высококачественные ролики для шланга, троса и троса
Blacoh
Sentry Pulsation Dampners
Surge Suppressors
VACUUM PUMPS & PACKAGES
Travaini Pumps
Liquid Rin & Rotary Vane
Vacuum Pumps
Tri-Lobe PD Blowers & Boosters
Почувствуйте разницу Travaini
Вакуумные системы Travaini
Наши насосы используются в различных отраслях промышленности, включая сталелитейную, целлюлозно-бумажную, текстильную и пищевую промышленность.
ANSIMAG KM Безсальниковый магнитный привод с футеровкой из ETFE
Преимущества
Надежные, безопасные, компактные и эффективные насосы с герметичным магнитным приводом ANSIMAG с футеровкой из ETFE обеспечивают ряд эксплуатационных преимуществ:

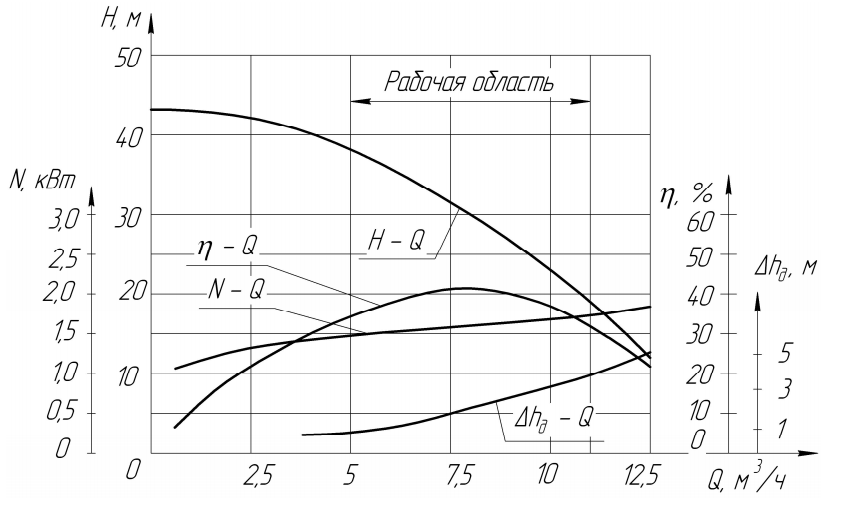
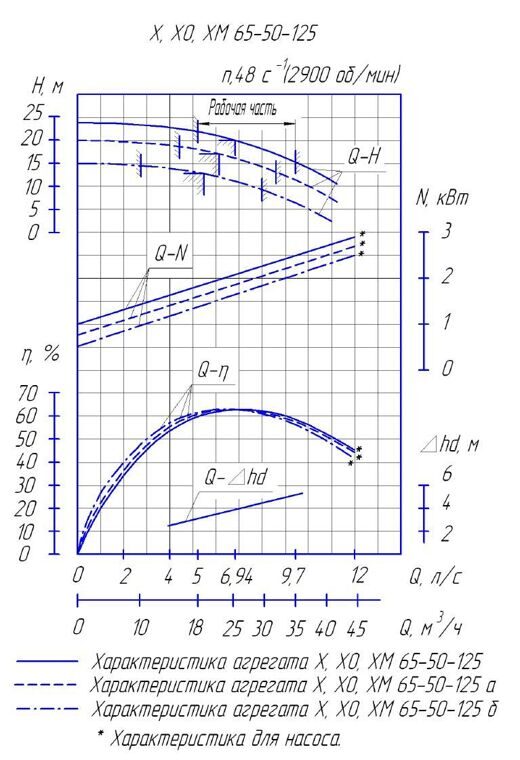
Технические характеристики
- головы до 140 футов
- ДЛЯ 147 ГОД
- Максимальная вязкость 700 SSU
- Концентрация диапазона твердых веществ до 20% мас./Мас. Размер: 1/16 ″ диаметр
- Детали двигателя C-Face и IEC B5
Пс.
. Класс 150 РФ
- Напор до 30 м
- Потоки до 27 м 3 /HR
- Максимальная мощность двигателя 5,5 кВт
- Диапазон температуры от -30 до 120 ° C
- Максимальный корпус. Сведения о двигателе NEMA C-face и IEC B5
- Диапазон твердых частиц Концентрация до 20% по весу Размер: диаметр 1,6 мм
- Конфигурация монтажа 3
- Доступные фланцы ISO PN16 и JIS 10 кг/см2
Материалы
- 0373 ETFE or PFA lined ductile iron (casing)
Performance
Cutaway
Dimensions
Power Monitor
POWER MONITOR
Installed in the Motor Control Center (MCC), монитор мощности измеряет мощность, необходимую для работы насоса. Установив верхнюю и нижнюю точки срабатывания, монитор мощности является идеальным решением для защиты насоса от:
- Сухой ход
- Low flow operation
- High flow operation
- Severe cavitation
- Magnet de-coupling
Long Coupled
LONG COUPLED
Long coupled configurations conform to ANSI B73.3 dimensions for easy replacement of mechanically герметичные насосы (использующие одну и ту же опорную плиту, муфту, защитный кожух и двигатель).
Вспомогательная защитная оболочка
ВТОРИЧНАЯ УПРАВЛЕНИЕ И ЗАЩИТА
Резервное копирование, соответствующее стандарту ASME B73.3, для контроля или локализации утечек в случае нарушения основной защитной оболочки давления.
Перекачка твердых частиц
Перекачка твердых частиц
Благодаря большому внутреннему зазору насосы ANISMAG предназначены для перекачивания жидкостей с содержанием твердых частиц до 20%+ по весу, диаметром 1/8 дюйма.
В отличие от конкурирующих конструкций, насосы ANSIMAG не используют плотно прилегающие смоченные изнутри компенсационные кольца из карбида кремния (удерживаемые на месте с помощью неметаллических стопорных колец), которые могут задерживать твердые частицы или блокировать насос.
Frequently Handled Solids:
- Inorganic Salts
- Fine Sand
- Caustic Precipitates
- TiO2(Paints & Coatings)
- Slag (Steel Pickeling)
- Carbon Black
Liquid Leak Detector
ДАТЧИК УТЕЧКИ ЖИДКОСТИ
Твердотельное устройство для обнаружения жидкости в случае утечки в основной защитной оболочке.
Подшипники, устойчивые к сухому ходу
ПОДШИПНИКИ, УСТОЙЧИВЫЕ К СУХОМУ РАБОТЕ>
Установка на насос ANSIMAG радиальных втулок из углеродного волокна снижает коэффициент трения с валом насоса, продлевая срок службы насоса в условиях нарушения технологического процесса или работы всухую.
Как из сварочного инвертора сделать полуавтомат: Полуавтомат из инвертора своими руками: схема, видео, фото
Сварочный полуавтомат своими руками из инвертора: как сделать?
Екатерина
Время чтения: 7 минут
Полуавтомат для многих мастеров не просто инструмент. Это полноценный помощник в хозяйстве и на работе. Он может понадобиться каждому умельцу: от дачника до автолюбителя. Ведь полуавтомат отлично подходит для сварки всех типов металлов практически без ограничений по толщине и составу. При этом сварка может быть и профессиональной, и любительской.
Полуавтоматы появились не так давно в массовой продаже. Сварщики старой закалки помнят, как раньше варили металл с помощью больших громоздких трансформаторов. Однако, с развитием технического прогресса инженерам удалось сконструировать компактный и удобный полуавтомат. В начале 20 века он вытеснил аппараты прошлого поколения и завоевал уважения большинства сварщиков по всему миру.
Современный полуавтомат способен выполнять различные типы сварочных работ. Это может быть MMA сварка, MIG/MAG сварка, а также TIG сварка. Все это возможно благодаря «начинке» полуавтомата. В основе аппарата лежит стандартный инвертор. Это значит, что в теории полуавтомат можно собрать самому. Конечно, используя инвертор в качестве «донора». В этой статье будет все: и основы работы полуавтомата, и переделка сварочного инвертора в полуавтомат.
Содержание статьи
- Устройство полуавтомата
- Принцип работы
- Полуавтомат из инвертора
- Способ №1
- Способ №2
- Способ №3
- Вместо заключения
Устройство полуавтомата
Устройство полуавтомата — это первое, что вам нужно изучить, если вы хотите собрать свой аппарат.
Стандартный полуавтомат состоит из двух частей (или двух блоков): силовой и подающей. Подающая часть — это просто подающее устройство для полуавтоматической сварки. Но, давайте подробнее рассмотрим устройство полуавтомата.
Силовая часть, он же силовой блок — это, по сути, инвертор. Инвертор выполняет роль источника тока. Здесь все просто. А вот подающая часть представляет собой отдельно стоящий, подключаемый подающий механизм. Подающий механизм используется для подачи проволоки. Проволока продается в бобинах и бобина вставляется прямо в подающий механизм. Ее конец выходит через сопло горелки.
Конечно, вам необязательно использовать подающий механизм, чтобы выполнить полуавтоматическую сварку. Проволоку можно подавать и вручную. Но это крайне неудобно, и в таком случае теряется вся суть полуавтоматической технологии.
Вот и все компоненты. Этого, конечно, недостаточно, чтобы сделать сварочный полуавтомат своими силами. Еще вам придется докупить детали, но они зависят от типа вашего инвертора и способа, с помощью которого вы будете переделывать его в полуавтомат. Не забудьте про комплектующие (горелка, рукав, правильно подобранное сопло и т.д.).
Принцип работы
Принцип работы полуавтомата прост. Он будет понятен даже новичку, так что внимательно изучите эту информацию. Она пригодится для сборки самодельного аппарата.
Итак, все начинается с подачи горелки в зону сварки. Горелка совмещает в себе два устройства: из своего сопла она подает защитный газ и проволоку одновременно. Количество газа сварщик регулирует вручную, а вот проволока подается в полуавтоматическом режиме (отсюда и название «полуавтомат»). Именно поэтому в процессе у сварщика всегда занята лишь одна рука. Та, что держит горелку.
Как мы уже сказали, одновременно с проволокой в сварочную зону подается газ. В смеси газов между концом проволоки и поверхностью металл образовывается электрический разряд, благодаря которому плавится заготовка и сама проволока. Расплавленный металл смешивается с расплавленной проволокой. Далее можно формировать шов.
В данном случае проволока необходима и без нее сварка просто невозможна. Газ так же нужен, он защищает сварочную ванну от кислорода, поступающего извне. Но если у вас нет возможности использовать газ, вы можете взять специальную порошковую проволоку и варить только ею.
Полуавтомат из инвертора
Существует несколько способов, как можно из инвертора сделать рабочий полуавтомат. Мы перечислим самые интересные, на наш взгляд. Вы сможете воплотить их в домашних условиях, обладая базовыми знаниями в области электротехники.
Способ №1
Чтобы сделать инверторный сварочный полуавтомат своими руками, вам понадобится «донор». Без него сделать полуавтомат просто не получится. В качестве «донора» возьмите не самый слабый инвертор для ММА сварки. Он обязательно должен быть рабочим, и без проблем выполнять обычные сварочные операции.
Вам необходимо изменить вольт-амперные характеристики выбранного вами инвертора, чтобы он мог работать в режиме полуавтоматической сварки. Для этого можно использовать ШИМ-контроллер. Однако, этот вариант очень трудоемкий и не подойдет для тех, кто не силен в электротехнике.
Поэтому, чтобы собрать сварочный полуавтомат из инвертора своими руками, мы рекомендуем сделать дроссель. Для этого подойдет дроссель от лампы дневного света. И после дросселя нужно взять напряжение на обратную связь. Посмотрите ролик ниже, где подробно рассказывается суть этого способа. Там же в ролике есть понятная схема.
Способ №2
Второй способ крайне прост и подойдет для тех, кто обладает определенной инверторнойсваркой.Дело в том, что в продаже существуют инверторы, способные переключаться в режим с жестким изменением вольт-амперной характеристики.Если вы обладатель именно такого инвертора, то можете только порадоваться за себя.Чтобы превратить такой аппарат в полуавтомат, вам достаточно докупить внешний подающий механизм.
Способ №3
Последний способ превращения из сварочного инвертора в полуавтомат своими руками потребует некоторых знаний и навыков. В этом случае вам так же понадобится инвертор-донор. Учтите, что подойдет не любой аппарат. Вам нужен инвертор с компоновкой ZX-7. На выходе у него должен быть шунт, а на «первичке» должен быть трансформатор тока. Еще лучше, если у аппарата не будет никаких дополнительных функций вроде горячего старта или форсажа дуги.
Читайте также: Как собрать сварочный аппарат своими руками?
Вместо заключения
Теперь вы знаете, как переделать сварочный инвертор в полуавтомат в домашних условиях. Такой аппарат станет отличной заменой полуавтомату заводского изготовления. Переделка обойдется недорого, и вы сможете развить свои навыки в сборке электроприборов. Самодельный полуавтомат хорошо переносит неаккуратное хранение и в целом неприхотлив к условиях работы. Еще одно преимущество самодельного аппарата — это его «начинка». Вы с точность до детали знаете, из чего он собран. Поэтому смоете быстро и недорого его починить в случае необходимости.
Но учтите, что не всегда самодельный полуавтомат из сварочного инвертора может решить все ваши трудности. Мы не рекомендуем переделывать инвертор под полуавтомат, если вы планируете использовать его как постоянный рабочий инструмент. Вы должны понимать, что самодельный аппарат может быть не таким надежным и продуманным, как заводской. И если вы будете выполнять сварку на выезде, то рискуете попасть в неприятную ситуацию. Для выполнения полупрофессиональной сварки лучше все-таки купить аппарат в магазине.
Конечно, в этой статье мы не затронули множество нюансов сборки самодельного полуавтомата. Но мы рассказали о самом главном. Инвертор можно переделать в полуавтомат, но это довольно трудоемко и самодельный аппарат будет работать немного хуже заводского. Вы должны понимать это, прежде чем примете верное решение. Желаем удачи в работе!
Похожие публикации
Сварочный полуавтомат своими руками: описание, чертежи, схемы
Сварка металлических изделий может выручить хорошего хозяина в любой момент. Поэтому сварочный аппарат можно считать незаменимой вещью в домашнем хозяйстве. С таким аппаратом можно выполнять мелкие ремонтные работы самостоятельно. Наиболее часто сварочные работы необходимы в сельской местности, где может появиться потребность в ремонте заграждений, постройке теплицы или создания любой другой металлической конструкции.
Покупка нового заводского полуавтомата может влететь в немалую копеечку, поэтому у каждого хозяина в какой-то момент возникает дилемма, что делать, покупать новый аппарат или сделать сварочный полуавтомат своими руками.
Наиболее просто своими руками сделать полуавтомат из инвертора. Если в хозяйстве есть обычный инвертор, сделать полуавтомат не составит особого труда, нужно всего лишь соблюдать инструкцию изготовления и приобрести несколько дополнительных деталей.
Сварочный полуавтомат своими руками
Но следует отметить, что для выполнения подобных работ нужно иметь базовые знания электротехники и простейших физических законов. При этом важно добросовестно подойти к изготовлению, собрать необходимый инструмент и не бросать начатое дело.
Содержание
Устройство самодельного сварочного полуавтомата
Схема сварочного полуавтомата довольно проста, и мало чем отличается от обычного сварочного аппарата. Устройство сварочного полуавтомата отличается тем, что вместо классических электродов, которые необходимо менять в процессе роботы, используется присадочная проволока. Такая особенность заключается в том, что там установлен механизм подачи сварочной проволоки, который подает ее в свариваемую область постепенно и непрерывно. Это позволяет выполнять сварочные работы непрерывно, выполняя максимально ровный и равномерный шов.
Устройство сварочного полуавтомата
При этом сопротивление такого аппарата значительно ниже в сравнении с дуговой, поэтому можно выполнить ремонт сварочного полуавтомата своими руками без особых усилий и инструментов.
При подаче проволоки в зоне сварки образуется область расплавленного металла, который моментально соединяет поверхности, буквально склеивая их, образуя максимально качественный шов высокой прочности.
С помощью самодельного сварочного полуавтомата можно сваривать практическая все типы металлических изделий, в том числе нержавеющие стали и цветные металлы. Причем техника выполнения сварочных работ довольно проста и освоить ее легко самостоятельно с помощью обучающих материалов. Но также можно пройти специальные курсы, где вас обучат технике сварки, расскажут о специфике и малейших особенностях использования полуавтомата. Посещая курсы, научиться сварочному делу может даже новичок, никогда не имеющий дело со сварочными аппаратами любого дела.
Грубо говоря, сварочный полуавтомат состоит из трех частей, электрической, ответственной за подачу тока, проволочный механизм, отвечающий за подачу присадочной проволоки, а также горелки, необходимой для создания газовой среды с помощью специального сопла.
Газовая среда необходима для создания защитного инертного облака, которое препятствует окислению расплавленного металла. Для этих целей чаще всего используют углекислый газ. Газовый баллон подключается к аппарату через входной штуцер.
Схема сварочного полуавтомата
В некоторых случаях использование баллона не обязательно, так как можно применять присадочную проволоку со специальным покрытием, которое создает самозащитную среду. Простота использования и отсутствие необходимости в применении баллона сделало полуавтомат с такой проволокой особо популярным среди домашних умельцев.
Принцип работы аппарата довольно простой, от электросети подается переменный ток, который преобразовывается в постоянный. Такую функцию выполняет специальный модуль в совокупности с трансформатором и выпрямителями.
При выполнении сварочных работ важно наблюдать за сохранением баланса силы тока, напряжения и скорости подачи присадочной проволоки. Изменение баланса в любую из сторон может привести к получению некачественного шва. Для сохранения баланса в подобных случаях используют источник питания жесткой вольт-амперной характеристики. Это позволяет в зависимости от скорости подачи присадочной проволоки регулировать напряжение и силу подаваемого тока, что позволяет добиться наиболее качественного соединения.
Необходимые инструменты и материалы
Чтобы изготовить полуавтомат из инвертора нужно подготовить следующее оборудование:
- Инвертор. При выборе этого комплектующего важно обратить внимание на такой показатель как сила формированного тока. Важно чтобы его уровень не был менее 150А.
- Механизм подачи проволоки для полуавтомата. Именно он будет отвечать за непрерывную подачу присадочной проволоки, которая должна ложиться равномерно, без рывков и замедлений.
- Горелка. Это комплектующее отвечает за плавление присадочной проволоки.
- Подающий шланг. Через этот шланг будет происходить подача присадочной проволоки к рабочей области.
- Газовый шланг. Необходимый для подачи защитного газа, обычно углекислого, в сварочную область для защиты шва от окисления.
- Катушка. На катушке должна располагаться присадочная проволока, с которой она должна подаваться без задержек.
- Электронный блок. Необходим для управления работой полуавтомата, с его помощью регулируется сила подачи тока, напряжение и скорость выполнения работы.
Большинство комплектующих можно найти высокого качества без особых усилий и использовать их без значительных изменений. Но особое внимание стоит уделить механизму подачи. Для того что сварочные работы соответствовали всем требованиям, подача проволоки через гибкий подающий шланг должна проводиться в соответствии со скоростью ее плавления.
Учитывая тот факт, что полуавтомат можно использовать для скрепления различных металлов, скорость сварки и тип присадочной проволоки может значительно варьироваться. Именно поэтому очень важно иметь возможность регулировки скорости работы подающего механизма.
Выбор проволоки зависит от целей выполнения сварочных работ и обрабатываемого металла. Присадочная проволока отличатся не только в зависимости от материала, но и от диаметра. Обычно можно найти проволоку диаметром 0,8, 1, 1,2, и 1,6 мм. Соответствующую проволоку нужно предварительно намотать на катушку. От качества выполнения этой подготовительной роботы напрямую зависит качество готового шва.
Затем катушка крепится с помощью специального крепления или самодельной конструкции к аппарату. Во время выполнения работ проволока автоматически разматывается и подается в рабочую область. Это позволяет значительно упростить и ускорить процесс соединения металлических элементов с помощью сварки, делая ее более эффективной и простой для новичков.
Изготовление сварочного полуавтомата
Блок управления состоит из микроконтроллера, необходимого для стабилизации тока. Следует отметить, что именно этот составной элемент отвечает за возможность регулировки тока во время выполнения работ.
Создание полуавтомата из сварочного инвертора
Перед использованием инвертора в качестве основы для сварочного полуавтомата нужно произвести некоторые манипуляции с его составным трансформатором. Его нужно переделать, причем переделка инвертора в полуавтомат не требует особых знаний и усилий, ее легко произвести, соблюдая лишь некоторые правила.
Все, что нужно сделать, это нанести на него дополнительный слой, который должен состоять из медной полосы и термобумаге. Отметим, что ни в коем случае для этих целей нельзя применять обычную медную проволоку, так как она в процессе работы может перегреться и вывести из строя весь аппарат.
Небольшие манипуляции также нужно провести с вторичной обмоткой. Согласно инструкции нужно нанести три слоя жести, изолированную фторопластовой лентой. Концы имеющей и нанесенной обмотки следует спаять. Такая простая манипуляция позволит значительно увеличить проводимость токов.
Очень важно чтобы инвертор был оснащен вентилятором, необходимым для охлаждения аппарата и предотвращения перегрева.
Механизм подачи проволоки
Механизм подачи проволоки для полуавтомата можно приобрести практически в каждом магазине электротехники. Но его также можно произвести самостоятельно из подручных средств. Специалисты рекомендуют для этих целей найти двигатели от автомобильных дворников, пару подходящих пластин, подшипников и ролик диаметром 2,5 см, который необходимо установить на вал двигателя. На пластины в свою очередь устанавливаются подшипники. Полученная конструкция прижимается к ролику с помощью пружины.
Схема регулятора подачи проволоки для сварочного полуавтомата
Намотанная на ролик проволока протягивается между подшипником и роликом. Все комплектующие крепятся на пластине, толщина которой не должна быть менее 1 см, изготовленную из прочного пластика. Вывод проволоки должен совпадать с местом крепления подающего шланга.
Подготовка трансформатора
Подготовка трансформатора состоит из создания дополнительной обмотки, установки необходимых комплектующих и тестового подключения к сети. Собранный сварочный аппарат должен нормально функционировать, не перегреваться после подключения к сети и что очень важно, полноценно откликаться на регулировку тока.
Также очень важно проверить изоляцию и нанести дополнительную при выявлении проблем. Затем проверить работу подающего механизма, скорость и равномерность подачи проволоки.
После подготовки и проверке рабочих узлов можно перейти к выполнению работ.
Источник питания
Питанием для полуавтоматической сварки может служить различный источник, например, ранее упомянутый инвертор, выпрямитель и трансформатор. Электрический ток поступает к сварочному аппарату из трехфазной сети. Рекомендуется при изготовлении самодельного аппарата использовать инвертор.
При соблюдении соответствующих рекомендаций и выборе качественных комплектующих можно получить качественный аппарат, сделанный своими руками, который будет служить в хозяйстве не один год и станет настоящим помощник при выполнении мелкого домашнего ремонта.
Полуавтоматический сварочный аппарат
– лучший выбор
Готовы оптимизировать процесс ручной сварки, сделать его более эффективным и постоянно улучшать конечные продукты? Обновление ваших методов сварки с помощью полуавтоматического сварочного аппарата выведет ваш производственный процесс на новый уровень, увеличив при этом вашу прибыль.
Роботизированная или полностью автоматизированная сварка не идеальна для каждого проекта — ожидаемый срок службы, стоимость инструментов и требуемая гибкость — все это факторы, которые следует учитывать. При этом полуавтоматические сварочные системы являются отличным вариантом, поскольку они могут удвоить производительность квалифицированного сварщика вручную, сохраняя при этом высокий уровень контроля.
Что такое полуавтоматическая сварка?
Полуавтоматическая сварка — это форма ручной сварки, при которой используется соответствующее оборудование, которое автоматически контролирует один или несколько режимов сварки. Оператор машины манипулирует органами управления машины, чтобы начать сварку, и наблюдает за процессом и конечным результатом для обеспечения качества. Это полезно для рабочих, поскольку требует гораздо меньше физических усилий, чем ручная сварка.
Преимущества полуавтоматических сварочных аппаратов
Области применения, в которых полуавтоматическое оборудование дает наибольшую выгоду. прошли дополнительные процессы до начала сварки. Полуавтоматические сварочные системы предлагают множество преимуществ для различных областей применения:
- Повышает безопасность рабочих
- Обеспечивает высокое качество сварки — целостность и воспроизводимость
- Увеличивает общий выход продукта
- Сокращение производства брака
- Дешевле, чем роботизированная сварка
- Может использоваться с различными методами, включая сварку TIG и сварку MIG
Готовы перейти на систему автоматической сварки? Свяжитесь с нашими инженерами по сварке сегодня.
Типы сварочных аппаратов для любого применения
Bancroft Engineering специализируется на надежных полуавтоматических сварочных аппаратах — как типовые, так и нестандартные решения. Независимо от того, какой тип сварки у вас есть, полуавтоматические сварочные аппараты обеспечивают повторяемость одним нажатием кнопки!
Токарно-сварочные станки : Наша линейка токарно-сварочных станков создана для обеспечения скорости и качества. Мы также предлагаем токарные станки со встроенными дополнительными операциями, такими как сверление, фрезерование и резка, чтобы еще больше увеличить производительность вашей производственной линии.
Вращательное сварочное оборудование : Экономичная, компактная и надежная, наша линейка ротационных сварочных аппаратов Welda-Round является отличным вариантом для сварки различных деталей и материалов.
Машины для сварки швов : Сварка швов распространена во многих отраслях промышленности после формирования из материалов цилиндров или труб. Полуавтоматические сварочные аппараты способны обеспечить равномерную консистенцию по всей длине материала.
Линейные сварочные аппараты : Системы линейной сварки предназначены для автоматизации операций прямой сварки. Эти машины обычно используются как для небольших, так и для крупных проектов.
Полуавтоматические сварочные системы Изготовлено в Ваукеша, Висконсин
Наша команда предлагает сварочное оборудование от простых машин с вращающимся и линейным приводом до многоосевых сервосистем с роботизированной интеграцией. Хотите узнать больше о Bancroft Engineering и о том, что мы можем сделать для вашего сварочного процесса? Свяжитесь с нами, чтобы обсудить ваш проект!
ЗАПРОСИТЬ ЦЕНУ
Что такое полуавтоматическая сварка? — Weldingtech.
net
от Welding Tech
При сварке полуавтоматическая сварка — это процесс, при котором скорость подачи проволоки, расход защитного газа и напряжение предварительно задаются на оборудовании. Затем оператор направляет ручной сварочный пистолет вдоль свариваемого соединения. Этот вид сварки можно использовать сплошной сплошной проволокой или электродом с флюсовой сердцевиной.
Полуавтоматическая сварка — отличный вариант для тех, кто ищет более эффективный способ сварки. Этот тип сварки может помочь повысить производительность, а также улучшить качество сварных швов. При этом типе сварки оператор меньше утомляется, что может привести к более качественному сварному шву. Кроме того, полуавтоматическая сварка может помочь сократить время, необходимое для завершения сварки.
Если вас интересует полуавтоматическая сварка, то важно правильно подобрать оборудование. На рынке представлено множество различных типов сварочных аппаратов, поэтому важно провести исследование, чтобы найти лучший аппарат для ваших нужд. Кроме того, также важно найти авторитетную компанию по поставкам сварочных материалов, которая может предоставить вам материалы и поддержку, в которых вы нуждаетесь.
Каковы примеры процессов полуавтоматической сварки?
Одним из наиболее распространенных примеров процесса полуавтоматической сварки является дуговая сварка металлическим электродом в среде защитного газа (GMAW). В этом типе сварки используется электрод, изготовленный из сплошной проволоки. Проволока подается через сварочную горелку и используется для создания дуги между электродом и заготовкой.
Является ли сварка MIG полуавтоматической?
Сварка MIG является разновидностью GMAW и поэтому представляет собой полуавтоматический процесс сварки.
Каковы преимущества полуавтоматической сварки?
Полуавтоматическая сварка имеет ряд преимуществ по сравнению с другими видами сварки:
- Одним из самых больших преимуществ является то, что она более эффективна, чем ручная сварка.
При полуавтоматической сварке оператор меньше утомляется, что может привести к более качественному сварному шву. Кроме того, полуавтоматическая сварка может помочь сократить время, необходимое для завершения сварки.
- Еще одним преимуществом полуавтоматической сварки является то, что ее можно использовать с различными материалами. Это включает в себя металлы, пластмассы и даже композиты.
- Наконец, полуавтоматическая сварка относительно проста в освоении и может использоваться теми, кто только начинает заниматься сваркой.
В чем разница между машинной и автоматической сваркой?
Автоматическая сварка — это тип сварки, при котором сварочный процесс контролируется машиной. Сюда входят:
- скорость подачи проволоки,
- расход защитного газа,
- и напряжение.
Машинная сварка, с другой стороны, представляет собой тип сварки, при котором оператор управляет машиной. При машинной сварке оператор должен вести сварочную горелку вдоль свариваемого соединения.
Состав смеси формовочной: Виды и состав формовочных смесей для литейного производства
Виды и состав формовочных смесей для литейного производства
Виды и состав формовочных смесей
От favorit-adminраздел Полезные статьи
1051
Основные требования, которым должны соответствовать формовочные смеси – это прочность и стойкость к высоким температурам. Особенно важно правильно подобрать компоненты формовочной массы при изготовлении крупных отливок. Для повышения показателей прочности и стойкости к термохимическому воздействию формы отправляют на сушку. При этом увеличивается время технологической операции, из-за чего большое распространение получили быстротвердеющие составы.
Литье стали
В технологическом процессе литья стали широко используются смеси на основе жидкого стекла. Они отлично переносят высокие температуры и используются при производстве форм для крупных изделий из стали.
Хромомагнезитовые смеси на основе жидкого стекла характеризуются немного меньшей податливостью, чем их аналоги на основе технического лигносульфоната (ЛСТ). К недостаткам данного продукта можно отнести низкий показатель газопроницаемости, из-за чего облицовочный слой не может быть боле 15 мм толщиной. Состав изготавливают из переработанного хромомагнезитового кирпича с содержанием 15 – 20% Сr2O3 и не ниже 42% MgO.
Для изготовления форм отливок с массой до 160 тонн применяются вещества на основе хромистого железняка. Типовой состав формовочной смеси для литья должен содержать не более 40% мелкой фракции железняка, а для увеличения прочности иногда добавляется до 3% ЛСТ. Толщина облицовочного слоя может достигать 150 мм.
В случае необходимости изготовления отливок с высокой чистотой поверхности применяются циркониевые смеси. Однако из-за высокой стоимости песка применяются в исключительных случаях.
Для производства отливок небольшой массы широкое применение получили песчано-глинистые смеси на основе жидкого стекла. Их применение позволяет значительно сократить продолжительность технологического цикла, повышая производительность и качество отливок. Однако при этом потребление свежих материалов несколько увеличивается.
Литье чугуна
При изготовлении чугунных отливок широко распространены формы из единой смеси. Она изготавливается из отработанной смеси с добавками свежего кварцевого песка и огнестойкой глины. При замене глины на бентонит удается повысить качество отливок. Для повышения прочности добавляется каменноугольная пыль, ЛСТ и прочие материалы. С их помощью повышаются и противопригарные показатели.
Литье бронзы
При изготовлении отливок из сплавов меди, в том числе и бронзы используются кристобалито-гипсовые формы. Для изготовления форм применяют компоненты с высокой химической очисткой. Такие материалы существенно облегчают процесс формовки, извлечения и очистки отливок. Однако есть и недостаток – входящий в состав гипс разлагается при относительно низкой температуре 650 градусов.
Состав формовочной смеси для литья алюминия
Для изготовления отливок из цветных металлов необходимо, чтобы обеспечивалась чистота поверхности изделий. К огнеупорности применяются более мягкие требования в виду сравнительно низких рабочих температур. Для этого применяются формовочные массы на основе мелкозернистого песка. Состав формовочной смеси для литья алюминия может содержать небольшое количество отработанных материалов. В качестве противопригарного покрытия используется мазут.
Стабилизация состава формовочной смеси
Оптимизация является важным элементом при контроле качества отливок. При нестабильности свойств формовочной массы снижается качество отливок, увеличивается процент брака. Для достижения оптимального качества используются лабораторные исследования, на основании которых корректируется состав.
Специальное литейное оборудование
Для приготовления формовочной массы применяется такое литейное оборудование как смесители песка, позволяющие повысить производительность хтс литья. Благодаря энергоэффективному оборудованию существенно повышается качество формовочных материалов, без значительного увеличения себестоимости продукции. К данному оборудованию относятся и манипуляторы для транспортировки и сборки форм.
Формовочные и стержневые смеси. Приготовление формовочной смеси. Свойства формовочных смесей. Состав формовочной смеси. Состав стержневой смеси.
Для приготовления смесей используются природные и искусственные материалы. Песок – основной компонент формовочных и стержневых смесей. Обычно используется кварцевый или цирконовый песок из кремнезема. Глина является связующим веществом, обеспечивающим прочность и пластичность, обладающим термической устойчивостью. Широко применяют бентонитовые или каолиновые глины.
Для предотвращения пригара и улучшения чистоты поверхности отливок используют противопригарные материалы: для сырых форм – припылы; для сухих форм – краски.
В качестве припылов используют: для чугунных отливок – смесь оксида магния, древесного угля, порошкообразного графита; для стальных отливок – смесь оксида магния и огнеупорной глины, пылевидный кварц. Противопригарные краски представляют собой водные суспензии этих материалов с добавками связующих.
Свойства формовочных и стержневых смесей
- прочность – способность смеси обеспечивать сохранность формы без разрушения при изготовлении и эксплуатации;
- поверхностная прочность (осыпаемость) – сопротивление истирающему действию струи металла при заливке;
- пластичность – способность воспринимать очертание модели и сохранять полученную форму;
- податливость – способность смеси сокращаться в объеме под действием усадки сплава;
- текучесть – способность смеси обтекать модели при формовке, заполнять полость стержневого ящика;
- термохимическая устойчивость или непригарность – способность выдерживать высокую температуру сплава без оплавления или химического с ним взаимодействия;
- негигроскопичность – способность после сушки не поглощать влагу из воздуха;
- долговечность – способность сохранять свои свойства при многократном использовании.
По характеру использования различают: облицовочные, наполнительные и единые смеси.
Облицовочная – используется для изготовления рабочего слоя формы. Содержит повышенное количество исходных формовочных материалов и имеет высокие физико-механические свойства.
Наполнительная – используется для наполнения формы после нанесения на модель облицовочной смеси. Приготавливается путем переработки оборотной смеси с малым количеством исходных формовочных материалов.
Облицовочная и наполнительная смеси необходимы для изготовления крупных и сложных отливок.
Единая – применяется одновременно в качестве облицовочной и наполнительной. Используют при машинной формовке и на автоматических линиях в серийном и массовом производстве. Изготавливается из наиболее огнеупорных песков и глин с наибольшей связующей способностью для обеспечения долговечности.
Приготовление формовочной смеси
Сначала подготавливают песок, глину и другие исходные материалы. Песок сушат и просеивают. Глину сушат, размельчают, размалывают в шаровых мельницах или бегунах и просеивают. Аналогично получают угольный порошок.
Затем подготавливают оборотную смесь. Оборотную смесь после выбивки из опок разминают на гладких валках, очищают от металлических частиц в магнитном сепараторе и просеивают.
Приготовление формовочной смеси включает несколько операций: перемешивание компонентов смеси, увлажнение и разрыхление.
Перемешивание осуществляется в смесителях-бегунах с вертикальными или горизонтальными катками. Песок, глину, воду и другие составляющие загружают при помощи дозатора, перемешивание осуществляется под действием катков и плужков, подающих смесь под катки.
Готовая смесь выдерживается в бункерах-отстойниках в течение 2…5 часов, для распределения влаги и образования водных оболочек вокруг глинистых частиц.
Готовую смесь разрыхляют в специальных устройствах и подают на формовку.
Приготовление стержневой смеси
Стержневые смеси соответствуют условиям технологического процесса изготовления литейных стержней, которые испытывают тепловые и механические воздействия. Они должны иметь более высокие огнеупорность, газопроницаемость, податливость, легко выбиваться из отливки.
Огнеупорность смеси – способность смеси и формы сопротивляться растяжению или расплавлению под действием температуры расплавленного металла.
Газопроницаемость смеси – способность смеси пропускать через себя газы (песок способствует ее повышению).
В зависимости от способа изготовления стержней смеси разделяют: на смеси с отвердением стержней тепловой сушкой в нагреваемой оснастке; жидкие самотвердеющие; жидкие холоднотвердеющие смеси на синтетических смолах; жидкостекольные смеси, отверждаемые углекислым газом.
Приготовление стержневых смесей осуществляется перемешиванием компонентов в течение 5…12 минут с последующим выстаиванием в бункерах.
В современном литейном производстве изготовление смесей осуществляется на автоматических участках.
Формовочная масса, формовое изделие и способ изготовления
Изобретение относится к формовочной массе, способу приготовления композиции и формованным изделиям из нее.
Целью изобретения является получение формовочной массы и формованных изделий, состоящих из твердого вещества в порошкообразной, гранулированной или волокнистой форме и полимеризуемого или полимеризуемого органического материала, причем указанное твердое вещество и указанный органический материал объединены таким образом, что внутренняя структура формованные изделия не имеют или могут не иметь или практически не иметь межфазной поляризации, обычно встречающейся при приложении электрического потенциала к формованным телам, изготовленным из гетерогенной смеси связующего, такого как натуральный или синтетический смолистый материал, и мелкодисперсного наполнителя, которые не ионный обмен или иное химическое соединение. Изобретение основано на концепции использования в качестве формовочной массы порошкообразного, гранулированного или волокнистого твердого вещества, к которому посредством ионного обмена присоединен полимеризуемый материал. Второй целью изобретения является изготовление формованных изделий, устойчивых к относительно высоким температурам.
При рассмотрении следующего раскрытия становится очевидным, что изобретение имеет многочисленные варианты осуществления, некоторые из которых будут подробно описаны ниже в качестве иллюстрации.
Лучшее понимание приведенных выше общих утверждений может быть получено при рассмотрении 3 конкретной композиции изобретения, такой как композиция глины, обладающей свойствами обмена оснований, например. грамм. бентонит натрия и соль полимеризуемой олефиновой карбоновой кислоты, т.е. грамм. акрилат свинца. Бентонит натрия можно обработать 3 раствором акрилата свинца, чтобы заменить комплексный катион акрилата свинца на ион натрия бентонита путем основного обмена, и полученную молекулу бентонит-акрилат свинца полимеризовать с получением продукта, имеющего превосходные электрические 4 и механические свойства, которые делают его пригодным для использования в качестве изоляционного материала или корпуса. По-видимому, в дополнение к иону акрилата свинца, который вводится в бентонит и химически соединяется с ним за счет замены оснований, дополнительный акрилат свинца может просто адсорбироваться и/или абсорбироваться на частицах бентонита, и что в полимеризации этот дополнительный акрилат свинца химически соединяется за счет полимеризации его акриловой группы с теми 56, которые связаны с бентонитом. Независимо от того, присутствует ли в формовочной смеси свободный акрилат свинца, видно, что в результате полимеризации образуется гомогенная гигантская молекула, содержащая частицы бентонита, свинцовые и акрилатные группы, все химически объединенные и свободные от межфазной поляризации.
Говоря о химической связи полимеризуемого соединения олефиновой карбоновой кислоты с ионообменным твердым веществом, мы имеем в виду химическую связь, которая может отличаться по типу или степени от химической связи, существующей между e. грамм. натрий и хлор в хлориде натрия, но который, с другой стороны, представляет собой нечто большее, чем простая механическая связь, без ионного обмена, между составляющими простой смеси, такой как гетерогенные системы органических пластмасс и наполнителей, т.е. грамм. смеси асбестовых или целлюлозных волокон, частиц слюды или кварца и т.п. с бакелитом, акриловыми смолами и т.п.
Различия, возникающие в результате такого химического связывания, по сравнению с простой механической смесью, лучше всего можно проиллюстрировать путем сравнения данных по коэффициентам мощности, полученных с формованными испытательными образцами !0, изготовленными в соответствии с настоящим изобретением и состоящими из e. грамм. 50 % свинцовой глины (описано ниже) и 50 % акрилата свинца (образец I), механическая смесь неосновной обменной молотой слюды (50 %) и акрилата свинца 50 % (образец II) и смесь !5 50 % молотой кварц и 50 % акрилата свинца (образец III).
Коэффициент мощности, проценты, 60 циклов, как получено. — Коэффициент мощности, проценты, 60 циклов, через 48 часов. кондиционирование, при 85% R. HКоэффициент мощности, %, 60 циклов, через 48 часов. при 100° C..——..—……… Измерение темп.
атЦ.
25 100 25 100 100 Образец li Образец 1n Электрические измерения с использованием электродов Aquadap диаметром 1 дюйм.
Образцы диаметром 1 M и толщиной приблизительно 100 мил. в..
Из приведенных данных видно, что химическая связь в случае образца I устраняет характерную для механических смесей межфазную поляризацию, отсутствие межфазной поляризации обусловливает низкий коэффициент мощности по сравнению с полученными с образцы II и III.
Изобретение охватывает композиции твердого вещества, к которым полимеризуемый органический материал присоединен химической связью ионообменного типа, и не исключает присутствия либо твердого материала, не связанного таким образом, либо полимеризуемого органического материала, не связанного таким образом, т. е. не исключают присутствия либо избытка твердого ионообменного вещества, либо избытка соли полимеризуемого органического материала сверх того, что объединяется посредством ионного обмена.
Следует понимать, что изобретение охватывает все виды твердых обменных материалов, включая органические, неорганические и смешанные органо-неорганические материалы. В этой связи следует обратить внимание на текущую литературу, в которой материалы, обладающие упомянутым выше типом химической связи, называются ионообменно-адсорбирующими материалами. Конкретными примерами твердых основообменных веществ, которые рассматриваются в настоящем изобретении, являются природные и синтетические основообменные материалы, такие как бентонит, цеолиты, каолинит очень тонкого помола и фенолформальдегидная смола, способная к катионному обмену.
При использовании твердых обменных веществ, которые представляют собой гидросиликаты или гидросиликаты алюминия или магния типа бентонита натрия и содержат структурную воду и склонны к гидратации и набуханию при контакте с водой, желательно использовать соль полимеризуемого олефинового карбоновая кислота, которая заменит натрий катионом, который уменьшит или предпочтительно устранит способность твердого вещества набухать в воде. Таким образом, обрабатывая такие твердые обменные вещества солью способной к полимеризации олефиновой карбоновой кислоты, такой как акрилат свинца, получают продукт, который после формования и нагревания для осуществления полимеризации обладает превосходными свойствами в отношении низкого влагопоглощения и стойкости. разрушаться при контакте с водой.
Действительный механизм реакции между твердым веществом обмена основания и полимеризуемым соединением олефиновой карбоновой кислоты точно не известен, но кажется вероятным, используя для иллюстрации акрилат свинца и бентонит натрия, что в концентрированных растворах мы можем рассматривать обмен основания как протекающий между обменным натрием бентонита и комплексом ионов o 11 H Pb-O—C=CHa+. Чистый результат в два раза; во-первых, частицы бентонита перестают набухать в воде благодаря замещению на плоскостях поверхности ионов Na+, имеющих малый ионный радиус, ионами Pb-O—C-C=CHs+, имеющими гораздо больший ионный радиус, и, во-вторых, , края и углы бентонитовых частиц покрыты ионами акрилата свинца, подвергшимися обмену основаниями. Ионы акрилата свинца не только удерживаются на поверхности, но и проникают между элементарными кристаллическими пластинами, составляющими частицу бентонита, так что при полимеризации этих групп акрилата 6u первоначально открытая текстурированная частица бентонита становится заполненной и прочно связанной между собой настоящими химическими связями. Ионы акрилата свинца, удерживаемые на поверхности отдельных частиц бентонита, служат для химической связи таких частиц между собой. Продукт обладает свойствами термореактивного или термоотверждаемого пластика.
На практике все, что необходимо сделать, это смешать бентонит натрия с раствором (желательно концентрированным) акрилата свинца, высушить смесь, размолоть полученную комковатую массу до тонкости, пригодной для формования, например, с помощью шаровой мельницы. , подвергнуть полученный порошок формованию под давлением и нагреть отформованную массу для осуществления полимеризации акрилатной группы. Эта простая процедура, однако, имеет недостаток, заключающийся в том, что ион натрия, замещенный из бентонита реакцией основного обмена, остается в формовочной смеси, вероятно, в виде акрилата натрия. Поскольку натрий хорошо гидратируется, его присутствие снижает водостойкость продукта. Ион натрия можно отделить несколькими способами, например, сначала обработав бентонит раствором соли менее гидратируемого катиона, такого как Mg или Pb, т.е. грамм. нитрата свинца и промывки обработанного бентонита от образовавшегося нитрата натрия и избытка нитрата свинца с последующей обработкой его акрилатом свинца. Или бентонит натрия можно обработать раствором акрилата свинца, отделить и промыть для удаления акрилата натрия, образовавшегося при обмене основаниями, добавить дополнительное количество акрилата свинца к промытому бентониту и полученную смесь высушить, измельчить и отлить в форму, как описано выше.
Вместо акрилата свинца, использованного выше для иллюстрации обработки бентонита, мы можем использовать соли металлов, таких как Ba, Sr и т. д., или аммиак в качестве солей замещенного аммиака (диакрилат этилендиамина) 1. e. соли, которые имеют катионы с низкой степенью гидратации и ионным диаметром не менее примерно 2,6 ангстрем, с полимеризуемыми олефиновыми карбоновыми кислотами, такими как акриловые, метакриловые, винилуксусные, кротоновые, фенилакриловые и замещенные кислоты этого типа и т. д. При обработке других твердых веществ с щелочным обменом можно использовать любое полимеризуемое соединение, которое может быть подвергнуто щелочному обмену с твердым материалом с щелочным обменом. В случае твердых обменных веществ, отличных от бентонита, размер катиона соли щелочного обмена может учитываться, а может и не приниматься во внимание, но катионы с низкой гидратацией предпочтительны для получения продуктов, обладающих хорошими водостойкими свойствами.
При обработке бентонита натрия, как описано выше, он может находиться либо в сухой форме, либо в форме суспензии в воде во время применения соли обмена основаниями. При обработке бентонитовой суспензии или геля e. грамм. нитрата свинца он флокулирует, и полученный материал можно промыть водой, а затем обработать e. грамм. раствор акрилата свинца.
Для конкретного случая, когда сначала обрабатывают Na-глину Pb(NO3)2 для образования Pb-глины, а затем добавляют акрилат свинца с образованием замененного бентонита свинцово-акрилатного комплекса, предлагается следующий механизм: Если Na-бентонит добавляется к концентрированного раствора нитрата свинца, измеряя уменьшение концентрации раствора нитрата свинца, находят, что глина обменялась на 240 м. е. (млэквивалент) Pb/100 г. из Na-глины.
Если теперь промывать глину до тех пор, пока промывочный раствор не даст результатов теста на Pb с KCrO4, и аналитически определить количество Pb, удерживаемого глиной, то окажется, что это соответствует обменной емкости 110 м. е. Pb/100 г. исходной Na-глины. Очевидно, что реакция основного обмена сильно зависит от концентрации.
Уравнения, которые, как предполагается, объясняют эти факты, следующие: — 1ty + 2NsNOa I N» I I PbNOa I—PbNOs разбавить на 1—\ (2) elay PbNOs w — ay Pb + Pb(NOi)s Таким образом образуется Pb-глина, обладающая способностью к обмену оснований полностью насыщен двухвалентными ионами Pb.
Если теперь к такой Pb-глине добавить концентрированный раствор акрилата свинца, произойдет реакция, обратная описанному выше типу 2. То есть: (3) 0 o |1\ I H — Ph-0-C-C=CH, dlay )>Pb+Pb(0-C-C=CHr) конус. — глина …. Pb-O-C-C=CH II H и содержание свинца в глине снова увеличивается до 240 м.д. е./100 г.
На практике достаточно добавить Pb-глину в раствор Pb-акрилата. При сушке этой смеси концентрация акрилата свинца достигает такой степени, что реакция (3) протекает автоматически. При полимеризации основного комплекса ионов свинцово-акрилатного комплекса, присоединенных к одной частице, с ионами, связанными с другими частицами, может образоваться гигантская молекула благодаря настоящей химической связи или мостику, который теперь существует между этими частицами глины.
Было обнаружено, что слишком маленькое соотношение акрилата свинца к бентониту в формовочной смеси, например. грамм. менее 30%, имеет тенденцию давать формованные изделия, которые проявляют некоторый эффект межфазной поляризации.
С другой стороны, когда соотношение акрилата свинца к бентониту слишком велико, например. грамм. выше 60% или 70% формованное тело, вероятно, будет демонстрировать следы, когда оно подвергается воздействию высокого электрического потенциала для проверки его изолирующих или диэлектрических свойств. Отношение акрилата свинца к бентониту примерно от 30% до 40% оказалось наиболее удовлетворительным с точки зрения продукта, который имеет оптимальные свойства в отношении межфазной поляризации, с одной стороны, и трекинга, с другой.
Будет видно, что можно получить большое разнообразие комбинаций твердого вещества, заменяемого основанием, и полимеризуемых соединений олефиновой карбоновой кислоты. Например, бентонит натрия может быть подвергнут щелочному обмену с любым катионом низкой гидратации, предпочтительно с ионным диаметром по меньшей мере около 2,6 ангстремных единиц, таким как свинец, барий, аммиак и т. д., а затем обработан той же или другой солью полимеризуемая олефиновая карбоновая кислота. В частности, свинцовый бентонит можно обрабатывать акрилатом свинца 4 или акрилатом бария, а бентонит бария можно обрабатывать акрилатом бария или акрилатом свинца и т. д.
В случае твердых обменных веществ, таких как бентонит натрия или водородный бентонит, катион соли должен, как указано, обеспечивать ненабухание водного оксида. В случае других материалов обмена основаниями это должен быть только негидратирующий ион. Продукт полимеризации должен быть нерастворимым и гидрофобным, если формованное изделие должно быть хорошим изолятором. По-видимому, соли многовалентных катионов, способные давать комплексные ионы типа Pb-O-C-CH=Ch3+0, вообще наиболее удовлетворительны.
Примеры I. 200 г. Вайомингский бентонит (состоящий в основном из глинистого минерала монтмориллонита) был диспергирован в 2000 г. водного раствора 10% по массе акрилата свинца. Затем эту смесь помещали в плоские формы и сушили в печи при 100°С в течение 24 часов. Затем высушенный материал измельчали в шаровой мельнице в течение 8 часов и полученный порошок использовали для прессования. Используемое давление формования составляло 10 000 фунтов/кв. дюйм; температура 210°С; и время в форме было 5 минут. Таким образом, были изготовлены изделия различной формы. II. 200 г. бентонита штата Вайоминг было рассеяно в объеме 2000 куб.см. 10% по весу раствора нитрата свинца, чтобы заменить свинцом все способные к обмену основаниями ионы, присутствующие в природном бентоните. Затем смесь разбавляли до 10 литров и глине давали отстояться. Надосадочную жидкость декантировали, суспензию снова разбавляли до 10 литров, и процесс повторяли десять раз. Цель этой процедуры состояла в том, чтобы удалить все присутствующие излишки нитрата свинца.
К суспензии, полученной после этой окончательной декантации, добавили 2000 г. 10-процентного раствора акрилата свинца в воде. Затем эту смесь помещали в плоские поддоны и сушили в печи при 110°С в течение 24 часов. Дальнейшая обработка идентична описанной в примере I.
III. Повторяли процесс примера II с заменой акрилата свинца равным по весу количеством акрилата бария.
IV. Повторяли процесс примера II с заменой акрилата свинца равным по массе количеством акрилата кальция.
V. Повторяли процесс примера II с заменой акрилата свинца равными по массе количествами соли этилендиамина и акриловой кислоты.
VI. 200 г. зеленого песка (природный цеолит) добавляли к 2000 г. 10% по массе раствора акрилата свинца в воде и полученную смесь измельчали в шаровой мельнице в течение 12 часов. После измельчения в шаровой мельнице смесь помещали в плоские чаши и сушили в течение 12 часов при 110°С. Высушенный материал снова подвергали измельчению в шаровой мельнице и полученный порошок прессовали прессованием. Черный, похожий на стекло материал был получен при давлении формования 10000 фунтов/кв. дюйм, температуре 200°С и времени 15 минут.
VII. Был повторен процесс примера I с заменой вайомингского бентонита равным количеством фуллеровой земли.
VIII. 200 г. модифицированной фенолформальдегидной смолы, специально приготовленной для использования в качестве катионообменника (коммерческий продукт), добавляли к 2000 г. 10% по массе раствора акрилата свинца в воде и полученную смесь измельчали в шаровой мельнице в течение 12 часов. После измельчения в шаровой мельнице смесь помещали в плоские чаши и сушили в течение 12 часов при 1100°С. Высушенный материал снова измельчали в шаровой мельнице, а полученный порошок подвергали прессованию. Используемое давление формования составляло 2000 фунтов/дюйм2; температура 1600°С; и время 5 минут.
5 Мы заявляем: 1. Формовочная масса, включающая тонкоизмельченный ионообменный состав в количестве от примерно 30 до примерно 70 частей по весу тонкоизмельченного твердого вещества основного обмена и от примерно 70 до примерно 30 частей по весу ионизируемого соль полимеризуемой олефиновой карбоновой кислоты, причем указанное соединение содержит полимеризуемую олефиновую группу указанной соли.
2. Композиция по п.1, в которой твердое вещество основного обмена представляет собой бентонит.
3. Композиция по п.1, в которой твердым основообменным веществом является бентонит натрия.
4. Композиция по п.1, в которой твердое основообменное вещество представляет собой фенолформальдегидную смолу.
5. Композиция по п.1, в которой твердое вещество основного обмена представляет собой цеолит.
6. Композиция по п.1, в которой соль представляет собой соль акриловой кислоты.
7. Композиция по п.1, в которой соль представляет собой соль амина.
8. Композиция по п.1, в которой соль представляет собой акрилат свинца.
99. Композиция по п.1, в которой соль представляет собой соль щелочноземельного металла.
10. Композиция по п.1, в которой соль представляет собой соль бария.
11. Композиция по п.1, в которой соль представляет собой соль поливалентного металла.
12. Композиция по п.1, в которой соль представляет собой соль металла, ион которого менее гидратирован, чем ион натрия.
13. Композиция по п.1, в которой твердым основообменным веществом является бентонит, а солью является акрилат свинца.
14. Композиция по п.1, в которой соединение полимеризуется.
15. Композиция по п.1, в которой смесь полимеризуют и формуют. ЭРНСТ А. ХАУЗЕР.
ЭЛИ МЕРСЕР ДАННЕНБЕРГ.
Способ получения карбамидоформальдегидных формовочных масс и изделий из них
Изобретение относится к продуктам реакции мочевины или эквивалентных веществ с формальдегидом или эквивалентными веществами.
Целью моего изобретения является равномерное получение превосходной композиции для горячего формования с повышенной пластичностью или «текучестью» и быстрым «отверждением». Другой задачей является быстрое и однородное получение формовочной массы любого заданного цвета или «потока» из одного продукта конденсации.
Еще одной целью является получение однородных формованных изделий с повышенной прочностью и долговечностью и пониженной хрупкостью путем воздействия на мою формовочную массу комбинированного воздействия тепла и давления.
При приготовлении формовочных масс на основе карбамида и формальдегида, которые быстро «схватываются» при помещении в форму и при совместном воздействии тепла и давления, возникают затруднения из-за отсутствия «растекаемости» композиции при приложении давления к этому. Это отсутствие «текучести» в форме обычно вызвано тем, что реакция в композиции зашла слишком далеко до помещения композиции в форму, т.е. т. е. композиция частично «схватывается» и с трудом принимает форму формы.
Я обнаружил, что при добавлении тиомочевины или мочевины, предпочтительно тиомочевины, в композицию перед ее помещением в форму «растекание» композиции будет увеличиваться, когда композиция подвергается комбинированному воздействию тепла и давления. в форме.
На практике тиомочевину или мочевину в ее кристаллической форме предпочтительно измельчают в порошок, а затем добавляют к формованной композиции в виде порошка. Затем формованную композицию с добавленной тиомочевиной или мочевиной тщательно перемешивают до образования однородной массы перед ее помещением в форму. Я обнаружил, что если тиомочевина или мочевина тщательно не измельчены и не смешаны с формовочной массой, формованное изделие имеет тенденцию быть «пятнистым». Доля тиомочевины или мочевины в формовочной массе может варьироваться в довольно широких пределах, но должна составлять менее 10% (десяти процентов) по массе формовочной массы и предпочтительно должна превышать ту, которая будет реагировать с присутствующим формальдегидом. в композиции, так что в формовочной массе будет присутствовать свободная тиомочевина или мочевина.
Например, мочевиноформальдегидная формовочная масса была изготовлена в соответствии с моей одновременно находящейся на рассмотрении заявкой, серийный номер 363,397, поданной 15 мая 1929 г., следующим образом: 100 г. мочевины реагировали с 200 куб. формальдегида. рН раствора составлял 6,0. Затем его смешивали с 80 г. бумаги. Смесь сушили и измельчали.
Когда указанную выше формовочную массу помещали в заданную горячую форму и подвергали заданному давлению без добавления свободной мочевины, для закрытия формы требовалось тридцать секунд.
При 100 гр. указанной формовочной массы тщательно растирали с 5 г. мочевины эту композицию помещали в ту же форму при тех же условиях, и для закрытия формы требовалось всего восемь секунд.
Тиомочевина предпочтительнее мочевины, поскольку она не только пластифицирует композицию, но и действует как ускоритель при формовании. Он идеален для этой цели, поскольку не увеличивает заметно кислотность композиции и, таким образом, не влияет на стабильность композиции. В процессе горячего формования образуется достаточное количество тиоцианата аммония, что значительно ускоряет реакцию. (При нагревании тиомочевины она образует равновесную смесь с тиоцианатом аммония.) Если используется обычная стальная форма, нежелательно добавлять намного больше тиомочевины, чем 5%, потому что она будет иметь тенденцию окрашивать форму.
Другим преимуществом является то, что из мочевины и формальдегида можно приготовить композицию, содержащую меньше требуемой пропорции мочевины к формальдегиду во время реакции и процесса сушки, при этом композиция будет более стабильной из-за избытка формальдегида. (Оптимальные пропорции, а именно от 1,05 до 1,40 моль мочевины на 2 моль формальдегида, изложены в находящейся на рассмотрении заявке № 363397.) Затем необходимое количество сухой мочевины или тиомочевины смешивают с композицией и реакционную смесь завершается в процессе формования. Например, 1 моль мочевины реагировал с 2 молями 40%-ного раствора формальдегида (рН 6,0) при кипячении до тех пор, пока испытуемый образец не мутнел при охлаждении. Около 25% воды удаляли перегонкой под вакуумом и вязкий продукт сливали в неглубокие тарелки. Затем его закаливали при 60°С до тех пор, пока он не превращался в мелкий порошок. Затем 0,25 моля тонкоизмельченной мочевины, или тиомочевины, или их смеси тщательно смешивали с ним. Это дало стабильную формовочную массу, которая легко растекалась в горячей форме и давала формованное изделие, устойчивое к атмосферным воздействиям.
Одним из недостатков использования сухой мочевины или тиомочевины является то, что, если они не будут тщательно перемешаны или измельчены с композицией, они будут иметь тенденцию быть «пятнистыми». Если для измельчения тиомочевины или мочевины использовать галечную мельницу, то будет обнаружено, что состав становится «жестче» по мере измельчения, что нейтрализует действие добавки. Другим недостатком является то, что, поскольку расход различных композиций различается и, таким образом, количество добавляемой тиомочевины или мочевины пропорционально различается, композиция будет различаться по соотношению мочевины и формальдегида. Соответственно, показанное ниже изобретение предлагает способ преодоления обоих вышеуказанных недостатков и изложено в заявке с серийным номером 5.4544, поданной 1 июня 19 г.31.
Мочевиноформальдегидные формовочные композиции, содержащие бумагу в качестве наполнителей, которые используются в коммерческих целях, описаны в моей одновременно находящейся на рассмотрении заявке с серийным номером 363397, поданной 15 мая 1929 г. Их получают реакцией мочевины с формальдегидом и затем смешивание или перетирание продукта конденсации с бумагой. Затем материал сушат, обычно с применением тепла. В процессе сушки состав частично переходит в конечное неплавкое, нерастворимое состояние. Чем ближе реакция к завершению, тем больше сопротивление композиции течению. Различные партии имеют тенденцию различаться по своей текучести даже при сушке в одних и тех же условиях из-за переменных, которые трудно, если не практически невозможно контролировать. Именно это разнообразие партий затрудняет получение формовочных масс с однородной текучестью.
Необходимо соблюдать большую осторожность, чтобы получить состав, который будет должным образом растекаться. Если материал перед измельчением недостаточно сухой, он не будет легко измельчаться. Стадия измельчения обычно достигается, когда материал еще содержит влагу. На этой стадии влажность может составлять от 5 до 10%. Если сушка зайдет слишком далеко, полученный материал будет плохо течь. Один из методов получения однородного потока состоит в том, чтобы смешать вместе большое количество порций, получив, таким образом, среднее значение, но это обременительно и не всегда удовлетворительно.
Основная цель настоящего изобретения, соответственно, состоит в том, чтобы предложить способ производства превосходной мочевиноформальдегидной формовочной массы, которая имеет по существу однородную текучесть при нагревании и давлении и дает продукты, обладающие высокой устойчивостью к кипящей воде и другими желательными характеристиками. как в таких коммерческих продуктах.
В соответствии с этим изобретением я обнаружил, что формовочная масса с однородной текучестью может быть получена простым добавлением к такой массе раствора мочевины и формальдегида или, предпочтительно, продуктов их реакции, чтобы сделать ее как пластик s5 по желанию. Другими словами, я могу нагревать свою мочевиноформальдегидную формовочную массу до тех пор, пока не буду уверен, что она сухая и легко измельчается, и независимо от того, насколько «жесткой» (т. е. устойчивой к текучести) стала композиция, я могу сделать ее любой текучей. желание, просто добавлением раствора мочевины. Чем больше такого раствора добавлю, тем более пластичной будет композиция. Удобный способ приготовления раствора мочевины – из 40% водного раствора формалина и мочевины. Присутствие воды или других растворителей не оказывает на него заметного влияния, и хотя предпочтительнее отгонять часть воды в вакууме или без него, я обнаружил, что умеренное количество воды или других растворителей не является недостатком. подарок. Раствор мочевины и формальдегида можно добавлять в количестве до 20 мас.% без заметного воздействия на формованное изделие.
Пример 1. 100 фунтов мочевины растворяли в 216 фунтах формальдегида (рН 6,0), нагретого до 30°С. Это смешивали с 50 фунтами альфа-волокна с последующей сушкой до полного нагревания и восстановлением до пудра. Для потери этого порошка в данной форме требовалось 30 секунд. Добавляли раствор, приготовленный путем нагревания 5 фунтов мочевины в 10 фунтах 40% формалина (pH 3,0) до 50°C, и теперь для закрытия той же формы требовалось 8 секунд.
Пример 2. — 100 фунтов мочевины были растворены в 216 фунтах формальдегида (pH 6,0), нагретого до 30°C. Это было смешано с 50 фунтами альфа-волокна, после чего была проведена сушка до полного нагревания и превращение в порошок.Этот порошок в данной форме требует 30 секунд для Добавляли раствор, приготовленный путем нагревания 5 фунтов тиомочевины в 10 фунтах 40% формалина (рН 3,0) до 500°С, и для закрытия той же формы требовалось 8 секунд.
Пример 3.-Вместо добавления раствора фунта мочевины в 10 фунтов формалина, как в примере 1, 15 фунтов раствора, приготовленного таким же образом (1 часть мочевины в 2 частях 40% формалина), но 25 % по весу воды удаляли под вакуумом и таким же образом уменьшали поток.
Пример 4. Вместо добавления раствора мочевины в формалине к 5 фунтам триэтаноламина добавили 5 фунтов параформальдегида и 5 фунтов мочевины. Если ее нагреть до растворения и частичной реакции, полученную смесь можно использовать для повышения пластичности карбамидоформальдегидных формовочных масс.
Пример 5. 5 фунтов мочевины и 5 фунтов параформальдегида добавляли к 5 фунтам смеси 1:1 этилового спирта и воды и смесь нагревали. Затем полученную непрозрачную жидкость смешивали с карбамидоформальдегидными формовочными массами и соответственно повышали ее пластичность.
Формовочные массы, изготовленные в соответствии с вышеприведенными примерами, обладают быстрой однородной текучестью и дают отличные формованные изделия. Продукты обладают устойчивостью к кипящей воде и другими характеристиками, необходимыми для коммерческого использования.
Конечно, сухая формовочная масса может быть приготовлена с молярной долей мочевины в конечном продукте меньше желаемой. В этом случае «умягчающая» смесь должна содержать избыток мочевины, достаточный для восполнения недостатка.
Чем больше доля формальдегида, прореагировавшего с мочевиной в высушенном составе, тем выше будет его пластичность, а чем больше доля мочевины в жидкой смеси, тем больше будет пластичность. Обогащенная формальдегидом «смягчающая» смесь может быть добавлена к формовочной массе, содержащей избыток мочевины, но обычно это нежелательно, поскольку формальдегид находится в водном растворе, а добавление любого значительного количества водного формальдегида может слишком сильно смочить порошок. Однако это можно преодолеть, используя твердые формы формальдегида, такие как параформ или гексаметилентетрамин, растворенные в небольшом количестве общего растворителя с мочевиной.
Формованные изделия, приготовленные из карбамидоформальдегидных формовочных масс, относительно хрупкие. Чтобы уменьшить хрупкость и повысить эластичность, необходимо наличие того же материала, который действует как смягчитель. Я обнаружил, что если я добавляю пластификаторы, такие как те, которые используются в других смолах для уменьшения хрупкости, они плохо смешиваются. Установлено, что после формования формованное изделие «выпотевает» из добавленных мягчителей. Некоторые вещества, растворимые в карбамидоформалиновой смеси, например глицерин, можно использовать в качестве мягчителей формованных изделий, но их растворимость в воде снижает водостойкость и атмосферостойкость изделия, поэтому их использование нежелательно.
Я обнаружил, что причина, по которой вещества, которые являются наиболее желательными смягчителями, не могут быть использованы, связана с наличием воды (или образовавшейся в процессе формования), присутствие которой снижает растворимость пластификатора. Я обнаружил, что для того, чтобы смешать мягчитель с формовочной массой мочевины и формальдегида, приготовленной обычным способом из мочевины и формалина, необходимо поддерживать очень низкое содержание воды в смеси. Если мочевино-формальдегидную формовочную массу нагреть, чтобы высушить ее и снизить содержание воды до достаточно низкого уровня, и добавить смягчитель, смесь окажется настолько жесткой, что ее ценность в качестве формовочной массы будет невысокой.
Теперь я обнаружил, что если я продолжу сушку моих мочевиноформальдегидных формовочных масс (например, приготовленных в моей одновременно находящейся на рассмотрении заявке с серийным номером 363 397, поданной 15 мая 1929 г.) до тех пор, пока содержание воды не станет очень низким, я можно добавить мою пластифицирующую смесь, состоящую из продукта конденсации карбамида с формальдегидом в присутствии неводного растворителя и пластификатора. Получение продукта конденсации мочевины с формальдегидом в жидком растворе, по существу не содержащем воды, является относительно дорогим, и в описанном выше способе необходимо использовать не более 20% этой дорогой безводной смеси. Я обнаружил, что приготовленная таким образом композиция более стабильна при стоянии, чем композиция, приготовленная непосредственно из мочевиноформалина или пластифицированная им. Такой состав имеет лучшие формовочные характеристики, 1. т. е. более равномерное течение материала при закрытой форме.
Готовое формованное изделие, содержащее мягчитель, менее хрупкое. Тот факт, что присутствует меньше воды, снижает вероятность образования пузырей на формованном изделии из-за меньшего количества газа, присутствующего во время операции формования. Кроме того, из-за небольшого количества воды требуется более высокая температура и, следовательно, требуется более короткое время в форме.
Можно использовать несколько методов приготовления жидких пластифицирующих смесей, не содержащих воды, в которых растворяется большинство обычных пластификаторов.
1. Формальдегид в растворе органического растворителя взаимодействует с мочевиной.
2. Сухая диметилолмочевина в органическом растворителе взаимодействует с формальдегидом.
3. Реакция мочевины и водного формальдегида и удаление присутствующей воды с помощью бинарных, тройных и т.д. смесей органических растворителей.
4. Параформальдегид или твердые полимеры формальдегида реагируют с мочевиной, и во время или после реакции добавляют органические растворители.
Примеры «смягчителей», которые могут быть использованы отдельно или в смеси в соответствии с данным изобретением, следующие: диэтиловый или дибутиловый эфиры щавелевой, винной или фталевой кислоты, п-толуолсульфонамидная смола, бензиловый спирт, борнеол, камфора, сложные эфиры гликоля или глицерина, ацетанилид, виниловые смолы, сложные эфиры целлюлозы и т.п.
Ниже приведен пример реализации моего изобретения: фунты параформа перемешали с 2 фунтами целлозольва. Полного решения не было.
Затем смесь подкисляли уксусной кислотой, так что испытание, проведенное с порцией, растворенной в дистиллированной воде, дало рН приблизительно 5. 6 фунтов мочевины растворяли в 1 фунте целлозольва, и этот раствор медленно выливали в кипящую смесь параформа. Кипячение продолжают до тех пор, пока раствор не станет вязким. Раствор на холоду был липким и вязким и не совсем прозрачным. При нагревании он становился подвижным, менее вязким и не проявлял склонности к желатинизации. Если 2 фунта триэтаноламина смешать со смесью параформа целлозольва, конечный полученный раствор окажется чистым и прозрачным. К смеси, в которой он был растворим, добавляли 5 фунтов дибутилфталата. Затем пластифицирующую смесь добавляли к 100 фунтам тщательно высушенной карбамидоформальдегидной формовочной массы, приготовленной в соответствии с моей вышеупомянутой одновременно находящейся на рассмотрении заявкой с серийным номером 363,39.7. рН водного экстракта пластифицированной формовочной массы составлял 6,5. До добавления пластифицирующей смеси состав был настолько «жестким», что почти не растекался в форме, а после добавления стал очень пластичным.
Использование моей жидкой пластифицирующей смеси дает множество преимуществ. Формовочную массу желательно готовить в крупнозернистой или гранулированной форме, чтобы заготовки можно было легко приготовить на машине для предварительного формования или таблеточной машине. Чтобы получить однородную смесь продукта конденсации, включающую наполнитель, пигмент, лак или краситель и, возможно, смазку для форм, обычно необходимо измельчить смесь до мелкого порошка в галечной мельнице. Теперь я обнаружил, что могу легко получить гранулированную грубую формовочную массу из смеси, пластифицированной моим жидким конденсатом, несколькими способами. Один из способов заключается в пропускании мелкодисперсного порошка через теплые (предпочтительно не выше 60°С) или холодные валки, поверхность которых покрыта жидкой пластифицирующей смесью (предпочтительно распылением). Это дает листы или секции, которые могут быть отшлифованы до желаемого размера. Другой способ состоит в том, чтобы поместить формовочную массу и жидкую пластифицирующую смесь в подходящую мельницу, миксер или жевательную резинку. Либо прикладывают тепло, либо смесь перемешивают до тех пор, пока температура не поднимется за счет тепла реакции, пока не образуется лепешка. После охлаждения и самопроизвольного или принудительного высыхания лепешка затем разбивается на гранулы требуемого размера.
Еще один способ состоит в том, чтобы взять композицию, смоченную жидкой пластифицирующей смесью, и продавить ее через сито или сито заданного размера посредством трения или перекатывания.
Еще одна особенность вышеупомянутого изобретения заключается в том, что оно адаптировано к коммерческому производству большого разнообразия продуктов экономичным способом. Например, желательно иметь в наличии формовочные массы большого количества различных цветов. Опять же желательно сделать лепной состав под любой цвет по желанию.
Тогда желательны композиции с разной текучестью в разных формах. Для высоких объектов, отформованных в глубокой матрице, больше подходит очень пластичный материал, тогда как плоская матрица потребует использования «более жесткого» состава. Подготовить и высушить каждый из этих вариантов по мере необходимости было бы утомительно и дорого, требуя частой очистки всего оборудования. Запас всех цветов был бы невозможен. Тот факт, что очень многие композиции застывают при стоянии, усугубляет трудности. Вышеупомянутое изобретение показывает способ сначала приготовить и высушить неокрашенную формовочную массу, которую можно использовать в качестве основы для быстрого приготовления формовочных масс практически любого желаемого цвета или текучести. В наличии имеется большой запас порошкообразного сухого неокрашенного материала. Когда требуется определенный цвет, пигмент, лак или краситель добавляют к неокрашенному порошку и все тщательно перемешивают. Затем добавляется пластифицирующая смесь, чтобы отрегулировать «поток» до желаемого. Так как в процессе смешивания и измельчения композиция имеет тенденцию схватываться или «застывать», лучше всего добавлять пластифицирующую смесь после процесса смешивания и измельчения. Если требуется более «жесткий» материал, чем полученный после измельчения, состав выдерживают в мельнице до тех пор, пока не будет получена желаемая «текучесть».
Вместо мочевины можно использовать тиомочевину или продукты замещения мочевины или тиомочевины, если они конкретно не ограничены, все из которых я хочу включить вместе с мочевиной в обозначение «мочевина», используемое в следующих пунктах формулы изобретения .
Формальдегид может применяться либо в виде технического водного раствора, либо в газообразном состоянии, либо в виде раствора безводного формальдегида, либо в виде полимеров.
Таким образом, хотя я описал свое усовершенствование подробно и в отношении некоторых предпочтительных форм, я не хочу ограничиваться такими деталями или формами, поскольку, как заметят специалисты в данной области техники, после понимания моего изобретения многие изменения и могут быть внесены модификации, и изобретение может быть воплощено в самых разных формах, не отступая от его сущности и объема в его более широких аспектах, и я желаю охватить все модификации, формы и усовершенствования, входящие в объем любой одной или нескольких прилагаемых пунктов формулы изобретения. ..
Настоящая заявка является продолжением части заявки с серийными номерами 422,544, поданной 22 января 1930 г., теперь патент № 2,209,943, датированный 30 июля 1940 г.; 541,544, подана 1 июня 1931 г.
Композиции, включающие легкоплавкие продукты реакции мочевины и формальдегида и латентный катализатор или ускоритель, и процесс осмоления таких продуктов при нагревании и давлении не заявлены здесь, поскольку такие композиции и процесс заявлены в моем соавторстве. — ожидающая рассмотрения заявка США, серийный номер 489, 099, подана 29 мая 1943 г.
Таким образом, описав мое изобретение, я заявляю, что оно новое и что я желаю защитить его патентным письмом: 1. Сыпучий формовочный порошок, содержащий порошкообразный твердый промежуточный продукт конденсации мочевины и формальдегида. содержащий целлюлозный наполнитель, порошок, содержащий не более 20 мас.% абсорбированной жидкости, выбранной из группы, состоящей из (а) раствора мочевины и формальдегида и (б) раствора продукта мочевино-формальдегидной реакции , причем сумма абсорбированной мочевины и формальдегида в общей массе находится в молярном отношении от 1,05 до 1,40 мочевины к 2 формальдегида, при этом указанная абсорбированная жидкость придает формовочному порошку повышенную пластичность в форме при нагревании и давлении.
2. Сыпучий формовочный порошок по п.1, в котором абсорбированная жидкость является водной.
3. Сыпучий формовочный порошок по п.1, в котором абсорбированная жидкость содержит органический растворитель.
4. Сыпучий формовочный порошок, содержащий порошкообразный твердый промежуточный продукт конденсации мочевины и формальдегида, содержащий целлюлозный наполнитель, при мольном соотношении мочевины в нем менее 1,40 моль мочевины на 2 моль формальдегида, порошок содержащая не более 20 мас.% абсорбированной жидкости, выбранной из группы, состоящей из (а) раствора мочевины и формальдегида и (б) раствора продукта мочевино-формальдегидной реакции, при этом указанная жидкость содержит достаточный избыток мочевины для получения молярного отношения мочевины к формальдегиду в общей массе от 1,05 до 1,40 мочевины к 2 формальдегида, при этом указанная абсорбированная жидкость придает формовочному порошку повышенную пластичность в форме при нагревании и давлении.
5. Сыпучий формовочный порошок, содержащий порошкообразный твердый промежуточный продукт конденсации мочевины и формальдегида, содержащий .2 целлюлозный наполнитель, молярное соотношение формальдегида в котором составляет менее 2 молей формальдегида на 1,40 моль мочевины, порошок содержащей не более 20 мас. % абсорбированной жидкости, выбранной из группы, состоящей из (а) раствора мочевины и формальдегида и (б) раствора продукта мочевино-формальдегидной реакции, при этом указанная жидкость содержит избыток формальдегида, достаточный для дают молярное отношение мочевины к формальдегиду в общей массе от 1,05 до 1,40 мочевины к 2 формальдегида, при этом указанная абсорбированная жидкость придает формовочному порошку повышенную пластичность в форме при нагревании и давлении.
6. Сыпучий формовочный порошок по п.1, в котором абсорбированная жидкость содержит мягчитель для твердого продукта конденсации.
7. Способ изготовления сыпучего формовочного порошка, включающий сушку твердого промежуточного продукта конденсации мочевины и формальдегида, содержащего целлюлозный наполнитель, до тех пор, пока твердое вещество не станет легко измельчаемым, измельчение указанного твердого продукта конденсации с образованием порошка и смешивание указанного порошка с не более 20% по массе жидкости, выбранной из группы, состоящей из (а) раствора карбамида и формальдегида и (б) раствора продукта карбамидоформальдегидной реакции, суммы абсорбированных мочевины и формальдегида в общая масса находится в молярном отношении от 1,05 до 1,40 мочевины к 2 формальдегида, при этом указанная абсорбированная жидкость придает формовочному порошку повышенную пластичность в форме под воздействием тепла и давления.
Мм2 в м2 калькулятор: Онлайн калькулятор мм2 в м2. Удобный и быстрый конвертер
Конвертер величин / Калькулятор единиц измерения
Изначальное значение:
Калькулятуру классических единиц измерения:
Категории измерений:Активность катализатораБайт / Битвес ткани (текстиль)ВремяВыбросы CO2Громкость звукаДавлениеДинамическая вязкостьДлина / РасстояниеЁмкостьИмпульсИндуктивностьИнтенсивность светаКинематическая вязкостьКоличество веществаКулинария / РецептыМагнитный потокмагнитодвижущая силаМасса / ВесМассовый расходМолярная концентрацияМолярная массаМолярный объемМомент силыМощностьМощностью эквивалентной дозыМузыкальный интервалНапряжённость магнитного поляНефтяной эквивалентОбъёмОбъёмный расход жидкостиОсвещенностьПлоский уголПлотностьПлотность магнитного потокаПлощадьПоверхностное натяжениеПоглощённая дозаПриставки СИпроизведение дозы на длинупроизведения дозы на площадьПроизводительность компьютера (флопс)Производительность компьютера (IPS)РадиоактивностьРазмер шрифта (CSS)Световая энергияСветовой потокСилаСистемы исчисленияСкоростьСкорость вращенияСкорость передачи данныхТекстильные измеренияТелесный уголТемператураУскорениеЧастей в . ..ЧастотаЭквивалентная дозаЭкспозиционная дозаЭлектрическая эластичностьЭлектрический дипольный моментЭлектрический зарядЭлектрический токЭлектрическое напряжениеЭлектрическое сопротивлениеЭлектрической проводимостиЭнергияЯркостьFuel consumption
Изначальное значение:
Изначальная единица измерения:Ангстрем [Å]Астрономическая единица [AU]аттометр [ам]гектометр [гм]Гигаметр [Гм]декаметр [дам]дециметр [дм]Дюйм [in]Икс-единица — СигбанКабельтовКвартеркилометр [км]ЛинкЛокоть (британский)Мегаметр [Мм]Метр [м]Метрическая милямикрометр [мкм]миллиметр [мм]Миль — тыcячМиля (международная) [mi]Миля (США)Морская миляМорская саженьнанометр [нм]Парсек [pc]Перчпикометр [пм]Планковская длинаПольРимская миляРодсантиметр [см]Световые годыСветовые дниСветовые минутыСветовые секундыСветовые часыСтатутная миляТвипфемтометр [фм]ФурлонгФут [ft]Чейн [ch]Ярд
Требуемая единица измерения:Ангстрем [Å]Астрономическая единица [AU]аттометр [ам]гектометр [гм]Гигаметр [Гм]декаметр [дам]дециметр [дм]Дюйм [in]Икс-единица — СигбанКабельтовКвартеркилометр [км]ЛинкЛокоть (британский)Мегаметр [Мм]Метр [м]Метрическая милямикрометр [мкм]миллиметр [мм]Миль — тыcячМиля (международная) [mi]Миля (США)Морская миляМорская саженьнанометр [нм]Парсек [pc]Перчпикометр [пм]Планковская длинаПольРимская миляРодсантиметр [см]Световые годыСветовые дниСветовые минутыСветовые секундыСветовые часыСтатутная миляТвипфемтометр [фм]ФурлонгФут [ft]Чейн [ch]Ярд
Перевод единиц измерения никак нельзя назвать банальной задачей:
Миллиметр, сантиметр, дециметр, метр, километр, миля, морская миля, фут, ярд, дюйм, локоть, парсек и световой год.
С помощью этих измерений могут быть рассчитаны расстояния. И это далеко не все возможные измерения, а лишь наиболее распространенные из них.
В случаях измерений площади (квадратный метр, квадратный километр, ар, гектар, морган, акр и другие), температуры
(в градусах по Цельсию, по Кельвину, по Фаренгейту), скорости (м/с, км/час, миль/ч, узлы, мах), веса
(центнер, килограмм, метрическая тонна, американская тонна, стандартная тонна, фунт и другие) и объема
(кубический метр, гектолитр, английский галлон жидкости, американский жидкий галлон, американский сухой галлон, баррель и другие)
ситуация не намного лучше. А если всего этого вам показалось мало — большинство из этих единиц также имеют подразделения и высшие единицы
(например, милли-, санти-, деци-). Короче говоря, хаос, в котором так трудно разобраться без помощи справочника или других средств.
Данный калькулятор единиц измерения идеально подходит для перевода данных единиц.
Калькулятор-конвертор для единиц измерения. Способен преобразовать огромное количество единиц измерения.
Калькулятор для расчета площади
Данный онлайн-калькулятор позволяет рассчитать площадь различных геометрических фигур, таких как:
|
|
Для удобства расчетов вы можете выбрать единицу измерения (миллиметр, сантиметр, метр, километр, фут, ярд, дюйм, миля). Также полученный результат можно конвертировать в другую единицу измерения путем выбора её из выпадающего списка.
Полезные калькуляторы
Конвертер единиц площади
|
Конвертер единиц длины
a=ммсммкмфутярддюйммиля | |
b=ммсммкмфутярддюйммиля |
Вычислить
Способ нахождения площади треугольника:
По трем сторонамПо одной стороне и высоте, опущенной на эту сторонуПо двум сторонам и углу между ними
a=ммсммкмфутярддюйммиля | |
b=ммсммкмфутярддюйммиля | |
c=
|
Вычислить
Рассчитать площадь круга, если известен:
радиус круга – r
диаметр круга – d
r=ммсммкмфутярддюйммиля |
Вычислить
Способ нахождения площади параллелограмма:
По основанию и высоте параллелограммаПо двум сторонам и углу между нимиПо двум диагоналям и углу между ними
a=ммсммкмфутярддюйммиля | |
h=ммсммкмфутярддюйммиля | |
|
Вычислить
Многоугольник с числом сторон n и длиной стороны аМногоугольник с числом сторон n, вписанный в окружность радиуса RМногоугольник с числом сторон n, описанный вокруг окружности радиуса r
n= 3456789101112131415 | |
a= ммсммкмфутярддюйммиля |
Вычислить
a=ммсммкмфутярддюйммиля | |
b=ммсммкмфутярддюйммиля |
Вычислить
Рассчитать площадь сектора круга, если известен:
угол сектора – θ
длина дуги – L
r=
| |
θ=
|
Вычислить
Способ нахождения площади трапеции:
По двум основаниям a,b и высоте hПо двум основаниям a,b и боковым сторонам c,d
a=ммсммкмфутярддюйммиля | |
b=ммсммкмфутярддюйммиля | |
h=
| |
|
|
Площадь — численная характеристика двумерной (плоской или искривлённой) геометрической фигуры.
Метрические единицы измерения площади: | |
Квадратный метр, производная единица системы СИ 1 м2 = | 1 са (сантиар) |
Квадратный километр — 1 км2 = | 1 000 000 м2 |
Гектар — 1 га = | 10 000 м2 |
Ар (сотка) — 1 а = | 100 м2 (сотка как правило применяется для измерения земельных участков и равна 100 м2 или 10м х 10м) |
Квадратный дециметр, 100 дм2 = | 1 м2; |
Квадратный сантиметр, 10 000 см2 = | 1 м2; |
Квадратный миллиметр, 1 000 000 мм2 = | 1 м2. |
Данный онлайн-калькулятор удобен при расчете площадей помещений и земельных участков.
2 по простой формуле.
Читайте дальше!
Знаете ли вы!
- 1 квадратный миллиметр (мм2) равен 1e-6 квадратных метров (м2)
- 1 квадратный метр (м2) равен 1e+6 квадратных миллиметров (мм2)
Квадратный миллиметр в Квадратный метр Формула:
Формула (мили в ярды):
м2 = мм2 ÷ 1 000 000
пример ниже, чтобы получить представление об этих преобразованиях единиц площади поверхности (шаг за шагом). 92?
Необходимо преобразовать квадратный миллиметр (мм2) в квадратный метр (м2), есть два способа, один из которых вам просто нужно вставить значения в приведенный выше конвертер или, если вы хотите сделать это вручную, то приведенный ниже пример помогает вам!
Пример преобразования квадратных миллиметров (мм2) в квадратные метры (м2):
Проблема: преобразовать 60 000 квадратных миллиметров в м2?
Решение:
Шаг 1 (формула):
- м2 = мм2 ÷ 1 000 000
92
Преобразование квадратных мм в квадратные м
Онлайн-калькулятор для преобразования квадратных миллиметров в квадратные метры (мм 2 в м 2 ) с формулами, примерами и таблицами. Наши преобразования обеспечивают быстрый и простой способ преобразования между единицами площади.
Калькулятор конвертации
Введите значение в калькулятор конвертации ниже.
Преобразование мм
2 в м 2
СОВЕТ: Если результат вашего преобразования равен 0, попробуйте увеличить «Десятичные числа».
Как преобразовать мм 2 в м 2 : Введите значение в поле мм 2 и нажмите кнопку «Рассчитать квадратный м». Ваш ответ появится в поле m 2 .
Определения преобразования
Ниже приведен список определений, относящихся к преобразованию квадратных миллиметров в квадратные метры.
Что такое квадратный миллиметр (мм
2 )?
Квадратный миллиметр — единица площади в метрической системе. Символ квадратного миллиметра — мм 9.0219 2 . В одном квадратном метре 1 000 000 квадратных миллиметров. Квадратный миллиметр рассчитывается как площадь квадрата, каждая сторона которого равна 1 миллиметру. Международное написание этой единицы измерения – квадратный миллиметр.
Что такое квадратный метр (м
2 )?
Квадратный метр — единица площади в метрической системе. Символ квадратного метра: м 2 . В одном квадратном миллиметре 0,000001 квадратных метра. Квадратный метр рассчитывается как площадь квадрата, каждая сторона которого равна 1 метру. Международное написание этой единицы измерения – квадратный метр.
Формула преобразования
Давайте подробнее рассмотрим формулу преобразования, чтобы вы могли сами выполнить эти преобразования с помощью калькулятора или старомодного карандаша и бумаги.
Формула для преобразования мм 2 в м 2 выглядит следующим образом:
м 2 = мм 2 ÷ 1 000 000
Далее рассмотрим пример преобразования
1. участвуют в переводе квадратных миллиметров в квадратные метры (мм 2 до m 2 ).
Пример преобразования квадратных миллиметров в квадратные метры
Задача: преобразовать 40 000 квадратных миллиметров в квадратные метры (показать работу) Формула: мм 2 ÷ 1 000 000 = м 2 Вычисления: 40 000 мм 2 ÷ 1 000 000 = 0,04 м 2 Результат: 40 000 мм 2 равно 0,04 м 2
Таблица пересчета
Для быстрого ознакомления ниже приведена таблица пересчета, которую можно использовать для пересчета из мм 2 к м 2 .
Квадратные миллиметры в Квадратные метры. Таблица преобразования
квадратных миллиметров (мм 2 ) | квадратных метров (м 2 ) | |||
---|---|---|---|---|
1 mm 2 | 0.000001 m 2 | |||
2 mm 2 | 0.000002 m 2 | |||
3 mm 2 | 0.000003 m 2 | |||
4 mm 2 | 0.000004 m 2 | |||
5 mm 2 | 0.000005 m 2 | |||
6 mm 2 | 0.000006 m 2 | |||
7 mm 2 | 0.000007 m 2 | |||
8 mm 2 | 0.000008 m 2 | |||
9 mm 2 | 0.000009 m 2 | |||
10 mm 2 | 0.![]() | |||
20 mm 2 | 0.00002 m 2 | |||
30 mm 2 | 0.00003 m 2 | |||
40 mm 2 | 0.00004 m 2 | |||
50 mm 2 | 0.00005 m 2 | |||
75 mm 2 | 0.000075 m 2 | |||
100 mm 2 | 0.0001 m 2 | |||
250 mm 2 | 0.00025 m 2 | |||
500 mm 2 | 0.0005 m 2 | |||
750 мм 2 | 0,00075 M 2 | |||
1000 мм 2 | 0,0011 M 2 2 | 0,001 M 2 2 | 0,001 М | .0076 0.0025 m 2 |
5,000 mm 2 | 0.![]() Притупление кромок: Притупление кромкиДля чего делают притупление кромокПодготовка деталей под сварку заключается в разделке кромок и очистке мест сварки от ржавчины, окалины, жира и т. п. Кромки разделывают для улучшения условий сварки. В соединении с разделкой (односторонней и двусторонней) часть кромки оставляют нескошенной (притупление). При односторонней разделке притупление расположено внизу соединения, при двусторонней — в середине соединения. Притупление необходимо для того, чтобы при прихватке и сварке быстро расплавляющиеся острые кромки не создавали широкую щель, которую трудно заваривать. Отсутствие притупления приводит к образованию прожогов при сварке по стыку соединения. Форма разделки кромок характеризуется углом их скоса, размером притупления и зазором между свариваемыми кромками. Она зависит от типа сварного соединения, толщины свариваемых элементов и применяемого способа сварки. При толщине свариваемых элементов до 5 мм скос кромок не требуется. В элементах толщиной 5—30 мм и более применяют V-образную разделку с суммарным углом скоса 60—80°. Не нашли то, что искали? Воспользуйтесь поиском: Лучшие изречения: Только сон приблежает студента к концу лекции. А чужой храп его отдаляет. 78.85.5.182 © studopedia.ru Не является автором материалов, которые размещены. Но предоставляет возможность бесплатного использования. Есть нарушение авторского права? Напишите нам | Обратная связь. Отключите adBlock! Притупление – кромкаПритупление кромок 1 5 – 2 мм, зазор в стыке 1 5 – 2 5 мм в зависимости от толщины стенки трубы. [1] Притупление кромок предохраняет от прожога нижние грани стыка при наложении первого слоя и обычно принимается равным 2 – 3 мм для ручной сварки и 4 – 6 мм для автоматической. [3] Притупление кромок при всех типах разделок составляет 1 – 2 мм, а зазор в стыке – 2 мм. [4] Притупление кромок не допускается. [6] Притупление кромок выполняют для обеспечения устойчивого ведения процесса сварки при выполнении корневого слоя шва. Отсутствие притупления способствует образованию прожогов при сварке. [8] Притупление кромок должно составлять примерно 1 0 – 1 5 мм. Притупление кромок делают для того, чтобы избежать прожога при сварке. [10] Притупление кромок при всех типах разделок составляет 1 – 2 мм, а зазор в стыке – 2 мм. [11] Притупление кромок выполняется для обеспечения устойчивого ведения процесса сварки при выполнении корневого шва. Отсутствие i притупления способ – – ствует образованию прожогов при сварке. [13] Притупление кромок выполняется для обеспечения устойчивого ведения процесса сварки при выполнении корневого шва. [15] Перед выполнением сварочных работ следует произвести этапы подготовки рабочего изделия. Одной из подобных процедур является разделка кромок. Суть данного процесса заключается в придании кромкам, подлежащих свариванию, необходимых размеров и формы. Разделку следует проводить при сваривании изделий, толщина которых превышает 5 мм. при осуществлении односторонней сварки и 8 мм. — при двусторонней. Разделка кромок изделий разной конфигурации осуществляется в соответствии с определенными правилами. Для чего выполняется: цель подготовки и зачисткиПрежде чем приступать к разделке кромок, необходимо произвести очистку поверхности. Присутствие загрязнений отрицательно сказывается на качестве, надежности и прочности шва: в соединении формируются поры, трещины и шлаковые отложения. Как следует проводить зачистку рассказано в следующем подразделе. После зачистки поверхности осуществляется разделка. Данная процедура производится для достижения следующих целей:
Подготовка свариваемых поверхностей Предварительная подготовка свариваемых металлических поверхностей включает выполнение нескольких процедур: Правка может выполняться вручную на специальных правильных плитах из стали или чугуна с помощью пресса или посредством ударов молотка. Предварительная зачистка. В процессе подготовки металл необходимо очистить от масел, красок и лаков с помощью бензина или любого растворителя. Грязь и ржавчина удаляются кордщеткой, абразивными кругами или болгаркой. Изделия из высоколегированных сталей необходимо вычищать до блеска. Кордщетки, насадки на болгарку Разметка позволяет определить формы и размеры будущего изделия. Выполнять разметку нужно внимательно, так как даже небольшая неточность приведет к дефекту. Важно помнить о припуске на обработку. Небольшой подогрев деталей. Механическая резка металлических листов осуществляется с помощью роликовых ножниц, которые оборудованы ножами. Резка деталей из углеродистых сталей проводится плазменно-дуговой или газокислородной технологиями, легированные стали — кислородно-флюсовый и плазменно-дуговой методы. При необходимости изделия подвергаются гибке. После выполнения данных процедур, можно приступать к разделке кромок. Грамотно выполненный скос обеспечивает плавность перехода между свариваемыми заготовками, снизит возможное напряжение на область шва. О том, как правильно это сделать расскажем далее. Скос под сварку труб, трубопроводовСваривание труб осуществляется в различных сферах деятельности: в быту и промышленности, на производстве. Потребность в соединении труб возникает и при первоначальной прокладке и при ремонтных работах. Поэтому важно знать, в каких случаях следует осуществлять разделку, а когда можно обойтись без этой процедуры. Под отводыОтвод представляет собой фитинг, использующийся для изменения направления потока жидкости, газа или пара в трубопроводе. Для получения качественного стыкового соединения отвода с трубой, исполнителю необходимо выполнить односторонний скос одной или двух кромок под углом в 45 градусов относительно оси трубы. Кроме этого, сварщик может сделать угловое соединение, которое осуществляется без скоса. Под штуцерыШтуцер — это патрубок (небольшое отрезок трубы), привариваемый к любой конструкции и служащий для подключения к ней трубопровода с целью отвода жидкости, газа или пара. Штуцер с трубопроводом может соединяться следующими способами:
Скосы с торцов труб можно снимать с помощью механической обработки или газовой резкой. Для сосудов и резервуаровПри разделке кромок под сварку различного рода сосудов и резервуаров следует следовать следующим рекомендациям:
Стыкового соединенияСтыковое соединение (сварка встык) — тип соединения, при котором заготовки расположены в одной плоскости и примыкают друг к другу торцами. Такой тип соединения обеспечивает высокие прочностные характеристики, поэтому применяется при работе с ответственными конструкциями. Изделия толщиной 1,0-3,0 мм. свариваются встык после отбортовки кромок. Для деталей с толщиной стенок до 26 мм. следует выполнить односторонний скос одной или обеих кромок, с толщиной до 60 мм. — двухсторонний скос каждой кромки. Угловых соединенийУгловое соединение — тип соединения, в котором угол между рабочими поверхностями двух заготовок в месте примыкания кромок превышает 30 градусов. При толщине стенок изделия до 3 мм. рекомендуется выполнять отбортовку кромок. При работе с большими толщинами (до 20 мм. Под сварку двутавра (двутавровой балки)Двутавр (двутавровая балка) — стандартный профиль, имеющий сечение близкое по форме к букве «Н». Приваривание балки к различным конструкциям осуществляется посредством таврового соединения, при котором заготовки располагаются под прямым углом друг к другу. Сварка деталей, толщина которых от 4 до 26 мм. осуществляется с односторонним скосом, толстостенные изделия (до 60 мм.) варятся после проведения двухстороннего скоса. Виды (типы, формы) скосов для швов при РДС (ручной дуговой сварке)Различают несколько типов скосов, каждый из которых следует использовать при работе с определенными изделиями и при особых требованиях к сварочному соединению. V-образнаяV-образный скос — односторонний прямолинейный скос одной или двух кромок. Данный тип применяется при работе с листовым металлом, толщина которого варьируется в диапазоне от 3 до 26 мм. X-образнаяX-образный скос — двухсторонний прямолинейный скос двух кромок, который используется при сварке изделий толщиной 12-60 мм. Угол разделки — 60 градусов. U-образнаяU-образный скос — односторонний криволинейный скос обеих кромок, применяется для металла толщиной от 20 до 60 мм. Данный тип особенно активно используется именно при проведении ручной дуговой сварки, так как происходит значительное уменьшение расхода электродов за счет сокращения объема наплавленного металла. Также иногда выделяют K-образный скос, который применяется, когда одно из одна из кромок имеет двухсторонний скос, а другая — односторонний. ОбозначенияПри ознакомлении с чертежами сварных соединений можно встретить буквенные обозначения. Каждому исполнителю необходимо знать их значение. Элементы, встречающие на чертежах по подготовке кромок для сварки:
Способы выполнения обработки (разделки кромок)Как уже было сказано ранее существует несколько способов выполнения разделки кромок:
Для тел вращения механическая обработка проводится на расточном станке; для прямолинейных элементов предназначена фрезерная обработка, механическая строжка, использование метода пневмошлифовки, угловой шлифовальной машинки (болгарки). Ручная обработка подразумевает рубку зубилом или доработку напильником. Правила подготовки изделийПодготовка изделий для последующего проведения сварки — один из важнейших этапов, независимо от используемого метода. Обязательно проведение нескольких процедур: правка, зачистка, разметка, резка. В зависимости от типа обрабатываемых изделий и их толщины возможен нагрев деталей, который обеспечит более качественное соединение. Требования к готовым поверхностямПеред выполнением сварки кромки должны соответствовать следующим требованиям:
Под каким угломУгол скоса — острый угол между плоскостью скоса кромки и торца. Угол скоса зависит от следующих факторов:
Оборудование и инструментИсполнителям предлагается широкий выбор ручных инструментов и автоматического оборудования для подготовки изделия к сварке. Ручная правка осуществляется на правильных машинах ударами молотка, механическая — на листоправильных вальцах. Зачистка может выполняться с помощью специальных растворителей, абразивными кругами, болгаркой. Подогрев осуществляется газовой горелкой. Для резки металла можно использовать газовую горелку, роликовые ножницы. Ручная гибка осуществляется кувалдами, молотками, тисками или наковальнями, роликовые гибочные станки обеспечивают механическую обработку. Станки для обработки кромокДля обработки кромок могут использоваться стандартные инструменты, имеющие широкий диапазон сфер применения: болгарка или напильник. Кроме этого, исполнителям предлагается специализированное оборудование — кромкорезы (на картинке). ВидеоТехнология (разделки кромок)Сущность технологии разделки кромок состоит в снятии части металла под определенным углом (углом скоса) с изделия, который в последствии будет подвергаться свариванию. При снятии необходимо оставить притупление. Оно нужно для того, чтобы во время процессов прихватки и сварки расплавляющиеся кромки не создавали щель, которую будет сложно заварить. Разделка трещин в металле перед сваркойТрещины обязательно разделывать полностью, чтобы имелась возможность проварить их на всю глубину. Разделка осуществляется строго по всей длине трещины, с одной или с двух сторон, в зависимости от толщины детали и удобства проведения процесса. Разделка может проводиться следующими способами:
После разделки углы трещины необходимо засверлить по краям, чтобы предотвратить появление подобных дефектов. Для элементов различной толщиныстыковое соединение с отбортовкой кромок (для тонкого металла) Различные конструкции и элементы имеют разную толщину стенок:
Данные правила являются стандартными для разных деталей и для различных типов соединений. Элементы подготовки кромок под сваркуЭлементы подготовки кромок под сварку Категория: Сварка металлов Элементы подготовки кромок под сварку ГОСТ 5264—80 («Ручная дуговая сварка. Угол скоса кромки а — острый угол между плоскостью скоса кромки и плоскостью торца. При скосе обеих кромок установлен в пределах а=25±2°. При скосе одной кромки угол скоса принимают равным а=45±2°. Скос кромок может быть односторонний и двусторонний, прямолинейный и криволинейный. Угол разделки кромок ((3) образуется скошенными поверхностями двух соединяемых частей изделия. Угол разделки кромок выполняется при толщине металла более 3 мм. Отсутствие угла разделки кромок может привести к непровару по сечению сварного соединения, а также к перегреву и пережогу металла. Рис. 1. Элементы подготовки кромок под сварку: При сварке толстого металла угол разделки кромок позволяет вести сварку отдельными слоями, что улучшает структуру сварного шва и уменьшает сварочные напряжения и деформации. Притупление кромки (с) — нескошенная часть торца кромки, подлежащей сварке. Выполняется для обеспечения устойчивого процесса сварки при выполнении первого (корневого) слоя шва. Отсутствие притупления кромок способствовало бы протеканию металла при сварке (прожог). Величина притупления кромки чаще всего принимается равной 2±1 мм. Зазор между стыкуемыми кромками (в) обеспечивает полный провар по сечению сварного шва при наложении первого (корневого) слоя шва. Отсутствие зазора может привести к непровару корня шва и способствовать увеличению сварочных напряжений. Большое значение для качества сварки имеет равномерность величины зазора по всей длине шва, т. е. соблюдение параллельности свариваемых кромок. Величина зазора чаще всего принимается равной 2±1 мм. Сварка стыковых соединений деталей неодинаковой толщины при разнице, не превышающей значений, указанных в таблице, должна проводиться так же, как деталей одинаковой толщины; конструктивные элементы подготовленных кромок и размеры сварного шва следует выбирать по большей толщине. Для осуществления плавного перехода от одной детали к другой допускается наклонное расположение поверхности шва. При разности в толщине свариваемых деталей свыше значений, указанных в таблице, на детали большей толщины должен быть сделан скос с одной или двух сторон до толщины тонкой детали. Рис. 2. Сварка и подготовка кромок листов неодинаковой толщины: При этом конструктивные элементы подготовленных кромок и размеры сварного шва следует выбирать по меньшей толщине. Скос кромки (листа) регулирует плавный переход от толстой свариваемой детали к тонкой, уменьшая напряжения в сварной конструкции. В стыковых, тавровых и угловых соединениях толщиной более 16 мм, выполненных в монтажных условиях, допускается увеличение зазора между стыкуемыми кромками (в) до 4 мм с одновременным уменьшением значения угла скоса кромок (а) на 3°. Допускается смещение свариваемых кромок перед сваркой относительно друг друга, не более: Реклама:Читать далее:Швы сварных соединений
Статьи по теме:
Влияние затупления передней кромки на локальный теплообмен и распределение давления по плоским пластинам в сверхзвуковом потокеОдин из 4 107 отчетов в серии: Технические примечания NACA доступны на этом сайте. Показаны 1-4 из 55 страниц в этом отчете. PDF-версия также доступна для скачивания. ОписаниеОтчет, представляющий исследование влияния толщины передней кромки на обтекание плоских пластин с квадратным и цилиндрическим затуплением при числе Маха 4 и числах Рейнольдса набегающего потока на дюйм 2380 и 6600. Для условий испытаний носовая часть ударная волна была оторвана, и форма передней кромки не влияла на поверхностное давление за двумя толщинами передней кромки. Представлены результаты по поверхностному давлению, исследованиям поля течения, теплопередаче, толщине пограничного слоя, распределению поверхностного давления, локальному числу Маха, локальному числу Рейнольдса и теплопередаче. Физическое описание54 стр. : больной. Информация о создании Крегер, Маркус О. Декабрь 1957 года. КонтекстЭтот отчет входит в состав сборника под названием: Коллекция Национального консультативного комитета по аэронавтике а также предоставлено отделом государственных документов библиотек ЕНТ цифровой репозиторий, размещенный на Его просмотрели 233 раза. Более подробную информацию об этом отчете можно посмотреть ниже. КтоЛюди и организации, связанные либо с созданием этого отчета, либо с его содержанием. Автор
Создатель
Предоставлено Библиотеки ЕНТ Отдел государственных документовЯвляясь одновременно федеральной и государственной депозитарной библиотекой, отдел государственных документов библиотек ЕНТ хранит миллионы единиц хранения в различных форматах. Департамент является членом Программы партнерства по контенту FDLP и Аффилированного архива Национального архива. О | Просмотрите этого партнера Свяжитесь с нами Исправления и проблемы какая Описательная информация, помогающая идентифицировать этот отчет. Титулы
Описание Отчет, представляющий исследование влияния толщины передней кромки на обтекание плоских пластин с квадратным и цилиндрическим затуплением при числе Маха 4 и числах Рейнольдса набегающего потока на дюйм 2380 и 6600. Физическое описание54 стр. : больной. Предметы Ключевые слова
Язык
Тип вещи
Идентификатор Уникальные идентификационные номера для этого отчета в электронной библиотеке или других системах.
Коллекции Этот отчет является частью следующих сборников связанных материалов. Коллекция Национального консультативного комитета по аэронавтикеНациональный консультативный комитет по аэронавтике (NACA) был федеральным агентством США, основанным 3 марта 1915 года для проведения, продвижения и институционализации авиационных исследований. 1 октября 1958 года агентство было распущено, а его активы и персонал переданы недавно созданному Национальному управлению по аэронавтике и исследованию космического пространства (НАСА). О | Просмотрите эту коллекцию Архив технических отчетов и библиотека изображений Эта подборка материалов из Архива технических отчетов и библиотеки изображений (TRAIL) включает труднодоступные отчеты, опубликованные различными государственными учреждениями. О | Просмотрите эту коллекцию Какие обязанности у меня есть при использовании этого отчета? Цифровые файлы
КогдаДаты и периоды времени, связанные с этим отчетом. Дата создания
Добавлено в цифровую библиотеку ЕНТ
Описание Последнее обновление
Статистика использованияКогда последний раз использовался этот отчет? Дополнительная статистика Взаимодействие с этим отчетомВот несколько советов, что делать дальше. Поиск внутриПоиск Начать чтение PDF-версия также доступна для скачивания.
Цитаты, права, повторное использование
Международная структура взаимодействия изображенийМы поддерживаем IIIF Презентация API Распечатать/поделиться Полезные ссылки в машиночитаемом формате. Архивный ресурсный ключ (ARK)
Международная структура взаимодействия изображений (IIIF)
Форматы метаданных
Картинки
URL-адреса
Статистика
Крегер, Маркус О. декабрь 1957 г .; (https://digital.library.unt.edu/ark:/67531/metadc56855/: Усовершенствованная модель затупления кромки инструмента при обработке«>Качмарек Дж. (1970) Основы режущей, абразивной и эрозионной обработки. PWN, Варшава Google ученый Мирник М. (1996) Применение нечетких множеств к анализу немонотонной функции стойкости инструмента при резке. Post Technol Masz i Urządz 20(4):41–51 Google ученый Taylor W (1907) Об искусстве резки металлов. Транс ASME 28:31–428 Google ученый Degner W, Lutze HG, Smejkal E (1972) Spanendeformung. ВЭБ, Verlag-Technik, Берлин Google ученый Пакосевич Б. (1979) Условия обработки при точении стали и чугуна. Стандарты IOS. WPN, WEMA, Варшава Google ученый Przybylski L (2000) Стратегия выбора условий обработки современными инструментами. Google ученый Торговец М.Е. (1967) Методы производства, относящиеся к международной программе кооперативного развития резки металлов. Первый технический отчет по проекту ММП № 9-712 подготовка. по контракту AF 33(615)-3835 Essel K, Hänsel W (1972) Analyze der Standzeitgleichungen. Industrie-Anzeiger 94(5):92–93 Google ученый Кроненберг М. (1954) Grundzüge der Zerspanungslehre. Springer, Берлин Google ученый Кроненберг М. (1971) Ersatz der Taylor-Formel durch eine neue Standzeitgleichung. Zeitschrift für Wirtschaftliche Fertigung 66(1):4–7 Google ученый Spur G (1079) Handbuch der Fertiguntechnika—Spanen. Carl Hauser Verlag, Мюнхен Google ученый Schultz H, Kalhöfer E (1998) Standzeit vorhersagen. Werkstatt und Betrieb 131(5):374–375 Google ученый Ojha DK, Dixit US (2005) Экономичная и надежная процедура оценки стойкости инструмента для токарной обработки. Int J Adv Manuf Technol 26 (7–8): 726–732 Артикул Google ученый Harasymowicz J (1999) Анализ значения экспоненты s формулы Тейлора в обработке разрезания [Analiza wartości wykładnika s wzoru Taylora w obróbce skrawaniem]. Арх Технол Маш Автомат 19(2):15–23 Google ученый Pilafidis EJ (1971) Наблюдения за значениями Taylor n , используемыми при резке металлов. Google ученый Холодная обработка B (1961 г.) Обрабатываемость металлов и затраты на механическую обработку. Int J Mach-Tool Des Res 1(3):220–248 Статья Google ученый König W, Depiereux WR (1969) Wie lassen sich Vorschub Und Schnittgeschwindigkeit optimieren? Industrie-Anzeiger 61:1481–1484 Google ученый Florek H (1978) Современные формулы зависимости стойкости инструмента при резке от параметров резания. Материалы научно-технической конференции: «Постэмпы с техникой wytwarzania. Skrawanie wiórowe, kształtowanie erozyjne i urządzenia technologiczne. Колобжег 21–23:36–39 Google ученый Кроненберг М (1970) Замена формулы Тейлора новым уравнением стойкости инструмента. Статья Google ученый Colding B (1959) Трехмерное уравнение стойкости инструмента. Экономика обработки. Trans ASME J Eng Ind 81:239 Google ученый Колдинг Б., Кениг В. (1971) Справедливость уравнения Тейлора при резании металлов. Анналы CIRP 19: 793–812 Google ученый Florek H (1975) Анализ применимости формулы Кроненбера в зависимости стойкости инструмента при резке от параметров резания [Анализа przydatności wzoru Kronenberga na zależność okresu trwałości ostrza od parametrów skrawania]. Материалы конференции: «Постэмпы в розвою бадан с закресу технологии машин». Kraków 3(A) Ковстубхан М.В., Филиг П.К. (1991) Об уравнении стойкости инструментов из быстрорежущей стали с покрытием TiN. Артикул Google ученый Abdou G, Yien J (1975) Анализ силовых характеристик и стойкости инструмента при фрезерных операциях. Int J Adv Manuf Technol 10(1):11–18 Статья Google ученый Джейкобс Х.-Дж., Библер К. (1993) Werkzeugstandzeit: прогноз по Рехнеру. ВДИ-З 135(9):112–114, 117–118 Google ученый Галанте Г., Ломбардо А., Пассаннанти А. (1998) Моделирование срока службы инструмента как стохастический процесс. Int J Mach Tools Manuf 38(10–11):1361–1369 Артикул Google ученый Озлер Л., Инан А., Озлер С. (2001) Теоретическое и экспериментальное определение стойкости инструмента при горячей обработке аустенитной марганцовистой стали. Статья Google ученый Аксинте Д.А., Беллуко В., Де Шифф Л. (2001) Надежные измерения стойкости инструмента при токарной обработке — применение для оценки эффективности смазочно-охлаждающей жидкости. Int J Mach Tools Manuf 41(7):1003–1014 Статья Google ученый Oraby SE, Hayhurst DR (2004) Определение срока службы инструмента на основе измерения износа и изменения коэффициента усилия инструмента. Int J Mach Tools Manuf 44(12–13):1261–1269 Артикул Google ученый Астахоф В.П., Галицкий В.В. (2005) Проверка стойкости инструмента в пушечном сверлении: применение группового метода обработки данных (GMDH). Int J Mach Tools Manuf 45(4–5):509–517 Артикул Google ученый Jandecka K, Skopecek T, Syriste D (2005) Standzeit rauf, Kosten runter. Programm optimiert Schnittparameter und Bearbeitungsstrategien bei Fräsen. Машиненмаркт 9:28–29 Google ученый Цай М.К., Ли Б.И., Ю С.Ф. (2005) Расчетное моделирование стойкости инструмента при высокоскоростном фрезеровании инструментальной стали SKD61. Int J Adv Manuf Technol 26(7–8):711–717 Статья Google ученый Мазур М. (1961) Техническая терминология. WNT, Варшава Google ученый Pluta Z (1994) Рефлексия над термином «скорость движения». Нормализация 9:10–11 Google ученый Pluta Z (2007) Основы выравнивания поверхности эластичными колесами. Wydawnictwo Politechniki Koszalińskie, Кошалин, стр. |